铝材编号方法及加工常识
铝材料新旧状态代号介绍
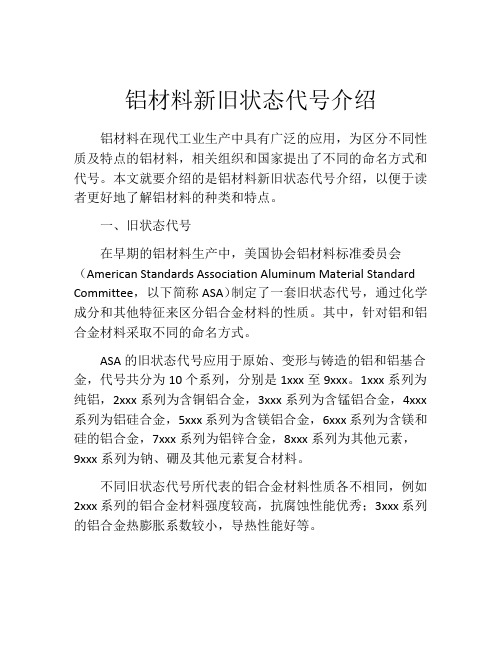
铝材料新旧状态代号介绍铝材料在现代工业生产中具有广泛的应用,为区分不同性质及特点的铝材料,相关组织和国家提出了不同的命名方式和代号。
本文就要介绍的是铝材料新旧状态代号介绍,以便于读者更好地了解铝材料的种类和特点。
一、旧状态代号在早期的铝材料生产中,美国协会铝材料标准委员会(American Standards Association Aluminum Material Standard Committee,以下简称ASA)制定了一套旧状态代号,通过化学成分和其他特征来区分铝合金材料的性质。
其中,针对铝和铝合金材料采取不同的命名方式。
ASA的旧状态代号应用于原始、变形与铸造的铝和铝基合金,代号共分为10个系列,分别是1xxx至9xxx。
1xxx系列为纯铝,2xxx系列为含铜铝合金,3xxx系列为含锰铝合金,4xxx 系列为铝硅合金,5xxx系列为含镁铝合金,6xxx系列为含镁和硅的铝合金,7xxx系列为铝锌合金,8xxx系列为其他元素,9xxx系列为钠、硼及其他元素复合材料。
不同旧状态代号所代表的铝合金材料性质各不相同,例如2xxx系列的铝合金材料强度较高,抗腐蚀性能优秀;3xxx系列的铝合金热膨胀系数较小,导热性能好等。
然而,随着铝合金技术的不断发展和升级,ASA的旧状态代号已不能完全反映铝材料的性质和特点。
因此,在1982年之后,ASA逐步被代替。
二、新状态代号新状态代号是在ASA代号基础上,根据铝合金的适用范围、材料特性和国际标准制定的一种新的命名方式。
它是由铝材料的型式、孔隙、硬度、加工状态、热处理状态等因素组成的。
新状态代号由英文ABCD四个字母和阿拉伯数字组成。
其中:A表示铝材料的形态,如F表示粉末、C表示连铸、W表示锭条、T表示锻件;B表示铝材料的孔隙度,数字表示0-8级别,级别越小、孔隙越少,密度越高;C表示铝材料的硬度,数字表示0-9级别,级别越高、硬度越大;D表示铝材料的状态,如F表示表面处理好、H表示冷加工硬化、T表示热处理等;其后接1-10数字,代表具体的状态。
铝材编号规则

铝材编号规则
铝材的编号规则主要依据其合金成分和加工工艺进行标注,包括数字分类、字母分类和中文分类等方式。
1. 数字分类:以1、2、3、4、5、6、7开头的编码,代表不同的铝材系列。
其中1开头是纯铝材料系列;2开头是铝锰合金;3开头是铝硅合金;4开头是铝铜合金;5开头是铝镁合金;6开头是铝镁硅;7开头是铝锌镁铜。
2. 字母分类:以a、b、c、d、e、f、g、h、k、l、m、n、p、q、r、s、t、u、v、w、x、y、z开头的编码,代表不同的铝材合金或者加工状态。
其中a表示纯铝;h表示高强度系列;o表示加热退火状态;t表示已经进行温度处理;w表示固溶热处理状态。
3. 中文分类:铝材的中文分类方法是以铝的基本元素和组成为基础,将铝合金分成不同的系列。
此外,根据铝合金按加工方法可以分为变形铝合金和铸造铝合金,其中变形铝合金的国际牌号(用四位阿拉伯数字表示)包括1XXX (99%以上的纯铝系列)、2XXX(铝-铜合金系列)、3XXX(铝-锰合金系列)、4XXX(铝-硅合金系列)、5XXX(铝-镁合金系列)、6XXX(铝-镁-硅合金系列)、7XXX(铝-锌合金系列)和8XXX(上述以外的合金体系)。
6063-T5材质及工艺流程解析汇总

6063-T5工业铝型材材质及工艺流程解析
一、6063材质
1 6063 为铝锭原材,6063为铝材编号,我国目前通用的是美国铝业协会〈Aluminium Association〉的编号
第一位数:表示主要添加合金元素
6表示主要添加合金元素为矽和镁
第二位数:表示原合金中主要添加合金元素含量或杂质成分含量经修改的合金
