机械加工精度PPT课件
合集下载
机械制造工艺课件第三章机械加工精度
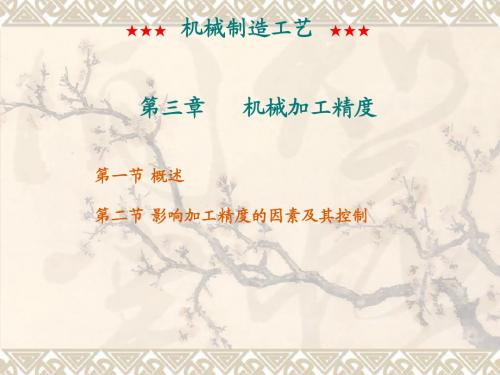
★★★
机械制造工艺
★★★
三、影响加工精度的原始误差
机械加工时,机床、刀具、夹具和工件等组成了一个工艺系统, 工艺系统的各个部分在加工过程中,应该保持严格的相对位臵关系。 由于受到许多因素的影响,系统的各个环节难免会产生一定的偏移, 使工件和刀具间相对位臵的准确性受到影响,从而引起加工误差。 原始误差即导致工艺系统各环节产生偏移的这些因素的总称。原始 误差中,有的取决于工艺系统的初始状态,有的与切削过程有关。 当原始误差的方向发生在加工表面法线方向时,引起的加工误 差最大;当原始误差的方向发生在加工表面的切线方向时,引起的 加工误差最小,一般可以忽略不计。为了便于分析原始误差对加工 精度的影响程度,我们把对加工精度影响最大的那个方向(即通过 切削刃的加工表面的法向)称为误差的敏感方向。而把对加工精度 影响最小的那个方向(即通过切削刃的加工表面的切向)则称为误 差的不敏感方向。
★★★
机械制造工艺
★★★
一、加工原理误差
原理误差即是在加工中由于采用近似的加 工运动、近似的刀具轮廓和近似的加工方法而 产生的原始误差。 完全符合理论要求的加工方法,有时很难实 现,甚至是不可能的。这种情况下,只要能满 足零件的精度要求,就可以采用近似的方法进 行加工。这样能够使加工难度大为降低有利于 提高生产效率降低成本。
★★★
机械制造工艺
ห้องสมุดไป่ตู้
★★★
3)定尺寸刀具法:是直接利用刀具的相应尺寸来 保证加工尺寸的方法。如用钻头钻孔,铰刀铰孔,用拉 刀、铣刀加工键槽等。加工尺寸精度的高低主要与刀具 的制造精度,安装精度和磨损及机床运动精度等因素有 关。这种加工方法加工精度稳定,生产率也高。 4)自动获得尺寸法:是利用测量装臵、调整装臵 和控制系统等组成的自动化加工系统,在加工过程中能 自动测量、补偿调整,当工件达到尺寸要求时,能自动 退回停止加工的方法。
机械加工质量培训课件PPT(共 104张)

例: ①滚刀用阿基米德蜗杆代替渐开线蜗杆 (近似的刀具轮廓); ②模数铣刀铣齿(近似的刀具轮廓); ③用公制丝杆车蜗杆或英制螺纹。 (近似的加工运动)
2.1 机械加工精度
i工 机件 (蜗 床杆 丝) 杆 PP螺 1螺 ZZ距 距 21ZZ34
例1. 在公制车床上车模数为2mm蜗杆时,挂轮计算式为 :
z1 z2
z3 z4
P(P机 (1 床 蜗丝 杆杆 螺螺 距距 )) ,若P=6mm,
Z 1 1,1 Z 2 0 7,Z 0 3 8,Z 0 4 1,2 求加0 工后蜗杆螺距
误差是多少?
i
P1=2
P=6
解: i工 机件 (蜗 床杆 丝) 杆 PP螺 1螺 ZZ距 距 21ZZ34 P ห้องสมุดไป่ตู้iP Z Z2 1Z Z3 4P1 71 0 2 800 066.2857
1)主轴回转误差。 纯径向跳动误差 轴向窜动误差 纯角度摆动误差
①主轴纯径向跳动误差对加精度的影响。 产生的主要原因:主轴支承轴颈的圆度误差、轴承工作表面的
圆度误差等。 a. 切削力F的作用方向不变(见图2-5 车外圆的情形)
2
R
1
3
R3
R1 △R
o o′
理论位置
实际位置
R
4
车外圆时它使加工面产生圆度和圆柱度误差。
@加工质量与设备、工艺方法、工艺措施有关。
2.1 机械加工精度
2.1.1 概述 1、机械加工精度(简称加工精度):是指零件在机械加工后
的几何参数(尺寸、几何形状和表面间相互位置)的实际值和理 论值相符合的程度。
2、加工误差:实际参数与理论参数的差值
2.1 机械加工精度
2.1.2 影响加工精度的因素及其分析 在机械加工中,零件的尺寸、几何形状和表面间相互位置的
2.1 机械加工精度
i工 机件 (蜗 床杆 丝) 杆 PP螺 1螺 ZZ距 距 21ZZ34
例1. 在公制车床上车模数为2mm蜗杆时,挂轮计算式为 :
z1 z2
z3 z4
P(P机 (1 床 蜗丝 杆杆 螺螺 距距 )) ,若P=6mm,
Z 1 1,1 Z 2 0 7,Z 0 3 8,Z 0 4 1,2 求加0 工后蜗杆螺距
误差是多少?
