产品不良分类
产品不良应对策略
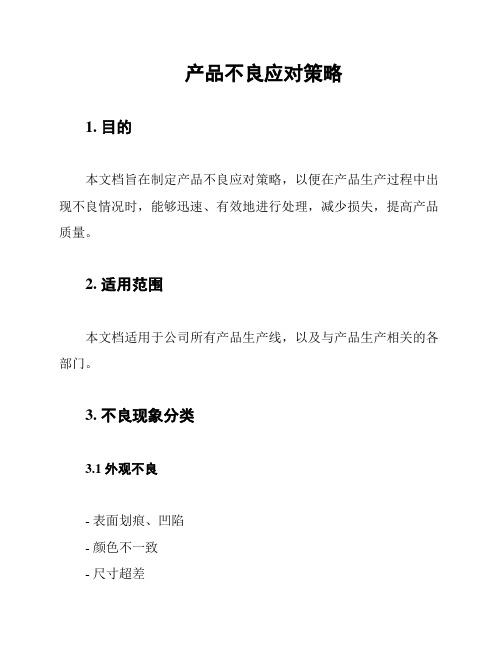
产品不良应对策略1. 目的本文档旨在制定产品不良应对策略,以便在产品生产过程中出现不良情况时,能够迅速、有效地进行处理,减少损失,提高产品质量。
2. 适用范围本文档适用于公司所有产品生产线,以及与产品生产相关的各部门。
3. 不良现象分类3.1 外观不良- 表面划痕、凹陷- 颜色不一致- 尺寸超差3.2 功能不良- 性能不稳定- 故障率高- 无法满足使用要求3.3 结构不良- 组装困难- 结构松动- 部件脱落3.4 包装不良- 包装破损- 标识不清- 防护措施不足4. 不良现象原因分析4.1 原材料问题- 材质不达标- 供应商质量问题4.2 生产设备问题- 设备精度不足- 设备维护不当4.3 生产工艺问题- 工艺不合理- 操作不规范4.4 人员素质问题- 技能不足- 责任心不强5. 不良现象应对措施5.1 外观不良- 加强质量培训,提高员工对产品外观的认识- 优化生产工艺,减少外观缺陷产生- 加强原材料验收,严控原材料质量5.2 功能不良- 对产品进行功能测试,确保产品出厂前符合要求- 对生产设备进行精度校准,保证生产过程稳定- 加强过程质量控制,及时发现并处理功能问题5.3 结构不良- 优化产品设计,提高结构稳定性- 加强组装过程质量控制,确保部件装配正确- 定期对生产设备进行维护和校准5.4 包装不良- 加强包装工艺培训,提高包装质量- 选择合格包装材料,确保包装防护效果- 加强包装过程质量控制,确保标识清晰、完好6. 不良现象记录与反馈6.1 建立不良现象记录表,详细记录不良现象、原因、数量等信息6.2 对不良现象进行定期统计、分析,找出共性问题,制定改进措施6.3 将不良现象记录反馈给相关部门,促使改进生产工艺、提高产品质量7. 培训与监督7.1 对员工进行质量培训,提高其质量意识及技能水平7.2 加强生产过程的监督与检查,确保各项措施得以执行7.3 定期对质量管理体系进行评审,持续改进,提高产品质量8. 文件修改记录本文档涉及的内容和措施会根据实际情况进行持续更新和完善,以适应公司产品质量管理的需求。
产品质量问题的分类
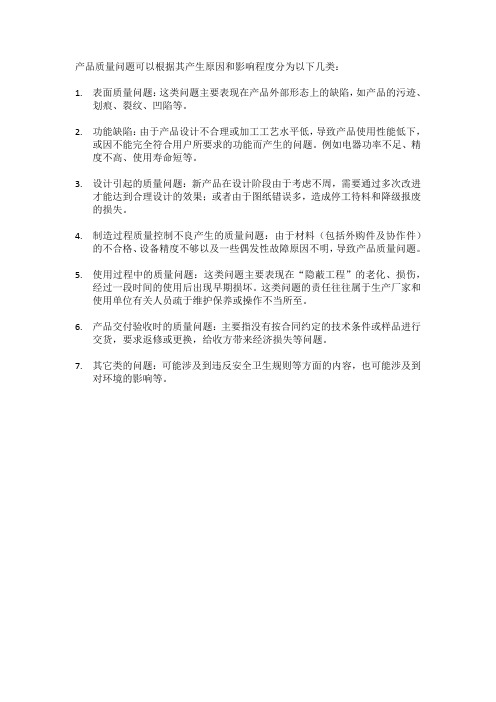
产品质量问题可以根据其产生原因和影响程度分为以下几类:
1.表面质量问题:这类问题主要表现在产品外部形态上的缺陷,如产品的污迹、
划痕、裂纹、凹陷等。
2.功能缺陷:由于产品设计不合理或加工工艺水平低,导致产品使用性能低下,
或因不能完全符合用户所要求的功能而产生的问题。
例如电器功率不足、精度不高、使用寿命短等。
3.设计引起的质量问题:新产品在设计阶段由于考虑不周,需要通过多次改进
才能达到合理设计的效果;或者由于图纸错误多,造成停工待料和降级报废的损失。
4.制造过程质量控制不良产生的质量问题:由于材料(包括外购件及协作件)
的不合格、设备精度不够以及一些偶发性故障原因不明,导致产品质量问题。
5.使用过程中的质量问题:这类问题主要表现在“隐蔽工程”的老化、损伤,
经过一段时间的使用后出现早期损坏。
这类问题的责任往往属于生产厂家和使用单位有关人员疏于维护保养或操作不当所至。
6.产品交付验收时的质量问题:主要指没有按合同约定的技术条件或样品进行
交货,要求返修或更换,给收方带来经济损失等问题。
