汽车前驱主减速器柔性装配线的设计
机械设计—学做一体化课件:减速器装配图的设计

减速器装配图的设计
应注意,轴段长度一般不与轴上相配零件宽度相等,以保 证轴向压紧。
决定轴承座的宽度L 时,除应考虑轴承座两旁连接螺栓 的扳手空间位置外,还应考虑轴 承的润滑方式、有无挡油环、 封油环及轴承端盖结构所需位置的大小。一般情况下,低速 轴 轴承较宽,故画图时应先从低速轴轴承画起,并使高速轴和 中间轴的轴承座宽与低速轴轴承 座宽度相等,从而使各轴承 座外端面在同一平面上,以便于一块加工(刨或铣)。在这一阶 段 绘制的一级圆柱齿轮减速器如图10-2所示。
减速器装配图的设计
② 键的选择计算。轴与齿轮、带轮、联轴器等的连接 常用普通平键,其尺寸可根据轴的 直径选取。键的长度可根 据轮毂的宽度从键的长度系列值中选取,键长一定要比轮毂 的宽度 稍短一些。然后验算键的挤压强度,如果验算结果强 度不足,可增加键的长度(但不得超过轮 毂宽度)或改用两个 键(互成120°或180°),或增大轴的直径,以满足强度要求。 使用两个键 时,考虑到各键受载不均,其承载能力应按单键的 1.5倍计算,即在验算挤压强度时,将许 用挤压力提高1.段的主要工作是设计轴系部件(包括轴上所有零 件及与轴承组合有关的零件)。 (1)传动件的结构设计。 当小齿轮齿根圆(锥齿轮为小端 根圆)到键槽顶面的距离a≤(2~2.5)mm 时,应采用齿 轮与轴做 成一体的轴齿轮,此时俯视图中的大齿轮采用全剖视而小齿 轮只能采用局部剖,以 表明两齿轮 的 啮 合 情 况。若 为 斜 齿 轮,则 应 在 小 齿 轮 未 剖 外 形 部 分 用 三 条 细 线 画 出 齿 斜方向。
减速器装配图的设计
减速器装配图的设计
3.绘图准备 1)选择图纸幅面 装配图用 A0或 A1号图纸绘出,图纸幅 面及图框格式应符合机械制图标准。 2)选择视图 一般减速器选用三个视图(正视图、俯视图 和侧视图),结构简单者可选用两个视图及必 要的剖视和局部 视图来表达。
柔性智能装配生产线的设计与实现

柔性智能装配生产线的设计与实现近年来,伴随着工业智能化的不断推进,柔性智能装配生产线的应用越来越广泛,成为未来工业生产的热门话题。
在智能制造领域,柔性智能装配生产线是一种基于智能化技术的高效、精确和自动化生产方式,可以适应不同生产需求的变化,并且具备快速反应和高自适应性能的生产线。
本文将着重介绍柔性智能装配生产线的设计与实现,分享柔性产线实际应用的经验和思路,希望能够对智能制造领域的研究者和实践者有所启示。
一、柔性智能装配生产线的概念和特点柔性智能装配生产线是指一种在自动化生产过程中具备智能化技术、可变性和高灵活性的生产线,能够快速响应不同需求的变化,并能够快速调整生产节奏和产品种类。
柔性智能装配生产线主要包括了机器人技术、智能传感技术、自适应控制技术和信息技术等多种领域的技术,能够完成高效、高精度的生产。
在具体应用中,柔性智能装配生产线可以优化生产流程,提高生产效率和产品质量,并大大减少了人工干预,降低了生产成本。
二、柔性智能装配生产线的设计思路1.需求分析在设计柔性智能装配生产线时,首先需要进行需求分析。
需求分析是确保柔性产线能够满足生产需求的关键步骤,需要明确生产线的生产规模、生产种类、产品变化和生产要求等细节问题,以确定设计目标和实现路径。
2.流程设计流程设计是柔性智能装配生产线设计的重要环节,可以根据需求分析和利用工艺流程图等工具,确定机器人、工人和设备之间的生产流程。
