操作规程英文版
优秀的操作规程模板英文

优秀的操作规程模板英文Standard Operating Procedure TemplateTitle: [Title of the SOP]Effective Date: [Date of implementation]Review Date: [Date of next review]Approved By: [Name and position of the approving authority]1. Purpose:The purpose of this Standard Operating Procedure (SOP) is to provide clear guidelines and instructions for [specify the purpose of the procedure].2. Scope:This SOP applies to all employees and personnel involved in [describe who this SOP is applicable to].3. Definitions:[List any specific terms or acronyms used in this SOP and provide their definition]4. Responsibilities:[List the roles and responsibilities of individuals or departments involved in the procedure]5. Procedure:[Provide a step-by-step guide on how to carry out the procedure. Use clear and concise language to ensure understanding and minimize errors. Include any necessary forms, checklists, or templates that need to be filled out.]5.1 [Procedure Step 1][Provide a detailed explanation of the first step, including any specific actions, equipment, or tools required.]5.1.1 [Sub-step 1][Describe sub-step 1 in detail]5.1.2 [Sub-step 2][Describe sub-step 2 in detail][Continue numbering and describing each sub-step until the procedure is complete]5.2 [Procedure Step 2][Provide a detailed explanation of the second step][Continue numbering and describing each step until the procedure is complete]6. Documentation:[Indicate any specific documentation requirements, such as recording data, completingforms, or updating logs. Provide instructions on where and how to access necessary documents]7. Training:[Describe any training requirements that must be completed prior to performing the procedure. Specify any specific training materials, courses, or certifications required]8. Safety Precautions:[Identify any safety precautions or personal protective equipment (PPE) requirements that must be followed throughout the procedure]9. References:[List any relevant documents, regulations, or standards that were used to develop this SOP]10. Appendices:[Attach any necessary forms, checklists, templates, or supporting documents here]11. Revision History:[Provide a summary of the changes made to this SOP, including the date and reason for each revision]12. Approval:[Include a signature block for the approving authority to sign and date the SOP]Note: This template is meant to serve as a general guide. Please adapt and customize it to suit the specific needs and requirements of your organization.。
实验室操作规程英文翻译

实验室操作规程英文翻译Laboratory Operating ProceduresIntroduction:Laboratory safety is of paramount importance to ensure the well-being of laboratory personnel and to prevent accidents or incidents that may compromise experimental results. These laboratory operating procedures aim to provide guidelines for safe and efficient laboratory practices. All personnel working in the laboratory are expected to adhere to these procedures at all times.1. General Safety Guidelines:1.1. Personal Protective Equipment (PPE): All laboratory personnel must wear appropriate PPE, including lab coats, gloves, and safety glasses, when working in the laboratory.1.2. Personal Hygiene: Maintain good personal hygiene by washing hands thoroughly before and after any laboratory activity.1.3. Fire Safety: Know the location of fire exits, fire extinguishers, and emergency showers. In the eventof a fire, immediately evacuate the laboratory and follow the designated emergency procedures.1.4. Chemical Safety: Properly handle chemicals and follow the Material Safety Data Sheet (MSDS) guidelines provided for each chemical. Avoid direct contact with skin, eyes, and inhalation of chemical fumes.1.5. Electrical Safety: Inspect electrical equipment regularly for frayed wires or