纳米压痕划痕技术在表征薄膜涂层体系力学性能中的应用
纳米压痕法测试微纳米涂层的力学性能

纳⽶压痕法测试微纳⽶涂层的⼒学性能涂层⼒学性能的重要性涂层的⼒学性能及其与基体材料的结合强度,关系到⼯件和产品的⼯艺优化和服役可靠性。
传统测试⽅法的不⾜之处⽬前,对于传统涂层材料的⼒学性能评价应⽤较多的是宏观压⼊硬度,如布⽒硬度、洛⽒硬度和维⽒硬度等。
然⽽,微纳⽶涂层中由于涂层薄、晶粒尺⼨⼩、晶界多,具有表⾯效应、尺⼨效应等,传统的测试⽅法难以满⾜薄膜⼒学性能测试的需要。
针对这⼀情况,笔者采⽤美国安捷伦公司⽣产的G200型微/纳⽶压痕仪,对不同材料制备的微纳⽶涂层的⼒学性能进⾏了测试,为检测和评价微纳⽶涂层材料的⼒学性能提供参考。
试验原理G200型微/纳⽶压痕仪提供了两种测试涂层⼒学性能的⽅法:⼀种是基础标准法,另⼀种是连续刚度标准法。
两种⽅法都是⽤基于对纳⽶压痕尺⼨测量基础上计算的硬度和弹性模量作为表征⼒学性能的指标。
01基础标准法如果只需知道某⼀个特定涂层的⼒学性能,就可以使⽤基础标准法进⾏测试。
试验在⼀个压痕点上进⾏⼀系列的(也可以是⼀个)加载-卸载过程,测试每⼀次卸载过程的载荷、深度曲线斜率,确定接触刚度,从⽽计算出硬度H 和弹性模量E,计算公式如下式中:P为压⼊载荷;A为压痕表⾯积。
式中:β是常数,根据压头的⼏何形状确定,对于本试验的压头,取β=1.034;S为接触刚度。
图1 基础标准法测量原理⽰意图图1是基础标准法测量原理⽰意图,图中hc是接触深度,ht是最⼤载荷时的位移,ε是与压头有关的仪器参数。
由图1可知,载荷从0逐渐增加到最⼤载荷30mN,随后载荷基本成直线下降,此时该直线的斜率即为该试样的接触刚度S。
通过测量压⼊载荷P、压痕表⾯积A以及接触刚度S就可以计算得到硬度H和弹性模量E。
02连续刚度标准法连续刚度标准法是采⽤微纳⽶压痕仪通过动态加载⽅式确定界⾯的弹性接触刚度,进⽽进⾏连续的、⼩范围的界⾯间弹性的加载-卸载过程,以此连续地测试出界⾯接触刚度的数值,从⽽计算出在不同载荷下不同深度处硬度和弹性模量的数值。
超薄纳米薄膜的划痕硬度评价方法及应用

超薄纳米薄膜的划痕硬度评价方法及应用范雪;刁东风【摘要】纳米压痕是一种常用的薄膜硬度评价方法.然而,当薄膜厚度< 10nm时,该方法难以去除基体对薄膜硬度的影响,因而无法获得薄膜自身的硬度,限制了纳米结构与硬度之间关系的认知,阻碍了超薄纳米结构薄膜的应用.本研究提出一种基于纳米压痕硬度标定下的纳米划痕硬度评价方法,并将其应用于纳米结构碳膜的硬度研究.首先,利用自行设计搭建的纳米刻划装置,通过对比碳膜在纳米划痕和纳米压痕方法下的残余变形深度,分析不受基体影响的临界薄膜厚度,得到纳米划痕深度不受基体影响的临界薄膜厚度.其次,采用压头形状等效接触模型,利用划痕的残余顶角、宽度和深度,通过计算压头前端的接触压力分布得到硅基体的纳米划痕硬度,与纳米压痕硬度标定结果一致.最后,将纳米划痕硬度方法应用在电子回旋共振等离子体溅射方法制备的3种不同纳米结构碳膜上,得到交联结构碳膜和非晶碳膜的硬度分别约为19.1 GPa和14.6 GPa,高于硅基体11.2 GPa的硬度,而石墨烯嵌入式碳膜的硬度约为2.7GPa.分析不同纳米结构碳膜的刻划机理表明,在sp2含量较高的纳米结构碳膜中,sp3含量并不是决定碳膜力学特性的唯一因素,小尺度、多石墨烯层间交联结构能够有效增加层间的剪切强度,薄膜展现出较好的耐刻划特性.研究结果有助于进一步拓展纳米划痕方法的应用,也为不同纳米结构碳膜的应用提供了理论基础.【期刊名称】《深圳大学学报(理工版)》【年(卷),期】2019(036)005【总页数】9页(P510-518)【关键词】测试计量技术及仪器;纳米划痕;纳米压痕;硬度;碳膜;纳米结构【作者】范雪;刁东风【作者单位】深圳大学纳米表面科学与工程研究所,广东深圳518060;广东省微纳光机电工程重点实验室,广东深圳518060;深圳大学纳米表面科学与工程研究所,广东深圳518060;广东省微纳光机电工程重点实验室,广东深圳518060【正文语种】中文【中图分类】TH117.1纳米薄膜的硬度是指薄膜局部抵抗硬物侵入其表面的能力,是薄膜材料重要的力学性能之一,也是指导其设计制备与工程应用的重要依据.目前,评价薄膜力学特性的方法主要有纳米压痕法和纳米划痕法[1-2].1992年,OLIVER等[3]基于压痕过程的载荷-位移曲线,提出一种硬度和弹性模量的计算方法,使纳米压痕演变为一种纳米硬度定量测试的标准实验.然而,将纳米压痕应用于超薄薄膜硬度测试时,其实验结果往往会受到基体材料力学性能的影响.为避免基体影响,压入过程中接触深度不应超过膜厚的10%~20%[4],这对超薄纳米薄膜的力学特性测量提出挑战,尤其是当薄膜的厚度小于10 nm时,由于压头钝化、样品表面粗糙度与仪器性能的限制,超薄薄膜的极端压痕实验结果已难以保证准确性.纳米划痕实验通过测试材料表面的划痕深度和宽度,定性衡量材料的软硬程度.与标准纳米压痕实验相比,纳米划痕测试结果受基体力学性能的影响更小,所以更适于评价超薄薄膜的硬度[5].然而,纳米划痕方法不受基体影响的临界薄膜厚度尚不明确,划痕硬度难以定量计算,划痕硬度与通用硬度(压痕硬度)的关系尚不明确,这均限制了纳米划痕在薄膜硬度测试上的深层应用,尤其是针对纳米结构影响下的超薄薄膜力学特性.随着微纳米科学与技术的不断发展,含有sp2纳晶结构的碳膜因其具有优异的力学[6]、摩擦学[7]、电学[9]、磁学[10]及光电[11]特性,被运用于微机电系统(micro-electro-mechanical, MEMS)、半导体和磁存储器件等领域.尤其是在机械性能方面,sp2杂化石墨烯结构具有极高的弹性模量[12],由于石墨烯层间易于剪切,可起到降低摩擦的作用[13].通过石墨烯层弯曲或sp3键将相邻石墨烯层连接起来,形成小尺度纳晶结构,sp3连接键使层间滑移减小,增强碳膜的力学性能[14].但是,由于制备方法和条件的不同,碳膜中的纳米结构会导致薄膜产生不同的力学性能[16].对于电子回旋共振等离子体溅射系统[17],通过调节碳膜沉积过程中的照射粒子,可实现电子和离子照射加工[18],研究发现,两种条件下均可以制备出含有sp2纳晶结构的碳膜,电子照射纳米结构碳膜耐磨损性能差[19],而离子照射纳米结构碳膜耐磨耐刻划性能好[20].为此,有必要深入系统地针对不同纳米结构的碳膜,研究纳米结构影响下的力学特性.本研究自行设计搭建纳米刻划装置,通过纳米划痕与纳米压痕的对比实验,探索纳米划痕的测试极限,提出基于纳米刻划测试的纳米划痕硬度计算方法,进一步将纳米划痕方法应用在电子回旋共振等离子体溅射纳米结构碳膜的力学特性评价上,得到纳米结构碳膜的划痕硬度,分析不同纳米结构所导致的刻划机理.1 实验1.1 纳米划痕测试本研究开发一种薄膜纳米刻划测试装置,其结构示意图如图1(a).样品放置在压电扫描的样品台上,使样品与刻划针尖沿y方向相对运动,样品台通过控制器来驱动,刻划速度为6 μm/s.悬臂梁安装在通过高精度导向螺丝控制的位移台上,在悬臂梁的自由端安装伯克维奇探针用于纳米刻划测试.探针针尖的曲率半径为100 nm,如图1(b).为施加刻划载荷,悬臂梁的法向厚度设计为100 μm,法向刚度(Kn)为24.43 N/m,标定结果如图1(c).通过控制导向螺丝施加法向载荷,控制器的步长为4 μm,进而根据悬臂梁的法向刚度得到法向加载精度为0.1 mN.利用法向应变片测量实际加载的法向载荷,加载范围为0.1~10.0 mN.利用切向应变片测量刻划过程中的摩擦力,悬臂梁的法向厚度设计为50 μm,切向力的测量精度为0.05 mN.