无损检测作业指导书工艺规程
NB47013无损检测通用工艺规程
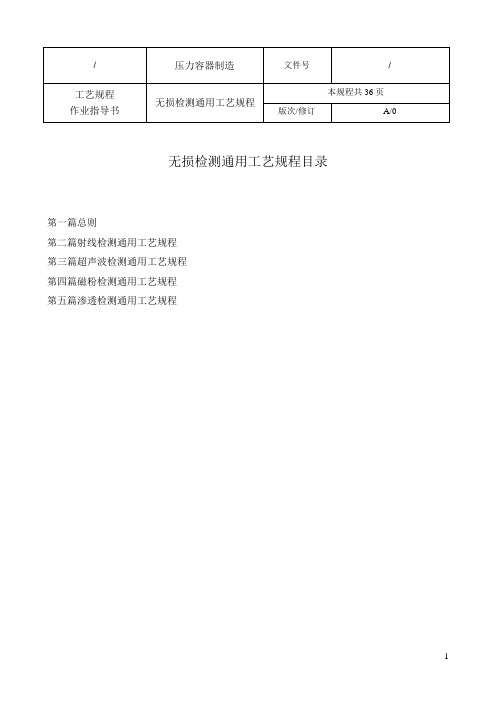
无损检测通用工艺规程目录第一篇总则第二篇射线检测通用工艺规程第三篇超声波检测通用工艺规程第四篇磁粉检测通用工艺规程第五篇渗透检测通用工艺规程无损检测通用工艺总则1.1 主题内容与适用范围本工艺规程规定了射线检测(RT)、超声波检测(UT)、磁粉检测(MT)、渗透探伤(PT)四种无损检测的工艺方法。
本工艺规程适用于本公司特种设备制造、安装、改造、维修原材料、零部件和焊缝的无损检测。
1.2 引用标准1)《固定式压力容器安全技术监察规程》2)《特种设备无损检测人员考核规则》3)《压力管道安全技术监察规程-工业管道》4)NB/T47013-2015《承压设备无损检测》1.3一般要求1.3.1 选择原则1.3.1.1 特种设备RT、UT、MT、PT的选择及抽检率应按《容规》、《压力管道安全技术监察规程-工业管道》、GB150、GB151及图样的要求执行。
1.3.1.2 有裂纹倾向的材料应在焊后24小时后,才能进行焊缝无损检测。
1.3.1.3 对要求无损检测的角接接头、T型接头,不能进行RT或UT检测时,应进行表面无损检测。
1.3.1.4 凡铁磁性材料制成的特种设备及零部件,优先使用MT检测表面缺陷确因结构形状等原因不能使用MT检测时,方可采用PT检测。
1.3.2 检测人员1.3.2.1 从事特种设备无损检测人员必须应按照《特种设备无损检测人员考核规则》的要求取得相应的无损检测资格。
1.3.2.2 取得不同无损检测方法的各技术等级人员,只能从事与该等级相应的无损检测工作,并负相应的技术责任。
1.3.2.3 各种检测方法的报告,均由II级以上资格人员签发,并加盖公章。
1.3.2.4 从事射线检测人员上岗前应进行辐射安全知识的培训,并取得放射工作人员证。
1.3.2.5 从事磁粉、渗透检测工作人员,不得有色盲。
1.3.2.6 射线检测人员未经矫正或经矫正的近(距)视力和远(距)视力应不低于5.0(小数记录值为1.0),测试方法应符合GB11533的规定。
无损检测作业指导书

无损检测指导书1目的与范围目的是使井架、底座、天车的无损检测质量得到有效控制。
所使用的检测方法包括渗透检测、磁粉检测与超声波检测、X射线检测。
2引用文件API spec 4F《钻井和修井井架、底座规范》AWS D1.1《钢结构焊接规范》ASTM A578《超声斜射波束接触法检测方法》ASTM E709《磁粉检测方法》ASTM E165《渗透检测方法》JB/T4730-2005《承压设备无损检测》3 一般要求3.1 人员资格参加无损检测的人员,至少有一名经过权威机关培训,并取得该无损检测方法的中级人员。
3.2 设备使用的设备应是经校验合格的设备。
磁粉设备应每年校验一次;超声波设备每年校验一次,但水平线性、垂直线性应每月校验一次。
3.3 被检件的表面准备所有被检表面首先应经目检合格,且无影响无损检测的杂物。
4 磁粉检测由设计者依据标准、规范和技术要求确定检测部位和关键焊缝。
4.1检测方法ASTM E709⑴磁粉检测以湿磁粉连续法进行检测。
选用黑磁粉、无味煤油配制的浓度为10~20g/l(沉淀浓度1.2~2.4ml/100ml)的磁悬液。
机加工表面进行湿荧光磁粉连续法进行检测。
选用荧光磁粉、无味煤油配制的浓度为0.5~3.0g/l(沉淀浓度0.1~0.4ml/100ml)的磁悬液。
灵敏度使用A-30% 试片。
⑵焊缝表面应使用交流小磁轭,进行相互垂直方向的磁化检测。
⑶磁化通电时间为2~4秒,磁悬液必须在通电时间内施加完毕,且至少应反复磁化两次。
⑷若焊缝母材料有延迟裂纹倾向时,磁粉探伤应安排在焊后48小时后进行。
⑸当焊缝及其热影响区表面难以清理至金属色,影响磁痕观查时,应使用白色反差增强剂以增加色彩对比度。
