硬质涂层概况资料
材料表面工程硬质合金涂层剖析课件
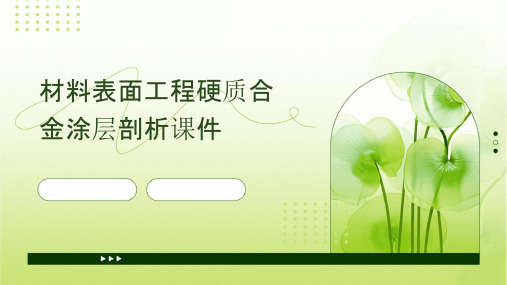
详细描述
通过涂覆硬质合金涂层,可以提高模具表面的硬度,从 而提高模具的抗磨损性能。
模具表面的涂层应用
总结词
提高成型精度
Hale Waihona Puke 详细描述硬质合金涂层具有优异的耐热性和化学稳定性,能够在 高温和高压力条件下保持稳定的成型精度。
机械零件表面的涂层应用
总结词
提高零件耐磨性
详细描述
在机械零件表面涂覆硬质合金涂层,能够显著提高零件的耐磨性,降低磨损率。
溶胶-凝胶法涂层具有高纯度、高致密 性、高结合力等特点,广泛应用于硬 质合金刀具和模具的表面强化。
电镀和电刷镀技术
电镀是通过电解的方法将金属 离子沉积在基体表面形成涂层 的过程。
电刷镀是一种特殊的电镀技术, 通过使用涂敷工具将电镀液涂 敷在基体表面,然后通过电化 学反应形成涂层。
电镀和电刷镀涂层具有高硬度、 高耐磨性等特点,广泛应用于 机械零件的表面强化。
硬质合金涂层能够改善零件表面的应力分布,从而提高零件的疲劳强度。
航空航天领域的涂层应用
总结词
耐高温性能优异
详细描述
硬质合金涂层具有出色的耐高温性能, 能够在高温环境下保持稳定的性能, 适用于航空航天领域的高温环境。
航空航天领域的涂层应用
总结词
抗氧化性能强
详细描述
硬质合金涂层的抗氧化性能强,能够有效抵抗航空航天领域中的高速气流和高温氧化环境。
模具表面的涂层应用
总结词
提高模具寿命
详细描述
在模具表面涂覆硬质合金涂层,能够有效提 高模具的耐磨性和抗咬合性,延长模具使用
寿命。
模具表面的涂层应用
要点一
总结词
降低热传导率
要点二
详细描述
硬质合金涂层用途
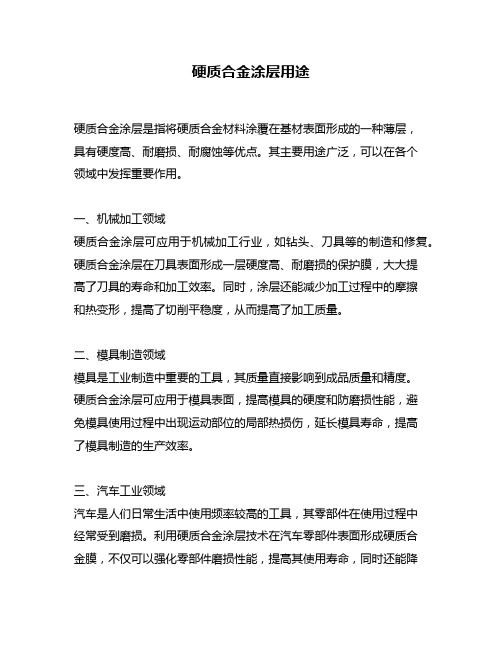
硬质合金涂层用途
硬质合金涂层是指将硬质合金材料涂覆在基材表面形成的一种薄层,
具有硬度高、耐磨损、耐腐蚀等优点。
其主要用途广泛,可以在各个
领域中发挥重要作用。
一、机械加工领域
硬质合金涂层可应用于机械加工行业,如钻头、刀具等的制造和修复。
硬质合金涂层在刀具表面形成一层硬度高、耐磨损的保护膜,大大提
高了刀具的寿命和加工效率。
同时,涂层还能减少加工过程中的摩擦
和热变形,提高了切削平稳度,从而提高了加工质量。
二、模具制造领域
模具是工业制造中重要的工具,其质量直接影响到成品质量和精度。
硬质合金涂层可应用于模具表面,提高模具的硬度和防磨损性能,避