利用400倍的光学放大模块观察探针与薄膜之间的加载和刻划过程.实验中将刻划长度控制在15 μm,刻划载荷为0.5 mN和1.0 mN.在刻划实验后,利用原子力显微镜(atomic force microscope, AFM)进行划痕扫描,用于扫描的探针为曲率半径20 nm 的硅探针.扫描尺寸为10 μm×10μm,扫描的载荷为1 μN.从三维结果中可观察到明显的划痕,如图1(d).对于每一次测试,采用8条沿划痕宽度方向的剖面计算平均划痕深度以及相对误差,如图1(e),从图中可以得到硅基体在0.5 mN载荷下的平均残余划痕深度为6.36 nm,均方根误差为0.69 nm.1.2 纳米压痕测试本研究采用伯克维奇探针进行纳米压痕测试,探针的曲率半径为100 nm,与纳米划痕所采用的压头一致,使纳米划痕与纳米压痕实验产生相似的接触应力.采用弹性模量为72 GPa的石英进行接触面积标定.纳米压痕测试的最大压入载荷分别为0.5 mN和1.0 mN.依据载荷-位移曲线,对比残余压痕深度与残余刻划深度,并利用OLIVER等[3]的方法计算压痕硬度(H).图1 纳米刻划装置示意图及其测试方法Fig.1 Schematic of the nanoscratchtest apparatus and the test method1.3 ECR纳米结构碳膜及其表征本研究采用电子回旋共振(electron cyclotron resonance, ECR)等离子体溅射技术制备碳膜[21],根据ECR制备的条件不同,可调节碳膜中的纳米结构,例如,非晶碳膜(a-C)、石墨烯交联碳膜(GLCL-C)和石墨烯嵌入式碳膜(GSE-C).实验采用发散式等离子体溅射方法制备非晶碳膜,微波功率为700 W,工作气压为0.04 Pa,基片偏压为+10 V,沉积速率4 nm/min.为研究纳米划痕和纳米压痕测试方法下的临界薄膜厚度,通过控制沉积时间分别制备2、4、6、8、10、20、40、60、100、240及300 nm的非晶碳膜.相同条件下,采用发散式等离子体溅射方法在基片偏压为-50、-75和-100 V的条件下制备石墨烯交联碳膜,薄膜厚度为40 nm.采用封闭式等离子体溅射方法在工作气压0.04 Pa、基片偏压+50V、微波功率500 W和700 W(对应基片电流为0.8 A和0.9 A)的条件下,制备石墨烯嵌入式碳膜,薄膜厚度150 nm.2 实验结果及分析2.1 纳米划痕临界薄膜厚度为了对比纳米划痕和纳米压痕测试中不受基体影响的临界薄膜测试厚度,首先进行纳米压痕实验,从载荷-位移曲线中提取残余压痕深度.图2为压入载荷为1.0 mN时,硅基体和不同厚度非晶碳膜的纳米压痕实验结果,图2(a)为载荷-位移曲线,相同载荷下,随着薄膜厚度的增大,最大压痕深度和残余压痕深度逐渐降低.从曲线中计算出非晶碳膜的纳米压痕硬度和残余压痕深度,其结果如图2(b).可见,随着薄膜厚度的增大,薄膜/基体的压痕硬度逐渐增大,直到薄膜厚度超过100 nm.相应地,残余压痕深度随薄膜厚度的增大而降低.结果表明,硅基非晶碳膜在1.0 mN纳米压痕实验中不受基体影响的临界薄膜测试厚度为100 nm,残余压痕深度能够反映出薄膜的塑性变形程度.图2 非晶碳膜纳米压痕及划痕测试结果Fig.2 The nanoindentation and nanoscratch test results of amorphous carbon films图3 不同薄膜厚度非晶碳膜的残余划痕深度和残余压痕深度,以获得不受基体影响的临界薄膜厚度Fig.3 The residual depth of nanoindentation tests and nanoscratch tests to reflect the critical test thickness without substrateeffect在1.0 mN载荷下对不同厚度非晶碳膜进行纳米划痕实验,图3对比了不同薄膜厚度非晶碳膜的残余划痕深度和残余压痕深度.可见,残余划痕深度和残余压痕深度均随薄膜厚度的增大先降低,而后趋于稳定.由于薄膜的硬度高于硅基体,这种变化趋势意味着基体的影响逐渐降低,直到残余深度仅代表薄膜发生的塑性变形.纳米压痕测试的临界薄膜厚度增大到100 nm,而临界刻划深度仍保持在10 nm.结果表明,纳米划痕方法中不受基体影响的临界薄膜厚度远小于纳米压痕方法,因此,纳米划痕方法更加适用于评价超薄薄膜的硬度.图4 划痕硬度分析计算模型Fig.4 Analysis model for nanoscratch hardness calculation2.2 划痕硬度分析计算为计算划痕硬度,需建立伯克维奇探针刻划样品表面的接触模型.刻划测试装置中所采用的金刚石伯克维奇压头的几何形状可用正三棱锥描述,棱面夹角为142.3°、棱棱夹角为155.0°,尖端曲率半径为100 nm.当压头划入材料表面时,接触区域将发生弹塑性变形,划痕形貌应与压头截面形状完全契合;而当压头划出时,卸载区域将发生弹性恢复,因此,残余划痕深度将小于划入时的刻划深度,残余划痕顶角将远大于压头的棱棱夹角,如图4(a).通过几何分析可知,残余划痕顶角θ(单位:°)可由残余划痕深度h(单位:nm)和宽度w(单位:nm)计算得到θ=180 °-2 tan-1(2 h/w)(1)为简化计算模型,当顶角足够大(>150°)时,划痕形貌可近似用一段圆弧表示,其中,圆弧的等效半径(Reff)[22]为(2)根据划痕的深度和宽度,可得每一种样品的平均等效半径.因此,将伯克维奇探针刻划过程简化成球形探针刻划,如图4(b).在刻划过程中,主要的接触区域发生在沿滑动方向前端的部分,探针后端部分产生的弹性恢复效应被忽略.图4(b)为球形压头在滑动接触时的受力分析.其中, R 为压头半径; r为球冠半径;α为球冠半角; H面代表水平(horizontal)投影面;V面代表垂直(vertical)投影面.取面元dA进行分析,其上所受力包含垂直于面元作用的平均接触压力p,及与平行于面元作用的平均剪切应力s.定义接触压力等于材料硬度,剪切应力在接触表面是常量.根据受力分析结果[23],通过对每个面元受到的切向力和法向力进行积分,得到总体的切向力和法向力,如式(3).其中, H*为刻划样品的等效硬度;本研究采用伯克维奇探针,压头半径取等效半径Reff; s为剪切应力;球冠半径α=sin-1(w/2R);切向力Ft和方向力Fn之间满足Ft=μFn,摩擦系数μ可由实验测得.对硅基体进行不同深度的纳米划痕实验,得到硅基体的θ=159.5°~178.3°,Reff=3.555 μm,平均摩擦系数为0.15~0.25.根据上述参数,计算得到硅基体H*的平均值为11.2 GPa,标准偏差为1.2 GPa.单晶硅基体的硬度一般为11~13 GPa,因此,认为根据上述等效接触模型计得的划痕硬度可以接受,可用来进一步研究碳膜的纳米划痕硬度.(3)2.3 ECR碳基结构薄膜的纳米划痕硬度为研究ECR纳米结构碳膜的纳米划痕硬度,采用0.4~1.0 mN的载荷对硅基体、a-C、GLCL-C和GSE-C进行纳米刻划实验.图5汇总了不同载荷下4种样品的划痕深度.可见,除了GSE-C,其他3种样品的划痕深度均随载荷的增大而线性增大.以硅基体的线性曲线为分界线,a-C和GLCL-C样品的划痕深度在硅曲线下方,而GSE-C样品的划痕深度均远远大于硅基体.从结果中可以定性得到,3种纳米结构碳膜的硬度变化,从硬到软依次是GLCL-C、a-C 和GSE-C.图5 不同刻划载荷时4种样品的刻划深度汇总Fig.5 Scratch depths of four kinds of samples under different scratch loads为进一步分析纳米结构碳膜的划痕硬度,对不同划痕的划痕宽度进行测量.