在具体操作中,需要充分考虑生产过程中的各种情形和故障,同时注意安全和质量问题。
3.系统设计系统设计是实现柔性智能装配生产线的关键环节,包括机器人和设备控制、物料传输控制、生产调度系统、质量控制系统和安全控制系统等多个部分。
在系统设计中,需要充分考虑生产过程中的各种情形和故障,同时使用可靠的技术方案和优化的算法,以确保生产线的可靠性和高效性。
此外,系统设计中也需要注意生产线的可维护性和可扩展性。
4.设备选型设备选型是柔性智能装配生产线设计的关键环节,需要根据生产要求和技术方案,选择合适的机器人、传感设备和计算机控制设备等。
减速器总成装配线新工艺设计

汽/ r : 1 桥 减 速 器总成 的新 装 配线 项 H I f J , 采H j 新 【 艺、 新技 术 、 提 升 减速 器总成 品质 保障 能
力, 为客 户提 供优 质 产 品 该项 H从 项 到 减 速 总成 装 配线 交付 公 刊批 碴尘 产 , 历时 2 年, 减 速 器 总成 的符项 技 术指标 均达 到 陔项 日的设 定 H标
-
在 减 速器 总 成 的 装配 过 程 中 , 必 须 对其 差 速 器功 能进行 1 0 0 % 检测 。传统 的检测方 式是在差 速 器总 成装 配 完 成后 , 人 T : 使用 T 具 检测 差 速器 功
能, 并检 测行 星齿 轮 及半 轴齿 轮 的 装配状 态是 否 满 足产 品 的设 计 要 求 采 用此 种 检测 方 式 , 如 果
动 力客 / r : 以及新 能 源 汽 乍 言 , 汽车 车桥 的低 噪 平稳运行 , 成 为 客 户 的 基 本需 求 ; 对 于 程
、
牵引车 、 k途 载 货汽 1 i f 言 . 汽乍 乍桥 的较 强
}
承载 能 力 、 免维护 周期 长等指 标 , 已 成为 各 乍厂 及终 端客 户的 要需 求 。
.
土 生 产 产 懊 瑛 l 塌 。
减 速 器 总 成装 配 线 新 工 艺 设 计
裴照明 谢锋 吴先 芹
( 尔 风德纳 年桥 有 限公 十堰 )
摘要 : 为 保 障 减速 器 总成 存 生 产 过 程 巾 品 质得 到 保 障 , 装酣 l 没 汁过 『 f l , 对轴 承 的 安装要求 、 差 速 器 总 成 的差 速 功 能 榆 控 、 主 动 锥 轮起 动 力矩 的装 j 』 I i l 】 可靠性 、 动 锥 轮 ^ 乏 从
自协调多柔性并行装配线的设计与研发

自协调多柔性并行装配线的设计与研发1.装配线的概念与优势:装配线是一种将产品的不同组件在制造过程中逐步装配完成的生产方式。
相比于传统的单线装配方式,多柔性并行装配线具有更高的灵活性和生产效率。
多柔性并行装配线能够自动协调不同任务之间的优先级,实现资源的最优分配,提高生产效率和产品质量。
2.装配线的设计原则:设计自协调多柔性并行装配线需要考虑的原则包括:产品种类的灵活性、任务分配和资源分配的均衡、信息交互的可靠性和实时性、设备和工人的安全等。
通过合理的设计原则,使装配线能够适应不同的产品种类和任务需求,提高生产效率和灵活性。
3.装配线任务调度算法:装配线的任务调度是指将不同任务分配给不同的工作站,并协调它们之间的完成顺序。
在设计自协调多柔性并行装配线时,需要借助任务调度算法来实现任务的自动分配和优先级的调整。
其中,常用的任务调度算法包括遗传算法、模拟退火算法、粒子群算法等,它们能够根据装配线的状态和任务需求实时调整任务分配和优先级。
4.装配线控制系统的设计与开发:装配线的控制系统是实现装配线自协调的关键。
