带电流截止负反馈转速单闭环直流调速系统设计
第二节 带电流截止负反馈的转速单闭环直流调速系统实训
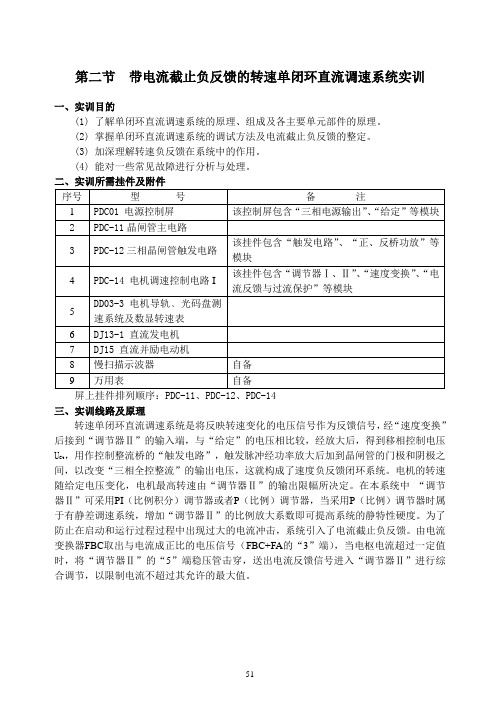
第二节带电流截止负反馈的转速单闭环直流调速系统实训一、实训目的(1) 了解单闭环直流调速系统的原理、组成及各主要单元部件的原理。
(2) 掌握单闭环直流调速系统的调试方法及电流截止负反馈的整定。
(3) 加深理解转速负反馈在系统中的作用。
(4) 能对一些常见故障进行分析与处理。
二、实训所需挂件及附件三、实训线路及原理转速单闭环直流调速系统是将反映转速变化的电压信号作为反馈信号,经“速度变换”后接到“调节器Ⅱ”的输入端,与“给定”的电压相比较,经放大后,得到移相控制电压U Ct,用作控制整流桥的“触发电路”,触发脉冲经功率放大后加到晶闸管的门极和阴极之间,以改变“三相全控整流”的输出电压,这就构成了速度负反馈闭环系统。
电机的转速随给定电压变化,电机最高转速由“调节器Ⅱ”的输出限幅所决定。
在本系统中“调节器Ⅱ”可采用PI(比例积分)调节器或者P(比例)调节器,当采用P(比例)调节器时属于有静差调速系统,增加“调节器Ⅱ”的比例放大系数即可提高系统的静特性硬度。
为了防止在启动和运行过程过程中出现过大的电流冲击,系统引入了电流截止负反馈。
由电流变换器FBC取出与电流成正比的电压信号(FBC+FA的“3”端),当电枢电流超过一定值时,将“调节器Ⅱ”的“5”端稳压管击穿,送出电流反馈信号进入“调节器Ⅱ”进行综合调节,以限制电流不超过其允许的最大值。
图4-1 带电流截止负反馈的转速单闭环直流调速系统四、实训内容(1) 三相晶闸管触发电路的调试。
(2) 测定和比较直流电动机开环机械特性和转速单闭环直流调速系统的静特性。
(3) 整定电流截止负反馈的转折点,并检验电流负反馈效应。
用慢扫描示波器观察和记录系统加入电流截止负反馈后,突加给定启动时电流Id和转速n的波形。
(4) 带电流截止负反馈的转速单闭环直流调速系统的排故训练。
五、实训方法(1) 系统的故障设置与分析请参考第二章相关内容。
(2) PDC-11和PDC-12上的“触发电路”调试①打开PDC01总电源开关,操作“电源控制屏”上的“三相电网电压指示”开关,观察输入的三相电网电压是否平衡。
带电流截止负反馈的单闭环脉宽调速系统
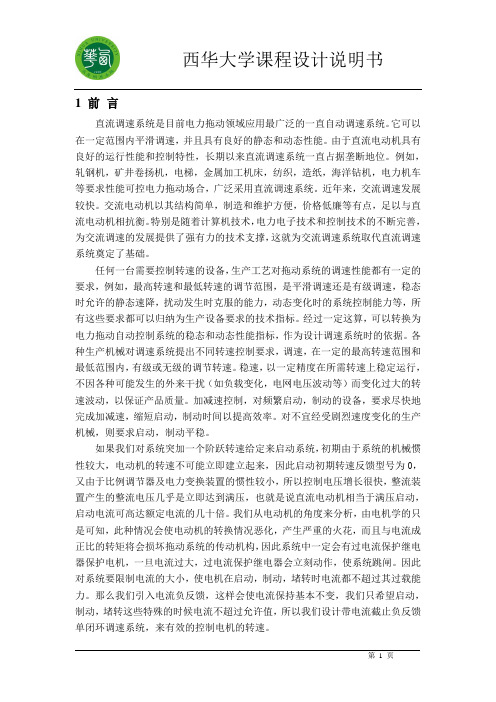
1 前言直流调速系统是目前电力拖动领域应用最广泛的一直自动调速系统。
它可以在一定范围内平滑调速,并且具有良好的静态和动态性能。
由于直流电动机具有良好的运行性能和控制特性,长期以来直流调速系统一直占据垄断地位。
例如,轧钢机,矿井卷扬机,电梯,金属加工机床,纺织,造纸,海洋钻机,电力机车等要求性能可控电力拖动场合,广泛采用直流调速系统。
近年来,交流调速发展较快。
交流电动机以其结构简单,制造和维护方便,价格低廉等有点,足以与直流电动机相抗衡。
特别是随着计算机技术,电力电子技术和控制技术的不断完善,为交流调速的发展提供了强有力的技术支撑,这就为交流调速系统取代直流调速系统奠定了基础。
任何一台需要控制转速的设备,生产工艺对拖动系统的调速性能都有一定的要求,例如,最高转速和最低转速的调节范围,是平滑调速还是有级调速,稳态时允许的静态速降,扰动发生时克服的能力,动态变化时的系统控制能力等,所有这些要求都可以归纳为生产设备要求的技术指标。
经过一定这算,可以转换为电力拖动自动控制系统的稳态和动态性能指标,作为设计调速系统时的依据。
各种生产机械对调速系统提出不同转速控制要求,调速,在一定的最高转速范围和最低范围内,有级或无级的调节转速。
稳速,以一定精度在所需转速上稳定运行,不因各种可能发生的外来干扰(如负载变化,电网电压波动等)而变化过大的转速波动,以保证产品质量。
