汽车变速器齿轮的疲劳强度分析文件综述
变速器疲劳强度评估及提高措施
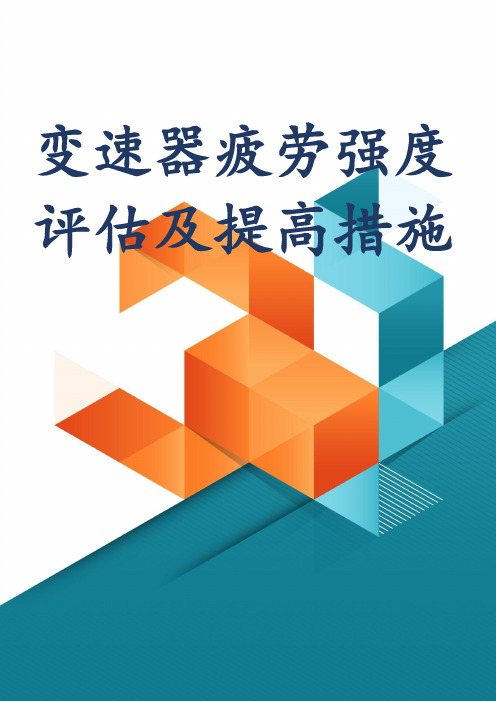
变速器疲劳强度评估及提高措施变速器疲劳强度评估及提高措施变速器是汽车重要的传动装置之一,其疲劳强度评估和提高措施对于保障汽车的可靠性和安全性至关重要。
下面将以逐步思考的方式,分析变速器疲劳强度评估和提高措施。
第一步:了解变速器的工作原理和受力情况首先,我们需要了解变速器的工作原理和受力情况。
变速器主要通过齿轮传动实现不同速度的转换。
在工作过程中,变速器会承受来自发动机的动力输出,并将其传递至车轮。
由于高速运转和长时间使用,变速器会面临较大的疲劳载荷。
第二步:进行变速器疲劳强度评估接下来,我们需要对变速器进行疲劳强度评估。
这可以通过有限元分析等方法来实现。
有限元分析能够对变速器内部各部件的应力分布和变形情况进行模拟,从而得出其疲劳寿命。
通过评估变速器的疲劳强度,我们可以了解其在使用过程中可能出现的问题,并采取相应的措施进行改进。
第三步:优化变速器结构设计根据疲劳强度评估的结果,我们可以对变速器的结构设计进行优化。
通过改变齿轮的材料、减小齿轮的尺寸、增加齿轮的强度等方式,可以提高变速器的疲劳强度。
此外,还可以采用表面强化处理、增加润滑油的冷却效果等手段来提高变速器的疲劳寿命。
第四步:加强制造工艺控制除了优化结构设计,加强制造工艺控制也是提高变速器疲劳强度的重要措施。
在变速器的制造过程中,应严格控制材料的质量,并确保零部件的加工精度和装配质量。
合理的加工和装配工艺能够减小零部件之间的间隙,提高变速器的传动效率和疲劳强度。
第五步:定期检查和维护在变速器投入使用后,定期检查和维护也是确保其疲劳强度的重要手段。
及时更换磨损严重的零部件,保持变速器良好的润滑状态,定期清洗和更换润滑油等,都可以延长变速器的使用寿命,并提高其疲劳强度。
总结:变速器疲劳强度评估和提高措施是确保汽车可靠性和安全性的重要环节。
通过逐步思考,我们可以了解变速器的工作原理和受力情况,进行疲劳强度评估,并根据评估结果优化变速器的结构设计和制造工艺控制。
汽车变速器齿轮疲劳寿命试验强化系数计算分析

汽车变速器齿轮疲劳寿命试验强化系数计算分析栾振;卢剑伟;赵方洲;王涛;程建羊【摘要】以某SUV手动变速器齿轮为研究对象,在一般公路和试验场强化道路、山路和高环路上进行了栽荷谱采集.用雨流计数法得到了载荷的分布形式,采用数理统计方法推断和检验了载荷的分布规律,并将采集到的载荷分为8级载荷谱.将此载荷谱施加到变速器齿轮轴系的多体动力学模型中,得到了关键节点的应力.用Miner 理论计算了各挡齿轮在各个工况下的损伤,从而得到了各种试验场路面和变速器总成台架相对于一般道路的强化系数,对汽车耐久性试验的组织实施和汽车试验场的设计提供了重要依据.【期刊名称】《农业装备与车辆工程》【年(卷),期】2019(057)002【总页数】5页(P9-13)【关键词】疲劳可靠性;载荷谱;强化系数;雨流计数法【作者】栾振;卢剑伟;赵方洲;王涛;程建羊【作者单位】230009 安徽省合肥市合肥工业大学汽车与交通工程学院;230009 安徽省合肥市合肥工业大学汽车与交通工程学院;230009 安徽省合肥市合肥工业大学汽车与交通工程学院;230601 安徽省合肥市江淮汽车集团股份有限公司技术中心;230601 安徽省合肥市江淮汽车集团股份有限公司技术中心【正文语种】中文【中图分类】U463.2120 引言汽车道路可靠性试验是考察和评价汽车可靠性的最终技术措施和手段。
为了缩短汽车研发和试验的周期,道路可靠性试验一般都在配备有各类强化道路的汽车试验场进行。
为了使道路可靠性试验里程与设计里程之间有可比性,需要确定各种试验场路面对于一般道路的强化系数。
强化系数指某一汽车零部件在规定条件下达到相同程度的破坏时,该车在一般道路上行驶里程与强化道路上可靠性试验的行驶里程的比值[1],即K=Sp/S。
由于不同零部件的载荷谱不同,同一强化路下不同零部件的强化系数也不相同。
针对试验场强化系数的确定方法,国内外学者进行了大量研究,并取得了很多成果[2-4]。
汽车变速器齿轮的强度分析【毕业作品】
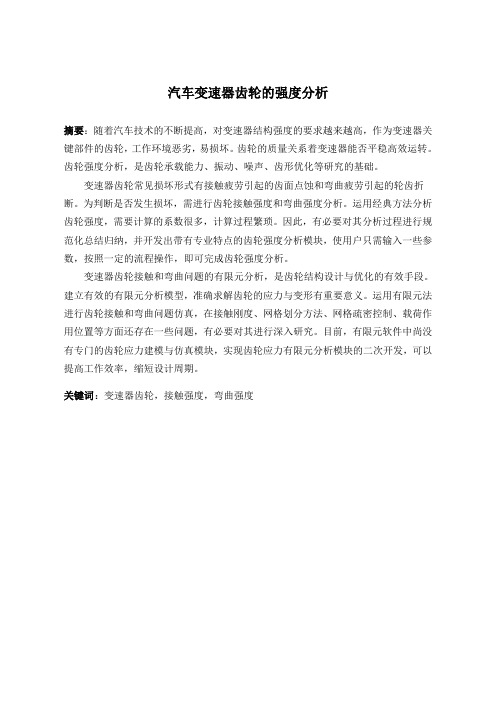
汽车变速器齿轮的强度分析摘要:随着汽车技术的不断提高,对变速器结构强度的要求越来越高,作为变速器关键部件的齿轮,工作环境恶劣,易损坏。
齿轮的质量关系着变速器能否平稳高效运转。
齿轮强度分析,是齿轮承载能力、振动、噪声、齿形优化等研究的基础。
变速器齿轮常见损坏形式有接触疲劳引起的齿面点蚀和弯曲疲劳引起的轮齿折断。
为判断是否发生损坏,需进行齿轮接触强度和弯曲强度分析。
运用经典方法分析齿轮强度,需要计算的系数很多,计算过程繁琐。
因此,有必要对其分析过程进行规范化总结归纳,并开发出带有专业特点的齿轮强度分析模块,使用户只需输入一些参数,按照一定的流程操作,即可完成齿轮强度分析。
变速器齿轮接触和弯曲问题的有限元分析,是齿轮结构设计与优化的有效手段。
建立有效的有限元分析模型,准确求解齿轮的应力与变形有重要意义。
运用有限元法进行齿轮接触和弯曲问题仿真,在接触刚度、网格划分方法、网格疏密控制、载荷作用位置等方面还存在一些问题,有必要对其进行深入研究。
