轮对动平衡试验作业指导书
动平衡作业指导书

3231560
检测时装配TR413的气门嘴后静不平衡量≤25g(0.881盎司)
全检
在重点的位置用白色油性笔点上约5mm的圆点。
序号
产品图号
特殊特性分类
控制要求
检验频次
备注
42
3241560
静不平衡量≤36g(1.269盎司)
全检
用白色油性笔点上约5mm的圆点
43
3281450
◎
静不平衡量≤28.5g(1.005盎司)
11
24英寸
动不平衡量≤65.1g(2000g.cm)
6.7选择平衡块安装模式——双边夹重,双边粘重,单边粘重,混合模式(按一次中央粘重,按两次外缘粘重、内缘粘重,按三次外缘粘重、内缘夹重,按四次内缘夹重,按五次CTS系统)。
6.8选择检测单位,按住两秒,测量单位可在克与盎司间切换。
6.9检测时需将平衡机的保护罩拉下,按START键开始检测。
6.10待轮子转动停止后,将保护罩掀起,如动平衡检测合格,则确定其轻点部位,根据其要求在轻点(或重点)上贴圆点标签(或油漆笔标示),将轮子转入下工序;如轮子动平衡检测不合格,则在轮子喷上红色手喷漆,用红色记号笔标识“动平衡不合格废”字样,并放在动平衡不合格品的专用架上,具体按《回炉品管理规定》执行。
全检
用3mm的蓝点标出轻点位置
62
4031665
装上气门嘴后静不平衡量≤24.7g
全检
63
4041665
◎
装上气门嘴后静不平衡量≤24.7g
全检
64
4051560
装上气门嘴后静不平衡量≤26.3g
全检
65
4111460
装上气门嘴后总不平衡量≤28g
车轮动平衡安全操作工作任务书
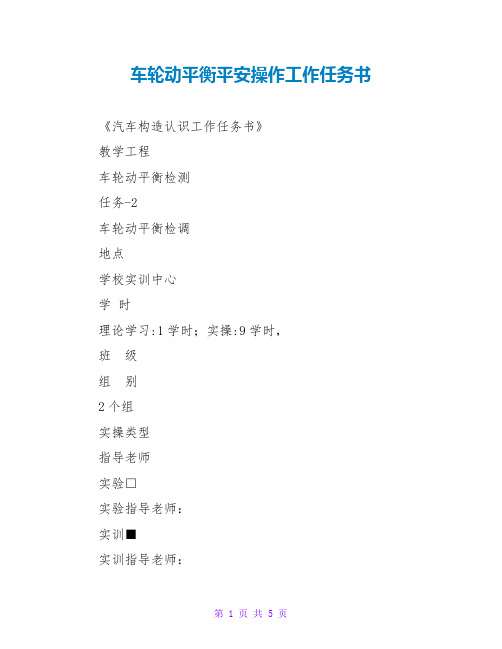
车轮动平衡平安操作工作任务书《汽车构造认识工作任务书》教学工程车轮动平衡检测任务-2车轮动平衡检调地点学校实训中心学时理论学习:1学时;实操:9学时,班级组别2个组实操类型指导老师实验□实验指导老师:实训■实训指导老师:实习□实习指导老师:企业指导老师:是□ 否■ 进展消费实习理念根据专业特点,课堂进车间,学中做,做中学,培养学生动手才能。
目的要求纯熟掌握车轮动平衡检测与调整车轮动平衡。
根底知识1.轮胎的功用2.轮胎的类型3.轮胎的构造4.子午线轮胎的规格5.车轮动平衡仪的使用方法及考前须知理论形式在老师指导下分2个小组进展实训。
材料及器具车轮总成,动平衡检测仪、专用卡尺、拆卸钳及平衡块。
内容方法步骤1、准备好相关器材,去除被测车轮上的泥土、石子和旧平衡块,检查轮胎气压。
2、根据轮辋中心孔的大小选择锥体,仔细装上车轮,用大螺距螺母上紧。
3、翻开设备电开关,检查指示与控制面板指示是否正确,4、用平衡仪上的标尺测量轮辋边缘至平衡仪机箱间隔,用卡尺测量轮辋宽度、由胎侧读出轮辋直径,并将测量的数值输入到指示面板上。
5、放下车轮防护罩,按下启动键,车轮旋转,平衡测试开场,微机自动采集数据,从显示面板上读取车轮内、外两侧不平衡量和不平衡位置。
6、抬起车轮防护罩,用手渐渐转动车轮,当指示装置发出指示(显示点阵指示灯)时停顿转动,在轮辋的内侧或外侧的上部(时钟12点位置)分别加装相应质量的平衡块,平衡块止粘贴、卡要结实。
