DCS实验报告刘金琳
DCS与工业组态软件实验报告

评分:DCS与工业组态软件实验报告学号:班别:姓名:实验一:硬件系统熟悉与操作一、实验目的:1、了解集散控制系统的组成和结构;2、熟悉系统规模、控制站规模;3、掌握控制站卡件型号、名称、性能及输入/输出点数;4、掌握控制站卡的地址设置。
二、实验内容:硬件简介:1、JX-300X DCS系统网结构如图1.1所示:图1.1 JX-300X DCS系统网结构示意图通讯网分为三层:信息管理、过程控制(SCnet II)和控制站内部I/O控制总线(SBUS)。
2、控制站卡件控制站卡件位于控制站卡件机笼里,主要由主控卡、数据转发卡和I/O卡组成。
卡件按一定的规则组合在一起,完成信号采集、信号处理、信号输出、控制、计算、通讯等功能。
控制站卡件一览表如表1.1所示:表1.1 控制站卡件一览表硬件选型:1、根据测点性质确定系统I/O卡件的类型及数量(适当留有余量),对于重要的信号点要考虑是否进行冗余配置;2、根据I/O卡件数量和工艺要求确定控制站和操作站的个数;3、根据上述设备的数量配置其它设备,如机柜、机笼、电源、操作台等;4、对于开关量,根据其数量和性质要考虑是否选配相应的端子板、转接端子和继电器。
Scnet II网络组件地址设置:对TCP/IP协议地址采用如表1.2所示的系统约定:表1.2系统约定的参数网络码128.128.1和128.128.2代表两个互为冗余的网络。
在控制站表现为两个互为冗余的通讯口,上为128.128.1,下为128.128.2。
在操作站表现为两块网卡,每块网卡所代表的网络号由IP地址设置决定。
三、实验条件:1、JX-300X集散控制系统一套2、DELL工控机计算机一台3、JX-300X DCS系统组态软件包一套四、实验练习:1、参考实验四的工程项目进行硬件配置。
2、TCP/IP协议地址的系统约定。
五、思考题:1、硬件选型时,I/O卡件选型的主要依据是什么?实验二:JX-300系统的组态设计一、实验目的:1、了解JX-300X系统组态软件包;2、掌握控制站、操作站等硬件设备在软件中的配置;3、掌握I/O设备、信号参数的设置。
中国石油大学(华东)仿真实训报告

中国石油大学(华东)仿真实训报告仿真实训实习报告姓名:靳朝卉学号:12091303班级:化工卓越1202实习时间:2015.07.25-2015.08.032015年8月2日一、实习简介。
名称:仿真实训时间:2015.07.25-2015.08.03大三暑假期间地点:工科楼A座仿真实训室介绍:我们在学校练习了化工仿真软件的实际操作,让我们为将来从事化工生产又更进一步奠定了厚实的基础,了解了化工生产的全自动化,认识化工生产软件DCS的模拟操作,虽然学习的时间很短,但是在将来的工作与学习中我们将会学到更多的关于实际应用的技能与技巧,为成为一个合格化工生产操作人员而不懈的努力,这是只是我们迈出的第一步。
在本次的仿真实训中我们主要学习练习了催化裂化装置的基本DCS操作。
二、实习目的。
1、理解催化裂化反应再生工段反应原理、工艺流程;2、了解各类工艺设备、控制仪表;3、学习生产中的事故现象分析、判断、处理方法;4、能进行本工段的各项操作。
三、实验仪器。
计算机、催化裂化反应仿真软件四、关于催化裂化生产装置。
催化裂化装置是重油变成轻质油品重要的一步,是炼油工业中重要的二次加工过程,是重油轻质化的重要手段。
它是原料油在适宜的温度、压力和催化剂存在的条件下,进行分解、异构化、氢转移、芳构化、缩合等一系列化学反应,原料油转化成气体、汽油、柴油等主要产品及油浆、焦炭的过程。
催化裂化具有轻质油收率高、汽油辛烷值较高、气体产品中烯烃含量较高等特点。
催化裂化生产主要包括:反应再生部分、分馏部分、吸收稳定部分。
催化裂化装置流程说明:混合原料油从装置外自吸进入原料油泵,经原料油换热器加热至200℃左右,分十路经原料油雾化喷嘴进入提升管反应器(R01)下部;自分馏部分来的回炼油和回炼油浆混合后同原料一起进入提升管反应器下部,与催化剂接触完成反应,反应油气与待生催化剂在提升管出口经三组粗旋风分离器进入沉降器六组单级旋风分离器,再进一步除去携带的催化剂细粉后,反应油气离开沉降器,进入分馏塔。
DCS实习报告

计算机控制技术实习报告班级:电气1331班小组成员:罗欢、刘双、罗鸣指导教师:胡乃清、熊媛媛实习地点:实B301一、实习目的1熟悉集散控制系统(DCS)的组成2掌握Advan Trol Por组态软件的使用方法。
