第1章超精密研磨与抛光
研磨

超精密研磨抛光现状综述摘要:超精密研磨抛光过程中材料去除规律对提高加工的稳定性十分重要。
本文对超精密研磨抛光技术进行综述,重点介绍各种典型加工方法及其材料去除机理。
并对超精密研磨抛光加工的发展趋势进行预测。
关键词:化学机械研磨弹性发射加工动压浮离抛光浮法抛光低温抛光磁场辅助抛光磨粒加工1 前言研磨是用研磨工具和研磨剂从工件表面上磨去一层极薄的金属,使工件表面达到精确的尺寸、准确的几何形状和很高的表面光洁度。
研磨的方法很多,按照加工方法来分类可以分为干研磨,湿研磨和抛光三类。
超精密研磨抛光是超精密加工的最主要的终加工手段,目的是降低表面粗糙度并去除前道加工工序形成的损伤层(通常为磨削),获得光滑、无损伤的加工表面。
因此了解超精密研磨抛光加工的方法和中材料的去除规律,对提高表面超精密加工质量有重大的意义。
2 常见的超精密研磨抛光技术2.1化学机械研磨(Chemical-echanical p01ishing,CMP)技术。
CMP加工通过磨粒一工件一加工环境之间的机械、化学作用,实现工件材料的微量去除,能获得超光滑、少/无损伤的加工表面;加工轨迹呈现多方向性,有利于加工表面的均匀一致性;无需精度很高的加工设备[15]。
CMP技术可以获得超光滑无损伤表面的有效方法,可获得0.1 nm级表面粗糙度和极小的表面损伤层,但也存在一定的局限性,主要体现在加工精度对磨粒尺寸差异敏感。
在理想状况下,工件与磨具之间的磨粒粒度均匀一致,磨粒上的载荷相等(图1a)。
当加工区内有硬质大颗粒产生(磨粒团聚或工件磨屑)或进入(外界环境中的大颗粒灰尘)时,若磨具为刚性,则加工载荷由少量大颗粒承担,导致大颗粒对工件的切深增加因而形成划痕、凹坑等损伤,或者大颗粒在载荷作用下破碎,但在破碎前往往已在工件表面形成损伤(图1b);为此,通常采用弹性抛光垫(沥青、聚氨酯等材料)的方法来缓解大颗粒对工件表面的负面作用仍会造成工件表面的划痕等损伤形式(图1c)。
精密研磨与抛光(精密加工)
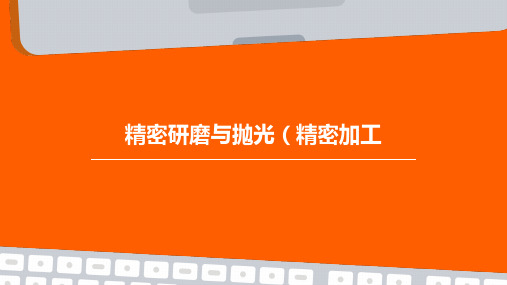
表面平滑
在抛光过程中,工件表面逐渐被 磨平,最终达到镜面或高度平滑
的效果。
表面改性
在抛光过程中,工件表面可能会 发生物理或化学变化,如表面层 晶格结构的变化或表面化学成分
的改变。
抛光工艺参数
压力
抛光压力是影响抛光效果的重要参数,压力过大会导致工件表面 损伤,过小则抛光效率低下。
02
精密研磨技术
研磨材料
01
02
03
04
刚玉
常用作研磨材料,具有高硬度 和耐磨性,适用于硬材料的研
磨。
碳化硅
具有高硬度和高韧性,适用于 研磨硬而脆的材料。
氧化铝
具有较好的韧性和耐磨性,适 用于研磨软材料和中等硬度的
材料。
天然磨料
如河砂、海砂等,可用于粗研 磨和抛光。
研磨机理
切削作用
研磨材料表面上的磨粒在压力作 用下切入工件表面,切削出微小
智能化的发展
智能检测与监控系统
通过引入传感器和智能化检测技术,实现对 研磨与抛光过程的实时监测和数据采集,提 高加工过程的稳定性和可靠性。同时,通过 数据分析与处理,优化加工参数,提高加工 效率和表面质量。
自动化生产线
通过集成机器人、自动化设备和智能化管理 系统,构建自动化生产线,实现研磨与抛光 过程的自动化和连续化生产。这将大幅提高 生产效率,降低人工成本,提升企业竞争力
总结词
高分子材料的研磨与抛光是实现高分子材料表面高精度和高光洁度的重要手段。
详细描述
高分子材料的研磨与抛光主要采用金刚石、刚玉等硬质材料作为磨料,通过研磨、抛光等工艺去除高 分子材料表面的凸起和划痕,以提高其表面质量和性能。高分子材料的研磨与抛光广泛应用于塑料、 橡胶、涂料等领域。
