损耗与散热设计.doc
开关电源散热设计

开关电源散热设计第一篇:开关电源散热设计散热设计的一些基本原则从有利于散热的角度出发,印制版最好是直立安装,板与板之间的距离一般不应小于2cm,而且器件在印制版上的排列方式应遵循一定的规则: ·对于采用自由对流空气冷却的设备,最好是将集成电路(或其它器件)按纵长方式排列,如图3示;对于采用强制空气冷却的设备,最好是将集成电路(或其它器件)按横长方式排列.·同一块印制板上的器件应尽可能按其发热量大小及散热程度分区排列,发热量小或耐热性差的器件(如小信号晶体管、小规模集成电路、电解电容等)放在冷却气流的最上流(入口处),发热量大或耐热性好的器件(如功率晶体管、大规模集成电路等)放在冷却气流最下游.·在水平方向上,大功率器件尽量靠近印制板边沿布置,以便缩短传热路径;在垂直方向上,大功率器件尽量靠近印制板上方布置,以便减少这些器件工作时对其它器件温度的影响.·对温度比较敏感的器件最好安置在温度最低的区域(如设备的底部),千万不要将它放在发热器件的正上方,多个器件最好是在水平面上交错布局.·设备内印制板的散热主要依靠空气流动,所以在设计时要研究空气流动路径,合理配置器件或印制电路板.空气流动时总是趋向于阻力小的地方流动,所以在印制电路板上配置器件时,要避免在某个区域留有较大的空域.整机中多块印制电路板的配置也应注意同样的问题.电子设备散热的重要性在电子设备广泛应用的今天.如何保证电子设备的长时间可靠运行,一直困扰着工程师们.造成电子设备故障的原因虽然很多,但是高温是其中最重要的因素(其它因素重要性依次是振动Vibration、潮湿Humidity、灰尘Dust),温度对电子设备的影响高达60%.温度和故障率的关系是成正比的,可以用下式来表示: F = Ae-E/KT 其中: F = 故障率, A=常数 E = 功率K =玻尔兹曼常量(8.63e-5eV/K)T = 结点温度随着芯片的集成度、功率密度的日愈提高,芯片的温度越来越成为系统稳定工作、性能提升的绊脚石.作为一个合格的电子产品设计人员,除了成功实现产品的功能之外,还必须充分考虑产品的稳定性、工作寿命,环境适应能力等等.而这些都和温度有着直接或间接的关系.数据显示,45%的电子产品损坏是由于温度过高.可见散热设计的重要性.如何对产品进行热设计,首先我们可以从芯片厂家提供的芯片Datasheet为判断的基础依.如何理解Datasheet的相关参数呢?下面将对Datasheet 中常用的热参数逐一说明.一、Datasheet中和散热有关的几个重要参数P--芯片功耗,单位W(瓦).功耗是热量产生的直接原因.功耗大的芯片,发热量也一定大.Tc--芯片壳体温度,单位℃.Tj--结点温度,单位℃.随着结点温度的提高,半导体器件性能将会下降.结点温度过高将导致芯片工作不稳定,系统死机,最终芯片烧毁.Ta--环境温度,单位℃.T stg--存储温度,单位℃.芯片的储存温度.Rja/θja--结点到环境的热阻,单位℃/W.Rjc/θjc--结点到芯片壳的热阻,单位℃/WΨjt--可以理解为结点到芯片上表面的热阻.当芯片热量只有部分通过上壳散出的时候的热阻参数.LFM--风速单位,英尺/分钟.提供最大Ta、Tj、P--早期的芯片Datasheet一般都是这种.理论上我们只需要保证芯片附近的环境温度不超过这个指标就可以保证芯片可以正常工作.但是实际并非如此.Ta这个参数是按照JEDEC标准测试而得.JEDEC标准是这样定义的:把芯片置于一块3X4.5英寸的4层PCB中间,环境温度测试探头距离这块PCB的板边缘12英寸.可见我们产品几乎不可能满足这种测试条件.因此,T a在这里对我们来说,没什么意义.在这种情况下保守的做法是:保证芯片的壳体温度T c﹤T a-max,一般来说芯片是可以正常工作的.>br> 直接提供Tc-max--这种情况相对较少,处理也相对简单.只需保证Tc﹤Tc-max即可.>br> 提供Tj、Rjc/θjc、P--近2年来,随着热设计的重要性不断提高,大部分的芯片资料都会提供上述参数.基本公式如下: Tj=Tc+Rjc*P只要保证Tj﹤Tj-max即可保证芯片正常工作.归根结底,我们只要能保证芯片的结点温度不超过芯片给定的最大值,芯片就可以正常工作.如何判断芯片是否需要增加散热措施第一步:搜集芯片的散热参数.主要有:P、Rja、Rjc、Tj等第二步:计算T c-max:Tc-max=Tj-Rjc*P第三步:计算要达到目标需要的Rca:Rca=(T c-max-Ta)/P第四步:计算芯片本身的Rca’:Rca’=Rja-Rjc如果Rca大于Rca’,说明不需要增加额外的散热措施.如果Rca小于Rca’,说明需要增加额外的散热措施.比如增加散热器、增加风扇等等.如前所述,Rja不能用于准确的计算芯片的温度,所以这种方法只能用于简单的判断.而不能用于最终的依据.下面举一个简单的例子: 例:某芯片功耗——1.7W;Rja——53℃/W;Tj——125℃;Rjc——25℃/W,芯片工作的最大环境温度是50℃.判断该芯片是否需要加散热器,散热器热阻是多少.Tc-max=Tj-Rjc*P =125℃-25℃/W*1.7W=82.5℃Rca=(T c-max-Ta)/P =(82.5-50)1.7 =19.12℃/WRca’=Rja-Rjc =53-25 =28℃/WRca小于Rca’,所以需要增加散热器.散热器的热阻假设为Rs,则有: Rs//Rca’小于Rca Rs*28/(Rs+28)小于19.12 Rs小于60.29℃/W 所以选用的散热器热阻必须小于60.29℃/W.在普通的数字电路设计中,我们很少考虑到集成电路的散热,因为低速芯片的功耗一般很小,在正常的自然散热条件下,芯片的温升不会太大.随着芯片速率的不断提高,单个芯片的功耗也逐渐变大,例如:Intel的奔腾CPU的功耗可达到 25W.当自然条件的散热已经不能使芯片的温升控制在要求的指标之下时,就需要使用适当的散热措施来加快芯片表面热的释放,使芯片工作在正常温度范围之内.通常条件下,热量的传递包括三种方式:传导、对流和辐射.传导是指直接接触的物体之间热量由温度高的一方向温度较低的一方的传递,对流是借助流体的流动传递热量,而辐射无需借助任何媒介,是发热体直接向周围空间释放热量.在实际应用中,散热的措施有散热器和风扇两种方式或者二者的同时使用.散热器通过和芯片表面的紧密接触使芯片的热量传导到散热器,散热器通常是一块带有很多叶片的热的良导体,它的充分扩展的表面使热的辐射大大增加,同时流通的空气也能带走更大的热能.风扇的使用也分为两种形式,一种是直接安装在散热器表面,另一种是安装在机箱和机架上,提高整个空间的空气流速.