流化床气流磨工艺
简析先进陶瓷生产设备之硫化床气流磨
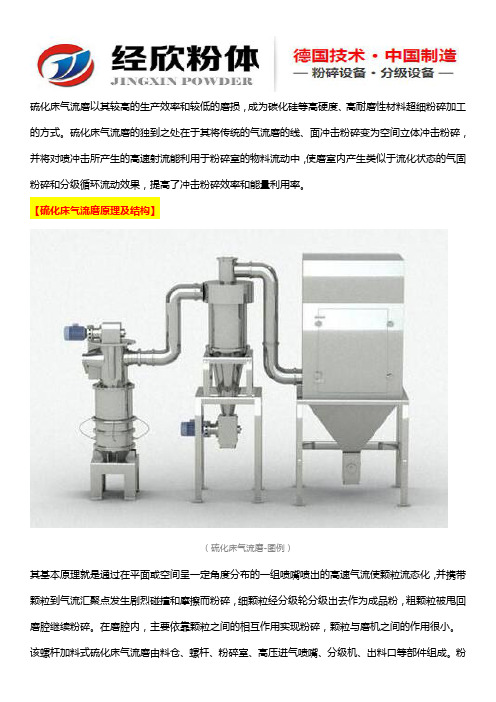
硫化床气流磨以其较高的生产效率和较低的磨损,成为碳化硅等高硬度、高耐磨性材料超细粉碎加工的方式。
硫化床气流磨的独到之处在于其将传统的气流磨的线、面冲击粉碎变为空间立体冲击粉碎,并将对喷冲击所产生的高速射流能利用于粉碎室的物料流动中,使磨室内产生类似于流化状态的气固粉碎和分级循环流动效果,提高了冲击粉碎效率和能量利用率。
【硫化床气流磨原理及结构】(硫化床气流磨-图例)其基本原理就是通过在平面或空间呈一定角度分布的一组喷嘴喷出的高速气流使颗粒流态化,并携带颗粒到气流汇聚点发生剧烈碰撞和摩擦而粉碎,细颗粒经分级轮分级出去作为成品粉,粗颗粒被甩回磨腔继续粉碎。
在磨腔内,主要依靠颗粒之间的相互作用实现粉碎,颗粒与磨机之间的作用很小。
该螺杆加料式硫化床气流磨由料仓、螺杆、粉碎室、高压进气喷嘴、分级机、出料口等部件组成。
粉碎室物料通过翻板阀1进入料仓2,由螺杆输送器3将物料送入粉碎室4。
气流通过喷嘴5进入流化床,颗粒在高速喷射气流交点碰撞,该点位于流化床中心,是靠气流对颗粒的高速冲击及粒子间的相互碰撞而使颗粒粉碎,与腔壁接触少、影响小,所以磨损大大减弱。
进入粉碎腔内的物料利用数个喷嘴喷汇产生的气流冲击能,及其气流膨胀成流态化床悬浮翻腾而产生碰撞、摩擦进行粉碎,并在负压气流带动下通过顶部设置的涡轮式分级装置,然后细粉排列出口外由旋风分离器及袋式收尘器捕集,粗粉受重力沉降返回粉碎区继续粉碎。
【硫化床气流磨的优点】(硫化床气流磨-结构图例)在粉碎室,颗粒流的对撞不但加强了颗粒间的碰撞、摩擦,而且降低了颗粒对腔体的磨损;粉碎后达到要求的颗粒可及时被分离出来,大大减少了过粉碎,提高了能量的利用率;硫化床气流磨将高速气流与物料分路进入粉碎室,避免了颗粒与管路的碰撞和摩擦,大大降低了喷嘴和管路的磨损;生产易于实现自动化控制,后续分级和粉碎实现了一体化,提高了效率。
【硫化床气流磨的配套工艺设备】(气流磨及配套工艺设备-图例)1-空压站及管路,2-气流磨,3-进料仓,4-旋风收集器,5-布袋除尘器,6-引风机图2是某氧化锆粉体工程与设备实例,由空压站及管路、气流磨、进料仓、旋风收集器、布袋除尘器、引风机、控制柜等配套工艺装备组成一个干法一段式开路流程。
气流磨的一般原理 将干燥无油的压缩空气或过热蒸

工作原理:喂入磨内的物料利用二维或三维设置的:数个喷嘴(3~7个)喷汇的气流冲击能,及其气流膨胀呈流化床悬浮翻腾而产生的碰撞、摩擦进行粉碎,并在负压气流带动下通过顶部设置的涡轮式分及装置,细粉排出机外由旋风分离器及袋式收尘器捕集,粗粉受重力沉降返回沉降区继续粉碎。
显然,这一流化床对喷式气流磨是在对喷式气流磨的基础上开发的新产品,流化床对喷式气流磨特点:产品细度高达d97=3~10μm,:粒度分布窄且无大颗粒;粉磨效率高,能耗低,比其它类型气流磨节能30%;采用Al2O3、SiC或Pu(钚)作易磨损件,磨耗低,产品受污染少,可加工无铁质污染的粉体产品和莫氏10级的物料;结构紧凑、噪音小、操作自动化,但成本贵。
另外,该磨采用涡轮分级,转速高,使用过热蒸汽为粉碎工质时,难以实现。
分级粒度也较扁平式宽。