7、假设安装平衡块后产生新的不平衡,应重新进平衡调式,直至指示装置显示00或0K为止,8、动平衡测试调整完毕,松开大螺距锁紧螺母,取下车轮,关闭电开关。
考核评价标准1.操作标准、纯熟程度及工作效果〔70分〕:(1)、认真检查车轮上有无泥土、石子等异物5分,(2、正确用专用钳取下平衡块5分,(3)、车轮挪动至平衡机主轴方向准确无误5分,(4)、选择定位锥套及紧固准确无误5分,(5)、翻开电开关,用用标尺、卡尺及看胎侧测量α、b、d三个数据5分,(6)在平衡仪显示屏上正确输入α、b、d三个测量数值5分,(7)、正确说出轮胎型号各代表的含义(如195/60R 16 89H) 5分,(8)、在平衡仪上能迅速找到不平衡点位置,并找到平衡块安装位置5分,(9)准确找到相对应的平衡块,(10)、用专用钳将平衡块固定在安装位置上,左右手配合将平衡块分别逐个安装在钢圈上,铝合金轮毂在相应位置处粘贴(粘贴时去除污垢)10分,(11)、启动按钮主轴旋转,停顿后看显示屏数据两边是否为零10分,(如不为零继续加装相应平衡块,直到为零合格为止),(12)、关闭电,取出大螺距螺母、锥套及车轮5分。
轮对镟修作业指导书(3号车轮车床)
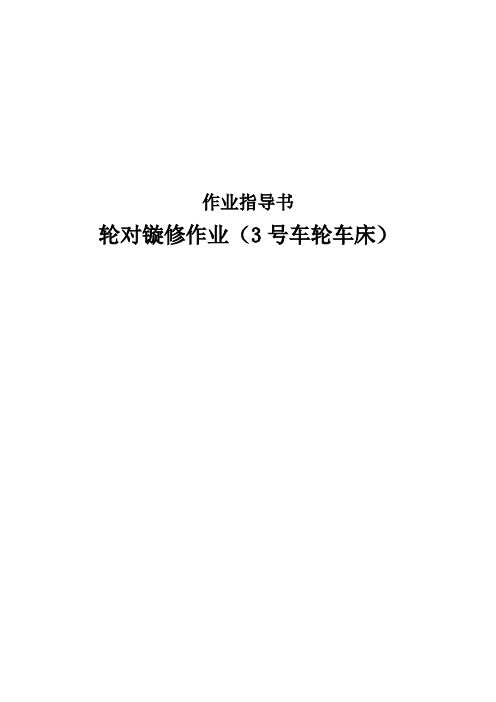
擦伤、局部凹入、熔粘、垂直磨耗与辗堆等
轮径尺、第四
4. 轮 对 镟 种检查器、LM 缺陷必须彻底镟除;轮缘外侧及踏面部位允
许局部留有黑皮,但连接部位应平滑过渡。
4 修 后 测 型检查样板、
4.2 踏面及轮缘加修后,其加工部位的表面
量、检查
Ra25μm 粗糙 粗糙度须达到Ra25μm[图14],粗糙度不达标,
陷面积不得大于原中心孔圆锥面积的 1/8,
最高运行速度为 160km/h 时修复后不得大于
1/16,超过时送大修。[图 4]
2.1.4 在轴颈上安装橡胶保护套进行保护。
[图 3]
作业图示
图 3 轴颈安装保护套 图 4 检查轴颈中心孔状态
序号 作业项目 工装及材料
3
车轮车床镟修作业指导书
作业程序和标准
作业程序和标准
作业图示
4.4 轮缘及轮辋厚度的测量[图16]:轮缘厚度
轮径尺、第四 应满足[表2],超过时须重新进行镟修;
轮对镟修 种检查器、LM
表 2 轮缘及轮辋厚度标准
4 后测量、 型检查样板、
检查
Ra25μm 粗糙
最高运行速度 (km/h)
轮缘厚度(mm) 轮辋厚度(mm)
局管路用车
≥28
度样板
度样板
可降低车轮车床主轴转速和进给倍率,重新
镟修。
图 14 比对踏面粗糙度
序号 作业项目 工装及材料
12
车轮车床镟修作业指导书
作业程序和标准
作业图示
4.3 使用轮径尺测量车轮直径[图15]:同一车
轮相互垂直的轮径差应满足[表1]。同一轮对
轮径尺、第四 相对车轮的轮径差,即左右侧车轮直径之差
(完整)轮胎动平衡实训指导书、评分标准、实训工单

(完整)轮胎动平衡实训指导书、评分标准、实训工单(完整)轮胎动平衡实训指导书、评分标准、实训工单编辑整理:尊敬的读者朋友们:这里是精品文档编辑中心,本文档内容是山我和我的同事精心编辑整理后发布的,发布之前我们对文中内容进行仔细校对,但是难免会有疏漏的地方,但是任然希望((完整)轮胎动平衡实训指导书、评分标准、实训工单)的内容能够给您的工作和学习带来便利。
