浅谈水泥粉磨工艺
风选磨半终粉磨工艺在水泥粉磨中的应用

风选磨半终粉磨工艺在水泥粉磨中的应用南京苏材重型机械有限公司刘永贵水泥粉磨工艺的优化设计直接影响到后期水泥生产成本,粉磨工艺选型除考虑系统产量,系统投资,系统电耗,还需考虑熟料利用率,水泥性能,水泥强度,设备的可靠性、系统的运转率、易损件磨耗等。
如何选取最优的粉磨工艺,最简洁的工艺配置,最可靠实用的生产设备,用最小的投资取得最大的经济效益,成为广大水泥企业所追求的目标。
现有粉磨工艺比较目前比较常见的粉磨工艺:预破碎设备(锤破、立轴破、对辊机等)+球磨机;预粉磨设备(辊压机、风选磨、CKP磨)+球磨机。
采用上述工艺设备都是尽量利用多破少磨粉磨原理,尽可能最大限度发挥预粉磨设备挤压破碎功能,后道球磨机起研磨修形作用,提高水泥粉磨能力。
目前半终粉磨系统在水泥粉磨中已经得到快速应用,半终粉磨系统即预粉磨产生的细粉通过分级生产的水泥成品直接采用高浓度布袋收尘器收集入成品库,避免了大量<45um细粉进入管磨机内部,导致细磨仓出现“过粉磨”所引起的研磨体及衬板表面严重粘附现象,使管磨机系统始终保持较高而稳定的粉磨效率。
扬中市大地水泥有限公司半终粉磨开路系统改造及运行情况扬中市大地水泥有限公司现有两条水泥粉磨生产线,主机配置两台φ3.5×13m水泥磨,其中一台采用辊压机半终粉磨工艺,另一台无预粉磨设备,本技术改造在无预粉磨的生产线上,采用南京苏材重型机械有限公司风选磨半终粉磨工艺。
图示11、粉磨系统改造前扬中市大地水泥有限公司水泥粉磨生产线φ3.5×13m磨机1台,采用开路磨工艺,配套收尘器PPC96-6。
磨机分为三仓,Ⅰ仓为阶梯衬板,仓长4.0m;Ⅱ仓位为中波纹衬板,仓长2.75m;Ⅲ仓位为小波纹衬板,仓长5.5m。
采用高铬研磨体,最大钢球为φ90mm,最小钢段为φ8×8mm;前隔仓采用双层隔仓,后隔仓为单层隔仓,台时产量65吨/时,粉磨电耗为36kWh/t。
工艺流程见图示1。
图示22、粉磨系统改造后扬中市大地水泥有限公司粉磨生产线φ3.5×13m磨机1台,采用前闭路后开路工艺见图示2;即FM40(有效长度5.0m)风选磨作为水泥预粉磨设备,熟料、明矾石、石膏等进入风选磨进行预粉磨(生产42.5级水泥时配比:熟料86%,磷石膏含煤渣12%,明矾石2%),配套O-sepa改进型选粉机S1500,合格成品直接通过收尘器入库,选粉机粗粉进入φ3.5×13m磨机,磨机分为三仓,采用带筛分的双层隔仓装置,增加通风面积,磨尾采用线切割热处理出料篦板;风选磨钢球采用φ60mm-φ100mm,高细磨机采用φ30mm-φ60mm钢球和φ10mm-φ25mm的钢锻。
水泥粉磨工艺的优化选择
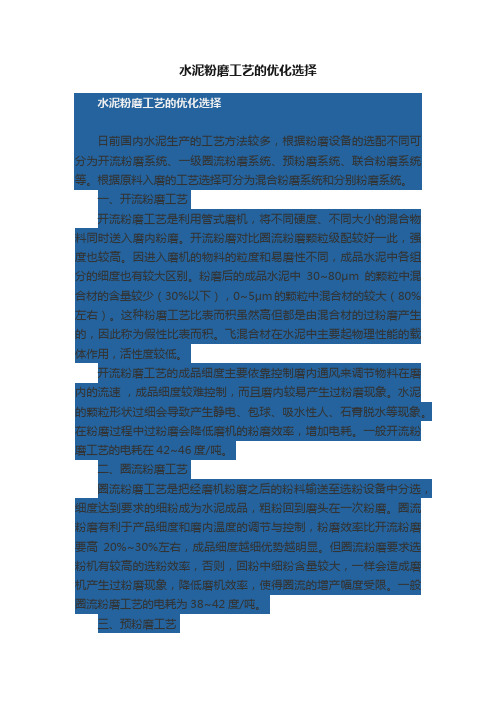
水泥粉磨工艺的优化选择水泥粉磨工艺的优化选择日前国内水泥生产的工艺方法较多,根据粉磨设备的选配不同可分为开流粉磨系统、一级圈流粉磨系统、预粉磨系统、联合粉磨系统等。
根据原料入磨的工艺选择可分为混合粉磨系统和分别粉磨系统。
