注塑模具实例
ug注塑模具设计实例

ug注塑模具设计实例以下是一个简单的注塑模具设计实例,模具设计的基本概念和步骤。
设计案例:一个简单的塑料瓶盖模具1. 确定产品尺寸和形状产品是一个简单的塑料瓶盖,直径为20mm,高度为3mm。
瓶盖表面有纹理,以增加摩擦力,方便开启。
2. 确定模具结构模具采用典型的双板模结构,由动模板和定模板组成。
动模板上设有型腔,定模板上设有浇口和流道。
3. 确定型腔布局由于瓶盖尺寸较小,可以采用一模一腔的布局。
型腔布置在动模板上,浇口和流道布置在定模板上。
4. 设计浇口和流道浇口和流道的设计需要考虑塑料的填充和流动。
本例中,采用点浇口,浇口直径为1mm,流道直径为4mm。
5. 设计推出机构推出机构用于将成型后的产品从模具中推出。
本例中,采用推杆推出,推杆直径为8mm,数量为4个。
推杆安装在动模板上,推出时推动瓶盖脱离型腔。
6. 设计冷却系统冷却系统用于将成型过程中的热量从模具中带走,防止产品变形和开裂。
本例中,采用水管冷却,水管直径为4mm,布置在动模板和定模板上。
7. 设计排气系统排气系统用于将成型过程中的气体从模具中排出,防止气体的积聚和压力的升高。
本例中,采用排气槽,排气槽直径为2mm,数量为4个。
排气槽布置在定模板上。
8. 设计模具零件加工工艺性模具零件的加工需要考虑其工艺性。
本例中,采用数控加工中心进行加工,材料选择不锈钢。
9. 设计模具装配工艺性模具装配需要考虑其工艺性。
本例中,采用螺钉连接动模板和定模板,并使用定位销进行定位。
以上是一个简单的注塑模具设计实例,希望能帮助您更好地理解模具设计的基本概念和步骤。
第二章注射模具设计实例样稿.doc

第二章 注塑模具设计实例实例一:单分型面注塑模具设计一、塑件工艺性分析该塑件是一塑料瓶盖,如图2一1所示,塑件壁厚属薄壁塑件,生产批量很大,材料为聚乙烯(PE ,在高密度聚乙烯中掺入了部分低密度聚乙烯,改善塑件的柔韧性),成型工艺性很好,可以注射成型。
二、塑成型设备的选择与成型工艺规程的编制 1. 注射机的选用 1)注射量的计算通过计算或Pro/E 建模分析,塑件质量m 为2.8g ,塑件体积V 1=3.077cm 3流道凝料的质量m 2还是个未知数,可按塑件质量的0.6倍来估算。
从上述分析中确定为一模八腔,所以注射量为:m =1.6nm = 1.6 ×8 ×2.8=35. 84g2)塑件和流道凝料在分型面上的投影面积及所需锁模力的计算流道凝料(包括浇口)在分型面上的投影面积A 2,在模具设计前是个未知值,根据多型腔模的统计分析,A 2是每个塑件在分型面上的投影面积A 1的0.2倍~0.5倍,因此可用0. 35 nA 1来进行估算,所以A=nA 1+A 2=nA 1+0. 35nA 1=1.35nA 1=8412. 336mm2式中 A 1=24d= 0. 785 ×31. 52=778. 92mm 2F m =A p 型=8412. 336 ×30=252370N =252. 37kN 式中型腔压力p 型取30MPa (因是薄壁塑件,浇口又是潜伏式浇口,压力损失大,取大一些)。
3)选择注射机根据每一生产周期的注射量和锁模力的计算值,可选用SZ 一60/450卧式注射机,见表2一12. 注塑成型工艺参数选用图2—1三、塑模具结构方案设计1.型腔数量的确定及型腔的排列1)型腔数量的确定该塑件精度要求不高,又是大批大量生产,可以采用一模多腔的形式。
考虑到模具制造费用、设备运转费用低一些,初定为一模八腔的模具形式。