7.其它类的问题:可能涉及到违反安全卫生规则等方面的内容,也可能涉及到
对环境的影响等。
不良品统计分析报告
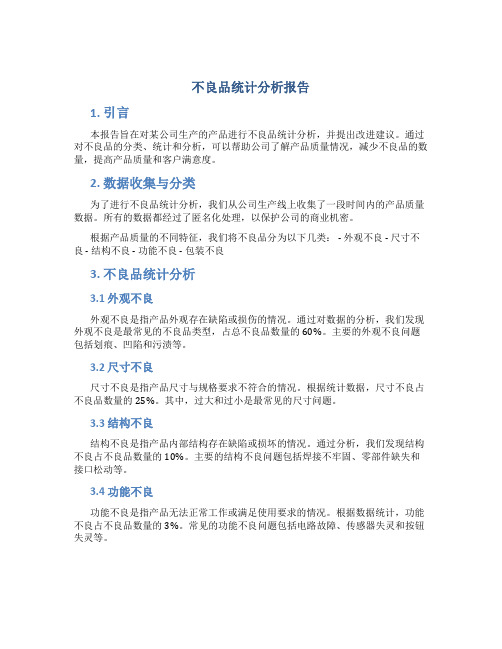
不良品统计分析报告1. 引言本报告旨在对某公司生产的产品进行不良品统计分析,并提出改进建议。
通过对不良品的分类、统计和分析,可以帮助公司了解产品质量情况,减少不良品的数量,提高产品质量和客户满意度。
2. 数据收集与分类为了进行不良品统计分析,我们从公司生产线上收集了一段时间内的产品质量数据。
所有的数据都经过了匿名化处理,以保护公司的商业机密。
根据产品质量的不同特征,我们将不良品分为以下几类: - 外观不良 - 尺寸不良 - 结构不良 - 功能不良 - 包装不良3. 不良品统计分析3.1 外观不良外观不良是指产品外观存在缺陷或损伤的情况。
通过对数据的分析,我们发现外观不良是最常见的不良品类型,占总不良品数量的60%。
主要的外观不良问题包括划痕、凹陷和污渍等。
3.2 尺寸不良尺寸不良是指产品尺寸与规格要求不符合的情况。
根据统计数据,尺寸不良占不良品数量的25%。
其中,过大和过小是最常见的尺寸问题。
3.3 结构不良结构不良是指产品内部结构存在缺陷或损坏的情况。
通过分析,我们发现结构不良占不良品数量的10%。
主要的结构不良问题包括焊接不牢固、零部件缺失和接口松动等。
3.4 功能不良功能不良是指产品无法正常工作或满足使用要求的情况。
根据数据统计,功能不良占不良品数量的3%。
常见的功能不良问题包括电路故障、传感器失灵和按钮失灵等。
3.5 包装不良包装不良是指产品包装存在损坏或不完整的情况。
通过数据分析,我们发现包装不良占不良品数量的2%。
常见的包装问题包括破损、缺少标签和错误的封装方式等。
4. 不良品原因分析通过对不良品统计数据的分析,我们可以初步确定不良品产生的主要原因: 1. 员工技能不足:部分员工缺乏必要的技能和经验,导致生产过程中操作不规范,增加了不良品的产生风险。
2. 设备故障:生产设备存在故障或老化问题,影响了产品质量的稳定性。
3. 原材料质量不稳定:某些原材料的质量不稳定,导致生产过程中难以控制产品的质量。
不良品的处理流程及注意事项
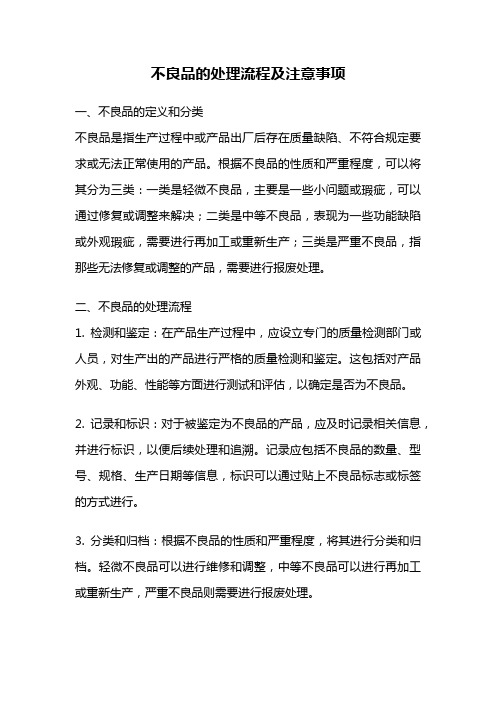
不良品的处理流程及注意事项一、不良品的定义和分类不良品是指生产过程中或产品出厂后存在质量缺陷、不符合规定要求或无法正常使用的产品。
根据不良品的性质和严重程度,可以将其分为三类:一类是轻微不良品,主要是一些小问题或瑕疵,可以通过修复或调整来解决;二类是中等不良品,表现为一些功能缺陷或外观瑕疵,需要进行再加工或重新生产;三类是严重不良品,指那些无法修复或调整的产品,需要进行报废处理。
二、不良品的处理流程1. 检测和鉴定:在产品生产过程中,应设立专门的质量检测部门或人员,对生产出的产品进行严格的质量检测和鉴定。
这包括对产品外观、功能、性能等方面进行测试和评估,以确定是否为不良品。
2. 记录和标识:对于被鉴定为不良品的产品,应及时记录相关信息,并进行标识,以便后续处理和追溯。
记录应包括不良品的数量、型号、规格、生产日期等信息,标识可以通过贴上不良品标志或标签的方式进行。
3. 分类和归档:根据不良品的性质和严重程度,将其进行分类和归档。
