注塑模具各类问题原因分析及解决办法
注塑模具不良现象的原因及处理办法

不良现象的原因及处理办法1.充填不足2.溢料3.气孔4.波纹5.银条纹6.表面晕喑7.融合线8.气泡9.黑条纹及烧痕10.龟裂11.离模溢料12.弯曲13.脱模不良14.直浇口的脱模不良15.材料的叠边不良不良现象及其原因处理办法3气孔在材料为充分干燥时,是挥发物或空气所致;大多时候发生在产品胶厚的位置,实际是材料的收缩引起的真空气泡[1] 流道或浇口过小[2] 成形品的壁厚差大[3] 材料的温度高[4] 离浇口的流动距离长[5] 脱模过早[6] 射出压力低[7] 冷却时间短[8] 保压不充分4 波纹[1]材料流动不畅i)将流道或浇口扩展。
ii)增强射出压力。
i)尽量使壁厚度要均匀。
ii)要使壁厚差不显著。
i)降低材料的温度。
ii)要改进发生气孔的部位的冷却条件。
i)增强射出压力。
ii)加快射出速度。
iii)在成形品上设置棱或厚层部位。
i)延长冷却时间。
i)增强射出压力。
i)延长冷却时间。
ii)降低模具温度。
i)延长保压时间。
ii)增强保压压力。
[2]模具温度低[3]进浇口过小i)升高材料的温度。
ii)换用流动性高的材料。
iii)增强射出压力。
iiii)设定冷料井。
加速射出速度。
i)采用热油机或热水机提高模温。
i)加大进浇口。
ii)升高材料的温度。
5 银条纹[1]水分或挥发成分[2]材料的温度过高[3]模具温度低[4]排气不良[5]成形品或模具的设计不良i)使材料充分干燥。
ii)使用料斗式装载机。
i)降低材料的温度。
ii)放慢射出速度。
i)升高模具温度。
i)在模具耦合面加上排气用的条缝。
ii)放宽模具与推挺钉梢的间隙。
iii)设置真空排气结构间隙i)放大浇口或流道。
ii)消除急剧的壁厚差现象。
[6]模具面上的水分或挥发成分[8]混入夹杂的材料[9]螺桨的运转不当6.表面晕暗[1] 润滑或挥发成分过多[2]脱模材过多7 融合线------实际是2股或多股材料汇合时,材料的融合线。
与材料汇合时,材料的粘度有很大的关系。
注塑过程中常见的问题及解决方案

注塑过程中常见的问题及解决方案一、飞边(披锋)1. 问题描述- 这飞边就像塑料偷偷长出来的小翅膀,在注塑件的边缘或者分型面那里冒出来,看着可闹心了。
就像好好的一块蛋糕,边缘突然多出了一些不规则的奶油坨坨。
2. 解决方案- 首先得检查模具的合模力。
要是合模力不够,那塑料就会像调皮的小孩从门缝里挤出来。
适当增加合模力,把模具紧紧抱住,让塑料乖乖待在该待的地方。
- 模具的磨损也会导致飞边。
就像穿破了的鞋子会漏脚指头一样,磨损的模具缝隙变大了。
这时候就得修模啦,把那些磨损的地方补一补或者磨平。
- 注塑压力也不能太大。
如果压力太大,塑料就像被大力士猛推的水,到处乱流。
降低注塑压力,找到一个合适的值,既能把模具填满,又不会让塑料溢出来。
二、短射(缺料)1. 问题描述- 短射就像给一个杯子倒水,结果没倒满一样。
注塑件看着不完整,有些地方该有塑料的却空着,就像一个没发育好的小怪物。
2. 解决方案- 先看看注塑压力是不是太小。
压力小的话,塑料就像没力气的小蚂蚁,爬不到模具的每个角落。
增加注塑压力,让塑料充满整个模具型腔。
- 塑料的流动性也很关键。
如果塑料太黏,就像浓稠的糨糊,很难流到模具的远端。
这时候可以提高料筒温度,让塑料变得稀一点,流动性更好,就像把糨糊加热变成稀粥一样,能顺利流到各个地方。
