供应商质量管理文献翻译(外文翻译-中英对照)
质量手册翻译中英文对照解析

质量手册翻译中英文术语表3.1.1 质量 quality3.1.2 要求 requirement3.1.3 等级 grade3.1.4 顾客满意 customer satisfaction3.1.5 能力 capability3.2.1 体系(系统) system3.2.2 管理体系 management system3.2.3 质量管理体系 quality management system 3.2.4 质量方针 quality policy3.2.5 质量目标 quality objective3.2.6 管理 management3.2.7 最高管理者 top management3.2.8 质量管理 quality management3.2.9 质量策划 quality planning3.2.10 质量控制 quality control3.2.11 质量保证 quality assurance3.2.12 质量改进 quality improvement3.2.13 持续改进 continual improvement3.2.14 有效性 effectiveness3.2.15 效率 efficiency3.3.1 组织 organization3.3.2 组织结构 organizational structure3.3.3 基础设施 infrastructure3.3.4 工作环境 '77ork environment 3.3.5 顾客 customer3.3.6 供方 supplier3.3.7 相关方 interested party3.4.1 过程 process3.4.2 产品 product3.4.3 项目 project3.4.4 设计和开发 design and development 3.4.5 程序 procedure3.5.1 特性 characteristic3.5.2 质量特性 quality characteristic 3.5.3 可信性 dependability3.5.4 可追溯性 traceability3.6.1 合格(符合) conformity3.6.2 不合格(不符合) nonconformity 3.6.3 缺陷 defect3.6.4 预防措施 preventive action3.6.5 纠正措施 corrective action3.6.6 纠正 correction3.6.7 返工 rework3.6.8 降级 regrade3.6.9 返修 repair3.6.10 报废 scrap3.6.11 让步 concession3.6.12 偏离许可 deviation permit3.6.13 放行 release3.7.1 信息 information3.7.2 文件 document3.7.3 规范 specification3.7.4 质量手册 quality manual3.7.5 质量计划 quality plan3.7.6 记录 record3.8.1 客观证据 objective evidence3.8.3 试验 test3.8.4 验证 verification3.8.5 确认 validation3.8.6 鉴定过程 qualification process3.8.7 评审 review3.9.1 审核 audit3.9.2 审核方案 audit programme3. 9.3 审核准则audit criteria3.9.4 审核证据 audit evidence3.9.5 审核发现 audit findings3.9.6 审核结论 audit conclusion3.9.7 审核委托方 audit client3. 9.8 受审核方 auditee3.9.9 审核员 auditor3.9.10 审核组 audit team3.9.11 技术专家 technical expert3.9.12 能力 competence3.10.1 测量控制体系 measurement control system 3.10.2 测量过程 measurement process3.10.3 计量确认 metrological confirmation3.10.4 测量设备 measuring equipment3.10.5 计量特性metrological characteristic 3.10.6 计量职能 metrological function Aaudit 3.9.1 审计audit client 3.9.7 客户审计audit conclusion 3.9.6 审计结论audit criteria 3.9.3 审计标准audit evidence 3.9.4 审计证据audit findings 3.9.5audit programme 3.9.2 审计大纲audit team 3.9.10 审计团队auditee 3.9.8auditor 3.9.9Ccapability 3.1.5characteristic 3.5.1concession 3.6.11conformity 3.6.1continual improvement 3.2.13 correction 3.6.6corrective action 3.6.5customer 3.3.5customer satisfaction 3.1.4 competence 3.9.12Ddefect 3.6.3dependability 3.5.3design and development 3.4.4 deviation permit 3.6.12document 3.7.2Eeffectiveness 3.2.14efficiency 3.2.15Ggrade 3.1.3Iinformation 3.7.1infrastructure 3.3.3inspection 3.8.2interested party 3.3.7Mmanagement 3.2.6management system 3.2.2 measurement control system 3.10.1 measurement process 3.10.2 measuring equipment 3.10.4 metrological characteristic 3.10.5 metrological confirmation 3.10.3 metrological function 3.10.6Nnonconformity 3.6.2Oobjective evidence 3.8.1 客观证据organization 3.3.1 organizational structure 3.3.2 Ppreventive action 3.6.4 procedure 3.4.5process 3.4.1product 3.4.2project 3.4.3Qqualification process 3.8.6 quality 3.1.1quality assurance 3.2.11quality characteristic 3.5.2 quality control 3.2.10quality improvement 3.2.12 quality management 3.2.8quality management system 3.2.3 quality manual 3.7.4quality objective 3.2.5quality plan 3.7.5quality planning 3.2.9 质量计划quality policy 3.2.4Rrecord 3.7.6 记录regrade 3.6.8release 3.6.13 放行repair 3.6.9requirement 3.1.2review 3.8.7rework 3.6.7 返工Sscrap 3.6.10specification 3.7.3supplier 3.3.6 供应商system 3.2.1 系统Ttechnical expert <audit> 3.9.11 技术出口test 3.8.3 测试top management 3.2.7 高层管理traceability 3.5.4 可塑性Vvalidation 3.8.5verification 3.8.4 验证Wwork environment 3.3.4 工作环境质量管理体系基础和术语 Quality management syst ems--Fundamentals and vocabulary质量管理和质量保证标准第2部分: GB/T 19001、GB /T 19002和GB/T 19003实施通用指南 Quality manag ement and quality assurance standards--Part 2: Generic guidelines for the application of GB /T 19001、GB/T 19002 and GB/T 19003质量管理和质量保证标准第3部分: GB/T 19001在计算机软件开发、供应、安装和维护中的使用指南 Qual ity management and quality assurance standards --Part 3: Guidelines for the application of G B/T 19001 to the development, supply, installat ion and maintenance of computer software质量管理和质量保证标准第4部分:可信性大纲管理指南 Quality management and quality assurance s tandards--Part 4: Guide to dependability prog ramme management质量管理体系要求 Quality management systems--Requirements质量管理体系业绩改进指南 Quality management sy stems--Guidelines for performance improvement s质量管理和质量体系要素第2部分: 服务指南 Quali ty management and quality system elements--Pa rt 2: Guidelines for services质量管理和质量体系要素第3部分: 流程性材料指南 Quality management and quality system elements --Guidelines for processed materials质量管理和质量体系要素第4部分: 质量改进指南 Q uality management and quality system elements--Guidelines for quality improvement质量管理质量计划指南 Quality management--Gui delines for quality plans质量管理项目管理质量指南 Quality management--Guidelines to quality in project management质量管理技术状态管理指南 Quality management--Guidelines for configuration management质量体系审核指南审核 Guidelines for auditing q uality systems--Part 1: Auditing质量体系审核指南质量体系审核员的评定准则 Guide lines for auditing quality systems--Part 2: Q ualification criteria for quality systems audit ors质量体系审核指南审核工作管理 Guidelines for au diting quality systems--Part 3: Management of audit programmes测量设备的质量保证要求第一部分: 测量设备的计量确认体系 Quality assurance requirements for mea suring equipment Part 1: Metrological confirmat ion system for measuring equipment测量设备的质量保证第2部分: 测量过程控制指南 Q uality assurance for measuring equipment--Par t 2: Guidelines for control of measurement proc esses质量手册编制指南 Guidelines for developing qual ity manuals质量经济性管理指南 Guidelines for managing the economics of quality质量管理培训指南 Quality management--Guideli nes for training English Chinesereceipt (入厂)接受,验收,进货handling 搬运packaging 包装storage 保存protection 保护comparison 比较identification 标识replacement of identification mark 标识标志更换maintenance of identification 标识的保持records of identification control 标识控制记录tender 标书normative document 标准文件supplemental 补充nonconforming product 不合格品control of nonconforming product 不合格品控制control procedure of nonconforming products 不合格品控制程序tendency of nonconformance 不合格倾向purchasing 采购verification of purchased product 采购的产品验证purchasing process 采购过程purchasing control procedure 采购控制程序purchasing information 采购信息reference standard 参照标准reference instructions 参照细则stockhouse 仓库measurement, analysis and improvement 测量,分析和改进measurement result 测量结果control procedure of monitoring and measuring d evices 测量设备控制程序planning 策划preservation of product 产品保护control procedure for maintenance, replacement and records of product identification 产品标识的保持, 更换和记录控制程序procedure for product identification and tracea bility 产品标识和可追溯性程序conformity of product 产品的符合性monitoring and measurement of product 产品的监督和测量product plan 产品方案control procedure for product preservation 产品防护控制程序method of product release 产品放行方法conformity of product, product conformity 产品符合性product realization 产品实现planning of product realization 产品实现策划product characteristics 产品特性input to product requirements 产品要求的输入product status 产品状态final acceptance of product 产品最后验收procedure 程序program documents 程序文件continual improvement 持续改进procedure for continual improvement of quality management system 持续改进质量体系程序adequacy 充分性storage location 存放地点agency personnel 代理人员submission of tenders 递交标书adjustment 调整,调节statutory and regulatory requirements 法律法规要求rework, vt 返工repair, vt 返修subcontractor 分承包方annex 附录improvement 改进improvement actions 改进措施on-the-job training 岗位技能培训responsibility of individual department and pos t 各部门, 各岗位职责change identification 更改标记change order number 更改单编号process sheets 工艺单process specification 工艺规程procedure(process card) 工艺规程(工艺卡) process characteristics 工艺特性Job Description Format 工种描述单work environment 工作环境impartiality 公正性functional requirements 功能要求supplier 供方supplier evaluation procedure 供方评价程序supplier provided special processes 供方提供的特殊过程verification at supplier's premises 供方现场验证supply chain 供应链criteria for supplier selection, evaluation and re-evaluation 供应商选择、评估和再评估准则communication 沟通customer 顾客customer property 顾客财产control procedure for customer property 顾客财产控制程序customer feedback 顾客反馈Customer Service Contact Form 顾客服务联系表customer communications 顾客沟通customer satisfaction 顾客满意statistical analysis of customer satisfaction 顾客满意度统计分析customer complaint 顾客投诉identification of customer requirements 顾客要求的识别management review 管理评审records from management review 管理评审记录management review control procedure 管理评审控制程序management representative 管理者代表management responsibility 管理职责specified limits of acceptability 规定的可接受界限specified use 规定的用途process 过程complexity of processes 过程的复杂性monitoring and measurement of processes 过程的监视和测量operation of process 过程的运行status of processes 过程的状态process approach 过程方法process controls 过程控制process control documents 过程控制文件process performance 过程业绩appropriateness 合适性changes to contractor 合同的更改contract review control procedure 合同评审控制程序internet sales 互联网销售environmental conditions 环境条件monogram pragram requirements 会标纲要要求type of activities 活动类型infrastructure 基础建设infrastructure 基础设施fundamentals and vocabulary 基础与词汇control of records 记录控制technical specificaion 技术规范process trace sheet 加工跟踪单monitoring and measurement 监视和测量monitoring and measuring device 监视和测量装置control of monitoring and measuring devices 监视和测量装置控制check method 检查方法frequency of checks 检查频次calibration status 检定状态inspection and test control procedure 检验和试验控制程序identification procedure for inspection and tes t status 检验和试验状态标识程序inspection witness point 检验见证点inspection hold point 检验停止点buildings 建筑物delivery 交付post-delivery activities 交付后的活动delivery activities 交付活动interface 接口acceptance of contract or orders 接受合同或定单type of medium 介质类型experience 经验correction action 纠正措施Corrective action response time 纠正措施答复时间,纠正措施响应时间management procedure for corrective actions 纠正措施管理程序corrective action response times 纠正措施响应时间development activity 开发活动traceability mark 可追溯性标志objectivity 客观性Customer Service Log 客户服务记录簿control feature 控制特性,控制细节control features 控制细则periodic assessment of stock 库存定期评估justification 理由routine 例程,惯例,常规质量职能分配表论证范围internal communication 内部沟通internal audit 内部审核internal audit procedure 内部审核程序internally controlled standard 内控标准internal audit 内审results of internal and external audits 内外部审核结果competence 能力training 培训training needs 培训需要evaluate 评价records of the