一、开流粉磨工艺开流粉磨工艺是利用管式磨机,将不同硬度、不同大小的混合物料同时送入磨内粉磨。
开流粉磨对比圈流粉磨颗粒级配较好一此,强度也较高。
因进入磨机的物料的粒度和易磨性不同,成品水泥中各组分的细度也有较大区别。
粉磨后的成品水泥中30~80μm的颗粒中混合材的含量较少(30%以下),0~5μm的颗粒中混合材的较大(80%左右)。
这种粉磨工艺比表而积虽然高但都是由混合材的过粉磨产生的,因此称为假性比表而积。
飞混合材在水泥中主要起物理性能的载体作用,活性度较低。
开流粉磨工艺的成品细度主要依靠控制磨内通风来调节物料在磨内的流速,成品细度较难控制,而且磨内较易产生过粉磨现象。
水泥的颗粒形状过细会导致产生静电、包球、吸水性人、石膏脱水等现象。
在粉磨过程中过粉磨会降低磨机的粉磨效率,增加电耗。
一般开流粉磨工艺的电耗在42~46度/吨。
二、圈流粉磨工艺圈流粉磨工艺是把经磨机粉磨之后的粉料输送至选粉设备中分选,细度达到要求的细粉成为水泥成品,粗粉回到磨头在一次粉磨。
圈流粉磨有利于产品细度和磨内温度的调节与控制,粉磨效率比开流粉磨要高20%~30%左右,成品细度越细优势越明显。
但圈流粉磨要求选粉机有较高的选粉效率,否则,回粉中细粉含量较大,一样会造成磨机产生过粉磨现象,降低磨机效率,使得圈流的增产幅度受限。
一般圈流粉磨工艺的电耗为38~42度/吨。
三、预粉磨工艺日前我国在2 OOOt/d以上的新型干法水泥生产线中有较多采用辊压机(或立磨)与球磨机组成的预粉磨系统,这是因为辊压机在粉磨效率上几乎是球磨机的2倍左右,有很大幅度的节电效果。
辊压机作为预粉磨设备与球磨机闭路系统配合工作。
主要工艺特点是,挤压机的出料直接进入球磨机,可以较普通圈流粉磨大幅度地(30~40%)提高磨机产量,但挤压机与后续粉磨系统的设备生产能力同步匹配十分困难,工艺参数不易调控。
水泥粉磨工艺
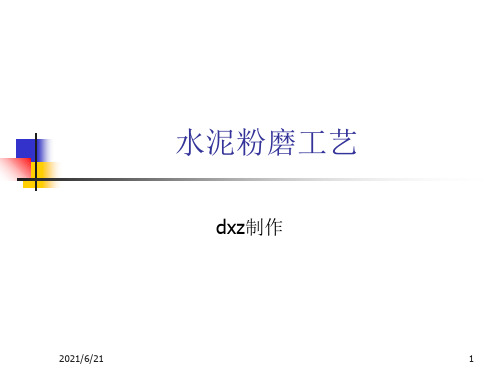
球磨机
成品
2021/6/21
6
闭路粉磨工艺流程
传统的闭路
回粉
成品
物料
球磨机
新的闭路系统
粗粉 称重仓
物料 辊压机
2021/6/21
打散机(V型 选粉机)
回粉
细粉
成品
7
第二部分水泥粉磨常用的原料
熟料 石膏 矿渣 粉煤灰 石灰石
2021/6/21
8
熟料
熟料是组成水泥颗粒的最主要成分,由C3S、C2S、C3A、 C4AF四种矿物组成。其中影响水泥强度的最主要矿物 是C3S,熟料中随着C3S含量的增加,早期强度提高, 熟料组成中含量在60%以上;C2S是熟料中的次要矿物, 它会对水泥的长期强度起到重要作用,尤其是一年之 后的长期强度;C3A可以调节水泥的性能,水化热高、 水化速度快,因此含量不能太多,一般不能超过8%; C4AF水化热比C3A低,提高耐磨性。其中随着熟料中硅 率、C2S的提高熟料的易磨性降低,随Al2O3、C3S、KH、 含量的增加易磨性提高。
2021/6/21
34
6.2研磨体装载量、材质及其级 配
6.2.1研磨体装载量