damaged plugs. Only authorized personnel should make repairs or adjustments to electrical equipment.1.6. Equipment Safety: Follow manufacturer instructions for the operation, maintenance, and disposal of laboratory equipment. Do not use equipment without proper training or authorization.2. Laboratory Procedures:2.1. Experiment Planning: Before conducting any experiment, thoroughly read and understand the experimental procedures. Identify potential hazards and plan accordingly to mitigate risks.2.2. Workspaces: Keep workspaces clean, organized, and free from unnecessary clutter. Maintain clear pathways to avoid accidents and spills.2.3. Handling Glassware: Handle glassware with caution to prevent breakage and injuries. Dispose of broken glassware in designated sharps containers.2.4. Chemical Storage: Store chemicals in appropriate containers and cabinets, following chemical compatibility guidelines. Clearly label all chemical containers with their contents and expiration dates.2.5. Waste Disposal: Dispose of laboratory waste in designated waste containers. Separate hazardous waste from non-hazardous waste and ensure proper disposal according to regulatory requirements.2.6. Spill Procedures: Promptly report and clean up any spills, following the appropriate spill containment and cleanup procedures. Use suitable absorbent materials and dispose of them as hazardous waste.2.7. Laboratory Instruments: Use laboratory instruments, such as balances, pipettes, and centrifuges, according to manufacturer instructions. Calibrate and maintain instruments regularly to ensure accurate results.3. Emergency Procedures:3.1. First Aid: Familiarize yourself with the location of first aid kits and emergency eyewash stations. Report all injuries, accidents, or near misses to the laboratory supervisor immediately.3.2. Chemical Spills: In the event of a chemical spill, immediately notify the laboratory supervisor and follow the spill procedures. Evacuate the affected area if necessary.3.3. Fire Emergencies: In the event of a fire, activate the fire alarm, evacuate the laboratory, and follow the designated emergency procedures. Do not use elevators during a fire emergency.3.4. Gas Leaks: In the event of a gas leak, immediately evacuate the laboratory and inform the laboratory supervisor. Do not use any electrical devices or create any sources of ignition.Conclusion:These laboratory operating procedures provide guidelines for safe laboratory practices. It is the responsibility of all personnel to familiarize themselves with these procedures and adhere to them at all times. Any deviations or unsafe conditions should be reported to the laboratory supervisor immediately. By following these procedures, we canensure a safe and productive laboratory environment for all.。
作业操作规程英文简称
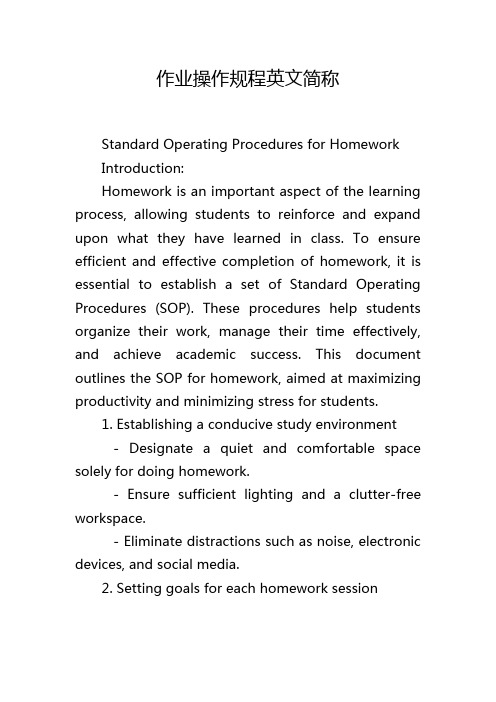
作业操作规程英文简称Standard Operating Procedures for HomeworkIntroduction:Homework is an important aspect of the learning process, allowing students to reinforce and expand upon what they have learned in class. To ensure efficient and effective completion of homework, it is essential to establish a set of Standard Operating Procedures (SOP). These procedures help students organize their work, manage their time effectively, and achieve academic success. This document outlines the SOP for homework, aimed at maximizing productivity and minimizing stress for students.1. Establishing a conducive study environment- Designate a quiet and comfortable space solely for doing homework.- Ensure sufficient lighting and a clutter-free workspace.- Eliminate distractions such as noise, electronic devices, and social media.2. Setting goals for each homework session- Break down the homework into smaller tasks to make it more manageable.