results of the review 评审结果的记录review output 评审输出review input 评审输入Purchase Requisition 请购单authority 权限validation 确认concession 让步human resources 人力资源job training of personnel 人员岗位培训qualification of personnel 人员资格equipment control procedure 设备控制程序device type 设备类型order of design changes 设计更改通知单design and development control procedure 设计和开发控制程序design and development 设计开发design and development planning 设计开发策划control of design and development changes 设计开发更改控制design and development review 设计开发评审design and development validation 设计开发确认design and development outputs 设计开发输出design and development inputs 设计开发输入design and development verification 设计开发验证design validation 设计确认design documentation 设计文件编制design acceptance criteria 设计验收准则design verification 设计验证audit program 审核大纲conduct of audits 审核行为audit criteria 审核准则production process control 生产过程控制production process control procedure 生产过程控制程序production and service provision 生产和服务提供control of production and service provision 生产和服务提供的控制validation of processes for production and serv ice provision 生产和服务提供过程的确认production order 生产令identification and traceability 识别和可追溯性identification and traceability maintenance and replacement 识别和可追溯性维护与替换invalidate 使失效market survey 市场调研suitability 适宜性scope 适用范围controlled condition 受控状态terms and definitions 术语与定义analysis of data 数据分析sequence 顺序transfer of ownership 所有权转移system document 体系文件statistical technique 统计方法outsource(vt) a process 外包过程external source 外部来源documents of external origin 外来文件outsource, vt 外协unique identification 唯一的标识maintenance 维护Document Change Control 文件更改控制Request For Document Change (RDC) 文件更改需求单control of documents 文件控制documentation requirements 文件要求enquiry 问询,询价field nonconformity analysis 现场不符合分析relevance 相关性interaction 相互作用detail design 详细设计,详图设计,零件设计,施工设计sales department 销售部sales contract 销售合同checklist 校验表,一览表,检查一览表calibration 校准submission of action plans 行动计划的递交documented procedures 形成文件的程序documented statement 形成文件的声明performance requirements 性能要求licensee responsibilities 许可证持有者责任acceptance criteria 验收准则verification arrangement 验证安排verification results 验证结果customer focus 以客户为关注点,以客户为焦点awareness 意识introduction 引言,概述,介绍normative references 引用标准application 应用visit to user 用户访问review of requirements related to the product 有关产品的要求评审competent 有能力的effectiveness 有效性determination of requirements related to the pr oduct 与产品有关的要求的确定customer-related processes 与顾客有关的过程preventive action 预防措施management procedure for preventive actions 预防措施管理程序planned results 预期的结果intended use 预期的用途procedure for competence, knowledge and trainin g of personnel 员工能力, 知识和培训程序personnel training procedure 员工培训程序supporting services 支持性服务functions 职能部门responsibility 职责assignment of responsibility 职责分工workmanship 制造工艺manufacturing acceptance criteria 制造验收准则quality policy 质量方针quality programs 质量纲领quality management system 质量管理体系quality management system planning 质量管理体系策划performance of the quality management system 质量管理体系业绩quality plan 质量计划quality records 质量记录quality objectives 质量目标quality audit 质量审核quality manual 质量手册quality problem handling form 质量问题处理单quality requirements 质量要求allocation table of quality responsibilities 质量职能分配表availability of resources 资源的可获得性resource management 资源管理allocation of resources 资源配置provision of resources 资源提供general requirements 总要求,一般要求constituent part 组成部件organization 组织continual improvement of the organization 组织的持续改进size of organization 组织的规模Organizational Diagram 组织机构图final acceptance 最终验收work instructions 作业指导书11 / 11。
采购管理中的供应商关系管理外文翻译(可编辑)

采购管理中的供应商关系管理外文翻译(可编辑)采购管理中的供应商关系管理外文翻译外文翻译原文Determining the Purchase Situation: Cornerstone ofSupplierRelationship ManagementMaterial Source: google scienceAuthor: Evi HartmannThomas RitterAbstract:Purchasing has moved to the agenda of senior management reflecting an increasing strategic attention to benefits that can be gained from management of and cooperation.with suppliers. Modern purchasing approaches reflect this changing emphasis towards the importance of quality and innovativeness of suppliers as opposed to pure price negotiations. However, different approaches are suitable for different purchase situations,for the specific circumstances the buying firm is in. Detailed evaluation and analysis of the purchase situation are even more cr ucial to a company’s sustainable success since new ways of interacting such as electronic marketplaces are developing fast and changing the way firms work together. In this paper, the authors structure different classification models of purchase situations by identifying the underlying dimensions. Based on the literature review the authors havegrouped the indicators in four dimensions. Then by combining these dimensions an overall integrated classification model is developed. Finally, suggestions for future research are discussed.IntroductionThe field of purchasing has evolved significantly in the last two centuries. The growing pressure of global competition and less internal value-creation has led to the recognition that purchasing is animportant co ntributor to a firm’s competitive advantage by both academics and practitioners. An appropriate sourcing strategy can contribute significantly to increase profitability, market share and technological innovation. This increased importance of purchasingrelates to different reasons as cost, quality and technology.Because purchase costs account on average for more than 40% of total expenses they are clearly a major area for potential cost savings. The present invention relates to a system and method for a Commercial credit card. Credit cards operate by having the enabling buyers and sellers of goods to transact with each institution issuing the credit card, the merchant bank, proother. More particularly, the present invention provides. Besides cost benefits purchasing and supply management has a majorimpact on quality. Companies have tended to concentrate on their core competencies with the aim to increase effectiveness and efficiency Hamel, Prahalad 1995. The need to nurture core competences has lead to an increased emphasis on outsourcingVenkatesan 1992. This development reduced a company’s internaladded value in the product value chain to its core competences and atthe same time the supplier’s influence on quality increased to a dominant role.A further lever for an increased importance of purchasing is the extremely short life cycle of new technology. Companies focus on highly customized supplies instead of purchasing commodities. They hand-over product responsibility and risk to their suppliers to cope withincreased product development pressure. Early and extensive supplier involvement shortens the product development process and is an important source of innovation von Hippel 1988, Bozdogan, Deyst, Hoult, Lucas 1998. The focus of attention has shifted to the significance of co-operative buyer-seller relationships to“enable purchasing to support a firm’s strategic positioning” Harland, Lamming, Cousins 1999, p. 659. Based on these trends one of the most important objectives of the purchasing function is the development of a supplier network, since a firm’sability to produce a quality product at reasonable cost and in timely manner is mainly influenced by its suppliers’ capabilities Hahn, Watts, Kim 1990. Firms conclude that they will more readily attain long-term cost reduction by forming closer working relationships with “key” suppliers Harland, Lamming, Cousins 1999. But partnering in general is not the solution for success because of related costs, high resource intensity and risk of dependency. The relationships need to be adaptedto the specific purchasesituation. Depending on different external contingencies the appropriate relationship type should be developed with different governance structure and relational design. Bensaou 1999 showed thatfir ms “balance aportfolio of different types of relationships rather than rely on one type” which leads to the key question: Which kind of supplier cooperation needs to be established in which purchasing situation to contribute to the success of a company? Or in other words, under which circumstances should a firm try to establish a relationship with its suppliers? The appropriate analysis of the purchasing situation is even more important since the establishment of electronic marketplaces and web-supported trading Kaplan, Sawhney 2000, which builds a new dimension for purchasing with reduced interpersonal contact but transactional focus. In a nut shell e-trade offers an even more different approach to do business and as such the decision of how to interact with thesupplier base or parts thereof becomes more critical.In the literature various dimensions for structuring the purchasing situation have been developed, although an integrated model is missing Cousins, Spekman 2000, M?ller,F?rr?nen 2000, Dyer, Fr?hling 1999, Cho, Chu 1998, Metcalf, Frear 1993, Hubmann,Barth 1990, Müller 1990, Witt 1986, Bogaschewsky, Rollberg 1999, Baumgarten, Wolff 1999, Wildemann 1999, Mittner 1991, Kraljic 1983, Elliott, Glynn 2000, Bensaou,1999,Cannon, Homburg, Willauer 1998, Olsen, Ellram 1997, Krapfel, Salmond,Spekman1991, Lamming, Cousins, Notman 1996 etc.. This paper tries to integrate several aspects by building a systematic and consistent framework, which enables managers to identify the appropriate purchasing strategy depending on the situational circumstances. The paper is organized as follows: Firstly, we provide an overview of the literature on classification and portfolio models of supplier relationships by developing a conceptual framework. Then, based on this literature classification by synthesizing all aspects an integrated classification model is proposed. We close with an outlook of further research opportunities and some managerial implications.Purchase situation classification dimensions.In the past portfolio models have been successfully used for assessing more efficiently a company’s position in respect to its current position, the projected future and the future desired positions in various dimensions Wind, Douglas 1981, Ansoff, Leontiades 1976,Markowitz, 1952. The pioneering portfolio theory for management of equity was developed by Markowitz in 1952. In