铸造生产过程控制程序(含表格)
压铸生产过程管理控制程序

压铸生产过程管理控制程序压铸生产过程管理控制程序1.目标1.1根据客户的要求和公司的品质目标,制定产品压铸生产的过程控制程序。
2.范围2.1此程序使用于公司所有的压铸产品的生产及控制3.设备及物料3.1压铸机及周边设备、压铸模具、保温炉、行车等。
3.2测试仪器,辅助性工器具。
3.3铝锭,锌锭,水,电力等公共资源。
3.4包装材料及其他辅料。
4.参考文件4.1质量手册4.2客户产品要求规范4.3作业指导书—压铸工艺卡4.4品质控制计划4.5过程控制图标5.安全与培训5.1新员工上岗前须进行上岗培训,并做好记录,由安全员及组长负责执行。
5.2生产设备参数调试人员只能是经过授权并有充分经验的资深压铸管理人员,经面试考评/考核合格方可上岗。
6.职责6.1计划部门6.1.1负责制定生产排期和生产工单。
6.2 生产部门6.2.1 负责按生产计划及作业指导文件的要求实施生产。
6.2.2 对生产现场进行管理确保产品质量达到品质要求及安全生产。
6.2.3 负责对部门使用的设备进行定期保养和例行维护。
6.3 品质部门6.3.1 IPQC 负责按检查规范/标准对产品进行检验,判定检验结果,并贴检验状态标签。
6.3.2 QE 负责依客户/产品要求制订检验标准及其跟进工作。
6.4 PIE6.4.1负责按生产工艺及产品要求编制/更新作业指导文件6.5物流部门6.5.1 要确保收货时供应商的来料要符合品质标准。
6.5.2 要确保储存在货仓的物料要在良好的周围环境和储存条件下存放。
6.5.3 要确保成品完好无损的存放在成品仓,不能有灰尘和变形。
6.5.4要确保成品在运输途中也要保持完好无损。
7.程序压铸生产制程流程图88.附件8.1《压铸件试模报告》8.2《压铸工艺参数卡》8.3《压铸件生产首件尾件单》8.4《压铸机台每日生产记录表》客户要求产品资料压铸作业指导书生产排期/打样申请单品质控制计划压铸生产压铸件首件合格?维修/返工/重检/报废重熔N0 连续生产 YES 巡检合格?N0 清点数量包装入库。
ISO13485生产和服务过程控制程序(含表格)

ISO13485生产和服务过程控制程序(含表格)生产和服务过程控制程序(YY/T0287-2017 idt ISO13485-2016)1.目的保证对过程中影响产品和服务质量的因素处于受控状态,确保产品和服务质量符合规定要求。
2.范围本程序适用于生产和服务提供的所有过程的控制。
3.参考资料作业指导书检验控制程序标识和可追溯性控制程序采购控制程序GB/T19001-2016 idt ISO9001-2015质量管理体系要求YY/T0287-2017idt ISO13485-2016医疗器械质量管理体系用于法规的要求YY/T0316-2016医疗器械风险管理对医疗器械的应用医疗器械生产质量管理规范(总局公告2014年第64号)(2015年3月1日起施行)医疗器械生产质量管理规范附录无菌医疗器械(2015年第101号)(2015年10月1日起实施)医疗器械生产质量管理规范无菌医疗器械现场检查指导原则(食药监械监〔2015〕218号附件2)(2015年9月25日发布实施)4.职责4.1销售部负责对客户合同或订单的评审。
4.2人事部负责提供有效版本的作业标准和相关技术资料。
4.3质检部对生产过程中所使用的监视和测量设备的准确性负责。
4.4生产部对生产全过程进行控制。
5.作业程序5.1生产计划的控制5.1.1生产部依据合同或订单状况,综合编制车间生产通知单。
