换热器制造工艺
换热器制造工序过程卡
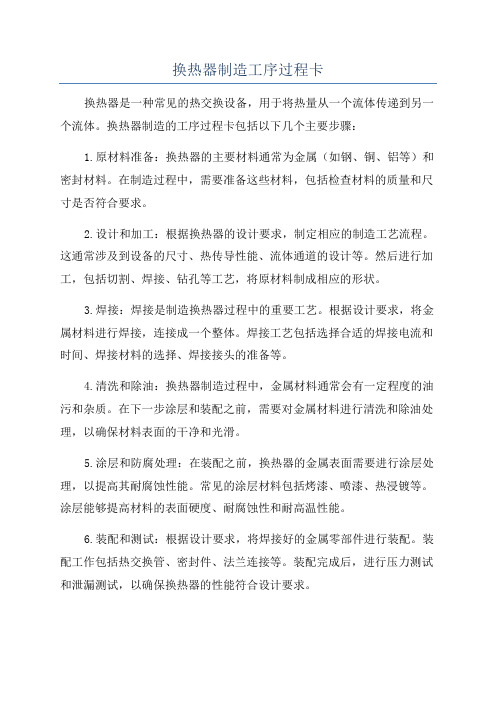
换热器制造工序过程卡换热器是一种常见的热交换设备,用于将热量从一个流体传递到另一个流体。
换热器制造的工序过程卡包括以下几个主要步骤:1.原材料准备:换热器的主要材料通常为金属(如钢、铜、铝等)和密封材料。
在制造过程中,需要准备这些材料,包括检查材料的质量和尺寸是否符合要求。
2.设计和加工:根据换热器的设计要求,制定相应的制造工艺流程。
这通常涉及到设备的尺寸、热传导性能、流体通道的设计等。
然后进行加工,包括切割、焊接、钻孔等工艺,将原材料制成相应的形状。
3.焊接:焊接是制造换热器过程中的重要工艺。
根据设计要求,将金属材料进行焊接,连接成一个整体。
焊接工艺包括选择合适的焊接电流和时间、焊接材料的选择、焊接接头的准备等。
4.清洗和除油:换热器制造过程中,金属材料通常会有一定程度的油污和杂质。
在下一步涂层和装配之前,需要对金属材料进行清洗和除油处理,以确保材料表面的干净和光滑。
5.涂层和防腐处理:在装配之前,换热器的金属表面需要进行涂层处理,以提高其耐腐蚀性能。
常见的涂层材料包括烤漆、喷漆、热浸镀等。
涂层能够提高材料的表面硬度、耐腐蚀性和耐高温性能。
6.装配和测试:根据设计要求,将焊接好的金属零部件进行装配。
装配工作包括热交换管、密封件、法兰连接等。
装配完成后,进行压力测试和泄漏测试,以确保换热器的性能符合设计要求。
7.填充介质:根据客户的需求和设备使用环境,填充合适的介质。
常见的介质包括水、蒸汽、空气等。
填充介质后,进行再次测试,确保介质流动和温度变化符合设计要求。
8.包装和出厂:最后一步是对换热器进行包装和出厂。
根据客户要求,用适当的材料进行包装,以保护换热器的表面。
然后进行最后的检查,确保换热器的外观和性能符合要求,准备发货给客户。
总之,换热器制造的工序过程包括原材料准备、设计和加工、焊接、清洗和除油、涂层和防腐处理、装配和测试、填充介质、包装和出厂等步骤。
每个步骤都需要严格控制和测试,以确保最终制造出的换热器具有良好的质量和性能。
固定管板式换热器制造工艺

2012年05月第13期科技视界Science &Technology Vision随着社会的不断发展,大量的生活小区在不断的进行改造和建设,小区如何取暖就成了一个现实问题。
正是在这种状况下,换热器的开发、生产应允而生。
我公司目前已经成功制造了多个系列的换热器产品,并且使用效果良好。
现就非常普及的一种管板式换热器的制造工艺做一论述,给今后同类型的产品制造提供一定的经验。
固定管板式换热器属压力容器产品,结构形式如图1。
图1换热器基本结构示意图主要由上管帽、下管帽和壳程三大部分组成;每一部分又由许多零部件构成,尤其壳程部分零件数量最多,结构复杂,吨位大,给生产带来很大困难。
如何在工艺上采取有效措施保证壳程制造质量,是生产整个换热器的关键。
壳程是换热器的心脏部分,直径ϕ1800、筒体δ16、材质16MnR。
紫铜换热器(ϕ19×2),数量众多。
壳程上换热器与管板间采用强力焊加贴胀的连接结构形式。
壳程制造完后,要作1.25MPa 水压试验。
其中穿管、胀管、焊管是制造壳程的关键。
为了顺利完成该产品的生产任务,我们在工艺上采取了相应的措施,对各主要零部件的生产环节及壳程组装环节进行了严格控制,取得了较为理想的结果。
