转底炉直接还原炼铁工艺的发展
国内外转底炉的发展趋势及我国发展转底炉技术的建议

一、国内外转底炉技术的发展过程简介
1、转底炉直接还原工艺简介
转底炉炼铁工艺是非高炉炼铁工艺的一种,从1978年加拿大国际镍集团 (Inco,Ltd)建成第一座转底炉以来,已有近30年的历史,它从美国发源ห้องสมุดไป่ตู้先在日 本推广、后在中国得到发展。
转底炉法以其原料适应性强和操作工艺的灵活性等优点,引起冶金界的高度重视。 但由于原料加工方法条件和对产品质量要求的不同,转底炉直接还原炼铁分为 Inmetco法、DRYIRON法, FASTMET法和ITKM3等不同工艺路线。
国内外转底炉的发展趋势及 我国发展转底炉技术的建议
周渝生 齐渊洪 严定鎏 洪益成
钢铁研究总院先进钢铁流程及材料国家重点实验室 钢研晟华工程技术有限公司 20141106
目录
一、国内外转底炉技术的发展过程简介 二、国内外转底炉技术的发展趋势 三、我国发展转底炉技术的背景 四、对我国发展转底炉技术的建议
项目
单位
原料 铁精矿粉 还原煤 皂土 有机粘结剂 小计 能源 电 天然气 氮气 水 小计 其他 消耗品 维修与备件
kg kg kg kg
kwh m3(STP) m3(STP) t
美元 美元
消耗量 单位
1335 410 5 5
65 60 10 0.30
炼钢工艺发展的趋势
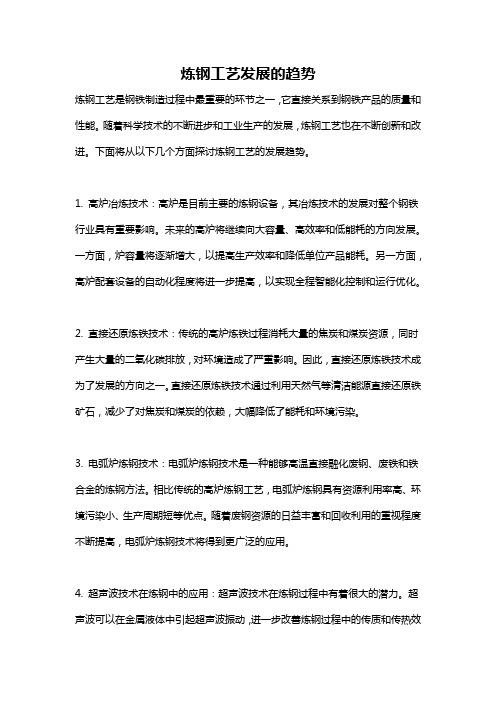
炼钢工艺发展的趋势炼钢工艺是钢铁制造过程中最重要的环节之一,它直接关系到钢铁产品的质量和性能。
随着科学技术的不断进步和工业生产的发展,炼钢工艺也在不断创新和改进。
下面将从以下几个方面探讨炼钢工艺的发展趋势。
1. 高炉冶炼技术:高炉是目前主要的炼钢设备,其冶炼技术的发展对整个钢铁行业具有重要影响。
未来的高炉将继续向大容量、高效率和低能耗的方向发展。
一方面,炉容量将逐渐增大,以提高生产效率和降低单位产品能耗。
另一方面,高炉配套设备的自动化程度将进一步提高,以实现全程智能化控制和运行优化。
2. 直接还原炼铁技术:传统的高炉炼铁过程消耗大量的焦炭和煤炭资源,同时产生大量的二氧化碳排放,对环境造成了严重影响。
因此,直接还原炼铁技术成为了发展的方向之一。
直接还原炼铁技术通过利用天然气等清洁能源直接还原铁矿石,减少了对焦炭和煤炭的依赖,大幅降低了能耗和环境污染。
3. 电弧炉炼钢技术:电弧炉炼钢技术是一种能够高温直接融化废钢、废铁和铁合金的炼钢方法。
相比传统的高炉炼钢工艺,电弧炉炼钢具有资源利用率高、环境污染小、生产周期短等优点。
随着废钢资源的日益丰富和回收利用的重视程度不断提高,电弧炉炼钢技术将得到更广泛的应用。
4. 超声波技术在炼钢中的应用:超声波技术在炼钢过程中有着很大的潜力。
超声波可以在金属液体中引起超声波振动,进一步改善炼钢过程中的传质和传热效果,提高钢的纯净度和均匀性。
此外,超声波还可以用于检测和监测钢铁产品中的缺陷和杂质,提高质量控制的准确性和效率。
5. 粉煤气化技术:粉煤气化技术是一种利用煤炭资源进行炼钢的新技术。
通过对煤炭进行气化,产生合成气,再利用合成气进行炼钢,既能够提高煤炭资源的利用率,又能够减少对传统能源的依赖和环境污染。
粉煤气化技术属于绿色环保型炼钢工艺,对于改善钢铁行业的能源结构和减少碳排放具有重要意义。
总体来说,炼钢工艺的发展趋势是朝着高效、环保、智能化和资源综合利用的方向发展。
