机翼与机身连接设计分析
翼身融合技术的发展过程

翼身融合技术的发展过程翼身融合技术是一种将机翼和机身融为一体的航空技术,它的发展经历了多个阶段。
本文将从最初的概念提出到现在的应用发展,介绍翼身融合技术的发展过程。
翼身融合技术最早的概念可以追溯到20世纪60年代。
当时,航空工程师们开始思考如何减少飞机的阻力,提高飞行效率。
他们发现,传统的机翼和机身之间存在着明显的间隙,这个间隙会导致空气流动的不连续,增加了阻力。
于是,他们开始尝试将机翼和机身融为一体,以减少这个间隙,提高飞行效率。
在翼身融合技术的初期阶段,航空工程师们主要通过改变机翼和机身的形状来实现融合。
他们设计了一些具有流线型外形的机翼和机身,使它们能够更好地连接在一起,减少了间隙。
这种方法在一定程度上提高了飞机的飞行效率,但仍然存在一些问题,比如结构强度不足和重量过大等。
随着科技的不断进步,翼身融合技术逐渐得到了改进和完善。
在20世纪80年代,航空工程师们开始采用复合材料来制造机翼和机身,以提高结构强度和减轻重量。
复合材料具有优异的力学性能和轻质化的特点,能够更好地满足翼身融合技术的需求。
同时,他们还引入了一些先进的制造工艺,如自动化制造和三维打印等,以提高生产效率和降低成本。
到了21世纪,翼身融合技术进一步得到了发展和应用。
航空工程师们开始将更多的功能集成到机翼和机身中,以提高飞机的性能和安全性。
他们在机翼和机身上安装了一些传感器和执行器,用于监测飞机的状态和控制飞行。
同时,他们还利用翼身融合技术设计了一些新型的机翼结构,如可变弯曲机翼和无尾翼机翼等,以进一步提高飞机的操纵性和机动性。
翼身融合技术的发展不仅在民用航空领域有所应用,也在军事航空领域发挥了重要作用。
在军用飞机中,翼身融合技术可以提高飞机的隐身性能,减少雷达反射面积,增加飞机的生存能力。
同时,它还可以提高飞机的载荷能力和作战效能,使飞机能够携带更多的武器和设备。
总的来说,翼身融合技术的发展经历了从概念提出到应用发展的过程。
随着科技的不断进步,翼身融合技术在航空领域的应用越来越广泛,为飞机的性能和安全性提供了更多的可能性。
飞机机身连接件的航空航天技巧与技术
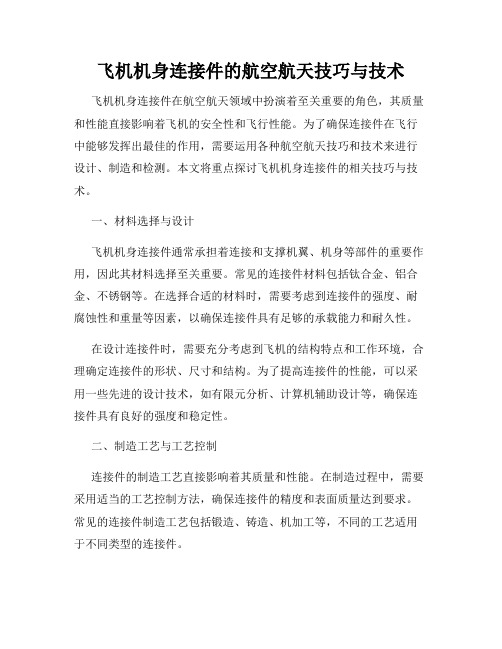
飞机机身连接件的航空航天技巧与技术飞机机身连接件在航空航天领域中扮演着至关重要的角色,其质量和性能直接影响着飞机的安全性和飞行性能。
为了确保连接件在飞行中能够发挥出最佳的作用,需要运用各种航空航天技巧和技术来进行设计、制造和检测。
本文将重点探讨飞机机身连接件的相关技巧与技术。
一、材料选择与设计飞机机身连接件通常承担着连接和支撑机翼、机身等部件的重要作用,因此其材料选择至关重要。
常见的连接件材料包括钛合金、铝合金、不锈钢等。
在选择合适的材料时,需要考虑到连接件的强度、耐腐蚀性和重量等因素,以确保连接件具有足够的承载能力和耐久性。
在设计连接件时,需要充分考虑到飞机的结构特点和工作环境,合理确定连接件的形状、尺寸和结构。
为了提高连接件的性能,可以采用一些先进的设计技术,如有限元分析、计算机辅助设计等,确保连接件具有良好的强度和稳定性。
二、制造工艺与工艺控制连接件的制造工艺直接影响着其质量和性能。
