电线插座外壳的冷冲模结构设计方案
插座外壳逆向建模及模具设计

过修 剪、 镜像、 缝合 、 加 厚、 倒 角等 命 令 后 求 得 插 座 壳 实 体 模
图2 — 3 原始点云 ( 背面)
( 二) 点 云 处理 Ge o ma g i c S u t d i o 2 0 1 2是 美 国 R a i n d r o p Ge o ma g i c软 件 公 司
( 一) 点 云采 集
逆 向 建 模 实 物 插 座 壳 为 西 门 子 照 明 的插 座 壳 , 5 U B 0 1 0 6 1 C C 1 , 如图2 - 1 。 点 云 采 集 设备 为 R O ME R公 司生 产 的
I NF I NI T E 2 . 0柔性 关 节臂 测 量 机 。 该 插 座 壳的 面 板 的 采 用 德 国进 口 P C 聚碳 酸 脂 , 注 塑 工 艺 很好、 光 洁度 非常 高、 不 变 色和 耐 老 化 。 安 装 电流要 求 1 0 A, 电 压要求 2 5 0 V; 插 座 保 护 门可 承 受 2 0 N力; 插座壳为对称体 , 仅 需要扫描一半即可 , 另 一 半 在 建 模 后 镜 像 即 可 获 得 完 整模 型 。数 据 扫 描 结 果如 图 2 — 2 、 2 — 3 Biblioteka 图2 - 4 处理后点云
一
图2 — 5 外形 曲面集
图2 — 6 插座壳实体模 型
一 ■
( 三) 片体 构 造
I
、 ,
I ma g e wa r e 1 3 有 非常 强的 云 处 及 曲 面 编辑 和构 建 能 力。用
I ma g e w a r e l 3可 以构 造 出 良好 的插 座 壳 外 形 曲 面 。如 图 2 — 5即
冷冲模冷冲压模具的结构与设计1课件

工作零件
工艺零件 定位零件
冲裁模零部件
卸料与推件零部件
结构零件 导向零件 连接与固定零件
其它零件
二、模具零件的结构与设计
1、凸模组件及其结构设计 2、凹模设计 3、定位零件 4、卸料与推件零件 5、模架
1、凸模组件及其结构设计
凸模组件:凸模、凸模固定板、垫板和防转销、 上模座、螺钉、销钉固定
倒装模凸凹模的最小壁厚: 查p.102表4-4
3、定位零件
横向定位装置:使条料由正确的送进方向
导料销、导料板及侧压装置
纵向定位装置:控制条料在冲裁中送进步距
挡料销、导正销、侧刃
定位板和定位钉
横向定位装置
导料销
导料销两个,位于条料的同侧
导料板
两导料板之间距离L=条料最大宽度+间隙值 导料板厚度H=材料厚度t或挡料销高度+(2∽8) 整体式导料板其长度和宽度与凹模板外形尺寸
缺点:模具结构复杂,材料有额外消耗,定位 精度不高。
连续模排样
连续模排样设计:
1、零件精度对排样要求:
精度要求高——尽量减少工位数 孔距公差较小——尽量同一工位冲出
2、模具结果对排样要求:
零件较大或较小但工位多——采用连续复合排样
3、模具强度对排样要求:
孔距小——分布冲 工位间凹模壁厚小——增设空工位 外形复杂——分布冲
动力由压力机传递给 模具
相关链接:动力
第一节 冲压模的分类
一、按工序组合程度分 二、按上下模导向方式分 三、按凹模位置分 四、按自动化程度分
一、按工序组合程度分
1、单工序模(简单模)
单工序模是指压力机在一次行程中只完成一道工序的冲裁模