利用式(2)得到3种碳膜残余划痕顶角的变化范围,结果如表1.与硅基体一样,3种碳基结构薄膜的残余划痕顶角均大于150°,可采用等效压头的方法计算纳米划痕硬度.结合实际测得的摩擦系数,采用压头等效方法,利用式(3)计算得到测试样品,即薄膜和基体的等效硬度H*.表1 不同纳米结构碳膜的刻划硬度计算参数Table 1 Parameters of nanoscratch hardness calculation for carbon films with different nanostructures样品θ/(°)Reff/μmμa-C168.9~178.75.0140.07~0.17GLCL-C 168.7~179.12.2180.14~0.17GSE-C157.4~174.81.9540.10~0.19对于膜/基结合系统,采用压头等效方法得到的H*代表了薄膜和基体之间的等效硬度.为提取碳膜的纳米划痕硬度,等效硬度(H*)、基体硬度(Hs)及碳膜硬度(Hl)之间的关系[24]为(4)(5)其中,σl 和σs分别代表碳膜和硅基体的屈服强度; El和Es代表碳膜和硅基体的弹性模量; t为膜厚.对于a-C和GLCL-C,由于其硬度值高于硅基体,因此采用式(4)计算薄膜的纳米划痕硬度,令定常项a=Hl/Hs-1,b=-(Hl/Hs)(σl/σs)-1 (El/Es)-1/2;以x=h/t,y=H*/Hs为自变量和因变量,式(4)可简化为y=1+aebx(6)对于GSE-C,由于其硬度值低于硅基体,因此,采用式(5)计算其纳米划痕硬度,令b=-(σl/σs)(El/Es)-1,该式可简化为y=1+aebx2(7)上述推导为不同纳米结构碳膜的纳米划痕硬度估算提供了思路:将H*和h分别用Hs和t进行量纲一化处理,然后将所得数据按式(6)或式(7)进行最小二乘拟合,求出参数a与b,最终便可确定碳膜自身的纳米划痕硬度.具体过程为:① 根据式(2)和式(3),利用碳膜h和w,以及对应的Fn、μ和Reff,计算出相应硅基碳膜的H*;② 取单晶硅基体的Hs=11.2 GPa,对H*进行量纲一化,用t对h进行量纲一化,这样就得到纳米表面H*/Hs随h/t的变化情况;③ 令x=h/t、 y=H*/Hs,将分布图中的散点按式(6)或式(7)进行最小二乘拟合,得到拟合曲线方程,以确定参数a和b的值.拟合结果如图6,图6(a)和(b)分别为a-C和GLCL-C H*/Hs随h/t的变化情况,根据前期测量结果,这两种碳膜的硬度比基体高,因此采用式(6)进行拟合.图6(c)为GSE-C的分布情况,该碳膜比硅基体软,因此对实验数据则按式(7)进行拟合.由图6(a)至(c)可见,随着划痕深度增大并接近纳米表面厚度,即h/t→1时,拟合曲线都逐渐平缓且趋近常数1,即H*/Hs→1,膜-基等效硬度将逐渐表现出基体的力学特性.相反地,随着划痕深度的减小,基体对碳膜纳米划痕硬度计算的影响将越来越小,所以拟合曲线趋于不同的值,这个值反映了不同纳米结构碳膜自身的软硬程度.其中,图6(a)和(b)的拟合曲线趋向大于1,表明离子照射下a-C和GLCL-C的划痕硬度高于单晶硅基体.图6(c)中的拟合曲线趋向小于1,表明电子照射GSE-C的划痕硬度低于单晶硅基体.根据图6的拟合结果,当h/t=0时,记膜-基等效硬度为H0,即理想情况下的碳膜纳米划痕硬度.但通常情况下划痕深度过小,形貌测试仪器将难以检测得到,所以H0是没有工程意义的.对此,依据经验当h/t<0.1时,基体对碳膜力学性能的影响可忽略不计,这里将h/t=0.1时的硬度作为碳膜纳米划痕硬度,记为H0.1.表2 拟合得到的a和b值,以及当h/t=0.1时计算得到的刻划硬度H0.1Table 2 The fitted constant values of a, b, and the calculated scratch hardness H0.1 with h/t=0.1样品abH0.1/GPaa-C 0.855-10.2514.6GLCL-C 1.008-3.5519.1GSE-C 1.008-7.122.7图6 不同刻划深度下不同纳米结构碳膜的划痕硬度Fig.6 The nanoscratch hardness of different nanostructured carbon films with different scratch depths表2为根据实验结果拟合的参数a、 b值以及计得3种纳米结构碳膜的刻划硬度H0.1. a-C、 GLCL-C及GSE-C的刻划硬度分别为14.6、19.1及2.7 GPa.对3种厚度大于100 nm的纳米碳膜进行纳米压痕实验,得到纳米压痕硬度,并与H0.1对比,两者非常接近,如图6(d).因此,纳米划痕硬度的方法更适用于对含有纳米结构的超薄碳膜(如GLCL-C)的力学性能进行定量研究.对3种碳膜刻划行为及其纳米划痕硬度的机理进行分析,结合透射电子显微镜(transmission electron microscope,TEM)观察结果以及拉曼、XPS测试分析(结果请扫描论文末页右下角二维码),观察到碳膜中的石墨烯纳晶结构如图7.得到离子照射得到的GLCL-C纳晶尺寸在1 nm左右,电子照射得到的GSE-C纳晶尺寸在2.5 nm左右,a-C的sp3含量最高,GLCL-C的sp3含量次之,GSE-C 的sp3含量最低.综合分析发现,sp3含量并不是决定碳膜力学特性的唯一因素,在纳米尺度下,薄膜中微小的纳米结构变化将引起明显力学性能变化,而纳米划痕硬度方法可以更有效分析超薄薄膜的纳米划痕硬度,进而反映出纳米结构对薄膜力学性能的影响.图7 GLCL-C中纳晶结构的高分辨TEM照片Fig.7 High resolution TEM picture of nanocrystal structure3 结论本研究提出一种基于纳米压痕硬度标定下的纳米划痕硬度评价方法,并将其应用于纳米结构碳膜的硬度研究.综上研究结论如下:① 自行设计搭建了纳米刻划装置进行纳米薄膜的刻划测试,得到纳米划痕不受基体影响的临界薄膜厚度远小于纳米压痕;② 采用压头形状等效接触模型,利用划痕的残余变形量、摩擦系数以及压头滑动前端的接触压力,分析得到硅基体的纳米划痕硬度与纳米压痕硬度标定结果一致;③ 将纳米划痕方法应用于3种ECR纳米结构碳膜上,得到交联结构碳膜和非晶碳膜的硬度分别约为19.1 GPa和14.6 GPa,高于硅基体硬度,而石墨烯嵌入式碳膜的硬度约为2.7 GPa.阐明了在sp2含量较高的纳米结构碳膜中,小尺度及多石墨烯层间交联结构能够有效增加层间的剪切强度,薄膜展现出较高的纳米划痕硬度.研究结果将有助于进一步拓展纳米刻划方法的应用范围,同时,也为纳米结构碳基薄膜的开发和应用提供了理论研究基础.参考文献【相关文献】[1] 龙东平, 薛建荣, 晏智鑫. 纳米压痕和划痕法测定TiO2纳米薄膜的力学性能[J]. 表面技术, 2015, 44(6): 115-119.LONG Dongping, XUE Jianrong, YAN Zhixin. Nanoindenation and nanoscratchmeasurements to determine the mechanical properties of TiO2 nano films[J]. Surface Technology, 2015, 44(6): 115-119.