玻璃钢船工艺流程样本
玻璃钢船艇模具制作工艺流程

欢迎阅读玻璃钢船艇模具制作工艺流程二、防潮层,批嵌腻子,喷易打磨胶衣1、糊防潮层:在木模表面上糊2层400g玻璃纤维布,用于加固木模强度,防止模具表面变形及防潮。
在玻璃钢固化后,再进行表面外理(如棱角、毛刺、重叠等)。
2、在胎膜上批嵌原子灰:在原子灰中加入适量固化剂,一般每桶原子灰在20℃的条件下,加入固化剂用量为2%,然后搅拌均匀,涂抹在胎膜上,用软管或挎尺照模型形状,将其挎圆顺,光滑。
反复按以上顺序操作,直至胎膜达到理想形状。
3、喷易打磨胶衣:打磨完成后,将胎膜表面灰尘、杂物清理干净后,将易打磨胶衣(产品胶衣可替代)均匀地喷涂在胎膜表面。
a)定)。
b)c)41光为止(2、抛光:用1号研磨剂均匀涂在胎模表面,用羊毛抛盘进行抛光,杜绝漏抛,1号研磨剂结束后再使用3号研磨剂,进行抛光清理干净。
3、脱模蜡处理:通常使用固体蜡和液体蜡两种。
a)固体蜡(8号蜡)一般以回旋法的方式用海绵擦拭,为了防止表面残留的蜡液引起厚度的增加,我们在上完第一层蜡以后通常要等半小时左右,使蜡完全渗透里层后,再用干净的线头擦去多余的蜡液,然后再上第二遍。
固体蜡在使用过程中擦的次数较多,一般15~16遍左右。
b)液体蜡(水蜡)一般以回旋法的方式用线头擦拭,它形成蜡模的时间较短,价格较昂贵,可以连续擦拭,液体蜡通常只需3~4次即可。
3、抛光:一般分别使用1号蜡、3号蜡进行两次抛光。
模型擦拭干净,将干净的4完毕后12、胶衣喷完后1-3小时,等胶衣固化后,表面基本不粘手或12小时之内进行首层铺层。
3、将调配好的树脂液涂刷到模具胶衣,随即铺一层短切毡(一般第一层不用纤维布;防止在模具表面上留下布印痕)。
用刷子、滚筒工具仔细滚压,排出气泡。
玻璃纤维是以GC-M-M-R-M-R-M……(GC表示胶衣,M表示短切毡,R表示玻璃纤维布)的积累方法进行逐层糊制的。
4、糊制过程中,要严格控制每层树脂胶液的用量,既要充分浸润纤维,又不能过多。
含胶量高,气泡不易排除,而且造成固化防热大,收缩率大,一般规定玻璃纤维短切毡的成型胶量为65%-70%,方格布为50%-55%。
【政务民生】玻璃钢游船生产流程

玻璃钢游船生产流程1️⃣ 初步设计与规划玻璃钢游船的生产始于详尽的设计与规划阶段。
这一阶段,设计师们会依据客户需求、使用环境及安全规范,运用CAD(计算机辅助设计)软件进行游船的三维建模与结构设计。
设计过程中,需综合考虑游船的外观美学、航行性能、载重能力以及乘客舒适度等多个维度。
完成初步设计后,还需进行多次评审与优化,确保设计方案既满足客户需求又符合行业标准。
2️⃣ 模具制作与准备设计定稿后,进入模具制作环节。
模具是玻璃钢游船成型的基础,其精度与质量直接影响最终产品的外观与性能。
模具制作包括材料选择、加工成型、表面处理等多个步骤,要求极高的工艺水平。
同时,为确保模具与后续玻璃钢层合工艺的兼容性,还需对模具进行预处理,如涂覆脱模剂等,以便在层合完成后轻松脱模。
3️⃣ 玻璃钢层合与固化玻璃钢(也称玻璃纤维增强塑料)是由玻璃纤维与树脂基体复合而成的高性能材料,具有质轻、强度高、耐腐蚀等优点,是制造游船的理想材料。
