滚齿机工作原理 功能分析 介绍
滚齿机加工原理【解析】
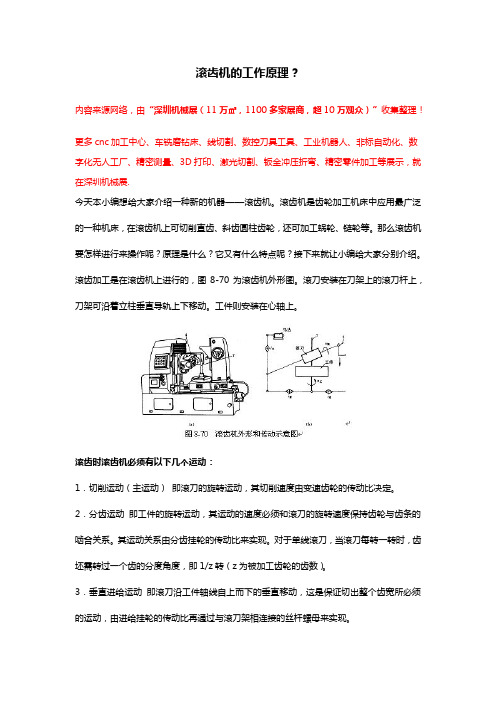
滚齿机的工作原理?内容来源网络,由“深圳机械展(11万㎡,1100多家展商,超10万观众)”收集整理!更多cnc加工中心、车铣磨钻床、线切割、数控刀具工具、工业机器人、非标自动化、数字化无人工厂、精密测量、3D打印、激光切割、钣金冲压折弯、精密零件加工等展示,就在深圳机械展.今天本小编想给大家介绍一种新的机器——滚齿机。
滚齿机是齿轮加工机床中应用最广泛的一种机床,在滚齿机上可切削直齿、斜齿圆柱齿轮,还可加工蜗轮、链轮等。
那么滚齿机要怎样进行来操作呢?原理是什么?它又有什么特点呢?接下来就让小编给大家分别介绍。
滚齿加工是在滚齿机上进行的,图8-70为滚齿机外形图。
滚刀安装在刀架上的滚刀杆上,刀架可沿着立柱垂直导轨上下移动。
工件则安装在心轴上。
滚齿时滚齿机必须有以下几个运动:1.切削运动(主运动)即滚刀的旋转运动,其切削速度由变速齿轮的传动比决定。
2.分齿运动即工件的旋转运动,其运动的速度必须和滚刀的旋转速度保持齿轮与齿条的啮合关系。
其运动关系由分齿挂轮的传动比来实现。
对于单线滚刀,当滚刀每转一转时,齿坯需转过一个齿的分度角度,即1/z转(z为被加工齿轮的齿数)。
3.垂直进给运动即滚刀沿工件轴线自上而下的垂直移动,这是保证切出整个齿宽所必须的运动,由进给挂轮的传动比再通过与滚刀架相连接的丝杆螺母来实现。
在滚齿时,必须保持滚刀刀齿的运动方向与被切齿轮的齿向一致,然而由于滚刀刀齿排列在一条螺旋线上,刀齿的方向与滚刀轴线并不垂直。
所以,必须把刀架扳转一个角度使之与齿轮的齿向协调。
滚切直齿轮时,扳转的角度就是滚刀的螺旋升角。
滚切斜齿轮时,还要根据斜齿轮的螺旋方向,以及螺旋角的大小来决定扳转角度的大小及扳转方向。
齿轮滚刀是一种专用刀具,每把滚刀可以加工模数相同而齿数不等的各种大小不同的直齿或斜齿渐开线外圆柱齿轮。
在滚齿机上除加工直齿、斜齿外圆柱齿轮外,也可以加工蜗轮、链轮。
但不能加工内齿轮。
对于加工双联齿轮和三联齿轮它也受到许多限制。
数控滚齿机工作原理

数控滚齿机工作原理
数控滚齿机是一种用于加工齿轮的机械设备,其工作原理主要包括以下步骤:
1. 设计加工轮廓:根据齿轮的设计要求,使用专业的
CAD/CAM软件设计出齿轮的加工轮廓。
2. 编写数控程序:将设计好的齿轮轮廓转化为数控程序,编写G代码,包括齿轮尺寸、齿数、模数等参数。
3. 加工准备:安装工件(齿轮原料),将其固定在滚齿机工作台上,并校准工件位置和刀具位置。
4. 设置加工参数:根据加工要求,设置滚齿机的加工参数,包括滚齿速度、压力、进给速度等。
5. 加工操作:启动数控滚齿机,机床按照预先编写的程序,控制刀轮进行自动滚齿加工。
刀轮与工件之间通过机械传动系统实现独立运动,其中一只刀轮作为主导刀进行转动,另一只刀轮则通过传动与主导刀同步运动。
6. 检测和调整:完成加工后,使用测量工具(如齿轮测量仪)对加工后的齿轮进行检测,对不合格齿轮进行调整或修正。
7. 加工结束:将加工好的齿轮从滚齿机上取下,进行后续的装配或其他加工工序。
总之,数控滚齿机通过数控编程和机械运动控制技术,实现对齿轮的精确加工,提高了加工效率和加工质量。
滚齿的加工原理及常见缺陷处理办法