2)型腔排列形式的确定该塑件有两圈内螺纹,要使螺纹型芯从塑件上脱出,必须设计一套自动脱螺纹的齿轮传动结构,并且型腔的分布圆直径和齿轮分布圆直径相吻合,若采用一模八腔,型腔分布圆直径就相当大了,这样模具结构尺寸就比较大,加上齿轮传动系统,模具结构复杂,制造费用也很高。
注塑模具设计第5讲 实例4-2D-05 斜推杆(斜顶)机构的设计

4-1-32所示。
3
七、斜推杆机构的设计
注塑模具设计实例教程
❖ (2)斜推杆座与斜推杆相关尺寸的确定 ❖ 斜推杆座长宽一般由斜推杆的大小来确定,本例斜推杆座尺寸设计为20×40×53。 ❖ (3)斜推杆座在正剖视图中的绘制 ❖ 本例的斜推杆座在正剖视图中的绘制如图4-1-33所示,锁紧斜推杆座的螺钉选用
❖ 导向块的作用是加强斜推杆的强度和刚性,并对斜推杆进行支撑和导向。
❖ (1)导向块相关尺寸的确定
❖ 导向块的厚度一般为10~15mm,长宽一般由斜推杆的大小来确定。本例导
向块的的厚度取15mm,并选用规格为M5的螺钉锁紧。
4
七、斜推杆机构的设计
注塑模具设计实例教程
❖ (2)导向块在正剖视图中的绘制 ❖ 根据所确定的导向块相关尺寸,导向块在正剖视图中的绘制如图4-1-36所示。因
复习:热流道系统的设计
检查上次布置作业的完成情况
新课: 七、斜推杆机构的设计
❖ 斜推杆机构包括斜推杆、斜推杆座、导向块等。 1. 斜推杆的设计
❖ 设计斜推杆前,首先要处理剖视图中 一些不必要的图线,如图4-1-26所示, 正剖视图同样要处理。
❖ (1)斜推杆的设计形式
❖ 本例的斜推杆可设计成三种形式,如 图4-1-27所示。各种形式的优缺点在前 面的实例中已作介绍。本例的斜推杆 选择图4-1-27(b)和图4-1-27(c)两 种设计形式。
5
❖ (3)斜推杆宽度的确定
❖ 本例的扣位宽度有四个为31.8mm,有一个为19.57mm,单边可延伸做大 1mm左右,即将斜推杆宽度设计为四个34mm和一个22mm。
❖ (4)斜推杆抽芯行程的确定
❖ 本例的扣位深度为0.75mm,斜推杆的抽芯行程=扣位深度+2mm左右,故 斜推杆抽芯行程作到2.75mm左右即可。
双色注射模具设计10个实例(经典案例)

双⾊注射模具设计10个实例(经典案例)这是⼀款⼿机护套,如下图产品分析:此款为某品牌⼿机的外圈护套,由⼆种塑料(PC+TPE)组成。
由于要求外形美观光滑,分模线必须做在内侧圆弧切点,所以外模要四⾯滑开,再看内侧,四周全部是内扣的,必须全⽅位内抽芯,也就是俗称的“爆炸芯”。
关于“爆炸芯”的模具结构,假如是普通的注塑模具,已经有⾮常经典的机构,我下⾯将有详细的介绍。
现在问题是双⾊模具,有⼆组动模和⼆组定模,⼆组动模的所有部件是完全⼀致的,要在双⾊注塑机的转盘上进⾏180度旋转,⼆种不同的塑料分别射进模腔,注射硬胶(PC)时动模的顶出机构和抽芯机构不动作,再注射软胶(TPE)并开模后,对准软胶料筒的⼀侧的动模的抽芯机构和顶出机构才开始动作,将完整的双⾊制品顶出。
由于动模旋转后,交换⼜合模后的浇⼝必须在同⼀位置,所以软胶和硬胶的浇⼝的处理显得令⼈困惑。
由于模具必须四周都要进⾏“内外同抽”,内、外滑块怎样排列,轨道设置在哪⾥?这个问题同样有被逼⼊墙⾓的感觉。
且不谈模具滑块机构的复杂性,我们从双⾊模具的基本原理来考虑,硬胶部分的成型和内外同抽机构是⼀定要设置在定模⼀侧的,软胶部分的成型机构也要设置在定模。
⽽且这个部分是由内外同抽的机构组成的凸起插⼊到动模的凹槽中。
转盘旋转180度后,这组凸起刚好插⼊到另外⼀个动模的凹槽中。
也就是说,⼆个定模上的由内外同抽滑块组成的凸起的外部形状和尺⼨是完全相同的。