加减速控制,对频繁启动,制动的设备,要求尽快地完成加减速,缩短启动,制动时间以提高效率。
对不宜经受剧烈速度变化的生产机械,则要求启动,制动平稳。
如果我们对系统突加一个阶跃转速给定来启动系统,初期由于系统的机械惯性较大,电动机的转速不可能立即建立起来,因此启动初期转速反馈型号为0,又由于比例调节器及电力变换装置的惯性较小,所以控制电压增长很快,整流装置产生的整流电压几乎是立即达到满压,也就是说直流电动机相当于满压启动,启动电流可高达额定电流的几十倍。
我们从电动机的角度来分析,由电机学的只是可知,此种情况会使电动机的转换情况恶化,产生严重的火花,而且与电流成正比的转矩将会损坏拖动系统的传动机构,因此系统中一定会有过电流保护继电器保护电机,一旦电流过大,过电流保护继电器会立刻动作,使系统跳闸。
带电流截止负反馈的转速单闭环直流调速系统的设计与仿真

专业课程实践训练报告本次实践训练的要求是“带电流截止负反馈的转速闭环直流调速系统的设计与仿真”。
(一)设计参数1)电动机:额定数据为10kv,220v,52A,1460r/min,电枢电阻RS=0.5Ω,飞轮力矩GD2=10N.m2。
2)晶闸管装置:三相桥式可控整流电路,整流变压器Y/Y联结,二次线电压E2t=230v,触发整流环节的放大系数Ks=40。
3)V-M系统主电路总电阻R=1Ω。
4)测速发电机:永磁式,ZYS231/110型;额定数据为23.1w,110v,0.18A,1800r/min。
5)系统静动态指标:稳态无静差,调速指标D=10,s≤56)电流截止负反馈环节:要求加入合适的电流截止负反馈环节,使电动机的最大电流限制(1.5-2)I N。
(二)设计要求1)闭环系统稳定。
2)在给定和扰动信号作用下,系统稳态无静差。
(三)设计任务1) 根据题目要求,分析论证确定系统的组成,画出系统组成的原理框图;2) 对转速单闭环直流调速系统进行稳态分析及参数设计计算;3) 绘制原系统的动态结构图;4) 动态稳定性判断,校正,选择转速调节器并进行设计;5) 绘制校正后系统的动态结构图;6) 应用MATLAB软件对转速单闭环直流调速系统进行仿真,验证所设计的调节器是否符合设计要求;7) 加入电流截止负反馈环节;8) 应用MATLAB软件对带电流截至负反馈的转速单闭环直流调速系统进行仿真,完善系统。
(四) 原理1) 闭环调速系统组成原理与电动机同轴安装一个测速发电机,从而产生与转速成正比的负反馈电压U n,与给定电压U n*相比较后,得到转速偏差电压,经过放大器A,产生电力电子变换器UPE所需的控制电压U c,用以控制电动机的转速。
PI 调节器作用是使系统无静差电流截止负反馈的作用是在电动机发生超载或堵转的时候电流截止负反馈和给定信号相比较抵消。
使电动机处于停止运行状态,以保护电机。
(五)闭环直流调速系统稳态参数的计算 1)额定负载时的稳态速降应为: 7.68r/minmin /68.7min /)05.01(1005.01460)1(r r s D s n n N cl =-⨯⨯≤-=∆ 2)闭环系统应有的开环放大系数:计算电动机的电动势系数:0.1329V.min/rr V r V n R I U C N a N N e min/1329.0min/14605.052220⋅=⋅⨯-=-=闭环系统额定速降为:391.27r/minmin /27.391min /1329.0152r r C R I n e N op =⨯==∆ 闭环系统的开环放大系数为:49.99.49168.727.3911=-≥-∆∆=clop n n K 3)计算转速负反馈环节的反馈系数和参数测速发电机的电动势:0.0611V.min/rr V min/0611.01800r/min110VC etg ⋅==转速反馈电压:16.05 V (α=α2C etg α2取0.18)转速反馈系数为:0.010998 V.min/r4) 计算运算放大器的放大系数和参数 