4.2 灵敏度交流小磁轭的提升力应不小于45N(4.5千克力)。
4.3 缺陷的判定除能确认磁痕是由于工件材料局部磁性不均或操作不当造成之外,其它一切磁痕显示均作为缺陷处理。
4.4磁粉检测的验收(依据AWS D1.1第六节):4.4.1任何裂纹都不合格,不论其尺寸或部位。
无损检测作业指导书
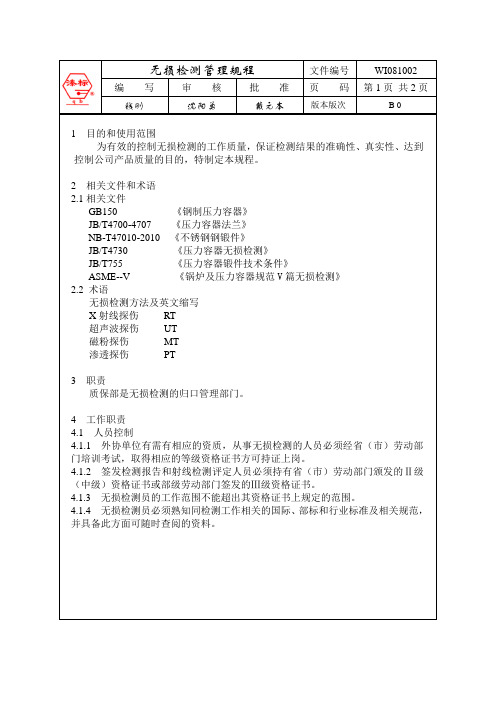
文件编号
WI081002
编写
审核
批准
页码
第1页共2页
钱刚
沈阳勇
戴元本
版本版次
B 0
1目的和使用范围
为有效的控制无损检测的工作质量,保证检测结果的准确性、真实性、达到控制公司产品质量的GB150《钢制压力容器》
JB/T4700-4707《压力容器法兰》
4.1.1外协单位有需有相应的资质,从事无损检测的人员必须经省(市)劳动部门培训考试,取得相应的等级资格证书方可持证上岗。
4.1.2签发检测报告和射线检测评定人员必须持有省(市)劳动部门颁发的Ⅱ级(中级)资格证书或部级劳动部门签发的Ⅲ级资格证书。
4.1.3无损检测员的工作范围不能超出其资格证书上规定的范围。
NB-T47010-2010《不锈钢钢锻件》
JB/T4730《压力容器无损检测》
JB/T755《压力容器锻件技术条件》
ASME--V《锅炉及压力容器规范V篇无损检测》
2.2术语
无损检测方法及英文缩写
X射线探伤RT
超声波探伤UT
磁粉探伤MT
渗透探伤PT
3职责
质保部是无损检测的归口管理部门。
4工作职责
4.1人员控制
4.1.4无损检测员必须熟知同检测工作相关的国际、部标和行业标准及相关规范,并具备此方面可随时查阅的资料。
无损检测管理规程
文件编号
WI081002
编写
审核
批准
页码
第2页共2页
钱刚
沈阳勇
戴元本
版本版次
B 0
4.3现场检测工作的实施
4.3.1无损检测员按客户订单上的要求进行检测准备工作。
4.3.2无损检测员按无损检测工艺规程和相关规定进行现场检测工作,检测的情况要如实记录,发现的情况要画图说明。
无损检测作业指导书
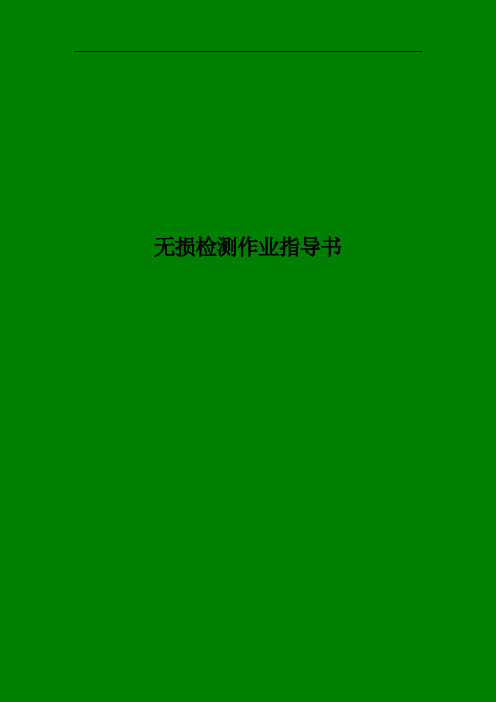
无损检测作业指导书一、射线探伤检测1.X射线对人体有不良影响,应尽量避免射线的直接照射及散射线的影响。
2.从事X射线工作人员应配有剂量仪,并对计量仪定期进行检定。
3.检验人员及审核人员的资质必须符合国家的相关规定。
4.应选用合适的透照方式,并符合JB4730.2-2005标准要求。
5.在透照前应对工件表面进行外观检查,表面的不规则状态在底片上的图像,不掩盖焊缝中的缺陷或与之混淆,否则应做适当的修理。
6.胶片的定位标记和识别标记,应符合JB4730.2-2005的标准规定。
7.像质计的要求及摆放位置,应按JB4730.2-2005的标准规定执行。
8.射线透照等级要求至少达到JB4730.2-2005的标准AB级。
9.胶片和増感屏的要求,应符合国家相关规定的要求。
10.透照条件的选择应视具体情况,选择合适的透照条件,以达到最佳的检测灵敏度。
11.胶片处理应按胶片的使用说明书或公认的有效处理方法,可采用自动或手工冲洗的方法。
12.显、定影液的控制,应采用添加补充液的方法,来维持显、定药液的恒定。
如洗片效果仍不佳,应更换全新的药液。
13.在底片上应显示出最小线径及像质指数,底片的黑度应符合国家的相关规定的要求。
14.底片质量不允许存在的假缺陷:(1)灰雾(2)洗片处理时产生的条纹、水迹或化学污物等缺陷。
(3)划痕、指纹、脏物、静电痕迹、黑点或撕裂等。
(4)由于増感屏不好造成的缺陷显示。
15.评片应在专用的,室内光线暗淡,但不全暗,室内照明用光不得在底片表面产生反射的暗室。
16.观片灯的亮度应符合国家相关规定的要求。
