MAGMAIRON帮助文件(翻译)
Magma学习版安装说明

1、检查日期2007-01-29 2007-05-012、安装3、安装Exceed 12,重启4、安装5、安装dongle,插入狗6、安装node-server7、安装客户信息8、安装licence文件从邮件9、运行一、检查日期检查硬盘空间安装后用了检查当前用户属于administrators组检查是不是有网卡,有网卡就行,不需联网二、安装没microsoft windows services for UNIX 插入光盘,自动运行用户和组织随意标准安装在C:\SFU,也能够自概念,不要更改安装组件,然后自概念安装途径二、安装exceed v12 2007,放入安装光盘,选择Install Exceed选择Personal InstallationPer User Directory每一个用户成立自己的同意目录,Shared User Directory用户共享目录任意选择,Shared占空间小些,易用户设置冲突选择yes3、安装放入光盘,自动运行安装完后,自动运行magma的dongle的驱动安装,就不用在手动安装狗驱动了~4、狗驱动安装选择no五、安装node-server运行exceed(运行magma前都必需打开exceed)第一次运行会需要设定键盘默许ok能够按×关掉,只留bar工具正版插入狗,运行magmasoft-setup(magmasoft-dongle setup已经安装完);学习版是覆盖破解文件到C:\\\NT_INTEL\bin\点安装node serverInstall安装成功,按任意键终止,按dismiss推出node server安装。
再按start installation安装客户信息。
信息随意,按ok生成信息,ok按Ok——quit退出生成的信息文件在C:\\ms_sysinfo六、License文件安装注:的文件格式参考,把破解中的key生成如下格式文件拷贝license文件()到d:\显示的是运算机名称和用户名称,回车选择3 License Keys选择4,输入文件地址:/dev/fs/D/,回车读入license文件后,选择2 Write license database写license信息到系统数据库后,按0推出再按0退出安装完毕。
MAGMA操作教程

MAGMA操作教程MAGMA(矩阵代数工具)是一个用于计算数学和代数问题的计算机程序。
它在计算线代或数论问题时非常有用,同时也可以用于多项式插值、点计数和椭圆曲线等其他领域。
本教程将向您介绍如何使用MAGMA进行常见操作。
一旦您进入MAGMA界面,您就可以开始输入和执行各种操作。
下面是一些常见操作的示例:1.简单的矩阵和向量操作:- 创建一个2x2的矩阵A:`A := Matrix([[1, 2], [3, 4]])`- 创建一个长度为4的向量v:`v := Vector([1, 2, 3, 4])`- 计算矩阵A的逆矩阵:`InvA := A^-1`-计算向量v与矩阵A的乘积:`Av:=A*v`2.矩阵特征问题:- 计算矩阵A的特征多项式:`p := CharacteristicPolynomial(A)` - 计算矩阵A的特征值:`eigenvalues := Eigenvalues(A)`3.矩阵分解:- 计算矩阵A的QR分解:`Q, R := QRFactorization(A)`- 计算矩阵A的特征值分解:`A = P*D*P^-1, D := DiagonalMatrix(Eigenvalues(A)), P := EigenvectorMatrix(A)`4.矩阵方程:- 解线性方程组Ax = b:`x := Solution(Transpose(A),Transpose(b))`- 解齐次方程组Ax = 0 的零空间:`NullSpace(A)`- 解非齐次方程组Ax = b 的特解:`ParticularSolution(A, b)`5.矩阵运算:- 计算矩阵A的迹:`Trace(A)`- 计算矩阵A的秩:`Rank(A)`- 计算矩阵A的行列式:`Determinant(A)`6.数论问题:- 计算一个数n的质因数分解:`Factorization(n)`- 计算一个数n是否为素数:`IsPrime(n)`- 计算一个数n的欧拉函数值:`EulerPhi(n)`值得一提的是,MAGMA是一款商业软件,虽然它提供了免费试用版本,但在进行商业和科研项目时可能需要购买正式许可证。
magma中文手册
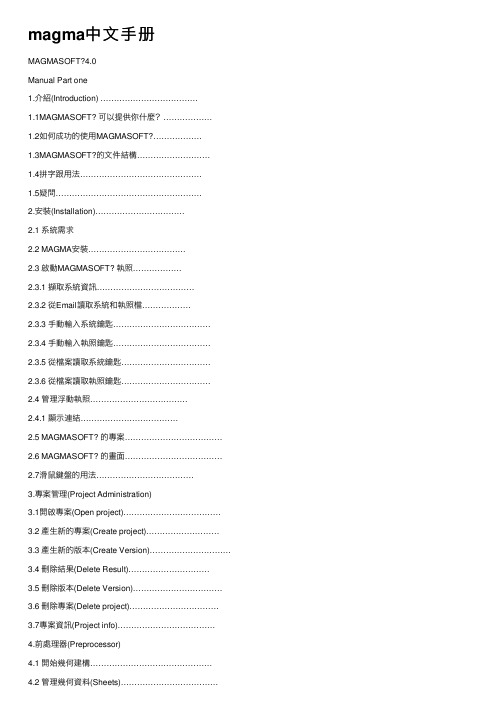
magma中⽂⼿册MAGMASOFT?4.0Manual Part one1.介紹(Introduction) ………………………………1.1MAGMASOFT? 可以提供你什麼?………………1.2如何成功的使⽤MAGMASOFT?………………1.3MAGMASOFT?的⽂件結構………………………1.4拼字跟⽤法………………………………………1.5疑問………………………………………………2.安裝(Installation)……………………………2.1 系統需求2.2 MAGMA安裝………………………………2.3 啟動MAGMASOFT? 執照………………2.3.1 擷取系統資訊………………………………2.3.2 從Email讀取系統和執照檔………………2.3.3 ⼿動輸⼊系統鑰匙………………………………2.3.4 ⼿動輸⼊執照鑰匙………………………………2.3.5 從檔案讀取系統鑰匙……………………………2.3.6 從檔案讀取執照鑰匙……………………………2.4 管理浮動執照………………………………2.4.1 顯⽰連結………………………………2.5 MAGMASOFT? 的專案………………………………2.6 MAGMASOFT? 的畫⾯………………………………2.7滑⿏鍵盤的⽤法………………………………3.專案管理(Project Administration)3.1開啟專案(Open project)………………………………3.2 產⽣新的專案(Create project)………………………3.3 產⽣新的版本(Create Version)…………………………3.4 刪除結果(Delete Result)…………………………3.5 刪除版本(Delete Version)……………………………3.6 刪除專案(Delete project)……………………………3.7專案資訊(Project info)………………………………4.前處理器(Preprocessor)4.1 開始幾何建構………………………………………4.2 管理幾何資料(Sheets)………………………………4.3 幾何資料庫(Geometry database)………………………4.4 輸⼊CAD資料(Importing CAD Data)…………………4.5 定義⾓度及精度(Definition of Angles & Accuracy)………4.6 選擇畫⾯(View options)………………………………4.7建構指令(Construction commands)……………………4.8操作指令(Manipulation commands)……………………4.9控制點(Control Point)………………………………4.10⽀援幾何功能(Support functions)………………………5.網格化(Mesh Generation)5.1 概論(Overview)………………………………5.1.1格⼦⼤⼩ / ‘wall thickness’………………………5.1.2格⼦再細化/ ‘accuracy’, ‘element size’……………5.1.3格⼦的修飾/ ‘smoothing’………………………5.1.4個⼦的外觀/ ‘aspect ratio’………………………5.2材料群的選⽤與網格化的改善………………………5.3產⽣網格(Generate mesh)……………………………5.4檢查網格(Check enmeshment)………………………5.4.1觀看網格(view mesh)…………………………5.4.2觀看網格品質(view mesh quality)………………6.模擬計算(Simulation)6.1 概論(Overview)………………………………6.1.1 充填(Mold filling)………………………………6.1.2 凝固(Solidification)…………………………6.1.3 充填和凝固………………………………6.1.4 批次⽣產(Batch production)……………………6.2 模擬參數定義(Defining simulation parameters)…………6.2.1 材料 / ‘Material definition’………………………6.2.2 熱傳導係數/ ‘Heat transfer definition’…………MAGMAshakeout選項…………………………6.2.36.2.4 充填 / ‘filling’………………………………6.2.5 注湯速率/ ‘pouring rate’………………………6.2.6 凝固 /‘solidification’……………………………6.2.7 批次⽣產/ ‘batch production’……………………6.3 模擬的開始與控制(Simulation control)…………………6.4 錯誤訊息(Error and Warning messages)…………………7. 選項與模組7.1模組………………………………7.2 選項………………………………1介紹(Introduction)鑄造就是將⾦屬液倒⼊模⽳中成形的⼀種⽣產技術,也是⼀種從設計到成品最快速的⽅法之⼀。
铝合金压铸模英文翻译

program, and then other sections such as biscuit, runner, gate, and overflow were also modeled in the order. Figure 1 shows an example of mold modeling to manufacturer clutch housing parts in application of the high-pressure die casting method. Five gates were used, and the thickness was 3 mm. Figure 2 shows the 3D image of a mold in actual size modeled by using Pro/ENGINEER. The total weight of the mold weighed in 3D modeling was about 12.52 ton, the fixed mold about 3.83 ton, and the moving mold about 8.69 ton, respectively. Two slide cores were operated with five tunnel pins. Specially applied was a chill block with no vacuum device. To prevent dispersion toward the chill block upon casting, a vent insert was added between the moving core and chill block as a shock-observing device to decelerate melting. A slipper was added around the four guide pins to handle problems that might occur to the mold. To prevent the slide core from being pushed toward the hydraulic cylinder upon closing the mold, a retrograding-preventive plate was installed on the fixed mold base. A distributor in contact with the sleeve was designed in a plate type. The hydraulic cylinder applied to
铸造模拟软件MAGMA操作教程
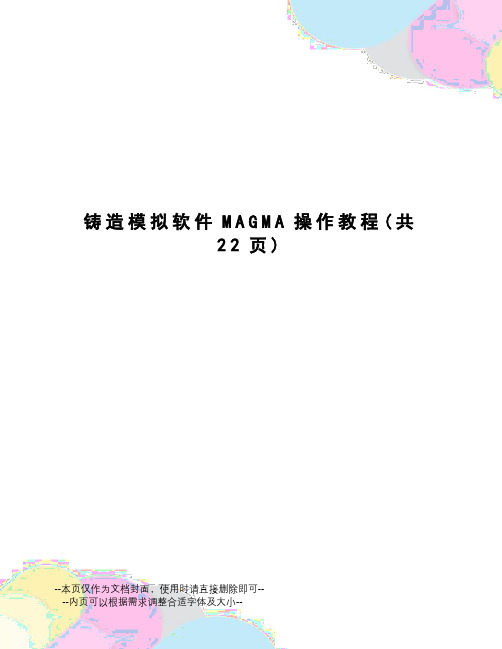
图(2_13)
说明:如图(2_13)中选择,若选择move before(移动方式)则inlet会放在gating1前面。
参照Overlay原理进行排序。一般砂模(sandm)放在最前面,铸件(cast)放在最后。
2-7、设置点
图(2_14)
流迹点选择在inlet下,20个点左右。热点选择在入水口相连的铸件内,选择热点时步骤2替换为THERMO。
2-3、载入.stl档
接上动把.stl档存在CMD文件夹下后,在创建专案的界面(图(2_1))按下preprocess 键,进入载档界面.见图(2_9)
图(2_9)
图(2_10)
载入顺序如上图所标的序号和箭头指向。注意在载前一定要确定群组属性正确。当载入一物件
后,欲载入同样的群组另一物件。则需要在以上图中的3操作之前按下MAT ID +键(上图虚线框标示)。
4_7 应力设置(stress simulation options)
图(4_7)
4_8 运算
5、后处理
6、Info
五、数据库(DATABASE)
设置完成之后,选择图(2_9)中的SAVE ALL AS1存档。然后离开界面进行下一动作。
3、切网格
图(3_1)
自动切割一般设置3百万的网格数。对于很薄的gating和ingate需要进行单独细切,视切出网格的质量而定。我们用细切的网格数自动切割时,若网格质量比细切的要好,则需要检查一下.Stl档有没有错误。
在建构实体时有一些区域重合。如图(2_7),ingate连接cast和gating,其和两者都有交接的部分。我们希望各部分独立不干涉,保证分析的精确。利用overlay原理切割重合区域。如图(2_8)排在前面的ingate被排在后面的gating和cast切割。在载入.stl档后需利用此原理进行排序。
optimazation of foundry process