在一定范围内增加研磨体装载量可以提 高磨机产量,降低单位产品电耗,超过 一定范围仍可提高产量,但是却提高单 位电耗。中长磨和长磨的填充系数分别 为25%~35%,30%~35%时产量较高; 30%左右时电耗较低。
2021/6/21
35
6.2.2钢球装填方式
对于水泥粉磨系统如果比表面积较高 (>350m2/kg,<400 m2/kg)控制时,一般采 用一仓填充率比二仓低的方法来延缓物料流速, 增加磨内的过粉磨现象,增加台时产量;如果 比表面积较低(>290 m2/kg,<340 m2/kg)控 制时,一般采用一仓填充率比二仓高的方法, 来增加物料流速,减少过粉磨现象。
水泥厂立磨第七节立磨(图立磨生料粉磨工艺)【最新】

第七节立磨(图立磨生料粉磨工艺)一、立磨的工作原理及立磨的类型1.立式磨的工作原理主要工作部分为磨盘及磨辊。
电动机通过减速器带动磨盘转动,磨辊在磨盘上绕自身轴心滚动。
物料通过锁风喂料装置经下料溜管落到磨盘中央,由于离心力的作用形成环形料床,并被钳入磨辊与磨盘之间,受到挤压作用而被粉碎,并由于相对滑动产生剪切力,使物料被磨细。
立磨上部带有选粉设备,从下部侧面通入热空气,对物料进行烘干。
在磨盘的惯性离心力作用下,被粉磨的物料从磨盘边缘溢出,被高速气流扬起到分离器进行分级,粗粉返回磨盘再次受到粉磨(称为内循环),细粉则被气流带到磨外。
没有被热空气带起的粗颗粒物料,溢出磨盘后被斗式提升机重新喂入选粉机,再次挤压粉磨(称为外循环)。
理解挤压粉磨、悬浮烘干,选粉分级三位一体的工作过程。
2.立磨的分类按磨辊、磨盘的几何形状分为:(1)莱歇磨(锥辊--平盘式)(2) MPS磨(鼓辊--碗式)(3)雷蒙磨(锥辊--碗式)(4)伯力鸠斯磨(双鼓辊--碗式)(5)彼得斯磨,又称E型磨(球--环式)(6)ATOX磨(圆柱辊--平盘式)二、立磨的构造1.磨盘:包括导向环、风环、挡料圈、衬板、盘体、刮料板和提升装置等。
2.磨辊:辊套为易磨损件,要求有足够的韧性和良好的耐磨性能。
3.选粉机,可分为静态、动态和高效组合式选粉机三大类。
a.静态选粉机工作原理类似于旋风筒,结构简单,无可动部件,不易出故障。
但调整不灵活,分离效率不高。
b.动态选粉机这是一个高速旋转的笼子,含尘气体穿过笼子时,细颗粒由空气摩擦带入,粗颗粒直接被叶片碰撞拦下,转子的速度可以根据要求来调节,转速高时,出料细度就越细,与离心式选粉机的分级原理是一样的。
它有较高的分级精度,细度控制也很方便。
c.高效组合式选粉机将动态选粉机(旋转笼子)和静态选粉机(导风叶)结合在一起,即圆柱形的笼子作为转子,在它的四周均布了导风叶片,使气流上下均匀地进入选粉机区,粗细粉分离清晰,选粉效率高。
简述水泥生产工艺过程两磨一烧

简述水泥生产工艺过程两磨一烧
水泥的生产工艺过程通常分为两个阶段:磨和烧。
1. 磨阶段:
在磨阶段,原料(包括石灰石、粘土、铁矿石等)首先被送入破碎机进行破碎,并混合在一起。
然后,破碎后的原料被送入磨机进行细磨,以产生足够细的粉末,这些粉末称为“生料”。
生料通常被送入回转窑之前,还需要通过预热器进行预热。
2. 烧阶段:
