塑料模具设计(大全)
塑料模具设计(大全)

塑料模具设计1.塑料的全然概念2、热塑料的成型加工性能3、热塑料制品设计原那么4、注射成型概述5、注射成型模具全然结构及分类6、型腔分型面及浇注系统〔一〕7、型腔分型面及浇注系统〔二〕8、注射成型模具零部件的设计〔一〕9、注射成型模具零部件的设计〔二〕10、注射成型模具零部件的设计〔三〕11、注射成型模具的设计12、塑料模具设计步骤13、塑料模具课外资料〔一〕感谢大伙儿对我分享的文档资料的支持.假如大伙儿有技术的我推举大伙儿在猪八戒威客网帮不人设计,中标有钞票赚.正规网站.能够上百度寻.塑料的全然概念:〈一〉、塑料的定义及组成,塑料是指以高分子合成树脂为要紧成份、在一定温度和压力下具有塑性和流淌性,可被塑制成一定外形,且在一定条件下维持外形不变的材料。
组成:聚合物合成树脂〔40~100%〕辅助材料:增塑剂、填充剂、稳定剂、润滑剂、着色剂、发泡剂、增强材料。
辅助材料作用:改善材料的使用性能与加工性能,节约树脂材料〔贵〕〈二〉塑料的分类:300余品种,常用的是40余种名称是以所使有的合成树脂作为名称来称呼:聚乙烯、聚丙烯、聚氯乙烯、酚醛树脂、氧树脂,俗称:电木〔酚醛树脂〕,有机玻璃〔聚甲基丙烯酸甲脂〕,玻璃钢〔热固性树脂用玻璃纤维增强〕;英文名称:尼龙〔聚酰胺〕PA聚乙烯PE分类:热固性塑料与热塑性塑料〔按塑料的分子结构〕1、热塑性塑料具有线型分子链成支架型结构加热变软,泠却固化不可逆的2、热固性塑料:具有网状分子链结构加热软化,固化后不可逆.通用塑料:指产量大,用途广。
价格低廉的一类塑料。
如:聚乙烯,聚丙烯,聚氯乙烯,聚苯乙烯,醛酚塑料,氨基塑料占塑料产量的60%工程塑料:指机械性能高,可替代金属而作工程材料的一类,尼龙,聚磷酸脂,聚甲醛,ABS特种塑料:隙氧树脂〈三〉塑料的性能2、比强度高:是金属材料强度的1/10。
玻璃钢强度更高3、化学稳定性好4、电气尽缘性能优良5、尽热性好6、易成型加工性,比金属易7、缺乏:强度,刚度不如金属,不耐热。
塑料模具毕业设计题目

塑料模具毕业设计题目1.塑料套管2.小模数双联圆柱直齿轮材料为聚甲醛,大批量生产。
3.卡尺盒(+qq1162401387,获取图纸)4.透明塑料试管5.折页盒6.螺纹盖7.斜三通8.顺水三通9.灭火器壳10.锥齿轮11.螺母12.刷座14.塑料桶盖16.线轮17.导向轮18.台历架19.电视机按钮20.泡沫灭火器喷嘴21.快换接头22.塑料罩23.菜篮24.分油套25.油管接头26.上罩27.矩形罩128.端盖29.圆形盖30.盒子31.矩形罩2 32.矩形罩333.罩盖34.圆端盖35.饮料瓶盖36.座块盖37.连接座38.盒盖39.弯头40.三通管41.外壳42.旋钮43.外壳45.旋钮47.骨架48.罩49.放大镜产品名称:放大镜要求:表面无缺痕材料:透明pp生产批量:大批量50.壳盖名称材料尺寸参数值A B C D E F G H I J塑料壳盖PS 60 80 25 4 3 45 20 74 12 35 技术要求:1. 大批量生产,精度为MT5,壁厚均匀;2. 塑件不允许有裂纹和变形缺陷;3. 脱模斜度30'~1°;4. 未注圆角R=251.塑料扣盖名称材料尺寸参数值A B C DE(Φ)F(Φ)G(Φ)H(Φ)δ(Φ)塑料扣盖PP 75 30 20 5 16 65 10 50 4 技术要求:1. 大批量生产,精度为MT5,壁厚均匀;2. 塑件不允许有裂纹和变形缺陷;3. 脱模斜度30'~1°;4. 未注圆角R=152.塑料仪表盖名称材料尺寸参数值A B C D E F G H塑料仪表盖ABS 70 30 25 35 65 10 5 50 技术要求:1. 大批量生产,精度为MT5,壁厚处处相等;2. 塑件不允许有裂纹和变形缺陷;3. 脱模斜度30'~1°;4. 未注圆角R2~R35. 未注尺寸公差按所有塑料的高精度级查取。
53.多孔塑料罩名称材料尺寸参数值A B C D E F G H I多孔塑料罩PP 60 50 30 4 3 44 8 5 26 技术要求:1. 大批量生产,精度为MT5;2. 塑件不允许有裂纹和变形缺陷;3. 脱模斜度30'~1°;4. 未注圆角R2~R354. 穿线塑料盒盖名称:穿线塑料盒盖技术要求:1. 大批量生产,精度为MT5;2. 塑件不允许有裂纹和变形缺陷;3. 脱模斜度30'~1°;55.对称塑料套管名称:对称塑料套管技术要求:1. 大批量生产,精度为MT5;材料ABS;2. 塑件不允许有裂纹和变形缺陷3. 脱模斜度30'~1°;56. 塑料后盖板名称:塑料后盖板技术要求:1. 大批量生产,精度为MT5;材料ABS;2. 塑件不允许有裂纹和变形缺陷;3. 脱模斜度30'~1°;57.花边塑料盖名称:花边塑料盖技术要求:1. 大批量生产,精度为MT5;材料PP;2. 塑件不允许有裂纹和变形缺陷;3. 脱模斜度30'~1°;58.