10.3 箱体类零件的孔系加工(了解)
箱体类零件的数控加工介绍

箱体类零件的数控加工介绍本文从网络收集而来,上传到平台为了帮到更多的人,如果您需要使用本文档,请点击下载按钮下载本文档(有偿下载),另外祝您生活愉快,工作顺利,万事如意!摘要:摘要:箱体是构成机器设备的一个重要部件,它的加工质量直接影响机器的精度、性能和使用寿命。
文章介绍了箱体类零件的加工技术特点,数控加工时应注意的一些问题,重要参数的选取原则。
关键词:关键词:箱体;定位;切削中图分类号:TP39 文献标识码:A 文章编号:1. 前言箱体类零件在机械加工行业经常接触,是机械设备的主要基础件之一,在机械、汽车、飞机制造等行业广泛应用。
箱体类零件由平面、型腔以及孔系组成,一般结构形式较复杂,腔体壁厚不均匀,加工部位多,各个方向各孔、各平面的尺寸精度、位置公差等要求多,有较大的加工难度。
因此,在加工时要全面考虑。
2. 设备的选择箱体类零件一般采用具有三坐标联动、双工作台自动交换、由机械手自动换刀、传感器自动测量工件坐标系和自动测量刀具长度等功能的卧式加工中心进行加工。
一次装夹可完成不同工位的钻、扩、铰、铣、攻丝等工序。
3.一般性技术要求孔的尺寸精度与表面粗糙度要求,保证安装在孔内的轴或轴承的回转精度;平面的平面度、垂直度和平行度要求,保证装配后整机的接触面刚度、导向面的定位精度和密封等作用。
箱体类零件加工的主要问题是平面和孔,主要体现在:孔的尺寸精度、孔与孔之间精度、孔与平面位置精度。
4. 确定定位基准粗基准的确定是否合理,直接影响到各加工表面加工余量的分配,以及加工表面和不加工表面相互关系。
箱体上孔与孔、孔与平面、平面与平面之间都有较高的尺寸精度、位置精度要求。
为保证重要加工面的余量均匀,应选择重要加工面为粗基准,因此选择孔作为粗基准。
这样切削量始终均匀,能获得较高的加工精度。
只有在金属切除厚度相同的情况下,已加工表面才具有相近的物理性能。
箱体类零件加工精基准通常遵循基准重合原则,既选择加工基准与设计基准重合的方法。
箱体孔系加工
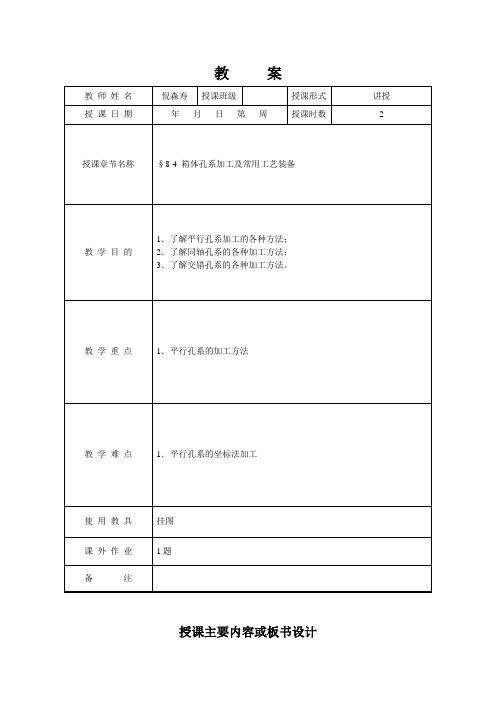
无锡职业技术学院
教案
教师姓名
倪森寿
授课班级
授课形式
讲授
授课日期
年月日第周
授课时数
2
授课章节名称
§8-4箱体孔系加工及常用工艺装备
三、镗夹具
教学目的
1.了解镗夹具的设计要点;
2.掌握镗夹具结构分析和设计方法
教学重点
1.镗模导向装置的布置方式和特点;
2.镗夹具的结构分析。
教学难点
1.镗夹具精度分析
使用教具
挂图
课外作业
1题
备注
授课主要内容或板书设计
§8-4箱体孔系加工及常用工艺装备
三、镗模
(一)镗模的设计要点
1.镗模导向装置的布置方式和特点
(1)单支承前导向
(2)单支承后导向
(3)双支承前后导
(4)双支承后导向
2.镗套结构形式及选择、镗杆、镗刀及浮动接头
(1)镗套
a.固定式镗套b.回转式镗套
教案
教师姓名
倪森寿
授课班级
授课形式
讲授
授课日期
年月日第周
授课时数
2
授课章节名称
§8-4箱体孔系加工及常用工艺装备
教学目的
1.了解平行孔系加工的各种方法;
2.了解同轴孔系的各种加工方法;
3.了解交错孔系的各种加工方法。
教学重点
1.平行孔系的加工方法
教学难点
1.平行孔系的坐标法加工
使用教具
挂图
课外作业
1题
系加工及常用工艺装备
一、箱体零件孔系加工
(一)平行孔系加工
1.镗模法
2.找正法
3.坐标法
(二)同轴孔系加工
箱体类零件定位以及销孔加工方法