i
P1=2
P=6
解: i工 机件 (蜗 床杆 丝) 杆 PP螺 1螺 ZZ距 距 21ZZ34 P ห้องสมุดไป่ตู้iP Z Z2 1Z Z3 4P1 71 0 2 800 066.2857
1)主轴回转误差。 纯径向跳动误差 轴向窜动误差 纯角度摆动误差
①主轴纯径向跳动误差对加精度的影响。 产生的主要原因:主轴支承轴颈的圆度误差、轴承工作表面的
圆度误差等。 a. 切削力F的作用方向不变(见图2-5 车外圆的情形)
2
R
1
3
R3
R1 △R
o o′
理论位置
实际位置
R
4
车外圆时它使加工面产生圆度和圆柱度误差。
@加工质量与设备、工艺方法、工艺措施有关。
2.1 机械加工精度
2.1.1 概述 1、机械加工精度(简称加工精度):是指零件在机械加工后
的几何参数(尺寸、几何形状和表面间相互位置)的实际值和理 论值相符合的程度。
2、加工误差:实际参数与理论参数的差值
2.1 机械加工精度
2.1.2 影响加工精度的因素及其分析 在机械加工中,零件的尺寸、几何形状和表面间相互位置的
机械加工表面质量PPT51页课件

5.2 加工表面质量对零件使用性能的影响
*
3. 表面纹理对耐磨性的影响
表面纹理的形状及刀纹方向对耐磨性的影响,纹理形状及刀纹方向影响有效接触面积与润滑液的存留。
4.表面层产生的金相组织变化对零件耐磨性的影响
金相组织的变化引起基体材料硬度的变化,进而影响零件的耐磨性。
5.2 加工表面质量对零件使用性能的影响
5.2 加工表面质量对零件使用性能的影响
*
2.表面层冷作硬化与残余应力对耐疲劳性的影响 适度的表面层冷作硬化能提高零件的疲劳强度; 残余应力有拉应力和压应力之分, 残余拉应力:易使已加工表面产生裂纹并使其扩展而降低疲劳强度。 残余压应力:能够部分地抵消工作载荷施加的拉应力,延缓疲劳裂纹的扩展,从而提高零件的疲劳强度。
5.4 影响加工表面层物理机械性能的因素
*
衡量表面层加工硬化程度的指标有下列三项: 1)表面层的显微硬度H; 2)硬化层深度h; 3)硬化程度N N=(H-H0)/H0×100% 式中 H0——工件原表面层的显微硬度。
粗糙度越大,耐腐蚀性越差
压应力提高耐腐蚀性,拉应力反之则降低耐腐蚀性
总结:
*
机械加工中,表面粗糙度形成的原因大致可归纳为几何因素和物理力学因素两个方面。
(一)切削加工时表面粗糙度的影响因素
1. 几何因素
刀尖圆弧半径rε 主偏角kr、副偏角kr′ 进给量f
5.3 影响加工表面粗糙度的因素
(一)表面质量对零件耐磨性的影响
5.2 加工表面质量对零件使用性能的影响
零件磨损三个阶段:初期磨损阶段;正常磨损阶段;剧烈磨损阶段
零件耐磨性的影响因素: 摩擦副的材料;润滑条件;表面质量(接触面积)。
图5-1 磨损过程的基本规律
*
3. 表面纹理对耐磨性的影响
表面纹理的形状及刀纹方向对耐磨性的影响,纹理形状及刀纹方向影响有效接触面积与润滑液的存留。
4.表面层产生的金相组织变化对零件耐磨性的影响
金相组织的变化引起基体材料硬度的变化,进而影响零件的耐磨性。
5.2 加工表面质量对零件使用性能的影响
5.2 加工表面质量对零件使用性能的影响
*
2.表面层冷作硬化与残余应力对耐疲劳性的影响 适度的表面层冷作硬化能提高零件的疲劳强度; 残余应力有拉应力和压应力之分, 残余拉应力:易使已加工表面产生裂纹并使其扩展而降低疲劳强度。 残余压应力:能够部分地抵消工作载荷施加的拉应力,延缓疲劳裂纹的扩展,从而提高零件的疲劳强度。
5.4 影响加工表面层物理机械性能的因素
*
衡量表面层加工硬化程度的指标有下列三项: 1)表面层的显微硬度H; 2)硬化层深度h; 3)硬化程度N N=(H-H0)/H0×100% 式中 H0——工件原表面层的显微硬度。
粗糙度越大,耐腐蚀性越差
压应力提高耐腐蚀性,拉应力反之则降低耐腐蚀性
总结:
*
机械加工中,表面粗糙度形成的原因大致可归纳为几何因素和物理力学因素两个方面。
(一)切削加工时表面粗糙度的影响因素
1. 几何因素
刀尖圆弧半径rε 主偏角kr、副偏角kr′ 进给量f
5.3 影响加工表面粗糙度的因素
(一)表面质量对零件耐磨性的影响
5.2 加工表面质量对零件使用性能的影响
零件磨损三个阶段:初期磨损阶段;正常磨损阶段;剧烈磨损阶段
零件耐磨性的影响因素: 摩擦副的材料;润滑条件;表面质量(接触面积)。
图5-1 磨损过程的基本规律
机械加工质量及其控制概述ppt68页课件

第一节 概述
二、机械加工表面质量
(一)表面质量的概念
粗糙度太大、太小都不耐磨
适度冷硬能提高耐磨性
对疲劳强度的影响
对耐腐蚀性能的影响
对工作精度的影响
粗糙度越大,疲劳强度越差
适度冷硬、残余压应力能提高疲劳强度
粗糙度越大、工作精度降低
残余应力越大,工作精度降低
粗糙度越大,耐腐蚀性越差
压应力提高耐腐蚀性,拉应力反之则降低耐腐蚀性
本章提要
机械产品质量取决于零件的加工质量和产品的装配质量,机器零件的加工质量是整台机器质量的基础。 机器零件的加工质量一般用机械加工精度和加工表面质量两个重要指标表示,它的高低将直接影响整台机器的使用性能和寿命。 机械产品加工的首要任务,就是保证零件的机械加工质量要求。 本章重点讨论影响机械加工精度和表面质量的因素及其控制方法。
(1)主轴回转误差
第二节 机械加工精度的影响因素及控制
一、工艺系统几何误差对加工精度的影响
(一)机床的几何误差
(1)主轴回转误差
第二节 机械加工精度的影响因素及控制
一、工艺系统几何误差对加工精度的影响
(一)机床的几何误差
主轴回转误差的基本形式
车床上车削
