航空复合材料结构件常用的成型方法
航空复合材料整体成型技术应用

航空复合材料整体成型技术应用(作者单位:哈尔滨飞机工业集团有限责任公司)◎郭璐璐整体成型技术的应用对以往的装配流程进行了简化,可以在较短的时间内完成零部件的装配作业,有利于提高生产制造效率,减少成本投入。
航空复合材料整体成型技术具有经济性、装配简单和翼身一体化等特点,要加强对这项技术的研究与应用,选择合适的整体成型技术方法,以此促进施工工艺的有效落实,保证这项技术应用的有效性,对航空制造业的进一步发展有着重要意义。
一、航空复合材料整体成型技术优点复合材料在多个领域中都得到了广泛应用,在大型机械设备制造中也能够取得良好效果,逐步向着大型化的方向发展。
大型化构件在应用期间方便装配作业,节省了施工时间,同时也可以避免多构件装配过程中存在的隐患问题。
航空复合材料整体成型技术应用优点比较多,主要体现在以下几个方面:1.经济性良好。
整体成型技术在应用期间能够利用多种连接方法将多种复合材料零件连接在一起,组成一个整体结构,这在一定程度上节省了装配时间,不需要进行零件对接,使得航空构件内部分段数量减少,航空设备的整体性得到了提升。
在成本投入方面,由于整体成型技术的应用省去了多个环节,减轻了结构重量,复合材料的用量也有所减少,节约了材料成本投入,具有良好的经济性特点。
2.便于装配工作的顺利开展。
航空产品的内部结构较为复杂,组成的零件数量和种类比较多,以往在进行装配时需要的紧固构件有几十万个,装配人员的工作量比较大,同时,容易出现监控管理不到位的情况,无法保证构件之间连接的有效性,所以存在一定的质量隐患。
复合材料整体成型技术的应用能够将多种零件形成一个整体,使装配期间使用的紧固构件缩减到几千个甚至几百个,便于装配工作的顺利开展,节省了装配时间,方便了装配期间的管理与控制工作。
原有的航空制造中,装配期间需要使用专门的工具设备对构件进行打孔操作,在此期间要保证孔的精度和质量。
另外,为了对电化腐蚀现象进行有效控制一般都会用湿化装配方法,这种方法所需的资金量比较大,增加了设备制造成本。
复合材料结构及其成型原理
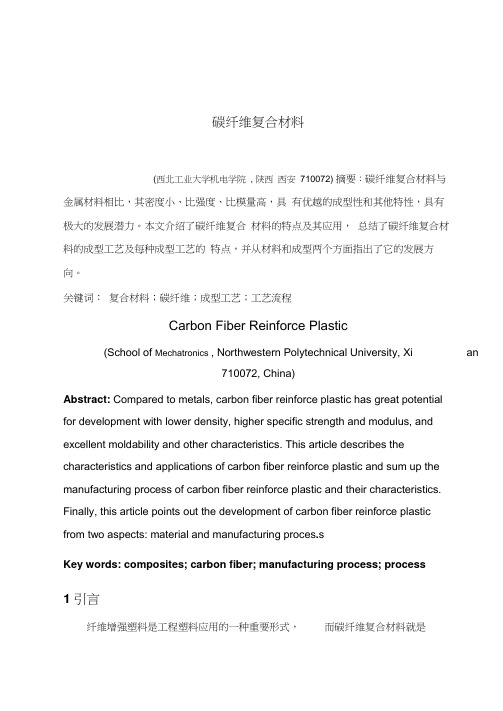
碳纤维复合材料(西北工业大学机电学院, 陕西西安710072) 摘要:碳纤维复合材料与金属材料相比,其密度小、比强度、比模量高,具有优越的成型性和其他特性,具有极大的发展潜力。
本文介绍了碳纤维复合材料的特点及其应用,总结了碳纤维复合材料的成型工艺及每种成型工艺的特点,并从材料和成型两个方面指出了它的发展方向。
关键词:复合材料;碳纤维;成型工艺;工艺流程Carbon Fiber Reinforce Plastic(School of Mechatronics , Northwestern Polytechnical University, Xian710072, China)Abstract: Compared to metals, carbon fiber reinforce plastic has great potentialfor development with lower density, higher specific strength and modulus, and excellent moldability and other characteristics. This article describes