层合过程是将预先裁剪好的玻璃纤维布或毡,按设计要求逐层铺设在模具内,并逐层涂刷树脂,通过手工或机械方式压实,形成连续的玻璃纤维增强结构。
层合完成后,需进行固化处理,即在特定温度与压力下,使树脂基体充分交联固化,形成坚固的玻璃钢船体。
固化过程需严格控制时间与温度,以保证船体的强度与稳定性。
4️⃣ 细节加工与装配固化后的玻璃钢船体需进行细节加工,包括切割多余材料、打磨表面、钻孔安装设备等。
此阶段还需进行船体内部结构的搭建与加固,如安装甲板、舱壁、座椅等。
所有部件均需经过精密测量与调试,确保装配精度与功能性。
此外,根据游船的功能需求,还可能涉及电气系统、导航设备、消防设施的安装与调试。
5️⃣ 质量检验与试航生产流程的最后阶段是对玻璃钢游船进行全面质量检验。
这包括外观检查、尺寸测量、结构强度测试、水密性测试等多个方面,确保游船符合设计要求与安全标准。
完成质量检验后,游船将进行试航测试,以验证其在真实水域中的航行性能、操控性及乘客舒适度。
玻璃钢船体制作原料和制作工艺流程

玻璃钢船体制作原料和制作工艺流程做玻璃钢船,例子:捕鱼的的玻璃钢小船,3米长,一米宽,40CM高的来算吧,一体成形的。
材料你需要准备的如下:1.树脂191A类型的,(20公斤,单价是13元左右/公斤)胶衣树脂2公斤,配套钴水和固化剂各1公斤2.玻璃纤维,分玻璃纤维毡和玻璃纤维布,(一共要毡就5-10公斤,12元左右/公斤,玻璃布10-20个平方吧,1.5元左右/公斤)3.脱模蜡(一盒,大概50块左右)和原子灰(40左右一桶2.5公斤重),滑石粉一袋(1000目以上的,一袋大概20左右)4.木方,木板,铁丝,铁钉(有空气压缩机和钉枪就用钉枪)剪刀一把,砂纸从60-200目的准备各10张,水磨砂纸从400-800-1000的各不少于10张,木工曲线锯和配套木工锯条一板,角向打磨机1把(就是电磨),磨机砂片几片(进口的十几块一片,不容易炸片的,安全点)5.塑料瓢,毛刷1寸到3寸的各几把6.船体其它附加五金设备建议用不锈钢,材料多少就自己计算着办以上做法是按做一条船来算的,所以没有考虑模具树脂,都用191A的树脂来做吧,具体做法是先设计船的草图和尺寸---用木板木方按图纸做出船的外轮廓木质模型,模型做成阴模,船体部件做法一样,也就是里面空的,用滑石粉混合树脂补缝,用砂纸打磨平滑,因为这就是模具了,做一条船就不用再翻制树脂模型了,之后就把这个当船体的模具来用就行,有部件的就调好尺寸最后合模吧---调好尺寸,打磨光滑后的木模用原子灰很薄地刮一层并用粗砂纸和水磨砂纸打磨平整光滑并涂抹上脱模蜡,脱模蜡多打几遍,抹光滑之后---刷上胶衣树脂,干后铺上纤维毡并刷上树脂---再干后就裁好玻璃纤维布铺上并刷好树脂,做到3层毡2层布就够结实牢固了,然后把配件按同样的方法做出来,用磨机打磨好边合模用,合模用纤维切碎混合滑石粉和树脂,干后打磨好,喷上漆即可,。
玻璃钢船制作工艺

玻璃钢船制作工艺玻璃钢船艇是玻璃钢产品中的主要种类,由于船艇尺寸较大,弧面多,玻璃钢手糊成型工艺能一体成型,很好地完成船艇的建造。
关键词:玻璃钢船艇;模具设计;工艺设计由于玻璃钢质轻,耐腐蚀,可整体成型等优点,十分适合建造船艇,因而在开发玻璃钢产品时,往往把船艇作为首选目标。