3培养灵活组态的能力。
4掌握系统组态与装置调试的技能。
二、实训内容以CS2000型实训装置为对象,按照实习任务书利用Advan Trol Por组态软件完成组态包括:1 数据库组态2 设备组态3控制器算法组态4 画面组态5 系统调试实习任务书如下:CS2000型实训装置DCS控制系统设计与调试任务书1.装置简述CS2000型实训装置是我院所购的微型装置,主要包括水槽、水箱、锅炉、换热器等对象。
它还集成了差压式流量计、涡轮流量计、液位计、热电阻等检测仪表,还集成了电动调节阀、变频泵、交流调压模块等执行器。
可配调节仪表或DCS 实现常规仪表控制和DCS控制。
可实现的主要控制方案包括:液位单回路控制、流量单回路控制、流量—液位串级控制、液位—液位串级控制、前馈控制、温度单回路控制、流量比值控制。
2.项目要求:要求按照DCS工程项目的设计、施工流程完成以下工作:(1)用户管理要求见表1表1 CS2000DCS系统用户管理要求表(2)按照表2所见的测点配置清单完成I/O组态表2 CS2000DCS系统测点配置清单(4)控制站及操作站配置✓项目由1个控制站、1个工程师站构成✓控制站地址根据网络确定(为02或04或06),工程师站地址设为本机地址。
✓要求主控卡、电源、数据转发卡、网络均冗余配置✓利用工程师站或操作员站可查看水箱和换热器的所有过程参数和画面(5)数据分为锅炉数据组和液位数据组,炉数据组分为锅炉、换热器两个数据区;水箱操作小组设置液位数据组,液位数据组分为流量、液位数据区.(6)工程师操作小组要求见表4表4 CS2000操作小组设置表图中实现比值控制(7)流程图要求:A在工程师操作小组下绘制相关回路流程图B在分组画面第二页中显示累积量C添加液位的动画效果.(8)完成系统调试、投运。
art1000191
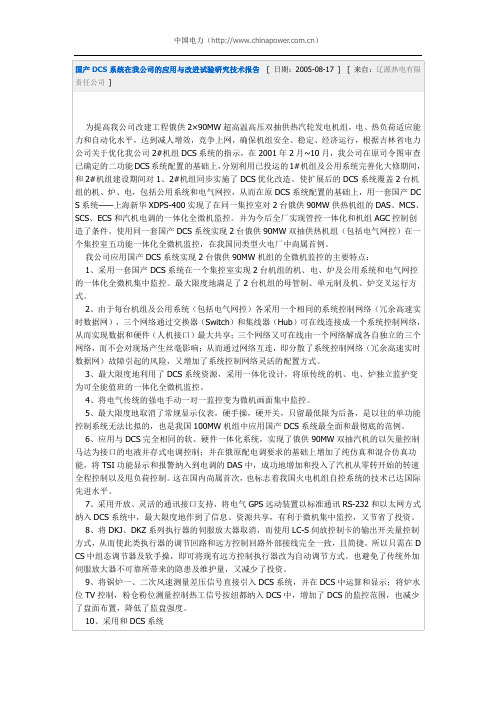
国产DCS系统在我公司的应用与改进试验研究技术报告 [ 日期:2005-08-17 ] [ 来自:辽源热电有限责任公司]为提高我公司改建工程俄供2×90MW超高温高压双抽供热汽轮发电机组,电、热负荷适应能力和自动化水平,达到减人增效,竞争上网,确保机组安全、稳定、经济运行,根据吉林省电力公司关于优化我公司2#机组DCS系统的指示,在2001年2月~10月,我公司在原司令图审查已确定的二功能DCS系统配置的基础上,分别利用已投运的1#机组及公用系统完善化大修期间,和2#机组建设期间对1、2#机组同步实施了DCS优化改造。
使扩展后的DCS系统覆盖2台机组的机、炉、电,包括公用系统和电气网控,从而在原DCS系统配置的基础上,用一套国产DC S系统——上海新华XDPS-400实现了在同一集控室对2台俄供90MW供热机组的DAS、MCS、SCS、ECS和汽机电调的一体化全微机监控。
并为今后全厂实现管控一体化和机组AGC控制创造了条件。
使用同一套国产DCS系统实现2台俄供90MW双抽供热机组(包括电气网控)在一个集控室五功能一体化全微机监控,在我国同类型火电厂中尚属首例。
我公司应用国产DCS系统实现2台俄供90MW机组的全微机监控的主要特点:1、采用一套国产DCS系统在一个集控室实现2台机组的机、电、炉及公用系统和电气网控的一体化全微机集中监控。
最大限度地满足了2台机组的母管制、单元制及机、炉交叉运行方式。
2、由于每台机组及公用系统(包括电气网控)各采用一个相同的系统控制网络(冗余高速实时数据网),三个网络通过交换器(Switch)和集线器(Hub)可在线连接成一个系统控制网络,从而实现数据和硬件(人机接口)最大共享;三个网络又可在线由一个网络解成各自独立的三个网络,而不会对现场产生丝毫影响;从而通过网络互连,即分散了系统控制网络(冗余高速实时数据网)故障引起的风险,又增加了系统控制网络灵活的配置方式。
DCS实训报告