0表示原合金
第三及四位数:纯铝:表示原合金合金:表示个别合金的代号
3 表示主要添加合金元素为锰或锰与镁
2 -后面的Tn表示加工硬化的状态或热处理状态的鍊度符号
T5 表示由高温成型冷却,然后人工时效的状态.
适用于由高温成型过程冷却后,不经过冷加工(可进行矫直、矫平,但不影响力学性能极限),予以人工时效的产品。
二 6063-T5 工艺流程
6063-T5铝型材采用质轻高钢性的铝锭原材熔铸、挤压、铸造、上色的工序后,表面经电脑化喷砂、阳极氧化、电泳处理,再以压克力树脂涂布,表面更加美观与耐刮性。
1、熔铸 : 1配料 2 熔炼 3 铸造
2、挤压
3、铸造
4、上色 : 1表面预处理2 电脑化喷砂、阳极氧化、电泳 3封孔
下面附上常规的自动化设备工业铝型材的图片
详询:116363 9363。
铝行业通用版 -编码规则

铝业公司
常用标号汇总
一,型材系列推拉门窗:
上滑-01 下滑-02 边框-03 上方-04
下方-05 光企-06 勾企-07 中柱-08
转角-09 固定框-10 边框盖板-11 下滑盖板-12
收口-13 纱芯-14 压线-15
二,型材系列幕墙:
01-立柱套筒-02 横梁-03 04-横梁盖板05-全(半)扣06-玻框07-悬窗框08-悬窗扇09-转角立柱10-封盖11-压板12-外盖板
三,型材系列平开门窗:
窗框-01 中柱-02 窗扇-03 转向框-04
框压线-05 扇压线-06 07-组角码假中柱-08 转角-09
四,型材系列工业型材:
依次以GY打头按GY01 GY02 GY03
五,型材系列栏杆:
扶手-01 立柱--02 横梁-03 横梁盖板-04
六,型材系列断桥分型号:
按主型号加01-室外02-室内编分型号有三,四及更多的分型号从外至内依次编号
七,型材系列圆管
以YG打头编码
八,型材系列扁管
以G打头编码
九,型材系列角铝
以JL打头编码
十,型材系列工字百叶分别以GZ BY 打头编码十一,型材系列装饰型材以ZS打头编码。
铝及铝合金的八大系列编号含义

铝及铝合金的八大系列编号含义铝材的比重较轻,在成型时的回弹较小,强度比较高,接近或超过优质钢,塑性好,产品成形较复杂时,较不锈钢更易控制,具有优良的导电性、导热性和抗蚀性,且目前铝材的表面处理工艺阳极氧化、拉丝、喷砂等已经很成熟,铝材在手机上的使用也非常的多。
根据铝合金按加工方法可以分为变形铝合金和铸造铝合金,铝及铝合金的编号主要分为八个系列。
合金牌号表示方法国际牌号(用四位阿拉伯数字,现常用表示方法):1XXX 表示为99%以上的纯铝系列如1050、11002XXX 表示是铝-铜合金系列如20143XXX 表示是铝-锰合金系列如30034XXX 表示是铝-硅合金系列如40325XXX 表示是铝-镁合金系列如50526XXX 表示是铝-镁-硅合金系列如6061、60637XXX 表示是铝-锌合金系列如70018XXX 表示是上述以外的合金体系一系在所有系列中1000系列属于含铝量最多的一个系列,纯度可以达到99.00%以上。
1000系列铝板根据最后两位阿拉伯数字来确定这个系列的最低含铝量,比如1050系列最后两位阿拉伯数字为50,根据国际牌号命名原则,含铝量必须达到99.5%以上方为合格产品。
一系的铝成形性、表面处理性良好,在铝合金中其耐蚀性最佳。
其强度较低,纯度愈高其强度愈低。
手机上常用的到的有1050、1070、1080、1085、1100,做简单挤压成型(不做折弯),其中1050和1100可以做化学打沙、光面、雾面,法线效果,有较明显的材料纹路,着色效果好;1080和1085镜面铝常用来做亮字、雾面效果,无明显材料纹路。
一系的铝材都相对较软,主要用来做装饰件或内饰件。
二系特点是硬度较高,但耐蚀性不佳,其中以铜原属含量最高,2000系列铝合金代表2024、2A16、2A02。