the characteristics and applications of carbon fiber reinforce plastic and sum up the manufacturing process of carbon fiber reinforce plastic and their characteristics. Finally, this article points out the development of carbon fiber reinforce plasticfrom two aspects: material and manufacturing proces.sKey words: composites; carbon fiber; manufacturing process; process1引言纤维增强塑料是工程塑料应用的一种重要形式,而碳纤维复合材料就是其中的佼佼者,它以其所具有的低密度、高比强度、高比模量和优越的成型性和其他物理、化学特性在军事、航天、航空、电子等领域被广泛地应用,具有极大的发展潜力。
航空复合材料的分类,工艺技术以及在航空领域的应用情况研究

航空复合材料的分类,工艺技术以及在航空领域的应用情况研究近几十年来,随着复合材料技术的进步,复合材料因在航空领域的广泛应用,继铝、钢、钛等金属材料之后成为四大航空基本结构材料之一。
用复合材料去带取代传统的机械金属结构能够减轻20%~30%的结构重量,减低飞机制造成本。
本文通过研究了航空复合材料的分类、制造航空复合材料的工艺技术、复合材料在航空领域的应用情况等角度分析航空复合材料的性能特点在飞机上的应用,复合材料的制备技术对航空结构的影响、航空复合材料在飞机上的应用发展情况。
关键词:航空;复合材料;航空运用;研究一、航空复合材料1.1树脂基复合材料树脂基复合材料,具有良好的化学稳定性、超高韧性和高耐热性;碳纤维是一种基于有机聚合物的纤维增强材料,具有质量轻、强度高、韧性强、机械性能优良等优点,是一种能够灵活设计结构的理想材料。
1.2陶瓷基复合材料陶瓷基复合材料是一种耐热结构复合材料,具有高强度、比重大、体积小、抗氧化、耐高温性能好、热膨胀系数低、抗腐蚀能力强,其缺点是受力易产生裂纹,脆性大[1]。
通过采用高强度、高弹性的纤维和基体复合,得到有优良韧性的纤维增强陶瓷基复合材料能够解决应力状态下会产生裂纹的问题。
硼化物陶瓷基复合材料具有优异的性能,如熔点高、硬度高、导热率高等,广泛应用在超高温的发动机部位,美国空军将其应用在液体火箭发动机高温静止部件上[2]。
二、航空复合材料技术随着飞行器向更高、更快、智能化、无人化、低成本化演变,航空复合材料技术研究的目标是扩大复合材料在航空结构中的应用范围,以尽可能低的使用成本生产高性能的航空零部件。
复合材料制造技术的不断突破和性能不断提高在解决复合材料过高的制造成本起着重要作用,这是目前复合材料在应用上的一个大难题。
复合材料的制造技术分为以下几种。
2.1零件成形技术(1)树脂传递模塑成型技术(RTM)自上世纪90年代之后,已经开发了应用于高强度主承力结构技术的低成本制造技术,如今已应用在F-35战斗机的垂尾上。
复合材料结构特点、设计要点以及成型方法
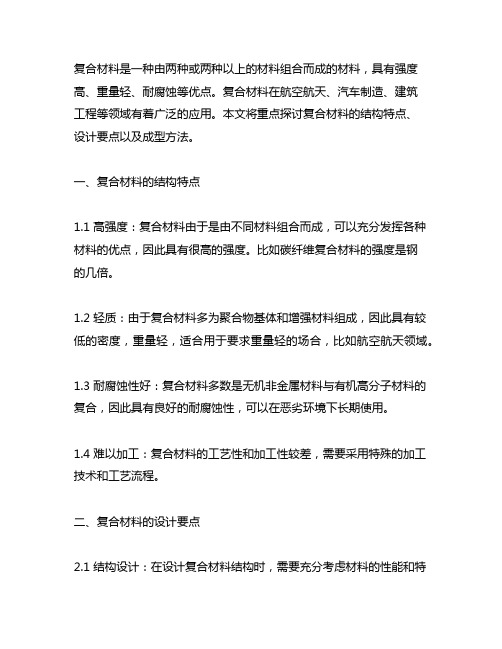
复合材料是一种由两种或两种以上的材料组合而成的材料,具有强度高、重量轻、耐腐蚀等优点。
