PLC控制系统设计方案流程
plc控制系统设计

B地启动
1
小车前进
B点行程开关闭合
2
启动2S定时
2S定时到
3
小车后退
A点行程开关闭合
4
启动5S定时
5S定时到
4 、SFC转换为梯形图
1)初始(第0)工作步的梯形图
该步的启动条件之一是其它工作步均未 工作。
第1步
第2步
第n步
第0步
当初始步的建立需要一定的条件时, 还
应将各条件的逻辑组合作为启动条件。
2.集中控制系统
上位机
PC
受控对象A 受控对象B 受控对象C
该形式系统构成简单, 相对成本低。一般用于各 受控对象位置比较集中且相互之间有一定联系的
场合。
3.分散控制系统
上位机A
上位机B
PC — A
PC—B
PC—C
受控对象A 受控对象B 受控对象C
该形式系统安全性较高, 便于维护。多用于 大型生产装置或多条流水线的控制。
V1、V2.V3均关闭,搅拌器
液体A
V1
不工作。 控制要求:按启动按钮后,
液体B
V2
V1打开,充液体A;充至I
位 H后,V1关闭,V2打开
,充液 I体B;充至H位后
,V2关闭,
L
搅拌器启动,搅拌6秒;搅 拌停止后,开V3阀排放,排 放至L位2秒后,关闭V3,
V3 M
按开停始止下按循钮环后。, 系统不立即停止工作, 须待一个循环
其它设备电源
采用UPS备用电源:
220VAC
总 电 源
UPS 控制器电源 I/O电源
其它设备电源 隔离变压器
双路供电:
双
A路 AA
路 切
plc控制方案

plc控制方案PLC(Programmable Logic Controller)即可编程逻辑控制器,是一种可以根据用户程序自动运行、控制工业过程的数字化运动设备。
PLC控制方案是指基于PLC的控制系统设计方案。
下面将介绍一个PLC控制方案的基本步骤和要素。
首先,PLC控制方案需要确定需要控制的对象和目标。
例如,如果需要控制一个自动化生产线,就需要确定需要控制的设备、工艺和产品等。
然后,需要确定控制的目标,例如提高生产效率、降低成本等。
其次,PLC控制方案需要进行硬件设计。
这包括选取适配的PLC型号、确定需要的输入输出(I/O)数量和类型,以及设计各种传感器和执行器的连接电路。
同时,还需要考虑整个控制系统的供电、通信和安全等方面。
然后,PLC控制方案需要进行软件编程。
对于大型控制系统来说,通常需要编写PLC程序和人机界面(HMI)程序。
PLC程序是基于对控制对象的分析和目标的需求,通过逻辑和算法编写的一系列指令,用于控制和监控机器和设备的运行。
HMI程序则用于展示和操作整个控制系统,提供人机交互界面。
最后,PLC控制方案需要进行调试和优化。
在调试阶段,需要验证PLC程序的正确性和可行性,检查输入输出的正常工作,并验证控制对象是否按照预期进行操作。
在优化阶段,需要根据实际情况对PLC程序进行修改和改进,以达到更好的控制效果和性能。
除了上述步骤外,一个PLC控制方案还应考虑以下几个要素:1. 安全性:PLC控制系统需要提供安全保护措施,例如急停按钮、安全开关等,以确保工作人员和设备的安全。
2. 可靠性:PLC控制系统需要具备良好的可靠性,能够在各种工作环境和条件下稳定运行,并能够及时检测和处理故障。
3. 扩展性:PLC控制系统应具备较强的扩展性,能够满足未来业务的需求变化,例如增加新的设备、调整工艺流程等。