滚齿的加工原理及常见缺陷处理办法齿轮是机械产品设计中的常用零件,而在齿轮齿形加工中,滚齿应用最广泛,它除可加工直齿、斜齿圆柱齿轮外,还可以加工蜗轮、花键轴等。
滚齿适用于单件小批量生产和大批大量生产。
本文将为大家介绍一下滚齿的加工原理及常见缺陷处理办法。
滚切齿轮可看作无啮合间隙的齿轮与齿条传动。
当滚齿旋转一周时,相当于齿条在法向移动一个刀齿。
滚齿是目前应用最广的切齿方法,可加工渐开线齿轮、圆弧齿轮、摆线齿轮、链轮、棘轮、蜗轮和包络蜗杆,精度一般可达到DIN4~7级。
目前滚齿的先进技术有多头滚刀滚齿、硬齿面滚齿技术、大型齿轮滚齿技术、高速滚齿技术等。
1齿数不正确主要原因1)分齿交换齿轮调整不正确2)滚刀选用错误3)工件毛坯尺寸正确4)滚切斜齿轮时,附加运动方向不对解决方法1)重新调整分齿交换齿轮,并检查中间轮加置是否正确2)合理选用滚刀3)更换工件毛坯4)增加或减少差动交换齿轮中的中间轮2齿形不正常——齿面出棱主要原因滚刀齿形误差太大或分齿无能无力瞬时速比较变化大,工件缺陷状况有四种1)滚刀刃磨后,刀齿等分性差2)滚刀轴向窜动林3)滚刀径向跳动大4)滚刀用钝解决方法主要方法:着眼于滚刀刃磨质量,滚刀安装精度以及机床主轴的几何精度:1)控制滚刀刃磨质量2)保证滚刀的安装精度,同时安装滚刀时不能敲击;垫圈端面平整;螺母端面要垂直;锥孔内部应清洁;托架装上后,不能留间隙3)复查机床主轴的旋转精度,并修复调整滚刀主轴轴承,尤其是止推垫片4)更换新刀3齿形不正常——齿形不对称主要原因1)滚刀安装不对中2)滚刀刃磨后,前刃面的径向误差大3)滚刀刃磨后,螺旋角或导程误差大4)滚刀安装角的误差太大解决方法1)用“啃刀花”法或刀规对刀2)控制滚刀刃磨质量3)重新调整滚刀的安装解4齿形不正常——齿形角不对主要原因1)滚刀本身的齿形角误差太大2)滚刀刃磨后,前刃面的径向性误差大3)滚刀安装角的误差大解决方法1)合理选用滚刀的精度2)控制滚刀的刃磨质量3)重新调整滚刀的安装角5齿形不正常——齿形周期性误差主要原因1)滚刀安装后,径向跳动或轴向窜动大2)机床工作台回转不均匀3)跨轮或分齿交换齿轮安装偏心或齿面磕碰4)刀架滑板有松动5)工件装夹不合理产生振摆解决方法1)控制滚刀的安装精度2)检查机床工作台分度蜗杆的轴向窜动,并调整修复之3)检查跨轮及分齿交换齿轮的安装及运转状况4)调整刀架滑板的塞铁5)合理选用工件装夹的正确方案6齿圈径向跳动超差主要原因工件内孔中心与机床工作台回转中心不重合(1)有关机床、夹具方面:•工作台径向跳动大•心轴磨损或径向跳动大•上下顶针有偏差或松动•夹具定位端面与工作台回转中心线不垂直•工作装夹元件,例如垫圈和并帽精度不够(2)有关工作方面:•工件定位孔直径超差•用找正工件外圆安装时,外圆与内孔的同轴度超差•工件夹紧刚性差解决方法着眼于控制机订工作台的回转精度与工件的正确安装(1)有关机床和夹具方面:•检查并修复工作台回转导轨•合理使用和保养工件心轴•修复后立柱及上顶针的精度•夹具定位端与工作台回转中心线不垂直•提高工件装夹元件精度,例如垫圈和并帽(2)有关工件方面:•控制工件定位孔的尺寸精度•控制工件外圆与内孔的同轴度误差•夹紧力应施于加工刚性足够的部件主要原因7齿圈径向跳动超差主要原因滚刀垂直进给方向与齿坯内孔轴线方向偏斜太大。
滚齿机(Y3150E)的工作原理介绍

