晶圆切割晶圆切割和微加工新技术
半导体晶圆切割工艺
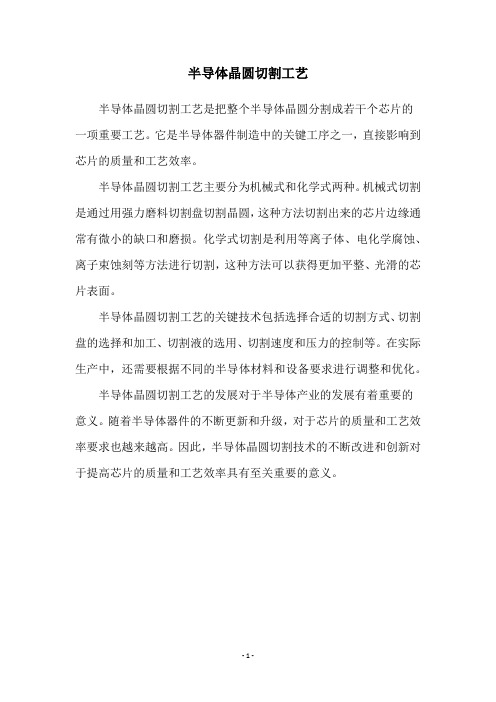
半导体晶圆切割工艺
半导体晶圆切割工艺是把整个半导体晶圆分割成若干个芯片的
一项重要工艺。
它是半导体器件制造中的关键工序之一,直接影响到芯片的质量和工艺效率。
半导体晶圆切割工艺主要分为机械式和化学式两种。
机械式切割是通过用强力磨料切割盘切割晶圆,这种方法切割出来的芯片边缘通常有微小的缺口和磨损。
化学式切割是利用等离子体、电化学腐蚀、离子束蚀刻等方法进行切割,这种方法可以获得更加平整、光滑的芯片表面。
半导体晶圆切割工艺的关键技术包括选择合适的切割方式、切割盘的选择和加工、切割液的选用、切割速度和压力的控制等。
在实际生产中,还需要根据不同的半导体材料和设备要求进行调整和优化。
半导体晶圆切割工艺的发展对于半导体产业的发展有着重要的
意义。
随着半导体器件的不断更新和升级,对于芯片的质量和工艺效率要求也越来越高。
因此,半导体晶圆切割技术的不断改进和创新对于提高芯片的质量和工艺效率具有至关重要的意义。
- 1 -。
晶圆切割的方法范文
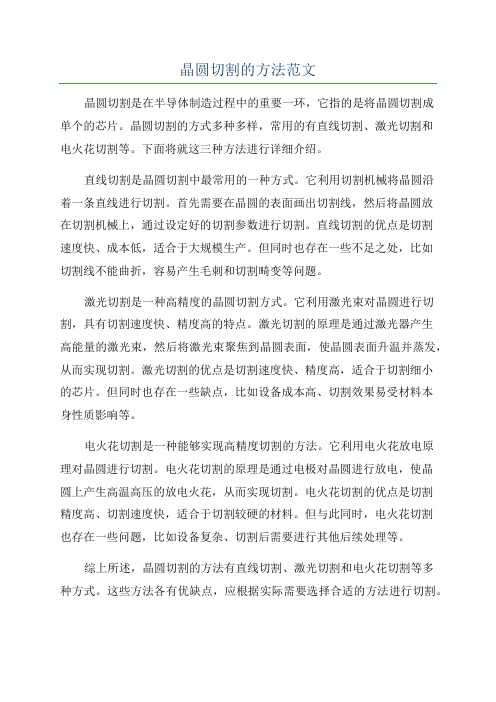
晶圆切割的方法范文晶圆切割是在半导体制造过程中的重要一环,它指的是将晶圆切割成单个的芯片。
晶圆切割的方式多种多样,常用的有直线切割、激光切割和电火花切割等。
下面将就这三种方法进行详细介绍。
直线切割是晶圆切割中最常用的一种方式。
它利用切割机械将晶圆沿着一条直线进行切割。
首先需要在晶圆的表面画出切割线,然后将晶圆放在切割机械上,通过设定好的切割参数进行切割。
直线切割的优点是切割速度快、成本低,适合于大规模生产。
但同时也存在一些不足之处,比如切割线不能曲折,容易产生毛刺和切割畸变等问题。
激光切割是一种高精度的晶圆切割方式。
它利用激光束对晶圆进行切割,具有切割速度快、精度高的特点。
激光切割的原理是通过激光器产生高能量的激光束,然后将激光束聚焦到晶圆表面,使晶圆表面升温并蒸发,从而实现切割。
激光切割的优点是切割速度快、精度高,适合于切割细小的芯片。
但同时也存在一些缺点,比如设备成本高、切割效果易受材料本身性质影响等。
电火花切割是一种能够实现高精度切割的方法。
它利用电火花放电原理对晶圆进行切割。
电火花切割的原理是通过电极对晶圆进行放电,使晶圆上产生高温高压的放电火花,从而实现切割。
电火花切割的优点是切割精度高、切割速度快,适合于切割较硬的材料。
但与此同时,电火花切割也存在一些问题,比如设备复杂、切割后需要进行其他后续处理等。
综上所述,晶圆切割的方法有直线切割、激光切割和电火花切割等多种方式。
这些方法各有优缺点,应根据实际需要选择合适的方法进行切割。
随着半导体技术的不断发展,相信晶圆切割技术也会得到进一步的改进和完善。
半导体晶圆切割工艺
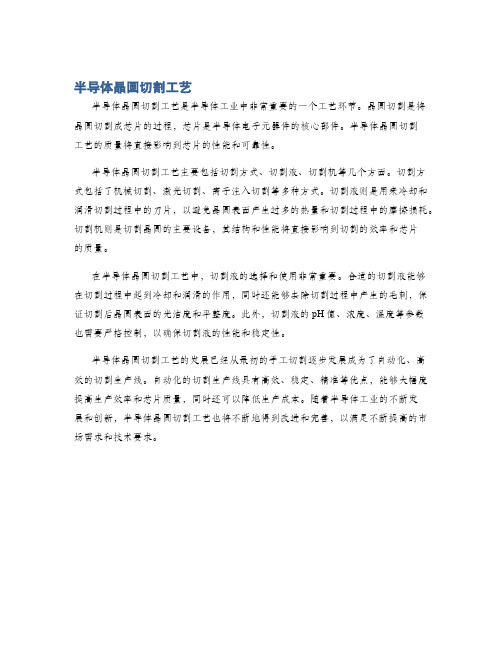
半导体晶圆切割工艺
半导体晶圆切割工艺是半导体工业中非常重要的一个工艺环节。