专业综合课程设计题目:加热炉集散控制系统设计专业:电气工程及其自动化班级:电气11-5 班姓名:温遂云学号:11034020525指导老师:康珏设计时间2014 年10 月8 日至2015 年11 月 1 日目录摘要................................................................................................2 关键词.............................................................................................2 正文................................................................................................2 JX-300XP 概述 (2)各操作站作用 (3)I/O 卡件机笼包括卡件组成以及它们的功能………………………………… 4 JX-300X DCS 系统的组态软件包各软件的作用.................................... 5 JX-300X DCS 系统通信网络的构成及其各个部分的基本特性.................. 5 项目的设计.......................................................................................6 工艺简介.................................................................................... 6 加热炉控制流程图........................................................................ 6 控制方案.................................................................................... 6 原料油罐液位控制............................................................... 6 原料加热炉烟气压力控制...................................................... 7 原料加热炉出口温度控制...................................................... 7 控制站及操作站配置..................................................................... 7 系统组态..........................................................................................8 新建一个组态.............................................................................. 8 I/O 组态........................................................................... 8 操作小组的组态........................................................................ 11 常规控制方案的组态................................................... 12 创建数据组(区)..................................................................... 14 位号的区域划分............................................................... 15 光字牌设置.............................................................................. 16 设置网络策略..................................................................... 16 操作站标准画面组态.................................................................. 16 流程图的制作..................................................................... 