QPQ盐浴复合处理技术的基本原理及操作注意事项
QPQ盐浴复合处理技术的基本原理及操作注意事项

QPQ盐浴复合处理技术的基本原理及操作注意事项QPQ盐浴复合处理技术是一种表面改性技术,主要用于提高金属表面硬度、耐磨性和耐腐蚀性。
它的基本原理是将工件浸入含有特殊组成的盐浴中,在高温下溶解出盐中的氮、碳和氧等元素,然后在钢铁表面上形成高度附着的合金层。
下面将从原理和操作注意事项两方面进行详细介绍。
一、基本原理:1.盐浴的组成:盐浴通常由氯化钠、氯化亚铜、氯化亚硝酸铵等多种盐组成。
其中的氯化钠提供了导电性,氯化亚铜提供了活化元素,氯化亚硝酸铵提供了氮化元素。
这些盐在高温下溶解,形成一层活化元素和氮化元素浸透到钢铁表面的溶液。
2.反应机理:在高温下,盐浴会溶解出含有活化元素和氮化元素的溶液。
接下来,通过扩散作用,活化元素和氮化元素会渗透到钢铁表面,将表面化学成分改变。
在冷却过程中,元素以固溶的方式重新结晶成固态,将表面形成的导电活性相和氮化物相紧密地结合到钢铁基体上。
二、操作注意事项:1.清洁工件表面:在进行盐浴处理前,需要对工件的表面进行彻底的清洁。
不论是钢铁还是其他金属,表面都不能有油脂、灰尘等杂质,以保证盐浴能够与金属表面充分接触。
2.控制处理温度:QPQ盐浴处理需要在高温下进行,一般温度控制在500-630℃之间。
过低的温度会导致盐浴无法充分融化,而过高的温度则可能引发工艺问题,如产生过多的氧化物。
因此,在进行处理时,必须控制好温度。
3.控制处理时间:处理时间的长短对成品件的性能有着很大的影响。
处理时间过长会导致过多的元素溶解,降低处理质量,而处理时间过短则可能无法形成完整的合金层。
因此,需要根据工件种类和要求来合理控制处理时间。
4.进行氮化后处理:盐浴处理完成后,工件的表面通常会有一层粗糙的氮化层,需要进行后处理才能得到满意的结果。
后处理可以包括机械去皮、打磨、表面处理等步骤,以提高工件的外观质量。
5.对设备的要求:QPQ盐浴处理的设备应具备高温工作能力和良好的控温性能。
盐浴处理中产生的气体和废液也需要妥善处理,以避免对环境和人体的伤害。
QPQ盐浴及质量控制
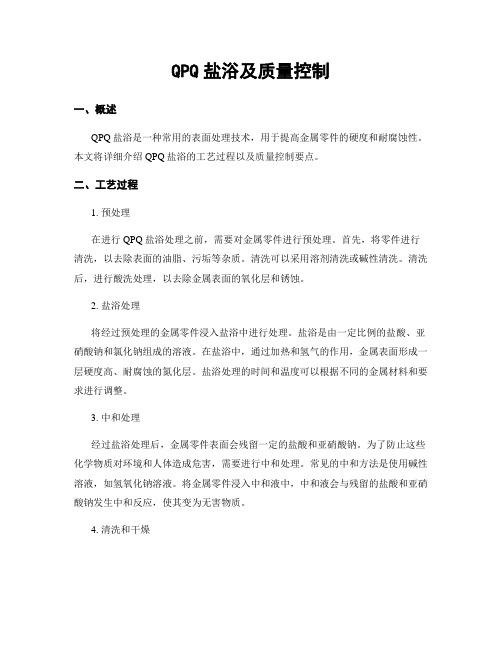
QPQ盐浴及质量控制一、概述QPQ盐浴是一种常用的表面处理技术,用于提高金属零件的硬度和耐腐蚀性。
本文将详细介绍QPQ盐浴的工艺过程以及质量控制要点。
二、工艺过程1. 预处理在进行QPQ盐浴处理之前,需要对金属零件进行预处理。
首先,将零件进行清洗,以去除表面的油脂、污垢等杂质。
清洗可以采用溶剂清洗或碱性清洗。
清洗后,进行酸洗处理,以去除金属表面的氧化层和锈蚀。
2. 盐浴处理将经过预处理的金属零件浸入盐浴中进行处理。
盐浴是由一定比例的盐酸、亚硝酸钠和氯化钠组成的溶液。
在盐浴中,通过加热和氢气的作用,金属表面形成一层硬度高、耐腐蚀的氮化层。
盐浴处理的时间和温度可以根据不同的金属材料和要求进行调整。
3. 中和处理经过盐浴处理后,金属零件表面会残留一定的盐酸和亚硝酸钠。
为了防止这些化学物质对环境和人体造成危害,需要进行中和处理。
常见的中和方法是使用碱性溶液,如氢氧化钠溶液。
将金属零件浸入中和液中,中和液会与残留的盐酸和亚硝酸钠发生中和反应,使其变为无害物质。
4. 清洗和干燥中和处理后,金属零件需要进行清洗和干燥。
清洗可以采用水洗或溶剂清洗的方式,以去除中和液的残留物。