在制造过程中,需要采用适当的工艺控制方法,确保连接件的精度和表面质量达到要求。
常见的连接件制造工艺包括锻造、铸造、机加工等,不同的工艺适用于不同类型的连接件。
为了提高连接件的制造精度,可以采用一些先进的工艺技术,如数控加工、激光切割等,提高制造效率和质量稳定性。
同时,还需要对制造过程进行严格的工艺控制,确保每个环节都符合设计要求,避免出现质量问题。
三、检测技术与质量控制连接件的质量检测是保证其安全性和可靠性的关键环节。
采用先进的检测技术可以有效发现连接件的缺陷和隐患,确保其符合飞行要求。
常见的连接件检测技术包括超声波检测、磁粉探伤、射线检测等,这些方法可以全面、准确地检测连接件的内部和表面缺陷。
为了提高连接件的质量控制水平,需要建立完善的质量管理体系,严格执行质量标准和检测程序。
同时,还可以采用一些质量控制方法,如质量保证、过程检测等,提高连接件的质量稳定性和可靠性。
总结:飞机机身连接件的制造和检测涉及到多种航空航天技巧和技术,只有充分发挥这些技术的优势,才能确保连接件的质量和性能达到要求。
航模机翼与机身的连接方法

航模机翼与机身的连接方法
1.螺钉连接法:将机翼和机身通过螺钉连接起来,这种方法连接牢固,但是需要钻孔,容易损坏模型。
2. 弹性连接法:将机翼和机身通过弹性材料连接起来,如橡皮带、弹簧等,这种方法可以减少模型在飞行中的震动和抖动,提高模型的稳定性和飞行性能。
3. 磁力连接法:将机翼和机身通过磁力连接起来,这种方法连接方便,不需要钻孔,但是需要使用特殊的磁铁,连接不牢固,需要加强定位。
4. 插接式连接法:将机翼和机身通过插接方式连接起来,这种方法连接简单方便,但是需要注意插头的大小和位置,以及插头和插座的质量。
总之,航模机翼与机身的连接方法要选择适合自己的连接方式,以确保飞机模型的飞行性能和安全性。
- 1 -。
翼身融合技术
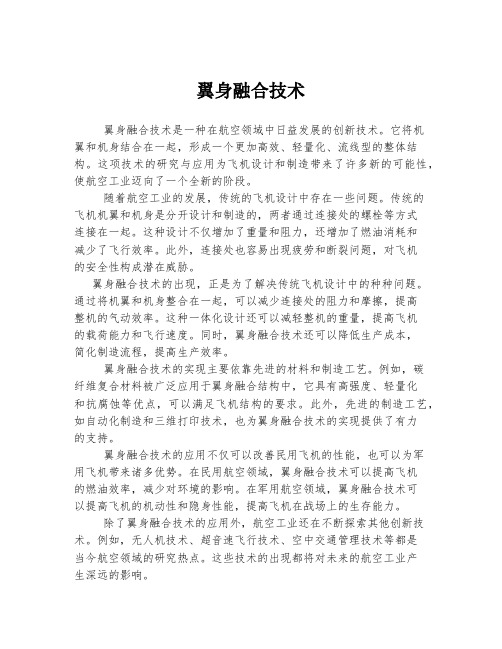
翼身融合技术翼身融合技术是一种在航空领域中日益发展的创新技术。
它将机翼和机身结合在一起,形成一个更加高效、轻量化、流线型的整体结构。
这项技术的研究与应用为飞机设计和制造带来了许多新的可能性,使航空工业迈向了一个全新的阶段。
随着航空工业的发展,传统的飞机设计中存在一些问题。
传统的飞机机翼和机身是分开设计和制造的,两者通过连接处的螺栓等方式连接在一起。
这种设计不仅增加了重量和阻力,还增加了燃油消耗和减少了飞行效率。
此外,连接处也容易出现疲劳和断裂问题,对飞机的安全性构成潜在威胁。
翼身融合技术的出现,正是为了解决传统飞机设计中的种种问题。
通过将机翼和机身整合在一起,可以减少连接处的阻力和摩擦,提高整机的气动效率。
这种一体化设计还可以减轻整机的重量,提高飞机的载荷能力和飞行速度。
同时,翼身融合技术还可以降低生产成本,简化制造流程,提高生产效率。
翼身融合技术的实现主要依靠先进的材料和制造工艺。
例如,碳纤维复合材料被广泛应用于翼身融合结构中,它具有高强度、轻量化和抗腐蚀等优点,可以满足飞机结构的要求。
此外,先进的制造工艺,如自动化制造和三维打印技术,也为翼身融合技术的实现提供了有力的支持。