目前,有限元软件中尚没有专门的齿轮应力建模与仿真模块,实现齿轮应力有限元分析模块的二次开发,可以提高工作效率,缩短设计周期。
关键词:变速器齿轮,接触强度,弯曲强度Auto ransmission gear strength analysisAbstract:With the continuous improvement of automotive technology,the demand of the transmission structural strength has become more and more increasingly.As a key component of the transmission,the working conditions of gears are poor and the gears are easy to damage.The quality of gears decides whether the transmission can operate smoothly and efficiently or not.The analysis of gear strength is the basis for the research of the gears carrying capacity,vibration,noise,profile optimization.The common forms of damage are tooth surface pitting caused by contact and tooth broken caused by bending fatigue.As to determine whether the damage occurred,the gear contact and bending strength need to ing classical method to calculate gear strength, many factors need to calculate,the process is very trouble.It is necessary to normalize and summarize the analysis process,and to develop the gear strength analysis professional module.The complete gear strength can be finished the certain input parameters are only provided.The finite element analysis of transmission gear contact and bending is an effective means of gear structural design and optimization.To establish the efficient and precise analysis of the gear contact and bending stress,there are some problems in the contact rigidity,mesh method,mesh density control,load lines.It is necessary to conduct in-depth study.There are so many gear pairs in transmission that it is difficult to analyze and calculate.At present, there is no application software having special module for gear stress simulation analysis.To develop professional modules of parametric modeling and simulation for gear stress analysis can greatly improve efficiency and shorten the design cycle.目录1绪论------------------------------------------------------------------ 1 1.1变速器齿轮强度分析的研究背景---------------------------------------- 1 1.1.1变速器齿轮失效形式------------------------------------------------ 1 1.1.2变速器齿轮强度分析方法-------------------------------------------- 1 1.2变速器齿轮强度分析与评价的研究现状---------------------------------- 2 1.2.1变速器齿轮强度分析的经典方法-------------------------------------- 