温度及频率对轮胎橡胶材料生热率的影响
轮胎材料热生成率的确定
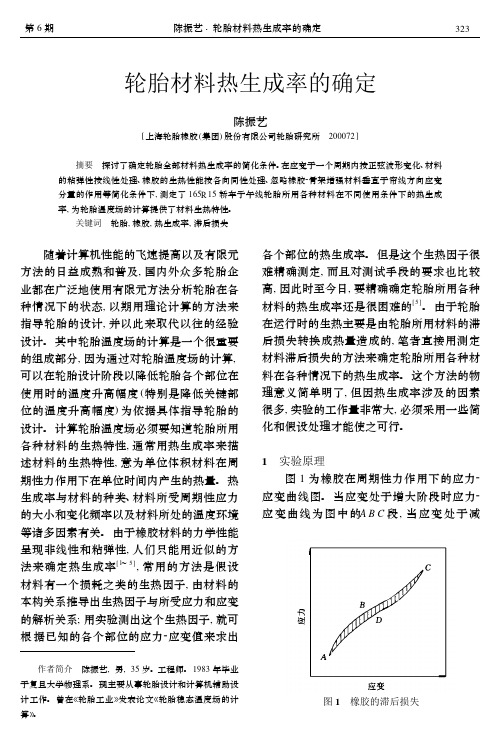
轮胎材料热生成率的确定
陈振艺
[ 上海轮胎橡胶 (集团) 股份有限公司轮胎研究所 200072 ]
摘要 探讨了确定轮胎全部材料热生成率的简化条件。在应变于一个周期内按正弦波形变化、材料 的粘弹性按线性处理、橡胶的生热性能按各向同性处理、忽略橡胶2骨架增强材料垂直于帘线方向应变 分量的作用等简化条件下, 测定了 165R 15 轿车子午线轮胎所用各种材料在不同使用条件下的热生成 率, 为轮胎温度场的计算提供了材料生热特性。
ro lling lo ss distribu tion in au tom ob ile tires. T ire Sci.
and T ech. , 1988; 16 (2) : 78 3 R eed. H eat bu ild2up of dynam ically loaded engineered
32 6 轮 胎 工 业 1997 年第 17 卷
化和假设下进行的, 而简化和假设越多, 误 差也就越大。 尽管如此, 在测试手段相对比 较落后的国内轮胎行业, 这不失是个可行的 方法。 笔者用上述实验结果计算了上轮公司 正泰橡胶厂生产的 165R 16 轿车子午线轮胎 的稳态温度场[8], 其计算结果有相当的可信 性。
(1) 轮胎在行驶中各个部位的应变是周 期性变化的, 对轮胎上的某一点来说, 在一个 周期内其所处的各个位置的应变数值可用有 限元法求出, 取其处在最低点和最高点位置 (相对于地面) 时的应变数值为周期性应变的 两个峰值, 近似地认为应变在一个周期内按 正弦波形变化, 其振幅为两个峰值位置应变 数值之差的一半。 根据各种材料具体的应变 变化情况, 在振幅变化范围内从小到大均匀 选择几个数值 (变化范围大的多取, 变化范围 小的少取) 作为测量点, 对落在测量点以外的 情况则用插值的方法得到。
热裂解工艺参数分析
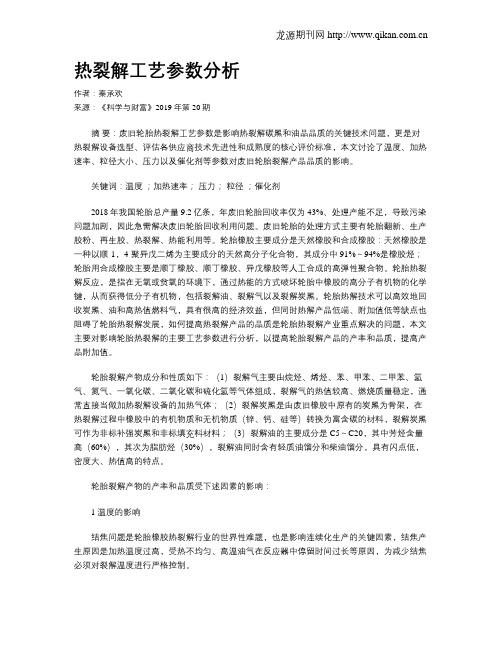
热裂解工艺参数分析作者:秦承欢来源:《科学与财富》2019年第20期摘要:废旧轮胎热裂解工艺参数是影响热裂解碳黑和油品品质的关键技术问题,更是对热裂解设备选型、评估各供应商技术先进性和成熟度的核心评价标准,本文讨论了温度、加热速率、粒径大小、压力以及催化剂等参数对废旧轮胎裂解产品品质的影响。
关键词:温度;加热速率;压力;粒径;催化剂2018年我国轮胎总产量9.2亿条,年废旧轮胎回收率仅为43%、处理产能不足,导致污染问题加剧,因此急需解决废旧轮胎回收利用问题。
废旧轮胎的处理方式主要有轮胎翻新、生产胶粉、再生胶、热裂解、热能利用等。
轮胎橡胶主要成分是天然橡胶和合成橡胶:天然橡胶是一种以顺-1,4-聚异戊二烯为主要成分的天然高分子化合物,其成分中91%~94%是橡胶烃;轮胎用合成橡胶主要是顺丁橡胶、顺丁橡胶、异戊橡胶等人工合成的高弹性聚合物。
轮胎热裂解反应,是指在无氧或贫氧的环境下,通过热能的方式破坏轮胎中橡胶的高分子有机物的化学键,从而获得低分子有机物,包括裂解油、裂解气以及裂解炭黑。