转底炉工艺技术存在的问题与发展建议

( 1 . T e c h n o l o g y Ce n t r e o f A n g a n g S t e e l C o . ,L t d .,An s h a n 1 1 4 0 1 1 ,L i a o n i n g ;2 . S c i e n c e a n d T e c h n o l o g y De p a  ̄-
提 出 了发 展 转 底 炉 工 艺 技术 的 几 点建 议 。 关键词 转底炉 ; 冶金尘泥 ; 直接 还 原 文献标识码 : A 文章编号 : 1 6 7 1 — 3 8 1 8 ( 2 0 1 3 ) 0 2— 0 0 4 2—0 3 .
中图 分 类 号 : T F 7 0 2 . 9
d e s c r i be d i n t h e p a p e r ,a n d s o me p r o b l e ms d u r i n g p r o d u c t i o n p r o c e s s a r e s y s t e ma t i c a l l y i n t r o d u c e d a n d
o b j e c t i v e l y a n a l y z e d .At t h e e n d,s o me a d v i c e s f o r d e v e l o p me n t o f Ro t a r y He a r t h F u r n a c e a r e p r o p o s e d .
me n t o f A n g a n g S t e e l G r o u p,An s h a n 1 1 4 0 1 1,L i a o n i n g )
Abs t r a c t Th e c u r r e n t s t a t u s o f Ro t a r y He a r t h F ur n a c e d i r e c t r e d u c t i o n pr o c e s s a t h o me a n d a b o a r d i s
直接还原铁生产工艺及发展方向

直接还原铁(海绵铁)生产工艺及发展方向习惯上,我们把铁矿石在高炉中先还原冶炼成含碳高的生铁,而后在炼钢炉内氧化,降低含碳量并精炼成钢,这项传统工艺,称作间接炼钢方法;在低于矿石熔化温度下,通过固态还原,把铁矿石炼制成铁的工艺,称作直接炼铁(钢)法或者直接还原法,用这种方法生产出的铁也就称作直接还原铁(即DRI)。
由于这种铁保留了失氧时形成的大量微气孔,在显微镜下观察形似海绵,所以直接还原铁也称之为海绵铁。
一、直接还原铁(海绵铁)的用途直接还原铁是精铁粉在炉内经低温还原形式的低碳多孔状物质,其化学成分稳定,杂质含量少(碳、硅含量低),主要用作电炉炼钢的原料,也可作为转炉炼钢的冷却剂,如果经二次还原还可供粉末冶金用。
一次还原铁粉(海绵铁)的主要用途有:①作为粉末冶金制品的原料,耗用量约占铁粉总耗用量的60~80%;②作为电焊条的原料,在药皮中加入10~70%铁粉可改进焊条的焊接工艺并显著提高熔敷效率;③作为火焰切割的喷射剂,在切割钢制品时,向氧-乙炔焰中喷射铁粉,可改善切割性能,扩大切割钢种的范围,提高可切割厚度;④还可作为有机化学合成中的还原剂、复印机油墨载体等。
