铝合金车体焊接 (5)
浅谈铝合金车体探伤焊缝的焊接

1、枕梁盖板焊缝的焊接
枕梁盖板焊缝结构一般未板材与型材进行连接,对接破口角度一般为70°,具体焊缝形式间下图:
浅谈铝合金车体探伤焊缝的焊接
摘要:主要论述了MIG焊焊接中出现的常见焊接缺陷的类型,总结了由于铝合金特殊的金属特性和焊接规范、焊接方法使用不当等引起焊接缺陷的原因,并针对铝合金车体探伤焊缝的焊接方法及注意事项进行阐述。
关键词:铝合金焊接焊接缺陷探伤焊缝
引言
焊接技术是一门重要的金属加工技术,尽管焊接技术发展很快,自动化程度也越来越高,但手工电弧焊仍占有不可替代的地位。在铝合金车体生产过程中,重要连接焊缝需要进行射线探伤(RT)。优质的焊缝表面应圆滑过渡至母材,表面不得有裂纹、未熔合、夹渣、气孔、焊瘤、咬边等缺陷,焊缝内部同样不允许有缺陷。但焊接过程中由于设备、材料、工艺及操作等原因,使得形成的焊缝达不到质量要求,从而对结构的工作质量和使用寿命产生严重的影响。
3、未熔合焊接时,焊道与母材之间或焊道与焊道之间未能完全熔化结合的部分称为未熔合。焊接区表面有氧化膜,焊接的时候热输入量不足未能将其打破,容易引起未熔合现象;焊接接头处接头打磨的夹角不够大,焊丝伸出长度太大也引起接头处未熔合。
4、咬边由于焊接参数选择不当,或操作技术不正确,沿焊趾的母材部位生沟槽或凹陷称为咬边。根据ISO10042标准规定,咬边长缺陷(100mm内长度>25mm的一个或多个缺陷)的深度不能>0.2mm,短缺陷(100mm风长度<25mm的一个或多个缺陷)的深度不能>0.5mm。产生咬边的原因主要是焊接规范参数过大,热输入量过大,速度过快,焊丝还来不及将弧坑填充满应离开熔池,便会出现咬Biblioteka ;咬边是铝合金焊接中比较常见的缺陷。
轨道车辆铝合金车体焊接工艺研究

轨道车辆铝合金车体焊接工艺研究摘要:轨道车辆车体采用铝合金进行焊接制造,在车体制造技术条件中要求极为严格,铝合金熔点低、导热系数及热膨胀系数较大,在焊接过程中需要进行大电流快速焊接的特点,加大了难度;通过在车体生产制造过程中不断探索、改进,逐步提高铝合金车体制造技术;减少焊接中出现的缺陷,从而提高焊接质量和工作效率。
关键词:轨道车辆;铝合金车体;焊接工艺;一般情况下,轨道车辆铝合金车体大部件采用挤压铝型材料焊接而成,由于焊缝都是规则的、纵向的、平直的,所以能够自动焊接。
不过铝合金的导热性较大,高出钢材的四倍,膨胀系数也刚出钢材的一倍,所以铝合金车体焊接时,有很大的变形,且这种变形不好控制。
一、轨道车辆铝合金车体焊接工艺研究1.工艺要求。
一是焊接方法的选择。
铝合金的焊接方法有很多种,铝合金车体焊共采用了熔化极惰性气体的保护焊(MIG)、钨极惰性气体的保护焊(TIG)和电阻点焊三种焊接方法。
二是焊接速度的选择。
在焊接时候,对于厚板的焊缝,为了能够保证焊接的质量在焊接的过程中使焊缝充分的融合,并且使焊缝内的气体充分的溢出,在进行焊接的过程中一般采用较慢的焊接速度和较大的电流进行焊接,对于薄板焊缝,为了避免焊缝过热,在焊接的过程中一般采用较快的焊接速度和较小的焊接电流,从而保证焊接的质量。