第5章 超精密研磨与抛光(康仁科) 大连理工大学
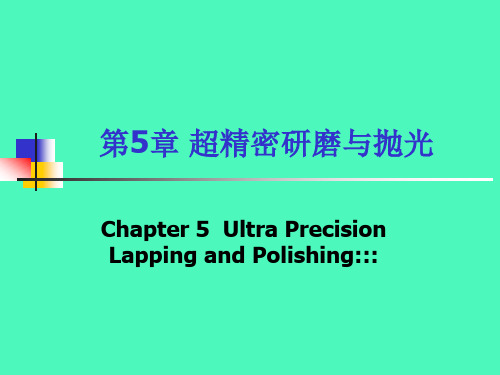
固结磨料研磨
圆柱面和球面的研磨
5.5.1 液中研磨
磨料:微细的 磨料:微细的Al2O3磨粒 磨粒 研具: 研具:聚氨酯 加工液:过滤水、蒸馏水、 加工液:过滤水、蒸馏水、净化水 机理:将研磨操作浸入在含有磨粒的研磨剂中 机理: 进行,借助水波效果, 进行,借助水波效果,利用浮游的微细磨粒进 行研磨加工。以磨粒的机械作用为中心, 行研磨加工。以磨粒的机械作用为中心,由加 工液进行磨粒的分散,起缓冲和冷却作用。 工液进行磨粒的分散,起缓冲和冷却作用。 应用:加工硅片,可以得到完全高质量的镜面。 应用:加工硅片,可以得到完全高质量的镜面。
研具
磨粒
加工液 工件、 工件、研具相对速度 加工压力 加工时间 环境
温 度 尘 埃
室温设定温度± 室温设定温度±0.1℃ ℃ 利用净化槽、 利用净化槽、净化操作台
5.4 超精密平面研磨和抛光
超精密研磨和抛光是加工误差<0.1 µm,表面粗 糙度Ra<0.02 µm的加工方法。 用于制造高精度高表面质量的零件,如大规模 集成电路的硅片,不仅要求极高的平面度,极 小的表面粗糙度,而且要求表面无变质层、无 划伤。光学平晶、量块、石英振子基片平面, 除要求极高平面度、极小表面粗糙度外,还要 求两端面严格平行。
5.5 新原理的超精密研磨抛光
传统的研磨抛光方法是完全靠微细磨粒的机械 作用去除被研磨表面的材质, 作用去除被研磨表面的材质,达到很高的加工 表面。 表面。 最近出现新原理的研磨抛光方法其工作原理有 些已不完全是纯机械的去除, 些已不完全是纯机械的去除,有些不用传统的 研具和磨料。 研具和磨料。这些新的研磨抛光方法可以达到 分子级和原子级材料的去除, 分子级和原子级材料的去除,并达到相应的极 高几何精度和无缺陷无变质层的加工表面。 高几何精度和无缺陷无变质层的加工表面。
研磨与抛光的区别
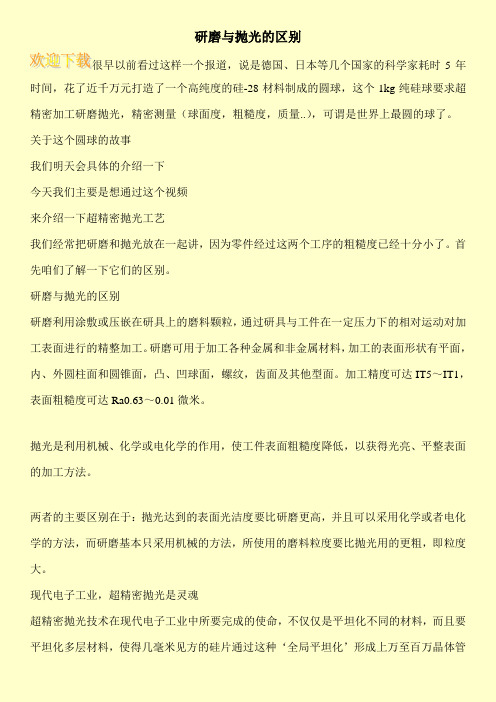
研磨与抛光的区别
很早以前看过这样一个报道,说是德国、日本等几个国家的科学家耗时5年时间,花了近千万元打造了一个高纯度的硅-28材料制成的圆球,这个1kg纯硅球要求超精密加工研磨抛光,精密测量(球面度,粗糙度,质量..),可谓是世界上最圆的球了。
关于这个圆球的故事
我们明天会具体的介绍一下
今天我们主要是想通过这个视频
来介绍一下超精密抛光工艺
我们经常把研磨和抛光放在一起讲,因为零件经过这两个工序的粗糙度已经十分小了。
首先咱们了解一下它们的区别。
研磨与抛光的区别
研磨利用涂敷或压嵌在研具上的磨料颗粒,通过研具与工件在一定压力下的相对运动对加工表面进行的精整加工。
研磨可用于加工各种金属和非金属材料,加工的表面形状有平面,内、外圆柱面和圆锥面,凸、凹球面,螺纹,齿面及其他型面。
加工精度可达IT5~IT1,表面粗糙度可达Ra0.63~0.01微米。
抛光是利用机械、化学或电化学的作用,使工件表面粗糙度降低,以获得光亮、平整表面的加工方法。
两者的主要区别在于:抛光达到的表面光洁度要比研磨更高,并且可以采用化学或者电化学的方法,而研磨基本只采用机械的方法,所使用的磨料粒度要比抛光用的更粗,即粒度大。
现代电子工业,超精密抛光是灵魂
超精密抛光技术在现代电子工业中所要完成的使命,不仅仅是平坦化不同的材料,而且要平坦化多层材料,使得几毫米见方的硅片通过这种‘全局平坦化’形成上万至百万晶体管。
精密研磨与抛光ppt课件
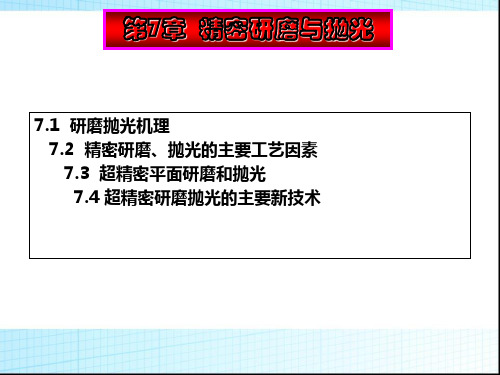