镗床上镗削
内、外圆
端面
螺纹
孔
端面
纯径向跳动
机械加工中,采用近似的成形运动或近似的刀刃形状进行加工,虽然会由此产生一定的原理误差,但却可以简化机床结构和减少刀具数,只要加工误差能够控制在允许的制造公差范围内,就可采用近似加工方法。
原始误差
工艺系统动误差
工艺系统受力变形
刀具磨损
残余应力引起变形
测量误差
工艺系统热变形
第二节 机械加工精度的影响因素及控制
二、机械加工表面质量
(一)表面质量的概念
粗糙度太大、太小都不耐磨
适度冷硬能提高耐磨性
对疲劳强度的影响
对耐腐蚀性能的影响
对工作精度的影响
粗糙度越大,疲劳强度越差
适度冷硬、残余压应力能提高疲劳强度
粗糙度越大、工作精度降低
残余应力越大,工作精度降低
粗糙度越大,耐腐蚀性越差
压应力提高耐腐蚀性,拉应力反之则降低耐腐蚀性
本章提要
机械产品质量取决于零件的加工质量和产品的装配质量,机器零件的加工质量是整台机器质量的基础。 机器零件的加工质量一般用机械加工精度和加工表面质量两个重要指标表示,它的高低将直接影响整台机器的使用性能和寿命。 机械产品加工的首要任务,就是保证零件的机械加工质量要求。 本章重点讨论影响机械加工精度和表面质量的因素及其控制方法。
(1)主轴回转误差
第二节 机械加工精度的影响因素及控制
一、工艺系统几何误差对加工精度的影响
(一)机床的几何误差
(1)主轴回转误差
第二节 机械加工精度的影响因素及控制
一、工艺系统几何误差对加工精度的影响
(一)机床的几何误差
主轴回转误差的基本形式
车床上车削
镗床上镗削
内、外圆
端面
螺纹
孔
端面
纯径向跳动
机械加工中,采用近似的成形运动或近似的刀刃形状进行加工,虽然会由此产生一定的原理误差,但却可以简化机床结构和减少刀具数,只要加工误差能够控制在允许的制造公差范围内,就可采用近似加工方法。
原始误差
工艺系统动误差
工艺系统受力变形
刀具磨损
残余应力引起变形
测量误差
工艺系统热变形
第二节 机械加工精度的影响因素及控制
《机械加工技术》课件

促进产业发展
机械加工技术的发展对于推动相 关产业的发展具有重要意义,如 汽车、航空航天、电子等产业。
机械加工技术的发展历程
传统机械加工
传统机械加工主要依靠手工操作和简单的机械装置,加工精度和效率较低。
数控加工
随着计算机技术的不断发展,数控加工技术逐渐兴起,实现了加工过程的自动化和智能 化。
智能制造
切削刀具磨损形式
包括磨料磨损、粘结磨损、扩散磨损和氧化磨损等,这些磨损形 式相互作用,共同影响着刀具的寿命。
2023
PART 03
机械加工工艺流程
REPORTING
毛坯制造技术
铸造技术
通过将熔融的金属倒入模具中,冷却凝固后形 成毛坯。
锻造技术
通过施加外力使金属坯料变形,以获得所需形 状和性能的毛坯。
切削速度、进给量和切削 深度,是衡量切削运动大 小的三个重要参数。
切削用量选择原则
根据工件材料、加工精度 和刀具材料等条件,合理 选择切削用量,以提高加 工效率和降低成本。
刀具材料与几何参数
刀具材料的种类
01
常用的刀具材料有高速钢、硬质合金、陶瓷和立方氮化硼等。
刀具几何参数
02
包括前角、后角、主偏角、副偏角和刃倾角等,对切削力、切
特点
机械加工技术具有高效、高精度、高 自动化的特点,能够满足各种复杂、 精密的零件加工需求,是现代制造业 中不可或缺的重要环节。
机械加工的重要性
保障产品质量
机械加工能够保证零件的尺寸、 形状和性能要求,提高产品的质 量和可靠性。
提高生产效率
通过高效的机械加工,可以快速 、准确地完成大量零件的加工, 提高生产效率,降低生产成本。
PART 05
机加工基础知识培训ppt课件

铣床
01
02
03
定义
铣床是一种主要用于加工 平面、沟槽、成形表面的 机床,通过刀具的旋转和 进给实现切削加工。
工作原理
工件固定在工作台上,通 过工作台的移动和刀具的 旋转和进给实现切削加工 。
应用范围
适用于加工平面、沟槽、 成形表面等,如板类、模 具类零件等。
钻床
定义
钻床是一种主要用于加工 孔的机床,通过钻头的高 速旋转实现钻孔加工。
智能化与自动化趋势明显
随着信息技术和人工智能技术的快速发展,机加工技术的智能化和自动
化趋势日益明显。智能化的机加工设备能够实现自动调整、自动补偿等
功能,提高生产效率和加工精度。
03
定制化与个性化需求增长
随着消费者需求的多样化,机加工技术的定制化和个性化需求也在增长
。机加工设备需要具备更高的灵活性和可变性,能够适应不同的材料和
工件尺寸。
对机加工技术未来发展的展望与建议
提升设备性能与可靠性
未来,机加工技术的发展将更加注重设备的性能 和可靠性。通过研发更先进的机加工设备,提高 加工精度、降低误差率,提升产品质量和生产效 率。
适应绿色环保要求
随着环保意识的提高,机加工技术的发展需要更 加注重环保和节能。研发低能耗、低污染的机加 工设备,推广清洁生产技术,实现绿色制造。
其他机加工设备
数控机床
数控机床是一种采用数字控制技 术的机床,具有高精度、高效率 的特点,适用于加工各种复杂零
件。
激光切割机
激光切割机是一种采用激光束切割 材料的机床,具有切割速度快、精 度高的特点,适用于切割各种金属 材料。
水切割机
水切割机是一种采用高压水流切割 材料的机床,具有切割效果好、无 热影响区的特点,适用于切割各种 非金属材料。
机械加工质量控制与检测PPT课件
❖工艺系统:机床、夹具、刀具、工件
❖ 质量控制的重点:工艺过程的正确性、 操作者的技能和经验
大连职业技术学院
4
绪论
例如:加工有色金属右旋梯形 螺纹螺母时,表面粗糙度达不 到要求?