2 1.2.2变速器齿轮强度分析的有限元法-------------------------------------- 3 1.2.3变速器齿轮强度评价方法-------------------------------------------- 4 1.3有限元软件ANSYS概述------------------------------------------------ 5 1.3.1 ANSYS简介-------------------------------------------------------- 5 1.3.2 ANSYS内部语言简介------------------------------------------------ 5 1.3.3 ANSYS二次开发功能------------------------------------------------ 5 1.4本文主要研究工作---------------------------------------------------- 6 2齿轮强度经典分析方法-------------------------------------------------- 7 2.1齿轮接触应力和齿根应力分析的经典方法-------------------------------- 7 2.1.1齿轮接触应力分析经典方法------------------------------------------ 7 2.1.2齿根应力分析经典方法---------------------------------------------- 7 2.2齿轮许用接触应力分析经典方法---------------------------------------- 8 2.2.1齿轮许用接触应力-------------------------------------------------- 8 2. 2. 2接触寿命系数---------------------------------------------------- 9 2.2.3润滑剂系数------------------------------------------------------- 10 2.2.4速度系数--------------------------------------------------------- 10 2.2.5粗糙度系数------------------------------------------------------- 11 2.2.6工作硬化系数----------------------------------------------------- 11 2.2.7接触尺寸系数----------------------------------------------------- 12 2.3齿轮许用齿根应力分析经典方法--------------------------------------- 12 2.3.1齿轮许用齿根应力------------------------------------------------- 122.3.2弯曲寿命系数----------------------------------------------------- 12 2.3.3相对齿根圆角敏感系数--------------------------------------------- 14 2.3.4相对齿根表面状况系数--------------------------------------------- 15 2.3.5弯曲尺寸系数----------------------------------------------------- 16 2.4本章小结----------------------------------------------------------- 16 3齿轮应力分析有限元法------------------------------------------------- 16 3.1面-面接触有限元分析关键问题---------------------------------------- 17 3.1.1接触面和目标面确定----------------------------------------------- 17 3.1.2单元类型选择----------------------------------------------------- 17 3.1.3接触协调条件----------------------------------------------------- 19 3.2斜齿轮接触应力分析有限元法----------------------------------------- 20 3.2.1单元属性定义----------------------------------------------------- 20 3.2.2网格划分方法研究与应用------------------------------------------- 21 