- Set specific goals for each session to keep track of progress.- Prioritize tasks based on urgency and importance.3. Managing time effectively- Create a schedule that includes designated homework hours.- Allocate sufficient time for each task, considering their complexity and estimated completion time.- Avoid procrastination by adhering strictly to the schedule.4. Taking notes and organizing materials- Take clear and concise notes during class to facilitate understanding and revision.- Organize materials (textbooks, notebooks, and online resources) in a systematic and easily accessible manner.- Label and categorize materials based on subjects or topics.5. Understanding the requirements- Carefully read the homework instructions provided by teachers.- Seek clarification from teachers or classmates if any part of the instructions is unclear.- Identify the expected deliverables or outcomes.6. Planning the approach- Break down complex tasks into smaller steps.- Develop a logical sequence or order of completion for tasks.- Determine the resources and reference materials needed.- Create a rough outline or draft before starting the actual work.7. Conducting research and gathering information- Use reliable and reputable sources for collecting information.- Take notes while researching to avoid plagiarism and ensure proper citation.- Record all sources to facilitate referencing and citation.8. Starting with the easier tasks first- Begin with tasks that are relatively easier and require less time.- Build momentum and confidence by completing these tasks promptly.- This approach helps in managing time efficiently and reducing stress.9. Managing distractions and interruptions- Minimize interruptions by informing family members or roommates about designated study hours.- Turn off or silence electronic devices during study periods.- Use productivity apps or website blockers to limit distractions from the internet.10. Seeking help when needed- Reach out to teachers, classmates, or online resources for assistance when facing difficulties.- Do not hesitate to clarify doubts or ask for explanations.- Seek additional help outside of school if required.11. Reviewing and revising the completed work- Double-check the completed work for errors, omissions, or inconsistencies.- Review the work against the requirements to ensure all aspects have been addressed.- Make necessary revisions or improvements before submitting the homework.Conclusion:Following these Standard Operating Procedures for homework will not only enhance students' academic performance but also develop essential skills such as time management, organization, and problem-solving. These guidelines emphasize on effective planning, goal-setting, and creating a conducive study environment. By implementing these SOPs, students can optimize their productivity, reduce stress, and ultimately excel in their academic pursuits.。
加油车安全操作规程中英文版
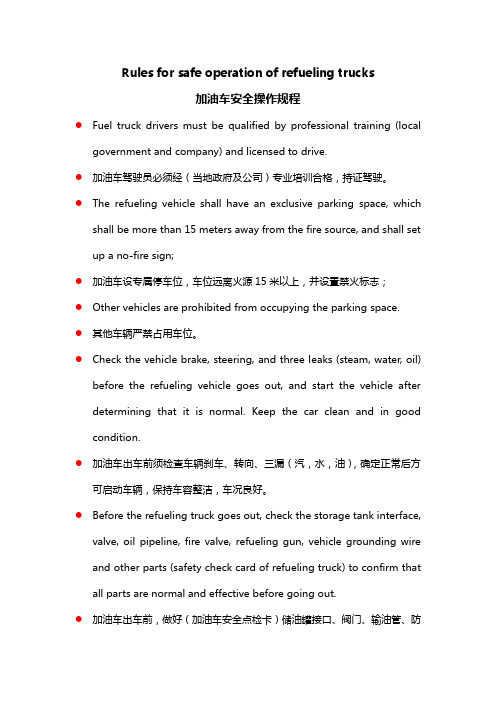
Rules for safe operation of refueling trucks加油车安全操作规程●Fuel truck drivers must be qualified by professional training (localgovernment and company) and licensed to drive.●加油车驾驶员必须经(当地政府及公司)专业培训合格,持证驾驶。
●The refueling vehicle shall have an exclusive parking space, whichshall be more than 15 meters away from the fire source, and shall set up a no-fire sign;●加油车设专属停车位,车位远离火源15米以上,并设置禁火标志;●Other vehicles are prohibited from occupying the parking space.●其他车辆严禁占用车位。
●Check the vehicle brake, steering, and three leaks (steam, water, oil)before the refueling vehicle goes out, and start the vehicle after determining that it is normal. Keep the car clean and in good condition.●加油车出车前须检查车辆刹车、转向、三漏(汽,水,油),确定正常后方可启动车辆,保持车容整洁,车况良好。