the field of industrial marketing and purchasing recently several portfolios have been developed for evaluating customer and supplier relationships since the early 1980s. The different approaches can be structured by four segmentation dimensions: product, market, supplier and relationship characteristics.With the term purchase situation we consider all relevant forces and influences related to the acquisition of required materials, services and equipment, which have a potential impact on the way buyerand seller work together. The following four characterization dimensions underline the magnitude of various aspects impacting this sourcing environment.Figure 1: ABC-Analysis in Chemical industryThis classification differs suppliers with significant spent fromthe mass of suppliers with only small purchase volume Bogaschewsky, Rollberg, 1999 and clearly demonstrates he economic importance of the supplier Baumgarten, Wolff, 1999. Especially in the industrialproduction industry the ABC-analysis is very helpful, since there it is a common situation that the majority of the purchase spent is caused by only few material categories Corsten 1996. Another volume characteristic is number of parts, which is especially important in discrete production. But besides economic volume and number of parts the physical size can also have an important business impact, especially for products which need large storage space. To reduce inventory carrying cost for large products just- in-time order policies could be in place. Therefore some authors not only categorize the monetary sourcing spent but also number of parts and physical volume Bogaschewsky, Rollberg, 1999.But purchase volume alone can sometimes be misleading. The cheapest component is, in the long run, not necessarily the least expensive. Once the cost of poor quality is factored in the cheapest maywell be the most expensive Burt, 1989. Decisions on sourcingstrategies cannot only be based on purchase value or volume, the perceived risk has to be evaluated including its various components asfinancial risk, performance risk, social risk and other componentsGemünden 1985, p.84,85.Therefore some researchers talk about product and purchase importance Cannon, Perreault 1999, Homburg 1999, Olsen, Ellram 1997, Homburg 1995, Matthyssens, Van den Bulte 1994, Metcalf, Frear 1993, Kraljic 1983. Olsen and Ellram 1997 detail the importance by economic factors in terms of “dollar value and the impact on the company’s profits” Olsen, Ellram 1997, p.103, by competence factors, which “describe the extent to which the item purchased is part of the company’s core competencies” Olsen, Ellram 1997, p. 103 and by strategic importance. The closer the purchased product is to the core competencies of the firm, the greater is the strategic importance of the purchased good Olsen, Ellram 1997. Product importance as “the extent to which a consumer links a product to salientenduring or situ ation specific goals” Bloch, Richins 1983, p. 71 is a broader definition for product characteristics. For Metcalf and Frear 1993 the product importance is not an inherent product characteristic, but its perception by the buyer will relate to the “product’s ability to satisfy the goals of the buying firm” Metcalf, Frear 1993, p. 66. Product importance is also influenced by the risk of the supply for the production process, if the delivery is delayed Mittner 1991, p.22. But not only risk due to delays has to be included in the product importance evaluation, also functional and qualitative aspects relating to product performance, financial factors or social effects have to befurther detailed Gemünden1985, p. 90. Product importance also refers to theposition of the supply in the value chain of the producing company, which then determines a potential impact of short innovation and product cycle of the supply.To evaluate the product complexity and standardization another product segmentation dimension is the degree of product customization Cannon, Homburg, Willauer 1998,Dyer, Cho, Chu 1998, Metcalf, Frear 1993, which can reflect in product specification, delivery agreements and specific payment schemes. Metcalf and Frear 1993 talk about “adaptations”, which occur when “one party in a relationship alters its processes or the item exchanged to accommodate the other party” Wilson 1995, p. 339. Adaptations develop over time by implying cost. They can be grouped in different types of adaptation as technical knowledge-based, administrative, economic and legal Hakansson, Gadde 1992, 408 and may include customizing products, financial terms, information sharing routines, pricing inventory stocking policies, delivery schedules and production processes Cannon Narayandas 2000,p.412. The product specification dimension is frequently used in the automotive industry, where only limited suppliers deliver highly customized productsThey fall in the “keiretsu-category” Dyer, Cho, Chu 1998, p. 60, withroughly 30 suppliers of more than 300. Keiretsu suppliers in the automotive industry deliver parts as engine parts, body panels or seats Dyer, Cho, Chu 1998. The degree of customization underlines the supplier willingness to invest in the relationship. On the other hand it showsthe trust and commitment Morgan, Hunt 1994 of the buying company to rely on a single source The demand pattern defines the continuity and age of the relationship Bogaschewsky,Rollberg 1999, Baumgarten, Wolff 1999, Baumgarten, Bodelschwingh 1996. Suppliers use this measurement as a key indicator for planning the production. As a result of derived demand Fiocca 1982 emphasizes the importance that “industrial marketers must always be up to date about the current and prospective trends” p. 54.By reviewing those four sub criteria of product characteristics they are all too important to be excluded. But they need to be weighted depending on their relevance according to the specific circumstance. A balanced scorecard approach can helps to simplify this evaluation process.Market characteristicsFor classifying a supplier relationship not only the productspecific characteristics areimportant. Many different market aspects influence the purchasing situation, although they may not be fully influenced by both parties of the purchasing process. One frequently used segmentation dimension is the supply risk determined by production shortages, product availability,availability of alternatives, which is the “degree to which a buying firmhas alternative sources of supply to meet a need” Cannon, Perreault 1999,p.444, on time delivery, quality acceptance or seasonality Baumgarten, Wolff 1999,Orths 1999, Wildemann 1999, Baumgarten, Bodelschwingh 1996, Homburg 1995,Hubmann, Barth 1990, Müller 1990, Witt 1986. Wildemann 1999 differentiates between “internal and external supply risk” p.441. Company external risks are influenced by supply problems with substitutes, seasonality, transport logistics complexity and delivery time, whereas internal risk factors are such as the possibility of indoor production, availability of production know-how and product and production complexity Wildemann 1999, Lamming et al. 1996.The second market characteristic besides supply risk is the buying power, each firm must be able to understand its competitive environment Lamming et al. 1996, p. 176. For defining the buying power, which describes the governance in the purchasing situation, several market indicators have to be summarized - such as industry growth and exit barriers, number of competitors, the number of suppliers and an understanding of the rivalry in the market Porter 1996, p. 23. Following traditional economic theory when many suppliers compete to sell comparable goods, the marketbecomes a ready source of information on prices and quality Cannon, Perreault 1999, which strengthens the position of the buyer. But theopposite occurs if only limited suppliers are in the market, the buying company has to cope with the uncertainty and dependence. The buying power is further described by Geck and Petry 1983 with three characteristics: dominant size of the buying company compared to the supplier, market knowledge advantage of the buyer and the servicefunction of the supplier “customer is king” Geck, Petry 1983, p.17.The geographic spread is a further sub-criteria of the buying power, which defines the buying company’s opportunities concerning global sourcing strategies Monczka, Trent, Handfield 1998, Kiedaisch 1997. Similar to the buying power definition Cannon, Homburg and Willauer 1998 talk about situational factors as dynamism of price and quality.Supplier characteristicsSupplier characteristics are only used by a few researchers for supplier relationship classification Elliott, Glynn 2000, Wildemann 1999, Bensaou 1999, whereas many supplier aspects have been evaluated in the literature dealing with the supplier evaluation and selection process Monczka, Trent, Handfiel 1998, Saunders 1997, van Weele 2000, Koppelmann 1997, Hartmann 1992, Hildebrandt, Koppelmann 2000.The definition of resources goes along with Hofer, Schendel 1978, p. 145, Helfert 1998, p.51-52, Ritter 1998, p.82-83, who cluster the resource base in four groups: financial resources, physical resources, personnel resources and information resources p.82, 83. In business market the buying company depends in part on these resources of the supplier Ford et al. 1999, p. 76. Standard performance indicators asin the annual report enable a differentiated judgment for the purchasing management concerning financial stability of the supplier. For a better basis of price negotiation supplier’s margins need to be recalculatedor at least estimated Olsen, Ellram 1997. The resource potential describes the suppliers commercial and financial competence, but the technical perspective is as well important Olsen, Ellram 1997.译文采购管理中的供应商关系管理资料来源: 谷歌学术网作者:哈特曼.艾威托马斯.瑞特摘要:采购已经进入了高级管理的议事日程,它反映出了对利益高度的战略关注,这些利益可以从与供应商的合作和管理中获得。
《供应商认证与管理》中英文版
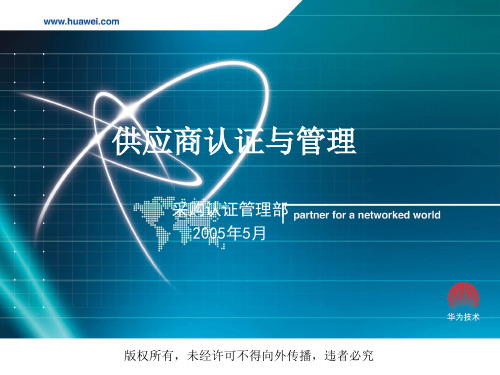
1.1 供应商认证 特别注意:
1、对于新供应商新器件,必须严格按照前面的6步 进行认证。 2、对于合格供应商(已经我司认证合格上网)的 新器件,通常只进行器件认证,即:
A、样品测试、在板测试 B、小批量试用 C、供应商实地考察(必要时)
All Rights Reserved. No transmission is allowed without permission.