3.2.3接触单元和目标单元生成------------------------------------------- 25 3.2.4接触应力求解与结果分析------------------------------------------- 26 3.2.5接触应力仿真影响因素分析----------------------------------------- 27 3.3斜齿轮弯曲应力分析有限元法----------------------------------------- 30 3.3.2整体单元尺寸对仿真影响分析--------------------------------------- 32 3.3.3线网格细化对仿真影响分析----------------------------------------- 34 3.3.4面网格细化对仿真影响分析----------------------------------------- 37 3.3.5网格划分控制确定------------------------------------------------- 42 3.3.6不同载荷作用位置对仿真影响分析----------------------------------- 43 3.4本章小结-------------------------------------------- 错误!未定义书签。
减速器齿轮的疲劳强度分析

董志文 机械工程系
所学专业:机械设计制造及其自动化 导师姓名: 完成时间: 宁欣 2017 年 5 月 10 日
摘 要
随着汽车工业与交通运输的发展,汽车更新换代的速度不断加快。对于报废 汽车而言,一方面是社会与环境的沉重负担,另一方面又是极具经济价值的“资 源”。报废汽车不仅可以进行材料回收和零部件再制造,部分零部件甚至可以直 接重复利用。 但目前还缺乏对服役零件进行再制造的评判依据,其中零件剩余寿 命是衡量零件再制造的主要依据之一。 论文先从疲劳寿命预测基本方法和流程出发, 介绍了目前惯用的四种疲劳寿 命计算方法,即名义应力法、局部应力应变法、应力场强法和裂纹扩展寿命法。 并对其进行了对比分析, 最终选择适合本文的研究方法名义应力法。接着文中重 点介绍了减速器齿轮疲劳寿命预测过程,包括减速器齿轮三维模型的建立,有限 元模型的建立,其工作载荷谱的提取及齿轮轴材料 S-N 曲线的得出。最后在专 业疲劳分析软件 MSC.Fatigue 中计算出该齿轮轴的疲劳寿命。 最后引用了一个算 例验证了该方法的准确性和可行性。
关键词:齿轮轴;疲劳寿命;三维模型
ABSTRACT
With the development of automobile industry and transportation, the speed of automobile replacement is accelerating. For scrap cars, on the one hand, it is a heavy burden of society and environment, on the other hand, it is a resource with great economic value". Scrap cars can not only carry out material recycling and parts remanufacturing, and some parts can even be reused directly. However, there is still a lack of evaluation criteria for remanufacturing of service parts, in which spare life of parts is one of the main criteria to measure parts remanufacturing. The paper starts from the basic fatigue life prediction method and process, introduces the calculating method of four kinds of fatigue life is currently used, i.e. the nominal stress method, local stress-strain, stress field and crack propagation life method. And make a comparative analysis of them, and finally select the research method which is suitable for this paper, the nominal stress method. Then this paper focuses on the prediction of fatigue life of gear deceleration process, including the establishment of three-dimensional model of