- 浇口尺寸也可能有问题。
要是浇口太小,就像一个小得可怜的水龙头,水流不出来多少。
适当扩大浇口尺寸,让塑料能畅快地流进模具。
三、气泡(气穴)1. 问题描述2. 解决方案- 注塑速度可能太快了。
塑料像一阵风呼呼地冲进模具,把空气都裹在里面了。
降低注塑速度,让塑料慢慢流进去,就像散步一样,这样空气就有机会跑出来了。
- 模具的排气也很重要。
如果模具没有排气孔或者排气不良,空气就被困在里面出不来。
在模具上开排气槽或者使用透气钢材料,给空气一条逃跑的路。
- 塑料干燥不彻底也会产生气泡。
如果塑料里有水份,加热的时候就会变成水蒸气,形成气泡。
注塑缺陷原因分析与解决方案

注塑缺陷原因分析与解决方案注塑是一种常见的塑料加工方法,广泛应用于各个行业。
然而,在注塑过程中,可能会出现各种缺陷,如气泡、翘曲、短射等问题,影响产品的质量和性能。
为了解决这些问题,我们需要进行缺陷原因分析,并提出相应的解决方案。
一、缺陷原因分析1. 气泡缺陷气泡是注塑过程中常见的缺陷之一。
其主要原因可能包括以下几个方面:- 塑料材料中含有挥发性物质,如水分、溶剂等,这些物质在高温下蒸发产生气泡。
- 注塑机温度设置不当,过高的温度会使塑料材料中的气体膨胀形成气泡。
- 注塑模具设计不合理,存在气孔或死角,导致塑料充填不均匀,形成气泡。
2. 翘曲缺陷翘曲是注塑产品常见的缺陷之一,其主要原因可能包括以下几个方面:- 注塑机温度不均匀,导致塑料材料在冷却过程中收缩不均匀,引起产品翘曲。
- 注塑模具设计不合理,存在过于薄弱的部位,无法承受注塑过程中的压力,导致产品变形。
- 注塑过程中冷却时间不足,使得产品在脱模后还未完全固化,导致变形。
3. 短射缺陷短射是指注塑产品未能充填满模具而产生的缺陷,其主要原因可能包括以下几个方面:- 注塑机温度设置不当,导致塑料材料粘度过高,无法充填满模具。
- 注塑模具设计不合理,存在过于狭窄的充填道或浇口,导致塑料流动受阻,无法充填满模具。
- 注塑过程中注射速度过快,导致塑料材料无法充填满模具。
二、解决方案1. 气泡缺陷的解决方案- 检查塑料材料的质量,确保其含水量和挥发性物质含量符合要求。
- 调整注塑机的温度,确保塑料材料在注塑过程中不会过热。
- 优化注塑模具的设计,避免气孔和死角的存在,确保塑料充填均匀。
2. 翘曲缺陷的解决方案- 调整注塑机的温度分布,确保塑料材料在冷却过程中收缩均匀。
- 优化注塑模具的设计,增加产品的结构强度,避免过于薄弱的部位。
- 增加注塑过程中的冷却时间,确保产品完全固化后再进行脱模。
3. 短射缺陷的解决方案- 调整注塑机的温度,降低塑料材料的粘度,促进充填。
注塑缺陷原因分析与解决方案
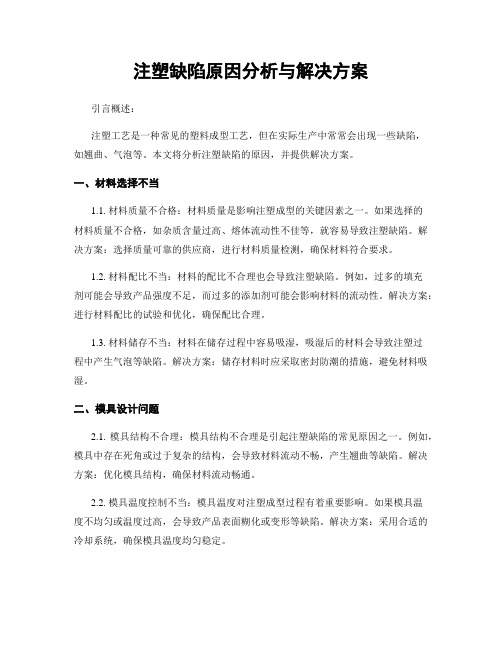
注塑缺陷原因分析与解决方案引言概述:注塑工艺是一种常见的塑料成型工艺,但在实际生产中常常会出现一些缺陷,如翘曲、气泡等。
本文将分析注塑缺陷的原因,并提供解决方案。
一、材料选择不当1.1. 材料质量不合格:材料质量是影响注塑成型的关键因素之一。
如果选择的材料质量不合格,如杂质含量过高、熔体流动性不佳等,就容易导致注塑缺陷。
解决方案:选择质量可靠的供应商,进行材料质量检测,确保材料符合要求。
1.2. 材料配比不当:材料的配比不合理也会导致注塑缺陷。
例如,过多的填充剂可能会导致产品强度不足,而过多的添加剂可能会影响材料的流动性。