供应商认证与管理
采购认证管理部 2005年5月
版权所有,未经许可不得向外传播,违者必究
Supplier Qualification and Management
Procurement Qualification Management Dept Mar,2005
All Rights Reserved. No transmission is allowed without permission.
All Rights Reserved. No transmission is allowed without permission.
1.1 Supplier Qualification
(2) Communication with potential suppliers If the questionnaire and documents are acceptable, a meeting (or a conference call) can be arranged to communicate with the supplier to understand the supplier‟s capacity and discuss the cooperation affairs.
All Rights Reserved. No transmission is allowed without permission.
供应链管理外文文献及翻译

供应链管理外文文献及翻译供应链管理的实践和理论已经在全球范围内得到广泛应用和研究。
本篇文献回顾了最近的文献,旨在提供一个有关供应链管理的广泛和多样化的视角。
本文献主要关注采购、生产和物流等方面。
本文献指出了供应链管理的重要性以及不断变化的环境对供应链管理的挑战。
作者还强调了合作伙伴关系、信息共享、风险管理和绩效评估等方面的关键因素。
总的来说,对于供应链管理的研究,应该包括广泛的实践案例和深入的理论研究。
只有这样,才能理解不断变化的环境对供应链管理的影响,从而制定更好的供应链管理策略。
翻译:Supply Chain Management Foreign Literature and TranslationThe practice and theory of supply chain management have been widely applied and studied worldwide. This literature review aims toprovide a broad and diversified perspective on supply chain management, focusing mainly on procurement, production, and logistics.The literature points out the importance of supply chain management and the challenges that the constantly changing environment poses to it. The authors also emphasize critical factors such as partnership relationships, information sharing, risk management, and performance assessment.In general, research on supply chain management should include diverse practical cases and in-depth theoretical studies. Only in this way can we understand the impact of the constantly changing environmenton supply chain management and formulate better supply chain management strategies.。
供应商管理程序《中英文版》

1.PURPOSE 目的:To establish a guideline to control and monitor supplier quality performance, manage supplier to improve quality system and product quality to meet XXX (ZhongShan) expectations.建立监控供货商质量绩效的方针,管理供货商改进质量系统及产品质量以达到乂乂乂(中山)的期望目标.2.SCOPE 范围:2.1This procedure applies to all suppliers that provides production material products to XXX (ZhongShan).此程序适合于XXX(中山)提供生产性物料的所有供货商.2.2This procedure is applicable for QA to manage supplier quality and related issue only.此文件仅适用于QA管理供货商质量及相关问题.3.DEFINITIONS 定义:3.1Key Sup plier :The supplier provides the material that is either valuable and / or critical impact to product’s characteristics关键供货商:提供对产品价值或性能有关键影响物料的供货商.3.2SRS: Supplier Rating System.SRS:供货商评估系统.3.3FAI: First Article Inspection.FAI:首件检验.3.4LAR: Lot Accept Rate from incoming inspection.LAR:来料检查批接收率.4.REFERENCE DOCUMENT 参考文件:4.1BZQP-7-06 Supplier Rating System Procedure 供货商评估系统程序.4.2BZQP-8-07 Corrective and preventive actions procedure 纠正及预防措施程序.5.RESPONSIBILITY 职责:5.1Purchasing staff 采购5.1.1Arrange consolidation of the overall material supplier performance and distribute to related parties. 整理供货商质量绩效并发布给相关部门5.1.2Review the supplier performance and enhance supplier improvement management.评估供货商绩效加强供货商改善管理.5.1.3Coordinate and plan supplier’s support both for ongoing & future if necessary.协调和规划供货商现在及将来的支持5.2QA质量工程师.5.2.1Follow supplier corrective action in line complaint.跟进产线投诉问题和供货商的改善行动.5.2.2Define key supplier for evaluation or assessment with purchasing staff.与采购定义关键供货商以便评估.5.2.3Review the assessment result for further improvement or supplier quality related matters..审核供货商质量相关的事项的评估结果,达到持续改善.5.3ME制造工程If necessary, ME will support QA to perform supplier process audit and technology evaluation.必要时,ME将协助QA执行供货商制程审核及技术评估.6.PROCEDURE 程序:6.1Supplier Rating System 供货商级别评估体系.Purchasing and QA shall select the key supplier and perform SRS. Refer to Supplier Rating System Procedure(BZQP-7-6).采购和QA选择关键供货商进行评估,参照供货商评估系统程序(BZQP-7-6)6.2Material qualification 物料资格认证.6.2.1Under selection of a potential supplier, Sourcing or purchasing sends the specification or drawing componentrequirements to supplier and Engineer instruct supplier to submit sample and related document (Attachment 1.)选定部分供货商后,资材部或采购将部件规格要求或图纸转交给供货商,工程部工程师指导供货商按照提交样品和相关档(附禧1)6.2.2Engineer will cooperate to complete FAI, detail operation process refer to “Incoming First Article InspectionInstruction (BZQAWI-003)”.工程师将完成物料的FAI检查,具体作业方法请参考“来料首件检查指示(BZWIQA-003)”6.2.3After the internal inspection completed, QA submit the passed part and FAI documents to customer for make finalapprove if need. After customer approve the sample, QA distribute the approved sample and relative files to IQC and buyer as the proof of approved by XXX (ZhongShan).内部检查完成后,如客户要求,QA将零件批准的数据(零件样板)和FAI报告送与客户批准.客户检查并批准后,QA将客户最终承认的样板及相关文件分发至IQC和采购,作为样板被乂乂乂(中山)承认的依据.6.2.4If material is rejected by customer, the original copy of material approval should return back to QA. Return processfrom 6.2.1 to 6. 2.4如零件承认被客户否决,则承认零件退回给QA.重复步骤6.2.1至6.2.4.6.2.4.1For the critical to quality indirect material and not customer specified ,new developed suppliermaterial needs to pass Engineer’s approval, and send to customer for approval as required.对于客户未指定的间接物料,在其对产品质量有重要影响的状况下,新物料需要经过工程师批准,如果客户要求将送给客户进行批准.6.2.5Material disqualification procedure.物料资格取消程序6.2.5.1In the below cases, IQC or buyer has the authority to request and disqualify supplier’s part supply, andIQC rise a material disqualification request.( BZQP-7-07F01.1)当发现如下情况时,IQC或采购有权对供货商提出取消其生产件供应资格的申请,并且该申请将以物料供应资格取消申请书形式提出(BZQP-7-07F01.1)6.2.5.1.1Serious quality issue from supplier (example: safety issue, use banned material, or seriouslyimpact production in XXX etc).部品发现重大质量问题(如安全问题,使用禁用物料,或对XXX造成重大生产影响等).6.2.5.1.2More than 3 times claims for material quality from IQC or production line within one month and thereis no effective action to improve the quality after IQC warn or QA perform factory audit.在一个月内IQC拒收三批以上的物料或生产线对该物料有三次以上的质量投诉并且在IQC通知供货商或对供货商进行审核后供货商在质量方面没有有效改善.6.2.5.1.3Continual twice get red card in supplier rating system (for single sourcing supplier, materialis disqualified except customer approval)在供货商级别评定中连续两次评定为不合格(对于单一货源供货商,除非客户批准,否则将取消其资格).6.2.5.1.4Customer requirement 客户要求.6.2.5.1.5Others 其它.6.3 Supplier Qualification & disqualification 供货商资格认证及取消6.3.1For new supplier (or second source) who is opened by XXX (ZhongShan), QA needs to qualify new supplier.For the current suppliers, purchasing can list them directly in the AVL list.对于XXX(中山)开发的新供货商(或者第二供货商),QA需要进行新供货商的资格认证.对于现有的供货商,可直接进入AVL表.6.3.2There are 5 classifications of “supplier qualification” process will be applied:将有5个不同级别的文件被引用到供货商认证中去:6.3.2.1NDA (Non-disclosure agreement):保密协定This is a non-disclosed agreement for supplier with XXX (ZhongShan) before business. Supplier mustobey XXX (ZhongShan) business requirements, can not disclose any XXX (ZhongShan) businessinformation, drawing, technical information, pricing information to any other 3rd party under thisagreement withoutXXX(ZhongShan) permissions.此档是供货商与乂乂乂(中山)生意合作之前的保密协定.供货商必须遵守乂乂乂(中山)商业要求, 不能揭露任何乂乂乂(中山)生意方面信息、图纸、技术信息、价格信息等给任何未经XXX(中山)授权的第三方机构.6.3.2.2Supplier reliable investigate report:供货商信誉度调查This report is to investigate supplier reliable information in market and ensure supplier can show enoughcapability to support XXX (ZhongShan)此文件用以调查供货商的市场信息以保证供货商有足够能力和XXX(中山)配合.6.3.2.3Supplier Qualification Summary Report 供货商认证总结报告This report is conducted by purchasing for one supplier evaluation summary report & qualificationstatus.此份报告由采购主导用以供货商评估总结及认证状况.6.3.2.4Supplier audit report, QA is responsible for perform audit ,if it is necessary and applicable, QA releasesthe copy of report to purchasing.供货商审核报告,QA有必要且可实施状态下将对供货商进行审核,QA将复印件分发至采购.6.3.2.5Supplier Disqualification Request 供货商资格取消申请.This report will be requested by purchasing & QA to disqualify a supplier; and the applicant will fill inthe application. It will be effective by their manager and Plant Manager approval.此份报告由采购及QA用以供货商资格取消申请.由各自部门经理和厂长签名后生效.6.3.3Primary opportunities for one qualified supplier:供货商认证的首选机会:6.3.3.1 A well developed quality management system.优秀的质量发展管理系统.6.3.3.2Reasonable price and forwardly to support XXX (ZhongShan) on cost down approach.可以接受的价格水平并主动配合乂乂乂(中山)降低成本.6.3.3.3Capability of ensuring stable and punctual material supply chain system.能够保证稳定而准时的供应链系统.6.3.3.4Good service can support XXX (ZhongShan) at emergency; provide XXX (ZhongShan) on reliable &acceptable information; quickly respond on claims & remarks; support XXX (ZhongShan) on flexibility;forwardly to provide XXX (ZhongShan) on Information (News, Technical support).