运算放大器放大系数K p 为: 12.27运算放大器型号:R 0=40K Ω,R 1=490.8 K Ω 5)判断系统的稳定性计算:电枢回路的总电感为17.70mHmin2693.0d I U L = V V U U l 8.1323230322===系统中各环节的时间常数: 电磁时间常数T l:0.018S机电时间常数T m :0.158Ss C C R GD T me m 158.01329.0301329.03751103752=⨯⨯⨯⨯==π晶闸管装置的滞后时间常数T s :0.00167S63.10300167.0017698.000167.0)00167.0017698.0(158.0)(22=⨯+⨯⨯=++s l s s l m T T T T T T K计算出开环放大系数应满足的稳定条件为K ≤103.48,又因为 K=40.6,所以系统稳定。
带电流截止负反馈的转速单闭环直流调速系统

实验八带电流截止负反馈的转速单闭环直流调速系统一、实验目的(1)了解单闭环直流调速系统的原理、组成及各主要单元部件的原理。
(2)掌握晶闸管直流调速系统的一般调试方法及电流截止负反馈的整定。
(3)通过实验,加深理解负反馈原理及转速负反馈电流截止负反馈的在调速系统中的作用。
二、实验所需挂件及附件三、实验线路及原理为了提高直流调速系统的动静态性能指标,通常采用闭环控制系统(包括单闭环系统和多闭环系统)。
对调速指标要求不高的场合,采用单闭环系统,而对调速指标较高的则采用多闭环系统。
按反馈的方式不同可分为转速反馈,电流反馈,电压反馈等。
在单闭环系统中,转速单闭环使用较多。
在本装置中,转速单闭环实验是将反映转速变化的电压信号作为反馈信号,经“速度变换”后接到“速度调节器”的输入端,与“给定”的电压相比较经放大后,得到移相控制电压U Ct,用作控制整流桥的“触发电路”,触发脉冲经功放后加到晶闸管的门极和阴极之间,以改变“三相全控整流”的输出电压,这就构成了速度负反馈闭环系统。
电机的转速随给定电压变化,电机最高转速由速度调节器的输出限幅所决定,速度调节器采用P(比例)调节对阶跃输入有稳态误差,要想消除上述误差,则需将调节器换成PI(比例积分)调节。
这时当“给定”恒定时,闭环系统对速度变化起到了抑制作用,当电机负载或电源电压波动时,电机的转速能稳定在一定的范围内变化。
在电流单闭环中,将反映电流变化的电流互感器输出电压信号作为反馈信号加到“电流调节器”的输入端,与“给定”的电压相比较,经放大后,得到移相控制电压U Ct,控制整流桥的“触发电路”,改变“三相全控整流”的电压输出,从而构成了电流负反馈闭环系统。
电机的最高转速也由电流调节器的输出限幅所决定。
同样,电流调节器若采用P(比例)调节,对阶跃输入有稳态误差,要消除该误差将调节器换成PI(比例积分)调节。
当“给定”恒定时,闭环系统对电枢电流变化起到了抑制作用,当电机负载或电源电压波动时,电机的电枢电流能稳定在一定的范围内变化。
带电流截至负反馈的转速单闭环直流调速系统概要

带电流截至负反馈的转速单闭环直流调速系统概要概述直流调速系统是现代工业中常见的一种控制系统,其主要作用是通过控制电机的转速来调节其输出的功率。
转速单闭环直流调速系统是其中一种常见的控制系统,它采用了带电流截至负反馈的技术,可以有效地提高系统的稳定性和响应速度。
系统结构转速单闭环直流调速系统主要由三部分组成:电机控制电路、转速测量电路和控制器。
其中电机控制电路用于控制电机的转速,转速测量电路用于测量电机的转速,控制器用于计算误差并发送控制信号到电机控制电路。
具体来说,电机控制电路包括电源、电机以及功率调节器等组件。
电源提供电流给电机,功率调节器则可以控制电流的大小和方向,从而实现对电机转速的控制。
转速测量电路主要用于测量电机的转速,它通常包括一些传感器和信号处理电路。
