金属切削过程热力耦合的三维数值仿真_颜怡霞
球面磨削温度场数值仿真的研究
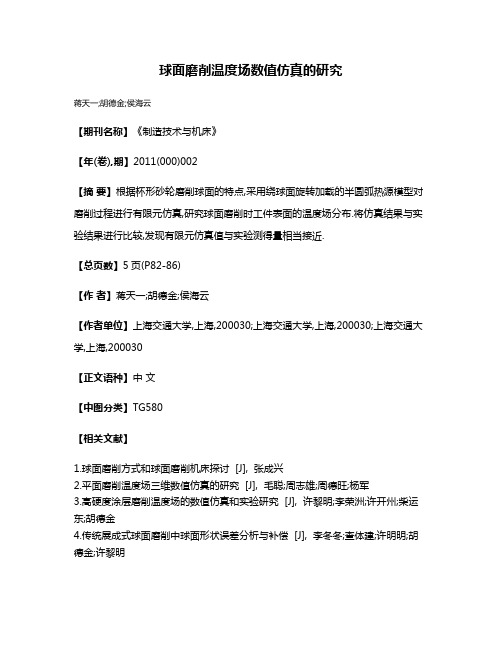
球面磨削温度场数值仿真的研究
蒋天一;胡德金;侯海云
【期刊名称】《制造技术与机床》
【年(卷),期】2011(000)002
【摘要】根据杯形砂轮磨削球面的特点,采用绕球面旋转加载的半圆弧热源模型对磨削过程进行有限元仿真,研究球面磨削时工件表面的温度场分布.将仿真结果与实验结果进行比较,发现有限元仿真值与实验测得量相当接近.
【总页数】5页(P82-86)
【作者】蒋天一;胡德金;侯海云
【作者单位】上海交通大学,上海,200030;上海交通大学,上海,200030;上海交通大学,上海,200030
【正文语种】中文
【中图分类】TG580
【相关文献】
1.球面磨削方式和球面磨削机床探讨 [J], 张成兴
2.平面磨削温度场三维数值仿真的研究 [J], 毛聪;周志雄;周德旺;杨军
3.高硬度涂层磨削温度场的数值仿真和实验研究 [J], 许黎明;李荣洲;许开州;柴运东;胡德金
4.传统展成式球面磨削中球面形状误差分析与补偿 [J], 李冬冬;查体建;许明明;胡德金;许黎明
5.高硬度球面磨削中球面形状误差分析与补偿 [J], 李冬冬;许明明;侯海云;胡德金;许黎明
因版权原因,仅展示原文概要,查看原文内容请购买。
典型零件形体的热变形模型及其有限元仿真
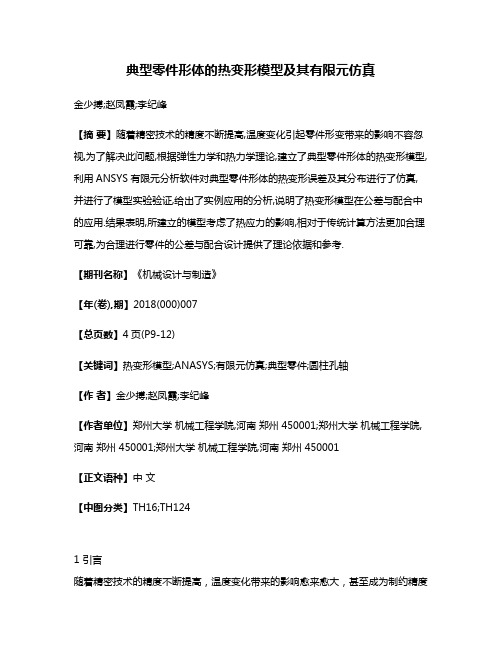
典型零件形体的热变形模型及其有限元仿真金少搏;赵凤霞;李纪峰【摘要】随着精密技术的精度不断提高,温度变化引起零件形变带来的影响不容忽视,为了解决此问题,根据弹性力学和热力学理论,建立了典型零件形体的热变形模型,利用ANSYS有限元分析软件对典型零件形体的热变形误差及其分布进行了仿真,并进行了模型实验验证,给出了实例应用的分析,说明了热变形模型在公差与配合中的应用.结果表明,所建立的模型考虑了热应力的影响,相对于传统计算方法更加合理可靠,为合理进行零件的公差与配合设计提供了理论依据和参考.【期刊名称】《机械设计与制造》【年(卷),期】2018(000)007【总页数】4页(P9-12)【关键词】热变形模型;ANASYS;有限元仿真;典型零件;圆柱孔轴【作者】金少搏;赵凤霞;李纪峰【作者单位】郑州大学机械工程学院,河南郑州 450001;郑州大学机械工程学院,河南郑州 450001;郑州大学机械工程学院,河南郑州 450001【正文语种】中文【中图分类】TH16;TH1241 引言随着精密技术的精度不断提高,温度变化带来的影响愈来愈大,甚至成为制约精度的决定因素,并使传统的热变形误差理论失去作用[1]。
近年来,文献[2-5]中对轴类、孔类零件在均匀温度场和非均匀温度场下的热变形规律进行了研究和探索。
文献[6]中以有限元为工具,研究了稳态场下圆柱筒尺寸变化规律;文献[7]中基于ANSYS对主轴热变形进行了建模与预测分析;文献[8]中对模块化工具系统中非线性温度下的主轴热变形位移量进行了数学建模,并提出了补偿模型。