解决方案:进行材料配比的试验和优化,确保配比合理。
1.3. 材料储存不当:材料在储存过程中容易吸湿,吸湿后的材料会导致注塑过程中产生气泡等缺陷。
解决方案:储存材料时应采取密封防潮的措施,避免材料吸湿。
二、模具设计问题2.1. 模具结构不合理:模具结构不合理是引起注塑缺陷的常见原因之一。
例如,模具中存在死角或过于复杂的结构,会导致材料流动不畅,产生翘曲等缺陷。
解决方案:优化模具结构,确保材料流动畅通。
2.2. 模具温度控制不当:模具温度对注塑成型过程有着重要影响。
如果模具温度不均匀或温度过高,会导致产品表面糊化或变形等缺陷。
解决方案:采用合适的冷却系统,确保模具温度均匀稳定。
2.3. 模具磨损严重:模具长时间使用后会出现磨损,磨损严重的模具会导致产品尺寸不准确或表面粗糙等缺陷。
解决方案:定期检查和维护模具,及时更换磨损严重的模具部件。
三、注塑工艺参数设置不当3.1. 注射压力过高或过低:注射压力是影响注塑成型的关键参数之一。
如果注射压力过高,会导致产品变形或开裂,而注射压力过低则会导致产品表面光洁度不高。
解决方案:根据产品要求和材料特性,合理设置注射压力。
3.2. 注射速度不合理:注射速度对产品的充填和冷却过程有着重要影响。
如果注射速度过快,会导致产品内部产生气泡或短射,而注射速度过慢则会导致产品表面瑕疵。
模具注塑常见问题及解决方法

模具注塑常见问题及解决方法模具注塑是一种常见的制造工艺,广泛应用于汽车、电子、家电等行业。
然而,在注塑过程中常会遇到一些问题,例如产品质量不合格、生产效率低下等。
本文将针对这些常见问题进行分析,并提出相应的解决方法。
1. 产品尺寸不准确产品尺寸不准确是模具注塑过程中常见的问题之一。
造成尺寸不准确的原因可能有很多,例如模具设计不合理、注塑机调试不当等。
解决这个问题的方法是对模具进行优化设计,确保模具的尺寸精度和稳定性;同时,对注塑机进行精确调试,保证注塑过程的准确性。
2. 产品表面缺陷产品表面缺陷是另一个常见的问题,例如气泡、痕迹、烧焦等。
这些表面缺陷会影响产品的外观和质量。
要解决这个问题,可以从以下几个方面入手:优化模具通气系统,确保注塑过程中的气体能够顺利排出;调整注塑参数,控制注塑温度和压力,避免过高或过低造成烧焦或气泡;定期清洁模具,防止灰尘和杂质对产品表面造成影响。
3. 模具磨损严重模具在长期使用过程中会出现磨损,导致产品尺寸不准确或者产生其他问题。
要解决这个问题,可以采取以下几种措施:定期对模具进行保养和维护,及时更换磨损严重的零部件;使用高质量的模具材料,提高模具的耐磨性;注塑过程中控制好注塑温度和压力,避免过高过低造成模具磨损。
4. 注塑机故障注塑机故障是导致生产效率低下的主要原因之一。
为了避免注塑机故障,可以采取以下几个措施:定期对注塑机进行维护和保养,清洁注塑机内部的杂质和积聚物;使用高质量的注塑机零部件,避免因零部件质量差导致故障;培训操作人员,提高其对注塑机的操作技能和维修能力。
5. 塑料材料选择不当塑料材料的选择对注塑产品的质量和性能有很大影响。
如果选择的塑料材料不合适,可能会导致产品强度不足、耐热性差等问题。
因此,在进行模具注塑之前,应仔细选择合适的塑料材料,根据产品的要求和使用环境来进行选择。
6. 生产成本过高生产成本过高是许多企业关注的问题。
要降低生产成本,可以从以下几个方面入手:优化模具设计,减少材料的浪费;提高注塑机的效率,减少能耗;采用高效的生产工艺,提高生产效率。