免模具使用过程中出现运动部位的局部热损伤,延长模具寿命,提高
了模具制造的生产效率。
三、汽车工业领域
汽车是人们日常生活中使用频率较高的工具,其零部件在使用过程中
经常受到磨损。
利用硬质合金涂层技术在汽车零部件表面形成硬质合
金膜,不仅可以强化零部件磨损性能,提高其使用寿命,同时还能降
低汽车零部件的能耗和噪音,为汽车工业的发展提供了技术支持。
四、航空航天领域
航空航天工业作为国家高端制造业的代表,涉及到行业科技创新、国防安全以及相关产业的发展。
利用硬质合金涂层技术,可以提高航空发动机叶片、涡轮叶片的耐磨性、抗腐蚀性、高温性和高压力性能,延长其工作寿命,为航空航天产业的发展起到了重要的推动作用。
综上所述,硬质合金涂层在工业制造中具有广泛的应用前景。
未来,随着工业制造技术的不断进步和国家经济的快速发展,硬质合金涂层技术将会得到越来越广泛的应用。
材料表面工程-硬质合金涂层
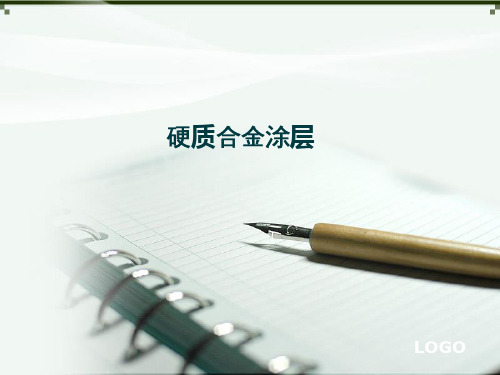
LOGO
目录
定义 涂层工艺 涂层材料 涂层结构 基体 发展
定义及目的
定义:硬质合金涂层是在韧性好的硬质合金 基体上涂覆耐磨性高的硬质涂层。 目的:使刀具能抵抗各种特定的耐磨机理 , 显著提高刀具的功能和刀具的使用寿命 ,并 可大幅度提高刀具的加工效率。
涂层工艺
CVD技术主要用于硬质合 金车削类刀具的表面涂层 ,涂层刀具适用于中到重 型切削的高速粗加工。
涂层工艺
离子镀法
离子镀(IP)法是 采用离子和具有 能量的中性原子 轰击溅射净化后 的基体(沉积前) 并在沉积过程中 控制涂层成核和 生长过程。
涂层工艺
溅射法
溅射法是在高真 空充入适量的氩 气,氩气发生电 离,氩离子被阴 极加速并轰击阴 极靶表面,将靶 材表面原子溅射 出来沉积在基底 表面上形成薄膜 。
涂层材料
涂层结构
单层及多元涂层 多层涂层
梯度涂层
涂层结构
多层涂层金相结构图
TiN-TiCN-TiN-Al2O3-TiN
涂层基体
发展
(1)涂层工艺温度越来越低, 尽量减少了涂层过程中产生的应 力集中。 (2)为满足不同的切削加工需求, 涂层成分更加复杂、更有针 对性。 (3)复合涂层中各单一成分涂层的厚度越来越薄, 并逐步趋于 纳米化。 (4)涂层硬质合金刀具将采用复合表面处理技术, 实现成分、 组织结构的梯度过渡, 获得性能更好的涂层组织以及更高界 面结合强度的产品。
PVD技术适用于硬质合金 精密复杂刀具的涂层处理 。
涂层工艺
工艺过程
汽化
物理气相沉积
相互间反应
涂层材料
原子,分子,离子