2.铝合金车体焊接工艺。
根据铝合金焊接技术的经验总结及铝合金车体焊接变形规律,对车体总组装焊接制定了焊接工艺流程:车体预组→焊前尺寸调整→焊前清理→自动焊接→焊后打磨。
通过上述的焊接工艺流程可以看出,要控制铝合金车体焊接质量及整体几何尺寸满足技术要求,减小车体的焊后调修量;必须加强过程控制,通过在预组及焊前尺寸调整过程中对铝合金车体几何尺寸进行预变形控制,减小车体焊接变形,提高焊接质量。
一是车体焊接几何尺寸控制。
铝合金车体焊接过程中,由于焊缝的中心线与结构截面的中性轴(通过重心的轴)不重合或不对称,导致了车体焊接完成后侧墙发生弯曲变形。
地铁铝合金车体焊接工艺
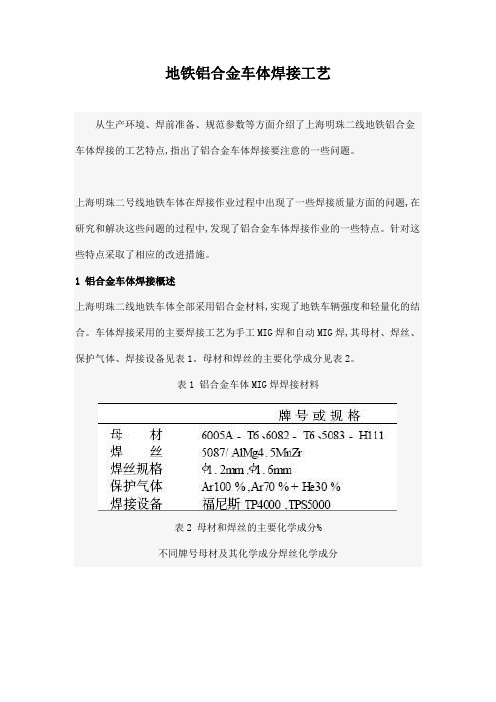
地铁铝合金车体焊接工艺从生产环境、焊前准备、规范参数等方面介绍了上海明珠二线地铁铝合金车体焊接的工艺特点,指出了铝合金车体焊接要注意的一些问题。
上海明珠二号线地铁车体在焊接作业过程中出现了一些焊接质量方面的问题,在研究和解决这些问题的过程中,发现了铝合金车体焊接作业的一些特点。
针对这些特点采取了相应的改进措施。
1 铝合金车体焊接概述上海明珠二线地铁车体全部采用铝合金材料,实现了地铁车辆强度和轻量化的结合。
车体焊接采用的主要焊接工艺为手工MIG焊和自动MIG焊,其母材、焊丝、保护气体、焊接设备见表1。
母材和焊丝的主要化学成分见表2。
表1 铝合金车体MIG焊焊接材料表2 母材和焊丝的主要化学成分%不同牌号母材及其化学成分焊丝化学成分2 生产储存环境和辅助材料使用的要求2. 1 生产储存温度湿度的要求铝合金的生产和储存环境必须防尘、防水、干燥。
环境温度通常控制在5 ℃以上, 湿度控制在70 %以下。
应尽量保证焊接环境的湿度不能太高,湿度过高会使焊缝中气孔的产生几率明显增加,从而影响焊接质量。
空气的剧烈流动会引起气体保护不充分,从而产生焊接气孔,可设置挡风板以避免室内穿堂风的影响。
2. 2 焊丝及送气软管的使用要求对焊材的使用应该注意:铝焊丝要与钢焊材分开储存,使用期不超过1a 。
焊接完成后,要在焊机中取出焊丝进行密封处理,防止污染。
不同材质的送气软管抵抗湿气进入的能力不同,尤其在送气压力高时,送气软管的影响更明显。
送气软管最好使用特富龙软管(Teflon) 。
2. 3 工装的选用铝合金焊接最好选用点接触形式的工装,以减小工装与工件的接触面积。
如果工装对工件是面接触,就会很快带走工件的热量,加速了熔池的凝固,不利于焊缝气孔的排除。
工装液压系统的压力最好控制在9~9. 5 MPa 。
压力过小达不到预设反变形的目的,但是压力过大,又会使铝合金结构的拘束度增大。
由于铝合金的线胀系数大,高温塑性差,焊接时易产生较大的热应力,可能会使铝合金结构产生裂纹。
高速动车组用铝合金特种焊接技术
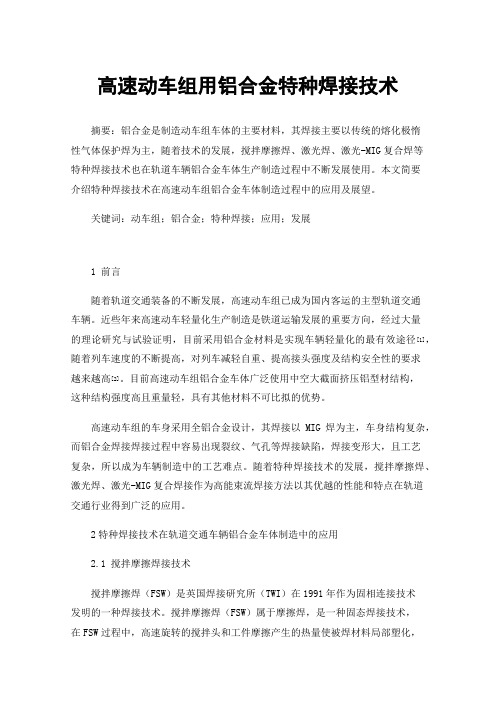