18 报表的制作.............................................................................. 20 下载调试 (22)组态的编译和下载.....................................................................22 手操器检测系统工作是否正常......................................................22 图形化编程 (23)基本步骤.................................................................................... 23 常用的图形编程模块............................................................ 25 应用举例........................................................................... 26 参考文献......................................................................................................27 心得....................................................................................27 附录 1-卡件的选择..............................................................................28 附录 2-测点清单.................................................................................30 实验十(空气压力控制实验)...................................................30 实验目的........................................................................ 30 实验设备........................................................................ 30 实验原理 (30)压力基本回路控制工段………………………………………………. 31 实验内容与步骤……………………………………………………………32 实验数据处理………………………………………………………………34 实验心得体会 (35)摘要集散控制系统是一个由过程控制级和过程监控级组成的以通信网络为纽带的多级计算机系统,综合了计算机,通信、显示和控制等 4C技术,其基本思想是分散控制、集中操作、分级管理、配置灵活以及组态方便。
探讨丙酮氢醇装置中冷器的模拟
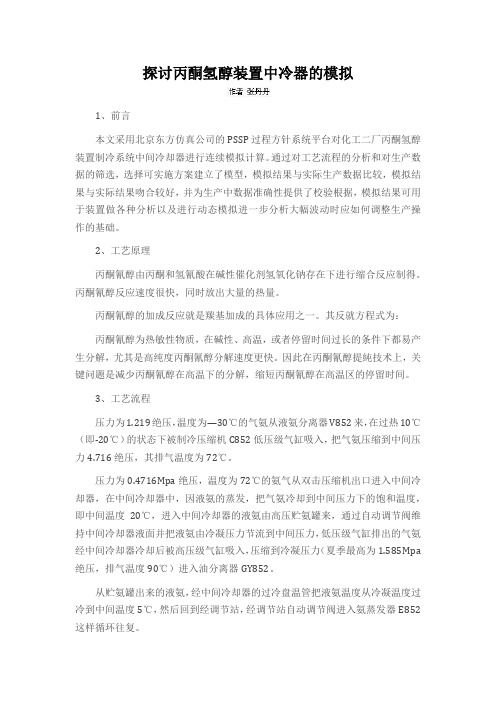
探讨丙酮氢醇装置中冷器的模拟1、前言本文采用北京东方仿真公司的PSSP过程方针系统平台对化工二厂丙酮氢醇装置制冷系统中间冷却器进行连续模拟计算。
通过对工艺流程的分析和对生产数据的筛选,选择可实施方案建立了模型,模拟结果与实际生产数据比较,模拟结果与实际结果吻合较好,并为生产中数据准确性提供了校验根据,模拟结果可用于装置做各种分析以及进行动态模拟进一步分析大幅波动时应如何调整生产操作的基础。
2、工艺原理丙酮氰醇由丙酮和氢氰酸在碱性催化剂氢氧化钠存在下进行缩合反应制得。
丙酮氰醇反应速度很快,同时放出大量的热量。
丙酮氰醇的加成反应就是羰基加成的具体应用之一。
其反就方程式为:丙酮氰醇为热敏性物质,在碱性、高温,或者停留时间过长的条件下都易产生分解,尤其是高纯度丙酮氰醇分解速度更快。
因此在丙酮氰醇提純技术上,关键问题是减少丙酮氰醇在高温下的分解,缩短丙酮氰醇在高温区的停留时间。
3、工艺流程压力为1.219绝压,温度为—30℃的气氨从液氨分离器V852来,在过热10℃(即-20℃)的状态下被制冷压缩机C852低压级气缸吸入,把气氨压缩到中间压力4.716绝压,其排气温度为72℃。
