机床铸件技术要求及验收
铸造材料技术要求和验收规范
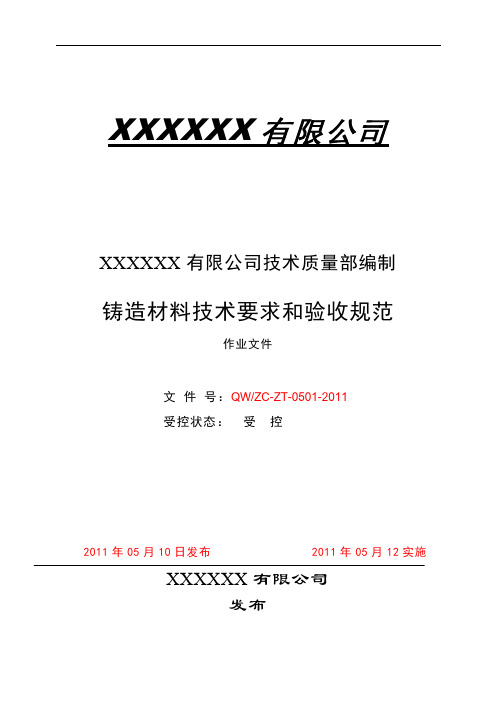
XXXXXX有限公司XXXXXX有限公司技术质量部编制铸造材料技术要求和验收规范作业文件文件号:QW/ZC-ZT-0501-2011受控状态:受控2011年05月10日发布 2011年05月12实施XXXXXX有限公司发布1.目的规范众鑫机械公司主要铸造原材料的各项技术要求及原材料进厂检验标准2.范围适用于铸造、熔化等材料的验收。
3. 技术要求和验收规范3.1生铁3.1.1铸造用生铁技术条件a)各种牌号的生铁应符合表1的规定。
b)各牌号生铁应铸成5±2kg小块,而大于7kg和小于2kg的铁块其重量之和不超过总重量的10%,最大长度不超过220 mm,质量不大于10 kg。
表1 铸造用生铁(GB/T 718—2005)c)铸铁块表面应洁净,不得有炉渣和砂粒,但允许有石灰和石墨。
d)铸铁生铁应做含碳量的分析,但其结果不作考核依据。
e)生铁中钛、砷、铅、铋、锑等微量元素含量的总和不得超过0.12%。
3.1.2生铁验收规范3.1.2.1生铁的验收应凭供方质量合格证明和本公司理化部门的成分化验单进行验收,硅、锰、硫、磷均作为验收指标,含碳量也应化验,但不作为验收指标。
如化学成分不符合要求,要做退货处理或请示主管领导批准让步接收处理。
3.1.2.2化验取样方法a)验证试样的代表批量以供方来货生铁重量为批。
b)从生铁堆上取样时,按批量大小在铁堆上均匀分布若干个取样部位,每个部位采取完整的一块生铁作为一个试样。
具体取样份数,按下列原则确定:小于30t取三块,30~100t每增加10t多取一块。
c)无论取几个样块进行化验,化验结果应符合同一个铁号及相同的化学成分,有一个样块不合格,应视为整批不合格,要做退货处理或请示主管领导批准让步接收处理。
3.1.2.3化验方法1.硅的测定:草酸-硫酸亚铁硅钼蓝光度法2.锰的测定:过硫酸铵氧化光度法3.磷的测定:铋磷钼蓝光度法4.碳的测定:气体容量法5.硫的测定:碘酸钾容量法3.2废钢3.2.1范围:适用于电炉熔炼铸铁调整成分用碳素废钢3.2.2废钢技术条件a)废钢应是45号钢以下的普通碳素钢,其化学成分(%)应符合下列要求:C:≤0.45; Si:0.01~0.6; Mn:≤1.60; p:≤0.045; S:≤0.04 Cr: ≤0.06; Ti:≤0.06;铝<0.8% Mo、Ni不作为验收合格条件,但必须化验用于指导生产;球铁用:Mn:≤0.60,灰铁用:Mn:≤1.60b)废钢中不允许混有高锰钢、轴承钢、不锈钢、硅钢片,灰口、白口铸铁和球铁。
铸件通用技术要求

铸件通用技术要求
铸件表面上不允许有冷隔、裂纹、缩孔和穿透性缺陷及严重的残缺类缺陷(如欠铸、机械损伤等)。
铸件应清理干净,不得有毛刺、飞边,非加工表明上的浇冒口应清理与铸件表面齐平。
铸件非加工表面上的铸字和标志应清晰可辨,位置和字体应符合图样要求。
铸件非加工表面的粗糙度,砂型铸造R,不大于50μm。
铸件应清除浇冒口、飞刺等。
非加工表面上的浇冒口残留量要铲平、磨光,达到表面质量要求。
铸件上的型砂、芯砂和芯骨应清除干净。
铸件有倾斜的部位、其尺寸公差带应沿倾斜面对称配置。
铸件上的型砂、芯砂、芯骨、多肉、粘沙等应铲磨平整,清理干净。
对错型、凸台铸偏等应予以修正,达到圆滑过渡,一保证外观质量。
铸件非加工表面的皱褶,深度小于2mm,间距应大于100mm。