17.缺陷的评定及验收等级,严格按照JB4730.2-2005的标准要求执行。
18.探伤报告的内容及要求,应符合国家相关标准规定的要求。
19.底片和检测报告保存期不得少于7年,7年后若用户需要可由用户保管。
20.探伤合格的工件上,应做永久性或半永久性的标记。
21.对于需要返修的焊缝,检测长度为补焊部位延长到两端50毫米。
无损检测VT PT作业指导书SOP

6.记录和反馈
例图
例图
(2)测量 尺寸; 例图
眼睛应位于距离 600 mm处,观 察角度不小于约30°
主要测量点:焊缝宽度、 余高,缺陷的长处
编制修订履历
主要内容描述 新文件编制
审核/日期:
批准/日期:
5、焊后检 验 (1)清理焊 缝检验区;
检查内容:层间清理氧化皮、 夹渣、气孔等影响焊缝质量
的异物或缺陷
例图
例图
(2)检验; 例图
3、焊前 检验 (1)检查 焊接件坡 例图
(3)检查 焊件定位
例图
(2)检查ห้องสมุดไป่ตู้坡口区域
例图
检查点: 坡口角度
和钝边
检查点:焊 接区
检查点:坡口间 隙和径向错边量
例图
清理掉影响判定的氧化 皮、飞溅等,以免误判
客户名称
适用范围 一作业 流程
1.确认产品和工 艺要求
产品名称 2.检测前准备
检测方法
目视检测VT
碳钢、不锈钢和铝合金焊缝的外观检验
文件编号
3.焊前检测
4.焊中检验
5.焊后检验
二、作 业步骤 1、确认 产品和
根据《客车真空集便装置污物箱技术规格书》,产品污物箱的焊缝外观符合ISO 5817-B,需进行100%VT, 检测内容和要求: (1)对各 个(2焊)对接各件 个焊接件
(3)对各个焊接件焊后焊缝尺寸和外观质量进行检测:①焊缝及热影响区表面不得有气孔、夹渣、裂纹、弧坑 、未填满、焊瘤等缺陷,②焊缝余高≤1+0.15b(mm),③焊接咬边≤0.1t,且最大不能超过0.35mm;
2、检测 前准备 (1)工具 、(2用)检具查准 条(3件)检准测 人员应经
无损检测作业指导书
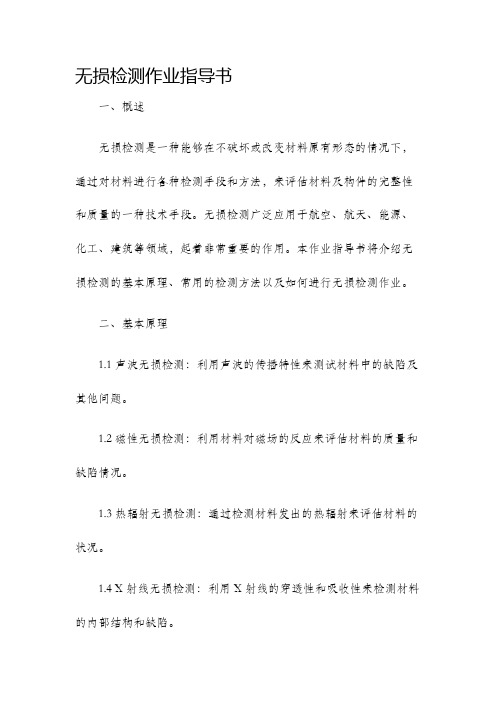
无损检测作业指导书一、概述无损检测是一种能够在不破坏或改变材料原有形态的情况下,通过对材料进行各种检测手段和方法,来评估材料及构件的完整性和质量的一种技术手段。
无损检测广泛应用于航空、航天、能源、化工、建筑等领域,起着非常重要的作用。
本作业指导书将介绍无损检测的基本原理、常用的检测方法以及如何进行无损检测作业。
二、基本原理1.1 声波无损检测:利用声波的传播特性来测试材料中的缺陷及其他问题。
1.2 磁性无损检测:利用材料对磁场的反应来评估材料的质量和缺陷情况。
1.3 热辐射无损检测:通过检测材料发出的热辐射来评估材料的状况。
1.4 X射线无损检测:利用X射线的穿透性和吸收性来检测材料的内部结构和缺陷。
1.5 超声波无损检测:利用超声波在材料中传播的速度和反射来判断材料的质量和缺陷情况。
三、常用的检测方法2.1 直接声传播法:将声源直接放置在被检测的材料上,并通过分析声波的传播情况来判断材料的状况。
2.2 磁粉检测法:通过在被检测材料表面涂覆磁性粉末,在施加磁场的情况下观察磁性粉末的分布,以判断材料是否存在缺陷。
2.3 热红外检测法:利用热红外相机来检测材料发出的热辐射,通过分析热辐射的分布情况来评估材料的状况。
2.4 射线透射法:利用X射线的穿透性和吸收性,通过对材料进行透射检测,观察X射线透射的情况来评估材料的内部结构和缺陷。
2.5 超声波扫描法:利用超声波在材料中的传播速度差异和反射情况,通过对超声波信号进行扫描和分析,来判断材料的完整性和质量。
四、无损检测作业步骤3.1 确定检测目标和需求,了解被测材料的特点,以及可能存在的缺陷情况。
3.2 选择合适的检测方法和设备,根据被测材料的特点和要求,选择适用的无损检测方法和设备。