注塑缺陷原因分析与解决方案
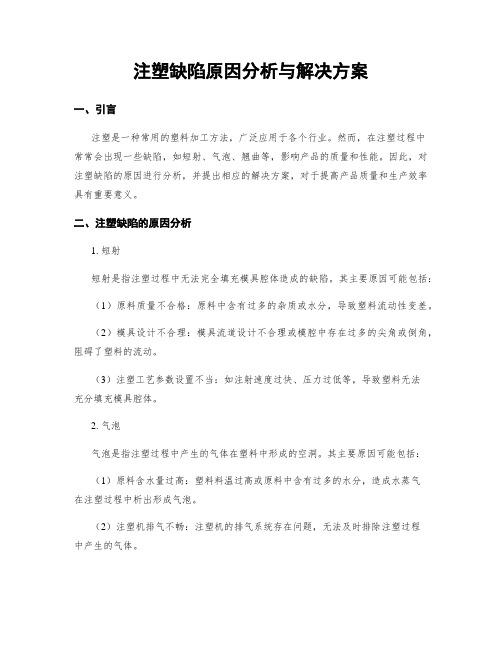
注塑缺陷原因分析与解决方案一、引言注塑是一种常用的塑料加工方法,广泛应用于各个行业。
然而,在注塑过程中常常会出现一些缺陷,如短射、气泡、翘曲等,影响产品的质量和性能。
因此,对注塑缺陷的原因进行分析,并提出相应的解决方案,对于提高产品质量和生产效率具有重要意义。
二、注塑缺陷的原因分析1. 短射短射是指注塑过程中无法完全填充模具腔体造成的缺陷。
其主要原因可能包括:(1)原料质量不合格:原料中含有过多的杂质或水分,导致塑料流动性变差。
(2)模具设计不合理:模具流道设计不合理或模腔中存在过多的尖角或倒角,阻碍了塑料的流动。
(3)注塑工艺参数设置不当:如注射速度过快、压力过低等,导致塑料无法充分填充模具腔体。
2. 气泡气泡是指注塑过程中产生的气体在塑料中形成的空洞。
其主要原因可能包括:(1)原料含水量过高:塑料料温过高或原料中含有过多的水分,造成水蒸气在注塑过程中析出形成气泡。
(2)注塑机排气不畅:注塑机的排气系统存在问题,无法及时排除注塑过程中产生的气体。
(3)注塑工艺参数设置不当:如注射速度过快、压力过高等,造成塑料内部气体无法顺利排出。
3. 翘曲翘曲是指注塑制品在冷却后出现变形的现象。
其主要原因可能包括:(1)模具温度不均匀:模具温度不均匀导致注塑制品冷却不均匀,从而引起翘曲。
(2)注塑过程中的应力积累:注塑过程中,塑料在注射后会受到冷却和收缩的影响,如果释放不及时,会导致应力积累引起翘曲。
(3)注塑工艺参数设置不当:如注射速度过快、冷却时间过短等,造成塑料冷却不充分,引起翘曲。
三、注塑缺陷的解决方案1. 短射的解决方案(1)优化原料质量:选择质量合格的原料,避免杂质和水分的存在。
(2)优化模具设计:合理设计模具流道,避免尖角和倒角的存在,保证塑料的顺畅流动。
(3)优化注塑工艺参数:合理设置注射速度和压力,确保塑料能够充分填充模具腔体。
2. 气泡的解决方案(1)控制原料含水量:确保塑料料温适宜,原料中的水分含量符合要求。
注塑模具常见缺陷问题及改进方案
改进方法(2)
注塑机 工艺条件
▪检查止逆阀和料筒内壁是否磨损严重,上述磨损会导致
注塑压力和注塑量损失严重。
▪检查加料口是否有料或是否架桥。
▪增大注塑压力 ▪增大注塑速度,增强剪切热 ▪增大注塑量 ▪增大料筒温度和模具温度
21
成型问题-银丝/水花
银纹是指水分、空气或炭化物顺着流动方向在制件表面呈现发射状分 布的一种表面缺陷。
17
成型问题-欠注(缺料)
•欠注是指模具型腔不能被完全填充满的一种现象。
欠注形成原因
任何阻止聚合物熔体流动或使聚合物注塑量不足的因素均可能导致欠注现象。这 些因素包括:
• 熔体温度、模具温度或注塑压力和速度过低 • 原料塑化不均 • 排气不良 • 原料流动性不足 • 制件太薄或浇口尺寸太小 • 聚合物熔体由于结构设计不合理导致过早硬化
气眼可能引起的问题: 困在型腔内气体不能被及时排出,易导致出现表面 起泡,制件内部夹气,注塑不满等现象。
2
案例 (表面起泡)
Air bubble cut open
3
改进方法
结构设计 模具设计
工艺条件
• 减少厚度的不一致,尽量保证壁厚均匀. ▪ 在最后填充的地方增设排气口 ▪ 重新设计浇口和流道系统. ▪ 保证排气口足够大,使气体有足够的时间和空间排走.