关键
学习如何在加工过程中 实施质量“控制”
大连职业技术学院
5
绪论
(二)检测 ❖目的:量具、仪器或专用检具对加工好
的零件进行检测、比较,得到误 差值或判断其是否符合质量要求 的过程
❖ 检测方法:
检测原理
复杂的计算
查表
经验公式
❖掌握各种精度指标项目的定义—获得检测原 理—确定检测方法—选取相应的量具及辅助 工具—获取正确的误差值—数据分析处理— 得出检测结论—对工艺过程进行指导
大连职业技术学院
6
目录
1
加工质量控制基础
2
检测技术基础
3
几何量误差检测
4
各类毛坯的检测
5 典型零件加工质量控制与检测
直线度 形
状 平面度
无
平行度
有
定
位
垂直度
有
无
向 倾斜度
有
公 圆度 差 圆柱度
形状 或位 置公
差
线轮廓 度
面轮廓 度
无 无 有或无 有或无
置
位置度
定 同轴度
公 位 对称度
圆跳动
差跳 动 全跳动
有或无 有 有 有 有
13
1.1 零件的使用性能与加工质量
1.1.2零件加工质量
(二)表面质量的概念 1、表面层的几何形状
表面粗糙度:表面微观几何形状误差,其波长与波高的比值在 L1/H1<40的范围内,波距<1mm。由刀刃切削后形成。 表面波度:介于加工精度(宏观几何形状误差L3/H3 = 1000)和表 面粗糙度间的一种带有周期性的几何形状误差,其波长与波高的比值 在40<L2/H2<1000的范围,波距=1~10mm。由工艺系统的振动引起。 纹理方向: 表面刀纹的方向,它取决于表面形成过程中所采用的 机械加工方法。 伤痕:加工表面上一些个别位置上出现的缺陷。例如:砂眼、气孔、 裂痕等。
❖ 质量控制的重点:工艺过程的正确性、 操作者的技能和经验
大连职业技术学院
4
绪论
例如:加工有色金属右旋梯形 螺纹螺母时,表面粗糙度达不 到要求?
关键
学习如何在加工过程中 实施质量“控制”
大连职业技术学院
5
绪论
(二)检测 ❖目的:量具、仪器或专用检具对加工好
的零件进行检测、比较,得到误 差值或判断其是否符合质量要求 的过程
❖ 检测方法:
检测原理
复杂的计算
查表
经验公式
❖掌握各种精度指标项目的定义—获得检测原 理—确定检测方法—选取相应的量具及辅助 工具—获取正确的误差值—数据分析处理— 得出检测结论—对工艺过程进行指导
大连职业技术学院
6
目录
1
加工质量控制基础
2
检测技术基础
3
几何量误差检测
4
各类毛坯的检测
5 典型零件加工质量控制与检测
直线度 形
状 平面度
无
平行度
有
定
位
垂直度
有
无
向 倾斜度
有
公 圆度 差 圆柱度
形状 或位 置公
差
线轮廓 度
面轮廓 度
无 无 有或无 有或无
置
位置度
定 同轴度
公 位 对称度
圆跳动
差跳 动 全跳动
有或无 有 有 有 有
13
1.1 零件的使用性能与加工质量
1.1.2零件加工质量
(二)表面质量的概念 1、表面层的几何形状
表面粗糙度:表面微观几何形状误差,其波长与波高的比值在 L1/H1<40的范围内,波距<1mm。由刀刃切削后形成。 表面波度:介于加工精度(宏观几何形状误差L3/H3 = 1000)和表 面粗糙度间的一种带有周期性的几何形状误差,其波长与波高的比值 在40<L2/H2<1000的范围,波距=1~10mm。由工艺系统的振动引起。 纹理方向: 表面刀纹的方向,它取决于表面形成过程中所采用的 机械加工方法。 伤痕:加工表面上一些个别位置上出现的缺陷。例如:砂眼、气孔、 裂痕等。
机加工基础知识培训ppt课件
机加工基础知识培训
汇报人:可编辑
2023-12-24
2023
机加工概述机加工设备机加工刀具机加工工艺机加工质量控制机加工安全与环保
目 录
CATALOGUE
2023
PART
01
2023
机加工是一种利用机械设备对原材料进行加工,使其成为所需形状和尺寸的工艺过程。
机加工是制造业中不可或缺的一环,它能够将原材料转化为具有特定性能和用途的零件或产品,广泛应用于汽车、航空、能源、医疗等领域。
总结词:了解质量管理体系的构成和作用,如何建立和实施质量管理体系,以及质量管理体系认证的意义和流程。
PART
06
机加工安全与环保
2023
在操作机加工设备前,应检查设备是否正常,确保安全装置完好无损。
操作前检查
严格按照设备操作规程进行操作,不得擅自更改或省略操作步骤。
遵守操作规程
操作时应穿戴符合规定的防护用品,如防护眼镜、口罩、手套等。
表面质量影响因素
表面质量包括表面粗糙度、表面完整性和表面力学性能等,受到切削用量、刀具材料和工件材料等因素的影响。
PART
05
机加工质量控制
2023
了解误差产生的原因,如机床精度、刀具磨损、操作不当等,以及采取相应的控制措施,如定期维护、选择合适的刀具、规范操作等。
详细描述
在进行机加工过程中,由于各种因素的影响,加工结果可能会与预期存在一定的偏差,即加工误差。误差产生的原因有很多,如机床的精度问题、刀具的磨损、操作员的操作不当等。为了减小误差,需要采取一系列的控制措施。首先,应定期对机床进行维护和保养,确保其处于良好的工作状态;其次,根据加工需求选择合适的刀具,避免因刀具问题导致的误差;最后,规范操作员的操作,避免因人为因素导致的误差。