(in Chinese)[2] SHAHSAVARI F, EHTESHAMZADEH M, NAIMI JAMAL R M, et al. Nanoindentation and nanoscratch behaviors of DLC films growth on different thickness of Cr nanolayers[J]. Diamond & Related Materials, 2016, 70: 76-82.[3] OLIVER W C, PHARR G M. Measurement of hardness and elastic modulus by instrumented indentation: advances in understanding and refinements to methodology[J]. Journal of Material Research, 2004, 19(1): 3-20.[4] SAHA R, NIX W D. Effects of the substrate on the determination of thin film mechanical properties by nanoindentation[J]. Acta Materilia, 2002, 50(1): 23-38.[5] 张飞虎, 李琛, 孟彬彬, 等. 基于变切深纳米刻划的K9 玻璃表面成形特征及去除机制研究[J]. 机械工程学报, 2016, 52(17): 65-71.ZHANG Feihu, LI Chen, MENG Binbin, et al. Investigation of surface deformation characteristic and removal mechanism for K9 glass based on varied cutting-depth nano-scratch[J]. Journal of Mechanical Engineering, 2016, 52(17): 65-71.(in Chinese)[6] FAN Xue, NOSE K, DIAO Dongfeng, et al. Nanoindentation behaviors of amorphous carbon films containing nanocrystalline graphite and diamond clusters prepared by radio frequency sputtering[J]. Applied Surface Science, 2013, 273: 816-823.[7] CHEN Cheng, XUE Peidong, FAN Xue, et al. Friction-induced rapid restructuring of graphene cap layer at sliding surfaces: short run-in period[J]. Carbon, 2018, 130: 215-221.[8] WANG D S, CHANG S Y, CHEN T S, et al. Stress writing textured graphite conducting wires/patterns in insulating amorphous carbon matrix as interconnects[J]. Scientific Reports, 2017, 7: 9727.[9] WANG Chao, DIAO Dongfeng. Self-magnetism induced large magnetoresistance at room temperature region in graphene nanocrystallited carbon film[J]. Carbon, 2017, 112: 162-168.[10] YANG Lei, HU Gaijuan, DIAO Dongfeng, et al. Nanosized graphene sheets enhanced photoelectric behavior of carbon film on psilicon substrate[J]. Applied Physics Letters, 2016, 109(3): 031910.[11] ZHAO H, MIM K, ALURU N R. Size and chirality dependent elastic properties of graphene nanoribbons under uniaxial tension[J]. Nano Letters, 2009, 9: 3012-3015. [12] BERMAN D, ERDEMIR A, SUMANT A V. Few layer graphene to reduce wear and friction on sliding steel surfaces[J]. Carbon, 2013, 54: 454-459.[13] ZHANG Y Y, WANG C M, CHENG Y F, et al. Mechanical properties of bilayer graphene sheets coupled by sp3 bonding[J]. Carbon, 2011, 49(13): 4511-4517.[14] 刘广桥, 董丽梅, 张俊彦. 类富勒烯/非晶多层碳膜的制备及性能[J]. 中国表面工程, 2016, 29(1): 51-57.LIU Guangqiao, DONG Limei, ZHANG Junyan. Preparation and properties of fullerene-like/amorphous multilayer carbon based film[J]. China Surface Engineering, 2016, 29(1): 51-57.(in Chinese)[15] SHAKERZADEH M, TEO E H T, SORKIN A, et al. Plasma density induced formation of nanocrystals in physical vapor deposited carbon films[J]. Carbon, 2011, 49(5): 1733-1744.[16] FAN Xue, DIAO Dongfeng, WANG Kai, et al. Multi-functional ECR plasma sputtering system for preparing amorphous carbon and Al-O-Si films[J]. Surface & Coatings Technology, 2011, 206(7): 1963-1970.[17] DIAO Dongfeng, WANG Chao, FAN Xue. Frictional behavior of nanostructured carbon films[J]. Friction, 2013, 1(1): 63-71.[18] ZHANG Wenlei, FAN Xue, DIAO Dongfeng. Three-layered sandwich structured carbon film prepared by ECR ion/electron/ion alternative irradiation technique[J]. Surface & Coatings Technology, 2015, 278: 12-17.