高速动车组用铝合金特种焊接技术摘要:铝合金是制造动车组车体的主要材料,其焊接主要以传统的熔化极惰性气体保护焊为主,随着技术的发展,搅拌摩擦焊、激光焊、激光-MIG复合焊等特种焊接技术也在轨道车辆铝合金车体生产制造过程中不断发展使用。
本文简要介绍特种焊接技术在高速动车组铝合金车体制造过程中的应用及展望。
关键词:动车组;铝合金;特种焊接;应用;发展1 前言随着轨道交通装备的不断发展,高速动车组已成为国内客运的主型轨道交通车辆。
近些年来高速动车轻量化生产制造是铁道运输发展的重要方向,经过大量的理论研究与试验证明,目前采用铝合金材料是实现车辆轻量化的最有效途径[1],随着列车速度的不断提高,对列车减轻自重、提高接头强度及结构安全性的要求越来越高[2]。
目前高速动车组铝合金车体广泛使用中空大截面挤压铝型材结构,这种结构强度高且重量轻,具有其他材料不可比拟的优势。
高速动车组的车身采用全铝合金设计,其焊接以MIG焊为主,车身结构复杂,而铝合金焊接焊接过程中容易出现裂纹、气孔等焊接缺陷,焊接变形大,且工艺复杂,所以成为车辆制造中的工艺难点。
随着特种焊接技术的发展,搅拌摩擦焊、激光焊、激光-MIG复合焊接作为高能束流焊接方法以其优越的性能和特点在轨道交通行业得到广泛的应用。
2特种焊接技术在轨道交通车辆铝合金车体制造中的应用2.1 搅拌摩擦焊接技术搅拌摩擦焊(FSW)是英国焊接研究所(TWI)在1991年作为固相连接技术发明的一种焊接技术。
搅拌摩擦焊(FSW)属于摩擦焊,是一种固态焊接技术,在FSW过程中,高速旋转的搅拌头和工件摩擦产生的热量使被焊材料局部塑化,在旋转搅拌头的临近区域内,形成了一层充分的塑化金属层,当搅拌头沿着焊接界面移动时,塑化材料在搅拌头的转动摩擦力作用下由搅拌头的前部移向后部,搅拌头的前段不断形成热塑性金属并出现金属的挤压流动现象,进而填补搅拌头后部的空腔,并在搅拌头的挤压下形成致密的固相焊缝。
轨道交通车体用铝合金材料及其焊接技术
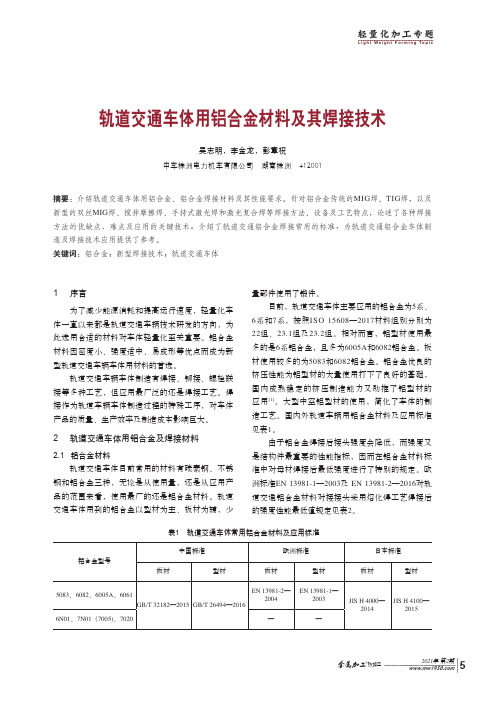
1 序言为了减少能源消耗和提高运行速度,轻量化车体一直以来都是轨道交通车辆技术研发的方向,为此选用合适的材料对车体轻量化至关重要。
铝合金材料因密度小、强度适中、易成形等优点而成为新型轨道交通车辆车体用材料的首选。
轨道交通车辆车体制造有焊接、铆接、螺栓联接等多种工艺,但应用最广泛的还是焊接工艺。
焊接作为轨道车辆车体制造过程的特殊工序,对车体产品的质量、生产效率及制造成本影响巨大。
2 轨道交通车体用铝合金及焊接材料2.1 铝合金材料轨道交通车体目前常用的材料有碳素钢、不锈钢和铝合金三种,无论是从使用量,还是从应用产品的范围来看,使用最广的还是铝合金材料。
轨道交通车体用到的铝合金以型材为主、板材为辅,少量部件使用了锻件。
目前,轨道交通车体主要应用的铝合金为5系、6系和7系,按照ISO 15608—2017材料组别分别为22组、23.1组及23.2组。
