基于有限元法的车架轻量化设计和仿真分析
一种重卡车架轻量化结构设计及有限元分析
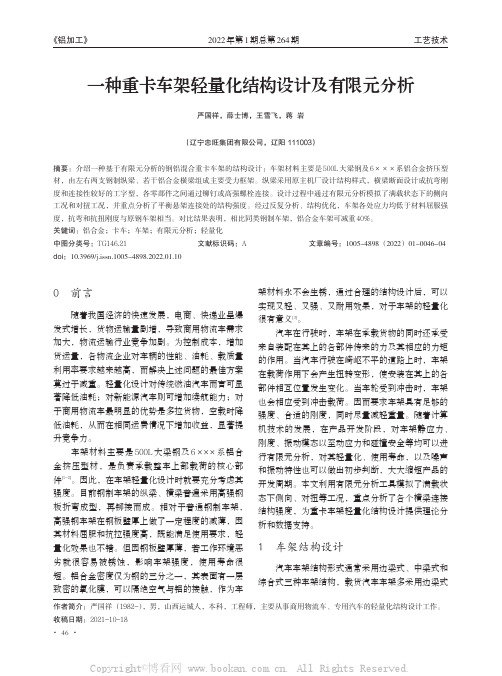
作者简介:严国祥(1982-),男,山西运城人,本科,工程师,主要从事商用物流车、专用汽车的轻量化结构设计工作。
收稿日期:2021-10-18一种重卡车架轻量化结构设计及有限元分析严国祥,薛士博,王雪飞,蒋岩(辽宁忠旺集团有限公司,辽阳111003)摘要:介绍一种基于有限元分析的钢铝混合重卡车架的结构设计:车架材料主要是500L 大梁钢及6×××系铝合金挤压型材,由左右两支钢制纵梁、若干铝合金横梁组成主要受力框架。
纵梁采用原主机厂设计结构样式,横梁断面设计成抗弯刚度和连接性较好的工字型,各零部件之间通过铆钉或高强螺栓连接。
设计过程中通过有限元分析模拟了满载状态下的侧向工况和对扭工况,并重点分析了平衡悬架连接处的结构强度。
经过反复分析、结构优化,车架各处应力均低于材料屈服强度,抗弯和抗扭刚度与原钢车架相当。
对比结果表明,相比同类钢制车架,铝合金车架可减重40%。
关键词:铝合金;卡车;车架;有限元分析;轻量化中图分类号:TG146.21文献标识码:A文章编号:1005-4898(2022)01-0046-04doi:10.3969/j.issn.1005-4898.2022.01.100前言随着我国经济的快速发展,电商、快递业呈爆发式增长,货物运输量剧增,导致商用物流车需求加大,物流运输行业竞争加剧。
为控制成本,增加货运量,各物流企业对车辆的性能、油耗、载质量利用率要求越来越高,而解决上述问题的最佳方案莫过于减重。
轻量化设计对传统燃油汽车而言可显著降低油耗;对新能源汽车则可增加续航能力;对于商用物流车最明显的优势是多拉货物,空载时降低油耗,从而在相同运费情况下增加收益,显著提升竞争力。
车架材料主要是500L 大梁钢及6×××系铝合金挤压型材,是负责承载整车上部载荷的核心部件[1-2]。
因此,在车架轻量化设计时就要充分考虑其强度。
目前钢制车架的纵梁、横梁普遍采用高强钢板折弯成型,再铆接而成。
基于ANSYS的自行车车架结构有限元分析

基于ANSYS的自行车车架结构有限元分析自行车车架是自行车的核心组成部分,它承载着骑手的重量和外界的力量,直接影响着自行车的性能和稳定性。
为了确保自行车车架的可靠性和安全性,有限元分析被广泛应用于自行车车架结构设计。
有限元分析是一种应用于工程领域的数值计算方法,通过将实际结构离散为若干个小单元,近似计算每个小单元的力学特性和应力分布,从而得到整体结构的力学性能。
在进行自行车车架的有限元分析时,需要先对车架进行几何建模。
通常可使用计算机辅助设计软件或三维建模软件进行建模,将车架几何形状、尺寸和连接方式等细节进行精确描述。
接下来,将车架模型导入ANSYS软件中进行分析。
在分析过程中,需要先对车架进行网格划分,将其离散为数个小单元,以便进行后续的力学计算。
划分网格时需要考虑车架各处应力分布的均匀性和准确性。
进行有限元分析时,需要对车架施加相应的边界条件和载荷。