[19] FAN Xue, DIAO Dongfeng. Ion excitation and etching effects on top-surface properties of sp2 nanocrystallited carbon films[J]. Applied Surface Science, 2018, 462: 669-677.[20] GUO Meiling, DIAO Dongfeng, FAN Xue, et al. Scratch behavior of re-structured carbon coating by oxygen plasma etching technology for magnetic disk application[J]. Surface & Coatings Technology, 2014, 251: 128-134.[21] 刁东风, 范雪, 陈成. 一种ECR等离子体溅射装置及其溅射方法:ZL 201610103436.2[P]. 2016-06-08[2018-02-13].DIAO Dongfeng, FAN Xue, CHEN Cheng. An ECR plasma sputtering apparatus and its sputtering method: ZL 201610103436.2[P]. 2016-06-08[2018-02-13].(in Chinese)[22] KOMVOPOULOS K, SAKA N, SUH N P. The mechanism of friction in boundary lubrication[J]. Journal of Tribology, The Transactions of ASME, 1985, 107(4): 452-462. [23] TAYABI N, CONRY T, POLYCARPOU A A. Determination of hardness from nanoscratch experiments: corrections for interfacial shear stress and elastic recovery[J]. Journal of Material Research, 2003, 18(9): 2150-2162.[24] BHATTACHARYA A K, NIX W D. Analysis of elastic and plastic deformation associated with indentation testing of thin films on substrates[J]. International Journal of Solids Structures, 1988, 24(12): 1287-1298.。
纳米压痕技术实验及其应用
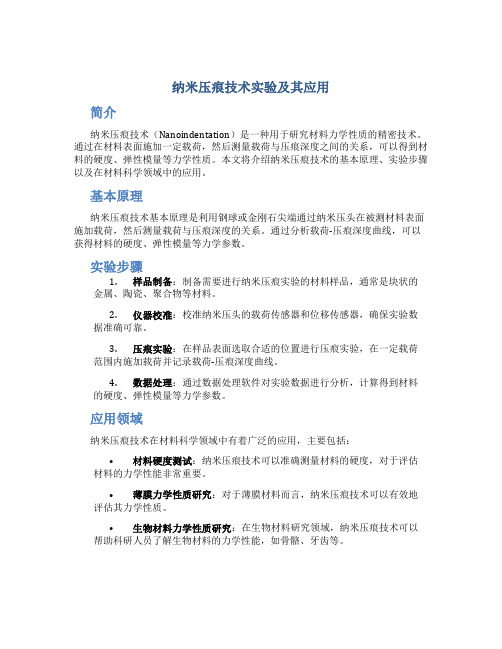
纳米压痕技术实验及其应用简介纳米压痕技术(Nanoindentation)是一种用于研究材料力学性质的精密技术。
通过在材料表面施加一定载荷,然后测量载荷与压痕深度之间的关系,可以得到材料的硬度、弹性模量等力学性质。
本文将介绍纳米压痕技术的基本原理、实验步骤以及在材料科学领域中的应用。
基本原理纳米压痕技术基本原理是利用钢球或金刚石尖端通过纳米压头在被测材料表面施加载荷,然后测量载荷与压痕深度的关系。
通过分析载荷-压痕深度曲线,可以获得材料的硬度、弹性模量等力学参数。
实验步骤1.样品制备:制备需要进行纳米压痕实验的材料样品,通常是块状的金属、陶瓷、聚合物等材料。
2.仪器校准:校准纳米压头的载荷传感器和位移传感器,确保实验数据准确可靠。
3.压痕实验:在样品表面选取合适的位置进行压痕实验,在一定载荷范围内施加载荷并记录载荷-压痕深度曲线。
4.数据处理:通过数据处理软件对实验数据进行分析,计算得到材料的硬度、弹性模量等力学参数。
应用领域纳米压痕技术在材料科学领域中有着广泛的应用,主要包括:•材料硬度测试:纳米压痕技术可以准确测量材料的硬度,对于评估材料的力学性能非常重要。
•薄膜力学性质研究:对于薄膜材料而言,纳米压痕技术可以有效地评估其力学性质。
•生物材料力学性质研究:在生物材料研究领域,纳米压痕技术可以帮助科研人员了解生物材料的力学性能,如骨骼、牙齿等。
结论纳米压痕技术作为一种精密的材料力学测试方法,在材料科学领域有着广泛的应用前景。
通过实验分析,可以更准确地评估材料的力学性能,为材料设计和研发提供重要参考。
以上就是关于纳米压痕技术实验及其应用的文档内容,希术能对您有所帮助。
纳米压痕划痕技术在表征薄膜涂层体系力学性能中应用共27页文档

66、节制使快乐增加并使享受加强。 ——德 谟克利 特 67、今天应做的事没有做,明天再早也 是耽误 了。——裴斯 泰洛齐 68、决定一个人的一生,以及整个命运 的,只 是一瞬 之间。 ——歌 德 69、懒人无法享受休息之乐。——拉布 克 70、浪费时间是一桩大罪过。——卢梭
1、不要轻言放弃,否则对不起自己。
2、要冒一次险!整个生命就是一场冒险。走得最远的人,常是愿意 去做,并愿意去冒险的人。“稳妥”之船,从未能岸边走远。-戴尔.卡耐基。
梦 境
3、人生就像一杯没有加糖的咖啡,喝起来是苦涩的,回味起来却有 久久不会退去的余香。
纳米压痕划痕技术在表征薄膜涂层体系力 4、守业的最好办法就是不断的发展。 5、当爱不能完美,我宁愿选择无悔,不管来生多么美丽,我不愿失 去今生对你的记忆,我不求天长地久的美景,我只要生生世世的轮 回里有你。 学性能中应用
纳米压痕的工作原理及应用

纳米压痕的工作原理及应用1. 纳米压痕的定义纳米压痕是一种实验技术,它通过在材料表面施加小型压力,然后测量压痕的尺寸和形状,从而推断材料的力学性质和表面特征。
2. 纳米压痕的工作原理纳米压痕技术基于材料的弹性和塑性行为,通过在材料表面施加小型压力,使之发生弹性和塑性形变。
测量压痕的尺寸和形状可以确定材料的硬度、弹性模量等力学性质,以及表面的粗糙度和涂层厚度等表面特征。
3. 纳米压痕的应用纳米压痕技术在各个领域有着广泛的应用,下面列举几个常见的应用领域:•材料科学与工程:纳米压痕可以用于研究材料的力学性能,比如硬度、弹性模量、塑性行为等,这对于材料科学和工程的研究非常重要。
此外,纳米压痕还可以用于研究材料的磨损特性、涂层的性能等。
•纳米技术:纳米压痕可以用于研究纳米材料的力学性能,比如纳米颗粒、纳米薄膜等。
纳米材料的力学性能对于纳米技术的应用非常重要,纳米压痕可以提供对纳米材料力学性能的准确测量。
•医学领域:纳米压痕可以在医学领域中应用于材料和组织的力学性质研究。
例如,可以通过纳米压痕测量人体组织的硬度,从而对组织的健康状况进行评估。
•电子学:纳米压痕可以用于研究电子器件和材料的力学性能,如半导体材料、导线材料等。
这对于电子器件的性能和可靠性的评估和优化非常重要。
•能源领域:纳米压痕可以用于研究能源材料的力学性质,如锂离子电池的电极材料、太阳能电池的表面材料等。
这对于能源材料的研究和开发具有重要意义。
•环境科学:纳米压痕可以用于研究环境材料的力学性能和耐久性。
例如,可以通过纳米压痕来评估建筑材料的抗风蚀性能、海洋材料的耐久性等。
4. 纳米压痕的发展趋势随着纳米科学和纳米技术的快速发展,纳米压痕技术也在不断改进和完善。
目前,一些新的纳米压痕技术已经出现,如纳米压痕显微镜、纳米压痕机械测试仪等。
这些新技术的出现使得纳米压痕技术在应用上更加方便和准确。
5. 总结纳米压痕是一种重要的实验技术,可以用于研究材料的力学性质和表面特征。