迁移
吸附 堆集 形核 长大
超硬材料涂层

超硬材料涂层1.金刚石、类金刚石(DLC)涂层金刚石涂层是新型刀具涂层材料之一。
它利用低压化学气相沉积技术在硬质合金基体上生长出一层由多晶构成的金刚石膜,用其加工硅铝合金和铜合金等有色金属、玻璃纤维等工程材料及硬质合金等材料,刀具寿命是一般硬质合金刀具的50~100倍。
金刚石涂层采纳了很多金刚石合成技术,最一般的是热丝法、微波等离子法和DC等离子喷射法。
通过改进涂层方法和涂层的粘结,已生产出金刚石涂层刀具,并在工业上得到了应用。
近年来,美国、日本和瑞典等国家都已相继推出了金刚石涂层的丝锥、铰刀、铣刀以及用于加工印刷线路板上的小孔金刚石涂层硬质合金钻头及各种可转位刀片,如瑞典Sandvik公司的CD1810和美国Kennametal公司的KCD25等牌号产品。
美国Turchan公司开发的一种激光等离子体沉积金刚石的新工艺,用此法沉积金刚石,由于等离子场包围整个刀具,刀具上的涂层均匀,其沉积速度比常规CVD法快1000倍。
此法所成的金刚石涂层与基体之间产生真正的冶金结合,涂层强度高,可防止涂层脱落、龟裂和裂纹等缺陷。
CemeCon公司具有特色的CVD金刚石涂层技术,2000年建立生产线,使金刚石涂层技术达到工业化生产水平,其技术含量高,可以批量生产金刚石涂层。
类金刚石涂层在对某些材料(Al、Ti及其复合材料)的机械加工方面具有明显优势。
通过低压气相沉积的类金刚石涂层,其微观结构与天然金刚石相比仍有较大差异。
九十时代,常采纳激活氢存在下的低压气相沉积DLC,涂层中含有大量氢。
含氢过多将降低涂层的结合力和硬度,增大内应力。
DLC中的氢在较高的温度下会渐渐释放出来,引起涂层工作不稳定。
不含氢的DLC硬度比含氢的DLC高,具有组织均匀、可大面积沉积、成本低、表面平整等优点,已成为近年来DLC涂层讨论的热点。
美国科学家A.A.Voevodin提出沉积超硬DLC涂层的结构设计为Ti—TiC—DLC梯度变化涂层,使硬度由较软的钢基体渐渐提高到表层超硬的DLC涂层。
硬质涂层概况方法培训
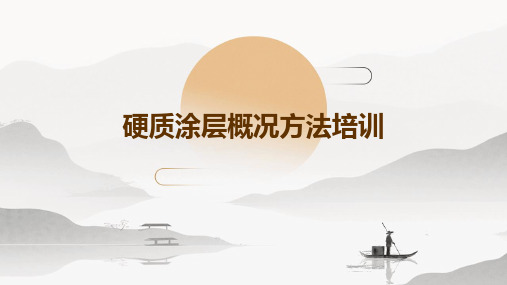
物理气相沉积法通过将气态物质在基材表面进行物理吸附和反应,形成固态沉积物,形成涂层。该方 法制备的涂层具有高纯度、高致密、高结合力等优点,广泛应用于光学、电子、薄膜等领域。
热喷涂法
总结词
热喷涂法是一种利用热源将喷涂材料熔化或软化后喷射到基材表面形成涂层的制备方法。
详细描述