与电路计算中最基本的欧姆定律类似,散热的计算有一个最基本的公式: 温差= 热阻× 功耗在使用散热器的情况下,散热器与周围空气之间的热释放的“阻力”称为热阻,散热器与空气之间“热流”的大小用芯片的功耗来代表,这样热流由散热器流向空气时由于热阻的存在,在散热器和空气之间就产生了一定的温差,就像电流流过电阻会产生电压降一样.同样,散热器与芯片表面之间也会存在一定的热阻.热阻的单位为℃/W.选择散热器时,除了机械尺寸的考虑之外,最重要的参数就是散热器的热阻.热阻越小,散热器的散热能力越强.风冷散热原理从热力学的角度来看,物体的吸热、放热是相对的,凡是有温度差存在时,就必然发生热从高温处传递到低温处,这是自然界和工程技术领域中极普遍的一种现象.而热传递的方式有三种:辐射、对流、传导,其中以热传导为最快.我们要讨论的风冷散热,实际上就是强制对流散热.对流换热是指流体与其相接触的固体表面或流体,而这具有不同温度时所发生的热量转移过程.热源将热量以热传导方式传至导热导热介质,再由介质传至散热片基部,由基部将热量传至散热片肋片并通过风扇与空气分子进行受迫对流,将热量散发到空气中.风扇不断向散热片吹入冷空气,流出热空气,完成热的散热过程.对流换热即受导热规律的支配,又受流体流动规律的支配,属于一种复杂的传热过程,表现在对流换热的影响因素比较多.1.按流体产生流动的原因不同,可分为自然对流和强制对流.2.按流动性质来区分,有层流和紊流之别.流体从层流过渡到紊流是由于流动失去稳定性的结果.一般以雷诺数(Re)的大小,作为层流或紊流的判断依据.3.流体的物性对对流换热的影响.例如,粘度、密度、导热系数、比热、导温系数等等,它们随流体不同而不同,随温度变化而变化,从而改变对流换热的效果.4.换热表面的几何条件对对流换热的影响.其中包括: 1)管道中的进口、出口段的长度,形状以及流道本身的长度等;2)物体表面的几何形状,尺寸大小等;3)物体表面,如管道壁面、平板表面等的粗糙程度;4)物体表面的位置(平放、侧放、垂直放置等)以及流动空间的大小.5.流体物态改变的影响.6.换热面的边界条件,如恒热流、恒壁温等,也会影响对流换热.7.风量和温度的关系 T=Ta+1.76P/Q 式中Ta--环境温度,℃ P--整机功率,W Q--风扇的风量,CFM T--机箱内的温度,℃举一个电路设计中热阻的计算的例子: 设计要求: 芯片功耗: 20瓦芯片表面不能超过的最高温度: 85℃环境温度(最高): 55℃ 计算所需散热器的热阻.实际散热器与芯片之间的热阻很小,取01℃/W作为近似.则(R + 0.1)× 20W = 85℃-55℃得到R = 1.4 ℃/W只有当选择的散热器的热阻小于1.4℃/W时才能保证芯片表面温度不会超过85℃.使用风扇能带走散热器表面大量的热量,降低散热器与空气的温差,使散热器与空气之间的热阻减小.因此散热器的热阻参数通常用一张表来表示.如下例: 风速(英尺/秒)热阻(℃/W)0 3.5 100 2.8 200 2.3 300 2.0 400 1.8 PCB表面贴装电源器件的散热设计以Micrel公司表贴线性稳压器为例,介绍如何在仅使用一个印制电路板的铜铂作为散热器时是否可以正常工作.1.系统要求: VOUT=5.0V;VIN(MAX)=9.0V;VIN(MIN)=5.6V;IOUT=700mA;运行周期=100%;TA=50℃根据上面的系统要求选择750mA MIC2937A-5.0BU稳压器,其参数为: VOUT=5V±2%(过热时的最坏情况)TJ MAX=125℃.采用TO-263封装,θJC=3℃/W;θCS≈0℃/W(直接焊接在电路板上).2.初步计算: VOUT(MIN)=5V-5×2%=4.9VPD=(VIN(MAX)-VOUT(MIN))+IOUT+(VIN(MAX)×I)=[9V-4.9V]×700mA+(9V×15mA)=3W 温度上升的最大值, ΔT=TJ(MAX)-TA = 125℃-50℃=75℃;热阻θJA(最坏情况):ΔT/PD=75℃/3.0W=25℃/W.散热器的热阻, θSA=θJA-(θJC+θCS);θSA=25-(3+0)=22℃/W(最大).3.决定散热器物理尺寸: 采用一个方形、单面、水平具有阻焊层的铜箔散热层与一个有黑色油性涂料覆盖的散热铜箔,并采用1.3米/秒的空气散热的方案相比较,后者的散热效果最好.采用实线方案,保守设计需要5,000mm2的散热铜箔,即71mm×71mm(每边长2.8英寸)的正方形.4.采用SO-8和SOT-223封装的散热要求:在下面的条件下计算散热面积大小:VOUT=5.0V;VIN(MAX)=14V;VIN(MIN)=5.6V;IOUT=150mA;占空比=100%;TA=50℃.在允许的条件下,电路板生产设备更容易处理双列式SO-8封装的器件.SO-8能满足这个要求吗?采用MIC2951-03BM(SO-8封装),可以得到以下参数: TJ MAX=125℃;θJC≈100℃/W.5.计算采用SO-8封装的参数: PD=[14V-5V]×150mA+(14V×8mA)=1.46W;升高的温度=125℃-50℃=75℃;热阻θJA(最坏的情况): ΔT/PD=75℃/1.46W=51.3℃/W;θSA=51-100=-49℃/W(最大).显然,在没有致冷条件下,SO-8不能满足设计要求.考虑采用SOT-223封装的MIC5201-5.0BS调压器,该封装比SO-8小,但其三个引脚具有很好的散热效果.选用MIC5201-3.3BS,其相关参数如下: TJ MAX=125℃SOT-223的热阻θJC=15℃/WθCS=0 ℃/W(直接焊在线路板上的).6.计算采用SOT-223封装的结果:PD=[14V-4.9V]×150mA+(14V×1.5mA)=1.4W 上升温度=125℃-50℃=75℃;热阻θJA(最坏的情况): ΔT/PD=75℃/1.4W=54℃/W;θSA=54-15=39℃/W(最大).根据以上的数据,参考图1,采用1,400 mm2的散热铜箔(边长1.5英寸的正方形)可以满足设计要求.以上的设计结果可以作为粗略的参考,实际设计中需要了解电路板的热特性,得出更准确、满足实际设计的结果.散热器材料的选择: 散热片的制造材料是影响效能的重要因素,选择时必须加以注意!