底喷流化床
药用负压底喷式流化床包衣机创新性与应用性浅析
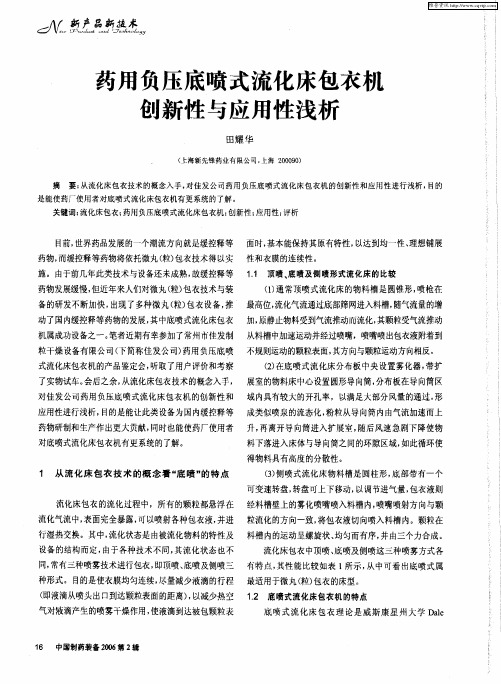
3 佳 发公 司药 用 负压 底喷 式 流 化床 包 衣 机创 新 性 浅析
31 药 用负压底 喷式流化床包 衣机关键技 术创新性 .
浅 析
顶喷 底喷 侧喷
大 中 小
中 高 低
随机 规则 规则
高 低 低
快 中 低
大 中
制粒 包衣
低 包衣、 制粒 ( 丸)
流化气流中, 表面完全暴露, 喷射各种包衣液, 可以 并进 粒流化的方向一致, 将包衣液切 向喷入料槽内。颗粒在
行湿热交换。其 中, 流化状态是 由被流化物料 的特 性及 料槽内的运动呈螺旋状、 均匀而有序, 并由三个力合成。 设备的结构而定, 由于各种 技术 不 同, 其流化状态 也不
基本原 理 负压技术是整机的关键之首, 其负压的创新性体现 在其系统的优化设置, 从而使包衣的整个工艺过程处于 工作时, 将物料按规格不低于 8% 0 的投料量投入流 密闭与负压状态, 达到了以下效果: 化床室, 通过气缸升压将各筒体密封, 开启引风机和加 ( 系统负压工艺流程可有效地避免包衣材料中有 1 )
气对液滴产生的喷雾干燥作用 , 使液滴 到达被包颗粒表 底喷 式流 化 床包 衣 理论 是 威斯 康 星 州大 学 D l a e
1 中国制药装备 2 0 2辑 6 06第
维普资讯
曼 :
表 1 i 种 喷 雾 方 式 性 能对 比
床型 风量 … 适用
流化床包衣中顶喷、 底喷及侧喷这三种喷雾方式各
同, 常有三种喷雾技术进行包衣, 即顶喷、 底喷及侧喷三 有特 点 , 能 比较如表 l 其性 所示 , 中可看 出底喷式属 从
种形式 。目的是使衣膜均匀连续, 尽量减少液滴的行程 最适用于微丸 ( 包衣 的床型。 粒)
流化床工作原理

流化床工作原理流化床是一种重要的化工设备,它在化工、冶金、环保等领域有着广泛的应用。
流化床工作原理是指在一定的条件下,固体颗粒物料在气体流动的作用下呈现出流态化的状态,这种状态下颗粒物料表现出液体的特性,具有较高的传热、传质性能。
下面我们来详细介绍一下流化床的工作原理。
首先,流化床的工作原理是基于气体流动的作用。
当气体通过床体底部喷嘴喷入时,床内的颗粒物料受到气体流动的冲击,开始呈现出流态化的状态。
在这种状态下,颗粒物料之间的空隙增大,表面积增加,使得颗粒物料表现出液态的特性,可以充分混合、传热、传质。
其次,流化床的工作原理还与颗粒物料的密度和粒径有关。
通常情况下,当颗粒物料的密度较大、粒径较小时,流化床的流态化效果会更好。
因此,在实际应用中,需要根据颗粒物料的性质和工艺要求来选择合适的颗粒物料。
另外,流化床的工作原理还与气体流速和流化剂的选择有关。
气体流速的大小会直接影响床内颗粒物料的流态化状态,通常情况下,流速越大,颗粒物料的流态化效果越好。