热喷涂法通过将喷涂材料加热至熔化或软化状态,然后以高速气流将熔融或软化的材料喷射到基材表面,形成涂 层。该方法具有涂层厚度可调、工艺灵活、适应性广等优点,广泛应用于防腐、耐磨、耐高温等领域。
汽车工业领域的应用
硬质涂层在汽车工业中主要用于保护汽车表面免受腐蚀、划痕和磨损等影响,提高 汽车的美观度和使用寿命。
硬质涂层具有高硬度、高耐磨性和高耐腐蚀性等特点,能够提高汽车的抗划痕和抗 冲击能力。
硬质涂层在汽车发动机、车身、车轮等部位广泛应用,能够提高汽车的耐久性和可 靠性。
建筑行业领域的应用
硬质涂层概况方法培训
目录
• 硬质涂层简介 • 硬质涂层的应用 • 硬质涂层的制备方法 • 硬质涂层性能的检测与评价 • 硬质涂层的发展趋势与展望 • 培训总结与展望
01
硬质涂层简介
硬质涂层的定义
01
硬质涂层是一种特殊类型的涂层 ,通过在基材表面涂覆一层硬度 较高的材料,以提高表面的耐磨 、耐腐蚀、耐高温等性能。
功能化涂层
通过在涂层中添加特殊元素或化合物,赋予涂层 特殊的功能,如抗菌、防辐射和自修复等。
06
培训总结与展望
培训内容的回顾与总结
硬质涂层定义
01
硬质涂层是一种具有高硬度、高耐磨性、高耐腐蚀性的表面涂
层,广泛应用于机械、航空、化工等领域。
硬质涂层制备方法
加硬涂层原理 -回复
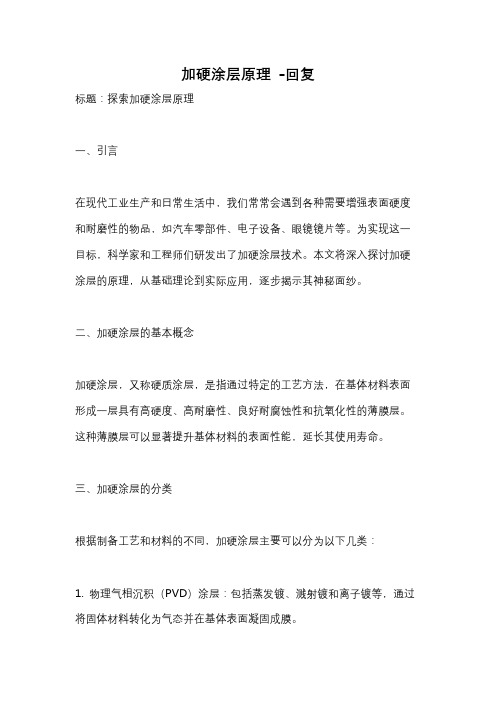
加硬涂层原理-回复标题:探索加硬涂层原理一、引言在现代工业生产和日常生活中,我们常常会遇到各种需要增强表面硬度和耐磨性的物品,如汽车零部件、电子设备、眼镜镜片等。
为实现这一目标,科学家和工程师们研发出了加硬涂层技术。
本文将深入探讨加硬涂层的原理,从基础理论到实际应用,逐步揭示其神秘面纱。
二、加硬涂层的基本概念加硬涂层,又称硬质涂层,是指通过特定的工艺方法,在基体材料表面形成一层具有高硬度、高耐磨性、良好耐腐蚀性和抗氧化性的薄膜层。
这种薄膜层可以显著提升基体材料的表面性能,延长其使用寿命。
三、加硬涂层的分类根据制备工艺和材料的不同,加硬涂层主要可以分为以下几类:1. 物理气相沉积(PVD)涂层:包括蒸发镀、溅射镀和离子镀等,通过将固体材料转化为气态并在基体表面凝固成膜。
2. 化学气相沉积(CVD)涂层:通过化学反应在基体表面生成固体物质并沉积成膜。
3. 涂料涂覆:利用涂料中的树脂、颜填料等成分在基体表面形成硬化膜。
4. 电镀和化学转化膜:通过电解或化学反应在基体表面生成金属或非金属膜。
四、加硬涂层的原理1. 物理气相沉积(PVD)涂层原理在PVD过程中,首先将固体材料加热至蒸发或溅射状态,形成气态原子或分子。
