晶圆切割处理
半导体制造工艺流程大全
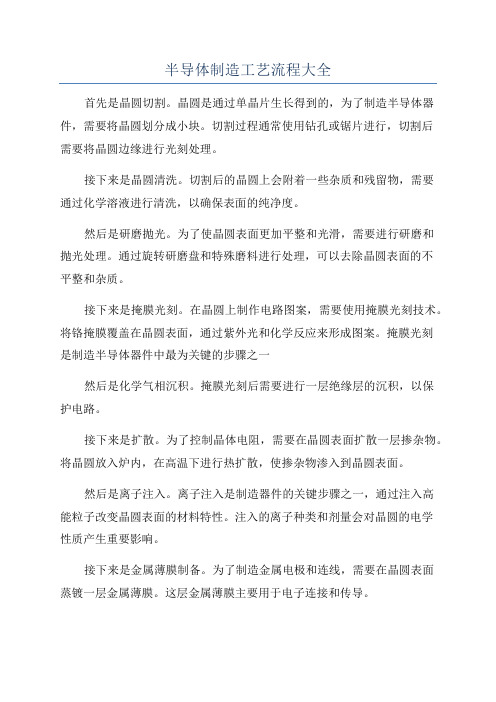
半导体制造工艺流程大全首先是晶圆切割。
晶圆是通过单晶片生长得到的,为了制造半导体器件,需要将晶圆划分成小块。
切割过程通常使用钻孔或锯片进行,切割后需要将晶圆边缘进行光刻处理。
接下来是晶圆清洗。
切割后的晶圆上会附着一些杂质和残留物,需要通过化学溶液进行清洗,以确保表面的纯净度。
然后是研磨抛光。
为了使晶圆表面更加平整和光滑,需要进行研磨和抛光处理。
通过旋转研磨盘和特殊磨料进行处理,可以去除晶圆表面的不平整和杂质。
接下来是掩膜光刻。
在晶圆上制作电路图案,需要使用掩膜光刻技术。
将铬掩膜覆盖在晶圆表面,通过紫外光和化学反应来形成图案。
掩膜光刻是制造半导体器件中最为关键的步骤之一然后是化学气相沉积。
掩膜光刻后需要进行一层绝缘层的沉积,以保护电路。
接下来是扩散。
为了控制晶体电阻,需要在晶圆表面扩散一层掺杂物。
将晶圆放入炉内,在高温下进行热扩散,使掺杂物渗入到晶圆表面。
然后是离子注入。
离子注入是制造器件的关键步骤之一,通过注入高能粒子改变晶圆表面的材料特性。
注入的离子种类和剂量会对晶圆的电学性质产生重要影响。
接下来是金属薄膜制备。
为了制造金属电极和连线,需要在晶圆表面蒸镀一层金属薄膜。
这层金属薄膜主要用于电子连接和传导。
最后是封装测试。
将制造好的晶圆进行封装,以保护器件免受环境和机械损坏。
通过测试和筛选,可以保证器件的质量和性能。
总结以上所述,半导体制造工艺流程包括晶圆切割、晶圆清洗、研磨抛光、掩膜光刻、化学气相沉积、扩散、离子注入、金属薄膜制备等多个关键步骤。
这些步骤不仅要求高度精确和耐心,而且需要高科技设备和专业技能的支持。
半导体制造工艺的不断改进和创新将推动半导体技术的进一步发展和应用。
晶圆切割工艺
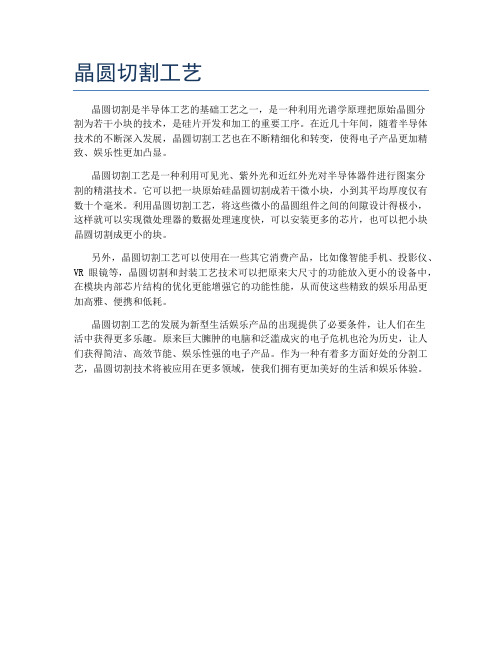
晶圆切割工艺
晶圆切割是半导体工艺的基础工艺之一,是一种利用光谱学原理把原始晶圆分
割为若干小块的技术,是硅片开发和加工的重要工序。
在近几十年间,随着半导体技术的不断深入发展,晶圆切割工艺也在不断精细化和转变,使得电子产品更加精致、娱乐性更加凸显。
晶圆切割工艺是一种利用可见光、紫外光和近红外光对半导体器件进行图案分
割的精湛技术。
它可以把一块原始硅晶圆切割成若干微小块,小到其平均厚度仅有数十个毫米。
利用晶圆切割工艺,将这些微小的晶圆组件之间的间隙设计得极小,这样就可以实现微处理器的数据处理速度快,可以安装更多的芯片,也可以把小块晶圆切割成更小的块。
另外,晶圆切割工艺可以使用在一些其它消费产品,比如像智能手机、投影仪、VR眼镜等,晶圆切割和封装工艺技术可以把原来大尺寸的功能放入更小的设备中,在模块内部芯片结构的优化更能增强它的功能性能,从而使这些精致的娱乐用品更加高雅、便携和低耗。
晶圆切割工艺的发展为新型生活娱乐产品的出现提供了必要条件,让人们在生
活中获得更多乐趣。