技术参数:入料目数<20目,出料度最小是2 (6000目),型号LHL—6,成品产量40—250kg/h空气压力>0.8MPa,装机功率53Kw,空气耗量6m3/h, 筛网面积5.5*2.88m2型号QLM-ⅠQLM-1.5QLM-ⅡQLM-ⅢQLM-3.5QLM-ⅣQLM-Ⅴ原料粒度mm <3mm<3mm <3mm<3mm<3mm <3mm <3mm产品粒度μm2 2 2 2 2 2 2生产能力系数0.024 0.075 0.16 0.4 0.5 1 3.5 喷咀数量 3 4 4 4 4 4 4主机尺寸cm Φ16*50Φ25*80 Φ35*16Φ41*200Φ52*280Φ70*260Φ102*568收尘器面积㎡3 10 16-20 26-42 42-47 47-60 170 分几轮功 1.1 34 5.5 7.5 15(11)15率(11)*3电机最高转数18000 12000 8000 6000 6000 4000 4(5)000空压机压力≥0.7mpa≥0.7mpa≥0.7mpa≥0.7mpa≥0.7mpa≥0.7mpa≥0.7mpa空压机气量≥3m³≥6m³≥10m³≥20m³≥20m³≥40m³≥120m³高压风机功率2.2 2.2 4 7.5 7.5 18.5 55气流磨功率3.3 9 10 15 18 35 108标准操作空间2*2*2 4*2*4 6*3*6 7*4*6 7*4*6 9*4*9 18*12*11价格由于从上一个机械过来的粒径在0.075毫米200目左右,所以在超细磨碎阶段选择了流化床对喷式气流磨,这样可以把200目的初产品粉碎到3μm即5000目左右,根据要求需要设计出日产2吨的产品,所以我们选择了。
第五章流化床气化工艺分析

三 加压流化床气化的特点
1.压力对流化床的流体力学影响 (1)对阻力的影响 流化床的阻力降等于单位截面上床层的重力。 当加入的固体原料数量恒定,且他们的膨胀度相 同时,压力的变化,对流化床的阻力没有影响。
三 加压流化床气化的特点
1.压力对流化床的流体力学影响 (2)床层膨胀度的影响
当气流的重量流量不变时,随着压力的提高床层膨胀 度α 急剧下降。为了使α 达到保证正规流化所必需的值, 则须提高气体的线速度即增加鼓风量。同时也使气体在床 层中的停留时间相应增加,从而为强化气化过程创造了条 件。而且,一般情况下加压流化床的工作状态比常压下稳 定。
三 加压流化床气化的特点
1.压力对流化床的流体力学影响 (3)对带出物带出条件的影响
2.压力对流化床气化过程的影响
(1) 加压流化床与常压流化床相比,压力对气 化过程最大的影响是使气化炉的生产能力得到了很 大的提高。
三 加压流化床气化的特点
2.压力对流化床气化过程的影响
(2)加压气化有利于提高煤气组成中的有效成分。压力 的提高,有利于甲烷的生成反应,故在压力煤气中,甲烷 含量均高于常压煤气,使煤气热值得到相应提高。甲烷生 成热的释放,降低了气化的氧耗。如若氧气用量不变,则 炉温可得到相应提高,在灰熔点允许的范围内,炉温的适 当提高则有利于一氧化碳和氢气的生成,并可部分抵消因 压力增加,对该两反应造成的不利影响。
四 对原料的要求
流化床气化一般要求原煤破碎成<10mm粒径的煤, <1mm粒径细粉应控制10%以下,经过干燥除去大部分外 在水分,进气化炉的煤含水量<5%为宜。 试验证明流化床更适合活性高的褐煤、长焰煤和弱黏 烟煤,气化贫煤、无烟煤、焦粉时需提高气化温度和增加 煤粒在气化内的停留时间。 固体干法排渣,为防止炉内结渣除保持一定的流化速 度外,要求煤的灰熔点ST应大于1250℃,气化炉操作温度 (表温)一般选定在比ST温度低150~200℃的温度下操作 比较安全。