这些气态粒子在真空环境中运动,并在基体表面碰撞、吸附和凝聚,最终形成均匀、致密的薄膜层。
2. 化学气相沉积(CVD)涂层原理在CVD过程中,首先将含有沉积元素的气体引入反应室中,与基体表面发生化学反应。
反应产物在基体表面析出并沉积,逐渐形成硬质涂层。
3. 涂料涂覆原理涂料涂覆是通过将含有树脂、颜填料、固化剂等成分的液体涂料均匀涂布在基体表面,然后经过干燥或固化过程,形成坚硬、耐磨的涂层。
4. 电镀和化学转化膜原理电镀是通过电解作用使金属离子在基体表面还原沉积,形成金属膜。
化学转化膜则是通过化学反应使基体表面生成一层氧化物、磷酸盐或其他化合物膜。
五、加硬涂层的应用加硬涂层技术广泛应用于各个领域,包括:1. 切削刀具和模具:通过在刀具和模具表面添加硬质涂层,可以提高其耐磨性和抗粘附性,延长使用寿命。
hardcoat层化学物质
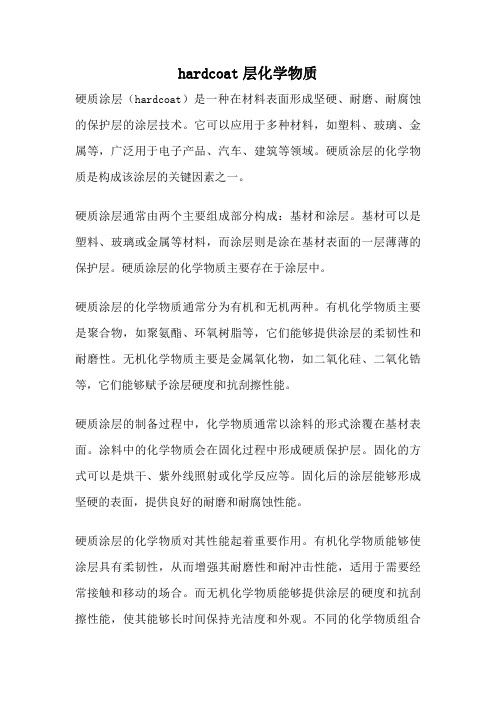
hardcoat层化学物质硬质涂层(hardcoat)是一种在材料表面形成坚硬、耐磨、耐腐蚀的保护层的涂层技术。
它可以应用于多种材料,如塑料、玻璃、金属等,广泛用于电子产品、汽车、建筑等领域。
硬质涂层的化学物质是构成该涂层的关键因素之一。
硬质涂层通常由两个主要组成部分构成:基材和涂层。
基材可以是塑料、玻璃或金属等材料,而涂层则是涂在基材表面的一层薄薄的保护层。
硬质涂层的化学物质主要存在于涂层中。
硬质涂层的化学物质通常分为有机和无机两种。
有机化学物质主要是聚合物,如聚氨酯、环氧树脂等,它们能够提供涂层的柔韧性和耐磨性。
无机化学物质主要是金属氧化物,如二氧化硅、二氧化锆等,它们能够赋予涂层硬度和抗刮擦性能。
硬质涂层的制备过程中,化学物质通常以涂料的形式涂覆在基材表面。
涂料中的化学物质会在固化过程中形成硬质保护层。
固化的方式可以是烘干、紫外线照射或化学反应等。
固化后的涂层能够形成坚硬的表面,提供良好的耐磨和耐腐蚀性能。
硬质涂层的化学物质对其性能起着重要作用。
有机化学物质能够使涂层具有柔韧性,从而增强其耐磨性和耐冲击性能,适用于需要经常接触和移动的场合。
而无机化学物质能够提供涂层的硬度和抗刮擦性能,使其能够长时间保持光洁度和外观。
不同的化学物质组合可以调整涂层的性能,以满足不同领域和应用的需求。
硬质涂层的化学物质还可以通过添加功能性材料来改善其性能。
例如,添加纳米颗粒可以增强涂层的硬度和耐磨性,提高其表面光洁度和耐刮擦性能。