机器产品铸件的非加工表面均需喷丸处理或滚筒处理,达到清洁度Sa2 1/2级的要求。
铸件必须进行水韧处理。
铸件表面应平整,浇口、毛刺、粘砂等应清除干净。
1、铸件必须符合通用技术条件JB/T5000.6-1998的规定进行,尺寸公差C级,行为公差G 级
2、铸件不得有影响强度及外观的缺陷,要求进行探伤处理,安装受力处重点探伤,探伤按JB/T5000.14中Ⅲ级质量等级验收
3、铸件应进行正火处理消除内应力,然后进行机加工,铸件正火处理硬度169-217HB
4、调质处理241-286HB
5、所有油路必须仔细清洗
6、未注圆角R10-R15
7、棱角倒钝,未注倒角C2
8、各加工孔对称位置的偏差不大于0.2m。
铸造材料技术要求和验收规范
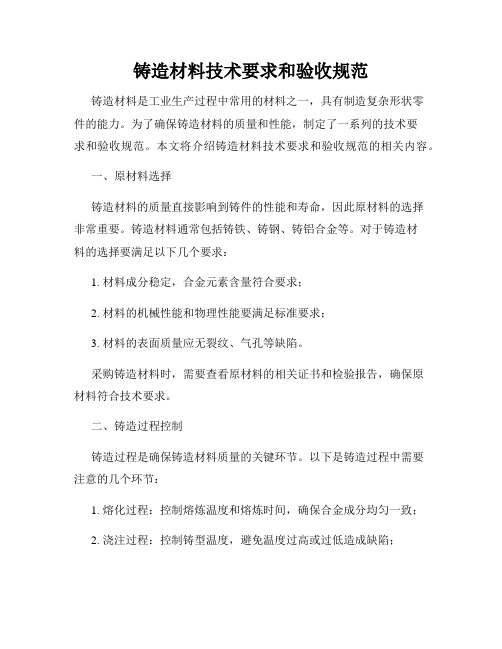
铸造材料技术要求和验收规范铸造材料是工业生产过程中常用的材料之一,具有制造复杂形状零件的能力。
为了确保铸造材料的质量和性能,制定了一系列的技术要求和验收规范。
本文将介绍铸造材料技术要求和验收规范的相关内容。
一、原材料选择铸造材料的质量直接影响到铸件的性能和寿命,因此原材料的选择非常重要。
铸造材料通常包括铸铁、铸钢、铸铝合金等。
对于铸造材料的选择要满足以下几个要求:1. 材料成分稳定,合金元素含量符合要求;2. 材料的机械性能和物理性能要满足标准要求;3. 材料的表面质量应无裂纹、气孔等缺陷。
采购铸造材料时,需要查看原材料的相关证书和检验报告,确保原材料符合技术要求。
二、铸造过程控制铸造过程是确保铸造材料质量的关键环节。
以下是铸造过程中需要注意的几个环节:1. 熔化过程:控制熔炼温度和熔炼时间,确保合金成分均匀一致;2. 浇注过程:控制铸型温度,避免温度过高或过低造成缺陷;3. 热处理过程:根据不同的铸造材料,进行适当的热处理,提高材料的性能;4. 温度控制:铸造材料的温度对最终产品的性能影响很大,需要控制好铸造温度。
三、铸造材料的质量检验铸造材料的质量检验是保证产品质量的重要环节。
以下是一些常见的铸造材料的质量检验方法:1. 成分分析:通过化学分析仪器来检测铸造材料的合金成分,以确保其符合标准要求;2. 金相检验:利用金相显微镜观察铸造材料的显微组织,评估其组织性能;3. 机械性能测试:通过拉伸试验、冲击试验等方法来测试铸造材料的力学性能;4. 铸件表面检查:观察铸件表面是否存在缺陷、夹杂物等;根据不同的铸造材料,可以选择相应的检验方法来确保铸造材料质量。
四、验收规范为了确保铸造材料的质量,制定了一系列的验收规范。
以下是一些常见的验收规范要求:1. 材料的外观质量:表面应无裂纹、气孔、夹杂物等缺陷;2. 成分符合要求:合金成分应符合设计要求,不得低于或高于标准限制;3. 机械性能:铸造材料的抗拉强度、屈服强度、伸长率等力学性能应符合标准;4. 金相组织:铸造材料的金相组织应均匀细致,不得存在夹杂物和非金属夹杂。
大型铸件铸造及验收规程

大型铸件铸造及验收规程1.适用供应商按图制作的大型浇铸件,如G20MN5等。