2在、一多副模工具中序,模在模具的同一位置上能同时完成数种 工序的模具 (在压力机的一次行程中,在模具的同一位置上同时 完成A几、道连工序续的模冲(模)级进模、跳步模) 在一副模具中,材料在模具的不同位置上能同时完成各 自工(B序是、指复压合力机模在一次行程中依次在几个不同的位置上 同时完成多道工序的冲模)
冷冲模设计方案步骤

冷冲模设计步骤(冷板制件)-----云云制作工艺性分析根据生产批量、零件图样及零件的技术要求,评审制件是否适合冲压,确定其进行冲裁加工的可能性及加工难易程度;1)冲裁件的形状冲裁件的形状应力求简单、对称,有利于材料的合理利用2) 冲裁件内形及外形的转角冲裁件内形及外形的转角处要尽量避免尖角,应以圆弧过渡,以减少热处理应力集中及冲裁时的破裂现象3)冲裁件上凸出的悬臂和凹槽尽量避免冲裁件上过长的凸出悬臂和凹槽,悬臂和凹槽宽度也不宜过小,其最小取值为b宽度>2t,l长度≤5t4)冲裁件的孔边距与孔间距b 、b1 为避免工件变形和保证模具强度,孔边距和孔间距不能过小,一般取b≥1.5t,b1≥2t5)在弯曲件或拉深件上冲孔时,孔边与直壁之间应保持一定距离,以免冲孔时凸模受水平推力而折断6)冲孔时,因受凸模强度的限制,孔的尺寸不应太小,否则凸模易折断或压弯,普通冲裁模的冲孔最小孔径一般应大于材料厚度确定合理的冲裁工艺方案(重要)在工艺分析的基础上,拟定出可能的冲裁方案,再根据制件的形状、尺寸、公差要求、材料性能、生产批量、冲压设备、模具加工难度等多方面因素,进行全面的分析研究,比较其综合的经济效果,在满足制件质量要求的前提下,以最大限度的降低生产成本为目的,选择确定一个合理的冲压工艺方案;模具总体结构的构思(重要)✧确定模具的类型,主要与制件的尺寸大小、形状、精度、和生产批量有关✧在确定模具设计方案时,不仅要考虑总体设计方案,同时也要对主要零部件的结构进行设计。
对于结构极其复杂的模具,若总体方案设计时难以清楚表达模具中某个零件的结构特征时,也往往先勾画出该零件的结构草图,以便衡量该零件对模具总体结构的适应性。
模具主要零件的结构设计,就是确定工作零件、定位零件、卸料和出件零件、导向零件以及连接与固定零件的结构形式和固定方法✧冲裁模总体结构尺寸必须与所选用的压力机相适应,即模具的总体平面尺寸应该与压力机工作台或垫板尺寸和滑块下平面尺寸相适应;模具的封闭(闭合)高度应与压力机的装模高度或封闭高度相适应。
冷冲模设计教案(2010年版)
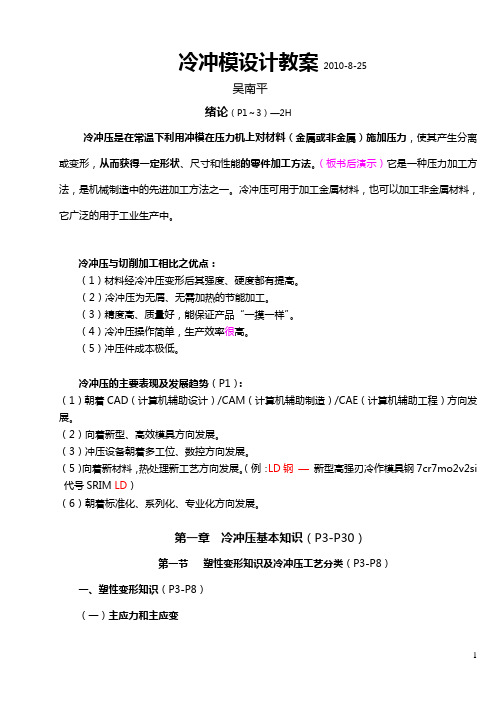
冷冲模设计教案2010-8-25吴南平绪论(P1~3)—2H冷冲压是在常温下利用冲模在压力机上对材料(金属或非金属)施加压力,使其产生分离或变形,从而获得一定形状、尺寸和性能的零件加工方法。
(板书后演示)它是一种压力加工方法,是机械制造中的先进加工方法之一。
冷冲压可用于加工金属材料,也可以加工非金属材料,它广泛的用于工业生产中。
冷冲压与切削加工相比之优点:(1)材料经冷冲压变形后其强度、硬度都有提高。
(2)冷冲压为无屑、无需加热的节能加工。
(3)精度高、质量好,能保证产品“一摸一样”。
(4)冷冲压操作简单,生产效率很高。
(5)冲压件成本极低。
冷冲压的主要表现及发展趋势(P1):(1)朝着CAD(计算机辅助设计)/CAM(计算机辅助制造)/CAE(计算机辅助工程)方向发展。
(2)向着新型、高效模具方向发展。