●Before the refueling truck goes out, check the storage tank interface,valve, oil pipeline, fire valve, refueling gun, vehicle grounding wire and other parts (safety check card of refueling truck) to confirm that all parts are normal and effective before going out.●加油车出车前,做好(加油车安全点检卡)储油罐接口、阀门、输油管、防火阀、加油枪、车辆接地线等部位检查,确认各部位正常有效,方可出车。
装载机安全操作规程-英文版
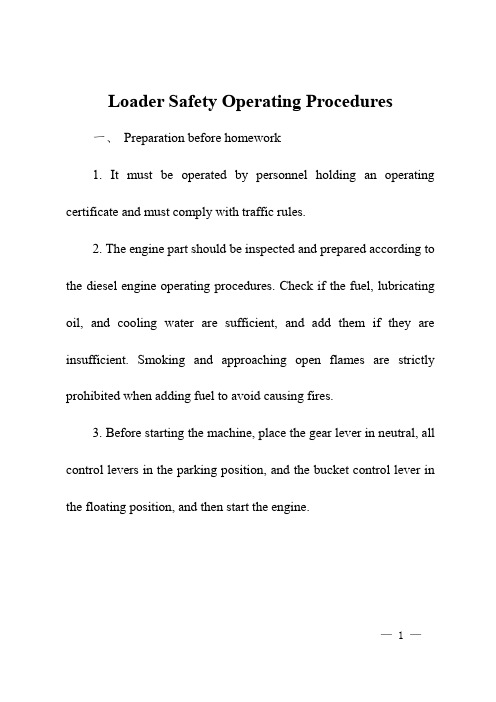
Loader Safety Operating Procedures一、Preparation before homework1. It must be operated by personnel holding an operating certificate and must comply with traffic rules.2. The engine part should be inspected and prepared according to the diesel engine operating procedures. Check if the fuel, lubricating oil, and cooling water are sufficient, and add them if they are insufficient. Smoking and approaching open flames are strictly prohibited when adding fuel to avoid causing fires.3. Before starting the machine, place the gear lever in neutral, all control levers in the parking position, and the bucket control lever in the floating position, and then start the engine.— 1 —4. Before starting work, it is necessary to check for any obstacles and dangerous goods around the work site, and level the construction site to facilitate the entry and exit of loaders and vehicles.5. Before starting the operation, the loader should run without load for 3-5 minutes, check if all parts are intact, and confirm that everything is normal before starting the loading operation.6. Check if the reverse warning device is working properly.7. Before starting, make a sound to indicate, observe for any personnel or obstacles around, and lift the bucket away; Before driving, the reliability of the brake system should be tested.二、Requirements for homework and driving8. Except for the driver inside the cabin, it is strictly prohibited to carry passengers in other areas of the aircraft.— 2 —9. In the case of hard soil, it is not advisable to forcefully load materials. Instead, other machinery should be used to loosen the material before loading with a loader.10. When unloading onto the vehicle, the bucket must be lifted toa height that will not touch the cargo loading baffle of the cargo compartment, to prevent the bucket from colliding with the cargo compartment.11. When unloading into the vehicle, it is not allowed to lift the bucket over the top of the car cab.12. During loading operations, it is important to regularly monitor the oil temperature of the hydraulic torque converter. When the oil temperature exceeds the specified value, the machine should be stopped to cool down before resuming operations.— 3 —13. Efforts should be made to avoid driving and shoveling materials horizontally on slopes.14. When going downhill, braking should be used to slow down, and neutral should not be used to prevent power from being cut off and causing a rolling accident.15. If the driver needs to leave the vehicle during work, the bucket should be placed on the ground, and it is forbidden for the driver to leave the vehicle while the bucket is suspended.16. During driving, the bucket should be kept 30-50cm off the ground.17. During the operation of the loader, it is strictly prohibited to stand under the bucket. If it is necessary to inspect the vehicle during bucket lifting, support measures should be taken for the bucket and ensure its firmness and reliability.— 4 —18. When working under overhead pipelines, be careful not to touch obstacles above when lifting the bucket. When working under high-voltage transmission lines, the bucket should also maintain a sufficient safe distance from the transmission lines.19. When working at night, there should be good auxiliary lighting equipment.20. No long-distance walking is allowed. When using a trailer for transportation, there should be a dedicated person to direct the loading and unloading of the trailer.21. During the operation, if there is a serious dust situation, the person in charge of the construction site must be notified to carry out methods such as watering and dust removal to avoid environmental pollution.