2.制做2.1 制做以及试验·检验工序铸造方案/模型/ ————模型检验造型(附带机械性能试样的造型)/熔炼/ ————化学成分分析浇铸/砂中缓冷/脱箱·清砂/退火(A)/割断冒口/正火·回火(NT)/ ————机械性能试验(参考)铸后处理/ ————尺寸检验(DT)、外观检验(VT)、超声波探伤(UT) / ————磁粉探伤(MT)或渗透探伤(PT)挖缺陷·打磨/ ————打磨部再检验(MT或PT)焊补/ ————焊补处MT或PT(如有必要UT)除应力退火(SR)/—————机械性能试验Scale off/粗加工/—————DT、VT、UT、MT或PT去除缺陷/—————去除缺陷检验MT或PT焊补/——————焊补处MT或PT(如有必要UT)除应力退火(SR)/——————机械性能试验Scale off/——————DT、VT、UT、MT或PT(MH检验员联检)堆焊/———————堆焊部MT或PT(如有必要UT)加工至交货尺寸/———————MT或PT修整/———————DT、VT、UT、MT或PT(MH检验员联检)涂装/发货 2周前提交联检申请2.2 铸造方案(1)制作时注意在拐角部不要出现裂纹。
(2)提高冒口效应,不出现缩孔。
*不使用内冷铁等的填充金属块。
2.3 制作模型(1)按照铸造方案图,使用木材、胶合板、发泡固醇等制作模型。
(2)按照铸造方案图对已完工的模型进行形状、尺寸检验。
2.4 造型(1)按照铸造方案图,制作铸型。
(2)对铸型进行排气。
(3)不使用内冷铁。
(4)铸型必须充分干燥。
2.5 熔炼(1)熔炼在使用能精炼的碱性电炉、碱性平炉、钢包精炼炉等、在调整到规定成分的同时,减少P、S杂质。
(2)熔炼用碎钢要选用P、S含量低、Sn、Cu等杂质含量少的。
2.6 落砂(1) 浇铸结束后,铸型内缓冷到100℃以下方可进行落砂、清砂(喷丸等)工序。
机床铸件技术要求及验收
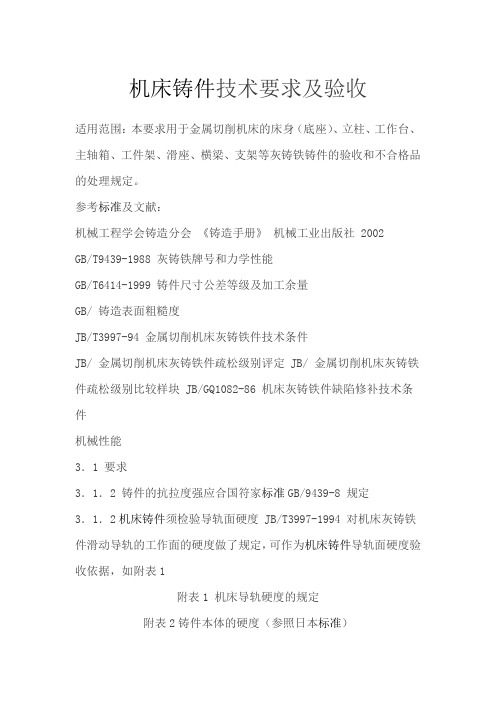
机床铸件技术要求及验收适用范围:本要求用于金属切削机床的床身(底座)、立柱、工作台、主轴箱、工件架、滑座、横梁、支架等灰铸铁铸件的验收和不合格品的处理规定。
参考标准及文献:机械工程学会铸造分会《铸造手册》机械工业出版社 2002GB/T9439-1988 灰铸铁牌号和力学性能GB/T6414-1999 铸件尺寸公差等级及加工余量GB/ 铸造表面粗糙度JB/T3997-94 金属切削机床灰铸铁件技术条件JB/ 金属切削机床灰铸铁件疏松级别评定 JB/ 金属切削机床灰铸铁件疏松级别比较样块 JB/GQ1082-86 机床灰铸铁件缺陷修补技术条件机械性能3.1 要求3.1.2 铸件的抗拉度强应合国符家标准GB/9439-8 规定3.1.2机床铸件须检验导轨面硬度 JB/T3997-1994 对机床灰铸铁件滑动导轨的工作面的硬度做了规定,可作为机床铸件导轨面硬度验收依据,如附表1附表1 机床导轨硬度的规定附表2铸件本体的硬度(参照日本标准)注:1,当导轨厚度大于60mm时,附表1 中的下限值允许降低5HBS。
2,要求表面淬火的导轨,附表1中的下限值应当提高5HBS。
当表面硬度达不到表中要求时,须在设计的许可下,由供需双方协商依据金相组织进行铸件验收。
3.1.3 表面贴塑(或其他耐磨材料)或者不属于滑动摩擦的导轨面,其表面硬度值可依照附表2 中的重要件作为参考。
3.2 检验方法3.2.1 抗拉强度采用Φ30 单铸试棒加工成试样测定。
试样的制作和试验方法应符合GB/9439-88 规定。
3.2.2 硬度的测定直接在铸件导轨面上进行。
导轨长度小于2500 时测定应不少于三点,大于2500 铸件重量大于5吨时应不少于四点。
3.3 检验规则3.3.1 批量划分:根据JB/T3997-94 规定,每包铁水浇注的铸件为一个批量,每批量铸件须提供一组试棒;如同一牌号铁水熔化量大,每包铁水均严格采用一定形式的工艺控制(光谱分析、热分析、及三角试样检验)时,可每炉次同牌号铁水浇一组试棒。