目前加工散热片所采用的金属材料与常见金属材料的热传导系数: 金 317 W/mK 银 429 W/mK 铝401 W/mK 铁 237 W/mK 铜 48 W/mK AA6061型铝合金 155 W/mK AA6063型铝合金 201 W/mK ADC12型铝合金 96 W/mK AA1070型铝合金 226 W/mK AA1050型铝合金 209 W/mK 热传导系数的单位为W/mK,即截面积为1平方米的柱体沿轴向1米距离的温差为1开尔文(1K=1℃)时的热传导功率.热传导系数自然是越高越好,但同时还需要兼顾到材料的机械性能与价格.热传导系数很高的金、银,由于质地柔软、密度过大、及价格过于昂贵而无法广泛采用;铁则由于热传导率过低,无法满足高热密度场合的性能需要,不适合用于制作计算机空冷散热片.铜的热传导系数同样很高,可碍于硬度不足、密度较大、成本稍高、加工难度大等不利条件,在计算机相关散热片中使用较少,但近两年随着对散热设备性能要求的提高,越来越多的散热器产品部分甚至全部采用了铜质材料.铝作为地壳中含量最高的金属,因热传导系数较高、密度小、价格低而受到青睐;但由于纯铝硬度较小,在各种应用领域中通常会掺加各种配方材料制成铝合金,寄此获得许多纯铝所不具备的特性,而成为了散热片加工材料的理想选择.各种铝合金材料根据不同的需要,通过调整配方材料的成分与比例,可以获得各种不同的特性,适合于不同的成形、加工方式,应用于不同的领域.上表中列出的5种不同铝合金中:AA6061与AA6063具有不错的热传导能力与加工性,适合于挤压成形工艺,在散热片加工中被广为采用.ADC12适合于压铸成形,但热传导系数较低,因此散热片加工中通常采用AA1070铝合金代替,可惜加工机械性能方面不及ADC12.AA1050则具有较好的延展性,适合于冲压工艺,多用于制造细薄的鳍片.风扇的选择: 风扇是风冷散热器中必不可少的组成部分,对散热效果起着至关重要的作用,是散热器中唯一的主动部件;同时,更对散热器的工作噪音有着决定性的影响.风扇在散热中的职责为:凭借自身的导流作用,令空气以一定的速度、一定的方式通过散热片,利用空气与散热片之间的热交换带走其上堆积的热量,从而实现“强制对流”的散热方式.散热片即使结构再复杂,也只是一个被动的热交换体;因此,一款风冷散热器能否正常“工作”,几乎完全取决于风扇的工作状态.在不改变散热器结构与其它组成部分的情况下,仅仅是更换更加合适、强劲的风扇,也可以令散热效果获得大幅度的提升;反之,如果风扇搭配不合适或不够强劲,则会使风冷散热器效能大打折扣,令散热片与整体设计上的优点被埋没于无形;更有甚者,由于风扇是风冷散热器中唯一确实“工作”的部分,它本身的故障也就会导致散热器整体的故障,令其丧失大部分的散热性能,进而引起系统的不稳定或当机,甚至因高温而烧毁设备.风扇可分为:含油轴承、单滚珠轴承、双滚珠轴承、液压轴承、来福轴承、Hypro轴承、磁悬浮轴承、纳米陶瓷轴承等,下面是其性能比较表从由表中可以看出,轴承技术对风扇的性能、噪音、寿命起着重要的决定性作用,实际选购风扇时必须加以注意.通常可根据性能、噪音、寿命以及价格四方面要求综合考虑:1.性能不高,噪音小,价格低,含油轴承是唯一的选择,但寿命较短,使用一段时间后噪音可能会逐渐增大,需做好维护或更换的心理准备.2.性能强悍,寿命长,价格不高,滚珠轴承是不二之选,但需忍受其工作时产生的较大噪音.3.性能与噪音都没有特殊要求,但希望寿命长,价格不高,来福、Hypro轴承等含油轴承的改进型均是值得考虑的选择.4.性能好,噪音低,寿命长,如此便不能对价格提出进一步的要求了,只要资金充足,液压、精密陶瓷等特色轴承技术都可列入选择范围之内.5.对静音与寿命要求极高,磁悬浮轴承是仅有的选择,只是性能不佳,价格过高.第二篇:开关电源设计笔记1.开关电源设计前各参数以NXP的TEA1832图纸做说明。
MOSFET损耗计算

MOSFET损耗计算MOSFET(金属-氧化物-半导体场效应晶体管)是一种常用的功率开关器件,广泛应用于电力电子领域。
在使用MOSFET进行功率开关时,会产生一定的损耗,包括导通损耗和关断损耗。
正确计算MOSFET的损耗对于设计和选择合适的散热系统非常重要,下面将详细介绍MOSFET的损耗计算方法。
1.导通损耗计算:导通损耗是指MOSFET在导通状态下产生的功耗。
导通损耗可以通过以下公式计算:P_cond = I^2 * Rds(on)其中,P_cond为导通损耗,I为MOSFET的导通电流,Rds(on)为MOSFET的导通电阻。
导通损耗主要由两部分组成:静态导通损耗和动态导通损耗。
静态导通损耗是指MOSFET在导通状态下的稳态功耗,可以通过上述公式计算得到。
动态导通损耗是指由于MOSFET的导通电阻在开关过程中的变化引起的功耗,通常可以通过MOSFET的参数手册或者开关特性曲线来得到。
2.关断损耗计算:关断损耗是指MOSFET在关断状态下产生的功耗。
关断损耗由MOSFET 的关断电流和关断电压引起,可以通过以下公式计算:P_sw = Vds * Id * t_sw其中,P_sw为关断损耗,Vds为MOSFET的关断电压,Id为MOSFET 的关断电流,t_sw为关断时间。
关断损耗由两部分组成:静态关断损耗和动态关断损耗。
静态关断损耗是指MOSFET在关断状态下的稳态功耗,可以通过上述公式计算得到。
动态关断损耗是指由于开关过程中MOSFET的关断电流和关断时间的变化引起的功耗,通常可以通过MOSFET的参数手册或者开关特性曲线来得到。
3.总损耗计算:总损耗是指MOSFET在导通和关断状态下产生的功耗之和。
总损耗可以通过以下公式计算:P_total = P_cond + P_sw4.散热设计:4.1确定MOSFET的最大工作温度,一般来说,MOSFET的最大工作温度应该低于其额定温度。
4.2 计算MOSFET的热阻(Rth):Rth = (Tj - Ta) / P_total其中,Tj为MOSFET的结温,Ta为环境温度,P_total为MOSFET的总损耗。
电子产品散热设计

YEALINK电子产品散热设计经营乐享2012-12-4电子产品的散热设计一、为什么要进行散热设计在调试或维修电路的时候,我们常提到一个词“**烧了”,这个**有时是电阻、有时是保险丝、有时是芯片,可能很少有人会追究这个词的用法,为什么不是用“坏”而是用“烧”?其原因就是在机电产品中,热失效是最常见的一种失效模式,电流过载,局部空间内短时间内通过较大的电流,会转化成热,热**不易散掉,导致局部温度快速升高,过高的温度会烧毁导电铜皮、导线和器件本身。
所以电失效的很大一部分是热失效。
高温对电子产品的影响:绝缘性能退化;元器件损坏;材料的热老化;低熔点焊缝开裂、焊点脱落。