优良的服务;能够在紧急状况下支持XXX(中山);提供给XXX(中山)合理的和可以接受的信息; 迅速回馈XXX(中山)的抱怨及相关要求;弹性地服务XXX(中山);主动配合XXX(中山)有用的信息(新闻、技术支持).6.3.4Buyer gathering information of supplier: company profiles, brochures; products information (samples, specs),etc. If it matches current business requirments, then will send “Supplier Reliable Investigate Report” tosupplier for self-evaluation, request supplier to submit self-evaluation data to purchasing for evaluation, based oncurrent commodity supplier base status, technology, quality, cost, responsiveness, service, delivery, stability&capability, environmental & safety, If recommended supplier matches XXX’s requirements, purchasing willlead the “Development team” to audit supplier.采购收集供货商信息:公司资料及手册;产品信息(样品、规格)等如果供货商符合当前XXX(中山)商业需求,负责采购将“供货商信誉度调查报告”发给供货商进行自我评估;要求供货商提供自我评估数据并回馈给采购,采购依据XXX现有商品供货商基础、技术、质量、成本、反应速度、服务、交期、稳定性和能力、环境及安全等予以综合评估.如果推荐的供货商符合乂乂乂(中山)要求,采购将安排发展团队予以评鉴.6.3.5Purchasing will lead “development team” to summarize “Supplier Qualification Summary Report”,to evaluaterecommended supplier will be qualified supplier. XXX (ZhongShan) qualified supplier must be required:采购将主导“发展团队”总结“供货商认证总结报告”,以评估推荐供货商成为合格供货商.XXX (中山)合格供货商必须同时满足如下要求:6.3.5.1Pass XXX (ZhongShan) QA audit if it is applicable. The approval classification will refer to “BZWIQA-015supplier audit &qualification”.在审核可以进行和需要的条件下,供货商须通过乂乂乂(中山)。
供应商管理库存系统外文文献翻译最新译文
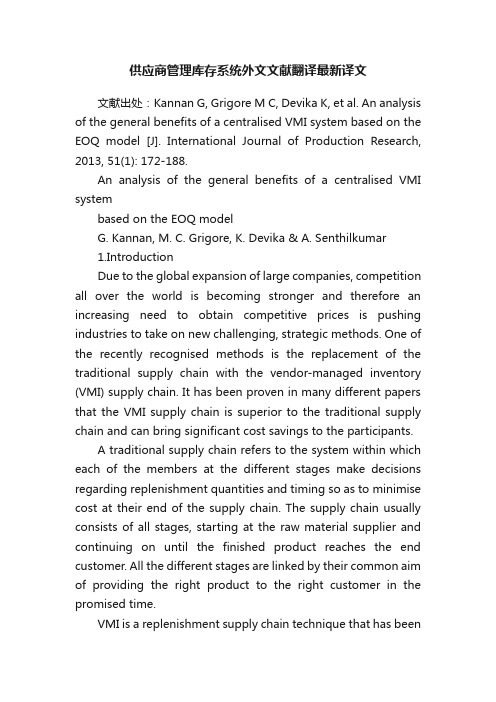
供应商管理库存系统外文文献翻译最新译文文献出处:Kannan G, Grigore M C, Devika K, et al. An analysis of the general benefits of a centralised VMI system based on the EOQ model [J]. International Journal of Production Research, 2013, 51(1): 172-188.An analysis of the general benefits of a centralised VMI systembased on the EOQ modelG. Kannan, M. C. Grigore, K. Devika & A. Senthilkumar1.IntroductionDue to the global expansion of large companies, competition all over the world is becoming stronger and therefore an increasing need to obtain competitive prices is pushing industries to take on new challenging, strategic methods. One of the recently recognised methods is the replacement of the traditional supply chain with the vendor-managed inventory (VMI) supply chain. It has been proven in many different papers that the VMI supply chain is superior to the traditional supply chain and can bring significant cost savings to the participants.A traditional supply chain refers to the system within which each of the members at the different stages make decisions regarding replenishment quantities and timing so as to minimise cost at their end of the supply chain. The supply chain usually consists of all stages, starting at the raw material supplier and continuing on until the finished product reaches the end customer. All the different stages are linked by their common aim of providing the right product to the right customer in the promised time.VMI is a replenishment supply chain technique that has beenimplemented since the beginning of the 1980s by Wall-Mart and Procter & Gamble (Waller et al. 1999), and has its roots back in 1958 when Magee (1958) first introduced the concept.Within a VMI agreement, the upstream supply chain member (the vendor) takes responsibility for managing the inventory of the downstream member (the buyer) within specific levels previously agreed upon without the need for orders from the customer side to be placed. Therefore, the vendor can focus on optimising production efficiency and capacity planning, while the customer has to improve forecastaccuracy.The success of VMI is dependent on communication between the partners, their willingness to share data, collaboration and coordination, and an information technology system which enables fast access to critical information (Duchessi and Chengalur-Smith 2008).The general characteristics of a traditional supply chain and of a VMI supply chain, formed by three stage.The research here is meant to offer a simple overview of the possible outcomes after VMI implementation in a two-stage supply chain, between the vendor and its multiple buyers. The analysis focuses on the overall supply chain cost impact, which VMI can show under specific conditions, based on the practical experience learned in the pharmaceutical industry.Using VMI in a supply chain brings transparency regarding essential information among the partners, thus giving the opportunity at each stage to adjust the decisions in a timely manner and avoid emergency situations.The VMI supply chain implies coordination between the partnering stages, continuous information sharing, and regularmeetings where critical issues are discussed and follow-up actions are noted.The general benefits model analysed in this paper is based on the economic ordering quantity (EOQ) model and is an extension of Bookbinder et al.'s (2010) paper. As an extension of the aforementioned work, the model has been adjusted to integrate different requirements and constraints from within the pharmaceutical industry. It has been further extended from analysing a one-vendor, one-buyer deterministic demand case to analysing a one-vendor, multiple-buyer stochastic demand case.The mathematical model applies to two echelons, the vendor and its multiple buyers. An observation is made here to distinguish that the buyers are not the end-consumers but represent sales organisations from each country. At the same time both the vendor and buyers belong to the same organisation.In the literature, one of the main challenges when implementing VMI has beenidentified in providing the right incentives for all partners to do their best for the supply chain and the right contract to share the overall profits (Nagarajan and Rajagopalan 2008).The fact that both stages belong to the same organisation facilitates simpler developments further. There is no need for complicated contracts for profit sharing between the two partners in a VMI case, as the most important thing is the total supply chain profit. It can be assumed that both partners have the right incentives to increase overall supply chain profits.Based on the assumptions above, the traditional supply chain model is developed according to its general characteristics within which the centralised organisation does not show anyimpact, while the VMI model is developed as and when decisions are taken centrally to obtain overall supply chain cost reductions.2. Literature reviewThe literature review of this paper is divided into two categories: first, an overview of general positive characteristics observed after the VMI implementation (or) assumed to occur behind the theoretical model and then the second part looks at the literature which clearly focused on the EOQ modeling to determine the potential benefits of a VMI supply chain.2.1 General characteristics of VMI outcomesThis section verifies the outcomes of a VMI relationship and presents a short literature review of different benefits which have been recognised by other authors to be the outcome of VMI partnerships. A couple of articles have directly addressed the general benefits which can be achieved from a VMI partnership without necessarily developing a model to prove their arguments but through empirical research.Lee et al. (2008) analysed how lean systems would perform with VMI, Collaborative Planning, Forecasting and Replenishment (CPFR), and continuous replenishment and identified that expenses can be significantly decreased and flexibility improved under VMI. Elvander et al. (2007) developed a framework for a VMI configuration with four categories: inventory-related dimensions, information-related dimensions, decision-making dimensions, and a systemintegration level. Dorling et al. (2006) evaluated VMI under oligopolistic competition and defined five steps towards VMI implementation. Donget al. (2007) surveyed the literature and identified that VMI is adopted when the supplier deals with high market competitiveness and when there is good cooperationbetween the supplier and the buyer.Blatherwick (1998), Disney et al. (2003), and Sari (2008) identified that VMI can be outperformed by other strategies in specific situations.2.2 General benefits models of VMI based on the EOQ modelThe literature review