下面介绍工艺过程。
1零部件的加工要求该换热器连接部分多,孔的数量很大,加工要求高。
因此,在工艺上对各部件间的加工提出了如下要求。
1.1管板在钻管孔时,要求将上、下管板、折流板按装配位置由上而下(即上管板在上、折流板在中、下管板在下)叠在一起钻孔,便于保证管孔同心度。
在划管孔线时,同时在上管板上划出装配用十字线,打上0°、90°、180°、270°标记,并引至折流板及下管板上。
后续工序不得将标记加工掉。
1.2与管板一起加工完的折流板,三块叠在一起扩钻孔至图纸要求,并划线钻出拉杆孔,便于保证同心度。
(十字线标记在车外圆时移植至端面上)。
1.3上管板与上管帽上的大法兰,下管板与下管帽上的法兰的连接孔应分别配钻成。
翅片管式换热器的制造工艺

2.3 管箱隔板与侧板的焊接
管箱为承压部位 ,其质量取决于隔板与侧板是否焊接牢固 ,因结构无法从管箱内侧焊接 , 为此在两(a)A 侧 (b)B侧侧板上用数控等离子气割机割出宽为 8mm 的承插槽 ,见图 6。 每条承插槽断开120mm,在隔板相应的位置割出凹槽 ,以便隔板扣入侧板上 ,最后满 焊槽孔 。
翅片管热交换器制造工艺及其检漏方法
以方形翅片管式换热器为例
• 结晶箱简介
• 制造工艺及过程控制
结晶箱简介
方形翅片管热交换器的结构示图见图。 壳体由6块方形平板焊接而成 ,2块管板镶嵌于壳体中, 除顶面外,热交换器余几面均布有加热外盘管 。
制造工艺及过程控制
2Hale Waihona Puke 1翅片管制造及检漏2.1.1 制造 采用高频焊将1mm 正方形薄片均匀焊在无缝钢管上 (图 )。翅片管的质量体现在 翅片与管子焊合度 、翅片间距及平整度的三点要求上 。 隔板用剪板机剪成定宽长板 ,在平台上绘出隔板排布图 ,后依照尺寸将其焊为 迷宫状 ,待组装 。
基于方形翅片管热交换器结构的特殊性,对其工艺过程分别设计了合理的试压工装 , 为类似热交换器的制造可提供一定的借鉴 。
End
thanks for watching
2.4 组装及其他
(1)翅片管组装组装时先将一块管板垂直于底板 ,另一块管板稍微倾斜一定的角度 , 两管板间用葫芦拉住 ,由下向上逐层穿入翅片管 ,并逐渐拉紧葫芦直至翅片管全部穿 入。 (2)管箱隔板组装隔板为迷宫型 ,是由很多块长条板组焊而成 ,拼装时应严格校对各 个隔板位置的准确性 ,并做好防变形工作 。 (3)管箱试压步骤新的检漏方法可避免对壳体打压 ,在换热管与管板的焊接接头检验合 格后 ,只需在管箱试压即可保证设备质量达到要求。
管壳式换热器制造工艺

两道冷压和一道热压 水压机,冲头,温度 900-1000
100%射线探伤 立车坡口加工,钻床钻孔
2-20 椭圆封头尺寸
2.筒体 材料为 16MnR,展开的坯料尺寸为 9850X8325X16 (mm),拼接图如图 2-69
所示。它的制造过程列于表 2-19 2-19 筒体的制造过程
液化石油气储罐示意图一储罐主要构件的加工制造板材成型前的通用工艺流程列于表217序号工作内容要求加工方法加工内容或设备原材料复验外观几何尺寸和理化检验及钢板的超声波探伤钢印标记小于5毫米的板材用风刻电刻和不退色的墨水标记边缘加工气割或等离子弧坡口用机加工方法进行边缘加工二主要受压元件的成型和焊接工艺该封头为标准椭圆形封头材料为16mnr
许偏差分别列于表 2-25 和表 2-28。