课后思考题
习题6-2 习题6-15
第7章 精密研磨与抛光
7.1 研磨抛光机理 7.2 精密研磨、抛光的主要工艺因素 7.3 超精密平面研磨和抛光 7.4 超精密研磨抛光的主要新技术
第1节 研磨抛光机理
一、研磨加工的机理
1.研磨时磨料的工作状态 1)磨粒在工件与研具之间发生滚动,产生滚轧 效果;
2)磨粒压入到研具表面,用露出的磨粒尖端对 工件表面进行刻划,实现微切削加工;
软质磨粒机械抛光(弹性发射加工)
最小切除可以达到原子级,直至切去一层 原子,而且被加工表面的晶格不致变形,能 够获得极小表面粗糙度和材质极纯的表面。 加工原理实质是磨粒原子的扩散作用和加速 的微小粒子弹性射击的机械作用的综合效果。 真空中带静电的粉末粒子加速法、空气流或 水流来加速。
化学机械抛光
3.金属材料的研磨
当金属表面用硬度计压头压入时,只在表面 产生塑性变形的压坑,不会发生脆性材料那 样的破碎和裂纹。
研磨时,磨粒的研磨作用相当于极微量切削 和磨削时的状态,且表面不会产生裂纹。
二、抛光加工的机理
抛光的机理:1)以磨粒的微小塑性切削生成切屑, 但是它仅利用极少磨粒强制压入产生作用。2)借助磨 粒和抛光器与工件流动摩擦使工件表面的凸凹变平。
磁流体精密研磨
磁性流体为强磁粉末在液相中分散为胶态尺寸 (<0.015μm)的胶态溶液,由磁感应可产生流动性,特 性是:每一个粒子的磁力矩较大,不会因重力而沉降,磁 化强度随磁场增加而增加。当将非磁性材料的磨料混入磁 流体,置于磁场中,则磨粒在磁流体浮力作用下压向旋转 的工件而进行研磨。磁流体精研的方法又有磨粒悬浮式加 工、磨料控制式加工及磁流体封闭式加工。
五、获得高质量平面研磨抛光的工艺规律
超精密研抛及超声波研抛技术分析
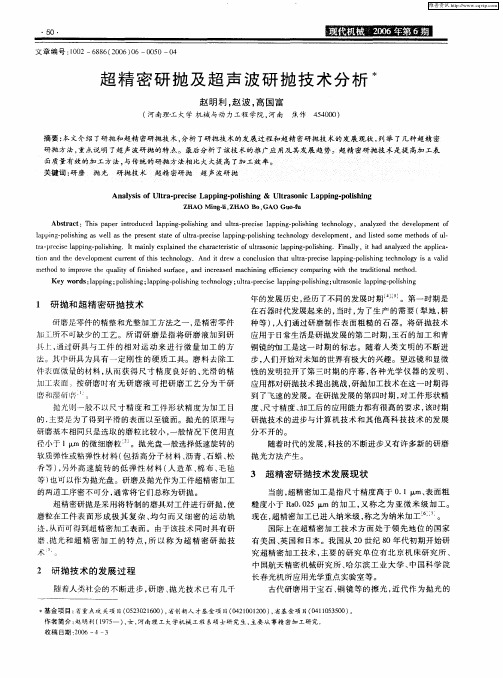
摘 要 : 文介 绍 了研 抛 和 超 精 密研 抛技 术 , 本 分析 了研 抛技 术 的发 展 过 程 和 超 精 密研 抛 技 术 的 发 展 现 状 , 举 了 几种 超 精 密 列
研抛方法, 重点说明 了超声波研抛 的特 点。最后 分析 了该技术的推广应 用及其发展 趋势。超精 密研 抛技术是提 高加 工表
维普资讯
5 0
文 章 编 号 :0 2— 8 6 20 )6— 0 0—0 10 6 8 (0 6 0 0 5 4
超 精 密研 抛 及超 声 波研 抛技 术 分 析 水
赵明利 , 赵波 。 国富 高
( 南理, 大 学 机 械 与动 力 工程 学 院 , 南 焦作 河 工 河 44 0 ) 5 00
面质量有效的加工方法, 与传统的研抛 方法相比大大提 高了加工效率。 关键词Fra bibliotek 研磨抛光
研抛 技术
超精 密研抛
超声波研抛
An l s so t a p e ie La p n - o ih n & U t a o i p i g p l h n a y i fUlr - r c s p i g p ls i g l r s n c La p n ・ o ii g s
1 研 抛和 超 精 密 研 抛 技 术
研磨 足零件 的精整 和光 整加工 方法之 一 , 是精 密零 件 加 工所 不 l缺少 的工 艺 。所 谓 研磨 是 指将 研 磨 液加 到 研 口 『
卜, 通过研 具 与 工 件 的 相 对 运 动 来 进 行微 量 加 工 的 方