晶圆切割是将晶圆切割成芯片的过程,芯片是半导体电子元器件的核心部件。
半导体晶圆切割
工艺的质量将直接影响到芯片的性能和可靠性。
半导体晶圆切割工艺主要包括切割方式、切割液、切割机等几个方面。
切割方式包括了机械切割、激光切割、离子注入切割等多种方式。
切割液则是用来冷却和润滑切割过程中的刀片,以避免晶圆表面产生过多的热量和切割过程中的摩擦损耗。
切割机则是切割晶圆的主要设备,其结构和性能将直接影响到切割的效率和芯片
的质量。
在半导体晶圆切割工艺中,切割液的选择和使用非常重要。
合适的切割液能够在切割过程中起到冷却和润滑的作用,同时还能够去除切割过程中产生的毛刺,保证切割后晶圆表面的光洁度和平整度。
此外,切割液的pH值、浓度、温度等参数
也需要严格控制,以确保切割液的性能和稳定性。
半导体晶圆切割工艺的发展已经从最初的手工切割逐步发展成为了自动化、高效的切割生产线。
自动化的切割生产线具有高效、稳定、精准等优点,能够大幅度提高生产效率和芯片质量,同时还可以降低生产成本。
随着半导体工业的不断发
展和创新,半导体晶圆切割工艺也将不断地得到改进和完善,以满足不断提高的市场需求和技术要求。
晶圆切割环节变化
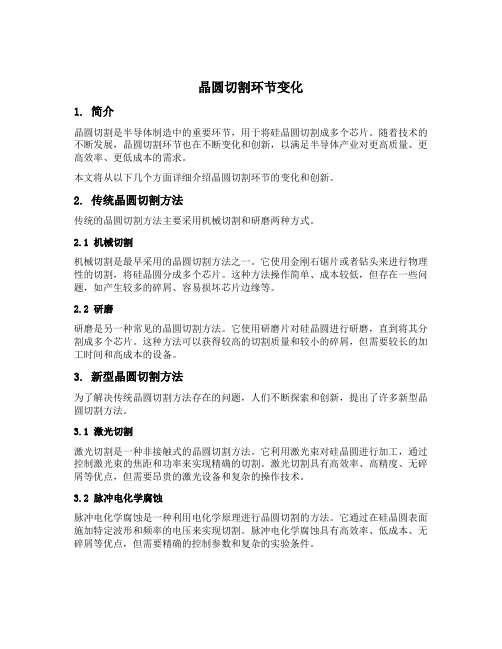
晶圆切割环节变化1. 简介晶圆切割是半导体制造中的重要环节,用于将硅晶圆切割成多个芯片。
随着技术的不断发展,晶圆切割环节也在不断变化和创新,以满足半导体产业对更高质量、更高效率、更低成本的需求。
本文将从以下几个方面详细介绍晶圆切割环节的变化和创新。
2. 传统晶圆切割方法传统的晶圆切割方法主要采用机械切割和研磨两种方式。
2.1 机械切割机械切割是最早采用的晶圆切割方法之一。
它使用金刚石锯片或者钻头来进行物理性的切割,将硅晶圆分成多个芯片。
这种方法操作简单、成本较低,但存在一些问题,如产生较多的碎屑、容易损坏芯片边缘等。
2.2 研磨研磨是另一种常见的晶圆切割方法。
它使用研磨片对硅晶圆进行研磨,直到将其分割成多个芯片。
这种方法可以获得较高的切割质量和较小的碎屑,但需要较长的加工时间和高成本的设备。
3. 新型晶圆切割方法为了解决传统晶圆切割方法存在的问题,人们不断探索和创新,提出了许多新型晶圆切割方法。
3.1 激光切割激光切割是一种非接触式的晶圆切割方法。
它利用激光束对硅晶圆进行加工,通过控制激光束的焦距和功率来实现精确的切割。
激光切割具有高效率、高精度、无碎屑等优点,但需要昂贵的激光设备和复杂的操作技术。
3.2 脉冲电化学腐蚀脉冲电化学腐蚀是一种利用电化学原理进行晶圆切割的方法。
它通过在硅晶圆表面施加特定波形和频率的电压来实现切割。
脉冲电化学腐蚀具有高效率、低成本、无碎屑等优点,但需要精确的控制参数和复杂的实验条件。
3.3 离子束切割离子束切割是一种利用离子束对硅晶圆进行加工的方法。
它通过控制离子束的能量和角度来实现切割,可以得到较高质量的芯片表面。
离子束切割具有高精度、无碎屑等优点,但需要昂贵的设备和复杂的操作技术。
4. 创新技术与发展趋势晶圆切割环节的变化和创新不断推动半导体产业的发展。