翼身融合技术的应用不仅可以改善民用飞机的性能,也可以为军用飞机带来诸多优势。
在民用航空领域,翼身融合技术可以提高飞机的燃油效率,减少对环境的影响。
在军用航空领域,翼身融合技术可以提高飞机的机动性和隐身性能,提高飞机在战场上的生存能力。
除了翼身融合技术的应用外,航空工业还在不断探索其他创新技术。
例如,无人机技术、超音速飞行技术、空中交通管理技术等都是当今航空领域的研究热点。
这些技术的出现都将对未来的航空工业产生深远的影响。
总之,翼身融合技术是航空领域中一项重要的创新技术。
它通过将机翼和机身整合在一起,提高了飞机的性能和效率。
翼身融合技术不仅在民用航空领域具有广泛的应用前景,也在军用航空领域具有重要的战略价值。
随着科技的不断进步和创新的推动,相信翼身融合技术将会在未来的航空领域中继续发挥重要作用,推动航空工业迈向新的高度。
机身结构

Pz与座舱地面 剪流 qPz 平衡;
力矩Mx通过轴 承上的集中力 Pzh/b 与剪流qMt 平衡。
前起落架载荷作用下机身结构受力分析
纵向力Px的传递
Px由轴承上的力Rdx和挡块上的力 Rex 平衡
挡块中力的平衡
轴承加强件中力的平衡
可见,起落架上的力Px、Py 、Pz通过加强框以剪流形式作用 到与加强框相连的H型开剖面薄壁结构上,然后传到中机身。
➢ 前机身的结构 ➢ 前起落架的布置
设备舱
驾驶舱
起落架舱
挡块
电瓶舱
前起落架载荷作用下机身结构受力分析
前起落架的 约束条件 1)轴承能够 提供除 Mz 以外的所有 约束;
2)挡块只能 提供x方向向 后的约束。
前起落架所 受的载荷
集中力 Py、 Pz、Px
Py的传递与平衡
前起落架载荷作用下机身结构受力分析
❖ 机身为圆截面时,增压舱的受力情况最好; ❖ 为椭圆形截面时,框内会产生弯曲内力; ❖ 如果是双圆截面机身,则在两圆弧交汇处会产生分力Fn。
结构特点:
可以在机的一边与蒙皮铆在一起。
四、战斗机增压舱的设计特点 战斗机驾驶员增压舱一般空间小、形状复杂。
水平加强板
弯矩Mx的平衡 剪力P的平衡
加强框上中 的剪流平衡
当平尾置于垂直尾翼上时
当平尾置于垂直尾翼上时
垂直尾翼的垂直载荷传递到加 强框,由加强框将载荷传给机 身蒙皮
垂直尾翼上载荷通过各种 途径传到机身壳体蒙皮中,以 蒙皮中剪流形式向机身中部传 递,达到全机受力平衡。
三、前起落架载荷作用下机身结构受力分析
第十六讲结束
谢谢
V-22飞机
机翼与机身的连接配置
翼身融合布局客机概念设计的结构重量预测方法
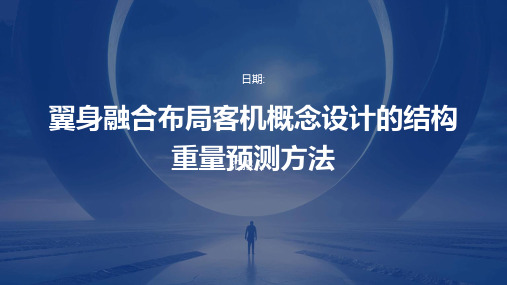
乘坐体验改善
翼身融合布局客机在客舱布局、噪音和振 动控制等方面进行了优化,提高了乘客的 乘坐舒适度。
03
结构重量预测方法
基于经验公式的预测方法
总结词
经验公式是基于历史数据和统计分析得 出的公式,可用于初步估算结构重量。
缺点
精度受限于公式的适用范围和数据的 可靠性,无法考虑多种设计和材料因
素,可能导致较大误差。
02
翼身融合布局客机概念设计分析
布局特点
1 2 3
一体化设计
翼身融合布局客机采用机翼与机身一体化设计, 无明显的机翼和机身界限,从而减小飞行阻力, 提高飞行效率。