相对而言,铝型材使用最多的是6系铝合金,且多为6005A和6082铝合金。
板材使用较多的为5083和6082铝合金。
铝合金优良的挤压性能为铝型材的大量使用打下了良好的基础,国内成熟稳定的挤压制造能力又助推了铝型材的应用[1]。
大型中空铝型材的使用,简化了车体的制造工艺。
国内外轨道车辆用铝合金材料及应用标准见表1。
由于铝合金焊接后接头强度会降低,而强度又是结构件最重要的性能指标,因而在铝合金材料标准中对母材焊接后最低强度进行了特别的规定。
欧洲标准EN 13981-1—2003及 EN 13981-2—2016对轨道交通铝合金材料对接接头采用熔化焊工艺焊接后的强度性能最低值规定见表2。
轨道交通车体用铝合金材料及其焊接技术吴志明,李金龙,彭章祝中车株洲电力机车有限公司 湖南株洲 412001摘要:介绍轨道交通车体用铝合金、铝合金焊接材料及其性能要求。
针对铝合金传统的MIG焊、TIG焊,以及新型的双丝MIG焊、搅拌摩擦焊、手持式激光焊和激光复合焊等焊接方法、设备及工艺特点,论述了各种焊接方法的优缺点、难点及应用的关键技术。
铝合金车体焊接垫板焊缝裂纹分析与解决

铝合金车体焊接垫板焊缝裂纹分析与解决发布时间:2023-01-17T02:05:46.568Z 来源:《中国科技信息》2022年18期作者:李光辉钱瑶[导读] 铝合金车体在各城市地铁项目中运用广泛李光辉钱瑶(中车南京浦镇车辆有限公司,江苏南京)摘要:铝合金车体在各城市地铁项目中运用广泛,焊接垫板作为车体焊接过程中的辅助工艺材料,对焊缝背透成形及充分焊透起到关键作用,焊接垫板焊缝存在缺陷,将对结构焊缝质量及车体强度产生较大影响,本文以某城市地铁项目焊接垫板焊缝裂纹问题为案例,对其相关结构及受力情况进行分析计算,结合铝合金车体结构特点制定了相关解决措施,并提供了优化方案。
关键词:铝合金车体;焊接垫板;裂纹焊接垫板作为焊接工艺中常见的辅助材料,其主要作用是确保焊缝熔透及背透成形,有利于提高产品的焊接质量。
当产品焊缝难以双面施焊时可设置垫板进行单面焊,或板厚虽薄但对于焊缝需求较高时也可设置垫板。
焊接垫板分为可移除垫板及永久垫板两种形式,可移除垫板顾名思义即在正式焊缝焊接完成后去除。
永久垫板一般分为两种结构,一种是采用型材自带结构,在铝合金型材生产时一体挤压形成焊接垫板槽,另一种是采用同等材质的板材,通过点固焊接的方式与焊缝区域母材固定。
焊接垫板的点固规范质量直接决定着垫板的安装质量,影响主结构焊缝的焊接质量,因此应对焊接垫板点固焊缝提高重视。
1.铝合金车体焊接垫板焊缝开裂问题某城市地铁车辆在日常运用检查中发现TC车一位端牵枕缓连接座区域焊接垫板端部点固焊缝存在裂纹,裂纹长度约10mm。
现车问题照片(图1)及三维模型(图2)示意如下:图1 焊接垫板焊缝开裂照片图2 缺陷位置示意图2.原因分析通过现车实物及对应位置关系,可以分析出异常开裂为焊接垫板与腹板永久定位焊缝。
图纸要求该处主结构连接座焊缝为12mmHV加永久性垫板T型接头。