5
改进方法
注塑机 工艺条件
•选择合适的注塑机吨位 •检查料筒内表面、螺杆表面是否刮伤积料. •降低料筒和喷嘴的温度. •清洁注塑过程的各个环节. •避免已经产生黑点/黑纹的料被重新回收利用.
6
案例 (黑纹)
7
改进方法
材料 模具设计
•采用无污染的原材料 •将材料置于相对封闭的储料仓中 •增加材料的热稳定性
注塑成型常见不良现象及处理措施
注塑成型常见不良现象及处理措施注塑成型常见的不良现象有以下几种:
1. 短射:指注塑料进模型中未充满模腔,导致产品缺陷。
处理措施:增加注射
压力、延长注射时间、增加料缸温度、增加模具温度、增加模具出料口直径等。
2. 气泡:指产品表面或者内部浮现气泡,影响产品质量。
处理措施:增加注射
压力、延长注射时间、增加模具温度、增加料缸温度、增加模具出料口直径、增加模具排气孔等。
3. 热熔线:指产品表面浮现细小的线状缺陷,通常是由于注射速度过快导致的。
处理措施:减小注射速度、增加模具温度、增加模具出料口直径等。
4. 毛刺:指产品表面浮现细小的凸起,通常是由于模具设计不合理或者模具磨
损导致的。
处理措施:修复模具、修改模具设计、增加模具温度、增加模具出料口直径等。
5. 缩水:指产品尺寸缩小,通常是由于注射压力不足或者冷却时间不足导致的。
处理措施:增加注射压力、延长冷却时间、增加模具温度等。
6. 毛洞:指产品表面或者内部浮现凹陷,通常是由于注射速度过快或者模具设
计不合理导致的。
处理措施:减小注射速度、修改模具设计、增加模具温度等。
处理不良现象的关键是找到问题的根源,然后针对性地采取相应的处理措施。
同时,注塑成型过程中的参数控制和模具维护也是关键的因素,需要进行定期检查和调整。
注塑模具常见缺陷、产生原因和调整方法表
制件பைடு நூலகம்量不好:
1.有飞边
2.有缺料
3.有顶白
4.有拖花
5.变形大
6.级位大
7.溶接线明显
1.配合间隙过大;
2.走胶不畅, 困气;
3.顶针过小, 顶出不均匀;
4.斜度过小, 有毛刺, 硬度不足;
5.注塑压力不均匀, 产品形态强度不足;
6.加工误差;
7.离浇口远, 模温低。
注塑模具常见缺陷、产生原因和调整方法表
注塑模
装配缺陷
产 生 原 因
调 整 方 法
模具开闭
顶出复位
动作不顺
1.模架导柱、导套滑动不顺,配合过紧
2.斜顶、顶针滑动不顺。
3.复位弹簧弹力或预压量不足。
1修配或者更换导柱、导套。
2检查并修配斜顶、顶针配合。
3增加或者更换弹簧。
模具与注塑
机不匹配
1.定位环位置不对、尺寸过大或过小。
1.合理调整间隙及修磨工作部分分型面;
2.局部加胶, 加排气;
3.加大顶针, 均匀分布;
4.修毛刺, 加斜度, 氮化;
5.修整浇口, 压力均匀, 加强产品强度;
6.重新加工;
7.改善浇口, 加高模温。
2.模具的限位行程不够,模具的抽芯行程不够,模具的顶出行程不够;
1.检查浇注系统各段流道和浇口,修整有关零件;
2.检查各限位、抽芯、顶出行程是否符合设计要求,调整不符合要求的行程;
模具运水
不通或漏水
1模具运水通道堵塞,进出水管接头连接方式错误。
2封水胶圈和水管接头密封性不够。
1.检查冷却系统进出水管接头连接方式及各段水道,修整有关零件;
注塑产品常见的13种质量缺陷原因分析及解决办法
注塑产品常见的13种质量缺陷原因分析及解决办法注塑工艺是一种常用的塑料加工方法,广泛应用于各个领域的产品创造中。
然而,在注塑过程中,往往会浮现一些质量缺陷问题,这些问题可能会导致产品的性能下降,甚至影响产品的安全性和可靠性。
因此,及时分析和解决这些质量缺陷是非常重要的。
本文将介绍注塑产品常见的13种质量缺陷原因分析及解决办法,以供参考。