温度对元器件的影响:一般而言,温度升高电阻阻值降低;高温会降低电容器的使用寿命;高温会使变压器、扼流圈绝缘材料的性能下降,一般变压器、扼流圈的允许温度要低于95C;温度过高还会造成焊点合金结构的变化—IMC增厚,焊点变脆,机械强度降低;结温的升高会使晶体管的电流放大倍数迅速增加,导致集电极电流增加,又使结温进一步升高,最终导致元件失效。
那么问一个问题,如果假设电流过载严重,但该部位散热极好,能把温升控制在很低的范围内,是不是器件就不会失效了呢?答案为“是”。
由此可见,如果想把产品的可靠性做高,一方面使设备和零部件的耐高温特性提高,能承受较大的热应力(因为环境温度或过载等引起均可);另一方面是加强散热,使环境温度和过载引起的热量全部散掉,产品可靠性一样可以提高。
二、散热设计的目的控制产品内部所有电子元器件的温度,使其在所处的工作环境条件下不超过标准及规范所规定的最高温度。
最高允许温度的计算应以元器件的应力分析为基础,并且与产品的可靠性要求以及分配给每一个元器件的失效率相一致。
三、散热设计的方法1、冷却方式的选择我们机电设备常见的是散热方式是散热片和风扇两种散热方式,有时散热的程度不够,有时又过度热设计、冷却方式、散热器、热管技术散热了,那么何时应该散热,哪种方式散热最合适呢?这可以依据热流密度来评估,热流密度=热量/ 热通道面积。
DCDC变换器热损耗分析与散热系统设计工具

DCDC变换器热损耗分析与散热系统设计工具DCDC变换器是一种常见的电力转换器件,用于将电源中的直流电压转换为所需的电压等级。
然而,这种转换过程通常伴随着热损耗的产生,如果不能有效地散热,可能会导致变换器的过热甚至损坏。
因此,在DCDC变换器的设计过程中,热损耗的分析和散热系统的设计变得至关重要。
热损耗分析是DCDC变换器设计中不可或缺的一步。
热损耗的分析能够帮助工程师们了解电路中的功耗分布,并确定哪些部分会产生较大的热量。
一般来说,DCDC变换器的主要热源包括开关管、电感和电容等元件。
通过对这些元件的热耦合和传导进行深入分析,可以准确计算出它们的热损耗,并进而为散热系统的设计提供依据。
在热损耗分析之后,散热系统的设计就成为了关注的重点。
散热系统的设计需要综合考虑多个因素,如空间限制、散热材料的选择和散热结构等。
首先,根据电路板的尺寸和布局,确定散热器的大小和形状。
然后,选择合适的散热材料,如铝、铜或其他导热性能良好的材料,以提高散热效果。
最后,根据热损耗分析的结果,设计合适的散热结构,如散热片、散热鳍片或导热管等,以增加散热面积和散热效率。
为了更方便地进行DCDC变换器的热损耗分析和散热系统的设计,工程师们通常会使用专门的工具。
这些工具通常包括热仿真软件和散热设计软件。
热仿真软件可以帮助工程师们建立准确的热传导模型,并进行热分析和热仿真,以预测变换器在不同工况下的温度分布。
散热设计软件则可以提供各种散热器的参数选择和设计方案,如散热片的数量和尺寸、风扇的转速和风量等,以满足变换器的散热需求。
综上所述,DCDC变换器的热损耗分析和散热系统的设计是变换器设计过程中十分重要的一环。
通过准确的热损耗分析和合理的散热系统设计,可以有效地避免变换器的过热问题,提高系统的可靠性和稳定性。
同时,借助热仿真软件和散热设计软件等工具,可以帮助工程师们更快、更准确地完成DCDC变换器的设计工作。
总结:本文描述了DCDC变换器热损耗分析与散热系统设计工具的重要性以及设计的基本步骤。
变频器中的IGBT模块损耗计算及散热系统设计

变频器中的IGBT模块损耗计算及散热系统设计一、本文概述随着电力电子技术的快速发展,变频器作为电能转换与控制的核心设备,在工业自动化、新能源发电、电动汽车等领域得到了广泛应用。
绝缘栅双极晶体管(IGBT)作为变频器的关键功率器件,其性能直接影响到变频器的效率和可靠性。
IGBT模块的损耗计算和散热系统设计是变频器设计中的重要环节,对于提高变频器性能、降低运行成本、延长设备寿命具有重要意义。
本文旨在探讨变频器中IGBT模块的损耗计算方法和散热系统设计原则。
我们将分析IGBT模块的工作原理和损耗产生机制,包括通态损耗、开关损耗等。
在此基础上,我们将介绍损耗计算的数学模型和计算方法,以及如何通过实验手段验证计算结果的准确性。
我们将重点讨论散热系统的设计原则和优化方法,包括散热器结构设计、散热风扇的选择与控制、散热系统的热仿真分析等。
本文将总结一些实际应用中的经验教训,提出针对IGBT模块损耗计算和散热系统设计的优化建议,为变频器设计工程师提供有益的参考。
通过本文的研究,我们期望能够为变频器设计中的IGBT模块损耗计算和散热系统设计提供理论支持和实践指导,推动变频器技术的持续发展和应用创新。
二、IGBT模块损耗计算绝缘栅双极晶体管(IGBT)是变频器中的关键元件,其性能直接影响变频器的效率和可靠性。
IGBT模块的损耗计算是散热系统设计的基础,对于确保变频器的稳定运行具有重要意义。
IGBT模块的损耗主要包括通态损耗和开关损耗两部分。
通态损耗是指IGBT在导通状态下,由于电流通过而产生的热量损耗。
开关损耗则发生在IGBT的开通和关断过程中,由于电压和电流的乘积在时间上的积分不为零,导致能量损失。
通态损耗的计算公式为:Pcond = Icoll * Vce(sat),其中Icoll 为集电极电流,Vce(sat)为饱和压降。
饱和压降是IGBT导通时电压降的一个重要参数,它与集电极电流、结温和门极电流等因素有关。
有关散热器设计
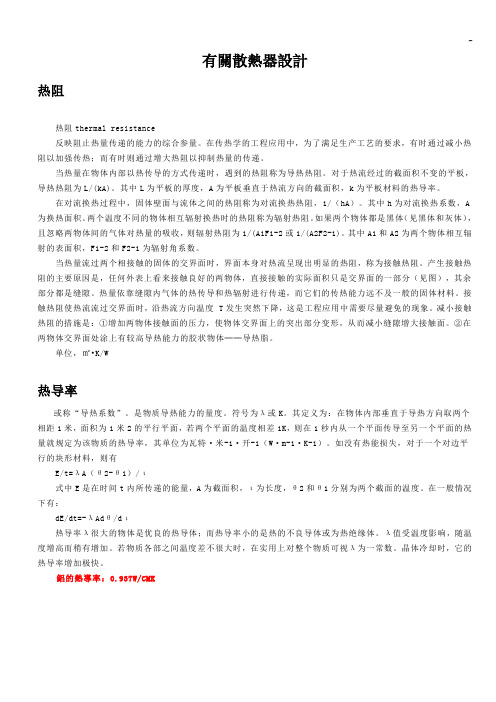
有關散熱器設計热阻热阻thermal resistance反映阻止热量传递的能力的综合参量。
在传热学的工程应用中,为了满足生产工艺的要求,有时通过减小热阻以加强传热;而有时则通过增大热阻以抑制热量的传递。
当热量在物体内部以热传导的方式传递时,遇到的热阻称为导热热阻。
对于热流经过的截面积不变的平板,导热热阻为L/(kA)。
其中L为平板的厚度,A为平板垂直于热流方向的截面积,k为平板材料的热导率。
在对流换热过程中,固体壁面与流体之间的热阻称为对流换热热阻,1/(hA)。
其中h为对流换热系数,A 为换热面积。
两个温度不同的物体相互辐射换热时的热阻称为辐射热阻。
如果两个物体都是黑体(见黑体和灰体),且忽略两物体间的气体对热量的吸收,则辐射热阻为1/(A1F1-2或1/(A2F2-1)。
其中A1和A2为两个物体相互辐射的表面积,F1-2和F2-1为辐射角系数。
当热量流过两个相接触的固体的交界面时,界面本身对热流呈现出明显的热阻,称为接触热阻。
产生接触热阻的主要原因是,任何外表上看来接触良好的两物体,直接接触的实际面积只是交界面的一部分(见图),其余部分都是缝隙。