年 的发展 历史 , 经历 了不 同的发展 时期 “ 。第一 时期 是 在石 器时 代发展起 来 的 , 时 , 了生 产 的需 要 ( 当 为 犁地 , 耕 种等 ) 人们 通过研 磨 制作 表 面粗 糙 的石 器 。将研 抛 技术 , 应用 于 日常生 活是研抛发 展 的第 二 时期 , 玉石 的加工 和青 铜镜 N' q是这 一时 期 的标 志 。随 着 人类 文 明 的不 断进 / - J  ̄ 步, 人们 开始对 未知 的世界有 极大 的兴趣 。望 远镜 和显 微
《精密和超精密加工技术(第3版)》第3章精密磨削和超精密磨削
2018/3/11
第1节 概述
二、精密和超精密砂轮磨料磨具
磨料及其选择
超硬磨料制作的磨具在以下几方面能够满足精密加工和超精密加工 的要求,因此使用广泛。
1)磨具在形状和尺寸上易于保持,使用寿命高,磨削精度高。
2)磨料本身磨损少,可较长时间保持切削性,修整次数少,易于保持精度。
3)磨削时,一般工件温度较低,因此可以减小内应力、裂纹和烧伤等缺
磨具的形状和尺寸及其基体材料
根据机床规格和加工情况选择磨具的 形状和尺寸。 基体材料与结合剂有关。
2018/3/11
第1节 概述
三、精密和超精密涂覆磨具
涂覆磨具分类
根据涂覆磨具的形状、基底材料和工作条件与用途等,分类见下表
涂 覆 磨 具
工 作 条 件
基 底 材 料
形 状
耐 水 (N)
2018/3/11
精密砂带磨削:砂带粒度F230~F320,加
工精度1μm,Ra0.025; 超精密砂带磨削:砂带粒度W28~W3,加工精 度0.1μm,Ra0.025~0.008μm。
2018/3/11
第1节 概述
一、精密和超精密加工分类
游离磨料加工
磨料或微粉不是固结在一起, 而是成游离状态。 传统方法:研磨和抛光 新方法:磁性研磨、弹性发射 加工、液体动力抛光、液中研 抛、磁流体抛光、挤压研抛、 喷射加工等。
第3章 精密磨削和超精密磨削 3.1 概述
3.2 精密磨削 3.3 超硬磨料砂轮磨削
3.4 超精密磨削
3.5 精密和超精密砂带磨削
2018/3/11
第1节 概述
精密和超精密磨料加工是利用细粒度的磨粒和 微粉对黑色金属、硬脆材料等进行加工,得到高 加工精度和低表面粗糙度值。对于铜、铝及其 合金等软金属,用金刚石刀具进行超精密车削是 十分有效的,而对于黑色金属、硬脆材料等,用 精密和超精密磨料加工在当前是最主要的精密 加工手段。
精密与超精密加工试题和答案
1)精密和超精密加工的精度范围分别为多少?超精密加工包括哪些领域?2)答:精密与超精密加工的精度随着科学技术的发展不断提高, 以目前的加工能力而言, 精密加工的精度范围是0.1~1μm, 加工表面精度Ra在0.02~0.1μm之间。
超精密加工的精度高于0.1μm, 加工表面精度Ra小于0.01μm。
3)超精密加工领域:4)超精密切削,5)超精密磨削,6)超精密研磨和抛光。
超精密切削对刀具有什么要求?天然单晶金刚石、人造单晶金刚石、人造聚晶金刚石和立方氮化硼刀具是否适用于超精密切削?答: 超精密切削对刀具的要求:1) 刀具刃口锋锐度ρ刀具刃口能磨得极其锋锐, 刃口圆弧半径ρ极小, 能实现超薄切削厚度, 减小切削表面弹性恢复和表面变质层。
ρ与切削刃的加工方位有关, 普通刀具5~30μm, 金刚石刀具<10nm;从物理学的观点, 刃口半径ρ有一极限。
2) 切削刃的粗糙度。
切削时切削刃的粗糙度将决定加工表面的粗糙度。
普通刀刃的粗糙度Ry0.3~5 μm, 金刚石刀具刀刃的粗糙度Ry0.1~0.2 μm, 特殊情况Ry1nm, 很难。
3) 极高的硬度、极高的耐磨性和极高的弹性模量, 保证长的刀具寿命。
4) 刀刃无缺陷, 足够的强度, 耐崩刃性能。
5) 化学亲和性小、与工件材料的抗粘结性好、摩擦系数低, 能得到极好的加工表面完整性。
单晶金刚石硬度极高。
自然界最硬的材料, 比硬质合金的硬度高5~6倍。
摩擦系数低。