presented below focuses strictly on research papers which have developed specific models to evaluate the benefits of a VMI supply chain based on EOQ modelling.Bookbinder et al. (2010), Yao et al. (2007), and Razmi et al. (2010) evaluated the supply chain costs under a traditional supply chain compared to a VMI situation. All cases considered a two-echelon model formed by a vendor and a buyer, and the model development was based on the EOQ formula.Bookbinder et al. (2010) compared three cases: the traditional supply chain, VMI, and central decision making. The difference between traditional supply chains and VMI was obtained through transferring the cost of placing an order, which was incurred by the buyer, to the vendor under the VMI. Also, the vendor's cost of placing an order has been considered to be lower than the buyer's. One of the findings of the model is that both the vendor and the buyer are better off as long as the vendor's holding costs divided by the buyer's holding cost are higher than the ordering cost.Yao et al. (2007) showed that total costs can be decreased under VMI as long as the ordering cost of the vendor is lower than that of the buyer. However, results also show that the buyer has greater benefits than the vendor.Razmi et al. (2010) effectuated a sensitivity analysis by varying the parameter values of the total cost function whileincluding a backordering cost in the calculation. While in the traditional supply chain model both the vendor and the customer incurred costs, in the case of VMI all the costs have been attributed to the vendor. Pasandideh et al. (2010) used an EOQ model to evaluate the impact of differentparameters on the total cost when applying VMI and when shortage is backlogged. The EOQ model developed showed that VMI could bring important cost savings but this has its limitations on the values of the ordering costs of the two participants.Zhang et al. (2007) analysed the total cost function incurred under a VMI partnership where an exponential function of the ordering costs was taken. The model was applied to a one-vendor, one-buyer case and proved that decreasing the ordering cost represents an investment which brings lower costs for all buyers. Teng et al. (2005) used integer programming to extend the classic economic production quantity (EPQ) model to allow for time varying cost, with deterministic demand. The findings showed that the total cost is a convex function of the number of replenishments, for which the minimum number should be identified for savings to be obtained. Chen and Wei (2011) examined the optimal dynamic joint decisions using a calculus-based formulation combined with dynamic programming techniques in a vertically decentralised single manufacturer Stackelberg and single-retailer channel over a multi-period planning horizon subject to deteriorating goods and multivariate demand function. Niranjan et al. (2011) analysed the issues surrounding the VMI implementation using 15 features categorised as product related, company related, or supplier related. In addition to the researchers mentioned in Table 1, the following researchers have also analysed the benefits of the VMIsystem (Disney and Towill 2002b, Sourirajan et al. 2008, Bakal and Geunes 2009, Battini et al. 2009, Wang 2009, Liu and ?etinkaya 2010, Borade et al. 2011).Zhang et al. (2007) developed an integrated VMI, where a joint cost model was built under the assumption of constant demand rate and production. The model evaluates the impact on the total cost function when varying the ordering cost. Ordering costs can be reduced through a VMI partnership, and the partners can share the benefits. Later, a model to indicate the general benefits which a VMI partnership could bring, and adjusted to the pharmaceutical case, will be developed.Many authors have focused their attention on the analysis of the VMI performance based on constant demand characteristics, for which the EOQ model represents the basis for the analysis. While researching the general benefits of VMIbased on EOQ model literature, one of the gaps identified is the fact that evaluations were done strictly between one vendor and one buyer. The only exception is identified in Zhang et al. (2007), who considered two buyers but focused on order cost reduction evaluation.Based on the findings in the literature, this paper extends previous research and analyses the possible benefits when dealing with one vendor and multiple buyers assuming a stochastic, constant type of demand.3. Problem definition and research scopeThe objective of this paper is to develop a relevant model which integrates specific constraints from the pharmaceutical industry and which has the ability to project the possible cost differences between a traditional supply chain and a VMI supply chain.Some of the aspects which the model will integrate are: constant demand, variable demand, evaluation of a two-stage supply chain composed of a vendor and his multiple buyers, and identification of the importance of fast reaction to demand changes and maintenance of a high customer service level as defined by the industry.The characteristics are integrated in both traditional and VMI supply chains, while the model is based on the EOQ model rational with the purpose of highlighting cost differences between the two. Under the VMI supply chain, the transportation cost and the cost of issuing an order are transferred from the buyer to the vendor.The structure of the paper is as follows: Section 4 develops the mathematical model for the traditional and VMI supply chains, and this is then numerically applied in Section 5. The results of the numerical application are discussed in Section 6, and Section 7 presents an overall conclusion of the paper and identifies directions for further research opportunities.3.1 Research highlightsThe model developed in this paper extends previous works which based their analysis of traditional versus VMI supply chains on EOQ models by acknowledging demand variability and integrating preventive actions.Another difference which is captured within this model represents the extendednumber of buyers evaluated. While previous research focused on one-vendor, one-buyer cases, the model here integrates one vendor and multiple buyers.Evaluating the situation of multiple buyers with whom the vendor has the possibility to establish VMI partnerships givesmore flexibility to the vendor to consolidate specific product demands. Based on this opportunity, the model is structured to evaluate benefits depending on the number of products shared among more buyers.译文基于经济订购量模式的供应商管理库存系统的综合效益分析G. Kannan, M. C. Grigore, K. Devika & A. Senthilkumar1 引言由于大公司的全球化扩张,世界各地的竞争越来越强烈,因此越来越需要获得具有竞争力的价格,这对企业来说是一个全新的挑战,但也是推动产业发展的战略方法。
质量与检测外文文献翻译、中英文翻译、检测检验类外文翻译
Quality and InspectionAccording to the American Society for Quality Control (ASQC), quality is the totality of features and characteristics of a product or service that bear on its ability to satisfy given needs. The definition implies that the needs of the customer must be identified first because satisfaction of those needs is the “bottom line” of achieving quality. Customer needs should then be transformed into product features and characteristics so that a design and the product specifications can be prepared.In addition to a proper understanding of the term quality, it is important to understand the meaning of the terms quality management, quality assurance, and quality control.Quality management is that aspect of the overall management function that determines and implements the quality policy. The responsibility for quality management belongs to senior management. This activity includes strategic planning, allocation of resources, and related quality program activities.Quality assurance includes all the planned or systematic actions necessary to provide adequate confidence that a product or service will satisfy given needs. These actions are aimed at providing confidence that the quality system is working properly and include evaluating the adequacy of the designs and specifications or auditing the production operations for capability. Internal quality assurance aims at providing confidence to the management of a company, while external quality assurance