热量依靠缝隙内气体的热传导和热辐射进行传递,而它们的传热能力远不及一般的固体材料。
接触热阻使热流流过交界面时,沿热流方向温度 T发生突然下降,这是工程应用中需要尽量避免的现象。
减小接触热阻的措施是:①增加两物体接触面的压力,使物体交界面上的突出部分变形,从而减小缝隙增大接触面。
②在两物体交界面处涂上有较高导热能力的胶状物体──导热脂。
单位,㎡•K/W热导率或称“导热系数”。
是物质导热能力的量度。
符号为λ或K。
其定义为:在物体内部垂直于导热方向取两个相距1米,面积为1米2的平行平面,若两个平面的温度相差1K,则在1秒内从一个平面传导至另一个平面的热量就规定为该物质的热导率,其单位为瓦特·米-1·开-1(W·m-1·K-1)。
svg热损耗计算及散热设计

DOI:10.3969/j.issn.2095-509X.2019.12.017SVG热损耗计算及散热设计张中胜ꎬ于海波ꎬ盛晓东ꎬ刘国伟(南京南瑞继保工程技术有限公司ꎬ江苏南京㊀211102)摘要:可靠的散热设计是SVG产品长期稳定运行的关键ꎬ在详细分析IGBT模块热功耗构成的基础上ꎬ通过ICEPAK热仿真软件对某SVG产品的整机热设计进行全面优化ꎬ最终实现温升低于37K㊁保证SVG产品长期稳定运行的控制目标ꎬ并结合实验测试验证了设计数据ꎮ关键词:SVGꎻ热损耗计算ꎻ离心风机ꎻICEPAKꎻ风冷散热器中图分类号:TM762㊀㊀㊀文献标识码:A㊀㊀㊀文章编号:2095-509X(2019)12-0076-04㊀㊀静止无功发生器(staticvargeneratorꎬSVG)依靠大功率电力电子器件的高频开关实现无功能量的变换ꎮ基本原理是将自换相桥式拓扑电路通过电抗器直接并联在电网上ꎬ通过调节桥式电路交流侧输出电压的相位和幅值或者直接控制其交流侧电流相位或幅值ꎬ实现动态无功补偿的目的ꎮSVG系统工作时ꎬ功率器件在开通㊁关断过程中会产生大量的功率损耗ꎬ产生的损耗会以热量的形式耗散出来[1]ꎬ因此能否保证SVG系统可靠散热ꎬ对SVG系统运行寿命至关重要ꎮ本文以某SVG系统为例ꎬ对产品的散热设计进行了较为详细的阐述ꎮ1㊀SVG系统介绍无功补偿技术发展历程是一个不断创新㊁发展㊁完善的过程ꎬ如图1所示ꎮ其经历了固定补偿㊁以调压调容(VCQV/TSC)的方式进行无功补偿㊁动态无功补偿等阶段ꎮ图1㊀无功补偿技术发展历程图㊀㊀SVG系统装置可提供连续快速可调的感性和容性无功ꎬ装置无级动态补偿调节范围大ꎬ响应速度快[2]ꎬ整机响应时间<5msꎮ同时控制灵活ꎬ可单独补偿电压㊁无功㊁功率因数ꎬ各种模式可无缝切换ꎮSVG系统完全能满足电网无功补偿及谐波治理的要求ꎬ是目前最先进的无功补偿技术之一ꎮ2㊀功率模块功耗计算在SVG系统中ꎬIGBT模块是控制整个系统关断㊁整流逆变的核心器件ꎬSVG系统运行时IGBT模块会产生大量的热量ꎬ是SVG系统损耗的主要来源ꎮIGBT模块损耗包括通态损耗和开关损耗ꎬ将IGBT的输出特性曲线运用线性化思想近似为一条直线ꎬ由于开关过程分为开通㊁关断和恢复3个时刻[3]ꎬ因此相应地将IGBT模块的总损耗分为4部分ꎬ即通态损耗㊁开通损耗㊁关断损耗和恢复损耗ꎮ本文所述SVG系统的工作参数见表1ꎮ表1㊀SVG系统工作参数参数数值额定集电极电流ICN/A650SVG额定电流ICQ/A462额定压降VCEN/V1.6额定的开通时间trN/μs0.12额定关断时间tfN/μs0.57反向恢复时的额定峰值电流IrrN/A653续流二极管反向恢复时间trrN/μs0.50IGBT开启电压VCE0/V1.0续流二极管门槛电压VF0/V1.0集电极峰值电流ICM/A653集电极电压Vcc/V1000开关频率fs/Hz450㊀㊀把各个参数数值代入损耗计算公式ꎬ得到IG ̄BT模块各部分损耗值如下ꎮ收稿日期:2018-06-29作者简介:张中胜(1985 )ꎬ男ꎬ工程师ꎬ硕士ꎬ主要从事电力系统一次设备的结构设计工作ꎬzhangzs@nari-relays.com.67 2019年12月㊀㊀㊀㊀㊀㊀㊀㊀㊀㊀㊀㊀㊀㊀㊀㊀机械设计与制造工程㊀㊀㊀㊀㊀㊀㊀㊀㊀㊀㊀㊀㊀㊀㊀㊀㊀Dec.2019第48卷第12期㊀㊀㊀㊀㊀㊀㊀㊀㊀MachineDesignandManufacturingEngineering㊀㊀㊀㊀㊀㊀㊀㊀㊀㊀㊀Vol.48No.12㊀㊀1)通态损耗Pfw/VꎮPfw/V=12πʏπ0νCEiCδdα=12πʏπ0(VCE0+rCEsinα)ˑ(ICMsinα)ˑ{12[1+Msin(α+θ)]}dα=(18+Mcosθ3π)VCEN-VCEOICNI2CM+(12π+Mcosθ8)ˑVCE0ICM=232W式中:νCE为IGBT的通态电压ꎻδ为占空比ꎻiC为集电极电流ꎻrCE为通态电阻ꎻM为调制度ꎻθ为电压和电流之间的相角ꎻα为调制角度ꎮ2)开通损耗PonꎮPon=18VcctrNI2CMICNfs=4.5W3)关断损耗PoffꎮPoff=VccICMtfNfs(13π+124ICMICN)=25W4)恢复损耗Prrꎮ开通IGBT时其集电极电流达到iC后会继续上升ꎬ一直达到峰值后再下降到iCꎬ因此会出现一段超调量ꎮPrr=fsEoff=fsVcc{[0.28+0.38ICMπICN+0.015ˑ(ICMICN)2]ˑIrrNtrrN2+(0.8π+0.05ICMICN)ICMtrrN}=75W式中:Eoff为功率谱密度ꎮ综上ꎬ1个IGBT模块由4个IGBT器件(注:本文所述的1个IGBT模块封装中含有2个IGBT器件)和1个电阻组成ꎬ电阻损耗值为100Wꎬ所以单模组总的热损耗PIGBT为:PIGBT=2ˑ2ˑ(Pfw/V+Pon+Poff+Prr)+100=1446W3㊀散热仿真计算3.1㊀冷却方式选择对于SVG等大功率大损耗系统ꎬ自然冷却是无法满足设计需求的ꎮ常规的强迫冷却方式主要有风冷㊁水冷和油冷ꎮ鉴于水冷和油冷成本高ꎬ维护工作量大等原因ꎬ本文采用强迫风冷[4]进行系统冷却ꎮSVG功率单元在柜体内呈阵列放置ꎬ为保证功率单元的风量均匀性ꎬ选用离心风机进行抽风冷却ꎮ3.2㊀结构描述图2为SVG散热器热源分布图ꎬ其中2个IG ̄BT模块和1个电阻安装在散热器上组成散热器组件ꎮ散热器组件和电容㊁控制板卡等共同组成SVG功率单元ꎬ如图3所示ꎮ6个功率单元分3层放置于1个功率柜体内ꎬ功率柜后侧安装1个离心风机ꎬSVG功率柜结构如图4所示ꎮ图2㊀SVG散热器热源分布图㊀图3㊀SVG功率单元结构3.3㊀热仿真计算模型搭建根据2中计算的损耗结果ꎬ结合IGBT模块和电阻尺寸ꎬ散热器尺寸选定为260mmˑ380mmˑ100mmꎬ材质选用常规的6061ꎬ单齿厚度1.5mmꎬ相邻齿中心距为4mmꎮ根据允许温升和理论计算的功率损耗ꎬ本散热器的热阻为:热阻=温升损耗=371446=0.026K/W在ICEPAK软件中建立散热器组件模型和功率柜模型[5]ꎬ如图5和图6所示ꎮ㊀图4㊀SVG功率柜结构㊀㊀㊀图5㊀ICEPAK软件中散㊀㊀㊀㊀㊀㊀㊀㊀㊀㊀㊀㊀㊀㊀㊀㊀热器组件模型图6㊀ICEPAK软件中SVG功率柜模型77 