轮胎-硫化基础知识分析
轮胎-硫化基础知识30页PPT
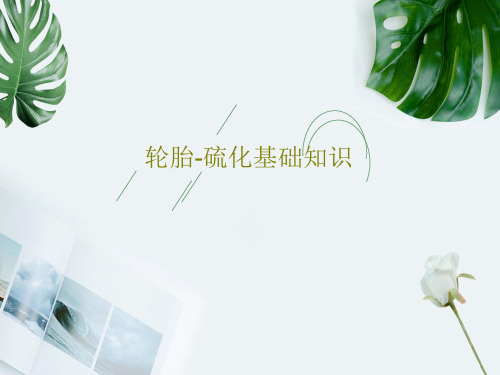
轮胎-硫化基础知识
56、极端的法规,就是极端的不公。 ——西 塞罗 57、法律一旦成为人们的需要,人们 就不再 配享受 自由了 。—— 毕达哥 拉斯 58、法律规定的惩罚不是为了私人的 利益, 而是为 了公共 的利益 ;一部 分靠有 害的强 制,一 部分靠 榜样的 效力。 ——格 老秀斯 59、假如没有法律他们会更快乐的话 ,那么 法律作 为一件 无用之 物自己 就会消 灭。— —洛克
拉
60、生活的道路一旦选定,就要勇敢地 走到底 ,决不 回头。 ——左
轮胎硫化知识

11.5±1.5 ±
12±2.5 ±
11±1.5 ±
11R22.5各胶料重量 各胶料重量kg 各胶料重量
10.916 2.600 2.972 4.199 3.233
2.149
2.896
1.522 4.039
10.00R20各胶料分布 各胶料分布
热喂料 冷喂料 冷 喂 料 热 热 喂 喂 料 料 热 喂 料 热喂料
初始状态时的粘度
t10 t90 t100
硫化程度达到10%时的时间(秒或分) 硫化程度达到10%时的时间(秒或分) 10 硫化程度达到90%时的时间(秒或分) 硫化程度达到90%时的时间(秒或分) 90 硫化程度达到100%时的时间(秒或分) 硫化程度达到100%时的时间(秒或分) 100 理论正硫化时间
时间单位通常用秒或分钟
返回
焦烧时间: 焦烧时间:从 硫化返原 上升1扭矩 上升 温度一般151℃ 160℃、185℃ 151℃、 温度一般151℃、160℃3%所用 ML上升 扭矩 、 % 单位的时间 的时间
前面
Cure Curve
后面
前面
Cure Curve
返回
前面
门尼粘度计
打印机 数据显示 和控制 上下模腔 胶料试样 温度控制及设定
目录
• • • • • 门尼粘度计及门尼粘度 门尼焦烧 硫化历程图 胶料的流变曲线 典型胶料的流变曲线和数据 A019流变 A083流变 流变 流变 A061流变 A056流变 流变 流变 A073流变 流变
目录
• • • • • • • • • 橡胶轮胎的大致结构 轮胎的不同花纹结构 剖面结构1,2 本公司轮胎断面的胶料位置 本公司轮胎各胶料的正硫化时间 本公司轮胎各胶料的用量 冷热喂料的示意图 各胶料在各部位的对应分布 轮胎硫化时的热量和压力示意图
很经典的橡胶硫化理论知识
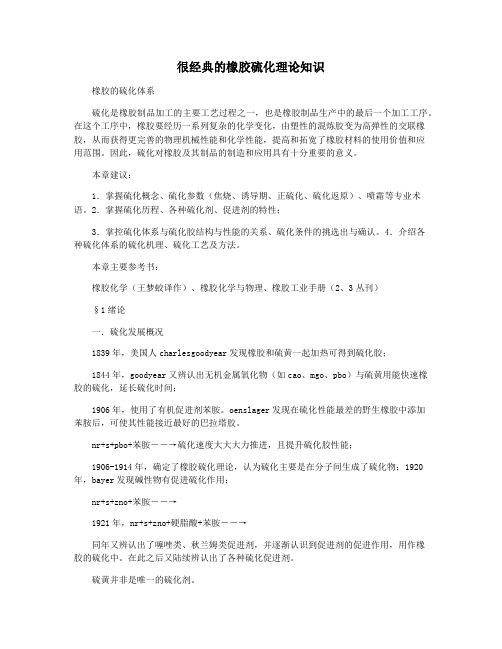
很经典的橡胶硫化理论知识橡胶的硫化体系硫化是橡胶制品加工的主要工艺过程之一,也是橡胶制品生产中的最后一个加工工序。
在这个工序中,橡胶要经历一系列复杂的化学变化,由塑性的混炼胶变为高弹性的交联橡胶,从而获得更完善的物理机械性能和化学性能,提高和拓宽了橡胶材料的使用价值和应用范围。
因此,硫化对橡胶及其制品的制造和应用具有十分重要的意义。
本章建议:1.掌握硫化概念、硫化参数(焦烧、诱导期、正硫化、硫化返原)、喷霜等专业术语。