2000系列铝板的含铜量在3%~5%左右。
2000系列铝棒属于航空铝材,作为构造用材使用,目前在常规工业中不常应用。
三系3000系列铝棒是由锰元素为主要成分。
铝的材料牌号

铝的材料牌号
铝的材料牌号是用于标识和识别铝及铝合金的类别和性能的一种标准。
在铝及铝合金的命名体系中,主要采用两种方法:一种是纯铝的牌号命名法,另一种是铝合金的牌号命名法。
1.纯铝的牌号命名法:当铝含量不低于99.00%时,被称为纯铝。
其牌号用
1XXX系列表示,其中牌号的最后两位数字表示最低铝百分含量。
例如,1050表示铝含量不低于99.50%的纯铝。
牌号第二位的字母表示原始纯铝的改型情况,如果第二位的字母为A,则表示为原始纯铝;如果是B~Y的其他字母(按国际规定用字母表的次序选用),则表示为原始纯铝的改型,与原始纯铝相比,其元素含量略有改变。
2.铝合金的牌号命名法:铝合金的牌号用2XXX~8XXX系列表示。
牌号的最后
两位数字没有特殊意义,仅用来区分同一组中不同的铝合金。
牌号第二位的字母表示原始合金的改型情况,如果牌号第二位的字母是A,则表示为原始合金;如果是B~Y的其他字母(按国际规定用字母表的次序选用),则表示为原始合金的改型合金。
一些常见的铝材料牌号包括1050、1060、3003、5052、6061、6063和7075等。
这些牌号在不同的应用领域中表现出不同的性能特点,因此需要根据具体需求选择合适的牌号。
需要注意的是,不同国家和地区对铝材料牌号的标识和命名可能存在差异,因此在使用或购买时应根据当地的标准和规范进行选择。
铝板牌号及状态的详解

铝板牌号及状态的详解以1060-H24为例,其中各位数所代表的意思如下:一、第一位阿拉伯数1代表是纯铝(纯铝即是铝含量99%以上的铝,除了以一开头还有以2-8开头的都有,2###为铜铝镁合金、3###为铝锰合金、4###为铝硅合金、5###铝镁合金等等)二、第二位阿拉伯数0表示原合金、如为1则表示原合金经过一次修改、2则表示原合金经过二次修改。
三、第三及第四位60两位阿拉伯数据在纯铝中表示纯铝含量百分99%后面的数值,60则表示铝含量99.60%的纯铝,以此为标准1050则表示铝含量为99.50%的纯铝、1070则表示铝含量为99.70%的纯铝。
在合金铝中后面两位阿拉伯数没有特别意义,仅用来识别同一组中的不同合金,其第2位表示改型情况。
四、H24中的H表示加工硬化的状态,有的不用H而是T就表示是热处理状态。
24表示控制硬度等物性的加工工艺,除了24还有12、14、16、18、22、26、34、36等等,通常4结尾的都是半硬状态的。
1060O态、1060-H22、1060-H24、1060-H18是从软到硬的排列。
状态代号的含义内容字母H字母H后面一般跟两位数字:第一位数字表示的就是加工硬化处理的方法。
H后面的第一位数字有:1,2,3,4即H1* H1*表示单纯加工硬化处理H2* H2*表示加工硬化及不完全退火H3* H3*表示加工硬化及稳定化处理H4* H4*表示加工硬化及涂漆处理第二位数字表示的就是材料所达到的硬化程度。
H后面的第二位数字有:1,2,3,4,5,6,7,8,9既H*1 0与2之间的硬度H*2 1/4硬H*3 2与4之间的硬度H*4 1/2硬H*5 4与6之间的硬度H*6 3/4硬H*7 6与8之间的硬度H*8 全硬状态H*9 超硬状态(H后面跟三个数字的情况不多,只有几个。
H111表示最终退火后又进行了适量的加工硬化。
H112表示适用于热加工成型的产品。
H116表示含镁量≥4.0%的5***系合金制成的产品.)字母T我们常见的热处理强化型铝合金后面的状态代号一般是字母T加添加一位或多位阿拉伯数字表示T的细分状态在T后面添加0—10的阿拉伯数字,表示细分状态(称作TX状态)。
铝材统一状态代号.