轮胎热解技术可以高效地回收炭黑、油和高热值燃料气,具有很高的经济效益,但同时热解产品低端、附加值低等缺点也阻碍了轮胎热裂解发展,如何提高热裂解产品的品质是轮胎热裂解产业重点解决的问题,本文主要对影响轮胎热裂解的主要工艺参数进行分析,以提高轮胎裂解产品的产率和品质,提高产品附加值。
轮胎裂解产物成分和性质如下:(1)裂解气主要由烷烃、烯烃、苯、甲苯、二甲苯、氢气、氮气、一氧化碳、二氧化碳和硫化氢等气体组成,裂解气的热值较高、燃烧质量稳定,通常直接当做加热裂解设备的加热气体;(2)裂解炭黑是由废旧橡胶中原有的炭黑为骨架,在热裂解过程中橡胶中的有机物质和无机物质(锌、钙、硅等)转换为富含碳的材料,裂解炭黑可作为非标补强炭黑和非标填充料材料;(3)裂解油的主要成分是C5~C20,其中芳烃含量高(60%),其次为脂肪烃(30%),裂解油同时含有轻质油馏分和柴油馏分,具有闪点低,密度大、热值高的特点。
提高混炼温度对Sulfron3001改性轮胎胎面胶料性能的影响

1 3 混炼 .
1 实 验
1 1 材 料 .
混炼 顺 序是 影响 S l o 0 1和炭 黑之 间反 uf n3 0 r
应 的重 要参 数 。制备 母炼 胶 的实 际混炼 顺序 为 :
本研 究所 用 的材料 如表 1 示 。 所
表 1 试 验 用 材 料
基团
3 01 0
降低填料 一填料 之间 的 作 用 , 增强 填 料 一聚合 物
之间 的作用 。 S l o 0 1 uf n3 0 和填 料炭 黑 之 间的 反应 始 于 混 r
图 1 炭 黑 和 芳 纶 纤 维 之 间 的 相 互 作 用
在 混炼 的后期 S l o 0 1才 与橡 胶 反 应 。 uf n 3 0 r 此 时 , uf n3 0 化学 基 团在 硫 黄 、 进剂 和 其 S l o 0 1 r 促
5 4
橡 胶 参 考 资 料
21 0 2薤
提 高混 炼 温度 对 S lrn3 0 ufo 0 1改性 轮 胎 胎 面胶 料 性 能 的影 响
孙亚斌 石 志宇 杜 娟 编 译 12 2) 3 0 2 ( 吉林 石化 公 司研 究 院高分 子合成 研究 所 , 林 吉
新一代 特别 设 计 的 化学 改 性芳 纶短 纤 维 , 即
炼 之初 。已证 实 , ufo 0 1与 炭 黑 粒 子 的 活 S l n30 r 性表 面- OH 基作 用 , 形成 化学键 。图 1为 S l o ui n r 3 0 与 炭黑 一OH 基 相互 作 用 , 炭 黑 和芳 纶 纤 01 在
维之 间形成 与混炼 温度 有关 的化学键 。
S l o 0 1 对 轮胎 胎 面 胶料 性 能 有 重 要 影 响 。 uf n3 0 , r
影响轮胎使用寿命的因素影响轮胎使用寿命的因素影响轮胎使用寿命的因素影响轮胎使用寿命的因素

影响轮胎使用寿命的因素摘要:影响汽车轮胎寿命的因素很多,大多数与汽车的运行工况和技术状况相关。
要保障轮胎的使用寿命,首先必须保证轮胎的技术状况在要求的范围内,其次是要保证车辆处于良好的运行工况,同时,要防止和避免在运行中意外爆胎。
合理使用轮胎,对延长轮胎的使用寿命、降低运输成本和保障汽车的安全运行至关重要。