5.1.2生产车间依据生产部车间生产通知单的指令,合理安排生产的作业计划。
生产部主管对生产进度实施跟踪监督。
5.2生产过程的控制:5.2.1工艺文件的控制人事部负责提供有效版本的作业标准和相关技术资料。
5.2.2过程监控和产品检验5.2.2.1操作者在生产过程中按作业指导文件的要求,做好每一工序的检验并记录。
5.2.2.2检验员对各工序进行监督,做好检验并记录。
5.2.2.3生产主管监督操作者按作业文件的要求进行作业,并实施检查、确认,确保产品实现过程中资源的正常运作。
IATF16949生产过程控制程序(含流程表格)

生产过程控制程序(IATF16949-2016/ISO9001-2015)1.0目的1.1 对生产过程进行控制,以确保过程受控,且防止不合格品的发生。
1.2 通过实施适当有效的生产管理,有效计划、组织、控制、协调各项生产活动,使现有的人员、材料、设备、资金等资源得到最佳调配和运用。
1.3 对质量管理体系过程(生产过程)进行监视和测量(以下简称监测),以证实过程的质量保证和产品实现能力。
2.0范围适用于公司散热器生产自领料至产品包装完成后为止的产品实现过程的管理,包括对经确定的各生产过程的监测。
3.0职责3.1 技术部负责策划制定生产技术性文件,如作业指导书等。
3.2 生产部负责生产计划的制定、安排、组织实施。
3.3 车间负责按计划进行生产加工,并负责现场管理。
3.4 生产部及车间负责采用适宜的方法对过程和工序产品实施监测,负责策划和组织实施应急措施。
4.0程序内容4.1 生产控制程序4.2 其他管理要求4.2.1生产部车间执行生产操作和质检部执行产品、过程监测的人员,应视情况按《人力资源管理程序》的规定接受培训,并持证上岗。
4.2.2 生产过程各阶段存在作业或产品质量问题时,各部门应及时与质检部进行沟通,视需要采取纠正措施或预防措施,执行《纠正措施/预防措施管理程序》。
4.2.5 生产过程及监测产生的记录由生产部予以收集、保存。
5.0相关文件《采购管理程序》《产品监测管理程序》《不合格品质理程序》《产品质量策划管理程序》《交付服务管理程序》《设备管理程序》《合同管理程序》《文件管理程序》《纠正措施/预防措施管理程序》《人力资源管理程序》《监测设备管理程序》《持续改进管理程序》《仓库管理程序》《工装管理程序》《生产管理制度》《作业指导书》《生产任务单》生产任务单.xl s《生产日报表》生产日报表 (9).xl s。
GJB9001C-2017生产过程控制程序含记录表格
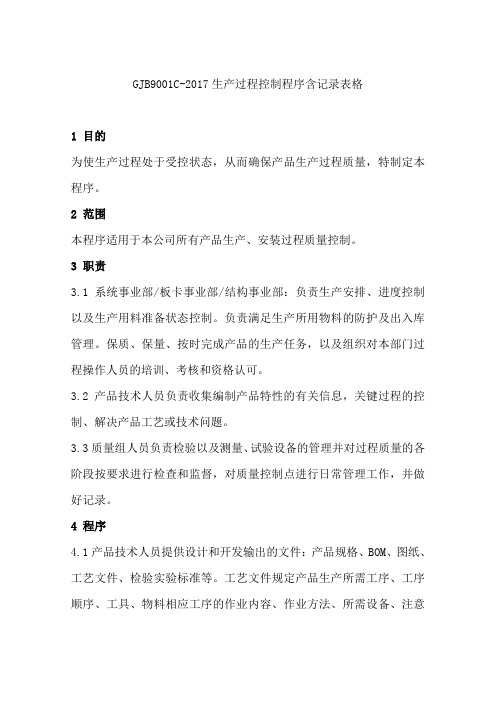
GJB9001C-2017生产过程控制程序含记录表格1 目的为使生产过程处于受控状态,从而确保产品生产过程质量,特制定本程序。
2 范围本程序适用于本公司所有产品生产、安装过程质量控制。
3 职责3.1 系统事业部/板卡事业部/结构事业部:负责生产安排、进度控制以及生产用料准备状态控制。
负责满足生产所用物料的防护及出入库管理。
保质、保量、按时完成产品的生产任务,以及组织对本部门过程操作人员的培训、考核和资格认可。
3.2 产品技术人员负责收集编制产品特性的有关信息,关键过程的控制、解决产品工艺或技术问题。
3.3质量组人员负责检验以及测量、试验设备的管理并对过程质量的各阶段按要求进行检查和监督,对质量控制点进行日常管理工作,并做好记录。
4 程序4.1产品技术人员提供设计和开发输出的文件:产品规格、BOM、图纸、工艺文件、检验实验标准等。