在烧阶段,生料被送入回转窑,回转窑是一个大型的旋转筒,其内部温度可达到约1450°C。
在回转窑内,生料经历一系列
的热化学反应,这些反应将生料转化为熟料。
其中最重要的反应是石灰石和粘土之间的煅烧反应,这反应产生了水泥的主要成分——熟料。
熟料由于热化学反应已经完全发生,颗粒之间纠结在一起,形成块状物称为“熟料团”。
整个磨和烧的过程通常被称为“两磨一烧”,这一工艺过程是水泥生产的关键环节。
由于磨和烧的过程都需要高温和能量消耗,水泥生产对能源的需求非常高。
因此,寻找使用更加环保且高效的磨和烧工艺也成为了水泥工业的重要课题。
浅谈粉磨工艺的两“度”对水泥质量的影响

I 关键词 】水泥粉磨; 两个 度” ; 质量
理, 都 会影 响系统产 量和 质量 ; 而一个 能耗高 、 产量 低的球 磨机粉磨 系 凝 土在使用 中反而 因这 种误 导的 信息而造 成试 配 的难度 。 对于 有些助 统, 必然在 工艺上存在 很多问题使 系统无法达 到理 想状态 。 在此 , 首先 磨剂 中的减水 剂与混 凝土使 用的减 水剂相 容性 差 , 致 使混 凝土 的抗 拉
理 想 的水 泥是 一 个在 l ~8 0 H m范 围 内呈 连 续分 布的 颗粒 组合 粉 泥熟料和混合材采用分 别粉 磨, 将水泥熟料和 混合材磨制各 自需要 的细 体, 符合F a i l e r 曲线 最佳堆积密度 曲线, 其粒径 分布如下表 : 度再 进行勾兑、 混 合均化 , 尽量使 水泥颗粒 组成接 近 F a i l e r 最佳 堆积密 度曲线, 这样 的水 泥才是 配制混凝土 的好水泥 。 F a i l e r曲线最佳堆积密度 的粒 径分布: u m 三、 水 泥温 度 u m 1 1 . 0 I 3 . 0 l 5 . 0 l 1 O l 1 5 l 2 0 l 2 5 1 3 0 l 3 5 l 4 0 1 4 5 I 6 0 l 8 O 所有 的粉 碎 机械 , 特 别是 球 磨机 , 在 粉 碎物 通 过%l 1 7 . 3 3 l 2 6 . 8 9 l 3 2 . 9 9 l 4 3 . 5 3 l 5 2 . 4 3 1 5 7 . 4 3 I 6 1 . 8 7 I 6 7 . 5 5 l 7 1 . 4 5 1 7 5 . 7 9 l 7 9 . 4 4 l 8 9 . 1 3 1 1 0 0 料时, 研磨 体的运 动 , 在 砸碎 和研磨物 料过 程 中, 根 据水泥水化 实验, ≤3 m水泥 颗粒 主要 是C 3 S  ̄ n C 3 A晶体, 水化 由于产生热 、 声、 光 等物理 现象 , 会转变大 部分 的输入能 量转换 为为热 快, 基本上在l 天 内完 成, 主要提 供1 d 和3 d 强度 。 我 国水泥 绝大多数采用 量。 我国 目 前 水泥磨制 基本上 采用球 磨机 , 通 过热 平衡 计算 , 约8 7 %的 的是熟料和混 合材配 比后共同入 磨, 目 前 混合材主要 为粉煤 灰, 矿渣基 输 入 能量 转换 为热 量 。 这 样 增加 的 热量会 使 粉磨 物料 上升 到1 0 0 E以 本 已单独粉磨 了。 