各式接插件模具设计制造
电器接插件多工位复合模具设计

1.3 模具形式
成形过程分六步完成,即需六套模具。 第一套:落料、拉深倒装复合模; 第二套:胀形、冲孔复合模; 第三套:胀形、冲孔复合模; 第四套:修边、冲孔复合模; 第五套: 弯曲单工序模; 第六套:冲孔、翻边复合模; (由于工作量的原因,主要设计前两套模具)
1.4 毛坯展开计算
1.4.1 拉深部分
方案一:先落料冲孔,后拉深,再胀形,最后弯曲翻边; 方案二:先落料拉深,后冲孔,再胀形,再冲孔,最后弯曲翻边; 方案三:先落料拉深,再胀形冲孔,再胀形冲孔,最后弯曲翻边。 方案一如果先冲孔后拉深,肯定会影响拉深的质量和孔之间的定位尺 寸,并且会影响其后的成形工序,提高了经济成本。那么对于此件上的孔应 该分开冲,比如胀形上的孔,拉深底部的大孔。为了保证零件的质量,方案 一的成形工序还不足。 方案二单从模具结构来看过于简单,中间三步都是简单的单工序模。而 且方案也不完善,从零件的结构来看,胀形部分不能一步完成。需要从两个 方向分别胀形,才能保证零件的质量 方案三解决了前两个方案的缺点,但所生产的零件的尺寸精度不高。 总结以上三种方案,得出方案四: 落料、拉深——胀形、冲孔——胀形、冲孔——修边、冲孔——弯曲——冲 大孔、翻边 方案四虽然分六步工序完成,简单的说需要六套模具。对于模具制造工 作比较繁重,成本也比较高。但是由于是批量生产,而且根据零件外形和尺 寸精度来说,这是优佳的方案。
(1-2)
A3 1/ 2 48 94.6 24.3 =1/2×3465.18mm² A01 A1 2 A2 2 A3
=12870.82-3888.66+3465.18=12447.44mm² 故:拉深部分面积 A01=12447.44mm² 1.4.2 弯曲部分
62 67 A1 . 4 57.5 30 113 360 360
DLP实例 电器接插件

数据处理 诊断修复
在工具栏点击打开“修复向导”窗 口(如图所示),所有已导入的模 型均可进行诊断修复。选中当前零 件,若想直接修复,点击“自动修 复”软件会后台直接修复模型。也 可以点击左上角的“诊断”命令, 观察判断模型的大体情况。
数据处理 诊断修复
点击诊断,跳转到诊断界面,点击更新 按钮可查看模型的所有问题。为了避免 分析不必要的项目,可以有选择地分析 一些重点项目,以节约处理时间。例如, 本例零件选择检测法向错误、坏边、错 误轮廓、缝隙、孔和壳体等项目。重叠 三角面片和交叉三角面片,这两项由于 不会对快速成型加工的模型质量构成影 响,一般不推荐对这两项进行修复。
数据处理 生成支撑
支撑是SLA类加工技术的必要条件,它能够帮助产品顺利完成制作。 Magics软件提供的自动生成支撑功能,能够快速、高效的生成支撑,大大 减少用户的准备时间并帮助操作人员在符合支撑强度的条件下尽可能节省 支撑的材料使用。
数据处理 切片
支撑添加完毕,打开“切片”选项卡, 弹出切片窗口。在“切片属性”窗口 设置切片的相关参数。切片参数框内 的切片厚度即激光成型每扫描一层固 化的厚度,对于如本例所示的小型工 件,一般设为0.1mm,若是大型工件 可采用0.15mm的厚度。
数据处理 切片
切片文件格式选择默认的CLI即可。设置切片参数一定要勾选下方的“包 含支撑”激活设置支撑参数,支撑的切片厚度要与零件的切片厚度保持一 致。然后设置保存文件的位置点击确定,进行自动切片,切片完成后将在 保存文件的位置生成*.cli及*_s.cli两个文件。 最后,将切片生成的文件拷贝至相应的文件夹,数据处理完毕,存入相应 的成型设备准备进入快速成型阶段。
模型诊断和修复完成,关闭“修复向导”窗口。点击“文件”-“零件另存为” 将修复的模型重新保存,等待下一步操作。
模具设计与制造专业毕业论文--电位器接线片冲压工艺与模具设计

摘要本次设计的任务是电位器接线片零件冲压工艺分析和模具的具体结构设计。