在装配线的设计与研发过程中,需要开发装配线控制系统,实现任务调度、资源分配、设备控制和产品追溯等功能。
通过合理的控制系统设计和开发,可以实现装配线的自动协调和生产过程的实时监控。
5.装配线的实验验证与优化:设计与研发完成后,需要进行实验验证和优化。
实验验证可以通过模拟装配线运行,根据实际的任务需求和资源情况来评估装配线的效果。
同时,还可以通过实验数据来优化装配线的设计和任务调度算法,进一步提高装配线的效率和灵活性。
综上所述,自协调多柔性并行装配线的设计与研发涉及到装配线的概念与优势、装配线的设计原则、装配线任务调度算法、装配线控制系统的设计与开发以及装配线的实验验证与优化。
通过合理的设计与研发过程,可以实现装配线的自协调,提高生产效率和产品质量。
汽车驱动桥主减速器装配工艺设计分析

汽车驱动桥主减速器装配工艺设计分析驱动桥是车辆的重要组成部分,一般由桥壳、主减速器、差速器、半轴、轮边减速器等组成。
汽车驱动桥处于动力传动系的末端,其基本功能是增大由传动轴或变速器传来的转矩,并将动力合理地分配给左、右驱动轮,另外还承受作用于路面和车架或车身之间的垂直力、纵向力和横向力。
因此,汽车生产商一般都会对每一批驱动桥进行可靠性试验,以考核驱动桥的质量。
1、主减速器和差速器的主要零件清单根据零件模糊语义配合关系确定驱动桥中主减速器和差速器存在的零件。
汽车驱动桥是个很复杂的整体,通过分解、分析并建立各个零件间功能、联接、物理关联关系,确定汽车驱动桥中主减速器及差速器总成的主要零件清单,如表1所示。
表1汽车驱动桥中主减速器的主要零件清单2、驱动桥桥壳垂直弯曲疲劳试验2.1、试验方法驱动桥桥壳承受着复杂的作用力,尤其是在汽车行驶过程中通过不平的路面、车轮与地面间所产生的冲击载荷。
如果桥壳疲劳强度不够,会引起桥壳的变形或断裂。
桥壳垂直弯曲疲劳试验主要是模拟桥壳在实车上的垂向工况,一般取样5件,以中值疲劳寿命不低于80万次、且试验样品中最低寿命不低于50万次来评判。
,将桥壳安装在支架上,支点为该桥轮距的相应点,垂直载荷加载点为二钢板弹簧中心。
安装时加力方向应与桥壳轴管中心线垂直,支点应能滚动,以适应加载变形不致运动干涉。
以驱动桥满载轴荷的2.5倍作为最大载荷,以应力为零时的载荷作为最小载荷,利用液压疲劳试验机施加近似正弦波的交变载荷,频率一般为5~6Hz,直至桥壳破裂。
2.2、失效分析机械零部件在循环载荷的作用下,在某个或者某些应力较大部位产生损伤并且逐渐累积,以致机械性能退化,裂纹产生、扩展直到完全断裂的失效形式,即为疲劳失效。
受到垂向载荷的桥壳,最容易产生疲劳失效的地方是过渡连接的地方,比如说桥壳凸缘与半轴套管过渡区域、板簧位置和桥壳连接焊缝处等。
是垂直弯曲疲劳试验波形曲线,是一款桥壳在28.96万次试验后板簧座下侧旁开裂的情况,是一款桥壳在42.58万次试验后套管与支架处断裂的情况。
柔性制造系统中的自动化装配线设计与应用
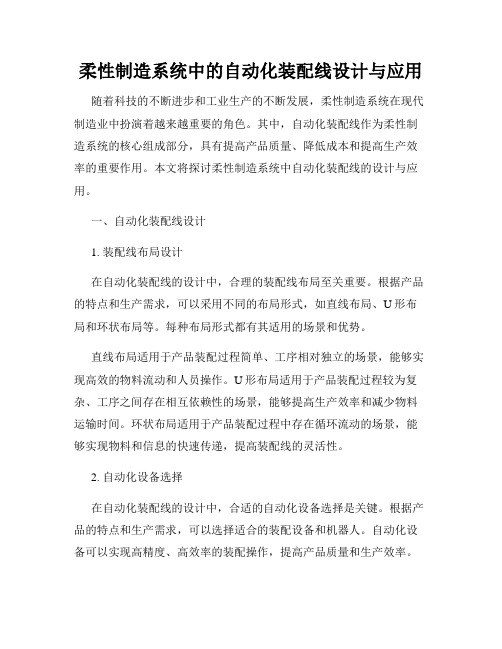
柔性制造系统中的自动化装配线设计与应用随着科技的不断进步和工业生产的不断发展,柔性制造系统在现代制造业中扮演着越来越重要的角色。
其中,自动化装配线作为柔性制造系统的核心组成部分,具有提高产品质量、降低成本和提高生产效率的重要作用。
本文将探讨柔性制造系统中自动化装配线的设计与应用。
一、自动化装配线设计1. 装配线布局设计在自动化装配线的设计中,合理的装配线布局至关重要。