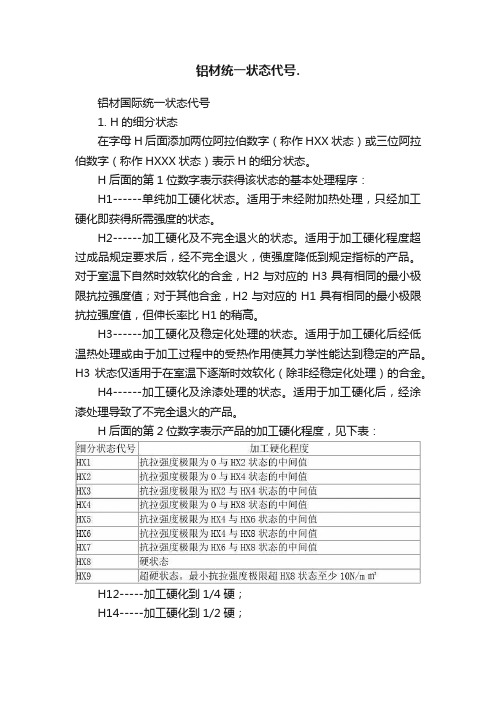
铝材统一状态代号.铝材国际统一状态代号1. H的细分状态在字母H后面添加两位阿拉伯数字(称作HXX状态)或三位阿拉伯数字(称作HXXX状态)表示H的细分状态。
H后面的第1位数字表示获得该状态的基本处理程序:H1------单纯加工硬化状态。
适用于未经附加热处理,只经加工硬化即获得所需强度的状态。
H2------加工硬化及不完全退火的状态。
适用于加工硬化程度超过成品规定要求后,经不完全退火,使强度降低到规定指标的产品。
对于室温下自然时效软化的合金,H2与对应的H3具有相同的最小极限抗拉强度值;对于其他合金,H2与对应的H1具有相同的最小极限抗拉强度值,但伸长率比H1的稍高。
H3------加工硬化及稳定化处理的状态。
适用于加工硬化后经低温热处理或由于加工过程中的受热作用使其力学性能达到稳定的产品。
H3状态仅适用于在室温下逐渐时效软化(除非经稳定化处理)的合金。
H4------加工硬化及涂漆处理的状态。
适用于加工硬化后,经涂漆处理导致了不完全退火的产品。
H后面的第2位数字表示产品的加工硬化程度,见下表:H12-----加工硬化到1/4硬;H14-----加工硬化到1/2硬;H16-----加工硬化到3/4硬;H18-----加工硬化到4/4硬,即完全硬化状态;H19-----超加工硬化状态。
此种材料的抗拉强度应比H18状态材料的高 10N/m ㎡以上;H22-----加工硬化后部分退火到1/4硬;H24-------加工硬化后部分退火到1/2硬;H26-------加工硬化后部分退火到3/4硬;H28-------加工硬化后部分退火到4/4硬;H32-------加工硬化后稳定化处理到1/4硬;H34-------加工硬化后稳定化处理到1/2硬;H36-------加工硬化后稳定化处理到3/4硬;H38-------加工硬化后稳定化处理到4/4硬;H42-------加工硬化后涂漆的,1/4硬;H44-------加工硬化后涂漆的,1/2硬;H46-------加工硬化后涂漆的,3/4硬;H48-------完全加工硬化后涂漆的,4/4硬;HXX4-----用相应HXX状态板,带加工的花纹板、带。
- 1、下载文档前请自行甄别文档内容的完整性,平台不提供额外的编辑、内容补充、找答案等附加服务。
- 2、"仅部分预览"的文档,不可在线预览部分如存在完整性等问题,可反馈申请退款(可完整预览的文档不适用该条件!)。
- 3、如文档侵犯您的权益,请联系客服反馈,我们会尽快为您处理(人工客服工作时间:9:00-18:30)。
一、分类:展伸材料分非热处理合金及热处理合金1.1 非热处理合金:纯铝—1000系,铝锰系合金—3000系,铝矽系合金—4000系,铝镁系合金—5000系。
1.2 热处理合金:铝铜镁系合金—2000系,铝镁矽系合金—6000系,铝锌镁系合金—7000系。
二、合金编号:我国目前通用的是美国铝业协会〈Aluminium Association〉的编号。
兹举例说明如下:1070-H14(纯铝)2017-T4(热处理合金)3004-H32(非热处理合金)2.1第一位数:表示主要添加合金元素。