以下是一些当前的创新技术和发展趋势:4.1 薄片晶圆切割随着移动设备和物联网等应用的兴起,对芯片尺寸和厚度要求越来越高。
制造工艺中的精密加工技术

制造工艺中的精密加工技术精密加工技术在制造工艺中扮演着至关重要的角色。
精密加工技术的使用可以大大提升产品的质量和精度,同时还能提高生产效率。
本文将以精密加工技术的应用为重点,介绍一些常见的精密加工技术,并探讨其在制造工艺中的优势和应用领域。
一、数控加工技术数控加工技术是一种基于计算机数控系统的加工方式,通过预先编程的方式控制机床进行工件的加工。
相比传统的手工操作,数控加工技术具有高度自动化和高精度的特点。
数控加工技术的应用范围非常广泛,可以用于金属加工、木材加工、塑料加工等方面。
在航空航天、汽车制造、电子器件等领域中,数控加工技术已经成为不可或缺的一部分。
通过数控加工技术,可以实现复杂零件的加工,提高产品的质量和精度。
二、激光加工技术激光加工技术利用激光束对工件进行切割、打孔、焊接等加工操作。
相比传统的机械加工方式,激光加工技术具有无接触、高精度、高灵活性的特点。
激光加工技术广泛应用于微电子、光电子、精密机械等领域。
例如,在集成电路制造中,激光加工技术可以实现对晶圆的切割和打孔,从而生产出精密的微芯片。
在精密机械加工中,激光加工技术可以用于切割薄板、制作高精度的零件等。
三、电火花加工技术电火花加工技术是利用电火花放电原理进行加工的一种方法。
通过在工件表面产生电火花,可以实现对硬度高、形状复杂的工件进行加工和修复。
电火花加工技术主要应用于模具制造和精密零件加工领域。
在模具制造中,电火花加工技术可以用于加工模具的复杂内部结构和毛坯。
在精密零件加工中,电火花加工技术可以实现对微小孔眼的加工,提高产品的质量和精度。
四、数码喷墨技术数码喷墨技术利用喷墨头对工件进行颜色印刷和图案装饰。
相比传统的印刷方式,数码喷墨技术具有高分辨率、无版面限制、快速定制等优势。
数码喷墨技术广泛应用于纺织品印刷、陶瓷器件装饰、平面广告制作等领域。
通过数码喷墨技术,可以实现对织物、陶瓷、纸张等材料的高精度印刷,提高产品的质量和外观。
晶圆切割工艺
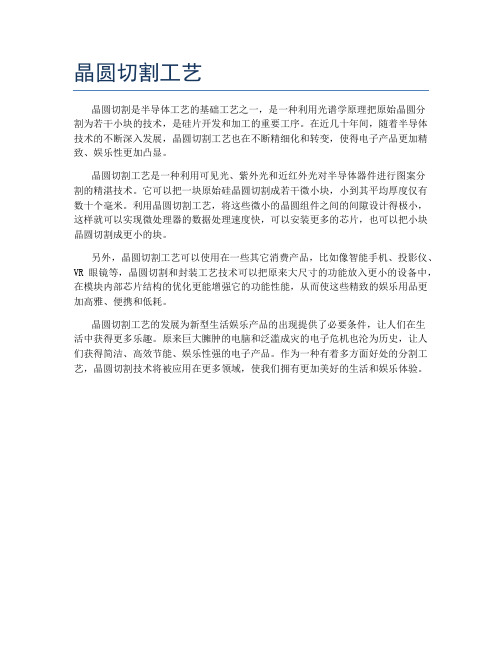
晶圆切割工艺
晶圆切割是半导体工艺的基础工艺之一,是一种利用光谱学原理把原始晶圆分
割为若干小块的技术,是硅片开发和加工的重要工序。
在近几十年间,随着半导体技术的不断深入发展,晶圆切割工艺也在不断精细化和转变,使得电子产品更加精致、娱乐性更加凸显。
晶圆切割工艺是一种利用可见光、紫外光和近红外光对半导体器件进行图案分
割的精湛技术。
它可以把一块原始硅晶圆切割成若干微小块,小到其平均厚度仅有数十个毫米。
利用晶圆切割工艺,将这些微小的晶圆组件之间的间隙设计得极小,这样就可以实现微处理器的数据处理速度快,可以安装更多的芯片,也可以把小块晶圆切割成更小的块。
另外,晶圆切割工艺可以使用在一些其它消费产品,比如像智能手机、投影仪、VR眼镜等,晶圆切割和封装工艺技术可以把原来大尺寸的功能放入更小的设备中,在模块内部芯片结构的优化更能增强它的功能性能,从而使这些精致的娱乐用品更加高雅、便携和低耗。