Application of a Multi Objective Genetic Algorithm and a Neural Network to the optimisation of foundry processes.G.Meneghetti *, V. Pediroda**, C. Poloni ***Engin Soft Trading Srl, Italy** Dipartiento di Energetica, Università di Trieste, ItalyAbstractAim of the work was the analysis and the optimisation of a ductile iron casting using the Frontier software. Five geometrical and technological variables were chosen in order to maximise three design objectives. The calculations were performed using the software MAGMASOFT, devoted to the simulation of foundry processes based on fluid-dynamics, thermal and metallurgical theoretical approaches. Results are critically discussed by comparing the traditional and the optimised solution.1. IntroductionA very promising field for computer simulation techniques is certainly given by the foundry industry. The possibility of reliably estimating both the fluid-dynamics, thermal and microstructural evolution of castings (from the pouring of the molten alloy into the mould till the complete solidification) and the final properties are very interesting. In fact if the final microstructure and then the mechanical properties of a casting can be predicted by numerical simulation, the a-priori optimisation of the process parameters (whose number is usually high) can be carried out by exploring different technological solutions with significant improvements in the quality of the product, managing of human and economical resources and time-savings.This approach is extremely new in foundry and in this work an exploratory project aimed at the process optimisation of an industrial ductile iron casting will be presented.2. The simulation of foundry processes and foundamental equationsFrom a theoretical point of view, a foundry process can be considered as the sequence of various events [1-4]:-the filling of a cavity by means of a molten alloy, as described by fluid-dynamics laws (Navier-Stokes equation),-the solidification and cooling of the alloy, according to the heat transfer laws (Fourier equation),-the solid state transformations, related to the thermodynamics and the kinetics.A full understanding of the whole foundry process requires an investigation throughout all these three phenomena. However under some hypotheses (regular filling of the mould cavity, homogeneous temperature distribution at the end of filling, etc.) the analyses of the solidification and the solid state transformation only can lead to reliable estimation of the final microstructure and of the properties of the casting.The accuracy in simulating the solidification process depends mainly on:- the use of proper thermophysical properties of the materials involved in the process, taking into account their change with temperature,- the correct definition of the starting and boundary conditions, with particular regard to the heat transfer coefficients.From a numerical point of view, the investigation of the solidification process could be carried out by means of a pure heat flow calculation described by Fourier’s law of unsteady heat conduction :∂∂ρ∂∂λ∂∂t ()x [x C T T p j j=However a more correct evaluation requires to incorporate the additional heat transport by convective movement of mass due to temperature dependent shrinkage of the solidifying mush.Doing that temperature-dependent density functions are needed, so that the shrinkage can be calculated basing on the actual temperature loss. The total metal shrinkage within one time interval will lead to a corresponding metal volume flowing from the feeder into the casting passing through the feeder-neck. The actual temperature distribution in the feeder neck can be calculated on the basis of the following equation :∂∂ρ∂∂ρ∂∂λ∂∂t ()x (u )x [x ]C T C T T S p j p j j j+=+where the second term on the left hand side of the equation is the convective term while the first one on the right hand side is the conductive term. S denotes the additional internal heat source. The additional heat transport by convective movement of mass means that feeding may last much longer than being calculated by heat flow based uniquely on conduction.Anyway, when the feeder-neck freezes to a certain temperature, the feeding mechanism locks.Therefore the solidification of any other portion of the cast, now insulated, will take place independently from one another and the feed metal required during solidification will come from the remaining liquid. The final volume shrinkage will result in a certain porosity, which typically will be located at the hot spots.From the point of view of the real industrial interest, the above phenomena and the related equations can be approached only numerically: in fact complex 3D geometries have to be taken into account, as well as manufacturing parameters ensuring compliance with temperature-dependent thermophysical properties of the materials, production and process parameters. Finite elements,finite differences, control volumes or a combination of these are typical methods implemented in the software packages [2-3].The final result of the simulation is the knowledge of the actual feeding conditions, which is the basis for correctly design the size of feeders. It must be recalled that this knowledge-based approach is often by-passed by the use of empirical rules and in most cases the optimisation of the feeder size is not really performed (so that the feeders are simply oversized) or it is carried out by means of expensive in-field trial-and-correction procedures.The analyses were performed by using the MAGMASOFT ® software, specifically devoted to the simulation of foundry processes, based on fluid-dynamics, thermal and metallurgical theoretical approaches. In particular MAGMASOFT has a module, named MAGMAIron, devoted to the simulation of mould filling, casting solidification, solid state transformation, with the related mechanical properties (such as hardness, tensile strength and Young Modulus) of cast irons [8]3. Optimisation toolFormally, the optimisation problem addressed can be stated as follows.Minimise: F j (X ) , j=1,nWith respect to:X Subject to c X i mi (;,≥=01X (F ),......X (F ),X (F n 21Where X is the design variables vector, F i(X) are the objectives, and c i(X) are the constraints. FRONTIER’s optimisation methods are based on Genetic Algorithms (GA) and hill climbing methods. These allow the user to combine the efficient local convergence of traditional hill climbers, with the strengths of GA’s, which are their robustness to noise, discontinuities and multimodal characteristic, their ability to address multiple objectives cases directly, and their suitability for parallelisation.GA GENERAL STRUCTURE. A GA has the following stages:1.initialise a population of