滚齿机(Y3150E)的工作原理介绍一、Y3150E的意义Y——齿轮加工机床;3——滚齿机及铣齿机;1——小模数齿轮滚齿机;50——φ500(取1/10为50);E——第五次改进。
二、滚齿机的刀具:齿轮滚刀1.切削部分的材料:作为刀具切削部分的材料,应具有下列几个方面的基本性能:(1)较高的常温和高温硬度;(2)必要的强度和韧性;(3)较高的耐磨性;(4)良好的热导性和耐热性;(5)较好的化学惰性。
2.刀体材料由于硬质合金材料比较昂贵,烧结和加工也比较困难,所以滚刀一般都做成非整体式结构。
材料应考虑到滚到的结构形式和工艺要求,并应具有较高的硬度。
可选用中碳合金钢40Cr、40CrNiMo、50CrV或工具钢T10A、T12A、9SiCr等。
对于焊接式滚刀,不仅应具有硬度高,变形小的性能,还应当有较好的可焊性,通常可用9SiCr等工具钢。
3.结构形式分为机夹式、焊接式和机夹——焊接式。
机夹式一般用于m10以内的滚刀。
结构比较复杂,加紧的可靠性较差。
焊接式结构简单,连接强度高,刀片烧结容易、材料节省,因此应用较广泛。
但焊接工艺复杂,焊接应力大,刀片和刀体易焊裂。
4.基本尺寸滚刀具有外径、孔径、长度等基本尺寸。
这些基本尺寸要根据滚刀的规格、用途、结构形式和机床条件等因素进行确定。
由于滚刀的结构形式和设计原则不同,各厂生产的滚刀的基本尺寸也不尽相同,没有统一标准。
为了避免刀杆的弯曲振动,滚刀应具有较大的孔径。
滚刀的长度由切削部分和轴台部分组成。
滚刀工作长度较短,为了便于制造,基本长度可按三圈完整螺纹计算。
5.刀齿的角度(1)前角试验和使用情况表明:随着滚刀负前角的增大,滚齿过程变得平稳。
刀齿的耐用度明显提高。
但是,负前角值越大,保证滚刀的齿形精度就越困难。
一般选用-30°左右的前角。
(2)后角由于刀刃切入齿面比较困难,而且刀齿具有负前角,为了使刀齿保持较好的锋利性,应采用较大的后角。
而且试验表明:刀具的耐用度随后角的增大而成比例的提高。
滚齿机加工原理【详解】

滚齿机加工原理内容来源网络,由“深圳机械展(11万㎡,1100多家展商,超10万观众)”收集整理!更多cnc加工中心、车铣磨钻床、线切割、数控刀具工具、工业机器人、非标自动化、数字化无人工厂、精密测量、3D打印、激光切割、钣金冲压折弯、精密零件加工等展示,就在深圳机械展.一.滚齿机介绍滚齿机是齿轮加工机床中应用最广泛的一种机床,在滚齿机上可切削直齿、斜齿圆柱齿轮,还可加工蜗轮、链轮等,这种机床使用特制的滚刀时也能加工花键和链轮等各种特殊齿形的工件。
广泛应用汽车、拖拉机、机床、工程机械、矿山机械、冶金机械、石油、仪表、飞机航天器等各种机械制造业。
齿轮加工机床品种规格繁多,有加工几毫米直径齿轮小型机床,加工十几米直径齿轮大型机床,还有大量生产用高效机床加工精密齿轮高精度机床。
二.滚齿加工的工艺特点(1)加工精度高属于展成法的滚齿加工,不存在成形法铣齿的那种齿形曲线理论误差,所以分齿精度高,一般可加工8~7级精度的齿轮。
(2)生产率高滚齿加工属于连续切削,无辅助时间损失,生产率一般比铣齿、插齿高。
(3)一把滚刀可加工模数和压力角与滚刀相同而齿数不同的圆柱齿轮在齿轮齿形加工中,滚齿应用最广泛,它除可加工直齿、斜齿圆柱齿轮外,还可以加工蜗轮、花键轴等。
但一般不能加工内齿轮、扇形齿轮和相距很近的双联齿轮。
滚齿适用于单件小批量生产和大批大量生产。