而流化剂的选择也会对流化床的工作原理产生影响,不同的流化剂对颗粒物料的流态化特性有着不同的影响。
此外,流化床的工作原理还与床内物料的混合、传热、传质等过程密切相关。
在流化床中,气固两相之间的充分混合使得床内物料的传热、传质效果得到了显著提高,这对于一些需要进行反应、干燥、吸附等工艺过程具有重要的意义。
综上所述,流化床的工作原理是基于气体流动的作用,通过控制气体流速、选择合适的颗粒物料和流化剂,实现颗粒物料的流态化状态,从而达到充分混合、传热、传质的效果。
流化床在化工生产中具有重要的应用价值,了解其工作原理对于提高流化床的工艺效果具有重要的意义。
希望本文能够帮助大家更深入地了解流化床的工作原理,为相关领域的工程技术人员提供参考。
流化床使用的10项基本原则
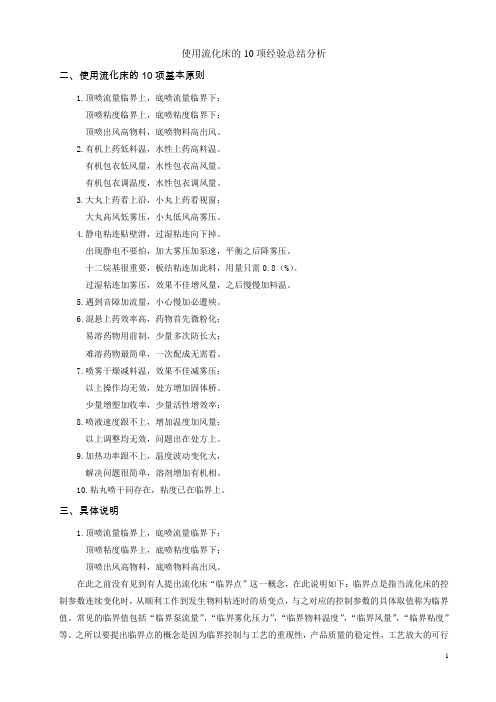
使用流化床的10项经验总结分析二、使用流化床的10项基本原则1.顶喷流量临界上,底喷流量临界下;顶喷粘度临界上,底喷粘度临界下;顶喷出风高物料,底喷物料高出风。
2.有机上药低料温,水性上药高料温。
有机包衣低风量,水性包衣高风量。
有机包衣调温度,水性包衣调风量。
3.大丸上药看上沿,小丸上药看视窗;大丸高风低雾压,小丸低风高雾压。
4.静电粘连贴壁滑,过湿粘连向下掉。
出现静电不要怕,加大雾压加泵速,平衡之后降雾压。
十二烷基很重要,板结粘连加此料,用量只需0.8(%)。
过湿粘连加雾压,效果不佳增风量,之后慢慢加料温。
5.遇到音障加流量,小心慢加必遭殃。
6.混悬上药效率高,药物首先微粉化;易溶药物用前制,少量多次防长大;难溶药物最简单,一次配成无需看。
7.喷雾干燥减料温,效果不佳减雾压;以上操作均无效,处方增加固体桥。
少量增塑加收率,少量活性增效率;8.喷液速度跟不上,增加温度加风量;以上调整均无效,问题出在处方上。
9.加热功率跟不上,温度波动变化大,解决问题很简单,溶剂增加有机相。
10.粘丸喷干同存在,粘度已在临界上。
三、具体说明1.顶喷流量临界上,底喷流量临界下;顶喷粘度临界上,底喷粘度临界下;顶喷出风高物料,底喷物料高出风。
在此之前没有见到有人提出流化床“临界点”这一概念,在此说明如下:临界点是指当流化床的控制参数连续变化时,从顺利工作到发生物料粘连时的质变点,与之对应的控制参数的具体取值称为临界值。
常见的临界值包括“临界泵流量”,“临界雾化压力”,“临界物料温度”,“临界风量”,“临界粘度”等。
之所以要提出临界点的概念是因为临界控制与工艺的重现性,产品质量的稳定性,工艺放大的可行性密切相关,直接关系到研发的成败。
“顶喷流量临界上,底喷流量临界下”说的是在顶喷造粒时应当将泵流量控制高于流量临界点以上,使得喷出的粘合剂多于临界泵流量时的粘合剂量,这时的粘合剂能在细粉粒子之间形成液体桥,逐步干燥过程形成固体桥,干燥后形成稳定的颗粒。