通过查阅了相关文献资料,对接触片零件进行工艺性分析,选择并确定符合于给定条件的最优工艺方案,及进行了工艺与设计的有关计算,如:选择基本工序,确定其顺序、工序数目及工序组合形式。
介绍了主要零部件的设计理念,详细剖析了设计过程中一些思路,以及某些非标准零件的使用特点。
阐述了工位级进模的设计要点, 使产品质量达到设计要求。
然后以此为基础,设计出冲压模具主要零件的结构。
并在设计中,介绍了零件的排样图、定位设计、冲裁力的计算和压力中心的计算。
关键词:电位器接线片;翻边模;级进模;模具设计目录摘要 (I)目录.................................................................................................................... I I 1 绪论. (1)1.1 概述 (1)1.2 冲压技术的进步 (1)1.3模具的发展与现状 (2)1.4模具CAD/CAE/CAM技术 (3)1.5冲压模具及级进模的发展现状 (5)1.6课题的主要特点及意义 (8)2 冲压工艺方案的确定 (11)2.1制件工艺分析 (11)2.2零件成型工艺分析 (13)3 冲裁工艺方案及模具结构的确定 (14)3.1方案种类 (14)3.2方案比较及确定 (14)3.3模具结构形式的确定 (14)4 级进模排样设计 (16)4.1级进模排样简介 (16)4.2排样的设计原则 (17)4.2.1确定冲压方向 (17)4.2.2 确定排样形式 (17)4.3工序顺序的安排 (17)5 主要零件的尺寸计算 (19)5.1凸、凹模刃口尺寸的计算方法 (19)5.1.1 凹凸模加工方法: (19)5.1.2 按凸模与凹模图样分别加工法 (20)5.2孔凹凸模工作部分尺寸计算 (21)5.2.1 冲1 mm孔 (22)5.2.2 落“T”形料 (22)6 多工位级进模工艺零件的设计 (24)6.1凸模结构的设计 (24)6.2凸模长度的设计 (25)6.3凸模的强度计算 (26)6.3.1 凸模承受能力的校核 (27)6.3.2 失稳弯曲应力校核 (27)6.4凹模结构的设计 (28)6.5凹模的固定形式 (30)6.6凹模的厚度设计 (30)6.6.1 凹模的厚度 (30)6.6.2 凹模的刃壁高度及凹模镶块尺寸设计 (31)6.7模板的设计 (31)6.8卸料弹簧的选用 (32)6.9其他零件的设计 (32)7 冲压设备的选用 (33)7.1冲压力的计算 (33)7.2压力机的选择 (34)8 级进模结构零件的设计 (36)8.1模架的设计 (36)8.2模架导向零件设计 (37)8.3模柄的设计 (38)8.4支撑零件的设计 (38)8.5卸料装置 (39)9 模具的整体设计 (40)9.1模具的整体设计 (40)9.2模具工作原理 (40)10 模具的装配 (42)结论 (44)致谢..................................................................................... 错误!未定义书签。
汽车接插件小圆插头端子冲模设计

成为该行业的首推任务,而设计制造出精密的模具,又 发生跳屑现象,跳出的屑直接对产品的外观、尺寸及
是保证一切的根本。该小圆汽车接插件插头端子由于 模具造成损伤,应坚决阻止。常用的办法是将凹模做
尺寸小,形状各异,外形含圆形、方形、U形等。产品高低 成拼合分隔凹模,效果较好。见图 3 所示拼合凹模,中
落差相对较大,在模具高速冲压的工作状况下,冲裁区 间留一个 0.003mm 左右的台阶缝。
4 模具工作过程