gear reducer, finite element model, the extraction and the load spectrum of gear shaft material S-N curve. Finally, the fatigue life of the gear shaft is calculated in the professional fatigue analysis software MSC.Fatigue. Finally, a numerical example is given to verify the accuracy and feasibility of the proposed method. Keywords: gear shaft; fatigue life; 3D model
变速器齿轮接触疲劳强度分析

变速器齿轮接触疲劳强度分析刘大龙;李稳迪;张瑞;张凯;施伟辰【摘要】基于ANSYS对变速器各档啮合齿轮进行瞬态动力学分析,再结合齿轮接触理论和疲劳损伤累积理论,求得各档齿轮的接触应力大小和疲劳寿命曲线.从所求结果看出,二档和三挡齿轮啮合时接触应力不大,小于齿轮的许用接触应力,且疲劳寿命较高,满足设计要求;一档和四挡齿轮啮合时的接触应力大于了齿轮的许用接触应力,且疲劳寿命较低,不能满足设计要求.基于以上原因,利用齿向和齿廓相结合的轮齿修形方法,对一档和四挡齿轮进行了轮齿修形,从最终求得结果来看,两组啮合齿轮的接触应力均大幅度降低,同时疲劳寿命得到了提高,轮齿修形达到了很好的效果.【期刊名称】《汽车实用技术》【年(卷),期】2018(000)017【总页数】5页(P33-36,138)【关键词】变速器;齿轮;瞬态动力学;接触应力;疲劳寿命【作者】刘大龙;李稳迪;张瑞;张凯;施伟辰【作者单位】上海海事大学物流工程学院,上海 200120;上海海事大学物流工程学院,上海 200120;上海海事大学物流工程学院,上海 200120;上海海事大学物流工程学院,上海 200120;上海海事大学物流工程学院,上海 200120【正文语种】中文【中图分类】TH123引言在蒸汽机车诞生之时,人类就行通过一种装置能够改变蒸汽机车的输出载荷,以便达到人类想要达到的要求。
在1784年,James Watt申请了常啮合齿轮传动机构的专利,至此出现了变速器的雏形。
1879年,塞尔登成功申请了带有离合器和倒挡中间轴转动装置的变速器专利。
1886年,戈特利布∙戴勒姆创造了世界上第一台真正的汽车0。
发动机的动力经由齿轮和链条传至后轮,从而实现了汽车的行驶。
在接下来的100多年的时间里,变速器呈现出多样性发展,手动变速器、自动变速器、双离合变速器、无级变速器等应运而生。
1 变速器有限元模型创建1.1 三维实体模型创建本文对利用SolidWorks对某乘用车五档汽车变速器进行3D建模,主要包括传动轴、齿轮,其中传动轴包括输入轴、中间轴、输出轴和倒挡轴。
汽车变速器齿轮设计及问题研讨

汽车变速器齿轮设计及问题研讨1. 引言1.1 研究背景汽车变速器齿轮设计是汽车传动系统中的核心部件,直接影响着汽车的性能和稳定性。
随着汽车工业的快速发展,对于汽车变速器齿轮设计的要求也越来越高。
目前市场上存在着很多变速器齿轮设计方面的问题,例如噪音过大、传动效率低、寿命短等。
这些问题不仅影响了汽车的运行效果,还可能对驾驶员的驾驶体验造成不良影响。
进一步研究汽车变速器齿轮设计原理及问题成为了当下的重要课题。
通过对现有变速器齿轮设计进行深入分析,找出问题所在,并提出优化设计方法,可以有效提高变速器齿轮的性能和可靠性。
对材料选择与加工工艺进行研究,也能够为汽车变速器齿轮的设计和制造提供更好的支持。
通过性能测试与评估,更加客观地了解汽车变速器齿轮的性能表现,为进一步的优化设计提供依据。
【这是研究背景的内容,总字数2000字。
】1.2 研究目的汽车变速器齿轮设计及问题研讨研究目的:研究目的是通过深入探讨汽车变速器齿轮设计及存在的问题,找出优化设计方法,提高变速器的效率和性能,减少故障率,增强汽车的可靠性和耐久性。
研究目的还包括对现有的材料选择和加工工艺进行分析和评估,以寻找更加适合变速器齿轮的材料和工艺,从而提高变速器的质量和寿命。
通过对变速器齿轮的性能测试和评估,进一步验证优化设计方法的可行性和效果,为汽车行驶安全和稳定提供更好的保障。
研究目的在于为汽车行业提供更加先进和可靠的变速器技术,促进汽车工程的发展和进步,为广大汽车用户提供更好的驾驶体验和安全保障。
通过本研究,希望能够为汽车变速器齿轮设计领域的研究和实践提供一定的参考和借鉴,推动汽车工业的持续发展和提升。
1.3 意义和价值汽车变速器齿轮设计及问题研讨的意义和价值在于提高汽车传动系统的效率和性能,从而提升整车的性能和驾驶体验。
通过深入研究变速器齿轮的设计原理,分析现有设计中存在的问题,探讨优化设计方法和材料选择与加工工艺,可以有效提高汽车变速器的可靠性和耐久性,减少故障率和维修成本。
变速器从动齿轮疲劳开裂分析

分装线共7 个部分组成。B C D 是车身存储区,负责从涂
疲 劳开 裂 ,并最 终 导致齿 轮 轮 毂的疲 劳开 裂 。
c焊缝 的熔深 不 足是 导 致从 动齿 轮 疲 劳开 裂 的主 .