关键词:轮胎、温度、花纹、气压、路面影响轮胎使用寿命的因素很多,造成轮胎损坏的原因主要有:一、温度对轮胎的影响轮胎是热的不良导体,其导热性平均为0.25 米/米•小时•度,仅为铁导热性的1/232。
一般轮胎使用时胎体温度约在100℃以内,可认为是正常温度。
在100℃时帘线强度大约已降低20%。
橡胶与帘线间的粘附强度大约降低一倍,轮胎在100℃~121℃是临界温度,超过121℃时,轮胎在较高温度影响下,帘线的物理性能将急剧下降,而导致引起轮胎的脱层或爆破。
二、花纹在使用中应怎样选择1、纵向花纹:主要优点是滚动阻力小、防滑性能好、散热性能好及噪音小;缺点是牵引性能差。
2、横向花纹:特别是越野花纹,轮胎与路面的接触性能好。
在道路较差或泥泞路面上牵引和通过性好,轮胎的自洁性也好;但行驶噪音大且防滑性能差。
3、混合花纹:混合花纹轮胎抓着性介于纵向花纹和横向花纹之间,主要缺点是耐磨性较差,胎肩部花纹容易产生磨耗不均现象。
三、负荷对轮胎的影响轮胎承受的静负荷对轮胎的行驶里程有很大的影响,有超负荷现象就会显著地降低轮胎的行驶里程。
轮胎在超负荷下轮胎的下沉量变形将增加,从而使轮胎的内部材料及帘线间所受的应力,特别是剪切力增加,将导致轮胎的使用寿命缩短。
在轮胎超负荷时,适当增加内压可以使轮胎的下沉量减少,但不能完全弥补轮胎超负荷的损失。
四、气压对轮胎的影响气压对轮胎的影响气压对轮胎的影响气压对轮胎的影响:1、气压是轮胎的生命,不按标准充气是轮胎早期损坏的主要原因之一。
内压不足会降低轮胎的行驶里程,因轮胎的变形,会因气压的降低而增大,使轮胎的内部材料生热和应力增加。
内胎材料的热传导性能与胎温分析
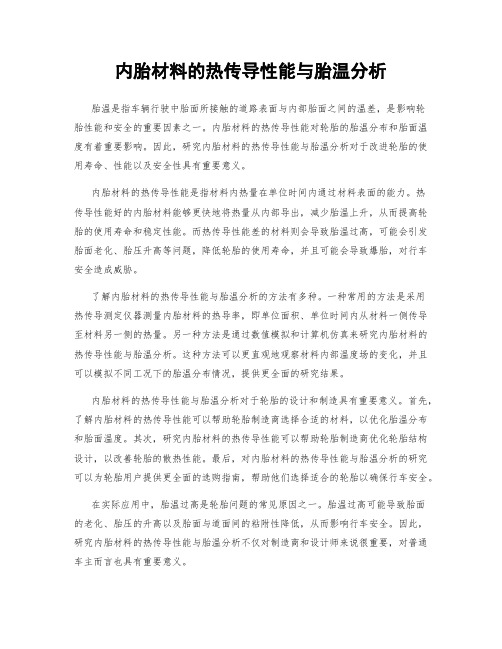
内胎材料的热传导性能与胎温分析胎温是指车辆行驶中胎面所接触的道路表面与内部胎面之间的温差,是影响轮胎性能和安全的重要因素之一。
内胎材料的热传导性能对轮胎的胎温分布和胎面温度有着重要影响。
因此,研究内胎材料的热传导性能与胎温分析对于改进轮胎的使用寿命、性能以及安全性具有重要意义。
内胎材料的热传导性能是指材料内热量在单位时间内通过材料表面的能力。
热传导性能好的内胎材料能够更快地将热量从内部导出,减少胎温上升,从而提高轮胎的使用寿命和稳定性能。
而热传导性能差的材料则会导致胎温过高,可能会引发胎面老化、胎压升高等问题,降低轮胎的使用寿命,并且可能会导致爆胎,对行车安全造成威胁。
了解内胎材料的热传导性能与胎温分析的方法有多种。
一种常用的方法是采用热传导测定仪器测量内胎材料的热导率,即单位面积、单位时间内从材料一侧传导至材料另一侧的热量。
另一种方法是通过数值模拟和计算机仿真来研究内胎材料的热传导性能与胎温分析。
这种方法可以更直观地观察材料内部温度场的变化,并且可以模拟不同工况下的胎温分布情况,提供更全面的研究结果。
内胎材料的热传导性能与胎温分析对于轮胎的设计和制造具有重要意义。
首先,了解内胎材料的热传导性能可以帮助轮胎制造商选择合适的材料,以优化胎温分布和胎面温度。
其次,研究内胎材料的热传导性能可以帮助轮胎制造商优化轮胎结构设计,以改善轮胎的散热性能。