原来巨大臃肿的电脑和泛滥成灾的电子危机也沦为历史,让人们获得简洁、高效节能、娱乐性强的电子产品。
作为一种有着多方面好处的分割工艺,晶圆切割技术将被应用在更多领域,使我们拥有更加美好的生活和娱乐体验。
晶圆切割工艺流程
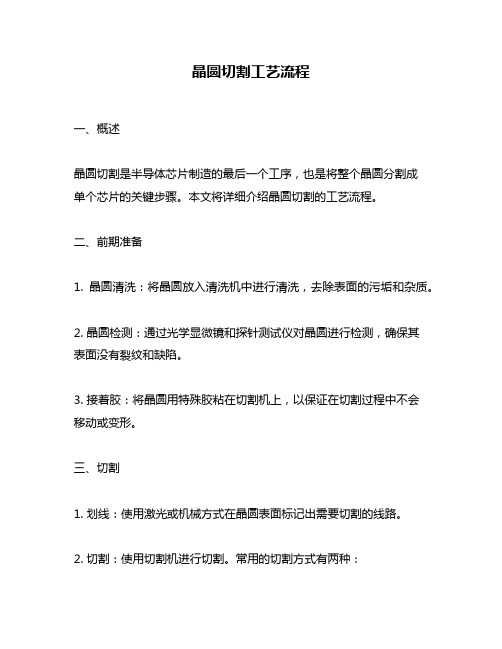
晶圆切割工艺流程一、概述晶圆切割是半导体芯片制造的最后一个工序,也是将整个晶圆分割成单个芯片的关键步骤。
本文将详细介绍晶圆切割的工艺流程。
二、前期准备1. 晶圆清洗:将晶圆放入清洗机中进行清洗,去除表面的污垢和杂质。
2. 晶圆检测:通过光学显微镜和探针测试仪对晶圆进行检测,确保其表面没有裂纹和缺陷。
3. 接着胶:将晶圆用特殊胶粘在切割机上,以保证在切割过程中不会移动或变形。
三、切割1. 划线:使用激光或机械方式在晶圆表面标记出需要切割的线路。
2. 切割:使用切割机进行切割。
常用的切割方式有两种:(1)内部分离式(dicing):通过高速旋转的金刚石锯片沿着预定好的线路进行切割,将晶圆分离成单个芯片。
(2)外部分离式(scribing):使用激光或机械方式在晶圆表面划出一条深度为几微米的线路,然后用力折断晶圆,将其分离成单个芯片。
3. 清洗:将切割好的芯片放入清洗机中进行清洗,去除表面的胶水和杂质。
四、后期处理1. 晶圆去胶:将芯片放入脱胶机中进行去胶处理,将接着胶从芯片上清除。
2. 芯片检测:通过光学显微镜和探针测试仪对芯片进行检测,确保其表面没有裂纹和缺陷。
3. 切边:使用切割机对芯片边缘进行切割,使其变得平整光滑。
4. 分选:将符合要求的芯片分别按照规格、等级等分类,并打上标记。
五、总结晶圆切割是半导体制造过程中最关键的一个环节之一。
本文介绍了晶圆切割的工艺流程,包括前期准备、切割和后期处理。
通过严格的操作流程和严密的质量控制,可以保证生产出高质量的半导体芯片。
晶圆生产流程及每道工序的关键工艺参数
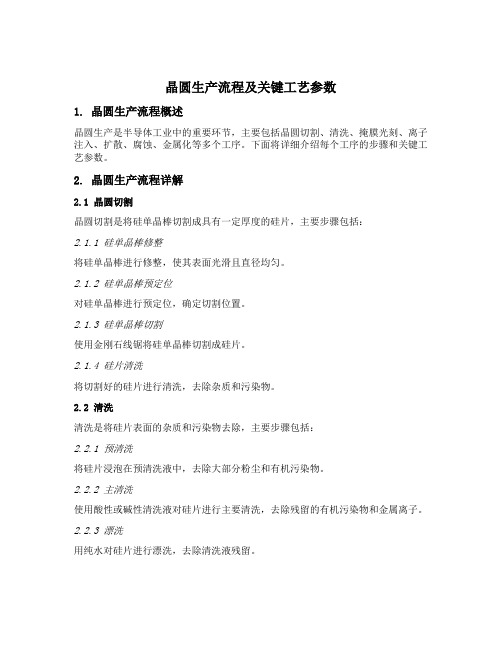
晶圆生产流程及关键工艺参数1. 晶圆生产流程概述晶圆生产是半导体工业中的重要环节,主要包括晶圆切割、清洗、掩膜光刻、离子注入、扩散、腐蚀、金属化等多个工序。
下面将详细介绍每个工序的步骤和关键工艺参数。
2. 晶圆生产流程详解2.1 晶圆切割晶圆切割是将硅单晶棒切割成具有一定厚度的硅片,主要步骤包括:2.1.1 硅单晶棒修整将硅单晶棒进行修整,使其表面光滑且直径均匀。
2.1.2 硅单晶棒预定位对硅单晶棒进行预定位,确定切割位置。
2.1.3 硅单晶棒切割使用金刚石线锯将硅单晶棒切割成硅片。
2.1.4 硅片清洗将切割好的硅片进行清洗,去除杂质和污染物。
2.2 清洗清洗是将硅片表面的杂质和污染物去除,主要步骤包括:2.2.1 预清洗将硅片浸泡在预清洗液中,去除大部分粉尘和有机污染物。
2.2.2 主清洗使用酸性或碱性清洗液对硅片进行主要清洗,去除残留的有机污染物和金属离子。
2.2.3 漂洗用纯水对硅片进行漂洗,去除清洗液残留。
