焙烧电极
电极糊和电极烧结 (9)

电极糊和电极烧结 (9)电极糊和电极烧结第一节概述连续式自动焙烧电极(简称自烧电极)是由电极糊和铁壳组成的。
电极在电石炉内工作时是要不断消耗的,所以需要继续不断地下放电极,以资补充。
当电极下放到导电颚板下部时,经过1000?左右的高温焙烧,使电极糊碳化而成电极。
因为电极铁壳可以在电炉不停电的情况下继续焊接,电极糊不断地向铁壳内加入,而且又是在电石炉内烧结而成的,所以叫做连续式自动焙烧电极。
自烧式电极广泛地用于电石炉和铁合金炉。
这种电极的特点是直径可以扩大到2米,不用螺丝接头,在电石炉上连接时非常方便,而且价格低廉,这就给电石炉向大容量发展创造了有利的条件。
在整个电石炉的设备中,电极就是心脏。
在电石生产中,电流是通过电极输入炉内,产生电弧,进行冶炼电石,电极在整个电炉中是占有着极其重要的地位。
在设计电石炉中,有许多参数是参考电极直径进行的。
电极直径之大小,由通过电极截面积上的电流所允许的电流密度来决定,如直径小,则允许的电流密度大,直径大,则允许的电流密度小。
电流密度与电极直径选择恰当与否,对整个电炉来讲是非常重要的。
电极直径大小的决定,对设计中考虑电极同心圆直径、电极间距、炉膛内径、炉膛深度,甚至于炉膛外径,炉底厚度等都有很大的指导意义。
因为这些尺寸的数据均参考与电极成倍数关系的经验数据。
三相电炉电极,一般多采用三角形布置,设计时,既要考虑电极之间的距离,使它有足够而均匀的温度分布,并能形成相互串通的更大高温区,又要考虑电极与炉壁之间有足够的距离,使它对炉壁辐射均匀,避免炉壁过快烧坏。
电极同心圆直径与炉壁内径之比,一般为 0.44(炉之内径为电极同心圆直径的2.25 倍)。
关于电极同心圆直径与电极直径的比例,所采用的经验数据,目前大多数为2.7倍较好。
炉膛深度是电极直径的2.3倍。
另外,电炉直径、电极插入炉料深度,炉底厚度、炉底面积、炉子容量等的计算都和电极有关系,这里不一一叙述了。
由此可见,电极在设计整个电炉的设备中,占着极其重要的地位。
电极焙烧及相关要点

电极焙烧及相关要点电极电极是电石炉的心脏,只有充分地了解电极的组件,才能更好的控制、操作及保护好电极,才能更好的完成生产任务。
电极好比人的身体,电极壳是躯干、电极糊好比营养、那么电流就是精神,只有控制好这三样,才能更好的把电极保护好。
1.电极壳电极壳是自焙电极的关键部分。
电极壳的完好与否直接关系到生产能否安全、连续、稳定运行,是生产过程中必不可少的保障因素。
25500KV A密闭型电石炉自焙电极是以¢1250mm电极壳为铠装,进行电极的自焙。
在电极焙烧过程中,电极壳不仅使电极成型而且还兼起导电作用。
(根据有关资料介绍,由于钢质材料的导电系数大以及在导电过程中的集肤效应,电极壳中通过的电流为总电流的80%左右)因此,电极壳在电石生产中成为不可或缺的器件。
电极壳的构成是有均匀的12片3mm的筋板;12片2mm的弧形板和12跟¢18mm厚的圆钢,经过裁剪、冲压、折弯、缝焊而成。
1.1电极壳的导电特性(1)外壳有效导电截面积约1250×3.14×2=7850㎜2(2)外筋板有效导电截面积大约30×7×12=2520㎜2(3)内筋板有效导电截面积约185×2×12=4440㎜2(4)圆钢有效导电截面积约81×3.14×12=3052㎜2电极壳的有效导电截面积=17862㎜2钢材的电流密度为2.2~2.4A/㎜2故电极壳的有效导电截面积可承受的电流为39296~42869A与《埃肯手册》中所提到的:在电极焙烧初期为防止电极壳烧损,操作电流应控制在40000A以内基本相符。
1.2电极壳的物理特性由于电极壳为钢质材料制成,故其物理特性与钢材相符,据查找相关钢材特性为:密度 7.86g/㎝3;软化点 450~550℃;熔点1535℃;沸点 2750℃1.3电极壳外筋板最大可输入电流接触元件夹紧外筋片面的有效长度约为435㎜,夹电极壳外筋板厚度约为 7㎜电极壳外筋板可输入的最大电流为S=435×7×12=36540㎜2电极壳外筋板可输入的最大电流为I=36540×(2.2~2.4 A/㎜2)=(80388~87700)A常温下。
电极焙烧管理技术标准

内蒙宜化-电石公司-管理标准生产中心—工艺模块GLBZ-DS-SC
电极焙烧管理技术标准
1 目的
为保障生产安全,规范电极焙烧操作。
2 电极焙烧
2.1当电极工作长度小于1900mm时,必须对电极进行一次补长焙烧.