同时也真诚的希望收到您的建议和反馈,这将是我们进步的源泉,前进的动力。
本文可编辑可修改,如果觉得对您有帮助请收藏以便随时查阅,最后祝您生活愉快业绩进步,以下为(完整)轮胎动平衡实训指导书、评分标准、实训工单的全部内容。
教案首页车轮动平衡检测授课班级:授课时间:教学设计:仁实训准备[5分钟]1>考勤:2、工具准备:轮胎4个、汽车使用手册、一字螺丝刀、轮胎平衡钳、化清剂、抹布、轮胎平衡机,平衡块若干等。
3、实训要求:2、实验目的[5分钟]同学们,今天我们的实训项目是:轮胎的动平衡。
有谁告诉我,做轮胎动平衡的目的是什么?参考答案:我们对能够“使用的”轮胎进行平衡调校.鼓包了轮胎、轮毂变形了轮胎、被钉子戳破了轮胎,我们还有没有必要进行轮胎的平衡检测呢?同学们首先得搞清楚对象,别拿了一个不能使用的轮胎做动平衡, 结果不能使用,或者根本就平衡不了。
怎样对一个跑偏的轮胎做动平衡呢?我们需要仪器设备,下面,我们一起来看看这台轮胎平衡机,型号SBM 96:轮胎平衡机具有自动诊断和自动调校系统,能将传感器送来的电信号通过电脑运算、分析判断后显示出不平衡量及不平衡位置。
3、轮胎动平衡的注意事项[5分钟]同学们在操作的过程,可能会岀些错,请大家注意:1、首先要检查轮胎,检查胎面有无鼓包、有无裂纹、有无异物嵌入等,检查轮網是否变形,然后清除轮胎上的异物和旧平衡块。
这一步不能省略,它是我们做轮胎动平衡的前提.2、装卸轮胎,一定要轻拿轻放,安装要可靠、牢固.如果安装不正,会引起严重的不平衡.3、注意轮網的式样,不同的轮網选用不同的模式。
叶轮动平衡测试作业指导书
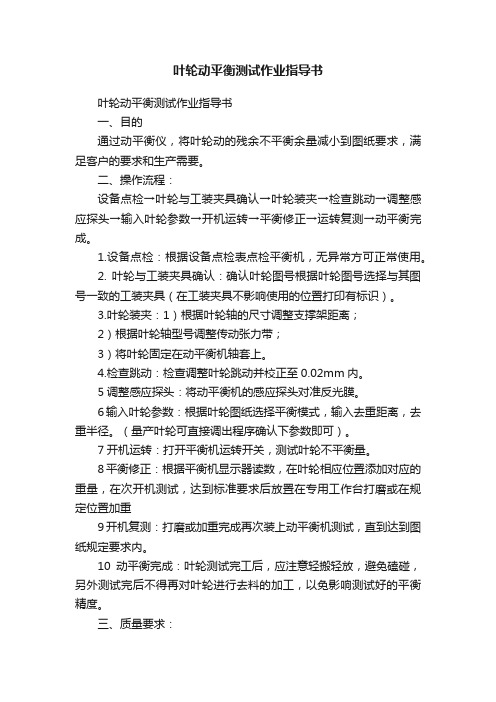
叶轮动平衡测试作业指导书
叶轮动平衡测试作业指导书
一、目的
通过动平衡仪,将叶轮动的残余不平衡余量减小到图纸要求,满足客户的要求和生产需要。
二、操作流程:
设备点检→叶轮与工装夹具确认→叶轮装夹→检查跳动→调整感应探头→输入叶轮参数→开机运转→平衡修正→运转复测→动平衡完成。
1.设备点检:根据设备点检表点检平衡机,无异常方可正常使用。
2. 叶轮与工装夹具确认:确认叶轮图号根据叶轮图号选择与其图号一致的工装夹具(在工装夹具不影响使用的位置打印有标识)。
3.叶轮装夹:1)根据叶轮轴的尺寸调整支撑架距离;
2)根据叶轮轴型号调整传动张力带;
3)将叶轮固定在动平衡机轴套上。
4.检查跳动:检查调整叶轮跳动并校正至0.02mm内。
5调整感应探头:将动平衡机的感应探头对准反光膜。
6输入叶轮参数:根据叶轮图纸选择平衡模式,输入去重距离,去重半径。
(量产叶轮可直接调出程序确认下参数即可)。
7开机运转:打开平衡机运转开关,测试叶轮不平衡量。
8平衡修正:根据平衡机显示器读数,在叶轮相应位置添加对应的重量,在次开机测试,达到标准要求后放置在专用工作台打磨或在规定位置加重
9开机复测:打磨或加重完成再次装上动平衡机测试,直到达到图纸规定要求内。
10动平衡完成:叶轮测试完工后,应注意轻搬轻放,避免磕碰,另外测试完后不得再对叶轮进行去料的加工,以免影响测试好的平衡精度。
三、质量要求:
1)、残余不平衡量见图纸要求图纸无要求见检验记录要求:2)、上下叶轮、周转叶轮避免碰撞;
3)、除去或配重修正不得超出图纸规定部位,填写动平衡记录。
编制:日期:批准:日期。
动平衡实验指导书

动平衡实验一前言:平衡技术广泛应用于航天,航空,船舶,汽车,纺织,机电等各个行业。
几乎所有的转子都有极严格的平衡工艺要求,以延长机器的使用寿命,改善其性能,消除振动,减少噪音,达到平稳运行的目的。
GYQ-300动平衡实验机是实现平衡技术,该平衡实验机试验对象为Φ≤950mm的转子,检测刚性转子在运转中的不平衡量并对振动进行分析的最有效设备之一。
二实验目的:1.掌握GYQ-300动平衡实验机的操作使用。
2.熟悉利用GYQ-300动平衡实验机进行刚性转子的加(减)重量标定。
三实验原理:1.通过动平衡设计,理论上已平衡的宽径比D/d<5的刚性转子,制成产品后还需要进行动平衡试验。
2.该动平衡实验机用于测量零件不平衡量的大小和相位,为在校正面上加重或减重提供重要依据,最后达到平衡的目的。
零件在旋转时由于不平衡量产生的离心力作用在支承架上,支承架产生前后振动,并带动振动传感器活动线圈,把振动信号变为电信号。
为确定不平衡量的相位,动平衡实验机上必须装有光电传感器,在动平衡实验前必须在被平衡的转子上涂黑色标记。
3.用光电传感器对准标记,通过反射光的变化,光电传感器能输出反映转子的电脉冲信号。
把振动传感器与光电传感器的信号同时输入电测箱,电测箱对两种信号进行分频、滤波、运算等信息处理,最后在显示器上显示出不平衡量的大小和相位。
4.该动平衡实验机可用于纺织机械、小型电机、增压器、枪弹头等各类精密转子的动平衡实验。
四实验步骤:1.动平衡实验机通电,控制箱的“POWER”旋钮指到“1”,控制计算机和动平衡实验机已接通电源,按下计算机电源按键,打开计算机。
双击桌面的“软USBPrint”文件,进入动平衡实验界面。
2.空气压缩机通电,给动平衡试验机供气,供气压力为6bar∕min 。
3.动平衡实验机安放好标准转子,套上皮带并打开动平衡实验机气源开关,使皮带夹紧标准转子。
在标准转子的“0刻度”涂上深黑色清晰标记,动平衡实验机的光电探头对准黑色标记。
轮对动平衡作业指导书

轮对动平衡 作业指导书1.去重加工时必须佩戴护目镜,防止铁屑飞溅入眼睛。
工作时必须穿防砸皮鞋,防止车轮碾伤。
类别:A2、A3修系统:走行装置部件:轮对及轴箱轮对动平衡作业指导书适用车型:25K、25T型车(v>120km/h)作业人员:轮对动平衡试验人员1名作业时间:20~60分钟/条工装工具: 1. 动平衡试验台;2. 标准试块(80g砝码);3. 驱动压板、紧固螺栓、内六角扳手、活动扳手。
作业材料: 1. 棉纱、纱布;2. 粉笔。
参考资料:1. 《铁路客车轮对和滚动轴承轴箱组装及检修规则》铁运〔2013〕191号2. 《MTJ9761B(3)轮对数控动平衡自动去重机床资料》. S.761.1-1安全防护及注意事项:1. 警告——去重加工时必须佩戴护目镜,防止铁屑飞溅入眼睛;2. 警告——工作时必须穿防砸皮鞋,防止车轮碾伤。