铸件外观质量验收技术条件
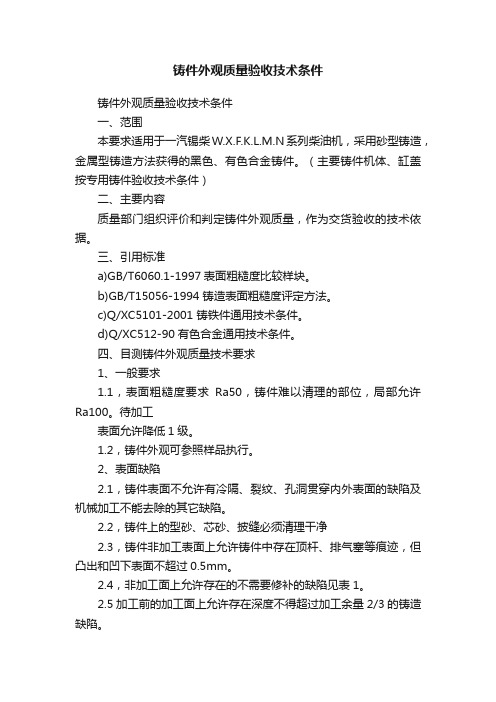
铸件外观质量验收技术条件铸件外观质量验收技术条件一、范围本要求适用于一汽锡柴W.X.F.K.L.M.N系列柴油机,采用砂型铸造,金属型铸造方法获得的黑色、有色合金铸件。
(主要铸件机体、缸盖按专用铸件验收技术条件)二、主要内容质量部门组织评价和判定铸件外观质量,作为交货验收的技术依据。
三、引用标准a)GB/T6060.1-1997表面粗糙度比较样块。
b)GB/T15056-1994 铸造表面粗糙度评定方法。
c)Q/XC5101-2001 铸铁件通用技术条件。
d)Q/XC512-90有色合金通用技术条件。
四、目测铸件外观质量技术要求1、一般要求1.1,表面粗糙度要求Ra50,铸件难以清理的部位,局部允许Ra100。
待加工表面允许降低1级。
1.2,铸件外观可参照样品执行。
2、表面缺陷2.1,铸件表面不允许有冷隔、裂纹、孔洞贯穿内外表面的缺陷及机械加工不能去除的其它缺陷。
2.2,铸件上的型砂、芯砂、披缝必须清理干净2.3,铸件非加工表面上允许铸件中存在顶杆、排气塞等痕迹,但凸出和凹下表面不超过0.5mm。
2.4,非加工面上允许存在的不需要修补的缺陷见表1。
2.5 加工前的加工面上允许存在深度不得超过加工余量2/3的铸造缺陷。
2.6 加工后的加工面上允许存在ф≤1mm,深度<1mm的单个孔洞的铸造缺陷。
3、浇冒口残根3.1,需加工的表面上的浇冒口残根高度允许≤1mm。
3.2,非加工表面的浇冒口残根可以高于非加工表面,但高度不得超过0.5mm,同时不得影响机加工时的定位基准。
4、铸件的错型值铸件分型面处最大错型值≤0.8mm。
铸件各表面突起的分型线,或者与铸件表面圆滑过渡,或者突出高度小件不超过0.5mm, 中、大件不超过0.8 mm,分型面上的飞边不应有锋利锐边,以免引起人身伤害。
5、铸件缺陷的修补铸件缺陷的修补按有关技术条件执行,修补后的`铸件不得有渗漏和影响外观质量的缺陷。
6、铸件表面的防锈处理6.1,铸件表面须经过防锈处理,保证在铸件进入面加工时不得有任何的锈蚀。
铸件外观质量验收规程

铸件表面质量验收规程编制:审核:批准目录1、目的 (2)2、适用范围 (3)3、引用标准 (3)4、验收方案及检验频次 (3)5、验收项目及标准 (3)5.1铸件表面缺陷的检验 (3)5.1.1表面缺陷检验一般要求 (3)5.1.2铸件外观质量等级 (4)5.1.3检验方法 (5)5.2 铸件尺寸的检验 (5)5.2.1铸件毛坯尺寸公差 (5)5.2.6铸件尺寸检验的规范 (8)5.2.7铸件尺寸的检验方法 (9)5.3 铸件重量检验 (9)5.4 表面粗糙度检验 (9)5.5 表面清理质量检验 (11)6、其他验收要求 (11)1、目的为加强本公司对外协铸件的质量控制,保证本公司产品的外观质量及加工性能,特制订铸件表面质量验收规程。
2、适用范围本规范适用于公司所有采用砂型铸造,黑色和有色合金铸件的外观质量验收,包括表面缺陷、尺寸精度、重量偏差、表面粗糙度的验收。
3、引用标准(1)JB/T 5000.4-2007重型机械通用技术条件第4部分铸铁件(2)JB/T 5000.6-2007重型机械通用技术条件第6部分铸钢件(3)GB6414-1999 铸件尺寸公差与机械加工余量(4)GB/T6060.1-1997 表面粗糙度比较样块。