2.掌握硫化历程、各种硫化剂、促进剂的特性;3.掌控硫化体系与硫化胶结构与性能的关系、硫化条件的挑选出与确认。
4.介绍各种硫化体系的硫化机理、硫化工艺及方法。
本章主要参考书:橡胶化学(王梦蛟译作)、橡胶化学与物理、橡胶工业手册(2、3丛刊)§1绪论一.硫化发展概况1839年,美国人charlesgoodyear发现橡胶和硫黄一起加热可得到硫化胶;1844年,goodyear又辨认出无机金属氧化物(如cao、mgo、pbo)与硫黄用能快速橡胶的硫化,延长硫化时间;1906年,使用了有机促进剂苯胺。
oenslager发现在硫化性能最差的野生橡胶中添加苯胺后,可使其性能接近最好的巴拉塔胶。
nr+s+pbo+苯胺――→硫化速度大大大力推进,且提升硫化胶性能;1906-1914年,确定了橡胶硫化理论,认为硫化主要是在分子间生成了硫化物;1920年,bayer发现碱性物有促进硫化作用;nr+s+zno+苯胺――→1921年,nr+s+zno+硬脂酸+苯胺――→同年又辨认出了噻唑类、秋兰姆类促进剂,并逐渐认识到促进剂的促进作用,用作橡胶的硫化中。
在此之后又陆续辨认出了各种硫化促进剂。
硫黄并非是唯一的硫化剂。
1846年,parkes辨认出scl的溶液或蒸汽在室温下也能够硫化橡胶,称作“热硫化法”;1915年,辨认出了过氧化物硫化;1918年,发现了硒、碲等元素的硫化;1930年,发现了低硫硫化方法;1940年,相继辨认出了树脂硫化和醌肟硫化;1943年,辨认出了硫黄给与体硫化;二战以后又出现了新型硫化体系,如50年代发现辐射硫化;70年代脲烷硫化体系;80年代提1出了平衡硫化体系。
硫化学习资料

载重子午胎硫化培训资料1、硫化条件内温:171±2℃.内压:2.6±0.1Mpa模套温度:158±2℃(12.00R20BT368/568/118/188/168A为162±2℃.) 侧板温度:148±2℃2、硫化步序第一步:5分钟内压蒸汽进第二步:一分钟一次热水进第三步:热水进、热水回第四步:5bar排第五步:0bar排第六步:抽真空3、硫化预热要求冬季(11月1日——4月30日)预热时间6小时,夏季(5月1日——10月31日)4.5小时,用正常标准温度预热,不许吹模,两合模口间距10——20㎜。
4、待胎胚预热如果机台待胎胚,开模时间15——20分之间,需合模预热30分钟。
如果机台待胎胚,开模时间20——40分之间,需合模预热40分钟。
如果机台待胎胚,开模时间40——60分之间,需合模预热60分钟。
如果机台待胎胚,开模时间20——40分之间,需合模预热40分钟。
如果机台待胎胚,开模时间60分以上,需合模预热120分钟。
5、合模力要求施工表给出合模力是指正硫化时间的合模力(左、右模力之差50kN)二、胶囊喷隔离剂要求1、定型,胶囊微微鼓起,并把抽真空开关打到断位置。
2、调整风压大约2个大气压左右。
3、喷壶嘴离胶囊表面大约20——30㎝4、自上而下,做到不多喷\不漏喷,隔离剂不往下淌.5、喷完后,用抹布把上下夹盘擦净,把一侧板擦净。
6、新上的胶囊首班必须喷两次(第四锅第二次)三、正确操作要点1、首先按抓胎器下降按钮,抓胎器页片闭合下降。