3. 折流板等
下图为最常用的 20%DN 圆缺高度的弓形折流板,为保证加工精度和效率,常将圆板
坯以 8~10 块为一叠进行钻孔和切削加工外圆,折流板孔的允许偏差列于表 2-26。
4. 管子 换热器的管表面就是传热面积。常用管子外径 10~57 (mm);其长度一般用 2000、 3000、6000(mm)等。管子应作下列试验:以管子数的 5%,且不少于 2 根作拉力、硬度 和扩口等抽样检验;进行水压试验(试验压力为设计压力的(1.5~2)倍,合格者才可使 用。 如采用胀接,管子两端应作软化退火处理,使管端的硬度低于管板硬度;另外,还 应对管端两倍于管板厚度的长范围内进行打磨,打磨后的粗糙度,钢管为
<0.5%DN
<5
<7
壳体内径过大或圆度误差会引起壳程介质短路而降低换热效率。
壳体的直线度误差会影响管束的抽装,对其要求列于表 2-24。
固定管板式换热器制造工艺

将其铣至图纸要求。( 组装时不应调换其钻孔方 向, 以保证折
流板的同心度 , 便于穿管 ) 。
23 换热器 : 尺寸锯管一 检查管子两端 的切 口有无裂纹一 . 按 磨管 , 管端清锈至呈现金属光泽 , 不得将 管子磨扁 , 清锈长度
不小 于管板厚度 的两倍 。
1Mn 6 R。紫铜换热器 ( 1x )数量众多 。壳程上换热器与管  ̄92, b
一
管 帽
中之 12 3 、 、 要求执行。
22 折 流板采用 A . 3钢板拼接而成 , 拼焊后校平 , 三块叠放点
焊 。加 工管孔 时先按 要求 一中第一条进行 , 然后按第二条进
图 1 换 热 器 基 本 结 构 示 意 图
行 。车完外 圆再分别拆开 ( 标记需移植 ) 按各 自的装配位置 ,
板间采用 强力 焊加贴胀的连接结构形 式 。壳程制 造完后 。 要
2 上下 管帽: 据图纸将所 属各零 件整体组 对 , . 4 依 根据 大法
兰上 的十字 线标记处 , 管孔位置线 组焊接 管( 按 法兰 与接 管 已预先组 焊成组件 ) 。对大法兰与封 头之 间焊缝进行 10 0 %磁 粉探 伤 . 合格后加工大法 兰密封面 。 2 筒体根据 图纸要 求作拼料 、接缝 图一 按拼料 图分块 下 . 5
主要 由上 管帽 、 下管 帽和壳 程三 大部分组 成 ; 每一 部分 又 由许多零 部件 构成 , 尤其壳程 部分零 件数量 最多 , 构复 结 杂, 吨位大 , 给生产 带来很大 困难 。如何在工艺上采取有效措 施保证壳程制造质量 , 是生产整个 换热器的关键 。
壳 程 是 换 热 器 的 心 脏 部 分 , 径 610 、 体 8 6 材 质 直 80 简 1、
换热器加工工艺规程(过程装备制造工艺)

紧密面形式 用途或名称
平面
通道积水出口
平面 平面 平面 平面
冷凝用水入口 纯苯蒸汽入口 冷凝用水出口 纯苯凝液出口
E
端盖与密封板连接详图 不按比例
14
拉杆φ16 L=2270
2 Q235-A
13
筒体DN400×6L=2890 2 16MnR
12 R2003-6-4 右管箱
1 组合件
11 R2003-6-3 管板
2 16MnR
10
法兰 DN90
2
20
9
换热管φ25×2.5L=3000 78 Q235-A
8
定距管φ25×2.5L=297 30
20
过程装备制造工艺
西北大学
陕西 西安
以换热器加工为例
讨论 主要零部件有哪些? 加工要求? 安装要求?