轻微不良品可以进行维修和调整,中等不良品可以进行再加工或重新生产,严重不良品则需要进行报废处理。
4. 维修和调整:对于轻微不良品,可以通过维修和调整来解决问题。
维修可以包括更换部件、修补损坏等操作,调整可以包括重新调整参数、校准仪器等操作。
维修和调整应由专业人员进行,确保修复后的产品符合质量要求。
5. 再加工或重新生产:对于中等不良品,可以进行再加工或重新生产来修复问题。
再加工包括修复外观瑕疵、改进功能缺陷等操作,重新生产则需要重新制造符合要求的产品。
再加工和重新生产应按照标准流程和要求进行,确保产品质量。
6. 报废处理:对于无法修复或调整的严重不良品,应进行报废处理。
报废处理可以包括销毁、回收或处理成其他材料等方式。
报废处理应符合环保要求,防止对环境造成污染。
三、不良品处理的注意事项1. 及时处理:对于不良品,应及时进行处理,以避免对生产和客户造成不必要的影响。
处理不良品的时间越短,损失也就越小。
不良品管理办法
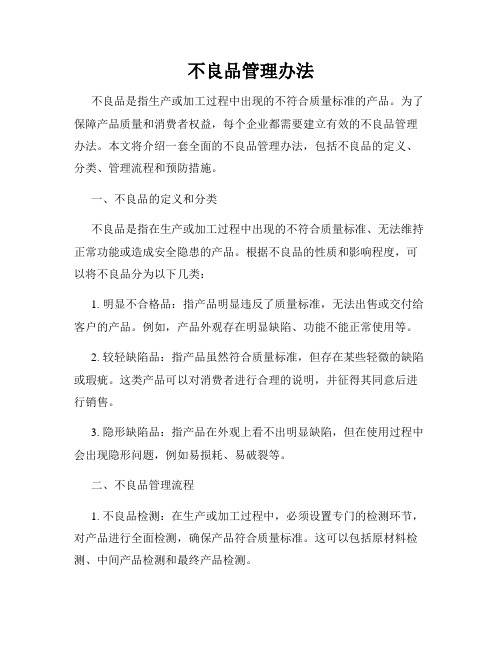
不良品管理办法不良品是指生产或加工过程中出现的不符合质量标准的产品。
为了保障产品质量和消费者权益,每个企业都需要建立有效的不良品管理办法。
本文将介绍一套全面的不良品管理办法,包括不良品的定义、分类、管理流程和预防措施。
一、不良品的定义和分类不良品是指在生产或加工过程中出现的不符合质量标准、无法维持正常功能或造成安全隐患的产品。
根据不良品的性质和影响程度,可以将不良品分为以下几类:1. 明显不合格品:指产品明显违反了质量标准,无法出售或交付给客户的产品。
例如,产品外观存在明显缺陷、功能不能正常使用等。
2. 较轻缺陷品:指产品虽然符合质量标准,但存在某些轻微的缺陷或瑕疵。
这类产品可以对消费者进行合理的说明,并征得其同意后进行销售。
3. 隐形缺陷品:指产品在外观上看不出明显缺陷,但在使用过程中会出现隐形问题,例如易损耗、易破裂等。
二、不良品管理流程1. 不良品检测:在生产或加工过程中,必须设置专门的检测环节,对产品进行全面检测,确保产品符合质量标准。
这可以包括原材料检测、中间产品检测和最终产品检测。
2. 不良品分类:根据不良品的性质和影响程度,对不良品进行分类,并进行记录和统计。
例如,可以建立不良品库,对明显不合格品进行集中存放和管理。
3. 不良品追溯:针对发现的不良品,需要进行追溯,找出问题出现的原因,并采取相应的纠正措施。
这可以包括对生产设备、操作流程、人员培训等方面进行改进。
4. 不良品处理:对于不同类型的不良品,需要采取不同的处理方式。
明显不合格品可以进行退货、报废或重新加工;较轻缺陷品可以通过修复或降价出售;隐形缺陷品需要通过改进设计和生产工艺来解决。
5. 不良品改进:根据不良品管理的经验总结,不断改进产品设计、生产工艺和质量控制措施,以降低不良品发生的概率。
三、不良品预防措施为了避免不良品的发生,企业可以采取以下预防措施:1. 加强供应商管理:与供应商建立稳定的合作关系,确保供应的原材料和零部件符合质量要求。
不良品的处理流程及注意事项
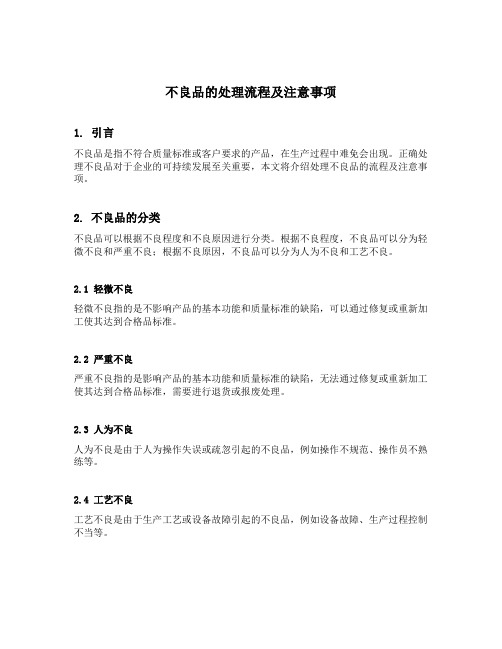
不良品的处理流程及注意事项1. 引言不良品是指不符合质量标准或客户要求的产品,在生产过程中难免会出现。
正确处理不良品对于企业的可持续发展至关重要,本文将介绍处理不良品的流程及注意事项。