3.3 准备工作,包括材料的清洁、表面处理、安全措施等工作。
3.4 进行无损检测作业,根据选定的检测方法和设备,按照操作规程进行检测,记录数据和观察结果。
3.5 数据分析和结果评估,对检测数据进行分析和评估,判断材料的质量和缺陷情况。
RT通用工艺规程及作业指导书
1.4无损检测工艺规程的编制要求
v
按照NB/T47013.1《承压设备无损检测 通用要求》 标准4.3.2.2 条规定;应根据相关法规、产品标准、有 关的技术文件和本标准的要求,并针对本检测单位的特 点和技术条件编制工艺规程;工艺规程应按本部分和 NB/T 47013.2~NB/T 47013.13的规定明确其相关因素的 具体范围或要求,如相关因素的变化超过规定时,应重 新编制或修订。 编制工艺规程的依据中相关因素(类似焊接工艺评定 中的重要变量)
v v v
h)增感屏和滤光板型号(如使用); i) 暗室处理方法或条件; j) 底片观察技术;
v
v v v v v v
2.3、编制依据的标准、法规或其他技术文件
NB/T47013-2015《承压设备无损检测》 产品标准(如GB150等) 《锅炉安全技术监察规程》 《固定式压力容器安全技术监察规程》 《压力管道安全技术监察规程》 本机构的质量管理体系要求等
1.2作用: 工艺规程是组成技术文件的主要部分,是工艺 装备、材料定额、工时定额设计与计算的主要依据,是 直接指导检测的技术法规,它对产品成本、劳动生产率、 原材料消耗有直接关系。工艺规程编制的质量对保证产 品质量起着重要作用。 1.3、编制原则 (1)、所编制的工艺规程必须保证检测工作质量,达到 相关法规、标准各项技术要求。 (2)、工艺过程应具有较高的生产效率。 (3)、尽量降低检测成本。 (4)、注意减轻检测人员的劳动强度,保证安全。
v v v v v v v v
2.4、无损检测操作指导书的编制原则 根据无损检测操作指导书的作用,其编制要符合 “针对性、符合性、可操作性”三方面的原则。
v △针对性 v 要针对特定的检测对象,编制特定的无损检测
无损检测作业指导书
无损检测作业指导书一、背景介绍无损检测(Non-Destructive Testing,NDT)是指在不破坏被测对象完整性的前提下,利用各种技术手段和设备对其进行检测、测量、评价或判定的一种方法。
在工业领域中,无损检测被广泛应用于材料、构件和设备的质量检测、安全评估和性能监测,以确保生产和运营过程的安全和可靠。
无损检测作为一项关键技术,对从航空航天到能源和化工等各个领域的工业生产和产品质量有着重要影响。
本作业指导书旨在为相关从业人员提供一份详细的无损检测作业指南,以确保检测工作的质量和准确性。
二、作业前准备1. 熟悉被测对象:在进行无损检测之前,必须对被测对象有足够的了解,包括其构成、制造工艺和使用条件等。
这将有助于选择合适的检测方法和设备,以及准确评估结果。
2. 熟悉检测方法和设备:根据被测对象的特点,选择适合的无损检测方法和设备。
熟悉这些方法和设备的原理、操作步骤和注意事项,以确保正常进行检测工作。
3. 检测区域准备:清理被测对象的表面,确保其干净、无油污和杂质。
必要时,使用适当的清洗剂进行清洗。
另外,确保检测区域的通风良好,以便于操作和排除可能的风险。
4. 确定检测参数:根据被测对象的性质和要求,确定适当的检测参数,如波长、频率、电流功率等。
这将有助于获取准确的检测结果,并快速发现可能存在的缺陷。
三、作业步骤1. 根据被测对象的特点和要求,选择适当的无损检测方法,如超声波、射线、涡流、磁粉等。
了解每种方法的原理、优缺点,并根据实际情况进行选择。
2. 根据选择的无损检测方法,准备相应的设备和工具。
确保设备的正常工作状态,如电源供应、传感器的校准和标定等。
3. 在检测之前,对被测对象进行必要的预处理。