4. 可维护性:PLC控制系统需要易于维护和维修,包括界面友好、故障排除简单、备件易于获取等方面。
简述可编程控制器控制系统的设计步骤

简述可编程控制器控制系统的设计步骤
可编程控制器(PLC)控制系统的设计步骤如下:
1. 确定系统要求:收集用户对控制系统的功能、性能和可靠性要求,并确定系统的输入、输出和操作模块的类型和数量。
2. 制定硬件配置:根据系统要求,选定PLC主机、I/O模块、
通信模块和其他必要的外围设备。
设计电源系统、信号调理电路及接线等。
3. 确定软件结构:根据系统要求,设计PLC程序的结构,包
括输入和输出模块的配置、逻辑控制、数据处理和通信功能等。
4. 开发PLC程序:根据软件结构,编写PLC程序,包括输入
和输出的连接、逻辑控制的设计、数据处理的算法和通信功能的设置等。
5. 联调测试:将开发好的PLC程序下载到PLC主机中,与实
际的硬件连接起来,进行联调测试。
对输入和输出进行检查,验证系统的功能和性能。
6. 调试和优化:根据联调测试的结果,调试PLC程序并优化
系统的性能。
解决可能出现的问题,确保系统正常运行。
7. 文档编制:编写控制系统的设计文档和用户手册,包括系统框图、PLC程序说明、操作说明和维护手册等。
8. 安装和调试:按照设计文档和用户手册,进行控制系统的安装和调试。
确保系统按照设计要求进行安装,并满足用户的需求。
9. 系统运行和维护:控制系统正常运行后,进行系统的运行和维护工作。
定期检查系统的运行状态,及时处理故障,保证系统的可靠性和稳定性。
以上是可编程控制器控制系统设计的一般步骤,具体的设计步骤和流程可能会根据不同的项目和要求有所差异。
plc程序方案

plc程序方案一、概述在现代工业控制领域中,可编程逻辑控制器(PLC)是一种常用的自动化控制设备。
PLC程序方案的制定是为了实现对工业过程或机器设备的自动控制和监控。
本文将介绍一个针对某生产线的PLC程序方案。
二、方案设计1. 系统架构设计在该生产线上,我们需要控制多个终端设备,包括传感器、执行器和控制阀等。
为了实现高效的控制与协调,我们采用了以PLC为核心的分布式控制系统。
该系统采用了现场总线作为通信媒介,将各个终端设备与PLC连接起来,实现数据的交换与传输。
2. PLC程序结构设计为了使PLC程序易于编写和维护,在设计时我们采用了对功能进行模块化划分的方式。
主要包括以下几个模块:- 输入模块:用于接收各个传感器的数据,并进行数据处理和校验。
- 输出模块:用于控制各个执行器的动作,实现对终端设备的控制。
- 逻辑控制模块:根据输入信号的状态和控制策略,对输出信号进行逻辑运算和处理。
- 状态监测模块:实时监测各个设备的状态信息,包括温度、压力和速度等指标。
3. PLC程序编写在PLC程序的编写过程中,我们需要根据实际需求进行逻辑设计和编程调试。
主要包括以下几个步骤:- 确定输入输出点位:根据工艺流程和设备布置,确定各个传感器和执行器的输入输出点位,进行标号和命名。
- 编写逻辑控制程序:根据生产线的工艺过程和控制要求,编写逻辑控制程序,实现设备的启停、顺序控制和报警处理等功能。
- 设置定时器和计数器:根据需要,设置定时器和计数器来实现对时间和数量的控制。
- 调试程序逻辑:通过在线调试工具,对编写的PLC程序进行逻辑调试和参数优化,确保程序的正常运行。