近年来由于钢铁产品朝小型轻量化、功能高级化、复合化方向发展,故钢材中非金属材料和有色金属使用比例增加,致使废钢质量不断下降。
废钢作为电炉钢原料,由于其来源不同,化学成分波动很大,而且很难掌握、控制,这给电炉炼钢作业带来了极大的困难。
如果用一定比例的直接还原铁(30~50%)作为稀释剂与废钢搭配不仅可增加钢材的均匀性,还可以改善和提高钢的物理性质,从而达到生产优质钢的目的。
因此,直接还原铁(海绵铁)不仅仅是优质废钢的替代物,还是生产优质钢材必不可少的高级原料(天津无缝钢管公司国外设计中就明确要求必须配50%的直接还原铁(海绵铁))。
根据国外报导,高功率电炉冶炼时,炉料搭配30~50%直接还原铁,生产率提高10~25%,作业率提高25~30%。
直接还原铁生产工艺的分析

直接还原铁生产工艺的分析世界上直接还原铁生产技术已经成熟, 技术发展极为迅速, 根据Midrex 公司预测, 2010年全世界直接还原铁产量将超过7300万t。
于高炉流程存在着生产成本过高和环境污染的两大难题, 炼铁工艺由高炉流程逐步向直接还原铁短流程过渡已成为定局。
当今的钢铁企业对这一革命性技术工艺越早开发越能占据主动; 不敢承担风险, 迟疑不前, 必将处于被动和落后的局面。
因此, 直接还原铁的开发不是“有所为”和“有所不为”的问题, 而是生产工艺的选择问题。
1 世界直接还原铁生产技术现状1.1 生产工艺发展态势由于某些国家天然气资源丰富, 直接还原铁生产技术在南美洲、南非和东南亚诸国的发展极为迅速,而印度则后来居上; 特别是委内瑞拉、墨西哥等国, 生产历史已超过20余年, 生产规模不断扩大, 直接还原铁产量已占本国钢铁产量的绝对份额; 而奥钢联、韩国合作开发的直接还原与熔融还原技术与日俱进; 浦项钢铁公司的直接还原铁生产大有代替高炉炼铁之势。
对这样的发展态势, 作为世界钢铁生产大国的中国, 我们绝不可掉以轻心。
1.2 世界直接还原铁主要生产工艺??? 世界直接还原铁生产工艺大致可分为两大类: 一种是气基竖炉生产工艺; 一种是煤基回转窑生产工艺。
前者生产量约占总产量的92%, 而后者约占总产量的8%。
在这两种生产技术的基础上, 又发展了熔融还原生产技术。
近年来, 将直接还原与熔融还原技术加以组合, 形成了COREX-Midrex联合流程, 颇受人们的关注。
直接还原铁主要生产工艺见表1。
??? 应该指出, 世界上Midrex法和HYL法应用的比较普遍, 各项技术经济指标亦趋稳定, 生产工艺成熟可靠。
特别是墨西哥的HYL法, 生产技术不断创新, 由于开发了“自重整”技术, 使建设费用减少了26% , 电炉的耗电降低了5%~6%。
印度由于缺乏天然气, 但精煤的资源丰富, 因此多采用煤基回转窑的生产方法。
透视ITmk3炼铁新工艺发展历程与技术特点

透视ITmk3炼铁新工艺发展历程与技术特点非高炉炼铁作为21世纪全世界钢铁行业的前沿技术,是未来技术发展的主要方向。
在此领域,国际冶金工作者不断进行着广泛、深入的研究和开发,形成了众多直接还原、熔融还原技术。
煤基转底炉法因其原料适应性强、操作灵活受到很多国家的重视。
日本神户制钢在过去几十年转底炉技术基础上提出了ITmk3(Ironmaking Technology Mark Three)工艺,使金属化球团在还原时能进一步熔化并实现渣铁分离,在短时间内生产出成分如生铁的高纯度粒铁产品。