晶圆切割工艺的发展为新型生活娱乐产品的出现提供了必要条件,让人们在生
活中获得更多乐趣。
原来巨大臃肿的电脑和泛滥成灾的电子危机也沦为历史,让人们获得简洁、高效节能、娱乐性强的电子产品。
作为一种有着多方面好处的分割工艺,晶圆切割技术将被应用在更多领域,使我们拥有更加美好的生活和娱乐体验。
晶圆切割设备原理
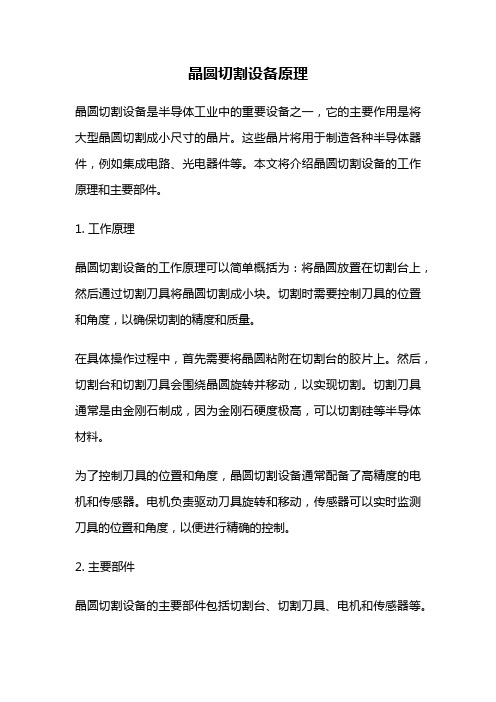
晶圆切割设备原理晶圆切割设备是半导体工业中的重要设备之一,它的主要作用是将大型晶圆切割成小尺寸的晶片。
这些晶片将用于制造各种半导体器件,例如集成电路、光电器件等。
本文将介绍晶圆切割设备的工作原理和主要部件。
1. 工作原理晶圆切割设备的工作原理可以简单概括为:将晶圆放置在切割台上,然后通过切割刀具将晶圆切割成小块。
切割时需要控制刀具的位置和角度,以确保切割的精度和质量。
在具体操作过程中,首先需要将晶圆粘附在切割台的胶片上。
然后,切割台和切割刀具会围绕晶圆旋转并移动,以实现切割。
切割刀具通常是由金刚石制成,因为金刚石硬度极高,可以切割硅等半导体材料。
为了控制刀具的位置和角度,晶圆切割设备通常配备了高精度的电机和传感器。
电机负责驱动刀具旋转和移动,传感器可以实时监测刀具的位置和角度,以便进行精确的控制。
2. 主要部件晶圆切割设备的主要部件包括切割台、切割刀具、电机和传感器等。
其中,切割台是整个设备的核心部件,它需要具备高精度的平面度和稳定性,以确保切割的精度和一致性。
切割刀具通常由金刚石制成,根据切割模式的不同,可以分为内切和外切两种类型。
内切是指将刀具从晶圆的中心开始旋转,逐渐向外切割,直到晶圆被切成小块。
外切则是相反的过程,从晶圆的外边缘开始切割,向内逐渐切割直到晶圆被切成小块。
电机是控制刀具旋转和移动的关键部件之一,通常采用高精度的步进电机。
这种电机可以非常精确地控制刀具的位置和角度,以实现高质量的切割。
传感器则是用于监测刀具位置和角度的关键部件之一。
晶圆切割设备通常配备多个传感器,以确保对刀具位置和角度的多重监测,从而提高切割的精度和可靠性。
晶圆切割设备是半导体制造过程中不可或缺的设备之一。
它的工作原理是通过控制刀具的位置和角度来实现对晶圆的精确切割,从而生产出高质量的半导体器件。
半导体芯片晶圆切割工艺研究
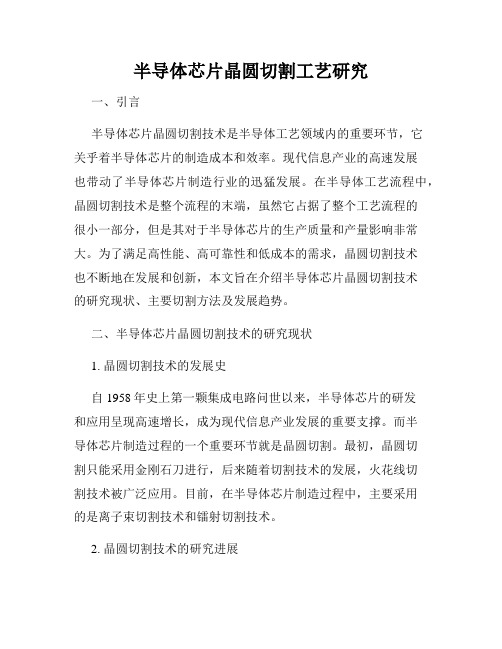
半导体芯片晶圆切割工艺研究一、引言半导体芯片晶圆切割技术是半导体工艺领域内的重要环节,它关乎着半导体芯片的制造成本和效率。
现代信息产业的高速发展也带动了半导体芯片制造行业的迅猛发展。
在半导体工艺流程中,晶圆切割技术是整个流程的末端,虽然它占据了整个工艺流程的很小一部分,但是其对于半导体芯片的生产质量和产量影响非常大。
为了满足高性能、高可靠性和低成本的需求,晶圆切割技术也不断地在发展和创新,本文旨在介绍半导体芯片晶圆切割技术的研究现状、主要切割方法及发展趋势。