candidate designs and evaluate them, then2.create a new population by selecting some individuals which reproduce or mutate, and evaluatethis new populationStage 2 is repeated until terminationGA MECHANISMS. Design variables are encoded into chromosomes by means of integer number lists. Though there is an inherent accuracy limitation in using integer values, this is not significant since accuracy can easily be refined using classical optimisation techniques. The initial selection of candidates is important especially when evaluations are so expensive that not many can be afforded in the total optimisation. Initialisation can be done in FRONTIER either by reading a user-defined set, or by random choice, or by using a Sobol algorithm [9] to generate a uniformly distributed quasirandom sequence. The optimisation can also be restarted from a previous population.The critical operators governing GA performance are selection, crossover reproduction, and reproduction by mutation.Four selection operators are provided, all based on the concept of Pareto dominance. They are; (1) Local Geographic Selection; (2) Pareto Tournament Selection; (3) Pareto Tournament Directional Selection; and (4) Local Pareto Selection. The user can choose from these though (4) is recommended for use with either type of crossover, and (2) to generate the proportion of the population which is sent to the next generation unmodified.Most emphasis in FRONTIER is on use of directional crossover, which makes use of detected direction of improvement, and has some parallels with the Nelder & Mead Simplex algorithm. Classical two-point crossover algorithm are also provided.Mutation is carried out when chosen, by randomly selecting a design variable to mutate, then randomly assigning a value from the set of all possibilities.In all cases, GA probabilities can be selected by the user, in place of recommended defaults, if desired. All the algorithm are described in more detail in [10].OPERATIONAL USER CHOICE. Traditional GA’s generate a complete new population of designs from an existing set, at each generation. This can be done in FRONTIER using its MOGA algorithm. An alternative strategy is to use steady state reproduction via a MOGASTD algorithm. In this case, only a few individuals are replaced at each generation. This strategy is more likely to retain best individuals. The FRONTIER algorithm removes any duplicates generated. Population size are under the user’s control. FRONTIER case study work has usually used population from 16 to 64, due to the computational expense of the design evaluations.Classical hill climbers can be chosen by the user not only the refine GA solution. They can be adopted from the start of the optimisation, if the user can formulate his problem suitably, and if he is confident that the condition are appropriate.Returning to the problem of expansive design evaluation, many research have made use of response surface. These interpolate a set of computed design evaluation. The surface can then be used to provide objective functions which are much faster to evaluate. Interpolation of nonlinear functions in many variables, using polynomial or spline functions, becomes rapidly intractable however. FRONTIER provides a response surface option based on use of a neural net, with two nodal planes.Tests have shown this to be an extremely effective strategy when closely combined with the GA to provide a continuous update to the neural net.FITNESS AND CONSTRAINTS HANDLING. The objective values themselves are used as fitness values. Optionally, the user can supply weights to combine these into a single quantity. Constraints are normally used to compute a penalty decrementing the fitness. Alternatively, the combined constraint penalty can be nominated as an extra objective to be minimised.PARALLELISATION OF GA. The multithreading features of Java have been used to parallelise FRONTIER’s GA’s. The same code is usable in a parallel or sequential environment, thus enhancing portability. Multithreading is used to facilitate concurrent design evaluations, with analyses executed in parallel as far as possible, on the user’s available computational resources.DECISION SUPPORT. Even where there are a number of conflicting objectives to consider, we are likely to went to choose only one design. The Pareto boundary set of designs provides candidates for the final choice. In order to proceed further, the designer needs to focus on the comparative importance of the individual objectives. The role of decision support in FRONTIER is to help him to do this, by moving to a single composite objective which combines the original objectives in a way which accurately reflect his preferences.LOCAL UTILITY APPROACH. A wide range of methods has been tried for multiple criteria decision making . The main FRONTIER technique used is the Local Utility Approach (LUTA)[11]. This avoids asking the designer to directly weight the objectives relative to each other (though he can if he wishes), but rather asks him to consider some of the designs which have already been evaluated, and state which he prefers, without needing to give reasons. The algorithm then proceeds in two stages. First it decides if the preferences give are consistent in themselves, and guides the designer to change them if they are not. Then, it proposes a ‘common currency’ objectives measure, termed a utility, this being the sum of a set of piecewise linear utility functions, one for each individual objective. The preference information which the designer has provided can then be stated as a set of inequality relations between the utilities of designs. The algorithm uses the feasible region formed by these constraints to calculate the most typical composite utility function which is consistent with the designer’s preferences.This LUTA technique can be invoked after accumulating a comprehensive set of Pareto boundary designs as a result of a number of optimisation iterations. The advantage of the latter approach is that the focusing of attention on the part of the Pareto boundary which is of most interest can result in considerable computational saving, by avoiding computing information on the whole boundary. In practice so far in FRONTIER, we have generally used the LUTA technique after a set number of design evaluations, after which the utility function for a local hill climber to rapidly refine a solution.4. Object of the study and adopted optimisation procedureThe