根据产品的特点和生产需求,可以采用不同的布局形式,如直线布局、U形布局和环状布局等。
每种布局形式都有其适用的场景和优势。
直线布局适用于产品装配过程简单、工序相对独立的场景,能够实现高效的物料流动和人员操作。
U形布局适用于产品装配过程较为复杂、工序之间存在相互依赖性的场景,能够提高生产效率和减少物料运输时间。
环状布局适用于产品装配过程中存在循环流动的场景,能够实现物料和信息的快速传递,提高装配线的灵活性。
2. 自动化设备选择在自动化装配线的设计中,合适的自动化设备选择是关键。
根据产品的特点和生产需求,可以选择适合的装配设备和机器人。
自动化设备可以实现高精度、高效率的装配操作,提高产品质量和生产效率。
3. 灵活的控制系统柔性制造系统中的自动化装配线需要具备灵活的控制系统,能够适应生产需求的变化。
传统的PLC控制系统已经无法满足柔性制造系统的要求,因此可以采用基于工业互联网和人工智能技术的控制系统,实现装配线的智能化和自适应。
二、自动化装配线的应用1. 汽车制造汽车制造是自动化装配线应用最广泛的领域之一。
通过自动化装配线,可以实现汽车零部件的高效装配和成品车的生产。
自动化装配线可以提高汽车制造的生产效率和质量稳定性,降低人力成本和生产周期。
2. 电子产品制造电子产品制造也是自动化装配线的重要应用领域之一。
通过自动化装配线,可以实现电子产品的高速装配和测试。
自动化装配线可以提高电子产品制造的生产效率和质量稳定性,降低人力成本和产品缺陷率。
3. 医疗器械制造随着医疗器械的广泛应用,自动化装配线在医疗器械制造中也扮演着重要的角色。
浅谈柔性发动机装配线的规划

1完 美 的规 划 案
同所 有的装 配线 一样 , 它 必 须 满 足节
设 备 自动 化 程 度 的 选 择 直 接 影 响 项 目
托盘设计为双层, 下 层与 传 输 线 配 合 , 上 层 与C / B 精 确定 位 , 定位 的部分 要考 虑更 换 的 方法。 自动 设 备 自带 停止 器 , 自带 托 起 定位
1 1 0 1 7 9 )
摘 要 : 发动机 是汽车 产业技 术最密集的核心零部件, 在 发动机的生产过程中, 装 配线是发动机 最终 状态, 最终精度的展示, 而装配线的规划水
平 一定 程度 上也 代 表 了发动 机 工 厂的 规 划水 平,其重要 性 不 言而嗡 。 那 么怎样 才算是 一个 成 功 的 规 划 , 如 何 才能做 好 装 配线 的规 划, 这 成 为璜 目
主管技术 工作者常常会探讨的课题 。 关键 词 : 柔性发动机 AL C 系统
中图分类号 : U 4 6 8
文献标 识码: A
文章编 号: l 6 7 4 一 o 9 8 x ( 2 0 1 3 ) 0 6 ( b ) 一 0 0 7 7 — 0 2
采 用 自动 设 备 。 其次 , 规 划工 程 师 需 要 根 据 间是 必须 要 考虑 的课 题 。 同完成 给 定 条件 的 如 果 没 有场 地 、 预 算 的限 制 , 理 论 上也 设 计 任 务 和 预 算 整 体定 义装 配 线 的 自动 化 规 划 工作 比 , 预 留扩 展 空间的 水 平 才真正 体 许 存在 最优 的装 配 线 规 划 。 程度, 盲 目地 追 求 自动 是 错误 的 。 现 设 计 师的 实 力。 几点思路: 总 装 传 输 线 的
安装零件 , 实 现 自动 容 易 ; B类 设 备 尽 可 能 旦 产 品改 型非 常有用 。 模块 化 的 布局 和 P L c