provides assurance of product quality to those who buy from that company.Quality control companies the operational techniques and activities that sustain a quality of product or service so that the product will satisfy given needs. The quality control function is closest to the product in that various techniques of unsatisfactory sources of quality performance.Many of the quality systems of the past were designed with the objective of sorting good products from bad products during the various processing steps. Those products judged to be bad had to be reworked to meet specifications. If they could not be reworked, they were scrapped. This type of system is known as a “detection correction” system. With this system, problems were not found until the products were inspected or when they were used by the customer. Because of the inherent nature of human inspectors, the effectiveness of the sorting operations was often less than 90%. Quality systems that are preventive in nature are being widely implemented. These systems prevent problems from occurring in the fist place by placing emphasison proper planning and problem prevention in all phases of the product cycle.The final word on how well a product fulfills needs and expectations is given by the customers and users of that product and is influenced by the offering of competitors that may also be available to those customers and users. It is important to recognize that final word is formed over the entire life of the product, not just when it was purchased.Being aware of customers’ needs and expectat ions is very important, as was previously discussed. In addition, focusing the attention of all employees in an enterprise on the customers and users and their needs will result in a more effective quality system. For example, group discussions on product designs and specifications should include specific discussion of the needs to be satisfied.A basic commitment management should be that quality improvement must be relentlessly pursued. Actions should be ingrained in the day-to-day working of the company that recognize that quality is a moving target in today’s marketplace driven by constantly rising customer expectations. Traditional efforts that set a quality level perceived to be right for a product and direct all efforts to only maintain that level will not be successful in the long haul. Rather, management must orient the organization so that once the so--called right quality level for a product has been attained; improvement efforts continue to achieve progressively higher quality levels.To achieve the most effective improvement efforts, management should understand that quality and cost are complementary and not conflicting objectives. Traditionally, recommendations were made to management that a choice had to be made between quality and cost--the so--called tradeoff decision--because better quality inevitably would somehow cost more and make production difficult. Experience throughout the world has shown that this is not true. Good quality fundamentally leads to good resource utilization and consequently means good productivity and low quality costs. Also significant is the higher sales and market penetration result from products that are perceived by customers to have high quality and performance reliability during use.Four basic categories of quality costs are described in the following:(1)Prevention--costs incurred in planning, implementing, and maintaining a quality system that will ensure conformance to quality requirement at economical levels. An example of prevention cost is training in the use of statistical process control.(2)Appraisal—costs incurred in determining the degree of conformance toquality requirements. An example of appraisal cost is inspection.(3)Internal failure—costs arising when products, components, and materials fail to meet quality requirements prior to transfer of ownership to the customer. An example of internal failure cost is scrap.(4)External failure—costs incurred when products fail to meet quality requirements after transfer of ownership to the customer. An example of external failure cost is warranty claims.A problem—solving approach should be followed in seeking quality improvement. The results of any improvement effort will not be permanent unless the root causes of the problems have been found so appropriate (irreversible) corrective action can be implemented.The root cause can be defined as the real cause of a problem. This is often quite different from the apparent cause, which appears after a superficial investigation. A frequently asked question is how to known when the root cause is found and when the investigator is not still being deceived by the apparent cause. A meaning answer is that if the root cause has been found, the problem is able to be turned on and off by adding or removing the cause.Once the root cause has been found, an irreversible corrective action must be implemented so there is no foreseeable situation by which the root cause can return and so permanent improvement results.Although the level of quality control is determined in large part by probability theory and statistical calculations, it is very important that the data collection processes on which these procedures depend be appropriate and accurate. The best statistical procedure is worthless if fed faulty data, and like machining processes, inspection data collection is itself a process with practical limits of accuracy, precision, resolution, and repeatability.All inspection and/or measurement processes can be defined in terms of their accuracy and repeatability, just as a manufacturing process is evaluated for accuracy and repeatability. Controlled experiments can be performed, and statistical measures of the results can be made to determine the performance of a method of inspection relative to the parts to be inspected. Suitability of one or another method can be judged on the basis of standard deviations and confidence levels that apply to each approach as used in a given inspection situation.质量与检测根据美国质量管理协会的定义,质量是产品或服务能够满足规定需求而具有的特性和特征的总和。
质量控制中英文对照
QE=品质工程师(Quality Engineer)MSA: Measurement System Analysis 量测系统分析LCL: Lower Control limit 管制下限Control plan 管制计划Correction 纠正Cost down 降低成本CS: customer Sevice 客户中心Data 数据Data Collection 数据收集Description 描述Device 装置Digital 数字Do 执行DOE: Design of Experiments 实验设计Environmental 环境Equipment 设备FMEA: Failure Mode and Effect analysis 失效模式与效果分析FA: Failure Analysis 坏品分析FQA: Final Quality Assurance 最终品质保证FQC: Final Quality control 最终品质控制Gauge system 量测系统Grade 等级Inductance 电感Improvement 改善Inspection 检验IPQC: In Process Quality Control 制程品质控制IQC: Incoming Quality Control 来料品质控制ISO: International Organization for Standardization 国际标准组织LQC: Line Quality Control 生产线品质控制LSL: Lower Size Limit 规格下限Materials 物料Measurement 量测Occurrence 发生率Operation Instruction 作业指导书Organization 组织Parameter 参数Parts 零件Pulse 脉冲Policy 方针Procedure 流程Process 过程Product 产品Production 生产Program 方案Projects 项目QA: Quality Assurance 品质保证QC: Quality Control 品质控制QE: Quality Engineering 品质工程QFD: Quality Function Design 品质机能展开Quality 质量Quality manual 品质手册Quality policy 品质政策Range 全距Record 记录Reflow 回流Reject 拒收Repair 返修Repeatability 再现性Reproducibility 再生性Requirement 要求Residual 误差Response 响应Responsibilities 职责Review 评审Rework 返工Rolled yield 直通率sample 抽样,样本Scrap 报废SOP: Standard Operation Procedure 标准作业书SPC: Statistical Process Control 统计制程管制Specification 规格SQA: Source(Supplier) Quality Assurance 供应商品质保证Taguchi-method 田口方法TQC: Total Quality Control 全面品质控制TQM: Total Quality Management 全面品质管理Traceability 追溯UCL: Upper Control Limit 管制上限USL: Upper Size Limit 规格上限Validation 确认Variable 计量值Verification 验证Version 版本QCC Quality Control Circle 品质圈/QC小组PDCA Plan Do Check Action 计划执行检查总结Consumer electronics 消费性电子产品Communication 通讯类产品Core value (核心价值)Love 爱心Confidence 信心Decision 决心Corporate culture (公司文化)Integration 融合Responsibility 责任Progress 进步QC quality control 品质管理人员FQC final quality control 终点品质管制人员IPQC in process quality control 制程中的品质管制人员OQC output quality control 最终出货品质管制人员IQC incoming quality control 进料品质管制人员TQC total quality control 全面质量管理POC passage quality control 段检人员QA quality assurance 质量保证人员OQA output quality assurance 出货质量保证人员QE quality engineering 品质工程人员FAI first article