×
、、
×
× ×4
第2、4、6块
×
技术要求
本设备按GB150《钢制压力容器》和GB151《钢制管壳式换热器》进 行制造。检验和验收并接受国家质量监督局监督颁发的《压力容器 安全技术监察》规程的监督。 焊接采用电弧焊,低合金钢之间焊条牌号:J507焊条,低合金钢与 碳钢之间,碳钢之间采用J426焊条。 焊接接头型式及尺寸除图注明外,均按HG20583-1998的规定,法兰 焊接按相应法兰的焊接标准的规定进行。 筒体和管板之间的焊接采用弧焊打底,焊底表面进行着色检验。 容器上的A类和B类焊缝应进行X射线探伤检查,探伤长度为20%, X 射线应符合相应的标准规定。 换热管与管板的连接采用焊接法。 设备制造完毕后,应按有关标准进行水压试验。
列管式换热器的典型制造工艺
的圆度 线 度 Dmax-Dmin
•
线
DN
• 要求更<
表 2- 23。
<4.5mm
1格000)。L 且对壳•体的内<
<6mm
差 00 )L 同 一断面上的直径差列于
表2 - 2 3
壳体同一断面上的直径差
壳体内径过大或圆度误差会引起壳程介质短路而降低换热效率 。壳体的直线 度误差会影响管束的抽装 ,对其要求列于表 2-24。
表 2-24 壳体的直线度要求
2. 管板
管板的作用是固定管子的。一般采用 Q235、20等碳素钢和16Mn、15MnV 等低合 金钢制作;可以用锻件或热轧厚钢板作坯料 ,当管板的厚度较大时 ,原则上使用锻 件 , 因为钢板愈厚 ,其轧压比愈小 ,钢板内部缺陷存在的可能性愈大 。 管板是典型的群孔结构 ,单孔质量会影响管板的整体质量 ,所以孔加工方法的选择 至为重要 。群孔加工有下列方法:
2-26。
3. 折流板
下图为最常用的 20%DN 圆缺高度的弓形折流板,为保证加工精度和效率, 常将圆板 坯以 8~10 块为一叠进行钻孔和切削加工外圆 ,折流板孔的允许 偏差列于表 2-26。
4. 管子
换热器的管表面就是传热面积。常用管子外径 10~57 (mm);其长度一 般用 2000 、 3000 、6000(mm)等 。管子应作下列试验: 以管子数的 5% ,且 不少于 2 根作 力 、硬度 和扩口等抽样检验;进行水压试验(试验压力为 设计压力的(1.5 2)倍 ,合格者才可使用。
列管式换热器的典型制造工艺
制作人:Leo
1
目录
一、列管式换热器简介 1、壳体 2 、管板 3 、折流板 4 、管子
二、列管式换热器组装工艺 三、列管式换热器工艺流程
管壳式换热器制造工艺规程
管壳式换热器制造工艺规程1、主题内容与适用范围:本规程规定了本公司管壳式换热器组装制造中的具体工艺要求外,还应执行JB3343《高压加热器技术条件》,JB8184《汽轮机低压加热汽技术条件》,JB7838《热网加热器》等标准中的规定。
2、引用标准:《固定式压力容器安全技术监察规程》——TSG《管壳式换热器》——GB151-2011《固定式压力容器》——GB150-20143、基本要求管壳式换热器主要受压部分的焊接接头分为A、B、C、D、E五类,按下图所示。