三、Requirements after homework— 5 —22. The loader should be parked in a flat, safe, and unobstructed parking area, and the bucket should be lowered to the ground.23. Before shutting down, the engine should idle for 5 minutes and avoid sudden stopping and stalling.24. According to the warranty regulations, the loader shall be subject to periodic warranty.25. During maintenance and repair, waste oil, wastewater, etc. should be collected and centrally treated to avoid environmental pollution.— 6 —。
各岗位安全操作规程的英文

各岗位安全操作规程的英文Post Name: Safety Operation Procedures for Various Positions1. IntroductionSafety operation procedures are crucial in maintaining a safe working environment. By following these procedures, employees can prevent accidents, reduce risks, and ensure their own safety as well as the safety of others. The following are the safety operation procedures for various positions.2. Warehouse Worker- Always wear appropriate personal protective equipment (PPE) such as safety shoes, gloves, and helmets.- Follow proper lifting techniques to avoid back injuries.- Be aware of the location and proper handling of hazardous materials in the warehouse.- Keep the aisles clear and organized to prevent trips and falls.- Report any damaged or malfunctioning equipment immediately to the supervisor.仓库工作人员安全操作规程:- 总是穿着适当的个人防护装备,如安全鞋、手套和安全帽。
企业操作规程缩写英文

企业操作规程缩写英文Enterprise Operation Rules Abbreviation in EnglishIntroduction:In the business world, it is common for enterprises to have various operation rules and procedures in place. These documents are crucial for establishing consistency, efficiency, and accountability within an organization. However, operation rules can often be lengthy and tedious to read. To overcome this challenge, enterprises often use abbreviations to simplify the rules and make them more accessible. In this article, we will explore the commonly used abbreviations for enterprise operation rules in English.I. General Abbreviations:1. SOP - Standard Operating Procedure: An SOP is a set of step-by-step instructions that employees must follow to perform their tasks correctly and consistently. It ensures that all employees, regardless of their level of expertise, can perform their duties efficiently.2. OHS - Occupational Health and Safety: Refers to the measures and procedures in place to protect employees from workplace hazards and ensure a safe working environment.3. HRM - Human Resource Management: The management of an organization's workforce, including recruitment, training, performance evaluation, and employee relations.4. IT - Information Technology: The use, development, and management of computer systems, software, and networks within an organization.5. QA/QC - Quality Assurance/Quality Control: QA involves the systematic monitoring, evaluation, and improvement of products and services to ensure they meet specific standards. QC, on the other hand, focuses on identifying and rectifying defects in products or services.6. CRM - Customer Relationship Management: A strategy used by organizations to manage interactions and relationships with existing and potential customers. It involves collecting and analyzing customer data to improve customer satisfaction and loyalty.II. Financial Abbreviations:1. P&L - Profit and Loss: The financial statement that summarizes the revenues, costs, and expenses incurred during a specific period. It determines whether a company has generated a profit or incurred a loss.2. ROI - Return on Investment: A measure used to evaluate the efficiency or profitability