我国钒钛磁铁矿直接还原分析
钛磁铁矿直接还原——磁选钛铁分离主要影响因素探析
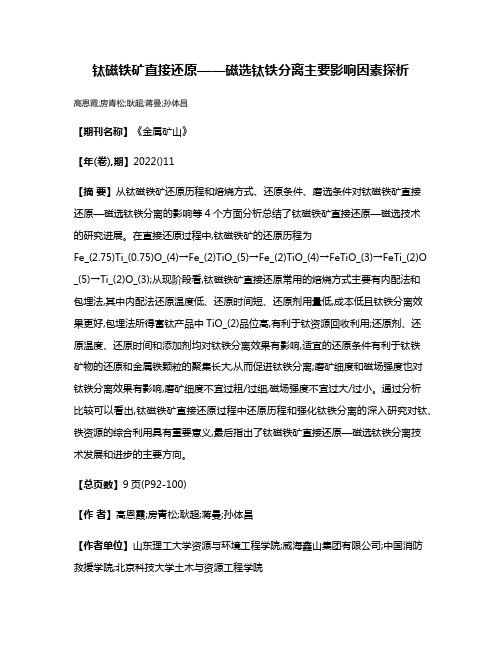
钛磁铁矿直接还原——磁选钛铁分离主要影响因素探析高恩霞;房青松;耿超;蒋曼;孙体昌【期刊名称】《金属矿山》【年(卷),期】2022()11【摘要】从钛磁铁矿还原历程和焙烧方式、还原条件、磨选条件对钛磁铁矿直接还原—磁选钛铁分离的影响等4个方面分析总结了钛磁铁矿直接还原—磁选技术的研究进展。
在直接还原过程中,钛磁铁矿的还原历程为Fe_(2.75)Ti_(0.75)O_(4)→Fe_(2)TiO_(5)→Fe_(2)TiO_(4)→FeTiO_(3)→FeTi_(2)O _(5)→Ti_(2)O_(3);从现阶段看,钛磁铁矿直接还原常用的焙烧方式主要有内配法和包埋法,其中内配法还原温度低、还原时间短、还原剂用量低,成本低且钛铁分离效果更好,包埋法所得富钛产品中TiO_(2)品位高,有利于钛资源回收利用;还原剂、还原温度、还原时间和添加剂均对钛铁分离效果有影响,适宜的还原条件有利于钛铁矿物的还原和金属铁颗粒的聚集长大,从而促进钛铁分离;磨矿细度和磁场强度也对钛铁分离效果有影响,磨矿细度不宜过粗/过细,磁场强度不宜过大/过小。
通过分析比较可以看出,钛磁铁矿直接还原过程中还原历程和强化钛铁分离的深入研究对钛、铁资源的综合利用具有重要意义,最后指出了钛磁铁矿直接还原—磁选钛铁分离技术发展和进步的主要方向。
【总页数】9页(P92-100)【作者】高恩霞;房青松;耿超;蒋曼;孙体昌【作者单位】山东理工大学资源与环境工程学院;威海鑫山集团有限公司;中国消防救援学院;北京科技大学土木与资源工程学院【正文语种】中文【中图分类】TD95;TF55【相关文献】1.添加剂对海滨钛磁铁矿直接还原磁选钛铁分离的影响2.煤泥作还原剂对海滨钛磁铁矿直接还原焙烧磁选的影响3.煤种对钛磁铁矿直接还原-磁选钛铁分离的影响4.还原剂种类对钛磁铁矿直接还原—磁选制备钛酸镁的影响5.CaO对海滨钛磁铁矿精矿直接还原-磁选工艺中还原气氛的影响因版权原因,仅展示原文概要,查看原文内容请购买。
直接还原炼铁工艺现状及攀枝花钒钛磁铁矿处理工艺选择
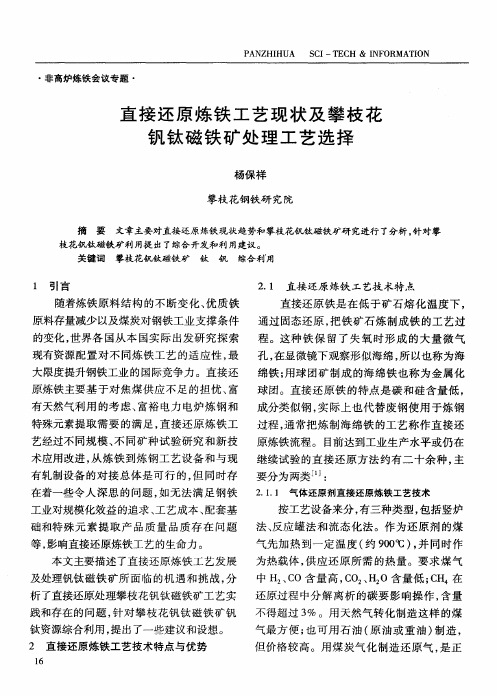
但价格 较高 。用 煤炭气 化制造 还原气 , 是正
第3 5卷
第 4期
攀 枝 花科技 与信 息
( 第 13期 ) 总 0
在 研 究 的课 题 。
排料 , 因此不 怕炉 料粘结 , 操作 温度 较高 , 虽 系 间断作 业 , 产率并 不 低。缺点 是煤 气 利 生
用 差 , 耗 达 ( 34X16千 卡/ )产 品 质 热 达 . 0 吨 , 量 不 均 匀 。 H l海 绵 铁 含 碳 高 ( . % ~ y 12
原炼 铁 主 要 基 于 对 焦 煤 供 应 不 足 的 担 忧 、 富
球团。直接 还原 铁 的特点 是碳 和硅含 量低 ,
有天然气利用 的考虑 、 富裕 电力 电炉炼 钢 和 成分类似钢 , 际上也代替 废钢使 用 于炼 钢 实 特殊元素提取需 要 的满足 , 直接 还原炼 铁工 过程 , 通常把炼 制 海绵铁 的工艺称 作直 接还 艺经过不 同规模 、 同矿 种试验研究 和新 技 原炼铁流程。 目前达到工业生产水平或仍 在 不 术应用改进 , 从炼铁 到炼 钢工艺设备 和 与现 继续试验 的直 接还原 方法 约有二 十余 种 , 主 有轧制设备 的对接 总体是 可行 的, 同时存 要分 为两 类 … : 但
经过预热 、 还原及 冷 却 三个 阶段 。还 原所 得
的 Hy 法 已放弃 四个 反应罐 , l 改用 一个反 应
接近 Mirx法 。 de 的海绵铁 , 却 到 5  ̄ 排 出炉外 , 防再 罐 , 冷 0 C后 以 流态化法 : 流化床 中用煤 气 还原 铁 矿 在 氧化 。还原煤气用 天然气及 竖炉本身 的一部
P ANZ HUA HI
SCI—T ECH & I NF0RMA I rON
直接还原铁工艺技术的对比分析论述

直接还原铁工艺技术的对比分析论述张建国【期刊名称】《资源再生》【年(卷),期】2018(000)002【总页数】5页(P57-61)【作者】张建国【作者单位】北京瀚川鑫冶工程技术有限公司【正文语种】中文在低于矿石融化状态下,通过固态还原,把铁矿石炼制成铁的工艺称作直接还原法,用这种方法生产出的铁也叫作直接还原铁(DRI),由于这种铁保留了失去氧时形成的大量微小气孔,在显微镜下观察形似海绵,所以直接还原铁也称为海绵铁。