塑料罩桶名称:塑料罩桶技术要求:1. 大批量生产,精度为MT5;材料ABS;2. 塑件不允许有裂纹和变形缺陷;3. 脱模斜度30'~1°;60.圆形塑料扣盖名称:圆形塑料扣盖技术要求:1. 大批量生产,精度为MT5;材料:ABS;2. 塑件不允许有裂纹和变形缺陷;3. 脱模斜度30'~1°;61.圆形塑料罩壳名称:圆形塑料罩壳技术要求:1. 大批量生产,精度为MT5;材料ABS;2. 塑件不允许有裂纹和变形缺陷;3. 脱模斜度30'~1°;62.阶梯圆筒塑料盖名称:阶梯圆筒塑料盖技术要求:1. 大批量生产,精度为MT5;材料PP;2. 塑件不允许有裂纹和变形缺陷;3. 脱模斜度30'~1°;63. 阶梯圆筒塑料支架名称:阶梯圆筒塑料支架技术要求:1. 大批量生产,精度为MT5;材料ABS2. 塑件不允许有裂纹和变形缺陷;3. 脱模斜度30'~1°;64. 圆形塑料纱筒名称:圆形塑料纱筒技术要求:1. 大批量生产,精度为MT5;材料PP;2. 塑件不允许有裂纹和变形缺陷;3. 脱模斜度30'~1°;65. 圆形塑料桶盖名称:圆形塑料桶盖技术要求:1. 大批量生产,精度为MT5;材料PP;2. 塑件不允许有裂纹和变形缺陷;3. 脱模斜度30'~1°;66. 塑料盒上盖名称:塑料盒上盖技术要求:1. 大批量生产,精度为MT5;材料PE;2. 塑件不允许有裂纹和变形缺陷;3. 脱模斜度30'~1°;67. 塑料方盒上端盖名称:塑料方盒上端盖技术要求:1. 大批量生产,精度为MT5;材料尼龙1010黑色;2. 塑件不允许有裂纹和变形缺陷;3. 脱模斜度30'~1°;68. 圆形塑料包装盒名称:圆形塑料包装盒技术要求:1. 大批量生产,精度为MT5;材料:高密度聚乙烯;2. 塑件不允许有裂纹和变形缺陷;3. 脱模斜度30'~1°;69.弹簧上座名称:弹簧上座技术要求:1. 大批量生产,精度为MT5;材料:ABS;2. 塑件不允许有裂纹和变形缺陷;3. 脱模斜度30'~1°;70.圆形塑料扣盖名称:圆形塑料扣盖技术要求:1. 大批量生产,精度为MT5;材料:ABS;2. 塑件不允许有裂纹和变形缺陷;3. 脱模斜度30'~1°;71.圆形塑料封盖名称:圆形塑料封盖技术要求:1. 大批量生产,精度为MT5;材料:ABS;2. 塑件不允许有裂纹和变形缺陷;3. 脱模斜度30'~1°;72.塑料旋钮名称:塑料旋钮技术要求:1. 大批量生产,精度为MT5;材料:ABS;2. 旋钮表面数字凹进0.4,并涂红色蜡,字型选用3.5#字体;3. 脱模斜度30'~1°;塑件不允许有裂纹和变形缺陷。
塑料端盖注射模具设计(含全套CAD图纸)
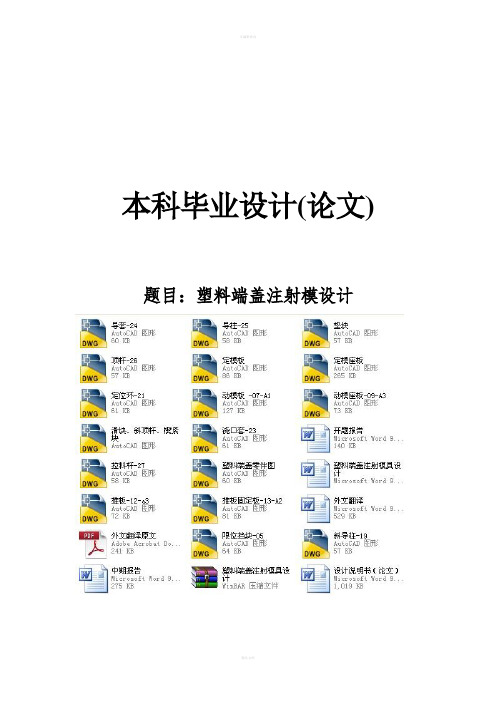
本科毕业设计(论文) 题目:塑料端盖注射模设计塑料端盖注射模设计摘要随着社会的发展,不同品种和功能的塑料的出现,塑料产品与我们的日常生活越来越密切。
塑料模具设计对生产与生活也越来越重要。
本次毕业设计的课题为塑料端盖注塑模具设计,主要在对塑件从材料上进行工艺分析,确定分型面及型腔数;完成浇注系统的设计,浇口采用侧浇口;抽芯机构采用斜导柱实现塑件的侧孔成型;脱模机构采用顶杆推出。
同时通过合理地选择注射机并对注塑压力、最大注塑量、锁模力、开模行程等相关方面进行校核,进一步保证设计的合理型,并设计温度调节系统和阐述模具装配等方面。
本次设计完成了塑料端盖的生产,此次设计不仅结构简单,生产效率高,而且运动可靠生产成本低。
最重要的是适用于人们的生活中。
关键词:端盖注塑模具;分型面;注塑模具;注射机Plastic end cap injection mold designAbstractWith the development of society different varieties and function plastic appearance in our lives, plastic productions have closer to our daily lives. Plastic mold design is more and more important to the production and life.The topic of this graduation design for the plastic end cover injection mold design, mainly in based on the analysis of the molding for plastic parts are made from the raw material analysis, forming characteristics, parting surface selection, the design of the gating system, cooling system design, the