清洗后,将零件进行干燥,以防止水分对金属表面的腐蚀。
三、质量控制要点1. 盐浴配方QPQ盐浴的配方对于处理效果至关重要。
合理的配方可以保证形成均匀、致密的氮化层。
盐酸、亚硝酸钠和氯化钠的比例需要根据不同的金属材料和要求进行调整。
此外,盐浴的浓度和温度也需要严格控制。
2. 处理时间和温度QPQ盐浴处理的时间和温度对于氮化层的形成和性能有着重要影响。
过短的处理时间会导致氮化层的硬度和耐腐蚀性不达标,而过长的处理时间则可能导致氮化层过厚,影响零件的尺寸精度。
温度过高或过低也会影响氮化层的质量。
因此,在实际操作中,需要根据金属材料和要求确定合适的处理时间和温度。
3. 中和效果中和处理的效果直接影响到QPQ盐浴处理后的金属零件质量。
中和液的浓度、浸泡时间和搅拌方式都会影响中和效果。
QPQ盐浴及质量控制

QPQ盐浴及质量控制一、介绍QPQ(Quench-Polish-Quench)是一种常用的表面处理技术,通过在高温下淬火、抛光和再淬火的过程中,形成一层坚硬的氮化物层,以提高金属件的表面硬度、耐磨性和腐蚀性能。
本文将详细介绍QPQ盐浴工艺及其质量控制。
二、QPQ盐浴工艺1. 盐浴配方盐浴是QPQ工艺的核心环节,合理的盐浴配方能够保证工艺的稳定性和成品的质量。
一种常用的盐浴配方如下:- 碳化钠(NaCN):30%;- 硝酸钠(NaNO3):30%;- 碳酸钠(Na2CO3):25%;- 氯化钠(NaCl):15%。
2. 工艺步骤QPQ盐浴工艺主要包括以下步骤:- 预处理:将金属件进行去油、除锈等表面处理,确保表面干净。
- 盐浴浸泡:将金属件浸入预热至500°C的盐浴中,保持一定时间,使金属表面发生化学反应。
- 淬火:将浸泡后的金属件迅速冷却至室温,形成氮化物层。
- 抛光:对淬火后的金属件进行抛光处理,提高表面光洁度。
- 再淬火:再次将金属件浸入盐浴中进行淬火处理,增加氮化物层的硬度。
三、QPQ质量控制1. 盐浴温度控制盐浴温度是影响QPQ工艺效果的重要因素,应严格控制在500°C摆布,过高或者过低都会影响氮化物层的形成和质量。
2. 盐浴浸泡时间控制盐浴浸泡时间决定了氮化物层的厚度,普通在30-90分钟之间,过长或者过短都会影响氮化物层的硬度和均匀性。
3. 淬火速度控制淬火速度应尽可能快,以确保氮化物层的形成,但过快的冷却速度可能导致金属件变形或者开裂,需要根据具体金属材料进行调整。
4. 抛光质量控制抛光过程中,应确保金属表面光洁度达到要求,避免浮现划痕、气泡等缺陷。
5. 再淬火时间控制再淬火时间普通在5-15分钟之间,过长会导致氮化物层变脆,过短会影响氮化物层的硬度。
6. 检测与评估完成QPQ工艺后,需要对成品进行质量检测和评估。
常用的检测方法包括硬度测试、厚度测量、耐腐蚀性测试等,以确保产品符合要求。
QPQ盐浴及质量控制

QPQ盐浴及质量控制一、介绍QPQ盐浴是一种常用的表面处理技术,用于提高金属工件的硬度、耐磨性和耐腐蚀性。
本文将详细介绍QPQ盐浴的工艺流程和质量控制要点。
二、工艺流程1. 准备工作在进行QPQ盐浴处理之前,需要对金属工件进行清洗和预处理。
清洗过程可以采用碱洗、酸洗等方法,以去除表面的油脂、氧化物和其他污染物。
预处理包括除锈、退火等步骤,以确保金属表面的纯净度和均匀性。
2. 盐浴处理a. 盐浴配制:根据工件的材料和要求,选择合适的盐浴配方。