直接还原铁是精铁粉在炉内经低温还原形成的低碳多孔状物质,其化学成分稳定,杂质含量少,主要用作电炉炼钢的原料,也可作为转炉炼钢的冷却剂,如果经过二次还原还可供给粉末冶金用。
从上世纪80年代末以来,我国一直宣传推广使用直接还原技术,并对直接还原技术进行了广泛的开发研究,取得了众多成果,为直接还原技术发展奠定了基础。
但是,因铁矿、煤炭、气源等原燃料条件限制,中国直接还原发展的实际成效不大,与钢材、生铁等行业相比还有相当差距。
一、直接还原铁的应用优势直接还原铁生产是指在低于熔化温度之下将铁矿石还原成海绵铁的过程,与传统高炉炼铁方法相比取消了焦炉、烧结等工序,具有流程短、污染小、消耗少,不受炼焦煤短缺影响等优点。
同时海绵铁中硫、磷、硅等有害杂质含量低,有利于电炉冶炼优质纯净钢种。
近年来,由于钢铁产品向小型轻量化、功能高级化、复合化方向发展,因此钢材产品中的非金属材料和有色金属的使用比例在增加,在废钢的破碎分拣过程中,又不能完全有效的剔除非金属和有色金属材料,况且,即使是纯粹完全的黑色废钢料,由于来源不同,化学成分波动也是较大的。
致使加工后的成品入炉废钢的质量很难掌握控制,给电炉炼钢作业带来一定的困难。
如果用一定比例的直接还原铁(30~50%)作为稀释剂与废钢搭配使用,不仅可增加钢的均匀性,还可以改善和提高钢的物理性质,从而达到生产优质钢的目的。
因此,直接还原铁不仅仅是优质废钢的替代品,还是生产优质钢必不可少的高级原料(如天津无缝钢管公司的国外产品设计中就明确要求,必须配置50%的直接还原铁)。
攀枝花钒钛磁铁矿直接还原新工艺流程-攀枝花交流材料

(4)目前,正在开展前期示范生产线放大的可研工作。
转底炉煤基直接还原-电炉熔分冶炼 钒钛磁铁矿新工艺
1、四川龙蟒集团
(1)自2003年起,四川龙蟒集团与攀枝花学院合作研究,进行了大 量钒钛铁精矿生球团制备、转底炉直接还原和电炉熔分工艺试验。
(2)2006-2007年,建成一期7万吨/年示范生产线,进行了3轮工业 性试验。
(3)2008年,进行示范生产线放大,启动了年处理铁精矿20万吨的 二期工程;
攀 枝 花 钒 钛 磁 铁 矿 区 分 布
攀枝花钒钛磁铁矿资源储量
钒钛磁铁矿保有储量
67.3亿吨
钛资源量保有储量
4.28亿吨
钒资源保有储量
1047.86万吨
铬保有储量
696万吨
钴保有储量
152万吨
钪保有储量
23万吨
镓保有储量
21万吨
攀枝花钒钛磁铁矿资源 综合开发利用情况
攀枝花钒钛磁铁矿经过四十多年 的开发,已形成了钒材料、钛材料、 钢铁新材料系列产品。2001年被国 家科技部批准为攀枝花国家新材料 成果转化及产业化基地。2007年新 材料产业实现产值110亿元,成为攀 枝花经济增长的新亮点。
攀枝花---国家新材料成果转化及产业化基地
2001年12月18日,国家科技部批准攀枝花为国家新材 料成果转化及产业化基地,并给予了大力支持。
攀 枝 花 钒 钛 磁 铁 矿 资 源 综 合 开 发 工 艺 流 程 图
钢铁产业
攀枝花钢铁产业作为主导产业,目前已形成年产生铁600多万 吨、钢600多万吨的能力;
1、可全部回收钒钛铁精矿中的钛资源。经转底炉还原后的金 属化球团经过电弧炉熔化分离后,可得到含量为50%以上 的熔分钛渣和含钒生铁,实现铁钒与钛的分离。熔分钛渣 可用于硫酸法钛白生产原料。
电炉熔分工艺处理钒钛磁铁矿

电炉熔分工艺处理钒钛磁铁矿电炉熔分工艺处理钒钛磁铁矿一、引言钒钛磁铁矿是一种重要的钛资源,广泛应用于冶金、化工、建材等领域。
然而,由于其复杂的化学成分和矿物结构,其加工和利用一直面临着挑战。
电炉熔分工艺是一种被广泛采用的处理钒钛磁铁矿的方法。
该方法通过利用电炉的高温和电能,将钒钛磁铁矿矿石在还原气氛下进行熔融和分离,以获得钛铁合金和钒铁合金等有价值的产品。
本文将深入探讨电炉熔分工艺处理钒钛磁铁矿的原理、技术及其在实际应用中的优势和发展前景。
二、电炉熔分工艺的原理及技术(1)原理概述电炉熔分工艺是利用电炉高温和电能的特点,将钒钛磁铁矿在还原条件下进行熔融和分离的过程。
在这个过程中,钒和铁进入钒铁合金,而钛则进入钛铁合金。
这种工艺的基本原理是根据各元素的熔点和还原性能的不同,通过合理的炉内温度和还原气氛控制,实现钒、铁、钛的分离和提取。
(2)技术要点在电炉熔分工艺中,关键的技术要点包括矿石预处理、还原条件控制、温度控制和产物分离等。
矿石预处理是为了提高矿石中有价值元素的回收率和产物质量。
常见的矿石预处理方法包括碎石、磁选和浸出等。
还原条件控制对于熔分工艺的成功与否至关重要。