边界条件包括固定支撑或约束,以模拟车架与其他部分的连接方式。
载荷可以是骑手的重力、外界风阻、不平坦路面等因素,通过合理选择载荷类型和大小来模拟实际使用条件。
在进行有限元分析时,需要定义适当的材料参数,包括车架的弹性模量、泊松比、材料屈服强度等。
这些参数直接影响着车架的刚度和性能。
通过对车架进行有限元分析,可以得到车架各处的应力、应变分布情况。
基于分析结果,可以对车架进行优化设计,以满足强度和刚度的要求。
例如,在高应力处添加加强结构或材料,以提高车架的强度和稳定性。
此外,有限元分析还可以在车架结构设计阶段进行疲劳寿命预测。
通过加载一定的循环载荷,可以计算出车架在特定循环次数下的疲劳损伤情况,从而评估车架结构的可靠性和耐久性。
总之,基于ANSYS的有限元分析在自行车车架结构设计中扮演着至关重要的角色。
它可以帮助设计师评估车架的强度、刚度和耐久性,并优化设计以提高车架的性能和稳定性。
通过有限元分析,可以减少设计过程中的试错成本,提高设计效率,为自行车车架的可靠性和安全性提供保障。
自卸车车架有限元分析与轻量化设计

自卸车车架有限元分析与轻量化设计
于发加
【期刊名称】《汽车实用技术》
【年(卷),期】2024(49)4
【摘要】自卸车车架的轻量化一直是整车厂的设计目标之一,车架轻量化不仅可以节约材料和成本,也可以减少油耗,提高经济性。
文章以某型自卸车为研究对象,运用ANSYS软件对车架进行三种工况静力学分析,根据仿真分析数据对车架进行轻量化设计,选取最佳优化方案,对轻量化的车架进行静态和模态分析,验证其是否满足使用要求,分析及轻量化设计自卸车车架对增加自卸车辆的整车使用寿命,对提高其安全可靠性和经济性有一定的工程实践意义。
【总页数】4页(P125-128)
【作者】于发加
【作者单位】青岛港湾职业技术学院继续教育与技能培训中心
【正文语种】中文
【中图分类】U270.32
【相关文献】
1.基于相对灵敏度分析的自卸车车架轻量化设计
2.矿用自卸车车架副梁轻量化设计
3.电动轮自卸车车架结构抗疲劳轻量化设计
4.基于静动态特性的自卸车车架轻量化设计
5.无副车架的重型自卸车架轻量化优化设计
因版权原因,仅展示原文概要,查看原文内容请购买。
基于有限元分析的节能车车架轻量化设计
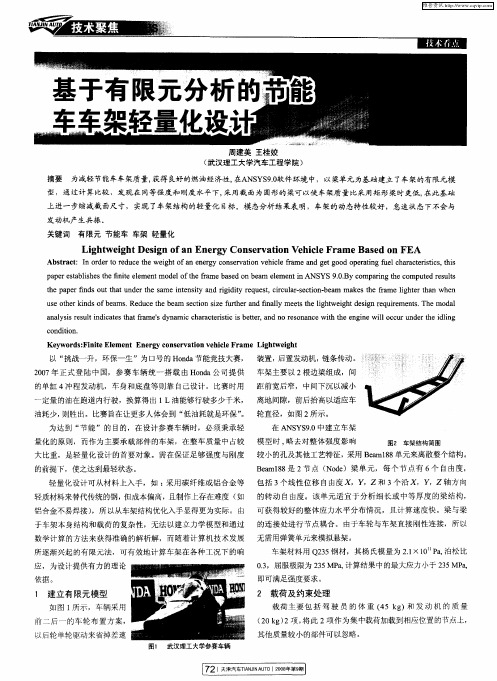
在A Y 9 NS S . 建 立 车 架 0中 图2 车架结构简图
量 化 的原 则 , 而 作 为 主要 承 载 部 件 的车 架 ,在 整 车 质 量 中 占较 模 型 时 , 去 对 整 体 强 度 影 响 略
大 比重 ,是 轻 量 化 设计 的 首要 对 象 。需 在保 证 足 够 强 度 与 刚 度 较小的孔及其他工艺特征,采用 B a em18单元来离散整个结构。 8
上进一步缩减截面尺寸, 实现 了车架结构 的轻量化 目标。模 态分析结果表 明 ,车架的动态特性较好 ,怠速状 态下不会 与
发 动机 产 生 共 振 。
关键词
有 限元 节 能车 车架 轻量化