箱体类零件定位以及销孔加工方法摘要:箱体类零件的加工中,其定位面、定位孔的选取,夹具定位销、支承面、夹紧点的设定等工艺非常重要,国外一些机床制造商在这方面已经有了很多新的突破与创新。
销孔的尺寸设定、支承面的形状确定、夹紧装置的设计等其合理与否对这些箱体零件的输送、到位、夹紧、离开及加工尺寸的Cpk值能力保证等都起着决定性的作用。
目前,国外机床制造商在设计箱体零件加工的工艺时,在设备选用和夹具的设计上与我们传统的工艺有所不同,在很多方面均有了新的突破与创新,因此如何提高定位销孔的加工精度其意义重大关键词:箱体类零件;定位销孔;位置精度1 选择机床对于加工孔一般用钻床,镗床等机床,但我们加工的零件不是纯粹的孔,因此不合适选择钻床,镗床,针对这一问题,选择机床就十分重要,而加工中心是一种综合加工能力较强的,高效可靠的自动化设备,所以加工中心机床应为首选机床2 刀具麻花钻、扩孔钻、中心钻、套料钻�p铰刀�p镗刀、丝锥�p特殊用途孔加工刀具等3 工件定位在切削加工中,箱体零件的定位面有两种:毛坯零件浇铸面、毛坯零件切削加工面。
箱体毛坯零件一般采用熔模或砂模浇铸而成,毛坯的初始定位基准到型腔之间的相互位置尺寸较稳定准确。
以毛坯零件的浇铸面作为工件加工定位面,当夹具采用合适的定位支承面时,一般能满足产品零件图的相关位置尺寸对毛坯基准的尺寸要求。
采用毛坯来定位时,一般多采用六点定位限制其自由度。
而毛坯经过初始切削后,一般采用“一面两销”来定位,其定位面由1个大平面或24个错落的小平面组成。
目前国外机床制造商在设备的定位支承面上,由原先简单的定位块(麻将块)→定位块带气孔检测孔→定位块由气孔检测孔变成冷却液孔,根据流量与压力来达到检测与冲洗的双功能作用的改进过程,以此检测功能来验证零件是否已经到位。
在加工过程中起到夹具夹紧前的防错作用及清除定位块上的切屑作用,保证加工零件相对定位面的尺寸准确稳定工件定位孔的尺寸箱体零件的定位孔,有输送定位孔、加工工艺定位孔和装配定位孔。
箱体类零件的加工

第二节箱体类零件的加工一、箱体零件概述箱体类零件通常作为箱体部件装配时的基准零件。
它将一些轴、套、轴承和齿轮等零件装配起来,使其保持正确的相互位置关系,以传递转矩或改变转速来完成规定的运动。
因此,箱体类零件的加工质量对机器的工作精度、使用性能和寿命都有直接的影响。
箱体零件结构特点:多为铸造件,结构复杂,壁薄且不均匀,加工部位多,加工难度大。
箱体零件的主要技术要求:轴颈支承孔孔径精度及相互之间的位置精度,定位销孔的精度与孔距精度;主要平面的精度;表面粗糙度等。
箱体零件材料及毛坯:箱体零件常选用灰铸铁,汽车、摩托车的曲轴箱选用铝合金作为曲轴箱的主体材料,其毛坯一般采用铸件,因曲轴箱是大批大量生产,且毛坯的形状复杂,故采用压铸毛坯,镶套与箱体在压铸时铸成一体。
压铸的毛坯精度高,加工余量小,有利于机械加工。
为减少毛坯铸造时产生的残余应力,箱体铸造后应安排人工时效。
二、箱体类零件工艺过程特点分析下面我们以某减速箱为例说明箱体类零件的加工。
1.箱体类零件特点一般减速箱为了制造与装配的方便,常做成可剖分的,如图6-6所示,这种箱体在矿山、冶金和起重运输机械中应用较多。
剖分式箱体也具有一般箱体结构特点,如壁薄、中空、形状复杂,加工表面多为平面和孔。
减速箱体的主要加工表面可归纳为以下三类:⑴主要平面箱盖的对合面和顶部方孔端面、底座的底面和对合面、轴承孔的端面等。
⑵主要孔轴承孔( 150H7、 90H7)及孔内环槽等。
⑶其它加工部分联接孔、螺孔、销孔、斜油标孔以及孔的凸台面等。