(3)冲压设备朝着多工位、数控方向发展。
(5)向着新材料,热处理新工艺方向发展。
(例:LD钢—新型高强刃冷作模具钢7cr7mo2v2si 代号SRIM LD)(6)朝着标准化、系列化、专业化方向发展。
第一章冷冲压基本知识(P3-P30)第一节塑性变形知识及冷冲压工艺分类(P3-P8)一、塑性变形知识(P3-P8)(一)主应力和主应变1、应力与应变应力:内力在物体截面上分布的密集程度称为应力。
(即;内力(被除数)除以物体截面积(除数)叫做应力(商)。
内力:物体的内部力量,内力=外力。
根据作用反作用,力的平衡原理,结构物体的内力=外力。
外力:物体自重及外部所受的力量。
外力通常有物体自身重量、人群活动负载、太阳辐射、引力等……。
应变:指微小平行六面体素内的“应力变化”的简称或缩写。
正应力:垂直于截面的应力称为正应力用σ(西格马)表示。
如下图所示。
切应力:同截面相切的应力称为切应力用τ(滔)表示。
如下图所示2、点的应力状态(P3)常用三个面的正应力来表示一个点的主应力。
3、主应力和主应力图主应力:指主要应力,常用一个点的三个方向正应力来表示一个主应力。
毕业设计(论文)-电源插头冲压模具设计(含全套CAD图纸)

论文题目:电源插头冲压模具设计学生姓名指导教师专业班级专业系部提交日期目录前言 (3)一、电源插头冲裁模设计1、电源插头零件图 (13)2、冲压件工艺分析 (13)3、方案及模具结构类型 (14)4、排样设计 (14)5、压力与压力中心计算 (15)6、压力中心 (16)7、零件刃口尺寸计算 (17)8、冲床选用 (18)9、模具总体设计 (19)10、主要零部件设计 (20)11、模具总装配 (18)二、模具零件加工工艺1、模具零件加工工艺及工序卡 (25)2、模具零件图 (25)3、模具装配图 (25)设计总结 (35)参考文献 (36)前言毕业设计是06年高技学生的综合性实践环节,目的是通过课题的设计研究,培养综合运用各门课程知识的能力,培养独立分析问题和解决问题的能力。
毕业设计应密切与生产实际相结合,应与培养职业能力相结合,应体现职高的特点。
在指导教师周密安排和精心指导下,这次毕业设计从确定设计课题、拟定设计方案、设计过程到毕业答辩都按照毕业设计工作计划进行。
第一,充分调研,确定应用型毕业设计课题。
选好毕业设计题目是实现毕业设计目标、保证毕业设计质量的前提,我们的毕业设计的课题取自企业生产实际。
这个课题能较全面地应用学生所学专业知识或者将来工作所需的专业技术,达到综合运用的目的,既能够解决企业急需解决的生产技术问题,又能够培养学生的职业岗位能力,难度不是很大,符合我们高职专科生的专业理论知识水平和实际设计能力,工作量恰当,能够在规定时间内完成。
但是该课题是真题真做,虽然难度不是很大,但要使设计图纸能真接用于生产,去造出零件,装配成机器,并能满足使用要求,也是不容易的。
第二,反复论证,确定产品设计方案。
明确课题的性质、意义、设计内容、设计要达到的技术经济指标和完成时间,并确定好正确合理的设计方案是完成设计任务的保证,指导教师、企业技术员让我们参与设计方案的讨论,使我们对课题设计方案心中有数。
冷冲压模具设计

冷冲压模具设计冷冲压模具设计是一门重要的制造技术,该技术通过塑造和压制金属原材料翻译成最终产品。
冷冲压模具设计的方法包括计算机辅助设计、3D打印和机器加工等技术的应用。