流化床式气流粉碎机

流化床式气流粉碎机流化床式气流粉碎机是一种常用于粉碎各种物料的设备,特别适用于粉碎细粒度的物料。
它采用了流化床技术,通过将气流经过粉碎室,将物料悬浮在气流中进行粉碎,实现了高效的粉碎效果。
下面将详细介绍流化床式气流粉碎机的工作原理、结构特点以及应用前景。
一、工作原理流化床式气流粉碎机采用气流粉碎的原理,即通过将气流从底部经过狭缝进入粉碎室,使物料被悬浮在气流中,然后经过与高速旋转的粉碎器撞击、摩擦和剪切等作用,实现物料的粉碎。
同时,利用气流的携带能力,将粉碎后的物料和气流一起送至分离器,通过气流的排出和分离器的作用,分离出细粉和粗粉两部分,达到所需的粒度要求。
二、结构特点1.粉碎室:流化床式气流粉碎机的粉碎室由进料装置、喷射装置、旋转刀盘和排料装置组成。
进料装置将物料导入粉碎室,喷射装置将气流导入粉碎室,旋转刀盘用来粉碎物料,排料装置将粉碎后的物料和气流分离并排出。
2.分离器:分离器通常采用旋风分离器,通过离心力的作用,将粉碎后的物料和气流进行分离。
细粉在离心力的作用下沉降到底部,并通过排料装置排出,而粗粉则被气流带走,经过循环利用或进一步处理。
3.控制系统:流化床式气流粉碎机的控制系统主要包括气流控制系统和粉碎控制系统。
气流控制系统用于控制气流的流量、速度和温度等参数,以满足不同物料的需要。
粉碎控制系统用于控制粉碎的程度,调整刀盘的转速和喷射装置的气流压力等。
三、应用前景1.粉体冶金工业:流化床式气流粉碎机可用于粉碎金属粉末、合金粉末等,并广泛应用于粉体冶金工业中的冶金矿石破碎、焙烧和制备金属粉末等工艺。
2.化学工业:流化床式气流粉碎机可用于粉碎化学品、石英、氧化铁、氧化锌等物料,并可应用于化工行业中的颜料、涂料、涂料、染料等制造过程。
3.环保工程:流化床式气流粉碎机可用于粉碎废弃物料、废旧物料等,并可应用于环境保护领域中的垃圾处理、固废处理等工艺。
4.食品工业:流化床式气流粉碎机可用于对食品原料进行粉碎,并广泛应用于食品工业中的食品加工和食品制造过程。
流化床气流磨气流粉碎机设备工艺原理

流化床气流磨气流粉碎机设备工艺原理流化床气流磨气流粉碎机也称气力磨,是一种新型气流粉碎设备。
其粉碎方法利用气流对物料进行冲击磨损,粉碎速率快、效率高,对热敏性和易物质反应性较高的物料具有较好的粉碎效果。
本文将从设备结构、工艺原理、操作方法及应用范围等方面介绍流化床气流磨气流粉碎机的相关知识。
设备结构流化床气流磨气流粉碎机主要由进料装置、磨粉室、出料装置、气体分配系统、气力循环系统、热风循环系统、控制系统等部分组成。
具体结构如下:进料装置进料装置包括进料口、进料管及进料调节阀等,负责将待处理的物料送入磨粉室。
磨粉室磨粉室是流化床气流磨气流粉碎机的主要工作区域,包括磨盘、磨轮、磨盘盖、风道等部分。
磨盘和磨轮由高速电机带动旋转,使物料受到强烈的气流作用,达到快速粉碎的目的。
出料装置出料装置由出料口、出料管及出料调节阀组成,负责将被粉碎的物料从磨粉室中排出。
气体分配系统气体分配系统包括送风装置、排风装置、气流控制装置等,负责调节磨粉室内的空气流量及压力等参数,保证设备运行的稳定性。