1:纯铝2:主要添加合金元素为铜3:主要添加合金元素为锰或锰与镁4:主要添加合金元素为矽5:主要添加合金元素为镁6:主要添加合金元素为矽与镁7:主要添加合金元素为锌与镁8:不属於上列合金系的新合金2.2第二位数:表示原合金中主要添加合金元素含量或杂质成分含量经修改的合金。
0:表原合金1:表原合金经第一次修改2:表原合金经第二次修改2.3第三及四位数:纯铝:表示原合金合金:表示个别合金的代号”-〃:后面的Hn或Tn表示加工硬化的状态或热处理状态的鍊度符号-Hn :表示非热处理合金的鍊度符号-Tn :表示热处理合金的鍊度符号2 铝及铝合金的热处理一、鍊度符号:若添加合金元素尚不足於完全符合要求,尚须藉冷加工、淬水、时效处理及软烧等处理,以获取所需要的强度及性能。
这些处理的过程称之为调质,调质的结果便是鍊度。
鍊度符号定义F 制造状态的鍊度无特定鍊度下制造的成品,如挤压、热轧、锻造品等。
H112 未刻意控制加工硬化程度的制造状态成品,但须保证机械性质。
O 软烧鍊度完全再结晶而且最软状态。
如系热处理合金,则须从软烧温度缓慢冷却,完全防止淬水效果。
H 加工硬化的鍊度H1n:施以冷加工而加工硬化者H2n:经加工硬化后再施以适度的软烧处理H3n:经加工硬化后再施以安定化处理n以1~9的数字表示加工硬化的程度n=2 表示1/4硬质n=4 表示1/2硬质n=6 表示3/4硬质n=8 表示硬质n=9 表示超硬质T T1:高温加工冷却后自然时效。
挤型从热加工后急速冷却,再经常温十效硬化处理。
亦可施以不影响强度的矫正加工,这种调质适合於热加工后冷却便有淬水效果的合金如:6063。
T3:溶体化处理后经冷加工的目的在提高强度、平整度及尺寸精度。
T36:T3经6%冷加工者。
T361:冷加工度较T3大者。
T4:溶体化处理后经自然时效处理。
T5:热加工后急冷再施以人工时效处理。
人工时效处理的目的在提高材料的机械性质及尺寸的安定性适用於热加工冷却便有淬水效果的合金如:6063。
T6:溶体化处理后施以人工时效处理。
此为热处理合金代表性的热处理,无须施以冷加工便能获得优越的强度。
於溶体化处理后为提高尺寸精度或矫正而施以冷加工,如不保证更高的强度时,亦可当作是T6鍊度。
T61:溶体化处理后施以温水淬水再经人工时效处理,温水淬水的目的在防止发生变形。
T7:溶体化处理后施以安定化处理(亦及人工时效处理的温度或时间较T6处理高或长)。
其目的在改善耐硬力腐蚀裂及防止淬水时发生变形。
T7352:溶体化处理后除去残余应力再施以过时效处理(亦及人工时效处理的温度或时间较T6处理高或长)。
目的在改善耐硬力腐蚀裂。
於溶体化处理后施以1~5%永久变形的压缩加工,以消除残余应力。
T8:溶体化处理后施以冷加工再施以人工时效处理,冷加工时断面减少率为3%及6% 各为T83 及T86。
T9:溶体化处理后人工时效处理,最后施以冷加工,最后冷加工的目的在增加强度。
二、软烧处理:2.1目的:展伸用材料包括压延用材料,挤压用材料及锻造用材料,通常其制造程序为:铸造→热加工→冷加工→材料成品在热加工或冷加工的过程中,材料发生加工硬化的情况,使强度变大或导致加工硬化的情况,使强度变大或导致加工性减低。