压力为0.4716Mpa绝压,温度为72℃的氨气从双击压缩机出口进入中间冷却器,在中间冷却器中,因液氨的蒸发,把气氨冷却到中间压力下的饱和温度,即中间温度20℃,进入中间冷却器的液氨由高压贮氨罐来,通过自动调节阀维持中间冷却器液面并把液氨由冷凝压力节流到中间压力,低压级气缸排出的气氨经中间冷却器冷却后被高压级气缸吸入,压缩到冷凝压力(夏季最高为1.585Mpa 绝压,排气温度90℃)进入油分离器GY852。
从贮氨罐出来的液氨,经中间冷却器的过冷盘温管把液氨温度从冷凝温度过冷到中间温度5℃,然后回到经调节站,经调节站自动调节阀进入氨蒸发器E852这样循环往复。
4、流程模拟分析制冷是借助于制冷剂状态的变化,通过吸收被冷却对象的热量——载冷剂,而达到制冷目的,氨制冷热力过程(以两级压缩为例),采用氨作致冷工质的热力过程,见图4-1。
自动控制原理2 实验报告
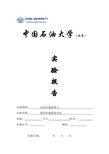
中国石油大学(北京)实验报告实验课程:自动控制原理2实验名称:采样控制系统分析班级:学号: 姓名:实验台号:成绩:实验日期:年月日实验1采样控制系统一、实验目的考察连续时间系统的采样控制中,零阶保持器的作用与采样时间间隔Ts对系统稳定性的影响。
二、实验步骤1、典型单位负反馈连续时间系统的开环传递函数为G(s)=K/(s2+s),借助于Matlab 仿真,并分析并验证K对系统性能的影响。
步骤:Matlab相关命令:Gs=tf([1],[1 1 0]) ;pzmap(Gs);figure(1)rlocus(Gs);K值变化时的阶跃相应曲线for k=[0,0.01,0.05,0.10,0.15,0.20,0.25]num=[k];den=[1,1,0]Gs=tf(num,den);figure(1)margin(Gs);figure(2)t=0:0.001:500;step(Gs,t);grid;hold onend2、将上述连续系统离散化,成为带零阶保持器的采样系统。
借助于Matlab仿真,调整采样周期T 和增益K 的大小,观察T 和K 对系统稳定性和调节性能的影响。
调整系数,给出[1]p384-385习题7-24和7-26的答案。
实验步骤:(1) 确定有零阶保持器的开环系统脉冲传递函数G(z)。
))(1()1()(T T e z z z e K z G -----=Matlab 相关命令:for k=[0,0.01,0.05,0.10,0.15,0.20,0.25]num=[k*0.1,0];den=[1,-1.9,0.9];G1=tf(num,den);G=tf2zp(num,den);Gd=c2d(G,0.1,’zoh ’);G0=feedback(Gd,a);t=0:0.1:50;u=1;tsim(G0,u,t,0);gridfor k=[0,0.01,0.05,0.10,0.15,0.20,0.25]G=tf([5],[1 1 0]);Gd=c2d(G,0.1,'zoh');G0=feedback(Gd,1);t=0:0.1:50;step(G0,t); gridxlabel('t');ylable('c(t)');title(‘ramp response ’)hold onend当T=0.1,0.5,1,2时分别重复上面的命令习题7-247-24(1)求出脉冲传递函数:程序代码:rlocus(G)G0=tf([1],[1 10 0 ]);G=c2d(G0,0.1,'zoh')G =0.003679 z + 0.002642----------------------z^2 - 1.368 z + 0.3679Sample time: 0.1 secondsDiscrete-time transfer function.(2)求闭环系统的z特征方程feedback(G,1)ans =0.003679 z + 0.002642----------------------z^2 - 1.364 z + 0.3705Sample time: 0.1 secondsDiscrete-time transfer function.(3)计算使系统稳定的K的最大值rlocus(G)(4)K=78(5)求闭环脉冲传递函数并绘出单位阶跃响应曲线程序代码:G0=tf([78],[1 10 0 ]);G=c2d(G0,0.1,'zoh')Gd= feedback(G,1);t=0:0.1:6;step(Gd,t)Gd =0.2869 z + 0.2061---------------------z^2 - 1.081 z + 0.574Sample time: 0.1 seconds Discrete-time transfer function. 