电解铜阳极板标准
电解铜入门简介

电解铜铜的电解提纯:将粗铜(含铜99%)预先制成厚板作为阳极,纯铜制成薄片作阴极,以硫酸(H2SO4)和硫酸铜(CuSO4)的混和液作为电解液。
通电后,铜从阳极溶解成铜离子(Cu)向阴极移动,到达阴极后获得电子而在阴极析出纯铜(亦称电解铜)。
粗铜中杂质如比铜活泼的铁和锌等会随铜一起溶解为离子(Zn和Fe)。
由于这些离子与铜离子相比不易析出,所以电解时只要适当调节电位差即可避免这些离子在阳极上析出。
比铜不活泼的杂质如金和银等沉积在电解槽的底部。
这样生产出来的铜板,称为“电解铜”,质量极高,可以用来制作电气产品。
沉淀在电解槽底部的称为“阳极泥”,里面富含金银,是十分贵重的,取出再加工有极高的经济价值。
电解铜-原材料铜废碎料涉及的范围较广,包括紫铜、黄铜、青铜、白铜的废杂料,本标准规定的铜废碎料仅指紫杂铜。
紫杂铜为铜制品所产生的各类废料、废件。
如废旧电缆、紫铜管、棒、板、块、带及带薄镀层的上述材料和其它非合金类铜废料等。
电解铜-铜的性质:①物理性质铜是一种玫瑰红色金属,柔软、有金属光泽,密度为8.92克/厘米3,溶点为1083.5℃,沸点为2595℃,富于延展性,易弯曲,强度较好,在导电性和导热性方面,铜仅次于银,居第二位,它可以进行冷热压力加工,由于其具有面心立方晶格,铜及其化合物无磁性。
熔点时铜的蒸气压很小,因而在冶金过程温度下,不易挥发。
②化学性质液体铜能溶解某些气体,H2、O2、SO2、CO2、CO和水蒸气等,溶解气体对铜的机械性质及导电性均有一定影响,纯铜在常温下与干燥空气和湿空气不起作用,但在CO2湿空气中,表面会产生绿色薄膜CuCO3Cu(OH)2又称铜绿,它能保证铜不再被腐蚀。
铜在空气中加热到185℃即开始与氧作用,表面生成一层暗红色铜氧化物,当温度高于350℃时,铜颜逐渐从玫瑰色变成黄铜色,最后变成黑色。
铜不能溶解于硝酸和有氧化剂存在的硫酸中,铜能溶解于氨水中,也能与氧、卤等元素直接化合电解铜-铜的用途:以铜为基体的合金称为铜合金,铜加入合金元素后,可改变其某些机械性能,同时又能保持纯铜的某些优良特性,常用的铜合金有黄铜、青铜、白铜三类,它在电子、电器、造船、建筑、汽车工业、国防工业及各种冷凝器、换热器等方面有特定的用途,尤其是在制造核废料容器、大型集成电路、记忆合金等方面。
电解铜标准
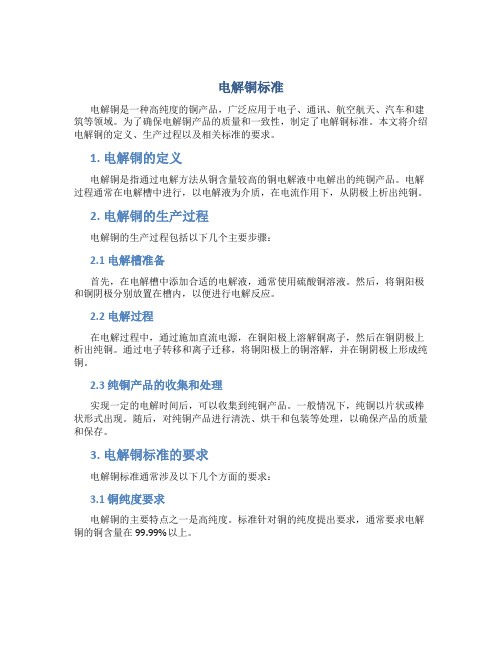
电解铜标准电解铜是一种高纯度的铜产品,广泛应用于电子、通讯、航空航天、汽车和建筑等领域。
为了确保电解铜产品的质量和一致性,制定了电解铜标准。
本文将介绍电解铜的定义、生产过程以及相关标准的要求。
1. 电解铜的定义电解铜是指通过电解方法从铜含量较高的铜电解液中电解出的纯铜产品。
电解过程通常在电解槽中进行,以电解液为介质,在电流作用下,从阴极上析出纯铜。
2. 电解铜的生产过程电解铜的生产过程包括以下几个主要步骤:2.1 电解槽准备首先,在电解槽中添加合适的电解液,通常使用硫酸铜溶液。
然后,将铜阳极和铜阴极分别放置在槽内,以便进行电解反应。