柔性制造系统中的自动化装配线设计与实现
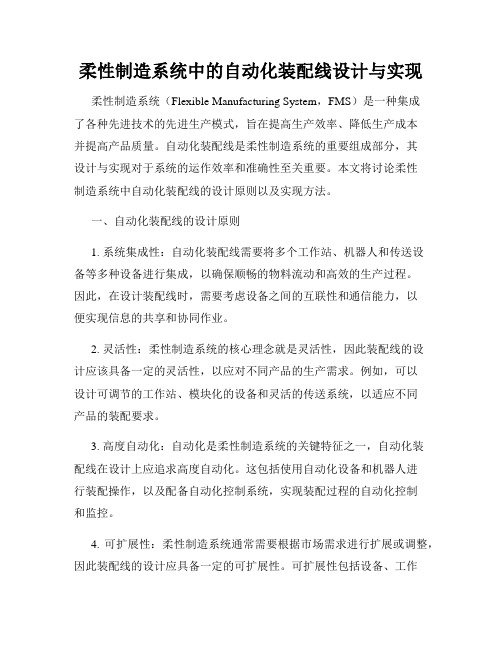
柔性制造系统中的自动化装配线设计与实现柔性制造系统(Flexible Manufacturing System,FMS)是一种集成了各种先进技术的先进生产模式,旨在提高生产效率、降低生产成本并提高产品质量。
自动化装配线是柔性制造系统的重要组成部分,其设计与实现对于系统的运作效率和准确性至关重要。
本文将讨论柔性制造系统中自动化装配线的设计原则以及实现方法。
一、自动化装配线的设计原则1. 系统集成性:自动化装配线需要将多个工作站、机器人和传送设备等多种设备进行集成,以确保顺畅的物料流动和高效的生产过程。
因此,在设计装配线时,需要考虑设备之间的互联性和通信能力,以便实现信息的共享和协同作业。
2. 灵活性:柔性制造系统的核心理念就是灵活性,因此装配线的设计应该具备一定的灵活性,以应对不同产品的生产需求。
例如,可以设计可调节的工作站、模块化的设备和灵活的传送系统,以适应不同产品的装配要求。
3. 高度自动化:自动化是柔性制造系统的关键特征之一,自动化装配线在设计上应追求高度自动化。
这包括使用自动化设备和机器人进行装配操作,以及配备自动化控制系统,实现装配过程的自动化控制和监控。
4. 可扩展性:柔性制造系统通常需要根据市场需求进行扩展或调整,因此装配线的设计应具备一定的可扩展性。
可扩展性包括设备、工作站和传送系统的可扩展性,以及控制系统的可编程性,以便根据需要进行快速调整和改变。
二、自动化装配线的实现方法1. 设备选择:在设计自动化装配线时,需要根据产品的特性和装配需求选择合适的设备。
可以考虑使用工业机器人、自动装配设备和传送带等设备,并确保它们具备高度自动化和可编程的特点。
2. 传送系统:自动化装配线需要一个高效可靠的传送系统,以确保物料的顺畅流动。
可以选择采用传送带、输送机或悬挂链等传送系统,根据装配过程的特点和产品的需求进行选择。
3. 自动化控制系统:自动化控制系统是自动化装配线的核心部分,负责对整个装配过程进行控制和监控。
- 1、下载文档前请自行甄别文档内容的完整性,平台不提供额外的编辑、内容补充、找答案等附加服务。
- 2、"仅部分预览"的文档,不可在线预览部分如存在完整性等问题,可反馈申请退款(可完整预览的文档不适用该条件!)。
- 3、如文档侵犯您的权益,请联系客服反馈,我们会尽快为您处理(人工客服工作时间:9:00-18:30)。
最终确定下来的布局方案称之为支线环绕布局,
如图2。
图2最终整体布局平面规划
3.3
(1)简单化原则:装配线布局要力求简洁,一目了 然,使管理简便,避免复杂化; (2)流向合理,移动最短原则:装配线布局设计要 按照装配工艺流程统一协调,保证物流设计的合理性, 即整个产品装配过程是连续的,中间没有停顿、倒流和 长距离运输; (3)有效利用面积原则:在装配线布局中,要充分 有效地利用面积,设备间隔在保证一定维修空间下尽
[3]
社,2010. 胡宗武.非标准机械设备设计手册[M].北京:机械工业 出版社,2002. [4] 杨叔子.机械加工工艺师手册[M].北京:机械工业出版 社,2008. [5] 龚永平.主减速器装配线的设计与实施[J].大众科技, 2012,(6):150—152. [6] 王树韬.驱动桥主减速器装配工艺的流程改造[J].科技 信息,2007,(27):90—93. [7] 曾亿山.液压与气压传动[M].合肥:合肥工业大学出版 社,2008. [8] 付永领.LMS