该工艺突破了直接还原工艺范畴,彻底改变了直接还原产品对原料品位苛求的状况,而且还可以使用粉矿和非焦煤作原料,因而备受瞩目。
高炉-转炉工艺被称为第一代炼铁法,以气基梅德瑞克斯(MIDREX)法为代表的直接还原工艺被称为第二代炼铁法,而把煤基ITmk3工艺称作具有划时代意义的第三代炼铁技术。
目前首座ITmk3商业工厂已成功在美国投产。
1 ITmk3工艺发展过程ITmk3转底炉炼铁工艺由日本神户制钢开发。
最早的技术思想源于1994年,当时神户制钢对美国子公司梅德瑞克斯(Midrex)开发的快速融化(Fastmet/Fastmelt)法进行了一次评价试验,目的是考察适宜的反应温度和原料条件,却意外发现还未到铁的熔点时球团就熔化,而且形成的粒状小铁块与渣能干净利落地分离,所得粒铁纯度很高(铁含量为96%-97%)。
随后,神户制钢对此发现进行了一些基础实验,逐渐掌握了ITmk3的基本原理。
1996年神户制钢同Midrex子公司开始对ITmk3技术进行深入研究和改进,1999年在加古川厂区内建成了规模为年产能3000吨的中试厂,同年10月连续运转成功,到2000年12月完成了2次生产测试,其工艺设计得到实际验证。
随后ITmk3的发展转移到美国,2001年9月实施了梅萨比纳吉特(Mesabi Nugget)计划,于明尼苏达州合资建设一座年产能2.5万吨的示范工厂,成立梅萨比纳吉特公司,投资方除了神户制钢之外,还包括明尼苏达州政府、北美最大矿山公司克利夫兰·克利夫斯公司和美国第二大电炉制造厂钢动态公司(SDI),此外还得到了美国能源部(DOE)的资助,项目总投资达到2600万美元。
转底炉
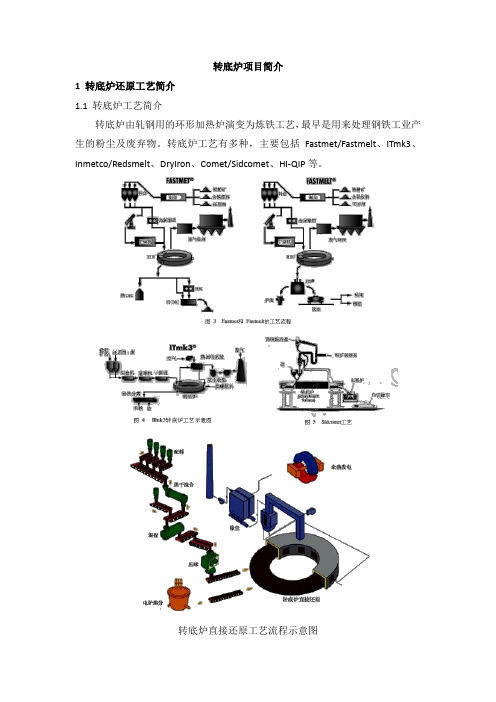
转底炉项目简介1 转底炉还原工艺简介1.1 转底炉工艺简介转底炉由轧钢用的环形加热炉演变为炼铁工艺,最早是用来处理钢铁工业产生的粉尘及废弃物。
转底炉工艺有多种,主要包括Fastmet/Fastmelt、ITmk3、Inmetco/Redsmelt、DryIron、Comet/Sidcomet、HI-QIP等。
转底炉直接还原工艺流程示意图1.2 转底炉工艺与其它相似工艺比较转底炉是煤基直接还原工艺中的核心设备之一,煤基直接还原工艺主要包括回转窑法(如SL-RN法)和转底炉法(如COMET法)。
而煤基直接还原工艺和气基直接还原工艺都是直接还原工艺,以铁产品为例直接还原工艺的产品为海绵铁(又称直接还原铁—DRI即Direct Reduced Iron)。
直接还原和熔融还原是两种主要的非高炉炼铁思路。
当转底炉的原料加入含碳球团时,其产品为金属化球团,可供电炉使用,也作为高炉的原料。
而链篦机—回转窑—环冷机(链回环)生产出来的产品是氧化球团,是为高炉炼铁提供的原料之一,称之为球团矿,而高炉炼铁的含铁原料还包括天然块矿、烧结矿。
转底炉直接还原技术采用含碳球团作原料,反应速度快,同时符合中国以煤为主要能源的特点。
以直接还原技术用于钒钛磁铁矿为例,转底炉技术相比隧道窑、回转窑工艺,以ITmk3为代表的转底炉工艺的优点主要是:○1还原原料在预热和还原过程中始终处于静止状态下随炉底一起进行,所以对生球强度要求不高;○2较高的还原温度(1350℃或更高)、反应快、效率高。