三、功能实现在该PLC程序方案中,我们实现了以下功能:1. 自动化控制:根据设定的工艺要求和控制策略,对生产线的各个设备进行自动控制,实现工艺过程的自动化。
2. 过程监控:实时监测生产线的运行状态,包括温度、压力和速度等参数的监控,确保生产过程的稳定性。
PLC控制系统设计流程
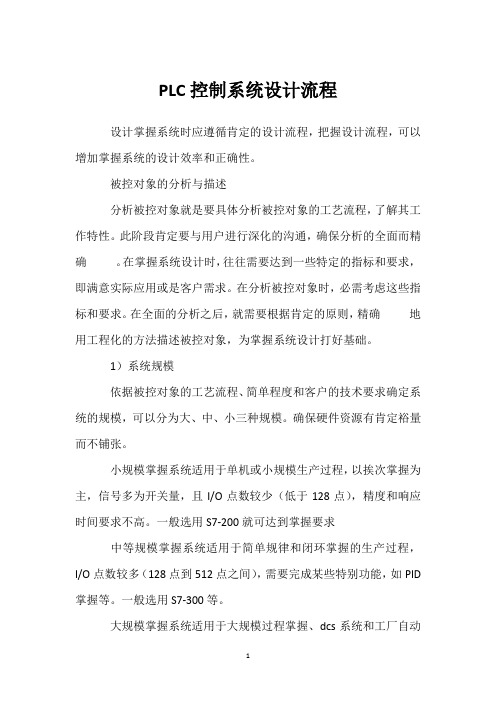
PLC控制系统设计流程设计掌握系统时应遵循肯定的设计流程,把握设计流程,可以增加掌握系统的设计效率和正确性。
被控对象的分析与描述分析被控对象就是要具体分析被控对象的工艺流程,了解其工作特性。
此阶段肯定要与用户进行深化的沟通,确保分析的全面而精确。
在掌握系统设计时,往往需要达到一些特定的指标和要求,即满意实际应用或是客户需求。
在分析被控对象时,必需考虑这些指标和要求。
在全面的分析之后,就需要根据肯定的原则,精确地用工程化的方法描述被控对象,为掌握系统设计打好基础。
1)系统规模依据被控对象的工艺流程、简单程度和客户的技术要求确定系统的规模,可以分为大、中、小三种规模。
确保硬件资源有肯定裕量而不铺张。
小规模掌握系统适用于单机或小规模生产过程,以挨次掌握为主,信号多为开关量,且I/O点数较少(低于128点),精度和响应时间要求不高。
一般选用S7-200就可达到掌握要求中等规模掌握系统适用于简单规律和闭环掌握的生产过程,I/O点数较多(128点到512点之间),需要完成某些特别功能,如PID 掌握等。
一般选用S7-300等。
大规模掌握系统适用于大规模过程掌握、dcs系统和工厂自动化网络掌握,I/O点数较多(高于512点),被控对象的工艺过程较简单,对于精度和响应时间要求较高。
应选用具有智能掌握、高速通信、数据库、函数运算等功能的高档plc,如S7-400等。
2)硬件配置依据系统规模和客户的技术对掌握系统I/O点数进行估算。
分析被控对象工艺过程,统计系统I/O点数和I/O类型。
根据设备和生产区域的不同进行划分,明确各个I/O点的位置和功能。
再加上10%~20%的备用量列出具体的I/O点清单。
3)软件配置依据掌握系统设计要求选择适合的软件,包括系统平台软件、编程软件。
上位机监控软件的选择。
首先需考虑监控的点数限制;是否有报警显示、趋势分析、报表打印以及历史记录功能。
4)掌握功能要正确的进行掌握系统的规模选择,首先要了解各家掌握器的特性,比如性能参数、应用场合、行业解决方案,以及牢靠性和通用性等。
使用plc完成控制系统的流程
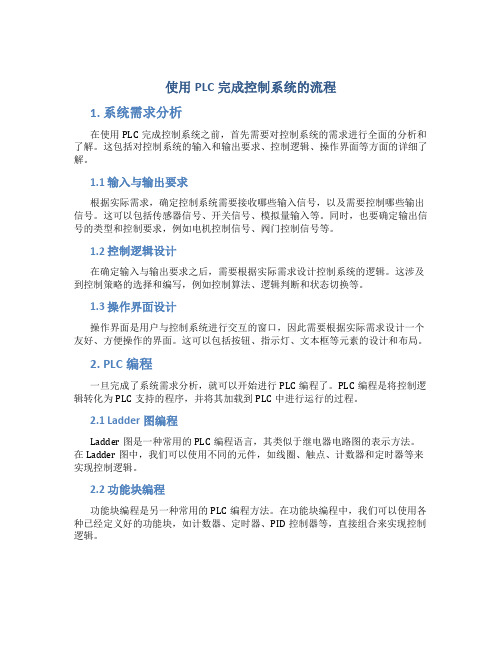
使用PLC完成控制系统的流程1. 系统需求分析在使用PLC完成控制系统之前,首先需要对控制系统的需求进行全面的分析和了解。
这包括对控制系统的输入和输出要求、控制逻辑、操作界面等方面的详细了解。
1.1 输入与输出要求根据实际需求,确定控制系统需要接收哪些输入信号,以及需要控制哪些输出信号。
这可以包括传感器信号、开关信号、模拟量输入等。
同时,也要确定输出信号的类型和控制要求,例如电机控制信号、阀门控制信号等。
1.2 控制逻辑设计在确定输入与输出要求之后,需要根据实际需求设计控制系统的逻辑。
这涉及到控制策略的选择和编写,例如控制算法、逻辑判断和状态切换等。