三.滚齿加工原理根据齿轮的成形原理,综合考虑滚切中对机械进给系统跟随性、快速性的要求及改造成本等因素,在保留原普通滚齿机分齿传动链的基础上,按照数控理论中两坐标圆弧插补原理,对机床的刀架垂直进给运动和水平径向进给进行数控化控制改造,实现齿轮加工。
滚齿加工是按照展成法的原理来加工齿轮的。
用滚刀来加工齿轮相当于一对交错轴的螺旋齿轮啮合。
在这对啮合的齿轮副中,一个齿数很少、只有一个或几个,螺旋角很大,就演变成了一个蜗杆状齿轮,为了形成切削刃,在该齿轮垂直于螺旋线的方向上开出容屑槽,磨前、后刀面,形成切削刃和前、后角,于是就变成了滚刀。
大连工业大学机床概论-滚齿机运动分析分解
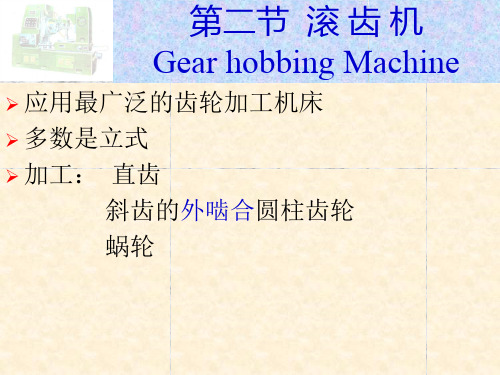
➢ 换置机构uy——适应工件螺旋线导程S和螺旋方向 的变化。
2024/7/16
22
齿轮机床
齿轮加工机床习题
➢ 1.按加工原理,齿轮加工方法
有和
。
➢ 2.滚齿机广泛用来加工 和 圆柱齿轮, 此外,它还可以用于加工 和 。
➢ 4.插齿机主要用于加工 、 和齿条。
➢ 5.分析成型法与范成法加工齿轮的优缺点。
刀架位移量
15
齿2.加工斜齿圆柱齿轮时的 运动和传动原理
2024/7/16
17
2024/7/16
18
齿轮机床
➢不同处: 齿线为螺旋线
➢所需运动: 范成运动
主运动
轴向进给运动
附加运动
➢即滚刀移动一个工件螺旋线导程S时,
工件应准确地附加转过一转
2024/7/16
➢ 6.叙述滚齿机滚切直齿轮、斜齿圆柱齿轮的
原理,并画出其传动原理图。
2024/7/16
23
齿轮机床
2024/7/16
11
齿轮机床
范成运动传动链
➢ 联系滚刀主轴(B11)和工作台(B12) ➢ 传动路线:“4-5-ux-6-7” ➢ 保证滚刀和工件旋转运动之间的严格运动关系。 ➢ 换置机构ux用于适应工件齿数和滚刀头数的变化。 ➢ 内联系传动链,要求传动比数值绝对准确及滚刀
和工件两者的旋转方向互相配合。
6
齿轮机床
滚刀和工件之间关系
➢ 为了得到所需的渐开线齿廓和齿轮齿数, 滚齿时滚刀和工件之间必须保持严格的相 对运动关系为:
滚刀1转——工件转k/z转
k——滚刀头数,Z——工件齿数
2024/7/16
7
齿轮机床
数控滚齿机原理

数控滚齿机原理
数控滚齿机是一种用于制造不同类型齿轮的机床。
它基本原理是利用机械加工方法,在齿轮的工作表面上形成齿槽,并确保齿槽的精度和质量。
数控滚齿机的操作主要由数控系统控制,数控系统根据事先编制的程序和刀具轨迹来控制机械运动。
数控滚齿机通常由滚刀架、工作台、数控系统和供润滑液的系统组成。
在工作过程中,工件夹持在滚刀架上,与滚刀头接触,滚刀头上有一组刀齿,它们可以在工件表面上滚动并形成齿槽。
滚刀架的位置、滚刀头与工件的接触力、滚刀头的旋转速度等参数都由数控系统控制。
数控滚齿机的滚刀头上的刀齿通常按照特定形状的齿轮来设计,这样可以保证滚刀头能够成形所需的齿槽形状。
滚刀头的形状和切削条件在数控系统的程序中进行描述,程序还包括了滚刀头在工作过程中的运动轨迹和滚刀头与工件的相对位置等信息。
通过数控滚齿机,可以实现齿轮的批量生产,提高生产效率和产品质量。
数控滚齿机的数控系统可以根据需求进行调整和更改,以适应不同类型的齿轮加工要求。
同时,数控滚齿机可以用于加工各种类型的齿轮,如圆柱齿轮、锥齿轮、螺旋齿轮等。
