合成氨原料气净化工艺比较
合成氨几种原料气的净化工艺浅析

合成氨几种原料气的净化工艺浅析摘要简述了铜洗、联醇、双甲、醇烃化等几种原料气净化的方法及其特点。
关键词合成氨原料气净化合成氨原料气的净化是生产中至关重要的工序,原料气微量(C0+C02)超高将导致氨合成催化剂中毒而无法运行,目前我国以煤为原料固定层气化的大多数中小氮肥厂采用铜洗法脱除微量(C0+C02)。
传统的铜洗法是一种较为落后的净化工艺,存在着设备多、工艺复杂、操作麻烦而物耗高,又是生产中的主要环境污染源等缺点。
随着耐硫低温变换催化剂的开发和精脱硫技术的发展,近期中小氮肥厂在原料气净化中相继出现各级压力的联产甲醇、甲烷化、双甲和醇烃化工艺替代铜洗净化,这些原料气净化工艺正逐渐完善和成熟,比传统铜洗法具有明显优势。
1 铜洗净化工艺的不足传统的铜洗净化工艺已在中小氮肥厂应用了几十年,现仍然继续在大多数厂中运行。
尽管铜洗净化在各厂运行效果不一,但普遍存在着许多不足。
1.1铜洗是合成氨生产事故的易发工序由于铜洗工艺流程长,设备多,铜液组分受各种因素的影响,各厂铜洗生产都出现过大小不同的事故。
许多厂都出现过微量(CO+CO2) 超高、铜塔带液、设备填料堵塞、铜液成分波动、铜比难调等问题,是事故易发工序。
1.2 铜洗法净化物耗高铜洗在气体净化过程中,铜液要补充氨、铜和酸,铜液在低温下吸收脱除微量而在高温下解吸再生,既消牦热量又消耗冷量(蒸汽和电),铜液在净化过程吸收了(CO+CO2),同时亦溶解了H2有效气体,即使设置了再生回收,仍然存在着气体的损失。
铜洗运行成本各厂水平不一物耗有所差异,但一般不低于50元/tNH3,甚至高达100元/tNH3以上。
1.3 铜洗是生产现场环境较差,污染多的工序铜洗现场的跑冒滴漏是管理难点。
铜液渗漏和再生气排放污染水体和大气,不利企业环保工作的提高。
2 联产甲醇减轻了铜洗净化的生产负荷目前已有相当多的中小氮肥厂于铜洗前增加了联产甲醇工艺,联醇生产不仅增加了企业化工产品,更为重要的是减轻了铜洗净化的负荷,变换和脱碳的生产亦相对变得宽松,其综合效益是明显的。
合成氨工艺原理
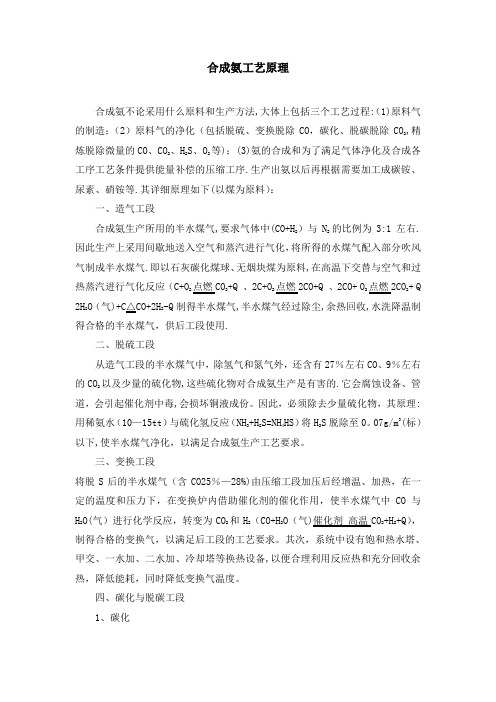
合成氨工艺原理合成氨不论采用什么原料和生产方法,大体上包括三个工艺过程:(1)原料气的制造;(2)原料气的净化(包括脱硫、变换脱除CO,碳化、脱碳脱除CO2,精炼脱除微量的CO、CO2、H2S、O2等);(3)氨的合成和为了满足气体净化及合成各工序工艺条件提供能量补偿的压缩工序.生产出氨以后再根据需要加工成碳铵、尿素、硝铵等.其详细原理如下(以煤为原料):一、造气工段合成氨生产所用的半水煤气,要求气体中(CO+H2)与N2的比例为3:1左右.因此生产上采用间歇地送入空气和蒸汽进行气化,将所得的水煤气配入部分吹风气制成半水煤气.即以石灰碳化煤球、无烟块煤为原料,在高温下交替与空气和过热蒸汽进行气化反应(C+O点燃CO2+Q 、2C+O点燃2CO+Q 、2CO+ O点燃2CO2+ Q2H2O(气)+C△CO+2H2-Q制得半水煤气,半水煤气经过除尘,余热回收,水洗降温制得合格的半水煤气,供后工段使用.二、脱硫工段从造气工段的半水煤气中,除氢气和氮气外,还含有27%左右CO、9%左右的CO2以及少量的硫化物,这些硫化物对合成氨生产是有害的.它会腐蚀设备、管道,会引起催化剂中毒,会损坏铜液成份。
因此,必须除去少量硫化物,其原理:用稀氨水(10—15tt)与硫化氢反应(NH3+H2S=NH4HS)将H2S脱除至0。
07g/m3(标)以下,使半水煤气净化,以满足合成氨生产工艺要求。
