新产品试生产记录
试生产流程

编号:SSTS/QPC3-2页码:第1页共5页试生产流程1. 目的:新产品试制验证合格后,模拟批量生产来验证是否具备批量生产新产品的能力。
2. 适用范围:本流程规定了新产品试生产过程的管理。
3. 术语:首批样品:是从一日生产或PPAP生产中抽取的已验证为合格的样品。
试生产周期:1个班模具验收:模具验收是试生产的主要部分,在试生产Ⅰ:产品验证合格后,PPAP审核前,主要是为了验证生产过程和质量控制过程,暴漏过程问题,侧重点在模具问题和生产工艺过程验证。
特殊情况下,试生产1和PPAP审核可以合并一起进行。
试生产Ⅱ:PPAP审核后,主要验证试生产Ⅰ过程中遇到的问题是否得到解决和关闭,生产过程是否按照工艺流程规划执行;4. 职责分配4.1生产部为本程序的归口管理部门,负责试生产执行,需验证班产统计。
4.2项目负责组织对委外模具的验证工作,负责试生产前的管理和监控工作,协调小组成品(项目组)全程参与,对过程审核中的不合格项的整改进行跟踪。
4.3生产计划负责新品试生产计划编制、试生产和订单所需要的原材料、外协件、包装箱等物料点检,并控制物料库存;负责安排新品试生产计划和生产计划并下达生产指令;负责各工序物料的出入路、存储等工作。
4.4采购部根据项目部下达的试生产物料需求采购物料。
4.5工程部负责对自制模具、工装的验收,并配合项目部对委外模具进行验收工作,负责注塑工艺单的编制。
4.6 品保部负责对试生产进行过程审核和工序合格率统计,负责对检具的验收等工作。
编号:SSTS/QPC3-2页码:第2页共5页5. 流程说明5.1新品试生产流程图编号:SSTS/QPC3-2页码:第3页共5页5.2流程说明项目部负责人根据项目进度召开试生产准备会议;(1)介绍新项目目前进度,现阶段情况,确定安排试生产的时间(2)各部门根据《试生产条件检查表》去准备,项目部根据《试生产条件检查表》在规定时间内对以下5大项内容进行确认,齐全的打“√”,缺失的打“×”。
生产线试产验收报表
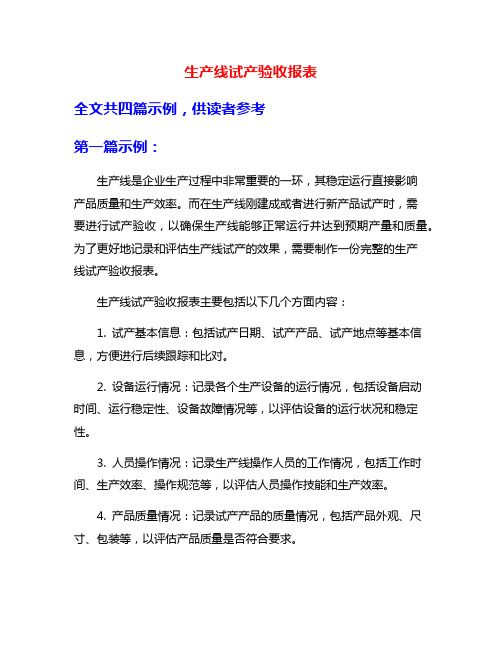
生产线试产验收报表全文共四篇示例,供读者参考第一篇示例:生产线是企业生产过程中非常重要的一环,其稳定运行直接影响产品质量和生产效率。
而在生产线刚建成或者进行新产品试产时,需要进行试产验收,以确保生产线能够正常运行并达到预期产量和质量。
为了更好地记录和评估生产线试产的效果,需要制作一份完整的生产线试产验收报表。
生产线试产验收报表主要包括以下几个方面内容:1. 试产基本信息:包括试产日期、试产产品、试产地点等基本信息,方便进行后续跟踪和比对。
2. 设备运行情况:记录各个生产设备的运行情况,包括设备启动时间、运行稳定性、设备故障情况等,以评估设备的运行状况和稳定性。
3. 人员操作情况:记录生产线操作人员的工作情况,包括工作时间、生产效率、操作规范等,以评估人员操作技能和生产效率。
4. 产品质量情况:记录试产产品的质量情况,包括产品外观、尺寸、包装等,以评估产品质量是否符合要求。
5. 生产工艺流程:记录生产线试产的工艺流程,包括原料投入、加工流程、生产工艺等,以评估工艺流程的合理性和稳定性。