汇报人:可编辑
2023-12-24
2023
机加工概述机加工设备机加工刀具机加工工艺机加工质量控制机加工安全与环保
目 录
CATALOGUE
2023
PART
01
2023
机加工是一种利用机械设备对原材料进行加工,使其成为所需形状和尺寸的工艺过程。
机加工是制造业中不可或缺的一环,它能够将原材料转化为具有特定性能和用途的零件或产品,广泛应用于汽车、航空、能源、医疗等领域。
总结词:了解质量管理体系的构成和作用,如何建立和实施质量管理体系,以及质量管理体系认证的意义和流程。
PART
06
机加工安全与环保
2023
在操作机加工设备前,应检查设备是否正常,确保安全装置完好无损。
操作前检查
严格按照设备操作规程进行操作,不得擅自更改或省略操作步骤。
遵守操作规程
操作时应穿戴符合规定的防护用品,如防护眼镜、口罩、手套等。
表面质量影响因素
表面质量包括表面粗糙度、表面完整性和表面力学性能等,受到切削用量、刀具材料和工件材料等因素的影响。
PART
05
机加工质量控制
2023
了解误差产生的原因,如机床精度、刀具磨损、操作不当等,以及采取相应的控制措施,如定期维护、选择合适的刀具、规范操作等。
详细描述
在进行机加工过程中,由于各种因素的影响,加工结果可能会与预期存在一定的偏差,即加工误差。误差产生的原因有很多,如机床的精度问题、刀具的磨损、操作员的操作不当等。为了减小误差,需要采取一系列的控制措施。首先,应定期对机床进行维护和保养,确保其处于良好的工作状态;其次,根据加工需求选择合适的刀具,避免因刀具问题导致的误差;最后,规范操作员的操作,避免因人为因素导致的误差。
《精密超精密加工》课件
04
精密超精密加工材料
金属材料
01
02
03
钢铁
常用的金属材料,具有高 强度、耐磨性和耐腐蚀性 ,适用于各种精密超精密 加工应用。
铜合金
具有良好的导热性和导电 性,广泛用于电子和通信 行业。
钛合金
具有高强度、轻质和耐腐 蚀性,常用于航空和医疗 领域。
非金属材料
陶瓷
具有高硬度、耐高温和化学稳定性,适用于高精度和 高硬度的加工需求。
详细描述
防止加工过程中的损伤需要从多个方面入手,包括优化刀具设计、选择合适的切削参数 、加强刀具管理和维护等。此外,采用新型的涂层技术和刀具材料也是防止损伤的有效
手段。
06
பைடு நூலகம்
精密超精密加工的应用案例
航空航天领域的应用案例
总结词
精密超精密加工技术在航空航天领域的应用广泛,涉 及发动机叶片、涡轮盘、航空仪表等关键部件的制造 。
这些技术包括离子束加工、电子束加工、激光束加工等。这些技术通常具有更高的加工精度和更广泛 的适用范围,可以应用于各种不同的材料和领域。
03
精密超精密加工设备与工具
超精密切削加工设备
01
超精密切削加工设备主要用于高 精度零件的切削加工,其特点是 切削精度高、加工表面质量好、 加工效率高。
02
常见的超精密切削加工设备包括 数控机床、激光切割机、水切割 机等。
汽车工业领域的应用案例
总结词
精密超精密加工技术在汽车工业领域的应用主要涉及 汽车发动机、变速器、制动系统等关键零部件的制造 。
详细描述
在汽车工业领域,精密超精密加工技术主要用于制造汽 车发动机、变速器、制动系统等关键零部件。这些零部 件的性能对汽车的性能和安全性有重要影响。精密超精 密加工技术能够提高零部件的精度和耐磨性,降低摩擦 和阻力,提高燃油经济性和排放性能。同时,还能缩短 产品研发周期,提高生产效率,降低制造成本。
机械制造工艺学课件第7章 精密、超精密及微细加工工艺
5
第7章 精密、超精密及微细加工工艺
➢ 精密、超精密磨削和磨料加工
超精密磨削和磨料加工是利用细粒度的磨粒和微 粉主要对黑色金属、硬脆材料等进行加工,可分为固 结磨料和游离磨料两大类加工方式。
固结磨料加工主要有:超精密砂轮磨削和超硬材 料微粉砂轮磨削、超精密砂带磨削、ELID 磨削、双 端面精密磨削以及电泳磨削等。
第7章 精密、超精密及微细加工工艺
第7章 精密、超精密及微细加工工艺
7.1 概述
现代制造业持续不断地致力于提高加工精度和加
工表面质量,主要目标是提高产品性能、质量和可靠性
,改善零件的互换性,提高装配效率。超精密加工技术
是精加工的重要手段,在提高机电产品的性能、质量和
发展高新技术方面都有着至关重要的作用,因此,该技
第7章 精密、超精密及微细加工工艺
游离磨料类加工是指在加工时磨粒或微粉成游离状态,如研磨时的研磨 剂、抛光时的抛光液,其中的磨粒或微粉在加工时不是固结在一起的。 游离磨料加工的典型方法是超精密研磨与抛光加工。
① 超精密研磨技术
研磨是在被加工表面和研具之间置以游离磨料和润滑液,使被加工表面
和研具产生相对运动并加压,磨料产生切削、挤压作用,从而去除表面
7
第7章 精密、超精密及微细加工工艺