2.2.4 干燥将硅片在干燥器中进行干燥,去除水分。
2.3 掩膜光刻掩膜光刻是通过光刻胶和掩膜模板将芯片图形转移到硅片上,主要步骤包括:2.3.1 光刻胶涂覆将光刻胶均匀涂覆在硅片上。
2.3.2 掩膜对位将掩膜模板对准硅片,并通过对位器进行精确定位。
2.3.3 曝光使用紫外光将掩膜模板上的芯片图形转移到硅片上。
2.3.4 显影使用显影液去除未曝光的光刻胶,形成芯片图形。
2.4 离子注入离子注入是将特定元素注入硅片表面,改变硅片的导电性能,主要步骤包括:2.4.1 离子源准备准备离子源和加速器设备,确定注入元素和能量。
2.4.2 离子束对准将离子束对准硅片表面,并通过对位器进行精确定位。
2.4.3 注入通过加速器加速离子束,使其注入硅片表面,并控制注入剂量和深度。
2.5 扩散扩散是将特定元素在硅片中进行扩散,形成PN结构,主要步骤包括:2.5.1 清洗将注入后的硅片进行清洗,去除污染物。
不同尺寸芯片在同一片晶圆的切割方法
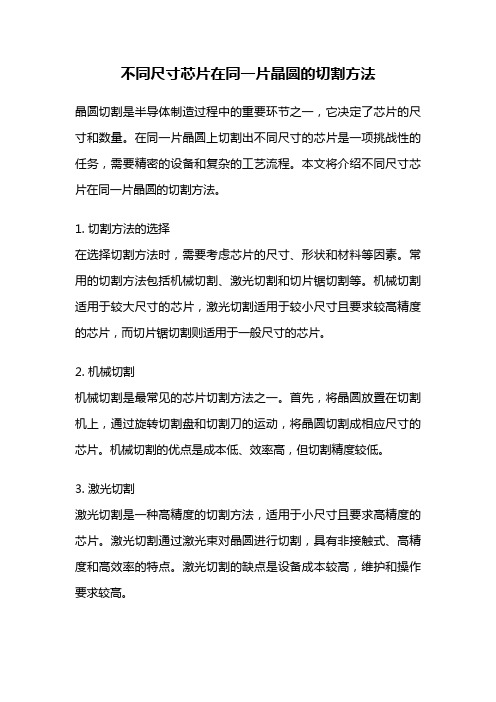
不同尺寸芯片在同一片晶圆的切割方法晶圆切割是半导体制造过程中的重要环节之一,它决定了芯片的尺寸和数量。
在同一片晶圆上切割出不同尺寸的芯片是一项挑战性的任务,需要精密的设备和复杂的工艺流程。
本文将介绍不同尺寸芯片在同一片晶圆的切割方法。
1. 切割方法的选择在选择切割方法时,需要考虑芯片的尺寸、形状和材料等因素。
常用的切割方法包括机械切割、激光切割和切片锯切割等。
机械切割适用于较大尺寸的芯片,激光切割适用于较小尺寸且要求较高精度的芯片,而切片锯切割则适用于一般尺寸的芯片。
2. 机械切割机械切割是最常见的芯片切割方法之一。
首先,将晶圆放置在切割机上,通过旋转切割盘和切割刀的运动,将晶圆切割成相应尺寸的芯片。
机械切割的优点是成本低、效率高,但切割精度较低。
3. 激光切割激光切割是一种高精度的切割方法,适用于小尺寸且要求高精度的芯片。
激光切割通过激光束对晶圆进行切割,具有非接触式、高精度和高效率的特点。
激光切割的缺点是设备成本较高,维护和操作要求较高。
4. 切片锯切割切片锯切割是一种常用的切割方法,适用于一般尺寸的芯片。
切片锯切割通过旋转切割盘和带有切割锯片的切割机,对晶圆进行切割。
切片锯切割的优点是成本适中、效率高,但切割精度相对较低。
5. 切割工艺流程不同尺寸芯片的切割工艺流程相似,但具体参数和设备设置会有所不同。
一般而言,切割工艺流程包括以下几个步骤:(1) 切割前的准备:对晶圆进行清洗和检查,确保表面平整和无瑕疵。
(2) 切割参数设置:根据芯片尺寸和要求,设置切割机的参数,如切割速度、刀具压力等。
(3) 切割过程:将晶圆放置在切割机上,启动切割机并调整参数,开始切割过程。
(4) 切割后处理:将切割好的芯片进行清洗和检查,确保质量合格。
(5) 包装和封装:对切割好的芯片进行包装和封装,以保护芯片不受损坏。
6. 工艺优化和改进为了提高切割效率和精度,工艺优化和改进是必不可少的。
可以通过优化切割参数、改进切割设备和提高工艺控制等方式来实现。