按用途分,玻璃钢船艇主要有以下几类:(1)游乐船。
用于公园水面及水上旅游景点。
小型的有手划船、脚踏船、电瓶船、碰碰船等;供众多游客集体游览用的有大中型游览观光及富有古建筑情趣的画舫船等,此外还有高档次的家用游艇。
(2)快艇。
用于水上公安航行执法及水面管理等部门巡逻执勤,也作为快速客运及水上带刺激性的游乐之用。
(3)救生艇。
作江、海航行的大中型客货运输及海上石油钻井平台必须配备的救生设备。
(4)渔业用船。
用于捕鱼、养殖及运输等。
(5)军用艇。
用于军事用途,例如扫雷艇,就十分适合用无磁性的玻璃钢建造。
(6)运动艇。
用于运动及体育比赛帆板、赛艇、龙舟等。
由于我国江河湖泊众多,海岸线长,海域辽阔,玻璃钢船艇有广阔的发展前景。
生产玻璃钢船艇较一般玻璃钢产品繁琐,由于是涉及到人身及财产安全的交通、游乐工具,因此生产企业必须具有工商行政管理部门颁发的营业执照,且要获得地方船舶检验部门对生产条件的检查及认可,也就是说必须具有相关生产资质才能投产。
当完成船艇产品设计工作后,由玻璃钢专业技术人员进行模具设计及船艇建造工艺设计。
模具设计首先根据船艇生产数量确定模具性:如生产批量较多,可制作经久耐用的玻璃钢模具。
在设计模具时,须根据船型复杂程度及脱模需要将模具设计成整体式或组合式,并根据搬移需要设置滚轮。
根据船艇尺度大小和刚度需要定出模具厚度及加强筋用材、断面尺寸。
最后编写出模具建造工艺文件。
在模具用材上,玻璃钢模具应考虑到脱模敲击及反复经受制品固化时的放热量等因素。
选用既有一定韧性又能耐热的树脂品种,如专用的模具树脂、模具胶衣等。
船艇建造工艺设计包括以下内容:(1)根据船艇使用性能及防老化性能等要求选择适宜的合成树脂及增强材料品种、牌号、规格,并根据壳板厚度作出相应的铺层设计。
玻璃钢小船制作方法

玻璃钢小船制作方法
制作玻璃钢小船通常包括以下步骤:
1. 准备工作:确定小船的设计和尺寸,准备制作模具、材料和工具。
2. 制作模具:按照小船的设计,制作木质或金属模具,包括船身、船底和船面等部分。
3. 准备材料:准备玻璃纤维布和环氧树脂等玻璃钢制作材料。
4. 制作船体:将玻璃纤维布剪成适当尺寸,涂抹一层环氧树脂在模具表面,然后将玻璃纤维布铺在上面,再涂抹一层环氧树脂。
逐渐叠加多层,形成船体的厚度和强度。
注意避免气泡的产生,使玻璃钢均匀贴合在模具表面。
5. 固化和翻转:等待环氧树脂固化,然后将整个船体翻转过来,处理船底和船面等其他部分。
6. 完善细节:修整船体边缘,添加支撑和加强部件,如船舱、船床和船桨架等。
7. 粘接和打磨:使用玻璃纤维布和环氧树脂粘接各个零部件,然后使用打磨工具将船体表面打磨平整。
8. 上漆:涂抹防水涂层和船底漆,以保护船体和提高外观。
9. 完成:安装船桨、操纵杆和其他附件,进行必要的检查和测试,并保养船体以保持其良好状态。
需要注意的是,制作玻璃钢小船需要专业知识和技能,建议找到专业的船舶制造公司或有经验的制作人员进行操作。
玻璃钢船工艺流程
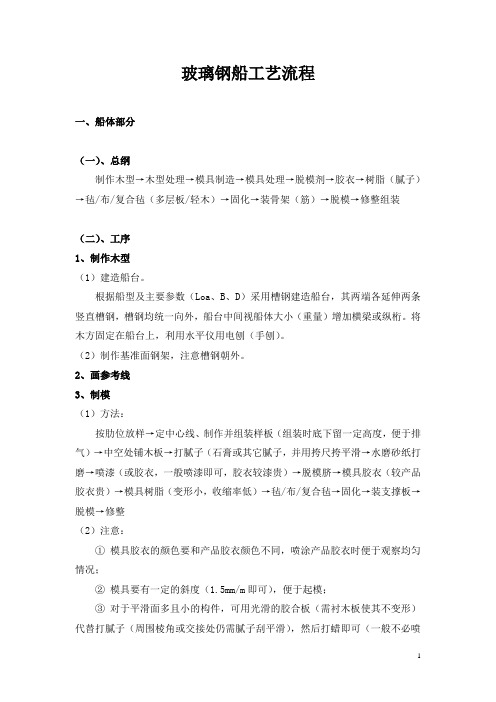
玻璃钢船工艺流程一、船体部分(一)、总纲制作木型→木型处理→模具制造→模具处理→脱模剂→胶衣→树脂(腻子)→毡/布/复合毡(多层板/轻木)→固化→装骨架(筋)→脱模→修整组装(二)、工序1、制作木型(1)建造船台。