反应时间可在10-50min范围,可与矿热电炉熔炼容易实现同步热装;○3可调整喷入炉内燃料(可以是煤粉、煤气或油)和风量,能准确控制炉膛温度和炉内气氛;○4过程能耗低,回转窑法折算成每吨海绵铁的煤耗通常大于800kg,而转底炉法为600kg;○5从工艺角度来看,ITmk3技术流程简单,投资成本低,产品价格低,铁矿石原料及还原剂选择灵活。
另外,据马鞍山钢铁设计研究总院秦廷许的研究:转底炉-电炉炼铁流程与高炉传统炼铁流程比较,虽在铁精矿消耗量、还原剂和燃料的能源消耗量上相差不大,但吨铁成本低约10%;基建投资省22%左右;全流程电耗低48.6%。
直接还原铁生产工艺
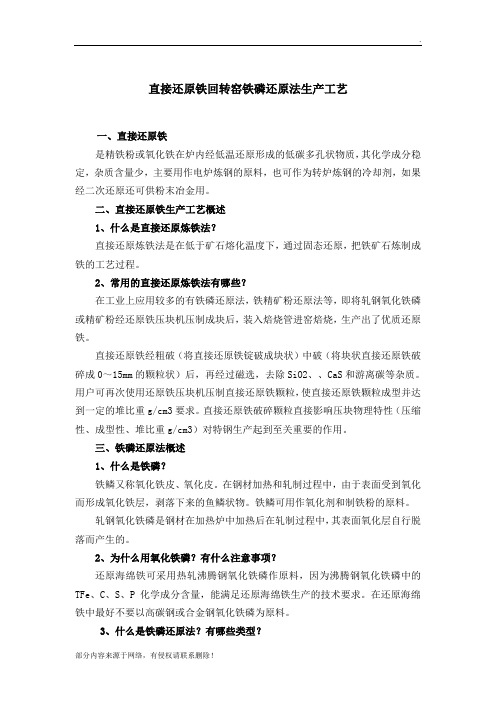
直接还原铁回转窑铁磷还原法生产工艺一、直接还原铁是精铁粉或氧化铁在炉内经低温还原形成的低碳多孔状物质,其化学成分稳定,杂质含量少,主要用作电炉炼钢的原料,也可作为转炉炼钢的冷却剂,如果经二次还原还可供粉末冶金用。
二、直接还原铁生产工艺概述1、什么是直接还原炼铁法?直接还原炼铁法是在低于矿石熔化温度下,通过固态还原,把铁矿石炼制成铁的工艺过程。
2、常用的直接还原炼铁法有哪些?在工业上应用较多的有铁磷还原法,铁精矿粉还原法等,即将轧钢氧化铁磷或精矿粉经还原铁压块机压制成块后,装入焙烧管进窑焙烧,生产出了优质还原铁。
直接还原铁经粗破(将直接还原铁锭破成块状)中破(将块状直接还原铁破碎成0~15mm的颗粒状)后,再经过磁选,去除SiO2、、CaS和游离碳等杂质。
用户可再次使用还原铁压块机压制直接还原铁颗粒,使直接还原铁颗粒成型并达到一定的堆比重g/cm3要求。
直接还原铁破碎颗粒直接影响压块物理特性(压缩性、成型性、堆比重g/cm3)对特钢生产起到至关重要的作用。
三、铁磷还原法概述1、什么是铁磷?铁鳞又称氧化铁皮、氧化皮。
在钢材加热和轧制过程中,由于表面受到氧化而形成氧化铁层,剥落下来的鱼鳞状物。
铁鳞可用作氧化剂和制铁粉的原料。
轧钢氧化铁磷是钢材在加热炉中加热后在轧制过程中,其表面氧化层自行脱落而产生的。
2、为什么用氧化铁磷?有什么注意事项?还原海绵铁可采用热轧沸腾钢氧化铁磷作原料,因为沸腾钢氧化铁磷中的TFe、C、S、P化学成分含量,能满足还原海绵铁生产的技术要求。
在还原海绵铁中最好不要以高碳钢或合金钢氧化铁磷为原料。
3、什么是铁磷还原法?有哪些类型?铁鳞还原法就是以铁鳞为原料的直接还原法生产工艺。
铁鳞还原法生产过程可分为粗还原与精还原。
在粗还原过程中,铁氧化物被还原,铁粉颗粒烧结与渗碳。
增高还原温度或延长保温时间皆有利于铁氧化物还原、铁粉颗粒烧结,但会生产部分渗碳。
鉴于在精还原过程中脱碳困难,在粗还原过程中,控制铁氧化物还原到未渗碳的程度是必要的。
- 1、下载文档前请自行甄别文档内容的完整性,平台不提供额外的编辑、内容补充、找答案等附加服务。
- 2、"仅部分预览"的文档,不可在线预览部分如存在完整性等问题,可反馈申请退款(可完整预览的文档不适用该条件!)。
- 3、如文档侵犯您的权益,请联系客服反馈,我们会尽快为您处理(人工客服工作时间:9:00-18:30)。
转底炉直接还原炼铁工艺的发展2010-02-24 17:02:19 作者:phpcms来源:浏览次数:571 网友评论 0 条一、前言为了满足冶炼高纯净钢的要求, 炼钢生产对纯净铁资源的需求越来越大。
与此同时, 优质废钢与铁资源却日益短缺其价格不断升高, 对炼钢生产影响很大, 为此,各国冶金工作者开发了许多直接还原或熔融还原工艺来为炼钢生产提供质优价廉的纯净铁资源。