2. 不良品的分类不良品可以根据不良程度和不良原因进行分类。
根据不良程度,不良品可以分为轻微不良和严重不良;根据不良原因,不良品可以分为人为不良和工艺不良。
2.1 轻微不良轻微不良指的是不影响产品的基本功能和质量标准的缺陷,可以通过修复或重新加工使其达到合格品标准。
2.2 严重不良严重不良指的是影响产品的基本功能和质量标准的缺陷,无法通过修复或重新加工使其达到合格品标准,需要进行退货或报废处理。
2.3 人为不良人为不良是由于人为操作失误或疏忽引起的不良品,例如操作不规范、操作员不熟练等。
2.4 工艺不良工艺不良是由于生产工艺或设备故障引起的不良品,例如设备故障、生产过程控制不当等。
3. 不良品的处理流程正确的不良品处理流程可以最大程度地减少损失和影响,以下是一个常用的不良品处理流程:3.1 检测和识别在生产过程中需要对产品进行全面的检测和识别,及时发现不良品。
可以通过设立检测点或检测工艺,使用检测设备和工具,进行抽样检测等方法。
3.2 记录和分类对每个发现的不良品进行记录,并根据不良程度和不良原因进行分类。
记录需要包括不良品的数量、照片、不良原因等信息,以便后续处理和分析。
3.3 制定处理方案根据不同的不良品情况,制定针对性的处理方案。
轻微不良可以通过修复或重新加工来达到合格品标准;严重不良需要进行退货或报废处理。
3.4 处理不良品根据制定的处理方案进行相应的操作。
对于轻微不良,可以进行修复或重新加工;对于严重不良,需要按照退货或报废的程序进行处理。
3.5 分析原因并改进处理完不良品后,需要对不良原因进行分析和总结。
通过分析原因,及时采取措施改进生产过程,避免同类问题的再次发生。
4. 不良品处理的注意事项在处理不良品时,还需要注意以下事项:4.1 及时处理发现不良品后,需要及时进行处理,避免不良品的数量和影响进一步扩大。
质量控制部门不良品分析

质量控制部门不良品分析在现代生产和制造行业中,质量控制部门扮演着至关重要的角色。
他们负责检查和评估产品的质量,以确保公司生产的产品符合质量标准和客户需求。
在这个过程中,不可避免地会出现不良品,而质量控制部门也需要进行分析和处理这些不良品,以改进生产流程和保持产品的高质量。
1. 不良品的定义和分类不良品是大多数公司都会遇到的问题,它们指的是不符合质量标准的产品。
不良品主要可以分为三类:外观不良、功能不良和结构不良。
外观不良指的是产品在外观方面存在瑕疵,比如划痕、污渍等;功能不良则是产品无法正常使用或无法达到预期的性能指标;结构不良是指产品在组装或制造过程中存在的问题,比如松动、断裂等。
2. 不良品分析的重要性不良品分析是质量控制部门必不可少的一项工作。
它可以帮助质量控制部门确定不良品的具体原因,并提供解决方案以确保类似问题不再发生。
通过不良品分析,可以深入了解产品的生产流程、质检环节和可能存在的隐患,为质量改进提供有力的依据。
3. 不良品分析的步骤(1)收集和记录不良品信息:质量控制部门需要及时收集和记录不良品的相关信息,包括不良品数量、不良品类型、出现的时间和地点等。
这些信息对于后续的分析和处理非常重要。
(2)排查不良品的原因:通过对不良品进行排查和分析,确定造成不良品的主要原因。
这涉及到对生产流程、材料选择、人工操作等各个环节进行仔细检查和排查。
(3)制定改进方案:根据不良品的原因和分析结果,制定相应的改进方案。