滚齿加工原理
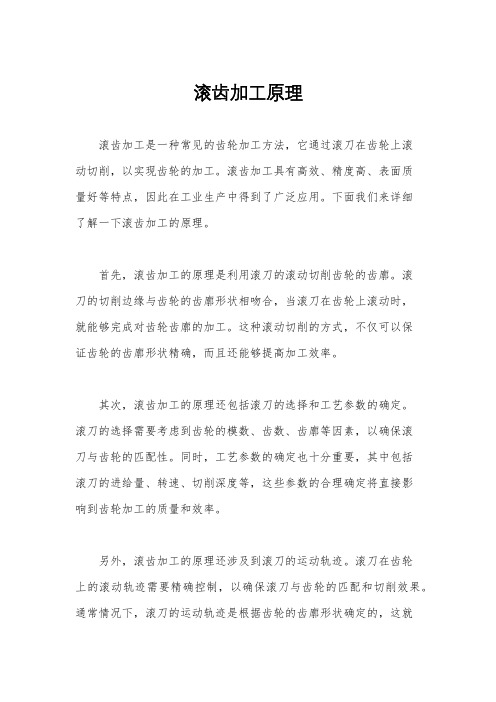
滚齿加工原理滚齿加工是一种常见的齿轮加工方法,它通过滚刀在齿轮上滚动切削,以实现齿轮的加工。
滚齿加工具有高效、精度高、表面质量好等特点,因此在工业生产中得到了广泛应用。
下面我们来详细了解一下滚齿加工的原理。
首先,滚齿加工的原理是利用滚刀的滚动切削齿轮的齿廓。
滚刀的切削边缘与齿轮的齿廓形状相吻合,当滚刀在齿轮上滚动时,就能够完成对齿轮齿廓的加工。
这种滚动切削的方式,不仅可以保证齿轮的齿廓形状精确,而且还能够提高加工效率。
其次,滚齿加工的原理还包括滚刀的选择和工艺参数的确定。
滚刀的选择需要考虑到齿轮的模数、齿数、齿廓等因素,以确保滚刀与齿轮的匹配性。
同时,工艺参数的确定也十分重要,其中包括滚刀的进给量、转速、切削深度等,这些参数的合理确定将直接影响到齿轮加工的质量和效率。
另外,滚齿加工的原理还涉及到滚刀的运动轨迹。
滚刀在齿轮上的滚动轨迹需要精确控制,以确保滚刀与齿轮的匹配和切削效果。
通常情况下,滚刀的运动轨迹是根据齿轮的齿廓形状确定的,这就要求滚刀的设计和制造具有高精度。
最后,滚齿加工的原理还包括切削液的使用。
在滚齿加工过程中,切削液的使用对于降低切削温度、减少摩擦和延长刀具寿命都起着重要作用。
因此,合理选择切削液的种类和使用方法,对于滚齿加工的效果有着直接的影响。
总的来说,滚齿加工的原理是基于滚刀的滚动切削齿轮的齿廓,需要合理选择滚刀和确定工艺参数,控制滚刀的运动轨迹,并合理使用切削液。
这样才能够实现齿轮加工的高效、高精度和高质量。
滚齿加工作为一种重要的齿轮加工方法,在工业生产中具有着重要的地位和作用,值得我们深入学习和研究。
- 1、下载文档前请自行甄别文档内容的完整性,平台不提供额外的编辑、内容补充、找答案等附加服务。
- 2、"仅部分预览"的文档,不可在线预览部分如存在完整性等问题,可反馈申请退款(可完整预览的文档不适用该条件!)。
- 3、如文档侵犯您的权益,请联系客服反馈,我们会尽快为您处理(人工客服工作时间:9:00-18:30)。
功能原理设计随着现代设计方法的发展及应用越来越广泛,人们对系统原理设计时常采用一种“抽象化”的方法---“黑箱法”。
之所以称为“黑箱法”是因为对于待设计产品来说,在求解之前,犹如一个看不见内部结构的“黑箱子”。
这种“黑箱”只能用来描述系统的功能目标,“黑箱”的内部结构需要设计人员进一步构思的设计。
由此可知,“黑箱法”是根据系统的输入、输出关系来研究实现系统功能目标的一种方法,即根据系统的某输入及要求获得某种输出要求,从中寻找某种原理来实现输入---输出之间的转化,得到相应的解决办法,从而推求出“黑箱”的功能结构,使“黑箱”变成“白箱”的一种方法。
1、黑箱法寻找总功能的转化关系物料流包括材料、毛坯半成品、成品,液体、气体等各物体;能量流包括电能、光能、机械能、热能、核能等;信号流包括数据、测量值、控制信号、波形等。
通过对Y38滚齿机的综合分析,可得以下“黑箱”示意图通过黑箱法分析,滚齿机是将轮坯通过一定的加工过程,最终得到所需产品—齿轮的机器。
该过程有各种能量的交换、损失,同时还与外界的环境密切相关。
2、滚齿加工原理齿轮是现代机械传动中的重要组成部分。
从国防机械到民用机械,从重工业机械到轻工业机械,无不广泛的采用齿轮传动。