要 原 因。 而焊 缝熔 深 的不 足则 与焊 接 过程 中电子 束倾 斜偏 离 接合 缝有 关 。
2 年 第6 01 2 期
亦有影响。 圈
汽 车 工 艺 与 材 料 A& J T M 51
生
产 装 备
汽 车装 配线 线速 提高 的解决 方案
摘要 :以总装车 间B 线设计 节拍 由3 辆/ 提升 到4 辆/ 线速 提高 的解决 方案 为例 ,综合 分析 了 5 h 2 h 汽车装 配生产线 线速最 大能力 ,识别 出输送 设备 系统、工 艺设备 的节拍提升瓶颈 ,并结 合工艺需 求 详细 阐述 了一 系列 瓶颈 改造 的 可行性 解决 方案。该 方案 以保证 设备 的正 常使 用寿命 及 不增加 日常 维护 为前 提而制 定 ,改造 过程 中对 瓶颈点 数据 进行 了详细 分析 ,简化输 送设备工 艺动作 ,优 化A V G (自动 导航小车 ) 运行 路线 、涂胶 机器人动 作等 。 以投入较 少的 改造成 本产 生最 大化 的效益 ,使 生 产线效 率提升 了2 % ,充分体 现 了汽车行 业低成本 、高价值 的精益 生产模 式。 0
设计 节 拍 3 辆 / 5 h,由于 市 场 的 旺 盛 需 求 ,公 司 果 断
改造 活 动 。
1 生产 线 概 况
总 装 B 是 由车 身 存储 分 配 区 ( D 线 B C)、 内饰 一 线 、 内饰 二线 、底 盘 一线 、底 盘 二线 、终 线及 发 动机
决 策 挖 掘 总 装 最 大 产 能 输 出 , 提 升 B 产 能最 大 输 线 出 , 目标 为4 辆 / 。 制造 部 设 备 团 队 进 行 了系 统 的 2 h 技 术 论 证 、 分 析 及 识 别 瓶 颈 设 备 ,开 展 了一 系 列 的
汽车变速器齿轮强度的分析与评价

汽车变速器齿轮强度的分析与评价一、本文概述本文旨在深入分析与评价汽车变速器齿轮的强度特性。
汽车变速器作为汽车动力传动系统的重要组成部分,其性能直接影响到汽车的动力性、经济性和驾驶舒适性。
而齿轮作为变速器中的关键元件,其强度性能对于变速器的整体性能具有决定性的影响。
因此,对汽车变速器齿轮强度的分析与评价,对于提高汽车性能、保障行车安全以及推动汽车工业的持续发展具有重要意义。
本文将从齿轮材料的选择、齿轮的结构设计、制造工艺以及使用环境等多方面进行综合分析,探讨齿轮强度的主要影响因素。
结合现代强度分析理论和方法,建立汽车变速器齿轮强度的评价体系,为齿轮的优化设计和制造提供理论支持和实践指导。
本文还将对国内外相关研究成果进行综述,以期在总结前人经验的基础上,为齿轮强度的进一步研究提供参考和借鉴。
二、齿轮强度理论基础齿轮作为汽车变速器中的核心部件,其强度性能直接决定了变速器的使用寿命和性能稳定性。
因此,对齿轮强度的深入分析和评价显得尤为重要。
齿轮强度分析主要依赖于强度理论,其中最为基础和常用的是疲劳强度理论和接触强度理论。
疲劳强度理论主要研究齿轮在循环交变应力作用下的疲劳失效问题。
齿轮在传动过程中,齿面承受的是周期性的交变应力,当这种应力的幅值超过材料的疲劳极限时,齿轮就会产生疲劳裂纹,进而导致断裂。
因此,疲劳强度分析是齿轮强度分析的重要组成部分。
在实际分析中,通常使用名义应力法、局部应力应变法或损伤力学法等方法来评估齿轮的疲劳寿命。
接触强度理论则主要研究齿轮在啮合过程中的接触应力分布及其引起的齿面失效问题。
齿轮啮合时,齿面间的接触应力分布不均,如果最大接触应力超过齿面材料的许用接触应力,就会发生齿面点蚀、胶合等失效形式。
接触强度分析通常基于赫兹接触理论和弹塑性力学理论,通过计算齿面接触应力和接触变形来评估齿轮的接触强度。
除了上述两种基本强度理论外,齿轮强度分析还需要考虑齿轮的弯曲强度、剪切强度以及热强度等因素。
- 1、下载文档前请自行甄别文档内容的完整性,平台不提供额外的编辑、内容补充、找答案等附加服务。