流化床制粒技术介绍
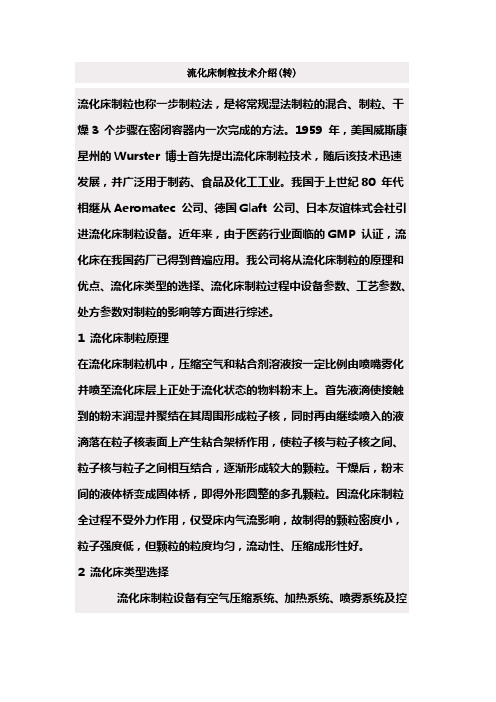
流化床制粒技术介绍(转)流化床制粒也称一步制粒法,是将常规湿法制粒的混合、制粒、干燥3 个步骤在密闭容器内一次完成的方法。
1959 年,美国威斯康星州的Wurster 博士首先提出流化床制粒技术,随后该技术迅速发展,并广泛用于制药、食品及化工工业。
我国于上世纪80 年代相继从Aeromatec 公司、德国Glaft 公司、日本友谊株式会社引进流化床制粒设备。
近年来,由于医药行业面临的GMP 认证,流化床在我国药厂已得到普遍应用。
我公司将从流化床制粒的原理和优点、流化床类型的选择、流化床制粒过程中设备参数、工艺参数、处方参数对制粒的影响等方面进行综述。
1 流化床制粒原理在流化床制粒机中,压缩空气和粘合剂溶液按一定比例由喷嘴雾化并喷至流化床层上正处于流化状态的物料粉末上。
首先液滴使接触到的粉末润湿并聚结在其周围形成粒子核,同时再由继续喷入的液滴落在粒子核表面上产生粘合架桥作用,使粒子核与粒子核之间、粒子核与粒子之间相互结合,逐渐形成较大的颗粒。
干燥后,粉末间的液体桥变成固体桥,即得外形圆整的多孔颗粒。
因流化床制粒全过程不受外力作用,仅受床内气流影响,故制得的颗粒密度小,粒子强度低,但颗粒的粒度均匀,流动性、压缩成形性好。
2 流化床类型选择流化床制粒设备有空气压缩系统、加热系统、喷雾系统及控制系统等组成。
主要结构由容器、空气分流板、喷嘴、过滤袋、空气进出口、物料排出口等组成。
按其喷液方式的不同分为3 类:顶喷流化床、转动切喷流化床、底喷流化床。
流化床制粒一般选择顶喷流化床。
近年来,为了发挥流化床制粒的优势,亦出现了一系列以流化床为母体的多功能复合型制粒设备。
如我公司新推出的多功能流化床、搅拌流化制粒机、转动流化制粒机、搅拌转动流化制粒机等。
现我们仅就流化床制粒进行探讨。
3 流化床制粒的优点尽管流化床制粒受到诸多因素影响,但与其他制粒方式相比,该技术仍具有很多优点。
a .物料的干混、湿混、搅拌、颗粒成型、干燥都在同一台流化床设备内完成,减少了大量的操作环节,节约了生产时间。
实验室多功能流化床包衣设备(制粒、微丸、干燥)

实验室多功能流化床包衣设备(制粒、微丸、干燥)概述:实验型多功能流化床是专为科研机构,各高校量身定制的功能强大的研发型设备,其设计兼顾了灵活性与适用性,可在一台设备中完成干燥、制粒、包衣、制备微丸等功能。
实验型多功能流化床是在消化吸收国外同类设备基础上推出的具有多种用途的流化床工艺设备,其设计目的是为了在同一设备中可进行干燥、制粒、制丸、包衣及包裹敷层。
根据不同工艺目的,可采取三种工艺(“顶喷”、“底喷”、“切线喷”)途径实现。
