脱氧及讲义精炼渣系分析
第四章 精炼渣系选择

钢中的酸溶铝[Al]S不会还原渣中的(SiO2),这时(SiO2)不会成为供氧源。
钢铁冶金研究所&特殊钢冶金学术方向
各精炼渣系脱硫能力的比较
LF炉精炼过程的脱硫的热力学参数主要有钢水中的溶解氧 含量和渣中的 CaO 活度(即作用浓度)。脱硫的表达式为: (CaO) +[S] = (CaS) + [O]
<0.1 -
♣ 几个主要结构单元的作用浓度
结构单元 作用浓度 A B 山 阳 东北大学 CaO N1 0.1641 0.2348 0.3676 0.3495 SiO2 N2 0.0005 0.0005 0.0002 0.0001 Al2O3 N3 0.0102 0.0097 0.0084 0.0238 MgO N4 0.2162 0.1145 0.0468 0.0598 MgO· Al2O3 N10 - - - 0.0598
钢铁冶金研究所&特殊钢冶金学术方向
精炼渣系选择的实验
小盖 炉盖 发热体 炉管 耐火砖 精炼渣 石墨坩埚 MgO坩埚 钢水
实验渣系及结果
实验号 1# 2# 3# 4# 5# 6# 7# 8# CaO 45~50 54~57 50~60 50~55 45~50 55~60 45~50 50~55 SiO2 20~25 10~15 13~17 10~15 20~25 13~15 20~25 5~10 Al2O3 24~27 24~27 10~15 13~17 13~17 13~17 25~30 25~33 MgO 3~7 3~7 2~6 8~12 8~12 3~8 3~7 5~10 CaF2 0 0 0 5~10 3~8 5~10 0 0 R=(CaO/SiO2) 2 4 4 4.2 2.2 4.5 2 >5 T.O 0.002 0.0013 0.0016 0.0015 0.002 0.0011 0.0015 0.0011
铸造技术:铸钢脱氧知识详细讲解
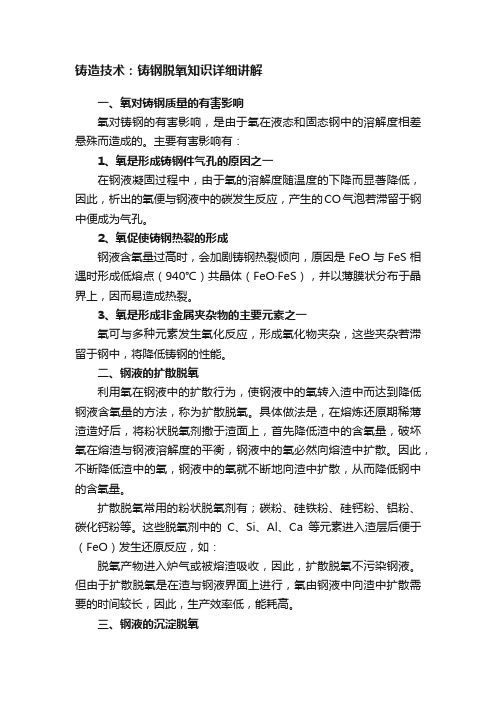
铸造技术:铸钢脱氧知识详细讲解一、氧对铸钢质量的有害影响氧对铸钢的有害影响,是由于氧在液态和固态钢中的溶解度相差悬殊而造成的。
主要有害影响有:1、氧是形成铸钢件气孔的原因之一在钢液凝固过程中,由于氧的溶解度随温度的下降而显著降低,因此,析出的氧便与钢液中的碳发生反应,产生的CO气泡若滞留于钢中便成为气孔。
2、氧促使铸钢热裂的形成钢液含氧量过高时,会加剧铸钢热裂倾向,原因是FeO与FeS相遇时形成低熔点(940℃)共晶体(FeO·FeS),并以薄膜状分布于晶界上,因而易造成热裂。
3、氧是形成非金属夹杂物的主要元素之一氧可与多种元素发生氧化反应,形成氧化物夹杂,这些夹杂若滞留于钢中,将降低铸钢的性能。
二、钢液的扩散脱氧利用氧在钢液中的扩散行为,使钢液中的氧转入渣中而达到降低钢液含氧量的方法,称为扩散脱氧。
具体做法是,在熔炼还原期稀薄渣造好后,将粉状脱氧剂撒于渣面上,首先降低渣中的含氧量,破坏氧在熔渣与钢液溶解度的平衡,钢液中的氧必然向熔渣中扩散。
因此,不断降低渣中的氧,钢液中的氧就不断地向渣中扩散,从而降低钢中的含氧量。
扩散脱氧常用的粉状脱氧剂有;碳粉、硅铁粉、硅钙粉、铝粉、碳化钙粉等。