a) 壳体圆筒部分的纵向接头、球形接头与圆筒连接的环向接头、各类凸形封头中的所有拼焊接头以及嵌入式接管与壳体对接连接的接头,均属A类焊接接头。
b) 壳体部分的环向接头、锥形封头小端与接管连接的接头、长颈法兰与接管连接的接头,均属B类焊接接头,但已规定为A类的焊接接头除外。
c) 平盖、管板与圆筒非对接连接的接头,法兰与壳体、接管连接的接头,内封头与圆筒的搭接接头,均属C类焊接接头。
d) 接管、人孔、凸缘、补强圈等与壳体连接的接头,均属D类焊接接头,但已规定为A、B类的焊接接头除外。
e)非受压元件吊耳、支座垫板与压力容器连接的焊缝,均属E类焊接接头。
3.1 对不同板厚对接的规定:a) 下列不同板厚必须削薄厚板:当2≤10mm,且1-2>3mm及2>10mm且1-2≥0.3n 或>5mm时,必须削薄厚板:削薄形式分单面削薄和双向削薄。
见图2。
b) 下列不同板厚对接无须削薄:当≤10mm且1-2≤3mm及2>10mm且1-2≤0.32或≤5mm时,无须削薄板厚,且对口错边量b以较薄板厚度为基准确定。
在测量对口错边量时,不应计入两板厚度的差值。
3.2 筒节长度应不小于300mm。
组装时不应采用十字焊缝,相邻圆筒的A类焊缝的距离(或封头A类焊缝,焊缝的端点与相邻圆筒A类焊缝的距离)应大于名义厚度n 的三倍,且不小于100mm,(当板厚不同时,n按较厚板计算)。
{生产工艺流程}换热器制造工艺指导流程
{生产工艺流程}换热器制造工艺指导流程换热器制造工艺指导流程包括以下主要步骤:1.设计和规划:首先,根据客户的要求和工艺参数,设计一个合适的换热器,并制定详细的工艺流程。
这包括选择材料、确定尺寸和形状、计算换热系数和压降等。
此外,还需要进行热力和流体力学分析,以确保换热器的性能和安全。
2.材料选购:根据设计要求,选择合适的材料,如不锈钢、碳钢、铜等,并购买所需的材料。
3.材料准备:将材料剪切、切割和修整至预定尺寸,并对接触面进行打磨、锉削和抛光,以确保接触面的平整度和光滑度。
4.组装焊接:将准备好的材料按照设计要求进行组装焊接。
这可能包括点焊、氩弧焊、电阻焊等不同的焊接方法。
焊接时需要注意焊缝的质量和焊接强度,以确保换热环境的安全和稳定。
5.绝热层安装:在换热器表面安装绝热层,以减少热能的散失。
绝热材料可以是玻璃纤维、岩棉、硅胶等。
6.压力测试和质量检验:组装和焊接完成后,对换热器进行压力测试,以确保其在设计压力下的安全运行。
同时,进行各项质量检验,如外观检查、尺寸检测、材质鉴定、焊缝检测等。
7.表面处理和防腐:对换热器进行表面处理,如喷涂防锈漆、烤漆等,以增加外观质量和防止腐蚀。
8.装配和测试:将换热器的各个部件进行装配,并进行功能和性能测试,以确保其满足设计要求和客户需求。
9.包装和交付:对换热器进行包装,以保护其在运输过程中的安全。
同时,制作产品说明书,并将换热器交付给客户。
10.售后服务:在交付后,及时响应客户的需求和问题,并提供相关的技术支持和维修服务。
以上就是换热器制造工艺指导流程的主要步骤。
在实际操作中,还需要根据具体的项目和要求进行调整和优化。