2.2 电解过程在电解过程中,通过施加直流电源,在铜阳极上溶解铜离子,然后在铜阴极上析出纯铜。
通过电子转移和离子迁移,将铜阳极上的铜溶解,并在铜阴极上形成纯铜。
2.3 纯铜产品的收集和处理实现一定的电解时间后,可以收集到纯铜产品。
一般情况下,纯铜以片状或棒状形式出现。
随后,对纯铜产品进行清洗、烘干和包装等处理,以确保产品的质量和保存。
3. 电解铜标准的要求电解铜标准通常涉及以下几个方面的要求:3.1 铜纯度要求电解铜的主要特点之一是高纯度。
标准针对铜的纯度提出要求,通常要求电解铜的铜含量在99.99%以上。
3.2 其他杂质要求电解铜标准还要求限制其他金属杂质的含量,以保证铜产品的纯净度。
例如,标准可能规定了铅、锌、镍、铁等金属杂质的最大含量限值。
3.3 形状和尺寸要求电解铜产品的形状和尺寸也是标准关注的内容。
例如,标准可能规定了电解铜板的厚度范围、宽度和长度的要求。
3.4 包装和标识要求标准还可能对电解铜产品的包装和标识提出要求。
这可以确保产品在储存和运输过程中不受到损害,并且能够正确识别和追溯。
结论电解铜标准是确保电解铜产品质量和一致性的关键要素。
这些标准涵盖了铜纯度、其他杂质限值、形状尺寸以及包装标识要求等方面。
通过遵守这些标准,可以生产出高质量的电解铜产品,满足不同领域的需求。
电解铜的规格和标准
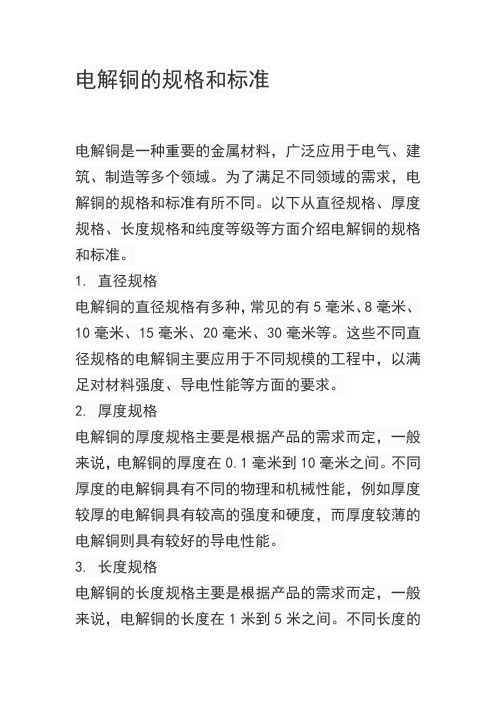
电解铜的规格和标准
电解铜是一种重要的金属材料,广泛应用于电气、建筑、制造等多个领域。
为了满足不同领域的需求,电解铜的规格和标准有所不同。
以下从直径规格、厚度规格、长度规格和纯度等级等方面介绍电解铜的规格和标准。
1. 直径规格
电解铜的直径规格有多种,常见的有5毫米、8毫米、10毫米、15毫米、20毫米、30毫米等。
这些不同直径规格的电解铜主要应用于不同规模的工程中,以满足对材料强度、导电性能等方面的要求。
2. 厚度规格
电解铜的厚度规格主要是根据产品的需求而定,一般来说,电解铜的厚度在0.1毫米到10毫米之间。
不同厚度的电解铜具有不同的物理和机械性能,例如厚度较厚的电解铜具有较高的强度和硬度,而厚度较薄的电解铜则具有较好的导电性能。
3. 长度规格
电解铜的长度规格主要是根据产品的需求而定,一般来说,电解铜的长度在1米到5米之间。
不同长度的
电解铜具有不同的使用场合,例如长度较短的电解铜主要应用于线材加工等领域,而长度较长的电解铜则主要应用于电缆制造等领域。
4. 纯度等级
电解铜的纯度等级是衡量其质量的重要指标之一。
一般来说,电解铜的纯度等级越高,其导电性能、机械性能、耐腐蚀性能等方面也就越好。
常见的电解铜纯度等级有CC1、CC2、CC3等,其中CC1级为最高级别,纯度达到99.95%以上。
总之,为了满足不同领域的需求,电解铜具有多种规格和标准。
在选择使用时,应根据具体需求和用途来选择相应的规格和标准。
钛阳极(钛电极)电解铜
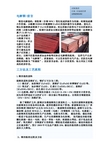