2.工艺过程设计应考虑的问题根据减速箱体可剖分的结构特点和各加工表面的要求,在编制工艺过程时应注意以下问题:⑴加工过程的划分整个加工过程可分为两大阶段,即先对箱盖和底座分别进行加工,然后再对装合好的整个箱体进行加工——合件加工。
为保证效率和精度的兼顾,就孔和面的加工还需粗精分开;⑵箱体加工工艺的安排安排箱体的加工工艺,应遵循先面后孔的工艺原则,对剖分式减速箱体还应遵循组装后镗孔的原则。
箱体类零件孔系的精加工方法
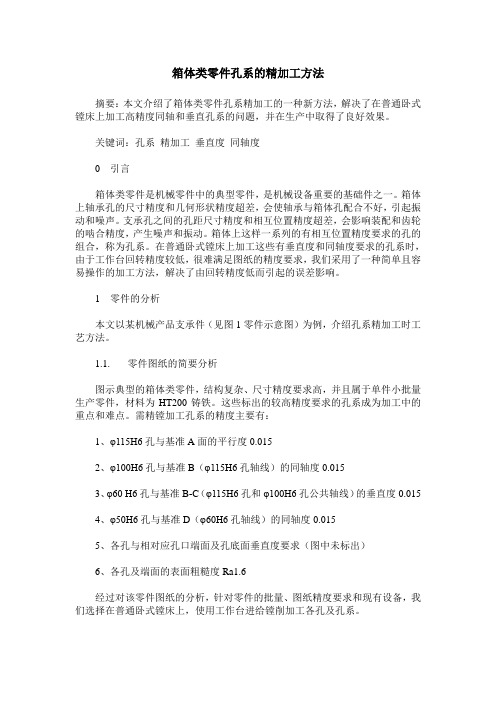
箱体类零件孔系的精加工方法摘要:本文介绍了箱体类零件孔系精加工的一种新方法,解决了在普通卧式镗床上加工高精度同轴和垂直孔系的问题,并在生产中取得了良好效果。
关键词:孔系精加工垂直度同轴度0 引言箱体类零件是机械零件中的典型零件,是机械设备重要的基础件之一。
箱体上轴承孔的尺寸精度和几何形状精度超差,会使轴承与箱体孔配合不好,引起振动和噪声。
支承孔之间的孔距尺寸精度和相互位置精度超差,会影响装配和齿轮的啮合精度,产生噪声和振动。
箱体上这样一系列的有相互位置精度要求的孔的组合,称为孔系。
在普通卧式镗床上加工这些有垂直度和同轴度要求的孔系时,由于工作台回转精度较低,很难满足图纸的精度要求,我们采用了一种简单且容易操作的加工方法,解决了由回转精度低而引起的误差影响。
1 零件的分析本文以某机械产品支承件(见图1零件示意图)为例,介绍孔系精加工时工艺方法。
1.1. 零件图纸的简要分析图示典型的箱体类零件,结构复杂、尺寸精度要求高,并且属于单件小批量生产零件,材料为HT200铸铁。
这些标出的较高精度要求的孔系成为加工中的重点和难点。
需精镗加工孔系的精度主要有:1、φ115H6孔与基准A面的平行度0.0152、φ100H6孔与基准B(φ115H6孔轴线)的同轴度0.0153、φ60 H6孔与基准B-C(φ115H6孔和φ100H6孔公共轴线)的垂直度0.0154、φ50H6孔与基准D(φ60H6孔轴线)的同轴度0.0155、各孔与相对应孔口端面及孔底面垂直度要求(图中未标出)6、各孔及端面的表面粗糙度Ra1.6经过对该零件图纸的分析,针对零件的批量、图纸精度要求和现有设备,我们选择在普通卧式镗床上,使用工作台进给镗削加工各孔及孔系。
1.2. 精加工孔和孔系的基准选择根据零件的加工基准选择原则,精加工时候一般要遵从基准重合原则和基准统一原则,可减少基准不重合误差,又可减少因定位基准多次转换而造成的装夹累积误差,并且可减少夹具、刀具、量具的数量,降低生产成本。
机械制造及工艺——箱体孔系加工

箱体孔系加工和常用工艺装备一、箱体零件孔系加工箱体上一系列相互位置有精度要求的孔的组合,称为孔系。
孔系可分为平行孔系「图8-35(a)〕、同轴孔系[图8-35(b)」和交叉孔系[图8-35(c)]。
孔系加工不仅孔本身的精度要求较高,而且孔距精度和相互位置精度的要求也高,因此是箱体加工的关键。
孔系的加工方法根据箱体批量不同和孔系精度要求的不同而不同,现分别予以讨论。
(一)平行孔系的加工平行孔系的主要技术要求是各平行孔中心线之间及中心线与基准面之间的距离尺寸精度和相互位置精度。
生产中常采用以下几种方法1.找正法找正法是在通用机床上借助辅助工具来找正要加工孔的正确位置的加工方法。
这种方法加工效率低,一般只适用于单件小批生产。
根据找正方法的不同,找正法又可分为以下几种:(l)划线找正法。
加工前按照零件图在毛坯上划出各孔的位置轮廓线,然后按划线一一进行加工。
划线和找正时间较长,生产率低,而且加工出来的孔距精度也低,一般在±0.5 mm 左右。
为提高划线找正的精度,往往结合试切法进行。