根据 中国建筑科 学研究 院的实验结 果 , 作为混 合材 的 上, 作为水泥缓凝 剂的二水石 膏, 在1 0 5 E就 开始脱水分 解 , 这 对水 泥的 粉 煤灰 必须 磨至6 8 0 m / k g 以上才能打 散其内部的球形 中空 团聚 结构, 质量影 响甚大 , 因此 , 控制水 泥温度也是一 个重要的 参数 。 水 泥温 度对 使 粉煤 灰球形表面产生缺 损, 激 发其活性 。 水泥 中其他 混合材也必须 比 水泥粉磨的影 响, 还远不止于预防二水石 膏脱水分解而产生假凝 现象 , 熟 料磨得更细 , 一般是 水泥熟料粒 径的0 . 4 1 4 倍。 只有这样 , 水泥在水化 在能耗 、 品质、 物流等方面也 同样产生不利 的影 响。 过 程 中混 合材 才能 有效 填充满 水泥 熟料之 间的空 隙, 减 少需水 量提 高 降低 水泥温度 , 不但可 以提高产质量 , 还可以节能 降耗 。 温 度对 水 水 泥密实度和 强度 。 而 在粉煤 灰与熟料的 共同粉磨过程 中, 虽然水泥熟 泥粉磨的影 响总结得 出以下有害 因素 : 料 磨至 ≤3 m, 但 此时 粉煤 灰比表 面积约 在4 2 0 m / k g 左右, 远 未达 到 6 8 0 m / k g 的要求 。 同理 对于其他混合材 的粒径也 都未达 到熟 料粒径 的
水泥磨操作工艺介绍
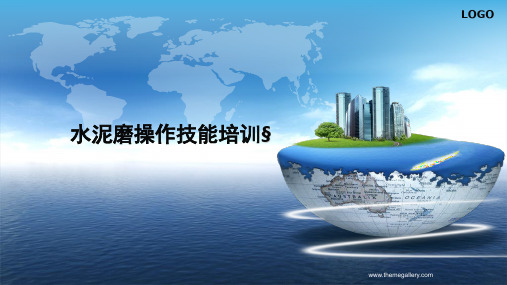
物料和出磨气体的温度都上升;产品筛余物中有薄片状物
料。这种薄片是在吸附作用下形成的,用手指轻压即成细
粉。
“包球”发生后,磨内温度很高,衬板可能翘起,又由于
B
磨内料量很少,钢球对衬板的冲击力增强,一仓衬板螺栓
可能断脱;由于磨内温度很高,磨出的水泥“发黏”,输
送设备容易堵塞,且磨机出口大,瓦温度很高(有的达
生产工艺流程图
第二部分:操作中常见的问题及解决办法
常见的问题及解决办法
1.成品大袋收尘器脉冲、提升阀存在故障或下料翻板下料堵、空气压力低于5.5Pa,造成 袋收尘器下料不稳,导致入库提升机电流不稳,出磨提升机电流波动大,原因是袋收尘工作不 正常导致;
2.稳定操作,操作上尽可能均衡喂料,而不应该大起大落,从而造成系统不稳定,失去平 衡状态,成品收尘风机风门开度应保证在100%,保证合适的料气比,提高选粉效率,在保证磨 内通风的前提下,稳定各风机风门,尽可能只通过调选粉机转数来控制比表面积;
第五部分:选粉机、辊压机工作原理
O-Sepa高效选粉机的工作原理
粉磨后的待选物料由上部两侧的两个喂料管喂入O-Sepa选粉机 内,通过转子撒料盘、缓冲板的充分分散落入选粉区,形成垂 直的料幕,被水平进入的二次风强烈冲散并被切向进入的一次 风带入回旋气流,在笼式转子回转时形成的内外压差的作用下, 较高固气比的物料得到充分的分散和多次的分选,分离的粗粉 在导向叶片涡旋向下运动时,又受到来自下部三次风的再次分 选后由底部卸出,合格的细粉随气流排出并被收集,产品细度 可以通过调节气流的回转转子速度和调节叶片的大小进行调节。