芯片切割工艺流程
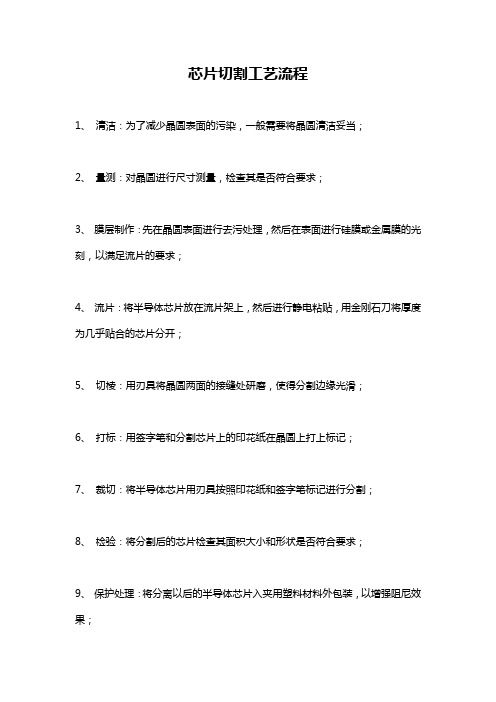
芯片切割工艺流程
1、清洁:为了减少晶圆表面的污染,一般需要将晶圆清洁妥当;
2、量测:对晶圆进行尺寸测量,检查其是否符合要求;
3、膜层制作:先在晶圆表面进行去污处理,然后在表面进行硅膜或金属膜的光刻,以满足流片的要求;
4、流片:将半导体芯片放在流片架上,然后进行静电粘贴,用金刚石刀将厚度为几乎贴合的芯片分开;
5、切棱:用刃具将晶圆两面的接缝处研磨,使得分割边缘光滑;
6、打标:用签字笔和分割芯片上的印花纸在晶圆上打上标记;
7、裁切:将半导体芯片用刃具按照印花纸和签字笔标记进行分割;
8、检验:将分割后的芯片检查其面积大小和形状是否符合要求;
9、保护处理:将分离以后的半导体芯片入夹用塑料材料外包装,以增强阻尼效果;
10、存放:将分割后的半导体芯片安全的存储在操作房中保持恒温、恒湿环境。
晶圆切割制程
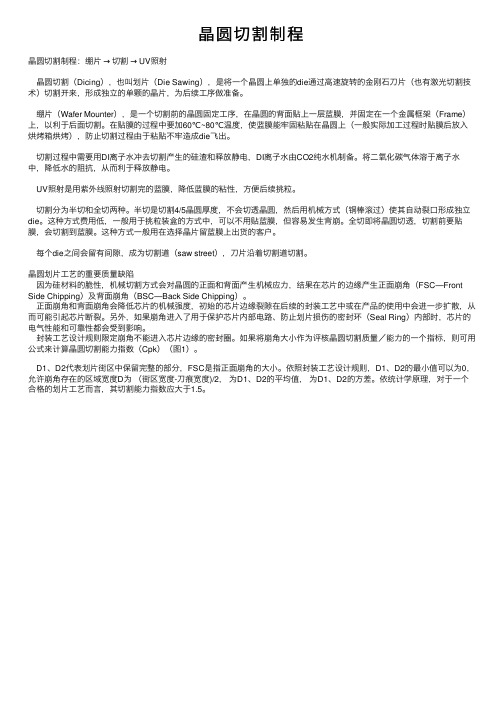
晶圆切割制程晶圆切割制程:绷⽚→切割→ UV照射晶圆切割(Dicing),也叫划⽚(Die Sawing),是将⼀个晶圆上单独的die通过⾼速旋转的⾦刚⽯⼑⽚(也有激光切割技术)切割开来,形成独⽴的单颗的晶⽚,为后续⼯序做准备。
绷⽚(Wafer Mounter),是⼀个切割前的晶圆固定⼯序,在晶圆的背⾯贴上⼀层蓝膜,并固定在⼀个⾦属框架(Frame)上,以利于后⾯切割。
在贴膜的过程中要加60℃~80℃温度,使蓝膜能牢固粘贴在晶圆上(⼀般实际加⼯过程时贴膜后放⼊烘烤箱烘烤),防⽌切割过程由于粘贴不牢造成die飞出。
切割过程中需要⽤DI离⼦⽔冲去切割产⽣的硅渣和释放静电,DI离⼦⽔由CO2纯⽔机制备。
将⼆氧化碳⽓体溶于离⼦⽔中,降低⽔的阻抗,从⽽利于释放静电。
UV照射是⽤紫外线照射切割完的蓝膜,降低蓝膜的粘性,⽅便后续挑粒。
切割分为半切和全切两种。
半切是切割4/5晶圆厚度,不会切透晶圆,然后⽤机械⽅式(铜棒滚过)使其⾃动裂⼝形成独⽴die。
这种⽅式费⽤低,⼀般⽤于挑粒装盒的⽅式中,可以不⽤贴蓝膜,但容易发⽣背崩。
全切即将晶圆切透,切割前要贴膜,会切割到蓝膜。
这种⽅式⼀般⽤在选择晶⽚留蓝膜上出货的客户。
每个die之间会留有间隙,成为切割道(saw street),⼑⽚沿着切割道切割。
晶圆划⽚⼯艺的重要质量缺陷因为硅材料的脆性,机械切割⽅式会对晶圆的正⾯和背⾯产⽣机械应⼒,结果在芯⽚的边缘产⽣正⾯崩⾓(FSC—Front Side Chipping)及背⾯崩⾓(BSC—Back Side Chipping)。
正⾯崩⾓和背⾯崩⾓会降低芯⽚的机械强度,初始的芯⽚边缘裂隙在后续的封装⼯艺中或在产品的使⽤中会进⼀步扩散,从⽽可能引起芯⽚断裂。
另外,如果崩⾓进⼊了⽤于保护芯⽚内部电路、防⽌划⽚损伤的密封环(Seal Ring)内部时,芯⽚的电⽓性能和可靠性都会受到影响。
封装⼯艺设计规则限定崩⾓不能进⼊芯⽚边缘的密封圈。