பைடு நூலகம்
Li h weg tDe i n o n Ene g ns r a i n Ve c eFr m eBa e n FEA g t i h sg fa r y Co e v to hil a s d o
c n io . o dt n i Ke wo d : i i e n e g o s r a i n v h ceFr m e Li h we g t y r sF n t El me t En r y c n e v t e i l a g t i h e o
以“ 挑战一升,环保一生”为 口号 的 H na节能竞技大赛, od
的前提下 ,使之达到最轻状态。
Ba 8 em18是 2节点 ( o e N d )梁 单元,每 个节 点有 6个 自由度 ,
个 ,Z和 3个沿 ,y,Z轴方 向 轻量化设计可从材料上入手,如 : 采用碳纤维或铝合金等 包括 3 线性位移 自由度 ,y 轻质材料来替代传统的钢 , 但成本偏高,且制作上存在难度 ( 如 的转动 自由度 。该单 元适 宜于分析细长 或中等厚度 的梁结构 , 铝合金不易焊接 ) ,所以从车架结构优化入手显得更为实际。由 可获得较好的整体应力水平分布情况,且计算速度快 。梁与梁 于车架本身结构和载荷的复杂性 ,无法 以建立力学模 型和通过 的连接处进行节点耦合 。由于车轮与车架直接 刚性连接 ,所 以
某车架有限元建模及仿真研究
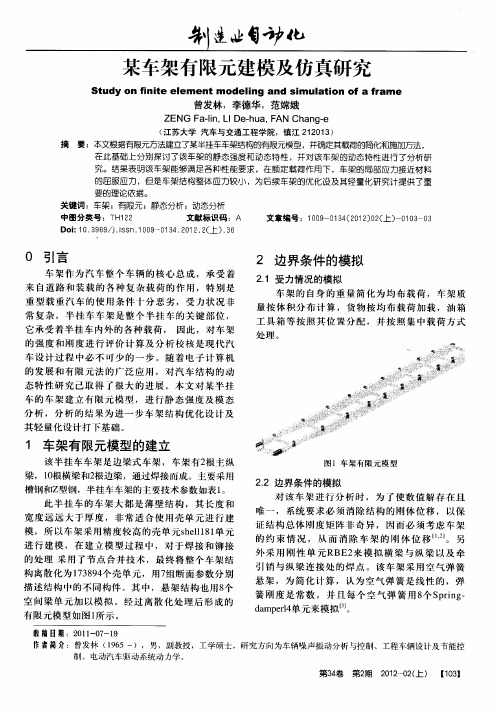
车 的 车 架 建 立 有 限元 模 型 ,进 行 静 态 强 度 及模 态 分 析 , 分 析 的 结果 为 进 一 步 车 架 结 构 优化 设 计 及
其 轻 量化设 计 打下基 础 。
1 车架有限元模型的建立
该 半 挂车 车 架 是边 梁式 车 架 ,车 架 有2 主 纵 根 梁 ,1根 横梁和2 边梁 ,通过焊 接而成 。主 要采用 O 根 槽钢 和z 型钢 ,半挂 车车架的主 要技 术参数如表 1 。 此 半 挂 车 的 车 架 大 都 是 薄 壁 结 构 ,其 长 度 和
收 稿 日期 :2 1- 7 9 0 1 0 -1 I 者简介:曾发林 (9 5一),男 ,副教授 ,工学硕 士,研究方 向为车辆噪声振动分 析与控制、工程车辆设计及节能控 1 E 16
制 、电动汽车驱动系统动力学 。
第3 卷 4
第2 期 2 1 — 2 上 ) [0 ] 0 2 0 ( 1 3
描 述 结构 中的不 同构 件 。其 中 ,悬 架 结构 也 用8 1 4
空 间 梁 单 元 加 以模 拟 。经 过 离 散 化 处 理 后 形 成 的 有限 元模 型如 图 1 示 。 所
簧 刚 度 是 常 数 ,并 且 每 个 空 气 弹 簧 用 8 - pig 4 S rn —
d mp r 单 元来模 拟 。 a el 4
样 完 全 消 除 结构 的 刚体 运 动 的 可 能 性 ,从 而 求 得 在载 荷作 用下 结构 变形 的精确 解 。 ,
31 非 对称 垂直 动载 荷工 .