core and cavity structure design, launch reset structure design, design of side core-pulling mechanism and the design of steering mechanism and other aspects detailed in this paper, the design of the end cover injection mold process. At the same time, through the rational selection of the injection machine and check the injection pressure, the maximum injection quantity, clamping force, mold opening stroke and other related aspects, further ensuring reasonable design, and design the temperature control system and elaborated the mold assembly.This design completed the production of plastic end cover, it not only has simple structure, but also has high production efficiency and the movement is reliable low production cost.The most important it is suitable for people's life.Key Words:cover injection mold;lateral core-pulling;parting surface;injection mold;injection machine主要符号表公P 公称压力 0P 注射压力v 公最大注射量 S 收缩率v q 体积流量 'α锁紧块的斜角α斜导柱倾斜角 S 机开模行程max S 最大收缩率 S 模具制造公差z δ模具制造公差 c δ模具磨损量3h 传热膜系数 d 斜导柱直径S 抽抽芯距 []σ材料的许用应力max H 模具最大闭合高度 min H 模具最小闭合高度P 导滑槽施加的压力 Q 总模具型腔的总热量i t 流道中各段流程的厚度 A 塑件包紧型芯的侧面积L 斜导柱的有效工作长度 i L 流道中各段流程的长度p 塑件对型芯产生的单位正压力[]δ为脱模板中心允许的最大变形量1F 斜导柱与滑块之间的摩擦阻力2F 导滑槽与滑块之间的摩擦阻力目录摘要 (I)Abstract (II)主要符号表 (III)1绪论 (V)1.1塑料的发展 (1)1.2塑料模具发展 (1)1.2.1国内外注塑模具的发展现状 (1)1.2.2国内外注塑模具的发展趋势 (2)1.3本文主要设计内容 (2)2 塑件材料及工艺的分析 (4)2.1PA1010基本特性 (4)2.2PA1010成型工艺分析 (4)2.3塑件结构分析 (4)2.4塑件尺寸及精度分析 (5)2.5塑件表面质量分析 (5)2.6塑件厚度分析 (5)2.7塑件的体积和质量 (6)3 塑件在模具中的布局 (7)3.1型腔数目的确定 (7)3.2型腔的分布 (7)3.3分型面设计 (7)3.3.1分型面的分类 (7)3.3.2分型面的选择原则 (7)4 浇注系统的设计 (9)4.1浇注系统设计的组成及要求 (9)4.2主流道设计 (9)4.3分流道设计 (10)4.3.1分流道设计要点 (10)4.3.2分流道的形状和尺寸 (11)4.3.3分流道的表面粗糙度 (11)4.4浇口设计 (11)4.4.1浇口的作用 (12)4.4.2浇口的截面形状和尺寸 (12)4.4.3浇口位置的选择 (13)4.5冷料穴的设计 (13)4.6拉料杆的设计 (14)5 成型零件的结构设计 (15)5.1成型零件的结构形式及设计 (15)5.1.1凹模结构设计 (15)5.1.2型芯结构设计 (16)5.2成型零件工作尺寸的计算 (16)5.2.1影响塑件尺寸精度的因素 (16)5.2.2模具成型零件的工作尺寸计算 (17)6 结构零部件设计 (18)6.1注射模架的选取 (20)6.2垫块的设计 (20)6.3合模导向机构的设计 (20)6.3.1导柱的设计 (20)6.3.2导套设计 (21)7 侧向分型与抽芯机构的设计 (22)7.1斜导柱的设计 (22)7.1.1斜导柱的形状及技术要求 (22)7.1.2斜导柱的倾斜角 (22)7.1.3斜导柱的长度 (22)7.1.4斜导柱的受力分析与直径计算 (23)7.2滑块的设计 (24)7.3导滑槽的设计 (24)7.4滑块定位装置 (25)7.4.1滑块定位装置的作用 (25)7.4.2结构形式 (25)7.5楔紧块 (25)7.6成型斜顶杆的设计 (22)8 推出机构设计 (23)8.1推出方式的选取 (23)8.2推出力计算 (23)8.3推出机构设计 (24)8.3.1推杆推出机构设计 (24)8.3.2推出机构导向与复位 (29)9 注射机的型号和规格选择及校核 (27)9.1初选注射机规格 (27)9.2注射机工艺参数校核 (27)9.2.1最大注射量的校核 (27)9.2.2注射压力的校核 (28)9.2.3锁模力的校核 (28)9.3注射机安装部分与模具相关尺寸校核 (28)9.3.1喷嘴尺寸校核 (28)9.3.2定位圈尺寸校核 (29)9.3.3最大最小模厚校核 (29)9.3.4开模行程校核 (29)10 冷却系统的设计 (30)10.1冷却装置设计要点 (30)10.2冷却回路布置 (30)11 模具的分析及保养 (31)11.1模具的经济效益分析 (30)11.2模具的保养 (30)12 结论 (31)参考文献 (37)致谢 (33)毕业设计(论文)知识产权声明 (39)毕业设计(论文)独创性声明 (40)1绪论1.1塑料的发展现代工业的飞速发展为素有“工业之母”美誉的模具工业带来前所未有的发展机遇,而模具材料的应用在模具制造中起举足轻重的作用。
《塑料模具》成型零件图(28页)

中间加一块支 撑厚板厚为原
厚的
1/2.7 1/3.4
按跨度比1∶1、2∶1 加支撑厚,板厚为原
厚的
1/4.3 1/6.8
表3-5三边固定一边自由矩形板C值表
a/l
0.3 0.4 0.5 0.6 0.7 0.8
l/a
2.33 2.5
2 1.66 1.43 1.25
C
0.930 0.570 0.330 0.188 0.117 0.073
图3-4-10模具径向尺寸与制件径向尺寸的关系
图3-4-11型腔径向尺寸与制件径向尺寸公差带
图3-4-12型芯径向尺寸与制件径向尺寸公差带
图3-4-13型腔深度尺寸与制件高度尺寸公差带
图3-4-14型芯修高图
图3-4-15型芯高度尺寸与制件孔深度尺寸公差带
图3-4-16型腔内中心距与制件对应中心距关系
图3-4-17型芯或成型孔中心距尺寸与制件尺寸公差带
图3-4-18圆形型腔受力图
图3-4-19组合式圆形型腔底板受力图
图3-4-20整体式圆形型腔侧壁受力图
图3-4-21组合式矩形型腔侧壁受图
图3-4-22组合式矩形型腔底板受力图
图3-4-23组合式矩形型腔底板加支撑减小跨度
图3-4-24整体式矩形型腔侧壁和底板受力图
l/b
1.6 1.7 1.8 1.9 2.0
c`
0.0251 0.0260 0.0267 0.0272 0.0277
表3-1 常用塑料排气槽厚度
·塑料名称
排气槽厚度(mm)
·尼龙类塑料
≤0.015
聚烯烃塑料
≤0.02
PS、AS、ABS、增强PA
≤0.03
POM、PBT、PET、PC、PVC ≤0.04
一模两腔的塑料模具设计

毕业设计论文一模两腔的塑料模具设计姓名:系别:机械工程系专业:模具设计与制造班级:学号:目录绪论 (5)1 模具概论 (8)1.1注射模简介 (8)1.1.1注射模的定义 (8)1.2塑料制件几何形状及材料 (11)2注射机的选用 (11)2.1注射机的分类 (12)2.2分析制件结构、尺寸精度及表面质量 (12)2.2.1结构分析 (15)2.2.2尺寸精度分析 (17)2.2.3表面质量分析 (17)2.3注射机选定 (17)2.3.1计算制品的体积和质量: (17)2.3.2 初步选定注射机 (18)3 确定型腔数目及位置布局 (19)3.1型腔数目的确定 (19)3.2 型腔布局方案 (20)4 确定模具结构方案 (21)4.1分型面 (21)4.1.1分型面的选择 (21)4.1.2分型面个数的确定 (21)4.3浇注系统设计 (22)4.3.1主流道设计 (22)4.3.2主流道浇口套的设计 (23)4.3.3分流道设计 (24)4.3.4浇口的设计 (25)4.3.5冷料穴的设计 (27)4.3.6排气系统的设计 (27)5 成型零件的设计与计算 (28)5.1成型零部件设计 (28)5.2成型零件工作尺寸的计算方法 (28)5.2.1 成型零件型腔的计算结果 (29)5.2.2 确定标准模架型号和规格 (29)6 侧向分型与抽芯机构的设计 (30)6.1抽芯距的确定 (31)6.2抽芯力的确定 (31)6.3合模导向机构 (35)6.4设计推出脱模机构 (32)6.5浇注系统凝料的脱出机构 (34)7 注射机与模具有关的参数及尺寸的校核 (36)7.1 注射机注射量的校核 (36)7.1.1注射压力和锁模力的校核 (36)7.2注射机闭合高度和开模行程的校核 (36)7.3 模具在注射机上安装尺寸的校核 (37)结论 (41)参考文献 (38)致谢 (39)绪论1.塑料工业在国民经济中的作用:由于塑料具有质量轻、强度高、耐腐蚀、绝缘性好、易着色、制件可加工成任意形状,而且具有生产率高、价格低廉等特点,所以应用日趋广泛,年增长居四大工业材料之首.已经深入到国民经济的各个部门。