基本技术要求:1. 效验试验台时,样板轮对左端(有轴号端)应朝向试验台左侧;2. 驱动压板安装时,基准点须与样板轮对的0°位置对齐;563. 动平衡试验合格标准参见[表1];4. 去重后清除的轮辋厚度不得超过4mm,长度不得超过半圆,每次进刀量不得超过2.5mm。
加工表面交接处须圆滑过渡,该处不作为轮辋厚度的测量点。
作业环境与作业位置:轮轴间质检组必查抽检项目:必查:动平衡车床日常性能校验抽检:动平衡测试及去重记录驱动压板衡试验台左侧。
基准点图2 驱动压板及其基准点0°相位图3 样板轮0°相位一致80g标准试块45°相位图4 将标准试块拧入样板轮驱动压板图5 安装驱动压板及擦拭轴颈对轴颈尺寸不符合图纸要求的轮对不活动导轨伸图6 活动导轨伸出托架上升活动导轨缩图7 活动导轨收缩托架下降轮对落入轴瓦图8 将轮对推入试验台限位机构压紧可调轴向限位机构图9 调整轴向限位机构与轴端接触序号作业项目工具及材料作业程序及标准作业图示的键块插入轮对驱动压板键槽[图13];设备安全风险点:危险——试验台零件因润滑不良烧坏。
动平衡机作业指导书-版本IRF-01
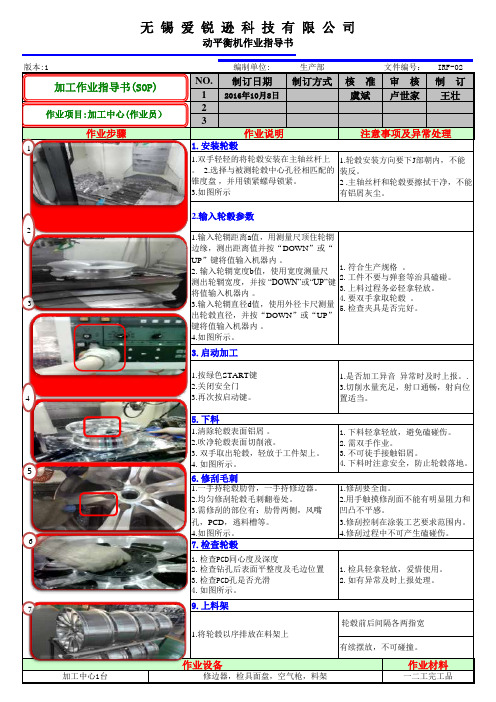
编制单位:生产部文件编号: IRF-02NO.制订日期制订方式核 准审 核制 订12016年10月8日虞斌卢世家王壮23照片样本 1.轮毂安装方向要下J 部朝内,不能装反。
2 .主轴丝杆和轮毂要擦拭干净,不能有铝屑灰尘。
1.双手轻轻的将轮毂安装在主轴丝杆上。
2.选择与被测轮毂中心孔径相匹配的锥度盘 ,并用锁紧螺母锁紧。
3.如图所示1.输入轮辋距离a 值,用测量尺顶住轮辋边缘,测出距离值并按“DOWN ”或“UP ”键将值输入机器内 。
2. 输入轮辋宽度b 值,使用宽度测量尺测出轮辋宽度,并按 “DOWN”或“UP”键将值输入机器内 。
3.输入轮辋直径d 值,使用外径卡尺测量出轮毂直径,并按“DOWN ”或“UP ”键将值输入机器内 。
4.如图所示。
1.清除轮毂表面铝屑 。
2.吹净轮毂表面切削液。
3. 双手取出轮毂,轻放于工件架上。
4. 如图所示。
1.下料轻拿轻放,避免磕碰伤。
2.需双手作业。
3.不可徒手接触铝屑。
4.下料时注意安全,防止轮毂落地。
1.一手持轮毂肋骨,一手持修边器。
2.均匀修刮轮毂毛刺翻卷处。
3.需修刮的部位有:肋骨两侧,风嘴孔,PCD ,逃料槽等。
4.如图所示。
1.修刮要全面。
2.用手触摸修刮面不能有明显阻力和凹凸不平感。
3.修刮控制在涂装工艺要求范围内。
4.修刮过程中不可产生磕碰伤。
1.符合生产规格 。
2.工件不要与弹套等治具磕碰。
3.上料过程务必轻拿轻放。
4.要双手拿取轮毂 。
5.检查夹具是否完好。
5.下料1.安装轮毂3.启动加工无 锡 爱 锐 逊 科 技 有 限 公 司动平衡机作业指导书加工作业指导书(SOP)作业项目:加工中心(作业员)作业步骤作业说明注意事项及异常处理2.输入轮毂参数6.修刮毛刺1.按绿色START 键2.关闭安全门3.再次按启动键。
1.是否加工异音 异常时及时上报。
.3.切削水量充足,射口通畅,射向位置适当。
1.检查PCD同心度及深度2.检查钻孔后表面平整度及毛边位置3.检查PCD孔是否光滑4.如图所示。