下面我们将从制造过程、设计流程、成本控制和应用领域等方面进行分析。
一、冷冲压模具制造过程冷冲压模具制造过程包括模具测量、设备加工、热处理、抛光和装配等环节。
在测量阶段,需要使用高精度测量工具,如3D扫描仪、测微计和显微镜等。
测量结果将被输入计算机进行模具设计,绘制3D模型。
模具设计完成后,需要设置加工设备,进行模块的制造。
常用的加工设备包括数控机床、电火花加工机和线切割机等。
设备加工完成后,需要进行热处理,使得模板具有较高的耐久性和稳定性。
在模具加工的过程中,抛光则是非常重要的一环节,其需要使用高性能抛光机,使得模板表面平滑、光亮且和物质摩擦力小。
在抛光之后,需要进行装配,使得模版的各个部分可以组合在一起,达到最终的高质量产品。
二、冷冲压模具的设计流程冷冲压模具的设计流程通常包括五个步骤:对产品的了解、设计评估、详细设计、模具制造、实验和完善。
对于产品的了解,设计团队首先要了解所需的产量、污染物、尺寸要求、货币化以及材料类型等信息。
然后针对所得信息进行分析、评估它们的可行性和可持续性。
接下来,设计团队会根据所得信息针对具体的产品进行详细的设计和制造。
三、冷冲压模具设计的成本控制冷冲压模具设计的成本主要是由以下方面组成:硬件成本、工具和设备的成本、人员费用和测试以及批量生产的成本,因此要实现成本控制,需要在这些方面做好以下工作。
首先,团队应该在设计模板时发挥更多的想象力。
这样不仅可以使得模板制造的复杂性减少,还可以大幅度降低制造成本。
其次,需要对材料进行有效的管理,以确保使用高品质、高耐久的材料制造模板。
同时,要尽可能地排除不必要的浪费,使得材料得到充分利用。
最后,改善生产流程和管理方法,以提高作业效率和节约工作时间。
此外,通过采用高性能和节能型的加工设备,也可以降低成本。
冷冲模设计说明书
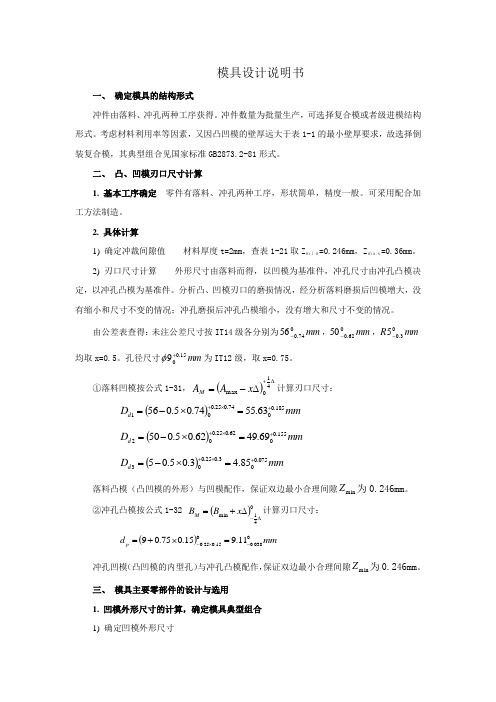
模具设计说明书一、 确定模具的结构形式冲件由落料、冲孔两种工序获得。
冲件数量为批量生产,可选择复合模或者级进模结构形式。
考虑材料利用率等因素,又因凸凹模的壁厚远大于表1-1的最小壁厚要求,故选择倒装复合模,其典型组合见国家标准GB2873.2-81形式。
二、 凸、凹模刃口尺寸计算1. 基本工序确定 零件有落料、冲孔两种工序,形状简单,精度一般。
可采用配合加工方法制造。
2. 具体计算1) 确定冲裁间隙值 材料厚度t=2mm ,查表1-21取Z min=0.246mm ,Z max=0.36mm 。
2) 刃口尺寸计算 外形尺寸由落料而得,以凹模为基准件,冲孔尺寸由冲孔凸模决定,以冲孔凸模为基准件。
分析凸、凹模刃口的磨损情况,经分析落料磨损后凹模增大,没有缩小和尺寸不变的情况;冲孔磨损后冲孔凸模缩小,没有增大和尺寸不变的情况。
由公差表查得:未注公差尺寸按IT14级各分别为mm 074.056-,mm 062.050-,mmR 03.05-均取x=0.5。
孔径尺寸mm 15.009+φ为IT12级,取x=0.75。
①落料凹模按公式1-31,()∆+∆-=410max x A A M 计算刃口尺寸:()mm D d 185.0074.025.00163.5574.05.056+⨯+=⨯-=()mm D d 155.0062.025.00269.4962.05.050+⨯+=⨯-= ()mm D d 075.003.025.00385.43.05.05+⨯+=⨯-=落料凸模(凸凹模的外形)与凹模配作,保证双边最小合理间隙min Z 为0.246mm 。
