机床重要部件的有限元分析及优化设计
立式加工中心立柱结构有限元分析及改进研究

—256—技术改造立式加工中心立柱结构有限元分析及改进研究崔争第 方秀菊 曲耀辉 颜 荣(中科美菱低温科技股份有限公司,安徽 合肥 230000)摘 要:立式加工中心是现代机械制造加工中十分重要的加工设备,包含了床身、主轴线以及立柱等。
为了进一步改进立柱结构,利用Solidworks 2018三维软件进行建模,并通过SOLIDWORKS Simulation 开展有限元分析,得到立柱结构应力图与位移图,以此为基础进行改进设计,在降低立柱结构重量的同时,缩小了最大位移量,并有效避免了应力集中。
关键词:立式加工中心;立柱结构;有限元;改进伴随着现代制造业的不断发展,对加工中心的需求量越来越多,所以,将现代设计方法融入到加工中心结构设计与完善工作中,力求进一步降低加工中心设备加工难度与周期。
一直以来,国内外都十分重视机床设备的优化与创新,依托于现代计算机辅助设计软件,使得机床动态设计工作更加成熟,可以根据设备使用环境的拓扑来弥补使用问题。
本文从两个方面入手进行分析和改进,其一是对立式加工中心材料运用的改进,既可以保证加工的便捷性,避免产生材料浪费,还能够改善加工中心性能;其二,对立柱结构中的大件进行改进,降低机构质量。
一、立式加工中心结构建模与有限元分析(一)模型建立立式加工中心涵盖的主要部件有床身、主轴箱以及立柱等,立柱通过螺栓与床身紧固在一起,主轴箱顺着导轨在立柱上做进给运动,可见立柱是立式加工中心十分重要的部件。
本研究中的立柱是通过整体铸造再进行机加工得到的,内侧为空心结构,在外侧壁上设置有加强筋,保证立柱强度。
加工中心工作时,立柱是需要承受较大的力,需要对立柱的强度进行仿真分析。
利用Solidworks 2018三维软件进行建模,如图1所示。
图1 加工中心立柱模型(二)有限元分析利用Solidworks 软件对力主结构进行简化,去除掉结构中的工艺孔、倒角、对强度影响不大的复杂结构等,加载SOLIDWORKS Simulation 开展有限元分析,假如结构中各个材料密度均匀,连接牢靠。
基于solidworks的槽钢构建有限元分析、优化设计及对有限元的展望
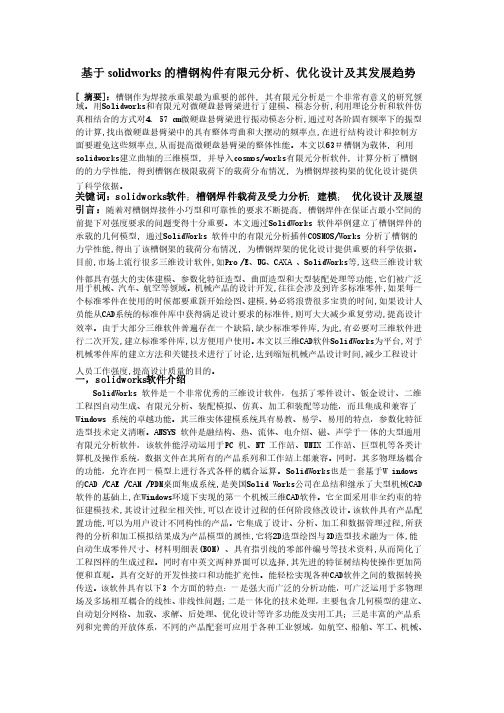
基于solidworks 的槽钢构件有限元分析、优化设计及其发展趋势[ 摘要]:槽钢作为焊接承重架最为重要的部件槽钢作为焊接承重架最为重要的部件, , , 其有限元分析是一个非常有意义的研究领其有限元分析是一个非常有意义的研究领域。
用域。
用Solidworks Solidworks Solidworks和有限元对微硬盘悬臂梁进行了建模、模态分析和有限元对微硬盘悬臂梁进行了建模、模态分析和有限元对微硬盘悬臂梁进行了建模、模态分析,,利用理论分析和软件仿真相结合的方式对真相结合的方式对4. 57 cm 4. 57 cm 4. 57 cm微硬盘悬臂梁进行振动模态分析微硬盘悬臂梁进行振动模态分析微硬盘悬臂梁进行振动模态分析,,通过对各阶固有频率下的振型的计算的计算,,找出微硬盘悬臂梁中的具有整体弯曲和大摆动的频率点找出微硬盘悬臂梁中的具有整体弯曲和大摆动的频率点,,在进行结构设计和控制方面要避免这些频率点面要避免这些频率点,,从而提高微硬盘悬臂梁的整体性能。