该处增加焊接垫板的主要作用为便于正面焊缝彻底焊透形成良好的背透焊缝,垫板上的段焊缝为焊接垫板的组装定位焊缝(开裂焊缝)。
铝合金车体长直焊缝的焊接缺陷及防止措施

在 车体 侧 墙 与边 梁 的 长 直焊 缝 中 , 气孔 是 出现 最多 的一 种缺 陷 。气孔 的存在 不但 会 降低 焊缝 的致 密性 , 减少 接头 承 载 面积 , 而且 使 接 头 强 度 、 塑性 降 低 , 别是 冷弯 和 冲击韧 性 , 孔必 须加 以 防止 。 特 气 在焊 接 工艺 评 定 时 , 过 长直 焊 缝 的金 相 对 比 通 可 以发现气 孔 主要存 在 焊缝 的上部 。通过 R T检 验
接 缺 陷及 防止 措 施 进 行 了分 析研 究 。
关 键 词 : 合 金 焊 接 ;长 直 焊缝 ; 接 缺 陷 ;防 止措 施 铝 焊
中图 分 类 号 :T 4 1 7 G 4 . 文 献 标 识 码 : B
1 铝 合金 车体 长 直 焊 缝 特 点
铝 合 金 车体 侧墙 与 底 架边 梁 的长直 焊 缝 , 在 是 铝合金 车体 总装工 序 中完成 的 。此 焊缝 位于 车体 两
采用横 焊姿 势 自动 MI G焊接 而成 , 内侧则 采用 手 工
M G焊 5 ( 5 段 焊 , 头 形 式 见 图 2 焊 接 参 数 见 I 07 ) 接 ,
表 1 。
表 l 铝合 金 车 体 侧 墙 与 底 架 边 梁 长 直焊 缝 的焊 接 参 数
也能 够看 出长 直焊缝 的气 孔 。
摘 要 : 合 金 车 体侧 墙 与 底 架 边 梁 长 直 焊 缝 在 车 体 焊 缝 组 成 中 尤 为 重 要 , 处 的 焊 缝 采 取 横 焊 铝 此
姿 势 , 易产 生 焊 接 缺 陷 , 因 大部 件 侧 墙 采 用 大 型 中空 挤 压 型 材 , 强 行 拉 出挠 度 , 接 后 还 要 极 又 需 焊 再 进 行 门框 组 装 , 此很 难 达到 理 想状 态 , 成 侧 墙 与 底 架 组 装 时焊 缝 的 根 部 间 隙 极 不 均 匀 , 对 因 造 更 焊 接 造 成 了相 3大 的 困难 。 本 文 结 合 铝 合 金 车 体 焊 接 试 验 及 现 车 生 产 中 实 际 经 验 对 此 焊 缝 的 焊 - '
高速列车铝合金车体焊接工艺浅析

《装备制造技术》2013年第1期大型铝合金挤压型材以其在减重性[1]、耐蚀性、加工性等方面具有其它材料无法比拟的优点,在高速列车车体上得到广泛应用[2]。
由于我国早期普通列车车体制造不采用此种材料,国内对高速列车用铝合金材料焊接性和工艺缺乏相应的研究。
随着近年来高速铁路行业的快速发展,轨道车辆用铝合金的焊接成为新的研究热点[3 ̄5]。
铝合金的热导率大和线膨胀系数较大的特点决定了焊接时易产生焊接变形,同时,铝合金焊接也极易产生气孔、裂纹等焊接缺陷。
高速动车组制造的关键材料,铝合金焊接品质是决定高速列车长期安全运行的基础,对于提高高速列车的运行寿命具有重要意义[6]。