这些脱氧剂中的C、Si、Al、Ca等元素进入渣层后便于(FeO)发生还原反应,如:脱氧产物进入炉气或被熔渣吸收,因此,扩散脱氧不污染钢液。
但由于扩散脱氧是在渣与钢液界面上进行,氧由钢液中向渣中扩散需要的时间较长,因此,生产效率低,能耗高。
三、钢液的沉淀脱氧沉淀脱氧是将块状的脱氧剂直接加入钢液中,脱氧剂与(FeO)发生沉淀反应而脱氧。
沉淀脱氧又称强制脱氧,沉淀脱氧法脱氧产物的排除,影响脱氧效果。
按脱氧产物的形成时间划分,脱氧产物可分为:一次脱氧产物——在炉内或包内加入脱氧剂后立即形成的脱氧产物;二次脱氧产物——已脱氧的钢液在其冷却至液相线之前所形成的脱氧产物;三次脱氧产物——在液相线与固相线之间凝固时所形成的脱氧产物。
精炼渣及复合脱氧剂在梅钢炼钢厂的应用

02
复合脱氧剂的特性包括熔点低、流动性好、反应速度快等,能
够快速有效地脱除钢水中的氧。
复合脱氧剂的组成和特性决定了其在炼钢过程中的重要作用和
03
应用价值。
复合脱氧剂在炼钢过程中的作用
复合脱氧剂在炼钢过程中主要起到去除钢水中的氧和 夹杂物的作用,从而提高钢的质量和纯净度。
通过与钢水中的氧发生化学反应,复合脱氧剂能够将 钢水中的氧转化为无害的产物,同时生成稳定的固体
优化生产流程
简化生产流程
精炼渣和复合脱氧剂的使 用可以简化炼钢流程,减 少生产环节,提高生产效 率。
提高自动化水平
通过精炼渣和复合脱氧剂 的优化,可以实现炼钢过 程的自动化控制,提高生 产自动化水平。
降低工人劳动强度
精炼渣和复合脱氧剂的应 用可以减轻工人的劳动强 度,提高工作效率,改善 工作环境。
随着环保意识的提高,复合脱氧剂需要向着环保化方向发 展,如采用无毒、无害的原料和添加剂,减少对环境的污 染。
多样化
为了满足不同品种和规格的钢材需求,复合脱氧剂需要向 着多样化方向发展,如开发具有特殊功能的复合脱氧剂, 如细化钢组织、提高钢材强度和韧性等。
在梅钢炼钢厂的应用前景
提高产品质量
通过采用新型的精炼渣和复合脱氧剂,可以提高钢水的纯净度和 成分稳定性,从而提高产品质量。
降低生产成本
高效化和环保化的精炼渣及复合脱氧剂可以降低能耗和原材料消耗, 从而降低生产成本。
提高生产效率
通过优化精炼渣和复合脱氧剂的配方及制备工艺,可以提高生产效 率,缩短生产周期。
感谢您的观看
THANKS
以确保其在炼钢过程中的有效性和安全 包括合理的添加量、加入时机和搅拌方
性。
式等,以实现最佳的脱氧效果和经济效
脱氧及精炼渣系分析

• 研究内容: • 1)研究多种脱氧元素的最佳的配比,以控制 脱氧产物的形态,使其形成低熔点的液相脱氧 产物,易于聚合长大; • 2)研究熔池反应促进元素,以保证熔池内的 搅拌强度,促进钢水中夹杂物传输到钢/渣界 面,但同时也须保证熔池反应的平稳性,防止 反应剧烈导致的喷溅事故; • 3)研究精炼基渣——精炼剂,以保证脱氧产 物及时被熔池内的熔渣吸收,吸收氧化物后的 产物必须是低熔点物质,更有利于上浮排除; • 4)精炼剂必须呈高碱性,尽量减少脱氧产物 对钢包渣碱性的降低影响。
22
• 3.2钢包二次精炼剂 • 钢包二次精炼剂用于出钢后钢水在钢 包内的二次精炼作用。其主要作用为: 脱硫、脱氧、吸附夹杂。 • 根据使用钢种不同分为两大类: • *铝酸钙渣系 • *硅灰石渣系