2、抓胎器页片对正胎胚圈中心,张开页片,抓取胎胚上升到位。
3、升下环使胶囊处于位伸状态,往胶囊均匀喷涂隔离剂,降下环,下模及中心机构吹风,同时定型胶囊,上环降,检查胶囊表面质量,检查下夹盘等密封件有无漏水。
4、放硫化小票,手动转入抓胎器对准中心,下降到预定位置。
5、手动调节左右一次定型压力,进一次定型蒸汽,同时上环降。
轮胎工艺知识点总结
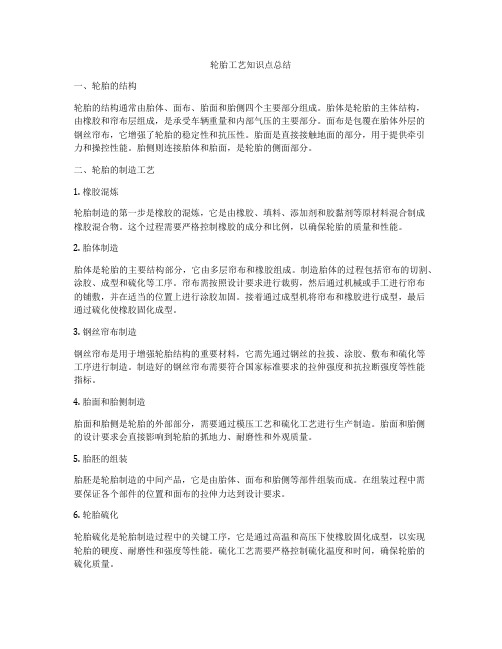
轮胎工艺知识点总结一、轮胎的结构轮胎的结构通常由胎体、面布、胎面和胎侧四个主要部分组成。
胎体是轮胎的主体结构,由橡胶和帘布层组成,是承受车辆重量和内部气压的主要部分。
面布是包覆在胎体外层的钢丝帘布,它增强了轮胎的稳定性和抗压性。
胎面是直接接触地面的部分,用于提供牵引力和操控性能。
胎侧则连接胎体和胎面,是轮胎的侧面部分。
二、轮胎的制造工艺1. 橡胶混炼轮胎制造的第一步是橡胶的混炼,它是由橡胶、填料、添加剂和胶黏剂等原材料混合制成橡胶混合物。
这个过程需要严格控制橡胶的成分和比例,以确保轮胎的质量和性能。
2. 胎体制造胎体是轮胎的主要结构部分,它由多层帘布和橡胶组成。
制造胎体的过程包括帘布的切割、涂胶、成型和硫化等工序。
帘布需按照设计要求进行裁剪,然后通过机械或手工进行帘布的铺敷,并在适当的位置上进行涂胶加固。
接着通过成型机将帘布和橡胶进行成型,最后通过硫化使橡胶固化成型。
3. 钢丝帘布制造钢丝帘布是用于增强轮胎结构的重要材料,它需先通过钢丝的拉拔、涂胶、敷布和硫化等工序进行制造。
制造好的钢丝帘布需要符合国家标准要求的拉伸强度和抗拉断强度等性能指标。
4. 胎面和胎侧制造胎面和胎侧是轮胎的外部部分,需要通过模压工艺和硫化工艺进行生产制造。
胎面和胎侧的设计要求会直接影响到轮胎的抓地力、耐磨性和外观质量。
5. 胎胚的组装胎胚是轮胎制造的中间产品,它是由胎体、面布和胎侧等部件组装而成。
在组装过程中需要保证各个部件的位置和面布的拉伸力达到设计要求。
6. 轮胎硫化轮胎硫化是轮胎制造过程中的关键工序,它是通过高温和高压下使橡胶固化成型,以实现轮胎的硬度、耐磨性和强度等性能。
硫化工艺需要严格控制硫化温度和时间,确保轮胎的硫化质量。
7. 轮胎检验和包装轮胎制造完成后需要进行严格的质量检验,包括外观质量、尺寸测量、硫化性能和性能测试等。
合格的轮胎在包装之前还需要进行气密性试验和动平衡试验等。
三、轮胎的检验和测试轮胎制造过程中的检验和测试是确保轮胎质量的重要环节。
轮胎硫化压力

轮胎硫化压力一、背景介绍轮胎硫化是指将橡胶制品在高温和高压下进行加热处理,使其产生交联反应,从而形成具有强度和弹性的物质。
而轮胎硫化则是指将橡胶轮胎进行硫化处理,以提高其耐磨性、耐老化性和抗裂性等性能。
二、硫化过程中的压力在轮胎硫化过程中,压力是一个非常重要的参数。
一方面,适当的压力可以促进橡胶材料之间的交联反应,从而提高轮胎的强度和耐久性;另一方面,过高或过低的压力则会影响硫化效果,并可能导致轮胎内部出现气泡或缺陷等问题。