1焊前清理铝合金工件及焊丝表面的水分和油污等,在焊接过程中向焊缝金属提供溶解氢,是焊缝产生气孔的重要原因之一。
氧化膜的存在很容易在焊缝进行中形成夹渣。
因此,焊前须用丙酮对工件表面、坡口及其附近20 ̄30mm范围进行严格的清理,去除油污和水分等杂质,用钢丝轮打磨以去除表面氧化膜、露出金属光泽。
2焊接位置在铝合金焊接时,金属液体粘度较大,熔池中的气体不易逸出而易形成气孔。
因此,铝合金焊接时应尽量采取使气体能够较容易逸出的平焊位置。
另外,平焊位置易于操作,对焊工技能的要求较低。
非平焊位置应通过焊接工装转化为平焊位置。
在高速列车制造过程中,设计的具有旋转功能的工装可以实现这一目的。
这种可以实现焊接变位的工装应用非常广泛,例如牵引梁旋转焊接工装可以使侧翼补强板的横焊位置转化为平焊位置,折弯处焊缝可以转化为方便焊接的横焊位置。
枕梁回转内部焊缝焊接工装可以非常方便地将其它焊接位置转化为平焊位置。
另外在端中梁焊接工装、减震器座焊接工装也具有此作用。
3焊接变形的控制在铝合金焊接中,必须采用大的热输入量,焊接结构很容易发生变形,必须采取必要措施对焊接变形加以控制,这是列车车体制造过程中非常重要的一个方面。
在车体制造过程中,对焊接变形的控制方法主要有以下几个方面:3.1工艺撑控制焊接变形此方法使用非常普遍,车体许多部件的生产中都采用的此方法。
- 1、下载文档前请自行甄别文档内容的完整性,平台不提供额外的编辑、内容补充、找答案等附加服务。
- 2、"仅部分预览"的文档,不可在线预览部分如存在完整性等问题,可反馈申请退款(可完整预览的文档不适用该条件!)。
- 3、如文档侵犯您的权益,请联系客服反馈,我们会尽快为您处理(人工客服工作时间:9:00-18:30)。
第六章铝及铝合金加热处理工艺
第一节焊前预热
由于铝合金的导热率高,当环境温度较低或材料厚度较大时,为保证焊接质量,一般焊接之前要对焊接区域进行预热,常用的预热方法采用火焰加热。
通常预热到90℃即足以保证开始焊接处有足够的熔深,因而不必要在起弧后重新调节电流。
一般铝合金预热温度很少超过150℃,因为在较高温度下某些铝合金的性能和热处理状态会受到不利的影响。
含4.0%-5.5%镁的铝镁合金(5083、5086和5756)的预热温度一般不应超过90℃,否则会降低其抗应力腐蚀开裂的性能。
对于可热处理的合金,预热温度高会扩大软化区范围。
使用AlZnMg合金,预热要尽快横跨200 °C –300 °C的危险温度范围!在此区间预热时间越长,强度损失越大。
温度保持时间太长会导致粗晶结构,造成晶间腐蚀抗力下降,因此不要输入太多的热量。
晶界对金属晶间滑移起自然阻碍作用,如果金属变的很热,那么结晶粒度就会变大,晶粒间的表面变小,滑面移动障碍物缺乏,金属就会失去它的强度。
预热时间和预热温度对强度影响如下:
一、预热时间
预热对不同的铝合金影响有很大的差异,对时效硬化铝合金,预热过大会使强度明显下降,有些铝合金强度下降后,自恢复能力很强,如AlZnMg合金在加热强度损失后,能够在30天左右很快恢复到基体强度,但有些铝合金,强度下降后不可恢复。