二、半导体芯片晶圆切割技术的研究现状1. 晶圆切割技术的发展史自1958年史上第一颗集成电路问世以来,半导体芯片的研发和应用呈现高速增长,成为现代信息产业发展的重要支撑。
而半导体芯片制造过程的一个重要环节就是晶圆切割。
最初,晶圆切割只能采用金刚石刀进行,后来随着切割技术的发展,火花线切割技术被广泛应用。
目前,在半导体芯片制造过程中,主要采用的是离子束切割技术和镭射切割技术。
2. 晶圆切割技术的研究进展随着科技和制造水平的提高,晶圆切割技术也在不断的优化和改进,不断推陈出新。
随着微加工技术的进步,离子束切割技术又有了新的突破,实现了芯片的更好切割精度和更高的产能。
而在镭射切割技术方面,一些新技术也被不断地研究和推广应用。
例如,在镭射切割技术中,几乎不需要进行后续处理,能够实现更加高效、少浪费的芯片切割,极大地提高了芯片制造的效率和成本控制。
三、主要晶圆切割方法1. 金刚石切割法金刚石切割法是史上最早使用的一种技术,该技术能够在早期对硅晶圆进行有效的分离处理。
其中,需要使用的是钢线镶有金刚石粉末的金刚线。
此法的切割质量非常不稳定,有很多的边角,生产周期较长且成本高昂。
因此,这种技术大部分已经被淘汰,不再被推广使用。
2. 火花线切割法火花线切割法是较早的一种切割方法,它属于宏观切割技术,主要用于硅晶圆的切割处理;它是将钢丝通过精细调节,再通过电火花放电释放来完成切割的过程。
- 1、下载文档前请自行甄别文档内容的完整性,平台不提供额外的编辑、内容补充、找答案等附加服务。
- 2、"仅部分预览"的文档,不可在线预览部分如存在完整性等问题,可反馈申请退款(可完整预览的文档不适用该条件!)。
- 3、如文档侵犯您的权益,请联系客服反馈,我们会尽快为您处理(人工客服工作时间:9:00-18:30)。
封装:晶圆切割晶圆切割和微加工新技术 (排2页)Derek Chiang ( 江朝宗),Bernold Richerzhagen和Sean Green;Synova电子产品“轻、薄、短、小”的市场趋势,要求许多电子器件除了要有更小的体积外,还要有更强、更快的功能。
生产技术也因此而快速发展。
但经年累月,有些技术已发展到物理极限,几乎难以更上层楼。
就半导体而言,如记忆体IC,已由早期的一层变成多层的封裝,一颗IC里叠了 7、8层芯粒(chip),而总体积反而只有原来的几分之一。
因此晶片(Wafer)的厚度也由650微米(Micron)一路减薄至120微米、100微米、75微米、50微米、25微米。
当厚度降到100um以下,传统的划片技术已经出现问题,产能节节下降,破片率大幅攀升。
晶片在此阶断价值不斐,几个百分点的破片率可能吃掉工厂辛苦创造的利润。
因此处理这类超薄晶片,工程师们无不战战兢兢。
当传统钻石片切削方式碰到了瓶颈,大家都想到试试激光。
从业界的实际案例来看,激光仍有不少难题需要克服。
其中最难解决的是热影响区(HAZ)过大及熔渣喷溅污染的问题。
这些缺点足以影响或破坏晶片的电性,尤其那些高阶的wafer。
因此改用激光并不如预期顺利。