即先按划线找正镗出一孔再按线将主轴调至第二孔中心,试镗出一个比图样要小的孔,若不符合图样要求,则根据测量结果更新调整主轴的位置,再进行试镗、测量、调整,如此反复几次,直至达到要求的孔距尺寸。
此法虽比单纯的按线找正所得到的孔距精度高,但孔距精度仍然较低且操作的难度较大,生产效率低,适用于单件小批生产。
(2)心轴和块规找正法。
镗第一排孔时将心轴插人主轴孔内(或直接利用镗床主轴),然后根据孔和定位基准的距离组合一定尺寸的块规来校正主轴位置,如图8-36所示。
校正时用塞尺测定块规与心轴之间的间隙,以避免块规与心轴直接接触而损伤块规。
镗第二排孔时,分别在机床主轴和加工孔中插入心轴,采用同样的方法来校正主轴线的位置,以保证孔心距的精度。
这种找正法的孔心距精度可达±0.3mm 。
(3)样板找正法。
用10~20mm 厚的钢板制造样板,装在垂直于各孔的端面上(或固定于机床工作台上),如图8-37所示。
箱体零件的加工
箱体类零件的加工一、箱体类零件的功用和结构特点功用:箱体类零件是机器或箱体部件的基础件。
它将机器或箱体部件中的轴、轴承、套和齿轮等零件按一定的相互位置关系装联在一起,按一定的传动关系协调地运动。
因此,箱体类零件的加工质量,不但直接影响箱体的装配精度和运动精度,而且还会影响机器的工作精度、使用性能和寿命。
结构:几种常见箱体零件的简图:主要结构特点:1)形状复杂;2)体积较大;3)壁薄容易变形;4)有精度要求较高的孔和平面。
一般说来,箱体不仅需要加工部位较多,而且加工难度也较大。
二、箱体零件的定位装夹方式箱体零件的结构复杂,加工表面较多,其应按基准统一原则选择精基准方案。
所采用的精基准方案主要有以下两种:(1)三个互相垂直的平面底面——具有较大的支承面积,为第一基准,限制三个自由度;某个侧面——长度较大,为第二基准,限制两个自由度;某个端面——为第三基准,限制一个自由度。
(2)一面两孔——一个平面和两个与平面垂直的孔,定位元件为:两块长条支承板(限制3)+ 短圆柱销(限制2)+ 短菱形销(限制1)三、箱体零件平面的加工方法四、箱体零件孔系的加工方法孔的加工:镗孔加工尺寸的调整:对刀仪+对刀样件孔系的加工:孔系分为平行孔系、同轴孔系、交叉孔系,如图:箱体上的孔不仅本身的精度要求高,而且孔距精度和相互位置精度也较高,这是箱体加工的关键。
根据生产规模和孔系的精度要求可采用不同的加工方法:(1)找正法——划线找正、用心轴和块规找正、用样板找正在工件上划线:在卧式镗床上找正工件:◇加工平行孔系时的找正:◇加工同轴孔系时的找正:◇加工垂直孔系时的找正:(2)坐标法机床上配备有精密的坐标测量装置,能精确地确定主轴箱、工作台等移动部件的位置。
借助于测量装置调整机床主轴与工件间在水平和垂直方向的相对位置,以保证孔距精度。
其孔距精度取决于机床坐标测量装置的精度。
目前应用的高精度坐标测量装置主要有光栅数显装置、感应同步器测量装置、磁栅和激光干涉仪等,测量精度为0.01~0.0025mm。
箱体零件的孔系加工方法与精度分析——《机械制造工程学》课程教学中的典型零件加工专题
机械加工精度作为机械制造工程学课程的重要内容之一,在教学中一般按照工艺系统的几何误差、受力变形等分立的内容进行教学。
为提高学生综合运用所需知识分析解决具体问题的能力,我们开展了“专题驱动式”教学方法研究。
下面以箱体零件的孔系加工为专题,对其工艺方案与加工精度进行分析。
箱体类零件是机械传动装置中重要的基础件,箱体上若干有相互位置精度要求的孔构成箱体孔系,包括平行孔系、同轴孔系等。
孔系的加工方法与孔系的加工精度对保证传动装置的性能和质量具有重要影响。