Bath)、瑞典的LinkOping大学等研究机构及高 校多年来在静液驱动技术领域都开展了相关研究
sity of
工作‘1圳1。
收稿日期:2012.12-28 作者简介:罗灯明(1968一),男,江西高安人,副教授,工学硕 士,主要从事汽车改装设计及其液压技术方面的科研和教学 工作。
度。在投资有限的条件下,结合公司产品实际,对工艺 和设备进行了优化,是一条比较成功的生产线。
的条件下,能方便地对装配线布置进行调整。在装配
速机总成装配过程中的附加载荷。如图4所示。
线设计阶段,必须对变化因素加以分析,留有余地,以
适应各种变化。
3.1
图4自动线体
初步整体布局设计方案 该方案结合了公司内的物流走向以及所装配产品
本输送线体具有以下特点:①自动线采用摩擦滚 轮传递,当托盘遇阻碍时,和托盘接触的滚轮停止转 动,内衬和轴摩擦转动,摩擦滚轮有效保护操作人员失 误造成的托盘带来的伤害;②输送线可完全互换,通 用性好;③输送线高度适当,适合当地身高水平,符合 人体工程学;④在输送线线体侧面根据需要,设计能 够装挂小零件料盒的料架和工具摆放台,便于操作者 拿取;⑤设置4个手动回转台。地脚采用调整固定机
性的试验和仿真结果对比分析,表明所研究的泵马达排量分段控制方法能获得较好的稳定性及响应速度,提
出了设定起始控制电流为排量控制死区最大电流的想法,从而减小了泵马达排量控制死区非线性对动态响 应特性的不利影响。 关键词:静液驱动;履带车辆;泵马达;仿真模型 中图分类号:THl37文献标志码:B文章编号:1000-4858(2013)07-0095-05 引言
责把发动机输出的高速低扭矩动力转化为低速高扭矩 动力,并改变其传递方向,其装配质量直接影响到动力 传递的效率和自身使用的寿命等。 某企业原先使用的纯手动减速器装配模式因生产 效率低、劳动成本高,制约了其大规模的生产,无法满 足其自身的发展的要求。针对其生产的产品,依照经 济、使用、先进、可靠、各型号柔性化生产的原则,设计 出一条满足用户要求的减速机装配线。
110
2013年第7期
mm,压装行程为20 mm;弹簧最大刚度为
177051.5
N/m。在输人以上参数后,可得到图9~
图11三个关系曲线。
"
,’◆‘:1
暖,I
图5四立柱/s
图8轴承压装机AMF璐im模型
由图9、10可以可以看出在一次压装过程中,随着
时间的增加,压装力和压装位移呈线性快速增加。 由图11可以看出压装位移和压装力的线性变化。 这些曲线准确反映了实际液压系统的动态特性, 为压装机液压系统的设计提供了宝贵的理论依据。
收稿日期:2013旬I.18 基金项目:中央高校基本科研业务费专项资金资助 (2011HGZl0004)
列行走减速机和回转减速机总成。 1.2生产纲领及工作制度 装配线生产节拍:5 min/件;工作制度:单班制
(8 h)/天,300天/年;设备负荷:85%。 1.3设计原则
以国内经济适用的“精益生产”方式为设计的指 导思想,充分贯彻成熟技术、经济、方便、安全的设计原 则,使该生产线具有一定的柔性生产能力。使整线既 经济适用,又先进可靠。
Imagine.Lab
图12主减速机装配线实物图 参考文献: [1] 成大先.机械设计手册[M].北京:化学工业出版 社.2008. [2] 隋秀凛.实用机床设计手册[M].北京:机械工业出版
匮
AMESim系统建模和仿真
[M].北京:北京航空航天大学出版社,2011.