23
• • • • • • • • • • • • •
1)铝酸钙渣系 成分及物性控制范围为: (CaO)50~60%、(FeO)<1%、 (Al2O3)16~35%、(MgO) 7~10%、 (SiO2)5~20%。 熔点1360~1400℃、粘度0.5~0.10P.S。 表面张力490~550×10-5 N/cm。 对粘度的控制,视精炼渣所要求的功能而异。 若以脱硫为主,精炼渣不仅硫容量要高,而且 粘度要低,有利于钢渣界面反应。若是以分离 夹杂为主,则粘度要高,避免渣与钢水混合, 以防二次氧化。所以精炼过程中应控制渣前期 粘度低、终渣粘度高。
11
• 2.4钙、钡脱氧: • 实践表明,含铝的脱氧剂中引入强脱
氧元素Ca可有效地对脱氧产生的高熔点夹 杂物进行变性处理,从而显著改善铝脱氧 钢液的流动性.但由于Ca自身尚存在着如 在钢中溶解度低、比重轻、蒸气压高等弱 点,如何提高其有效利用率成为确定脱氧 剂组成时必须考虑的问题,研究表明,Ba 元素不仅本身是具有比重大、蒸气压低的 强脱氧剂.而且与Ca完全互溶,并随其含 量的增加明显降低Ca的蒸气压.因此研制 和使用含钙的高钡低铝复合脱氧剂代表着 炼钢用脱氧剂的发展方向. 12
ER70S—6焊丝钢精炼渣系优化研究及生产实践

ER70S—6焊丝钢精炼渣系优化研究及生产实践近年来日照钢铁生产焊丝钢氧含量控制不稳定,脱氧较轻时夹杂物含量高,脱氧过重时浇注发生絮流,严重影响钢材质量和生产连续性。
在炼钢过程钢中夹杂物通过造渣吸收去除,ER70S-6焊丝钢关键点在于冶炼时精炼造渣,选择合理的渣系是保证焊丝钢质量的根本。
研究发现絮流炉次精炼出钢出现回铝现象,造成中包夹杂物过多,渣样中Al2O3一般>6%。
资料显示当精炼渣堿度在R=2.0左右时其发泡效果最好,Al2O3含量低于5%时较强的脱氧和高温下不易造成Al2O3的还原引起的絮流,采用石英砂+石灰的方式代替目前使用的低碳低硅精炼渣以达到降低精炼渣碱度和渣中Al2O3含量的目的。
通过渣系的调整成功解决了焊丝钢氧含量的控制,同时杜绝了絮流现象稳定了生产节奏。
标签:絮流;夹杂物;渣系;石英砂1 引言ER70S-6焊丝钢是采用美国标准生产的新一代CO2气体保护实芯焊丝的主要原料广泛应用于造船、桥梁、大型机械加工行业。
但是焊丝中过高的氧含量(在高温条件下,碳和氧易反应生成CO 气体)和大型夹杂物容易导致焊接过程中熔池的飞溅,严重影响焊接性能,降低焊接生产率,随着用户对钢材质量的要求越来越高[1],炉外精炼过程越来越重要,合理的造渣可以达到脱硫、脱氧甚至脱氮的目的;可以吸收钢中的夹杂物;可以控制夹杂物的形态;可以形成泡沫渣淹没电弧提高热效率,减少耐火材料侵蚀。
因此,在炉外精炼工艺中要特别重视造渣。
在我厂现有LF设备的基础上优化现有的造渣工艺,控制好埋弧、脱硫、脱氧等主要精炼环节,充分发挥LF精炼效果。
2 LF基本工艺参数处理容量:60t;额定容量(功率):12500KV A电极直径:φ400mm(超高功率UHP石墨电极)工艺流程:铁水→混铁炉→60t转炉→60tLF炉→3#连铸机3 ER70S-6焊丝钢渣系研究与调整炼钢就是炼渣,炉渣流动性好,碱度适当,再配以合适的吹氢参数,就能促进钢中A1203、SiO2夹杂向炉渣集聚,最大限度地降低点状夹杂和控制钢中夹杂物总量。