除黑色金属外, 与其它物质的亲和力小。
能磨出极锋锐的刀刃。
最小刃口半径1~5nm。
耐磨性好。
比硬质合金高50~100倍。
导热性能好, 热膨胀系数小, 刀具热变形小。
因此, 天然单晶金刚石被一致公认为理想的、不能代替的超精密切削刀具。
人造单晶金刚石已经开始用于超精密切削, 但是价格仍然很昂贵。
金刚石刀具不适宜切黑色金属, 很脆, 要避免振动而且价格昂贵, 刃磨困难。
人造聚晶金刚石无法磨出极锋锐的切削刃, 切削刃钝圆半径ρ很难达到<1μm, 它只能用于有色金属和非金属的精切, 很难达到超精密镜面切削。
超精密抛光工艺的定义-概述说明以及解释
超精密抛光工艺的定义-概述说明以及解释1.引言1.1 概述超精密抛光工艺是一种高度精细化的表面处理技术,通过对工件表面进行极其细致的抛光和修饰,使其获得极高的光学精度和表面平整度。
这项工艺在多个领域都有广泛的应用,包括光学、精密仪器制造、半导体制造等。
相比传统抛光工艺,超精密抛光工艺更注重精度和表面质量的控制,可以实现纳米级甚至更高的表面精度要求。
本文将介绍超精密抛光工艺的定义、应用领域和关键技术,旨在深入探讨这一先进表面处理技术的原理和发展趋势,为相关领域的研究人员和从业者提供参考和借鉴。
json"1.2 文章结构":{"本文将首先介绍超精密抛光工艺的定义,包括其概念、特点和优势。
接着将探讨超精密抛光工艺在不同领域的应用,例如光学、半导体和精密机械制造等。
然后将深入分析超精密抛光工艺的关键技术,包括材料选择、工艺流程和设备要求等。
最后,文章将总结超精密抛光工艺的意义和展望,展望未来在该领域的发展前景,以及对读者提出一些思考和建议。
"}1.3 目的本文旨在探讨超精密抛光工艺的定义、应用领域和关键技术,以帮助读者深入了解该工艺的特点和优势。
通过详细介绍超精密抛光工艺的概念和原理,读者将能够更好地理解其在实际生产中的应用场景和价值所在。
此外,本文还将探讨超精密抛光工艺面临的挑战和未来发展方向,为相关领域的研究和实践提供参考和借鉴。
通过本文的阐述,希望读者能够对超精密抛光工艺有一个全面而深入的认识,从而促进该工艺在工业生产中的广泛应用和推广。
2.正文2.1 超精密抛光工艺的定义超精密抛光工艺是一种高精度的表面处理技术,通过在材料表面施加特定的力和磨料,在微观层面上去除材料表面的凸起部分,从而获得非常光滑的表面。
它在纳米级和亚纳米级的精度下进行,能够获得极高的表面光洁度和平整度。
该技术主要应用于需要极高表面质量和精度的领域,如半导体制造、光学元件制造、精密仪器制造等。
磨工(技师、高级技师)第一章
2.低表面粗糙度磨削的原理
第一章 高精度轴类、套类零件的磨削工艺
第一章 高精度轴类、套类零件的磨削工艺
了解高精度万能外圆磨床的结构及精度要求,外圆磨床 精度标准,低表面粗糙度磨削工艺,现代成组磨削工艺,现 代机械制造知识。掌握工艺关键零件的高精度磨削工艺。了 解镜面磨削工艺。了解圆度仪的结构及其使用方法。能使用 超精密磨削法加工高精度主轴和精密套简零件,达到以下要 求:表面粗糙度值为0.05um,圆柱度公差0.001mm,圆度公差 0.0003mm。熟练掌握磨削高端技术,提高产品品质。
第一节 高精度轴类、套类零
四、低表面粗糙度磨削工艺
高精度磨削加工中,使工件表面粗糙度值低于Ra0.2μm的磨削称为 低表面粗糙度磨削。
1.低表面粗糙度磨削的特点
1)经低表面粗糙度磨削的表面可获得较高的加工精度和较低的表面粗 糙度值。 2)低表面粗糙度磨削与研磨相比较,具有较高的劳动生产率。
第一节 高精度轴类、套类零
第一节 高精度轴类、套类零
图1-1 高精度万能外圆磨床及传动系统 a)高精度万能外圆磨床 b)传动系统