但由于技术、投资等方面的原因,真正具有市场竞争力、适合于工业应用的并不多见。
同时,钢铁厂每年生产的大量含铁废弃物也给环保带来很大的压力。
如何对其进行回收利用是困扰冶金行业的一个难题。
直接还原工艺中气基法虽然具有生产效率高,生产规模大,能耗低和容易操作等优点,但必须以一次能源---天然气为还原剂,因此该工艺只能在天然气资源丰富的国家得以发展。
而煤基法以煤作为还原剂,较好的解决了气基法的不足。
目前世界上很多国家都在开发煤基直接还原新技术,有些技术已经应用于工业生产。
其中,转底炉法以其原料适应性强和操作工艺的零活性等优点,引起冶金界的高度重视。
但由于原料条件和对产品质量要求的不同,转底炉直接还原炼铁又发展为FASTMET,ITKM3和DRYIRON等不同工艺路线。
二、FASTMET工艺早在50年代Midex的前身Ross公司就发明了转底炉含碳球团直接还原法。
1964~1966年进行了2t/h规模试验。
1974年Inco公司开始研究把转底炉用于处理电炉生产不锈钢产生的氧化物粉尘的方法,并建立了一座年处理2.5万吨废料的工厂。
经转底炉预还原的球团,通过运输罐热装入电炉。
1978年美国Inmetco在宾州埃尔伍德市建成一座年处理5.6万吨电炉钢厂粉尘能力的转底炉,回收锌及可用作电炉原料的含Cr,Ni的还原铁。
1982年Mid ex公司将转底炉法命名为FASTMET,用于煤基直接还原。
神户制钢收购Midex公司后,199 5年开始建设2.5t/h示范装置,经过两年半试验后,认为Fastmet技术成熟可靠,已达到商业水平化水平。
神户制钢与三井公司合资对在美国建设年产DRI50~100万吨项目进行报价,1998年9月神户钢铁公司报价年产DRI50万吨的转底炉装置,每套售价1亿美元。
世界上首次利用FASTMET工艺以含铁废料为原料的商业化直接还原铁厂,于2000年二季度在日本新日本制铁株式会社广火田厂投产,年产能力19万吨,其中14万吨将直接装入广火田厂的氧气转炉。
神户制钢株式会社新加古川厂是第二个用该工业建设的直接还原铁厂。
2002年5月,日本神户制钢株式会社和尼日利亚签订基本协议,日方将帮助AJAOKUTA 钢公司建设一座年产50万吨的FASTMET直接还原铁工厂。
2.1 工艺流程FASTMET法的工艺流程见图1。
铁精矿(或含铁废料)、煤粉和粘结剂经混合搅拌器后进入造球机造球,生球可装入干燥器,也可直接装入转底炉。
在转底炉中,球团矿均匀地铺在炉底上,料层为1~3层球的高度。
随着炉底的旋转,球团矿被加热到1250℃~1350℃。
同时,约90%~95%的氧化铁被球团内部的固体碳还原成DRI。
球团矿在炉底停留时间一般为8~30分钟,它取决于原料的特性、球团矿层数及其他因素。
从转底炉出来的煤气经过焚化炉和热交换器将转底炉烧嘴助燃空气预热,并将高温废气用来干燥球团,生产用水循环使用,生产中产生的粉末回收利用。
2.2 工艺特点与其他直接还原工艺相比,FASTMET工艺具有以下特点:(1)以煤粉作为还原剂,摆脱了天然气地域分布不均的限制,对煤的质量也没有回转窑那么严格,故其应用地域广泛。
(2)主要设备是环形转底炉,与回转窑相比,该工艺设备简单、投资省、能耗低。
(3)对炉料的强度要求不高,因为料层很薄且随炉底一起转动,炉料既不受压,又与炉底之间没有相对运动,破碎量很少。