这可能包括修改生产工艺、改进操作规范、优化原材料选择等措施,以减少或消除不良品的发生。
(4)实施改进方案:质量控制部门需要和生产部门紧密合作,确保改进方案的顺利实施。
这可能涉及到培训员工、更新设备、改变工作流程等措施。
(5)监测和评估效果:改进方案实施后,质量控制部门需要持续进行监测和评估,以确保改进措施的有效性。
如果有必要,还可以适时调整和改进改进方案。
4. 不良品分析的技术工具随着科技的进步,质量控制部门可以借助一些先进的技术工具来提高不良品的分析效率和准确性。
问题产品不良处置方案

问题产品不良处置方案在生产制造过程中,难免会出现一些问题产品,这些不良产品的产生会对生产工艺、成本以及企业品牌形象等方面造成不利影响。
为了更好地解决问题产品,厂家需要制定出一些不良处置方案,以最小化损失并避免不可预知的风险。
1. 不良产品分类在制定不良处置方案前,我们需要先了解不良产品的分类,这样才能制定出更合理、更具针对性的处置方案。
通常情况下,不良产品可以分为以下几类:1.返修品:生产过程中,出现一些小问题需要重新加工或修补的产品。
2.报废品:因综合考虑成本等因素,将产品报废并不进行修缮的产品。
3.回收品:将不良产品进行再利用或重新回收制造成产品的过程中所需要的废弃材料。
2. 不良处置方案针对不同类型的不良产品,我们需要制定出相应的不良处理方案,以下介绍一些可能适用的方案:2.1 返工或返修对于一些有潜在价值的产品,如存在轻微瑕疵等需要进行修缮时,可以考虑返工或返修。
返工或返修的步骤:1.识别问题及其原因为了避免重复发生问题,必须找出问题原因,并充分考虑如何避免相似的问题在未来的生产中发生。
2.检查报告和机加工画面检查报告和机加工画面以确保返修项目的范围、要求和成功衡量标准都是正确的。
3.修改文档更新所有与产品类别、工序、操作指导和检查要求相关的文档,以便在以后的生产周期中改进该问题。
4.审核结果在返修完成后,必须对修复结果进行审核,确保所有问题都得到解决。
返工或返修依旧带来了一定的成本,需在产品成本计算基础上审核是否进行返工或返修。
2.2 报废处理在一些不可再修复的情况下,我们需要考虑报废处理。
针对报废处理,我们需要考虑如何将报废成本降低到最低。
报废处理的步骤:1.评估报废成本企业应当评估报废产品的成本,如人工成本、材料成本、环境污染等因素。
2.遵守相关法规企业在报废处理过程中无论是内部还是外部,都应严格遵守相关法规和政策。
3.建立收集机制企业可以根据产品特征建立收集机制,产品收集后可以进行分类、拆卸等处理方式。
- 1、下载文档前请自行甄别文档内容的完整性,平台不提供额外的编辑、内容补充、找答案等附加服务。
- 2、"仅部分预览"的文档,不可在线预览部分如存在完整性等问题,可反馈申请退款(可完整预览的文档不适用该条件!)。
- 3、如文档侵犯您的权益,请联系客服反馈,我们会尽快为您处理(人工客服工作时间:9:00-18:30)。
注射料成型的制件,在不良操作情况下,会出现不满、飞边、表面凹陷,尺寸变化等缺陷。
这些缺陷可能是模具设计,注射机台精度等造成,也可能是操作人员没有掌握好适当的工艺条件而造成。
因素错综复杂、变化纷繁,而又互为影响的。
在此,我们请教相关专业技术人员,搜集国内外解决此类缺陷资料希望能为您在生产过程中注塑成品率的提高有所帮助,这是我们的良好的目的。