添加抗菌剂可以使涂层具有抗菌和抗污染功能,适用于医疗和食品行业的应用。
通过调整化学物质的比例和添加其他材料,可以实现硬质涂层的多种功能。
硬质涂层是一种在材料表面形成坚硬、耐磨、耐腐蚀的保护层的涂层技术。
其化学物质是构成该涂层的关键因素之一,有机物质赋予涂层柔韧性,无机物质赋予涂层硬度和抗刮擦性能。
通过调整化学物质的比例和添加功能性材料,可以实现硬质涂层的多种功能。
硬质涂层的应用范围广泛,可以提供材料表面的保护和改善其性能,满足不同领域和应用的需求。
硬质镀膜涂层
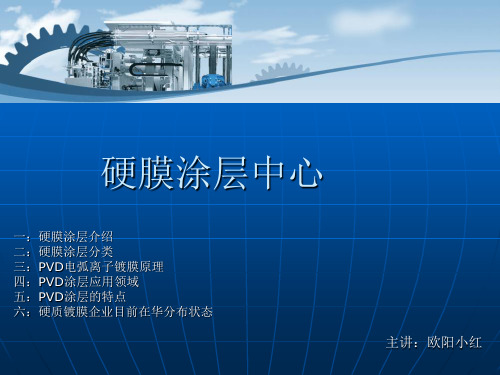
PVD电弧离子镀膜原理 PVD电弧离子镀膜原理 PVD电弧离子镀膜原理是指在真空条件下,采用 PVD电弧离子镀膜原理是指在真空条件下,采用 低电压、大电流的电弧放电技术,利用气体放电 使靶材蒸发并使被蒸发物质与气体都发生电离, 利用电场的加速作用,使被蒸发物质及其反应产 物沉积在工件上。
PVD涂层应用领域 PVD涂层应用领域 机械切削刀具 各类模具 零部件 医疗器械 其他应用
PVD镀膜指利用物理过程实现物质转移,将原子或分子 PVD镀膜指利用物理过程实现物质转移,将原子或分子 由源转移到基材表面上的过程。它的作用是可以是某些 有特殊性能(强度高、耐磨性、散热性、耐腐性等)的 离子沉积在性能较低的母体上,使得母体具有更好的性 能! PVD基本方法:真空蒸发、溅射 、离子镀(空心 PVD基本方法:真空蒸发、溅射 阴极离子镀、热阴极离子镀、电弧离子镀、活性反应离 子镀、射频离子镀、直流放电离子镀)目前在硬质镀膜 子镀、射频离子镀、直流放电离子镀)目前在硬质镀膜 使用较多的是电弧离子镀
PVD涂层的特点 PVD涂层的特点 高硬度 低摩擦系数 很好的耐磨性 化学稳定性等优点
硬质镀膜企业目前在华分布状态 长三角地区(10家) 长三角地区(10家) 珠三角地区(8 珠三角地区(8家) 成都, 汉中,沈阳,天津各有一家
硬膜涂层中心
一:硬膜涂层介绍 二:硬膜涂层分类 三:PVD电弧离子镀膜原理 三:PVD电弧离子镀膜原理 四:PVD涂层应用领域 四:PVD涂层应用领域 五:PVD涂层的特点 五:PVD涂层的特点 六:硬质镀膜企业目前在华分布状态
主讲:欧阳小红
一:硬膜涂层介绍
硬膜涂层技术是一项优质表面改性技术,它将基 体与硬质薄膜表层相结合,使基体保持良好韧性 和较高强度,硬质薄膜表层具有高耐磨性和低摩 擦系数,从而使被镀膜体的性能大大提高。广泛 应用于机械加工等行业!