本文以从而提高微硬盘悬臂梁的整体性能。
本文以636363#槽钢为载体#槽钢为载体#槽钢为载体, , , 利用利用solidworks solidworks建立曲轴的三维模型建立曲轴的三维模型建立曲轴的三维模型, , , 并导入并导入并导入cosmos/works cosmos/works cosmos/works有限元分析软件有限元分析软件有限元分析软件, , , 计算分析了槽钢计算分析了槽钢的的力学性能的的力学性能, , , 得到槽钢在极限载荷下的载荷分布情况得到槽钢在极限载荷下的载荷分布情况得到槽钢在极限载荷下的载荷分布情况, , , 为槽钢焊接构架的优化设计提供为槽钢焊接构架的优化设计提供了科学依据。
关键词:solidworks 软件;槽钢焊件载荷及受力分析;建模; 优化设计及展望 引言:随着对槽钢焊接件小巧型和可靠性的要求不断提高随着对槽钢焊接件小巧型和可靠性的要求不断提高, , , 槽钢焊件在保证占最小空间的槽钢焊件在保证占最小空间的前提下对强度要求的问题变得十分重要。
CATIA装配部件有限元分析
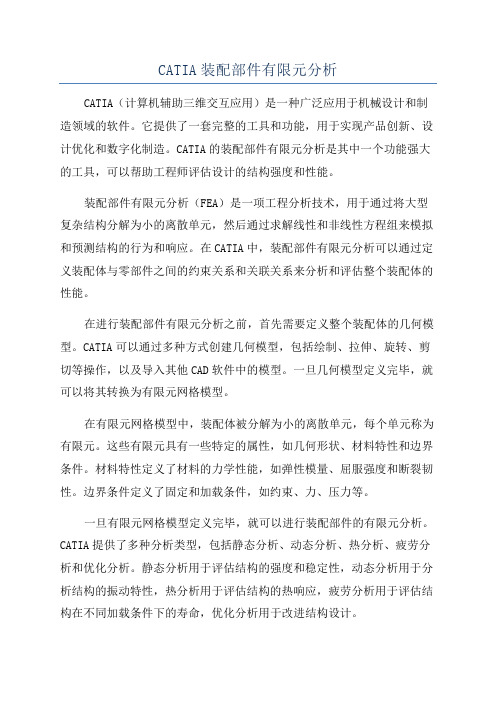
CATIA装配部件有限元分析CATIA(计算机辅助三维交互应用)是一种广泛应用于机械设计和制造领域的软件。
它提供了一套完整的工具和功能,用于实现产品创新、设计优化和数字化制造。
CATIA的装配部件有限元分析是其中一个功能强大的工具,可以帮助工程师评估设计的结构强度和性能。
装配部件有限元分析(FEA)是一项工程分析技术,用于通过将大型复杂结构分解为小的离散单元,然后通过求解线性和非线性方程组来模拟和预测结构的行为和响应。
在CATIA中,装配部件有限元分析可以通过定义装配体与零部件之间的约束关系和关联关系来分析和评估整个装配体的性能。
在进行装配部件有限元分析之前,首先需要定义整个装配体的几何模型。
CATIA可以通过多种方式创建几何模型,包括绘制、拉伸、旋转、剪切等操作,以及导入其他CAD软件中的模型。
一旦几何模型定义完毕,就可以将其转换为有限元网格模型。
在有限元网格模型中,装配体被分解为小的离散单元,每个单元称为有限元。
这些有限元具有一些特定的属性,如几何形状、材料特性和边界条件。
材料特性定义了材料的力学性能,如弹性模量、屈服强度和断裂韧性。
边界条件定义了固定和加载条件,如约束、力、压力等。
一旦有限元网格模型定义完毕,就可以进行装配部件的有限元分析。
CATIA提供了多种分析类型,包括静态分析、动态分析、热分析、疲劳分析和优化分析。
静态分析用于评估结构的强度和稳定性,动态分析用于分析结构的振动特性,热分析用于评估结构的热响应,疲劳分析用于评估结构在不同加载条件下的寿命,优化分析用于改进结构设计。
装配部件有限元分析的结果通常以图形和数值形式呈现。
CATIA可以生成各种图表和图形,以显示应力、应变、位移、刚度等参数的分布情况。
此外,CATIA还可以生成报告和动画,以帮助工程师更好地理解和解释分析结果。
总之,CATIA的装配部件有限元分析是一种强大的工具,可以帮助工程师评估装配体的强度、稳定性和性能。
通过使用CATIA的装配部件有限元分析,工程师可以优化设计、降低制造成本并提高产品质量。
有限元分析在机床结构优化设计中的应用