预热时间对铝合金强度的影响也很大,预热时间越长,越容易造成下降的强度不可恢复,因此,生产中,要严格控制预热时间,一般采用快速加热的热源来避免预热时间过长,在加热温度不变的前提下,预热时间对AlZnMg合金强度影响如下:
预热2 min,再冷却到室温的强度值为350 MPa
预热6 min,再冷却到室温的强度值为320 MPa
预热10 min,再冷却到室温的强度值为280 MPa
二、预热温度
对于AlZnMg合金,当材料加热到150 °C时,材料强度变为室温强度的80%,当加热到200°C时,材料强度是室温强度的60% ,当加热到400 °C时,材料强度只为室温强度的10%。
因此,不能过分预热金属。
材料加热温度的控制主要采用测温笔和点式温度测量计,测温笔
有各种温度范围,根据加热范围取不同型号,在使用时,当材料加热到合适温度,用笔往工件上画痕迹,如果痕迹迅速融化,表明工件已经达到了预定加热温度,如果温度没到,笔是坚硬的,在工件表面不留任何痕迹,预热温度对材料强度的影响见图6-1。
图6-1 预热温度对材料抗拉强度影响
预热温度要严格控制,一般用点式测温计测量。
当用点式测温计时,仪器反应需要一定时间,待温度稳定后再读取数值,用点式温度计时,要注意测量时间和加热撤离时间间隔。
预热要确保不会由于预热时间过长或可燃气体中含有过量氧气,而导致焊边上的氧化物层越积越厚,表6-1是推荐值。
表6-1 铝合金预热温度和时间指导值
将用于钢材预热的焊炬类型用于铝合金材料预热,要使用次一号的焊炬规格,表6-2说明了焊炬和预热厚度的关系。
表6-2 焊炬和预热厚度关系表
图6-2 示意了加热焊矩和加热的方式。
焊炬加热要采用中性火焰,过多的氧气会使铝合金表面氧化膜变厚,加热火焰要采用集中性火苗,过于分散会使加热时间变长。
图6-2 焊矩和加热方式
三、预热温度对6006AT6铝合金材料强度影响的试验研究
车辆工业所使用的铝合金型材,大部分都是6005AT6铝合金,由于该铝合金是时效硬化型铝合金,热强度损失作用明显。
在热作用下,铝合金可能出现强度下降、晶间开裂等等问题,尤其材料在焊接热循环作用下,在热影响区更容易出现该类问题,对此,要求材料在一定温度下,具有保持一定强度和晶间抗裂能力。
以下是辽宁总旺铝厂针对车辆型材所进行的试验研究,从试验结果看,过高的预热温度和过长的预热时间,对材料强度均会造成很大影响,以下是一部分试验结果,从试验结果读者应该清晰预热对材料强度的影响:
1、预热温度对6005A铝合金性能的影响
(1)6005AT6铝合金母材室温条件下的强度分析
在型材材料上,分别在其纵向、熔合口横向截取试验试样,取样满足标准,在标准设备上做拉深、弯曲等试验,表6-3是母材正常条件下的强度试验数值,该试验值要满足标准。
表6-3 母材正常条件下的强度试验数值表
(2)母材经过200度、1min预热后,再冷至室温,材料强度的变化。