根据船型及主要参数(Loa、B、D)采用槽钢建造船台,其两端各延伸两条竖直槽钢,槽钢均统一向外,船台中间视船体大小(重量)增加横梁或纵桁。
将木方固定在船台上,利用水平仪用电刨(手刨)。
(2)制作基准面钢架,注意槽钢朝外。
2、画参考线3、制模(1)方法:按肋位放样→定中心线、制作并组装样板(组装时底下留一定高度,便于排气)→中空处铺木板→打腻子(石膏或其它腻子,并用挎尺挎平滑→水磨砂纸打磨→喷漆(或胶衣,一般喷漆即可,胶衣较漆贵)→脱模脐→模具胶衣(较产品胶衣贵)→模具树脂(变形小,收缩率低)→毡/布/复合毡→固化→装支撑板→脱模→修整(2)注意:①模具胶衣的颜色要和产品胶衣颜色不同,喷涂产品胶衣时便于观察均匀情况;②模具要有一定的斜度(1.5mm/m即可),便于起模;③对于平滑面多且小的构件,可用光滑的胶合板(需衬木板使其不变形)代替打腻子(周围棱角或交接处仍需腻子刮平滑),然后打蜡即可(一般不必喷漆,但打腻子处如精度需要仍需喷漆);④支撑板要交叉组装,并用毡/布/复合毡等固定。
同时在与船体固定及支撑地面的部分做相应加强;⑤制模后要打抛光膏使模具质量更好。
4、脱模剂一次蜡即地板蜡(大量)+一次脱模剂适用于新模具,多打几次蜡,少打脱模剂,脱模后的船体外表面有一层保护模;脱模后,再打一次蜡(少量)+一次脱模剂。
5、胶衣(1)调配:胶衣+固化剂(过氧化甲乙酮,又名“白配方”,固化剂占胶衣重量的1-4%)(2)操作:①结构大的模具用喷枪喷洒,小的用刷子即可。
用喷枪喷洒时,胶衣与固化剂外混合,机器自动调配;②船体外彩色部分是先用分色纸将其挡住再喷主色部分,然后揭去分色纸挡住主色部分后喷彩色;③注意:胶衣不能太薄,应在0.4-0.6mm之间。
玻璃钢船体的手工糊制
玻璃钢船体的手工糊制玻璃钢船工艺流程毅中雪书屋玻璃钢船工艺流程玻璃钢船工艺流程。
1 制模(1)方法:①按肋位放样->定中心线、制作并组装样板(组装时底下留一定高度,便于排气)->中空处铺木板->打腻子(石膏或其它腻子,并用挎尺挎平滑->水磨砂纸打磨->喷漆(或胶衣,一般喷漆即可,胶衣较漆贵)->脱模剂->模具胶衣(较产品胶衣贵)->模具树脂(变形小。
③用结构胶混合相应配方(固化剂)连接船体构件,比腻子更具黏性及弹性,可粘光滑表面。
纤维增强环氧树脂复合材料成型工艺及其应用梦泽赤子纤维增强环氧树脂复合材料成型工艺及其应用。
按基体材料不同,复合材料可分为三大类:树脂基复合材料金属基复合材料无机非金属基复合材料,如陶瓷基复合材料、水泥基复合材料、碳基复合材料等。
树脂:常用不饱和聚酯树脂、环氧树脂、乙烯基酯树脂、酚醛树脂;树脂:主要采用环氧树脂、酚醛树脂。
(2)原材料树脂:通常用环氧树脂,不饱和聚酯树脂、酚醛树脂及高温树脂,如聚酰亚胺、氰酸酯、双马来酰亚胺树脂等;玻璃钢模具的制作与糊制梦泽赤子当两件模具对合后有那些凹凸位,便不会出现左右模具侈位问题我用的斜边小纸板这个是加上分模纸板、斜边纸板的船体不饱和脂糊粘力是很强的,如果直接在上面糊制最终是不能脱模的,所以糊制前先在工件上做点工夫:先油上一至三层PVA薄膜脱模剂再扫脱模蜡,如果没有PVA薄膜脱模剂,多用点脱模蜡也可以的。