of an investment. It compares the gain or loss from an investment relative to its initial cost.3. EBITDA - Earnings Before Interest, Taxes, Depreciation, and Amortization: This financial metric is used to assess a company's operating performance by evaluating its earnings before deducting non-operating expenses.III. Communication Abbreviations:1. KPI - Key Performance Indicator: A measurable value that indicates how effectively an organization is achieving its business objectives. KPIs are used to evaluate performance over time.2. SLA - Service Level Agreement: A contract between a service provider and a customer that outlines the level of service expected. It typically includes metrics such as response time, uptime, and resolution time.3. FAQ - Frequently Asked Questions: A compilation of commonly asked questions and their corresponding answers. It serves as a resource for customers or employees seeking quick answers to common queries.IV. Legal and Compliance Abbreviations:1. GDPR - General Data Protection Regulation: A regulation aimed at protecting the data privacy and rights of individuals within the European Union. It imposes strict rules on how organizations collect, process, and store personal data.2. FCPA - Foreign Corrupt Practices Act: A United States law that prohibits bribery of foreign officials by individuals and companies. It aims to promote transparency and integrity in international business transactions.3. FDA - Food and Drug Administration: A federal agency of the United States Department of Health and Human Services, responsible for protecting public health by ensuring the safety and efficacy of food, drugs, medical devices, and cosmetics.Conclusion:Abbreviations play a significant role in simplifying and streamlining enterprise operation rules. They allow for easier understanding and implementation of the rules while saving time and effort. By effectively utilizing abbreviations, enterprises can enhance communication, improve efficiency, and ensure compliance with various regulations.。
生产工艺操作规程英文缩写
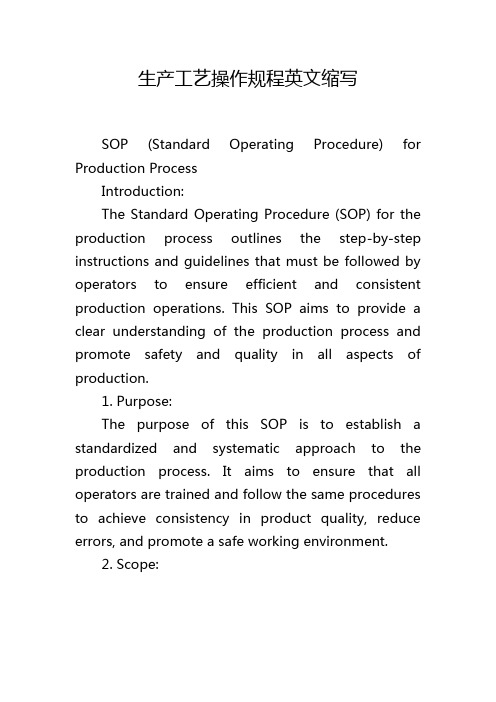
生产工艺操作规程英文缩写SOP (Standard Operating Procedure) for Production ProcessIntroduction:The Standard Operating Procedure (SOP) for the production process outlines the step-by-step instructions and guidelines that must be followed by operators to ensure efficient and consistent production operations. This SOP aims to provide a clear understanding of the production process and promote safety and quality in all aspects of production.1. Purpose:The purpose of this SOP is to establish a standardized and systematic approach to the production process. It aims to ensure that all operators are trained and follow the same procedures to achieve consistency in product quality, reduce errors, and promote a safe working environment.2. Scope:This SOP applies to all operators involved in the production process. It covers all production activities from material preparation to final product packaging.3. Responsibilities:3.1 Production Manager:- Establish and review the SOP for the production process- Ensure that all operators are trained on the SOP - Monitor and evaluate the implementation of the SOP- Provide necessary resources and support for the production process3.2 Operators:- Follow the instructions outlined in the SOP- Report any issues or deviations from the SOP to the supervisor- Maintain a clean and organized work area- Complete production records accurately and ina timely manner4. Equipment and Materials:4.1 Equipment:- List all equipment required for the production process, including their specifications, maintenance requirements, and calibration procedures.- Ensure that all equipment is properly cleaned, maintained, and calibrated before use.