一、平行孔系加工平行孔系的精度要求主要是各孔轴线之间及轴线与基准面之间的尺寸精度和轴线间的平行度等几何精度。
可以通过以下几种方法保证平行孔系精度要求。
1.找正法。
采用辅助装置来确定各个被加工孔的正确位置,如划线找正、心轴块规找正等。
2.镗模法。
镗模是引导镗刀杆在工件上镗孔用的机床夹具,利用镗模板上的孔系保证箱体孔系位置精度,镗杆与镗床主轴多采用浮动连接,以减小机床主轴的回转精度对加工精度的影响。
3.坐标法。
首先将被加工孔之间的孔距尺寸换算为两个相互垂直的坐标尺寸,然后精确地调整机床主轴与工件在水平和垂直方向的相对位置,以间接保证孔距精度。
为保证工作台和主轴的位移精度,必须在镗床上加上坐标测量装置。
二、同轴孔系加工在成批生产中,常采用镗模加工箱体同轴孔系以保证其轴线的同轴度。
在单件小批生产时,一般不采用镗模,常采用如下两种方法保证其轴线孔的同轴度。
1.利用已加工孔作支承导向。
在加工好的箱体前壁孔内装一个导向套,对镗杆起支承支撑和引导作用。
它适用于加工壁间距较小的箱体同轴孔。
2.利用镗床后立柱作支承导向。
镗床后立柱上的导向套作支承导向,可解决因镗杆悬臂过长而挠度大进而影响同轴度的问题。
这种方法需用较长的镗杆,而且调整后立柱导套比较麻烦、费时,通常适用于大型箱体的孔系加工。
三、孔系加工的精度分析(一)受力变形的影响1.镗杆受力变形的影响。
镗削过程中,随着镗杆的回转,径向力Fy 与切向力Fz 的合力Fyz 方向不断改变。
箱体类零件的加工工艺过程精品PPT课件
箱体毛坯制造方法有两种,一种是采用铸造,另一 种是采用焊接。对金属切削机床的箱体,由于形状较 为复杂,而铸铁具有成形容易、可加工性良好、并且 吸振性好、成本低等优点,所以一般都采用铸铁;对 于承受重载和冲击的工程机械、锻压机床的一些箱体, 可采用铸钢或钢板焊接。
四 箱体类零件的结构工艺性
(1)粗基准的选择 1)中小批生产时,由于毛坯精
度较低一般采用划线装夹。
主轴箱的划线
2)大批大量生产时,毛坯精度较高。
以主轴孔为粗基准铣顶面的夹具
(2)精在准的选择 1)单件小批生产用装配基准作定位基准。
吊架式镗模夹具
2)大批量生产时采用一面两孔作定位基准。
用箱体顶面急两销定位的镗模
3)所用设备依批量不同而异
5、箱体平面的刮研
二 平面的加工方案
平面工方案的加工经济精度和表面粗糙度
序 号
加工方案
1 粗车
2 粗车—半精车
3 粗车—半精车—精车
4 粗车—半精车—磨削
公差等级
IT11~IT13 IT8~IT10 IT7~IT8 IT6~IT8
表面粗糙度 Ra / μm
12.5~50
适用范围
3.2~6.3 0.8~1.6
箱体类零件加工
一 概述 二 典型箱体类零件加工工艺过程与分析
一 箱体类零件的功用及结构特点
1、箱体类零件的功用:
箱体是各类机器的基础零件,它将机器和部件中轴、套、 齿轮等有关零件连接成一个整体,并使之保持正确的位置, 以传递转矩或改变转速来完成规定的运动。
2、箱体类零件的结构特点
箱体零件的结构一般比较复杂,壁薄且壁厚不不均匀; 加工部位多,既有一个或数个基准面及一些支承面,又有 一对或数对加工难度大的轴承支承孔。
2019年重庆市高职分类招生考试中职类机械加工类真题_真题-无答案
2019年重庆市高职分类招生考试(中职类)机械加工类真题(总分200,考试时间120分钟)单项选择题共14 小题,每小题3 分,共42 分。