2.2,焙烧100mm以上电极,必须将变压器倒为星接,并按照电极焙烧进度表进行, 不允许角接焙烧.
2.3焙烧电极超过200mm,有生产中心出具电极焙烧进度表,各事业部按照电极焙烧进度表进行焙烧.
2.4焙烧电极必须在闭料状况下进行,不允许在干烧情况下焙烧.
3 电极焙烧操作
3.1焙烧电极时将把持器位置降至最低位置.
3.2焙烧电极期间不允许压放被焙烧电极.
3.3焙烧电极期间不允许移动(提升或下降)电极,如被焙烧电极电流超出控制电流时,可用另外两个电极进行调整.
3.4只有在停电状态下方可移动(提升或下降)被焙烧电极.
3.5当发生电极冒烟或其他故障时,应立即停电进行观察,确认没有漏糊或其他电极故障时,方可重新送电.
4 本规定由电石安全生产中心负责解释、考核,从下发之日开始执行。
起草:孙克鹏审核:蔡勇批准:熊俊更改状态:A/0 签发日期:2011年6月24日。
电石炉自焙烧电极事故分析及处理措施

电石炉自焙烧电极事故分析及处理措施在整个电石炉或铁台金炉设备中,电极就是心脏。
在电石生产中,电流通过电极输入炉内,产生电弧,进行电石冶炼。
电极起着导电和传热作用,自焙电极由电极糊和电极铁壳组成。
电极铁壳由厚度1~2.5㎜的铁板卷制而成,期中装有铁拉筋,以增强电极的强度和导电性。
电极铁壳装在电极把持器内,然后将电极糊装填在铁壳内。
该电极在电石炉工作时不断消耗,因此,需要不断地下放电极,以资补充。
当电极下放到导电颚板下部时,电极糊经过1000℃的高温焙烧碳化成电极。
由于电极铁壳可以在电石炉不停炉的情况下连续焊接,电极糊不断地加入到铁壳内,且又是在电石炉内烧结而成的,因此自焙电极又叫连续式自动烧结电极。
1、电极糊的原料电石炉对电极糊的要求较高,须具有连续的稳定性,适宜的流动性,良好的导热性能。
电极则必须具有高度的耐氧化性和导电性。
因此,电极在生产中应能够耐高温,同时热膨胀系数要小;具有较小的气孔率,以使加热状态下电极氧化缓慢;具有较小的电阻系数,以降低电能损耗;具有较高的机械强度,不致因机械或电气负荷的影响,使电极软断;必须经受得住炉料崩塌导致的轻微冲击。
根据这些要求,制造电极糊的原料有两大类:古体碳素原料和粘结剂。
以往对其成分的控制项目有:固定碳、挥发分、灰分和水分的含量。
固定碳素原料常用的有:无烟煤、焦炭和人造石墨。
它们是制造电极糊的基本原料,电极烧成后,就成为电极的骨架。
粘结剂常用煤焦油和煤沥青,经过焙烧后能够转变为坚固的焦炭纲,起焦结作用,形成自焙电极整体。
2、电极糊焙烧过程中的性质变化2.1焙烧热源在电石冶炼过程中,电极不断消耗而逐渐下放,电极糊温不断升高排除挥发物,最后完成烧结过程。
电极糊在烧结过中需要热量,其焙烧热源主要来自三个方面:(1)电极自身的传导热:其热量约占焙烧电极总热量的60%,是电极焙烧的主要热量来源。
(2)电阻热:包括料面以上电极电流通过时所产生的电阻热和铜瓦与电极接触的电阻热两部分。
自焙电极操作规程1
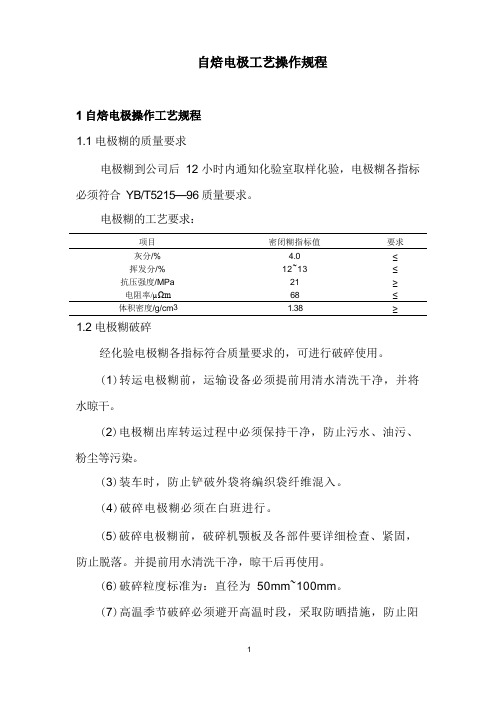
1.1 电极糊的质量要求电极糊到公司后12 小时内通知化验室取样化验,电极糊各指标必须符合YB/T5215—96 质量要求。