但鉴于我们的能力,本公司发布的解决措施,仅供您参考。
我们不负任何的法律责任。
◆注塑成型部分产品不良的解决措施一、注塑成型部分(注塑成型时发生不良现象的主要原因)二、处理不良现象的措施1、模具的缺陷2、塑料树脂的缺陷3、不适合的成型制件4、产品设计的上问题5、对成型机性能的过大评价6、周围环境的变化1、表面起膜2、飞边3、透明性低下4、异色、褪色5、表面突起6、未填满7、流痕8、黑线9、成型收缩10、黑斑11、银线12、熔接线13、破裂、白化1. 表面起膜树脂的添加剂流经产品表面时,形成的白色、灰色的蔓延现象被称为表面起膜。
产生的主要原因:1、树脂内部的添加剂是主要原因1、造成过度应力的注塑条件等也是引发原因2. 飞边产生的主要原因1、注塑机加工不良2、注塑机容量不足3、加工条件不良4、锁模力不足5、模具贴得不紧6、模具的变形7、树脂流动太好8、Gas Vent过大9、注塑压力较大10、模具面上存在异物对成型品的尺寸产生影响的因素多种多样,其主要变数有模具、产品形状、成型条件及后工程、树脂的种类等。
3. 透明性低下PPS、SAN等透明产品出现的透明性低下的现象产生的主要原因1、脱模剂使用过多2、混入其它树脂3、混入其它型号4、模具的加工状态,模具温度等加工条件不合适。
4. 异色、褪色产品的颜色与标准颜色不同的现象。
树脂颜色不同为异色;注塑后颜色发生改变的现象为变色。
产生的主要原因1、着色错误2、树脂污染3、过多使用粉碎品4、注塑机污染5、树脂的热化等5. 表面突起产生的主要原因1、原料内混入异物2、颜料未分散3、模具加工状态4、使用再利用原料6. 未填满树脂没有填满Cavity的全部,冷却凝固后成型品的一部分出现不足的现象。
1.进料调节不当A缺料 B多料2.注射压力不妥3.料量过低4.模具温度低或温度分布不合理5.塑料流动性高6.喷嘴配合不良7.塑料熔块堵塞加料通道8.喷嘴冷料入模9.模具设计不合理10.模具浇注系统有缺陷7. 流痕树脂的流动痕迹在产品表面表现出来的现象。
产生的主要原因1、绝大部分是由于树脂填充到模具内时树脂温度降低。
2、混入其它树脂。
3、树脂的分解。
4、模具的排气不良8. 黑线产品表面形成黑色线条的现象挥发物润滑剂或脱膜剂树脂的热化黑色颜料注塑要清洁不良模具表面受到污染(油、油脂等异物)排气不良成型机的老化及损伤过多使用再利用原料9. 成型收缩(a)随模具的设计及成型品的形状而产生的差异。
随Gate的位置、形状、面积、尺寸会有所不同通常Gate 附近所承受的注塑压较高,因此收缩较小。
当Gate及Runner面积较大、Runner的长度较短时收缩较小。
随模具温度及偏差,各部位的尺寸会有所不同。
模具随加工的尺寸公差而变形,因此收缩尺寸也会有不同。
按取出产品的方法而产生变形,因此尺寸也会改变。
(b)按产品的形状引起的收缩差异。
按产品厚度不同成型收缩也不,通常较厚的部分收缩较大。
(c)成型品尺寸随成型条件的变化按成型温度与模具温度,成型收缩不同。
同一Cavity压力下,通常温度越高收缩越大。
保压与注塑压力越大收缩越小。
同一Cavity压力下,填充、保压时间越增加,收缩越小。
与成型品不相适应的成型机大小(锁膜压、容量)也会对成型品的尺寸产生影响。
螺杆的防止回流Ring发生磨损时,适宜的注塑压不能传到成型品上,而且因计量不均匀,可发生较大的成型收缩。