常用的盐浴配方包括氰化盐、氯化盐和硝酸盐等。
b. 盐浴预热:将盐浴加热至适当的温度,通常在250-500摄氏度之间,以确保工件能够均匀地吸收盐浴中的元素。
c. 工件浸泡:将预处理过的金属工件浸入盐浴中,保持一定的时间,使其与盐浴中的元素发生反应。
d. 盐浴冷却:将工件从盐浴中取出,进行冷却处理,以使其表面形成一层硬度高、耐磨性强的层。
3. 后处理a. 清洗:将经过QPQ盐浴处理的工件进行清洗,去除表面的残留盐浴和其他污染物。
b. 中和处理:将工件浸泡在中和液中,中和盐浴残留的酸碱性物质,以防止其对环境和工件造成损害。
c. 涂层处理:根据需要,对工件进行涂层处理,以增加其耐腐蚀性和美观度。
d. 检验:对经过QPQ盐浴处理的工件进行质量检验,包括硬度测试、耐磨性测试和耐腐蚀性测试等。
三、质量控制要点1. 盐浴配方控制:根据工件的材料和要求,选择合适的盐浴配方,并确保其配比准确。
2. 温度控制:盐浴的温度对工件的处理效果有重要影响,需要控制在适当的范围内,以保证处理效果的稳定性。
3. 时间控制:工件在盐浴中的浸泡时间应根据工件的大小和要求进行合理控制,过长或过短的时间都会影响处理效果。
4. 清洗控制:清洗过程中要确保去除盐浴和其他污染物的彻底性,以免对工件的后续处理和性能产生负面影响。
5. 中和处理控制:中和液的配制和使用要符合相关标准,以防止对环境和工件造成损害。
QPQ盐浴及质量控制

QPQ盐浴及质量控制一、介绍QPQ盐浴是一种常用的表面处理工艺,用于提高金属零件的耐腐蚀性和磨损性能。
本文将详细介绍QPQ盐浴的工艺流程和质量控制措施。
二、工艺流程1. 准备工作在进行QPQ盐浴处理之前,需要对待处理的金属零件进行准备工作。
首先,对零件进行清洗,去除表面的油污和杂质。
然后,进行预处理,包括去除氧化层和磷化处理,以增加金属表面的粗糙度和吸附性。
2. 盐浴处理将经过准备的金属零件浸入预热的盐浴中,通常使用氰化钠和氰化钾的混合物作为盐浴。
控制盐浴的温度、浸泡时间和浓度,以确保金属表面形成硬质的氮化物层。
盐浴处理的时间和温度会影响氮化层的厚度和硬度。
3. 淬火处理盐浴处理后,将金属零件迅速冷却,以使氮化物层变得更加坚硬和耐磨。
淬火处理可以通过水冷或油冷的方式进行。
4. 清洗和润滑经过淬火处理的金属零件需要进行清洗和润滑,以去除表面的盐渍和残留物,并提供良好的润滑性能。
三、质量控制措施1. 温度控制在QPQ盐浴处理过程中,严格控制盐浴的温度是确保氮化层质量的关键。
通过使用温度传感器和自动控温装置,可以实时监测和调节盐浴的温度,保持在适宜的处理温度范围内。
2. 盐浴浓度控制盐浴的浓度也是影响氮化层质量的重要因素。
通过定期检测盐浴的浓度,并根据检测结果进行调整,可以确保盐浴的浓度在合适的范围内。
3. 盐浴寿命管理盐浴的寿命是指盐浴能够保持良好处理效果的时间。
通过定期检测盐浴的耗损情况和盐浴的化学成分,可以判断盐浴的寿命,并及时更换盐浴,以保证处理效果的稳定性。
4. 氮化层质量检测对经过QPQ盐浴处理的金属零件,需要进行氮化层质量的检测。
常用的质量检测方法包括显微硬度测试、金相显微镜观察、耐蚀性测试等。
通过对氮化层质量的检测,可以确保处理效果符合要求。
5. 零件尺寸控制在QPQ盐浴处理过程中,需要对金属零件的尺寸进行控制。
通过使用合适的夹具和测量工具,可以确保金属零件的尺寸符合要求。
四、总结本文详细介绍了QPQ盐浴及质量控制的相关内容。