1—手轮 2、3、4、5、6、7、18、21、22、23—齿轮 8、9、10、12、14、15、16—带轮 11—传动带 13—内圆磨具主轴 17—砂轮主轴 19—棘爪 20—棘轮 24—横进给丝杠 25—螺母
第一节 高精度轴类、套类零
*二、外圆磨床的精度标准
表1-1 外圆磨床精度标准
第一节 高精度轴类、套类零
三、高精度万能外圆磨床
这里主要介绍高精度万能外圆磨床的机械传动系统及其主要部件结构、 液压传动系统等。
- 1、下载文档前请自行甄别文档内容的完整性,平台不提供额外的编辑、内容补充、找答案等附加服务。
- 2、"仅部分预览"的文档,不可在线预览部分如存在完整性等问题,可反馈申请退款(可完整预览的文档不适用该条件!)。
- 3、如文档侵犯您的权益,请联系客服反馈,我们会尽快为您处理(人工客服工作时间:9:00-18:30)。
加工液
工件、研具相对速度
加工压力 加工时间
1~100m/min
0.01~30N/cm2 ~10h
环境
温 度
尘 埃
室温设定温度±0.1℃
利用净化槽、净化操作台
5.4 超精密平面研磨和抛光
超精密研磨和抛光是加工误差<0.1 μm,表面粗 糙度Ra<0.02 μm的加工方法。 用于制造高精度高表面质量的零件,如大规模 集成电路的硅片,不仅要求极高的平面度,极 小的表面粗糙度,而且要求表面无变质层、无 划伤。光学平晶、量块、石英振子基片平面, 除要求极高平面度、极小表面粗糙度外,还要 求两端面严格平行。
抛光机
多头、单头抛光机
Polish Overarm Substrate Carrier Polish Table
Substrate Carrier with Polish Overarm
抛光垫形状外貌
抛光垫材料和类型
Type I
注入聚合物的毛毡
Type II
微孔材料
Type III
充填聚合物
弹性发射加工-EEM
(Elastic Emission Machining)
加工时研具于工件不接触,使微细 粒子在研具与工件表面之间自由状 态流动,当使微细粒子撞击工件表 面时,则产生弹性破坏物质的原子 结合,从而获得无干扰的加工表面。 加工单位为0.1 μm以下,原理上是 采用喷射粒子的加工方式,要尽量 以小角度撞击加工表面,其加工精 度接近于原子级,可获得相当好的 表面。 加工方法是使用聚氨酯球作加工头, 在微细粒子混合均匀的悬浮液中, 使加工头边回转边向工件表面靠近, 是混合液中的微细粒子在工件表面 的微小面积(Φ1~2mm)内产生作 用,进行加工。
5.2.3 研磨的加工变质层
加工变质层使工件材质的结构、组织和组成遭到破坏或接近于破坏状态。 在变质层部分存在变形和应力,还有其物理的和化学的影响等。硬度和 表面强度变化等机械性质和耐腐蚀性等化学性质也与基体材料不同。 硬脆材料经研磨后的表面 ,经研磨的单晶硅表面,使用氟、硝酸系列的 溶液进行化学浸蚀,依次去掉表层,用电子衍射法进行晶体观察时,从 表层向内部的顺序为非晶体层或多晶体层、镶嵌结构层、畸变层和完全 结晶结构。另外,从使用 X射线衍射法的弹塑性学的观点来评价,则表 层是由极小的塑性流动层构成,其下是有异物混人的裂纹层,再下则是 裂纹层、弹性变形层和主体材料。 在研磨金属材料时,虽不发生破碎,但是磨粒转动和刮削时,由于材料 承受了塑性变形,通常形成与上述硅片相类似的加工变质层。相反,例 如是多晶的金属材料,则越接近被加工的表层,晶粒越微细,累积位错 在最表层,变成非晶质状态。在这部分,金属与大气中的活性氧结合, 变得活跃。另外,有时发生因塑性变形而使磨粒等容易嵌进金属。
浮动抛光