升力体设计
通过优化机翼与机身的融合方式,形成升力体结 构,增加机翼面积,降低翼载荷,提高客机的短 距起降能力。
先进的推进系统
翼身融合布局客机通常采用高涵道比涡扇发动机 ,以减小噪音和油耗,同时提高推力。
经验公式法
适用于传统布局客机或稍作改进的客机,对于全新布局的客机可能 不适用。
人工智能法
适用于具有大量历史数据的客机类型,对于缺乏数据的全新布局客机 可能不适用。同时,需要专业人员对模型进行训练和调优。
计算效率分析
有限元分析法
由于该方法涉及大量计算和迭代,计算效率相对较低,耗时较长。
经验公式法
计算效率较高,只需输入相关参数,即可快速得到预测结果。
成本控制
结构重量的增加通常意味着需要使用更多材 料,从而增加生产成本。准确预测重量有助 于控制成本。
本报告的目的和内容概述
目的
本报告旨在探讨翼身融合布局客机概念 设计阶段的结构重量预测方法,为设计 师提供有用的工具和指导。
VS
内容概述
报告将首先介绍翼身融合布局的基础知识 和设计理念。接着,将详细阐述结构重量 预测的方法和技术,包括基于经验的公式 、数值模拟等。最后,将讨论这些方法在 实际应用中的优缺点及适用范围。
翼身融合技术
翼身融合技术翼身融合技术是一项新颖的先进飞行器结构设计技术,常见于战斗机以及无人机等高速飞行器的设计之中。
具有极高的综合性能、灵活度和稳定性,也为飞行器的速度、机动性、载荷和飞行安全性等方面的优化提供了很多的可能性。
翼身融合技术的应用可以大大提高飞行器的飞行性能,为未来的高速、高机动性的飞行器设计提供了广阔的发展空间和可靠的技术支持。
一、翼身融合技术的定义和研究背景翼身融合技术就是通过重新设计飞行器外形,将机身和机翼完美结合,使得飞行器在飞行过程中具有更出色的飞行性能和灵活度。
翼身融合技术一般是指将机身和机翼进行融合设计,使得机身和机翼之间的分割线消失,将机身和机翼融为一体,就像把翅膀和身体结合在一起飞行一样。
这种设计可以大大减少空气阻力,提升速度、耐久度、操纵性和安全性,且避免因机翼区域过小产生的过弯等负面因果。
目前,翼身融合技术已经被广泛应用在各种高速、高敏捷性的飞行器设计中。
例如,常见的战斗机和无人机等都采用了这种设计,使得其具有更出色的飞行性能和机动性。
此外,翼身融合技术的出现也是由于飞行器在高速飞行时需要解决的一些问题,例如空气阻力和失速等,而翼身融合技术正好可以很好地解决这些问题。
因此,翼身融合技术的研究一直是设计和飞行器制造领域的研究热点,也是未来高性能飞行器设计的重要方向。
二、翼身融合技术的设计技术和方法1、翼身融合的设计方法设计一个翼身融合的飞行器需要考虑机身和机翼之间的配合、空气动力学特性、飞行性能等多个因素。
一般而言,翼身融合的设计方法可以分为三个层面:构造设计、空气动力学特性分析和飞行性能分析。
构造设计层面:构造设计主要是解决机身和机翼连接的问题,其关键是确定外形上的相互过渡区域,使得机身和翼面相互贴合,符合飞行特性的经验公式,进而优化外形和细节设计,确保飞机的力学特性和空气动力学性能在飞行中得到最大限度的维护。
空气动力学层面:空气动力学特性分析是为了优化外形设计和减少机身和翼面的阻力,提升飞机的速度、稳定性和机动性。