- 2、"仅部分预览"的文档,不可在线预览部分如存在完整性等问题,可反馈申请退款(可完整预览的文档不适用该条件!)。
- 3、如文档侵犯您的权益,请联系客服反馈,我们会尽快为您处理(人工客服工作时间:9:00-18:30)。
汽车变速器齿轮的疲劳强度有限元分析
汽车从问世至今已有一百余年,尤其是汽车大批量生产以及相应的汽车工业发展以来,汽车已经对世界经济的发展与人类生活水平的提高,产生了难以估计的巨大影响,为人类社会的进步与发展做出了难以磨灭的巨大贡献。
汽车变速器是汽车传动系统的重要总成,其主要功能是通过转变发动机曲轴的转速及转矩,来适应汽车在起步、加速、行驶过程中以及在不同行驶条件下,对驱动车轮牵引力和车速的不同要求的需求。
汽车的动力性、经济性、操纵的轻便性与可靠性、传动的平稳性与效率等都受到汽车变速器结构的直接影响。
为了确保变速器具有良好的工作性能,对于变速器的设计一般有下面几点要求:
1.确保变速器的档位和传动比选择正确,要与发动机的参数优化匹配。
2.操纵简便、迅捷省力。
3.传动效率高,工作平稳,噪音低。
4.体积小、质量轻、承载能力强,工作稳定可靠
5.寿命长
近些年,随着汽车技术的飞速发展,人们对汽车变速器的承载能力以及工作的可靠性要求是越来越高。
在变速器设计与研究工作中,对变速器主要零部件的刚度与强度的计算、校核的意义十分重大。
变速器齿轮是变速器中的重要部件,起着传递发动机转矩的巨大作用。
由于汽车速度的不断变化与频繁的换档,变速器齿轮的工况比较复杂多变,而且工作环境较为恶劣,因此对其进行准确科学的建模与强度计算显得尤为必要。
汽车变速器使用的齿轮有两种:直齿圆柱齿轮与斜齿圆柱齿轮。
与直齿圆柱齿轮对比,斜齿圆柱齿轮具有使用寿命长、运转平稳、噪音低等优点;缺点是制造工艺复杂,工作时有轴向力,容易对轴承造成损伤。
变速器中均将斜齿圆柱齿轮作为常啮合齿轮,直齿圆柱齿轮仅使用在低档与倒档。
传统的齿轮疲劳强度分析是建立在弹性力学的基础上,但在计算分析过程中有不少的假设,不能准确的反应齿轮在使用过程中的应力应变。
传统的设计方法还有精度低,易造成浪费的缺点。
此外,传统设计方法的结果受到设计人员所具有的知识程度、经验水平以及对实际掌握程度多少等多方面的因素而影响。
有限元分析法因为有着快速,精准以及计算灵活的优点,可以全面掌握齿轮的受力状态和应力水平,所以被广泛运用。
使用ANSYS对齿轮进行强度分析,可以给齿轮的疲劳强度设计提供可靠的依据,实现计算机辅助设计。
通过ANSYS有限元分析可以得到构件的刚度、强度等力学性能,之后将结果返到设计过程中,修改其中不合理的地方,这样可以加快设计进程、缩短研制周期,通过反复的优化,提高设计质量。
因此使用有限元分析法在齿轮的疲劳强度分析上具有非常明显的优势。
本文准备用ANSYS有限元软件对变速器齿轮模型进行网格划分和加载,分析计算齿轮的疲劳强度。
如今,研究变速器齿轮强度的方法主要有两种:一是试验研究法,利用齿轮的实际实验数据和结果作为基础,分析强度与变形,这个方法实用性较强;二是分析计算法,利用经典力学、边界元、有限元等方法,通过建立零部件的模型,将计算结果作为基础来研究其强度。
但因为试验研究需要花费较长的时间与昂贵的费用,并且,试验研究只能在成品上进行,设计阶段无法进行。
所以,人们很早就将精力投放在分析计算法上研究齿轮的强度。
20世纪50年代以前,主要是利用经典力学来分析机械结构强度问题,先将复杂的实际结构转换成简单的力学模型,再寻找一些方法来使较复杂的高次超静定或者非线性力学模型变成依据当时的条件能计算的静定、线性或者低次超静定模型,以此获得解答。
但这样的方法也有弊端,就是只能使用在各向同性体在弹性范围内受到小的变形问题,并且由于计算的模型结构过于简单,容易导致计算结果和实际情况相差很大。