复合材料在航空航天、汽车制造、建筑工程等领域有着广泛的应用。
本文将重点探讨复合材料的结构特点、设计要点以及成型方法。
一、复合材料的结构特点1.1 高强度:复合材料由于是由不同材料组合而成,可以充分发挥各种材料的优点,因此具有很高的强度。
比如碳纤维复合材料的强度是钢的几倍。
1.2 轻质:由于复合材料多为聚合物基体和增强材料组成,因此具有较低的密度,重量轻,适合用于要求重量轻的场合,比如航空航天领域。
1.3 耐腐蚀性好:复合材料多数是无机非金属材料与有机高分子材料的复合,因此具有良好的耐腐蚀性,可以在恶劣环境下长期使用。
1.4 难以加工:复合材料的工艺性和加工性较差,需要采用特殊的加工技术和工艺流程。
二、复合材料的设计要点2.1 结构设计:在设计复合材料结构时,需要充分考虑材料的性能和特点,合理设计结构,提高材料的使用效率。
2.2 成型工艺设计:不同的复合材料有不同的成型工艺,需要根据具体的材料性能和工艺流程来设计成型工艺,以保证产品质量。
2.3 自动化设计:现代复合材料加工已经向着自动化方向发展,因此设计时需要考虑如何实现自动化生产。
2.4 环境友好设计:在设计复合材料产品时,需要充分考虑材料的回收性和再利用性,采用环保的材料和工艺。
三、复合材料的成型方法3.1 手工层叠成型:手工层叠成型是一种常见的复合材料成型方法,通过人工将增强纤维层叠在一起,再浸渍树脂,最后经过固化得到成品。
3.2 压模成型:在压模成型中,复合材料预先放置于模具中,然后通过压力和温度的作用,使树脂固化,最终得到成品。
3.3 真空吸塑成型:真空吸塑成型是将复合材料覆盖在模具表面,然后利用真空负压使其贴紧模具表面,并通过加热固化得到成品。
3.4 自动化制备:随着自动化技术的发展,复合材料成型也越来越多地采用自动化制备技术,如自动化层叠机、自动化压模机等。
热压罐成型法简介
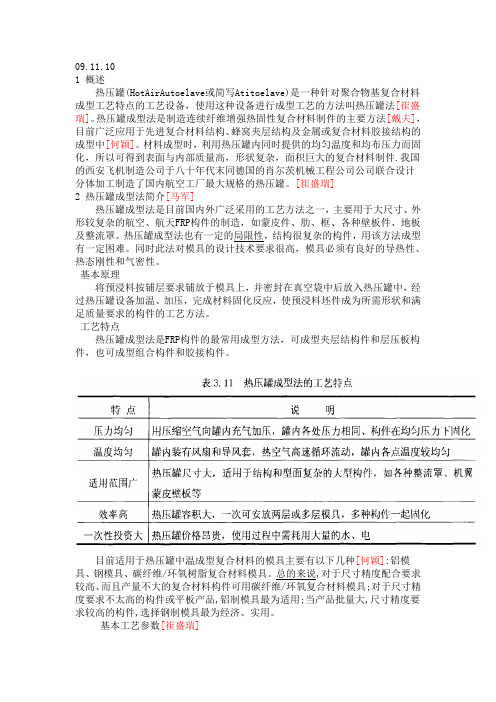
09.11.101 概述热压罐(HotAirAutoelave或简写Atitoelave)是一种针对聚合物基复合材料成型工艺特点的工艺设备,使用这种设备进行成型工艺的方法叫热压罐法[崔盛瑞]。
热压罐成型法是制造连续纤维增强热固性复合材料制件的主要方法[戴夫],目前广泛应用于先进复合材料结构、蜂窝夹层结构及金属或复合材料胶接结构的成型中[何颖]。
材料成型时,利用热压罐内同时提供的均匀温度和均布压力而固化,所以可得到表面与内部质量高,形状复杂,面积巨大的复合材料制件.我国的西安飞机制造公司于八十年代末同德国的肖尔茨机械工程公司公司联合设计分体加工制造了国内航空工厂最大规格的热压罐。
[崔盛瑞]2 热压罐成型法简介[马军]热压罐成型法是目前国内外广泛采用的工艺方法之一,主要用于大尺寸、外形较复杂的航空、航天FRP构件的制造,如蒙皮件、肋、框、各种壁板件、地板及整流罩。
热压罐成型法也有一定的局限性,结构很复杂的构件,用该方法成型有一定困难。
同时此法对模具的设计技术要求很高,模具必须有良好的导热性、热态刚性和气密性。
基本原理将预浸料按铺层要求铺放于模具上,并密封在真空袋中后放入热压罐中,经过热压罐设备加温、加压,完成材料固化反应,使预浸料坯件成为所需形状和满足质量要求的构件的工艺方法。
工艺特点热压罐成型法是FRP构件的最常用成型方法,可成型夹层结构件和层压板构件,也可成型组合构件和胶接构件。