三、变换工段将脱S后的半水煤气(含CO25%—28%)由压缩工段加压后经增温、加热,在一定的温度和压力下,在变换炉内借助催化剂的催化作用,使半水煤气中CO与H 2O(气)进行化学反应,转变为CO2和H2(CO+H2O(气)催化剂高温CO2+H2+Q),制得合格的变换气,以满足后工段的工艺要求。
其次,系统中设有饱和热水塔、甲交、一水加、二水加、冷却塔等换热设备,以便合理利用反应热和充分回收余热,降低能耗,同时降低变换气温度。
四、碳化与脱碳工段1、碳化将变换气中26%左右的CO2用浓氨水与其反应(CO2+ H2O+ NH3=NH4HCO3)生成碳酸氢铵副产品,同时制得合格的原料气.2、脱碳工段用MEDA脱碳溶液将变换气中26%左右的CO2除去,制成合格的原料气,供后工段使用。
合成氨工艺

合成氨工艺————————————————————————————————作者:————————————————————————————————日期:合成氨工艺流程(1)原料气制备将煤和天然气等原料制成含氢和氮的粗原料气。
对于固体原料煤和焦炭,通常采用气化的方法制取合成气;渣油可采用非催化部分氧化的方法获得合成气;对气态烃类和石脑油,工业中利用二段蒸汽转化法制取合成气。
(2)净化对粗原料气进行净化处理,除去氢气和氮气以外的杂质,主要包括变换过程、脱硫脱碳过程以及气体精制过程。
①一氧化碳变换过程在合成氨生产中,各种方法制取的原料气都含有CO,其体积分数一般为12%~40%。
合成氨需要的两种组分是H2和N2,因此需要除去合成气中的CO。
变换反应如下:CO+H2OH→2+CO2 =-41.2kJ/mol 0298HΔ由于CO变换过程是强放热过程,必须分段进行以利于回收反应热,并控制变换段出口残余CO含量。
第一步是高温变换,使大部分CO转变为CO2和H2;第二步是低温变换,将CO含量降至0.3%左右。
因此,CO变换反应既是原料气制造的继续,又是净化的过程,为后续脱碳过程创造条件。
②脱硫脱碳过程各种原料制取的粗原料气,都含有一些硫和碳的氧化物,为了防止合成氨生产过程催化剂的中毒,必须在氨合成工序前加以脱除,以天然气为原料的蒸汽转化法,第一道工序是脱硫,用以保护转化催化剂,以重油和煤为原料的部分氧化法,根据一氧化碳变换是否采用耐硫的催化剂而确定脱硫的位置。
工业脱硫方法种类很多,通常是采用物理或化学吸收的方法,常用的有低温甲醇洗法(Rectisol)、聚乙二醇二甲醚法(Selexol)等。
粗原料气经CO变换以后,变换气中除H2外,还有CO2、CO和CH4等组分,其中以CO2含量最多。
CO2既是氨合成催化剂的毒物,又是制造尿素、碳酸氢铵等氮肥的重要原料。
因此变换气中CO2的脱除必须兼顾这两方面的要求。
一般采用溶液吸收法脱除CO2。
合成氨不同工艺能耗对比

10万吨/年合成氨工艺技术比较工艺技术的选择1、造气工段煤气化工艺过程的发展已有百余年的历史,迄今为止已开发的气化方法不下数百种,按照煤在气化炉的运行和接触方式,可以分为(1)流化床气化、(2)气流床气化、(3)熔融床气化、(4)移动床气化(固定床)·流化床气化技术煤的流化床气化是指气化反应在以气化剂与煤形成的流化床内进行的。
流化床气化炉采用粉碎了的煤作为原料,用氧化剂(氧气或空气)来进行床体流化,其温度保持在1000℃以下,以预防灰熔化后与炉床里的物质发生结聚。
氧化剂的有限流量意味着大多数煤粒不会充分燃烧,而是收缩成碳素粒,被合成气带出气化炉。
这就需要大量的碳素粒循环,或被传送到分离燃烧室中燃烧。
流化床气化技术主要有温克勒(winkler)、高温温克勒(HTW)、U-Gas、恩德炉、灰熔聚等流化床粉煤气化技术。