工艺文件规定产品生产所需工序、工序顺序、工具、物料相应工序的作业内容、作业方法、所需设备、注意事项和质量要求等。
4.2 系统事业部/板卡事业部/结构事业部根据设计和开发输出文件与产品交期要求、库存情况结合各生产部门的生产能力,编制生产计划。
4.3 生产过程组织4.3.1生产部门按确认的生产计划,依据BOM领齐物料,安排合适员工及工具到位,人员的素质应满足工作岗位对人员的基本素质的要求;并根据工艺文件检查仪器、设备是否正确,确保所使用的生产设备、工装工具必须符合工艺规程的要求。
4.3.2 在相应的工位上张贴工艺文件,生产员工须按相关工艺文件要求进行生产,同时把转产前的工艺文件回收归档保管。
4.3.3 对生产现场进行7S管理,特别是根据产品实现的不同阶段对环境的不同要求,对人身安全、健康、产品质量等有损害或潜在损害的工作环境或设备要制定严格的操作规范或实施相应的防护措施。
4.3.4 上述各项检查有不符合地方应通知相关部门进行协调处理。
4.3.5 新产品生产前由产品技术人员讲解产品生产过程、品质要求及注意事项等,使生产员工了解作业内容、作业方法以及所采用的设备、工具。
铸造生产工艺流程
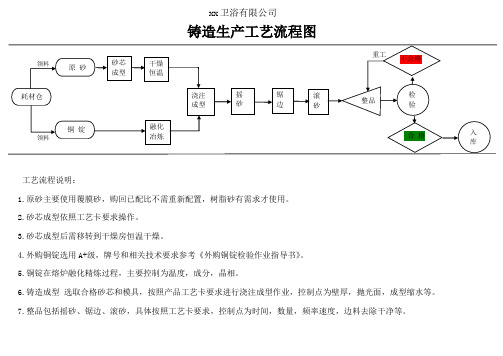
XX 卫浴有限公司
铸造生产工艺流程图
重工
领料
领料
工艺流程说明:
1.原砂主要使用覆膜砂,购回已配比不需重新配置,树脂砂有需求才使用。
2.砂芯成型依照工艺卡要求操作。
3.砂芯成型后需移转到干燥房恒温干燥。
4.外购铜锭选用A+级,牌号和相关技术要求参考《外购铜锭检验作业指导书》。
5.铜锭在熔炉融化精炼过程,主要控制为温度,成分,晶相。
6.铸造成型 选取合格砂芯和模具,按照产品工艺卡要求进行浇注成型作业,控制点为壁厚,抛光面,成型缩水等。
7.整品包括摇砂、锯边、滚砂,具体按照工艺卡要求,控制点为时间,数量,频率速度,边料去除干净等。
原 砂 铜 锭 砂芯 成型 融化 冶炼 浇注 成型 干燥 恒温
摇 砂 锯边 滚砂 整品 检 验 不合格 合 格 耗材仓 入 库。
CQI-27铸造过程表A球墨铸铁

及缺陷的位置应予以记录。
5、装配组芯最好使用自动装置,如果是手工作业,最好
带辅助定位装置。
1、芯盒存放时不可以堆放在一起,必须提供足够的存放 器具进行单层码放。 一般项 2、存放器具、集装箱和托盘等均需要有防护装置,例 如:泡沫衬垫或类似的东西,以避免芯盒在移动或搬运过 程中造成损伤。
1、在正常生产中,芯盒的库存不得超过48小时,最好少 于24小时。如果芯盒库存超过48小时作为常规方法,需 一般项 要得到顾客的批准。 2、采用冷芯盒制成的芯盒,制成后需要最少2小时的放置 时间,然后才能放入铸型中使用。
序号
类别/ 过程步骤
1.0 铸造设计和工装
A1.1
设计软件
A1.2
铸造模拟
A1.3
有限元分析
A1.4
铸造基准
A1.5 A1.6 A1.7
铸造工装材料 芯盒设计
芯盒排气道
A1.8
工装维护
过程表 A - 球墨铸铁
特性 评价 类别 结果
最低要求
1、铸造厂必须符合顾客特定的软件要求;
一般项 2、铸造厂必须具备和使用符合顾客特殊要求的工装、零
一般项 浇注过程,必须在每批新处理的金属液加入前检查化学成
分。 1、要求有一套具有镁丝矫直,并且能够控制供料速度的
镁丝供给系统。
一般项 2、推荐供料导管垂直插入金属溶液池内,即垂直供料。
3、镁丝的供应商必须通过ISO或类似的认证。
4、推荐处理包内部高度与直径比例最小为2:1。
1、必须有预防措施,确保镁处理的所有材料已正确放入
一般项 使用的任何芯撑或垫片必须完全清洁和干燥。