气力循环系统气力循环系统由排风装置、分集器、循环管道等构成,主要功能是将磨粉室内的粉尘气体收集,通过分离和回收处理,实现资源的循环利用。
热风循环系统热风循环系统包括热风装置、预热器、加热器、热媒循环系统和温控系统,主要功能是通过对热风的加热控制,提高设备的运行效率。
控制系统控制系统负责对设备整个系统进行综合控制,包括设备的启动、停机、调整、报警等等。
以上是流化床气流磨气流粉碎机的主要设备结构,总体上来说,设备结构紧凑,操作简便,粉碎效率高。
工艺原理流化床气流磨气流粉碎机的工艺原理主要是利用气流对物料进行粉碎,涉及到气流运行状态、物料性质等多方面因素。
具体原理如下:气流运行状态流化床气流磨气流粉碎机中的气流被分为三种状态:拖曳状态、摩擦状态和碰撞状态。
在进料过程中,物料被气流拖曳进入磨粉室,进而被气流带起形成循环流,最终达到快速粉碎的效果。
流化床气流磨粉碎硅灰石针状粉的形状分析
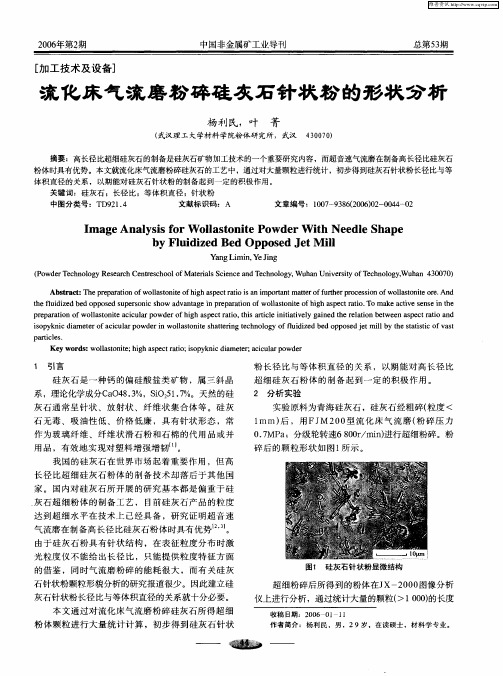
1 引 言
粉 长径 比与 等体 积直 径 的 关系 ,以期 能对 高 长径 比 超 细硅 灰石 粉 体 的制备 起 到一 定 的积极 作 用 。
2 分析实验
硅ቤተ መጻሕፍቲ ባይዱ灰石 是一 种钙 的偏 硅酸 盐类 矿 物 ,属 三 斜 晶
系 ,理论化学成分C 0 8 3 a 4 .%,SO,1 7 i 5 .%。天然 的硅 灰石 通常 呈 针状 、放 射状 、纤维状 集 合体 等 。硅 灰
关键词 :硅 灰石 ;长径 比;等体 积直 径 ;针状粉
中图分类号 :T 2 . D9 1 4 文献标识码 :A 文章编 号:10 — 3 62 0 )2 0 4 — 2 0 7 9 8 (0 60 — 0 4 0
I a eAn l ssf rW o l so iePo m g a y i o i t n t wde ih Ne d e S a e a rW t e l h p
i p k i da tr f cc l o d rnw l s nt sat n c n lg f liie e p oe t i yte t i i o s s y nc imee i a p w e ol t i t r gt h oo yo udzdb do p sd e m lb a sc f at o o a ur i ao eh e i e f j l h s t t v
实验原料 为青海 硅灰石 ,硅灰石 经粗碎 ( 粒度 <
1 mm) ,用FJ 2 0 流 化 床 气 流 磨 ( 碎 压 力 后 M 0型 粉 07 a .MP ;分级轮转速68 0 / n进行超细粉碎 。粉 0 r mi ) 碎 后的颗 粒形 状如 图1 示 。 所
灰石 超 细粉 体 的制备 工 艺 , 目前 硅灰 石产 品的粒 度
流化床工艺的三种类型PK

流化床工艺目前主要有三种类型:顶喷、底喷、旋转切线喷。
由于设备构造不同,物料流化状态也不相同。
采用不同工艺,包衣质量和制剂释放特性可能有所区别。
原则上为了使衣膜均匀连续,每种工艺都应尽量减少包衣液滴的行程,即液滴从喷枪出口到底物表面的距离,以减少热空气对液滴产生的喷雾干燥作用,使包衣液到达底物表面时,基本保持其原有的特性,浓度和粘度没有明显增加,以保证在底物表面理想的铺展成膜特性,形成均匀、连续的衣膜。