制作玻璃钢灶壳的模具采用水泥模,其方法与水泥灶相同,但水泥模具制成后还要进行表面封孔处理,这将更有利于模具的顺利脱模。
玻璃钢tdb890玻璃钢。
根据介质的不同,树脂可以选乙烯基树脂、聚酯树脂等。
3.配胶:树脂的固化体系有多种,现给你讲的是最常用的MEKP/钴盐固化体系。
把树脂倒入胶盆中,称量重量,先加入钴盐(环烷酸钴),钴盐的用量约为树脂重量的1-2%,搅拌均匀。
施工工艺:用毛刷在模具表面刷一层树脂,贴一层表面毡,用毛刷将表面毡紧紧贴合在模具上,要浸透树脂,不能有气泡。
玻璃钢工艺流程图
胶液
上 ↓ 配制
层毡 无Biblioteka →→浸碱纱
渍
下
层毡
→预
成
型
→ 加 → 牵→
切
温
引
固
割↓
化
.1
钻 孔
检 验
包 装
文件名称:物流部标准作业手册(SOP-04)
4、缠绕产品生产工艺流程
树脂胶液 制衬 缠绕纱 准备 缠绕 固化 修整
纤维、表面毡
检验 交付
.2
文件名称:物流部标准作业手册(SOP-04)
河北省枣强玻璃钢集团有限公司
生产工艺流程图
1、手糊产品生产工艺流程
树脂
促进剂
树脂胶液(加固化剂 )
加热固化 脱模
切割修整 检验
产成品
纤维纱
2、模压产品生产工艺流程 树脂 短切毡 纤维纱 辅料
片材制作 →入模 →模压成型→脱模→整理→检验→入库
3、拉挤产品生产工艺流程
玻璃钢船艇模具制作工艺流程
玻璃钢船艇模具制作工艺流程万国(南通)玻璃钢有限公司VANGUARD(NANTONG)F.R.P.CO., LTD.A、外壳模具制作一、木工制作1、制作底板。
在地面上打基线,根据基线在地面上用木板组成底板框架,调整使之水平,用玻璃钢将框架与地面固定,然后在木框架上铺木工板,调整使之水平。
2、确定俯视图。
按型值表在地板上绘制站距以及各站板的半宽边线,然后将各个站板半宽边线的端点连接,这样俯视图就能确定下来。
3、制作木模型。
根据型值表在木工板上绘制个站板线型图,切割使之成型。
用木条等将各站板与底板固定,站板之间用木条互相支撑固定,另用木工板将整个模型框架封闭。
二、防潮层,批嵌腻子,喷易打磨胶衣1、糊防潮层:在木模表面上糊2层400g玻璃纤维布,用于加固木模强度,防止模具表面变形及防潮。
在玻璃钢固化后,再进行表面外理(如棱角、毛刺、重叠等)。
2、在胎膜上批嵌原子灰:在原子灰中加入适量固化剂,一般每桶原子灰在20℃的条件下,加入固化剂用量为2%,然后搅拌均匀,涂抹在胎膜上,用软管或挎尺照模型形状,将其挎圆顺,光滑。
反复按以上顺序操作,直至胎膜达到理想形状。
3、喷易打磨胶衣:打磨完成后,将胎膜表面灰尘、杂物清理干净后,将易打磨胶衣(产品胶衣可替代)均匀地喷涂在胎膜表面。
a) 、喷胶衣时,稀释剂:胶衣=1:1.5,固化剂用量为胶衣的1%-2%(温度决定)。
b) 、胶衣厚度为不小于 l mm,胶衣分 2 层,喷涂过程分几次完成,直至胶衣厚度达到理想程度。
c) 、易打磨胶衣固化时间一般控制在 45 分钟为佳。
4 、打磨成衣:胶衣固化 12 小时后打磨,首先选用相应的铁砂纸,用平板打磨机打磨,使胶衣表面颗粒基本光滑,再用水砂打磨,直至平滑光亮。