QPQ盐浴及质量控制

QPQ盐浴及质量控制一、任务背景QPQ盐浴是一种常用的表面处理工艺,广泛应用于汽车、机械、航空航天等领域。
它通过在高温下将金属零件浸泡在含有盐类和氰化物的溶液中,形成一层硬度高、耐磨、耐腐蚀的氮化层,从而提高金属零件的表面硬度和耐磨性能。
二、工艺流程1. 预处理:将金属零件进行表面清洗,去除油污、铁锈等杂质,以确保后续工艺的顺利进行。
2. 盐浴处理:将清洗后的金属零件浸入预先配置好的盐浴溶液中,进行高温处理。
盐浴溶液中的盐类和氰化物会在高温下分解,释放出氮气,与金属表面发生反应生成氮化层。
3. 冷却:将处理完的金属零件从盐浴中取出,进行冷却。
冷却过程中,要确保金属零件的温度逐渐降低,避免产生应力和变形。
4. 清洗:将冷却后的金属零件进行清洗,去除残留的盐浴溶液和氮化层表面的杂质。
5. 检验:对处理后的金属零件进行质量检验,包括硬度测试、腐蚀性能测试等。
三、质量控制1. 盐浴溶液的配制:盐浴溶液的配制是影响QPQ工艺效果的重要因素之一。
配制过程中应严格控制盐类和氰化物的浓度、溶液的温度和PH值等参数,以确保溶液的稳定性和一致性。
2. 温度控制:QPQ工艺中的高温处理对于氮化层的形成至关重要。
在盐浴处理过程中,应确保金属零件达到适宜的处理温度,并且保持一定的时间,以确保氮化层的质量。
3. 冷却控制:在金属零件处理完毕后,应进行适当的冷却控制。
过快的冷却速度可能导致金属零件的变形和应力集中,影响氮化层的质量。
因此,应采取适当的冷却方法和时间,确保金属零件的温度均匀降低。
4. 清洗控制:清洗过程中要使用合适的清洗剂,彻底去除残留的盐浴溶液和杂质。
同时,要控制清洗的时间和温度,避免对氮化层造成损害。
5. 检验控制:对处理后的金属零件进行全面的质量检验,包括硬度测试、腐蚀性能测试等。
检验结果应符合相关标准和规范,确保氮化层的质量和性能。
四、关键参数及标准1. 盐浴溶液配制:盐类和氰化物的浓度应控制在合适的范围内,具体数值可根据工艺要求和实际情况进行调整。
QPQ技术讲义

QPQ盐浴复合处理技术(讲稿整理)1.性能特点:高耐磨、高耐蚀、微变形2.工艺流程:清洗―→预热―→氮化―→氧化―→清洗―→抛光―→氧化―→清洗―→自检―→浸油―→转序。
2.1清洗方式:①. 汽油清洗:单独用汽油清洗时,应洗2~3遍。
②. 金属清洗剂:油污严重的可用汽油先洗一遍,再用清洗剂洗净。
③. 喷砂:工件有锈蚀且外观要求较高者,根据需要选择粗砂或细砂吹洗。
④. 酸洗:锈蚀较轻者可用酸洗,基本不伤害表面及尺寸要求。
2.2 装卡:①. 装卡的原则:减少工件变形、获得均匀渗层;②. 装炉量:以φ500×700坩埚、工件预热370℃为例,装炉量对浴盐温度的影响为:2.3. 预热:目的在于烘干、减少入炉温降幅度,高合金钢与截面变化大的工件预热尤为重要。
一般钢材在300~400℃×20~60min预热呈现浅蓝或天蓝色为宜。
预热缺陷:白色为预热不足、黑色为预热过渡。
2.4氮化工艺:本所复合处理用氮化盐位SSG型,适用于470~650℃温度范围,常用最佳温度580℃;工具钢为保留心部较高硬度,一般用520℃处理;高速钢在540~550℃处理;时间因件而异,可在5~180min区间选择。
工艺参数选用原则:确保不降低心部硬度及控制最小变形。
氰酸根浓度:30~38%CN为宜,必须及时化验。