随着汽车、机械、航天等工业领域的高速发展,对齿轮的需求量日益增加,对齿轮加工的效率、质量及加工成本的要求愈来愈高,滚齿机是齿轮加工加床中的一种,由于滚齿机既适合高效率的齿形粗加工,又适合中等精度齿轮的精加工,因此受到广泛的应用。
为此滚齿机的研究仍是大家努力的方向齿轮加工机床的种类繁多,构造各异,加工方法也不相同,齿形加工可按在加工中有无切屑而区分为无屑加工和切削加工两大类。
无屑加工包括热轧、冷轧、压铸和粉末冶金等,无屑加工生产率高,材料消耗少,故成本低,但加工精度不高。
(1)冷轧冷轧是能在圆柱形零件上生产出齿轮的齿、花键、细齿、油槽或螺纹的一种很简单的方法。
生产率很高,用此方法扎制一个齿轮仅需3~5秒钟,但它受轧制形状和材料的限制较大。
密西根RoTo-Flo冷轧机是应用较早的齿轮冷轧机之一。
它用齿条作轧制工具。
其原理如2-1所示。
其中俩轧辊齿条被弄成斜面,最开始的轧制量小,当齿条运动时,轧制量逐渐增加,金属开始流动。
这种轧制方法,齿轮受到的弯曲负荷大,因而仅适用于轧制压力角大和齿形短的齿轮。
(压力角25度或25度以上)。
因此,RoTo-Flo设备通常用于轧制SAE 型压力角30度的齿深50%的和渐开线花键型的零件。
图2-1 密西根齿条轧制原理(2)热轧所谓热轧是在轧制之前将毛坯加热,使之较易轧制,是冷轧的补充。
对加工要求精度要求不高以及要求表面质量光洁度为6~8级的齿轮,可以用热轧法而不再经过机械加工。
热轧加工出来的齿轮与铣削出来的比较,除加工方法简易外,齿形的金属材质未被切断,质量较好,硬度较高,沿齿形有一层0.5~0.6公厘的压实金属层,硬度较高,疲劳极限也较高,寿命较长,此外,还大大节约了被铣削掉的金属。
图2-2为热轧齿轮示意图。
图2-3热轧与铣削所的齿轮比较。
图2-2 热轧示意图图2-3热轧齿轮与铣削齿轮材质比较(3)粉末冶金粉末冶金齿轮是各种汽车发动机中普遍使用的粉末冶金零件,通过一次成形和精整工艺,需要其他后处理工艺,可以完全达到尺寸精度要求,尤其是齿形精度。
因此,与用传统机械加工方法制造相比,在材料投入和制造上都大大减少,它是体现粉末冶金特点的典型产品。
粉末冶金齿轮在整个粉末冶金零件中难以单独统计,但无论是按重量还是按零件数量,粉末冶金齿轮在汽车、摩托车中所占的比例都远远大于其他领域中的粉末冶金零件。
因此,从汽车、摩托车在整个粉末冶金零件中所占比例的上升可以看出,粉末冶金齿轮在整个粉末冶金零件中处于飞速发展的地位。
图2-4为粉末冶金齿轮加工。
图2-4 粉末冶金齿轮加工(4)电火花加工齿轮下面介绍用电火花线切割加工直齿锥齿轮机床的基本结构和机床参数首先将机械加工齿轮毛坯安装在数控转台回转中心。
倾斜调整回转中心轴(大型机床调整丝线),使丝线与数控转台轴线夹角为直齿锥齿轮锥度角。
调整丝线位置,使丝线(钼丝或铜丝)一端以直齿锥齿轮的顶尖为定点(即锥齿轮回转球心),另一端以直齿锥齿轮齿面大端上基圆为进给基点,这时丝线在两水咀间跨度为直齿锥齿轮回转球心半径,启动伺服电机将回转台和丝线进给丝杠锁定。
启动数控系统,使数控转台转动角度与直齿锥齿轮齿面大端丝线进退,按直齿锥齿轮设计当量模数编制程序执行旋转与进退联动。
当电极丝处在齿顶时,数控转台转动,电极丝线不动,这是加工出的轨迹是直齿锥齿轮的齿顶;转过齿顶圆心角后,大端处电极丝线随工件转动进行相应进给即加工齿型部分,当到达齿根时电极丝线停止进给,工件继续转动,此时加工的是齿根部分;当转过齿根圆心角时电极丝线回退加工同齿的另半个齿型,到达齿顶时完成一个齿的加工。