目前适用于热压罐中温成型复合材料的模具主要有以下几种[何颖]:铝模具、钢模具、碳纤维/环氧树脂复合材料模具。
总的来说,对于尺寸精度配合要求较高、而且产量不大的复合材料构件可用碳纤维/环氧复合材料模具;对于尺寸精度要求不太高的构件或平板产品,铝制模具最为适用;当产品批量大,尺寸精度要求较高的构件,选择钢制模具最为经济、实用。
基本工艺参数[崔盛瑞]复合材料基体树脂的固化、除了与树脂的分子结构有关,还与其他组分(固化剂、交联促进剂等)有关.外界条件—温度、压力和时间因素对固化成型起着重要的作用,通常称这三个因素为工艺参数.就目前国内国外树脂体系固化所需压力而言,除聚酸亚胺类外,固化压力一般在的范围内[3].用于复合材料成型工艺的热压罐其使用压力一般小于,属于二类低压容器.从成型工艺的角度来看,基体树脂从线型结构转变成三维网状结构的全部历程可分为三个阶段:流动阶段,凝胶阶段和固化阶段,而且这一过程均是处在一定温度下进行的.根据文献〔3〕,〔6〕报道,国内重要的航空结构用复合材料基体树脂的固化温度最高在180士5℃的范围.将热压罐的最高使用温度设定在250℃是适宜的。
一文看透飞机蒙皮成形术
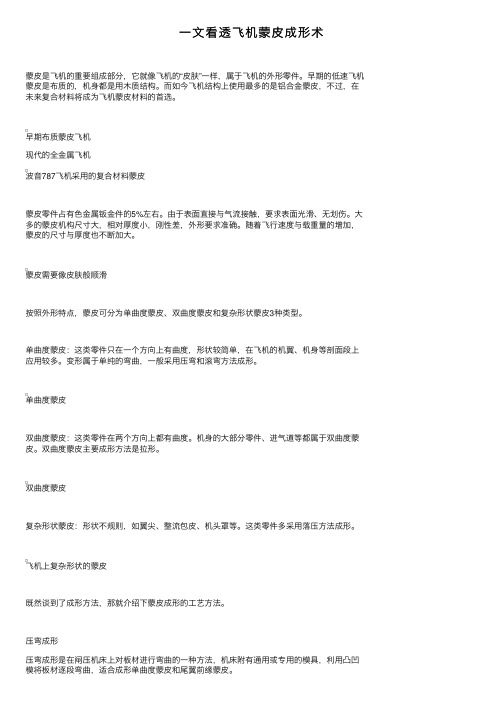
⼀⽂看透飞机蒙⽪成形术蒙⽪是飞机的重要组成部分,它就像飞机的“⽪肤”⼀样,属于飞机的外形零件。
早期的低速飞机蒙⽪是布质的,机⾝都是⽤⽊质结构。
⽽如今飞机结构上使⽤最多的是铝合⾦蒙⽪,不过,在未来复合材料将成为飞机蒙⽪材料的⾸选。
早期布质蒙⽪飞机现代的全⾦属飞机波⾳787飞机采⽤的复合材料蒙⽪蒙⽪零件占有⾊⾦属钣⾦件的5%左右。
由于表⾯直接与⽓流接触,要求表⾯光滑、⽆划伤。
⼤多的蒙⽪机构尺⼨⼤,相对厚度⼩,刚性差,外形要求准确。
随着飞⾏速度与载重量的增加,蒙⽪的尺⼨与厚度也不断加⼤。
蒙⽪需要像⽪肤般顺滑按照外形特点,蒙⽪可分为单曲度蒙⽪、双曲度蒙⽪和复杂形状蒙⽪3种类型。
单曲度蒙⽪:这类零件只在⼀个⽅向上有曲度,形状较简单,在飞机的机翼、机⾝等剖⾯段上应⽤较多。
变形属于单纯的弯曲,⼀般采⽤压弯和滚弯⽅法成形。
单曲度蒙⽪双曲度蒙⽪:这类零件在两个⽅向上都有曲度。
机⾝的⼤部分零件、进⽓道等都属于双曲度蒙⽪。
双曲度蒙⽪主要成形⽅法是拉形。
双曲度蒙⽪复杂形状蒙⽪:形状不规则,如翼尖、整流包⽪、机头罩等。
这类零件多采⽤落压⽅法成形。
飞机上复杂形状的蒙⽪既然谈到了成形⽅法,那就介绍下蒙⽪成形的⼯艺⽅法。
压弯成形压弯成形是在闸压机床上对板材进⾏弯曲的⼀种⽅法,机床附有通⽤或专⽤的模具,利⽤凸凹模将板材逐段弯曲,适合成形单曲度蒙⽪和尾翼前缘蒙⽪。
压弯成形由上下模组成,上模下⾏与下模相互作⽤即可成形。
压弯成形⽰意图以V形件的压弯为例,简要说明下板料压弯时的变形过程。
板料压弯变形过程(1)⾃由弯曲阶段。
板料开始弯曲时,板料与上、下模具为三点接触,随着上模的压下,板料弯曲半径不断减⼩。
(2)接触弯曲阶段。
随着上模的不断压⼒,板料的弯曲变形程度加⼤,其弯曲半径和弯曲⼒臂也在不断减⼩,直到板料与下模完全接触。
(3)矫正弯曲阶段。
上模继续压下,板料的弯曲程度变⼤,此时板料和上模为三点接触,与下模是两点接触,其弯曲⾓度⼩于下模⾓度,这是板料由接触弯曲阶段向矫正弯曲过渡的阶段。
复合材料的成型工艺

复合材料的成型工艺图1:热固性复合材料最基本的制备方法是手糊,通常包括将干层或半固化片层用手铺设到模具上,形成一个积层。