6. 试产效果评估:综合考虑以上各个方面的情况,对生产线试产的效果进行评估,包括设备运行状况、人员操作技能、产品质量等,以确定试产是否顺利通过验收。
1. 报表内容要全面准确,对于试产过程中的各方面情况要进行详细记录,确保报表内容完整。
2. 报表格式要清晰规范,对于每个部分的内容要进行分条清晰排列,方便查阅和评估。
3. 报表要及时填写,对于试产过程中发现的问题和不良情况要及时记录,并进行整改和改进。
4. 报表要保存完整,对于每次试产的报表都要保存备份,以便后续查阅和对比分析。
生产线试产验收报表的制作是一个重要的工作,通过对试产过程的全面记录和评估,可以及时发现问题,改进工艺,提高生产效率和产品质量。
只有保持报表的规范和完整,才能更好地指导生产线的实际操作,确保生产线的稳定运行和持续发展。
第二篇示例:生产线试产验收报表日期:2022年10月15日生产线名称:XXX生产线试产验收人:XXX一、试产情况1. 生产线整体运行情况- 生产线设备正常运转,未出现停工现象。
试生产检验记录表
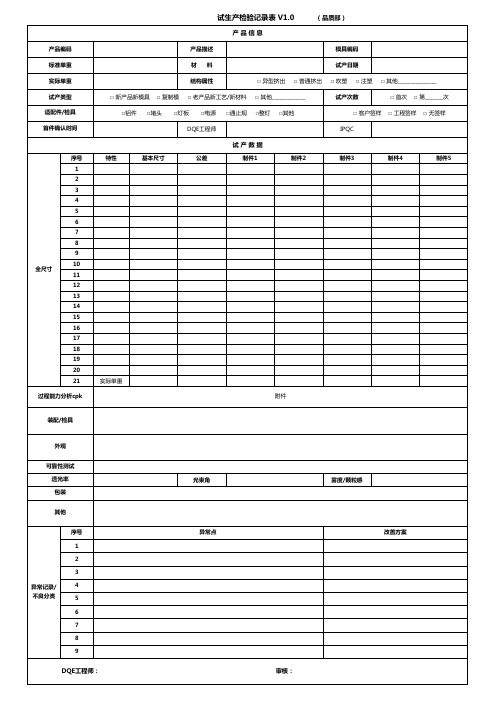
□ 新产品新模具 □ 复制模 □ 老产品新工艺/新材料 □ 其他_____________
试产次数
□ 首次 □ 第_______次
□铝件 □堵头 □灯板 □电源 □通止规 □整灯 □其他
□ 客户签样 □ 工程签样 □ 无签样
DQE工程师
IPQC
特性
基本尺寸
试产数据
公差
制件1
制件2
制件3
制件4
制件5
实际单重
产品编码 标准单重 实际单重 试产类型 适配件/检具 首 3 4 5 6 7 8 9 10 11 12 13 14 15 16 17 18 19 20 21
过程能力分析cpk
试生产检验记录表 V1.0
产品信息
(品质部)
产品描述
模具编码
材料
试产日期
结构属性
□ 异型挤出 □ 普通挤出 □ 吹塑 □ 注塑 □ 其他_______________
附件
装配/检具
外观
可靠性测试 透光率 包装
其他
异常记录/ 不良分类
序号 1 2 3 4 5 6 7 8 9
DQE工程师:
光束角 异常点
雾度/颗粒感 改善方案
审核:
新产品小批试装及试生产管理规范

新产品小批试装及试生产管理规范1 范围1.1 本标准规定了开发新产品工装样件的小批量上线试装流程,对批量试产前首批工装样件进行质量稳定性验证和设计确认,并进行新产品转入批量试产的技术准备进行评审确认。
1.2 本标准适用于在整车或系统零部件新产品开发中已完成设计定型的工装样件的验证。
2 术语2.1 工装样件:是配套协作厂按规定图样、技术文件和正式工艺文件生产、能满足批量化生产的汽车零部件。
2.2 小批量试装:为验证新开发汽车零部件工装样件的工艺可行性、产品质量,进行3-5套的新产品上线生产装配。
3 职责3.1 产品研发部:负责新产品的图纸、技术标准等相关技术文件的制定和发放,负责新产品小批试装的组织、协调及验证跟踪和设计更改;负责新产品样件及小批试装件的采购、负责新产品的资料及档案管理。
3.2 技术部:负责新产品投产前的工艺文件编制、工艺验证和工装保证。
3.3 生产部:负责新产品上线试装的生产组织和调度。
3.4 质量部:负责新产品上线试装装配质量的验证和检验文件的编制。
3.5 生产厂:负责新产品上线试装。