component investigated is a textile machine guide, for which both mechanical and integrity requirements are prescribed. Such requirements are satisfied, respectively, by reaching proper hardness values and by minimising the porosity content. Furthermore, from the industrial point of view, it is fundamental to maximise the process yield, lowering the feeder size.The chemical composition of the ductile iron is the following :C Si Mn P S Cu Sn Ni Cr Mg3.55 2.770.130.0380.00370.0480.0450.0170.0300.035The liquidus and solidus temperatures are 1155°C and 1120°C respectively. The thermo-physical properties of the material (thermal conductivity, density, specific heat, viscosity) are already implemented into the MAGMASOFT Materials Database.The GA optimisation process was performed starting from a configuration of the casting system which is already the result of the foundry practise optimisation.Only the solidification process was taken into account for the simulation, since it was considered to be more affected by the technological variables selected. Therefore the temperature of the cast at the beginning of the solidification process was set as a constant. Moreover the gating system was neglected in the simulation since its influence on the heat flow involved in the solidification process was thought to be negligible. As a consequence the numerical model considers only the cast, the feeder and the feeder-neck (see Fig. 1, referred to the starting casting system). The adopted mesh was chosen in such a way to balance the accuracy and the calculation time. As a consequence a number of metal cells ranging from 9000 to 12000 (resulting in a total number of cells approximately equal to 200000) was obtained in any analysed model.Five technological variables governing the solidification process have been taken into account and the respective ranges of possible variation were defined:1.temperature of the cast at the beginning of the solidification process , 1300 °C <T init.< 1380°C;2.heat transfer coefficients (HTC) between cast and sand mould , 400 W/m2K <HTC< 1200W/m2K;3.feeder height, 80 mm <H f< 180 mm4.feeder diameter, 30 mm<D f < 80 mm5.section area of the feeder-neck, 175 mm2 <A n< 490 mm2.These variables were considered to be representative of the foundry technology and significant in order to optimise the following design objectives :1.Hardness of the material in a particular portion of the cast2.casting weight (i.e. raw cast + feeder + feeder-neck)3.porosityAim of the analysis was to maximise the hardness and to minimise the total casting weight and the porosity. No constraints were defined for this analysis.Generally speaking, the optimisation procedure should be performed running one MAGMA simulation for each generated individual. That implies the possibility to assign all the input parameters and start the analysis via command files. Similarly the output files should be available in the form of ascii files from which the output parameters can be extracted. However at this stage a complete open interface between MAGMASOFT and Frontier is not still available. As a consequence another solution was adopted. First of all 64 analyses were performed in order to get sufficient information in all the variable domain. After that a interpolation algorithm was used to build a response surface model basing on a Neural Network, “trained” on the available results. It has been verified that the approximation reached is lower than 1% for all the available set of solutions with the exception of one point only where the approximation is slightly lower than 5%. After that the response surface model was used in the next optimisation procedure to calculate the design objectives. In such a way further time-expensive work needed to run one MAGMASOFT interactive session for each simulation was avoided.Concerning the Genetic Algorithm a mix between a classical and directional cross-over was used. The first population was created in a deterministic way.5. Results and discussionThe first optimisation task was done for 4 generations with 16 individuals for each generation. Since a complete simulation required about 20 minutes of CPU time on a workstation HP C200, the total CPU time resulted in about 21 hours and 20 minutes. Figs. 3, 4 and 5 report the obtained solutions. In particular from the tables it can be noted that the hardness values increase as we move from the first to the fourth generation, while the weights decrease. Not the same for the porosity, whose values seems to be less stable to converge towards an optimum solution: in fact the same range between the minimum and the maximum value is maintained both in the first and in the last generation. Moreover Fig. 2 illustrates the strong correlation between the casting weight and the hardness: such correlation is due to the particular geometry of the casting under examination and to the position where the hardness value was determined. Anyway the dependency between these two variables is favourable, the hardness increasing as the casting weight decreases, due to the changed cooling conditions. Figs 3 and 4 show that the other variables are not correlated to each other. From all these three figures it can be noted that the optimisation algorithm tends to calculate a greater number of solutions in a specific area of the design objectives plane, where the optimum solution can be expected to be located.As mentioned before the second optimisation step was performed using an approximation function consisting of three independent Neural Networks (one for each design objective) to fit the results obtained from the first optimisation procedure. Then to explore more extensively the variables domain, an optimisation task was done for 8 generation with 16 individuals for each generation.Figs. 5, 6 and 7 report the obtained solutions. By comparing this set of figures with the corresponding previous one (figs. 2, 3 and 4), it can be noted that the GA could reach better solutions, located at the top-right side area of each diagram. Since the raw casting weight was equal to about 2.5 kg and not influenced by any of the chosen variables, the casting weight resulted to be never lower than about 3 kg.All these design objectives were further processed to obtain the results in the form of Pareto Frontier. The Pareto set is reported in table 1, consisting of 11 non-dominated solutions. A direct comparison among them allowed for identifying three solutions (indicated with number 4, 7 and 8 in table 1) which seemed to reach the best compromise among the three objectives.These solutions were checked by running three MAGMAIron simulations. The comparison between the design objectives as predicted by the response surface model and as calculated by MAGMAIron is reported in table 2. It can be noted that the hardness values are predicted with good approximation by the Neural Network, while the porosity values do not match satisfactorily those calculated by MAGMAIron. Anyway the optimum set of variables (4, 7 and 8) reported in table 1 together with the objectives calculated by MAGMAIron were compared with the set of variables corresponding to the present foundry practise. The results, reported in table 3, suggest to decrease the heat transfer coefficient and the feeder size and to increase the feeder-neck section, in order to reach the objectives. The initial temperature instead is already very near to the optimised value.Finally Fig. 8 compares the sizes of the feeders and highlights the bigger feeder now adopted with respect to that of the optimised solution.6. ConclusionsFrontier was applied to MAGMASOFT code enabling the numerical simulation of mould filling and solidification of castings. On the other hand till now it was not possible to interface Frontier with MAGMASOFT since this software does not accept command files to input design parameters. As a consequence an initial optimisation procedure running MOGA for 4 generations with 16 individuals for each generation was performed and a Neural Network was built through the available design objectives. A second optimisation task running Frontier for 8 generations with 16 individuals for each generation was performed. Some design objectives belonging to the Pareto setwere then checked running MAGMASOFT simulations. The following conclusions could be drawn :•In this application the hardness could be increased from 207 HB up to 220 HB and the casting weight reduced from 4.53 kg to 3.11 kg with a slight increase in porosity from 1.27% to 1.80%.•The approximation that could be reached with the Neural Network is probably limited by the small number of available “training points” considering that five design variables were treated. Infact one of the three design objectives was not predicted satisfactorily, as compared with the solution obtained by MAGMASOFT.References[1]M.C. Flemings: "Solidification Processing", Mc Graw Hill, New York (1974).[2]ASM Metals Handbook, 9th ed., vol. 15: Casting (1988), ASM - Metals Park, Ohio.[3]P.R. Sahm, P.N. Hansen: "Numerical simulation and modelling of casting and solidificationprocesses for foundry and cast-house", CIATF (1984)[4] D.M. Stefanescu: "Critical review of the second generation of solidification models forcastings: macro transport - transformation kinetics codes", Proc. Conf. "Modeling of Casting, Welding and Advanced Solidification Processes VI", TMS (1993), pp 3-20.[5]T. Overfelt: "The manufacturing significance of solidification modeling", Journal of Metals, 6(1992), pp 17-20.[6]T. Overfelt: “Sensitivity of a steel plate solidification model to uncertainties inthermophysical properties”, Proc. Conf. "Modelling of Casting, Welding and Advanced Solidification Processes - VI", 663-670.[7] F. Bonollo, N. Gramegna: "L'applicazione delle proprietà termofisiche dei materiali nei codicidi simulazione numerica dei processi di fonderia", Proc. Conf. "La misura delle grandezze fisiche" (1997), Faenza, pp 285-299.[8]MAGMAIron User Manual[9] C.Poloni, V.Pediroda "GA Coupled with Computationally Expensive Simulations: Tool toImprove Efficiency" in "Genetic Algorithms and Evolution Strategies in Engineering and Computer Science", J.Wiley and Sons 1998[10]Paul Bratley and Bennett L. Fox, Algorithm 659, “Implementing Sobol’s QuasirandomSequence Generator”, 88-100, ACM Transactions on Mathematical Software, vol.14,No. 1, March 1988.[11]Pratyush Sen, Jian Bo Yang, “Multiple-criteria Decision-making in Design Selection andSynthesis”, 207-230, Journal of Engineering Design,vol.6 No. 3, 1995[12]I.L. Svensson, E. Lumback: "Computer simulation of the solidification of castings", Proc.Conf. "State of the art of computer simulation of casting and solidification processes", Strasbourg (1986), pp 57-64.[13]I.L. Svensson, M. Wessen, A. Gonzales: "Modelling of structure and hardness in nodular castiron castings at different silicon contents", Proc. Conf. "Modeling of Casting, Welding and Advanced Solidification Processes VI", TMS (1993), pp 29-36.[14] E. Fras, W. Kapturkiewicz, A.A. Burbielko: "Computer modeling of fine graphite eutecticgrain formation in the casting central part", Proc. Conf. "Modeling of Casting, Welding and Advanced Solidification Processes VI", TMS (1993), pp 261-268.[15] D.M. Stefanescu, G. Uphadhya, D. Bandyopadhyay: "Heat transfer-solidification kineticsmodeling of solidification of castings", Metallurgical Transactions, 21A (1990), pp 997-1005.[16]H. Tian, D.M. Stefanescu: "Experimental evaluation of some solidification kinetics-relatedmaterial parameters required in modeling of solidification of Fe-C-Si alloys", Proc. Conf."Modeling of Casting, Welding and Advanced Solidification Processes VI", TMS (1993), pp 639-646.[17]S. Viswanathan, V.K. Sikka, H.D. Brody: "The application of quality criteria for theprediction of porosity in the design of casting processes", Proc. Conf. "Modeling of Casting, Welding and Advanced Solidification Processes VI", TMS (1993), pp 285-292.[18]S. Viswanathan: "Industrial applications of solidification technology", Journal of Metals, 3(1996), p 19.[19] F. Bonollo, S. Odorizzi: "Casting on the screen - Simulation as a casting tool", Benchmark, 2(1998), pp 26-29.[20] F. Bonollo, N. Gramegna, L. Kallien, D. Lees, J. Young: "Simulazione dei processi difonderia e ottimizzazione dei getti: due casi applicativi", Proc. XIV Assofond Conf. (1996), Baveno.[21] F. Bonollo, N. Gramegna, S. Odorizzi: "Modellizzazione di processi di fonderia", Fonderia,11/12 (1997), pp 50-54.[22] F.J. Bradley, T.M. Adams, R. Gadh, A.K. Mirle: "On the development of a model-basedknowledge system for casting design", Proc. Conf. "Modeling of Casting, Welding and Advanced Solidification Processes VI", TMS (1993), pp 161-168.[23]G. Upadhya, A.J. Paul, J.L. Hill: "Optimal design of gating & risering for casting: anintegrated approach using empirical heuristics and geometrical analysis", Proc. Conf."Modeling of Casting, Welding and Advanced Solidification Processes VI", TMS (1993), pp 135-142.