一般项
铸造生产线上的芯盒不允许带有浮砂。芯盒和组芯放入铸 型前必须彻底地吹干净。
铸造制程管理程序

程序类文件(QUALITY PROCEDURES)铸造制程管理程序FOUNDRY PROCESS CONTROL PROCEDURE受控状态:受控文件编号:QT/BHHS-02-18制定单位:铸造部发行日期:版本:A/0修订日期版本REV 修订记录修订日期版本REV 修订记录批准审核制定会签:铸造制程管理程序( FOUNDRY PROCESS CONTROL PROCEDURE)1、目的:使铸件的生产过程均在管制状况下运行,以确保铸件品质及完工期。
2、范围:铸造部各生产单位依生产指令进行备料、生产,直至产品经检验合格的整个生产过程均适用。
3、职责:3.1生产指令:生管部制定周生产计划、日派工单;3.2 生产作业管理及制程中自检:铸造部各生产单位。
3.3 产成品检验及制程巡检:品保部QC。
3.4 入库接收:生管部仓储科。
4、流程图:见附件。
5、管理内容:5.1 生产指令:生管部根据周生产计划分解下达日派工单。
5.2生产活动:5.2.1熔解:熔解作业人员根据生产指令依《熔解作业标准书》,《电炉安全操作规程》进行熔解作业,用测温枪测试铁水温度,具体依《测温枪操作指导书》执行当铁水成分、温度、白口值等参数满足要求时,则可进行孕育处理或球化处理,球化处理依《球化作业要领》执行,铁水品质管制依《铁水品质管制作业要领》,《碳硅仪操作指导书》进行。
作业人员应按规定填写《熔解运行记录表》。
炉体因需要补炉或筑炉时,应按《补炉作业指导书》和《筑炉作业指导书》执行。
管制重点:A.所有物料要有合格证明及标识;B.投料要有详细的投料记录。
5.2.2 砂处理:砂处理人员按《混砂作业标准书》进行作业,当砂性能调整到能满足技术要求时,即可为造型机供砂,具体依《型砂供应作业要领》执行,控制指示及手段:a.水分:双盘红外线烘干器;b.湿压强度、液压万能强度试验机;c.紧实率:紧实率测定仪;d.透气性:透气性测定仪;e.破碎指数:破碎指数测定仪。
生产过程控制程序(含参数连续监控记录表)
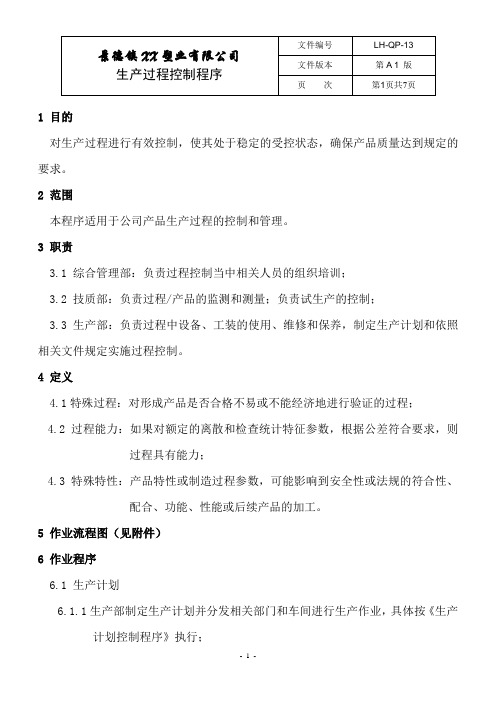
页次第1页共7页1 目的对生产过程进行有效控制,使其处于稳定的受控状态,确保产品质量达到规定的要求。
2 范围本程序适用于公司产品生产过程的控制和管理。
3 职责3.1 综合管理部:负责过程控制当中相关人员的组织培训;3.2 技质部:负责过程/产品的监测和测量;负责试生产的控制;3.3 生产部:负责过程中设备、工装的使用、维修和保养,制定生产计划和依照相关文件规定实施过程控制。
4 定义4.1特殊过程:对形成产品是否合格不易或不能经济地进行验证的过程;4.2过程能力:如果对额定的离散和检查统计特征参数,根据公差符合要求,则过程具有能力;4.3特殊特性:产品特性或制造过程参数,可能影响到安全性或法规的符合性、配合、功能、性能或后续产品的加工。
5 作业流程图(见附件)6 作业程序6.1 生产计划6.1.1生产部制定生产计划并分发相关部门和车间进行生产作业,具体按《生产计划控制程序》执行;页次第2页共7页6.1.2 生产部负责制定《生产应急计划》,以备出现偶发事故(如供应中断、劳动力短缺、设备故障等)时确保生产计划按时完成。
6.2 人员控制检验员、操作人员等由各部门主管按《培训控制程序》的有关规定进行组织培训,确认合格后方可上岗。