②冲孔凸模按公式1-32 ()041min ∆-∆+=x B B M 计算刃口尺寸: ()mmd p 0038.0015.025.011.915.075.09-⨯-=⨯+= 冲孔凹模(凸凹模的内型孔)与冲孔凸模配作,保证双边最小合理间隙min Z 为0.246mm 。
电源插头外壳注射模设计本科毕业设计.doc
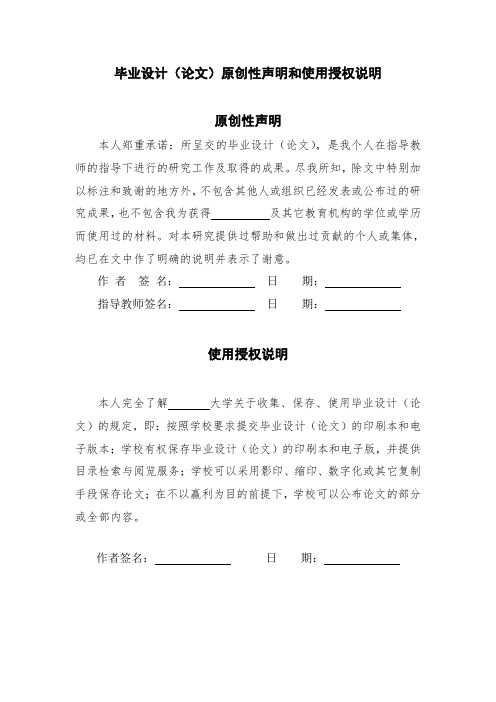
毕业设计(论文)原创性声明和使用授权说明原创性声明本人郑重承诺:所呈交的毕业设计(论文),是我个人在指导教师的指导下进行的研究工作及取得的成果。
尽我所知,除文中特别加以标注和致谢的地方外,不包含其他人或组织已经发表或公布过的研究成果,也不包含我为获得及其它教育机构的学位或学历而使用过的材料。
对本研究提供过帮助和做出过贡献的个人或集体,均已在文中作了明确的说明并表示了谢意。
作者签名:日期:指导教师签名:日期:使用授权说明本人完全了解大学关于收集、保存、使用毕业设计(论文)的规定,即:按照学校要求提交毕业设计(论文)的印刷本和电子版本;学校有权保存毕业设计(论文)的印刷本和电子版,并提供目录检索与阅览服务;学校可以采用影印、缩印、数字化或其它复制手段保存论文;在不以赢利为目的前提下,学校可以公布论文的部分或全部内容。
作者签名:日期:学位论文原创性声明本人郑重声明:所呈交的论文是本人在导师的指导下独立进行研究所取得的研究成果。
除了文中特别加以标注引用的内容外,本论文不包含任何其他个人或集体已经发表或撰写的成果作品。
对本文的研究做出重要贡献的个人和集体,均已在文中以明确方式标明。
本人完全意识到本声明的法律后果由本人承担。
作者签名:日期:年月日学位论文版权使用授权书本学位论文作者完全了解学校有关保留、使用学位论文的规定,同意学校保留并向国家有关部门或机构送交论文的复印件和电子版,允许论文被查阅和借阅。
本人授权大学可以将本学位论文的全部或部分内容编入有关数据库进行检索,可以采用影印、缩印或扫描等复制手段保存和汇编本学位论文。
涉密论文按学校规定处理。
作者签名:日期:年月日导师签名:日期:年月日指导教师评阅书评阅教师评阅书教研室(或答辩小组)及教学系意见1 引言模具是制造业的一种基本工艺装备,它的作用是控制和限制材料(固态或液态)的流动,使之形成所需要的形体。
用模具制造零件以其效率高,产品质量好,材料消耗低,生产成本低而广泛应用于制造业中。
- 1、下载文档前请自行甄别文档内容的完整性,平台不提供额外的编辑、内容补充、找答案等附加服务。
- 2、"仅部分预览"的文档,不可在线预览部分如存在完整性等问题,可反馈申请退款(可完整预览的文档不适用该条件!)。
- 3、如文档侵犯您的权益,请联系客服反馈,我们会尽快为您处理(人工客服工作时间:9:00-18:30)。
电线插座外壳的冷冲模结构设计1.1 模具市场发展趋势模具,是工业生产的基础工艺装备,在电子、汽车、电机、电器、仪表、家电和通讯等产品中,60%—80%的零部件都依靠模具成形,模具质量的高低决定着产品质量的高低,因此,模具被称之为“百业之母”。