此间瑞士联邦科技大学Dr.Bernold Richerzhagen发明的水导激光(Water-Jet-Guided Laser商业上称微水刀激光)正好派上用场。
该技术突破传统激光的概念, 巧妙地结合水刀和激光两种技术, 克服了热影响区等问题, 获得世界专利,可望成为晶片切割及精微加工的新利器。
水导激光原理几千年来‘水火不融’的观念, 1993年被瑞士杰出的科学家Dr.Bernold Richerzhagen打破。
他巧妙地结合水刀技术和激光技术的优点,创造出微水刀激光(Laser Micro Jet)。
更精确的说法是水导激光(Water Jet Guided Laser)。
他将激光聚焦后导入比发丝还细的微水柱中,从而引导光束,并冷却工件,消除了传统激光热影响区(Heat Affected Zone)过大的缺陷。
大大提高了激光切割的质量,因而非常适合半导体、医疗器材、电子、航天等高精密、高洁净要求的加工。
从图1可看出激光束(Laser Beam)由上方导入, 经过聚焦镜及水腔(Water Chamber)的窗户进入,聚焦于喷嘴(Nozzle)的圆心.图 1.低压纯净水从水腔左边进入,经钻石喷嘴(Diamond Nozzle)上的微孔喷出。
由于喷嘴考虑到流体力学的设计,出来的水柱像光纤一样又直又圆。
水柱的直径根据喷嘴孔径而异,一般比人的头发还细,有100到30微米等多种规格。
激光被导入水柱中心,利用微水柱与空气界面全反射的原理,激光将沿着水柱行进。
在水柱维持稳定不开花的范围内都能进行加工。
通常有效的工作距离为喷嘴孔径的一千倍。
如喷嘴为100微米, 则其有效工作距离为100毫米。
这是传统激光所望尘莫及的,因为传统激光只能在焦点处加工。
激光光源可选配不同的波长,只要该波长的能量不会被水吸收即可。
精密加工常用的波长,1064nm 到355nm的范围均适用。
另外,用于微加工的激光几乎都是脉沖激光(Pulsed Laser),传统激光不论是脉沖或连续,总会有能量残留在切割道上,该能量的累积和传导是造成烧伤切割道旁热损伤的主要原因。
而微水刀激光因水柱的作用,将每个脉沖残留的热量迅速带走,不会累积在工件上,因此切割道干净利落。
热影响区的困扰得到大幅改善。
因此, Laser MicroJet技术才适用于半导体等高精密的应用。
Laser MicroJet 特点相对于传统激光,微水刀激光有很多显著的特点。
如无热影响区(Zero Heat Affected Zone),完全不烧伤工件,切割道干净利落、无熔渣、无毛刺、无热应力、无机械应力、无污染,极适合半导体、电子、医疗、航天等高精密器件切割加工。
微水刀激光适用于从金属到其合金的多种材料,如不锈钢、钛、钼、镁、镍、铜、Invar等, 以及硅(Silicon)、锗(Ge)、砷化镓(GaAs)等半导体材料, 乃至碳化硅(Sic)、CBN、钻石、陶瓷、橡胶……软硬通吃。
甚至可同时切割橡胶及不锈钢片而不烧伤橡胶层,这在传统激光是完全不可能的事情。
该项技术可用于切割、钻孔、挖槽、打印、表面热处理等多项极细微及复杂的形状加工。