inspection 新品首件检查FAA first article assurance 首件确认CP capability index 能力指数SSQA standardized supplier quality audit 合格供应商品质评估FMEA failure model effectiveness analysis 失效模式分析AQL Acceptable Quality Level 运作类允收品质水准S/S Sample size 抽样检验样本大小ACC Accept 允收REE Reject 拒收CR Critical 极严重的MAJ Major 主要的MIN Minor 轻微的Q/R/S Quality/Reliability/Service 品质/可靠度/服务P/N Part Number 料号L/N Lot Number 批号AOD Accept On Deviation 特采UAI Use As It 特采FPIR First Piece Inspection Report 首件检查报告PPM Percent Per Million 百万分之一SPC Statistical Process Control 统计制程管制SQC Statistical Quality Control 统计品质管制GRR Gauge Reproducibility & Repeatability 量具之再制性及重测性判断量可靠与否DIM Dimension 尺寸DIA Diameter 直径QIT Quality Improvement Team 品质改善小组ZD Zero Defect 零缺点QI Quality Improvement 品质改善QP Quality Policy 目标方针TQM Total Quality Management 全面品质管理RMA Return Material Audit 退料认可7QCTools 7 Quality Control Tools 品管七大手法通用之件类ECN Engineering Change Notice 工程变更通知(供应商)ECO Engineering Change Order 工程改动要求(客户)PCN Process Change Notice 工序改动通知PMP Product Management Plan 生产管制计划SIP Standard Inspection Procedure 制程检验标准程序SOP Standard Operation Procedure 制造作业规范IS Inspection Specification 成品检验规范BOM Bill Of Material 物料清单PS Package Specification 包装规范SPEC Specification 规格DWG Drawing 图面系统文件类ES Engineering Standard 工程标准IWS International Workman Standard 工艺标准ISO International Standardization Organization 国际标准化组织GS General Specification 一般规格部类PMC Production & Material Control 生产和物料控制PCC Product control center 生产管制中心PPC Production Plan Control 生产计划控制MC Material Control 物料控制DCC Document Control Center 资料控制中心QE Quality Engineering 品质工程(部)QA Quality Assurance 品质保证处QC Quality Control 品质管制(课)PD Product Department 生产部LAB Laboratory 实验室IE Industrial Engineering 工业工程R&D Research & Design 设计开发部。
质量管理体系术语中英文对照
质量管理体系术语中英文对照以下是部分质量管理体系相关的基本术语中英文对照:1.质量管理体系(Quality Management System, QMS)o中文:质量管理体o英文:Quality Management System2.质量管理(Quality Control, QC)o中文:质量管理o英文:Quality Control3.持续改进(Continuous Improvement, CI)o中文:持续改进o英文:Continuous Improvement4.过程方法(Process Approach)o中文:过程方法o英文:Process Approach5.质量方针(Quality Policy)o中文:质量方针o英文:Quality Policy6.质量目标(Quality Objectives)o中文:质量目标o英文:Quality Objectives7.内部审核(Internal Audit)o中文:内部审核o英文:Internal Audit8.纠正措施(Corrective Action)o中文:纠正措施o英文:Corrective Action9.预防措施(Preventive Action)o中文:预防措施o英文:Preventive Action10.顾客满意度(Customer Satisfaction)o中文:顾客满意度o英文:Customer Satisfaction11.供方管理(Supplier Management)o中文:供应商管理o英文:Supplier Management12.产品实现(Product Realization)o中文:产品实现o英文:Product Realization13.设计和开发(Design and Development)o中文:设计与开发o英文:Design and Development14.测量、分析和改进(Measurement, Analysis andImprovement)o中文:测量、分析与改进o英文:Measurement, Analysis and Improvement 以上内容主要参考了ISO 9001:2015质量管理体系标准中的核心概念。
供应链管理毕业论文文献翻译中英文对照
供应链管理毕业论文文献翻译中英文对照附件1:外文资料翻译译文供应链管理ABC1.什么是供应链管理供应链是一种关于整合的科学和艺术,它主要探究提高企业采购生产商品所需的原材料、生产商品,并把它供应给最终顾客的效率的途径。
以下是供应链管理的五个基本组成模块:计划--它是供应链的战略层面。
企业需要有一个控制所有资源的战略以满足客户对产品或服务的需求。
计划的核心是建立一套机制去监控整条供应链以便使它能有效运作:低成本、高品质配送和增值客户服务。
该模块连结着供应链的作业与营运目标,主要包括需求/供给规划(Demand/Supply Planning)与规划基础建设(infrastructure)两项活动,对所有采购运筹流程、制造运筹流程与配送运筹流程进行规划与控制。
需求/供给规划活动包含了评估企业整体产能与资源、总体需求规划以及针对产品与配销管道,进行存货规划、配送规划、制造规划、物料及产能的规划。
规划基础建设管理包含了自制或外包决策的制定、供应链的架构设计、长期产能与资源规划、企业规划、产品生命周期的决定、新旧产品线规划与产品线的管理等。
采购—选择供给你提供用来生产产品或服务的原材料或服务的供应商。
和供应商建立一套价格、供应、支付过程的体系,创造一种机制以监控此过程、改善供应商关系。
理顺此过程以管理供应商交付的原材料库存或服务,其中包括收货、出货、检验、中转和批准支付。
此模块有采购作业与采购基础建设两项管理活动,其目的是描述一般的采购作业与采购管理流程。
采购作业包含了寻找供货商、收料、进料品检、拒收与发料作业。
采购基础建设的管理包含了供货商评估、采购、运输管理、采购品质管理、采购合约管理、付款条件管理、采购零组件的规格制定。
制造—这是制造步骤。
计划这些必需的活动:生产、测试、包装、预出货。
作为供应链的核心机制,它意味着质量水平、产品输出和工厂产能的有效控制。
此模块具有制造执行作业与制造基础建设两项管理活动,其目的是描述制造生产作业与生产的管理流程。
- 1、下载文档前请自行甄别文档内容的完整性,平台不提供额外的编辑、内容补充、找答案等附加服务。
- 2、"仅部分预览"的文档,不可在线预览部分如存在完整性等问题,可反馈申请退款(可完整预览的文档不适用该条件!)。
- 3、如文档侵犯您的权益,请联系客服反馈,我们会尽快为您处理(人工客服工作时间:9:00-18:30)。
互利共赢的供应商质量控制前言近年来,随着对供应链的重视,供应商管理正逐渐成为企业和学术界的关注对象,IS09000族标准以及QS 9000标准都对供应商的管理提出了相应的要求,与供应商管理有关的研究成果正逐渐增多,一些软件巨头也推出了供应商关系管理的软件,但是在这些研究成果和应用软件中,涉及到的供应商质量控制的内容只是一些最基本的要求,而供应商质量控制恰恰是供应商管理的最基本、最重要的内容。
另一方而,质量管理界对质量控制的研究取得了大量的成果,遗憾的是这些成果大多依然局限于企业的内部控制,仅仅研究从企业内部各环节如何改善产品的质量,而基于供应链的角度来研究质量控制的成果尚不多见。
因此,系统地研究经济全球化形势下供应商质量控制的理论与方法,将有助于推动我国企业产品质量的快速提高和供应链竞争优势的形成与巩固。
1、质量与企业共存质量一直是一个随着时代的变化而不断变化的概念,人们对质量的认识也往往因关注点不同而有所不同。
如,早在1908年,通用汽车公司的工程师们在皇家汽车俱乐部会员们的面前拆解了3辆凯迪拉克轿车,并把这些零件混在一起,而后从中选择零件重新组装成车,然后驾车绝尘而去。
这令在场的会员极为震惊,认为凯迪拉克车质量之高令人惊叹。
显然在当时,汽车零件具有互换性是一种了不起的质量特性,这也是福特公司的N型车和T型车取得辉煌成功的重要原因.时至今日,即使农用三轮车的零部件也具有极高的互换性,零部件的标准化和互换性已经是理所当然的事情,不再是吸引顾客的重要质量特性.可见质量的内涵是不断变化的.那么究竟什么是质量呢?(1)市场竟争就是企业间对“顾客”的争夺,在日益激烈的“顾客"争夺战中,质量、价格、交付(交付日期、方式和手段)和服务是企业常用的四个法宝,其中质量是根本,离开质量其他三项将变得毫无意义,因此可以说质量己成为市场竞争的焦点.它反映了产品是否能够反映顾客需求、能否满足顾客需求,从面决定了产品的市场前途。
有鉴于此,质量己成为一项全球性运动,世界上所有优秀企业无一不把质量作为企业战略的关键内容,从战略的角度来规划质量。
(2)对于企业经营者来说,认识到质量对企业的重要意义只是经营企业的第一步,重要的是如何利用科学的方法来保证产品和服务的质量,使顾客满意,来保证过程和工作的质量来获互利共炭的供应商质量控制得良好的业绩。
众所周知,企业管理是社会生产力发展到一定程度的历史产物,质量管理作为企业管理的组成部分,同样也是社会发展的客观要求,特别是顾客处于主导地位的今天,要使顾客满意,就必须有过硬的产品质量和服务质量,这就要求企业积极推行先进的质量管理理论与方法,不断进行质量管理创新.2、企业与供应商质量控制随着生产社会化的不断发展,企业的生产活动分工越来越细,专业化程度越来越强,促使生产技术水平越来越高,产品质量得到大幅度改善。
通常,某一产品不可能由一个企业从最初的原材料开始加工直至形成顾客最终使用的产品,往往是通过多个企业分工协作来完成.另外,先进生产方式的广泛应用,如准时生产、敏捷制造、零库存等,使企业与供应商的关系愈加紧密,企业与供应商的关系也由单纯的买卖关系向互利共底的合作关系演变。
ISO 9000族标准自1987年诞生以来受到了世界各国的一致追捧,全球约50多万家企业通过ISO9001质量管理体系认证足以说明这套管理标准在引领国际管理潮流方面的巨大成功。
在备受企业欢迎的新版标准ISO9000:2000中,互利的供应商关系被作为八项质量管理原则之一,充分体现了供应商关系管理在企业经营实践中的作用和价值。
企业要贯彻这一原则,就必须从思想上认识到供应商的重要性,重视与供应商良好关系的培育,并采取有力措施与之建立一种互利共赢的合作性关系。
3、供应商选择选择合适的供应商是对供应商进行质量控制最有效手段,如果供应商选择不当,无论后续的控制方法多么先进、控制手段多么严格,都只能起到事倍功半的效果。
因此要对供应商进行质量控制首先必须科学合理地选择供应商。
(1)企业在生产经营过程中,所需要的原材料和零部件不可能都由自己生产提供,决定其中哪些应由供应商提供不是一个简单的买不买的问题,因为这涉及企业的业务流程,甚至涉及到企业与供应商之间的业务流程再造,属于企业战略层次的问题。
因而对零部件的自产和外购的选择必须综合考虑企业的经营环境、企业自身实际情况以及供应商的总体情况.1)经营环境分析企业对于零部件自产还是外购的决策需要建立在对其经营环境的准确分析和把握的基础之上。
企业所在行业的整体状况与发展态势、国家宏观经济形势、企业产品的社会需求现状及未来预侧等因素都会影响到企业产品的产销量。
而预期的企业产销量是企业进行各项决策如互利共赢的供应商质量控制投资规模、设备配置的主要依据,也是企业零部件自产与外购决策的重要依据.另外,竞争对手的零部件自产与外购情况也是企业进行决策的重要参考依据。
2)市场供应情况零部件的社会供应状况也是企业决定自产还是外购的重要依据。
企业与其供应商的关系的实质就是相互依存的关系,正如一家势力雄厚、规模巨大的企业会吸引很多供应商在其周围投资设厂一样,具有完善配套供应商的区域也常常吸引大的企业甚至跨国公司前来投资办厂.某种零部件的社会供应能力、价格、质量和服务水平在很大程度上影响着企业的自产与外购决策。
因此,企业应全面了解其产品中零部件的社会供应情况,注意从互联网上、展览会、供应商来信等渠道收集供应商的企业介绍、产品样本、获奖证书、代理商授权书、营业执照、产品实物质量水平以及市场行情等方面的信息.然后,按照供应商提供物资种类,可分别建立原材料、零部件、包装材料等不同类别的潜在供应商档案。
(2)供应商的检测设备是供应商赖以测量、分析和改进的基础条件.如果供应商不具备必要的检测手段,就无法提供真实准确的质量数据,供应商的质量控制就如空中楼阁。
所以,在初选供应商时,了解供应商的检测设备的配备情况和先进程度同样是十分必要的。
(3)过程能力指数和过程性能指数是反映供应商生产过程质量保证能力的两个重要参数.过程能力指数反映供应商短期的过程能力满足公差要求的程度。
过程性能指数反映供应商长期的过程能力满足公差要求的程度。
供应商是否进行过程能力指数和过程性能指数的计算分析,可以在一定程度上反映其是否在生产过程中进行了预防控制。
过程能力指数和过程性能指数的变化则可以反映供应商的质量保证能力和质量改进潜力的大小,在很大程度上反映供应商的实力和管理水平.因此,调查供应商的过程能力指数和过程性能指数是选择供应商的重要依据。
4、供应商的质量控制质量管理的一项重要原则是“过程方法”,企业为了有效运作,必须识别并管理许多相互关联的过程,特别是这些过程之间的相互作用。
供应商是过程管理的源头之一,是过程输入的重要因素,因而,供应商提供的产品质量如何,对于企业的过程质量、体系质量和产品质量具有举足轻重的作用。
(1)产品开发设计阶段,根据不同产品的不同要求,在产品开发设计建议书或产品设计开发任务书中提出先行试验项目和课题,有针对性地为采用新原理、新结构、新材料、新工艺,进行先行试验,为了确保试验的效果和以后批量生产的需要,这一阶段的一项重要工作就是对供应商进行初步控制,确保在新产品设计的各个阶段以及批量生产时,都能够有适合新产品或新服务需要的合格供应商.(2)企业在批量生产过程中,对供应商的质量控制主要包括监控供应商的过程能力指数和过程性能指数、监控供应商的测量系统、审核供应商的质量管理体系、进货质量检验、推动供应商的质量改进、以及来自供应商的不合格品的处置和质量问题的解决等活动。
1)批量生产阶段,供应商提供的产品或服务的质量直接决定了企业向顾客提供的产品或服务的质量特性,企业在供应商合作的过程中,应监控供应商的质量保证能力的变化,为了使监控有效,企业应就此与供应商达成一致,并遵循协商一致的标准和程序进行。
监控的目的一般有两个,一是防止供应商的质量保证能力出现下降的情况,确保最终产品或服务的质量,实现顾客满意;二是与供应商共同发现改进的机会,寻找改进的切人点,在更高层次上创造价值.由于在批量生产阶段供应商大批量连续供货,采购产品的质量、价格、供货的及时性等对企业产品的质量和企业实现其经营方针、目标都有十分重要的作用,为了更加科学地评价和选择供应商,这一阶段的供应商评价应尽量采用定量分析的方法。
根据产品和服务的不同,定量分折的方法也不同,以下简单介绍常用的过程能力分析、测量系统分析、质量管理体系评价、水平对比法和优秀模式等方法。
①供应商过程能力分析过程能力是指过程加工质量方面的能力,而不是加工数量方面的能力。
在批量生产阶段,为了保证批量生产的产品满足顾客的需求和期望,供应商生产过程的稳定性就十分重要了,决定供应商是否有能力稳定地连续提供符合质量要求的产品的众多因素中,供应商的过程能力是一个决定性的因素。
因为当供应商的过程能力不足时,供应商提供合格产品只是个良好的愿望,即便是加大检验力度,也只能是在短期内有效,难以持续.所以,对过程能力不足,短期改进无望的供应商,应该停止合作。
②供应商测量系统分析企业对供应商的质量控制,包括对供应商的选择、评价和控制,都离不开数据和对数据的分析,缺少足够的数据,仅仅靠经验和直觉对供应商进行选择和评价,其风险是不言而喻的。
对供应商的评价和控制所使用的数据大多是由测量提供的,如果测量数据失真或误差很大,都会导致采购行为的缺陷或失败。
因此,在批量生产阶段,为了确保采购的质量,应该对供应商的测量系统进行监控。
2)与供应商的沟通与供应商沟通的方式是多种多样的,但是这些方式的目的是一致的,企业和供应商共同关注顾客,建立企业和供应商共同满意的融洽的合作伙伴关系,共同对产品和服务进行持续的改进,以便及时、有效地适应市场的变化.满足顾客的需求和期望,实现企业和供应商共同的价值,共同追求并实现卓越。
(3)不合格品的判定、分析和处置虽然有了以上各种控制措施,但是不合格品的出现仍然是正常现象,除单件或少数几件产品、安全性要求较高的产品等少数产品以外,在许多情况下不合格品的出现是难以完全避免的。
这时候就要根据不合格的性质、对最终产品的影响程度、供应商的信誉等因素对不合格品进行必要的评审,然后采取适当的措施处置不合格品,以防止不合格品的非预期使用或交付当出现不合格品以后,要分析产生不合格的囚素,采取纠正和预防措施。
防止不合格的再次发生。
对由于异常因素发生的不合格品,供应商要采取相应的措施,消除这些异常因素。
1)一致的技术标准和抽样方案使用、提出和制定规格的部门必须合理地描述出拟采购的产品是什么,以便使供应商得到准确的理解,使采购人员能够准确地采购所需的产品。
根据ISO 9001:2000标准的要求和企业的实际情况,这些技术标准一般是由设计、采购、管理、生产等部门制定,但在采购的实施时,采购部门要使用这些标准,因此.采购部门从一开始就应该介入这些标准的策划、起草和修订,否则,一旦这此标准止式发布实施,可能会使采购部门处于被动的地位,给采购工作带来麻烦。