模具又是“效益放大器”,用模具生产的最终产品的价值,往往是模具自身价值的几十倍、上百倍。
模具生产的工艺水平及科技含量的高低,已成为衡量一个国家科技与产品制造水平的重要标志,它在很大程度上决定着产品的质量、效益、新产品的开发能力,决定着一个国家制造业的国际竞争力。
我国模具工业的技术水平近年来也取得了长足的进步。
大型、精密、复杂、高效和长寿命模具上了一个新台阶。
大型复杂冲模以汽车覆盖件模具为代表,已能生产部分新型轿车的覆盖件模具。
体现高水平制造技术的多工位级进模的覆盖面,已从电机、电器铁芯片模具,扩展到接插件、电子枪零件、空调器散热片等家电零件模具。
在大型塑料模具方面,已能生产48英寸电视的塑壳模具、6.5K g大容量洗衣机全套塑料模具,以及汽车保险杠、整体仪表板等模具。
在精密塑料模具方面,已能生产照相机塑料模具、多型腔小模数齿轮模具及塑封模具等。
在大型精密复杂压铸模方面,国内已能生产自动扶梯整体踏板压铸模及汽车后桥齿轮箱压铸模。
其他类型的模具,例如子午线轮胎活络模具、铝合金和塑料门窗异型材挤出模等,也都达到了较高的水平,并可替代进口模具。
根据国内和国际模具市场的发展状况,有关专家预测,未来我国的模具经过行业结构调整后,将呈现十大发展趋势:一是模具日趋大型化;二是模具的精度将越来越高;三是多功能复合模具将进一步发展;四是热流道模具在塑料模具中的比重将逐渐提高;五是气辅模具及适应高压注射成型等工艺的模具将有较大发展;六是模具标准化和模具标准件的应用将日渐广泛;七是快速经济模具的前景十分广阔;八是压铸模的比例将不断提高,同时对压铸模的寿命和复杂程度也将提出越来越高的要求;九是塑料模具的比例将不断增大;十是模具技术含量将不断提高,中高档模具比例将不断增大,这也是产品结构调整所导致的模具市场未来走势的变化1.2 冲压模具的现状和技术发展一、现状改革开放以来,随着国民经济的高速发展,市场对模具的需求量不断增长。
近年来,模具工业一直以15%左右的增长速度快速发展,模具工业企业的所有制成分也发生了巨大变化,除了国有专业模具厂外,集体、合资、独资和私营也得到了快速发展。
浙江宁波和黄岩地区的“模具之乡”;广东一些大集团公司和迅速崛起的乡镇企业,科龙、美的、康佳等集团纷纷建立了自己的模具制造中心;中外合资和外商独资的模具企业现已有几千家。
随着与国际接轨的脚步不断加快,市场竞争的日益加剧,人们已经越来越认识到产品质量、成本和新产品的开发能力的重要性。
而模具制造是整个链条中最基础的要素之一。
近年许多模具企业加大了用于技术进步的投资力度,将技术进步视为企业发展的重要动力。
一些国内模具企业已普及了二维CAD,并陆续开始使用UG、Pro/Engineer、I-DEAS、Euclid-IS等国际通用软件,个别厂家还引进了Moldflow、C-Flow、DYNAFORM、Optris和MAGMASOFT等CAE软件,并成功应用于冲压模的设计中。
以汽车覆盖件模具为代表的大型冲压模具的制造技术已取得很大进步,东风汽车公司模具厂、一汽模具中心等模具厂家已能生产部分轿车覆盖件模具。
此外,许多研究机构和大专院校开展模具技术的研究和开发。
经过多年的努力,在模具CAD/CAE/CAM技术方面取得了显著进步;在提高模具质量和缩短模具设计制造周期等方面做出了贡献。