[24]T.E. Morthland, P.E. Byrne, D.A. Tortorelli, J.A. Dantzig: "Optimal riser design for metalcastings", Metallurgical Transactions, 26B (1995), pp 871-885.[25]N. Gramegna: "Colata a gravità in ghisa sferoidale", Engin Soft Trading Internal Report(1996)MATERIALSData-baseadopted mesh for the cast and the feeder-7.66-6.128-4.596-3.064-1.532198.3202.62206.94211.26215.58219.9Hardness Brinell C a s t i n g w e i g ht -6,29-5,032-3,774-2,516-1,2580198,3202,62206,94211,26215,58219,9Hardness BrinellP o r o s i ty -6.29-5.032-3.774-2.516-1.258-7.66-6.128-4.596-3.064-1.5320Casting weightP o r o s i t y Figs. 2,3 and 4 : solutions in the design objectives space obtained using MAGMASOFT software.VARIABLESDESIGN OBJECTIVES N°T init .(°C)HTC (W/m 2úK)H feeder (mm)D feeder (mm)A neck (mm 2)Hardness Brinell casting weight (kg)porosity (%)1130012008630194217 2.90 4.60213808119736289215 3.340.873134110378732276218 3.17 2.354135246010533400218 3.380.70513719408030176219 3.09 3.756133512008531225216 3.01 3.93713654008932341220 3.640.778133640011231400219 3.470.43913628148431315217 3.11 2.7810134610098932278219 3.18 2.6011133510598531225217 3.10 1.90Table 1: Pareto Set extracted from the 128 available solutions obtained with the Neural Network。
magmasoft后处理查看
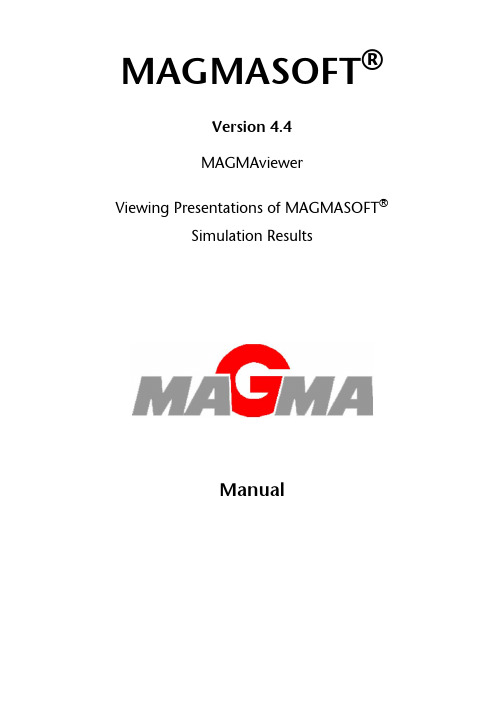
MAGMASOFT®Version 4.4MAGMAviewerViewing Presentations of MAGMASOFT®Simulation ResultsManual2MAGMA VIEWER 4.4 M ANUALThis manual supports MAGMASOFT® 4.4. No part of this document may be reproduced in any form or by any means without prior written consent of MAGMA GmbH.The use of the software described herein is restricted by a license agreement between MAGMA GmbH and the licensee.MAGMA and MAGMASOFT®, MAGMAiron, MAGMAdisa, MAGMAwheel, MAGMAhpdc and sim-ilar names are registered trademarks of MAGMA GmbH. The trademarks of all other products in this document are claimed as the trademarks of their respective owners.The information in this document is subject to change without notice.The information in this publication is believed to be accurate in all aspects; however, MAGMA does not assume responsibility for any consequential damages resulting from its use. The infor-mation contained herein is subject to change. Such changes may be incorporated through revi-sions and / or new editions.© Copyright 2006MAGMA G IESSEREITECHNOLOGIE G MB HK ACKERTSTRASSE 11D-52072 A ACHENG ERMANYT EL.: +49 / 241 / 88 90 1- 0F AX: +49 / 241 / 88 90 1- 60I NTERNET: E-MAIL: MAIL@MAGMASOFT.DET ABLE OF C ONTENTS3 Table of Contents1Introduction (5)1.1What is MAGMAviewer (5)2Licensing Procedure (7)3User Interface (11)3.1Short Overview – First Steps (11)3.2Importing a Presentation (12)3.3Functions – Overview (20)3.3.1General Handling (20)3.3.2Slide and Tree Navigation (20)3.3.3Files (21)3.3.4Windows (21)3.3.5Views (22)3.3.63-D Tools (22)3.4Example for a Presentation Tree (23)3.5Models and Animations (24)3.6Running Animations and/or Image Sequences (24)4Table of Figures (27)4MAGMA VIEWER 4.4 M ANUALC H. 1: I NTRODUCTION5 1Introduction1.1What is MAGMAviewerMAGMAviewer is a free software tool that allows running a presentation of MAGMASOFT® results quickly and easily within companies as well as with customers, suppliers, and designers. MAG-MAviewer enables the presentation of results composed with the MAGMAcomposer.A presentation created with MAGMAcomposer can only be displayed in MAGMAviewer after the data has been exported from MAGMAcomposer and packed into a MPZ file. You must then import this file into the MAGMAviewer.In the following, the term "presentation" is applied to a sequence of any number of MAGMASOFT®result images and further objects that have been generated from simulation results and composed to the presentation within the MAGMAcomposer. Usually, such a presentation is a collection of 3-D and 2-D results, 3-D and 2-D animations, and text elements.The file formats that are used by MAGMAviewer/MAGMAcomposer for storing and further pro-cessing of presentations are proprietary formats. This means that they can be used within MAG-MAviewer/MAGMAcomposer and MAGMASOFT® only, but not in any other presentation software.A full explanation of how a presentation is created is supplied in the MAGMAcomposer 4.4 Man-ual.6MAGMA VIEWER 4.4 M ANUALC H. 2: L ICENSING P ROCEDURE7 2Licensing ProcedureWhen you open the MAGMAviewer program for the first time, you will be prompted to enter the license information – normally sent by E-mail after submitting the download request on the MAG-MASOFT® website (Fig. 2-1 and Fig. 2-2).Fig. 2-1: Viewer licensing window8MAGMA VIEWER 4.4 M ANUALFig. 2-2: Viewer licensing window and license informationIf your licensing procedure fails, an error message appears and MAGMAviewer will terminate (Fig. 2-3 and Fig. 2-4).C H. 2: L ICENSING P ROCEDURE9Fig. 2-3: Viewer licensing window after invalid licensing procedureFig. 2-4: Licensing procedure failedThe main interface of the MAGMAviewer opens if your license information was correct (Î Fig. 3-1, page 11).10MAGMA VIEWER 4.4 M ANUAL3User Interface3.1Short Overview – First StepsAfter the MAGMAviewer has been opened, the main interface of MAGMAviewer appears (Fig. 3-1).Fig. 3-1: Main MAGMAviewer window (no presentation started)In order to display a presentation (that has been created with MAGMAcomposer) in the MAGMA-viewer software, the data has to be imported first of all, i.e. all necessary data and files have to beunpacked (similar to extracting ZIP files) and saved to the hard disc. Once the presentation has been imported (a presentation file in MP format is available on your disc), it can simply be opened.ÖTo open a presentation, click on the folder symbol or choose 'File' Î 'Open'. The main inter-face of MAGMAviewer appears like in Î Fig. 3-9, page 18.3.2Importing a PresentationÖTo import a presentation: Choose 'File' Î 'Import' or click on the Import symbol.