通过更换不同的流化床装置,即可进行三种工艺操作,而其他功能系统则可共用(空气处理系统,机身组件,供液系统,送风系统,控制系统)。
不同的流化床结构是最为核心的技。
三种工艺具有不同的能力,其实质区别仅在于物料的流化和液体的喷入方式不同。
实验室多功能流化床包衣设备(制粒、微丸、干燥)工作原理:在流化床上进行喷雾团聚造粒是一种可以增强粉末性质的成型方法。
通过在流化床系统中进行喷雾,我们可以将粉状、非流动性、溶解度普遍较差的颗粒转化成具有优异溶解度的自由流动的大颗粒。
该方法特别适用于制备片剂以及制造清洁剂、饮用粉末、速溶产品。
流化床喷雾团聚造粒可以移动流化床上极小的粉末颗粒,并对其喷以粘合溶液或悬浮液,产生液桥,使颗粒形成团聚体。
继续喷雾,直到团聚体达到所需大小。
当毛细管以及表面上的残余水分蒸发后,颗粒中形成中空的空间,而硬化的粘合剂也使新结构彻底凝固。
流化床中缺乏动能,会造成极为多孔的结构,其内部存在大量的毛细管。
团聚体的通常尺寸范围为100微米至3毫米,而起始材料可以是超微细的。
流化床干燥—颗粒受控干燥的高效解决方案(FLP1.5多功能流化床包衣机)流化床干燥是对湿润粉末进行受控、柔和、均匀的干燥的最佳方法。
流化床产品剧烈的热量/质量交换使这种方法变得特别有效、省时。
该技术还适用于残余水分极低的喷塑产品和挤塑产品的后干燥。
流化床干燥可用于整个粉末加工业。
在制药行业,这种创新的方法早已取代耗时的托盘干燥:使用流化床干燥的干燥工艺可以将干燥炉中的干燥时间减少约20倍。
综述-流化床微丸包衣影响因素探讨
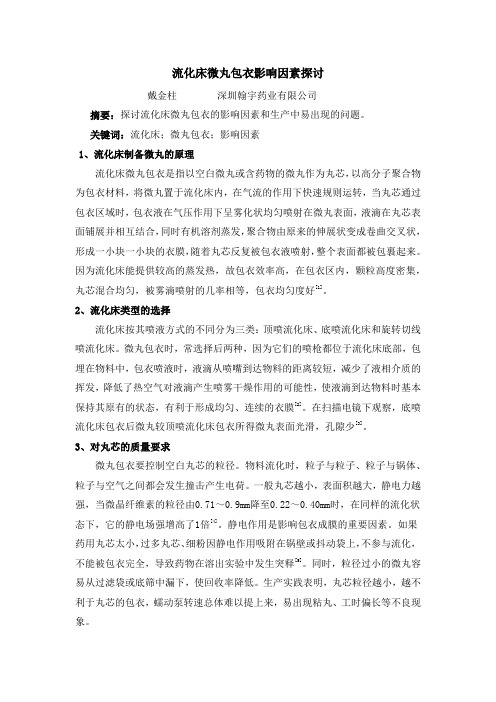
流化床微丸包衣影响因素探讨戴金柱深圳翰宇药业有限公司摘要:探讨流化床微丸包衣的影响因素和生产中易出现的问题。
关键词:流化床;微丸包衣;影响因素1、流化床制备微丸的原理流化床微丸包衣是指以空白微丸或含药物的微丸作为丸芯,以高分子聚合物为包衣材料,将微丸置于流化床内,在气流的作用下快速规则运转,当丸芯通过包衣区域时,包衣液在气压作用下呈雾化状均匀喷射在微丸表面,液滴在丸芯表面铺展并相互结合,同时有机溶剂蒸发,聚合物由原来的伸展状变成卷曲交叉状,形成一小块一小块的衣膜,随着丸芯反复被包衣液喷射,整个表面都被包裹起来。
因为流化床能提供较高的蒸发热,故包衣效率高,在包衣区内,颗粒高度密集,丸芯混合均匀,被雾滴喷射的几率相等,包衣均匀度好[1]。
2、流化床类型的选择流化床按其喷液方式的不同分为三类:顶喷流化床、底喷流化床和旋转切线喷流化床。
微丸包衣时,常选择后两种,因为它们的喷枪都位于流化床底部,包埋在物料中,包衣喷液时,液滴从喷嘴到达物料的距离较短,减少了液相介质的挥发,降低了热空气对液滴产生喷雾干燥作用的可能性,使液滴到达物料时基本保持其原有的状态,有利于形成均匀、连续的衣膜[2]。