例如,吉林大学汽车覆盖件成型技术所独立研制的汽车覆盖件冲压成型分析KMAS软件,华中理工大学模具技术国家重点实验室开发的注塑模、汽车覆盖件模具和级进模CAD/CAE/CAM软件,上海交通大学模具CAD国家工程研究中心开发的冷冲模和精冲研究中心开发的冷冲模和精冲模CAD软件等在国内模具行业拥有不少的用户。
虽然中国模具工业在过去十多年中取得了令人瞩目的发展,但许多方面与工业发达国家相比仍有较大的差距。
例如,精密加工设备在模具加工设备中的比重比较低;CAD/CAE/CAM技术的普及率不高;许多先进的模具技术应用不够广泛等等,致使相当一部分大型、精密、复杂和长寿命模具依赖进口。
二、未来冲压模具制造技术发展趋势模具技术的发展应该为适应模具产品“交货期短”、“精度高”、“质量好”、“价格低”的要求服务。
达到这一要求急需发展如下几项:1、全面推广CAD/CAM/CAE技术模具CAD/CAM/CAE技术是模具设计制造的发展方向。
随着微机软件的发展和进步,普及CAD/CAM/CAE技术的条件已基本成熟,各企业将加大CAD/CAM技术培训和技术服务的力度;进一步扩大CAE技术的应用范围。
计算机和网络的发展正使CAD/CAM/CAE技术跨地区、跨企业、跨院所地在整个行业中推广成为可能,实现技术资源的重新整合,使虚拟制造成为可能。
2、高速铣削加工国外近年来发展的高速铣削加工,大幅度提高了加工效率,并可获得极高的表面光洁度。
另外,还可加工高硬度模块,还具有温升低、热变形小等优点。
高速铣削加工技术的发展,对汽车、家电行业中大型型腔模具制造注入了新的活力。
目前它已向更高的敏捷化、智能化、集成化方向发展。
3、模具扫描及数字化系统高速扫描机和模具扫描系统提供了从模型或实物扫描到加工出期望的模型所需的诸多功能,大大缩短了模具的在研制制造周期。
有些快速扫描系统,可快速安装在已有的数控铣床及加工中心上,实现快速数据采集、自动生成各种不同数控系统的加工程序、不同格式的CAD数据,用于模具制造业的“逆向工程”。
模具扫描系统已在汽车、摩托车、家电等行业得到成功应用,相信在“十五”期间将发挥更大的作用。
4、电火花铣削加工电火花铣削加工技术也称为电火花创成加工技术,这是一种替代传统的用成型电极加工型腔的新技术,它是有高速旋转的简单的管状电极作三维或二维轮廓加工(像数控铣一样>,因此不再需要制造复杂的成型电极,这显然是电火花成形加工领域的重大发展。
国外已有使用这种技术的机床在模具加工中应用。
预计这一技术将得到发展。
5、提高模具标准化程度我国模具标准化程度正在不断提高,估计目前我国模具标准件使用覆盖率已达到30%左右。
国外发达国家一般为80%左右。
6、优质材料及先进表面处理技术选用优质钢材和应用相应的表面处理技术来提高模具的寿命就显得十分必要。
模具热处理和表面处理是否能充分发挥模具钢材料性能的关键环节。
模具热处理的发展方向是采用真空热处理。
模具表面处理除完善应发展工艺先进的气相沉积(TiN、TiC等>、等离子喷涂等技术。
7、模具研磨抛光将自动化、智能化模具表面的质量对模具使用寿命、制件外观质量等方面均有较大的影响,研究自动化、智能化的研磨与抛光方法替代现有手工操作,以提高模具表面质量是重要的发展趋势。
8、模具自动加工系统的发展这是我国长远发展的目标。
模具自动加工系统应有多台机床合理组合;配有随行定位夹具或定位盘;有完整的机具、刀具数控库;有完整的数控柔性同步系统;有质量监测控制系统。