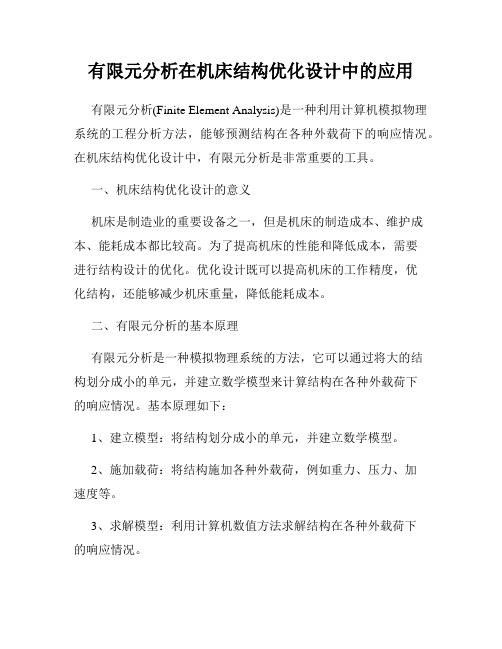
有限元分析在机床结构优化设计中的应用有限元分析(Finite Element Analysis)是一种利用计算机模拟物理系统的工程分析方法,能够预测结构在各种外载荷下的响应情况。
在机床结构优化设计中,有限元分析是非常重要的工具。
一、机床结构优化设计的意义机床是制造业的重要设备之一,但是机床的制造成本、维护成本、能耗成本都比较高。
为了提高机床的性能和降低成本,需要进行结构设计的优化。
优化设计既可以提高机床的工作精度,优化结构,还能够减少机床重量,降低能耗成本。
二、有限元分析的基本原理有限元分析是一种模拟物理系统的方法,它可以通过将大的结构划分成小的单元,并建立数学模型来计算结构在各种外载荷下的响应情况。
基本原理如下:1、建立模型:将结构划分成小的单元,并建立数学模型。
2、施加载荷:将结构施加各种外载荷,例如重力、压力、加速度等。
3、求解模型:利用计算机数值方法求解结构在各种外载荷下的响应情况。
4、分析结果:通过分析求解结果,评估结构的性能、强度、刚度等方面。
5、优化设计:根据分析结果,对结构进行优化设计。
三、有限元分析在机床结构优化设计中的应用有限元分析可以应用于机床结构的优化设计,主要包括以下几个方面。
1、材料的选择在机床结构中,材料的选择非常重要,因为不同材料的性质不同,会影响机床的工作精度和性能。
利用有限元分析可以预测机床在各种外载荷下的响应情况,并确定材料的合适选择。
2、优化结构设计机床结构非常复杂,因此在设计过程中可能存在缺陷或者弱点。
有限元分析可以帮助设计者预测和评估机床结构在各种载荷下的响应情况,并帮助设计者确定如何优化结构设计。
3、优化布局方案机床的各种部件需要进行合理的布局,以确保机床的工作精度和性能。
有限元分析可以模拟机床在各种外载荷下的响应情况,帮助设计者确定合适的布局方案。
4、降低材料成本机床的材料成本非常高。
有限元分析可以帮助设计者确定机床结构所需的材料数量,从而降低机床的材料成本。
大型数控车床床身结构的有限元分析

大型数控车床床身结构的有限元分析数控车床是一种高精度、高速、高自动化的机械设备。
其关键部分是床身结构,在高精度切削加工过程中承担着不小的负荷,因此对于其结构的优化设计至关重要。
本文将通过有限元分析对数控车床床身结构的强度和刚度进行优化设计。
一、有限元分析的基本概念有限元分析是求解强度、振动、热力学等问题的一种重要方法。
有限元方法将一个复杂的结构分割成有限个单元,每个单元可以看作是一个简单的结构,可以通过计算单元内各个点的力和位移,得到整个结构的力和位移的分布情况。
在有限元分析中,要首先进行预处理,包括建模、离散化和求解算法的选择等步骤。
然后进行求解过程,通过解出各个单元的刚度矩阵和外载荷矩阵,再根据边界条件组成总刚度矩阵和外载荷矩阵,最终求解结构中各点的位移和应力等参数。
最后进行后处理,对计算结果进行分析和优化。
二、建立数控车床床身的有限元模型在进行有限元分析之前,需要建立数控车床床身的有限元模型。
床身结构可以分为两部分:主床身和副床身。
主床身是床身的主要承载部分,唯一支撑和固定主轴箱和刀架;副床身是连接两端的连接体,起连接两端床身和承受工件切削力的作用。
我们分别对主床身和副床身进行静力学分析,求解其强度和刚度。