该模具为常见的典型的弹压卸料板形式。模具下 行时,首先是弹压卸料板与下模的弹性送料钉压紧材 料,继续下行时,冲裁、成形等凸模陆续工作。为了让 位,卸料板后半部被铣空,起不了作用。镶拼的卸料压 块正好弥补了这一点。整个工作回合,材料始终处于 压紧状态,利于产品的成形。该模具在最后安排了一 步空位,以备成形尺寸的调整。高速级进模中空位的 作用一般有两个:一是在前半部分的冲裁区,影响到 冲裁凹模强度时,必需增加一步;二是成形时的实际 效果达不到预定效果时,考虑增加空步。在工序的优 化安排上,步数的设计应遵循精而少的原则。
问题解决办法,以及各要点工序的设计技巧。
耐
关键词:主要工序;压料块;冲模
斯
Die Design for the Cir cular Plug
合
Ter minal Using in Automobile Connector
模
【Abstr act】Take the small circular plug terminal as an example, analyzed some very small and changeable product which made from very thinned material, introduced the question solution in
接插件产品加工中变形问题及解决方案和落实效果
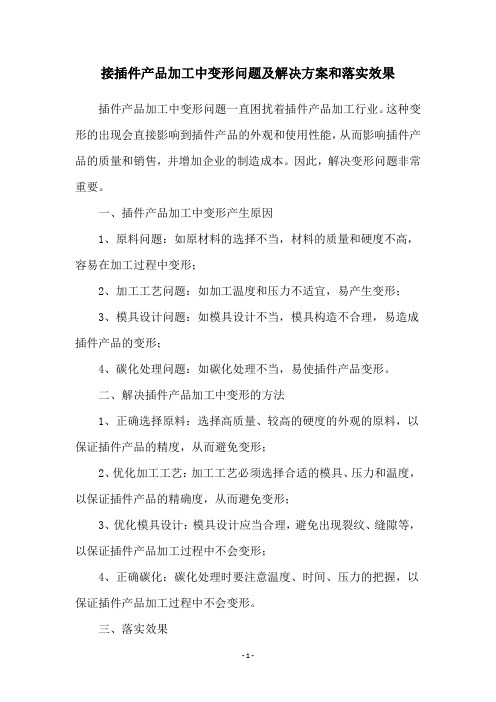
接插件产品加工中变形问题及解决方案和落实效果
插件产品加工中变形问题一直困扰着插件产品加工行业。
这种变形的出现会直接影响到插件产品的外观和使用性能,从而影响插件产品的质量和销售,并增加企业的制造成本。
因此,解决变形问题非常重要。
一、插件产品加工中变形产生原因
1、原料问题:如原材料的选择不当,材料的质量和硬度不高,容易在加工过程中变形;
2、加工工艺问题:如加工温度和压力不适宜,易产生变形;
3、模具设计问题:如模具设计不当,模具构造不合理,易造成插件产品的变形;
4、碳化处理问题:如碳化处理不当,易使插件产品变形。
二、解决插件产品加工中变形的方法
1、正确选择原料:选择高质量、较高的硬度的外观的原料,以保证插件产品的精度,从而避免变形;
2、优化加工工艺:加工工艺必须选择合适的模具、压力和温度,以保证插件产品的精确度,从而避免变形;
3、优化模具设计:模具设计应当合理,避免出现裂纹、缝隙等,以保证插件产品加工过程中不会变形;
4、正确碳化:碳化处理时要注意温度、时间、压力的把握,以保证插件产品加工过程中不会变形。
三、落实效果
1、通过改进插件产品加工工艺和设备,避免出现变形情况,提高插件产品的质量和使用性能;
2、减少加工和组装时间,提高产量,降低插件产品的生产成本;
3、提升企业形象,提高市场竞争力,有助于企业长期发展。
结论
插件产品加工中变形的原因多种多样,所以解决变形的方法也多种多样。
在实施相关措施的同时,要加强措施的执行力度,落实每一项措施,以最大限度地减少变形,提高插件产品的质量和使用性能,最终实现企业的长远发展。
电器接插件多工位级进模设计

分析,以获得更合理的工艺参数用 于指导 实际生
维普资讯
模具工业 2O 年第 3 卷第 5 08 4 期
图 2 零件 展开 图
3 所示的排样方 案: ①侧刃冲孔 ; ②冲 4 个 4 m 的 n 导正孔 ; ③冲 1 个 53 和 2 .m 个 2 的圆孔, m 2 个 2I mX4n 的方T ; ' o m L④冲废料 ; ⑤对称弯曲两侧 8。 l 圆弧; ⑥利用滚轴对称弯曲两侧 9。 ; 0圆弧 ⑦通过
纹理方 向有关。 双层真空保温容器外壳表面图案繁多、 形状各 异。 其成形工艺参数与成形特点还需要进一步研究
【】 强, 4于 杨连发, 巢鹏飞, 薄壁管液压胀形过程的数 等. 值模拟 【】 模具工业 ,053 (1 :6 J. 20,11)3 . - 【】 5印雄飞, 何丹农, 叶 又, 虚拟速度对板料成形数值 等. 模拟影响的实验研究【】 机械科学与技术,O01() J. 20,93 :
【】 3林耿兴. 双层金属保温容器同步液胀成型装置【 】 中 P.