2019年第12期㊀㊀㊀㊀㊀㊀㊀㊀㊀㊀㊀㊀张中胜:SVG热损耗计算及散热设计3.4㊀风机选型影响散热器性能的主要因素有散热器体积㊁热源位置㊁热源热密度以及风量ꎮ其中ꎬ风量与风机性能直接相关ꎮ风机选型和散热器的设计往往是相互依赖㊁相互调整㊁相互仿真适配的过程ꎮ柜体风道路径复杂ꎬ功率单元数量多ꎬ对风量要求高ꎬ对不同散热器的风冷均匀性要求较高ꎮ综合以上几点ꎬ离心风机更适合SVG类产品ꎮ经过对EBM厂家离心风机规格参数的研究ꎬ选择R3G-400-AQ23型号风机ꎬ风量风压曲线如图7所示ꎮ图7㊀R3G-400-AQ23风量风压曲线㊀㊀通过ICEPAK仿真模型计算ꎬ可以得到各个功率单元风量分布ꎬ如图8所示ꎮ图8㊀各功率单元风量分布图㊀㊀风量计算结果表明ꎬ单个散热器的风量最小为350CFMꎬ环境温度设定为40ħꎬ利用此边界条件计算单个散热器的温升ꎬ散热器仿真计算结果温度分布如图9所示ꎮ㊀㊀由图可知ꎬR3G-400-AQ23风机下散热器的最高温度为75.8ħꎬ满足设计需求ꎮ图9㊀散热器仿真计算结果温度分布云图4㊀试验为了验证仿真结果的可靠性ꎬ本文对所设计散热器进行试验验证.试验分两步:第一步ꎬ测试单个散热器散热能力ꎻ第二步ꎬ进行工程现场测量ꎬ即在SVG满功率运行状态下测试散热器散热能力ꎮ通过和仿真计算值进行对比ꎬ验证热设计的正确性ꎮ4.1㊀散热器试验在单个散热器实验测量中ꎬ使用可加热铜块代替IGBT模块ꎬ铜块外形尺寸和IGBT尺寸相同ꎬ紧固螺钉也相同ꎮ每个可加热铜块通过单独的直流源装置控制功耗ꎬ风量定为350CFMꎮ在散热器上特定的点布置两个热电耦ꎬ进行温度值测试采集ꎮ待系统稳定后(各测点温度值的变化稳定在1ħ范围内)ꎬ进行测量读数ꎮ测试时环境温度为24ħꎬ试验针对监测点仿真温升与实测温升进行对比ꎬ相关结果见表2ꎮ表2㊀仿真温升与实测温升对比表实测温升/ħ仿真温升/ħ误差/ħ监测点133.035.12.1监测点234.635.81.2㊀㊀由表2可知ꎬ实测温升与仿真温升的误差在3ħ以内ꎬ即误差在允许范围内ꎬ说明仿真数据是可靠的ꎮ4.2㊀实机满功率试验为进一步验证仿真的可靠性ꎬ选择在工程现场进行测试ꎮ需要指出的是ꎬ产品测温设备采用常规的PT100设备ꎬ如图10所示ꎮ由于其有一定的体积且需要与功率单元其他零件接线ꎬ因此PT100设备并不能放置到IGBT的正下方ꎬ选择将PT100放置于两个IGBT中间仿真温度最高的地方ꎮ新疆地区某SVG工程现场温度监控结果如图11所示ꎮ872019年第48卷㊀㊀㊀㊀㊀㊀㊀㊀㊀㊀㊀㊀㊀㊀㊀机械设计与制造工程㊀㊀㊀㊀㊀㊀㊀㊀㊀㊀㊀㊀㊀㊀㊀㊀㊀㊀㊀㊀㊀㊀图10㊀PT100设备㊀㊀图11㊀新疆地区某SVG工程㊀㊀㊀㊀㊀㊀㊀㊀㊀㊀㊀㊀㊀㊀现场温度监控图㊀㊀采集时间为2016年12月24日凌晨3点ꎬ环境温度为-2ħꎮ仿真温升与系统实测温升对比结果见表3ꎮ表3㊀仿真温升与系统实测温升对比表SVGA相功率单元实测温度/ħ温升/ħ仿真温升/ħ仿真与实测差值/ħ功率单元1283031.91.9功率单元2272931.22.2功率单元3272932.03.0功率单元4272931.52.5功率单元5272931.12.1功率单元6272931.02.0平均值27.229.232.12.9㊀㊀从表3可以看出ꎬ仿真温升和实测温升误差在3ħ以内ꎮ考虑到热电耦的传递损耗热阻等因素ꎬ可以认为针对IGBT损耗的热设计是可靠㊁准确的ꎮ5㊀结论本文通过功耗计算㊁热仿真㊁试验测试等工作ꎬ完成了整个SVG产品的热设计ꎬ计算结果表明:1)推导计算出的IGBT器件损耗是正确的ꎮ2)仿真计算数据与实测数据的误差在ʃ10%范围内ꎬ仿真计算的结果可以有效指导散热器的设计ꎬ提升产品研发效率ꎮ3)所设计的散热器可有效控制IGBT模块的温升ꎬ满足SVG散热设计的目标ꎮ参考文献:[1]㊀张明元ꎬ沈建清ꎬ李卫超ꎬ等.一种快速IGBT损耗计算方法[J].船电技术ꎬ2009ꎬ29(1):33-36.[2]㊀李超ꎬ崔大明ꎬ侯庆雷.关于电力系统动态无功功率优化调度的探讨[J].科技传播ꎬ2015(18):46ꎬ56.[3]㊀杜毅ꎬ廖美英.逆变器中IGBT模块的损耗计算及其散热系统设计[J].电气传动自动化ꎬ2011ꎬ33(1):42-46. [4]㊀郭永生ꎬ王志坚.大功率器件IGBT散热分析[J].山西电子技术ꎬ2010(3):16-18.[5]㊀毛志云ꎬ王艳ꎬ姚志国ꎬ等.基于ICEPAK的SVG功率柜散热系统分析[J].电气技术ꎬ2016(1):72-86.SVGheatlosscalculationandheatdissipationdesignZhangZhongshengꎬYuHaiboꎬShengXiaodongꎬLiuGuowei(NanjingNRJibaoElectricCo.ꎬLtd.ꎬJiangsuNanjingꎬ211102ꎬChina)Abstract:Theheatdissipationdesignisakeyfactorwhichaffectsthelong ̄termreliableoperationofSVGprod ̄ucts.OnthebasisofanalysisforthethermalpowerconsumptionofIGBTmodulesꎬitcomprehensivelyoptimizesthethermaldesignofaSVGproductwithICEPAKsoftwareꎬrealizesthatthetemperatureriseislowerthan37K.Thisensuresthelong ̄termstableoperationofSVGproducts.Thepapershowsthattheexperimentaltestsverifytheabovedesigndata.Keywords:SVGꎻcalculationofthermallossꎻcentrifugalfanꎻICEPAKꎻaircooledradiator972019年第12期㊀㊀㊀㊀㊀㊀㊀㊀㊀㊀㊀㊀张中胜:SVG热损耗计算及散热设计。
散热方案设计

散热方案设计散热方案设计是建筑、电力、能源等领域中不可或缺的一部分。
它的热学计算和方案设计,有着多方面的应用。