(5)GB/T15056-1994 铸造表面粗糙度评定方法。
(6) Q/XC5101-2001 铸铁件通用技术条件。
(7) Q/XC512-90 有色合金通用技术条件。
4、验收方案及检验频次4.1表面缺陷项目为全检项,样件首检和批量供货,均要进行逐个检验,检验频次为100%。
4.2关键尺寸实行100%全检,非关键尺寸抽检10%。
4.4重量偏差与表面粗糙度的验收根据具体技术要求执行,无要求时可不做检验。
5、验收项目及标准铸件的表面质量主要包括铸件的表面缺陷、尺寸精度、重量偏差、形状偏差、表面粗糙度和铸件表面清理质量等。
5.1铸件表面缺陷的检验5.1.1表面缺陷检验一般要求(1)铸件非加工表面上的浇冒口应尽可能清理得与铸件表面同样平整,加工面上的浇冒口残留量应符合技术要求,若无要求,则按表8执行。
铸件表面质量提升验收技术条件

铸件表面质量提升验收技术条件1范围本文件规定了铸件分类、目测铸件技术要求、检验规则。
本标准适用于中国一拖集团有限公司内/外供方采用砂型铸造,金属型铸造方法获得的黑色、有色合金铸件产品。
2规范性引用文件下列文件对于本文件的应用是必不可少的。
凡是注日期的引用文件,仅所注日期的版本适用于本文件。
凡是不注日期的引用文件,其最新版本(包括所有的修改单)适用于本文件。
GB/T 6060.1—1997 表面粗糙度比较样块铸造表面GB/T 15056—1994 铸造表面粗糙度评定方法Q/YT 014.2-2009 图样通用技术要求Q/YT 022.4—2011 砂型机器造型铸件尺寸公差Q/YT 022.10—2011 铸铁件机械加工余量Q/YT 303.1-2011 球墨铸铁件验收技术条件Q/YT 303.2-2011 灰铸铁件验收技术条件Q/YT 303.3-2011 铸造碳钢件验收技术条件Q/YT 303.5-2011 铝合金铸件验收技术条件Q/YT 303.6-2011 高锰钢履带板验收技术条件Q/YT 303.7-2011 铜合金铸件验收技术条件Q/YT 303.9-2011 硅锰钢履带板验收技术条件3铸件分类铸件根据其所处安装位置、工作条件及表面是否加工分三类,其定义和检验项目见表1。
表1 铸件分类4目测铸件技术要求4.1一般要求4.1.1砂型铸造全部外露件和部分外露件表面粗糙度要求Ra25~Ra50。
金属铸造和有色件表面粗糙度要求Ra25,待加工表面允许降低一级。
4.1.2铸件表面不得有影响零件强度、密封性能及严重影响外观的缺陷。
4.1.3铸件采购、质量检查和供方可在保证铸件满足铸件验收技术条件的前提下,鼓励三方协商建立铸件外观质量标杆样件(即合格的最低标准实物)库,便于铸件外观质量验收参照标杆样件执行,低于此实物标准时为不合格。
4.2灰铸铁件及碳钢铸件4.2.1表面缺陷4.2.1.1铸件表面不允许有冷隔、裂纹、孔洞贯穿内外表面的缺陷及机械加工不能去除的其它缺陷。
- 1、下载文档前请自行甄别文档内容的完整性,平台不提供额外的编辑、内容补充、找答案等附加服务。
- 2、"仅部分预览"的文档,不可在线预览部分如存在完整性等问题,可反馈申请退款(可完整预览的文档不适用该条件!)。
- 3、如文档侵犯您的权益,请联系客服反馈,我们会尽快为您处理(人工客服工作时间:9:00-18:30)。
机床铸件技术要求及验收适用范围:本要求用于金属切削机床的床身(底座)、立柱、工作台、主轴箱、工件架、滑座、横梁、支架等灰铸铁铸件的验收和不合格品的处理规定。