传感器可以检测电机转子的位置,信号处理电路则将传感器输出的信号转换为脉冲信号,供控制器使用。
控制器是这个系统的核心部件,它负责计算误差并发送控制信号到电机控制电路。
具体来说,控制器可以将目标转速和实际转速之间的差值作为误差,通过算法计算出电机电流的大小和方向,从而实现对电机转速的控制。
技术应用转速单闭环直流调速系统广泛应用于各种需要精确控制电机转速的场合,比如机床、风扇、电动机车、水泵等等。
用转速单闭环直流调速系统可以实现对电机的精确的控制,提高设备的工作效率和稳定性。
此外,带电流截至负反馈的技术也可以应用于其他类型的控制系统中,比如温度控制系统、光照控制系统等等。
它的优点是可以提高系统的稳定性和响应速度,从而提高设备的性能和可靠性。
转速单闭环直流调速系统是一种常见的控制系统,它采用了带电流截至负反馈的技术,可以实现对电机转速的精确控制。
该系统结构简单,应用广泛,可用于机床、风扇、电动机车、水泵等设备的控制。
此外,该技术也可以应用于其他类型的控制系统中,提高设备的性能和可靠性。
带电流截止负反馈的转速单闭环直流调速系统设计与仿真运动控制实验报告

带电流截止负反馈的转速单闭环直流调速系统设计与仿真 一、设计要求系统稳定并无静差 二、给定参数17,220,3000/min N N N P kw U V n r ===,I N =87.3A ,电枢回路电阻0.087a R =Ω,电感0.0032a L H =,励磁回路电阻181.5Ω,电动机的转动惯量20.76.J Kg m =三、闭环直流调速系统稳态参数的计算 1)额定负载时的稳态速降应为:m i n/12.6min /)02.01(1002.03000)1(r r s D s n n N cl =-⨯⨯≤-=∆2)闭环系统应有的开环放大系数:计算电动机的电动势系数: r V r V n R I U C N a N N e min/071.0min/3000087.03.87220⋅=⋅⨯-=-=闭环系统额定速降为:min /97.106min /071.0087.03.87r r C R I n e N op =⨯==∆闭环系统的开环放大系数为:5.16112.697.1061=-≥-∆∆=clop n n K003.0/max max n ==n U α3)计算运算放大器的放大系数和参数 运算放大器放大系数K p 为:5.16/e p ≥=s K KC K α电枢回路的总电感为0.0032H电磁时间常数为037.0/l ==R L T 27/1l ==τK4)电流截止负反馈 四加电网扰动(第8s电压220→240)负载扰动给定值扰动五、将PI调节器参数改变1.电网扰动(第8s电压220→240)2.负载扰动3.给定值扰动转速、电流双闭环直流调速系统设计与仿真一、设计要求系统稳定并无静差 二、给定参数17,220,3000/min N N N P kw U V n r ===,I N =87.3A ,电枢回路电阻0.087a R =Ω,电感0.0032a L H =,励磁回路电阻181.5Ω,电动机的转动惯量20.76.J Kg m =三、电流调节器ACR 参数计算允许电流过载倍数λ=2;设调节器输入输出电压im nm **U U ==10V ,电力电子开关频率为f=l kHz .首先计算电流反馈系数β和转速反馈系数α:06.0 I n im *==ββλU N U n nm *α= α=0.003s T 001.0s = ,电流环小时间常数为s T T T oi 002.0s i =+=∑电流调节器超前时间常数为s T K l i 015.0/1i ===τ 而对电流环开环增益局l K =250/5.0=∑i T ,于是ACR 的比例系数为:94.4/i l i ==s K R K K βτ 四、转速调节器ASR 参数计算 选中频段宽度h=5。
带电流截止负反馈的转速闭环的数字式直流调速系统的仿真与设计.