三、水磨,抛光,打蜡,上模具胶衣1、水磨:逐次用400#,600#,1000#,1200#的水砂纸水磨。
为了方便操作,一般制作长方体泡沫块裹上砂纸,沾水磨(一般水中放适量洗衣粉,起润滑作用,有效的增加了砂纸的利用率 ),按照模型形状往统一的方向砂磨,直到模型表面不在有亮光为止 ( 防止漏砂 ) ,达到平滑光亮。
玻璃钢船制作方法
玻璃钢船制作方法
玻璃钢船是一种轻便、耐用、防腐蚀的船只,广泛应用于各种水上运输和娱乐活动中。
下面是玻璃钢船制作的详细步骤:
1. 设计:首先需要根据船只用途和要求进行设计,包括船体形状、大小、结构等方面。
可以使用CAD等软件进行设计,并根据设计图纸制作模具。
2. 制备模具:根据设计图纸制作模具,模具可以采用木质或金属材料制作,要求精度高且表面光滑。
3. 制备玻璃钢材料:将玻璃纤维布和环氧树脂按一定比例混合搅拌均匀,待使用。
4. 涂抹模具:在模具表面涂上一层分离剂,然后将玻璃钢材料涂抹在模具表面上,压实并排除空气泡。
重复此过程直到达到所需厚度。
5. 固化:将涂抹好的模具放置在恒温室内或室外晾干固化,时间约为24小时左右。
6. 脱模:待模具固化后,将玻璃钢船体从模具中取出,注意避免损坏
船体表面。
7. 制作配件:根据设计要求制作船体配件,如桅杆、舵轮、座椅等。
8. 拼装:将制作好的配件拼装在船体上,使用螺丝和胶水固定。
9. 涂装:对玻璃钢船进行涂装,既可以美化外观,也可以增加防腐蚀
性能。
以上是玻璃钢船制作的详细步骤。
在实际操作中需要注意安全和精度,以确保制作出高质量的玻璃钢船。
- 1、下载文档前请自行甄别文档内容的完整性,平台不提供额外的编辑、内容补充、找答案等附加服务。
- 2、"仅部分预览"的文档,不可在线预览部分如存在完整性等问题,可反馈申请退款(可完整预览的文档不适用该条件!)。
- 3、如文档侵犯您的权益,请联系客服反馈,我们会尽快为您处理(人工客服工作时间:9:00-18:30)。
玻璃钢船工艺流程
一. 前言
1. 概念: 玻璃钢的学名为玻璃纤维增强塑料, 英文缩写GRP, 既Glass Reinforced Plastic。
2. 优点
2.1 质轻高强, 对减轻结构重量有较大潜力, 特别适用于限制重量的高性能船舶和赛艇。
2.2 耐腐蚀、抗海生物附着, 比传统的造船材料更适合在海洋环境中使用。
2.3 介电性和微波穿透性好, 适用于军用舰艇。
2.4 能吸收高能量, 冲击韧性好, 船舶不易因一般的碰撞、挤压而损坏。
2.5 导热系数低, 隔热性好。
2.6 船体表面能达到镜面光滑, 色彩多样, 特别是建造结构复杂、款式多样、外形美观的游艇。
2.7 可设计性好, 能按船舶结构各部位的不同要求, 经过选材、铺层研究和结构选型实现优化设计。
2.8 整体性好, 能够做到整个船体无接缝和缝隙。
2.9 船体成型简便, 比钢质、木质船省工, 且批量生产性特别好, 降低造价的潜力很大。
2.10 维修保养方便, 维修费比钢质、铝质和木质船少的多, 全寿命期的经济性能好。
3. 缺点
受刚性模量低和受成型技术等的限制, 尚不能建造太大的舰船, 加之原料价格较贵, 在整个造船材料中的用量仍较少。
4. 特性
玻璃钢固化后具有收缩的特性。
5. 要求