1.开机操作顺序
水泥库顶收尘→入库斜槽→水泥入库提升机→成品斜槽→细粉斜 槽→排风机→袋收尘→循环风机→粗粉斜槽→选粉机→入选粉机 斜槽→出磨提升机→磨主电机→入磨提升机→水泥喂料机组
水泥粉磨工艺技术特点与工艺改进措施分析

建材发展导向2018年第06期1121 水泥粉磨工艺技术特点1.1 开流粉磨工艺技术特点开流粉磨技术优点在于流程简单、操作便捷、使用设备较少、成本低、设备维护简单。
不过该种技术效率和产量不高,如若对产品粒度要求较严格时,被磨细的物料会在磨内形成冲层,进而形成粉磨,且还有部分数量颗粒会夹杂到成品当中,甚至还会出现粘结、包球等现象。
1.2 圈流粉磨工艺技术特点该种技术常常使用的是长管磨作为磨机,所以导致在磨内物料出现长时间停留,使得过粉磨大幅减少,从而达到提高了磨机的产量,具有效率高、能耗低、循环负荷小的特点。
而且可以采取不同级别的选粉技术来把控成品粒度,实际磨出物料较细。
不过该种技术流程较为复杂、操作难度较大,需要投入大量资金。
1.3 混合粉磨工艺技术特点混合粉末技术能够有效助磨熟料的粉磨,减少熟磨使用数量,降低能源消耗。
并且该项技术可以有效降低煅烧生料中石灰石所产生的二氧化碳,降低对环境的污染。
2 水泥粉磨工艺改进措施2.1 粉磨研磨体工艺改进措施用于水泥粉磨加工的原材料要求能够把小块物料变为颗粒,所以要用到巨大冲力把大块物料打碎,并且还要选用相应设备来控制物料大小间的空隙,尽可能将原材料和粉磨机接触面积加大,以便于能够将水泥粉磨效率提升。
要想改进粉磨研磨体工艺可从如下几方面着手:第一,在确保粉磨细度条件得到满足的基础上,合理加大物料接触面或增加设备循环次数,将研磨设备直径减小,以便于提升设备工作效率。
第二,如若要采取等级不同的两种等级钢锻,则应当选用平均组合钢锻。
如若是采取三段钢锻,就应当要结合具体情况来组合。
第三,磨设备如果是相邻的两个仓都是钢球,就需要确保后面最大,前面最小的原则,并根据特定比例来选用2-3级或3-5级钢锻,进而确定最佳研磨设备。
第四,如若所采用原材料硬度较大、颗粒较大,出料细度要求不高的情况下,可以选用较大直径的研磨设备,反之就选用直径较小的设备,即结合具体研磨要求来选择相应直径设备。
- 1、下载文档前请自行甄别文档内容的完整性,平台不提供额外的编辑、内容补充、找答案等附加服务。
- 2、"仅部分预览"的文档,不可在线预览部分如存在完整性等问题,可反馈申请退款(可完整预览的文档不适用该条件!)。
- 3、如文档侵犯您的权益,请联系客服反馈,我们会尽快为您处理(人工客服工作时间:9:00-18:30)。
浅谈水泥粉磨工艺
李纯茂刘骁(云南创兴建材新技术有限公司昆明650000)
摘要:介绍了现行的几种水泥粉磨工艺,并对其优劣作了分析,同时指出分别粉磨将成为水泥粉磨工艺发展的方向。
关键词:水泥;粉磨;工艺
水泥作为大宗建筑材料,在推动国家建设和国民经济发展中起着不可替代的作用,我国仅2009年就消耗了近16.3亿t水泥。
而水泥的生产伴随着大量的能源消耗,同时排放大量的CO2影响环境。