由于科学技术的飞速发展,有限元法与边界元法得到广泛的使用。
有限元法是利用离散的思想,将弹性连续体分为有限个单元组合而成的集合体,利用单元分析和组合,然后得到一组联力方程组,最终求出数值解。
利用有限元方法,可以得到齿轮的变形分布与应力分布等数据,使用这些数据可以对汽车变速器齿轮进行强度校核、计算使用寿命、优化设计等工作。
20世纪40年代出现了离散化的思想。
在1941年时,A.HRENNIKOFF率先提出利用构架问题求解弹性力学的问题,在当时被称为离散元素法。
到了1943年,R.CUORANT在求解扭转问题时,将截面分成若干个三角形区域来表征翘曲函数。
,并且在各个三角形区域内设定了一个线形翘曲函数。
这是对里兹法的推广,其实就是有限元法的基本思想,在电子计算机出现后这一思想得到应用。
到了20世纪50年代,由于航空工业的需要,美国波音公司Turner, Clough, Martin和Topp等人率先采用三节点三角形单元,通过矩阵位移法来解决平面问题。
同一时间,德国斯图加特大学的,从此这个名称得到了广泛认可[1]。
20世纪60年代有限单元法获得了快速的发展,因为众多科学家参加了这项工作,所以有限单元法理论基础得到了奠定。
1963年,Besseling等人证明了有限元法是基于变分原理的Ritz法的另一种形式。
1969年,Oden将有限元法推广应用于加权残量法(如Galerkin法)。
同年,Zienkiewicz提出了等参元的概念,从而使有限元法更加普及与完善。
并且发展了不同的单元模式,扩大了有限单元法的使用范围。
从弹性力学平面问题扩展至空间问题与板壳问题;从静力平衡问题扩展至稳定与动力学问题;从弹性问题扩展至弹性塑性与粘弹性问题、疲劳和断裂问题等。
20世纪70年代之后,随着电子计算机硬件和软件技术的发展,有限元法的研究和应用得到了飞速地进展。
出现了一些大型结构分析软件,如SAP,NONSAP等,安装在大中型计算机上。
80年代,多种功能扩大,大型通用程序如ADINA等,微型计算机,前后处理出现。
90年代,领域扩大,前后处理功能增强,大型商用软件,如ANSYS、MARC、NASTRAN 等。
目前,面向工程,与CAD结合成为CAE(计算机辅助工程)软件。
在工程领域,有限单元法率先用于航天航空工程,如今已快速推广到机械制造、汽车设计、船舶制造、建筑等多种工程领域,并且从固体力学领域扩展至流体、电磁场、电场和振动等学科。
有限元技术的问世,为工程设计领域提供了一个非常强而有力的计算工具,通过半个世纪的发展,它越来越成熟,几乎在所有的工程领域里发挥着日趋重要的作用。
变速器零部件齿轮的研究设计是有限元技术应用领域的一部分。
其应用提高了汽车变速器零部件设计的可靠性,缩短了设计的周期。
如今国内许多科研院所都使用有限元分析法对变速器进行研究,例如中国北方车辆研究所对变速箱有限元强度计算与优化的研究[2]、同济大学对桑塔纳轿车主减速器齿轮的有限元分析[3]等。
近些年,随着计算机软硬件水平的不断提高,变速器零部件的有限元分析向着更加精确细致的方向发展着。
在计算齿轮应力分布数值的方法中,有限元法毫无疑问是首选方法。
但在齿轮有限元计算中常常碰到的问题是,为了提高计算精度则需要将计算模型增大,与之而来的是计算费用的增加或者是计算机内存不足而无法运行。
为了兼顾计算精度与计算模型的矛盾,其有效途径则是采用局部网格细化。
本文将以变速器中齿轮为研究对象,利用大型有限元分析软件ANSYS,对三维造型软件做好的齿轮模块进行疲劳强度分析计算。
参考文献
[1]王立功.有限元的发展及应用[M].北京:人民交通出版社,2003:4-5.
[2]邵鹏礼,魏来生等.传动箱有限元强度计算与优化[J].车辆动力与技术:2002,87(3)
[3]李天兵,吴光强等.汽车变速器主减速齿轮应力场有限元分析[J].计算机技术应用:1999,3。