电极糊的工艺要求:项目密闭糊指标值要求灰分/% 4.0 ≤挥发分/% 12~13 ≤抗压强度/MPa 21 ≥电阻率/µΩm68 ≤体积密度/g/cm3 1.38 ≥1.2 电极糊破碎经化验电极糊各指标符合质量要求的,可进行破碎使用。
(1)转运电极糊前,运输设备必须提前用清水清洗干净,并将水晾干。
(2)电极糊出库转运过程中必须保持干净,防止污水、油污、粉尘等污染。
(3)装车时,防止铲破外袋将编织袋纤维混入。
(4)破碎电极糊必须在白班进行。
(5)破碎电极糊前,破碎机颚板及各部件要详细检查、紧固,防止脱落。
并提前用水清洗干净,晾干后再使用。
(6)破碎粒度标准为:直径为50mm~100mm。
(7)高温季节破碎必须避开高温时段,采取防晒措施,防止阳光直射温度升高电极糊粘连。
(8)电极糊出库后需及时全部破碎,避免增加转运等环节带来污染。
(9)破碎完毕后,破碎工必须及时将破碎好的电极糊装袋入库备用。
(10) 破碎工在电极糊装袋后应及时用标签标注电极糊批次、破碎时间、破碎人等信息。
(11) 入库前,库管员须对电极糊清洁情况进行详细检查,符合清洁要求后方可按入库程序验收入库。
2.1 电极筒制作(1)设备人员严格按照电极筒设计图纸及制作技术要求制作电极筒。
(2)用于制作电极筒的钢板要清洁,厚度均匀平整,不能有生锈现象。
(3)电极筒制作规格要准确,以便于接长,焊口必须坚固且光洁。
(4)接长电极壳时,必须对准中心线,筋片吻合并要插入一小部份,焊口表面光洁,以防止电极糊下入时卡住,造成悬糊。
(5) 为扩大电极糊和电极壳的接触面积,提高电极的烧结质量,在电极壳内部设有6-7 个筋片。
(6)制作电极壳的具体参数如下:电极壳大圆直 径/mm电极壳小圆直 径/mm钢板厚度/mm 筋片数量/个 筋片高度 /mm 触舌数 量/个触舌尺寸 /mm800-37200--2.2 电极筒安装(1)在电极筒进行装接前,必须认真检查,如发现变形、生锈 应将电极筒进行校圆、除锈后再进行安装(变形严重无法校正、焊缝 脱落或者生锈严重的不能进行安装)。
采用320小时曲线焙烧Φ400mm电极工艺探讨

1 前言
低温 阶段 : 1 0 3 0 ( 3 — 5 ℃)
由于 我厂 目前 环式 炉 焙 烧 能力 所 限 , 面
该 阶段 主 要 是 把 一 些 吸 附 的 冷 却 水 和
对大量焙烧品供不应求 的市场情况 , 我们对 粘结剂轻质馏份排除掉。此时制品内部的粘 原 30 2 小时焙烧 曲线进行 改进 , 运用 30 2 小 结剂处于软化状态 , 随着温度的提高粘结剂 时 升 温 曲线 成 功 地 对  ̄40 m 电极 进 行 了 完全熔 化 , 0m 粘度 大大降低 , 在重力的作用下 焙烧 , 改变了碳素行业  ̄ 5m 以上大规格 粘 结剂 向下 流动 , 30 m 同时 由于 电极 垂 直方 向存 电极用 3 0 6 小时焙烧 曲线的工艺方式。 在着温度梯 度,粘结剂次第进入软化状态 , 2 生产 工艺 这样就在上下端之间产生一个 张力 , 在这个
5 mmo 0
度不一样 而导致制品相互挤压产生变形。
出 于对 低 温 区易 出现 变形 情 况 的 考虑 ,
23 焙 烧 工 艺 .