如何节能减排,在生产成本和社会责任之间如何权衡,成为水泥生产厂家必须面对的问题。
在水泥生产过程中,粉磨系统电耗占整个水泥生产系统电耗的2%~65%(生料粉磨系统电耗约占水泥综合电耗的24%,水泥粉磨系统电耗约占水泥综合电耗的24%),成本占35%左右,因此水泥粉磨工艺对水泥生产效益影响极大。
1现行水泥粉磨工艺简介
目前国内水泥生产的工艺方法较多,根据粉磨设备的选配不同可分为开流粉磨、圈流粉磨和预粉磨,根据原料入磨的工艺选择可分为混合粉磨和分别粉磨。
1.1开流粉磨工艺
开流粉磨工艺是利用管式磨机,将不同硬度、不同大小的混合物料同时送入磨内粉磨。
开流粉磨对比圈流粉磨颗粒级配较好一些,强度也较高。
但粉磨后的成品水泥中30~80μm的颗粒中混合材的含量约有30%以下,5~30μm的颗粒中混合材的含量约有60%以下,0~5μm的颗粒中混合材的含量约有80%左右。
这种粉磨工艺比表面积虽然高但都是由混合材的过粉磨产生的,因此称为假性比表面积。
混合材在水泥中主要起物理性能的载体作用,活性度较低,水泥的颗粒形状过细会导致产生静电、包球、吸水性大、石膏脱水等现象。
在粉磨过程中过粉磨会耗费大量的电耗和时间,增加无用功。
1.2圈流粉磨工艺
圈流粉磨工艺是把经磨机粉磨之后的粉料输送至选粉设备中分选,细度达到要求的细粉成为水泥成品,粗粉回到磨头二次粉磨。
圈流粉磨有利于产品细度和温度的调节和控制,粉磨效率比开流粉磨要高10%~20%左右,成品细度越细优势越明显。
但圈流粉磨得到的水泥产品中20~40μm 的平均粒径明显增多,5~20μm以下的平均粒径含量减少,这种方法导致水泥的颗粒级配不合理,熟料强度没有最大限度地发挥出来。
1.3预粉磨工艺
目前我国在2000t/d以上的新型干法水泥生产线中已经普遍采用辊压机与球磨机组成的预粉磨系统(包括循环预粉磨、联合粉磨、半终粉磨等),这是因为辊压机在粉磨效率上几乎是球磨机的2倍左右,有很大幅度的节电效果。
辊压机与球磨机组成的预粉磨系统的节电水平因其消耗功率的大小而变化,辊压机每消耗1(kW·h)/t,可使球磨机电耗下降1.8~2(kW·h)/t左右,从而使辊压机和球磨机组成的预粉磨系统的总电耗降低0.8~1(k W·h)/t,节电效果显著。
节电效果显著。
遗憾的是由于我国工业水平相对滞后,材料工业及制造工艺等问题导致辊压机的辊压只能保持在8MPa左右。
料饼打散后比表面积在90~120m2/kg之间,而且粒内没有发生晶格裂变,使整个粉磨系统的电耗与国外相比,仍有一定差距。
如果将水泥折合成52.5的纯水泥比较,日本比我国低10(kW·h)/t,印度比我国低7~8(kW·h)/t,因此,我国粉磨工艺节能减排的空间还很大。
2混合粉磨和分别粉磨
2.1混合粉磨工艺
应用技术
59
2010年第3期
2010年第3期
混合粉磨工艺是将混合材(粉煤灰、矿渣、石膏、石灰石等)与熟料混合后入磨粉磨,由于矿渣的易磨性比水泥熟料差约30%,必然产生选择性粉磨,导致成品中2种物料的粒径分布不同。