基于纳米压痕技术及有限元模拟的薄膜力学性能研究的开题报告

基于纳米压痕技术及有限元模拟的薄膜力学性能研究的开题报告一、研究背景及意义随着现代科技的不断发展和进步,各行各业对于材料的需求也越来越高,尤其是在微电子、新材料等领域,对于材料的力学性能要求越来越高,这就需要进行深入的研究,了解材料内部的物理、化学等性质及其影响因素,以获取更好的材料性能。
纳米压痕技术是一种基于微纳米加工技术的新型制备方法,具有极高的实用性及在材料性能研究方面的应用前景。
限元模拟可通过计算机仿真技术,模拟出材料受力情况,使理论与实践更加贴近,进一步提高了研究的可靠性和准确性。
本研究旨在利用纳米压痕技术和有限元模拟技术,对薄膜的力学性能进行研究,以提高薄膜材料的力学性能并应用于实际生产中。
二、研究内容及主要思路1.采用纳米压痕技术对薄膜材料进行压力实验,测量薄膜的力学性能;2.采用有限元模拟技术模拟薄膜压力实验中的受力状态以及预测薄膜的力学性能;3.通过实验与模拟的比对,验证模拟的可靠性,进而提高薄膜材料的力学性能;4.将研究成果应用于实际生产中,提高产品质量和可靠性。
三、预期成果和创新点通过对纳米压痕技术及有限元模拟技术的理论研究,对薄膜材料进行力学性能研究,并提出了一种新型的研究方法,使得有限元模拟技术得到进一步的发展与完善。
研究成果可应用于产品质量控制、新材料的研究开发等多个领域,具有一定的创新点和实际应用价值。
四、研究计划及进度安排1.文献综述(1-2周):调研相关文献,了解纳米压痕技术及有限元模拟技术在材料力学性能研究中的应用;2.实验设计(2-3周):设计纳米压痕实验和有限元模拟方法,确定实验和模拟参数;3.实验和模拟(6-8周):进行纳米压痕实验和有限元模拟,并测量数据进行分析;4.数据处理与分析(4-6周):对实验数据进行处理和分析,利用有限元模拟结果进行比对和验证;5.研究成果撰写(2-3周):将研究成果进行总结、归纳和撰写,并定期向导师报告进展情况和研究成果。
五、研究所需条件和经济预算1.实验设备:纳米压痕仪、有限元模拟软件等(估计费用:50万元);2.实验材料:涂层膜等(估计费用:5万元);3.人员及其它费用:研究人员(2名)和实验室租金等(估计费用:15万元)。
基于纳米压痕技术及有限元模拟的薄膜力学性能研究
的所有节点的轴向 位 移 也 是 零,表 示 材 料 在 一 个 支
撑 面 上 .金 刚 石 压 头 在 有 限 元 分 析 中 被 模 拟 为 刚 体 , 在压头上设一个参 考 点,将 整 个 刚 体 的 约 束 和 位 移
集中到这个参考点 上.分 析 过 程 中 压 头 只 有 向 下 的 一 个 自 由 度 ,加 载 和 卸 载 过 程 是 时 间 的 线 性 函 数 ,第
载速率均为50μN/s,在 最 大 载 荷 处 保 载 5s.每 次 试 验 均 重 复 4 次 ,结 果 取 平 均 值 .图 1 为 薄 膜 在 不 同 载荷下的载荷—位移 曲 线.图 2 为 薄 膜 弹 性 模 量 E 随压痕深度的分布情况.
2 有限元模拟和量纲分析
2.1 有 限 元 模 拟 纳 米 压 痕 过 程 及 其 结 果 分 析 使用 ABAQUS 有 限 元 软 件 对 压 头 压 入 膜/基
文 章 编 号 :1006-4303(2011)06-0674-05
Research on mechanical properties of film based on nano-indentation technology and finite element simulation
RONG Jun-mei,CHAI Guo-zhong,HAO Wei-na
试 验 所 得 载 荷 — 位 移 曲 线 吻 合 得 比 较 好 ,因 此 验 证 了 有 限 元 模 型 的 正 确 性 和 材 料 模 拟 的 正 确 性 .
关 键 词 :纳 米 压 痕 ;有 限 元 模 拟 ;量 纲 分 析 ;力 学 性 能
中 图 分 类 号 :TH140.7 文 献 标 识 码 :A
微纳米力学及纳米压痕表征技术
微纳米力学及纳米压痕表征技术摘要:微纳米力学为微纳米尺度力学,即特征尺度为微纳米之间的微细结构所涉及的力学问题[1] 。
纳米压痕方法是通过计算机控制载荷连续变化,并在线监测压深量[2],适用于微米或纳米级的薄膜力学性能测试,本实验采用Oliver–Pharr 方法研究了Al2O3 薄膜,附着在ZnS 基底,得到了Al2O3 薄膜的力学性能。
关键词:微纳米力学纳米压痕杨氏模量硬度0引言近年来,随着工业的现代化、规模化、产业化,以及高新技术和国防技术的发展,对各种材料表面性能的要求越来越高。
20世纪80年代,现代表面技术被国际科技界誉为最具发展前途的十大技术之一。
薄膜、涂层和表面处理材料的极薄表层的物理、化学、力学性能和材料内部的性能常有很大差异,这些差异在摩擦磨损、物理、化学、机械行为中起着主导作用,如计算机磁盘、光盘等,要求表层不但有优良的电、磁、光性能,而且要求有良好的润滑性、摩擦小、耐磨损、抗化学腐蚀、组织稳定和优良的力学性能。
因此,世界各国都非常重视材料的纳米级表层的物理、化学、机械性能及其检测方法的研究。
[3]同时随着材料设计的微量化、微电子行业集成电路结构的复杂化,传统材料力学性能测试方法已难以满足微米级及更小尺度样品的测试精度,不能够准确评估薄膜材料的强度指标和寿命 ;另外在材料微结构研究领域中, 材料研究尺度逐渐缩小,材料的变形机制表现出与传统块状材料相反的规律 ,以上趋势要求测试仪器具有高的位置分辨率、位移分辨率和载荷分辨率 ,纳米压痕方法能够满足上述测试需求。
[4]现在,薄膜的厚度己经做到了微米级,甚至于纳米级,对于这样的薄膜,用传统的材料力学性能测试方法己经无法解决。
纳米压痕试验方法是一种在传统的布氏和维氏硬度试验基础上发展起来的新的力学性能试验方法。
它通过连续控制和记录样品上压头加载和卸载时的载荷和位移数据,并对这些数据进行分析而得出材料的许多力学性能指标,压痕深度可以非常浅,压痕深度在纳米范围,也可以得到材料的力学性能,这样该方法就成为薄膜、涂层和表面处理材料力学性能测试的首选工具,如薄膜、涂层和表面处理材料表面力学性能测试等。
用纳米压痕法表征薄膜的应力-应变关系
关键词:电沉积镍镀层;纳米压痕法;量纲分析;应力-应变关系;有限元法; 膜/基体系
i
ABSTRACT
Recently, more and more attentions have been paid to thin films, and research of the mechanical properties of thin films gets to be a hot subject. As a method to evaluate the mechanical properties of thin films, nanoindentation technique is in the popularity for its high displacement resolution, ultra low load and the capability of continuous measurement. In this master thesis, the stress-strain relationships of thin films were measured by nanoindentation combined with dimensional analysis and finite element method.