- Provide detailed instructions for the setup, operation, and shutdown of each equipment.4.2 Materials:- Specify the type and quality of materials required for the production process.- Outline the procedures for material handling, storage, and identification.- Provide guidelines for material inspection and quality control.5. Process Workflow:5.1 Material Preparation:- Provide instructions for the receipt, inspection, and storage of raw materials.- Specify the quantities and specifications of raw materials required for each production batch.- Outline the procedures for material preparation, including weighing, mixing, and blending.5.2 Production:- Provide step-by-step instructions for the production process, including the sequence of operations, operating parameters, and quality control checks.- Detail the procedures for equipment setup, product changeover, and cleaning between batches.- Specify the documentation requirements, such as production records, log sheets, and batch records.5.3 Quality Control:- Describe the quality control checks and tests required throughout the production process.- Specify the sampling procedures, testing methods, and acceptance criteria.- Outline the procedures for handling non-conforming products or deviations from quality standards.5.4 Packaging and Labeling:- Provide instructions for the packaging and labeling of finished products.- Specify the packaging materials and methods to be used.- Detail the procedures for product inspection, rejection, and rework.6. Safety Procedures:- Provide guidelines for safe work practices, including the use of personal protective equipment, handling hazardous materials, and emergency procedures.- Specify the procedures for reporting accidents, incidents, and near-misses.- Highlight the importance of maintaining a clean and safe work environment.7. Training and Documentation:- Specify the training requirements for operators involved in the production process.- Provide a record-keeping system for documenting training, as well as any deviations or incidents related to the SOP.- Ensure that all operators have access to a copy of the SOP and any associated documents.8. Revision and Approval:This SOP for the production process shall be reviewed and revised as needed by the Production Manager. Any changes to the SOP must be approved by the relevant stakeholders before implementation.Conclusion:This SOP outlines the instructions and guidelines for the production process to ensure a consistent and efficient workflow. It promotes safety, quality, and adherence to standard operating procedures. By following this SOP, operators will be able to producehigh-quality products while maintaining a safe and organized work environment.。
- 1、下载文档前请自行甄别文档内容的完整性,平台不提供额外的编辑、内容补充、找答案等附加服务。
- 2、"仅部分预览"的文档,不可在线预览部分如存在完整性等问题,可反馈申请退款(可完整预览的文档不适用该条件!)。
- 3、如文档侵犯您的权益,请联系客服反馈,我们会尽快为您处理(人工客服工作时间:9:00-18:30)。
机床操作规程Operating Procedure of Machine工作前穿戴好工作服及防护用品,扎好袖口,不准穿长衫、围围巾和头巾等丝带状物品,以及穿高跟鞋。
The worker shall wear the uniform, dress the protective equipments and fasten the cuff before work. Everyone is forbidden to wear gown, scarf, headband and high heels.女工应戴好工作帽。
高速切削或切削铸铁、铝、铜工件时,必须戴防护眼镜。
The workwoman shall wear helmet. The worker must wear protective glasses when the machine is fly cutting or cutting the iron, aluminum and copper materials接触旋转开关及旋转部位时,不得带手套作业,在夹装工件过程中允许带手套作业。
The worker does not allow wearing gloves when you touch the rotary switch or portions.1.车床技术安全操作规程1. Safety Operating Procedure of Lathe(1) 工作前须检查机床运转情况,检查工件及刀具是否夹紧,清除床面杂物。
(1) Before working, the lathe operator (lathe man) shall confirm the condition of lathe. The operator should check whether the work piece and cutter is tightened or not. The operator need clean the sundries from the platform before working.(2) 卡盘、花盘必须有保险装置,加工畸形和偏心零件时,要加平衡配重,先低俗运转,然后变为所要的速度。