1、底喷工艺又称为Wurster系统,是流化床包衣的主要应用形式,已广泛应用于微丸、颗粒,甚至粒径小于50μm粉末的包衣。
底喷装置的物料槽中央有一个隔圈,底部有一块开有很多圆形小孔的空气分配盘,由于隔圈内/外对应部分的底盘开孔率不同,因此形成隔圈内/外的不同进风气流强度,使颗粒形成在隔圈内外有规则的循环运动。
喷枪安装在隔圈内部,喷液方向与物料的运动方向相同,因此隔圈内是主要包衣区域,隔圈外则是主要干燥区域。
颗粒每隔几秒种通过一次包衣区域,完成一次包衣-干燥循环。
所有颗粒经过包衣区域的几率相似,因此形成的衣膜均匀致密。
实验和中试型设备(空气分配底盘直径大至18英寸)使用一个隔圈和喷枪,形成一个包衣区域。
大生产设备(空气分配底盘直径大至46英寸)增加隔圈和喷枪数量,扩大包衣区域以提高生产效率。
Wurster HS是底喷工艺的一项新技术,对传统Wurster喷枪系统进行了一些改进,使颗粒避免接触到喷嘴局部还未充分雾化的包衣液滴,和喷嘴局部由于雾化压力产生的负压区域,因此颗粒产生粘结的几率大大降低。
与传统Wurster系统相比,Wurster HS系统中:•喷液速率提高3-4倍,每个喷枪可达500-600g/min,因而充分利用了流化床的干燥效率,缩短生产周期;•喷枪可以使用较高的雾化压力,以形成非常小的雾化液滴,满足对小于100μm 颗粒的包衣需求;•颗粒避免接触喷嘴局部的压缩空气高速区域,减少包衣初期的表面磨损,有利于保持恒定的比表面积。
MBBR生物流化床工艺说明

MBBR™生物流化床工艺说明MBBR™生物膜工艺运用生物膜法的基本原理,充份利用了活性污泥法的优点,又克服了传统活性污泥法及固定式生物膜法的缺点。
技术关键在于研究与开发了比重接近于水,轻微搅拌下易于随水自由运动的生物填料。
生物填料具有有效表面积大,适合微生物吸附生长的特点。
填料的结构以具有受保护的可供微生物生长的内表面积为特征。
当曝气充氧时,空气泡的上升浮力推动填料与周围的水体流动起来,当气流穿过水流与填料的空隙时又被填料阻滞,并被分割成小气泡。
在这样的过程中,填料被充分地搅拌并与水流混合,而空气流又被充分地分割成细小的气泡,增加了生物膜与氧气的接触与传氧效率。
在厌氧条件下,水流与填料在潜水搅拌器的作用下充分流动起来,达到生物膜与被处理的污染物充分接触而生物分解的目的。
流动床TM生物膜反应器工艺由此而得名。
其原理示意图如图1所示。
因此,流动床TM生物膜工艺突破了传统生物膜法(固定床生物膜工艺的堵塞与配水不均,以及生物流化床工艺的流化局限)的限制,为生物膜法更广泛地应用于污水的生物处理奠定了较好的基础。
专利技术的Kaldnes悬浮填料工艺打开了污水生物处理工艺的新领域。
该工艺就是基于一种生物膜技术,其实质就是微生物以膜状生长悬浮填料上。
该悬浮填料由聚乙烯材料制成,在水中自由飘动。
在悬浮填料上没有附着生物膜的情况下,其比重接近于1g/cm3。
在好氧反应器中由于曝气器的曝气以及缺氧单元中的机械搅拌而不断运动。
悬浮填料反应器内最大填料填充率可以达到67%,其有效生物膜面积可以达到350m2/m3反应器容积。
该工艺可以通过硝化与反硝化作用完成生化好氧降解有机污染物(如BOD,COD)或完成生物脱氮,后者适用于预反硝化或后反硝化或者两者结合。
在后反硝化过程中在反应器中的总水力停留时间只要2、5-3小时就可以使脱氮率达到70%。