飞机机翼-机身连接结构受力特性分析研究
飞机机翼-机身连接结构受力特性分析研究叶聪杰;杜艳梅;于振波【摘要】机翼-机身连接结构作为飞机设计中最重要的一环,应当准确分析其受力特性,合理设计其连接结构.基于有限元计算结果对A、B两种机翼-机身连接结构形式进行受力特性研究,分析表明B结构的机翼后梁后梯形板(或A结构前三角板)分担了部分载荷,减轻了后梁站位加强框承受的载荷.B结构连接刚度相对柔性,减小了后梁处协调变形的影响.A结构设计了后三角板,通过后三角板将起落架部分机构与机身的连接,后三角板分担了部分起落架载荷,对于机身的内力均匀分布是有利的.【期刊名称】《民用飞机设计与研究》【年(卷),期】2017(000)002【总页数】8页(P59-66)【关键词】受力特性;梯形板;有限元分析【作者】叶聪杰;杜艳梅;于振波【作者单位】上海飞机设计研究院,上海201210;上海飞机设计研究院,上海201210;上海飞机设计研究院,上海201210【正文语种】中文【中图分类】V214.1+1机翼-机身连接结构作为飞机设计中最重要的一环,应当准确分析其受力特性,合理设计其连接结构。
基于有限元计算结果对A、B两种机翼-机身连接结构形式进行受力特性研究,分析表明B结构的机翼后梁后梯形板(或A结构前三角板)分担了部分载荷,减轻了后梁站位加强框承受的载荷。
B结构连接刚度相对柔性,减小了后梁处协调变形的影响。
A结构设计了后三角板,通过后三角板将起落架部分机构与机身的连接,后三角板分担了部分起落架载荷,对于机身的内力均匀分布是有利的。
飞机根据机翼相对于机身的位置可分为上单翼布局、中单翼布局和下单翼布局[1-2]。
现代民用飞机中多采用下单翼布局,其机翼-机身连接的典型设计,是把机身的主隔框螺接在中央翼盒的前、后翼梁上,多年来这种连接方法已广泛地为飞机设计人员采用[1]。
典型的机翼-机身连接结构如图1所示。
MD-82飞机在机翼-机身的连接上没有采用以上设计[3-4],机身在中央翼后梁位置并没有机身框,左右各设计一个向后延伸的梯形板,通过梯形板将机翼后梁与机身的框连接。
超轻型飞机总体设计
飞机构造学结课大作业——超轻型飞机结构总体设计目录一.超轻型飞机总体外形设计二. 机翼结构设计三. 起落架的构造设计四.机身构造的设计五. 尾翼构造设计六.连接设计七.心得与体会八.参考文献一.超轻型飞机总体外形设计飞机主机翼采用上单翼布局,垂尾平尾正常式布局,采用对称翼型。
飞机尾部下方设置尾鳍,飞机采用前三点不可收放式起落架,机轮上设置整流罩减阻,机翼中部和机身底部之间设置有斜拉杆。
二.机翼结构设计1.机翼的选择采用矩形机翼,因为矩形机构简单,结构重量轻,超轻型飞机一般飞行速度都很低采用平直翼以获得更大的升力,矩形机翼当一处失速时,其它位置仍可以产生升力。
上单翼使飞机的横向稳定性增大,机翼离地面距离大,减小在颠簸跑道上起降时杂草划伤机翼表面和翼尖擦地等情况的发生。
机翼外形对于飞机的气动性能和结构性能有重要的影响,因此选择合理的机翼平面形状是非常重要的。
该轻型飞机的机翼剖面形状是平凸翼型,结构简单,便与生产,而且气动特性比较好。
机翼翼尖有一定的后掠,能增加横向安定性。