为确保建筑物的安全、节能、稳定运行,散热方案设计是必须要进行的工作。
一、散热方案设计中的重要性建筑物在使用过程中,由于自身存在损耗和外界环境的影响,会产生较高的热量。
通过合理的散热方案设计,减少热量对建筑物和周围环境的影响,保证建筑物稳定运行。
另外,对于某些高温设备,由于产生过多的热量,必须通过散热方案设计进行降温,并将热量排出。
这类设备包括工业生产中的加工设备、冷却塔、空调机组等等。
所以,散热方案设计的重要性不容忽视。
二、散热方案设计的要素(一)散热族群散热族群是指需要使用散热器、散热风扇等器材进行散热的设备和系统。
散热族群中,还可分为制冷设备和制热设备。
(二)散热器散热器是散热方案设计中重要的组成部分。
它通过内外通道和管道的对应关系,实现热传递的目的。
散热器的材料、结构和位置的不同,对其散热效率有着显著的影响。
(三)气流与温度分布气流和温度分布是散热方案设计中的要素,对散热器的放置、数量和大小都有着影响。
(四)散热支持部件散热方案设计还需要考虑散热支持部件,包括散热风扇、散热减震器、电路板等等。
三、如何进行(一)根据散热族群进行分类分类有助于确定每种设备所需散热器的数量和大小。
在分类的基础上,通过选择散热器和确定散热器的放置位置、数量和大小等,来实现散热方案的设计。
(二)选用合适的散热器散热器的选用应该考虑到散热器的材料、结构和散热面积,以及与之配套的散热风扇和管道的匹配。
为最优化散热方案,应该强调散热效率和能耗情况。
(三)考虑气流分布与温度分布散热器的放置、数量和大小,会对气流和温度分布产生影响。
为确保良好的气流分布与温度分布,可通过实验室模拟仿真和现场实测来确定实际情况,并进行相应的调整。
(四)进行完整的散热系统设计散热系统设计也是散热方案设计中的重要部分。
合适的散热风扇、管道、电路板等支持部件,需要与散热器进行匹配,构成合适的散热系统。
- 1、下载文档前请自行甄别文档内容的完整性,平台不提供额外的编辑、内容补充、找答案等附加服务。
- 2、"仅部分预览"的文档,不可在线预览部分如存在完整性等问题,可反馈申请退款(可完整预览的文档不适用该条件!)。
- 3、如文档侵犯您的权益,请联系客服反馈,我们会尽快为您处理(人工客服工作时间:9:00-18:30)。
第8章 损耗与散热设计开关电源是功率设备,功率元器件损耗大,损耗引起发热,导致元器件温度升高,为了使元器件温度不超过最高允许温度,必须将元器件的热量传输出去,需要散热器和良好的散热措施,设备的体积重量受到损耗限制。
同时,输出一定功率时损耗大,也意味着效率低。
8.1热传输电子元器件功率损耗以热的形式表现出来,热能积累增加元器件内部结构温度,元器件内部温度受最高允许温度限制,必须将内部热量散发到环境中,热量通过传导、对流和辐射传输。
当损耗功率与耗散到环境的功率相等时,内部温度达到稳态。
1. 传导传导是热能从一个质点传到下一个质点,传热的质点保持它原来的位置的传输过程,如图8-1固体内的热传输。
热量从表面温度为T 1的一端全部传递到温度为T 2的另一端,单位时间传递的能量,即功率表示为 T R T l T T A P ∆=-=)(21λ (8-1) 式中 Al R T λ= (8-2) 称为热阻(℃/ W );l -热导体传输路径长度(m);A -垂直于热传输路径的导体截面积(m 2);λ-棒材料的热导率(W/m ℃),含90%铝的热导率为220W/ m ℃,几种材料的热导率如表8-1所示;ΔT =T 1-T 2温度差(℃)。
例:氧化铝绝缘垫片厚度为0.5mm ,截面积2.5cm 2,求热阻。
解:由表8-1查得λ=20 W/m ℃,根据式(8-2)得到340.5100.120 2.510t R --⨯==⨯⨯℃/ W 式(8-1)类似电路中欧姆定律:功率P 相当于电路中电流,温度差;ΔT 相当于电路中电压。
半导体结的热量传输到周围空气必然经过几种不同材料传输,每种材料有自己的热导率,截面积和长度,多层材料的热传输可以建立热电模拟的热路图。
图8-2是功率器件由硅芯片的热传到环境的热通路(a)和等效热路(b)。
由结到环境的总热阻为 sa cs jc js RR RR ++= (8-3) 上式右边前两个热阻可以按式(8-2)计算,最后一项的热阻在以后介绍的方法计算。
如果功率器件损耗功率为P ,则结温为 a sa cs jc j T R R R P T +++=)( (8-4) 式中R jc , R cs 及R sa 分别表示芯片结到管壳,管壳到散热器和散热器到环境热阻。
除了散热器到环境的热阻R sa 外,其余两个热阻可以按式(8-2)计算。
2 图8-1 热隔离的棒能量传输(a)(b) 图8-2功率器件热传输和等效热路图从式(8-4)可见,要使结温T j 不超过最高允许温度T jM ,应当器件降低功耗P ,或者减少热阻。
一定的封装,决定了管壳和芯片结构,也就决定了结到壳的内热阻R jc 。
如果希望R jc 小,热传输路径l 要尽可能短,但受到器件承受的电压、机械平整度等限制;还要使传输截面积尽可能大,但这受到例如寄生电容等限制。
封装一般采用高热导率材料减小热阻。
高功率器件直接安装在空气冷却,甚至水冷散热器上。
尽量减少结到壳热阻R jc ,一般可以小于1W/℃。
手册中常给出结到壳热阻R jc ,最高允许结温T jM 和最大允许损耗P M ,或最高允许结温T jM 最大允许功率损耗P M 和允许壳温T c 。
如果是后者,根据已知数据就可以知道结到壳热阻 jM cjc M T T R P -= W/℃ (8-5)壳到散热器通常有一层绝缘导热垫片,绝缘垫片可以用氧化铝、氧化铍、云母或其他绝缘导热材料。
壳到散热器热阻R cs 包含两部分:绝缘垫片热阻和接触热阻。
绝缘导热垫片热阻可按式(8-2)计算。
例如用于TO -3封装的75μm 绝缘云母片热阻大约1.3℃/ W 。
但是,固体表面再好精加工,表面总是点接触,存在很大接触热阻,应当施加适当的装配压力,增大接触面,即便如此,表面之间仍有空气隙存在,对热阻影响很大。
太大的压力会使器件内部结构变形,可能适得其反,一般使用力矩板手保证确定的压力,又不致器件安装变形。
同时,材料接触表面应当平整、无瘤、坑,并在适当压力的前提下,绝缘垫片涂有混合导热良好氧化锌的硅脂,驱赶表面间空气,使接触热阻下降50%~30%。
TO3封装当涂有硅脂或导热材料时热阻大约0.4℃/ W 。
如果应用复合材料过多,层太厚将增加热阻。
接触热阻可按下式计算 'cs R A β= W/℃ (8-6)A 为接触表面积,cm 2;β-金属对金属为1,金属对阳极化为2;如果有硅脂分别为0.5和1.4。