阶跃响应曲线:(6)系统闭环极点以及超调量程序代码:G0=tf([120],[1 10 0 ]);G=c2d(G0,0.1,'zoh');Gd=feedback(G,1);t=0:0.1:6;step(Gd,t)Transfer function:0.4415 z + 0.3171----------------------z^2 - 0.9264 z + 0.685 Sampling time: 0.1b = [0.4415 0.3171];a = [1 -0.9264 0.685]; [b,a] = eqtflength(b,a); [z,p,k] = tf2zp(b,a)z =-0.7182p =0.4632 + 0.6859i0.4632 - 0.6859i k =0.4415超调量为53.8%. (7) t=0:0.1:6;step(Gd,t)7-267-26.程序代码:G0=tf([1],[1 1 0]);G=c2d(G0,0.2,'zoh');Gd=feedback(G,1);t=0:0.2:20;step(Gd,t)hold onG0=tf([1],[1 1 0]);G=c2d(G0,0.4,'zoh');Gd=feedback(G,1);t=0:0.4:20;step(Gd,t)hold onG0=tf([1],[1 1 0]);G=c2d(G0,0.6,'zoh');Gd=feedback(G,1);t=0:0.6:25;step(Gd,t)hold onG0=tf([1],[1 1 0]);G=c2d(G0,0.8,'zoh');Gd=feedback(G,1);t=0:0.8:30;step(Gd,t)hold onG0=tf([1],[1 1 0]);G=c2d(G0,1.0,'zoh');Gd=feedback(G,1);t=0:1.0:30;step(Gd,t)hold onG0=tf([1],[1 1 0]);G=c2d(G0,1.2,'zoh');Gd=feedback(G,1);t=0:1.2:30;step(Gd,t)hold on实验图形记录:(1)T=0.2s%21%;8.38s T σ==(2)T=0.4s%26%;8.53s T σ==(3)T=0.6s%31%;11.4s T σ==(4)T=0.8ss(5)T=1.0s(6)%40%;15.3s T σ==(7)T=1.2ssT 从0.2s 到1.2s3、计算机控制系统如图5-7所示,采样周期T=0.1s ,试分析不同的PID 调节器及不同参数对系统性能的影响,并分析各种情况下PID 参数的选择方法。
dcs实验报告心得体会

dcs实验报告心得体会《DCS 实验报告心得体会》说起这次 DCS 实验,那可真是一次让我又爱又恨、充满曲折又收获满满的经历。
实验刚开始的时候,我就像个没头的苍蝇,在实验室里到处乱撞。
面对那些复杂的仪器设备和密密麻麻的线路,我整个人都懵了。
心里想着:“这都是啥呀?怎么感觉比解数学难题还让人头疼!”我们小组被分配的任务是通过 DCS 系统控制一个小型的化工生产流程。
听起来好像挺高大上的,可真正操作起来,才知道这其中的艰辛。
首先是设备的连接,每一根线都得小心翼翼地接好,生怕一不小心接错了,导致整个系统瘫痪。
我拿着螺丝刀,手都有点发抖,眼睛死死地盯着那些接口,嘴里还不停地念叨着:“千万别接错,千万别接错……”同组的小伙伴也都紧张得不行,大家大气都不敢出,实验室里安静得只能听到我们紧张的呼吸声。
好不容易把设备连接好了,接下来就是软件的设置。
打开那复杂的操作界面,我的脑袋瞬间又大了一圈。
各种参数、图表、按钮,看得我眼花缭乱。
这时候,我们小组的“技术大神”站了出来,他一边操作一边给我们讲解,可我还是听得云里雾里的。
没办法,只能硬着头皮跟着他的步骤一步一步来。
在设置参数的过程中,我们遇到了一个大问题。
无论怎么调整,系统的反应都达不到我们预期的效果。
这可把我们急坏了,大家围在一起,七嘴八舌地讨论着解决方案。
“是不是这个参数设置得太大了?”“会不会是传感器出了问题?”“要不我们重新检查一下线路?”各种猜测和想法满天飞。
经过一番仔细的排查,终于发现是一个小小的参数被我们忽略了。
当把这个参数调整好之后,系统终于正常运行了,那一刻,我们小组所有人都欢呼起来,那种成就感简直无法用言语来形容。