析出。
比铜不活泼的杂质如金和银等沉积在电解槽的底部。
1.铜冶炼的原料炼铜的原料是铜矿石。
铜矿石可分为三类:(1)硫化矿,如黄铜矿(CuFeS2)、斑铜矿(Cu5FeS4)和辉铜矿(Cu2S)等。
(2)氧化矿,如赤铜矿(Cu2O)、孔雀石[CuCO3Cu(OH)2]、蓝铜矿[2CuCO3Cu(OH)2]、硅孔雀石(CuSiO32H2O)等。
(3)自然铜。
铜矿石中铜的含量在1%左右(0.5%~3%)的便有开采价值,因为采用浮选法可以把矿石中一部分脉石等杂质除去,而得到含铜量较高(8%~35%)的精矿砂。
除了铜精矿之外,废铜亦为精炼铜的主要原料之一,包括旧废铜和新废铜,旧废铜来自旧设备和旧机器,废弃的楼房和地下管道;新废铜来自加工厂弃掉的铜屑(铜材的产出比为50%左右),一般废铜供应较稳定,废铜可以分为:裸杂铜:品位在90%以上;黄杂铜(电线):含铜物料(旧马达、电路板);由废铜和其他类似材料生产出的铜,也称为再生铜。
湿法冶炼:湿法冶炼一船适于低品位的氧化铜,生产出的精铜称为电积铜。
现代湿法冶炼有硫酸化焙烧-浸出-电积,浸出-萃取-电积,细菌浸出等法,适于低品位复杂矿、氧化铜矿、含铜废矿石的堆浸、槽浸选用或就地浸出。
湿法冶炼技术正在逐步推广,预计2009年可达总产量的25%,湿法冶炼的推出使铜的冶炼成本大大降低。
2、铜冶炼的过程及方法铜的冶炼方法可分为两类:火法冶金和湿法冶金。
世界上精铜产量的85%以上是用火法冶金从硫化铜精矿和再生铜中回收的,湿法冶金生产的精铜只占15%左右。
(1)铜矿石的冶炼过程:从铜矿石冶炼铜的过程比较复杂。
以黄铜矿为例,首先把精矿砂、熔剂(石灰石、砂等)和燃料(焦炭、木炭或无烟煤)混合,投入“密闭”鼓风炉中,在1000℃左右进行熔炼。
于是矿石中一部分硫成为SO2(用于制硫酸),大部分的砷、锑等杂质成为AS2O3、Sb2O3等挥发性物质而被除去:2CuFeS2+O2=Cu2S+2FeS+SO2↑。
1号电解铜标准

1号电解铜标准
电解铜是通过电解方法从含铜矿石或废铜中纯化得到的纯铜产品。
电解铜的纯度通常以“电解铜标准”表示,其中1号电解铜标准是高
纯度的电解铜产品之一。
1号电解铜标准的主要特点包括:
1. 高纯度:1号电解铜标准的纯度要求非常高,一般要求铜含量达到99.99%以上。
2. 无杂质:1号电解铜标准要求几乎没有其他金属元素的杂质存在,
其中常见杂质为铁、锌、镍、铅等。
3. 低氧含量:1号电解铜标准要求铜中的氧含量非常低,通常要求在0.02%以下。
4. 细粒度:1号电解铜标准要求铜的晶粒细小均匀,以保证良好的加
工性能和物理性能。
1号电解铜标准通常用于制造高精密电子器件、电子电路、半导
体材料等领域,因其高纯度和优良的导电、导热性能而受到广泛应用。
同时,1号电解铜标准也是其他纯铜合金制备的重要原材料。
总而言之,1号电解铜标准是高纯度的电解铜产品,具有高纯度、无杂质、低氧含量和细粒度等特点,被广泛应用于电子、半导体等领域。
电解铜成分标准

电解铜成分标准电解铜是指通过电解法从含铜矿石中提炼出来的纯铜。