6.3 物料的控制6.3.1 技质部检验员按《过程/产品监测和测量控制程序》的有关规定对进货物料的质量进行控制,杜绝不合格物料投入生产;6.3.2仓库保管员严格按《产品防护控制程序》的有关规定对物料进行管理,并根据生产计划提前准备生产所需的原、辅材料。
6.4 生产环境和安全控制6.4.1 生产现场消防设施齐全,各类出入物流规划有序,并做到定置管理,具体按《现场5S管理规范》执行;6.4.2 操作人员在生产过程中必须按《作业指导书》进行以确保操作安全;6.4.3 对生产过程中出现的废品,仓库进行收集,不定期选出或通知经营部取走,以确保符合环保法规。
6.5 过程制造和检验控制6.5.1 操作人员必须依相关的指导书、控制计划等文件规定进行操作和自检;6.5.2 检验人员必须依控制计划、检验标准、检验和试验相关程序规定执行生产过程的检验和试验;页次第3页共7页6.5.3 所有的检验标准均须以最清楚实用的方式规定(例如:图示或极限样品);6.5.4 对适宜的过程参数进行监视和控制,具体依据相关作业指导书执行;6.5.5 设备、工装的使用、维修和保养,按《设施、设备控制程序》和《工装管理程序》执行;6.5.6 若顾客要求较高或较低的过程能力或性能,控制计划必须作相应注释;6.5.7当产品或过程发生更改时,由技质部负责对批量生产前进行认可合格,并提交顾客批准后,方可批量生产,更改的相关文件依《技术文件管理规范》执行,当涉及PPAP文件时,对PPAP文件进行更改;6.5.8所有相关作业操作指导书和工艺文件均须置于工作现场,操作者须在不中断操作时易于得到。
- 1、下载文档前请自行甄别文档内容的完整性,平台不提供额外的编辑、内容补充、找答案等附加服务。
- 2、"仅部分预览"的文档,不可在线预览部分如存在完整性等问题,可反馈申请退款(可完整预览的文档不适用该条件!)。
- 3、如文档侵犯您的权益,请联系客服反馈,我们会尽快为您处理(人工客服工作时间:9:00-18:30)。
铸造生产过程控制程序
(ISO9001-2015)
1.目的
为使产品铸件的整个生产过程的质量、环境、职业健康安全处于受控状态。
2.适用范围
铸造车间所生产的本公司铸件的生产全过程。
3.职责
3.1车间主任负责各工序的生产管理,组织贯彻实施质量管理、环境管理、职业健康安全管理各控制程序,对铸件生产中的质量、环境、职业健康安全负责。
3.2车间计划调度员根据公司生产技术部下达的生产指令安排组织生产活动。
3.3车间技术组负责编制工艺文件,并对工艺文件的正确性、完整性、适用性负责。
3.4车间安全员负责车间生产的环境管理和职业健康安全管理的日常工作。
3.5各班组长对本班组的产品质量、生产作业计划及进度、环境管理、职业健康安全管理的完成情况负责。
4.工作程序
4.1过程准备
4.1.1车间计划调度员按照生产技术部下发的项目计划编制各班组的生产计划,及时下发到各班组,完成调度指令兑现率,准备好各种工装器具及原材料。
4.1.2车间生产所需各种工装器具及原材料放在有明显标识的指定区域,由车间统一管理。
4.1.3车间技术组由专人负责管理图纸和技术资料,进行分类、标识、定址存放,建立文件资料目录及管理规定。
4.1.4技术组的技术人员根据当月车间生产计划准备技术资料、图纸,并保证这些资料正确、清晰、完整、有效。
4.1.5原料、辅料和工艺装备上场前有关人员应检验其是否符合规定要求,检验结果应记录并明确标识。
4.1.6车间设备员要做好设备的日常管理和检查,其结果应记录备案。
4.1.7操作者上岗前应经过培训,培训合格后持证上岗,特殊过程(熔炼、浇注、造型、焊接、热处理、机动车司机)必须经过专门培训,考试结果记录备案。