最后,对内胎材料的热传导性能与胎温分析的研究可以为轮胎用户提供更全面的选购指南,帮助他们选择适合的轮胎以确保行车安全。
在实际应用中,胎温过高是轮胎问题的常见原因之一。
胎温过高可能导致胎面的老化、胎压的升高以及胎面与道面间的粘附性降低,从而影响行车安全。
因此,研究内胎材料的热传导性能与胎温分析不仅对制造商和设计师来说很重要,对普通车主而言也具有重要意义。
在研究中,除了热传导性能外,还需要考虑内胎材料的其他特性对胎温分布的影响。
例如,内胎材料的导热系数、热容量等都会对胎温产生影响。
轮胎温度与轮胎性能研究

轮胎是车辆中最基本的构件之一。
现代车辆的发展对轮胎的性能提出了越来越苛刻的要求,高速化的时代需要有高性能的轮胎。
防止轮胎早期失效破坏,延长使用寿命,提高经济效益,已越来越为轮胎的研究者、制造者和使用者所关注。
行驶中的轮胎在外载荷的作用下会产生大量的热量,引起温度的升高。
轮胎温度的升高是影响轮胎寿命的主要原因。
这种温升主要来源于两种热源:一是轮胎周期性变形而产生的橡胶材料滞后损失转变成热能;二是接地面的摩擦热。
由热造成的轮胎温度的升高将导致橡胶化学和物理性能的下降而丧失强度,严重时会导致轮胎爆破给乘坐者造成不可挽回的损失。
因此,为了有效降低因轮胎损坏而造成的灾难事故,许多机构纷纷对外力作用下的轮胎温度场进行研究。
大量的研究表明,斜交轮胎能正常工作并保证轮胎有足够耐久性的最高温度一般是121.1℃,子午线轮胎必须限制在93.3℃以内或更低些温度。
必须注意,这里所说的温度都是指轮胎内的“局部过热”点而言,也就是轮胎各部位相比较产生最高温度的点。
然而,不同的轮胎结构,不同的轮胎胶料,产生最高温度的部位以及温度的高低是不同的。
因此,迅速、精确、高效地确定滚动轮胎温度场,具有如下意义:第一,指导轮胎结构设计,缩短设计周期、节约成本。
轮胎的热学性能与力学性能紧密相连,轮胎在滚动行驶过程中由于摩擦和变形而产生大量的热量,导致温度升高;由于结构的原因,可造成局部温升过高,这将直接影响轮胎材料的热物理性能,造成肩空、脱胶或爆胎等结构方面的破坏。
为此设计者在设计之初需要了解轮胎断面温升状况,使设计的轮胎产生的应力和应变分布更加合理,从而降低局部过高的温升,延长轮胎的使用寿命。
第二,指导轮胎胶料配方设计。
一方面,合理地改进轮胎橡胶材料的配方有助于轮胎滚动阻力的降低。
轮胎滚动阻力的降低是降低能量损失、节约能耗的重要标志。
轮胎的滚动阻力下降百分之十车辆的油耗就会下降百分之一,油耗的降低又会对环境的优化起到积极的作用。
另一方面,配方人员可以根据热学分析的结果在轮胎变形剧烈、温度较高的部位,有意识地使用生热率较低、导热系数较高的胶料,这不但有助于该部分温升幅度的减小,还会降低轮胎的滚动阻力,节约能耗。
汽车轮胎稳态温升机理的研究