浴盐的维护:Ⅰ. 理论指导:⑴. 保持30~38%CN值,化验发现低于30%CN时,要加再生盐调整。
以坩埚盐容量为基数,每加1%的再生盐,可提升0.6% CN浓度。
⑵. 液面下降时,用基盐补充。
φ500×700坩埚加200kg浴盐可达深度60cm 左右,即:每降低3cm液面,应加入浴盐10kg。
⑶. 清渣:①.积极措施:尽量把造渣因素留在路外(清晰、选用钛合金坩埚等)。
②. 消极办法:用沉渣器捞渣。
使用降温沉渣法原理:渣重盐轻;断电消除电磁搅拌;保证足够的沉淀时间40~60min;有一定的降温区间:从580℃降至500℃清渣。
QPQ盐浴及质量控制

QPQ盐浴及质量控制一、概述QPQ盐浴是一种常用的表面处理技术,用于提高金属制品的耐腐蚀性能和表面硬度。
本文将详细介绍QPQ盐浴的工艺流程以及质量控制措施。
二、工艺流程1. 清洗预处理在进行QPQ盐浴处理之前,首先需要对金属制品进行彻底的清洗预处理。
清洗的目的是去除表面的油污、金属屑和其他杂质,以确保QPQ盐浴处理的效果。
2. 盐浴处理a. 盐浴淬火将清洗干净的金属制品浸入预热至适宜温度的盐浴中,通入适量的氮气或氨气,使金属制品表面形成一层氮化物层。
b. 盐浴氧化将经过盐浴淬火处理的金属制品转移到预热至适宜温度的氧化盐浴中,使金属表面形成一层黑色的氧化层。
3. 冷却处理在盐浴氧化处理完成后,将金属制品从盐浴中取出,进行冷却处理。
冷却处理可以通过水冷却或风冷却的方式进行。
4. 清洗后处理经过冷却处理后,金属制品需要进行清洗后处理,以去除表面的氧化层和其他残留物。
三、质量控制1. 温度控制在QPQ盐浴处理过程中,盐浴的温度是非常关键的参数。
需要根据金属材料的种类和要求的性能来确定盐浴的处理温度。
温度过高或过低都会影响氮化物层和氧化层的形成,从而影响最终的质量。
2. 盐浴成分控制盐浴的成分也是影响QPQ处理效果的重要因素。
需要控制盐浴中的盐类、氮化剂和氧化剂的含量,以保证金属制品表面形成均匀的氮化层和氧化层。
3. 盐浴浓度控制盐浴的浓度也需要进行严格的控制。
浓度过高会导致氮化层和氧化层过厚,浓度过低则会影响处理效果。
需要定期检测盐浴的浓度,并进行调整。
4. 处理时间控制处理时间也是影响QPQ处理效果的重要因素。
处理时间过短会导致氮化层和氧化层薄弱,处理时间过长则会导致过度氮化和过度氧化。
需要根据具体情况确定合适的处理时间。
5. 检测方法对于QPQ盐浴处理后的金属制品,可以采用多种检测方法来评估其质量。
常用的方法包括金相显微镜观察、硬度测试、耐腐蚀性能测试等。
6. 质量记录在QPQ盐浴处理过程中,需要对关键参数和处理结果进行记录。
- 1、下载文档前请自行甄别文档内容的完整性,平台不提供额外的编辑、内容补充、找答案等附加服务。
- 2、"仅部分预览"的文档,不可在线预览部分如存在完整性等问题,可反馈申请退款(可完整预览的文档不适用该条件!)。
- 3、如文档侵犯您的权益,请联系客服反馈,我们会尽快为您处理(人工客服工作时间:9:00-18:30)。
QPQ盐浴复合处理技术的基本原理及操作注意事项“QPQ”是英文“Quench—Polish—Quench”的字头缩写。
原意为淬火—抛光—淬火,在国内把它称作QPQ盐浴复合处理技术,其中“盐浴复合”的含义是指在氮化盐浴和氧化盐浴两种盐浴中处理工件。
Q PQ盐浴复合热处理技术既可以使工件几乎不变形,同时又可以大幅度提高金属表面的耐磨性、抗蚀性,是一种新的金属表面强化改性技术。