例如,清洁表面,移除可能影响检测效果的覆盖物和污垢。
4. 根据检测要求,将传感器或探头与被测对象适当接触或定位。
确保传感器的位置和角度与被测对象的几何形状和缺陷类型相匹配。
5. 开始无损检测,按照预定的检测规程和流程进行操作。
超声波无损检测作业指导书
超声波无损检测作业规范1.0目的本程序规定了依据API14A,对锻件与锻造产品进行超声波探伤测试的方法,人员要求以及接受的标准。
2.0•范围此规范适用于为本公司所有提供超声波探伤的供应商,也适用于诺斯石油工具按照相关规范的要求进行产品超声波探伤测试的情况。
3.0职责质量控制部负责按本规范要求的执行,确保所有产品符合本规范要求。
4.0术语定义无5.0程序5.1 安全与环境5.1.1 在使用者和承包人特殊安全,健康和环境方针的指导下安全地操作是使用者/承包人的责任。
5.1.2 安全操作由供货商的材料安全数据单(MSDS)来控制,在使用者和承包人特殊安全,健康和环境方针的指导下,使用者/承包人应依照本程序负责对浪费或危害环境的做法进行控制。
5.2 人员资格5.2.1 依据以下规范,进行检测、说明及对结果作出评价、记录的人员应具备至少2级资格证明;5.2.2 依据以下规范,所有进行本检测的人员都要求进行每年的视力测试及三年一次的辨色测试;5.2.3 所有无损检测人员应符合ISO9712要求。
5.3 检测方法锻件与精炼轧材的超声波探伤应采用脉冲回波联结或液浸方式进行。
5.4 扫描策划当相应过程文件作出要求时,即采购订单、质量计划、ECN等,应提交超声波探伤测试,并经WGPC质量代表认可后进行。
5.5 设备要求5.5.1 超声波设备5.5.1.1 超声波探伤设备:一个脉冲的反射型超声波探伤器械,频率范围至少为0.5~10兆赫,使用ASTME317最新版本对超声波脉冲检测系统的性能进行评估,其频率不应超过12个月。
5.5.1.2 脉冲/接收器:一个误差±10%或振幅比精确度在1dB的衰减器,设备控制对校准、核对或检测期间的线性影响应当没有或最小。
5.5.1.3 电池组:应当使用超声探伤或同类设备推荐的标准电池,电量低于50%时的电池组不能用于检测,且结果不被接受。
5.5.2 探测装置5.5.2.1 应使用标准直径为0.25~1英寸,且频率为1/2~5兆赫的传感器,选择相应的传感器尺寸与频率进行测量以得到最精确的显示结果。
无损检测作业指导书
无损检测作业指导书一、概述无损检测是一种以非破坏性的方法对材料和构件进行检测的技术。
它通过利用材料内部或外部的缺陷信息,来评估材料的质量,发现可能的缺陷并进行定位和评价。
本次作业主要是对无损检测的基本原理和常用方法进行学习和实践。
二、目标1.了解无损检测的基本概念和原理。
2.掌握无损检测的常用方法及其应用领域。
3.熟悉无损检测设备和工具的使用方法。
4.能够正确地选择合适的无损检测方法来检测材料和构件。
三、内容1.无损检测的基本原理和方法:a.无损检测的定义和概念。
b.无损检测的基本原理,如声波、电磁波、热辐射等的传播和相互作用。
c.常见的无损检测方法,如超声检测、磁粉检测、涡流检测等。
d.无损检测的应用领域和优缺点。
2.无损检测设备和工具的使用:a.超声波探伤仪的使用方法,包括仪器的开关、参数的调节和信号的捕获。
b.磁粉检测仪的使用方法,包括仪器的开启、磁粉的喷洒和缺陷的判读。
c.涡流检测仪的使用方法,包括仪器的操作和显示屏的读取。
3.实践部分:a.根据指定的材料或构件,选择合适的无损检测方法进行检测,并记录检测结果。
b.对检测结果进行分析和评价,如缺陷的定位和评估。
四、要求1.学员需分组进行实践,在指导老师的指导下进行检测。
2.学员需独立完成实践部分的检测和分析,撰写实验报告。
3.学员需参加课堂讨论,分享经验和心得。
五、安全注意事项1.使用无损检测设备时,需佩戴防护眼镜和手套。