现我国应用较多的是恩德炉、灰熔聚。
目前在朝鲜和我国共有十多台恩德气化炉在运行中,运行最好的是通辽梅花生物科技有限公司,现有2台发气量20000NM3/h的炉子,2006年11月投产,运行正常。
最关键的问题仍然是煤种,该炉要求煤种为褐煤、长焰煤、弱粘结煤,具体数据为灰熔点1250℃以上;煤活性950℃时大于65%,原则上控制在87%以上;粘结性、F.S.N ≤21/2。
另外内外水要干燥到12%以下,目前为止,恩德炉工艺最适宜的煤种是褐煤。
中科院山西煤化学研究所开发的灰熔聚流化床粉煤气化技术,该技术可用多种煤质作原料,如烟煤、焦炭、焦粉等,使用粉煤在1100℃下气化,固体排渣,无废气排放。
该技术工业示范装置已于2001年在陕西城固氮肥厂建成,小时投煤量4.2吨。
其煤种适应性广,操作温度约为1000~1080℃,反应压力为0.03~0.05MPa(G)。
气化炉是一个单段流化床,结构简单,可在流化床内一次实现煤的破粘、脱挥发份、气化、灰团聚及分离、焦油及酚类的裂解。
带出细粉经除尘系统捕集后返回气化炉,再次参加反应,有利于碳利用率的进一步提高。
合成氨原料气的精制

一 、 甲烷化法流程
甲烷化的流程主要有两种类型,即外加热与自热型。
一般流程如下:先用甲烷化反应后出口气体来换热使进 口温度上升,余下的温差再用一氧化碳变换工序来的热气体 或电加热器加热到催化反应所需要的入口气体温度。
脱碳气 脱碳气气水分离器
甲烷化换热器
来自变换气
脱碳气加热器
甲烷化气 甲烷化气水分离器
2、认真操作,做到勤观察、勤调节、优化运行,监控入 口净化气中(CO+ CO2)%的变化情况及脱碳岗位是否有带液 情况,保证甲烷化炉气中(CO+ CO2)%≤10PPm。
3、严密监控系统阻力变化情况。 4、仔细检查合成气分离器的排放情况。
由金属壳体或钢架各种配件组合的炉体结构,要求能承受相当 高的温度、各种介质的腐蚀以及承受一定的压力和荷载,由于气 体中氢分压较大,且气温较高,使氢腐蚀较严重,因此甲烷化炉 采用低合金钢制作。炉内催化剂一般不分层,也可分两层装填。 催化剂层的最低高度与直径之比一般为1:1。催化剂层和气体进 出口都设有热电偶,以测定炉温。
3.原料气成分
C
原料气中水蒸汽含量增加,对甲烷
化反应是不利的,并对催化剂的活性
有一定的影响,所以原料气中水蒸汽
含量越少越好。一般要求小于0.7%。
五、甲烷化法生产操作要点及异常现象处理
(一)装置原始开车及操作
A
1、开车前的准备工作: (1)各相关阀门检查完毕,开启灵活; (2)各相关管道已进行检查,无泄漏、无积水; (3)CO、CO2微量分析仪、温度、压力、流量等 监测、控制仪表安装完毕,调试合格。
升温期间由升温加热炉的燃烧烟气通过气/气换热 器提供的热量加热升温介质。
(1)氮、氢气升温 (2)净化气升温 (3)催化剂升温还原
第二组 合成氨原料气净化原理方法

原料气的精制
经CO变换和CO2的脱除后,原料气中含有少量的CO 、CO因此在原料 气送往合成之前,需要进一步净化。
常用方法:甲烷法、液氮洗涤法
甲烷法:可将碳的氧化物(co+co2)降低至10cm3/m3 CO+3H2 CH4+H2O
CO2+4H2
CH4+2H2O
条件:较低温度下进行,要求催化剂有很高活性,采用镍作为 催化剂。
合成氨原料气净化方法
指导老师:刘秀琼
小组成员:陈涛
蔺兴莲 方利 钟宇健 李川
净化
指除去原料气中氢气、氮气以外的杂质。
1、原料气的脱硫、
2、 一氧化碳的变换、 3、二氧化碳的脱除、 4、原料气的精炼等。
摘自:
工艺流程:原料气的脱硫
一氧化碳的变换
脱碳
精制
干法脱硫:活性炭法、氧化铁法、氧化锌法、钴钼加氢法。