在扫描电镜下观察,底喷流化床包衣后微丸较顶喷流化床包衣所得微丸表面光滑,孔隙少[3]。
3、对丸芯的质量要求微丸包衣要控制空白丸芯的粒径。
物料流化时,粒子与粒子、粒子与锅体、粒子与空气之间都会发生撞击产生电荷。
一般丸芯越小,表面积越大,静电力越强,当微晶纤维素的粒径由0.71~0.9mm降至0.22~0.40mm时,在同样的流化状态下,它的静电场强增高了1倍[4]。
静电作用是影响包衣成膜的重要因素。
如果药用丸芯太小,过多丸芯、细粉因静电作用吸附在锅壁或抖动袋上,不参与流化,不能被包衣完全,导致药物在溶出实验中发生突释[5]。
同时,粒径过小的微丸容易从过滤袋或底筛中漏下,使回收率降低。
生产实践表明,丸芯粒径越小,越不利于丸芯的包衣,蠕动泵转速总体难以提上来,易出现粘丸、工时偏长等不良现象。
底喷流化床(Wurster)包衣的操作要点 !

GSP认证及经营许可证办理交流区
ISO17025实验室管理交流区
欧盟CE认证交流区
FDA 美国食品和药物管理交流区
标准资料下载区
标准资讯快递
国外国际标准讨论下载发布区
[ ISO国际标准化组织标准]
[ IEC 国际电工委员会 ]
[ AOAC国际官方分析化学家协会标准 ]
[ BS 英国标准 ]
[ ASTM 美国材料试验协会标准 ]
[ DIN 德国标准 ]
[ JIS 日本标准 ]
[ EN标准 ]
[ NF标准 ]
[ ANSI 标准 ]
[ AATCC标准 ]
[ ETSI标准 ]
[ IS标准 ]
[ 美国标准 ]
国家标准发布下载区
医药行业标准发布下载区
此外,调节间距还可小幅度调节颗粒流化状态。比如遇到导流管外侧颗粒滞留不动时,增加间距,可促使滞留颗粒启动。因为增加间距,也就增加了导流管下面颗粒层的厚度,增大了阻力,逼使空气流向周边小孔。
底喷流化床包衣过程中常见的问题
静电
颗粒在流化床内不停运动,相互摩擦,有静电产生,导致颗粒相互吸引,也被筒壁吸附,颗粒不能正常流化。静电的出现反映颗粒己经比较干燥。用有机溶液包衣,或在干燥季节包衣更容易产生静电。提高进风相
GMT+8, 2009-11-1 01:20. Powered by Discuz! 7.0.0
© 2001-2009 Comsenz Inc.
药物检测分析讨论区
消毒灭菌讨论版块
中药讨论区
药品说明书
[抗病原微生物药]
世界顶尖流化床品牌-Glatt实验室流化床

包衣
具有和底喷系统几乎同样的包衣优点,
因此可以包出高质量的衣膜
粉末上药工艺
优 点: 同一设备中完成上药、干燥、 包衣工艺 生产效率高,生产周期短 适用于各种溶解度性质的药物 制备载药量大的微丸,适合大 剂量药物(增重400~500%) 局限性: 对工艺参数的控制要求较高 药物须微粉化,并加入助流剂
• 防潮及抗氧化 •缓释 特点:
工艺周期短
An Example...