为消除这些加工硬化,於冷加工前,中或后所施的热处理即为软烧处理,其目的在使材料具有使用上所需要的程度。
2.2分类:由於软烧条件的不同而分:2.2.1 部分软烧:仅消除部份加工硬化,处理温度在再结晶温度以下,实际温度则视强度而定,强度愈高则处理温度较低。
2.2.2 完全软烧:处理温度在材料的再结晶温度或稍高使材料发生再结晶而完全消除加工硬化,亦使强度达到最低的状态。
软烧处里就时机而分:2.2.3 中间软烧:再冷加工开始之前或冷加工过程中,所加的软烧处理,通常为完全软烧,其目的在恢复其加工性,使接下去的加功能较顺利,及控制其组织状态,俾能适合於最终成品的要求。
2.2.4 最终软烧:主要目的再调整成品最后的强度水准亦即调整鍊度。
3 加工常识一、铝合金成型加工通常出现之缺陷:缺陷原因改善对策● 胚料有瑕疵1. 空心壳壁或凸缘之龟裂1. 滚动缺陷(摺叠) 1. 改善品质管制2. 起耳状物2. 机械性质太过平均2. 退火(如不致生晶粒生长)工具有瑕疵1. 引伸一开始,空心壳之底部即被撕裂。
1. 冲头或模之圆角太小。
1. 加大冲头或模之圆角。
2. 引伸末了,空心壳之底部方被撕裂。
2. 引伸比太大,冲头未对准模孔中心。
2. 增加中间引伸,选用品质较佳之材料;若为方形空心壳则增加转角之冲模间隙。
3. 引伸刮痕。
3. 润滑不佳,工具表面之情况不佳(已磨耗)。
3. 使用特殊引伸用黄油(材料必须经磷酸盐处理或镀铜),再光制工具表面(镀铬),选用不易产生刮痕之材料。
4. 成品边缘有锯齿形,壳表面有皱纹。
4. 模圆角太大,冲模间隙太大。
4. 再轮模或更换引伸模具● 工具或机器之调整不常瑕疵1.凸缘上有皱纹。
1.胚料架压力太小。
1. 增加胚料架之压力。
2. 成品之一边有抓伤或其他痕迹,而工具表明面显之痕迹。
2. 冲头未对准模孔中心,或倾斜一角度,而造成磨损。
2. 再轮磨或重新校准模具3. 壳壁太粗,尤其是矩形深引伸成型成品为然。
3. 胚料架压力太小,或模之圆角太大。
3. 增加胚料架之压力,或於模与胚料架间制一加强之隆起。
4. 壳线有压平之皱纹或龟裂。
4. 胚料架压力太小,或冲模间隙太大。
4. 更换模具。
二、硫酸阳极处理通常出现之缺陷:缺陷原因改善对策工作物件局部位置电击烧伤或穿孔1. 工作物和阴极接触发生短路。
1. 放置工作物於处理槽内时,注意与阴极之距离,避免发生接触。
2. 工作物彼此之间接触发生短路。
2. 加大工作物间距离。
3. 工作物件和夹具接触不良。
3. 夹具使用前须加以清洗,与工作物间须夹紧。
氧化膜极疏松,用手就可擦掉1. 电解液温度太高。
1. 设法降低温度,例如进行搅拌或开动冷却设备,并控制温度差在±2℃内。
2. 氧化处理时间太久。
2. 缩短氧化时间。
3. 工作电流密度太高。
3. 降低电流密度。
氧化膜带红色斑点或整个表面或局部表面发红1. 导电棒和夹具之间的接触不好令铜沉积在铝表面。
1. 改善导电棒与夹具的接触,材质改用铝材。
2. 接触中断,如导电中断2. 加强氧化过程的检验。
氧化膜暗淡不够光亮或烧焦现象1. 工作物件在槽中长时间无给电,或断电后又给电。
1. 经常检查纠正与电器维修严格管制处理时程。