20~35MPa时总能量消耗较低。
3、温度:氨合成反应必须在催化剂的存在下才能进行,而催化剂必须在一定的 温度范围内才具有催化活性,所以氨合成反应温度必须维持在催化剂的
活性温度范围内。
4、空间速度:当空速增加时,氨合成的生产强度有所提高,氨产量有所增加。 一般中压法合成氨,空速在20000~40000h-1之间。
缺点:该法消耗氢,同时生成甲烷,只有当原料气中(co+co2) 的含量<0.7%时 采用甲烷法。
优点:工艺简单,操作方便,费用低。
工艺条件的控制
1、催化剂:催化剂长期使用活性下降,氨合成率降低,(衰老),也就是催化 剂长期慢性中毒,因此必须将毒物脱除保持其良好的活性。 2、压力:提高压力,对氨合成反应的平衡和反应速率都是有利的,操作压力在
3学习情境三合成氨原料气的净化

学习情境三合成氨工作任务合成氨原料气的脱硫授课地点多媒体教室3-8教学方法讲授法课时 4任务描述及任务目标掌握干法脱硫、氨水催化法脱硫及两生过程的基本原理、主要设备和工艺条件的选择包含章节第三章第三节主要教具、设备、工具多媒体学习重点及难点脱硫方法的选择与对比碱法脱硫的原理及工艺指标的确定学生学习基础已具有无机化学,化工单元操作,物理化学,化工热力学等的学习基础,具有一定的自学能力,接受知识的能力也较强.知识点:第一节原料气的脱硫脱硫方法很多,主要可分为干法脱硫和湿法脱硫。
干法脱硫一般适用于含S量较少的情况。
湿法脱硫一般适用于含S量较大的场合。
一、干法脱硫(一)钴-钼加氢法钴钼加氢法还可将烯烃加氢转变成饱和烷烃,从而减少蒸汽转化工序析碳的可能。
钴钼加氢催化剂以氧化铝为载体,由氧化钴和氧化钼组成。
经硫化后活性组分为MoS2,Co9S8也是活性成份。
主要反应如下:RCH2SH+H2=RCH3 + H2SRCH2-S-CH2R´+2H2=RCH3 + R´CH3 +H2SRCH2S-SCH2R´+3H2=RCH3 + R´CH3 +2H2S操作温度一般在300 ~ 400°C,压力由不同催化剂而定,加氢量一般按照保持反应后气体中有5~10%氢为准。
(二)氧化锌法氧化锌脱除有机硫的能力很强,可使出口硫含量<0.1ppm,当原料气硫含量<50×10-6时,仅用它一步脱硫就行了。
若硫含量较高,可先用湿法,再用此法。
其基本原理如下:ZnO(s)+H2S(g)=ZnS(s)+H2O(g)ZnO(s)+C2H5SH(g)=ZnS(s)+C2H5OH(g)氧化锌脱硫的反应速度主要是内扩散控制,所以氧化锌脱硫剂都做成高孔率的小颗粒。
氧化锌脱硫性能的好坏用硫容量表示。
所谓硫容就是每单位质量氧化锌能脱除S的量。
氧化锌脱硫性能的好坏用硫容量表示。
所谓硫容就是每单位质量氧化锌能脱除S的量二、湿法脱硫湿法脱硫可分为化学吸收法、物理吸收法和化学物理综合吸收法等。
合成氨原料气醇烃化净化精制新工艺

合成氨原料气醇烃化净化精制新工艺1. 醇烃化工艺开发简况合成氨原料气醇烃化净化精制工艺,即在用甲醇化、烃化(或甲烷化)反应的方法来净化精制合成氨原料气,使合成氨原料气进入氨合成工段之前的气体中CO、CO2(俗称气体中的“微量”指标)总量小于10ppm。
此工艺还可联产甲醇,用此工艺取代传统的“醋酸铜氨液洗涤法(俗称铜洗法)”的净化精制合成氨原料气的方法。
工艺简称醇烃化工艺(或双甲工艺)。
合成氨原料气醇烃化净化工艺是双甲工艺的升级技术,双甲工艺是湖南安淳高新技术有限公司开发成功的技术,该技术于上世纪1990年提出,1991年进行工业化实施,1992年9月第一套工业化装置在湖南衡阳市氮肥厂投产成功,国际上属于首先提出,最先进行工业化生产。