材料200度预热,基本在调质处理的范围内,对材料的各项指标均影响均不大,因此,在此温度范围内,预热的时间同样也影响不大,表6-4是200度预热、再冷却到室温的强度值。
母材经过200度、1min预热、冷却到室温后进行强度试验的结果
表6-4
材料经过300度预热后,会发生组织变化和晶粒大小变化,材料强度虽然在正常室温下
进行检测,强度的损失仍然不可避免,表6-5是经过300度预热后,再冷却到室温后的
强度试验值。
表6-5 母材经过300度、1min预热、冷却到室温后进行强度试验的结果
(4)材料经过400度、预热1min,再冷却室温的强度变化
材料预热400度以上,晶间和晶粒均会发生变化,进而影响材料强度,表6-6是材料400度、预热1min再冷却到室温下的工况强度试验值。
表6-6 母材经过400度、1min预热、冷却到室温后进行强度试验的结果
第二节焊后火焰调修
一、火焰加热的位置
粗略估计铝合金是否加热是否到位的一个简单方法就是观察材料的白热颜色的变化,如果材料不显示白颜色,或者显现的不够清楚,那么在实践中可以使用各种范围的测温笔来估计火焰的温度。
焊接变形调修需要火焰加热,加热位置原则上只能在焊缝位置,由于焊缝位置的填充金属没有经过时效强化,因此二次在焊缝位置加热对接头强度影响不大。
图6-3示意了焊后加热的操作模式。
图6-3 焊后调修操作模式
二、火焰加热的温度
焊后在焊缝位置加热应该采用集中性火焰,快速加热焊缝,焊缝加热越快、温度越高,焊接变形调修量越明显,加热温度的控制以不损伤母材为止,加热温度没有必要象母材预热那样有严格限制,但不能将热量大范围扩散,也就是严格控制加热时间。
第三节焊后热处理
焊后热处理的目的是为了改善焊接接头的组织和性能或消除残余应力,可热处理强化铝合金在焊接以后,可以重新进行热处理,使基体金属热影响区的强度恢复到接近原来的强度。
一般情况下,接头破坏处通常都是在焊缝的熔化区内。
在重新进行焊后热处理后,焊缝金属所获得的强度,主要取决于使用的填充金属。
填充金属与基体金属的成分不同时,强度取决于填充金属对基体金属的稀释度。
最好的强度与焊接金属所使用的热处理相适应。
虽然焊后
热处理增加了强度,但对焊缝的韧性可能会出现某些损失。
由于焊缝附近熔化区的沉淀和晶界的熔化,使可热处理强化铝合金的某些焊件的韧性很差。
假使情况不是太严重,焊后热处理可以使可溶的成分重新溶解,得到更均匀的结构,对韧性稍微有点改善,并会较大地增加强度。
焊件进行完全的重新热处理是不实际的,焊件可以在固溶热处理状态下焊接,焊后进行人工时效处理。
在这种焊接方法中,当使用高焊接速率时,有时性能能够获得显著的提高,超过了正常焊接状态的强度。
例如,对于6061合金在T4(固溶处理加自然时效)热处理状态焊接,焊后用T6(固溶处理加人工时效)处理,焊缝的强度可以达到280Mpa,强度提高显著,超过了190Mpa的焊接状态强度。
然而,焊件很少达到完全重新热处理的性能(固溶热处理加时效)。