2.操作超声波和磁粉检测仪时,需注意仪器的正常工作状态和声音的大小。
3.操作涡流检测仪时,需注意仪器的电压和电流,避免触电风险。
4.严禁在未经授权的情况下,拆卸或改装无损检测设备。
六、评价方式1.实验报告的完成程度和质量。
2.对实验过程中的问题的解决能力。
3.对实验结果的分析和评估的正确性和深度。
七、参考资料1.无损检测实验教程。
2.无损检测技术手册。
3.相关学术论文和文献。
- 1、下载文档前请自行甄别文档内容的完整性,平台不提供额外的编辑、内容补充、找答案等附加服务。
- 2、"仅部分预览"的文档,不可在线预览部分如存在完整性等问题,可反馈申请退款(可完整预览的文档不适用该条件!)。
- 3、如文档侵犯您的权益,请联系客服反馈,我们会尽快为您处理(人工客服工作时间:9:00-18:30)。
射线检测工艺规程1.适用范围本规范适用于检测厚度范围在2~200mm的钢制锅炉、压力容器、压力管道对接焊缝的埋藏缺陷。
2.引用标准NB/T47013-2015《承压设备无损检测》《固定式压力容器安全技术监察规程》《压力容器定期检验规则》《锅炉安全技术监察规程》《压力管道安全技术监察规程工业管道》《压力管道安全技术监察规程公用管道》JB/T 7902 《无损检测射线照相用线型像质计》GB/T 19802 《无损检测工业射线照相观片灯最低要求》3.人员资格3.1特种设备检验、检测机构的检验、检测人员应当经考核,取得检验、检测人员资格,方可从事检验、检测工作。
3.2焊缝射线检测底片评级、复评和出具报告必须由取得RTⅡ级及以上证书的人员进行。
3.3从事底片评定的人员视力要求应符合NB/T47013.1-2015标准要求。
4.设备、器材和材料4.1 X射线检测机4.1.1应保持完好,性能应满足《JB/T 6221-2012工业X射线检测机电气通用技术条件》、《JB/T 7413 携带式工业X射线检测机》、等标准的要求,穿透能力应满足受检设备的最大穿透厚度,且应有10%的裕度。
4.1.2使用的检测设备均有设备编号和制作相应的曝光曲线并在有效检定期内。
4.2胶片4.2.1射线照相用胶片必须符合 NB/T47013.2-2015 相关规定,其性能应符合表1。
胶片处理方法用胶片制造商提供的预先曝光胶片测试片进行测试和控制。
表1 胶片系统的主要特性指标4.2.2 A 级和 AB 级技术应采用 C5 类或更高类别的胶片,B 级技术应采用C4 类或更高类别的胶片。
胶片的本底灰雾应不大于 0.3。
4.2.3 采用γ射线和高能X射线进行射线检测时,以及对标准抗拉强度下限值Rm≥540MPa高强度材料射线检测时,应采用 C4 类或更高类别的胶片。
4.3 像质计:像质计及像质计灵敏度的选用按NB/T47013.2-2015标准的要求。
4.4 增感屏:按NB/T47013.2-2015标准选用,应保持干燥,经常保养,避免表面划伤,压凹或沾上油污等,屏上有明显损伤或增感效果不良时应及时更换。
4.5 暗盒:应不漏光、洁净,能保证胶片与增感屏良好接触。
4.6 标记:各种标记(“B”标记、中心标记、定位标记、铅字等)应按NB/T47013.2-2015标准选用和放置。
4.7 定影液、显影液:各种药液的选用和配制应与所选用的胶片相一致。
4.8观片灯4.8.1观片灯的主要性能应符合GB/T 19802的有关规定,噪音小,亮度可调,性能稳定。
4.8.2 观片灯的最大亮度应能满足单位照相底片最大黑度的评片要求。
4.9黑度计(光学密度计)和标准黑度片4.9.1黑度计可测的最大黑度应不小于 4.5,测量值的误差应不超过±0.05。
4.9.2 黑度计首次使用前应进行核查,以后至少每6 个月应进行一次核查。
核查方法可参照NB/T47013.2-2015 附录C的规定进行,每次核查后应填写核查记录。