论特殊钢精炼过程中的脱氧及夹渣物控制
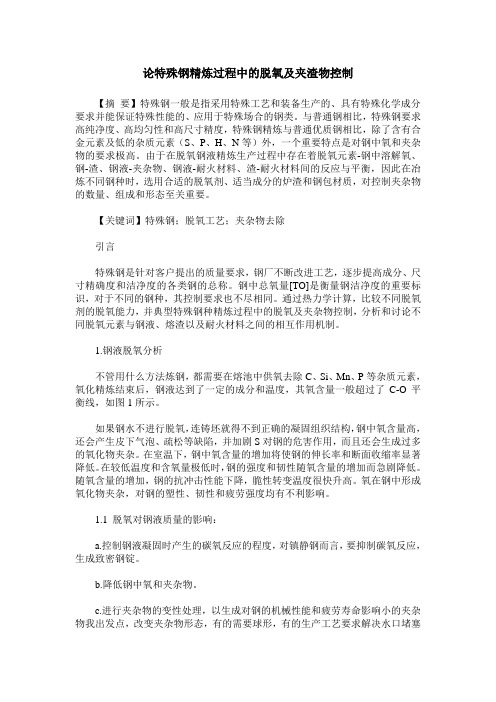
论特殊钢精炼过程中的脱氧及夹渣物控制【摘要】特殊钢一般是指采用特殊工艺和装备生产的、具有特殊化学成分要求并能保证特殊性能的、应用于特殊场合的钢类。
与普通钢相比,特殊钢要求高纯净度、高均匀性和高尺寸精度,特殊钢精炼与普通优质钢相比,除了含有合金元素及低的杂质元素(S、P、H、N等)外,一个重要特点是对钢中氧和夹杂物的要求极高。
由于在脱氧钢液精炼生产过程中存在着脱氧元素-钢中溶解氧、钢-渣、钢液-夹杂物、钢液-耐火材料、渣-耐火材料间的反应与平衡,因此在冶炼不同钢种时,选用合适的脱氧剂、适当成分的炉渣和钢包材质,对控制夹杂物的数量、组成和形态至关重要。
【关键词】特殊钢;脱氧工艺;夹杂物去除引言特殊钢是针对客户提出的质量要求,钢厂不断改进工艺,逐步提高成分、尺寸精确度和洁净度的各类钢的总称。
钢中总氧量[TO]是衡量钢洁净度的重要标识,对于不同的钢种,其控制要求也不尽相同。
通过热力学计算,比较不同脱氧剂的脱氧能力,并典型特殊钢种精炼过程中的脱氧及夹杂物控制,分析和讨论不同脱氧元素与钢液、熔渣以及耐火材料之间的相互作用机制。
1.钢液脱氧分析不管用什么方法炼钢,都需要在熔池中供氧去除C、Si、Mn、P等杂质元素,氧化精炼结束后,钢液达到了一定的成分和温度,其氧含量一般超过了C-O平衡线,如图1所示。
如果钢水不进行脱氧,连铸坯就得不到正确的凝固组织结构,钢中氧含量高,还会产生皮下气泡、疏松等缺陷,并加剧S对钢的危害作用,而且还会生成过多的氧化物夹杂。
在室温下,钢中氧含量的增加将使钢的伸长率和断面收缩率显著降低。
在较低温度和含氧量极低时,钢的强度和韧性随氧含量的增加而急剧降低。
随氧含量的增加,钢的抗冲击性能下降,脆性转变温度很快升高。
氧在钢中形成氧化物夹杂,对钢的塑性、韧性和疲劳强度均有不利影响。
1.1 脱氧对钢液质量的影响:a.控制钢液凝固时产生的碳氧反应的程度,对镇静钢而言,要抑制碳氧反应,生成致密钢锭。
b.降低钢中氧和夹杂物。
关于精炼过程中合成渣行为的探讨
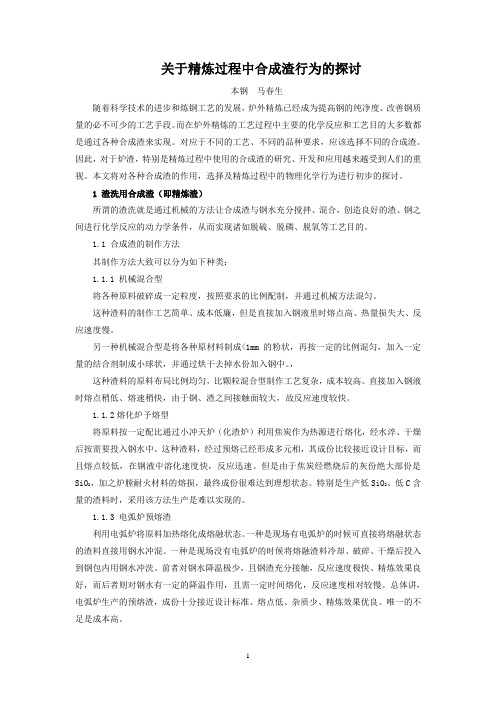
关于精炼过程中合成渣行为的探讨本钢马春生随着科学技术的进步和炼钢工艺的发展,炉外精炼已经成为提高钢的纯净度、改善钢质量的必不可少的工艺手段。
而在炉外精炼的工艺过程中主要的化学反应和工艺目的大多数都是通过各种合成渣来实现。
对应于不同的工艺、不同的品种要求,应该选择不同的合成渣。
因此,对于炉渣,特别是精炼过程中使用的合成渣的研究、开发和应用越来越受到人们的重视。
本文将对各种合成渣的作用,选择及精炼过程中的物理化学行为进行初步的探讨。
1 渣洗用合成渣(即精炼渣)所谓的渣洗就是通过机械的方法让合成渣与钢水充分搅拌、混合,创造良好的渣、钢之间进行化学反应的动力学条件,从而实现诸如脱硫、脱磷、脱氧等工艺目的。
1.1 合成渣的制作方法其制作方法大致可以分为如下种类:1.1.1 机械混合型将各种原料破碎成一定粒度,按照要求的比例配制,并通过机械方法混匀。
这种渣料的制作工艺简单、成本低廉,但是直接加入钢液里时熔点高、热量损失大、反应速度慢。