水泥的水化反应时间比矿渣、粉煤灰要提前一些,要想使水泥和矿渣的水化反应时间同步,就必须控制他们各自不同的最佳细度以充分发挥他们的活性,据相关资料显示:矿渣水泥中熟料比表面积≤350~400m 2/kg 即可,矿渣比表面积需达到
500m 2/kg 左右。
且矿渣、粉煤灰的硬度及易磨性
和水泥熟料相比都有较大的差别,如果矿渣达不到理想细度,就会造成矿渣过粗而不能充分发挥其潜在的水硬性,导致水泥制品的早期强度低,发展潜力小,矿渣不能充分发挥活性,浪费资源。
由于矿渣的易磨性比水泥熟料差约30%,如要达到矿渣的理想细度,务必造成水泥熟料的过粉磨,使水泥制品的早期强度大,但发展潜力小,28d 强度低。
反之粉煤灰硬度较小易粉磨,如要达到粉煤灰的理想细度,就会造成水泥熟料细度不够,不能充分发挥水泥的活性,早期强度也低。
2.2分别粉磨工艺
分别粉磨是将不同硬度、不同大小的各种物料根据他们不同的性状要求分别送入不同的粉磨系统内粉磨。
目前国内采用的分别粉磨工艺主要是把矿渣、粉煤灰、石膏等混合材和熟料进行分别粉磨,粉磨过程中根据各种物料的不同特性采用不同的粉磨设备及工艺。
矿渣因其硬度大,比表面积要求高(矿渣比表面积达到500m 2/kg 左右时,掺入水泥可发挥其最佳性能)等特点,目前大部分厂家主要采用圈流粉磨工艺;同时,有部分厂家已经采用烘干立磨的工艺;粉煤灰与石膏等其他混合材因其易磨性与熟料差距不大,且混磨有一定的助磨作用等特点,主要采用混磨+圈流或混磨+预粉磨与圈流相结合的联合粉磨工艺。
分别粉磨工艺根据物料和设备的特点选择最佳的工艺路线,可使水泥粉磨的综合能耗降到最低,使各种物料的潜力最大限度地发挥出来,混合材掺量大幅增加,更大程度地替代水泥熟料,资源得到充分利用,降低了水泥产品成本,提高企业竞争力。
以1条2000t/d 水泥生产线为例:熟料与混
合材百分配比按75∶25,在标号不变的情况下,每吨水泥多用5%的混合材替代熟料,即熟料与混合材百分配比变成70∶30,每天可替代133t 熟料,1t 熟料与混合材的成本差价按120元计,则每天可节约成本15000余元。
3结语
混合材的掺入能降低生产成本,改善水泥性
能,对熟料的粉磨有助磨作用,减少能耗;降低熟料的用量,从而减少生料中石灰石煅烧所带来的CO 2,既净化环境,又可减少开采,节约资源。
然而粉磨工艺的选择及预粉磨设备的选配直接影响到粉磨能耗和混合材的掺入量,分别粉磨充分考虑物料的特性从而选择最佳的粉磨工艺和设备,可以使熟料和混合材达到最佳的粒度分布,以便于对混合材填充效应、潜在活性的充分利用,对于提高水泥厂的综合效益有着重要意义。
因此,分别粉磨以其节能减排和资源综合利用优势必将成为水泥粉磨工艺发展的方向。
参考文献:
[1]陈新中.分别粉磨与水泥在混凝土中的适应性.2009年国内外
水泥粉磨新技术交流大会论文集.
[2]万新发,崔永飞.水泥粉磨工艺的几个问题及其发展趋势[J].新
世纪水泥导报,2008(6).
[3]张大康.分别粉磨工艺的水泥性能.2009年国内外水泥粉磨新
技术交流大会论文集.[4]邹伟斌.水泥粉磨工艺发展趋势及改造要点[J].四川水泥,2008(2).
(责任编辑:何彬)
应用技
术
60。