超薄硅片(Ultra Thin Silicon Wafer)切割速度比传统钻石刀快5到10倍,并且可以切任意形状,功能超强,在半导体晶片切割的应用上,突破了多年来晶片划片只能走直线的桎锢。
从此设计者可以毫无限制的发挥其创意。
从两张不锈钢切割的照片可清楚地看出热影响区(HAZ)大小所造成的差异。
传统激光因热影响区过大,无法进行精微切割,大大限制了其应用领域。
微水刀激光(Laser Micro Jet)以其优异的断热切割技术,大幅开拓精密微加工的领域,催生了许多新产品、新工艺。
Low-k Wafer 切割的问题原来只用于高阶产品的超薄晶圆(Ultra thin wafer )已经越来越普及,而且越来越薄。
处理超薄晶圆不仅是Silicon substrate 本身厚度的问题,在加上许多硬脆易碎及延展性高的金属Pad 后,问题更加复杂。
钻石刀片既使小心翼翼地切过Silicon substrate, 但金属层的碎屑却可能包粘在钻石颗粒上,使切削能力大打折扣。
此时若维持进刀速度,必然造成破片断刀的结果。
各主要划片机厂, 如Disco、TSK.等均转向激光,由此可见机械方式已经到了克服不了的困境。
不幸的是激光也有激光的问题。
在此,就钻石刀片,传统激光及微水刀激光的特性探讨如下:a. Diamond Saw:易造成wafer 表面崩边或龜裂。
遇金属层易断刀破片,切割速度慢,破片率高。
但在切割Silicon substrate 时断面平整,深度控制容易。
在使用DAF(Die Attach Film)时可正好切穿DAF 而不伤Blue Tape。
b. 传统激光:传统激光(Conventional Laser)或称干式激光(Dry Laser),因为热影响区的问题未克服,仅能用在低阶晶片,如太阳能晶片等。
采用三倍频方式虽然有改善,但也只能划划线。
如果切穿同样烧伤晶片和DAF 及Blue Tape。
c. 微水刀激光:可以轻易去除切割道表层材料及Silicon substrate。
切割超薄片(50um)时速度比diamondsaw 快數倍。
缺点为与干式激光同样会烧坏DAF,切割断面不如机械磨削光滑。
从上述看来各有所长, 也各有缺陷.图2: 不锈钢片以传统激光切割, 热损伤严重.图3: 不锈钢片以微水刀激光切割2. 解决方案既然没有十全十美的方法,只好退而求其次。
对Diamond Saw而言,难解决的是Wafer的表层材料。
对微水刀激光而言,头痛的是会烧坏DAF。
因此如各取所长,分成两个步骤处理,就差强人意。
首先用微水刀激光划浅浅的一刀,加工手段上称之为开槽(Grooving),以清除切割道上所有的材料,不管是金属或易碎材料。
Laser Microjet可以选用与切割道(Cutting Street)同宽的喷嘴,像推土机一样一次推掉Top layers上各种找麻烦的材料,露出Silicon Substrate。
再接着用Diamond Saw切穿silicon substrate和DAF,并刚好停在Blue Tape表面上。
因为Grooving只能去除表层几微米的深度,微水刀激光可以250mm/sec的高速进行。