4.2过程控制
4.2.1图纸资料的控制
4.2.1.1车间技术组负责图纸、技术文件的收发、归档、管理和更改。
4.2.1.2车间技术组签收图纸、资料后,加盖本车间专用标记章,填写《收图登记》,分类放置。
4.2.1.3车间技术组收到改图通知后,按要求更改,保证零件图、工艺图、工装图的有效性,做出更改标识并通知到相关技术人员。
车间技术组对车间图纸、资料的正确性、完整性负责,保证在生产过程中使用的图纸资料为有效版本。
4.2.1.4归口本部门管理的定型产品工艺改进、工装设计及新增零件的工艺、工装设计、履行审核、批准手续。
4.2.1.5车间的图纸、资料一律不外借,外部门人员借用需经主管主任批准,并填写《借阅登记》,当日归还,特殊情况当日不能归还的,需经车间主任签字
批准限期归还。
4.2.2工艺设计控制
4.2.2.1车间技术组负责铸件铸造工艺的编制,并对其正确性、适用性负责,主管技术人员校对、审核、标准化后,主管主任签字批准,并正确执行冶炼工艺。
4.2.2.2根据生产要求,图纸资料要向相关部门(模型分公司、生产技术部和本部门)提供相应的图纸资料。
4.2.2.3工艺设计要严格按照公司的有关标准规定执行。
4.2.3原材料控制
4.2.3.1车间所有领用的原材料必须符合《铸造用金属原材料》、《铸造用辅助原材料》、《造型用原材料》的要求,不合格品不能领用,并及时向有关部门反馈。
4.2.3.2运料人员按领料单、配料单领取各种原材料送至各班组或指定的位置存放,要有标识。
4.2.3.3对每批原材料,由质量管理部人员按公司规定取样送中心化验室和理化室化验分析,以文字报告的形式将原辅材料的质量信息反馈到质管部、生产技术部、铸造车间。
车间做到不领、不用不合格品。
4.2.4配砂工序控制
4.2.4.1每班生产前,要检查配砂设备是否正常,根据当日生产调度的安排配足当日或次日的造型用砂。
4.2.4.2型砂配制过程中,操作者要严格遵守《型砂制备工艺规程》,不得随意改变配方。
4.2.4.3生产所需特种砂由技术员下达专用配方后方可生产。
4.2.4.4型砂试验员每天取样检测,湿型砂每机检测,树脂砂、再生砂抽测,按砂种不同做型砂性能检测,填写《型砂检验报告单》,一般情况下,湿型砂检测湿透、湿压、水分,合脂砂检测湿压,树脂砂检测抗拉,再生砂检测微粉、砂温、灼减量。
4.2.4.5技术组负责分析型砂在造型过程中或铸件浇注后所出现问题的原因,与造型主管技术员商讨后,提出改进后的配砂工艺及配方,并记录在《型砂检验报告单》的“试验记录”一栏中并签字。
4.2.5造型工序控制
4.2.
5.1生产前由铸造技术员根据生产计划编制重要铸件的铸造作业指导书,保证其正确性、适用性。
4.2.
5.2生产前检查模型是否完整无损、符合使用要求,并校验模型的关键部位尺寸,生产班组长与准备组联系准备砂箱、冷铁、芯铁等所需物品。
4.2.
5.3每日生产前要检查造型、制芯设备是否正常,做好日常保养。
4.2.
5.4生产过程中严格遵守造型工艺守则。
4.2.
5.5严格执行铸件首件予投制度,首件合格方可投入生产,避免造成成批废品。
铸造过程如遇生产周期太短,没有时间进行首件试制的特殊情况时,如车间认为铸造工艺可靠时,可以直接投产。
如车间认为铸造工艺需评审时,可由车间召集有关部门评审后作出决定。
4.2.
5.6每日填写浇注标牌,铸件上要有零件号、材质号、生产日期号及班组序号。
4.2.
5.7由专门的造型工序巡检人员进行工序检查,并填写《型芯巡检记录》。
4.2.6熔炼、浇注工序的控制。