3.6 信息部负责物料代码的编制和调整。
3.7 配套供应部负责小批采购中大件采购的价格商务谈判和价格确定。
4 小批试装工作流程4.1 小批试装工作流程见《新产品小批试装工作流程图》。
4.1.1 小批采购中大件采购的价格由配套供应部商定,并通知产品研发部。
4.1.2 产品研发部项目负责人负责进行首批专用件的采购和技术文件的准备,专用件采购数量最多不得超过5台套,试装数量和次数由部门主管酌情指定。
4.1.3 项目负责人发布经审核的《小批试装通知书》(GA/QG(研)7.3-1),由生产部承认,报总经理或主管副总批准,并按设计输出清单将盖红色“试制用图”技术文件一起发放至各相关部门。
4.1.4 技术部及时按产品技术文件编制试装车型通用件投料表。
4.1.5 生产部按通知要求,安排自制件的生产,试装自制小件入研发库。
新产品试制控制程序

新产品试制控制程序1目的规定了产品试制在制造过程中的过程质量控制的职责、控制要求、内容和程序、报告和记录。
其目的是通过对试制和试制过程的控制,以保证试制产品的质量。
2 适用范围适用于本企业新产品的试制。
注:设计定型前各种试制用样机试制和老产品改进部份的试制或简单新产品试制,在保证试制要求的前提下,本文件内容经主管厂领导批准后可以剪裁。
3 职责3.1 设计定型前样机试制由设计部门归口管理。
3.2 设计定型后小批试生产及生产定型(或转厂鉴定)试制,由工艺部门归口管理。
3.3 各有关部门按自已承担的质量职能,对试制进行质量控制。
4 程序4.1 控制要求4.1.1 试制过程必须按设计图样和技术条件进行,确保文文相符、文实相符。
4.1.2 不同阶段的产品试制必须分别进行,前一阶段的试制和试验未完成前,或遗留问题未得到妥善处理前,不得进行下阶段的试制。
4.1.3 必须有经批准的试制计划。
设计定型前样机试制由企业主管领导批准;小批量生产及生产定型的试制,在征得顾客代表同意后,由企业主管领导批准。
4.1.4 试制前应编制试制大纲:设计定型前由设计部门编制,设计定型后由工艺部门编制。
4.1.5 试制生产由生产管理部门负责组织和协调,确保试制按质、按量、按进度完成。
4.1.6 承担试制工作的车间和部门,应严格按照本条件和有关规定进行质量控制,不得以任何借口降低试制产品质量。
4.2 试制大纲内容4.2.1 试制的目的和依据。
4.2.2 试制合同或计划中有关试制批量、质量和状态的具体要求。
4.2.3 试制工艺准备的要求:简要工艺流程;毛坯图;工艺装备图;关键、重要件工艺方案;关键、重要工装的评审及在试制程序中的位置等。
4.2.4 试制生产准备的要求;所需材料、毛坯、外协件的数量、进度及验证方法;新增设备或设备改造的项目名称和进度要求;检测设备的配置;工艺试验、工艺攻关项目的进度要求及负责部门和人员;特殊工序需培训的人员要求等。
新产品设备导入与试产流程经过设计

+\新产品导入与试产流程1目的规范新产品导入工作,保证设计输出正确地转换为完整的生产规范,使得批量生产的产品能够持续地满足预期用途。
2适用范围适用于产品新产品导入与试生产。
3名词定义3.1DFX (Design for X)可加工性、装配性、可测试性、可安装性、可维修性等非功能性能需求的总称。