纳米压痕技术及其在薄膜涂层体系中的应用
表面技术第51卷第6期纳米压痕技术及其在薄膜/涂层体系中的应用王宇迪1,王鹤峰1,2,杨尚余1,赵帅1,金涛1,肖革胜1,树学峰1(1.太原理工大学 机械与运载工程学院,太原 030024;2.太原清泽智成科技合伙企业,太原 030024)摘要:综述了纳米压痕技术的发展历程及其在薄膜领域的应用。
介绍了当前实验室条件下主要采用的电磁驱动式纳米压痕仪的构造和工作过程。
为了保证测试结果的准确性,要在合适的温度、湿度下进行压入实验,借助保载来消除一些可以避免的误差。
阐述了压头的分类和选择原则,玻氏压头相比于维氏压头具有更小的中心线与棱面夹角,避免了尖端横刃对于压入结果准确性的影响,因此最常用的压头为玻氏压头;表征断裂韧性最合适的压头为立方角压头;表征微机电系统的弯曲采用楔形压头。
总结了通过最大载荷和压入面积得到涂层力学参量的分析流程。
归纳了将纳米压痕法应用于表征薄膜涂层的硬度和弹性模量、室温下蠕变性能、断裂韧性、残余应力、塑性性能等力学量的研究,如表征硬度和弹性模量的Oliver-Pharr法的应用,识别蠕变柔量的Lee-Radok模型的应用,分析断裂韧性的Lawn-Evans-Marshall模型的应用。
在涂层制备过程中,制备参数的改变可以使得涂层具有不同的力学性能,涂层厚度远小于表面尺寸,硬度和弹性模量仍然存在各向异性,非晶态结构涂层具有更高的硬度和弹性模量。
采用碳纳米管强化可以提高涂层的断裂韧性,涂层内存在适量的残余应力数值和合适的残余应力类型,可以改善涂层的力学性能。
具有多层结构、梯度结构等新型结构的涂层相比于传统涂层具有更优良的力学性能。
纳米压痕法结合AFM原子力显微镜可以实现原位测量,结合有限元法可以对于理论模型进行完善,并拓宽模型的适用范围。
最后,对于纳米压痕技术在薄膜涂层中的应用前景进行了展望。
关键词:纳米压痕;薄膜;涂层;力学性能;研究现状中图分类号:TG174 文献标识码:A 文章编号:1001-3660(2022)06-0138-22DOI:10.16490/ki.issn.1001-3660.2022.06.012Nanoindentation Technique and Its Application in Film/Coating SystemWANG Yu-di1, WANG He-feng1,2, YANG Shang-yu1, ZHAO Shuai1,JIN Tao1, XIAO Ge-sheng1, SHU Xue-feng1(1. College of Mechanical and Vehicle Engineering, Taiyuan University of Technology, Taiyuan 030024, China;2. Taiyuan Qingze Zhicheng Technology Partnership, Taiyuan 030024, China)收稿日期:2021–05–06;修订日期:2021–09–02Received:2021-05-06;Revised:2021-09-02基金项目:山西省回国留学人员科研资助项目(2020-030);山西省科协项目(RZ2000004218);山西省留学人员科技活动择优资助项目(20200028)Fund:Research Project Supported by Shanxi Scholarship Council of China (2020-030); Shanxi Science and Technology Association Project (RZ2000004218); Shanxi Province Overseas Students Science and Technology Activity Funding Project (20200028).作者简介:王宇迪(1997—),男,硕士研究生,主要研究方向为金属力学性能实验表征。
- 1、下载文档前请自行甄别文档内容的完整性,平台不提供额外的编辑、内容补充、找答案等附加服务。
- 2、"仅部分预览"的文档,不可在线预览部分如存在完整性等问题,可反馈申请退款(可完整预览的文档不适用该条件!)。
- 3、如文档侵犯您的权益,请联系客服反馈,我们会尽快为您处理(人工客服工作时间:9:00-18:30)。
实验原理
1.纳米压痕法测试材料力学性能的基本原理 . 2.纳米压痕技术表征薄膜/涂层体系的应力应变关系的原理 .纳米压痕技术表征薄膜 涂层体系的应力应变关系的原理 3. 纳米划痕技术表征薄膜 涂层体系的界面强度的原理 纳米划痕技术表征薄膜/涂层体系的界面强度的原理 4. 纳米压痕技术表征薄膜 涂层体系的界面强度的原理 纳米压痕技术表征薄膜/涂层体系的界面强度的原理
能量释放率 (J/m2)
G (J/m )
2
20 10 0
(b)
70010 800 20
30 40 50
2
100
200
300
400
500
0 600
60
70
Indentation Depth (nm)
Interfacial fracture area (µm )
PZT薄膜试件的压痕载荷PZT薄膜试件的压痕载荷-深度曲线 薄膜试件的压痕载荷
Air Indent H-Pattern
光学显微 力-时间曲线 镜视场 Mark
(4) 选择位置,设定载荷、时间参数,进行压痕实验。 选择位置,设定载荷、时间参数,进行压痕实验。
保载
加载
卸载
时间
最大载荷 4000uN
(5)实验完毕,拷贝数据,关闭仪器,最后关闭电脑。 实验完毕,拷贝数据,关闭仪器,最后关闭电脑。 实验完毕
最大载荷为100mN的范围内,金刚石压头横向划过的长度为700µm。 的范围内,金刚石压头横向划过的长度为 最大载荷为 的范围内 。 痕 划 µ0= PT/PN PN,max (mN) PN,crit (mN) VI (µm3) a (µm) B0 (µm) A曲 d 摩擦 线 2 (µm 系 )
. 划 痕 距 离 划 痕 深 (c) 试 件 (a) 的PZT薄膜的 薄膜的 的
纳米压痕/划痕技术在表征薄膜/ 纳米压痕/划痕技术在表征薄膜/涂 层体系力学性能中压痕法测试材料力学性能的基本原理。 .了解纳米压痕法测试材料力学性能的基本原理。 2.学习用纳米压痕技术表征薄膜 涂层体系的应力应变关系 .学习用纳米压痕技术表征薄膜/涂层体系的应力应变关系 的原理和过程。 的原理和过程。 3.学习用纳米划痕 压痕技术表征薄膜 涂层体系的界面强度 .学习用纳米划痕/压痕技术表征薄膜 压痕技术表征薄膜/涂层体系的界面强度 的原理和过程。 的原理和过程。
三维扫描图
实验设备及材料
1.设备:纳米压痕仪 .设备: 2.样品:电沉积镍镀层试样、PZT压电薄膜试样 .样品:电沉积镍镀层试样、 压电薄膜试样 3.丙酮清洗剂 .