顶喷热熔融包衣
MAIN MENU
未包衣颗粒
30% 包衣增重 Compritol 888
制粒工艺
湿法制粒 – 摇摆式制粒 – 流化床制粒 – 高速混合制粒 干法制粒 熔融制粒
流化床底喷技术
底喷装置也成为Wurster系统, 由Dale Wuster教授研制,是
流化床技术简介
70 年代以来,流化床技术和喷枪技术相结合,应用上有
很大的突破,广泛应用于制粒、包衣、微丸制备等工艺,
主要用于制药、食品、化工、陶瓷等行业。
流化床类型
MAIN MENU
顶喷 制粒
底喷 包衣
切线喷 制微丸
流化床技术简介
设备发展趋势
规格齐全:批处理能力从 2.5g 到大于 1 吨
处方研究设备
Mini-Glatt
工作容积: 200 - 750ml 批 量: 30 - 300 g • 制粒 • 包衣
MAIN MENU
• 干燥
Mini-Glatt 对压缩空气的要求
Compressed air utility:
MAIN MENU
Working pressure: 6 bar flow pressure
- 1、下载文档前请自行甄别文档内容的完整性,平台不提供额外的编辑、内容补充、找答案等附加服务。
- 2、"仅部分预览"的文档,不可在线预览部分如存在完整性等问题,可反馈申请退款(可完整预览的文档不适用该条件!)。
- 3、如文档侵犯您的权益,请联系客服反馈,我们会尽快为您处理(人工客服工作时间:9:00-18:30)。
1.流化床包衣技术的基本概念
1.1 流化现象的概念
在一个设备中,将颗粒物料堆放在分布板上,当气体由设备下部通入床层,随气流速度加大到某种程度,固体颗粒在床层上产沸腾状态,这状态称流态化,而这床层也称流化床。
采用这样方法辅于其它技术可完成物料的干燥、制粒、混合、包衣和粉碎等功能。
由于固体颗粒物料的不同特性,以及床层和气流速度等因素不同,床层可存在三种形态:(1)、第一阶段,当流体速度较低时,在床层中固体颗粒虽与流体相接触,但固体颗粒的相应位置不发生变化,这时固定颗粒的状态为固定床;
(2)、第二阶段,当固定床阶段的流体流速逐渐增加到某一点时,固体颗粒就会产生相互间的位置移动,若再增加流体速度,而床层的压力损失保持不变,固体颗粒再床层就会产生不规则的运动,这时的床层就处于流态化;
(3)、第三阶段,当流体流速大于固体颗粒的沉降速度时,这时固体颗粒就不能继续停留再容器内,而被气流带出容器。
对制药工业应用来说,干燥、制粒、混合、包衣等是利用第二阶段运行的。
1.2 流化床包衣技术的概念
流化床包衣是在流化过程中,所有的颗粒都悬浮在流化气流中,表面完全暴露,可以喷射各种包衣液,并进行湿热交换。
其中,流化状态是由被流化物料的特性及设备的结构而定,由于每种技术不同,其流化状态不同,常有三种喷雾技术进行包衣,即顶喷、底喷及测喷三种形式。
为了使衣膜均匀连续,尽量做到减少液滴的行程(即液滴从喷头出口到达颗粒表面的距离),以减少热空气对液滴产生的喷雾干燥作用,使得液滴到被包颗粒表面时,基本能保持其原有特性,以达到均一性、理想铺展性和衣膜的连续性。
2.从三种流化床包衣技术的比较看“底喷”流化床包衣的特点
流化床包衣技术的三种型式分别为顶喷、底喷及侧喷,下面用表格形式对三种形式的流化床包衣技术作比较(见表1)。
从表1可以看到:三种流化床包衣形式是各有特点,然而综合各项与微粒(丸)包衣要求现也可看到底喷式属其中最适用于微丸(粒)包衣的床型。
底喷式流化床包衣是威斯康星洲大学Dale Wurster博士于1959年创立,其把喷动流态化与喷雾相结合,形成喷泉状态,使工业化包衣变得现实,其工艺的广泛运用至今尚无其它形式所能相比。
在流化床包衣设备分布板中央设置雾化器,即底喷流化床(也称Wurster系统),其中带扩展室的物料床中心设置圆形导向筒,分布板在导向筒区域内具有较大的开孔率,以满足大部分风量通过,形成类喷泉式的流态化,粉粒从导向筒之间的环隙区域,如此的循环。
使物料具有高度的分散性,因而底喷包衣工艺具有人们所期望的工艺重复性。