塑料模具课程设计实例
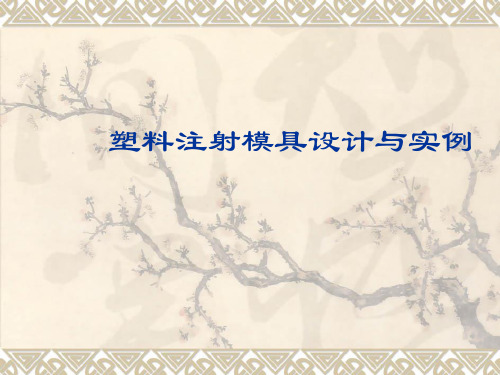
塑料注射模具设计与实例
本章基本内容
(2)模具钢
3Cr2Mo(P20)钢:可预硬化的塑料模具钢,预硬化后
硬度为36~38 HRC,适用于制作塑料注射模具型腔,其 加工性能和表面抛光性较好。 10Ni3CuAIVS(PMS)钢:析出硬化钢。预硬化后时效 硬化,硬度可达40~45 HRC。热变形极小,可做镜面抛 光,特别适合于腐蚀精细花纹。可用于制作尺寸精度高, 生产批量大的塑料注射模具。 6Ni7Ti2Cr钢:马氏体时效钢。在未加工前为固熔体 状态,易于加工。精加工后以480℃~520℃进行时效, 硬度可达50-57 HRC。适用于制造要求尺寸精度高的小 型塑料注射模具,可做镜面抛光。 8CrMnWMoVS(8CrMn)钢:为易切预硬化钢,可做镜面 抛光。其抗拉强度高,常用于大型注射模具。调质后硬 度为33-35 HRC,淬火时可空冷,硬度可达42-60 HRC。 25CrNi3MoAI钢:适用于型腔腐蚀花纹,属于时效硬 化钢。调质后硬度23 25 HRC,可用普通高速钢刀具加 工。时效后硬度38~42 HRC。可以做氮化处理,氮化处 理后表层硬度可达1100 HV。 Crl6Ni4Cu3Nb(PCR)钢:耐腐蚀钢。可以空冷淬火,
塑料注射模具制造特点 塑料注射模具零件常用加工方法和材料 塑料注射模具装配 塑料注射模具设计与制造实例
重点、难点
塑料注射模具制造特点 塑料注射模具零件常用加工方法和材料 塑料注射模具设计
注塑模具设计实例100例
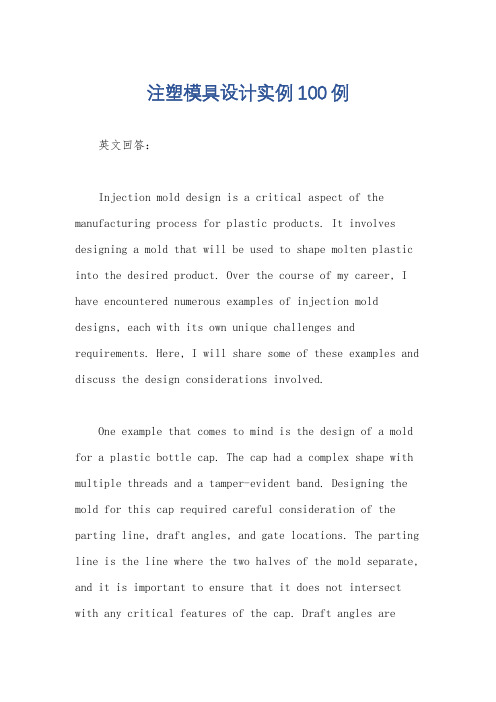
注塑模具设计实例100例英文回答:Injection mold design is a critical aspect of the manufacturing process for plastic products. It involves designing a mold that will be used to shape molten plastic into the desired product. Over the course of my career, I have encountered numerous examples of injection mold designs, each with its own unique challenges and requirements. Here, I will share some of these examples and discuss the design considerations involved.One example that comes to mind is the design of a mold for a plastic bottle cap. The cap had a complex shape with multiple threads and a tamper-evident band. Designing the mold for this cap required careful consideration of the parting line, draft angles, and gate locations. The parting line is the line where the two halves of the mold separate, and it is important to ensure that it does not intersect with any critical features of the cap. Draft angles arenecessary to facilitate the ejection of the part from the mold, and gate locations need to be strategically placed to ensure proper filling of the mold cavity.Another example is the design of a mold for a plastic automotive interior component. This component had intricate details and required a high level of precision. The