三、硫化压力的测量方法为了保证轮胎硫化过程中的压力符合要求,必须对其进行实时监测。
目前常用的方法有以下几种:1. 基于传感器的测量方法:通过在模具上安装压力传感器来实时监测模具内部的压力变化。
2. 基于液位计的测量方法:在模具中加入一定量的液体,通过监测液位变化来计算出压力大小。
3. 基于气压计的测量方法:在模具中加入一定量的气体,通过监测气压变化来计算出压力大小。
四、硫化压力的控制方法为了保证轮胎硫化过程中的压力稳定在合适范围内,必须采取相应的控制措施。
常用的方法有以下几种:1. 控制硫化温度:适当提高硫化温度可以促进橡胶材料之间的交联反应,从而提高轮胎硫化效果;但是过高的温度则会导致轮胎内部出现气泡或缺陷等问题。
2. 调整硫化时间:适当延长硫化时间可以保证橡胶材料之间充分反应,从而提高轮胎硫化效果;但是过长的时间则会影响生产效率和产品质量。
3. 调整模具结构:合理设计模具结构可以保证轮胎内部受到均匀的压力作用,从而提高硫化效果;但是不合理的模具结构则会导致轮胎内部出现不均匀的硫化情况。
4. 优化硫化工艺:通过对硫化工艺进行优化,如调整硫化温度、时间、压力等参数,可以提高轮胎的硫化效果,并保证产品质量和生产效率的平衡。
五、结论轮胎硫化压力是影响轮胎硫化效果和产品质量的重要参数之一。
为了保证轮胎硫化过程中的压力稳定在合适范围内,必须采取相应的测量和控制措施,并逐步优化硫化工艺,以提高产品质量和生产效率。
轮胎生产硫化氮气系统课件

变压吸附的原理
吸附量
任何一种吸附剂对于同一 被吸附气体来说,在吸附 平衡的情况下,温度愈低, 压力愈高,吸附量愈大, 如果温度不变,在加压的 情况下吸附,用减压或常 压解吸的方法,称为变压 吸附。
吸附压力
经过研磨、氧化、成型、碳化并经过特殊的孔型处理工艺加工而成 的,表面和内部布满微孔的柱形颗粒状吸附剂。碳分子筛孔径分布 图如下:
硫化蒸汽原单位的变化 原单位:蒸汽(吨)/轮胎生产重量(吨) (T/T), 使用T/B硫化机33台, P/C硫化机100台生产轮胎4500T/M时的实际成绩
1.以前的热水硫化
2.改进后的热水硫化 (热水回收,保温,缩 短硫化时间等)
3.P/C轮胎氮气硫化
硫化蒸汽消耗量 Kt/M
10.800
单位轮胎的蒸汽消
5、氮气硫化危险小,蒸汽使用高压热水,危险性较高。 6、提高硫化机胶囊的寿命
氮气纯度为99.9%时 ,胶囊 寿命仅为原来的80% 氮气纯度99.99%,胶囊寿命是原来的120% 氮气纯度99.999%时,胶囊寿命是原来的150%
二、氮气硫化的缺限:
• 氮气分子较小,对机台密封结构和密封材料的性能启,否则容 易造成泄漏。
耗量 t/t
2.4
比较成本 100
8.550
1.9
79
5.850
1.3
54
2、生产效率的改进
充氮硫化与热水硫化相比,定型、硫化机和模后向胶囊内充入高 温蒸汽和高压气体,蒸汽的高温热量和隔热压缩使得温度上升,硫化速 度变快,硫化时间被缩短。
大胎每条平均可节省4min,小胎约2min。
氮气硫化周期比过热水硫化周期缩短了5-15%(以小胎计),生产效率 提高了3.2%-10%。
轮胎硫化加工