2. 瞬态热抗众所周知,物体在传输热量之前,必须吸收一定的热能加热本身到高于环境的相应温度;而当热源去掉后,这部分热能经过一定时间释放掉,温度降低到环境温度。
这相似电容的充电和放电效应。
在热电模拟等效热路中引入热容的概念。
在电源开机、关机和瞬态过载等情况下,功率器件往往在瞬间损耗(浪涌)大大超过平均损耗,引起芯片结温瞬间升高,结温是否超过最大允许结温,这与功率浪涌持续时间以及器件的热特性有关。
在瞬态情况下,热传输的热路中必须考虑热容C s 。
材料的单位体积(或质量)的热容定义为热能Q 相对于材料温度T 的变化率,即 /v dQ dT C = 其中C v 是单位体积热容,每度(K )单位体积的焦耳,或称为比热。
对于矩形截面A 材料,长度(热传输方向)d 的热容C s 如下 s v C C Ad = (8-7) 结温瞬态特性类似于电力传输线,等效电路方程的解很复杂。
通过热电模拟可以得到方程的近似解,稳态模型如图8-2所示。
如果输入功率P(t)是阶跃函数(图8-3(a)),考虑热容的等效热路如图8-3(a)所示,短时间温升T j (t)为()120()4/j t s a T t P t R C T π=+⎡⎤⎣⎦ (8-8)式中P 0为功率阶跃幅值,并假定t 小于热时间常数近似解为/4t s R C τπ= (8-9)Pa t(c) 图8-3 等效热路瞬态热抗(a),阶跃输入(b)和瞬态热阻抗响应如果时间大于时间常数τ,T j 接近稳态值P 0R t +T a 。
图的纵轴T j /P 0是瞬态热阻抗Z t (t)=T j (t)/P 0。
但是,热传输相似于电网传输线,不是集中参数,热时间常数不能简单使用类似电路中的RC 时间常数。
式(8-9)是时间小于τ时的级数展开项,是t 的1/2次方,而不是简单的指数关系。
在实际器件中,热传输路径中不是一种材料,而是多种材料的多层结构,实际热系统是非线性高阶系统。
制造厂在功率器件手册中常提供如图8-4所示的瞬态阻抗曲线。
如果输入功率的时间函数已知,可以利用热抗曲线预计结温:()()()j a T t P t Z t T =+ (8-10)例如,IRFI4905通过启动时瞬时矩形功率脉冲150W ,脉冲宽度20μs ,占空比D =0.2,查得Z tjc =0.53W/℃,环境温度35 ℃于是1500.5335114.5j T =⨯+=℃实际上,功率脉冲一般不是矩形的,可以用幅值相等、能量(功率时间积分)相等原则求出脉冲宽度。
3. 散热器在式(8-3)中,我们已经解决了R jc 和R cs ,前者由器件厂商提供,后者可以根据绝缘要求选取适当的材料计算求得。
在一定的损耗功率P 时,要选择恰当的散热器,保证器件结温不超过最大允许结温。
目前使用的散热器平板、叉指型和翼片铝型材。
自然冷却散热器翼片之间的距离较大,至少应当10~15mm 。
散热器表面黑色阳极化使热阻减少25%,但成本增加。
自然对流冷却热时间常数在4~15分钟。
如果加风扇,热阻下降,使得散热器小而轻,同时也减少热容C s 。
对于强迫风冷散热器大大小于自然对流冷却散热器。
强迫风冷散热器的热时间常数典型值可以小于1分钟。
用于强迫风冷散热器叶片之间距离可以为几个mm 。
在高功率定额,采用热管技术或油冷、水冷进一步改善热传导。
散热器大小与器件可以允许的最高结温有关。
对于最坏情况设计,规定了最高结温T jM ,最高环境温度T amax ,最高工作电压和最大通态电流。
如果最大占空比、最大通态电流和最大通态电阻已知(由手册可以查得T jM 和最大电流)就可以计算功率器件中最大功率损耗。
如果器件结温125℃,TO -3晶体管,其功耗为26W ,制造厂提供R jc =0.9℃/ W 。
使用带有硅脂的75μm 云母垫片,其综合热阻为0.4℃/ W 。
散热器安装处最坏环境温度是55℃,根据式(8-4)求得散热器到环境的热阻为 12555(0.90.4) 1.3926t R -=-+=℃/ W图8-4 IRFI4905 MOSFET 结到壳最大瞬态热抗图(International Rectifier -IR) 矩形脉冲宽度(s) 单脉冲(热抗) 热阻抗(Z t j c )占空比峰值T j =P DM ×Z tjc +T c注:手册中常给出铝型材单位长度热阻,由计算出的散热器热阻求出需要该散热器型材的长度。
4. 对流和辐射传热生产厂提供的散热器数据是该散热器在规定环境温度散热器到环境的热阻R sa 。
此热阻包含了辐射和对流热阻,它们与环境温度有关。
因此有必要了解散热器对流和辐射热传输机理。
对流和辐射热阻与传导热阻并联。
辐射热阻根据斯蒂芬-波尔兹曼定律,经辐射传输的热能()8445.710s a P EA T T -=⨯- (8-11a )P 为辐射功率(W);E 为表面发射率;T s 为表面温度(°K) ;T a 为环境温度或周围温度(°K);A 为散热器外表面(包括叶片)(m 2)。
对于黑色表面如黑色阳极化铝散热器E =0.9。
对于磨光铝,E 可能小到0.05。
对于黑色阳极化铝散热器可以将上式重新写成 445.1100100s a T T P A ⎛⎫⎛⎫⎛⎫=- ⎪ ⎪ ⎪ ⎪⎝⎭⎝⎭⎝⎭ (8-11b ) 根据热路欧姆定律,辐射热阻为 445.1100100rt s a TR T T A ∆=⎡⎤⎛⎫⎛⎫-⎢⎥ ⎪ ⎪⎝⎭⎝⎭⎢⎥⎣⎦如果T s =120℃=393K ;T a =20℃=293K ,则辐射热阻 0.12rt R A=℃/ W 例:每边10cm 表面阳极化的黑色立方体,表面温度T s =120℃,环境温度为T a =20℃,辐射热阻 20.12260.1rt R ==⨯℃/ W 对流热阻 如果垂直高度d 小于1m ,对流带走的热能 ()1.250.251.34T P A d ∆=(W ) (8-12)ΔT 为物体温度与环境空气的温度差(℃),A 是垂直表面积(或物体总表面积)(m 2),d 物体垂直高度(m)。
根据热欧姆定律,对流热阻 1/411.34ct d R A T ⎛⎫= ⎪∆⎝⎭(8-13) 如果d=10cm ,ΔT =100℃ 0.13ct R A=℃/ W 例:有一个薄板表面温度为120℃,环境温度为20℃,板高10cm ,宽30cm ,求R ct : 1/410.1 2.21.3420.10.3100ct R ⎛⎫== ⎪⨯⨯⨯⎝⎭℃/ W如果立方体与薄板面积相同,对流热阻与上例相同,则辐射和对流总热阻为ct rt rct ct rt R R R R R =+=1℃/ W 热从水平向上表面比垂直表面移开多15%~25%。