合理的还原条件能够保证有价值元素的还原率和产物质量。
常用的还原条件包括还原剂种类和用量,还原温度和还原时间等。
温度控制是电炉熔分工艺中一个关键的环节。
适当的温度能够保证矿石充分熔化和元素的分离,同时避免产生不良的副反应。
温度控制的方法包括调整电炉电极的位置和电流强度等。
产物分离是电炉熔分工艺中的一项重要工作。
通过合理的分离装置,将钒铁合金和钛铁合金等产品分离出来,以提高产品质量和价值。
三、电炉熔分工艺的优势和发展前景电炉熔分工艺作为一种兼具深度和广度的处理钒钛磁铁矿的方法,具有以下优势和发展前景。
电炉熔分工艺对于复杂矿石的处理能力强。
由于钒钛磁铁矿的化学成分和矿物结构多样复杂,传统的处理方法存在着诸多限制。
而电炉熔分工艺通过熔融和分离的方式,能够有效地处理各种类型的矿石,实现有价值元素的高效提取。
钒钛磁铁矿精矿钙化焙烧直接提钒研究
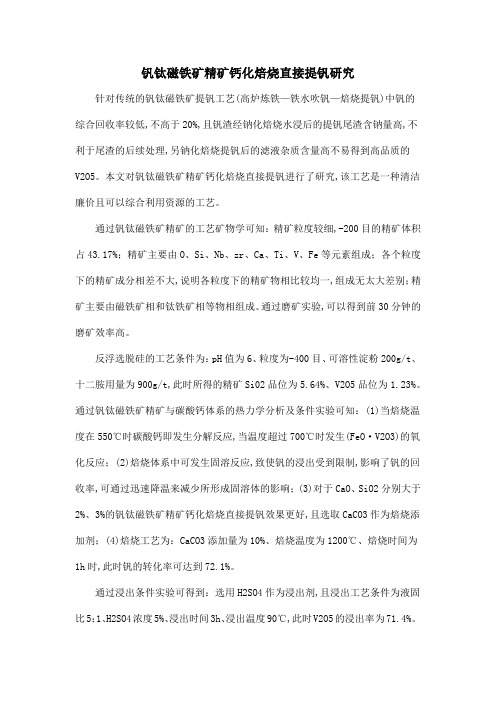
钒钛磁铁矿精矿钙化焙烧直接提钒研究针对传统的钒钛磁铁矿提钒工艺(高炉炼铁—铁水吹钒—焙烧提钒)中钒的综合回收率较低,不高于20%,且钒渣经钠化焙烧水浸后的提钒尾渣含钠量高,不利于尾渣的后续处理,另钠化焙烧提钒后的滤液杂质含量高不易得到高品质的V2O5。
本文对钒钛磁铁矿精矿钙化焙烧直接提钒进行了研究,该工艺是一种清洁廉价且可以综合利用资源的工艺。
通过钒钛磁铁矿精矿的工艺矿物学可知:精矿粒度较细,-200目的精矿体积占43.17%;精矿主要由O、Si、Nb、zr、Ca、Ti、V、Fe等元素组成;各个粒度下的精矿成分相差不大,说明各粒度下的精矿物相比较均一,组成无太大差别;精矿主要由磁铁矿相和钛铁矿相等物相组成。
通过磨矿实验,可以得到前30分钟的磨矿效率高。
反浮选脱硅的工艺条件为:pH值为6、粒度为-400目、可溶性淀粉200g/t、十二胺用量为900g/t,此时所得的精矿Si02品位为5.64%、V2O5品位为1.23%。
通过钒钛磁铁矿精矿与碳酸钙体系的热力学分析及条件实验可知:(1)当焙烧温度在550℃时碳酸钙即发生分解反应,当温度超过700℃时发生(FeO·V2O3)的氧化反应;(2)焙烧体系中可发生固溶反应,致使钒的浸出受到限制,影响了钒的回收率,可通过迅速降温来减少所形成固溶体的影响;(3)对于CaO、SiO2分别大于2%、3%的钒钛磁铁矿精矿钙化焙烧直接提钒效果更好,且选取CaCO3作为焙烧添加剂;(4)焙烧工艺为:CaCO3添加量为10%、焙烧温度为1200℃、焙烧时间为1h时,此时钒的转化率可达到72.1%。
通过浸出条件实验可得到:选用H2SO4作为浸出剂,且浸出工艺条件为液固比5:1、H2SO4浓度5%、浸出时间3h、浸出温度90℃,此时V2O5的浸出率为71.4%。
钒钛铁精矿含碳球团直接还原试验

钒 钛 铁 精 矿 含碳 球 团直 接 还 原 试 验
李俊 翰 , 邱 克 辉 , 杨 绍利
( 1 .成都 理 工 大学, 成都 6 1 0 0 5 9 ;
2 .攀枝 花 学 院 钒 钛 资源 综合 利用 四川 省 重点 实验 室 , 四川攀 枝花 6 1 7 0 0 0 )
摘要 : 采 用 正 交 试 验 和 单 因素 试 验 考 察 还 原 温 度 、 配碳 量 ( n c n o ) 、 还 原 时 间 对 某 钒 钛 磁 铁 矿 精 矿 直 接 还
0 . 4 ,t he me t a l l i z a t i o n r a t e o f r e d uc e d p e l l e t s c a n be i mpr o ve d t o 9 1 . 7 7 ,wi t h p ha s e c o mp os i t i o n of me — t a l l i c i r o n . Ke y wo r ds : v a na d i um a n d t i t a ni u m i r o n c on c e n t r a t e s;r e du c t i on;m e t a l l i z a t i o n r a t e;or t h og o na l e x pe r i me nt s
2 .S i c h u a n Pr ov i nc e Ke y La b o r a t o r y o f Co mp r e he n s i v e Ut i l i z a t i o n f o r Va na d i u m & Ti t a n i u m Re s ou r c e s.