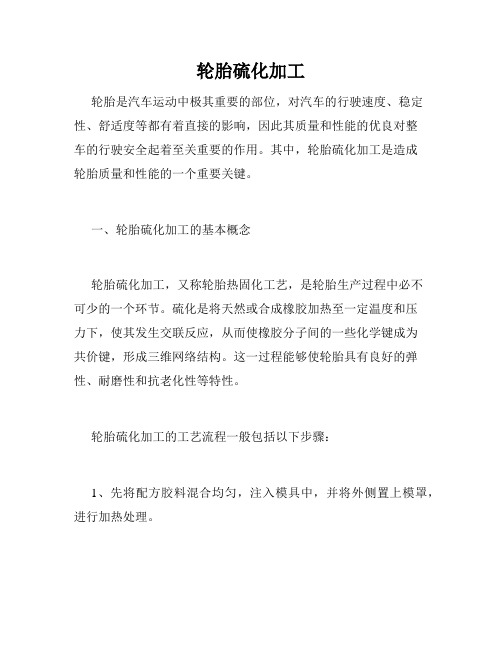
轮胎硫化加工轮胎是汽车运动中极其重要的部位,对汽车的行驶速度、稳定性、舒适度等都有着直接的影响,因此其质量和性能的优良对整车的行驶安全起着至关重要的作用。
其中,轮胎硫化加工是造成轮胎质量和性能的一个重要关键。
一、轮胎硫化加工的基本概念轮胎硫化加工,又称轮胎热固化工艺,是轮胎生产过程中必不可少的一个环节。
硫化是将天然或合成橡胶加热至一定温度和压力下,使其发生交联反应,从而使橡胶分子间的一些化学键成为共价键,形成三维网络结构。
这一过程能够使轮胎具有良好的弹性、耐磨性和抗老化性等特性。
轮胎硫化加工的工艺流程一般包括以下步骤:1、先将配方胶料混合均匀,注入模具中,并将外侧置上模罩,进行加热处理。
2、加热过程中,橡胶分子间的双键发生断裂而形成自由基,这些自由基随着时间的推移和温度的升高而加速形成分枝结构,进而发生交联反应。
加热的温度、压力和加热持续时间都对交联反应的速度和程度产生影响。
3、硫化完成后的轮胎需要进行清洗、装配、平衡等处理,最后交付给汽车工厂进行使用。
二、硫化加工中的关键技术1、加热温度与时间的控制加热温度是影响轮胎硫化反应速率的主要因素之一。
当温度升高时,硫化反应的速率会增加,但同时也会增加部分反应的副反应产生,导致高温下轮胎质量和性能的质量下降。
因此,控制硫化温度非常关键。
硫化温度一般在140℃-170℃之间,时间需要根据材料的不同来进行调整。
在低于140℃的温度下,反应速率很慢,需要持续的加热才能形成完整的三维交联网络结构。
在152℃左右的温度下,在10-20分钟时间内完成反应。
如果硫化温度过高,会导致水分和氧气进入,导致轮胎质量下降。
2、硫化时空气排除轮胎硫化时,轮胎内的气体会受到各种界面张力的作用,影响气体排除的效率。
如果气体不能及时排除,就难以填满各处的缝隙,这样便会导致轮胎内部压力的不均匀,最终影响轮胎的性能。
因此,要做好轮胎硫化时空气的排除,可以采用注气和震动抖动,使气泡不断上浮,加快排出速度,从而获得均质的硫化品。
- 1、下载文档前请自行甄别文档内容的完整性,平台不提供额外的编辑、内容补充、找答案等附加服务。
- 2、"仅部分预览"的文档,不可在线预览部分如存在完整性等问题,可反馈申请退款(可完整预览的文档不适用该条件!)。
- 3、如文档侵犯您的权益,请联系客服反馈,我们会尽快为您处理(人工客服工作时间:9:00-18:30)。
硫化基础知识
6、胎里漏线与胎体帘线弯曲 (1)机头宽度与帘线假定伸张值选取不合理 (2)胎胚周长大小选取不合理,周长小,伸张大,造成 胎里漏线,反之出现帘线弯曲。 (3)成型机传递环和机头扇形块出现故障可以造成胎圈 定位出现偏差 (4)成型时局部拉伸,造成尺寸变小;部件接头脱开。 (5)带束层偏歪 (6)硫化定型压力过大、时间过长,造成胎体帘线发生 弯曲,胎体反包高度降低,硫化后产生帘线弯曲。 (8)压辊压力过大 (9)硫化过程中,硫化胶囊渗漏,导致胶囊内热水渗到 胎里,压迫内衬层胶料内渗。 (10)内衬层厚度偏薄造成胎里漏线