三、床身结构的静力学分析床身结构主要受到外部力荷载和自重荷载的作用。
基本的受力情况如下:1. 主轴箱在切削时产生的切向力和径向力。
2. 刀架的重量产生的自重荷载。
3. 工件在切削时产生的切向力和径向力。
由于车床的高速旋转的特殊性,其受力情况十分复杂,难以通过简单的解析法求解,因此需要运用有限元分析的方法。
四、床身结构的优化设计基于前面的有限元分析结果,我们可以得到数控车床床身的强度和刚度情况。
若发现床身结构在受到切削载荷时强度不足或刚度不够,我们可以对床身结构进行优化设计,包括优化结构形状,材料选型等方式。
例如,我们可以通过增加床身的内部加强支撑件、合理改变断面的形状、优化床身连接部位的刚性等方式,提高其整体刚度和强度。
基于有限元分析的结构优化设计方法研究

基于有限元分析的结构优化设计方法研究在工程领域中,结构设计是一项重要的任务,它直接影响到工程项目的稳定性和安全性。
为了提高结构设计的质量和效率,近年来,人们开始广泛应用基于有限元分析的结构优化设计方法。
本文将探讨这一方法的原理、应用和未来发展方向。
一、有限元分析的原理有限元分析是一种数值计算方法,用于求解连续介质力学问题。
它基于有限元法的理论,将复杂的结构分解为有限的子单元,利用数值模拟和计算的方法,逐步逼近真实结构的行为。
有限元分析的原理可以总结为以下几个步骤:1. 网格划分:将结构划分为有限个小的单元,每个单元都有一组节点和自由度。
2. 单元本构关系:定义每个单元的材料性质和本构关系,例如弹性模量、泊松比等。
3. 边界条件:定义结构的边界条件,包括约束和荷载。
4. 求解方程:根据边界条件和单元本构关系,建立结构的运动方程,通过求解得到结构的应力和位移场。
二、结构优化设计结构优化设计是指在给定的设计变量和约束条件下,寻找最优的结构几何形状和材料分布,以满足设计要求。
基于有限元分析的结构优化设计方法主要包括以下两种形式:1. 拓扑优化:该方法通过在结构中添加或移除材料,改变结构的拓扑形状,实现结构的优化设计。
拓扑优化常用的算法包括密度法、梯度法等。
2. 尺寸优化:该方法通过改变结构的尺寸参数,如截面尺寸、厚度等,来实现结构的优化设计。
尺寸优化常见的算法包括等高线法、灰度法等。
三、应用案例基于有限元分析的结构优化设计方法在各个领域都得到了广泛应用。
以航空航天领域为例,研究人员利用该方法对飞机机翼结构进行优化设计。
通过调整材料分布和拓扑形状,他们成功提高了机翼的强度和刚度,同时减轻了重量,提高了飞机的性能。
类似的优化设计方法还可以应用于汽车、建筑、桥梁等领域,以实现更高效的结构设计。
四、未来发展方向虽然基于有限元分析的结构优化设计方法已经取得了一些重要成果,但仍存在一些挑战和待解决的问题。
未来的发展方向包括以下几个方面:1. 多学科优化:结构优化设计不仅需要考虑力学性能,还需要兼顾其他学科指标,如流体力学、热学等。
《液压机机身有限元分析与优化》范文

《液压机机身有限元分析与优化》篇一一、引言液压机作为现代工业生产中不可或缺的重要设备,其机身的设计与性能直接关系到设备的整体稳定性和工作效率。
随着计算机技术的飞速发展,有限元分析方法在液压机机身的设计与优化中得到了广泛应用。
本文旨在通过液压机机身的有限元分析,探讨其结构性能及优化策略,以提高液压机的整体性能和稳定性。