万方数据
液压与气动
DOI:10.11832/j.issn.1000-4858.2013.07.030
2013年第7期
汽车前驱主减速器柔性装配线的设计
曾奇,曾亿山,尹化保,朱瑞
Design of Flexible Assembly Line for Car Prodromal Main Reducer
ZENG
1设计依据 1.1产品品种 301、304、GOA91F-001、GOA91F-002、NGW、105系
差速器总成装配工艺流程:RG0lO差速器壳及从 动锥齿轮上线一RG020拆差壳,装止推垫和半轴齿 轮,十字轴齿轮总成等,合装差壳一RG030拧紧半壳 连接螺栓一RG040差速器吊装进入被齿中一RG050 检查转动情况,吊差壳总成到盘齿轮上并压装一 RG060手工预装连接螺栓一RG070拧紧差速器与盘 齿轮连接螺栓一RG080压装差速器上下轴承内环一 RG090拧紧固定啮合套锁紧螺母一RGl00差速器总 成翻转下线。 主减速器总成装配工艺流程:CA010减速器壳体 上线,夹紧,拆轴承盖,打标一CA020法兰面涂胶一 CA030主锥总成上线合装,手工预拧紧连接螺栓一 CA040拧紧主锥和主减壳连接螺栓一CA050差速器上
构调节高度,范围为0—50 mm;单滚轮承重大于50 4.2轴承压装机的设计
kg。
性质等要求,称之为支线单列布局,如图1。但评估后
认为,KBK覆盖存在无充分灵活性,对往后如产线调 整优化不好重新布局。
图1初步整体布局平面规划
减速机内轴承采用压装机完成压装,最初设计时
万方数据
液压与气动 采用的是四立柱式压装机,如图5所示。其特点是四 面有空间便于操作。但考虑到其零件多较复杂,液压 站布置在外等缺点,经研究,最后采用的是一体式压装 机,其液压站内置,结构紧凑,如图6所示。
量减小。选择通道宽度时,需根据人的流量、物流量 (运输手段)来考虑; (4)安全便于工作原则:安全生产是一件大事,它
KBK布局
在整体平面规划设计方案确定后,下步是KBK布 局的方案设计。各KBK根据各工位上下料、物流走 向、工件重量、工序间物料传递方式、高度等布局。最
终整线的布局(含KBK)如图3所示。
液压与气动
95
履带车辆静液驱动泵马达排量控制特性研究
罗灯明1,郑长松2,孙贺辉3
Study
on
Displacement Control Characteristics of Hydrostatic Drive Pump-motor for Tracked Vehicle
LUO Deng—min91,ZHENG Chang—son92,SUN He—hui3
涟
40
№
图6一体式压装机示意图
1.控制柜2.F制动组件3.上制动组件4.机身
通过滑台前后移动实现较重工件起吊合装以及再 次压装,实现设备重复利用,提高设备利用率。压机机 身采用箱体式,油箱内置,油缸单动,压机标准压力为 t,压力可调。其液压系统图如图7所示。
0.00 0.10 0.20 0.30 0.400.500.600.700.80
引言
分为一下三个模块。 主减速器在汽车传动系统中的作用非常重要,负 主锥总成装配工艺流程:PN010壳体上线一 PN020压装轴承座轴承外圈一PN030测量选取调整垫 片一PN040压装轴承内圈,调轴承预紧力--PN050压 油封、突缘--PN060拧突缘螺母,测主齿轴承预紧力一
PN070主锥总成下线。
2装配流程
减速机总成主要分为三部分:主动锥齿轮总成部 分;差速器总成部分;减速器总成部分。故装配流程可
作者简介:曾奇(1989一),男,安徽六安人,硕士研究生,主要
从事流体传动与控制的研究工作。
万方数据
2013年第7期
液压与气动
3.2最终整体布局设计方案
93
线合装,预拧紧轴承盖连接螺栓(法兰面朝下),调整 主被动齿轮间隙。检查斑点啮合及启动力矩,装螺母 锁片(双工位)一CA060拧紧轴承盖螺栓到设定扭 矩一CA070装圆柱齿轮壳一CA080装中桥轴间差速器 总成(法兰面朝上)一CA090装齿套、卡环,拔叉轴、拔 叉、接合套、压力弹簧、工作缸一cAl00拧紧螺栓一 CAll0空载磨合试验一CAl20主减速器总成吊装
装机的液压系统设计和参数的设定提供理论依据,可 以通过AMESim软件对压装机液压系统进行仿真。选
择压紧液压缸为研究对象,且假定轴承压装为弹性系
图11压装位移和压装力的关系曲线
统,利用AMESim软件得到的模型如图8所示。
电机转速1500 r/min;恒功率变量液压泵的排量 为40 mL/r,转速为1500 r/min;溢流阀的调定压力为
(1.承德石油高等专科学校汽车工程系,河北承德067000;2.北京理工大学机械与车辆工程学院,北京 3.中海油服务股份有限公司,天津300452)
100081;
摘要:针对履带车辆的变量泵一变量马达静液驱动系统,分析了变量泵和变量马达的排量控制特性,建
立了变量泵和变量马达排量控制机构数学模型和静液驱动系统仿真模型,通过对静液驱动系统动态响应特
Qi,ZENG