汽车轮胎稳态温升机理的研究宋喜岗;崔淑华;郑雪莲【摘要】阐述了汽车稳态行驶时的轮胎温升机理,即轮胎应力-应变与轮胎温度场的关系.轮胎以橡胶材料为基材、由多种复合材料组成.橡胶材料的弹粘性特性使得轮胎在滚动时,受周期应力的作用将产生滞后损失,在轮胎内部产生热源.滞后损失所产生的热量多少与轮胎应力、位移、界面摩擦系数、接触面积、基材的热性能以及轮胎的转动阻力系数有关.这些参数的变化将直接引起轮胎温度的变化.作者实际测量了秉用车轮胎的胎面、胎内和胎冠温度,并以试验数据为基础,分析了轮胎的实际温升状况和行车速度对轮胎温度的影响,得到了行车速度与轮胎温度的关系.【期刊名称】《机电产品开发与创新》【年(卷),期】2011(024)003【总页数】3页(P44-46)【关键词】汽车轮胎;温升机理;稳态行驶【作者】宋喜岗;崔淑华;郑雪莲【作者单位】东北林业大学,黑龙江,哈尔滨,150040;东北林业大学,黑龙江,哈尔滨,150040;吉林大学,吉林,长春,130022【正文语种】中文【中图分类】TQ336随着汽车行驶速度的提高,汽车行驶过程中轮胎的温升幅度大大提高,但轮胎在使用时不应超过限制温度,许多国家已经制定或开始制定这方面的标准。
在轮胎的设计和使用中,了解轮胎内部温度场的分布对合理设计轮胎结构和胶料配方、缩短设计周期、降低费用以及在使用中合理安排使用条件等都具有重要的经济价值和社会意义。
目前国外有关学者及专家用计算机模拟轮胎的行驶工况,来找出影响轮胎温度上升的各种因素并进行深入研究[1~8]。
轮胎橡胶材料作为一种热敏感材料,温度的上升将导致其性能的恶化:胶料强度以及界面粘合强度下降,易使轮胎产生肩空、肩裂甚至爆胎,轮胎寿命降低[2]。
由于轮胎温度太高失效造成的事故占交通事故的比例很大,因此,轮胎的耐久性以及轮胎在行驶过程中的温升是国内外业界人士最为关心的问题之一。
汽车轮胎按照胎体中帘线排列的方向不同,分为斜交轮胎和子午线轮胎。
预热温度对轮胎硫化温度场及程度场的影响
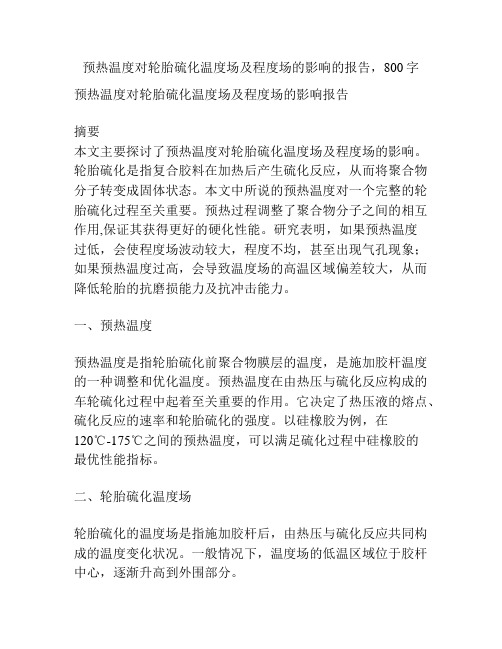
预热温度对轮胎硫化温度场及程度场的影响的报告,800字预热温度对轮胎硫化温度场及程度场的影响报告摘要本文主要探讨了预热温度对轮胎硫化温度场及程度场的影响。
轮胎硫化是指复合胶料在加热后产生硫化反应,从而将聚合物分子转变成固体状态。
本文中所说的预热温度对一个完整的轮胎硫化过程至关重要。
预热过程调整了聚合物分子之间的相互作用,保证其获得更好的硬化性能。
研究表明,如果预热温度过低,会使程度场波动较大,程度不均,甚至出现气孔现象;如果预热温度过高,会导致温度场的高温区域偏差较大,从而降低轮胎的抗磨损能力及抗冲击能力。
一、预热温度预热温度是指轮胎硫化前聚合物膜层的温度,是施加胶杆温度的一种调整和优化温度。
预热温度在由热压与硫化反应构成的车轮硫化过程中起着至关重要的作用。
它决定了热压液的熔点、硫化反应的速率和轮胎硫化的强度。
以硅橡胶为例,在120℃-175℃之间的预热温度,可以满足硫化过程中硅橡胶的最优性能指标。
二、轮胎硫化温度场轮胎硫化的温度场是指施加胶杆后,由热压与硫化反应共同构成的温度变化状况。
一般情况下,温度场的低温区域位于胶杆中心,逐渐升高到外围部分。
预热温度会直接影响温度场的分布范围及程度,如果预热温度过低,会导致温度场的低温区域范围过宽,程度也较低;如果预热温度过高,会使温度场的高温区域偏差较大,使轮胎硫化更加不均匀。
三、轮胎程度场轮胎程度场是指轮胎硫化完成后,形成硫化膜层时,所产生的硫化效果的分布情况。
一般情况下,程度场也是以胶杆中心为起始点,逐渐增大且程度逐渐加强,程度最高的部分位于胶杆外围。