仅仅是成型软胶和硬胶的型⾯不同⽽已。
问题的难点是,这个凸起会分成上下⼆层,⼀层向外移动,另⼀层向内移动,也就是俗称的“内外同抽”,合成的凸起的侧⾯是⼀个统⼀的斜⾯,但是,传统的滑块必须要有滑动轨道等必要的条件,怎样设置轨道?这便成了本案例的核⼼问题。
我是这样设置动模部分的凹槽和定模部分凸起的。
动模的凹槽是这样的。
下⾯我们来探讨定模部分的设计1.01定模内外同抽的设计基本机构是这样的当A板和定模底板分开35mm后拨块拨动内滑块,同时通过齿轮的传动,外滑块向外移动。
注塑模设计案例

2024年10月10日
三、注射模旳构造设计
3.浇注系统旳设计
⑶浇口设计 浇口形式旳选择
因为该塑件外观质量要求较高,浇口旳位置和大小应以不 影响塑件旳外观质量为前提。同步,也应尽量使模具构造 更简朴。
潜伏式浇口 浇口位置在塑件内表面,不影响其外 观质量。 但采用这种浇口形式增长了模具构造 旳复杂程度。
2024年10月10日
二、拟定成型设备选择与模塑工艺规程编制
2.拟定成型工艺参数
⑴塑件模塑成型工艺参数旳拟定 查附表9得出工艺参数见下表,试模时可根据实际 情况作适当调整。
聚碳酸脂
预热和干燥 料筒温度t/0C
喷嘴温度t/0C
温度t/0C110~120 时间τ/h8~12 后段 210~240 中段 230~280 前段 240~285
⑵塑件型腔较大,有尺寸不等旳孔,如Ф12、4-Ф10、4Ф4.5、4-Ф5它们均符合最小孔径要求。
⑶在塑件内壁有4个高2.2,长11旳内凸台。所以,塑件不 易取出。需要考虑侧抽装置。
结论:综上所述,该塑件可采用注射成型加工。
2024年10月10日
二、拟定成型设备选择与模塑工艺规程编制
1.计算塑件旳体积和重量
查有关手册得PC旳收缩率为Q=0.5%~0.7%,故平 均收缩率为:Scp=(0.5+0.7)%/2=0.6%=0.006,根 据塑件尺寸公差要求,模具旳制造公差取Z=Δ/3。
已知条件:平均收缩率SCP =0.006mm;模具旳制 造公差取Z=Δ/3。
类 零件 别 图号
模具 零件 名称
塑件尺寸
计算公式
塑料模设计及制造实例
二、拟定模具构造方案
1.拟定型腔数量及布局形式 2.选择分型面 3.拟定浇注系统与排气系统 4.选择推出方式 5.拟定侧凹部分旳处理方式 6.模具加热与冷却方式 7.拟定成型零件旳构造形式
注塑模具设计实例

注塑模具设计实例注塑模具是注塑成型过程中的重要工具,它决定了产品的形状、尺寸和质量。
下面将介绍一个注塑模具设计实例。
该注塑模具用于生产一个塑料小零件,产品尺寸为25mm × 10mm × 5mm。
根据客户要求,模具设计师需要考虑以下几个方面:1.产品结构设计:根据产品尺寸和功能要求,模具设计师需要确定模具中的产品结构。
在这个实例中,小零件是一个封闭的长方体,底部有一个孔。
设计师结合注塑工艺和产品功能要求,选择了一种单腔模具结构。
这个结构能够满足产品形状和尺寸的要求,同时保证注塑成型的稳定性。
2.模具材料选择:模具的材料选择直接影响着模具的使用寿命和成本。
根据产品的使用环境和注塑工艺要求,设计师选择了优质的冷作模具钢作为模具材料。
这种钢材具有良好的切削性能和耐磨性,可以满足长时间连续生产的需求。
3.注塑工艺参数:注塑模具的设计需要考虑注塑工艺的各个参数,如注塑温度、保压时间、保压压力等。
在这个实例中,设计师根据塑料材料的熔体温度和流动性选择了适当的注塑温度和保压时间。
同时,根据产品的厚度和尺寸,设计师设定了合适的保压压力,以确保产品的成型质量。