二、液压机机身有限元分析2.1 有限元分析基本原理有限元分析是一种通过将连续体离散成有限个单元进行分析的方法,其基本原理是将连续的实体离散化,通过对每个单元进行分析,得到整个结构的近似解。
在液压机机身的有限元分析中,通过建立机身的三维模型,划分网格,设定材料属性及边界条件,进行求解分析,从而得到机身的应力、应变等参数。
2.2 液压机机身模型建立与网格划分根据液压机机身的实际情况,建立三维模型。
在模型建立过程中,需充分考虑机身的结构特点、材料属性等因素。
网格划分是有限元分析的关键步骤,合理的网格划分可以保证分析结果的准确性。
在机身的网格划分中,需根据机身的结构特点选择合适的网格类型和大小,以保证分析结果的精确性和可靠性。
2.3 材料属性及边界条件设定在有限元分析中,需设定机身的材料属性,包括弹性模量、泊松比、密度等参数。
同时,还需设定边界条件,如约束、载荷等。
合理的材料属性及边界条件设定对于保证分析结果的准确性具有重要意义。
2.4 求解及结果分析根据设定的材料属性及边界条件,进行求解分析。
通过求解得到机身的应力、应变等参数,进而对机身的结构性能进行评估。
根据分析结果,可以找出机身的薄弱环节和潜在问题,为后续的优化设计提供依据。
三、液压机机身优化策略3.1 结构优化根据有限元分析结果,对液压机机身的结构进行优化。
优化策略包括改进结构布局、调整结构尺寸、采用新型材料等。
通过优化设计,可以提高机身的刚度、强度和稳定性,降低应力集中现象,延长设备的使用寿命。
3.2 工艺优化工艺优化主要包括加工工艺的改进和装配工艺的优化。
基于有限元方法的机械零部件结构优化设计
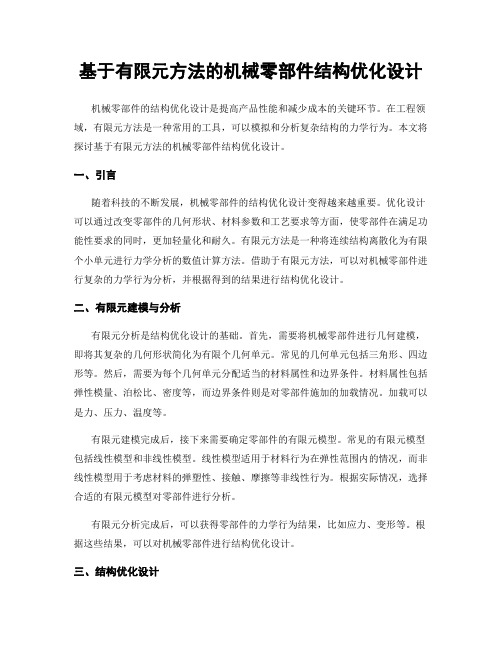
基于有限元方法的机械零部件结构优化设计机械零部件的结构优化设计是提高产品性能和减少成本的关键环节。
在工程领域,有限元方法是一种常用的工具,可以模拟和分析复杂结构的力学行为。
本文将探讨基于有限元方法的机械零部件结构优化设计。
一、引言随着科技的不断发展,机械零部件的结构优化设计变得越来越重要。
优化设计可以通过改变零部件的几何形状、材料参数和工艺要求等方面,使零部件在满足功能性要求的同时,更加轻量化和耐久。
有限元方法是一种将连续结构离散化为有限个小单元进行力学分析的数值计算方法。
借助于有限元方法,可以对机械零部件进行复杂的力学行为分析,并根据得到的结果进行结构优化设计。
二、有限元建模与分析有限元分析是结构优化设计的基础。
首先,需要将机械零部件进行几何建模,即将其复杂的几何形状简化为有限个几何单元。
常见的几何单元包括三角形、四边形等。
然后,需要为每个几何单元分配适当的材料属性和边界条件。
材料属性包括弹性模量、泊松比、密度等,而边界条件则是对零部件施加的加载情况。
加载可以是力、压力、温度等。
有限元建模完成后,接下来需要确定零部件的有限元模型。
常见的有限元模型包括线性模型和非线性模型。
线性模型适用于材料行为在弹性范围内的情况,而非线性模型用于考虑材料的弹塑性、接触、摩擦等非线性行为。
根据实际情况,选择合适的有限元模型对零部件进行分析。
有限元分析完成后,可以获得零部件的力学行为结果,比如应力、变形等。
根据这些结果,可以对机械零部件进行结构优化设计。
三、结构优化设计1. 基于强度和刚度的优化强度和刚度是机械零部件两个重要的性能指标。