- 1、下载文档前请自行甄别文档内容的完整性,平台不提供额外的编辑、内容补充、找答案等附加服务。
- 2、"仅部分预览"的文档,不可在线预览部分如存在完整性等问题,可反馈申请退款(可完整预览的文档不适用该条件!)。
- 3、如文档侵犯您的权益,请联系客服反馈,我们会尽快为您处理(人工客服工作时间:9:00-18:30)。
2 2. 性 能 校 动去重机床、 证至少每周开展一次校验。
验
动平衡样板轮
对
2.2 在样板轮车轴轴身上(对准速度传感器位
置)装上速度测试模块,速度模块需对准速度
传感器正上方,然后将轮对推入。[图 2]
图 2 安装速度模块
序号 作业项目 工装及材料
3
轮对动平衡试验作业指导书
作业程序和标准
作业图示
2.3 启动设备电源按钮,将操作按钮置“手动”
对 轴瓦上的防护罩取下。[图 1]
1.3 将样板轮轴颈擦拭干净,应无油污、锈蚀 和异物。
图 1 轮对动平衡自动去重机床
序号 作业项目 工装及材料
2
轮对动平衡试验作业指导书
作业程序和标准
作业图示
2.1 动平衡试验台性能校验每次开工均需进行
校验,由工作者、工长、质检员、验收员共同
轮 对 动 平 衡 自 对该设备进行性能校验。长时间不使用时须保
当测试界面出现测试结果后,按“K3”按钮,
将轮对转动刹车。[图 10]
3.4 合格轮对动平衡测试值满足:25K 型客车
轮对动平衡测试值不大于 75g.m, RD3A1 型客
车轮对动平衡测试值不大于 50g.m 。
作业图示
图 10 设备操作面板
序号 作业项目 工装及材料
10
轮对动平衡试验作业指导书
作业程序和标准
序号 作业项目 工装及材料
13
轮对动平衡试验作业指导书
作业程序和标准
作业图示
3.8 轮 对 动 平 衡 测 试 合 格 后 , 按 键 盘 上 的 “F10”键, 输入轮对轴号后按“ESC”键,选择“打印记 录”选项,设备自动将试验记录打印出来。[图 3 动平衡测 轮 对 动 平 衡 自 13] [图 14] 试、铣削 动去重机床 3.9 按操作台上的“K1”按钮,操作键盘上的 “↑”、“↓”,依次选择“轴瓦供油”、“主轴 后退”、“托工件平台上升”、“上料”、“托工件 平台下降”选项进行操作,将轮对推出,并用 止轮器将轮对止住做好防护。
转动,按“K2”按钮,系统开始进行动平衡的
测试,当测试界面出现测试结果后,按“K3”
按钮,进行轮对转动刹车。[图 4]
图 4 试验轮对轴端已连接好状态
序号 作业项目 工装及材料
5
轮对动平衡试验作业指导书
作业程序和标准
作业图示
2.6 按照上述 2.5 操作对样板轮对手动进行动
平衡测试,测试其动不平衡量,连续测量三次,
的测试界面。[图 3]
a)
b) 图 3 动平衡试验操作界面
序号 作业项目 工装及材料
4
轮对动平衡试验作业指导书
作业程序和标准
作业图示
2.5 按操作台上的“K3”按钮,将样板轮定位
好后按“K4”按钮,试验台的连接装置自动伸
出进入轴端螺栓孔将轮对连接好,然后按“K5”
按钮,轮对开始匀速转动,当轮对转动几分钟 轮对动平衡自 2 性能校验 动去重机床、 后轮对转速达 250 转/分时,按“K6”按钮, 动平衡样板轮 轴端连接装置自动退出,轮对此时在自由状态 对