另一种机械混合型是将各种原材料制成<1mm的粉状,再按一定的比例混匀,加入一定量的结合剂制成小球状,并通过烘干去掉水份加入钢中。
,这种渣料的原料布局比例均匀,比颗粒混合型制作工艺复杂,成本较高。
直接加入钢液时熔点稍低、熔速稍快,由于钢、渣之间接触面较大,故反应速度较快。
1.1.2熔化炉予熔型将原料按一定配比通过小冲天炉(化渣炉)利用焦炭作为热源进行熔化,经水淬、干燥后按需要投入钢水中。
这种渣料,经过预熔已经形成多元相,其成份比较接近设计目标,而且熔点较低,在钢液中溶化速度快,反应迅速。
但是由于焦炭经燃烧后的灰份绝大部份是SiO2,加之炉膛耐火材料的熔损,最终成份很难达到理想状态。
特别是生产低SiO2、低C含量的渣料时,采用该方法生产是难以实现的。
1.1.3 电弧炉预熔渣利用电弧炉将原料加热熔化成熔融状态。
一种是现场有电弧炉的时候可直接将熔融状态的渣料直接用钢水冲混。
一种是现场没有电弧炉的时候将熔融渣料冷却、破碎、干燥后投入到钢包内用钢水冲洗。
脱氧工艺讲课内容

脱氧工艺一、岗位任务主要任务是脱除来自经过洗涤的气化粗煤气和焦炉气的混合煤气中微量的氧气,为后工序提供氧气含量要求脱至30ppm以下的合格原料气以满足后工段的工艺要求。
防止氧气组分的存在对后工序甲烷分离的冷箱设备操作带来有害影响。
正确使用和维护催化剂,延长其使用寿命。
二、工艺原理利用适合于本项目原料气含硫、含油等杂质工况的专用脱氧剂,在适宜温度条件和催化剂作用下O2 与 CO、H2进行反应使氧气得以脱除,其反应为:2CO+O2→2CO2O2+2H2→2H2O三、脱氧剂硫化原理脱氧剂为钴钼系耐硫低变催化剂,主要活性组分为氧化钼,以氧化钴为促进剂,以氧化铝为载体。
脱氧催化剂中的Co与Mo是以氧化态形式存在,这种形态的催化剂不具有活性,只有将Co、Mo转化为硫化态,才具有活性。
将催化剂中Co、Mo由氧化态转化为硫化态的过程称为催化剂的硫化,硫化分为强制硫化与自然硫化两种形式。
我厂采用CS2强制硫化的方法。
为使气体中有足够的H2S含量,以保证硫化过程顺利进行,通常采取向系统连续添加CS2的方法,并在一定温度下(200℃)发生氢解作用生成H2S。
其主要反应为:CS2+4H2 2H2S+CH4 ΔH=240KJ/molCoO+H2S CoS+H2O ΔH=13.6KJ/mol'MoO3+2H2S+ H2 MoS2+3H2O ΔH=48.1KJ/mol上述CoO与MoO生成MoS2与CoS的反应是一个可逆的放热反应。
硫化氢穿透前,床层温度低于230℃。
催化剂上的金属氧化态在温度大于230℃后很容易被氢气还原,成为低价位的金属氧化物甚至成为单质金属,因此在硫化氢穿透催化剂床层前,应严格执行该指标(低价位的金属或单质金属难于硫化,同时被还原的金属对油有强的吸附作用,会加速裂解反应,造成催化剂大量积炭,使活性降低)四、工艺流程因催化剂为耐硫催化剂,开车前需先加入CS2气体,用以激活催化剂反应活性。
来自气化工段的粗煤气在界外与焦炉气混合后首先进入净化器(F61201A/B)中除去混合煤气中的油、粉尘等杂质,进入气气换热器(E61201)加热至160℃,然后进入脱氧器(D61201),在脱氧剂作用下将气体中的氧气脱除。