强度是指零部件在外部加载下不发生破坏的能力,而刚度则是指零部件在外部加载下不发生过大变形的能力。
通过在有限元模型中设置约束和目标函数,可以进行强度和刚度的优化设计。
优化设计的目标是在满足强度和刚度要求的前提下,尽可能减小零部件的重量。
2. 基于模态和动力学的优化模态和动力学是机械零部件另外两个重要的性能指标。
- 1、下载文档前请自行甄别文档内容的完整性,平台不提供额外的编辑、内容补充、找答案等附加服务。
- 2、"仅部分预览"的文档,不可在线预览部分如存在完整性等问题,可反馈申请退款(可完整预览的文档不适用该条件!)。
- 3、如文档侵犯您的权益,请联系客服反馈,我们会尽快为您处理(人工客服工作时间:9:00-18:30)。
机床重要部件的有限元分析及优化设计
摘要本文选取了某型机床中的重要部件床身作为研究对象,利用Solidworks软件进行三维设计造型,分析其在极限工作条件下的受力情况,并利用有限元分析软件ANSYS对模型进行受力分析和模态分析,得出了极限工作条件下,床身的受力、变形和振动的情况,找出设计中存在的缺陷进行优化设计,为机床的设计提供参考依据。
关键词机床;重要部件;有限元;优化设计
机床是加工制造的最基本的设备,它是由多个零部件组成的复杂组合结构,其机构的设计对机床的加工性能影响很大。
传统的设计需要在原型设计的基础上经过长期的实践,不断改进,逐渐完善,最终定型为一个成熟的产品。
现代的设计中,可以充分利用各种分析软件,在设计阶段就能够及时发现和解决原设计中存在的问题,对实现并行设计,提高质量和生产效率起到了非常重要的作用。
机床的各零部件中,床身作为支承和定位的主要零件对机床整体刚性和精度起到关键性作用。
本文选取了某厂CK6150型车床作为研究对象,综合分析了该机床在受到综合应力的情况下,床身的受力、变形和振动情况,并对设计中的缺陷进行优化设计。
1 机床的三维造型
此次设计采用Solidworks软件对机床各个零部件进行设计造型并进行整机装配。
2 受力及约束分析
床身在加工中受到的应力主要有切削力和工艺系统的重力。
为了模拟机床在极限工作条件下的变形和振动情况,此次分析中模拟了加工φ500*1000mm的45钢棒料毛坯,使用45°外圆车刀,背吃刀量ap=5mm,进给量f=0.5mm,切削速度vc=500r/mm,切削点位置为毛坯中段。
1)由切削45钢主切削力公式Fc≈2ap·f (kN)得:
Fc≈2ap·f =2*5*0.5=5 kN
由吃刀抗力公式Fp≈(0.2~0.5)Fc,估算出:
Fp≈4kN
由进给抗力公式Ff≈(0.1~0.4)Fc,估算出:
Ff≈3.5kN
图1 床身工作中的受力情况
2)利用Solidworks软件中的重力分析功能,分别得出主轴箱系统、床鞍和刀架系统、尾座顶尖系统和工件的重力及质心位置,见表1。
序号力大小kN 作用点方向
1 主切削力Fc 5 X=160.000
Y=775.000
Z=1580.201 Y
2 吃刀抗力Fp 4 X=160.000
Y=775.000
Z=1580.201 X
3 进给抗力Ff 3.5 X=160.000
Y=775.000
Z=1580.201 Z
4 主轴箱系统重力G1 11.8 X=310.000
Y=697.990
Z=339.266 -Z