电解铜的成分标准主要涉及到以下几个方面:1. 纯度:电解铜的纯度通常用铜含量来表示,纯度越高,铜含量越高。
一般来说,电解铜的纯度在99.99%以上。
2. 杂质含量:电解铜中的杂质含量对其性能和用途有一定影响。
常见的杂质包括铅、锌、镍、锡、铁、硫等。
根据不同应用场景,对电解铜的杂质含量有不同的要求。
例如,高纯度的电解铜用于电子、半导体等领域,对杂质含量要求较低;而一般用途的电解铜对杂质含量要求相对较高。
3. 物理性能:电解铜的物理性能,如密度、导电性、热稳定性等,也是评价其质量的重要指标。
高品质的电解铜应具有较高的导电性、良好的热稳定性和较高的密度。
4. 表面质量:电解铜的表面质量对其在后续加工和使用过程中的稳定性有很大影响。
通常要求电解铜表面光滑、无明显划痕、氧化物和油污等。
5. 尺寸和形状:电解铜产品有多种形状,如板材、棒材、线材等。
不同形状的电解铜应符合相应的尺寸标准。
在我国,电解铜的相关标准主要有以下几个:1. GB/T 1101-2008《铜及铜合金化学分析方法》:规定了电解铜中化学成分的分析方法。
2. GB/T 2059-2008《电解铜》:规定了电解铜的分类、技术要求、试验方法、检验规则和包装、运输、贮存等。
3. GB/T 375-2008《高纯铜》:规定了高纯铜的分类、技术要求、试验方法、检验规则和包装、运输、贮存等。
4. YB/T 4224-2010《电子级电解铜》:规定了电子级电解铜的分类、技术要求、试验方法、检验规则和包装、运输、贮存等。
以上标准为电解铜的成分、性能和质量提供了参考和依据。
在实际应用中,还需根据具体需求和用途选择合适的标准进行检测和评价。
电解铜的规格和标准

电解铜的规格和标准电解铜是一种高纯度的铜制品,广泛应用于电子、电气、通讯等领域。
要保证电解铜的质量和性能,必须制定相应的规格和标准。
本文将介绍电解铜的规格和标准,以期帮助读者更好地了解电解铜产品。
一、电解铜的分类根据应用领域和制造工艺不同,电解铜可以分为工业级电解铜和电子级电解铜两种。
1. 工业级电解铜:工业级电解铜的纯度要求相对较低,通常要求含铜量达到99.9%以上,并且允许含有一定比例的杂质,如铁、镍、锡等。
工业级电解铜主要用于制造电线、电缆、铜管、铜板等。
2. 电子级电解铜:电子级电解铜是一种高纯度的铜制品,纯度要求极高,通常要求含铜量达到99.99%以上,并且要求杂质含量极低,如铁、锡等杂质的含量需控制在极低的水平。
电子级电解铜广泛应用于半导体、电路板、电子元器件等高精密领域。
二、电解铜的规格要求1. 外观要求:电解铜应无裂纹、夹杂、气泡、皱褶、剥落等缺陷,表面应光洁平整,无明显划痕。
2. 尺寸要求:电解铜的尺寸应符合相关标准或合同要求,包括长度、宽度、厚度等尺寸参数。
尺寸偏差应在允许范围内。
3. 化学成分要求:电解铜的含铜量应满足标准要求,工业级电解铜的含铜量一般要求在99.9%以上,电子级电解铜的含铜量要求在99.99%以上。
同时,电解铜的杂质含量也要符合相关标准。