ÖThe MAGMAviewer Import Wizard opens. In the following, you find all wizard windows with explanations.Fig. 3-2: Importing a presentation, step 1Fig. 3-3: Importing a presentation, step 2ÖChoose the presentation that you want to import (Fig. 3-3).Fig. 3-4: Importing a presentation, step 3A short summary appears that includes the directory and the file name (Fig. 3-5).Fig. 3-5: Importing a presentation, step 4If the chosen directory for the import already exists, "Next>" in Fig. 3-5 is not active, and the fol-lowing error message appears:Fig. 3-6: Error message during importÖIf you get this error message, confirm with "OK". The window in Fig. 3-5 appears. Click on "<Back", change the directory and proceed as described to continue with the import. Other-wise click on "Cancel" to cancel the import process.Fig. 3-7: Importing a presentation, step 5ÖAfter you have clicked on "Next>" in Fig. 3-5, the program unpacks all necessary data and files (Fig. 3-7).Fig. 3-8: Importing a presentation, step 6ÖClick on "Finish" to finish the Import Wizard. If you activate "Open Presentation <name>.mp"(default setting), the imported presentation will be opened immediately (Fig. 3-9).Fig. 3-9: MAGMAviewer main window with opened presentation (title slide)Fig. 3-10: MAGMAviewer main window with opened presentation (image slide)The elements and their contents of the main interface are as follows:Main window Display of entered text and/or selected graphical objectsMenu bar Pull-down menus with the MAGMAviewer functionsTool bar Buttons for quick access to the MAGMAviewer functionsPresentation tree Hierarchical structure of the components of the presentation (chapters)and their individual slides. Use the plus and minus signs to unfold andminimize the tree.3.3Functions – Overview3.3.1General HandlingThe functions of MAGMAviewer are available via the following access modes. You can often choose from several access modes (e.g. choose the menu entry or the quick access button for the desired function).•Menu entries •Buttons •Key shortcuts •Pop-up menus (right mouse button)3.3.2Slide and Tree NavigationThe arrows located in the status bar to the left and right of the slide title have the following actions assigned (starting from the left):•Change to the first slide of the presentation and display of its contents •Change to the previous slide and display of its contents •Change to the next slide and display of its contents •Change to the last slide and display of its contents Status bar Information on the presentation, active slide, navigation tools (Î Ch.3.3.2, page 20, Î Ch. 3.6, page 24)!Not all access modes are always explained in this manual. Quite often, it is referred toone mode only.C H . 3: U SER I NTERFACE 213.3.3FilesFunctions of the buttons (from the left to the right, including "tool tip" and corresponding menu en-try):3.3.4Windows•Open presentation (Ctrl+O)'File' Î 'Open'Opens an existing presentation •Import'File' Î 'Import'Imports a presentation •Sidebar left'Window' Î 'Sidebar left'Shows presentation tree on the left of the main window •Sidebar right'Window' Î 'Sidebar right'Shows presentation tree on the right of the main window •No sidebar'Window' Î 'No sidebar'No presentation tree is shown22MAGMA VIEWER 4.4 M ANUAL3.3.5ViewsThese functions are available for models and animations only.3.3.63-D ToolsThese functions are available for models and animations only.With these functions, you assign certain actions to the mouse:•Show an isometric view (F5)'Window' Î 'Sidebar left'Shows model/animation in isometric view •Show a top view (F6)'Window' Î 'Sidebar right'Shows model/animation from above •Show a front view (F7)'Window' Î 'No sidebar'Shows model/animation from the front •Show a right view (F8)'Tools' Î 'View / Right'Shows model/animation from the right•No actions 'Tools' Î '3D' Î 'No actions'(No action)•Activate rotate 'Tools' Î '3D' Î 'Rotate'Rotates view by clicking and dragging the mouse •Activate panning 'Tools' Î '3D' Î 'Translate'Pans (moves) view by clicking and dragging the mouse •Activate zoom 'Tools' Î '3D' Î 'Zoom'Zooms view by clicking and dragging the mouse •Zoom to fit all'Tools' Î '3D' Î 'Fit all'Zooms view to fit the main windowC H. 3: U SER I NTERFACE233.4Example for a Presentation TreeFig. 3-11 shows a sample presentation tree.Fig. 3-11: Presentation treeAs you can see, each slide has an individual symbol assigned in the presentation tree. There are slides containing text only (title slide or text slide), slides containing graphical objects only, and slides containing both. Furthermore, each of the various graphical objects has an individual sym-bol allocated to allow an easy distinction (Fig. 3-12).24MAGMA VIEWER 4.4 M ANUALFig. 3-12: Icons of various graphical objectsFurther details about the different objects can be found in Ch. 3.1, page 19 of the MAGMAcom-poser 4.4 Manual.3.5Models and AnimationsGenerally speaking, each model corresponds to an image, and each animation corresponds to a sequence. Images and sequences can "only" be displayed or run within MAGMAviewer, but not edited any further. Models, on the other hand, are equipped with additional internal information and can be processed with the View and 3D functions that are explained in Î Ch. 3.3.5, page 22 and Î Ch. 3.3.6, page 22. The same holds true for animations. This means that – like in the post-processor of MAGMASOFT® – you can e.g. freely choose the view, angle, and any zooming area as you wish.3.6Running Animations and/or Image SequencesFig. 3-13: Status bar for animations and/or image sequencesFig. 3-13 shows the status bar for slides containing animations and/or image sequences. You can use the slider to select individual results within the animation / image sequence.If you want to run the animation, proceed as follows:C H. 3: U SER I NTERFACE25•Click on the arrow on the left. The images of the animations and/or image sequences areplayed, and the slider moves from the left to the right with those time steps that you have de-fined via the input field on the right. Whilst the animation is running, a pause button appears instead of the arrow.•If you want the animation or the image sequence to be paused, click on the pause button.Whilst the animation is paused, the play arrow appears instead of the pause button. If you click on the arrow, the animation continues.•If you want to stop the animation, click the rectangle placed next to the arrow. If you click on the arrow again, the animation will start from the beginning.•If you want to repeat the animation in an infinitive loop, activate 'Loop' (click on the checkbox, the box must be ticked). If you want to deactivate the loop, untick the box.•You can define the time steps between the images of the animation (in milliseconds) via the small arrows or the input field on the right of the bar. If you choose 'Auto' (like in Fig. 3-13), the animation runs as fast as the capacity of your computer allows.