浮动抛光(Float Polishing)使用高平面度平面并带有同心圆或螺旋沟槽的锡 抛光盘,使抛光盘及工件高速回转,在二者之间抛光液呈动压流体状态,形成一层液 膜,从而使工件在浮起状态下进行抛光。 1977 年,Namba和Tsuwa首次使用了浮动抛光加工蓝宝石单晶体时表面粗 糙度低于1nm。此技术发展应用到抛光不锈钢、铸铁、镍等金属(1980),以及硼硅 酸盐玻璃,熔融硅和低膨胀系数等光学材料(1980-1987),工件表面粗糙度达到了 1-2 Å。 Touge和Matsuo(1996)研究了铁酸盐多晶体的浮动抛光,采用金刚石磨料, 其抛光速度要比传统抛光方法高 2.7倍。目前,采用浮动抛光方法抛光计算机磁头的 磁隙面,可防止出现晶界差,获得Rz2nm的表面粗糙度。于浮动抛光容易获得很高精 度的平面形状,可用于光学平晶,铌酸锂、水晶等功能陶瓷材料基片批量加工。
微细粒子撞击工件表面时,在接触点产生高温高压。 高温使工件表层原子晶格中空位增大;高压使磨粒的 原子扩散到工件表层的原子空位上,工件表层的原子 也扩散到磨粒中。扩散到工件中的磨粒原子成为表层 的杂质原子,减弱了本体原子的联系。
EEM方法的剪切作用
加了速的微小 粒子弹性冲击 被加工表面的 原子晶格,使 表层不平的原 子晶格受到极 大的剪切力, 从而移去这层 不平的原子, 这是不需经过 扩散过程的机 械作用的结果。
5.2.1 研磨加工的机理和特点
研磨加工通常使用1μm到几十μm的氧化铝和 碳化硅等磨粒和铸铁等硬质材料的研具。
磨粒的工作状态
1) 磨粒在工件与研具之间 进行转动;
2) 由研具面支承磨粒研磨 加工面;
3) 由工件支承磨粒研磨加 工面。
研磨的机理
由于工件、磨粒、研具和研磨液等的不同,上述三种研磨方法 的研磨表面状态也不同。表面的形成,是在产生切屑、研具的磨损 和磨粒破碎等综合在一起的复杂情况下进行的。 硬脆材料的研磨 微小破碎痕迹构成的无光泽面; 磨粒不是作用于镜面而是作用在有凸凹和裂纹等处的表面上, 并产生磨屑。 金属材料的研磨 表面没有裂纹; 对于铝材等软质材料,研磨时有很多磨粒被压入材料内; 对刀具和块规等淬火工具钢等可确保有块规那样的光泽表面。
1.水蒸气发生器 2.工件 3.抛光盘 4.载荷 5.保持架 6.蒸汽喷嘴 7.加热器 8.偏心凸轮
第5章 超精密研磨与抛光
Chapter 5 Ultra Precision Lapping and Polishing
5.1 研磨和抛光的概述
利用工件与研具相对运动, 通过研磨剂作用而获得高质 量、高精度的加工方法。 研磨和抛光的历史很长。 玉器。 中国古代的铜镜。 眼镜,最早出现于1289 年的意大利佛罗伦萨。 望远镜和显微镜是在文 艺复兴时期发明的。
行星轮式双面平面研磨机
行星轮式双面平面研磨机
超精密平面研磨机
可以用单 面研磨, 也可以用 双面研磨。 进行高质 量平行平 面研磨时, 需使用双 面研磨。
单面研磨机
平面研磨的研具
为确保几何形状精度,研磨端面小的高精度平 面工件时要使用弹性变形小的研具;除特种玻 璃外,可以用在加工成平面的金属板上涂一层 四氟乙烯,或镀铅和铟; 为获得高的表面质量,在工件材料较软时,有 时使用半软质(如锡)和软质(如沥青)的研 磨盘,主要问题是不易保持平面度,优点是表 面变质层小、表面粗糙度小。
5.2.2 抛光加工的机理和特点
使用<1μm的微细磨粒; 软质材料抛光垫:沥 青、石蜡、合成树脂 和人造革等。 微小的磨粒微小的磨 粒被抛光器弹性地夹 持研磨工件。因而, 磨粒对工件的作用力 很小,即使抛光脆性 材料也不会发生裂纹。
抛光的加工机理