1.3 操作界面设计操作界面是用户与控制系统进行交互的窗口,因此需要根据实际需求设计一个友好、方便操作的界面。
这可以包括按钮、指示灯、文本框等元素的设计和布局。
2. PLC编程一旦完成了系统需求分析,就可以开始进行PLC编程了。
PLC编程是将控制逻辑转化为PLC支持的程序,并将其加载到PLC中进行运行的过程。
2.1 Ladder图编程Ladder图是一种常用的PLC编程语言,其类似于继电器电路图的表示方法。
在Ladder图中,我们可以使用不同的元件,如线圈、触点、计数器和定时器等来实现控制逻辑。
2.2 功能块编程功能块编程是另一种常用的PLC编程方法。
在功能块编程中,我们可以使用各种已经定义好的功能块,如计数器、定时器、PID控制器等,直接组合来实现控制逻辑。
2.3 程序调试与优化进行PLC编程后,需要对程序进行调试与优化。
这包括检查PLC连接是否正确,检查控制逻辑是否符合设计要求,以及通过逐步调试来验证控制系统的正确性。
3. 硬件配置与系统集成完成PLC编程后,需要将PLC与其他硬件设备进行配置和集成,以实现整个控制系统的功能。
3.1 选择适当的PLC设备根据实际需求,选择适当的PLC设备,并确保其与其他硬件设备的兼容性。
这包括PLC的输入输出模块、通信模块等。
基于PLC的自动化控制系统设计
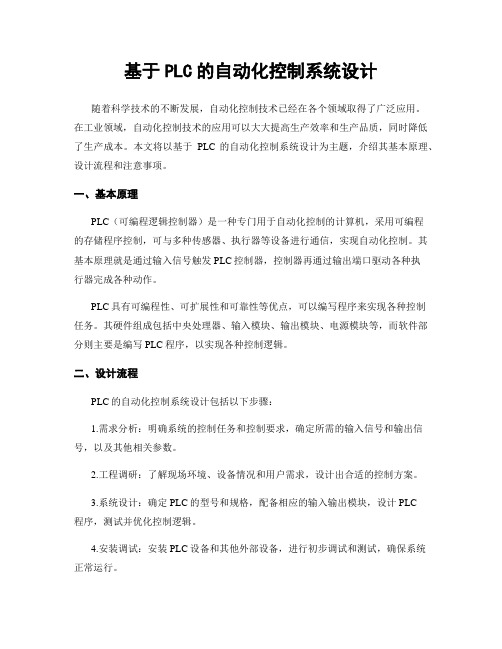
基于PLC的自动化控制系统设计随着科学技术的不断发展,自动化控制技术已经在各个领域取得了广泛应用。
在工业领域,自动化控制技术的应用可以大大提高生产效率和生产品质,同时降低了生产成本。
本文将以基于PLC的自动化控制系统设计为主题,介绍其基本原理、设计流程和注意事项。
一、基本原理PLC(可编程逻辑控制器)是一种专门用于自动化控制的计算机,采用可编程的存储程序控制,可与多种传感器、执行器等设备进行通信,实现自动化控制。
其基本原理就是通过输入信号触发PLC控制器,控制器再通过输出端口驱动各种执行器完成各种动作。
PLC具有可编程性、可扩展性和可靠性等优点,可以编写程序来实现各种控制任务。
其硬件组成包括中央处理器、输入模块、输出模块、电源模块等,而软件部分则主要是编写PLC程序,以实现各种控制逻辑。
二、设计流程PLC的自动化控制系统设计包括以下步骤:1.需求分析:明确系统的控制任务和控制要求,确定所需的输入信号和输出信号,以及其他相关参数。
2.工程调研:了解现场环境、设备情况和用户需求,设计出合适的控制方案。
3.系统设计:确定PLC的型号和规格,配备相应的输入输出模块,设计PLC程序,测试并优化控制逻辑。
4.安装调试:安装PLC设备和其他外部设备,进行初步调试和测试,确保系统正常运行。
5.维护保养:监测PLC的运行状况,定期检查和维护设备,及时处理故障。
三、注意事项在进行PLC的自动化控制系统设计时,还需要注意以下几个方面:1.合理性和可行性:设计方案应符合实际情况,具有可行性。
2.稳定性和可靠性:PLC设备应选择品质可靠、性能稳定的产品,以确保系统的长期稳定运行。
3.灵活性和扩展性:系统设计应具有一定的灵活性和扩展性,能够满足未来的发展需求。
4.安全性和操作性:PLC的自动化控制系统设计需考虑安全和操作性,以确保设备和人员的安全。