1. 毛刺毛刺是指注塑产品表面浮现的细小尖刺状突起。
毛刺的浮现可能是由于模具不平整、模具间隙过大、注塑压力过高等原因导致的。
解决办法是检查模具的平整度,调整模具间隙,并适当降低注塑压力。
2. 热缩热缩是指注塑产品在冷却过程中发生尺寸变化。
热缩的原因主要是由于塑料材料的热胀冷缩性质导致的。
解决办法是在设计模具时考虑热缩因素,合理控制注塑温度和冷却时间。
3. 翘曲翘曲是指注塑产品在冷却过程中发生形变,使得产品不平整。
翘曲的原因可能是由于注塑温度不均匀、模具温度不均匀、注塑压力不均匀等造成的。
解决办法是调整注塑温度、模具温度和注塑压力,使其均匀分布。
4. 气泡气泡是指注塑产品内部或者表面浮现的气体会萃现象。
气泡的浮现可能是由于塑料材料中的挥发物没有彻底挥发、注塑温度过高、注塑压力过高等原因导致的。
解决办法是控制注塑温度和压力,选择合适的塑料材料,并进行充分的挤出和干燥处理。
5. 缩孔缩孔是指注塑产品内部浮现的空洞状缺陷。
缩孔的原因可能是由于注塑温度过低、注塑压力不足、模具设计不合理等导致的。
解决办法是提高注塑温度、增加注塑压力,并优化模具设计。
6. 裂纹裂纹是指注塑产品表面或者内部浮现的裂纹状缺陷。
裂纹的浮现可能是由于注塑温度过高、注塑压力过大、冷却时间过短等原因导致的。
解决办法是降低注塑温度、减小注塑压力,并延长冷却时间。
7. 毛边毛边是指注塑产品边缘浮现的不平整现象。
毛边的原因可能是由于模具设计不合理、注塑压力过高、注塑速度过快等导致的。
解决办法是优化模具设计,降低注塑压力,并适当调整注塑速度。
- 1、下载文档前请自行甄别文档内容的完整性,平台不提供额外的编辑、内容补充、找答案等附加服务。
- 2、"仅部分预览"的文档,不可在线预览部分如存在完整性等问题,可反馈申请退款(可完整预览的文档不适用该条件!)。
- 3、如文档侵犯您的权益,请联系客服反馈,我们会尽快为您处理(人工客服工作时间:9:00-18:30)。
2. 模塑前胶粒避免受过大的温度变化及要干燥胶粒
3. 模具温度不均匀
3. 重新排列运水信道,使模具温度一致
.
实用文档
破裂或 龟裂
1. 填模太实 2. 模温太低
1.A 减低速度; B 减低压国 C 缩短注射时间 2. 提高模温
3. 不适当的脱模设计 如角度斜位及倒扣位
3. 修改工模
4. 顶针或环定不当
5.A 清洁熔胶筒 B 避免混入其它塑料
6. 工模润滑剂过多
6. 清洁模面,用小量润滑剂 (脱模剂 )
7. 水口小
7. 调节水口大小,使其得到良好的压力控制
水口四 周有条
纹
料温过高,流速太快
1. 料温度高易缩水
降低温度及注射速度
1.A 降低温度 B 减少螺杆旋转速度或背压
啤塑周 期需时
过长
2. 工模温度过高
2. 温度增加模温
3. 压力不足
3. 增加压力
4. 刚开机时射咀太冷
4. 多啤几啤或用火焰加热射咀
射胶不 足
5. 模温不均一 6. 空气不能排出模腔 (困气 )
5. 不用或少用脱模剂 6. 增加排气道数目及尺码
7. 注射时间不够
7. 增加注射时间
8. 流入多模腔工模的 熔胶流态不能适当平 行
8. 修正平行情形
.
实用文档
3. 注射速度慢
3. 增加注射速度
4. 模壁有水份
4. 清洁和修理漏水裂痕或防止水汽在模壁凝洁
5. 用脱模剂过多
5. 不用或少用脱模剂
6. 使用过多的内或外 润滑剂
6. 检查材料是适合和混料时减少矿油用量
7. 模表面粗糙
7. 再次抛光模壁
1. 熔胶管各段不够
1. 增加熔胶筒各段
2. 模温不够
6. 塑品切面厚薄不均 匀
6.A 设计塑件俾切面厚薄均一 B 去除制品上凸起的线条
7. 排气不足
7. 增加排气
塑料在 1. 模温太低
.