对于每个步骤,都需要严格遵守相关的工艺标准和质量控制要求,以确保产品的质量和安全性。
pche换热器制造方法
pche换热器制造方法【最新版4篇】目录(篇1)一、换热器概述二、换热器的制造过程1.清洗2.管壳制造3.管箱制造4.整体组装5.耐压试验正文(篇1)换热器是一种用于实现两个或多个流体之间热量传递的设备,广泛应用于化工、石油、冶金、电力等工业领域。
在制造换热器时,需要遵循一定的工艺流程以确保设备的质量和性能。
首先,进行换热器的清洗。
在制造过程中,换热器内部可能会残留油污等污垢,因此需要使用清洗剂对其进行清洗,以确保实验效果。
清洗过程中,还需使用渗透剂和显像剂检测管头焊接缺陷,以保证设备的质量。
接下来,进行管壳制造。
这一步骤包括法兰、封头与筒节的组对,环缝焊接以及环缝无损检测。
焊接过程中,应采用埋弧自动焊焊接,并在焊前进行预热处理。
此外,还需对焊接装备进行无损检测,以确保焊接质量。
然后,进行管箱制造。
这一步骤涉及接管法兰及补强圈与壳体组焊,补强圈信号孔通压缩空气检漏以及组焊隔板等。
在制造过程中,应注意消除应力,以保证设备的性能。
完成以上步骤后,进行整体组装。
在这一步骤中,需要将各个部件组装在一起,形成一个完整的换热器。
组装过程中,应注意确保各个部件的连接稳固,以保证设备的使用寿命。
最后,进行耐压试验。
这一步骤的目的是在超设计压力下,考核缺陷是否会发生快速扩展造成破坏或开裂造成泄漏,检验密封结构的密封性能。
试验过程中,应严格按照相关规定进行,以确保试验结果的准确性。
总之,在制造换热器时,应遵循一定的工艺流程,包括清洗、管壳制造、管箱制造、整体组装和耐压试验等步骤。
目录(篇2)一、换热器概述二、换热器的制造过程1.清洗2.管壳制造3.管箱制造4.整体组装5.耐压试验正文(篇2)换热器是一种用于实现两个或多个流体之间热量传递的设备,被广泛应用于化工、石油、电力等工业领域。
在制造换热器时,需要遵循一定的工艺流程以确保设备的性能和安全。
首先,进行换热器的清洗。
清洗的目的是去除表面的污垢和油污,防止影响实验效果。
- 1、下载文档前请自行甄别文档内容的完整性,平台不提供额外的编辑、内容补充、找答案等附加服务。
- 2、"仅部分预览"的文档,不可在线预览部分如存在完整性等问题,可反馈申请退款(可完整预览的文档不适用该条件!)。
- 3、如文档侵犯您的权益,请联系客服反馈,我们会尽快为您处理(人工客服工作时间:9:00-18:30)。
浅谈换热器管板与换热管胀焊并用连接的制造工艺
摘要:简要叙述了换热器管板与换热管胀焊并用连接的制造工艺,并提出了控制其连接质量的方法。
关键词:换热管管板连接问题及对策
GBl5l—l999标准中规定,强度胀接适用于设计压力~<4MPa、设计温度
≤300℃、无剧烈振动、无过大温度变化及无应力腐蚀的场合;强度焊接适用于振动较小和无间隙腐蚀的场合;胀、焊并用适用于密封性能较高、承受振动或疲劳载荷、有间隙腐蚀、采用复合管板的场合。
由此可见,单纯胀接或强度焊接的连接方式使用条件是有限制的。
胀、焊并用结构由于能有效地阻尼管束振动对焊口的损伤,避免间隙腐蚀,并且有比单纯胀接或强度焊具有更高的强度和密封性,因而得到广泛采用。