就生产线的平衡来看,一台微水刀激光系统需至少五台以上Diamond Saw与之配合才消化得掉。
从设备投资的角度来看,这似乎是最有效益的方式。
不仅不会因为引进新设备而闲置旧机器,反而会提高产能,真正相辅相成,相得益彰。
图4. Laser MicroJet在低k晶圆上开槽划片的情况Kerf宽度:50微米深度:12微米切割速度:250mm/sec其他应用微水刀激光技术除了上述在low-k、超薄晶片之应用外,还可以作硅片钻孔(Silicon Wafer Hole drilling)、硅片挖槽开孔(Silicon Wafer Grooving and Slotting)、异形晶粒切割(Free Shape Chip Dicing)、局部减薄(Partial Thining)等。
在超薄片的Wafer Edge Grinding切去晶片外沿像刀锋一样锐利的部份,竞然使超薄片的破片率降到零,真是小兵立大功。
在欧洲已经有半导体厂以此解决了破片的难题,大幅减少了破片的损失。
Wafer钻孔虽不普及,但在微机电(MEMS)领域则常有需求。
表面上看起来微不足道的微钻孔应用,常隐藏着丰厚利润和庞大商机。
图5. Silicon wafer以微水刀激光钻孔情況. 图6. 图5放大的显微照片.除Silicon Wafer外, Laser MicroJet还可以进行多种材料的微加工,并应用于多个产业,如电子业的印刷纲板、光电业的高精密蒸镀溅镀掩模(Mask)、医疗器材中的心血管支架、汽车工业的喷嘴、航太科技中喷射引擎叶片钻孔等等。
结论就半导体晶圆切割应用而言,激光显然是一条必走之路。
钻石刀片切割已完成其历史任务, 新一代的晶片切割和微加工势必使用更新的工具。
微水刀激光技术刚一出现,就给业界解决了不少问题,接着更开拓出许多新的思考空间,如异形晶粒等。
过去许多做不到的事,有了这项工具就变得容易了。
新科技开创新机会,善用別人还不知道的工具,往往会有意想不到的收获。
References[1] Dr. Bernold Richerzhagen and Delphine Perottet, Low-K SDS solutions. 2006.3.16[2] Dr. Yasushi Kozuki and Dr. Bernold Richerzhagen, Gentle dicing of thin semiconductor materials by water- jet-guided laser, Proceedings of the 4th international congress on Laser Advanced Materials Processing,2005.[3] Dr. Bernold Richerzhagen, Synova application notes.2002~ 2006.[4] Dr. Weimin Liang, Thin wafer dicing Issuese and New Technology Cost of Ownership. FUTUREFAB International: Issue 19.。