② 超精密砂带磨削技术 随着砂带制作质量的迅速提高,砂带上砂粒的等高性和 微刃性较好,并采用带有一定弹性的接触轮材料,使砂 带磨削具有磨削、研磨和抛光的多重作用,从而可以达 到高精度和低表面粗糙度值。
砂带磨削机构示意图
8
第7章 精密、超精密及微细加工工艺
③ ELID(电解在线修整)超精密镜面磨削技术
术是衡量一个国家先进制造技术水平的重要指标之一,
第7章 精密、超精密及微细加工工艺
➢ 精密、超精密磨削和磨料加工
超精密磨削和磨料加工是利用细粒度的磨粒和微 粉主要对黑色金属、硬脆材料等进行加工,可分为固 结磨料和游离磨料两大类加工方式。
固结磨料加工主要有:超精密砂轮磨削和超硬材 料微粉砂轮磨削、超精密砂带磨削、ELID 磨削、双 端面精密磨削以及电泳磨削等。
第7章 精密、超精密及微细加工工艺
第7章 精密、超精密及微细加工工艺
7.1 概述
现代制造业持续不断地致力于提高加工精度和加
工表面质量,主要目标是提高产品性能、质量和可靠性
,改善零件的互换性,提高装配效率。超精密加工技术
是精加工的重要手段,在提高机电产品的性能、质量和
发展高新技术方面都有着至关重要的作用,因此,该技
第7章 精密、超精密及微细加工工艺
游离磨料类加工是指在加工时磨粒或微粉成游离状态,如研磨时的研磨 剂、抛光时的抛光液,其中的磨粒或微粉在加工时不是固结在一起的。 游离磨料加工的典型方法是超精密研磨与抛光加工。
① 超精密研磨技术
研磨是在被加工表面和研具之间置以游离磨料和润滑液,使被加工表面
和研具产生相对运动并加压,磨料产生切削、挤压作用,从而去除表面
7
第7章 精密、超精密及微细加工工艺
② 超精密砂带磨削技术 随着砂带制作质量的迅速提高,砂带上砂粒的等高性和 微刃性较好,并采用带有一定弹性的接触轮材料,使砂 带磨削具有磨削、研磨和抛光的多重作用,从而可以达 到高精度和低表面粗糙度值。
砂带磨削机构示意图
8
第7章 精密、超精密及微细加工工艺
③ ELID(电解在线修整)超精密镜面磨削技术
术是衡量一个国家先进制造技术水平的重要指标之一,
- 1、下载文档前请自行甄别文档内容的完整性,平台不提供额外的编辑、内容补充、找答案等附加服务。
- 2、"仅部分预览"的文档,不可在线预览部分如存在完整性等问题,可反馈申请退款(可完整预览的文档不适用该条件!)。
- 3、如文档侵犯您的权益,请联系客服反馈,我们会尽快为您处理(人工客服工作时间:9:00-18:30)。
• *原始误差的
分类归纳如下:
图7.1为活塞销孔精镗工序中的各种原始误差:
图7.2以车削为例说明原始误差与加工误差的关系。 (图中实线为刀尖正确位置,虑线为误差位置。)
• 图7.2(a)刀尖位移△Z与加工半径误差 △ R的关系:R2 + △ Z2=(R+ △ R)2
化简推导得: △ R≈ △Z2/(2R) • 图7.2(b)刀尖位移△Y与加工半径误差 △ R’的关系:△ R’ =△Y
二 近似折线代替渐开线。 )
7.2.2机床误差
机床误差是指在无切削负荷下,来自
机床本身的制造误差、安装误差和磨损。 其常见形式:
主轴回转误差、导轨误差和传动链误差
7.2.2.1主轴回转误差
⑴主轴回转误差的概念
• (图7.3 机床主轴回转误差的类型)
• 纯径向跳动:实际回转轴线始终平行于理想回转轴线,在一个平 面内作等幅的跳动。
* 7.2.3.2
工艺系统 受力对加 工精度的 影响
⑴切削过程 中力作用位 置的变化对 加工精度的 影响 (见 图7.18)
• 图7.19 表示内圆 磨床、卧 式镗床上 加工时工 艺系统受 力变形随 受力点位 置变化而 变化的情 况。
⑵切削过程中受力大小变化对加工精度的影响
• 图7.20为车削有椭圆形圆度误差的短圆柱毛 坯外圆,刀尖调整到要求尺寸(图中虚线位 置),在工件的每一转中切深由毛坯长半径 的最大值 变化到短半径的最小值 时, 切削力也就是由最大 的变化到最小 的, 由Y=FY/K可知切削力变化引起对应的让刀 变形Y1 、Y2 。
7.2.2.2导轨误差
⑴导轨在垂直面内的直线度误差
•
卧式车床或外圆
磨床的导轨垂直面内
有直线度误差,是误
差非敏感方向,可忽ຫໍສະໝຸດ 略不计(图7.9(a)) 。
•
平面磨床、龙门
刨床这时是误差敏感
方向,所以导轨误差
将直接反映到被加工
的零件上。
⑵导轨在水平面内的真线度误差
△Y(见图7.9(b)) • 对于卧式车床是误
⑶工艺系统的刚度
• 由工艺系统受力总变形是各个组成部分 变形的叠加,
即 Y系统=Y机床+Y夹具+Y刀具+Y工件 • 而工艺系统各部件的刚度又为:
K系统=FY/Y系统
K机床=FY/Y机床
K夹具=FY/Y夹具
K刀具=FY/Y刀具
K工件=FY/Y工件
•
推导得P202公式7.11:
K系统=(1/K机床+1/K夹具+1/K刀具+1/K工件)-1
• 加工精度:零件加工后的实际几何参数 (尺寸、形状和位置)与理想几何参数相符的 程度。
• 零件加工后的实际几何参数对理想几何 参数的偏离程度称为加工误差。