1).翼梁翼梁是飞机中的主要受力构件,它承受机翼的剪力和弯矩.翼梁主要由上下缘条和腹板组成,缘条承受由弯矩而产生的拉,压轴向力;腹板承受剪切力.本机型采用的翼梁构造形式是工字形,沿长度方向采用等强度设计.腹板式翼梁的优点是在相同的高度和同等的重量的情况下,带有立柱加强而腹板上无任何开孔,其强度最大.这种结构的翼梁制造工艺简单,成本低.适用于轻型飞机的设计与制造.2).纵墙它是一根缘条很弱或无缘条的腹板式翼梁.位于机翼后缘的纵墙可用来连接副翼和襟翼.它不能承受弯矩,主要用来承受剪力,并与蒙皮构成闭室结构承受机翼扭矩.3).翼肋本机型翼肋---构架式翼肋.由缘条,直支柱,斜支柱组成.用于结构高度较大的机翼上.翼肋按功用为普通翼肋.此种翼肋只承受气动载荷,形成并维持翼剖面形状,把蒙皮传给它的局部气动力传给翼梁腹板.腹板用来承剪,上下缘条用来承受因弯矩而产生的正应力,并连接蒙皮,普通翼肋的腹板抗剪强度,本机型翼肋有较大的承受预度,因此在腹板上开减轻孔以减重.4).蒙皮蒙皮是包围在骨架外面保持机翼气动外形的构件.机翼还参与机翼的总体受力.蒙皮与翼梁腹板所构成的机翼盒式梁受到由各翼肋沿闭室周缘传来的引起机翼扭转变形的力矩。
航空器气动布局的设计和分析
航空器气动布局的设计和分析一、概述航空器气动布局的设计和分析是航空工程学科中的一个重要分支,主要针对飞机在高速飞行中遇到的气动力学问题进行研究。
其目的是通过优化气动布局设计,提高飞机的性能和安全。
本文将分为以下几个部分,对航空器气动布局的设计和分析进行探讨。
二、气动布局设计飞机的气动布局设计包括机翼、机身、尾翼、发动机及各个部位之间的协调与匹配。
将各个部位的气动流场加以调整,使之达到最佳状态,以达到最佳性能。
1.机翼设计机翼的设计是飞机气动布局设计中最为重要的一部分。
机翼的气动设计不仅决定了飞机的外形,而且也影响了飞机的稳定性和飞行性能。
设计时需考虑以下几个方面:(1)机翼的平衡性一般来说,机翼设计必须满足平衡性的要求。
这意味着机翼必须在作用力的作用下,保持稳定运行,以防止其在飞行过程中出现不必要的姿态变化。
平衡性是机翼设计的重要考虑因素之一。
(2)机翼的升力与阻力特性机翼的升力与阻力特性也是设计的重要考虑因素。
升力特性决定了所需要的起飞和降落速度,而阻力特性则影响了飞机的航程。
设计时需要考虑这些因素来优化机翼的效率。
(3)机翼的强度与刚度机翼必须具有足够的强度和刚度,以支撑整个飞行器的质量,同时要满足对不同飞行载荷的要求。
(4)机翼的结构机翼结构的设计也是机翼设计的重要考虑因素之一。
需要考虑机翼的几何形状和材料属性,以满足不同的要求。
2.机身设计机身是整个飞机的骨架,负责承载机翼和发动机。
机身设计需要满足以下要求:(1)机身的气流稳定性机身必须具有良好的气流稳定性,以确保飞机在飞行过程中稳定。
(2)机身重量和刚度机身必须具有足够的强度和刚度,同时尽可能减少机身重量,确保飞机在飞行过程中能够承受飞行载荷的各种挑战。
(3)机身内部布局的合理性机身内部的设备必须合理布置,以便维修和保养。
3.尾翼设计尾翼的设计必须考虑与机翼的匹配,以及满足稳定性和机动性等要求。
尾翼可以帮助控制飞机的稳定性,同时也能通过变动尾翼的位置和角度来帮助控制飞机。