参考标准及文献:机械工程学会铸造分会《铸造手册》机械工业出版社2002 GB/T9439-1988 灰铸铁牌号和力学性能GB/T6414-1999 铸件尺寸公差等级及加工余量GB/T6060.1-1997 铸造表面粗糙度JB/T3997-94 金属切削机床灰铸铁件技术条件JB/T7134.1-93 金属切削机床灰铸铁件疏松级别评定JB/T7134.2-93 金属切削机床灰铸铁件疏松级别比较样块JB/GQ1082-86 机床灰铸铁件缺陷修补技术条件机械性能3.1 要求3.1.2 铸件的抗拉度强应合国符家标准GB/9439-8 规定3.1.2机床铸件须检验导轨面硬度 JB/T3997-1994 对机床灰铸铁件滑动导轨的工作面的硬度做了规定,可作为机床铸件导轨面硬度验收依据,如附表1附表1 机床导轨硬度的规定附表2铸件本体的硬度(参照日本标准)注:1,当导轨厚度大于60mm时,附表1 中的下限值允许降低5HBS。
2,要求表面淬火的导轨,附表1中的下限值应当提高5HBS。
当表面硬度达不到表中要求时,须在设计的许可下,由供需双方协商依据金相组织进行铸件验收。
3.1.3 表面贴塑(或其他耐磨材料)或者不属于滑动摩擦的导轨面,其表面硬度值可依照附表2 中的重要件作为参考。
3.2 检验方法3.2.1 抗拉强度采用Φ30 单铸试棒加工成试样测定。
试样的制作和试验方法应符合GB/9439-88 规定。
3.2.2 硬度的测定直接在铸件导轨面上进行。
导轨长度小于2500 时测定应不少于三点,大于2500 铸件重量大于5吨时应不少于四点。
3.3 检验规则3.3.1 批量划分:根据JB/T3997-94 规定,每包铁水浇注的铸件为一个批量,每批量铸件须提供一组试棒;如同一牌号铁水熔化量大,每包铁水均严格采用一定形式的工艺控制(光谱分析、热分析、及三角试样检验)时,可每炉次同牌号铁水浇一组试棒。
每组试棒共四根(抗拉强度试验一根,金相组织化学成分分析一根,两根备用)。
3.3.2 试验有效性抗拉强度试验有下列情况使得试验结果不符合要求时,则该试验无效,应重新试验A.试样在试验机上安装不当或试验机操作不当。
B.试样有铸造缺陷或试样切削加工不当。
C.试样断口在平行段外。
D.试样拉断后断口上有铸造缺陷。
硬度试验有下列情况使得测试结果不符合要求时,该次测试无效,应重新测试。
A.硬度计操作不当。
B.铸件测定处有缺陷。
3.4 检验结果的评定和复检3.4.1 抗拉强度检验时,JB/T3997-94 规定:先用一根试样进行试验,如果满足GB/T9439-1988 中的要求,则该批铸件合格。
若试验结果达不到要求,且又不属于3.3.2 中的原因时。
可从同一批试样中另取两根进行复检。
若结果都达到要求,则该批铸件判定合格。
3.4.2 硬度试验时先在测试一组硬度值,如果满足 JB/T3997-94 中对硬度的要求,则该铸件合格,若不符合要求,且不是由于3.3.2 中原因引起时,可在不合格测试点附近再测两点硬度,若都符合要求,则铸件合格。
如有一点仍不符合要求,则该铸件不合格。
4.金相组织4.1 要求4.1.1 在设计图样、技术文件或技术协议中规定须检验铸件金相组织的,必须检验金相组织,检验结果应当符合图样、技术文件或技术协议的要求。
4.1.2 如果导轨面须淬火,其金相组织应满足相关标准的要求。
4.1.1JB/T3997-94 规定:机床铸件导轨表面的金相组织不作为判定铸件是否合格的依据,但一般应该控制在如附表3 的范围:附表35.形状尺寸5.1 验收要求5.1.1机床铸件的形状尺寸应符合设计图纸和国家标准(GB/T6414-1999)的要求。