我们加快 了低温的升温速度 , 起始 温度 由原
[ 收稿 日期] 20 —22 作者简介 : 02 0—5 叶麟 . 工艺工程师. 电话 2327 转 8 1 3825 28
一
根 据  ̄4 0 电极 的外 形 尺 寸 ( 3 x 0mm  ̄4 0
190 m, 4 m 单重 4 718 8 . 公斤 )采用每箱 每 2 ,
层装 6 每炉共装 7 根。计 3. 吨。保 根, 2 56 0 温料粒度 0 6 m, - m 水份 2 炉箱温度 4 ℃, %, 5 电极 间 距 3m 5 m, 电极 与 炉 墙 的 间 距 :
度变化进行 了研究 , 采取 在各个升温阶段使用不 同升温速度进行 工艺创新 。 关词 : 新工艺 焙烧电极
焙烧电极危险危害因素预防措施

焙烧电极危险危害因素预防措施
1、直接原因
电极压放过量,电极焙烧硬度不够造成电极变形、有裂纹,在提电极时电极断裂,电极糊外漏产生爆炸。
2、间接原因
2.1负责的工艺员对无法辨别的炉况,没有及时停炉观察,盲目操作造成电极断裂。
2.2操作人员观察不仔细,发现事故不及时,造成事故恶化。
2.3操作工安全意识淡薄,自我防护意识差。
2.4工艺负责人员责任心不强,思想麻痹大意,安全意识淡薄,没有相互沟通探讨,解决问题不及时。
2.5管理不当,电极糊质量差,灰分、油分过大,电极强度不够。
措施:
1、加强员工的培训,增强员工安全防护、保护意识。
2、严格管理,严格执行操作规程,工作认真仔细,精心操作,对变化较大的工艺要及时汇报上级领导。
3、加强电极糊管理,严格电极糊验收制度,杜绝不合格产品进入,防止事故再次发生。
4、各级管理人员要从细节上观察事物,不能盲目操作指挥,所有人员要认真分析、学习案例引以为戒。
炭素,碳素,电极,焙烧,煅烧,浸渍,石墨化

标题:探讨炭素材料的制备和特性摘要:炭素作为一种重要的材料,在电化学、材料科学和能源领域具有广泛的应用,其制备方法和性质特点备受关注。
本文将从炭素的定义和特性开始,探讨其制备过程中的焙烧、烧结和浸渍等关键步骤,最终展望其在未来科技发展中的潜在应用。
通过全面评估和深度分析,以期为读者提供更加全面、深刻和灵活的理解。
1. 炭素的定义和特性在自然界中,炭素是一种非常常见且重要的元素,其化学性质和物理性质使得其在材料科学中具有重要地位。
炭素可以以多种形态存在,包括金刚石、石墨、纳米碳管等,每种形态都具有不同的特性和应用领域。
2. 石墨化的制备过程石墨是一种典型的炭素形态,其制备过程主要包括焙烧和烧结两个关键步骤。
在高温下对原料进行焙烧,使得原料中的杂质得以氧化或挥发;接着进行烧结,将焙烧后的物质经过高温处理形成石墨结构。
对石墨材料进行浸渍处理可以改善其电化学性能,提高其在电极中的应用性能。
3. 炭素材料的应用展望基于石墨化炭素的制备过程和特性特点,其在电化学储能、光伏发电、导热材料等方面具有广泛的应用前景。
石墨电极作为锂离子电池、超级电容器等电化学储能装置的关键材料,具有很好的循环稳定性和电化学性能;石墨材料在光伏发电和导热材料领域也发挥重要作用,为可再生能源和高性能材料的发展提供重要支撑。
结论炭素材料作为一种重要的材料,在能源、材料和环境领域具有广泛的应用前景。
其制备过程中的焙烧、烧结和浸渍等关键步骤对其性能具有重要影响,因此对这些步骤的深入了解和优化将有助于提高炭素材料的性能和应用价值。
未来,随着科技的不断进步,炭素材料必将在更多领域展现出其巨大的潜力。
个人观点作为一种重要的功能材料,炭素材料的研究和应用一直备受关注。
石墨化炭素作为其重要形态之一,在能源、材料和电化学等领域具有广泛的应用前景。