1993年4月获国家发明专利权,相继又申请了可调节氨醇比的醇烃化工艺专利,美、英等权威化学文摘均作了报道。
1994年元月通过化工部科技鉴定,1994年6月国家科委将该项目列入《国家重大科技成果推广计划》项目。
第一套装置至今已正常运行13年,目前净化精制能力达到了总氨8万吨/年,副产1万吨甲醇/年,取得了很好的效益。
目前,推广的工艺最大处理合成氨能力为40万吨,在全国中、小合成氨厂推广达15家,目前正在进行工程设计的有5家。
湖南郴州桥口氮肥厂的双甲工艺工程被评为国家优秀创新工程,双甲工艺技术于2000年被授予湖南省科技进步一等奖。
双甲工艺评为1995年度原化学工业部十二大重大科技成果之一,给予重点推广。
2003年醇烃化工艺获得国家科技进步二等奖。
此工艺开发和发展可分为三个阶段,历时十多年的开发创新和竭力推广,有着超乎寻常的辛劳可谓十年磨一剑。
技术发展的第一阶段——确认了国产的甲烷化催化剂在高压条件下的运行条件。
技术发展之初,当有双甲净化这个工艺创意时,当时国内的很多厂家已经有了联醇工段,一般为联醇后再串铜洗工段进行净化精制方法,由于联醇出口的CO和CO2的指标与传统的甲烷化进口的气体成份指标不一样,且压力等级也不一样,要将铜洗去掉用甲烷化来替代必须首先解决进甲烷化炉的进口气体的气体成份问题——一定要使醇后气中的CO+CO2总量不超过0.7%,且较低为好。
- 1、下载文档前请自行甄别文档内容的完整性,平台不提供额外的编辑、内容补充、找答案等附加服务。
- 2、"仅部分预览"的文档,不可在线预览部分如存在完整性等问题,可反馈申请退款(可完整预览的文档不适用该条件!)。
- 3、如文档侵犯您的权益,请联系客服反馈,我们会尽快为您处理(人工客服工作时间:9:00-18:30)。
Cu( NH 3 ) 2 AC + CO+ NH3
Cu( NH 3 ) 3ACCO + Q
2NH 4 OH + CO2
(NH4 ) 2 CO3 + H 2 O+ Q
# 56#
云南化工
2008年第 5期
双甲工艺尽管将进甲烷化的一氧化碳降到了 0. 1% ~ 0. 3% , 到了甲烷化还是要消耗氢, 而且一 个一氧化碳耗三个氢, 一个二氧化碳耗四个氢, 消 耗了氢, 变成了无用的甲烷, 进 入到合成新鲜气 中, 放空量增加, 这是甲烷化普遍存在的问题。既 然消耗氢, 就把 CO 和 CO2 降得很低, 如 0. 01% ~ 0. 02% , 这就 带来了 另外一 个问 题, 因 为 CO 和 CO2 甲烷化反应时反应热很小, 1% 的一氧化碳反 应温度只增加 70e 左右, 散热损失多, 就要开电 炉, 从而增加了电耗 [ 2 ] 。
K ey word s: raw m aterial gases pur ificat ion; copper wash; m ethane- m ethanol technology; alcohol hydrocarbyla2 t ion; isop ies tic alcohol alky lation
化催化剂, 使 CO+ CO2 与 H 2 反应生成低碳烃化 物、ห้องสมุดไป่ตู้碳醇化物, 低碳烃化物、低碳醇化物在水冷
温度 下可冷凝为液相, 与气 体分离, 烃化后气体 CO + CO2 可控制在 10 mL /m3 左右 [ 1 ] 。烃化反应
式为:
( 2n+ 1)H2 + nCO CnH ( 2n+ 2) + nH2O 2nH2 + nCO CnH 2 n + nH2 O 2nH2 + nCO CnH ( 2n+ 1)OH + ( n- 1)H2O ( 3n+ 1)H2 + nCO2 CnH ( 2n+ 2) + 2nH2O 图 3为典型的醇烃化工艺流程图。