除设计图纸特殊规定的公差外,外观主要尺寸的公差按照 GB/T6414-1999 中规定的不低于 CT9 级验收;内腔尺寸按 CT10~13 验收或者另行规定;其他未涉及的有特殊要求的尺寸由铸造生产部门与设计部门协商规定。
5.1.2 壁厚尺寸:需要对铸件壁厚检验时可参照如下原则:(1),不受力内腔壁厚和肋厚,须满足CT10~12 级标准。
(2),铸件外围壁厚,普通机床铸件的外壁壁厚应满足CT10~12 级标准;对强度和刚性有较高要求的铸件,须满足CT9~11 级标准,但小于设计壁厚的部分不得超过总数的三分之一。
(3),对用于零件安装、强支撑等受力处铸件壁厚应不小于设计壁厚。
(4),当铸件壁厚大于设计壁厚时不得影响零件的其他性能。
5.1.3 加工余量:a,图样、工艺文件或技术协议对机械加工余量有要求的,应该按照图样、工艺文件或技术协议的要求执行;b,参照国家标准GB/T6414-1999 的规定,铸件毛坯不粗加工面的加工余量在没有特殊规定时应满足等级H,经过粗加工后表面留有余量应为3~6 ;c,在铸造工艺不易控制或者加工时有特殊要求的地方,加工余量由加工车间(工艺)和铸造厂商定,但原则上不应大于155.1.4铸件错型:铸件错型量应当控制在公差范围内,外露非加工面产生错型后,应修磨成不大于10的斜坡面。
5.2 检验方式方法5.2.1 铸件尺寸检验采用划线检测方法,由于设备及操作手段等原因无法划线检测的尺寸,可采用手工测量,但测量的量具和方法必须符合要求,测量结果作为参考,重要尺寸须经加工、装配检验。
检测依据是铸件图(铸造工艺图)。
5.2.2 全尺寸检验:新产品首件铸件和必须全尺寸检验;模型大修后上场生产的首件铸件须全尺寸检验;批量生产超过50 件后再生产的铸件须全尺寸检验;5.2.3 重要尺寸、控制尺寸检验:铸件每批次投料首件(5.2.2 规定除外)须检验;设计对局部进行设计更改与铸件毛坯有关的尺寸更改后生产的铸件应检测;工艺技术部门和质量管理部门特别要求须检验的。
5.2.4 用于加工用的划线检测:铸造生产厂要对铸件进行粗加工的铸件,必须划线划出铸件粗加工部分的尺寸线;和客户有技术合同要求的,须划出加工尺寸线。
5.2.5 分析性检测:加工和安装时反馈有问题的尺寸应进行分析检测;技术部门出于分析控制质量提出的尺寸分析检测。
5.3 尺寸检测结果评定5.3.1 尺寸检测结果全部符合工艺图纸要求,公差满足标准规定,则可判定铸件合格。
5.3.2 检测结果部分尺寸不符合工艺图纸要求,须由技术人员进行判定,判定时必须与设计沟通,确认需判定尺寸的性质(属非重要尺寸、重要尺寸还是关键尺寸)。
A.非重要尺寸不符合工艺图纸要求,公差不满足标准要求时,在不影响铸件使用性能的情况下铸件可以使用。
但铸造生产厂应拿出整改措施进行改进。
B.重要尺寸不符合工艺图纸要求,公差不满足标准要求时,铸件应判定为不合格。
铸造技术部门或质量管理部门应同设计协商,通报尺寸超差情况,判定该铸件是否报废、返修或回用。
如可以返修,须共同商定返修措施。
铸造厂必须拿出整改措施进行改进。
C.关键尺寸不符合工艺图纸要求,公差不满足标准要求时,原则上铸件应判定为报废。
如普通机床铸件确需要返修或回用,应会同产品设计、铸造技术质量主管领导、加工车间共同商定铸件挽救措施。
铸造厂必须拿出整改措施进行改进。