5.节能环保:系统设计应符合节能环保要求,避免过度能耗和环境污染。
四、结论基于PLC的自动化控制系统设计是现代工业生产中的重要技术,它能大大提高生产效率和品质。
PLC控制系统设计实现自动车库门控制方案
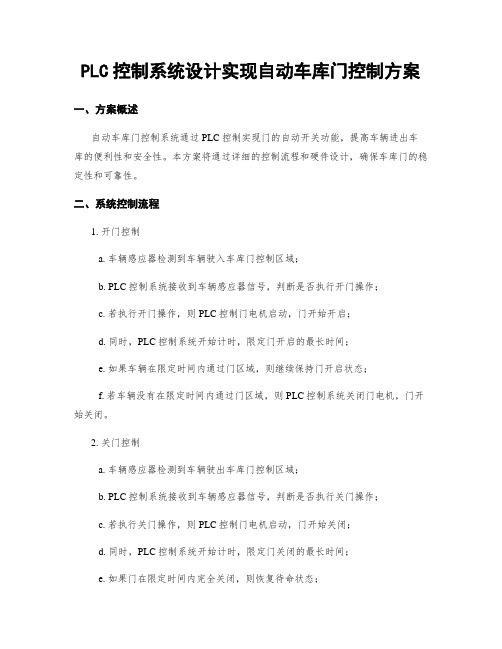
PLC控制系统设计实现自动车库门控制方案一、方案概述自动车库门控制系统通过PLC控制实现门的自动开关功能,提高车辆进出车库的便利性和安全性。
本方案将通过详细的控制流程和硬件设计,确保车库门的稳定性和可靠性。
二、系统控制流程1. 开门控制a. 车辆感应器检测到车辆驶入车库门控制区域;b. PLC控制系统接收到车辆感应器信号,判断是否执行开门操作;c. 若执行开门操作,则PLC控制门电机启动,门开始开启;d. 同时,PLC控制系统开始计时,限定门开启的最长时间;e. 如果车辆在限定时间内通过门区域,则继续保持门开启状态;f. 若车辆没有在限定时间内通过门区域,则PLC控制系统关闭门电机,门开始关闭。
2. 关门控制a. 车辆感应器检测到车辆驶出车库门控制区域;b. PLC控制系统接收到车辆感应器信号,判断是否执行关门操作;c. 若执行关门操作,则PLC控制门电机启动,门开始关闭;d. 同时,PLC控制系统开始计时,限定门关闭的最长时间;e. 如果门在限定时间内完全关闭,则恢复待命状态;f. 若门没有在限定时间内完全关闭,则PLC控制系统停止关门操作,并发送故障信息以及发出警报。
3. 紧急停止控制当遇到紧急情况时,PLC控制系统可以接收紧急停止信号,立即停止门电机的运动,并发出警报以确保人身和财产安全。
三、硬件设计1. PLC控制器选择适合的PLC控制器作为系统的核心控制设备,负责接收输入信号、判断逻辑和输出控制信号。
根据实际情况选择不同型号和品牌的PLC控制器。
2. 电机驱动器使用适当的电机驱动器控制车库门的开闭运动,确保门的平稳、准确的开关。
根据门的尺寸和重量选择合适的电机驱动器。
3. 车辆感应器采用合适的车辆感应器来检测车辆进出门控制区域,如磁感应器、红外线感应器等。
车辆感应器需要与PLC控制系统进行良好的通信。
4. 警报装置在系统中设置警报装置,用于发出警报信号,提醒人员注意车库门的运动和可能的危险。
- 1、下载文档前请自行甄别文档内容的完整性,平台不提供额外的编辑、内容补充、找答案等附加服务。
- 2、"仅部分预览"的文档,不可在线预览部分如存在完整性等问题,可反馈申请退款(可完整预览的文档不适用该条件!)。
- 3、如文档侵犯您的权益,请联系客服反馈,我们会尽快为您处理(人工客服工作时间:9:00-18:30)。
PLC控制系统设计流程
设计控制系统时应遵循一定的设计流程,掌握设计流程,可以增
加控制系统的设计效率和正确性。
被控对象的分析与描述
分析被控对象就是要详细分析被控对象的工艺流程,了解其工作特性。
此阶段一定要与用户进行深入的沟通,确保分析的全面而准确。
在控制系统设计时,往往需要达到一些特定的指标和要求,即满足实际应用或是客户需求。
在分析被控对象时,必须考虑这些指标和要求。
在全面的分析之后,就需要按照一定的原则,准确地用工程化的方法描述被控对象,为控制系统设计打好基础。
1)系统规模
根据被控对象的工艺流程、复杂程度和客户的技术要求确定系统的规模,可以分为大、中、小三种规模。