当进行 有 限元 模拟 时 ,路 面不 平 度高 度h , n 根 据 相关 资 料 ,取h = 0 mm,具 体 分 析 时 ,将车 n 10 架 的 自身 的 重 量 附件 及 载 货 重 量 乘 以 动 载 荷 系数 施 加 到 相 应 的 节 点上 ,在 复杂 的 工 况 下 ,车速 不 宜过 高 , 因此取 动载 系数 K I . = . 施加 约束 时 ,在约 5
基于有限元法的车架性能仿真分析

d i1 . 6 /.s. 7 — 122 1 . . 8 o :03 9js 1 3 3 4 . 0 40 9 in 6 0 0 0
基于有 限元法 的车架性能仿真分析
吴 百朋 , 赵栋杰 , 晓华 楚
( 聊城大学汽车与交通工程学 院, 山东 聊城 2 2 5 ) 50 9
摘要 : 用有限元法对某农用车车架进行 了仿真分析 。 应 首先在 U G软件 中建立 了车架实体模型 , 然后利用有限 元软件建立 了以板单元为基本 单元 的车 架有限元模 型 , 并对其进行 了线性静 态分析和模 态分析 , 获得 了车架 在 两种典型工况下的应力及位 移分布 以及前六阶 固有频率和振型 , 验证 了车架的刚强度 , 也为车架的改型设
型 .后 导人 有 限元软 件 中进行 网格 划分 和参 数设
长。近年来 , 随着计算机辅助工程技术的发展 , 有 限元 法在 农 用 车领 域逐 步 得 到应 用 . 取 得 了很 并
好 的效 果[ 1 ] 。 本文 应用 通用 有 限元软件 对 车架进 行 了静态 分 析和模 态分 析 ,得 到 了其在 各 工况下 的应 力分
WU B ip n . H O D n-i. HUX a— u a e g Z A ogj C ioh a - e
( i ce gU i rt, i e eg2 2 0 , hn ) La hn nv sy La h n 5 0 0 C i o ei o a
Ab ta t i l t n a ay i frs me tp r t c ce f me w sp r r e sn E meh d CA mo e a u l wi sr c :S mu ai n lss o o y e f m r y l a a e fm d u ig F A t o . D d l sb i t UG o a i r o w t h s f r . EM d l s sa l h db kn el s a i nt i o E o t r, n n l s f i e rsai n o a ot e F wa mo e tb i e yt i gs l a b scu i w t s meF A s f wa e s a h a h wa e a d a ay i o n a t a d n r l s l t c m mo e r a r d o t 1 e d fr ain a d sr s it b t n o y ia o dt n r b an d mo e v r n t r l r q e c ds we ec ri u . ’ eo e h m t n te sd s u i f wotp c l n i o s o i r o t c i we eo t i e , ro e , au a e u n y f
基于有限元分析的轻量化车身设计优化研究
基于有限元分析的轻量化车身设计优化研究随着汽车工业的不断发展,轻量化车身设计越来越受到关注。
轻量化车身设计可以降低汽车质量和能耗,同时提高车辆的安全性能和驾驶舒适性。
为了满足日益增长的市场需求,汽车制造商不断探索新的轻量化技术,其中有限元分析是一种广泛应用于车身设计的技术。
有限元分析是一种数字仿真技术,可用于预测材料和结构的反应和行为。
在轻量化车身设计中,有限元分析可以用于确定材料在负载下的性能,了解应力的传递和变形情况,并优化车身结构和性能。
这种技术不仅可以减少车身重量,而且可以提高车辆的刚度和承载能力。
轻量化车身设计的关键在于选择材料。
合理选择轻量化材料不仅可以减轻车身重量,还可以提高材料强度和刚度。
常用的轻量化材料包括高强度钢、镁合金、铝合金、碳纤维和复合材料等。