7.1.2研究加工精度的方法
研究加工精度的方法的一般有两种:
• 一是因素分析法(通过分析计算或实验、测试
等方法,研究某一确定因素对加工精度的影响。 一般不考虑其它因素的同时作用,主要是分析各 项误差单独变化规律)。
• 工艺系统刚度(K系统)是指切削力在加工表面 法向的分力FY与FX、FY、FZ同时作用下产 生的沿法向的变形Y系统之间的比值:
K系统=FY/Y系统
• (刚度的倒数称为柔度,柔度C=1/K系统= Y系统/ FY)
由于力与变形一般都是在静态条件下进行考 虑和测量的,故上述刚度、柔度分别 为静刚度和 静柔度
为分析工艺系统各组成部分的变形规律 及其特点,现介绍工艺系统各组成部分的 刚度
⑴零件的刚度
形状规则、简单的零件的刚度可用有关 力学公式推算,如公式7.9;公式7.10等。
⑵机床部件的刚度
• 机床部件(如 图7.13) 的受力变 形主要影响是间 隙、油膜层和薄 弱零件变形。其 刚度远比单个零 件小,一般用实 验方法测定。
差敏感方向,影响 较大,零件的加工 误差△R= △ Y 。 • 对于平面磨床、龙 门刨床这时是误差 非敏感方向,影响 可忽略。
⑶前后导轨的平行度误差 • 半径加工误差△R≈ △Y= △Z(H/B)较大
⑷导轨与主轴回转轴线的平行度误差
• 若车床导轨与主轴回转轴线在水平面内有平 行误差,车出的内外圆柱面就产生锥度;若 在垂直面内有平行误差,则圆柱面成双曲线 回转体(图7.11),因误差非敏感方向故可略
• 纯轴向跳动:实际回转轴线始终沿理想回转轴线作等幅的窜动。 • 纯角度摆动:实际回转轴线与理想回转轴线始终成一倾角,在一
个平面上作幅摆动,且交点位置不变。 • 由于主轴回转误差总是上述三者的合成。造成主轴回转误差的主
要因素与主轴部件的制造精度有关。
⑵主轴回转误差对加工精度的影响
• 不同型式的主轴回转误差对加工精度的影 响是不同的;而同一类型的回转误差在不同的 加工方式中的影响也不相同。如图7.5~图7.8和 表7.1所示
7.2.2.3传动链误差
• 传动链误差是指机床内联系传动链始末 两端传动元件之间相对运动的误差。
7.2.3工艺系统受力变形 7.2.3.1工艺系统刚度
• 工艺系统在切削 力、夹紧力、传 动力、重力和惯 性力等外力作用 下,使零件产生 加工误差。例如 图7.12(a)车细长 轴,图7.12(b)车 削粗短工件时, 图7.12〔c〕所 示在车床加工薄 壁零件的内孔。
第七章: 机械加工精度
本章提要
机器零件的加工质量是整台机器 质量的基础,零件的加工质量一般用 机械加工精度和加工表面质量两个重 要指标表示,本章仅研究机械加工精 度的问题,其讨论的内容有机械加工 精度的基本概念、影响加工精度的因 素、加工误差的综合分析及提高加工 精度的途径四个方面。
7.1机械加工精度的基本概念 7.1.1加工精度与加工误差
前者数值极小以致可忽略 后者造成的加工误差较大 前者是在加工表面切线方向 后者是在加工表面法线方向
后者加工表面的法线方向称加工误差敏感方向*
结论:加工误差敏感方向上刀尖位移会造成大 的加工误差
7.2.1加工原理误差
加工原理是指加工表面的形状原理。
*加工原理误差是由于采用了近似的切削运动
或近似的切削刃形状所产生的加工误差(如:齿轮滚刀: 一 阿基米德或法向直廓基本蜗杆代替渐开线基本蜗杆;
• 二是统计分析法(运用数理统计方法对生产中
一批工件的实测结果进行数据处理,用以控制工 艺过程的正常进行。主要是研究各项误差综合的 变化规律,只适用于大批、大量的生产条件)
7.2影响加工精度的因素
• 零件的机械加 工是在由机床、 夹具、刀具和 工件组成的工 艺系统中进行 的。工艺系统 中凡是直接引 起加工误差的 因素都称为原 始误差。
分类归纳如下:
图7.1为活塞销孔精镗工序中的各种原始误差:
图7.2以车削为例说明原始误差与加工误差的关系。 (图中实线为刀尖正确位置,虑线为误差位置。)
• 图7.2(a)刀尖位移△Z与加工半径误差 △ R的关系:R2 + △ Z2=(R+ △ R)2
化简推导得: △ R≈ △Z2/(2R) • 图7.2(b)刀尖位移△Y与加工半径误差 △ R’的关系:△ R’ =△Y
二 近似折线代替渐开线。 )
7.2.2机床误差
机床误差是指在无切削负荷下,来自
机床本身的制造误差、安装误差和磨损。 其常见形式:
主轴回转误差、导轨误差和传动链误差
7.2.2.1主轴回转误差
⑴主轴回转误差的概念
• (图7.3 机床主轴回转误差的类型)
• 纯径向跳动:实际回转轴线始终平行于理想回转轴线,在一个平 面内作等幅的跳动。
* 7.2.3.2
工艺系统 受力对加 工精度的 影响
⑴切削过程 中力作用位 置的变化对 加工精度的 影响 (见 图7.18)
• 图7.19 表示内圆 磨床、卧 式镗床上 加工时工 艺系统受 力变形随 受力点位 置变化而 变化的情 况。
⑵切削过程中受力大小变化对加工精度的影响