3 测试、铣 轮 对 动 平 衡 自 [图 8] 动去重机床
削
3.2 操作键盘上的“↑”、“↓”键,依次选择
“轴瓦回油”、“托工件平台上升”“托工件平
台下降”“轴瓦供油”选项进行操作,并确认
全部动作良好。[图 9]
图 8 安装速度模块 图 9 检查轴瓦供油良好
9
轮对动平衡试验作业指导书
序号 作业项目 工装及材料
轮对及轴箱装置作业指导书
类别:A2 级检修 系统:轮对及轴箱装置
部件:轮对
轮对动平衡试验作业指导书
适用车型:25K、19K、25T
作业人员:镟轮工 1 名
作业时间:20-40 分钟/条
工装工具: 轮对动平衡自动去重机床、动平衡样板轮对
材料:护目镜、擦机布、签字笔、A4打印纸、轴颈橡胶防护套
作业场所:轮对检修流水线 环境要求:室内地面清洁,无油泥、杂物,通风良好。 操作规程:
并将测量值Ⅰ、Ⅱ、Ⅲ填入《动平衡试验台校
验记录》。轮对动平衡性能校验标准:三次测
轮 对 动 平 衡 自 得的动不平衡量与样板轮标准动不平衡量最
2 性能校验 动去重机床、 大差不得超过 30g。如不符合规定需对试验台 动平衡样板轮
对
进行检查检修。[图 5]
2.7 轮对试验时转速不得小于 235 转/分。
对 1个A3修或5年。[图7]
图 7 动平衡试验校验记录
序号 作业项目 工装及材料
8
轮对动平衡试验作业指导书
作业程序和标准
作业图示
3.1 动平衡试验轮对进入测试工序前,将轴颈
滚动面及支撑面擦试干净,轴颈应无油污、锈
蚀和杂物。并在轴身上适当位置(对应速度传
3. 动 平 衡
感器的位置)安装速度测试模块,将轮对推入。
劳动防护用品穿戴整齐;动平 衡试验台状态良好;校验轮对
状态良好
三次测得的动不平衡量与样板 轮标准动不平衡量最大差不得
超过30g
25K型客车轮对动平衡测试值 不大于75g.m,19K型客车轮对 动平衡测试值不大于50g.m
打印相关记录并保存
第5步:完工清理
关闭电源、风源,清理工作场地
工完料尽场地清,确保关闭设 备电源、风源
作业程序和标准
3.3 选择“动平衡测量”选项后回车,进入动
平衡的测试界面。按操作台上的“K3”按钮,
将轮对定位好后按“K4”按钮,试验台的连接
装置自动伸出进入轴端螺栓孔将轮对连接固
定好,然后按“K5”按钮,轮对开始匀速转动,
当轮对转动几分钟后,按“K6”按钮,轴端连
3 动平衡测 轮 对 动 平 衡 自 接装置自动退出,轮对此时在自由状态转动, 试、铣削 动去重机床 按“K2”按钮,系统开始进行动平衡的测试,
作业指导书
轮对动平衡试验
轮对动平衡试验岗位作业要领
作业流程
第1步:工前准备
第2步:性能校验 第3步:动平衡测
试、铣削 第4步:打印记录
作业要点
劳动防护用品穿戴整齐;动平衡试 验台状态良好;校验轮对状态良好
连续三次测量样板轮对的动不平衡 值
按照操作程序进行动平衡测试和铣 削
打印相关记录并保存
重要质量标准
2 性能校验 动去重机床、 后退”、“托工件平台上升”、“上料”、“托工件 动平衡样板轮
对
平台下降”选项进行操作,将样板轮对推出,
并用止轮器将轮对止住防止滚动。[图 6]
图 6 设备操作界面
序号 作业项目 工装及材料
7