5 刀架及床鞍系统G2 5.2 X=156.205
Y=500.742
Z=1515.200 -Z
6 尾座顶尖系统G3 1.9 X=318.750
Y=622.023
Z=1920.20 -Z
7 工件的重力G4 5.4 X = 310.000
Y=775.000
Z=1257.500 -Z
表1 床身在工作中受力大小作用点、及方向
3 材料分析
本设计床身材料选用HT250。
其材料特性:
1)Isotropic:各向同性;
2)杨氏模量Young’s modulus:120吉帕(GP);
3)泊松比Poisson’s ratio:0.25;
4)材料密度Density:7300千克/立方米(kg/m3)。
4 模态及静力分析
将Solidworks造型的三维模型导入Ansys,选定模型材料类型,设定约束面及受力,为之后的分析做好准备。
4.1网格划分
利用ANSYS自动网格划分功能,设计单元尺寸大小为1mm,一共划分出个34493单元,61148个节点。
图2 网格的划分
4.2模态分析
模态是机械结构的固有振动特性,模态分析是研究结构动力特性的一种方法,通过分析求得结构振动的一些基本振型对应的频率,设计时要尽量避开这些
基本频率,防止共振。
图3 模态分析
通过ANSYS模态功能,分析出床身一阶、二阶、三阶固有频率数据分别为312.93 Hz、521.4 Hz、596.2 Hz(具体见表2)。
机/床主轴转速一般在50r/s(3000r/min)以下,与床身固有频率相差很远,所以不存在共振问题。
模态阶次固有频率(Hz)
1 312.93
2 521.4
3 596.2
表2 模态分析数值
4.2静力分析
通过ANSYS数据分析(见表3)可以看出,床身导轨中段在极限载荷下的变形较大,这是由床身工作结构特点决定。
床身工作中支撑约束在两端,而受力在中段,在床鞍重力及切削力的合力下,必然引起较大的变形。
变形方向变形量(μm)
综合最大变形11.757
X向最大变形10.878
Y向最大变形 4.533
Z向最大变形0.9563
表3 静力分析数值
图4 静力分析
5 优化设计
鉴于床身导轨的变形较大,因此在结构上加以改进,增加床身导轨下部厚壁支撑部分长度增加并适当增加床身筋板厚度,可以明显提高刚性,减小导轨的变形量。
改进后经模拟分析结果如下表。
变形方向变形量(μm)
综合最大变形 6.854
X向最大变形 4.912
Y向最大变形 3.132
Z向最大变形0.8913
表4 改进后静力分析数值
6 结论
本文是在某型车床设计过程中,利用有限元分析的方法,分析车床床身在极限工作条件下的受力、振动和变形情况,在设计之初就能了解机床在实际工作中的状态,有利于我们及时发现并改进设计中存在的缺陷,缩短设计周期,对保证加工质量,提到生产效率,降低生产成本有着重要意义。
参考文献
[1]覃文洁.机床整机的动态特性分析[J].机械设计,2000(10):1634-1636.
[2]王学林.机床模态特性的有限元分析[J].机床与液压,2005(2):48-50.
[3]ANSYS Inc3ANSYS技术报告.北京:美国ANSYS公司北京办事处,1998.
[4]张建润,卢熹,等3五坐标数控龙门加工中心动态优化设计[J]3中国机械工程,2005,16(21):1949-l953.。