DFX需求包括两种类型:1)通用DFX需求:适用于所有产品,一般以DFX设计准则、DFX设计指南的形式呈现。
2)专用DFX需求:适用于特定产品,一般以特定产品的DFX需求文档或产品DFX指标的方式呈现。
3.2新产品导入保证设计输出正确地转换为完整的生产规范的全部活动。
其主要工作内容是,DFX需求分析、DFX 检查落实、制作样机验证DMR文件的正确性、完整性、合理性、输出DMR文件。
3.3开发样机参见《新产品开发流程》。
3.4工程样机参见《新产品开发流程》。
3.5DMR(Device Master Record)即产品主记录。
是用于支持采购、加工、装配、质量检验、安装、维修所有文件及其审批状态的文件清单。
DMR包括三种成熟度状态:1)DMR0:DHF(即设计历史文件,其定义参见《新产品开发流程》)中支持工程样机制作的需求规格、测试方法、图纸、BOM及其相关数据文件(如CAD/EDA等产生的数据文件)组成的文件清单。
在开发样机评审前,DMR0中的文件必须通过审批,并且在档案室受控。
2)DMR 1:支持真实或模拟条件下工程样机制作、安装、维护的齐套文件清单。
在工程样机评审前,DMR1中的文件必须通过审批,并且在档案室受控。
3)DMR 2:新产品完成了试产,通过批量试产验证,可以批量生产的齐套文件清单。
转量产评审通过前,DMR2中的文件必须通过审批,并且在档案室受控。
3.6新产品导入开发文档新产品导入活动中生成的工作计划、工艺分析、测试验证、工艺评估和评审等文档的总称。
3.7PFMEA (Process Failure Mode Effects Analysis)新产品导入小组采用的一种工艺分析技术,用来保证各种潜在的工艺失效模式及其相关的机理已得到充分的考虑,并采取了有效的风险预防措施。
试生产方案样本
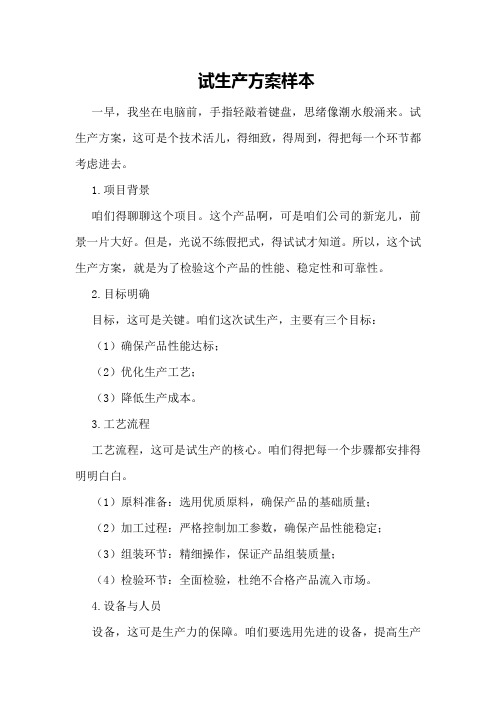
试生产方案样本一早,我坐在电脑前,手指轻敲着键盘,思绪像潮水般涌来。
试生产方案,这可是个技术活儿,得细致,得周到,得把每一个环节都考虑进去。
1.项目背景咱们得聊聊这个项目。
这个产品啊,可是咱们公司的新宠儿,前景一片大好。
但是,光说不练假把式,得试试才知道。
所以,这个试生产方案,就是为了检验这个产品的性能、稳定性和可靠性。
2.目标明确目标,这可是关键。
咱们这次试生产,主要有三个目标:(1)确保产品性能达标;(2)优化生产工艺;(3)降低生产成本。
3.工艺流程工艺流程,这可是试生产的核心。
咱们得把每一个步骤都安排得明明白白。
(1)原料准备:选用优质原料,确保产品的基础质量;(2)加工过程:严格控制加工参数,确保产品性能稳定;(3)组装环节:精细操作,保证产品组装质量;(4)检验环节:全面检验,杜绝不合格产品流入市场。
4.设备与人员设备,这可是生产力的保障。
咱们要选用先进的设备,提高生产效率。
(1)设备选型:根据生产工艺要求,选择合适的设备;(2)设备调试:确保设备运行稳定,满足生产需求;(3)人员培训:提高员工操作技能,确保生产顺利进行。
5.质量控制质量控制,这可是试生产过程中的重中之重。
(1)制定质量控制计划:明确质量目标,制定具体的质量控制措施;(2)过程监控:实时监控生产过程,确保质量达标;(3)成品检验:全面检验,确保产品合格。