轮对动平衡试验作业指导书
作业程序和标准
作业图示
2.3 将三次测试结果填写在《动平衡试验台校 轮对动平衡自 2 性能校验 动去重机床、 验记录》,校验记录完整整齐,不错不漏,工 动平衡样板轮 作者、工长、质检员、验收员签章完备,保存
安全风险提示 1. 车轮车削时,工作者必须戴护目镜,防止铁屑溅入眼睛; 2. 工作者工作时必须穿戴防砸皮鞋,防止车轮碾伤或铁屑扎伤;
目次
1.工前准备 ..................................................... 1 2.性能校验 ..................................................... 2 3.动平衡测试、铣削 .............................................8 4.打印动平衡试验记录 ..........................................14 5.完工清理 .................................................... 15
参考资料: 1.《中国铁路总公司铁路客车轮轴组装检修及管理规则》[铁总运〔2013〕191号]
安全防护及注意事项: 1. 警告——车轮铣削时,工作者必须戴护目镜,防止铁屑溅入眼睛; 2. 警告——工作者工作时必须穿戴防砸皮鞋,防止车轮碾伤或铁屑扎伤; 基本技术要求: 1.轮对试验时转速不得小于 235 转/分。 2.性能校验标准:三次测得的动不平衡量与样板轮标准动不平衡量最大差不得超过 30g。 3.25K 型客车轮对动平衡测试值不大于 75g.m, RD3A1 型客车轮对动平衡测试值不大于 50g.m 。
风险卡控措施:设备运转时操作者必须在 场监控,如有突发故障应立即按下 K7(紧急刹 车键)。
图 5 动平衡试验台校验记录
序号 作业项目 工装及材料
6
轮对动平衡试验作业指导书
作业程序和标准
作业图示
2.8 按操作台上的“K1”按钮,操作键盘上的
轮 对 动 平 衡 自 “↑”、“↓”,依次选择“轴瓦供油”、“主轴
记录
纸
存,保存1个A3修周期。
序号 作业项目 工装及材料
15
轮对动平衡试验作业指导书
作业程序和标准
5. 完 工 清 5
理
擦机布
5.1 按照设备操作规程关闭设备。 5.2 切断控制柜各对应设备电源。 5.3 清理现场,工具摆放整齐,工作场地整洁, 无污垢、水渍。 5.4 擦拭设备,设备内外壁洁净无油污、灰垢。
作业图示
3.6 动平衡试验超限时,按操作台上的“K1” 按钮,设备进入手动切削界面,操作者根据微 机提示,在键盘上按“F1”,动平衡切削刀具 移动到轮辋内侧切削点,操作者根据左右轮饼 的动不平衡量,根据界面提示按键盘上的“F5” 3 动平衡测 轮 对 动 平 衡 自 或“F9”,设备自动进行轮对左右轮饼切削, 试、铣削 动去重机床 该设备将对轮辋内侧进行切削校正,切削完 毕,按键盘上“ESC”,依次选择“铣刀后退”、 “铣刀上升”、“托轮下降”、“离合器开合”等 选项进行操作,按照上述 3.5 项操作程序进行 重新测试,直至合格。[图 11] [图 12]