收缩率随树脂不同出现的差异:玻璃纤维等填充剂得到补充的话,收缩率会变小;随树脂吸收水份的程度,尺寸也会有所不同。
10. 黑斑产品表面形成的小黑点、蓝点。
因注塑机环境,作业环境,树脂的清洁状态而引起的11. 银线[1] 产生的主要原因(a)因原料含有水份及挥发物由于原料干燥不足以及其它原因,超过适当的水份含量时,因为水份面加速了热分解及气体的产生。
夏季雨天时,因酷热的温度和较大的湿度,在移动原料或经长期保管时,吸收了较多的水份,因此不能以一般干燥条件来干燥,应使用除干燥机交原料进行较长时间的干燥。
(b)由于树脂的热分解通常,树脂应在适宜的使用范围内设定成型温度。
若在较高的成型温度下作业时,会由于热分解而导致产生银线及引起物性低下。
选择适合成型品的注塑成型机。
(产品重量一般为料筒容量的40-80%)加热器及热电偶接触不良时,实际设定温度正常或Barrel的一部分受到局部加热,也会出现银线。
[2] 预防的对策(a)成型条件注塑过程:填充到模具内时,所产生的气体应排出到模具外。
计量过程:螺杆转速过高的话,料筒温度上升,以致加速树脂扮解及气体的产生,因此应保持适当的螺杆速度。
而且以适宜的背压最大限度地抑制已达到可塑化的树脂之间的空隙与气体的流入。
(b)模具模具形状,设计模具时应考虑到填充时会导致流动阻碍的产品的深度差及厚度差。
模具内应设置有效的Gas Vent。
长期大量生产时,树脂产生的气体残量累积在模具的Vent部分,这也是造成Gas Vent堵塞,致使银线等不良现象产生的直接原因。
12. 熔接线成型品表面形成细线的现象。
熔接线发生在注塑成型时熔融树脂合流的地方。
熔融树脂填充凝固后,树脂互相遇合的界面显示在表面上,致使强度及外观降低。
出现在具有两个以上Gate的产品中或Hole,厚度存在差异的成型品上。
作为成型条件是不可避免的现象。
设计模具时,在改变Gate位置及厚度的同时,将有可能产生熔接线的部分移动到强度及外观质量不是重要的位置。
[1] 产生的主要原因熔接线位置不良及流动性不足。
(对策:增加树脂及模具温度,增加注塑压力及速度)模具内存在空气或挥发物时。
(对策:用酒精、香蕉水等清扫,设置Gas Vent)因脱模剂,着色剂等。
Gate位置不良时。
(对策:调整模具等)[2] 针对不良现象的详细对策(a)通过调节成型条件,降低熔接线的鲜明度,或改变位置或填充时使树脂的凝固达到最小化。
树脂温度及模具温度上升注塑速度及注塑压力上升保压及保压时间上升(b)设计模具时,将熔接线的位置移动到外观及强度不是很重要的地方。
扩大Weld部分的Gas Vent改变Gate位置及使Gate个数达到最适宜化增加产品厚度(c)原材料的充分干燥(抑制气体的产生)13. 破裂、白化广义的破裂包括破裂及细微破裂的Crazing。
接产生的原因可以分为机械性破裂与化学应力破裂。
[1] 机械性破裂(Mechanical Crack)作用于塑料上的物理性作用力比塑料固有物性及结构上的支持力大的时候,因随不了而产生破裂。
为了防止破裂的产生,在进行产品设计时,须引起注意。
设计时,选好所使用的材料与型号后,应考虑到作用于物体上的外力,设计出既可反映稳定率又可以分散作用力的结构。
提高结构上的支持力时,可加大产品的厚度或加固Rib,也可设计成Round 结构以分散作用力。