3.从微丸(粒)包衣工艺要求角度看“负压底喷规则流”流化床包衣的要点
3.1 微丸(粒)包衣工艺与规模生产要求
微丸(粒)包衣应适用于:≥50μm的粉末包衣、粒、丸(≤6mm)掩味、着色、热熔、防潮、抗氧化包衣、粒丸肠溶衣、环释包衣、悬浮液、溶液涂层放大等。
微丸(粒)包衣的要求:
(1)、物料能高度分散并伴随衣膜的喷涂而不产生粘连;
(2)、雾粒到达物料的距离应很短,湿分而不致于快速蒸发掉,与物料产生良好的附着,并具有极强的铺展性,使得衣膜牢固、连续;
(3)、物料与雾粒接触机会应均等,包衣均匀;
(4)、耗用包衣材料较少,且衣膜均匀。
微丸(粒)包衣规模生产时要求:高效、可靠、环保、安全等。
3.2 从微丸(粒)包衣工艺要求看“负压底喷”流化床包衣的要点
要达到上述包衣工艺与规模生产要求时,光有底喷流化床包衣技术是不能完美的,基于制药工业的特殊性,其生产设备力求高效性、可靠性、环保性、安全性和批量化,这就要把负压、底喷和规则流技术整合于一体。
负压技术是整机的关键之首,其负压的创新性是以系统优化设置,使包衣的整个工艺过程处于密封与负压状态,从而达到以下效果:
(1)系统负压工艺流程可有效地避免包衣材料中有机溶媒在气化时的气体外溢,消除易燃易爆事故隐患,减少环境污染;
(2)有利于突发性事故的泄爆,当系统内由于颗粒挤压摩擦、粉尘积累及有机溶媒气化膨胀所产生的压力升高至0.05Mpa时,泄爆装置即会自动打开,并会自动关闭电源,防止事故的发生;
(3)有利于流态化气流量的调节,保持物料流态化的稳定。
规则流型的流态化,喷泉式流态化能使设备中物料具有重现性良好的运行轨迹,这一点是严格包衣操作所不可缺少的,其目的是让物料与雾粒接触机会均等,包衣才会均匀。
同时,物料本身形成自转,其表面任一角度与雾粒接触机会均等。
因而,对于缓释、控释而言,底喷工艺形成的衣膜连续均匀。
生产设计了导向筒装置解决了这一难点。
这种特殊装置能使大部分气流量由中心区域的导向筒内通过,物料呈喷泉状的气流输送(亦称气流输送流化床),而导向筒外侧与塔体壁之间形成的流化床称为标准流化床。
此时,大部分气流量由导向筒下方的分风板进入,在流化床中央形成一粉粒物料柱,当其上升并离开导向筒时,由于风速急剧下降,颗粒将跌落在导向筒与床体间的流化区,再次向导向筒汇集上扬,如此反复循环,形成流化-气流输送-沉降-流化的过程,从而实现了规则流态化。
在结构上,一是导向筒高度可调,随着物料粒径变大,其高度会有所改变;二是流化分布板是随物料性质变化的,其开孔率及其分布采取更换方式调节;三是导向筒高度的合适设计,根据“死床”高度设计太高,碰撞加剧,会产生“衣层”脱落,高度设置太低会影响物料由流化区飞向包衣区迁移,从而引起产生包衣不均。
底喷的雾化不是随意就能达到有效雾化要求的,气流分布板要能使大部分气流量在分布板中心区域通过,分布板的中心区域位于导向筒的正下方,分布板的开孔率达70%以上,从而实现物料以气流输送状态上升,为喷泉流流态化创造必备的条件。
在导向筒与流化床壁环圆区域内,分布板的开孔率则为3%,使物料跌落在此区域内能形成标准的流化状态,有利于物料通过分布板与导向筒间的间隙向导向筒汇集。
这样起到每一滴雾粒能保持与颗粒附着前具有良好润湿性的作用,提高了附着率。
也由于雾化到达粉粒的距离短,不会被过早干燥,故颗粒在附着时其在物料表面具有良好的铺展性。
同时,能扩大衣膜面积,成膜厚薄均匀,润湿性又为衣膜附着牢固提供决定性的条件,最终达到包衣材料的目的。
4.结语
本文从流化床包衣技术概念着手,从三种流化床包衣的比较中看“底喷”流化床包衣的特点,也从微丸(粒)的包衣包衣工艺要求角度阐述“负压底喷规则流”流化床包衣的要点。
目前我公司产品产量从150g/批至200Kg/批。
应用于从粉体包衣至微丸的缓控释产品。
随着微丸制剂与缓控释包衣这一新型制药工艺的兴起,微丸制剂及缓控释包衣以掩味、着色、防潮、抗氧化、遮光、胃溶、隔热、肠溶、缓释及控释的特点决定了相应设备的市场。
文章链接:中国制药机械设备网/Tech_news/Detail/11004.html。