针对不同的应用场景和加工成本,汽车制造商需要仔细选择材料和结构。
在有限元分析的基础上,汽车制造商可以针对不同的应用场景进行车身设计优化。
例如,在碰撞测试中,车身的吸能能力是一个非常重要的参数。
为了提高车身的吸能能力,制造商可以选择具有高强度和韧性的材料,并改变车身结构来增加吸能区域。
同时,制造商还可以使用有限元分析来优化车身的裂纹传播路径,减少碰撞后车身的损坏范围。
另一个优化点是降低车身噪音和震动。
汽车在行驶过程中会产生各种噪音和震动,这些不仅影响驾驶舒适性,还会对车身结构造成损伤。
制造商可以使用有限元分析来分析材料和结构的固有频率,选择合适的材料和结构,进而减少车身的噪音和震动。
最后,轻量化车身设计还可以提高车身耐用性和可持续性。
轻量化车身可以减少汽车质量和燃油消耗,同时减少对环境的影响。
为了提高车身的耐用性和可持续性,制造商可以选择具有高耐腐蚀性的材料,并在车身结构上使用高效的防护措施。
总之,基于有限元分析的轻量化车身设计优化是一种有效的技术。
使用这种技术,制造商可以在不牺牲车身性能和安全性能的前提下,实现车身轻量化和优化设计。
基于有限元的客车车架轻量化设计
图1 车架有限元加载图2 车架的静态分析2.1 纯弯曲静力分析满载弯曲工况下,车架承受的载荷是最大的,这种工况下车架所受的应力和变形都相对较大。
如图2有限元模型图可知,最大应力值为199.87 MPa, 远小于车架的屈服强度,发生在车架前后车轮约束的位置。
最大变形量19.820 mm,发生在车架的后横梁上,此处缺少好的刚度支撑,变形较大,但仍符合刚度要求,此工况下车架安全。
2.2 紧急制动静力分析满载情况下车架可能受到较大的应力和变形,在此情况下紧急制动,车架的受力会更加复杂。
由图知,紧急制动情况下最大应力值为200.41 MPa,在吊耳与图2 满载弯曲工况下的应力图图4 紧急制动工况应力图图6 车架纯弯曲分析 图7 分析应力图 图8 分析形变图图3 满载弯曲工况下的形变图 图5 紧急制动工况形变图车架相接的位置,大于简单的满载弯曲工况。
最大变形量为19.800 mm,出现在车架的后横梁上,与满载弯曲工况相差不大,变形幅度较小,在合理范围之内,此工况下车架安全。
从分析结果来看,最大应力为200.41 MPa,未超过安全系数为1.5时的最大应力值233.00 MPa;车架有轻微变形,但符合刚度要求,车架变形的最大位移为19.800 mm。
综上所述,该车架结构满足刚度和强度要求,且有很大的轻量化空间,可进行轻量化设计。
3 车架轻量化设计3.1 车架尺寸优化先用车架的主纵梁进行优化设计。
取主纵梁的厚度和宽 4 结束语本文对运用ANSYS 对车架结构有限元模型进行了分析研究,分析纯弯曲工况和紧急制动工况下的强度和刚度特性。
掌握了车架结构特性,各个部分受力和变形的特点,并进行了车架的优化设计。
车架质量由6 970 kg 减少为6 290 kg,。
基于ANSYS的自行车车架结构有限元分析
基于ANSYS的自行车车架结构有限元分析自行车车架是连接自行车各个部件的重要结构,其设计优化对于提高整车性能和骑行舒适度至关重要。
有限元分析是一种常用的工程分析方法,可以用来评估自行车车架的结构强度、刚度和耐久性等特性。
在ANSYS软件中进行自行车车架有限元分析可以帮助设计师更好地理解和改进车架的设计。
首先,进行自行车车架有限元分析的第一步是建立几何模型。
可以使用ANSYS中的建模工具来创建车架的三维几何模型。
在建模过程中,需要考虑车架各个部件的几何形状、连接方式和材料参数等。
接下来,需要为车架模型分配材料属性。
车架材料的选择对于整体结构的强度和刚度具有重要影响。
可以利用ANSYS中的材料库来选择合适的材料,并为车架的不同部件分配相应的材料属性。
然后,需要进行约束和加载设置。
在真实的使用条件下,车架会受到各种力的作用,如骑行时的重力、路面不平和操控力等。
在有限元分析中,应根据实际工况和设计要求来设置适当的约束和加载。
例如,在车架的连接点设置约束,模拟骑行时的力加载。
随后,进行网格划分和网格质量检查。
网格划分是将车架模型离散化为有限元网格的过程。
在ANSYS中,可以使用自动划网工具或手动划网。