预热温度也会直接影响程度场的分布范围及程度。
如果预热温度过低,会使程度场波动较大,程度不均,甚至出现气孔现象;如果预热温度过高,会使程度变化更加明显,且程度变化很快,这将显著影响轮胎的耐磨性能和抗冲击性能。
综上所述,预热温度对一个完整的轮胎硫化过程至关重要,预热过程可以调整聚合物分子之间的相互作用,以确保获得更好的硬化性能。
- 1、下载文档前请自行甄别文档内容的完整性,平台不提供额外的编辑、内容补充、找答案等附加服务。
- 2、"仅部分预览"的文档,不可在线预览部分如存在完整性等问题,可反馈申请退款(可完整预览的文档不适用该条件!)。
- 3、如文档侵犯您的权益,请联系客服反馈,我们会尽快为您处理(人工客服工作时间:9:00-18:30)。
32 6
轮 胎 工 业 2006 年第 26 卷
3. 2 回归分析
为了简化分析过程 , 对轮胎用各种胶料的生
热率随温度和频率的 变化关系进行 双元回归分
析 , 用于轮胎温度场滞后热源的定量分析 。
在不同的频率下将每种胶料的生热率与温度
的关系进行单元多项式拟合 , 得到如下方程 :
胶料的动态力学特性值 用德国耐驰公 司生
32 4
轮 胎 工 业 2006 年第 26 卷
产 的 DM A 2 4 2 型 测 试 仪 进 行 测 试[ 5] 。试 验 温 度为 - 20 ~ +100 ℃;频率为 5 , 10 , 16. 6 , 25 和 3 3 . 3 H z ;应 变 振 幅 为 6 % ;加 热 速 率 为 3 ℃ min -1 。
89. 518 85θ+4 298. 091 67)f 2 +
1. 370 19θ2 +93. 393 04θ- 4 917. 673 92)f 2 -
(0. 195 26θ3- 24. 617 38θ2 +138. 941 23θ+
(0. 152 6θ3- 27. 847 52θ2 +1 754. 020 59θ-
2 实验 2. 1 胶料
试验用胶料为子午线轮胎的胎体帘布层胶 、 胎面基部胶 、钢丝带束层胶 、锦纶冠带层胶 、胎侧 胶 、胎圈护胶 、胎面胶 、气密层胶 、钢丝包胶和三角 胶 。 胶料完全按相应标准经混炼和硫化而成 。 2. 2 试样制备
将 10 种胶料裁剪成哑铃状试样 , 每种胶料做 3 个平行试验 , 取平均值 。 试样尺寸为 2 mm ×10 mm ×4 mm 。 2. 3 试验仪器
89. 518 85 f 2 +1. 098 6 f 3
(5b)
表 1 胎体帘布层胶生热率随温度变化的三次回归结果
项 目
A B1 B2 B3 相关因数 R
5 0. 117 047 ×106 - 3 027. 003 67
52. 290 36 - 0. 303 90
0. 99
10 0. 270 916 ×106 - 8 459. 369 73
(1)
式中 , ε0 为应变振幅 , E′为储存弹性模量 , tanδ为
作者简介 :何 燕(1973-), 女 , 山 东青 州 人, 青 岛科 技大 学讲 师 , 博士 , 主要从事轮胎温度场的分析研究 。
损耗因子 。
由轮胎的滚动速度(v)和轮胎直径(D)可确
定轮胎的滚动周期(t)
t
=
2π ω
=3.