晶圆生产主要工艺流程
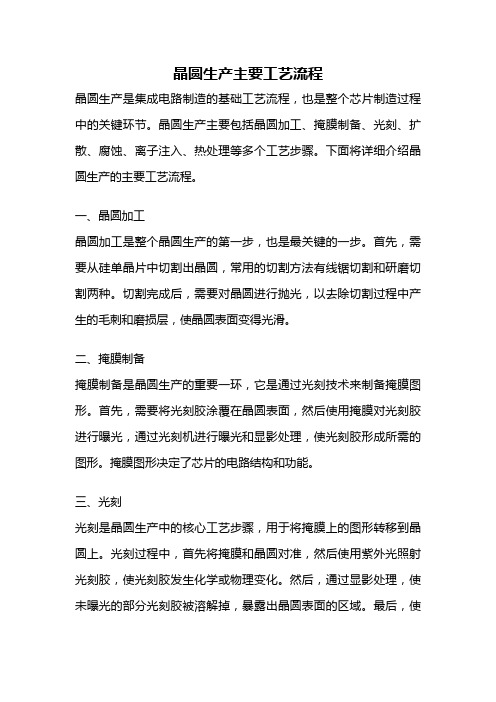
晶圆生产主要工艺流程晶圆生产是集成电路制造的基础工艺流程,也是整个芯片制造过程中的关键环节。
晶圆生产主要包括晶圆加工、掩膜制备、光刻、扩散、腐蚀、离子注入、热处理等多个工艺步骤。
下面将详细介绍晶圆生产的主要工艺流程。
一、晶圆加工晶圆加工是整个晶圆生产的第一步,也是最关键的一步。
首先,需要从硅单晶片中切割出晶圆,常用的切割方法有线锯切割和研磨切割两种。
切割完成后,需要对晶圆进行抛光,以去除切割过程中产生的毛刺和磨损层,使晶圆表面变得光滑。
二、掩膜制备掩膜制备是晶圆生产的重要一环,它是通过光刻技术来制备掩膜图形。
首先,需要将光刻胶涂覆在晶圆表面,然后使用掩膜对光刻胶进行曝光,通过光刻机进行曝光和显影处理,使光刻胶形成所需的图形。
掩膜图形决定了芯片的电路结构和功能。
三、光刻光刻是晶圆生产中的核心工艺步骤,用于将掩膜上的图形转移到晶圆上。
光刻过程中,首先将掩膜和晶圆对准,然后使用紫外光照射光刻胶,使光刻胶发生化学或物理变化。
然后,通过显影处理,使未曝光的部分光刻胶被溶解掉,暴露出晶圆表面的区域。
最后,使用蚀刻或其他加工方法,将暴露出来的晶圆表面进行加工。
四、扩散扩散是晶圆生产中的一种加工方法,用于控制晶圆表面杂质的浓度和分布。
扩散过程中,将晶圆置于高温炉中,与气体或液体中的杂质进行反应,使杂质从液体或气体中扩散到晶圆表面。
扩散后的晶圆表面形成了所需的掺杂区域,用于形成芯片中的电子器件。
五、腐蚀腐蚀是晶圆生产中的一种加工方法,用于去除晶圆表面的氧化层或其他不需要的杂质。
腐蚀过程中,将晶圆放置在腐蚀液中,使腐蚀液与晶圆表面发生化学反应,去除表面的氧化层或杂质。
腐蚀后的晶圆表面更加平整和清洁,有利于后续工艺的进行。
六、离子注入离子注入是晶圆生产中的一种加工方法,用于控制晶圆中杂质的浓度和分布。
离子注入过程中,将晶圆放置在离子注入机中,加速并定向注入离子束到晶圆表面。
注入的离子将与晶体中的原子进行替换或形成杂质,从而改变晶圆的电学性质。
- 1、下载文档前请自行甄别文档内容的完整性,平台不提供额外的编辑、内容补充、找答案等附加服务。
- 2、"仅部分预览"的文档,不可在线预览部分如存在完整性等问题,可反馈申请退款(可完整预览的文档不适用该条件!)。
- 3、如文档侵犯您的权益,请联系客服反馈,我们会尽快为您处理(人工客服工作时间:9:00-18:30)。
3.2 Centering Unit
• High accuracy Wafer Centering • Safe handling for thin wafer • No need conversion
Simple & Convenience
PDF created with pdfFactory trial version
Wafer hand
Cutter width -Tool free
Auto conversion Ring frame Buffer