运动控制课程设计带电流截止负反馈的转速闭环的数字式直流调速系统的仿真与设计专业:电气工程及其自动化班级:电气一班姓名:学号:指导老师:陈敏2014-12-25带电流截止负反馈的转速闭环的数字式直流调速系统的仿真与设计摘要:到目前为止,虽然在交流电动机的调速问题方面已经解决,但是在速度调节要求却较高,本文主要介绍转速闭环直流调速系统的工作原理,并在此基础上对转速闭环直流电动机的调速系统进行分析,借助MATLAB/SIMULINK 建立起仿真图并进行仿真与分析。
论文中给出了各个物理量的波形并对波形进行了分析从而对转速闭环调速系统的稳定性方面得出了一些结论。
该调速控制系统可以实现平滑的调速,且具有良好的动静态调速性能,仿真结果验证了系统设计的有效性、可行性。
关键词: 转速闭环调速系统; 直流电动机; MATLAB 仿真一、引言在分析电压负反馈电流补偿直流调速系统的基础上,本文提出在主电路中增加了串联的取样电感,用来提取电枢自感电动势产生的压降。
改进后的电流正反馈能补偿由电枢内阻和自感电动势产生的压降,提高了动态电流变化时电流补偿的精度。
根据转速、电流双闭环调速系统的设计方法,用Simulink做了带电流补偿的电压负反馈直流调速系统仿真,仿真结果证明,增加取样电感后可以消除电流补偿的滞后,在忽略参数变化的影响下精确地补偿电枢压降,改进后的电压负反馈电流补偿能够获得跟转速负反馈同样的效果。
电机是一种将电能转换成机械能的设备。
到目前为止,虽然交流电动机的调速问题已经解决,但是在速度调节要求较高,正、反转和启、制动频繁或多单元同步协调运转的生产机械上,仍采用直流电动机。
二、课程设计的目的:①学会使用MATLAB和PROTEL软件画图;②了解恒压频比控制交流调速系统的工作原理及其参数的确定;③学会应用MATLAB软件,建立数学模型对控制系统进行仿真研究,掌握系统参数对系统性能的影响;三、程设计课题:带电流截止负反馈的转速闭环的数字式直流调速系统的仿真与设计直流电动机控制系统设计参数直流电动机(1):输出功率为:7.5Kw 电枢额定电压220V电枢额定电流36A 额定励磁电流2A额定励磁电压110V 功率因数0.85电枢电阻0.2欧姆电枢回路电感100mH电机机电时间常数2S 电枢允许过载系数1.5额定转速1430rpm环境条件:电网额定电压:380/220V;电网电压波动:10%;环境温度:-40~+40摄氏度;环境湿度:10~90%.控制系统性能指标:电流超调量小于等于5%;空载起动到额定转速时的转速超调量小于等于30%;调速范围D=20;静差率小于等于0.03.四、转速负反馈的闭环直流调速系统的原理该系统由转速给定环节为Un*,放大倍数为KP的放大器、移相触发器CF、晶闸管整流器和直流电动机M、测速发电机TG等组成。
带电流截止负反馈转速单闭环V-M不可逆直流调速系统
带电流截止负反馈转速单闭环V-M不可逆直流调速系统摘要晶闸管—电动机调速系统(V—M系统)在20实际60年代开始逐步取代G—M系统而成为20世纪后30年中直流调速系统的主要形式。
电源是静止装置,由电力电子AC/DC变换器供电。
输出电压可调的电力电子AC/DC变换器最常见的就是大家所熟悉的晶闸管可控整流器,通过改变晶闸管的可控整流器的控制角α来改变可控整流器输出电压的极性和大小。
采用转速负反馈和PI调节器的单闭环的调速系统可以再保证系统稳定的条件下实现转速无静差。
带电流截止负反馈的闭环直流调速系统的在对调速精度要求不高的,大功率容量的电机中的应用是非常广泛的,它具有控制简单方便,调速性能较好,设备成本低等的优点。
通过对单闭环调速系统的组成部分可控电源、由运算放大器组成的调节器、晶闸管触发整流装置、电机模型和测速电机等模块的理论分析,比较原始系统和校正后系统的差别,得出直流电机调速系统的最优模型。
然后用此理论去设计一个实际的调速系统。
关键词:稳态性能稳定性单闭环电流截止负反馈无静差目录第0章前言 (3)第1章课程设计内容 (3)第2章性能指标 (4)第3章方案论证...................................................... .. (5)第4章主回路与控制回路设计..................................... . (8)第5章参数计算 (15)第6章Matlab建模与仿真 (16)第7章总电气图 (25)第8章结束语 (26)第9章致谢 (27)第10 章参考文献 (28)前言为了提高直流调速系统的动静态性能指标,通常采用闭环控制系统。
对调速指标要求不高的场合,采用单闭环系统,而对调速指标较高的则采用多闭环系统。
按反馈的方式不同可分为转速反馈,电流反馈,电压反馈等。
在单闭环系统中,转速单闭环使用较多。
在对调速性能有较高要求的领域常利用直流电动机作动力,但直流电动机开环系统稳态性能不能满足要求,可利用速度负反馈提高稳态精度,而采用比例调节器的负反馈调速系统仍是有静差的,为了消除系统的静差,可用积分调节器代替比例调节器。