[2]化学应力破裂(ESC Crack)化学应力破裂(ESC:Environmental Stress Crack)是指因化学药品的作用,塑料膨胀,从而加重了内部应力,致使总应力值高出塑料的破坏强度而产生的破裂。
化学应力破裂在成型品的装配过程中,使用润滑剂、洗剂等时,其所含有的一部分物质可诱发产品破裂。
根据产品的脆弱结构、残留应力标准,是否产生破裂存在一定的差异,受温度压力等的影响。
因化学药品造成的破裂,其破裂面根干净,有时会产生光泽,可轻易得到确认。
为了防止因化学应力引起的破裂,工艺上应禁止使用可诱发破裂的化学药品。
在用户的使用条件下,会形成问题的配件应通过改变材料等方法作到防患于未燃。
引发化学应力破裂的化学药品如下:冰乙酸、增塑剂(DOP等)。
酒精类、石蜡系列的油脂、酯、过多的硅系列脱模剂、汽油石油等油类、豆油等食用油、溶剂类等。
◆压出成型部分二、压出成型部分(压出成型加工时产生不良现象的主要原因)1、不稳定的压出(挤压不稳定)2、树脂的分解(降级)3、压出机的问题4、原料上的问题2. 树脂的分解:压出工艺中因树脂的分解而经常出现的问题包括变色、物性低下、产生气体等等。
究其原因可分为热分解、化学性分解、机械性分解,依Radiation的分解及生物学性的分解等。
大多数分解因复合性原因引起。
当两种以上的原因共存时,可加速分解。
[1]树脂分解的种类热分解:树脂处于高温时会产生分解,树脂本身的热稳定性决定其分解程度。
通常,发生单纯热分解的情况很少,绝大多数发生的是热化学性分解。
机械性分解:因作用于树脂的机械性应力引起的树脂分子断裂,不论是固态还是熔融状态都有可能发生。
压出工艺中主要发生在熔融状态。
机械应力作用于树脂分子的话,起应力将集中在较长的高分子链的中心,因此在分子链的中间折断的概率较高。
因机械应力引起的树脂分解,其结果使树脂的个体分子量减少到1/2、1/4、1/8。
几乎所有机械性分解都伴随有热分解,据情况不同,有时也伴有化学性分解。
压出机内部,位于螺杆与Barrel中间的Clearance形成的应力最大,局部温度也上升的较大,树脂的分解也会进行得很好。
化学性分解:当树脂产生反应而引起分解的物质存在时才会发生化学性分解。
此物质包括酸类、碱类、溶剂、具有反应性的气体等等。
即使存在这些物质,化学性分解也主要发生在高温条件下,且温度越高反应速度越快。
最典型的例子有水解和氧化反应,为防止水解最重要的是除去树脂所含有的水份,因此压出成型前须进行干燥;为了防止树脂的氧化,关键是要适当选择,使用抗氧化剂。
压出工艺中的树脂分解:大多数情况以热分解、机械分解、化学分解相综合的形态发生。
滞留时间越长、滞留时间颁越广、树脂温度越高,树脂的分解速度越快。
比起其它的部位来,Clearance处的温度上升得非常高,因此在此部位发生分解的概率最大。
压出工艺中减少树脂分解的方案缩短滞留时间及保持较小范围的滞卵巢时间分布清除诱发分解的物质压出机内,吐出量越大树脂的平均滞留时间越小,因此以最适宜的螺杆设计得到最大的吐出量的话,对抑制树脂分解会有一定的帮助。
减少压出机内的流动阻力,消除停滞点的设计也是防止树脂分解的一顶措施。
发生热氧化分解时,为了阻止树脂与氧气的接触,将压出工艺置于氮气中,从而可抑制树脂的分解。
3. 压出机的问题压出机本身的机械性质的变化关系到压出特性的变化,可引起几种压出不良的产生。
这种机械性变化或故障发生最多的地方是驱使装置和加热、冷却装置、螺杆或因桶磨损的烦恼等。