(4)炉料在转底炉内停留时间短(约20min),操作容易。
FASTMET法直接使用粉矿和煤粉,因而在矿石和能源上具有很好的适应性和经济性。
该法生产出的典型DRI成分主要与原料条件有关,若以铁精矿和低灰份煤为原料,生产的DRI 产品TFe可达98%,金属化率可达95%。
2.3 存在问题(1)由于采用敞焰加热,还原的铁可能会被再氧化,只有抑制这一现象才能获得较高的金属化率。
(2)燃烧燃料的选择与供应问题。
目前工业化及试验设备均用天然气或重油作燃料,使控制简化。
在气体、液体燃料较贵的地区,可以采用煤粉,但煤的储存、干燥、制粉及烟气除尘设备的投资、维护费用大。
而且污染环境,在大城市附近的工厂因环保要求严格而难于采用,使用煤气必须解决煤气稳定供应问题。
(3)由于全部还原剂均加入到球团矿内,因而还原剂中所含的灰分和有害元素将直接影响DRI的质量。
这对还原剂质量提出了较高的要求:固定碳的含量要高,灰粉及挥发分含量要低,硫磷含量也要低。
尽管如此,FASTMET法已日益引起人们的重视。
日本神户制钢株式会社新加古川厂建成了2.5t/h的试验设备,如果进展顺利,Midex公司拟在北美建设第一个工业性生产厂,年产规模45万吨,基建建设估计为6500~7500万美元。
三、干铁法MR&E公司新开发的专利技术干铁法(DRuIron)工艺是一种较理想的煤基直接还原工艺。
该工艺是由米德兰-罗斯快速加热工艺发展而来的,由于采用了无粘结剂干压块、能源利用及环保方面的最新技术,以及合理的转底炉设计,它克服了通常煤基还原带来的粉化、脉石含量高、硫高、金属化率低等缺点。
该工艺过程中的反应基于煤基直接还原动力学,加之在转底炉内的高温作用与短暂的停留时间(约10min),其操作具有巨大的灵活性,而且设备的操作控制非常容易。
煤的化学能在反应中100%得到利用,不会被其它工艺步骤(如气化等)所消耗。
尾气中的热能可回收用于发电或其他辅助工艺。
大量工业试验表明,该工艺不仅可用铁精粉矿为原料生产质量稳定的海绵铁或热压块铁,作为优质废钢的理想替代品供应电炉,而且可用于处理钢铁厂各类含铁废弃物。
所采用的转底炉工业化设备很适合规模化生产,当达到10万吨/年以上的生产规模时,效益就比较显著。
3.1 工艺流程干铁法的核心设备为转底炉,其工艺流程为:混料-冷态干法压球-转底炉焙烧-热压快。
其中,采用的冷态干法(无粘接剂)压球工艺使压制的球团无需干燥即可直接送入转底炉处理,简化了工艺步骤。
对于转底炉的加料、排料装置的改进则使得操作控制更为容易。
转底炉焙烧过程产生的尾气中蕴含着大量的化学能和热能,用余热锅炉回收产生的蒸汽或用来发电,还可用于预热助燃空气。
尾气中的粉尘与有害气体如SO2等采用喷有石灰水的布袋除尘装置去除,同时还使用MR&E公司的低NOX控制专利技术处理尾气,从而使其对环境的污染降至最低限度,尤其是通过一项称作金属氧化物粉末处理工艺的综合专利技术的使用,使得干铁法工艺不仅可用铁精矿粉作原料,而且同样适用于钢铁厂含铁粉尘的回收利用。
该专利包括一系列先进技术:无粘接剂压块,转底炉内的单层布料,高辐射加热,转底炉温控技术,各种非铁金属氧化物的有效去除。
这些技术的应用,大大地改进了海绵铁的生产。
3.2 基本原理干铁法工艺的理论基础是碳与铁氧化物之间的直接还原反应与固-固相反应动力学。
实际应用过程是将铁氧化物与煤粉或焦粉均匀混合后冷压成球,使得铁氧化物与碳紧密接触,具备良好的反应动力学条件。