Wafer & frame transfer
In/outlet Rail width
Tape width Simple & Convenience
ID Camera position
Simple & Convenience
PDF created with pdfFactory trial version
1.Feature 1. All process in a single machine 2. Safe handling for thin wafer 3. Stable tape removing device 4. Small Footprint 5. Easy conversion
Peeling bar position
OCR bar code position
PDF created with pdfFactory trial version
5. Special function (Dynatech Patent)
Chuck cleaning unit
Simple & Convenience
PDF created with pdfFactory trial version
6. MDS Capability Comparison Chart
No 1 2 3 4 5 6 7 8 9 10 Comparison Items Footprint Tape Changeover Time Chuck Surface Cleaner Tape Width Adjustment Cutter Blade Lifetime Tape Consumption Set Up Time UPEH Conversion Time Remove Bar (Tape rem oval) Chuck Table Remove Tape Air Locker Convenience DYNATECH (Lapmaster) 1830(d) x 2400(w) x 2240(h) mm 10 minutes Built in Automated 20,000 times 8”(per 1pc) ― 300mm 12”(per 1pc) ― 400mm 1 week 8” : 30pcs 12” : 28pcs Within 15 minutes Special function to prevent wafe r breakage (Patent Pending) Reasonable price(Less than 6 0% approx.) Available Easy changeover Tape (10 minutes) Available to individual T 2345(d) x 2230(w) x 2100(h) mm 15~20 minutes Not available Manual 10,000 times 8”(per 1pc) ― 320mm 12”(per 1pc) ― 430mm More than 