这种技术实现了渗氮工序和氧化工序的复合,氮化物和氧化物的复合,耐磨性和抗蚀性复合,热处理技术和防腐技术的复合。
我司经过多年的实践独立开发了成分独特的渗氮盐浴配方,其中添加了一种特殊的氧化剂,使盐浴中的有害氰根含量保持在0.2%以下,同时盐浴中的有效成分氰酸根含量长期保持稳定。
试验表明,现有气体软氮化和离子渗氮基本上都可以用QPQ盐浴复合处理技术来代替,而且可以大为提高工件的耐磨性和抗蚀性。
其抗蚀性可达到C u-Ni-Cr多层电镀的水平,成功的应用于气弹簧、刀具、模具、纺织机械、汽车等行业,通过对零件的滑动磨损试验,耐磨性比发黑处理高出几百倍。
通过海水防腐试验,QPQ处理的零件均比发黑处理的零件提高几十倍,效果很好。
由于新技术,所以工艺上就有其独特的要求,操作中必须严格规范,工件才能达到耐磨性和抗蚀性的要求,并得到较为美观的外表(黑亮色)。
下面就工艺中几个关键步骤加以分析讨论:一、QPQ技术的基本工艺过程1、工件清洗---清水漂洗—预热—盐浴氮化—盐浴氧化—冷水冷却—热水浸泡—清水漂洗—烘干—抛光—二次氧化—抛光—包装。
预热(空气炉)350-400℃、20-30min氮化(盐浴炉)550-580℃、60-180min氧化炉(盐浴炉)370-400℃、20-40min预热的作用:预热的作用是烤干工件表面的水分,使冷工件升温后再入氮化炉,以防带水工件入氮化炉后引起盐浴溅射和防止冷工件入炉后氮化炉温度下降太多。
一般温度下降不超过30℃,同时预热对减少工件变形和获得色泽均一的外观也有一定的作用。
氮化:氮化是QPQ盐浴复合处理技术的核心工序,由于氮化盐浴中氰酸根(CNO-)的分解产生活性氮原子,在金属表面形成耐磨和抗蚀性很高的化合物层和耐疲劳的扩散层。
氧化:氧化的主要作用可使工件从氮化炉带出的盐中的氰根(CN-)彻底分解,消除公害,同时在工件表面形成黑色的氧化膜(Fe3O4),增加抗蚀性,对提高耐磨也有一定的好处。
2、渗层外貌及特征QPQ盐浴复合处理以后在钢的表面形成的渗层外貌:最外面是氧化膜,主要成分是(Fe3O4),氧化物层里面是化合物层,也称“白亮层”,主要成分是Fe2-3CN,化合物层以内是扩散层,(1)化合物层:化合物层是QPQ盐浴复合处理技术所形成的渗层中最重要的部分,对渗层的耐磨性和抗蚀性都起主导作用。
通过金相分析,如图S45C和35CrMo在不同的氮化时间的金相图:35CrMo化合物层×400 QP120min 35CrMo化合物层×400 QP100minS45C化合物层×400 QP120min S45C化合物层×400 QP100min在QPQ盐浴复合处理过程中,随着C、N元素的不断渗入,达到一定浓度后,形成了化合物层Fe2-3N和Fe2-3CN,对碳钢基体来说,化合物层的硬度HV0.1/15至少在500以上,对低碳钢及中碳钢经QPQ处理以后,硬度在500-700(单位:Kg/mm2),化合物层即白亮层深度一般在10-25μm(生产工艺不同,渗层也不相同)。
合金钢如;38CrMoAl、5CrMnMo等氮化钢,硬度达到900-1100。
渗层在9-15μm,化合物层是耐磨、抗蚀的核心渗层,所以在做渗层检查时,都以检测化合物层为主,化合物层的深度与工艺条件(CNO%浓度、氮化时间及氮化温度)影响较大。
在工艺条件相同的时,化合物层的深度主要取决于合金元素的含量,对于高合金钢硬度高,不但渗层浅而扩散层也浅。