6.铸件表面质量6.1 要求6.1.1 铸件上的残砂、粘结物和芯骨应清理干净。
浇冒口、披缝、毛刺应清除。
多肉等应当打磨。
6.1.2 铸件的油池、油箱及油道部位不得留有粘砂和阻塞油路的披缝、毛刺等。
6.1.3 交验铸件在非加工面上的浇冒口和披缝、毛刺允许突出不大于2 。
加工面允许留有少量残根。
铸件内腔披缝允许残留突出不大于5 。
如铸件无法清理到的地方允许有少量披缝残留(5.1.2 中的情况除 21 外),但是不得影响零件的装配、穿线、起吊等使用性能。
6.1.4 铸件的表面粗造度:JB/T3997-94 规定机床铸件表面粗造度应符合附表4 的规定:附表4 铸件表面粗造度注:铸件内腔非主要表面和加工表面的粗造度允许放宽一级验收。
6.1.5 粘砂:铸件外表面、油池、油箱、油道的粘砂必须清除干净,活动部件的内腔也不得有残留粘砂。
非活动部件内腔如确实无法清理,在确定粘砂不会脱落的情况下,允许不做清理,铸件作回用处理。
6.1.6 油漆:铸件不加工表面,应在除锈和内外清理干净后涂防锈底漆,底漆应喷涂均匀,不应有起皱、堆积、流挂、露底、脱落等现象。
6.2 检验方法6.1.1 铸件表面质量检验通常采用目视检验,如内腔无法观察,可用内窥镜检查。
6.1.2 铸件表面粗造度的检查,如需要可参照GB/T6060.1-1997 规定,采用比较样块对比评定铸件的表面7.铸造缺陷7.1 要求7.1.1 加工表面7.1.1.1机床铸件的加工表面不允许存在空洞类、夹杂类和残缺类缺陷。
其它类型的缺陷根据铸件的使用性能另规定。
导轨、工作台面、滑动轴承孔等重要面还不能有裂纹、组织异常等缺陷。
疏松等级符合7.1.1.2 要求。
7.1.1.2机床铸件加工面疏松等级要求按照 JB/T7134.1-93 评定。
如附表5,疏松级别比较样块的对照评定参照JB/T7134.2-93 执行。
附表5 铸件疏松级别的允许范围7.1.1.3如缺陷不满足技术要求,可参照缺陷修补要求进行修补。
7.1.2 非加工表面7.1.2.1 铸件外表面在不影响性能和外观的情况下,允许存在Φ5 以下、深度不大于2 、每300*300不多于10处的气孔、砂孔、渣孔等孔洞类缺陷。
不符合此要求时,铸件应当按照相关的修补要求进行修补。
7.1.2.2 铸件内腔非加工面部分的缺陷不作具体的要求,但是必须符合下列条件:A,对粘砂缺陷应符合6.1 的要求。
B,内腔缺陷应不影响铸件的强度刚性及装配安装等使用性能。
C,铸件内腔油箱(油池)、油路不得有引起油(水)渗漏得缺陷。
8.缺陷修补8.1 修补的对象指铸件经验收不合格允许或要求返修的铸件,铸件常用的修补方式包括塞补、镶套、焊补、填补。
8.2 1JB/GQn1082-86 规定了铸件的塞补规范,质量大于 1000 或长度大于 1000 的大型机床铸件,如果导轨表面存在气孔、砂孔、渣孔,可用灰铸铁嵌入物塞堵。
多个塞子塞补时每个塞子的尺寸应不大于导轨宽度方向尺寸的四分之一,塞子相邻间距不小于其尺寸的5倍。
8.2.2其他重要加工面上缺陷的塞补参照导轨面规定。
一般加工面可以适当放宽。
8.2.3 非加工面一般不采用塞补方式修补缺陷。
8.3 镶套8.3.1在个别情况下,铸件的圆孔内加工后发现有气孔、缩孔、渣孔及孔径偏等缺陷时,在不影响装配机床性能的情况,可适当将铸件圆孔适当扩大后镶入套筒 8.3.2 镶入套筒的内径应符合附表6 的规定:附表6 套筒壁厚套筒的最小壁厚 1015 套筒与孔的的配合应符合H7/n6 或H7/p6 的要求。