1 week 8” : 20pcs 12” : 18pcs More than 30 minutes Easy wafer breakage D 2050(d) x 3700(w) x 1900(h) mm 30 minutes Not available Manual No Cutting Function 8”(per 1pc) ― 290mm 12”(per 1pc) ― 390mm More than 1 week 8” : 22pcs 12” : 20pcs More than 30 minutes No data
Simple & Convenience
PDF created with pdfFactory trial version
3.Function of each unit
Wafer Mount
OCR Bar code (Optional item)
Tape remove Robert hand
END
MAGAZINE CHECK
END
Simple & Convenience
PDF created with pdfFactory trial version
4. Conversion process
Manual conversion
Mount & Detape chuck - Tool free
3.6 OCR Bar code printing System (Option)
• CCD Camera reads wafer ID. • Bar code prints wafer ID • Attach label to frame tape
3.7 Unload Frame Cassette
PDF created with pdfFactory trial version
4. Conversion Process
RECIPE BUTTON
Auto conversion
MANUAL CONVERSION
RING FRAME PICKER
RING FRAME BUFFER
Unloader
Frame transfer
Simple & Convenience
PDF created with pdfFactory trial version
3.1 Wafer Transfer Robot hand
• Auto balance function • Robot transfers wafer from CMG
Table of Contents
1. Feature 2. MDS process 3. Function of Each Unit 4. Conversion process 5. Special function (Dynatech patent) 6. MDS Capability Comparison Chart 7. Goal 8. Utility