温度15至30℃; 湿度40%至60%, 不超过65%; 考虑通风、集尘、避光直射等。
二. 工艺流程
1. 总纲
制作木型→木型处理→模具制造→模具处理→脱模剂→胶衣→树脂( 腻子) →毡/布/复合毡( 多层板/轻木) →固化→装骨架( 筋) →脱模→修整组装
2. 工序
2.1 制作木型
2.1.1 上体
2.1.1.1 建造船台
根据船型及主要参数( Loa、B、D) 采用槽钢建造船台, 其两端各延伸两条竖直槽钢, 槽钢均统一向外, 船台中间视船体大小( 重量) 增加横梁或纵桁。
将木方固定在船台上, 利用水平仪用电刨( 手刨) ,
2.1.1.1.1 制作基准面钢架, 注意槽钢朝外
3. 画参考线
1 制模
( 1) 方法: ①按肋位放样→定中心线、制作并组装样板( 组装时底下留一定高度, 便于排气) →中空处铺木板→打腻子( 石膏或其
它腻子, 并用挎尺挎平滑→水磨砂纸打磨→喷漆( 或胶衣, 一般喷
漆即可, 胶衣较漆贵) →脱模剂→模具胶衣( 较产品胶衣贵) →模具树脂( 变形小。
收缩率低) →毡/布/复合毡→固化→装支撑板→脱模→修整②用她人造过的船/构件作模具, 举例: a.可用印花玻璃加
工模具做成防滑板; b.经过薄膜→毡/布→薄膜( 不要产生气泡) →造型→揭膜的方法制作石棉瓦
( 2) 注意: ①模具胶衣的颜色要和产品胶衣颜色不同, 喷涂产品胶衣时便于观察均匀情况; ②模具要有一定的斜度( 1.5mm/m即可) , 便于起模; ③对于平滑面多且小的构件, 可用光滑的胶合板( 需衬木板使其不变形) 代替打腻子( 周围棱角或交接处仍需腻子刮平滑) , 然后打蜡即可( 一般不必喷漆, 但打腻子处如精度需要仍需喷漆) ; ④支撑板要交叉组装, 并用毡/布/复合毡等固定。
同时在与船体固定及支撑地面的部分做相应加强; ⑤制模后要打抛光膏
使模具质量更好。
2.脱模剂
( 1) 种类: ①一次蜡即地板蜡( 大量) + 一次脱模剂适用于新模具,
多打几次蜡, 少打脱模剂, 脱模后的船体外表面有一层保护模; 脱膜后, 再打一次蜡( 少量) + 一次脱膜剂; ②一次蜡( 大量) + 多次脱模剂适用于老模具批量生产, 每脱模一次用干净抹布擦净即可再次喷胶衣。
不能沾水, 否则多次脱膜剂就浪费了, 须重新打腊; ③一次腊( 大量) + 多次蜡适用于老模具批量生产, 每脱模一次用干净抹布擦净即可再次喷胶衣。
如果沾水, 用抹布擦干后再打2次多次腊即可, 不需打一次腊了。
其实, 只打多次腊也能够脱膜, 但价格较一次腊贵。
( 2) 比较: ①脱模最保险; ②较③能脱模更多更方便, 但价格较贵; ②和③都不保护模具, 对模有损害, 需定期修整模具( 修整方法见10-( 1) - ②) 。
( 3) 注意: ①多次腊与脱模剂不相溶, 因此不能同时使用; ②采用回旋法打蜡,稍待5-10分钟( 让模具饱和) 用抹布擦至镜面效果后再打下遍; ③一般打蜡越多越好脱模, 应视具体情况决定; ④一次腊用于做底, 它价格便宜, 越多越好脱膜。
3.胶衣
( 1) 调配: 胶衣 + 固化剂( 过氧化甲乙酮, 又名”白配方”, 固化剂占胶衣重量的1-4%)
( 2) 操作: ①结构大的模具用喷枪喷洒, 小的用刷子即可。