1. 国家标准规定,公称尺寸在0~500 ㎜范围内,标准公差等级有A. 10 个B. 15 个C. 20 个D. 25 个2. 下列钢的牌号中,属于滚动轴承钢的是A. Q235B. ZG200-400C. T8D. GCr153. 机器在工作时,可随时完成两轴接合或分离的连接是A. 联轴器连接B. 离合器连接C. 销连接D. 键连接4. 两构件组成低副,其接触形式为A. 点或线接触B. 点或面接触C. 线或面接触D. 面接触5. 带传动的主要失效形式是A. 磨损B. 断裂C. 疲劳撕裂D. 变形6. 润滑油最重要的性能指标是A. 粘度B. 闪点C. 油性D. 凝点7. 将大量生产、成批生产和单件生产的成本进行比较,正确的是A. 单件生产成本较高B. 成批生产成本较高C. 大量生产成本较高D. 三种成本一样高8. 下列铣削加工的工艺特点,不正确的是A. 铣刀是一种多刃刀具B. 铣削时每个刀齿的切削都是断续的C. 铣削加工主要用于零件的精加工D. 铣削加工排屑容易9. 刃磨车刀时,不安全的操作是A. 刃磨时不能用力过大B. 刃磨时人站在砂轮的正面C. 砂轮旋转平稳后才能磨刀D. 必须戴上防护眼镜10. 适用于精基准较小接触平面的定位元件是A. 固定支承钉B. 可调支承钉C. 支承板D. 平头支承钉11. 在大量生产中,确定加工余量的方法应力求采用A. 查表修正法B. 分析计算法C. 经验估算法D. 查表和分析法12. 汽车自动装配线采用的装配组织形式是A. 集中装配B. 分散装配C. 自由移动装配D. 强制移动装配13. 下图中,点A 在四棱柱表面上,其正确的投影图是A. B.C. D.14. 下图所示的A-A 断面图中,正确的断面图是A.B.C.D.判断题共20 小题,每小题3 分,共60 分。
- 1、下载文档前请自行甄别文档内容的完整性,平台不提供额外的编辑、内容补充、找答案等附加服务。
- 2、"仅部分预览"的文档,不可在线预览部分如存在完整性等问题,可反馈申请退款(可完整预览的文档不适用该条件!)。
- 3、如文档侵犯您的权益,请联系客服反馈,我们会尽快为您处理(人工客服工作时间:9:00-18:30)。
对于大型箱体零件来说,由于镗模的尺寸庞 大笨重,给制造和使用带来了困难,故很少采 用。
用镗模加工孔系,既可以在通用机床上 加工,也可以在专用机床或组合机床上加工。
二、同轴孔系的加工
在中批以上生产中,一般采用镗模加工同 轴孔系,其同轴度由镗模保证;当采用精密刚 性主轴组合机床从两头同时加工同轴线的 各孔时,其同轴度则由机床保证,可达 0. 01 mm。
当卧式铣镗床的工作台90°对准装置精 度很低时,可用心棒与百分表找正法进行 。 即在加工好的孔中插人心棒,然后将工作台 转90°,揺动工作台用百分表找正,如图10-8 所示 。
箱体上如果有交叉孔存在,则应将精度要 求高或表面粗糙度小的孔先全部加工好,然 后再加工另外与之相交叉的孔。
四、孔系加工的自动化
该方法加工孔系不易出差错, 找正迅速,孔距 精度可达±0. 05 mm,工艺装备也不太复杂, 常用于加工大型箱体的孔系 。
2.用镗模加工孔系
如图 10-5所示,工件装夹在镗模上,镗杆被 支承在镗模的导套里,由导套引导镗杆在工件 上的正确位置镗孔。 镗杆与机床主轴多采用
浮动连接,机床精度对孔系的加工精度影响较 小,孔距精度主要取决于镗模,因而可以在精度 较低的机床上加工出精度较高的孔系 。 同时,ห้องสมุดไป่ตู้镗杆刚度大大地提高,有利于采用多刀同时切 削;定位夹紧迅速,不需找正,生产效率高。
( 3 ) 采用调头镗法 当箱体壁相距较远时,宜采 用调头镗法 。 即在工件的一次安装中,当箱 体一端的孔加工完后,将工作台回转 180°, 再加工箱体另一端的同轴线孔 。 掉头镗不