划分好网格后,还需要进行网格质量的检查和优化,以确保计算结果的准确性和可靠性。
然后,进行有限元分析求解。
有限元分析是通过将车架模型离散化为多个有限元单元,并根据材料特性、加载条件和边界条件来计算结构的应力、变形和刚度等参数。
在ANSYS中,可以选择不同的分析类型和求解器来进行分析。
根据需要,可以进行静力学、动力学、热力学和疲劳分析等。
最后,进行结果评估和优化。
通过有限元分析,可以得到车架在各个部件的应力分布图、变形图和刚度分析结果。
根据这些结果,可以评估车架的结构强度和刚度,并进行优化设计。
例如,可以优化车架的几何形状、材料选用和连接方式,以提高车架的性能。
总结起来,基于ANSYS的自行车车架结构有限元分析是一种重要的工程分析方法,可以帮助设计师评估和改进车架的设计。
基于有限元法的某8×4重型载货车车架轻量化仿真分析
10.16638/ki.1671-7988.2021.03.024基于有限元法的某8×4重型载货车车架轻量化仿真分析胡锐(安徽江淮汽车集团股份有限公司,安徽合肥230601)摘要:随着国家对安全、减重、节能和环保的重视,重卡轻量化的需求日益迫切。
车架作为重卡最大的零部件,在满足强度的同时减轻重量成为轻量化的重点研究对象。
文章基于有限元法对某8×4载货车车架进行轻量化仿真分析,对优化前后的车架各零部件的安全系数及总成模态值进行对比,确认方案的可行性。
关键词:轻量化;车架;仿真中图分类号:U463.32 文献标识码:A 文章编号:1671-7988(2021)03-80-03Lightweight Simulation Analysis of a 8x4 Heavy-duty Truck Frame Basedon Finite Element MethodHu Rui( Anhui Jianghuai Automobile Group Co., Ltd., Anhui Hefei 230601 )Abstract:With the country of safety, energy saving and environmental protection the importance of weight loss, heavy truck lightweight urgent demand. Frame heavy truck parts as the largest, at the same time to meet the strength reduce weight become the focus of the research object of lightweight. Based on the finite element method, the simulation and analysis of the lightweight of a 8×4 vehicle frame are carried out. The safety factor and the assembly mode of each frame before and after optimization are compared and the feasibility of the scheme confirmed.Keywords: Lightweight; Frame; SimulationCLC NO.: U463.32 Document Code: A Article ID: 1671-7988(2021)03-80-03前言随着国家对于汽车节能减排的要求日益提升,轻量化作为节能减排的重要手段已成为商用车整车开发的重要课题。
- 1、下载文档前请自行甄别文档内容的完整性,平台不提供额外的编辑、内容补充、找答案等附加服务。
- 2、"仅部分预览"的文档,不可在线预览部分如存在完整性等问题,可反馈申请退款(可完整预览的文档不适用该条件!)。
- 3、如文档侵犯您的权益,请联系客服反馈,我们会尽快为您处理(人工客服工作时间:9:00-18:30)。
基于有限元法的车架轻量化设计和仿真分析
有限元法在车架轻量化设计和仿真分析中是一种常用的工具。