mold design had to account for the shrinkage of the plastic material, as well as the need for cooling channels to dissipate heat during the molding process. Additionally, the mold needed to incorporate features such as inserts and sliders to create the desired shape and functionality of the component. This required careful consideration of the part geometry and the mold construction.中文回答:注塑模具设计是塑料制品制造过程中的关键环节。
塑料模具设计实例(word文档良心出品)

塑料模设计实例塑料注射模具设计与制造实例是通过设计图1.1所示的防护罩的注射模,全面介绍了从塑料成形工艺分析到确定模具的主要结构,最后绘制出模具的塑料注射模具设计全过程。
设计任务:产品名称:防护罩产品材料:ABS(抗冲)产品数量:较大批量生产塑料尺寸:如图1.1所示塑料质量:15克塑料颜色:红色塑料要求:塑料外侧表面光滑,下端外沿不允许有浇口痕迹。
塑料允许最大脱模斜度0.5°图1.1 塑件图一.注射模塑工艺设计1.材料性能分析(1)塑料材料特性ABS塑料(丙乙烯—丁二烯—苯乙烯共聚物)是在聚苯乙烯分子中导入了丙烯腈、丁二烯等异种单体后成为的改性共聚物,也可称为改性聚苯乙烯,具有比聚苯乙烯更好的使用和工艺性能。
ABS是一种常用的具有良好的综合力学性能的工程材料。
ABS塑料为无定型料,一般不透明。
ABS无毒、无味,成型塑料的表面有较好的光泽。
ABS具有良好的机械强度,特别是抗冲击强度高。
ABS还具有一定的耐磨性、耐寒性、耐水性、耐油性、化学稳定性和电性能。
ABS的缺点是耐热性不高,并且耐气候性较差,在紫外线作用下易变硬发脆。
(2)塑料材料成形性能使用ABS 注射成形塑料制品时,由于其熔体黏度较高,所需的注射成形压力较高,因此塑料对型芯的包紧力较大,故塑料应采用较大的脱模斜度。
另外熔体黏度较高,使ABS 制品易产生熔接痕,所以模具设计时应注意减少浇注系统对料流的阻力。
ABS 易吸水,成形加工前应进行干燥处理。
在正常的成形条件下,ABS 制品的尺寸稳定性较好。
(3)塑料的成形工艺参数确定查有关手册得到ABS (抗冲)塑料的成形工艺参数: 密 度 1.01~1.04克/mm³ 收 缩 率 0.3%~0.8%预热温度 80°c~85°c ,预热时间2~3h料筒温度 后段150°c~170°c ,中段165°C~180°c ,前段180°c~200°c 喷嘴温度 170°c~180°c 模具温度 50°c~80°c 注射压力 60~100MPa注射时间 注射时间20~90s ,保压时间0~5s ,冷却时间20~150s.2.塑件的结构工艺性分析(1)塑件的尺寸精度分析该塑件上未注精度要求的均按照SJ1372中8级精度公差值选取,则其主要尺寸公差标注如下(单位均为mm ):外形尺寸:26.0040+φ、 1.2050+、12.0045+、94.0025+R 内形尺寸:26.008.36+φ 孔 尺 寸:52.0010+φ孔心距尺寸:34.015± (2)塑件表面质量分析该塑件要求外形美观,外表面表面光滑,没有斑点及熔接痕,粗糙度可取Ra0.4μm ,下端外沿不允许有浇口痕迹,允许最大脱模斜度0.5°,而塑件内部没有较高的表面粗糙度要求。
- 1、下载文档前请自行甄别文档内容的完整性,平台不提供额外的编辑、内容补充、找答案等附加服务。
- 2、"仅部分预览"的文档,不可在线预览部分如存在完整性等问题,可反馈申请退款(可完整预览的文档不适用该条件!)。
- 3、如文档侵犯您的权益,请联系客服反馈,我们会尽快为您处理(人工客服工作时间:9:00-18:30)。
塑料模具设计1.塑料的全然概念2、热塑料的成型加工性能3、热塑料制品设计原那么4、注射成型概述5、注射成型模具全然结构及分类6、型腔分型面及浇注系统〔一〕7、型腔分型面及浇注系统〔二〕8、注射成型模具零部件的设计〔一〕9、注射成型模具零部件的设计〔二〕10、注射成型模具零部件的设计〔三〕11、注射成型模具的设计12、塑料模具设计步骤13、塑料模具课外资料〔一〕感谢大伙儿对我分享的文档资料的支持.假如大伙儿有技术的我推举大伙儿在猪八戒威客网帮不人设计,中标有钞票赚.正规网站.能够上百度寻.塑料的全然概念:〈一〉、塑料的定义及组成,塑料是指以高分子合成树脂为要紧成份、在一定温度和压力下具有塑性和流淌性,可被塑制成一定外形,且在一定条件下维持外形不变的材料。