图 1 胎体帘布层胶的 Q′-θ曲线 频率(H z):■— 5 ;●— 10 ;▲— 16. 6 ; — 25 ;◆— 33. 3 。
图 3 钢丝带束层胶的 Q′-θ曲线 注同图 1 。
图 2 胎体帘布层胶的 Q′-f 曲线 温度(℃):■— - 20 ;●— 0 ;▲—20 ; — 40 ;◆— 60 ;○— 80 。
轮胎生热是由胶料的重复变形引起的 。 由于 轮胎结构的复杂性 , 不同部位胶料产生的热量不 同 , 为了使轮胎断面温度分布合理 , 各部位所用胶 料的力学性能应有所不同 。研究轮胎各部位胶料 的生热特性 , 在温度场分析中 , 可以用有限元法将 其离散到各个节点上计算得到整个轮胎断面的温 度场分布 , 为轮胎结构和配方设计提供依据 。本 工作对子午线轮胎各部位胶料的生热率与温度和 频率的关系进行研究 。
胶数据对温度进行单元三次线性回归 , 回归结果
如表 1 所示 。
分别将表 1 中的待定因数对频率进行多项式
回归后得到如下方程式 :
A =- 218 826. 943 27 +84 085. 610 39 f -
4 298. 091 67 f 2 +106. 117 45 f 3
(5 a)
B1 =- 1 718. 410 71 +138. 941 23 f -
(2)钢丝带束层胶 钢丝带束层胶的 Q′-θ和 Q′-f 曲线分别如图 3 和 4 所示。 由图 3 可以看出 , 温度低于 - 10 ℃时钢丝带 束层胶的生热率随温度的升高呈增大趋势 , 而当 温度高于 - 10 ℃时钢丝带束层胶的生热率随温 度的升高而减小 , 在 - 20 ~ 0 ℃之间出现一个生 热率峰值 , 且频率越大 , 峰越明显 , 这可能与钢丝 带束层胶的配方有关 。 由图 4 可以看出 , 钢丝带束层胶生热率随频 率的变化趋势与胎体帘布层胶相同 。
3 结果与讨论 3. 1 生热率计算
将试验测得的各种胶料动态力学特性值代入 式(3)计算得到 Q′。由于篇幅关系 , 在此仅列出 5 种胶料 Q′随温度(θ)和 f 变化的曲线 。
(1)胎体帘布层胶 胎体帘布层胶的 Q′-θ和 Q′-f 曲线分别如图 1 和 2 所示。 由图 1 可以看出 , 在试验频率下 , 胎体帘布层 胶的生热率随温度升高呈逐渐下降趋势 , 且当温 度低于 0 ℃时 , 生热率随温度的变化较明显 , 而当 温度高于0 ℃时 , 生热率随温度的变化逐渐趋于 平缓 ;频 率越 高 , 生 热 率随 温度 的 变化 趋 势越 明显 。
图 5 胎圈护胶的 Q′-θ曲线 注同图 1 。
图 6 胎圈护胶的 Q′-f 曲线 注同图 2 。
图 7 气密层胶的 Q′-θ曲线 注同图 1 。
图 8 气密层胶的 Q′-f 曲线 注同图 2 。
越高 , 生热 率随频率增大的幅度越小 , 而在 - 20 ℃时 , 生热率随频率增大的幅度也较小 。
于橡胶材料动态力学性能呈现非线性和粘弹性 , 人们只能用近似的方法来确定这种热源[ 1 ~ 4] 。
滞后热源与材料的种类 、材料所受的周期性
应力的大小和频率以及材料所处的温度环境等因
素有关 。
根据轮胎滞后生热数学模型 , 得到每个滚动
周期轮胎所产生的热量(Q)如下[ 5] :
Q =πε20 E′t anδ
1 轮胎滞后生热机理
由于粘性阻力的存在 , 负荷下运转的轮胎胶
料和帘布层受力产生的是粘弹性变形 。 弹性变形
在周期运转下可以恢复 , 但粘性变形不能恢复 , 它