(2)扩散层扩散层是只在显微镜下观察到的化合物层与中心之间那层暗黑色组织。
由于氮的浓度由表面向中心逐步降低,到化合物层与扩散层交界处,氮的浓度下降到不足以形成化合物层,而只能形成氮在α-Fe 晶格中的固溶体或过饱和固溶体,这一层氮在α-Fe中的固溶体就是扩散层,由于它的抗蚀性不高,所以在显微镜下呈暗黑色。
(3)氧化膜工件经过氮化工序处理后在氧化盐浴保温时才会在表面形成氧化膜。
这种氧化膜只有在氮化处理后的表面上才比较容易形成,如果未作氮化处理的工件直接进入氧化盐浴中,则不能形成完整的氧化膜。
这可能与氮化处理后工件表面的活性状态有关,氧化膜的厚薄也与工件的预先氮化状态有关,对于大多数结构零件,氮化后表面形成较厚的氧化膜,氧化膜的抗蚀性很好,氧化膜在显微镜下呈灰白色,与化合物层极为相似,对结构钢样品,很难观察到。
但是试样外面的的黑色外观说明氧化膜确实存在,同时也由于化合物层外层常常存在疏松,氧化膜与化合物层之间没有明显的过渡,在制备金相时很难区分,因此只有在电子显微镜下才能看到这层氧化膜。
氧化工序不仅在工件的化合物层以外形成氧化膜。
而且化合物层也吸收了高达8%的氧,这比一般盐浴氮化后水冷的化合物层中的含氧量高6倍,即在氧化过程中不仅在表面生成氧化膜,还有一部分氧以间隙式形式溶入化合物晶格中使表面钝化。
改善了表面的抗蚀性和耐磨性。
工件经过氮化-氧化后再次抛光以后,不仅降低了工件表面的粗糙度,是其外表变得赏心悦目,更重要的是抛光后再次氧化可以大大提高化合物层中的含氧量,从而进一步提高抗蚀性。
(4)疏松层通常在QPQ盐浴复合处理以后,化合物层外面往往有一层海绵状或柱状的多孔组织,这一区域不是特别致密,一般称为疏松层,这层组织硬度低,耐磨性差,疏松层不仅盐浴处理技术有,而且气体氮化也会形成疏松。
而且疏松层更加严重。
二、QPQ盐浴复合处理技术的渗层性能1、极高的耐磨性在实验室进行的严格的滑动磨损试验表明,40Cr钢经过QPQ处理以后,耐磨性可以达到常规淬火的30倍,低碳钢渗碳淬火的14倍,离子氮化的2.8倍,镀硬铬的2.1倍。
2、极好的抗蚀性在潮湿的环境下,工件进行了露天遮雨放置试验,45(S45C)钢经QPQ处理后,抗蚀性可以达到镀硬铬的16倍。
1Cr13不锈钢的26倍,1Cr18Ni9Ti不锈钢的4.5倍。
3、良好的抗疲劳性能QPQ处理可以使钢、铁材料的疲劳强度提高20-200%,疲劳强度提高的大小受基体材料的种类、预先处理状态、QPQ处理的工艺参数等因素的影响。
4、极微小的变形由于QPQ技术的处理温度低于钢的相变温度、处理过程基体不会发生组织转变,因此没有组织应力产生,所以它比发生组织转变的常规淬火、高频淬火、渗碳所产生的变形小得多。
在正常的情况下,处理前后工件尺寸的变化量大约在0.01mm左右,外径增大0.005mm,内孔缩小0.005mm。
三、QPQ盐浴复合处理技术的实际操作及常见问题1、清洗:除油、去锈,切削时冷却润滑油以及某些金属清洗剂的残留物,在工件表面上以表膜的形式存在,微区分析说明,有磷酸盐,硅酸盐、钙、镁、氯、氧、硫等元素的化合物存在,会阻碍工件表面对氮和碳的吸收。
2、预热:工件不预热或预热不充分,直接进入氮化炉,处理后,外观容易不均匀,甚至产生芝麻点等表面缺陷,如果预热过度,处理后也会产生色泽不均匀,甚至发红等现象。
工件表面呈紫色为好,草黄色也可,工件仍保持金属光泽,说明预热不足,工件表面黑色,说明预热过度。