组成:聚合物合成树脂〔40~100%〕辅助材料:增塑剂、填充剂、稳定剂、润滑剂、着色剂、发泡剂、增强材料。
辅助材料作用:改善材料的使用性能与加工性能,节约树脂材料〔贵〕〈二〉塑料的分类:300余品种,常用的是40余种名称是以所使有的合成树脂作为名称来称呼:聚乙烯、聚丙烯、聚氯乙烯、酚醛树脂、氧树脂,俗称:电木〔酚醛树脂〕,有机玻璃〔聚甲基丙烯酸甲脂〕,玻璃钢〔热固性树脂用玻璃纤维增强〕;英文名称:尼龙〔聚酰胺〕PA聚乙烯PE分类:热固性塑料与热塑性塑料〔按塑料的分子结构〕1、热塑性塑料具有线型分子链成支架型结构加热变软,泠却固化不可逆的2、热固性塑料:具有网状分子链结构加热软化,固化后不可逆.通用塑料:指产量大,用途广。
价格低廉的一类塑料。
如:聚乙烯,聚丙烯,聚氯乙烯,聚苯乙烯,醛酚塑料,氨基塑料占塑料产量的60%工程塑料:指机械性能高,可替代金属而作工程材料的一类,尼龙,聚磷酸脂,聚甲醛,ABS特种塑料:隙氧树脂〈三〉塑料的性能2、比强度高:是金属材料强度的1/10。
玻璃钢强度更高3、化学稳定性好4、电气尽缘性能优良5、尽热性好6、易成型加工性,比金属易7、缺乏:强度,刚度不如金属,不耐热。
100C以下热膨胀系数大,易蠕变,易老化。
热塑性塑料成型加工性能:〈一〉吸湿性:吸水的〔ABS.尼龙,有机中玻璃〕懦水的〔聚乙烯〕含水量大,易起泡,需枯燥。
〈二〉塑料物态:1、玻璃态:一般的塑料状态TG高于室温。
2、高弹态:温度商于TG,高聚物变得像橡胶那样柔软,有弹性。
3、粘流态:沾流化温度以上,高聚物相继出现塑料流淌性与粘性液体流淌区移,塑料成型加工就在材料的粘流态进引。
〈三〉流淌性:塑料在一定温度压力作用下,能够充分满模具型腔各局部的性能,称作流淌性。
流淌性差,注射成型时需较大的压力;流淌性太好,轻易发生流涎及造成制件溢边。
〈四〉流变性:高聚物在外加作用下产生流淌性与变形的性质喊流变性。
牛顿型流体与非牛顿型流体。
牛顿流体:要紧取决于〔流变形为〕剪切应力,剪切速率和尽对粘度,低分子化合物的液体或溶液流体属于牛顿流体。
大多数高聚物熔体在成型过程中表现为非牛顿流体。
〈五〉结晶性:冷凝时能否结晶。
无定型塑料与结晶型塑料。
结晶型:尼龙,聚丙烯,聚乙烯,无定型塑料:ABS〈六〉热敏性与水敏性。
〈七〉相熔性:熔融状态下,两种塑料能否相熔到一起,不能那么会分层,脱皮。
〈八〉应力开裂及熔体破裂。
〈九〉热性能及冷却速度。
〈十〉分子定向〔取向〕。
〈十一〉收缩性。
〈十二〉毒性,刺激性,腐蚀性。
热塑料制品设计原那么一、尺寸,精度及外表精粗糙度〈一〉尺寸尺寸要紧满足使用要求及安装要求,同时要考虑模具的加工制造,设备的性能,还要考虑塑料的流淌性。
〈二〉精度妨碍因素许多,有模具制造精度,塑料的成份和工艺条件等。
〈三〉外表粗糙度由模具外表的粗糙度决定,故一般模具外表粗糙比制品要低一级,模具外表要进引研磨抛光,透过制品要求模具型腔与型芯的外表光洁度要一致Ra〈0.2um塑件圈上无公差要求的仍由尺寸,一般采纳标准中的8级,对孔类尺寸能够标正公差,而轴类各件尺寸能够标负出差。
中心距尺寸能够棕正负公差,配合局部尺寸要高于非配合局部尺寸。
二、脱模歪度由于塑件在模腔内产生冷却收缩现象,使塑件紧抱模腔中的型芯和型腔中的凸出局部,使塑件取出困难,强行取出会导至塑件外表擦分,拉毛,为了方便脱模,塑件设计时必须考虑与脱模〔及轴芯〕方向平行的内、外外表,设计足够的脱模歪度,一般1°——1°30`。
一般型芯歪度要比型腔大,型芯长度及型腔深度越大,那么歪度不减小。
三、壁厚依据塑件使用要求〔强度,刚度〕和制品结构特点及模具成型工艺的要求而定壁厚太小,强度及刚度缺乏,塑料填充困难壁厚太大,增加冷却时刻,落低生产率,产生气泡,缩孔等。
要求壁厚尽可能均匀一致,否那么由于冷却和固化速度不一样易产生内应力,引起塑件的变形及开裂。
四、加强筋设计原那么:〈一〉中间加强筋要低于外壁0.5mm以上,使支承面易于平直。
〈二〉应防止或减小塑料的局部聚积。
〈三〉筋的排例要顺着在型腔内的流淌方向。
五、支承面塑件一般不以整个平面作为支承面,而取而代之以边框,底足作支承面。
六、圆角要求塑件防有转角处都要以圆角〔圆弧〕过渡,因尖角轻易应力集中。
塑件有圆角,有利于塑料的流淌充模及塑件的顶出,塑件的外瞧好,有利于模具的强度及寿命。
七、孔〔槽〕塑件的孔三种成型加工方法:〔1〕模型直截了当模塑出来。
〔2〕模塑成盲孔再钻孔通。
〔3〕塑件成型后再钻孔。
先模塑出浅孔好。
1、模塑通孔要求孔径比〔长度与孔径比〕要小些,当孔径〈1.5MM,由于模芯易弯曲曲折折折断,不适于模塑模塑型芯的三种方式。
2、肓孔的深度:h〈〔3—5〕dd〈1.5时,h〈3d3、异形孔〔槽〕设计塑件如有侧孔或凹槽,那么需要活动块或抽芯机构"平行射成原那么"确定塑件侧孔〔槽〕是否适合于脱模。
热塑性塑料中软而有弹性的,如聚乙烯,聚丙烯,聚甲醛导制品,内孔与外像浅的可强制脱模。