• 图7.20为车削有椭圆形圆度误差的短圆柱毛 坯外圆,刀尖调整到要求尺寸(图中虚线位 置),在工件的每一转中切深由毛坯长半径 的最大值 变化到短半径的最小值 时, 切削力也就是由最大 的变化到最小 的, 由Y=FY/K可知切削力变化引起对应的让刀 变形Y1 、Y2 。
7.2.2.2导轨误差
⑴导轨在垂直面内的直线度误差
•
卧式车床或外圆
磨床的导轨垂直面内
有直线度误差,是误
差非敏感方向,可忽ຫໍສະໝຸດ 略不计(图7.9(a)) 。
•
平面磨床、龙门
刨床这时是误差敏感
方向,所以导轨误差
将直接反映到被加工
的零件上。
⑵导轨在水平面内的真线度误差
△Y(见图7.9(b)) • 对于卧式车床是误
⑶工艺系统的刚度
• 由工艺系统受力总变形是各个组成部分 变形的叠加,
即 Y系统=Y机床+Y夹具+Y刀具+Y工件 • 而工艺系统各部件的刚度又为:
K系统=FY/Y系统
K机床=FY/Y机床
K夹具=FY/Y夹具
K刀具=FY/Y刀具
K工件=FY/Y工件
•
推导得P202公式7.11:
K系统=(1/K机床+1/K夹具+1/K刀具+1/K工件)-1
• 加工精度:零件加工后的实际几何参数 (尺寸、形状和位置)与理想几何参数相符的 程度。
• 零件加工后的实际几何参数对理想几何 参数的偏离程度称为加工误差。
7.1.2研究加工精度的方法
研究加工精度的方法的一般有两种:
• 一是因素分析法(通过分析计算或实验、测试
等方法,研究某一确定因素对加工精度的影响。 一般不考虑其它因素的同时作用,主要是分析各 项误差单独变化规律)。
• 工艺系统刚度(K系统)是指切削力在加工表面 法向的分力FY与FX、FY、FZ同时作用下产 生的沿法向的变形Y系统之间的比值:
K系统=FY/Y系统
• (刚度的倒数称为柔度,柔度C=1/K系统= Y系统/ FY)
由于力与变形一般都是在静态条件下进行考 虑和测量的,故上述刚度、柔度分别 为静刚度和 静柔度
为分析工艺系统各组成部分的变形规律 及其特点,现介绍工艺系统各组成部分的 刚度
⑴零件的刚度
形状规则、简单的零件的刚度可用有关 力学公式推算,如公式7.9;公式7.10等。
⑵机床部件的刚度
• 机床部件(如 图7.13) 的受力变 形主要影响是间 隙、油膜层和薄 弱零件变形。其 刚度远比单个零 件小,一般用实 验方法测定。
差敏感方向,影响 较大,零件的加工 误差△R= △ Y 。 • 对于平面磨床、龙 门刨床这时是误差 非敏感方向,影响 可忽略。
⑶前后导轨的平行度误差 • 半径加工误差△R≈ △Y= △Z(H/B)较大
⑷导轨与主轴回转轴线的平行度误差
• 若车床导轨与主轴回转轴线在水平面内有平 行误差,车出的内外圆柱面就产生锥度;若 在垂直面内有平行误差,则圆柱面成双曲线 回转体(图7.11),因误差非敏感方向故可略
• 纯轴向跳动:实际回转轴线始终沿理想回转轴线作等幅的窜动。 • 纯角度摆动:实际回转轴线与理想回转轴线始终成一倾角,在一
个平面上作幅摆动,且交点位置不变。 • 由于主轴回转误差总是上述三者的合成。造成主轴回转误差的主
要因素与主轴部件的制造精度有关。
⑵主轴回转误差对加工精度的影响
• 不同型式的主轴回转误差对加工精度的影 响是不同的;而同一类型的回转误差在不同的 加工方式中的影响也不相同。如图7.5~图7.8和 表7.1所示
7.2.2.3传动链误差
• 传动链误差是指机床内联系传动链始末 两端传动元件之间相对运动的误差。
7.2.3工艺系统受力变形 7.2.3.1工艺系统刚度
• 工艺系统在切削 力、夹紧力、传 动力、重力和惯 性力等外力作用 下,使零件产生 加工误差。例如 图7.12(a)车细长 轴,图7.12(b)车 削粗短工件时, 图7.12〔c〕所 示在车床加工薄 壁零件的内孔。
第七章: 机械加工精度
本章提要
机器零件的加工质量是整台机器 质量的基础,零件的加工质量一般用 机械加工精度和加工表面质量两个重 要指标表示,本章仅研究机械加工精 度的问题,其讨论的内容有机械加工 精度的基本概念、影响加工精度的因 素、加工误差的综合分析及提高加工 精度的途径四个方面。
7.1机械加工精度的基本概念 7.1.1加工精度与加工误差
前者数值极小以致可忽略 后者造成的加工误差较大 前者是在加工表面切线方向 后者是在加工表面法线方向
后者加工表面的法线方向称加工误差敏感方向*
结论:加工误差敏感方向上刀尖位移会造成大 的加工误差
7.2.1加工原理误差
加工原理是指加工表面的形状原理。
*加工原理误差是由于采用了近似的切削运动
或近似的切削刃形状所产生的加工误差(如:齿轮滚刀: 一 阿基米德或法向直廓基本蜗杆代替渐开线基本蜗杆;
• 二是统计分析法(运用数理统计方法对生产中
一批工件的实测结果进行数据处理,用以控制工 艺过程的正常进行。主要是研究各项误差综合的 变化规律,只适用于大批、大量的生产条件)
7.2影响加工精度的因素
• 零件的机械加 工是在由机床、 夹具、刀具和 工件组成的工 艺系统中进行 的。工艺系统 中凡是直接引 起加工误差的 因素都称为原 始误差。