目前对常规的换热管通常采用“贴胀+强度焊”的模式;而重要的或使用条件苛刻的换热器则要求采用“强度胀+密封焊”的模式。
胀、焊并用结构按胀接与焊接在工序中的先后次序可分为先胀后焊和先焊后胀两种。
1先胀后焊
管子与管板胀接后,在管端应留有15ram长的未胀管腔,以避免胀接应力与焊接应力的迭加,减少焊接应力对胀接的影响,15ram的未胀管段与管板孔之间存在一个间隙(见图1)。
在焊接时,由于高温熔化金属的影响,间隙内气体被加热而急剧膨胀。
据国外资料介绍,间隙腔内压力在焊接收口时可达到200~
300MPa的超高压状态。
间隙腔的高温高压气体在外泄时对强度胀的密封性能造成致命的损伤,且焊缝收口处亦将留下肉眼难以觉察的针孔。
目前通常采用的机械胀接,由于对焊接裂纹、气孔等敏感性很强的润滑油渗透进入了这些间隙,焊接时产生缺陷的现象就更加严重。
这些渗透进入间隙的油污很难清除干净,所以采用先胀后焊工艺,不宜采用机械胀的方式。
由于贴胀是不耐压的,但可以消除管子与管板管孔的间隙,所以能有效的阻尼管束振动到管口的焊接部位。
但是采用常规手工或机械控制的机械胀接无法达到均匀的贴胀要求,而采用由电脑控制胀接压力的液袋式胀管机胀接时可方便、均匀地实现贴胀要求。
采用液袋式胀管机胀接时,为了使胀接结果达到理想效果,胀接前管子与管板孔的尺寸配合在设计制造上必须符合较为严格的要求。
只有这样对于常规设计的“贴胀+强度焊”可采用先胀后焊的方式,而对特殊设计的“强度胀+强度焊”则可采用先贴胀,再强度焊,最后强度胀的方法。
2先焊后胀
在制造过程中,一台换热器中有相当数量的换热管,其外径与管板管孔孔径之间存在着较大的间隙,且每根换热管其外径与管板管孔间隙沿轴向是不均匀的(见图2)。
当焊接完成后胀接时,管子中心线必须与管板管孔中心线相重合。
当间隙很小时,上端15mm的未胀管段将可以减轻胀接变形对焊接的影响。
当间隙较大时,由于管子的刚性较大,过大的胀接变形将越过15mm未胀区的缓冲而对焊接接头产生损伤,甚至造成焊口脱焊。
所以对于先焊后胀工艺,控制管子与管板孔的精度及其配合为首要的问题。
当管子与管板腔的间隙小到一定值后,胀接过程将不至于损伤到焊接接头的质量。
有关资料显示,管口的焊接接头承受轴向力的能力是相当大的,即使是密封焊,焊接接头在做静态拉脱试验时,管子拉断了,焊口将不会拉脱。
然而焊口承受切向剪力的能力相对较差,所以强度焊后,由于控制达不到要求,可能造成过胀失效或胀接对焊接接头的损伤。
3合理的制造工艺
3.1管子与管孔的公差控制
(1)换热管在采购换热管时要求每台换热器所使用的换热管在冷拔加工时应采用同一坯料(炉批次)的原料,并在同一台经校验试验合格的拉管机上生产,这样才能保证每根换热管具有相同的材质、规格与精度。
换热管外径的均匀一致能保证管子与管板管孔的间隙,内径的均匀一致能保证与液袋式胀管机胀头的匹配性,从而延长胀头的使用寿命。
一般管子与管板管孑L间隙要求控制在
(O.3±O.05)mm范围内,而液袋式胀管机胀头外径与管子内径的公差也应控制在(O.3±0.05)ram范围内。