4.模具结构设计:模具结构的设计需要考虑产品的成型要求和模具的制造工艺。
在这个实例中,设计师在模具上设置了合适的冷却水道和顶针机构,以确保注塑成型过程中的温度控制和产品的尺寸稳定。
同时,设计师在模具上设置了合适的排气装置,以避免产品出现气泡和缺陷。
5.模具制造和组装:根据设计图纸,模具制造师使用数控机床进行模具加工。
首先进行粗加工,然后进行精细加工和装配。
在模具加工和组装过程中,需要进行严格的尺寸和工艺控制,以确保模具的精度和质量。
综上所述,注塑模具设计需要综合考虑产品结构、模具材料、注塑工艺、模具结构以及模具制造和组装等方面的因素。
通过合理设计和制造,注塑模具可以满足产品的形状、尺寸和质量要求,提高注塑成型的效率和稳定性。
注塑模具设计实例
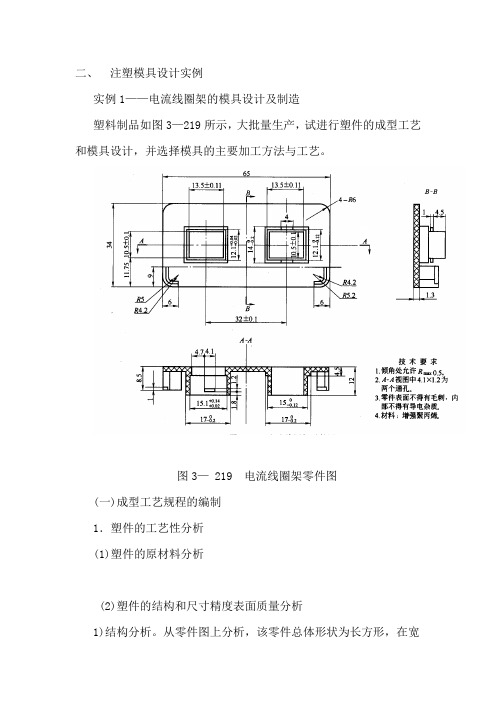
二、注塑模具设计实例实例1——电流线圈架的模具设计及制造塑料制品如图3—219所示,大批量生产,试进行塑件的成型工艺和模具设计,并选择模具的主要加工方法与工艺。
图3— 219 电流线圈架零件图(一)成型工艺规程的编制1.塑件的工艺性分析(1)塑件的原材料分析(2)塑件的结构和尺寸精度表面质量分析1)结构分析。
从零件图上分析,该零件总体形状为长方形,在宽度方向的一侧有两个高度为8.5mm ,R5mm 的两个凸耳,在两个高度为12mm 、长、宽分别为17mm 和13.5mm 的凸台上,一个带有的凹槽(对称分布),另一个带有4.lmmXl .2 mm 的凸台对称分布。
因此,模具设计时必须设置侧向分型抽芯机构,该零件属于中等复杂程度。
2)尺寸精度分析。
该零件重要尺寸如:012.01.12-mm 、04.002.01.12++mm 、14.002.01.15++mm 、012.01.15-mm 等精度为3级(Sj1372—78),次重要尺寸如:13.5±0.11、02.017-mm 、10.5±0.1mm 、02.014-mm 等的尺寸精度为4~5级(Sj 1372—78)。
由以上分析可见,该零件的尺寸精度中等偏上,对应的模具相关零件的尺寸加工可以保证。
从塑件的壁厚上来看,壁厚最大处为1.3mm ,最小处为0.95mm ,壁厚差为0.35mm ,较均匀,有利于零件的成型。
3)表面质量分析。
该零件的表面除要求没有缺陷、毛刺,内部不得有导电杂质外,没有特别的表面质量要求,故比较容易实现。
综上分析可以看出,注射时在工艺参数控制得较好的情况下,零件的成型要求可以得到保证。
(3)计算塑件的体积和质量计算塑件的质量是为了选用注射机及确定型腔数。
经计算塑件的体积为V =4087mm 3;计算塑件的质量:根据设计手册可查得增强聚丙烯的密度为ρ=1.04g /cm 3。
故塑件的质量为W =V ρ=4.25g采用一模两件的模具结构,考虑其外形尺寸、注射时所需压力和工厂现有设备等情况,初步选用注射机为XS—Z—60型。
注塑模具设计第11讲 实例3-2D-11 三板模标准件的设计

3030~4045 4045~5055 5055以上 限位螺钉 小拉杆直径mm 尼龙胶塞 (开闭器)直径mm
数量 4个
4个 4个 4个
13
16 20 25
13
16 20 20
1
十三、三板模标准件的设计
注塑模具设计实例教程
拉杆(水口边)的长度Y: Y=A+B+C+X+S+2; A—面板(定模座板)厚度; B—水口板(流道推板)厚度; C—A板(定模板)厚度; X—水口板和A板的打开距离; X=M+(15~20); X最少不能小于110mm; M—流道凝料总高度; S —面板和水口板的打开距离; S通常取10mm左右