3、氮化:氮化是QPQ盐浴复合处理技术中最重要的工序,氮化的目的是在工件表面形成足够深的致密的化合物层和相应深度的扩散层。
氮化盐浴中 CNO—控制在33-37%,当CNO—<30%时,会降低渗层的形成速度。
如果CNO—>40%时,则容易形成渗层不致密,甚至造成严重的疏松,,调整盐以每班少量多次添加为好,这样不会造成CNO—大起大落,不宜一次添加过多,这样会影响渗层的致密度。
4、氮化炉的维护:保持氮化炉盐浴的良好状态、对渗层质量有很大的影响,带有赃物、油脂、或铁锈的工件不准进入氮化炉内,铜铝、锌等有色金属件不准进入氮化炉,大批量的铜焊件不宜进入氮化炉,装工具的卡具及常用的工具要保持清洁。
不宜带杂物进入氮化炉。
要及时清除氮化炉内的炉渣,,对保证化合物层的致密度极为重要。
每班及时捞取氮化炉的悬浮的细渣及底部的沉渣(氧化皮),要及时补充新基盐,要保证盐浴成分的活性,同时要定时向氮化炉通气,以加速CNO—的分解,盐浴液面要保持一致,不要忽低忽高。
5、氧化炉的维护:从氮化炉出来的工件不能在空气中停留时间过长,否则,氧化后的工件可能产生表面发红现象。
在生产过程中,氧化盐浴不断与带入的氮化盐发生分解反应,生成碳酸盐渣产物,同时氧化盐浴还会与卡具反应,生成红色的Fe2O3,使盐浴老化,发红。
如果氧化盐浴上面有快状的浅黄色物体悬浮,似凝非凝,表明氧化盐浴已经老化,要及时更换新盐浴。
6、工件表面颜色不均匀(!)、处理前,工件表面有油污、锈迹及赃物或附着清洗剂的残留物。
(2)、工件预热温度低,或预热时间短,预热后工件仍保持金属光泽(3)、工件从氮化炉出来,进入氧化炉时,没有匀速下降,或在空气中停留时间过长。
(4)、氧化盐浴已老化,发红渣多;(5)、氧化盐炉或氮化盐炉表面有浮渣、赃物。
7、工件使用时耐磨性能不够(1)、渗层硬度低;(2)、渗层浅;(3)、化合物层疏松严重。
(4)、基体材料选择不当;(5)、热处理工艺参数选择不当,氮化时间短、处理温度低或CNO—浓度低。
8、工件抗蚀性差(1)化合物层浅或化合物层不连续,局部无化合物层。
(2)、化合物层外面的疏松层占化合物层的大部分;(3)工件在处理前局部有锈剂,处理时未除掉,处理后成为腐蚀源;(4)、氧化工序未搞好,工件表面发红,这种氧化物以后成为腐蚀源。
(5)、工件氮化时间、或处理温度低或CNO—浓度低。
9、渗层浅或渗层不均匀(!)、在制备金相时化合物层保护不好或试样倒棱使化合物层部分剥落,在显微镜下只能观察到化合物层的残留部分。
(2)工件表面除油不彻底、表面有锈迹杂物或不锈钢、耐热钢表面的钝化膜未去掉,造成局部无渗层或渗层过浅。
(3)、CNO—浓度低,氮化温度低,或保温时间短,(4)、化合物层外面的疏松层太厚,化合物层只占渗层的小部分。
总之,热处理过程中盐浴成分非常复杂,具体问题要具体分析,不再一一举例。
1、外观质量控制经QPQ盐浴复合处理的工件表面呈黑色或蓝黑色。
检验标准:按专利技术文件的规定为:在500LX的照度下,距灯300mm肉眼观察,表面颜色应比较均匀一致,不得有明显的花斑、锈迹、发红。
而不应在室外强烈阳光下检查工件外观。
生产中发现,熔盐和工艺稍有控制不好时,工件易产生发花、发红现象,尤其是材料含Si量多时,如27SiMn、30CrMnSi等材料,工件外表发花、发红现象极多,虽然此现象不影响工件的耐磨和抗蚀性,但影响工件的美观。