1.3冲压模具简介一、概念冲压模具--在冷冲压加工中,将材料<金属或非金属)加工成零件<或半成品)的一种特殊工艺装备,称为冷冲压模具<俗称冷冲模)。
冲压--是在室温下,利用安装在压力机上的模具对材料施加压力,使其产生分离或塑性变形,从而获得所需零件的一种压力加工方法。
冲压模具是冲压生产必不可少的工艺装备,是技术密集型产品。
冲压件的质量、生产效率以及生产成本等,与模具设计和制造有直接关系。
模具设计与制造技术水平的高低,是衡量一个国家产品制造水平高低的重要标志之一,在很大程度上决定着产品的质量、效益和新产品的开发能力。
二、分类冲压模具的形式很多,一般可按以下几个主要特征分类:1、根据工艺性质分类(1>冲裁模沿封闭或敞开的轮廓线使材料产生分离的模具。
如落料模、冲孔模、切断模、切口模、切边模、剖切模等。
(2>弯曲模使板料毛坯或其他坯料沿着直线<弯曲线)产生弯曲变形,从而获得一定角度和形状的工件的模具。
(3>拉深模是把板料毛坯制成开口空心件,或使空心件进一步改变形状和尺寸的模具。
(4>成形模是将毛坯或半成品工件按图凸、凹模的形状直接复制成形,而材料本身仅产生局部塑性变形的模具。
如胀形模、缩口模、扩口模、起伏成形模、翻边模、整形模等。
2、根据工序组合程度分类(1>单工序模压力机的一次行程中,只完成一道冲压工序的模具(2>复合模只有一个工位,在压力机的一次行程中,在同一工位上同时完成两道或两道以上冲压工序的模具。
(3>级进模<也称连续模)在毛坯的送进方向上,具有两个或更多的工位,在压力机的一次行程中,在不同的工位上逐次完成两道或两道以上冲压工序的模具。
3、根据产品的加工方法分类根据产品加工方法的不同,可将模具分成冲剪模具、弯曲模具、抽制模具、成形模具和压缩模具等五大类。
(1>冲剪模具:是以剪切作用完成工作的,常用的形式有剪断冲模、下料冲模、冲孔冲模、修边冲模、整缘冲模、拉孔冲模和冲切模具。
(2>弯曲模具:是将平整的毛胚弯成一个角度的形状,视零件的形状、精度及生产量的多寡,有多种不同形式的模具,如普通弯曲冲模、凸轮弯曲冲模、卷边冲模、圆弧弯曲冲模、折弯冲缝冲模与扭曲冲模等。
(3>抽制模具:抽制模具是将平面毛胚制成有底无缝容器。
(4>成形模具:指用各种局部变形的方法来改变毛胚的形状,其形式有凸张成形冲模、卷缘成形冲模、颈缩成形冲模、孔凸缘成形冲模、圆缘成形冲模。
(5>压缩模具:是利用强大的压力,使金属毛胚流动变形,成为所需的形状,其种类有挤制冲模、压花冲模、压印冲模、端压冲模。
4、冲模也依工作性质,模具构造,模具材料三方面来分类。
三、特点1.最重要的是有效率,生产率是惊人的。
2.对人工的依赖较低,从而导致了成本的降低3.安全隐患得到了控制,要知道一个成产型企业,安全是第一位的。
如果控制不好,是成本控制的第一阻碍。
4.根据设计的经验和技术的进步,可以生产更加精密的产品。
四、典型结构通常模具是由二类零件组成:第一类是工艺零件,这类零件直接参与工艺过程的完成并和坯料有直接接触,包括有工作零件、定位零件、卸料与压料零件等。
第二类是结构零件,这类零件不直接参与完成工艺过程,也不和坯料有直接接触,只对模具完成工艺过程起保证作用,或对模具功能起完善作用,包括有导向零件、紧固零件、标准件及其它零件等。
应该指出,不是所有的冲模都必须具备上述六种零件,尤其是单工序模,但是工作零件和必要的固定零件等是不可缺少的。