直流调速器电流截止负反馈单闭环调速系统设计
电力拖动控制系统课程设计题目:带电流截止负反馈的转速单闭环直流调速系统学号:姓名:专业班级:学院 :指导教师 :1引言单闭环直流调速系统概述从生产机械要求控制的物理量来看,电力拖动自动控制系统有调速系统、位置随动系统、张力控制系统等多种类型,而各种系统往往都是通过控制转速来实现的,因此调速系统是最基本的拖动控制系统。
相比于交流调速系统,直流调速系统在理论上和实践上都比较成熟。
直流调速是现代电力拖动自动控制系统中发展较早的技术。
在20世纪60年代发展起来的电力电子技术,使电能可以变换和控制,产生了现代各种高效、节能的新型电源和交直流调速装置,为工业生产,交通运输,楼宇、办公、家庭自动化提供了现代化的高新技术,提高了生产效率和人们的生活质量,使人类社会生产、生活发生了巨大的变化。
随着新型电力电子器件的研究和开发以及先进控制技术的发展,电力电子和电力拖动控制装置的性能也不断优化和提高,这种变化的影响将越来越大。
2控制直流调速系统简介2.1 调速系统组成及工作原理采用闭环调试系统,可以提高系统的静、动态性能指标。
转速单闭环直流调速系统是常用的一种形式,实验图1-1是带直流截止负反馈的转速单闭环直流调速系统的实验线路图。
图2.1 闭环调速系统组成结构图中电动机的电枢回路由晶闸管组成的三相桥式全控蒸馏电路VT 供电,通过与电动机同轴刚性连接的测速发电机TG 检测电动机的转速,并经过转速反馈环节FBS 分压后取出合适的转速反馈信号Un ,此电压与转速给定信号 Un*经过速度调节器ASR 综合调节,ASR 输出作为一项触发器GT 的控制电压Uc ,由此组成转速单闭环直流调速系统。
图中DZS 为零速封锁器,当转速给定电压Un*和转速反馈电压Un 均为零时,DZS 的输出信号使转速调节器ASR 锁零,以防止调节器零飘而使电动机产生爬行。
在本系统中ASR 采用比例调节器,属于有警察调速系统,增加ASR 的比例放大系数即可提高系统的静特性硬度。
带电流截止负反馈环节的单闭环直流调速系统设计
带电流截⽌负反馈环节的单闭环直流调速系统设计带电流截⽌负反馈环节的单闭环直流调速系统设计1设计⽬的(1)了解带电流截⽌负反馈的转速单闭环直流调速系统的⼯作原理,熟悉组成环节及每个环节的作⽤。
(2)应⽤所学的交、直流调速系统的基本知识与⼯程设计⽅法,结合⽣产实际,确定系统的性能指标与实现⽅案,进⾏运动控制系统的初步设计。
(3)应⽤计算机仿真技术,通过在MATLAB软件上建⽴运动控制系统的数学模型,对控制系统进⾏性能仿真研究,掌握系统参数对系统性能的影响。
2设计参数采⽤晶闸管三相桥式全控整流电路供电,基本数据如下:直流电动机UN=220V, IN=65A,nN =1000r/min,电枢电阻Ra=0.15Ω,电枢电感La=0.0002H,励磁电压Uf=220V,励磁电流If=1.5A,电枢绕组和励磁绕组互感Laf=0.82H,供电电源电压U2=130V;晶闸管装置Ts=0.00167s,放⼤系数Ks=40;电枢回路总电阻R=0.5Ω;电枢回路总电感L=15mH;电动机轴上的总飞轮惯量GD2=12.5N·m2;转速调节器最⼤给定值*nmU=10V;3 设计任务(1)分析电流截⽌负反馈环节的⼯作原理,画出系统稳态结构图;(2)在MATLAB中建⽴带电流截⽌负反馈环节的单闭环直流调速系统;(3调节控制器参数,确定最佳调节参数。
将Simulink仿真模型,以及启动过程中的电流、转速波形图附在设计说明书中。
⽐较带电流截⽌负反馈环节和不带电流截⽌负反馈环节启动过程的差异。
4设计要求1.稳态指标:转速⽆静差;2.动态指标:启动电流的最⼤值150 A。
空载启动到额定转速的转速超调量σn≤15%。
4 设计基本内容4.1问题的提出在转速反馈控制直流调速系统中存在⼀个问题,在启动、制动过程和堵转状态时,电枢电流会过⼤。
为了解决反馈闭环调速系统的起动和堵转时电流过⼤的问题,系统中必须有⾃动限制电枢电流的环节。
引⼊电流负反馈,可以使它不超过允许值。
- 1、下载文档前请自行甄别文档内容的完整性,平台不提供额外的编辑、内容补充、找答案等附加服务。
- 2、"仅部分预览"的文档,不可在线预览部分如存在完整性等问题,可反馈申请退款(可完整预览的文档不适用该条件!)。
- 3、如文档侵犯您的权益,请联系客服反馈,我们会尽快为您处理(人工客服工作时间:9:00-18:30)。
目录摘要 (2)1主电路的设计 (2)1.1变压器参数的设计与计算 (2)1.2平波电抗器参数的设计与计算 (3)1.3晶闸管元件参数的计算 (3)1.4保护电路的设计 (4)2反馈调速及控制系统 (4)2.1闭环调速控制系统 (4)2.2带电流截止负反馈闭环控制系统 (5)2.3调节器设定 (8)2.4控制及驱动电路设计 (9)3参数计算 (10)3.1基本参数计算 (10)3.2电流截止负反馈环节参数计算与设计 (12)3.3调节器的参数设计与计算 (12)3.4调节器串联校正设计 (15)4总电气图 (16)5心得体会 (18)参考资料 (18)带电流截止负反馈转速单闭环直流调速系统设计摘要直流电动机具有良好的起、制动性能,宜于在大范围内平滑调速,并且直流调速系统在理论和实践上都比较成熟,是研究其它调速系统的基础。