硫化基础知识
第二讲:硫化工艺要点及注意事项
1、胎坯检查: (1)胎坯倒放:标识线在上侧。 (2)胎坯要放正:减少变形。 ( 3 )胎坯修整:胎圈和子口处均匀扎眼,不得扎透,为 排气和进一步整修胎坯。 2、吊胎坯:启模前3—5分钟,主要为恢复胎胚的形状, 如时间过长,则胎坯部件移位、变形过大。 3、硫化记录确认: (1) 异常硫化条件的轮胎要单独存放 ( 2 )按要求正常对硫化工艺参数记录,确保记录真是可 靠、可追溯。
硫化基础知识
5、气密层气泡、脱层 (1)成型中超定型压力低或组合压辊压力小、组合滚压 各段压力及轨迹设置有问题; (2)半成品部件不粘、喷霜; (3)垫胶定位偏歪,胎体与带束层之间产生孔隙 (4)内衬层胶料含水过多,硫化时形成气泡。 (5)内衬层压延时贴合不实,层间存在气泡。 (6) 成型时有水或胶浆未干。 (7) 胎坯气泡未按标准修理。 (8)胶囊砂眼造成轻微漏水、汽。
T90=ML+(MH-ML)×90%
硫化基础知识
硫化条件的选取和确定
一般来讲,测定出正硫化时间后,并不等于找到了具体产品的最 适宜硫化条件,还必须考虑以下因素: 产品的厚度、胶料的导热系数、制品材料中其它材料对导热的影响、 模型尺寸、模型材料、产品具体形状、硫化介质(油、蒸汽、水、 气、射线) 硫化三要素:时间、温度、压力 1、硫化压力 (1)施加硫化压力的目的:通过水胎或胶囊传递热量,达到内外硫 化的目的;使胶料易于流动和充满模腔;提高胶料的致密性;提 高硫化橡胶的物理机械性能;提高胶料与骨架材料的粘合性能。 但不是越大越好,还应考虑生产成本和设备的承受能力。 (2)硫化压力的选取:随胶料配方、可塑性、产品结构不同而不同, 在工艺上遵循:塑性大压力小,产品厚、层数多、结构复杂压力 大。 2、硫化时间:交联反应完成的时间;与温度有相应的关系。
(2)硫化延时: 内温波动延时按下表进行 总欠程度 1-50 51-110 111-150 151-180 补时(分) 3 5 8 12 外温波动延时按下表进行 总欠程度 0-20 20-50 51-100 101-150 补时(分) 0 0.5 1.0 1.5 说明:每5分钟温度降低1度,总欠程度为1。 8、硫化过程参数控制: (1)定型:一次定型压力0.03~0.04Mpa;时间20秒 二次定型压力0.06 ~0.08Mpa,时间20~25秒。 定型高度的计算: 装胎高度:下胎圈距下侧板10—15mm。 注意:机械手对中精度±2mm。
自由基(或离子) 橡胶 2、交联反应阶段 交 联 交联键重排裂解、主链改性 3、网构形成阶段 硫化胶 在网构形成阶段的前期交联反应趋向完成,产生的交 联键发生重排和裂解反应;而此阶段的后期,交联反 应已经基本停止,随之发生的主要是交联键的重排和 裂解反应。
硫化基础知识
硫化反应历程图
强度
焦烧
热硫化
平坦硫化
硫化基础知识
第一讲:理论基础部分 硫化历程
一、硫化定义:硫化是在一定的条件平时所说的硫化三要素。 二、橡胶硫化反应历程: 促进剂、活性剂 硫磺 1、诱导阶段 促进剂多硫化合物 橡胶 含橡胶分子链的多硫化合物 分解