- 1、下载文档前请自行甄别文档内容的完整性,平台不提供额外的编辑、内容补充、找答案等附加服务。
- 2、"仅部分预览"的文档,不可在线预览部分如存在完整性等问题,可反馈申请退款(可完整预览的文档不适用该条件!)。
- 3、如文档侵犯您的权益,请联系客服反馈,我们会尽快为您处理(人工客服工作时间:9:00-18:30)。
电化学沉积(电镀)与化学镀
电镀 化学镀
电镀
化学镀
➢需要基体导电
➢不需要基体导电
➢受电力线变化影响,均匀性和致密度差 ➢镀层均匀,致密,抗腐蚀性更好
➢仿形性差
➢仿形性好,可对复杂部件施镀
➢可沉积材料相对较少
➢除Pb、Cd、Sn、Bi,大多数金属可沉积
➢成本相对低
➢成本相对更高
➢沉积速度相对较快
➢沉积速度相对较慢
性能 ▪ 硬度2200 Hv-2700Hv ▪ 摩擦系数 0.4 - 0.9 ▪ 最高使用温度 800℃(>TiN500℃) ▪ 沉积温度300 ℃
TiAlN
TiAlN涂层性能
TiAlN是目前高 速干式切削刀 具最常用的涂
层
TiAlN切削性能
TiN中Al的加入提 高了TiN硬度和抗 氧化能力是TiAlN 性能优于TiN的主
围窄 涂层应力大,膜基结合能力差 适用于加工有色金属,木材等不含铁成分的材
• 涂层的沉积技术与沉积条件严重影 响涂层性能
氮化物涂层
氮化钛TiN
▪ 研究应用最多的氮化物涂层
氮Байду номын сангаас铪HfN
▪ 相对氮化钛和碳化钛,提高温度能保持较高硬度
立方氮化硼 c-BN(4000Hv)
▪ 曾是金刚石之后发现最硬的材料之一 ▪ 需高温沉积,成本高
与碳化物相比,氮化物具有良好的韧性 涂层沉积技术与沉积条件严重影响涂层性能
▪ 真空蒸镀(Evaporation Deposition) ▪ 离子镀(Ion Plating) ▪ 溅射沉积(Sputtering)
直流溅射
溅射电源为直流电源,只适用金属和半导 体材料溅射
射频溅射
溅射电源为射频电源,可溅射导体、半 导体和绝缘体材料
磁控溅射
靶材背后安置强磁体,增强气体电离和电 子对基体轰击可实现低温高速沉积
碳化物涂层
碳化钛Ti-C (1000Hv-2800Hv) 应用最广的碳化物涂层 碳化钨 W-C(800-2100Hv) 在高温条件下能保持良好的硬度 碳化铬Cr-C 具有碳化钛、碳化钨更强的抗氧化性。 碳化硅SiC 高硬度,高温抗氧化性,抗腐蚀性
• 与氧化物相比具有更高的硬度
• 脆性增加
氮化钛涂层应用
性能
❖ 金黄色 ❖ 硬度 2200Hv ❖ 摩擦系数0.4-0.6 ❖ 磨损率 10-17 m3/Nm
TiN模具
涂层成分正向多样化趋势发展
多元氮化物
TiAlN TiZrN TiHfN TiAlVN TiAlZrN
二元、三元氮化物可明显提高一元氮化 物(如氮化钛)的性能
TiAlN涂层
金属基合金涂层
铁基 铬基 镍层 钼层 钴基和镍基合金涂
层 其他合金涂层
陶瓷涂层
氧化涂层
– 氧化铝/氧化钽/氧化铬
碳化物涂层
– 碳化钛/碳化钨/碳化铬 – 碳化铪/碳化锆/碳化硅
氮化物涂层
– 氮化钛 – 氮化铪/氮化锆/氮化硅 – 立方氮化硼(CBN)/多元
氮化物
硼化物 硅化物 硬质碳层
– 非晶碳层/金刚石涂层
金属基合金涂层硬度值 (<1500Hv)不是很高,不能完 全满足硬质涂层应用的需要!