该方法基于数学模型,将结构划分成一系列小的单元,通过计算每个单元的应力、变形等物理量,反推得到整个结构的力学性能。
在车架轻量化方面,有限元法可以帮助我们快速地找到轻量化的设计方案,并通过仿真分析验证其性能,从而提高车架的安全性和可靠性。
首先,在轻量化设计中,我们需要寻找轻量化的潜在方案。
有限元法可以帮助我们划分车架结构,并计算不同部件的受力情况。
通过对受力情况的分析,我们可以找到那些不必要的部件或重量过剩的区域,从而进行删减。
例如,我们可以尝试使用高强度材料或降低材料使用量等方式来达到轻量化的目的。
其次,在设计轻量化方案后,需要通过仿真分析来验证其性能。
在有限元法中,我们可以将车架结构的物理特性输入到数学模型中,并通过计算得出其应力分布、变形情况等。
通过这种方式,我们可以在实际试验之前,快速地评估轻量化方案的性能,并进行修改和优化。
最后,有限元法还可以帮助我们改进设计方案,以进一步提高车架的性能。
例如,在仿真分析中,我们可以调整材料的类型和厚度,以达到更好的性能。
我们还可以通过优化部件的形状和尺寸,来减少结构的应力集中和变形等问题。
总之,有限元法在车架轻量化设计和仿真分析中是一种非常有效的工具。
通过使用该方法,我们可以快速地找到轻量化方案,
并通过性能仿真进行验证和优化,最终提高车架的安全性和可靠性。
为了能更清楚地了解车架轻量化设计和仿真分析的数据,我们可以以一辆小型轿车为例,尝试列出相关数据并进行分析。
首先,我们需要了解该汽车原始的车架结构的总重量、尺寸和材料类型及数量等情况。
假设该汽车的车架总重量为1000千克,尺寸为4000毫米长、1500毫米宽和1500毫米高,使用
的材料为钢材和铝材,其中钢材使用量为80%。
我们可以看到,该车架的重量相对较高,需要进行轻量化设计。
接下来,我们可以通过有限元法对该车架进行轻量化设计。
我们可以尝试使用高强度材料替代部分钢材,或者减少材料的使用量等方式来达到轻量化的目的。
我们可以通过计算不同方案的重量、结构刚度、变形程度等来分析轻量化的效果。
假设我们使用了铝材替代了车架中25%的钢材,并只在必要部位增
加了一些加强筋,这样车架的重量就可以减少到900千克。
最后,我们可以使用有限元法对轻量化后的车架进行仿真分析。
我们可以将该车架的物理特性输入到数学模型中,并计算出其应力分布、变形情况等参数。
通过数字仿真分析,我们可以快速地评估轻量化方案的性能,并进行修改和优化。
通过几轮优化,我们可以进一步减轻车架重量,并增加其刚度和耐久性。
总之,对于车架轻量化设计和仿真分析来说,数据的分析对于整个设计过程都是至关重要的。
只有了解原始的数据,分析轻量化效果,以及通过仿真分析进行修改和优化,才能真正提高车架的安全性和可靠性。
车架轻量化设计和仿真分析在汽车行
业中得到了广泛的应用。
以Tesla Model S为例,该车型使用碳纤维复合材料来代替传统钢材,大幅提高了车架的强度和刚度,同时使整车重量得以降低,从而在提高车辆性能的同时提高了能源效率。
在该案例中,使用碳纤维复合材料替代传统的钢材,这样做的优势在于:
1. 提高了车架的强度和刚度,在汽车碰撞时可以更好地保护车内乘客的安全。
2. 碳纤维复合材料的重量轻,可以使整车重量得到有效控制,从而达到节能减排的目的。
3. 碳纤维复合材料的设计灵活性高,能够根据不同的需求进行个性化的设计以及生产,从而可以实现全新的车辆外观和性能表现。
此外,Tesla Model S还进行了有限元仿真分析,以分析车架的结构强度和稳定性,并通过多次修改和优化,提高了车架的性能。
从Tesla Model S的成功案例中,我们可以得到以下的经验和教训:
1. 选用合适的材料很关键:碳纤维复合材料可以达到较高的强度和刚度,并且重量较轻,这对汽车轻量化的设计具有很大的帮助。
2. 需要进行综合的设计与仿真分析:有限元仿真分析有助于我们分析车架的结构强度和稳定性,从而指导后续的优化设计。
3. 不断进行优化与改进:汽车设计是一个不断完善和改进的过程,需要通过多次的仿真分析和调整来逐步提高车架的性能和安全性。
4. 技术与创新是推动汽车行业的关键:Tesla Model S的成功不仅在于采用了碳纤维复合材料,更在于其创新性的技术和设计,这是汽车行业的未来方向。