图中展示的是自由宇航公司的技术员(佛罗里达州墨尔本)正在通过手糊工艺加工一个碳/环氧预浸料,将用于制造通用航空飞机部件。
资料来源:自由宇航公司在复合材料的加工成型过程中会使用一系列模具,用来给未成形的树脂及其纤维增强材料提供一个成型的平台。
手糊(hand layup)成型是热固性复合材料最基本的制备方法,即通过人工将干层或半固化片层铺设到模具上,形成一个积层。
铺层方式分为两种:一种称为干法铺层,是先铺层后将树脂浸润(例如,通过树脂渗透方式)到干铺层上的方式,另一种方式是湿法铺层,即先浸润树脂后铺层的顺序。
现在普遍使用的固化方式可以分为以下几种:最基本的是室温固化。
不过,如果提高固化温度的话,固化进程也会相应加快。
比如通过烤箱固化,或使用真空袋(vacuum ba g)通过高压釜固化。
如果采用高压釜固化的话,真空袋内通常会包含透气膜,被放置在经手糊的半成型制品上,再连接到高压釜上,等最终固化完成后再将真空袋撤去。
在固化过程中,真空袋的作用是将产品密封在模具和真空袋之间,通过抽真空对产品均匀加压,将产品中汇总的气体排出,从而使产品更加密实、力学性能更好。
图2:热压釜独有的高温和高压条件使其成为完成热固性树脂零部件的固化的重要工具。
控制软件的改进则能够帮助经营者提高35-40%的生产量。
同时,一些新的树脂配方正在开发当中,将通过低压固化处理。
图中是Helicomb国际公司(俄克拉荷马州塔尔萨)的一名操作人员正在使用高压釜进行固化处理。
来源:Helicomb国际公司许多高性能热固性零件都需要在高热高压的条件下完成固化。
但是高压釜(Autocl aves)的设备成本和操作成本都较昂贵。
采购高压釜设备的制造商通常会一次性固化一定数量的部件。
对于高压釜的温度,压力,真空和惰性气体(inert atmosphere)等一系列参数,计算机系统能帮助实现远程甚至无人监控和检测,并最大限度地提高该技术的利用效率。
航空用热压罐外固化预浸料复合材料的应用

航空用热压罐外固化预浸料复合材料的应用发布时间:2012-10-18 13:06:25目前,航空结构用复合材料主要采用预浸料和热压罐固化工艺制造。
尽管热压罐成型工艺制备的复合材料性能优异、质量稳定可靠,但其高昂的工艺成本一直被人诟病[1],热压罐设备成本比相同容积的烘箱高10~100万英镑。
另外,高压固化增加了芯材塌陷和真空袋破裂的风险;零件尺寸受到热压罐尺寸的限制,不利于大型整体化零件的成型[2]。
因此,热压罐外固化(主要是指烘箱固化)预浸料成型技术应运而生。
热压罐外固化预浸料(Out-of-Autoclave Prepreg),也叫非热压罐固化预浸料(Non-Autoclave Prepreg 或V a c u u m - B a g - O n l y - C u r a b l e Prepregs),最早于20 世纪90 年代提出,此后欧洲和美国投入了大量精力用于研究热压罐外固化预浸料复合材料技术,一些支持项目如:欧洲的CASCADE(Civil Aircraft StructuralComposites Application, Development and Exploitation)、EFFICOMP(LowTemperature Cure Cost Effective C o m p o s i t e M a t e r i a l s f o r A i r c r a f t Structure using Out of Autoclave Processing)、ALCAS(Advanced Low Cost Aircraft Structure)、NGCW(Next Generation Composite Wing)和美国的LCS(Lightweight Composite Structures)[3-4]。