(2) There must be insurance device in plate. When operator processes the deformation components, the balance weight must be used. At the beginning, the operator should operate slowly. Then, the operator changes the speed which you need.(3) 机床运转过程中不准用手清除切屑。
高速切削和建工铸件时,要戴防护眼镜或加防护罩。
加工钢件应合理使用刀具,用专用铁钩清理切屑。
(3) When the lathe is operating, don’t clean the scrap by using hand. The operator should wear safety glasses or put protective shield during fast cutting or processing the component. The operator should adopt properly cutter when the work man processes the steel. After working, the workman should use special hook to clean the scrap.(4) 用锉刀在车床上修锉工件时,必须右手在前左手在后,严禁用手缠绕纱布和棉纱砂光工件。
砂光内孔时必须用木棒垫缠纱布。
(4) When the operator uses the bastard file to cut the work piece on the lathe, he must use right hand in the front and left hand in the behind. The operator forbids tying gauze or cotton yarn on the hand during sanding artifacts. When operator sands the inner hole, you should use the stick to tie the gauze.(5) 加工长工件时,从主轴孔后伸出长度不得超出200毫米,并应加上醒目标志,超出200毫米时应装上支架。
(5) When operator processes long work piece, the stretch length of work piece should not exceed 200mm from main hole. When the length of work piece exceeds 200mm, the supporting device should be installed and also paste the attention logos.(6) 在装夹工件、调整卡盘、校正测量工件时,必须停机。
(6) The lathe should be stopped during putting the work piece, adjusting the plate and calibration measure piece.(7) 工作结束后应关闭电源,将各部位手柄置于安全位置。
(7) After working, the operator shall turn off all switches and pull the every handle in safety position.2.铣床技术安全操作规程2. Safety operating procedure of milling machine(1)工作前要检查机床各系统是否安全好用,各手轮摇把的位置是否正确,快速进刀有无障碍,各限位开关是否能起到安全保护的作用。
(1)Before working, The milling machine operator must check whether every system of machine is safety, the position of manual crank is right, the fast cutting is no obstruction and limit switch is safety or not.(2) 每次开车及开动各移动部位时,要注意刀具及各手柄是否在需要位置上。
扳快速移动手柄时,要先轻轻开动一下,看移动部位和方向是否相符。
严禁突然开动快速移动手柄。
(2) Operator shall pay attention to whether the cutters and cranks are in requiring position or not, when you use the milling machine. Using fast movable handle, the operator shall pull slowly and confirm the moving part and direction is right. Everyone forbids pulling the fast movable handle suddenly.(3) 安装刀杆、支架、垫圈、分度头、虎钳、刀孔等,接触面均应擦干净。
(3) The interface shall be cleaned, when the operator installs the hilt, bracket, cushion, dividing head, jaw vice, tool bore etc.(4) 机床开动前,检查刀具是否装牢,工件是否牢固,压板必须平稳,支撑压板的垫铁不宜过高或块数过多,刀杆垫圈不能做其他垫用,使用前要检查平行度。
(4) Before operating the milling machine, operator shall check whether cutter and work piece is fastness or not. The pressure plate must be stable and the cushion of supporting the plate shall not too height. The cushion of hilt barely use for hilt. The parallelism of every part should be checked by operator.(5) 在机床上进行上下工件、刀具、紧固、调整、变速及测量工件等工作时,必须停车,更换刀杆、刀盘、立铣头、铣刀时,均应停车。
拉杆螺丝松脱后,注意避免砸手或损伤机床。
(5) The milling machine should be cease when operator charge or discharge the work piece and cutter (including fasten, adopt, speed change, measure the work piece). When the operator changes the hilt, cutter, vertical milling head and so on, the machine also should cease. The worker should watch out and avoid hurt or damage the milling machine when the rob screw is loose.(6) 机床开动时,不准量尺寸、对样板或用手摸加工面。
加工时不准将头贴近加工表面观察吃刀情况。
取卸工件时,必须移动刀具后进行。
(6) When the milling machine operates, anyone shouldn’t measure the size, align the work piece or touch the surface using hand. The operator forbids observing the condition of cutter at nearly during processing the work piece. Charging or discharging the work piece, the operator must remove the cutter first.(7) 装平铣刀,使用扳手扳螺母时,要注意扳手开口选用适当,用力不可过猛,防止滑倒。