用夹具和长刀杆,准备周期短,镗杆悬伸长度 短,刚度好;但需要调整工作台的回转误差和 掉头后主轴应处于的正确位置,比较麻烦,又 费时。 掉头镗的调整方法如下:
由于箱体孔系的精度要求高,加工量大, 实现加工自动化对提高产品质量和劳动生 产率都有重要意义 。 随着生产批量的不同, 实现自动化的途径也不同 。 大批生产箱体 时,广泛使用组合机床和自动线加工,不但生 产率高 ,而且利于降低成本和稳定产品质量 。
单件小批生产箱体时,大多数采用万能 机床,产品的加工质量主要取决于机床操作 者的技术熟练程度。 但加工具有较多加工
①使工作台回转轴线与机床主轴轴线相交,定 好坐标原点。其方法如图10-7a所示。将百 分表固定在工作台上,回转工作台180°,分 别测量主轴两侧,使其误差小于 0. 01mm,记 下此时工作台在 x轴上的坐标值作为原点的 坐标值。
②调整工作台的回转定位误差,保证工作台精 确地回转180°。 其方法如图10-7b所示,先 使工作台紧靠在回转定位机构上,在台面上 放一平尺,通过装在镗杆上的百分表找正平 尺一侧面后将其固定,再使工作台回转180°, 测量平尺的另一侧面,调整回转定位机构,使 其回转定位误差小于 0.02 mm/1 000 mm。
mm厚的钢板制成的样板上,样板上孔系的孔距 精度较工件孔系的孔距精度高( 一般为:±0. 01 -0. 03 mm) ,孔径较工件的孔径大,以便镗杆通过; 孔的直径精度不需要严格要求,但几何形状精 度和表面粗糙度要求较高,以使找正。 使用时, 将样板装于被加工孔的箱体端面上(或固定于 机床工作台上) ,利用装在机床主轴上的百分表 找正器,按样板上的孔逐个找正机床主轴的位 置进行加工。
10.3 箱体类零件的孔系加工
箱体上一系列有相互位置精度要求的轴 承支承孔称为“孔系” 。 它包括平行孔系、 同轴孔系和交叉孔系,如图 10-2所示。 孔系 的相互位置精度有:各平行孔轴线之间的平 行度、孔轴线与基面之间的平行度、孔距 精度、各同轴孔的同轴度、各交叉孔的垂 直度等要求。 保证孔系加工精度是箱体类
如图10-3所示,将精密心轴分别插入机床 主轴孔和已加工孔中,然后用一定尺寸的块 规组合来找正心轴的位置。 找正时,在量块 心轴之间要用厚薄规测定间隙,以免量块与 心轴直接接触而产生变形 。 此法可达到较
高的孔距精度(± 0. 3 mm) ,但只适用于单件 小批生产。
(3)样板找正法 如图10-4所示,将工件上的孔系复制在10-20
平行孔系的主要技术要求为各平行孔中 心线之间及孔中心线与基准面之间的距离 尺寸精度和相互位置精度。 生产中常采用 以下几种方法保证孔系的位置精度。
1. 用找正法加工孔系
找正法的实质是在通用机床(如铣床、卧 式铣镗床)上,依据操作者的技术水平,并借助 一些辅助装置去找正每一个被加工孔的正 确位置。 根据找正的手段不同,找正法又可 分为划线找正法、量块心轴找正法和样板 找正法等。
( 1 )划线找正法
加工前先在毛坯上按图样要求划好各孔
位置轮廓线,加工时按划线一一 找正进行加 工。 这种方法所能达到的孔距精度一般为
± 0. 5 mm左右。 此法操作设备简单,但操 作难度大,生产效率低,同时,加工精度受操作 者的技术水平和采用的方法影响较大,故适 用于单件小批生产 。
(2) 量块心轴找正法
③当完成上述调整准备工作后,就可以进行加 工 。 先将工件正确地安装在工作台面上,用 坐标法加工好工件一端的孔,各孔到坐标原
点的坐标值应与掉头前相应的同轴线孔到 坐标原点的坐标值大小相等,方向相反,其误 差小于 0. 01 mm,这样就可以得到较高的同 轴度 。