在工作开始时或连续工作超过8小时后,应在拟测量黑度范围内选择至少两点进行检查。
4.9.3 标准黑度片应至少有8个一定间隔的黑度基准,且能覆盖0.3~4.5黑度范围,应至少每 2 年校准一次。
必须特别注意标准密度片的保存和使用条件。
4.10其他器材:磁钢、透明胶带等应能满足检验要求。
5.被检焊缝表面要求5.1在射线检测之前,焊接接头的表面应经目视检测并合格,表面的不规则状态在底片上的影像应不妨碍底片上缺陷的辨别,否则在拍片前应要求受检单位修补或处理。
5.2在用设备的表面要求,可根据情况酌情处理。
6.检测时机6.1在用检验时的检测时机应安排在被检测面经打磨、目视检测合格(满足上述5要求)后进行检测。
6.2其他检验时检测时机原则上应安排在热处理后,有延迟裂纹倾向的安排在焊接完成24h(球罐36h)之后,被检测面经打磨、目视检测合格(满足上述5要求)后进行检测。
7.编号7.1编号方法:7.1.1检测编号应有设备编号、底片编号,二者用“——”隔开。
7.1.2重照、返修后复照、扩探在底片编号后加字母,字母后的数字表示实施次数,无数字的为1次。
如:C──重照, R──返修复照,K──扩探。
7.1.3设备上每个片号定位标记的相对位置必须在检测布片草图上表示清楚。
8. 射线检测技术等级选择8.1 射线检测技术等级选择应符合制造、安装、在用等有关标准及设计图样规定。
锅炉、压力容器及压力管道对接焊接接头的制造、安装、在用时的射线检测,一般应采用 AB 级技术进行检测。
对重要设备、结构、特殊材料和特殊焊接工艺制作的焊接接头,可采用 B 级技术进行检测。
8.2锅炉、压力容器及压力管道在用检测中,由于结构、环境条件、射线设备等方面限制,检测的某些条件不能满足 AB级(或 B 级)技术的要求时, 经合同各方商定,在采取有效补偿措施(例如选用更高类别的胶片)的前提下,受限制条件可按 A 级(或 AB 级)要求实施,若底片的像质计灵敏度达到了 AB 级(或 B 级)的规定,则可认为按 AB 级(或 B 级)进行了检测。
8.3 锅炉、压力容器及压力管道在用检测中,由于结构、环境、射线设备等方面限制,检测的某些条件不能满足 AB 级技术的要求时, 经合同各方商定,在采取有效补偿措施(例如选用更高类别的胶片)后可采用 A 级技术进行射线检测,但应同时采用其他无损检测方法进行补充检测。
9.辐射防护9.1 放射卫生防护应符合 GB 18871、GBZ 117、GBZ 132 和我所《安全手册》的有关规定。
9.2 现场进行X射线检测时,应按 GBZ 117 的规定划定控制区和管理区、设置警告标志。
检测工作人员应佩带个人剂量计,并携带剂量报警仪。
10.布片与标记10.1按检验员确定的检测部位及检测比例布片。
10.2底片上必须有检测编号、中心标记、像质计、搭接标记等。
这些标记离焊缝边缘5mm,且应与设备上的标志一致。
10.3拍片时象质计应放在射线源一侧的焊缝表面,并靠近胶片的端部,细丝在外侧。
若因条件所限不能放在射线源一侧时,也可以放在胶片侧,但应做对比试验,并加字母F标记。
11.曝光参数的选择及透照操作11.1 400KV以下的X射线,在透照厚度下最高管电压的限制按NB/T47013.2-2015标准图1的要求。
11.2 X射线透照时,当焦距为700mm时,曝光量的推荐值为:A级和AB级≥15mA·min,B级≥20mA·min,当焦距改变时可按平方反比定律对曝光量的推荐值进行换算。
不能用缩短曝光时间提高KV值的办法来增加底片黑度。
11.3焦距的选择:按NB/T47013.2-2015标准中5.7条要求并结合仪器的曝光曲线选取。
11.4 X射线机的操作应按《安全手册》和相应设备操作规程执行。
11.5透照厚度比K值,环向焊接接头A级和AB级:K≤1.1,B级:K≤1.06;纵向焊接接头A级和AB级:K≤1.03,B级:K≤1.01。