陶瓷涂层的应用成为研究热点
陶瓷涂层的应用
Al2O3涂层
高硬度(750-2100Hv) 高熔点 化学性质稳定 热不良导体,阻止摩擦热向
基体扩散 抗腐蚀,抗磨损的理想材料 主要沉积技术:CVD 主要应用 刀具等
缺点
适用于加工有色金属,木材等不含铁 成分的材料
使用温度低<450℃,涂层应力大
PureDLCcoating
DLC Slidingparts,molds,inserts
DLC切割刀片
硬碳层
金刚石涂层 优点 具有很高的硬度,耐磨性能,摩擦系数低 缺点 采用CVD沉积技术,沉积温度高,基底材料范
要原因
TiAlN涂层性能
TiAlN钻孔试验
TiAlN涂层应用
noncoating
TiN
TiAlN.
Typical photographs of tool wear according to coating type in the case of cutting speed 200 m/min and feed per tooth 0.03 mm/rev; (a) noncoating; (b) TiN; (c) TiAlN.
TiAlN挤型模
TiN/TiAlN 钻头
(4)硬碳涂层
非晶碳层/类金刚石层(DLC) 兼有石墨和金刚石性能,优异的固体润滑 硬膜
金刚石(sp3),石墨(sp2) DLC (sp3+ sp2) 金刚石硬度100Gpa DLC硬度7.4-60Gpa
优点
摩擦系数小0.1, 沉积温度低可 <200℃
溅射沉积特点
溅射出粒子平均能量比真空蒸镀产生 的粒子大,薄膜与基体结合性好 膜厚较真空蒸镀均匀,材料的溅射特 性差别不如其蒸发特性差别大,易控制 成分 任何材料(导电体、绝缘体、有机、 无机)均能溅射成膜 磁控溅射沉积技术是应用最广泛的气相 沉积技术!磁控溅射仪可以称为万能镀 膜机。
硬质涂层的分类
– 沉积温度600℃-1200℃ – 基底适用范围(硬质合金\陶瓷部件) – 热变形大,应用于非精密部件
反应气体会污染环境
PVD与CVD的 区别导致不同 领域的应用
物理气相沉积(PVD)优点:
▪ 沉积温度低,应用范围广 ▪ 热变形小,可应用于精密部件(刀具、模
具) ▪ 没有废气排放,绿色环保
物理气相沉积(PVD)类型
精密冲压加工品的电镀 Ni
化学镀 Ni-P
电镀与化学镀的局限性:
沉积的硬质材料有限(Cr,Ni,Ni-P…) 沉积的硬质材料硬度一般偏小
(<1500Hv) 复合沉积的复合均匀性较差,不能应用于
精密部件
化学气相沉积(CVD)特点
最先使用的气相沉积技术 优点 沉积温度高,结合力比物理气相沉积强 缺点 沉积温度过高限制基底的适用范围
硬质涂层发展概况
江苏大学 邵红红
一、硬质涂层沉积技术
印刷用滚筒等离子陶瓷热喷涂(耐磨损) 等离子陶瓷热喷涂泵部件(耐磨损)
电极轴(铜)隔离部等离子陶瓷热喷涂 拉线机械用引导滚筒等离子陶瓷热喷涂
(耐磨损)
(耐磨损)
热喷涂存在的问题:
涂层厚,均匀性相对其他沉积方法差,难以 应用于精密部件 喷涂材料受限制,必须在熔融条件下不发 生分解、蒸发、升华、离解 沉积表面需要机械或化学粗化,基体不能 太薄