硫化基础知识
硫化基础知识
硫化基础知识
(2)内压蒸汽:压力0.8±0.1Mpa,温度170±3度。 (3)内压热水:压力2.6±0.1Mpa,温度169±2度。 (4)外压蒸汽:压力0.39±0.03Mpa,温度151±2度。 ( 5 )注意:内压回水温度低于 165 度或高于 175 度不得装 模硫化。外温低于或高于标准2度,不得装模硫化。 9、启模平放(考虑后硫化):外胎平放6月1日-9月30 日 40分钟以上;其他时间20分钟以上。 10、修剪:(1)部位活络块胶边、胎趾大边、排气孔胶 柱(2)修剪标准:≤1mm。(3)注意不得损伤外胎。
硫化基础知识
7、稀线 (1)成型时部件接头过大; (2)成型时对帘布拉伸过大 (3)帘布大传递速度与主鼓的速度不匹配; (4)帘布长度比标准短,接头机接头时对其进行拉伸; (5)胎胚在成型机上超定型时压力过大; (6)硫化定型压力过大; (7)胎体帘布和内衬层过渡层不粘,造成与胎体分离; (8)压延工序生产过程中产生稀线; (9)帘布在直裁接头造成的稀线
第三讲: 外观缺陷原因分析
硫化基础知识
1、子口大边(或子口大边漏钢丝) (1)胶料粘度偏低 (2)胎侧/子口半成品挤出厚度偏厚。 (3)内衬层压延时宽度超标。 (4)成型时,部件/灯光定位不准,成型时胎体反包/正包 (胎侧/子口)不好,导致胎圈部位胶料过多。 (5)胎坯成型时两边扣圈不对称或成型时钢丝圈变形、胎 坯存放不当变形的原因引起胎圈部位半成品迁移。 (6)胎坯装入高度不合适,过大会使胎坯过度拉伸、偏 歪,过小,则对胎坯支撑不牢,合模时把胎坯挤偏。 (7)机械手对中精度达不到要求,把胎坯装偏。 (8)机械手张开直径偏大,吊胎坯时胎坯偏歪 (9)胶囊膨胀不均匀,定型时把胎坯挤偏。 (10)钢丝圈直径比标准小。 (11)硫化胶囊不对 (12)同一硫化模具上的胎圈和胎圈卡环之间不配合
硫化基础知识
3、子口上抽 (1)胎胚在硫化定型过程中,胶囊打褶; (2)胎圈过大; (3)钢丝圈不园; (4)子口部位材料不足; (5)胎圈定位不准。
硫化基础知识
4、胎里皱疤、出沟、窝气、不平等 (1)隔离剂过多或未干,硫化汽化导致窝气。 (2)装胎定型或硫化过程中断电或失压,胎里与胶囊剥离。 (3)定型高度过大,上下卡盘紧紧拉住胎坯的胎圈,胶囊与 胎里的空气无法排出。 (4)定型压力超出上线,产生肩部弯情况,导致胎里反弧 (4)胎坯装模不正,重新定型时对胎坯反复进行抽真空,定 型动力导致胶囊与内衬层剥离。 (5)合模后蒸汽或热水未及时充入硫化胶囊,造成胶囊瞬间 失压。 (6)内衬层接头开或过大 (7)带束层紧或周长偏小 (8)垫肩胶上反或位置偏移造成胎里反弧 (9)胶囊伸展不充分
硫化基础知识
8、重皮、裂口、缺胶
( 1 )相应部位的胶料由于某种原因造成加工温度过高,焦烧时间 短。 (2)成型贴合偏歪,影响胶料流动; (3)成型的胎坯胎侧接头虚接;修补胎坯过渡不均匀。 (4)成型过程中半成品部件拉伸变形,局部胶料不足。 ( 5 )硫化模具表面不干净或排气孔堵塞,胎侧底板排气孔或排气 槽堵塞。 ( 6 )胎坯装模定型时压力过大或时间过长,胎坯变软局部拉伸变 薄或裂开。 (7 )硫化时二次暂停高度过小或时间过长,胎坯过早的接触胎侧, 局部缺胶。 (8)硫化机泄露,水或蒸汽喷到胎侧表面,导致表面缺胶。 (9)胶囊隔离剂涂刷过多,污染侧板,造成缺胶或裂口。 (10)材料不足、胎胚周长偏低等。