收稿日期: 2008208222
稿件修回日期: 2008209211
作者简介: 代现跃 ( 19792) , 男, 助理工程师, 从事化工工艺工作。
2008年第 5期
代现跃等: 合成氨原料气净化工艺比较
# 55#
2 低压甲烷化法
原料气甲烷化净化, 这是气相中 CO + CO2 在 催化剂作用下与 H2 反应转化为 CH 4 而得以净化, 是早期氮肥生产的一种传统气体净化工艺。
2. 1 甲烷化净化原理及工艺流程
甲烷化反应是一种强放热反应:
CO + 3H 2 CO2 + 4H 2
CH4 + H2 O + Q CH4 + 2H2 O + Q
典型的甲烷化工艺流程见下图 1。
图 1 甲烷化工艺流程图 F igur e 1. Pro cess cha rt of m eth anat ion
4. 2 醇烃化净化工艺特点 / 醇烃化工艺 0中烃化流程与 / 双甲工艺 0中
甲烷化流程基本类似, 烃化较甲烷化在工业生产 中具有如下优点: ¹脱除 CO + CO2 的量低 且稳 定, 并能较大幅度地提高联产甲醇的产量; º烃化 生产烃类物质, 高压常温下冷凝分离; »烃化操作 温度较甲烷化低 60~ 80e , 烃化反应床层更易维 持自热操作; ¼烃化催化剂活性温区宽, 不易烧 结、老化, 使用寿命长; ½烃化催化剂价格便宜; ¾
甲醇在烃化塔内无逆反应发生 [ 3] 。
5 全自热非等压醇烷化净化工艺法
全自热非等压醇烷化合成氨原料气净化新工 艺由南京国昌化工科技有限公司开发, 并在山东 肥城化肥厂装置上获应用, 该工艺比原铜洗工艺 降低吨氨成本 90元 [ 4] 。
5. 1 非等压醇烷化工艺原理及工艺流程 全自热非等压醇烷化净化是由中压醇化、高压
在合成氨工业中, 经变换和脱碳工艺处理, 合成 氨原料气中仍含有对氨合成催化剂有毒的 CO和 CO2 气体, 必须进一步处理将其降低至 10mL /m3 左右, 以 保护氨合成催化剂。目前合成氨厂脱除微量 CO、CO2 的工艺方法较多, 主要有醋酸铜氨液洗涤法 (铜洗 法 )、低压甲烷化法、甲醇甲烷化法 (双甲工艺 )、醇烃 化工艺、非等压醇烷化净化工艺等。
5. 2 非等压醇烷化净化工艺特点 非等压醇烷化净化工艺特点是中压联醇可大
幅度调节醇氨比、能耗较低; 高压甲醇 CO、CO2 转 化率高, 净化度能够保证。
图 3 醇烃化工艺流程图 Figur e 3. Process char t of a lcoh ol h yd rocarby la tion
醇烃化工艺灵活性强, 原料气中一氧化碳含 量范围较宽, 最高达 8% , 最低可至 1% , 既能产粗 甲醇, 又可产醚含量很高的醇 醚混合物 (只改变 触媒种类 )。
4 醇烃化净化工艺法
针对双甲工艺存在的一些问题, 湖南安淳公司 把双甲工艺做了改进, 即升级成为醇烃化精制工艺。
4. 1 醇烃化工艺原理及工艺流程 醇烃化工艺就 是醇醚化、醇烃 化精制工 艺。
第一步将双甲工艺中甲醇化催化剂更换成醇醚复 合催化剂, 使 CO+ CO2 与 H2反应生成甲醇, 并随
即水解为二甲醚, 其反应式为:
CH 4 + 2H2 O
典型的甲醇甲烷化工艺流程图如图 2。
图 2 双甲工艺流程图 Figur e 2. P rocess char t of m eth an e- m eth ano l t echn ology
3. 2 甲醇甲烷化净化工艺特点和不足 甲醇甲烷净化工艺法与传统工艺法相比, 这