八、螺纹塑件中的螺纹可用模塑成型出来,或切削方法获得通常折装或受力大的,要采纳金属螺纹嵌件来成型。
九、嵌件为了增加塑料制品整体或某一部位的强度与刚度,满足使用的要求,常在塑件体内设置金属嵌件。
由于装潢或某些特殊需要,塑料制品的外表常有文字图案。
1、标志2、凹凸纹:如把手,旋钮,手轮制品的固边,以增加摩擦力,凹凸纹要做成直纹,以便于脱模。
3、花纹:凹凸纹,皮革纹,桔皮纹,纹浪纹,点格纹,菱形纹。
加工花纹方法:电火花加工,照像化学磨蚀,雕刻冷挤压。
注射成型概述一、注射成型原理与过程:是热塑性塑料成型的一种要紧加工方法1、合模,加料,加热,塑化,挤压2、注射,保压,冷却,固化,定型3、螺杆嵌塑,脱模顶出二、注射成型设备〈一〉注射成型机的分类:〈1〉按用途:热塑性塑料注射成型机,热固性塑料注射成型机〈2〉按外形:立式,卧式,角式〈3〉按能力:小型〔〈50cm注射量,中型〔50~1000cm^〕大型〉1000cm^〈4〉按塑化分:有塑化装置,有塑化装置〈5〉按操作:手动,半回动,自动〈6〉按绕动:机械绕动,液压绕动,机械液压绕动〈二〉注射成型的结构组成1、注射紧绕:料斗,塑化部件〔料筒,螺杆,电热圈〕喷嘴。
2、锁模紧绕:实现模具的启闭,锁紧,塑件顶出。
3、传动操作操纵紧绕。
〈三〉注射机的型号,规格,全然参数1、一般以注射量表示注射机的容量,Xs-ZY,25表示:一次最大注射量为1-25CM^的倒式螺杆注射成型机.2、全然参数:公称注射量,合模压力,注射压力,注射速度,注射功率,塑化能力,合模与开模速率,机器盾隙次数,最大成型面积,模板尺寸,模板间距离,模板过程。
〈四〉注射成型机的工作过程注射成型模具全然结构及分类一、全然结构,依据局部起作用不同分类:〈一〉浇注系统将塑料由注射机喷嘴引向型腔的通道称浇注系统,其由主流道,分流道,内浇口,冷料穴等结构组成,由零件的浇注套,拉料杆等组成。
〈二〉成型零件是直截了当构成塑料件外形及尺寸的各种零件,由型芯〔成型塑件内部外形〕,型腔〔成型塑料外部外形〕,成型杆,镶块等构成。
〈三〉结构零件构成零件结构的各种零件,在模具中起安装,导向,机构动作及调温等作用。
导向零件:导柱,导套。
装配零件:定位隙,定模底板,定模板,动模板,动模垫板,模足冷却加热系统依据其运动特点均可分为两大局部:定模局部:一部份留于模具机座的定模板上,动模局部:随注射机动模板运动的局部定模局部与动模局部闭合那么可形成型腔与浇注系统二、模具的分类〈一〉按注射机类型分:立式注射机,卧式注射机,直角式注射机上用的模具〈二〉按注射模具的总体结构特征分:1、单分型面模分流道位于分型面上,需切除流道凝料。
〔模拟动画〕2、点浇口脱出模具〔三板式模具〕〔模拟动画〕3、带横向轴芯的分型模具〔模拟动画〕4、自动卸螺纹注射成型模具型腔分型面及浇注系统〔一〕一、分型面:分开模具能取出塑件的面,称作分型面,其它的面称作不离面或称分模面,注射模只有一个分型面。
分型面的方向尽量采纳与注塑机开模是垂直方向,外形有平面,歪面,曲曲折折面。
选择分型面的位置时,〈1〉分型面一般不取在装饰外外表或带圆弧的转角处〈2〉使塑件留在动模一边,利于脱模〈3〉将同心度要求高的同心局部放于分型面的同一侧,以保征同心度〈4〉轴芯机构要考虑轴芯距离〈5〉分型面作为要紧排气面时,分型面设于料流的末端。
一般在分型面凹模一侧开设一条深0.025~0.1mm宽1.5~6mm的排气槽。
亦能够利用顶杆,型腔,型芯镶块排气二、浇注系统浇注系统是指模具中从注射机喷嘴接触处到型腔为止的塑料熔体的流淌通道。
作用:〈1〉输送流体〈2〉传递压力〈一〉浇注系统的组成及设计原那么1、组成:由主流道,分流道,内浇口,冷料穴等结构组成。
2、浇注系统的设计原那么:〈1〉考虑塑料的流淌性,保征流体流淌顺利,快,不紊乱。
〈2〉防止熔体正面冲出小直径型芯或脆弱的金属镶件。
〈3〉一模多腔时,防止大小相差悬殊的制件放一模内。
〈4〉进料口的位置和外形要结合塑件的外形和技术要求确定。
〈5〉流道的进程要短,以减少成型周期及减少废料。
〈二〉主流道设计指喷嘴口起折分流道进口处止的一段,与喷嘴在一轴线上,料流方向不改变。
〔1〕便于流道凝料从主流道衬套中拔出,主流道设计成圆锥形。
7-15锥角=2°~4°粗糙度Ra≤0.63与喷嘴对接处设计成半球形凹坑,球半径略大于喷嘴头半经。
〔2〕主流道要求耐高暖和摩擦,要求设计成可拆卸的衬套,以便选用优质材料单独加工和热处理。
〔3〕衬套大端高出定模端面5~10mm,并与注射机定模板的定位孔成间隙配合,起定位隙作用。
〔4〕主流道衬套与塑料接触面较大时,由于腔体内反压力的作用使衬套易从模具中退出,可设计定住。
〔5〕直角式注射机中,主流道设计在分型面上,不需沿轴线上拔出凝料可设计成粗的圆柱形。
〈三〉分流道设计指塑料熔体从主流道进进多腔模各个型腔的通道,对熔体流淌起分流转向作用,要求熔体压力和热量在分流道中损失小。