1) 由磨粒进行的机械抛光可塑性地生成切 屑。但是它仅利用极少磨粒强制压入产 生作用。 2) 借助磨粒和抛光器与工件流动摩擦使工 件表面的凸因变平。 3) 在加工液中进行化学性溶析。 4) 工件和磨粒之间有直接的化学反应而有 助于上述现象。
1.工件 2.水晶平板 3.调节螺母 4.腐蚀液 5. 抛光盘
5.5.4 无磨料抛光
水合抛光(Hydration polishing)
水合抛光是一种利用在工件界面上产生水合反应的新型高效、超精密抛光方法。主 要特点是不使用磨粒和加工液,加工表面无污染。 使用杉木抛光盘抛光蓝宝石, 最终表面粗糙度Rz小于1nm。
5.3 研磨和抛光的主要工艺因素
项
研磨法
目
加工方式 加工运动 驱动方式 材料 形状 表面状态
内
容
单面研磨、双面研磨 旋转、往复 手动、机械驱动、强制驱动、从动 硬质、软质、人造、天然 平面、球面、非球面、圆柱面 有槽、有孔、无槽
研具
磨粒
种类 材质、形状 粒径
水质 油质
金属氧化物、金属碳化物、氮化物、硼化物 硬度、韧性、形状 0.01um~几十um
圆柱面的研磨
球面的研磨
5.5 新原理的超精密研磨抛光
传统的研磨抛光方法是完全靠微细磨粒的机械 作用去除被研磨表面的材质,达到很高的加工 表面。 最近出现新原理的研磨抛光方法其工作原理有 些已不完全是纯机械的去除,有些不用传统的 研具和磨料。这些新的研磨抛光方法可以达到 分子级和原子级材料的去除,并达到相应的极 高几何精度和无缺陷无变质层的加工表面。
水面滑行抛光
水面滑行抛光(Hydroplan Polishing),是 借助流体压力使工件基片从抛光盘面上浮起, 利用具有浸蚀作用的液体作加工液的抛光方法, 不使用磨料,是一种化学抛光方法。 Gormley(1981)等人以及Ives(1988)等 人为获Байду номын сангаасGaAs, InP 和HgCdTe等半导体晶体的 光滑、无损伤表面采用了此抛光方法。工件受 到甲醇、甘醇和溴的混合物的侵蚀,在H2气中、 600℃高温下热腐蚀15分钟,以10μm/min 的 去除率进行GaAs,InP基板表面无损伤抛光。 直径 2.5cm 基板,其平面度在 0.3μm以内。
5.2.4抛光的加工变质层
关于抛光的加工变质层,即使工件是硬脆材料, 抛光时也不会出现裂纹,加工变质层的结构与 深度应当与研磨有相当大的不同。 由氧化铈磨粒和沥青研具精加工的石英振子镜 面,其加工变质层的结构可使用氟化氨的饱和 水溶液腐蚀来检测。根据检测结果得知,由表 层向组织内部的结构顺序是抛光应力层,经腐 蚀出现的2次裂纹应力层,2次裂纹影响层和完 全结晶层,整个深度为3um。
Type IV
未充填聚合物
抛光垫的修整
抛光前
抛光后
修整器
三种磨粒分布方式
任意分布型
均匀分布型
成簇分布型
抛光液类型
絮状抛光液
胶状抛光液
高质量平面的研磨抛光工艺规律
研磨运动轨迹应能达到研磨痕迹均匀分布,并且不重叠; 硬质研磨盘在精研修形后,可以获得平面度很高的研磨表面,但要求很 严格的工艺条件。硬质研磨盘要求材质均匀,并有微孔容纳微粉磨料。 软质和半软质研磨盘容易获得表面变质层小、和表面粗糙度极小的研磨 抛光表面,主要问题是不易保持面型,不易获得很高的平面度。 使用金刚石微粉等超硬磨料可以达到很高的研磨抛光效率。在最后精密 抛光硅片、光学玻璃、石英晶片时,使用SiO2,CeO2微粉和软质研磨盘 容易得到表面变质层和表面粗糙度小的优质表面,不易获得很高的平面 度。 研磨平行度要求很高的零件时,可采用上研磨盘浮动以消除上下研磨盘 不平行误差;小研磨零件实行定期180°方位对换研磨,以消除因零件 厚度不等造成上研磨盘倾斜而研磨表面不平行。 在研磨剂中加入一定量的化学活性物质,可以提高研磨抛光的效率和表 面质量。