Pa nz h i h ua Uni v e r s i t y,Pa nz h i h ua 6 1 7 0 0 0,Si c h u a n,Ch i n a )
我国煤基直接还原炼铁工艺发展
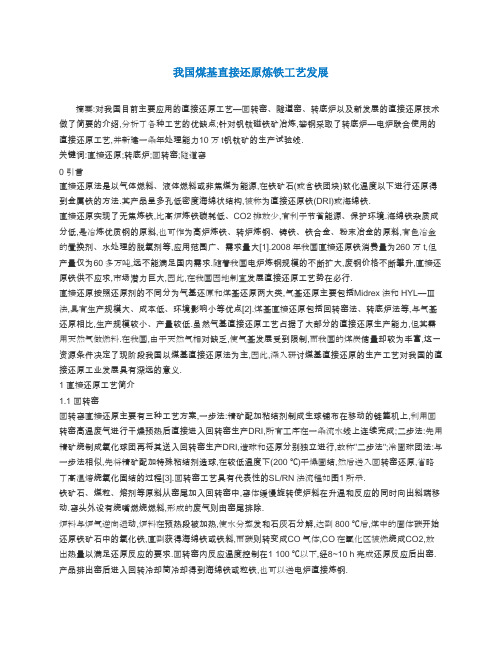
我国煤基直接还原炼铁工艺发展摘要:对我国目前主要应用的直接还原工艺—回转窑、隧道窑、转底炉以及新发展的直接还原技术做了简要的介绍,分析了各种工艺的优缺点;针对钒钛磁铁矿冶炼,攀钢采取了转底炉—电炉联合使用的直接还原工艺,并新建一条年处理能力10万t钒钛矿的生产试验线.关键词:直接还原;转底炉;回转窑;隧道窑0 引言直接还原法是以气体燃料、液体燃料或非焦煤为能源,在铁矿石(或含铁团块)软化温度以下进行还原得到金属铁的方法.其产品呈多孔低密度海绵状结构,被称为直接还原铁(DRI)或海绵铁.直接还原实现了无焦炼铁,比高炉炼铁碳耗低、CO2排放少,有利于节省能源、保护环境.海绵铁杂质成分低,是冶炼优质钢的原料,也可作为高炉炼铁、转炉炼钢、铸铁、铁合金、粉末冶金的原料,有色冶金的置换剂、水处理的脱氧剂等,应用范围广、需求量大[1].2008年我国直接还原铁消费量为260 万t,但产量仅为60多万吨,远不能满足国内需求.随着我国电炉炼钢规模的不断扩大,废钢价格不断攀升,直接还原铁供不应求,市场潜力巨大,因此,在我国因地制宜发展直接还原工艺势在必行.直接还原按照还原剂的不同分为气基还原和煤基还原两大类,气基还原主要包括Midrex法和HYL—Ⅲ法,具有生产规模大、成本低、环境影响小等优点[2].煤基直接还原包括回转窑法、转底炉法等,与气基还原相比,生产规模较小、产量较低.虽然气基直接还原工艺占据了大部分的直接还原生产能力,但其需用天然气做燃料.在我国,由于天然气相对缺乏,使气基发展受到限制,而我国的煤炭储量却较为丰富,这一资源条件决定了现阶段我国以煤基直接还原法为主,因此,深入研讨煤基直接还原的生产工艺对我国的直接还原工业发展具有深远的意义.1 直接还原工艺简介1.1 回转窑回转窑直接还原主要有三种工艺方案,一步法:精矿配加粘结剂制成生球铺布在移动的链篦机上,利用回转窑高温废气进行干燥预热后直接进入回转窑生产DRI,所有工序在一条流水线上连续完成;二步法:先用精矿烧制成氧化球团再将其送入回转窑生产DRI,造球和还原分别独立进行,故称"二步法";冷固球团法:与一步法相似,先将精矿配加特殊粘结剂造球,在较低温度下(200 ℃)干燥固结,然后送入回转窑还原,省略了高温焙烧氧化固结的过程[3].回转窑工艺具有代表性的SL/RN法流程如图1所示.铁矿石、煤粒、熔剂等原料从窑尾加入回转窑中,窑体缓慢旋转使炉料在升温和反应的同时向出料端移动.窑头外设有烧嘴燃烧燃料,形成的废气则由窑尾排除.炉料与炉气逆向运动,炉料在预热段被加热,使水分蒸发和石灰石分解,达到800 ℃后,煤中的固体碳开始还原铁矿石中的氧化铁,直到获得海绵铁或铁料,而碳则转变成CO气体,CO在氧化区被燃烧成CO2,放出热量以满足还原反应的要求.回转窑内反应温度控制在1 100 ℃以下,经8~10 h完成还原反应后出窑.产品排出窑后进入回转冷却筒冷却得到海绵铁或粒铁,也可以送电炉直接炼钢.与高炉工艺相比较,回转窑工艺设备简单,投资少,适用于地方钢铁工业,弥补了高炉—转炉工艺的不足,此外,回转窑还适用于复合矿冶炼,冶金灰尘及各种工业废渣的回收利用,减少环境污染,降低了钢铁生产能耗.同时,回转窑工艺也存在一些缺点,包括窑内结圈、还原温度低(1 100 ℃以下)、流程长、对块矿或球团矿冷强度要求高、要求使用低硫煤等[4].我国山东鲁中矿山公司通过采取提高冷固烧结球团的冷热态强度、加强还原煤的选择和管理、优化回转窑的送风、抛煤、控温温度等措施,预防并降低回转窑结圈,取得了较好的收效.图1 SL/RN法工艺流程1.2 隧道窑隧道窑工艺即将精矿粉、煤粉、石灰石粉,按照一定的比例和装料方法,分别装入还原罐中,然后把罐放在罐车上,推入条形隧道窑中或把罐直接放到环形轮窑中,料罐经预热到1 150 ℃加热焙烧和冷却之后,得到直接还原铁.目前江苏永钢集团拥有两条260 m长煤气隧道窑,为亚洲最长隧道窑.隧道窑生产海绵铁工艺流程如图2所示.图2 隧道窑生产海绵铁工艺流程煤基隧道窑直接还原工艺具有技术成熟、作简单的特点,可因地制宜采用此工艺,利用当地小型分散的铁矿及煤矿资源优势,发展直接还原铁生产,为电炉提供优质原料.