实例三 玩具面壳注塑模具2D设计
复习:顶出系统、排气系统的设计
注塑模具设计实例教程
检查上次布置作业的完成情况
新课:
十三、三板模标准件的设计 本例标准件主要包括流道钩针、小拉杆、开闭器、顶棍孔、支撑柱、限位柱 、弹簧、限位钉等。 ※三板模配件设计参考:见下表及下图 限位螺钉,小拉杆,尼龙胶塞(开闭器)的选定:
十三、三板模标准件的设计
注塑模具设计实例教程
流道推板与定模座板的打开距离一般常取6~10mm,本例取10mm。 ②流道推板与定模板的打开距离 流道推板与定模板的打开距离L=流道总长+(20~30mm)≥120 mm。本例的流道 总长为94mm,故流道推板与定模板的打开距离取120mm。 (4)小拉杆避空孔在动模视图中的添加 ①【燕秀工具箱】→【三板模相关】,在【三板模相关】对话框中选择第二排 的第一个视图,该视图为小拉杆避空孔的动模视图,选择小拉杆的直径为 Φ 16mm,如图3-1-56所示。
- 1、下载文档前请自行甄别文档内容的完整性,平台不提供额外的编辑、内容补充、找答案等附加服务。
- 2、"仅部分预览"的文档,不可在线预览部分如存在完整性等问题,可反馈申请退款(可完整预览的文档不适用该条件!)。
- 3、如文档侵犯您的权益,请联系客服反馈,我们会尽快为您处理(人工客服工作时间:9:00-18:30)。
注塑模具实例
1. 引言
注塑模具是用于制造塑料制品的模具。
它是塑料注塑成型工艺中最核心的设备,广泛应用于汽车、电子产品、家电等多个行业。
本文将介绍一个注塑模具的实例,以帮助读者更好地理解注塑模具的工作原理和应用场景。
2. 模具设计
注塑模具的设计是制造优质塑料制品的关键步骤之一。
一个好的模具设计能够保证塑料制品的质量和生产效率。
在本实例中,我们将以一个手机壳的注塑模具为例进行介绍。
2.1 模具类型
手机壳的注塑模具可以分为两个部分:上模和下模。
上模用于注塑塑料,下模用于固定塑料模型和顶出成品。
2.2 模具材料
模具通常由高硬度钢材制成,以保证其耐磨性和寿命。
常见的模具材料包括P20、718H和S136等。
2.3 模具结构
模具结构包括模具座、顶出装置、导柱和导套等部分。
手
机壳的注塑模具一般采用简单的结构,以提高生产效率和降低成本。
3. 注塑过程
注塑是将熔化的塑料注入到模具腔中,经过冷却和固化后
形成所需的塑料制品的过程。
以下将介绍手机壳的注塑过程。
3.1 模具准备
模具准备包括模具清洁和涂油处理。
清洁模具可以确保注
塑过程中的制品质量,而涂油处理可以增加模具表面的润滑性,方便塑料流动和顶出。
3.2 注塑操作
注塑操作包括模具安装、塑料料斗填料、加热和熔化、针
嘴输送和注塑动作等步骤。
其中,针嘴输送和注塑动作是注塑过程中的关键步骤。
3.3 冷却和固化
注塑完成后,需要等待塑料冷却和固化。
冷却时间的长短
会影响成品的质量和生产效率。
4. 模具维护和故障排除
为了保证注塑模具的正常运行,需要进行定期的维护和故
障排除。
模具维护包括模具清洁、润滑和磨损部件更换等。
在遇到模具故障时,需要及时排除故障原因并进行修复。
5. 模具的应用
注塑模具广泛应用于各个领域的塑料制品生产。
手机壳只
是其中之一。
其他常见的注塑模具应用包括汽车零件、电子设备外壳和家电配件等。
6. 总结
注塑模具是制造塑料制品的重要工具。
本文以手机壳的注
塑模具为例,介绍了模具的设计、注塑过程、维护和应用等方面的内容。
希望读者通过这个实例能更好地理解注塑模具的工作原理和应用场景,并在实际生产中能够更好地应用注塑模具。