(2)管板
为使换热器管板管孔与管子外径在同一公差范围内,首先必须根据到货换热管外径的实际精度尺寸决定管板管孔的加工精度,如上所述,管板管孔与已到货换热管实际均匀外径间隙仍应控制在(O.3±0.05)EITI范围内。
3.2换热管与管板的加工及验收
(1)换热管
①按要求采购进厂的换热管人库前应按相关标准逐项验收,精确测量内、外径及其公差范围。
②换热管穿管前按实际测量壳程长度一次性切好换热管,避免穿管后用脚向砂轮机修磨。
当采用砂轮机修磨时,砂轮磨粒易溅人管子与管板管孔的间隙中,硅酸盐磨粒在焊接时将会产生夹渣,给焊接接头造成隐患。
③换热管穿管前胀接范围内管区应进行除锈处理,管端除去内外毛刺,这对采用液袋式胀头时尤为重要。
(2)管板
①管板应是合格的锻件,内部材质应均匀,胀接面上无影响胀接质量的缺陷。
对于装置中关键的换热器,尽量采用高级别锻件,锻件除按相关标准验收后,应做超声波复查。
②管板与折流板上管孔加工必须保证同轴度。
采用同一块模板钻孔,确保每根换热管所通过的管板与折流板上的管孔在同一中心线上,否则将使穿管发生很大的困难。
③管板的钻削加工粗糙度、管板的管桥宽度均按GB151—1999 I级要求验收。
④管孔精度以自制的通规和止规来检验,并作记录。
如要求钻孔
(25.4±0.05)mm,即选25.45mm为止规,25.3mm为通规,可以逐孔检查,对于超差孔应作出标记,以便采取特殊措施予以弥补。
⑤如为强度胀,胀槽深度应确保(O.5±O.05)InlTl范围。
对于液袋式胀接的方式,根据目前科研试验的结果,建议槽宽为8mm,槽间距为8mm,通常采用双槽结构。
⑥胀接前应严格清洁管孔,除去槽边毛刺,不允许有影响胀接紧密性的杂质存在。
3.3管子与管板的连接
(1)胀接
推荐采用液袋式液压胀接方式,以保证胀接紧密程度均匀一致。
因为液袋式胀管机其胀接压力是由人工设定,电脑控制操作的,精度较高如+25×2.5的碳钢换热管其贴胀压力通常为1 10—120MPa,强度胀压力为170—180MPa。
当采用特殊规格换热管时可以先理论计算,然后通过模拟试验,确认其贴胀及强度胀的适宜液压范围,以保证胀接连接的可靠性。
(2)焊接
一般采用填丝氩弧焊。
焊缝高度H确保不小于管壁厚度的1.4倍。
采用双层氩弧焊,且第二层焊道起弧处至少要偏离第一层焊道起弧点15。
,以消除第一层焊道中特别是起弧和收弧点处可能产生的缺陷。
(3)连接方式
图纸设计为“贴胀+强度焊”时,可采用如下两种方式:
①贴胀(盛水试漏);强度焊(水压试验)。
②强度焊(压力试验);贴胀(水压试验)。
当管板孔超标时,应先贴胀,再焊接,以免胀接时影响焊缝质量。
图纸设计为“强度胀+密封焊”时,建议采用如下方式:
贴胀(盛水试漏);密封焊(压力试验);强度胀(水压试验)。
4结语
国产换热器由于基本材料、加工精度及加工工艺方法均未达到优化组合,导致换热器使用寿命的相对降低。
目前已大量使用的胀焊并用结构的换热器,结合我国的国情,通过一系列的质量控制措施,完全可以制造出高质量、寿命长、用户满意的换热器。