但是,总体上讲,我国隧道窑直接还原中存在生产规模较小、能耗高、污染严重、缺乏稳定的原料供应渠道等问题[5],所以,提高机械化程度、改变原料入炉方式、改进燃料及其燃烧、增设余热回收等成为各厂家不断努力改进工艺的方向.我国已建成或正在建设的隧道窑有100多座,约70多个单位规划建设产能5~30 万t/a的隧道窑直接还原铁厂,在不断总结实践经验的基础上,改进现行工艺,开发出诸如大型隧道窑直接还原、AMR—CBI隧道窑直接还原工艺、宽体球状海绵铁隧道窑、L-S快速还原工艺等多种新技术,掀开了隧道窑工艺规模扩大、产能提高、机械及自动化提升的序幕.1.3 转底炉转底炉煤基直接还原是最近几十年间发展起来的炼铁新技术,代表工艺为Fastmet,它由美国Midrex公司与日本神户制钢于20世纪60年发,是采用环形转底炉生产直接还原铁的一种方法.经过多年的半工业性试验和深入的可行性研究,现已完成工艺作参数和装置设计的优化.Fastmelt和ITmk3工艺是在此基础上增加对直接还原铁的处理.图3显示了这三种以转底炉为主体的直接还原工艺流程.图3 转底炉直接还原工艺流程煤粉与铁精粉按比例混匀制成球团,干燥后以1~3层球铺放在转底炉床面,随着炉底的旋转,炉料依次经过预热区、还原区和冷却区.还原区内球团被加热到1 250~1 350 ℃,由于煤粉与铁氧化物紧密接触,铁氧化铁被碳迅速还原成DRI,成品在800~1 000 ℃左右连续从转底炉卸出.球团矿在炉底停留8~30 min,这取决于原料特性、料层厚度及其他因素,成品可作电炉热装炉料或者转炉炉料,也可冷却或生产热压块(HBI).Fastmet工艺技术特点:①在高温敞焰下加热实现快速还原,反应时间只需10~20 min,生产效率高;②原料来源广泛,铁原料方面,除使用高品位粉矿、精矿外,还可用氧化铁皮、代油铁泥、炼钢粉尘、含En、Pb、As等有害杂质的铁矿等;还原剂方面,除煤以外焦末、沥青均可利用,不必担心出现结圈问题;③炉料相对炉底静止,对炉料强度要求不高;④废气中含有大量显热,可用作预热空气、干燥原料等[6]. Fastmelt工艺流程基本与Fastmet一致,只是在后续添加一个熔炉来生产高质量的液态铁水.Itmk3工艺是使金属化球团在转底炉中还原时熔化,生成铁块(Nuggets),同时脉石也熔化,形成渣铁分离.当然转底炉也存在着设备复杂、炉内气氛难控制、传热效率低以及对还原剂硫含量要求严格的缺点.就目前转底炉工艺开发的水平和规模而论,与高炉还有较大差距,但仍存在发展的广阔空间,天津荣程联合钢铁集团已兴建一条100万t级Fastmet生产线,建成目前世界最大的转底炉.另外,用转底炉可处理一些特殊铁矿,如含锌、铅、砷等有害杂质,或含镍、钒、钛等有用元素,均可利用转底炉的工艺优势,或高温挥发,或选择性还原,配合后续工艺,实现资源综合利用.马钢尘泥脱锌转底炉工程项目于2008年5月开工建设,2009年7月6日正式竣工投产,建成了整套转底炉(RHF)脱锌工艺技术装置,不仅解决了含锌尘泥循环利用的后顾之忧,而且将综合利用技术上升到高品质资源化水平.1.4 其他新工艺1.4.1 PF法煤基竖炉直接还原工艺中冶集团北京冶金设备研究设计总院,结合国内情况创新发明了PF法竖炉直接还原工艺.PF法是在吸收K-M法外热式竖炉煤基直接还原工艺的经验基础上,设计的以一种中国特色的罐式还原炉为主反应器的直接还原法.这种工艺技术可靠,技术经济指标在各种煤基直接还原工艺中属先进水平.PF法直接还原工艺流程如图4所示.图4 PF法直接还原工艺流程PF法直接还原工艺主要特点[1]:1)主体设备选用外热式竖炉,预热、还原、冷却三段根据不同的作用和温度选用不同材质和结构,便于传热和化学反应进行,提高热效率和设备寿命.2)原燃料适用性强,对精矿、还原剂和燃料没有特殊要求.3)采用外配碳工艺,还原剂适当过量,扩大了煤的选用范围,造球工艺也因不定量配入煤粉而简化,球团强度较高,DRI质量较好.4)多个反应罐可并列组成任意规模的还原设备,设计和组织生产灵活.1.4.2 低温快速还原新工艺2004年钢铁研究总院提出了低温快速冶金新工艺.新工艺利用纳米晶冶金技术的特点将铁矿的还原温度降低到700 ℃以下.新流程分为气基和煤基两种方法,工艺流程如图5、图6所示.