12.暗室处理12.1裁片规格一般是80mm×180mm ,80mm×240mm,80mm×300mm。
12.2药液的配制应与所选用的胶片相一致,新配药液应放置24小时使用。
12.3胶片在药液中的处理温度应控制在20℃左右,显影时间以4~8分钟为宜,并应经常翻动。
12.4定影后的底片用流动水冲洗,水质应清洁,无泥沙,无油污,水洗时间不应少于30分钟。
12.5底片冲洗后应烘干或自然晾干。
13.底片质量13.1底片黑度D(包括热影响区)应满足NB/T47013.2-2015标准5.16.1的要求。
13.2底片上的像质计灵敏度,应符合NB/T47013.2-2015标准5.16.2表5至表10的要求。
12.3其他要求应符合NB/T47013.2-2015标准中第5.16.3条的要求。
14.底片观察14.1底片完全干燥后在无背景反射光的室内进行观察评定。
14.2观片灯的主要性能应符合GB/T19802的有关规定,最大亮度应满足评片的要求。
15.焊缝射线透照缺陷等级评定15.1焊缝照相质量按NB/T47013.2-2015标准进行评定。
15.2底片必须由2名RTⅡ级及以上人员评定,其中一人初评,一人复评。
15.3埋藏缺陷与相应的安全状况等级按相应的检验规则的规定处理。
16记录、报告、存档16.1各类原始记录,表卡和检测报告应认真填写,字迹整齐、清洁,不得随意涂改(原始记录如需修改可采用划改并签名、签日期的方式)。
检测记录和报告应准确、完整,并经无损检测责任人签字认可。
16.2报告内容应符合NB/T47013-2015的规定。
16.2.1. 工件情况:产品编号、产品名称、类别、规格、材质、母材厚度及焊缝情况。
16.2.2检测设备:射线机型号。
16.2.3检测附件:胶片型号、像质计规格、增感屏类型等。
16.2.4检测工艺参数:KV、mA、t、f、L、%等。
16.2.5检测结果:验收标准、合格级别。
不合格缺陷应定性、定位、定量、定级。
16.2.6返修情况:部位、次数、最终级别。
16.2.7检测部位示意图(或布片示意图)16.2.8编制、审核人员及其技术资格16.2.9其他需要说明或记录的事项16.3检测记录、检测报告、RT底片、意见通知书等技术资料应整理汇总,按台归档。
17. 相关记录及报告编号:NTBG-JS162-2014 《射线检测记录》NTBG-JS163-2014 《射线检测报告》超声波检测工艺规程1.适用范围适用于铁素体钢制承压设备焊接接头的超声检测。
与承压设备有关的支承件和结构件的超声检测,也可参照使用。
2.编写依据NB/T47013-2015《承压设备无损检测》GB150-2011《钢制压力容器》GB/T27664《无损检测超声检测设备的性能与检验》JB/T9214《无损检测 A型脉冲反射式超声检测系统工作性能测试方法》3.检测人员资格3.1超声检测人员的一般要求应符合NB/T47013.1的有关要求。
3.2超声检测人员应具有一定的金属材料、设备制造安装、焊接及热处理等方面的基础知识,应熟悉被检工件的材质、几何尺寸及透声性等,对检测中出现的问题能作出分析、判断和处理。
4.检测设备和器材4.1超声波检测仪器和探头产品质量合格证明应符合NB/T47013.3-2015的4.2.1条规定。
4.2超声波检测仪器、探头和组合性能4.2.1检测仪器:采用A型脉冲反射式超声检测仪,其工作频率按-3dB测量应至少包括0.5MHz~10MHz频率范围,超声检测仪器各性能的测试条件和指标要求应满足附录A的要求并提供证明文件,测试方法按GB/T27664.1的规定。
4.2.2探头:圆形晶片直径一般不应大于40mm,方形晶片任一边长一般不应大于40mm,其性能指标应符合附录B的要求并提供证明文件,测试方法按GB/T27664.2的规定。