4. 物理性能要求:电解铜应具备良好的导电性和导热性,导电率的要求应符合标准。
此外,电解铜的延展性、强度等物理性能也需要满足相应要求。
三、电解铜的标准化为了确保电解铜的质量稳定和产品互换性,各个国家和地区制定了一系列的标准,以规范电解铜的生产和应用。
以下是一些常见的电解铜标准:1. ASTM B115-10 Standard Specification for Electrolytic Copper Cathode美国材料与试验协会制定的电解铜阳极板标准,规定了电解铜阳极板的尺寸、化学成分、物理性能等要求。
2. GB/T 3955-2008 电解铜中国国家标准化管理委员会发布的电解铜国家标准,规定了电解铜的分类、化学成分、尺寸要求、物理性能等。
电解铜标准

电解铜标准电解铜是一种重要的金属材料,广泛应用于电气、建筑、制造等领域。
为了规范电解铜的生产和使用,制定了一系列的标准。
本文将介绍电解铜标准的主要内容,包括电解铜原料标准、电解铜生产设备标准、电解铜生产工艺标准、电解铜产品质量标准、电解铜生产安全标准、电解铜环保标准、电解铜能源消耗标准和电解铜职业健康标准。
1.电解铜原料标准电解铜原料标准主要包括对原料的化学成分、物理性能等方面的要求。
标准中规定了电解铜原料的杂质含量、铜含量、尺寸规格等指标。
对于进口原料,还规定了杂质元素的含量要求。
2.电解铜生产设备标准电解铜生产设备标准主要包括设备的设计、制造、安装、调试等方面的要求。
标准中规定了设备的结构、性能、材料、安全防护等方面的要求。
同时,对于不同设备的验收、维修、保养等也做出了相应的规定。
3.电解铜生产工艺标准电解铜生产工艺标准主要包括对生产过程中的各个环节的要求。
标准中规定了原料的预处理、电解液的配制、电解过程控制等方面的要求。
同时,对于产品的后处理、废料的处理等也做出了相应的规定。
4.电解铜产品质量标准电解铜产品质量标准主要包括对产品化学成分、物理性能等方面的要求。
标准中规定了电解铜产品的铜含量、导电率、韧性等方面的指标。
同时,对于产品的外观、尺寸规格等也做出了相应的规定。
5.电解铜生产安全标准电解铜生产安全标准主要包括对生产过程中安全防护的要求。
标准中规定了设备的操作规程、安全设施的设置、危险品的管理等方面的要求。
同时,对于应急处理、事故报告等也做出了相应的规定。
6.电解铜环保标准电解铜环保标准主要包括对生产过程中环境污染控制的要求。
标准中规定了废气、废水、固体废物的排放要求和控制措施。
同时,对于环保设施的运行管理、环境监测等也做出了相应的规定。
7.电解铜能源消耗标准电解铜能源消耗标准主要包括对生产过程中的能源消耗控制的要求。
标准中规定了电能的消耗指标、热能的利用要求等方面的指标。
同时,对于节能设施的运行管理、能源监测等也做出了相应的规定。
- 1、下载文档前请自行甄别文档内容的完整性,平台不提供额外的编辑、内容补充、找答案等附加服务。
- 2、"仅部分预览"的文档,不可在线预览部分如存在完整性等问题,可反馈申请退款(可完整预览的文档不适用该条件!)。