相对于传统的热压罐固化预浸料体系,热压罐外固化预浸料体系在烘箱内即可加热固化,大大节省了设备费用;而且采用烘箱固化时,固化工艺制度简单,只需要控制温度和真空度水平(一般热压罐外固化预浸料固化过程中都采用满真空);烘箱的形状和尺寸更容易按零件大小要求定制,适合大型零件整体化成型。
- 1、下载文档前请自行甄别文档内容的完整性,平台不提供额外的编辑、内容补充、找答案等附加服务。
- 2、"仅部分预览"的文档,不可在线预览部分如存在完整性等问题,可反馈申请退款(可完整预览的文档不适用该条件!)。
- 3、如文档侵犯您的权益,请联系客服反馈,我们会尽快为您处理(人工客服工作时间:9:00-18:30)。
航空复合材料结构件常用的成型方法
航空工业,作为国家科技实力和工业水平的代表,始终在追求更高的性能和更轻的重量。
复合材料,作为一种先进的材料技术,在航空领域的应用日益广泛。
本文将重点探讨航空复合材料结构件常用的成型方法。
一、预浸料成型
预浸料成型是一种常用的复合材料成型方法,它首先将纤维和树脂预先制成片材,然后在一定的温度和压力下将片材压制成所需的形状。
预浸料成型的优点在于其可重复性强,产品质量稳定,适合大规模生产。
二、热压罐成型
热压罐成型是一种利用热压工艺将预浸料或手糊玻璃纤维材料固化成型的工艺。
该方法可以制造出形状复杂、尺寸精度高的复合材料构件。
热压罐成型的优点在于其产品性能优异,但设备成本和维护成本较高。
三、真空袋成型
真空袋成型是一种利用真空负压原理将预浸料或手糊玻璃纤维材料吸附在模具上固化的工艺。
该方法适用于制造大型、平面或曲率较小的复合材料构件。
真空袋成型的优点在于其设备简单、成本低,但产品质量和生产效率相对较低。
四、喷射成型
喷射成型是一种将树脂和纤维同时喷涂在模具表面,通过加热和加压使其固化的工艺。
该方法适用于制造形状复杂、大型且高性能要求的复合材料构件。
喷射成型的优点在于其生产效率高、产品性能优异,但设备成本和维护成本较高。
五、拉挤成型
拉挤成型是一种将纤维浸渍树脂后,在模具中加热加压固化成型的工艺。
该方法适用于制造具有连续纤维增强结构的复合材料构件,如梁、柱等。
拉挤成型的优点在于其产品性能优异、可连续生产,但设备成本和维护成本较高。
六、树脂转移模塑(RTM)
RTM是一种闭模成型工艺,它将纤维增强材料置于闭模的型腔中,然后注入树脂,在一定的温度和压力下固化成型。
RTM的优点在于其产品性能优异、适合制造大型和形状复杂的构件,但设备成本和维护成本较高。
七、纤维缠绕成型
纤维缠绕成型是一种利用纤维缠绕机将纤维连续缠绕在芯轴上的工艺。
该方法适用于制造具有旋转对称性的复合材料构件,如压力容器、管道等。
纤维缠绕成型的优点在于其生产效率高、产品性能优异,但设备成本和维护成本较高。
总结:
航空复合材料结构件的成型方法多样,各有优缺点。
选择合适的成型方法是确保产品质量和生产效率的关键。
随着科技的不断发展,相信未来会有更多高效、低成本的复合材料成型技术出现,推动航空工业的持续发展。