•If you run an animation that is based on models ('Animation' entry in the result browser), you can edit all images during the animation with the View and 3D functions, e.g. rotate, pan, and zoom.26MAGMA VIEWER 4.4 M ANUALC H. 4: T ABLE OF F IGURES27 4Table of FiguresFig. 2-1: Viewer licensing window (7)Fig. 2-2: Viewer licensing window and license information (8)Fig. 2-3: Viewer licensing window after invalid licensing procedure (9)Fig. 2-4: Licensing procedure failed (9)Fig. 3-1: Main MAGMAviewer window (no presentation started) (11)Fig. 3-2: Importing a presentation, step 1 (12)Fig. 3-3: Importing a presentation, step 2 (13)Fig. 3-4: Importing a presentation, step 3 (14)Fig. 3-5: Importing a presentation, step 4 (15)Fig. 3-6: Error message during import (15)Fig. 3-7: Importing a presentation, step 5 (16)Fig. 3-8: Importing a presentation, step 6 (17)Fig. 3-9: MAGMAviewer main window with opened presentation (title slide) (18)Fig. 3-10: MAGMAviewer main window with opened presentation (image slide) (19)Fig. 3-11: Presentation tree (23)Fig. 3-12: Icons of various graphical objects (24)Fig. 3-13: Status bar for animations and/or image sequences (24)28MAGMA VIEWER 4.4 M ANUAL Notes。
magmasoft帮助文档
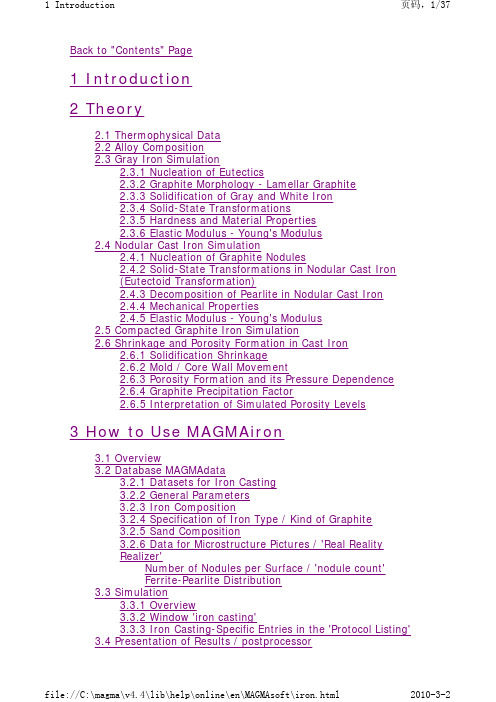
2.2 Alloy Composition
The composition of the alloy should be such that the alloying elements form a dilute solution in the iron melt. The total amount of alloying elements should not exceed a few percent. The content of carbon and silicon should be within the normal composition range for most cast iron alloys. Tab. 2-1 shows the recommended composition range (combined amount of elements marked 'x' should not exceed 2%). Element Recommended composition range % C Mg Si P S 3 to 4.3 0 to 0.05 1.5 to 4 0 to 0.2 0 to 0.1
4 Summary - What to Do
4.1 4.2 4.3 4.4 4.5 4.6 Data Specific to Iron Casting Project Definition Geometry Modeling Simulation Setup Presentation of Results Additional Information
file://C:\magma\v4.4\lib\help\online\en\MAGMAsoft\iron.html
- 1、下载文档前请自行甄别文档内容的完整性,平台不提供额外的编辑、内容补充、找答案等附加服务。
- 2、"仅部分预览"的文档,不可在线预览部分如存在完整性等问题,可反馈申请退款(可完整预览的文档不适用该条件!)。
- 3、如文档侵犯您的权益,请联系客服反馈,我们会尽快为您处理(人工客服工作时间:9:00-18:30)。
目录1 Introduction2 Theory2.1 热物理数据2.2 合金成分2.3 灰铸铁仿真2.3.1共晶核2.3.2石墨形态-层状石墨2.3.3灰铁和白口铁的凝固2.3.4固态转变2.3.5硬度和材料特性2.3.6弹性模量-杨氏模量2.4球墨铸铁仿真2.4.1石墨形核2.4.2球墨铸铁固态转变(共析转变)2.4.3球墨铸铁的珠光体分解2.4.4机械性能2.4.5弹性模量-杨氏模量2.5蠕墨铸铁仿真2.6铸铁收缩和疏松的形成2.6.1凝固收缩2.6.2砂型/芯子的变形2.6.3疏松形成和压力特性2.6.4石墨聚集因子2.6.5疏松级别模拟的说明3 How to Use MAGMAiron3.1概述3.2MAGMA数据库3.2.1铸铁数据集3.2.2一般参数3.2.3铸铁成分3.2.4铸铁类型/石墨种类3.2.5型砂成分3.2.6金相照片数据/单位面积形核数/铁素体、珠光体分布形核数3.3仿真3.3.1概述3.3.2窗口——铸铁3.3.3铸铁模拟菜单3.4结果演示/后处理3.4.1结果-概述3.4.2金相照片等——球墨铸铁的微观结构3.4.3单位系统4小结- 怎么办4.1铸铁的具体数据4.2项目定义4.3几何建模4.4仿真设置4.5结果显示4.6其他信息1 Introduction介绍MAGMAiron是微观建模软件,可以模拟凝固、固相转变及在铸铁中凝固中相关的物理现象。
MAGMAiron是一个附加的模块,可以模拟灰铸铁、球墨铸铁和蠕墨铸铁的凝固过程和固态相变过程。
冶金质量、工艺条件对铸铁合金的性能有很大的影响。
微观组织和铸件的力学性能不仅取决于铸造的流动过程,而且还由以下下参数决定:1)合金成分、2)金属处理、3)微量元素和杂质、4)熔炼炉、钢包金属液的处理(除氧、镁处理)5)孕育材料的类型和数量6)孕育法析出相的晶粒长大动力学和冷却条件决定了实际的微观组织的形成,因此必须考虑凝固、疏松和固态相变过程,它们共同影响铸铁的机械性能。
MAGMAiron使用全面的物理模型来预测铸件质量。
MAGMAiron是一个功能强大的工具,专门用于铸造设计、模型布置和工艺优化。
模型从文献资料和实用材料数据中提取。
然而,在铸铁铸造过程中,冶金、微观结构和机械性能是复杂的问题,常常是靠经验。
2理论2.1热物理数据MAGMASOFT标准模块中,凝固模拟是通过在数据库中增加一个固定的温度差(ΔT)的凝固潜热(ρCp)。
ΔT为液相和固相之间的温度差。
目前根据液-固质量百分比计算熔化潜热的大小及影响,同时热容量、导热系数和其他所有热物理数据也计入其中。
另一方面,凝固潜热和固态相变的程度根据实际预测的各阶段由内部程序计算,沉淀强化阶段也被考虑当中。
固液区域影响液态、固态的热容大小。
2.2合金成分合金成分应该是熔融在铁水中的合金元素。
总金额合金元素不应超过一定程度。
对大多数铸铁合金,碳、硅成分在以下范围内。
表2-1给出建议的成分范围。
表2-1合金元素的最大成分Element Recommended composition range %C 3-4.3Mg 0-0.05Si 1.5-4P 0-0.2S 0-0.1Cr 0-1.0(x)Mn 0-1.0(x)Ni 0-1.0(x)Cu 0-1.0(x)Mo 0-1.0(x)Sn 0-0.2(x)Ce 0-0.05Sb 0-0.04N 0-100ppm(x)标记x的元素的成分总和不应大于2%。
合金的化学成分影响其熔化和凝固过程。
可以计算凝固的灰铸铁、球墨铸铁和白口铸铁的共晶温度;计算初生析出和共晶析出过程。
石墨的析出用杠杆规则进行计算。
其他元素的析出,扩散率较低,使用修改后的Scheil-segregation方程计算。
奥氏体按照相图进行析出。
2.3灰铸铁模拟2.3.1共晶体形核灰铸铁的共晶体形核对凝固模拟、疏松形成、微观组织和机械性能的的模拟很重要。
白口共晶体在实际凝固过程中不该产生,为了避免白口共晶体的存在,设置合适含量的共晶核对凝固过程模拟是非常重要的。
如果A值太小,白口共晶体可能产生,其防止了成分的析出,疏松程度严重,机械性能降低。
孕育显著地影响形核率。
在铸铁中,石墨的形核是异质体形核,如必须在第二相粒子、基体、氧化质点等类似点。
在某一温度下活化的晶核数量,用形核公式表示,是由一些形核常数所决定。
孕育导致的石墨形核的基本公式如下:Nν=单位体积(mm3)共晶核数A= 形核常数ΔT=过冷度B=指数在MAGMAiron模块中,A常数采用默认的值,'fail','good'和'very good'三种孕育方式获得对应的A该值。
另外,在MAGMAiron模块中根据孕育方式和孕育操作可以更改或修改这些参数。
一定的过冷度可以激活一定数量石墨形核,如果温度更低,则更多数量的石墨形核被激活。
如果温度升高,新的形核过程停止,现有激活的形核过程也停止。
凝固结束过程中,这些形核能逐渐被激活,但对合金和铸件的热行为影响甚微。
然而,该过程影响了疏松的形成。
用户通过这个参数'graphite prec ipitation'的设置将该影响计入考虑。
2.3.2石墨形态-片状石墨灰铸铁共晶体生长速率和相应的形态受扩散控制,由温度决定。
根据过冷量,即当前熔体成分的共晶温度与形核温度的差值,生长形态可分为A、D型石墨。
较低过冷度时,以非耦合增长方式生长,形成A型片状石墨。
小于一定的过冷度时,将以耦合方式生长,生长速度增加。
这导致更细的片状石墨形态,生成D型石墨。
2.3.3灰口铁和白口铁的凝固The c ementite w ill not dissolve if the temperature exc eeds the metastable eutectic temperature.当合金在冷却过程中温度降到共晶温度,形核并生长,生成灰口铁。
如果温度继续冷却到亚稳定的温度,生成白口铁。
如果有新的形核析出渗碳体,白口铁能从熔体中直接析出长大,并与灰口铁的生成互相竞争。
灰口铁和白口铁的微观组织能同时发生。
如果温度超过亚共晶温度,渗碳体不会分解。
2.3.4固相转变灰铸铁的固态相变,程序假设已全部生成珠光体结构。
珠光体的增长速率根据亚稳相图和合金成分计算共析体的过冷度而得。
珠光体的粗细程度依赖于晶核长大温度,因此非常依赖冷却速度(热性能和传热系数)。
2.3.5硬度和材料特性灰铸铁的硬度值计算根据初生奥氏体的析出量和合金元素对珠光体片间距的影响而得。
珠光体中其它合金元素对铁素体的固溶强化也被考虑其中。
固相转变过程中的冷却速度对珠光体的硬度非常重要。
因此,在模拟时,建议使用已知、最了解的模具和芯子材料的传热和材料数据。
可以通过测试简单形状铸件的冷却速度,与模拟结果进行对比。
2.3.6弹性模量-杨氏模量The result of the modulus calc ulation depends on the amount and shape of the graphite in the microstructure. As no ferrite is allow ed to grow in gray iron mode of MAGMAiron, the modulus w ill be constant throughout the casting.弹性模量或杨氏模量也可以计算出来。
模量计算结果根据显微组织中石墨的形状和石墨的量所得。
在MAGMAiron模块中灰铸铁中不允许有铁素体形核生长,因此铸件的模量都是常数。
2.4球墨铸铁仿真2.4.1石墨核形核(Nucleation of Graphite Nodules)The formation of defec ts and final mechanical properties of nodularcast irons depend on the process of graphite nodule nuc leation. Thenumber of nodules per unit volume is dependent on the nuc leationpractic e, type of inoculant and fading time. You can adjust anuc leation factor in MAGMAiron to represent these proc esses andthereby modify the equations for the nuc leation, depending on theinoc ulant and the inoculation practic e used in the foundry. The basicequation has the same form as that for the nuc leation of gray ironeutectics:球墨铸铁的缺陷和最终的力学性能取决于石墨核的形核过程。
单位体积形核的数量取决于形核、孕育方式和衰退时间。
通过调整MAGMAiron模块中的形核因子,表示这些过程,从而修改了形核公式,取决于孕育和孕育工艺。
基本方程与灰铸铁共晶体形核方程类似:Nν=单位体积(mm3)共晶核数A= 形核常数ΔT=过冷度B=指数你可以修改这个常量,是有可能的应用治疗产量高于100%(“窗口”铸铁“)。
从数量和每平方毫米的结节数计算每立方毫米大小结节,考虑结节的大小。
在MAGMAiron模块中,A常数采用默认的值,'fail','good'和'very good'三种孕育方式获得对应的A该值。
可以修改该参数,孕育处理利用率值能大于100%。
单位面积的形核数用单位体积形核数和形核大小计算,将形核的尺寸考虑进去。
The function 'Real Reality Realizer' enables you to gain information about the microstructure morphology after solidific ation of nodular c ast iron.特别注意:通过'Real Reality Realizer'功能可以获得球墨铸铁凝固后的微观组织形态信息。
2.4.2球墨铸铁的固相变化(共析转变)球墨铸铁铸件的组织中,铁素体/珠光体的含量是铁素体、珠光体分别形核、长大互相竞争的结果。
原因是,有两个相转变图,稳定相转变图控制铁素体的形成,亚稳定相转变图控制珠光体的形成。