- 3、如文档侵犯您的权益,请联系客服反馈,我们会尽快为您处理(人工客服工作时间:9:00-18:30)。
电解铜阳极板标准
电解铜阳极板标准
电解铜阳极板是一种常见的金属制品,广泛应用于电子、电气、通信等领域。
它具有良好的导电性、导热性和耐腐蚀性,因此在各种设备和产品中都有着重要的作用。
为了确保电解铜阳极板的质量和性能,制定了一系列的标准,以便进行生产、检验和使用。
一、外观要求
电解铜阳极板应具有平整、光滑的表面,无明显的凹凸、气泡、裂纹等缺陷。
表面应无明显的色差和变色,无污渍、油污等杂质。
边缘应整齐、无毛刺。
二、尺寸要求
电解铜阳极板的尺寸应符合设计要求或合同规定。
其厚度、宽度和长度应在允许范围内,允许的偏差应符合相关标准的规定。
三、化学成分要求
电解铜阳极板的化学成分应符合相关标准的规定。
其中,铜的含量应在规定的范围内,同时控制其他杂质元素的含量,以确保电解铜阳极板的纯度和稳定性。
四、物理性能要求
1. 电阻率:电解铜阳极板的电阻率应在规定范围内,以保证其良好的导电性能。
2. 导热性:电解铜阳极板的导热系数应符合相关标准的要求,以保证其良好的导热性能。
3. 耐腐蚀性:电解铜阳极板应具有良好的耐腐蚀性能,能够抵抗酸、碱等化学物质的侵蚀。
五、机械性能要求
1. 强度:电解铜阳极板的强度应符合相关标准的规定,以确保其在使用过程中不易变形或断裂。
2. 延展性:电解铜阳极板应具有良好的延展性,能够在加工过程中进行弯曲、拉伸等操作而不易断裂。
3. 硬度:电解铜阳极板的硬度应符合相关标准的要求,以保证其在使用过程中不易变形或划伤。
六、检验方法
对于电解铜阳极板的检验,可以采用以下方法:
1. 外观检查:通过目视观察和触摸检查,判断表面是否平整光滑,有无缺陷和杂质。
2. 尺寸测量:使用测量工具对电解铜阳极板的厚度、宽度和长度进行测量,并与设计要求或合同规定进行比对。
3. 化学成分分析:采用化学分析方法对电解铜阳极板的化学成分进行检测,包括铜含量和其他杂质元素的含量。
4. 物理性能测试:通过相应的实验设备和方法,对电解铜阳极板的电阻率、导热性和耐腐蚀性进行测试。
5. 机械性能测试:通过实验设备和方法,对电解铜阳极板的强度、延展性和硬度进行测试。
七、包装和运输
电解铜阳极板在包装和运输过程中,应采取适当的措施,以防止表面受损和变形。
常见的包装方式包括木箱包装、纸箱包装和托盘包装等。
在运输过程中,应避免与其他金属制品或化学物品接触,防止发生化学反应或腐蚀。
八、存储和使用
电解铜阳极板在存储和使用过程中,应避免受潮和受热。
存放时应选择干燥通风的地方,并避免阳光直射。
在使用过程中,应注意防止过度弯曲和过度拉伸,以免影响其性能和寿命。
总结:
电解铜阳极板作为一种重要的金属制品,在各个行业都有着广泛的应用。
为了确保其质量和性能,制定了一系列的标准,包括外观要求、尺寸要求、化学成分要求、物理性能要求、机械性能要求等。
同时,在检验、包装、运输、存储和使用过程中也需要遵循相应的规定和要求,以确保电解铜阳极板能够正常使用并发挥其优良特性。