图5 煤基低温快速还原新工艺图6 气基低温快速还原新工艺煤基法使用煤粉为还原剂,在700℃左右快速还原铁精矿粉;气基法使用还原性气体还原铁精矿粉,还原温度可低于600℃.新工艺具有能耗低、环境友好等特点,省去了烧结或造球工艺,缓解了钢铁行业对焦煤的依赖,符合我国国情[7].2 攀钢现状钒钛磁铁矿是攀西地区的特色资源,与普通矿相比,钒钛矿直接还原温度较高、还原时间较长,还原过程产生特有的膨胀粉化现象,因此,存在竖炉结瘤、流化床失流和黏结、回转窑结圈等技术难题.高炉流程冶炼钒钛矿,只回收了铁和钒,钛进入高炉渣没有回收,造成钛资源的大量流失.2005年以来,攀钢科研人员在充分吸收、借鉴新流程及相关研究成果的基础上,通过大量的试验研究,针对钒钛磁铁矿特点,提出并验证了钒钛磁铁矿"转底炉直接还原—电炉深还原—含钒铁水提钒—含钛炉渣提钛"工艺路线,彻底打通了钒钛矿资源综合利用新工艺流程,稳定获得了质量满足要求的低碳生铁、达到GB3283-87要求的片状V2O5和PTA121质量要求的钛白产品.依托该研究成果,攀钢集团攀枝花钢铁研究院于2008年5月4日正式启动了攀钢10 万t/a钒钛矿资源综合利用新工艺中试线工程项目,新建一条转底炉—熔分电炉联合使用,年处理能力10万t钒钛矿的试验生产线,为更深入地研究实践,实现转底炉处理钒钛矿的规模化生产提供了广阔的平台.中试线工艺流程如图7所示.本流程采用硫含量较低的白马铁精矿,还原剂采用无烟煤煤粉,粘结剂为有机粘结剂,原料混合后经高压压球机压球,生球烘干后进入转底炉系统.球团在转底炉内停留10~30 min后出料,金属化球团直接热装进入熔分电炉,在一定温度下还原后,产出含钒铁水及含钛炉渣.继续对铁水进行脱硫、提钒后,得到半钢、脱硫渣及钒渣,半钢进入铸铁机铸铁,生产出铸铁块.钛渣制取钛白,实验室条件下钛回收率达到80%以上;钒渣制取钒氧化物(V2O5),实验室条件下,钒回收率达到65%以上.与高炉流程相比,转底炉流程采用100%钒钛矿冶炼,克服了高炉流程必须配加普通矿的不足,在当前铁资源紧张的形势下,有助于充分发挥攀西地区资源优势,拉动区域经济发展.此外,转底炉流程的铁精矿不需烧结处理,不使用焦炭,从根本上避免了烧结烟气脱硫、焦煤资源采购困难以及环保压力大等问题.3 结语图7 资源综合利用中试线工艺流程煤炭资源总量丰富、焦煤短缺,铁矿资源储量大、富矿少、贫矿和共生矿多是中国钢铁工业面临的现实状况.这种能源、资源结构给煤基直接还原法生产海绵铁的发展提供了机遇.转底炉直接还原技术由于在生产率、规模化、投资费用、单位成本等方面都占有明显的优势,可作为发展直接还原技术的首选工艺.鉴于转底炉处理钒钛磁铁矿技术尚属世界首创,并无较多的经验借鉴,因此要大力开展针对钒钛磁铁矿直接还原的基础研究工作,在实践中借鉴各种直接还原方法已取得的成果,开拓创新,开创钒钛矿直接还原新纪元.参考文献[1] 陈守明,黄超,张金良.煤基竖炉直接还原工艺//2008年非高炉炼铁年会文集.中国金属学会,2008:132-135.[2] 杨婷,孙继青.世界直接还原铁发展现状及分析.世界金属导报,2006.[3] 刘国根,邱冠周,王淀佐.直接还原炼铁中的粘结剂.矿产综合利用,2001(4):27-30.[4] 韩跃新,高鹏,李艳军.白云鄂博氧化矿直接还原综合利用前景.金属矿山,2009 (5):1-6.[5] 魏国,赵庆杰,沈峰满,等.非高炉生产技术进步//2004年全国炼铁生产技术暨炼铁年会文集.2004:878-882.[6] 陶晋. 环形转底炉直接还原工艺现状及发展趋势. 冶金信息工作, 1997.6.[7] 郭培民,赵沛,张殿伟.低温快速还原炼铁新技术特点及理论研究.炼铁,2007,26(1): 57-60.来源:攀枝花钢铁研究院网站。
- 1、下载文档前请自行甄别文档内容的完整性,平台不提供额外的编辑、内容补充、找答案等附加服务。
- 2、"仅部分预览"的文档,不可在线预览部分如存在完整性等问题,可反馈申请退款(可完整预览的文档不适用该条件!)。
- 3、如文档侵犯您的权益,请联系客服反馈,我们会尽快为您处理(人工客服工作时间:9:00-18:30)。
我国钒钛磁铁矿直接还原分析
摘要
本文概括地介绍了我国钒钛磁铁矿资源分布情况。
钒钛磁铁矿是重要的资源,世界各国的研究及生产实践表明,使用高炉冶炼法钒钛磁铁矿是难以冶炼的铁矿石。
因此钒钛磁铁矿冶炼大量使用非高炉冶炼法,即采用直接还原法。