• After label printing, frame placed on the rail • Pusher slides finished frame into frame cassette • 2 Floors elevator loads dual frame cassettes
Simple & Convenience
11 12 13
High price Not available Narrow space to change Tape Not easy De-Tape Roll Not available to use Stand Alone No data
High price Available No data
3. Wafer Alignment : < 0.05mm 4. No wafer broken rate & Zero Void 5. Precut, Normal and UV tape capability 6. The operation system can be select in-line 7. Air cleaning function to eliminate the particle of chuck table 8. Easy conversion
START
RAIL WIDTHቤተ መጻሕፍቲ ባይዱ
MOUNTER CHUCK
TAPE WIDTH DETAPE CHUCK OCR PRINT POSITION WAFER HAND I.D CAEMRA POSITION CUTTER POSITION
BOND ROLLER POSITION
PEER BAR POSTION
5. Special function (Dynatech Patent)
Tape remove unit
- No need to parameter adjustment depend on wafer thickness - Automatic adjustment depend on wafer condition from CMG (Wafer size & thickness) - Prevent wafer damage & breakage (Spring tension control)
- Clean the chuck surface before wafer loading - Prevent wafer damage & breakage
Simple & Convenience
PDF created with pdfFactory trial version
Simple & Convenience
PDF created with pdfFactory trial version
3.4 Wafer Mount
• Attach dicing tape to wafer after air blower and suction cleaning • Round cutting • Turn over(180˚)mounted frame after over(180˚ mounting