6.安全生产安全生产,这可是不能忽视的问题。
(1)制定安全生产制度:明确安全生产责任,确保生产安全;(2)安全培训:提高员工安全意识,避免安全事故;(3)应急处理:制定应急预案,确保突发事件得到及时处理。
7.成本控制成本控制,这可是提高产品竞争力的关键。
(1)原材料采购:合理采购,降低原材料成本;(2)生产效率:提高生产效率,降低生产成本;(3)人工成本:合理配置人力资源,降低人工成本。
8.试生产计划试生产计划,这可是咱们的时间表。
(1)项目启动:明确项目任务,启动试生产;(2)生产准备:完成设备调试、人员培训等准备工作;(3)试生产阶段:按照工艺流程进行试生产;9.风险评估与应对措施风险评估,这可是防范未然的重要环节。
新产品开发试生产流程

XXXX有限公司企业标准Q/XXXXXXXX39024-2004 新产品开发试生产流程2004-00-00 批准2004-00-00 实施XX汽车股份有限公司发布Q/JX39024-2004前言本标准根据公司实际操作情况,并结合国军标要求,对原2001版在运行过程中存在的问题进行了修订和完善。
本标准生效之日起,原《新产品开发试生产流程》Q/JX39024-2001同时作废。
本标准由江铃汽车股份有限公司人事企管部提出并归口。
本标准起草人:本标准审核人:本标准批准人:XXXXXX有限公司企业标准新产品开发试生产流程Q/XXXXX39024-20041. 范围:通过规范新产品开发过程中试生产阶段(TTO、PP和FEU 阶段)的各项活动和内容,以保证新产品开发各项活动保持良好的受控制状态。
本程序适用于公司新产品开发试生产过程控制。
2. 引用文件:下列标准所包含的条文,通过在本标准中引用而构成为本标准的条文。
本标准出版时,所示版本均为有效。
所有标准都会被修订,使用本标准的各方应确保使用下列标准最新有效版本。
Q/JX45052 《产品更改程序》Q/JX45025 《产品质量先期策划程序》Q/JX45310 《生产件批准程序》Q/JX37010 《非销售用件及产品管理规定》SZ-09-0001-2002 《工艺工装管理手册》3. 术语:3.1 TTO——工装(含工位器具)和工艺的连线调试3.2 PP——工艺工装(含工位器具)验证3.3 FEU——指定客户的样车评价3.4 PPAP——生产件批准3.5 APQP——产品质量先期策划4. 职责:4.1 产品开发技术中心负责项目开发计划(TDWP)的发布及更新、D状态和V状态产品清单及图纸的发布及其它相关技术文件的提供。
4.2 制造部负责组织在试生产前发布或更新相应的工艺路线和投料清单并组织编制试生产工艺文件;负责组织自制件的试制工作及自制件PPAP的提交;以及安排试制产品生产计划。
- 1、下载文档前请自行甄别文档内容的完整性,平台不提供额外的编辑、内容补充、找答案等附加服务。
- 2、"仅部分预览"的文档,不可在线预览部分如存在完整性等问题,可反馈申请退款(可完整预览的文档不适用该条件!)。
- 3、如文档侵犯您的权益,请联系客服反馈,我们会尽快为您处理(人工客服工作时间:9:00-18:30)。
状态确认 完成后"√"
11
原料粘稠度确认,要不要放烘房?设置烘房温度?