本文详细地阐述了直接还原法中隧道窑、回转窑、转底炉、竖炉这四种常见炉的结构、反应原理、国内工艺现状及反应特点,并指出了我国钒钛磁铁矿直接还原工艺的发展方向。
关键词钒钛磁铁矿直接还原隧道窑回转窑转底炉竖炉
前言
目前国外钒钛磁铁矿主要分布在南非、前苏联、新西兰、加拿大、印度等地。
我国钒钛磁铁矿矿床分布广泛,储量吩咐,储量和开采量居全国铁矿的第3位。
已探明储量98.3亿吨,远景储量达300亿吨以上,主要分布在四川攀枝花地区、河北承德地区、陕西洋县、甘肃什斯镇、广东兴宁几山西代县等地区。
钒钛磁铁矿冶炼的利用问题,远在上19世纪上半叶,瑞典、挪威、美国、英国都进行过试验,均未取得结果。
20世纪30年代开始日本、前苏联开始在不同容积的高炉上研究冶炼钒钛磁铁矿的工艺,结论是:炉渣中TiO2 限制在16%以下,实际生产中采用配10%—15%的普通矿冶炼含钒生铁,渣中TiO2为9%—10%,TiO2含量越高冶炼难度越大。
世界各国的研究及生产实践表明,钒钛磁铁矿是难以冶炼的铁矿石。
通过多年的努力,钒钛磁铁矿已解决高炉冶炼等多项技术难题,逐渐形成了以高炉-转炉流程为主的综合回收其中铁、钒和钛的技术路线,实现了铁、钒和钛元素的大规模化利用,形成了铁钒钛系列产品的大规模工业生产能力。
然而高炉-转炉流程最大的缺点是:为了利用钒钛磁铁矿中的铁和钒浪费了大量的高钛型炉渣,造成钛资源的严重浪费,又造成很大的污染,从而形成了巨大的环境压力,所以开发适宜钒钛磁铁矿综合回收利用的工艺流程势在必行。
本文对钒钛磁铁矿煤基直接还原工艺的炉体结构、原理、特点、现状、投资价格进行简单探讨,指出煤制气-竖炉直接还原工艺为还原钒钛磁铁矿的发展提供新的途径。
直接还原指在低于矿石熔化温度下,通过固态还原把铁矿石炼制成铁的工艺过程。
直接还原铁的特点是碳、硅含量低,成分类似钢,实际上也代替废钢用于炼钢。
作为传统工艺的补充,钒钛磁铁矿直接还原工艺以其环保、原料广泛的特点受到了市场的青睐。
按还原剂的不同,直接还原工艺分为煤基直接还原和气基直接还原。
气基直接还原方式生产直接还原铁在国外一直占有较大的市场份额。
我国煤基直接还原钒钛磁铁矿已经得到了广泛的应用。
隧道窑、回转窑、转底炉和竖炉的结构与还原原理
隧道窑结构与还原原理
结构:隧道窑的横截面为上部呈圆拱形,下部呈长方形,其长度从30—200m 不等,是从砖窑移植过来的。
隧道窑底部铺设有铁轨,窑车在铁轨上进行,物料放在还原罐内,还原罐整齐地放在窑车上,窑车在隧道窑内缓慢进行。
原理:隧道窑生产直接还原铁工艺是将铁原料、还原剂、脱硫剂按工艺要求加工好,按照一定的比例和装料方法,分别装入还原罐中,放在台车上推入隧道窑中,通入煤气点燃,料罐中的原料经预热,在1000—1200°C的温度条件下还原,在保持足够的还原时间和冷却时间后,得到直接还原铁。
回转窑结构与还原原理
结构:回转窑是一个倾斜放置的旋转圆筒体,其内壁上砌有耐火材料。
规格为筒体内径有效长度表示。
原理:窑体旋转很慢,由钒钛磁铁矿、细粒煤及脱煤及脱硫剂组成的物料在摩擦力作用下被窑体带起,超过物料运动角后,在重力作用下,自堆尖滚落到底部。
因窑体倾斜,物料也前移一段距离。
同一回转窑内,物料在窑内的停留时间与填充率成正比。
转底炉结构与还原原理
结构:转底炉(RHF)工艺的主体设备转底炉是由轧钢使用的环形加热炉演变而来,是一个平坦的、内有耐火材料衬的可以转动的环形高温窑炉。
其烧嘴位于炉膛上部,所用燃料可以是天然气、燃油、煤粉等。
原理:转底炉直接还原技术是铁矿粉(或红土镍矿、钒钛磁铁矿、硫酸渣或冶金粉尘、除尘灰、炼钢污泥等)经配料、混料、制球和干燥后的含碳球团加入到具有环形炉膛和可转动的炉底的转底炉中,在1350 ℃左右炉膛温度下,在随着炉底旋转一周的过程中,铁矿被碳还原。
竖炉结构与还原原理
结构:竖炉主要由烟罩、炉体钢结构、炉体砌砖、导风墙和干燥床、卸料器、供风和煤气管路等结构组成,分为上料系统、还原段、冷却段、排料系统、尾气净化系统等。
原理:竖炉还原流程由竖炉还原带、炉顶煤气换热器、炉顶煤气激冷/洗涤系统、工艺气循环压缩机、压缩机二次冷却器、CO2吸收器、工艺气加湿器和工艺气加热器等组成。
炉料在竖炉里下降,并逐步完成还原过程。
国内隧道窑、回转窑、转底炉和竖炉在煤基直接还原工艺中的现状
国内隧道窑工艺现状
隧道窑在还原工艺上是最成熟的,2002年中南工业大学、中南矿业研究院与攀钢合作完成了隧道窑罐混合还原剂还原的实验,取得了较好的效果。