国。0 70 5 19 2 2O .7 1 . 2 o2 04 1 . .0 70 .6
() 3 同步液压胀形成形三种浮雕 图案所需压力 从大到小依次为足球形、 排球形 、 篮球形, 且不同表 面浮雕图案成形所需压力大小 与花纹复杂程度及
量。
产。
参考文献 :
【】 1王南海. 金属无模爆炸加工技术在低温压力容器制造 领域里的应用 【】 化工设备与管道,0O3()5 1 J. 2O,73:- . 1
【】 2林耿兴 . 双层金属保温容器同步液胀成形装置及其成
型方 法 【】 中国 ,070213220.71. P. 2O 1 96..0r0.6 0 7r
电位器接线片零件冲压工艺分析及模具
电位器接线片零件冲压工艺分析及模具一、前言电位器是一种电子元器件,有时也被称为旋转式电阻器或可变电阻器。
它的主要作用是分压、调节电流、旋转补偿等。
与其他电子元器件一样,电位器也由多个零部件组成,而其中一个重要的组成部分就是接线片。
本文将从电位器接线片的零件冲压工艺和模具分析两个方面来介绍电位器接线片的制造过程。
二、电位器接线片的零件冲压工艺1. 工艺简介电位器接线片是由导电性材料(通常是铜、银等金属)制成的薄片,具有一定的弯曲性和强度。
它的形状各异,不同型号的电位器接线片也有不同的制造工艺流程。
但是,大体来说,电位器接线片的制造工艺可以分为五个步骤:原材料切割、冲压成形、焊接、打磨和表面处理。
2. 制造工艺详解(1)原材料切割最开始,铜带或银带等导电材料会被切成一定长度。
这个长度短到仅有几毫米,长至数十厘米都有可能,需要根据不同型号电位器的设计要求来决定。
(2)冲压成形接下来,将原材料放入模具中进行冲压。
模具一般会设计成平面式或者冲分模式。
在模具中,铜带或银带经过压力挤压,逐渐变成接线片的形状。
具体模具结构设计需根据电位器接线片的不同型号来进行调整和研究。
(3)焊接在接线片形成后,需要对其上的接线端进行焊接。
焊接分为自动焊接和手工焊接两种。
对于一些工作量较大的接线片,自动化焊接可提高效率。
(4)打磨在完成焊接之后,接线片的表面可能会存在毛刺或其他不光滑的现象。
这个时候需要将接线片进行打磨,使其表面光滑平整。
(5)表面处理最后一步就是对接线片进行表面处理。
根据需要,接线片可能被涂上保护膜、喷上保护剂或者进行其他特殊处理。
这样做有助于提高接线片的耐腐蚀性和使用寿命。
三、电位器接线片制造模具分析模具是生产电位器接线片的重要工具。
制造合适的模具可以提高电位器接线片的成品率和精度,降低生产成本。
因此,在进行电位器接线片制造前,实际制造中需要对模具做仔细分析。
1. 模具的材质模具通常是陶瓷、硬质合金、高速钢等材料制成。
五孔插座面板注射模具设计
五孔插座面板注射模具设计发布时间:2021-07-23T10:03:29.523Z 来源:《建筑科技》2021年7月下作者:宁艳亭,张姗姗,张利敏[导读] 模具是塑料制品成型的主要工具,在塑件的生产中应用十分广泛。
本问以五孔插座面板为例,从插座面板产品的设计要求出发,对五孔插座面板进行了工艺分析,进行注射机、模具模架的选型,对五孔插座面板注射模具型腔分型面主流道、衬套、分流道、推杆设计,为注射模具设计提供一定的借鉴。
河南商丘工学院机械工程学院,宁艳亭,张姗姗,张利敏 476000摘要:模具是塑料制品成型的主要工具,在塑件的生产中应用十分广泛。
本问以五孔插座面板为例,从插座面板产品的设计要求出发,对五孔插座面板进行了工艺分析,进行注射机、模具模架的选型,对五孔插座面板注射模具型腔分型面主流道、衬套、分流道、推杆设计,为注射模具设计提供一定的借鉴。
关键词:插座面板;注射成型;模具设计模具是工业生产的基础工艺装备,在电子、汽车、电动机、电器、仪器、仪表、家电和通信等产品中,60%~80%的零部件都要依靠模具成型[1]。
模具工业的每次进步和创新都意味着模具企业进行了一次重大的突破。
德国、日本、美国等国家的模具标准化程度已经达到70%~80%[2],今年来,我国模具行业发展越来越迅速,国家和一些个体对模具工业都投入了大量的资金,模具行业在创造和创新方面提升很大,为我国经济的发展起到了很大的作用,模具设计也逐渐向走向数字化发展的道路。
一插座面板工艺分析在插座面板中,五孔插座的利用率相当普遍。