在直流电动机中,带电流截止负反馈直流调速系统应用也最为广泛,其广泛应用于轧钢机、冶金、印刷、金属切割机床等很多领域的自动控制。
本次课设就带电流截止负反馈转速单闭环直流调速系统进行参数的设计。
1主电路的设计1.1变压器参数的设计与计算变压器副边电压采用如下公式进行计算: ⎪⎪⎭⎫ ⎝⎛-+=N sh Td I I CU A nU U U 2min max cos αβVU C I I U A n V U V U Nsh T d 110)105.05.09848.0(9.034.2122205.0105.0109.034.221,220222min max =⨯⨯-⨯⨯+==========则取已知αβ因此变压器的变比近似为:45.311038021===U U K 一次侧和二次侧电流I 1和I 2的计算 I 1=1.05×287×0.861/3.45=75A I 2=0.861×287=247A变压器容量的计算S 1=m 1U 1I 1=3×380×75=85.5kVA S 2=m 2U 2I 2=3×110×247=81.5kVAS=0.5×(S 1+S 2)=0.5×(85.5+81.5)=83.5kVA因此整流变压器的参数为:变比K=3.45,容量S=83.5kVA1.2平波电抗器参数的设计与计算U d =2.34U 2cos αU d =U N =220V, 取α=0° U 2=V U d 0171.9434.22200cos 34.2==I dmin =(5%-10%)I N ,这里取10% 则 L=0.693mH I U d 2308.375.171.00171.94693.0min 2=⨯⨯=⨯0067.0150010*===N nm n U α1.3晶闸管元件参数的计算晶闸管的额定电压通常选取断态重复峰值电压U DRM 和反向重复峰值电压U RRM 中较小的标值作为该器件的额定电压。
晶闸管的额定电流一般选取其通态平均电流的1.5-2倍。
在桥式整流电路中晶闸管两端承受的最大正反向电压均为22U ,晶闸管的额定电压一般选取其最大正反向电压的2-3倍。
带反电动势负载时,变压器二次侧电流有效值I 2是其输出直流电流有效值I d 的一半,而对于桥式整流电路,晶闸管的通态平均电流I VT =22I ,则在本设计中晶闸管的额定电流I VT(AV)=523-698A本设计中晶闸管的额定电压U N =311-466V1.4保护电路的设计对于过电压保护本设计采用RC 过电压抑制电路,该装置置于供电变压器的两侧或者是电力电子电路的直流上,如图1-1所示。
对于过电流保护本设计采用在电力变压器副边每相母线中串接快速熔断器的方法来保护电路图1-1过压保护电路2反馈调速及控制系统2.1闭环调速控制系统将开环系统改为单闭环转速负反馈调速系统,并采用PI 调节器,就既保证动态性能,又能作到转速的无静差,较好的解决开环系统的不足,此闭环系统的工作原理是:将直流电动机转速变化信号反馈到触发环节,来自动增大或减小触发角α来自动调节整流输出电压Uds ,即可达到稳定,其系统结构框图如图2-1所示图2-1 单闭环转速负反馈系统框图触发电路整流电路 电动机转速反馈 电 源αUdsΔU-2.2带电流截止负反馈闭环控制系统在转速反馈控制直流调速系统中存在一个问题,在启动、制动过程和堵转状态时,电枢电流会过大。
为了解决反馈闭环调速系统的起动和堵转时电流过大的问题,系统中必须有自动限制电枢电流的环节。
根据反馈控制原理,要维持哪一个物理量基本不变,就应该引入那个物理量的负反馈。
那么,引入电流负反馈,应该能够保持电流基本不变,使它不超过允许值。
通过对电流负反馈和转速负反馈的分析。
考虑到,限流作用只需在起动和堵转时起作用,正常运行时应让电流自由地随着负载增减,采用电流截止负反馈的方法,则当电流大到一定程度时才接入电流负反馈以限制电流,而电流正常时仅有转速负反馈起作用控制转速。
电流截止负反馈环节如图2-2中的(a)(b)(c)图:.(a)利用独立直流电源作比较电压(b)利用稳压管产生比较电压(c)封锁运算放大器的电流截止负反馈环节图2-2电流截止负反馈的环节图(a )中用独立的直流电源作为比较电压,其大小可用电位器调节,相当于调节截止电流。
图(b )中利用稳压管VS 的击穿电压U br 作比较电压,线路要简单得多,但不能平滑的调节电流值。
图(c )是反馈环节与运放的连接电路。
由系统稳态结构可写出该系统两段静特性的方程式:当d dcr I I >时,引入电流负反馈,静特性变为:图2-3带电流截止负反馈闭环调速系统的静特性静特性的几个特点:(1)电流负反馈的作用相当于在主电路中串入一个大电阻 Kp Ks Rs ,因而稳态速大, 特性急剧下垂。