下面依次加工出全部齿。
在数控系统的控制下电极丝线按大端当量齿轮的标准渐开线生成齿型。
丝线经高频放电产生电火花蚀除工件生成缝隙,加工出标准直齿锥齿轮。
当丝线与数控转台中心线平行即夹角为零度时,电极丝线沿齿轮中心方向平行进退,数控合成加工出的齿轮为标准直齿轮。
下图为电火花加工加床。
图2-5 电火花加工齿轮数控机床齿形切削加工按其加工原理可分为仿形法和展成法加工。
(1)成形法成形法加工齿轮所采用的刀具为成形刀具,其切削刃形状与被切齿轮齿槽的截面形状相同。
成形刀具有单齿廓和多齿廓两种。
成形法加工齿轮齿形的原理是利用与被加工齿轮齿槽法向截面形状相符的成形刀具,在齿坯上加工出齿形的方法。
成形法加工齿轮的方法有铣齿、拉齿、插齿及磨齿等,其中最常用的方法是在普通铣床上用成形铣刀铣削齿形。
当齿轮模数m<8时,一般在卧式铣床上用盘状铣刀铣削,见图2-1a;当齿轮模数m≥8时,在立式铣床上用指状铣刀铣削,见图2-1b(2)展成法展成法加工齿轮齿形是利用一对齿轮啮合的原理来实现的。
即把其中一个转化为具有切削能力的齿轮刀具,另一个转化为被切工件,通过专用齿轮加工机床,强制刀具和工件作严格的啮合运动(展成运动),在运动过程中,刀具切削刃的运动轨迹逐渐包络出工件的齿形(图2-2)。
展成法加工齿轮,一种模数和压力角的刀具,可以加工出相同模数和压力角而齿数不同的齿轮,其加工过程是连续的,具有较高的加工精度和生产效率,是齿轮齿形主要的加工方法。
滚齿和插齿是展成法中最常见的两种加工方法。
图2-2展成法滚齿加工成形法与展成法的差异成形法适用于单件小批生产,加工精度和生产效率低。
用展成法加工齿轮,可以用一把刀具加工同一模数不同齿数的齿轮,且加工精度和生产率也较高,因此各种齿轮加工机床广泛应用这种加工方法,如滚齿机、插齿机、剃齿机等。
此外,多数磨齿机及锥齿轮加工机床也是按展成法原理进行加工的。
本次设计的Y38滚齿机采用展成原理加工。
常见齿形加工的一些方法如下表一表一齿轮加工的方法3、功能分解图:(针对机械传动的滚齿机作功能分解)2、功能元求解3、各功能元求解方案分析1)主传动:2)进给:3)差动:4):分齿5)动力:4、排列组合系统方案解1)各总体方案简图及方案简单说明2)最佳系统方案的评价与决策评价一个方案是否为最佳方案,可通过系统方案的评价与决策来实现。
本滚齿机选择了加工准确性、加工范围、效率、结构紧凑,操作简易和成本来作为评价依据。
各评价目标的的加权系数如下表所示: 表4-1 加权系数的判别表i n -评价目标数; i g -加权系数;表4-2 三种系统方案各个项目标评分表有效值法计算如下:加权系数矩阵G=(0.28,0.18,0.18,0.12,0.12,0.12)评分矩阵P=⎥⎥⎥⎦⎤⎢⎢⎢⎣⎡321p p p =⎥⎥⎥⎦⎤⎢⎢⎢⎣⎡788778788999876767 有效值矩阵 N=[321N N N ,,]=GP T=[]52.752.882.6其中N 1 =GP 1T =0.28×7+0.18×6+0.18×7+0.12×6+0.12×7+0.12×8=6.82 N 2 =GP 2T =0.28×9+0.18×9+0.18×9+0.12×8+0.12×8+0.12×7=8.52 N 3 =GP 3T =0.28×8+0.18×7+0.18×7+0.12×8+0.12×8+0.12×7=7.52 由上面的分析,可知方案2为最佳方案。