Kaldnes工艺与传统活性污泥法相比优点很多,例如具有高容积利用率,反应器形状灵活,无污泥回流的优点。
- 1、下载文档前请自行甄别文档内容的完整性,平台不提供额外的编辑、内容补充、找答案等附加服务。
- 2、"仅部分预览"的文档,不可在线预览部分如存在完整性等问题,可反馈申请退款(可完整预览的文档不适用该条件!)。
- 3、如文档侵犯您的权益,请联系客服反馈,我们会尽快为您处理(人工客服工作时间:9:00-18:30)。
流化床气流磨工艺-标准化文件发布号:(9456-EUATWK-MWUB-WUNN-INNUL-DDQTY-KII流化床气流磨一、流化床气流磨原理简介流化床气流磨是压缩空气经拉瓦尔喷咀加速成超音速气流后射入粉碎区使物料呈流态化(气流膨胀呈流态化床悬浮沸腾而互相碰撞),因此每一个颗粒具有相同的运动状态。
在粉碎区,被加速的颗粒在各喷咀交汇点相互对撞粉碎。
粉碎后的物料被上升气流输送至分级区,由水平布置的分级轮筛选出达到粒度要求的细粉,未达到粒度要求的粗粉返回粉碎区继续粉碎。
合格细粉随气流进入高效旋风分离器得到收集,含尘气体经收尘器过滤净化后排入大气。
流化床气流磨用于各种硬度工业废弃物微粉化的研究与产品开发。
二、工艺流程介绍流化床气流磨对压缩空气的要求在0.7-0.8MPa之间,需要保持压力稳定,即使有波动,但是频率不宜过高,否则将会影响产品的质量。
其次,对气体质量,要求洁净、干燥,应对压缩空气进行净化处理,把气体中的水份、油雾、尘埃清除,使被粉碎的矿产物料不受污染,特别对要求纯度较高的物料的粉碎要求更高,因此当需要一级、二级过滤器以及冷冻式干燥机对空气进行净化处理。
用提升机把原料提升原料仓内,然后通过输料阀把原料送入气流粉碎机的粉碎室。
原料输送机输送原料的速度采用自动控制保持粉碎室的原料和空气混合的浓度相对稳定,我们采用这样的方法可以达到粉碎时超细粉产量最佳。
粉碎室内对称安装有两对喷嘴,压缩空气通过喷嘴时形成超音速气流带起原料进行加速,在空间相互碰撞,把原料粉碎成超细粉,粉碎效果和喷嘴内径形状、距离,对称性以及原料和空气的混合浓度有关。
喷嘴内径形状决定其形成音速的最佳速度、距离以及决定原料加速路程。
分级是通过高速旋转的分级轮进行,分级轮像一个圆“铁桶”底部的中心固定在直连电机的主轴上,由电机驱动高速旋转,开口处和微粉收集系统的管道入口相对,且保持一定间隙也不能过大,否则未经分选的粗粉从间隙进入微粉收集系统的管道,影响产品质量,为防止此类事件发生,在间隙处进行气封处理。
分级轮的用边安装有叶片,叶片间的缝隙为分选微粉的通道。
被粉碎的微粉随气流飘起,超细粉由于粒径小便于通过叶片间的缝隙进入微粉收尘器,较大的颗粒,在分级轮的离心力作用下,飞溅到外壁后降落,进行再次粉碎。
调整分级轮的转速,可以得到不同粒径的产品。
对于粉碎室内,原料和空气的混合浓度的控制,可以用电容式物料密度控制开关或传感器控制。
当物料和空气混合浓度增加时,随气流飘起的粉尘密度增加,撞击分级轮的粉尘增加,使驱动电机的电流增加,反之驱动电机的电流减小,利用电机电流的大小,控制输送原料的多少,可使物料和空气的混合浓度调到最佳,当驱动电流增加立即停止输料,以达到出粉和输料保持动态平衡,保证产品质量的稳定。
微粉收集系统由旋风分离器和粉尘收集组成,超细粉通过密封管道进入旋风分离器,气流在旋风分离器内旋转,把超细粉甩出降落,由排料系统排出包装即是成品。