确保硬件资源有一定裕量而不浪费。
小规模控制系统适用于单机或小规模生产过程,以顺序控制为
主,信号多为开关量,且I/O点数较少(低于128点),精度和响应
时间要求不高。
一般选用S7-200就可达到控制要求
中等规模控制系统适用于复杂逻辑和闭环控制的生产过程,I/O 点数较多(128点到512点之间),需要完成某些特殊功能,如PID 控制等。
一般选用S7-300等。
大规模控制系统适用于大规模过程控制、des系统和工厂自动化网络控制,I/O点数较多(高于512点),被控对象的工艺过程较复杂,对于精度和响应时间要求较高。
应选用具有智能控制、高速通信、数据库、函数运算等功能的高档ple,如S7-400等。
2)硬件配置
根据系统规模和客户的技术对控制系统I/O点数进行估算。
分析被控对象工艺过程,统计系统I/O点数和I/O类型。
按照设备和生产区域的不同进行划分,明确各个I/O点的位置和功能。
再加上10%- 20%勺备用量列出详细的I/O点清单。
3)软件配置
根据控制系统设计要求选择适合的软件,包括系统平台软件、编程软件。
上位机监控软件的选择。
首先需考虑监控的点数限制;是否有报警显示、趋势分析、报表打印以及历史记录功能。
4)控制功能
要正确的进行控制系统的规模选择,首先要了解各家控制器的特性,比如性能参数、应用场合、行业解决方案,以及可靠性和通用性等。
如何选择一个控制系统,一般遵循以下几点:
控制系统是否需要冗余、I/O信号模块是否需要冗余、通讯是否需要冗余。
控制点数有多少,包括数字量输入和输出点数、模拟量输入和输出点数。
被控对象工艺是否复杂,是否需要实现特殊功能,比如防喘控制等。
系统正常运行时,控制器的负载率是否有足够的工作裕量;I/O
信号点是否需要一定的余量。
针对数字信号,是否需要继电器隔离;考虑输入信号的电压和电流等级;输出信号是否需要固态继电器输出。
针对模拟量信号,是否需要安全隔离栅;信号的类型,电压型还是电流型;电压和电流的测量范围。
不一样的信号类型,需要选择不一样的I/O信号模块。
用于温度测量的信号模块,考虑是热电阻还是热电偶。
信号模块是否需要在线带电插拔更换。
如果需要,还需考虑附加特殊的背板插槽。
当系统和外部出现故障时,比如信号短路或锻炉,这时信号模块是否需要将输入输出信号自动切换到预先设置的安全值。
如有要求,需考虑选用故障安全型的控制器和信号模块。
当需要和第三方设备通讯时,需考虑通讯距离的长短,以及相应的通讯接口协议等,选用不同的通讯模块。
针对系统中的重要连锁信号,是否需要特殊的SOE模块,来记录信
号变化的时间先后顺序。
熟悉被控对象是设计控制系统的基础。
只有深入了解被控对象以
及被控过程,才能够提出合理科学的控制方案。
1)分析被控对象。
详细分析被控对象的工艺流程,了解其工作
特性。
此阶段一定要与用户进行深入的沟通,确保分析得全面而准确。
2)画出工艺流程图。
经过第一步,应对被控对象的整个工艺流程有了深入的了解,为了更直观、简洁的表示,画出工艺流程图,为后面的系统设计做准备。
3)分析并明确控制任务。
根据已经做好的工艺流程图,工程师可以把用户提出的控制要求转换为专业术语,对其逐一进行分解,并从控制的角度将其中的要求转化为多个控制回路。
对于过程控制系统可用P&ID图来表示其中的控制关系。