硫化基础知识
4、硫化工号: 放置:空白处,无商标、字体、凤线处,左单,右双。 5、模具清理:保证轮胎外观质量。 ( 1 )模具和花纹清理原则:模具每生产 1000 条轮胎清模, 一般每月清洗一次。 (2)气孔通透:花纹块或侧板每连续2个气孔堵塞,必须 进行通透处理。
硫化基础知识
6、硫化胶囊 (1)存放时要保证其自然状态。 (2)要经常检查胶囊,如发现出现胶囊裂口、局 部薄或损伤的要及时更换。 (3)更换胶囊进行预热,时间不少于15分钟。 注意:胶囊脱模剂滴落在下侧板上必须擦净。 7、硫化延时 ( 1 )季节转换:每年 6 月 1 日 —9 月 30 日使用外温 143度硫化(比正常低2度),考虑后硫化)。
硫化基础知识
硫化过程中胶料性能的变化
1、拉伸强度:峰值 2、定伸应力:峰值 3、弹性:峰值 4、硬度:几乎不变 5、伸长率:峰值 6、永久变形:峰值 7、磨耗性能:正硫化磨耗性能最好 8、耐热性:正硫化耐热性最好 9、透气性:硫化充分的胶料比硫化不足的胶料耐透气
硫化基础知识
正硫化及其测试方法正硫化及其测试方法
硫化基础知识
硫化介质:胶料加热传递热能量的物质,常见 的硫化介质包括饱和蒸汽、过热水、过热蒸汽、 过热水等。我厂生产全钢胎主要采用饱和蒸汽 和过热水。 1 、饱和蒸汽:压力和温度存在一一对应关系 的蒸汽。优点:给热系数大,导热效率高,放 热量大,传热均匀,可以改变压力来确定温度, 压力和温度比较稳定,好控制。 2、热水:在一定压力下,超过100℃的水。优 点:能够提供较高的温度,赋予较大的压力; 不可压缩性,可将动力站的压力尽量大的用于 硫化;能够提供比较稳定的压力。
硫化基础知识
3、硫化温度:硫化反应的前提。 我厂全钢胎外压温度在 151±2℃和155±2℃左右,斜交 载重轮胎温度145±2℃,还有其它使用温度(如工程轮 胎和轿车轮胎)。 一般情况下,温度越高,硫化速度越快,硫化温度每提 高10℃,硫化时间缩短一半(经验公式)。温度和时间 的关系一般采取范德霍夫公式: τ 1/τ 2=K(t2-t1)/10 其中: τ 1 为温度为 t1 时的硫化时间, τ 2 为温度为 t2 时 的硫化时间,K为硫化反应系数,一般情况下K=2。 硫化条件的确定单独讲
硫化基础知识
2、热硫化阶段:相当于硫化反应的交联阶段,逐渐产应 网构,使橡胶强度和弹性急剧上升。 3、平坦硫化阶段:相当于硫化反应网构形成的前期。在 这一时期胶料保持最佳硫化性能,所以我们正硫化时 间一般选在这一阶段。 正硫化时间:从胶料开始加热起至出现平坦期止所经历 的时间称正硫化时间,即剩余焦烧时间和热硫化时间之 和. 4、过硫化阶段:相当于硫化反应中网构形成的后期。在 这一阶段主要发生交联键的重排及交联键的裂解,因 此胶料性能明显降低。