旋风分离器可以用一级或两级,从旋风分离器飘出的气流,还有部分粉尘进入粉尘收集器,通过布袋上的粉尘,其尾气在引风机的作用下抽出,粉尘含量非常少,为防止这些粉尘排入大气中污染环境,可以增加一套粉尘过滤器,回收粉尘,尾气最后排入大气中。
整个生产过程由控制柜自动控制进行,控制柜供给整个生产用电机(不包括气源用电),还可以控制参数调整,自动启停,自动保护,故障报警及自动停机。
保障设备安全运行和产品质量的稳定。
图1所示为其工艺流程图。
图1 流化床气流磨工艺流程图三、主要设备由上面的工艺流程介绍,我们可以发现,一台完整的流化床气流磨系统由表1所列出的部件所组成。
表1 流化床气流磨主要设备构成四、控制要求4.1需要控制的参量①氮气浓度此系统内含一套高精度氧含量检测装置和自动补氮装置,其功能是在线实时控制。
将系统内的氧气含量检测出来,然后根据检测的结果来决定是否需要进行补氮。
如果系统中氧含量超标,则系统自动地启动补氮阀,高纯氮自动向系统补充。
当系统达到所需的氮气纯度时,补氮阀自动关闭。
在系统粉碎易燃物料时,该设备配套防火装置。
系统氧含量超标且不能及时补充纯氮时,系统会自动切断闭环系统的通路,以防止系统中火源进入过滤器和压机。
②分级机的转速在分级轮的离心力作用下,飞溅到外壁后降落,进行再次粉碎。
调整分级轮的转速,可以得到不同粒径的产品。
③气流磨喷嘴加速距离喷嘴出口到碰撞面的距离越短,颗粒的碰撞速度越高,从而粉碎产生的颗粒越细。
④给料量磨机内颗粒浓度是影响颗粒碰撞几率和颗粒所携平均动能的重要因素之一。
在气流磨中给料量的大小与其中的颗粒浓度极为相关。
当给料量大时,颗粒相互碰撞的几率较大,同时颗粒所携平均动能也较低。
在给料量较低的情况下,气流粉碎过程受颗粒所携平均动能的影响比颗粒碰撞几率的影响更大,粉碎产生的细颗粒也越多。
⑤气流磨的工作压力气流磨的工作压力是影响喷射气流速度的重要因素,往往工作压力越大,喷射气流速度越高。
在气流平稳、颗粒随流性较好的情况下,喷射气流的速度越高,往往被加速的颗粒其碰撞速度越高,因而粉碎程度越大,产品粒度越小,然而,当工作压力过高时,喷射气流速度随工作压力提高而增加缓慢,颗粒的粒径下降已不明显,而能耗急剧增大,因此一般采取的压力不宜过高;喷嘴入口压力与出口压力必须满足一定的条件才能使出口气流速度达到设计的值(音速或一定马赫数)当提高入口压力无法获得相应的高产量和足够的细度时,必须考虑能耗、成本及磨机的效率等问题。
⑥速度影响相应的气流粉碎工作时,其高速的气流能够带动物料,通过高速的转动将动能转化为对物料颗粒的粉碎能力,不过喷嘴的气流速度下降比较快,如果物料的粒度越小,那么其被加速达到的速度就会越大,其最大速度需要的加速距离也就越短;如果粒度越大,其需要的被加速达最大速度也就越小,则其加速的距离也相对越长。
所以,对于流化床气流磨的喷嘴的速度调整的合适与否。
直接影响着物料的最终粉碎效果。
其喷嘴的加速距离和颗粒的密度,进料的粒度,物料的气固浓度以及产品的力度存在着较为紧密的关系。
⑦原料和空气混合的浓度当物料和空气混合浓度增加时,随气流飘起的粉尘密度增加,撞击分级轮的粉尘增加。
4.2 生产工艺对控制系统的要求图2为流化床式气流磨超细粉生产线设备示意图。
物料由下料仓1经双翻板蝶阀2送入喂料机构3,再由喂料机构送入磨室7。