然后用转底炉进行加热处理。
在炉内的高温作用下,铁氧化物与固定碳反应生成金属铁并释放CO2。
干铁法压块中固定碳与铁氧化物的理论摩尔比为1.5:1,但这实际反应过程中均会产生CO2与CO,MR&E公司在试验中摸索到控制球团中碳与铁氧化物重量之比为1.6:1较为适当。
此时,不仅生成CO2与CO,而且在反应后的球团中留有约4%的残碳,这有利于保持球团中的还原气氛,加速还原反应速度,减少再氧化的发生。
因此,该工艺的关键是要控制CO2与CO的比率,以达到尽量降低再氧化,减少碳消耗与缩短炉内停留时间的目的。
3.3 干铁法的工业试验MR&E公司在俄亥俄州匹兹堡的工业试验厂对干铁法工艺进行了试验验证。
该试验厂分别用铁精粉矿粉、电炉除尘灰及传统流程钢铁厂的废弃物为原料进行了一系列工业试验,获得了大量工业试验数据。
(1)用铁精粉矿生产海绵铁(DRI)或热压块铁(HBI)将铁精矿粉与煤粉混合压球后加入转底炉,球团在炉内受控的还原气氛中被加热。
当达到反应温度时,铁氧化物被还原为金属铁。
反应所需的热能全部由煤提供。
从转底炉出来的海绵铁带有较多显热,可采用热压块工艺加工为热压块铁,以便运输与存储。
该法生产的热压块铁TFe含量达92%,金属化率高达95%,C含量约4%,脉石含量约2.4%,S含量仅为0. 04%,可见其品质纯净,脉石与硫等杂质含量很低,可作为优质废钢的理想替代品。
而且与废钢相比,其质量均匀稳定,波动小,对于炼钢生产极为有利。
(2)回收电炉除尘灰与轧钢铁鳞电炉除尘灰与轧钢铁鳞的特点是含有较多非铁金属的氧化物,如锌、铅、镉等,被美国环保部门定为有害物质,称作KO61。
在干铁法工艺处理过程中,这些非铁氧化物将以气态逸出,并在后续的烟气处理装置中予以收集,此时KO61已转化为提炼有价值非铁金属的原料。
球团中ZnO脱除率高于95%,生成的海绵铁金属化率高达91%。
转底炉焙烧含锌粉尘时以气态逸出的非金属氧化物在尾气处理过程中,由布袋除尘器收集,可作为提炼锌的原料使用。
(3)回收钢铁厂传统废弃物传统钢铁厂废弃物包括转炉尘泥,热轧污泥,连铸氧化铁皮及高炉粉尘与瓦斯泥。
这些物质总体来说碳含量很高,与电炉除尘灰相比,锌含量低,而铅、镉含量极少。
灰泥原料中的铁与碳含量较高,经转底炉焙烧后,生成的海绵铁金属化率高于90%,其尾气收尘富含Z nO,可以回收增加收入。
干铁法工艺的投资与效益估算。
建造年产100万吨海绵铁的生产厂的单位投资成本约1 25美元/(t.a),由于干铁法可以用较便宜的铁精粉矿作原料,用非炼焦煤做热源及还原剂,所以原料与能源价格较低,单位生产成本约为72美元/吨DRI。
干铁法工艺不仅在能源及原料结构上特别适合中国的国情,而且在投资与生产运行成本上都比传统的直接还原工艺法更有竞争力。
干铁法工艺用优质铁矿粉生产的海绵铁及热压块铁作为优质废钢的替代品供应电炉,所带来的效益十分显著,这主要源于其稳定均匀的成分与质量,与废钢相比,其质量与成分波动小,对稳定钢水质量有利。
且其生产成本不会象废钢价格那样随市场变化产生较大波动,对稳定电炉生产非常有利。
四、Itmk3工艺Itmk3是由神户钢铁公司开发的一种新型炼钢技术。
它是一种灵活、环保的一步法生产粒铁块的方法,其产品质量与高炉生铁相当。
神户钢铁公司视Itmk3为第三代炼铁方法。
第一代炼铁方法定义为高炉炼铁法,第二代则是包括Midrex技术在内的气基直接还原法。