2. 硫酸溶液内溶存的铝业增加导致氧化膜的透明性变差,最后发生烧焦现象。
2. 检验处理液中的铝量。
2.1 硫酸液中含铝量以1gm/l左右为宜。
2.2 新液则添加12~13 gm/l的硫酸铝。
氧化膜有黑斑或黑条纹1. 电解液中有悬浮的杂质1. 清理表面悬浮杂质。
2. 工作物件表面有油污渍或其它污染物。
2. 彻底纠正除油液成份;确实执行前处理。
3. 电解液中含铜和铁杂质太多。
3. 分析后除去并定期更新部份电解液。
4. 电解后工作物未洗乾净就进行封孔。
4. 电解后工作物要立即清洗乾净,避免处理液或杂质残留於氧化膜表面氧化膜局部表面被腐蚀1. 氧化后氧化膜上的电解液未洗乾净。
1. 加强氧化后的洗涤。
2. 深凹处藏有电解无洗乾净。
2. 均加强氧化后的洗涤。
3. 电解液无洗乾净就进行封孔处理。
3. 均加强氧化后的洗涤。
经重铬酸钾填充后氧化膜色淡而发白1. 溶液温度低,填充时间短。
1. 改正不适宜条件。
2. SO4-2含量太高。
2. 检查和校正SO4-2成份。
3. 氧化膜太薄。
3. 增加氧化处理时间。
氧化膜厚薄不均1. 工作物表面附有污染物未清理乾净。
1. 前处理须彻底将表面洗净。
2. 处理槽内溶液搅拌不够2. 加强搅拌作用。
3. 电流密度过高。
3. 一般硫酸液阳极处理的电流密度以1~2A/dm2为宜。
无色的工作物件经热水填充处理易沾上手印,水印,膜层发白1. 封孔的温度和时间不够1. 按适宜条件进行。
2. PH值不当2. 调整PH值。
3. 溶液氢氧化铝太多。
3. 更换用水。
三、铬酸阳极处理通常出现之缺陷:缺陷原因改善对策工作物件被烧伤1. 零件和夹具间的接触不良。
1. 夹紧改进接触。
2. 零件和阴极接触,零件之间彼此接触。
2. 设法消除避免接触。
3. 电压太高。
3. 降低电压。
零件被腐蚀成深坑1. 电解液中CrO3 含量低。
1. 调整增加之。
2. 铝本身有缺陷,合金成份不均匀。
2. 更换材料。
氧化膜薄,具发白现象1. 夹具和导电棒之接触不良。
1. 改善接触条件。
2. 氧化时间短。
2. 加强氧化时间。
3. 电流密度小。
3. 调整电流密度。
氧化膜上有粉末1. 电解液温度高。
1. 调整之。
2. 电流密度大。
2. 调整之。
膜层发黑1. 工作物件上的抛光膏无洗乾净。
1. 加强氧化前的洗涤。
2. 原铝材料本身有问题。
2. 更换原材料。
氧化膜发红1. 表面准备不好。
1. 改善准备工作。
2. 导电棒和零件夹具间接处不良。
2. 改善接触条件。
四、硬质阳极处理通常出现之缺陷:缺陷原因改善对策氧化膜的厚度不够1. 氧化的时间太短。
1. 增加氧化时间。
2. 电流密度太低。
2. 加大电流密度。
3. 氧化的面积计算不正确3. 正确计算零件面积。
氧化膜层硬度不够高1. 溶液温度高。
1. 降低电解液温度。
2. 电流密度太大。
2. 降低电流密度。
3. 膜层厚度太厚。
3. 缩小氧化时间。
氧化膜被击穿并烧坏工作物件1. 铝合金中含铜量高。
1. 更换原材料。
2. 工作物件散热不好。
2. 加强电解液搅动和冷却3. 工作物件和挂具接触不良。
3. 设法使接触良好。
4. 氧化时给电太急。
4. 注意改善作业过程。