磨室内设有四个对喷的喷嘴,物料被喷嘴喷出的高压高速气流旋起,在磨室内物料颗粒在高速气流所孕育的巨大动能的作用下被加速,在喷嘴8交汇处发生相互冲击碰撞,从而达到粉碎目的。
被粉碎的物料随上升气流到达到分级区,分级区内的涡轮式超微分选器6分选出所需细度的物料经过出料筒被高效旋风分离器9收集。
粉体的粉碎和分级在同一腔体内同时进行,大大提高了粉体的粉碎和分级的功效,未被分选器分选的粗料又返回到对撞粉碎区继续粉碎。
这样连续加料,在磨腔内按上述循环周而复始,连续出料生产。
输出的细料经高效旋风分离器出料口10收集产品,物料分离后的气流经过过滤器12过滤、净化后通过滤清粉单向阀13可反复循环使用。
图2 流化床式气流磨生产设备示意图根据生产工艺的要求,控制系统的动作描述如下:(1)开控制柜电源、开冷却水开关、系统进入初始化模块,在完成初始化操作后,进行低压补、排气操作。
(2)在低、高压罐压力到达额定值后,PLC 若处于远程控制下,压缩机运行按钮有效时,打开压缩机进气口阀,启动压缩机运行,并对压缩机的出口压力进行调节。
(3)在压缩机出口压力满足要求后,当开研磨阀按钮有效时,打开研磨阀,对研磨阀出口压力进行调节。
(4)在研磨阀出口压力满足要求后,根据操作时序,依次完成下料、喂料、分离、过滤等操作。
(5)系统在(1)到(4)之间循环,当停机按钮或急停有效时,系统退出循环。
五、控制策略5.1系统软件组成系统的控制软件按生产工艺的要求,划分为功能相对独立的模块,每一模块独立完成一项特定的功能最后由主控模块将它们按逻辑进行组装。
采用模块化设计,使程序的结构简单明了,易于调试。
本次控制系统共包含6 个大的控制模块,每个大的模块内可能含若干个完全独立的小模块。
如表 1 所示:表1 控制系统软件功能模块洗模块6 停机处理模块执行关机或紧急关机操作正常停机或紧急停机信号有效正常关机模块、紧急关机模块5.2料位控制磨室内料位的控制是提高磨机效率和粉碎产品质量的重要因素之一,是气流磨自控系统中的关键技术。
由于物料在磨室内是流动的,而且在空间的分布密度受压力、流速变化的影响很大,因此所谓的料位控制,实际上是物流量的控制。
本系统采用料位闭环变频调速控制方式,实现料位的闭环控制,其控制框图如图 3 所示。
图 3 料位闭环变频调速控制框图XLC-下料仓;FBJG-翻板机构;BPQ-变频器;GLJG-给料机构;MS磨室;LWFK-料位反馈;MLZLFK-磨室重量反馈物料由下料仓经翻板机构进入到由变频器控制电机拖动的螺杆推进式给料机构中,再由给料机构将物料送入磨室中。
其中翻板机构中蝶阀的开度受磨室重量信号的控制,当磨室重量由下限值(磨室空载)向上限值(磨室满载)变化时,蝶阀的开度相应的由大向小变化,下料仓通过蝶阀进入给料机构中的物料由多变少,当到达上限值时,蝶阀完全闭合,此时下料仓就停止向给料机构供料,直到磨室的重量下降到某一设定值,蝶阀开启恢复供料。
同时给料机构中的螺杆推进速度受料位信号的控制,当上限料位信号有效时,变频器输出零赫兹频率,给料电机停转,螺杆就停止往磨室送料。
当下限料位信号有效时,变频器输出设定的满赫兹频率,给料电机以设定的最高速旋转,推动螺杆以设定的最高速给磨室供料。
当料位在上、下限之间连续变化时,变频器的输出频率在零到设定的最大值之间连续变化,导致螺杆的推料速度也在相应的零到设定的最大值之间连续变化。
通过以上两级闭环控制,就可以使磨室内物料量适中、稳定,始终处于最佳研磨状态。