种新工艺更具吸引力。该工艺由两部分组成, 在 甲醇合成之后再是传统的甲烷化工艺工序, 净化 过程中把一氧化碳、二氧化碳变成了有用产品甲 醇, 同时双甲工艺比引进国外的深度低变甲烷化 优越。深度低变 甲烷要求变换的 一氧化碳降到 0. 3% , 双甲 工艺 不要求 降到 这么 低, 只要 降到 1% ~ 6% 就可以。双甲净化工艺操作工艺范围 弹性 比较大, 氨醇比调节大, 压力调节范围也很 宽, 此净化工艺法具有生产稳定、操作简单, 适应 性强、生产弹性大、经济效益好, 投资少、建设期短 等一些特点 [ 1] 。
DA I X ian2yue, L IU L i
( Zhej iang Jin ju C hem ical Co. Ltd. , Qu zhou 324004 )
Ab st ract: Prin cip le and characteristic on the purification process of raw material gases for the syn th es is of amm on ia was introduced, and d ifferent pu rification p rocess were com pared.
CO + 2H 2
CH 3 OH
CO2 + 3H2
CH3 OH + H 2 O
2CH3 OH
( CH3 ) 2 O + H2 O
2CO + 4H2
( CH 3 ) 2 O + H2 O
此过程称醇醚化, 醇醚化副产物是醇醚混合
物, 醇醚化后 CO+ CO2控制在 0. 2% ~ 0. 4% 。
第二步将双甲工艺的甲烷化催化剂更换为烃
2008年 10月 第 35卷第 5期
云南化工 Yunnan Chem ical Technology
Oct. 2008 Vo.l 35, No. 5
合成氨原料气净化工艺比较
代现跃, 刘 丽
(浙江晋巨化工有限公司, 浙江 衢州 324004)
摘 要: 主要简述了铜洗、双甲、醇烃 化、非等压 醇烷化等 几种合 成氨原 料气净 化的工 艺原理、方法及 其特 点, 对几种净化工艺进行了对比分析。
1 铜洗法
醋酸铜氨液洗涤法 (简称铜洗 )是最古老的方 法, 早在 1913年就开始应用。铜洗法以其工艺成 熟、操作弹性大, 长期在中小型合成氨厂占据主导 地位, 但国外早在 20世纪 60年代就逐步淘汰这种 落后的工艺 [ 1] 。
1. 1 铜洗法净化工艺原理 合成氨脱碳原料气中含有少 量的一氧化碳、
2. 2 甲烷化净化工艺优点和不足 用甲烷化脱除原料气中的 CO + CO2 可大幅
度简化生产流程, 降低建设和操作费用, 操作也较 平稳, 运行费用不足铜洗的 20% , 占地面积也较 铜洗装置要少。
该法存 在 的不 足 之处, 如反 应 中在 CO 和 CO2 被除去的同时, 消耗掉数倍于 CO 和 CO2 的 H2, 而且甲烷化后甲烷含量 增加, 造成氨 合成放 空量增大, 根据甲烷化反应方程式可知, 进口气中 每增加 0. 1% CO, 相 当 于 多 消 耗 0. 3% H 2 和 0. 1% CO, 即总共消耗 0. 4% ( CO 可转化为 H 2 ), 同时合成气 中增加 0. 1% CH4。经测 算, 如 有 0. 7% 的 CO + CO2 进行甲烷化, 以上二项累计增加 原料气耗约 10% , 足见其耗量之大。甲烷化还要 求变 换中 CO 含 量 < 0. 3% , ( CO + CO2 ) < 0. 7% , 以控制催化剂床层的温度, ( CO + CO2 )含量 指标的要求对以煤为原料固定层气化的中小氮肥 较为苛刻, 所以较难普及 [ 1] 。
2Cu( NH 3 ) 2 AC + 4NH 3 + 2HAC+ 1 /2O2