三、 交叉孔系的加工
交叉孔系的主要技术要求为控制各孔的 垂直度。 在卧式铣镗床上主要靠机床工作 台上的90 °对准装置 。 因为它是挡块装置, 故结构简単,但对准精度低 。 每次对准,需要 凭经验保证挡块接触松紧程度一致,否则不 能保证对准精度 。 所以,有时采用光学瞄准 装置 。
(1 )采用普通刻线尺与游标尺放大镜测量,其位 置精度为 0. 1 -0.3 mm。
(2) 采用百分表与量块(或量杆)测量,一般与普 通刻线尺配合使用,其位置精度为 0.04 -0. 08 mm,但测量操作繁琐,效率较低。
(3) 采用经济刻线尺与光学读数装置,其位置精 度可达±0. 01 mm。
一、 平行孔系的加工
因此,不仅在中批生产中普遍采用镗模技术 加工孔系,就是在小批生产中,对一些结构复 杂、加工量大的箱体孔系,采用镗模加工也 是合算的 。
另外,由于镗模自身的制造误差和导套
与镗杆的配合间隙对孔系加工精度有一定 影响,所以,该方法不可能达到很高的加工精 度。一般孔径尺寸精度为 IT7 左右,表面粗糙 度值 Ra为1.6 -0. 8 µm;孔与孔的同轴度和平 行度,当从一头开始加工为 0. 02-0. 03 mm,从 两头加工为0.04-0.05 mm;孔距精度一般为 ±0.05 mm左右。
单件小批生产时,在通用机床上加工,且 一般不使用镗模,保证同轴线孔的同轴度用 下列方法:
( 1 )利用已加工孔作支承导向 如图10-6所示, 当箱体前壁上的孔加工完后,在该孔内装一 导套,支承和引导镗杆加工后壁上的孔,以保 证两孔的同轴度要求 。 此法适于加工箱体
壁相距较近的同轴线孔。
(2) 利用镗床后立柱上的导向套支承镗杆 采用 这种方法,镗杆是两端支承,刚性好,但立柱导 套的位置调整麻烦、费时,往往需要用心轴 块规找正,且需要用较长的镗杆,此法多用于 大型箱体的同轴孔系加工。
例1 图10-9所示为剖分式箱体结构简图,生产 类型是大批生产。该箱体的加工工艺过程 见表10-5 ~表10-7。
表面的复杂箱体时,如果仍用万能机床加工, 则工序分散,占用设备多,要求有技术熟练的 操作者,生产周期长,生产效率低,成本高。
为了解决这个问题,可以采用适于单件小 批生产的自动化多工序数控机床。 这样,可 用最少的加工装夹次数,由机床的数控系统 自动地更换刀具,连续地对工件的各个加工 表面自动地完成铣 、钻、扩、镗( 铰 )及攻 螺纹等工序 。 所以,对于单件小批、多品种 的箱体孔系加工,这是一种较为理想的设备 。 这样的设备又称为“机械加工中心” 。
2.镗模法
在中批、大批生产中广泛采用镗模法加 工孔系 。 模板上的导向孔已经包括了箱体 各面上所有要加工的孔,镗杆一般都采用两 个支承来引导并与机床主轴浮动连接 。 这 样,可使工件的精度不依赖于机床精度,而主 要由 镗模、镗杆及刀具来保证。
3.坐标法
坐标法是按孔系的坐标尺寸,在普通镗床、 立式铣床或坐标镗床上借助测量装置进行 加工的 。 其孔距精度决定于坐标位移精度, 而且不需要专用夹具就能适应各种规格箱 体的加工,通用性好。 普通體床的坐标测量 方法主要有以下几种:
零件加工的关键 。 一般应根据不同的生产 类型和孔系精度要求采用不同的加工方法, 具体加工方法如下:
1.找正法
加工前先在毛坯上划出各孔的加工线, 未铸出的孔应先钻出通孔,然后在铣床或镗 床上按划线一一进行找正加工。 找正法所 能达到的孔距精度低。 若改用试切法找正 或样板找正可提高孔距精度 。 采用找正法 加工孔系工时长,工作量大,并要求有较高的 操作技术水平 。 该法只适用于单件小批生 产。