被吸收而转变成热 , 成为轮胎温度升高的滞后热
源 。 滞后热源引起的温度升高将导致硫化胶化学
和物理性能下降 , 严重时还会引起轮胎爆破 。由
由图 2 可以看出 , 在同一温度下 , 胎体帘布层 胶的生热率随着频率的增大而逐渐增大 , 且低温 时生热率随频率的增大幅度大于高温时 。在轮胎 行驶温度范围(0 ~ 80 ℃)内 , 当轮胎的行驶频率 在 5 ~ 25 Hz 时 , 胎体帘布层胶的生热率与频率基 本呈线性关系 , 但当频率大于 25 H z 后 , 生热率随 频率的增大急剧增加 ;低于 0 ℃时 , 生热率随频率 的增加呈现一种曲线变化关系 。
图 4 钢丝带束层胶的 Q′-f 曲线 注同图 2 。
第6期
何 燕等. 温度及 频率对轮胎橡胶材料生热率的影响
32 5
(3)胎圈护胶 胎圈护胶的 Q′-θ和 Q′-f 曲线分别如图 5 和 6 所示。 从图 5 可以看出 , 在测试温度范围内 , 胎圈护 胶生热率在频率为 5 , 10 和 16. 6 H z 时随温度升 高基本没有变化 ;频率为 25 和 33. 3 H z 时 , 温度 低于 60 ℃, 生热率随温度升高也基本保持不变 , 温度高于60 ℃, 生热率则随温度的升高呈下降 趋势 。 由图 6 可以看出 , 随着频率的增大 , 胎圈护胶 生热率明显增大 。 (4)气密层胶 气密层胶的 Q′-θ和 Q′-f 曲线分别如图 7 和 8 所示。 由图 7 可见 , 气密层胶生热率随温度的变化 趋势与钢丝带束层胶基本一致 , 只是生热率峰值 向高温方向移动 , 约在 0 ℃, 这与其配方有关 。 由图 8 可见 , 随频率的增大 , 各温度下气密层 胶的生热率均增大 ;在 0 ~ 80 ℃温度范围内 , 温度
(5c)
218 826. 943 27)
(6)
B3 =- 0. 795 23 +0. 195 26 f - 0. 023 02 f 2 +
3. 997 76 ×10- 4 f 3
(5d)
将式(5a)~ (5d)代入式(4), 得到胎体帘布层
胶生热率随温度和频率的变化关系式 :
Q′=(3. 997 76 ×10-4 θ3 - 0. 054 74θ2 +1. 098 6θ+
(5)三角胶 三角胶的 Q′-θ和 Q′-f 曲线分别如图 9 和 10 所示 。 由图 9 可以看出 , 在测试温度范围内 , 频率越 大 , 三角胶生热率随温度的变化幅度越大 , 频率为 33. 3 H z 时出现明显的谷值和峰值 ;温度高于 80 ℃时 , 各 频率下生 热率均随 温度的 升高 呈下降 趋势 。 由图 10 可以看出 , 三角胶生热率随频率的增 大而明显增大 。 此外 , 胎面基部胶和胎侧胶生热率随温度和 频率的变化趋势与胎体帘布层胶基本相同 。 锦纶 冠带层胶生热率随温度和频率的变化趋势与钢丝 带束层胶基本一致 , 只是生热率随温度的变化更 明显 。胎面胶生热率随温度和频率的变化趋势与 锦纶冠带层胶基本一致 。 钢丝包胶生热率随温度 和频率的变化趋势与气密层胶基本相同 。
6πD v
(2)
则单位面积 、单位时间内胶料的生热率(Q′)可表
示为 :
Q′=Q f
=Q t
=
E′ε20 v t an 3. 6D
δ=
πf
E′ε20 tan
δ
(3)
式中 , f 为频率 。
本工作进行的胶料生热率研究是根据轮胎的
实际运动状况确定轮胎行驶的频率范围 , 用动态
分析方法确定各种动态特性值 , 然后求得生热率 。
0. 98