现如今我国已建成和正在建设的隧道窑有100多座,随着直接还原铁需求量大增,隧道窑直接还原铁技术也得到不断完善。
钒钛磁铁矿攀枝花攀阳钒钛工贸有限公司通过四年产业化中试,于2009年建成了一条年产能2万t的遂道窑煤基直接还原
处理钒钛磁铁矿工业生产线,实现了产业化生产。
该工艺流程采用钒钛铁精矿粉与还原剂混合压块、装罐,罐放在窑车上直接进入隧道窑进行还原,制备成金属化物料,金属化物料再进行电炉熔分,实现钒、钛分离,产品为生铁和钛渣。
国内回转窑工艺现状
我国先后进行过回转窑试验的有攀钢西昌410厂、福州回转窑等,20世纪90年代,我国建设了一批用于直接还原普通铁精矿的回转窑,由于回转窑对原料的要求苛刻,能耗高,投资高,运行费用高,生产运行的稳定难度大,生产难扩大等原因在中国得不到很好的发展。
国内转底炉工艺现状
我国对转底炉工艺的研究有一定的历史,其中转底炉煤基热风熔融炼铁工艺,又称恰普法,是由北京科技大学冶金与生态工程学院冶金喷枪研究中心在转底炉直接还原基础上开发的新炼铁工艺。
攀枝花学院与四川龙蟒矿冶公司的科研人员从2004年起就开始进行该工艺研究,经过4年多大量艰苦努力,获得了重大技术突破,获得了高水平研究成果,为产业化提供打下了坚实基础。
目前,四川龙蟒集团攀枝花矿冶公司在攀枝花进行产业化建设,取得较好的经济效益。
但由于转底炉直接还原工艺中必须“内配煤”,因而对含钛炉渣造成了严重的污染,降低了TiO2的品位。
国内竖炉工艺现状
近年来,中国众多工作者对煤制气-竖炉直接还原铁生产进行了大量调查、研究工作,为中国采用煤制气-坚炉直接还原技术奠定了良好的基础。
但煤制气方法的选择、煤选择、煤制气-坚炉工艺的多联产的组合的选择及相关装备等问题还有进一步深入研究和探讨。
辽宁海城四型钢公司以煤制气为还原气,氧化球团为原料的竖炉项目,是竖炉是引进墨西哥希尔萨的HyL-ZR装置,设计生产能力为50万t/a;煤制气采用恩德法(流化床)单炉生产能力为40000m3/h。
隧道窑、回转窑、转底炉和竖炉在煤基直接还原工艺中的特点
隧道窑工艺特点:目前隧道窑直接还原铁工艺已经很成熟,对原料要求宽松具有灵活性,紧靠装灌方式不同,对原料的含水量有不同的要求,但是存在着流程过长,效率低,能耗高,生产周期长,污染严重,产品质量不稳定等,不适合用于处理大规模的钒钛磁铁矿。
生产实践表明,隧道窑生产直接还原铁还原时间超过50h。
回转窑工艺特点:回转窖对原料的冶金性能要求苛刻,要求球团必须具有足够的机械强度,较低的低温粉化率,还原过程中及还原过后必须有足够的耐磨强度和抗压强度。
回转窑内容易结圈,生产流程长,产品成本高,质量差。
转底炉工艺特点:工艺流程短,对原料要求宽松,对球团/压块的强度要求低原料适应性强,炉料不容易粘接、结圈,还原温度高、还原时间短(入炉到出炉20~30分钟),还原的金属化率高,生产效率高,可以很容易地开炉、停炉和
调整产量。
竖炉工艺特点:要求较高的还原气温度。
此外竖炉对球团的机械强度要求较高,较低的低温粉化率和还原膨胀率,还原过后球团必须有足够的强度,产品质量高、自动化程度高,能耗在现行还原方法中最低,可以大型化生产且符合国家节能减排的要求。
投资比较
按年产50万吨还原产品工艺投资估算的话:隧道窑、回转窑转底炉、天然气-竖炉、煤制气-竖炉分别投资人民币(亿元)2.5~3.0、7.0~8.0、7.5~10.0、5.0~6.0、7.0~7.5、9.0~10.0。
我们可见各种不同炉型在煤基直接还原钒钛磁铁矿的设备投资金额各不相同。
结论
隧道窑工艺能耗高,污染严重不符合国家“节能减排”的发展要求,不适宜在还原钒钛磁铁矿中发展此工艺;回转窑对原料要求苛刻,工艺成本高,流程长,产品质量差。
转底炉工艺流程短,对原料要求宽松,对球团/压块的强度要求低原料适应性强。
但是回转窑与转底炉这两种工艺只适用于中小型生产线进行生产。
气基竖炉可用于大规模处理钒钛磁铁矿,煤制气-竖炉直接还原工艺为还原钒钛磁铁矿的发展提供了新的途径,我国有丰富的煤炭资源,国内有成熟的煤制气技术和长期运行的经验。
虽然现在高炉冶炼还是主要的冶炼钒钛磁铁矿的方法,但是直接还原冶炼钒钛磁铁矿在不久的将来便可以成为冶炼钒钛磁铁矿的主要方法。
气基-竖炉直接还原钒钛磁铁矿工艺未来应用前景十分广阔,将逐步改变我国的煤基直接还原钒钛磁铁矿生产的格局,出现了一片大好的发展热潮。