然而,这只是万里长征的第一步。
接下来的实验过程中,我们还遇到了各种各样的突发状况。
比如说,系统突然出现了故障,报警声不停地响,吓得我心都提到了嗓子眼儿。
还有一次,因为操作不当,导致实验数据出现了很大的偏差,我们不得不重新做了一遍实验。
- 1、下载文档前请自行甄别文档内容的完整性,平台不提供额外的编辑、内容补充、找答案等附加服务。
- 2、"仅部分预览"的文档,不可在线预览部分如存在完整性等问题,可反馈申请退款(可完整预览的文档不适用该条件!)。
- 3、如文档侵犯您的权益,请联系客服反馈,我们会尽快为您处理(人工客服工作时间:9:00-18:30)。
集散控制系统
实验报告
姓名刘金琳
学号 10S030097 2011年4月
实验一 分布式网络伺服控制系统
实验目的:
1. 熟悉TureTime 仿真软件的安装和基本使用操作;
2. 熟悉网络控制系统的仿真;
3. 分析网络流量和调度策略对分布式网络控制系统时延和控制性能的影响。
实验内容: 设直流伺服系统的连续时间传递函数为:)1(1000
)(+=s s s G ,采用
四个计算机节点来实现该系统,一个时间驱动的传感器节点周期性地对过程进行采样,并通过网络把采样结果送到控制器。
控制节点计算控制信号并把结果送到执行器节点,产生连续执行结果。
还有一个节点模拟网络中的额外流量,并在控制器节点运行高优先级的任务模拟网络节点的任务分配。
实验步骤:
1. 安装TrueTime 仿真软件包,设置系统环境变量,运行Matlab 初始化命令;
2. 根据$DIR/examples/simple_pid/matlab 中的直流伺服过程PID 控制的实例,熟悉Truetime 的仿真操作;
3. 按照试验内容建立仿真系统,给出Simulink 仿真框图;
4. 首先考察没有额外网络流量,而且控制器节点也没有额外任务的情况,观察系统运行的延迟时间和控制性能,给出相关结果;
5. 打开额外网络流量,而且控制器节点也增加额外任务,采用两种不同的网络协议,和两种不同的调度策略,观察系统运行延迟时间和控制性能,给出相关结果并分析原因。
实验结果与分析:
1分布式网络伺服控制系统仿真框图如下:
2 仿真结果及分析:
2.1 设额外网络流量为零(BWshare=0.0),且控制器节点也没有额外任务的情况下,选择网络协议为:CSMA/AMP(CAN),调度策略为‘prioFP’,其输入,输出曲线如下图所示: 延迟时间为0.03s,超调量为20%,上升时间约为0.05s,调整时间约为0.11s,控制性能好.
2.2 设额外网络流量为0.1(BWshare=0.1),且控制器节点增加额外任务的情况下,选择网络协议为:CSMA/AMP(CAN),调度策略为‘prioFP’,其输入,输出曲线如下图所示: 延迟时间为0.03s,超调量为15%,上升时间约为0.05s,调整时间约为0.17s,控制性能较好.
2.3 设额外网络流量为0.2(BWshare=0.2),且控制器节点增加额外任务的情况下,选择网络协议为:CSMA/AMP(CAN),调度策略为‘prioRM’,
其输入,输出曲线如下图所示: 延迟时间为0.03s,超调量为20%,上升时间约为0.05s,调整时间约为0.15s,控制性能较好.
2.4 设额外网络流量为0.2(BWshare=0.2),且控制器节点增加额外任务的情况下,选择网络协议为:Round Robin,调度策略为‘prioFP’,其输入,输出曲线如下图所示: 延迟时间为0.035s,超调量为50%,上升时间约为0.05s,调整时间约较长,控制性能差.
2.5设额外网络流量为0.2(BWshare=0.2),且控制器节点增加额外任务的情况下,选择网络协议为:Round Robin,调度策略为‘prioRM’,其输入,输出曲线如下图所示: 延迟时间为0.035s,超调量大于50%,上升时间约为0.05s,调整时间较长,控制性能差.
由以上四幅曲线图可以看出,图2.3和图2.4曲线的超调量和调整时间明显比图2.1和图2.2的数值大.因此当分布式网络伺服控制系统的网络协议选择CSMA/AMP(CAN)时,其控制性能明显比选择Round Robin网络协议的系统好.同时,比较图2.1和图2.2(或图2.3与图2.4)的曲线, 其曲线的分布相似.综上所述,可以得出以下结论网络协议的选择对系统控制性能起决定性作用,而且对于同一网络协议,选择不同的调度策略对系统的控制性能影响较小.