插座面板是一种塑料制品,模具是塑料制品成型的主要工具,使用注射成型工艺进行加工。
五孔插座的两孔和三孔在同一中心线上,设计过程中三孔比较难设计,它有两个倾斜的插口,三插口和两插口都是中心对称的。
插座面板上还有6个对称的孔,那是推杆所在的位置,设计推杆是为了让成型后的塑件从模具中脱下来。
插座面板的生产过程[3]:注射机通过浇口套流入主流道,再通过主流道流入分流道进入分型面,最后到达型腔。
接插件端子级进模具设计
带导正销孔 的浮顶销 , 这样设计可 以使条料始 同时满足条料进给时的刚度和稳定性要求 ,采用 了 料块 、 终在下模表面 以上一定的距离 向前移动 ,从而保证 图 2 示 的排 样形 式 。 所 料带宽度 4 .nn 进给步距 2 m, 1 个工 了条料 的顺利送进 。 3 l, 6l 4m 共 6
《 备制 造技 术)0 1 装 ) 1 年第 8期 2
32 关键 零 件设 计 -
零件方框成形 , 是本模具设计的关键部分 , 分为 两大成形工序 ,预成形 与方框成形 。共分为 5步完
成, 考虑到尽 可能减小 回弹 , 提高成形精度 , 内、 故 外 侧折弯各分成两步 :
第l 步是最外侧 4 。 5 折弯成形( 4) 图 a; 第 2步外侧 9 。 0 折弯成形 ; 第3 步是 内侧 4 o 5 折弯成形 , 将折弯 凸、 凹模 设 计为如 图 4 c所示的结构 , () 既可以给前 面 已成形的 竖边让位又便于后续压边工序 的成形 ;
图 2 排样 图
圜
图 1 插 接 件 端 子 产 品 图
3 模具 结构 及关键零件设计
3 所示。该模具为卷料供料 , 使用
2 排样 设计
导料板导料 , 送料定距依靠模具外 自动送料装置 , 配
合导正销实现 了精密定位 ,故模具上不需设置侧 刃 为了使料带悬浮于凹( 模 下) 通过对零件的成形工艺与模具结构 的综合分析 进行定位。冲裁过程中, 料带两侧使用浮动导料销 , 以及采用浮动顶 考虑, 为满足大批量生产要求 , 保证零 件成形精度 , 上表面 ,
5 工 1为外 侧 折 弯 成 9 。; 位 l 0 工 2为 内侧 折 接 件接 口。 料使 用 C 20 — 是 JS标 准牌 号 的磷 4 。; 位 1 材 5 1R H, I 5 工 3为空 工 位 ; 位 l 工 4为 内侧 折 弯 成 青 铜带 , 具有 良好 的延 展性 , 冲性 能 以及 电镀性 , 深 广 弯成 4 。; 位 1 O 方 ; 5为整 形 ; 位 l 切 断 工 6为 泛用于电子接插件上。零件料厚为 0 n, .m q要求批量 9 。( 形 框 成 形 )工位 l 3 零 。 生产 , 零件结构复杂 , 具有 冲裁 、 多处弯 曲, 局部折弯 ( 件 与料 带分 离 )
键盘接插件外壳级进模设计
① ② ③ ④ ⑤ ⑥ 冲 冲 冲 切 压 翻 孔 废 废 边 线 孔 料 料 、
、
两端 有 五处 弯 曲成形 , 那
么 只 能 采 用 一 出 一 排 列 以带 料 本 体 为 中 间 载 体 的排样方 式 。
关 键 词 : 械 制 造 ; 进 模 ; 壳 ; 计 ; 压 加 工 机 级 外 设 冲
中 图 分 类 号 : G3 52 T 8 . 文 献 标 识 码 : 主 机 连
接 的 外 壳 零 件 。 料 S CC, 厚 材 P 板 03 .mm, 年 产 量 2 0 0 0多 万 件 , 属
一
面 间隙是零 配零 的 ,当凸模进 入 凹模 冲裁 时造成
图 3 零 件 展 开 图
单 边 受 力 , 的 方 向 全 部 集 中在 外 侧 一 边 , 模 在 脱 力 凸
】 2 3 4 5 6 7 8 9 】 1 2】 4 】 0l 】 31 5 】 7 】 9 2 2 3 2 5 2 6】 8 1 O 21 22 4 2 6
考
收稿 日期 :0 9 1— 6 20—00
规
作者简介 : 金龙建 (9 9 )男 , 17 一 , 工程师 , 从事冲压工艺及模具设计
须
墨
D I
u
8 .mm, 件 展 开 见 图 3 83 零 所 示 。 为 提 高 材 料 利 用
率 ,各 工 位 间 排 列 紧 凑 ,
1
‘。
‘。。。
L
。 。
曲成 9 。 0 ,然 后 将 D处 也 用 同样 的 方 法 弯 曲 成 9 。 0,