1. 升高电热、升高模温
实用文档
实用文档
浇口成 层状
2. 射速太慢 3. 注射压力不足
2. 提高注射速度 3. 提高注塑速度
4. 射胶时间过长
4. 缩短射胶时间
5. 胶料有杂质
塑料方面 结晶性的塑料比非结晶性塑料收缩历害,加工时要适当增加料量,或 在塑料中加成换剂,以加快结晶,减少收缩凹陷。
加工方面 (1) 料筒温度过高,容积变化大,特别是前炉温度,对流动性差的塑料 应适当提高温度、保证畅顺。 (2) 注射压力、速度、背压过低、注射时间过短,使料量或密度不足而 收缩压力、速度、背压过大、时间过长造成飞边而出现收缩。 (3) 加料量即缓冲垫过大时消耗注射压力,过小时,料量不足。 (4) 对于不要求精度的制件,在注射保压完毕,外层基本冷凝硬化而夹
材料方面
(1) 再生料含量太高,造成制件强度过低。
(2) 湿度过大,造成一些塑料与水汽发生化学反应,降低强度而出现顶
出开裂。
(3) 材料本身不适宜正在加工的环境或质量欠佳,
受到污染都会造成开
裂。
机台方面 注塑机塑化容量要适当,过小塑化不充分未能完全混合而变脆,过大 时会降解。 5 注塑件气泡的原因分析
注塑模具各类问题原因分析及解决办法
实用文档
问题
可能成因
解决方法
1. 清洗炮筒内壁(拆螺杆清小洗)
小黑点
熔胶筒内壁烧焦,胶 块脱落
2. 用较硬胶料进入,以擦净炮筒内壁(小船坞机,如用清 洗剂及亚加力等)
3. 避免胶料长时间受高温 (料温不宜太高, 储料不能太多,
1. 封盖料斗
黑点
空气带来肮脏物或模 腔腔内有空气引至
4. 炮筒内存有死角
4. 更换螺杆
产品哑 白
原料潮湿
烘干原料再生产
气泡
模腔填料不足, 原因: 模具达人微信: mujudaren
1.A 制品切面厚,模 腔壁上有突起线
1.A 再设计模具
B 注塑压力太低
B 加大注塑压力
C 注塑时间太长
C 增加注塑时间
D 入料不足
D 增加注塑速度及增加入水口阔度
2. 胶料潮湿
6. 料内有湿气
6. 烘干胶料
油温机
利用热传导原理,将热传导油加热至适当温度,输送至成型机模具之管道内,加 热模具至要求温度,并控制油温在要求温度范围内。适合模温要求高的成型。改
善塑料制品的质量,亦可提高生产效益。
1 注塑件收缩凹陷的原因分析
注塑成型过程中,制品收缩凹陷是比较常见的现象。造成这种情况的 主要原因有:
3. 熔溶位离入水位太 远
3. 再设定入水位或再加几个对称的入水
夹纹
4. 排气不良
4. 增设足够排气
5. 塑品切面厚薄转化 大
5. 再设计塑件及设定适当的入水位置
6. 模温太低
6. 提高模温
7. 注塑压力低及速度 慢
7. 升高注射压力或速度
塑件表 面粗糙
1. 模温低 2. 注射压力低
1. 提高模温 2. 增加注射压力
3. 前后模差太大
3. 使前且模温一致
产品变 形
4. 入水位设计不常 5. 塑件切面厚度不均 匀
4. 再设计入水位置 5. 尽可能保持切面厚度均匀
6. 工模温度过低
6. 增高模温
7. 料温过低
7. 升高料温 C 注 6 和 7 即变相减压
8. 螺杆背压过高
8. 减少螺杆背压
1. 注射压力或熔胶筒 温度过高
.