12
有无特殊的设备要求?(清洗料/洗釜/投料方式、顺序等)
生 13 产 生产操作单是否完成?
14 15
前 确 认
是否已完成生产人员培训? 生产前有无其他说明?
16
个人PPE按照要求准备就绪。
17
相关设备和工具已做好安全防护。(防静电夹可正常使用)
36
混兑罐大小、材质;搅拌功率和速度
37
控制温度是多少
38
取样分析指标是多少
39 混 是否有调整
40 兑 是否有返工
41 灌 循环时间 42 装 第一桶料按要求回混兑罐操作
43
首件样ห้องสมุดไป่ตู้按要求送QC,测试合格后继续灌装。
44
最终损耗
45
零头产品需确认其品名/重量并做好标识。(名称、净重、记录人、日期等)
54
洗罐溶剂已经送样并经QC确认清洗合格
相关部门会签:
备注 根据原料的物理参数与小样实际状况判断
18
确认原料全部备齐
21
核对原料的重量满足批次生产的要求。
22
确认混兑罐的取样阀在关闭状态。
23
打开人孔确认混兑罐内的洁净度、混兑罐内及循环管线内无任何液体和物 料。
24
确认混合罐的所有出料在关闭状态。
26
确认过滤器内干净并滤袋已更换。
28
确认泵出口进过滤器的手阀处于关闭状态。
29
确认过滤器出口与包装管线上的软管在断开位置。
新产品试生产记录
序号
1 2 3 4 5 6 7 8 9 10
试生产确认清单
包装形式,要求的是什么包装?材质,型号,规格? 本批次生产量(T) 原料SDS是否打印到生产/仓库现场 原料备料地址是否已确认? 是否经过评审会签? 保质期是否有异议? 原料是否完成测试? 配小样是否完成? 是否已完成QC人员培训? 哪条生产产线?
30
确认人孔垫片合格并人孔已关闭紧锢。
31
确认混兑罐顶所有加注原料管线手阀处于关闭状态。
32
确认加料区的静电接地夹完好并处于可正常使用状态。
33
零头料需确认其剩余净重量/品名后做好标识(品名、剩余净重量、人员姓 名、日期等)放到指定区域。
34
出料时确认静电接地夹完好并处于可正常使用状态。
35
生产中记录投每种原料/预混料开始和结束时间,每种原料/预混料 重量,混合搅拌时间,取样分析时间
46
原料处理完成后,投料现场的5S清理,加料工具的整理
47
原料/预混料在加料结束后关闭与混兑罐相连管线上的手阀。
48
混兑罐按清洗要求清洗完成
49
清 回流管线已清洗
50
洗 原料投料泵及加注管线已经清洗干净
51
设 过滤器按要求清洗干净,滤袋已经拆除
52
备 出料管线,出料枪头清洗干净
53
清洗水/清洗溶剂已收集和置换溶液是否完成并做好标识并放到指定位置。