用喷枪喷洒时, 胶衣与固化剂外混合, 机器自动调配; ②船体外彩色部分是先用分色纸将其挡住再喷主色部分, 然后揭去分色纸挡住主色部分后喷彩色。
( 3) 注意: 胶衣不能太薄, 应在0.4-0.6mm之间。
4.树脂
( 1) 调配: 树脂( 不饱和聚酯树脂) + 促进剂( 又名”红配方”, 促进固化) + 白配方( 促进剂和固化剂一般各是树脂重量的1-4%)
( 2) 作用: 胶结及饱和作用。
( 3) 注意: ①有些树脂已经含有促进剂( 如2597PT) , 可不在添加促进剂; ②促进剂的作用是促进固化作用, 固化剂作用是使树脂固化。
只有固化剂没有促进剂, 树脂固化时间缓慢。
只有促进剂, 没有固化剂树脂不固化。
因此两者缺一不可, 且要视情况按一定比例调配, 固化剂量过大可能引起燃烧。
有些化学品也可提高固化速度( 如氨水, 仰脸作业或提高效率等施工需要可少量添加) , 可是有可能使树脂变质, 因此要注意用量和使用方法。
一些树脂固化后表面发粘, 主要是因为树脂质量不好; ③温度越高, 固化剂的固化作用越明显。
因此天热时可比平时少放固化剂。
当然也可利用使其加快固化作用满施工需要; ④温度越低, 树脂越粘稠, 施工时用量不好控制, 因此要注意室内温度; ⑤树脂质量不好( 粘性小) , 可在放完催化剂后添加少量滑石粉( 如经济允许添加白碳黑, 即硅粉) , 增加粘性; ⑥固化剂要在施工前最后放, 以免树脂提前固化; ⑦树脂价格较高应节约使用。
6.树脂腻
( 1) 调配: 树脂 + 红配方 + 滑石粉 + 白配方
( 2) 作用: ①棱角或缝隙处填上腻子可起到过渡作用, 注意抹完
树脂腻子后要用沾树脂的毛刷将其抹均匀; ②能够固定多层板和结构复杂处的软木; ③可作为修补船用材料。
( 3) 缺点: 固化后发脆, 不能用来粘光滑表面。
( 4) 白炭黑( 硅粉) 也可用于调配腻子( 与胶衣或树脂) , 质量更好更光滑( 可用于修补船)
5.毡/布/复合毡
( 1) 区别: ①毡/布/复合毡的种类多样, 铺叠程度由易到难; ②表面毡较其它毡薄, 是喷完胶衣后铺的第一层毡, 而后再铺其它毡、布等; ③针制复合毡相当于布与毡的结合体, 一面为毡, 一面为布( 如1050) ; ④喷纱可代替复合毡, 可是机器喷洒时含树脂量大, 易浪费; ⑤m代表表面毡, M代表毡, R代表布, B代表轻木。
( 2) 操作: ①在不易铺叠的地方用树脂腻子过渡; ②模具结构复杂部分可用布、毡结合代替复合毡以减少铺叠难度( 如上体首部) ; ③用剪子将这边处的毡/布/复合毡顺势剪开以便于铺叠; ④将毡/布/复合毡定位后再刷树脂; ⑤大捻子用于易处理的平滑部分, 小捻子可处理棱角多的复杂部分, 要防止气泡出现。
如气泡处已经固化, 应用刀片将其削去并填补; ⑥每层毡/布/复合毡都应该吃透树脂, 应该视情况决定一次刷几层毡( 布/复合毡) , 一般对厚度超过5mm的工件积层要分两次进行。
例如300毡可同时铺2层再刷树脂, 一层300毡和一层1050复合毡也可; ⑦布/复合毡的交界如有毛刺可用小片/条毡铺平顺; ⑧每道工序完成后应该毡面朝外, 铺多层复合毡时最好先把毡面朝内( 美观) ; 有时, 可用角磨机。