3)绘制传动系统图5、执行机构的速度和功率计算,电动机的选择滚刀的速度和功率表2.4—1251)滚刀速度查参考文献【1】表2.4—125使用条件变化时切削用量修正系数,当采用单头齿轮滚刀粗加工模数为1.5~6mm 的钢材时,取使用条件不变时的0.1=v k 值,可得切削速度为(m/s )5.032.08.0)3~25.0(21600600.1281⨯⨯⨯=V (5-1)即切削速度范围为s m /4837.14283.0-=ν,滚刀最大直径mm d 1200=,由滚刀转速公式算出滚刀转速s r d n /)14.23617.68(12014.3)4837.14283.0(1000601000600-=⨯-⨯⨯=⨯=πν (5-2)当采用单头齿轮滚刀粗加工模数为1.5~8mm 的铸铁时,取使用条件不变时的0.1=v k 值,可得切削速度为(m/s )16.03.02.08.0)8~5.1()3~25.0(59600600.1178⨯⨯⨯⨯=V (5-3) 即切削速度为s m /4924.14313.0-=ν,滚刀最大直径mm d 1200=,由滚刀转速公式算出滚刀转速 s r d n /)52.23764.68(12014.3)4924.14313.0(1000601000600-=⨯-⨯⨯=⨯=πν(5-4)综合考虑滚刀速度取68~238r/s 2)滚刀功率采用单头齿轮滚刀加工钢材时,0.1=m p k (参考文献【1】表2.4—125);f=1.5mm/r; m=4mm;根据参考文献【1】表4.7—4齿轮滚刀的基本型式和尺寸,按模数m=4mm 取0.1=v k I 型滚刀,其外径d 0=120mm;其切削功率为(kw )3875.00.1120104837.1625.01246037.19.0=⨯⨯⨯⨯⨯⨯=m P kw (5-5)加工铸铁时,切削功率为(kw )5010.10.1120104238.063626037.19.0=⨯⨯⨯⨯⨯⨯=m P kw (5-6) 综合考虑取kw p m 45.1= 电动机选择 1)电动机功率根据参考文献【2】表2—1取传动的效率96.01=η;锥齿轮的传动效率97.02=η;圆柱齿轮的传动效率99.03=η,滚动轴承的效率99.04=η,则主传动链的效率为kw 72.099.099.097.096.05.1435.1443321=⨯⨯⨯==ηηηηη (5-7)则总功率为0.72kw根据参考文献【2】第1130页知,由于进给功率较小,进给传动和主传动共用一个电动机的机床所以不单独计算进给功率,而在计算主传动工率时引进一个系数,对于齿轮加工机床K 取0.8,因而768.08.096.01=⨯==k ηη (5-8) 故主电动机的功率为kw P 888.1768.045.1==主电动机 (5-9) 2)电动机转由主传动传动链的运动平衡式来转化电机与滚刀转速,从而求出电机的转速范围602017172323282436365527192105⨯⨯⨯⨯⨯⨯⨯⨯=B A n n 电机刀 (5-10) 则206017172323242836362755105192⨯⨯⨯⨯⨯⨯⨯⨯=A B n n 刀电机。