实用文档
气泡 ( 真空泡 )的气体十分稀薄属于真空泡。一般说来,如果在开模瞬 间已发现存在气泡是属于气体干扰问题。真空泡的形成是由于充注进 塑料不足或压力较低。在模具的急剧冷却作用下,与型腔接角的燃料 牵拉,造成体积损失的结果。
解决方法 (1) 提高注射能量:压力、速度、时间和料量,并提高背压,使充模丰 满。 (2) 增加料温流动顺畅。降低料温减少收缩,适当提高模温,特别是形 成真空泡部位的局部模温。 (3) 将浇口设置在制件厚的部份,改善喷嘴、流道和浇口的流动状况, 减少压务的消耗。 (4) 改进模具排气状况。
1.A 减低注射压力或机筒温度 B 降低螺杆的旋转速度或螺杆背压
2. 过多入料
2. 减少入料
塑件粘 模
3. 注射时间过长
3. 减少注射时间
4. 工 模 冷 却 不 足 ( 塑 件热膨胀 )
4. 延长工模冷却时间
5. 塑件因收缩而粘在 阳模上
5. 减少冷却时间,使前后模有不同温度
.
实用文档
6. 模内塑件未冷硬
2. 降低模温
3. 模 塑 时 间 不 稳 定 (工人问题 )
3. 用计时表及加强管制工人的操作速度
4. 塑料融化的温度和 所需时间不够
4. 增加温度和延长时间
5. 塑件较厚处冷却不
5.A 改变模内冷却水道位置
.
实用文档
足
B 用冷水机
1. 注射压力太大
1. 减低注射压力
2. 保压时间过长
2. 减少保压时间
3. 在检查塑件时周围 空气温度不固定
3.A 保持周围空气温度固定
B 在同一条件下测量及检查制品
漏胶
1. 胶料太热
1.A 降低胶料温度
B 减少螺杆转速和背压
.
2. 注塑压力过高
2.A 降低压力
B 减少枕压时间
3. 模具或射咀凸凹两 面接触不良
3. 再次打磨模具唧嘴
4. 射台增压不够
4. 检查机台射台射增压系统
4. 再按放顶针让制品能顺利顶出工模
5. 再 用 料 过 多 ( 拉 粒 水口 )
5. 少用或不用拉粒或水口
产品尺 寸性改
变
1. 模塑情况不稳定
2. 注塑条件与正常时 ቤተ መጻሕፍቲ ባይዱ一致
1.A 调节操作情况,直至得到最大平稳操作 B 视乎啤塑工人的操作情况而决定啤塑时间长短 2.A 更正跟平常时不用的注塑条件
B 检查注塑温度,压力 ,工模温度,模塑时间,入料, 电压,
2. 胶料封闭好,保持干净 3. 增加或减低熔胶筒和模具温度, 以改变胶料进入模腔的 速度
4. 减低注塑压力或速度
1. 料 筒 或 螺 杆 不 干 净,原料不干净
1. 清理料筒及螺杆并小心处理胶料不受污染
黑色条 纹
2. 料筒能胶料局部过 热 3. 冷胶料互相磨擦或 与炮筒壁磨擦时烧焦
2. 使炮筒之每段受热圴匀
6. 延长保压并加强工模冷却
7. 工模内有倒扣位
7. 却除倒扣位,打磨抛光,增加脱兔
模部份的斜度
8. 模腔内深入部份空 气压力小 (真空状态 )
8. 设立适宜的排气道
9. 工模内壁光洁度不 够
9. 模腔壁再次抛光
1. 料温太低
1. 升高料温
2. 模面有脱模剂等油 渍
2. 抹干净工模壁,不喷脱模剂或少脱模剂
.
实用文档
心部份尚柔软又能顶出的制件,及早出模,让其在空气或热水中缓慢 冷却,可以使收缩凹陷平缓而不那么显眼又不影响使用。
2 注塑件震纹的原因分析
PS 等刚性塑料制件在其浇口附近的表面, 以浇口为中心的形成密集的 波纹, 有时称为震纹。 产生原因是熔体粘度过大而以滞流形式充模时, 前端的料一接触到型腔表面便很快冷凝收缩起来,而后来的熔料又胀 开已收缩的冷料继续前进过程的不断交替使料流在前进中形成了表面 震纹。
模具方面 (1) 顶出要平衡,如顶杆数量、截面积要足够,脱模斜度要足够,型腔 面要有足够光滑, 这样才防止由于外力导致顶出残余应力集中而开裂。
.
实用文档
(2) 制件结构不能太薄,过渡部份应尽量采用圆弧过渡,避免尖角、倒 角造成应力集中。 (3) 尽量少用金属嵌件,以防止嵌件与制件收缩率不同造成内应力加 大。 (4) 对深底制件应设置适当的脱模进气孔道,防止形成真空负压。 (5) 主流道足够大使浇口料未来得及固化时脱模,这样易于脱模。 (6) 主流道衬套与喷嘴接合应当防止冷硬料的拖拉而使制件粘在定模 上。