实验二分布式无线网络控制系统
实验目的:
1.熟悉无线网络控制系统的仿真操作;
2.熟悉电源模块的使用方法;
3.分析不同网络协议和参数对分布式无线网络控制系统时延和控制性能的影响。
实验内容:
实验一中的模型,采用两个相距20米的无线计算机节点(各含有一个电池模块),来实现该系统,一个时间驱动的传感器/执行器节点周期性地对过程进行采样,并通过网络把采样结果送到控制器。
控制节点计算控制信号并把结果送回到传感器/执行器节点,产生连续执行结果。
电池模块产生功率控制任务,周期地ping另外的节点,如果接收到应答,则降低功率,否则增大功率直到达到阈值或者受到应答。
实验步骤:
1.按照试验内容建立仿真系统,给出Simulink仿真框图;
2.首先考察采用功率控制机制,观察两个节点的电池变化情况,记录曲线,并分析原因;
3.其次关闭控制节点的功率控制策略,观察功率消耗,记录曲线,并分析结果。
4.修改网络协议和参数,观察对控制性能的影响,记录结果并分析原因。
实验结果与分析:
1 分布式无线网络控制系统仿真框图如下:
2 实验结果及分析
设执行器节点和控制器节点的电源设置为0.1,仿真时间T=9秒2.1采用功率控制机制,设网络协议为802.11b/g(WLAN),调度策略为”prioFP”,仿真结果如下图所示:
图1 输入信号u曲线
图2 带功率控制机制的分布式无线网络控制系统输出信号r和y曲线
图3 带功率控制机制的分布式无线网络控制系统的网络控制策略
图4带功率控制机制的分布式无线网络控制系统的执行器节点的电池消耗曲线
图5带功率控制机制的分布式无线网络控制系统的控制器节点的电池消耗曲线由图2我们可以看出系统输出曲线Y(黄色)几乎与参考输出曲线R(红色)重合,同时图4和图5显示执行器和控制器的电源能量在9秒后耗尽,表明带功率控制机制的分布式无线网络控制系统的控制性能好,电池模块产生了较好的功率控制作用.
2.2 关闭控制节点的功率控制策略,设网络协议为802.11b/g(WLAN),调度策略为”prioFP”,仿真结果如下图所示:
图6 输入信号u曲线
图7 不带功率控制机制的分布式无线网络控制系统输出信号r和y曲线
图8 不带功率控制机制的分布式无线网络控制系统的网络控制策略
图9 不带功率控制机制的分布式无线网络控制系统的执行器节点的电池变化
图10 不带功率控制机制的分布式无线网络控制系统的控制器节点的电池变化由图6至图10我们可以看出,当系统运行到7.3秒的时候,系统的输入,输出曲线为零,而且执行器和控制器节点的电源能量也为零.表明不带功率控制机制的分布式无线网络控制系统功率消耗快,因无电源驱动导致系统失控.
总之,功率控制机制可以有效的降低系统的运行功率,系统控制性能明显优于不带功率控制机制的分布式无线控制系统.同时图3和图8显示系统存在 2.6秒的滞后,这是因为当节点采用电源模块控制时,传感器会丢失一些数据.
2.3 采用功率控制机制,设网络协议为802.15.4(ZIGBEE),调度策略为”prioFP”,仿真结果如下图所示:
图11 输入信号u曲线
图12 带功率控制机制且网络协议为802.15.4(ZIGBEE)系统输出信号r和y曲线
图13 带功率控制机制且网络协议为802.15.4(ZIGBEE)系统的执行器节点的电池
消耗曲线
图14带功率控制机制且网络协议为802.15.4(ZigBee)系统的控制器节点的电池
消耗曲线
由以上四幅图我们可以看出输入,输出信号明显偏离参考输入输出信号,控制性能差.且系统在2.7秒时,因系统电源耗尽而导致控制失败.同时ZigBee是一种近距离,低复杂度,低功耗的无线网络技术,主要用于近距离无线连接, 当距离超过10米时,信号将无法到达. 因此, 对于带有两个相距20米的无线计算机节点的分布式无线网络控制系统来说采用802.11b/g(WLAN)网络协议其控制性能明显优于采用802.15.4(ZigBee)网络协议的系统.。