实验步骤与方法
1.纳米压痕实验原理讲解; .纳米压痕实验原理讲解; 2.ABAQUS软件模拟压痕过程讲解和演示; . 软件模拟压痕过程讲解和演示; 软件模拟压痕过程讲解和演示 3.分组选择在镍镀层上压入不同的深度进行压痕实验和 . ABAQUS模拟,分析得到电沉积镍镀层的应力应变关系; 模拟,分析得到电沉积镍镀层的应力应变关系; 模拟 4. 在PZT薄膜上进行系列的压痕 划痕测试,根据给出的公式, 薄膜上进行系列的压痕/划痕测试 薄膜上进行系列的压痕 划痕测试,根据给出的公式, 分析得到PZT薄膜的界面强度,并对不同的测试模型进行 薄膜的界面强度, 分析得到 薄膜的界面强度 比较。 比较。
G= hσ I2 (1 − ν 2 ) f 2E f + (1 − β )
2 hσ R (1 − ν f
)
Ef
− (1 − β )
h(σ I − σ B ) (1 − ν f
2
)
Ef
+
2 τ xz
2G f
h
实验用材料为PZT压电薄膜 ,几何和性能参数如下表: 实验用材料为 压电薄膜 几何和性能参数如下表:
实验内容
结合纳米压痕实验与ABAQUS有限元分析 , 表 有限元分析, 结合纳米压痕实验与 有限元分析 征电沉积镍镀层材料的应力应变关系; 征电沉积镍镀层材料的应力应变关系; 用纳米划痕技术表征PZT压电薄膜的界面强度; 压电薄膜的界面强度; 用纳米划痕技术表征 压电薄膜的界面强度 用纳米压痕技术表征PZT压电薄膜的界面强度。 压电薄膜的界面强度。 用纳米压痕技术表征 压电薄膜的界面强度
纳米压痕法测试材料力学性能的基本原理 纳米压痕法测试材料力学性能的基本原理
通常情况下,压痕过程包括两个步骤, 通常情况下,压痕过程包括两个步骤,即所谓的加载过 Oliver-Pharr方法: 方法: 方法 程与卸载过程。 程与卸载过程。 硬度: 硬度
P ax H= m A c
P
Loading
杨氏模量: 杨氏模量
Unloading
P ax m
S
π S E = ⋅ r 2 A c
1 1−v2 1−vi 压痕示意图 = + E E E r i
2
h r
h ax m
载荷-位移曲线 载荷 位移曲线
h
纳米压痕技术表征薄膜/ 纳米压痕技术表征薄膜/涂层体系的 应力应变关系的原理 应力应变关系的原理
70.3° °
Indenter
纳米压痕技术表征薄膜/ 纳米压痕技术表征薄膜/涂层体系的 应力应变关系的原理 应力应变关系的原理 压 入 过 程 数 值 模 拟
纳米压痕技术表征薄膜/ 纳米压痕技术表征薄膜/涂层体系的 应力应变关系的原理 应力应变关系的原理 压入过程数值模拟的结果
100 80
σyf =1000M Pa
nf=0.5
与实验测得的载荷-位 移曲线比较, 移曲线比较,修正输入参数 直至模拟得到的载荷值 , 直至模拟得到的载荷 位移曲线与实验测得的载荷 -位移曲线重合 , 参数值即 位移曲线重合, 位移曲线重合 为薄膜真实的力学性能参数
60
Ef = 250G Pa
40
nf = 0.5
P(mN)
20
0 0.0 0.2 0.4 0.6 0.8 1.0
ABAQUS模拟压痕过程 ABAQUS模拟压痕过程
a. 建立几何模型 b. 输入参数 c. 划分网格 d. 提交文件进行计算 e. 用图形读出计算结果并进行后处理
实验报告要求
实验后每个人必须书写实验报告,报告内容包括: 实验后每个人必须书写实验报告,报告内容包括:
1. 目的、内容和实验的基本原理; 目的、内容和实验的基本原理; 2. 实验设备型号及有关参数,试样材质及几何尺寸; 实验设备型号及有关参数,试样材质及几何尺寸; 3. 实验和模拟的结果及其分析; 实验和模拟的结果及其分析; 4. 给出结论; 给出结论; 5. 实验体会; 实验体会; 6. 写明报告人班次、姓名及书写报告的日期。 写明报告人班次、姓名及书写报告的日期。
5 光纤灯
扫描器 控制器
6 1 4
防震器
传感器 控制器
光镜 控制器
2
XYZ 控制器
3
纳米压痕测试的注意事项
1. 进入实验室必须换鞋,在实验室保持安静,实验过程 进入实验室必须换鞋,在实验室保持安静, 中不能碰触仪器。 中不能碰触仪器。 2. 放置样品时遵循前低后高、左低右高的原则,样品间 放置样品时遵循前低后高、左低右高的原则, 隔要大于传感器的尺寸。 隔要大于传感器的尺寸。 3. 注意开关机顺序。 注意开关机顺序。 4. 实验过程中严格遵照软件提示操作。 实验过程中严格遵照软件提示操作。
谢谢大家! 谢谢大家!
−3 1 −12 KΙ = Ph cosω + 2 3Mh 2 sinω 2
−3 1 −12 KΙΙ = Ph sinω + 2 3Mh 2 cosω 2
c1 + c2 2 G= K 2 16cosh πε
纳米压痕技术表征薄膜/ 纳米压痕技术表征薄膜/涂层体系的 界面强度的原理 界面强度的原理 对比分析
2um
ABAQUS建模
Coating
圆锥压头
Substrate
2
3
1
100um
压头、 压头、薄膜与基底几何形状组合图
100um
轴对称模拟
纳米压痕技术表征薄膜/ 纳米压痕技术表征薄膜/涂层体系的 应力应变关系的原理 应力应变关系的原理
Coating
网格划分
四节点轴对称线性减缩积分
Substrate
单元(CAX4R) 单元 在压头附近采用密网格, 在压头附近采用密网格 , 远 离压头逐渐使用稀疏网格
网格划分示意图
纳米压痕技术表征薄膜/ 纳米压痕技术表征薄膜/涂层体系的 应力应变关系的原理 应力应变关系的原理 输入的 材料参数
材料应力应变关系遵循幂强化规律: 材料应力应变关系遵循幂强化规律:
Eε σ ≤σy σ = n Rε σ ≥σy
电沉积镍镀层与低碳钢基底的力学性能参数 材料 电沉积镍镀层 低碳钢基底 杨氏模量(GPa) 杨氏模量 50~250 210 泊松比 0.3 0.27 屈服强度(MPa) 应变硬化指数 屈服强度 100~2000 500 0.1~0.5 0.1
h(µm)
值。
模拟的电沉积镍镀层的载荷模拟的电沉积镍镀层的载荷-位移曲线
纳米划痕技术表征薄膜/ 纳米划痕技术表征薄膜/涂层体系的 界面强度的原理 界面强度的原理
Kriese等人提出适于估算脆性膜 脆性基底之间界面强度的理论模型: 等人提出适于估算脆性膜/脆性基底之间界面强度的理论模型 等人提出适于估算脆性膜 脆性基底之间界面强度的理论模型:
(c)
(b)
(a)
(a) )
(b) )
α (º)
G (J/m2)
A; (d)
(b) (a)划 的 划 (b) 划
(d)
(c) A的 的 (c) 划
件 度 B的 曲 的 线 B.
试
.
纳米压痕技术表征薄膜/ 纳米压痕技术表征薄膜/涂层体系的 界面强度的原理 界面强度的原理