对石墨化炭素制备过程和特性的深入理解和研究,将有助于推动其在各个领域的应用和发展。
我对炭素材料的未来发展充满期待,相信其一定会发挥出更多的潜力。
- 1、下载文档前请自行甄别文档内容的完整性,平台不提供额外的编辑、内容补充、找答案等附加服务。
- 2、"仅部分预览"的文档,不可在线预览部分如存在完整性等问题,可反馈申请退款(可完整预览的文档不适用该条件!)。
- 3、如文档侵犯您的权益,请联系客服反馈,我们会尽快为您处理(人工客服工作时间:9:00-18:30)。
电极焙烧及操作
1电极糊
1电极糊的组成
电极糊的主要由固定碳素原料、石墨粉和泥球(粘结剂)组成。
2电极糊的质量标准
固定碳含量≥80%,灰分≤4%,挥发分:12.5~15.5%
2电极焙烧
1电极焙烧的热源
⑴传导热:电极本身具有良好的导热性,而处在孤光区的电极部分具有2500℃以上的高温,因此电极可通过自下而上的热量传导,使上部的电极和电极糊得到更多的热量。
⑵电阻热:当大电流通过电机壳和熔化的电极糊而产生的较大的电阻热,尤其是当电极太短,无法满足生产需求时,补压电极后的电极焙烧所需热量主要靠电阻热来进行。
⑶辐射热:主要由炉料表面CO燃烧所释放的热量。
2电极焙烧的三个主要阶段
⑴第一阶段(软化阶段):从室温到200℃,电极糊块状固体逐渐软化的阶段。
⑵第二阶段(挥发阶段):从200℃~600℃,熔化的电极糊的挥发分开始挥发的阶段。
⑶第三阶段(固化阶段):600℃以上为电极糊的固化温度,成型过程。
`
三、电极压放量与焙烧时间
1、电炉正常运行时,通过电极本身自焙每小时可焙烧成型30~40mm,故在正常情况下,电极的压放时间间隔控制在半小时以上。
2、电极通过补压,在正常焙烧时,每100mm的电极需要一个小时的焙烧时间。
若电石炉长时间进行检修,导致炉温降低,可适当延长焙烧时间。
若电极在生产时,长时间未压放,焙烧时可适当缩短焙烧时间(缩短时间不超过2小时)。
若电极的补压量超大(500mm以上)时,电石炉操作工应开炉门操作(35档),向电极周围推料,并观察挥发分的挥发情况。
3、在焙烧电极期间,严禁中控工提升电极。
通过电流变化情况适当点落电极,切不可将电极落死,否则电极将产生巨大的涡流,容易发生电极事故。
在电极焙烧期间,中控工尽量不动该相电极,可通过操作控制其它两相电极来渐渐控制该相电极的二次电流。
4、焙烧电极时,用一半的焙烧时间在最低档位运行,待挥发分由小变大然后由大变小时再考虑升负荷继续焙烧。
5、在焙烧电极时尽量不出炉,待焙烧完时再安排出炉,焙烧电极所对应的炉眼尽量安排最后出炉。
如果焙烧电极过长,考虑到有可能出现翻电石的现象时,可在电极焙烧时间过半,安排出其它炉眼,最后再考虑对该炉眼出炉(同时降低电压等级,将二次电流控制在安全范围、注意下落电极),并控制出炉量,出完炉,检查电极,再升负荷。
短电极进行焙烧时,由于其自身重力小,对其进行补压后,操作工将电极糊柱高度控制在工艺指标范围以内(夏季:4.0~4.5m,冬季:3.8~4.3m)。
长电极进行焙烧时,由于其自身重力大,对其进行补压后,操作工可将电极糊柱高度控制在3.3~3.5m以内,待电极焙烧过半时间后(即挥发分已经由大变小固化阶段)将电极糊柱高度补充到工艺指标范围以内。
6、焙烧电极采用开炉门操作,对电极进行焙烧结束至净化正常开车后,方可关闭炉门,然后正常操作,升负荷切忌跳跃式提升负荷,应平稳提升负荷。
当电极焙烧完2小时后,根据电极长短可考虑对该相电极进行压放。
注:在目前形势下,严禁出现电极漏湖现象,焙烧电极的目地就是要保质保量的完成电极的焙烧,同时在焙烧中提高炉温,改善炉况,在操作中充分通盘考虑,从而达到正常生产的最终目标,。