(2)比较电压 Ucom 与给定电压 Un* 的作用一致, 好像把理想空载转速提高到(3)两段式静特性常称作下垂特性或挖土机特性。
当挖土机遇到坚硬的石块而过载电 动机停下,电流也不过是堵转电流,在式(1)中,令 n = 0,得 一般p s s K K R R >>,因此 (4)最大截止电流由给定条件知堵转电流 I dbl =2I N =35A, 截止电流 I dcr =1.5I N =26.25A(5)带电流截止负反馈的闭环直流调速稳态系统结构框图及结构图如图2-4及图2-5)1()()1()(e d s s p e com *n s p K C I R K K R K C U U K K n ++-++=)1()1(e de *n s p K C RI K C U K K n +-+=)1()('e com *n s p 0K C U U K K n ++=ss p com *n s p dbl )(R K K R U U K K I ++=scom *n dblR U U I +≈图2-4带电流截止负反馈的闭环直流调速稳态系统结构框图+-+-图2-5含电流截止负反馈的转速负反馈原理图2.3调节器设定如图2-6微PI 调节器即比例积分调节器既结构图用于实现系统的无静差调速系统图2-6 PI 调节器的结构图比例积分调节器的控制传递函数为:pi K =1R /2R pi K 为PI 调节器的比例放大系数1C = τ/0R τ为PI 调节器超前时间常数。
比例调节器的输出只取决于输入偏差量的现状,而积分调节器的输出则包含了输入偏差量的全部历史。
积分调节器到稳态时ΔUn =0,只要历史上有过ΔUn ,其积分就有一定数值,足以产生稳态运行所需要的控制电压。
如图2-7为采用PI 调节器单闭环调速系统动态校正特性s K s K s W K P pi pi P ττ1)(1+=图2-7采用PI调节器单闭环调速系统2.4控制及驱动电路设计晶闸管触发电路类型很多,有分立式、集成式和数字式,分立式相控同步模拟电路相对来说电路比较复杂;数字式触发器可以在单片机上来实现,需要通过编程来实现,本设计不采用。
由于集成电路可靠性高,技术性能好,体积小,功耗低,调试方便,所以本设计采用的是集成触发器,选择目前国内常用的KJ、KC系例,本设计采用KJ004集成块和KJ041集成块。
对于三相全控整流或调压电路,要求顺序输出的触发脉冲依次间隔60°。
本设计采用三相同步绝对式触发方式。
根据单相同步信号的上升沿和下降沿,形成两个同步点,分别发出两个相位互差180°的触发脉冲。
然后由分属三相的此种电路组成脉冲形成单元输出6路脉冲,再经补脉冲形成及分配单元形成补脉冲并按顺序输出6路脉冲。
本设计课题是三相全桥控桥整流电路中有六个晶闸管,触发顺序依次为:VT1—VT2—VT3—VT4—VT5—VT6,晶闸管必须严格按编号轮流导通,6个触发脉冲相位依次相差60O,可以选用3个KJ004集成块和一个KJ041集成块,即可形成六路双脉冲,再由六个晶体管进行脉冲放大,就可以构成三相全控桥整流电路的集成触发电路如图5.3。
图2-8 三相全控桥整流电路的集成触发控制电路3参数计算3.1基本参数计算1)额定负载时的稳态速降应为:15000.02=/min 3.06/min 101-0.02(1)N cl n sn r r D s ⨯∆==⨯-()2)闭环系统应有的开环放大系数: 计算电动机的电动势系数:22017.5 1.25min/0.132min/1500N N a e N U I R C V r V r n --⨯==⋅=⋅ 开环系统额定速降为:17.5 2.85/min 377.84/min 0.132N op e I R n r r C ⨯∆=== 闭环系统的开环放大系数为:377.8411122.483.06op cln K n ∆=-≥-=∆ 3)计算转速负反馈环节的反馈系数和参数设在额定转速下稳态时的给定电压为*10nU V =,则须有*10n n U U V == 故转速反馈环节的放大系数0.00667nNU n α== 4) 计算运算放大器的放大系数和参数 运算放大器放大系数K p 为:122.480.13260.5970.0066740e p s KC K K α⨯=≥=⨯ 5)判断系统的稳定性计算:由已知平波电抗器:R L =0. 3Ω。
电枢回路总电阻 R=2.85Ω ,总电感 L=200mH 所以系统中各环节的时间常数: 电磁时间常数T l :0.20.07022.85l L T R === 机电时间常数T m :2 3.53 2.850.161303753750.1320.132m e m GD R T s C C π⨯===⨯⨯⨯ 晶闸管装置的滞后时间常数T s :0.00167S2()0.161(0.0720.00167)0.001670.0016798.670.0720.00167m l s s l sT T T T KTT ++++⨯==⨯计算出开环放大系数应满足的稳定条件为K ≤98.67,又因为 K=122.48,所以系统不稳定。