但以上研究大都针对孔轴零件进行热变形研究,对球类、板类零件研究较少。
基于弹性力学和热力学建立了典型零件形体的热变形数学模型,基于ANSYS有限元分析软件对典型零件形体的热形误差及其分布进行了仿真,并进行了实验验证,最后进行了实例应用分析。
2 典型零件形体的热变形模型圆柱孔类、轴类、板类、球类零件是机械结构中的典型的基本零件形体。
齿轮成形磨削加工热力耦合数值仿真研究

削热会在齿轮表 面产 生较高的温度 , 容易引起工件表 面烧 伤 ; 另一方 面磨削热 会在工件 表层产生 梯度变化较
大 的温度场 , 从而形成磨削残余应力 , 造成工件 表层 金相组织 变化 , 既会影 响齿轮 磨削加工 的精度 , 也会影 响
齿轮使用 的寿命 。文 章借 助工程分 析软 件 A b a q u s 和 Ma t l a b , 基 于磨 削移 动热 源理 论和 三角形 热源 分布模
Ab s t r a c t : Ge a r f o r m g r i n d i n g, wh i c h i s c o m mo n l y u s e d f o r g e a r f i n i s h ma c h i n i n g,c a n g r e a t l y i mp r o v e
c o u pl i n g o f g e a r f o r m g r i nd i ng pr o c e s s
Z HANG Ku i — b a n g , HAN J i a n g, XI A Li a n, YANG Qi n g - y a n
中图分类号 : T G5 8 0 文献标识 码 : A 文章 编号 : 1 0 0 3 — 5 0 6 0 ( 2 0 1 5 ) 1 0 — 1 2 9 7 — 0 6
Nu me r i c a l s i mu l a t i o n o f t h e r mo - me c ha n i c a l
( S c ho ol o f Ma c h i n e r y a n d Au t o mo b i l e En g i n e e r i n g,He f e i Un i v e r s i t y o f Te c h n o l o g y,H e f e i 2 3 0 00 9 ,Chi na )
硬质合金相WC热力耦合分解热力学和动力学模型

硬质合金相WC热力耦合分解热力学和动力学模型陶盈龙;朱国辉;蒲春雷;杨树宝【摘要】以AISI 1045钢为工件材料,YG 8硬质合金为刀具材料,在800℃×700 MPa热力耦合条件下进行扩散偶实验,利用SEM和EDS分析高速切削条件下扩散偶界面附近WC相演化及元素扩散分布行为.结果表明,WC在热力耦合作用下发生塑性变形,并破碎形成细小的WC颗粒,同时在工件侧检测到WC组成元素的分布,证明热力耦合下WC确实发生了破碎、分解回溶及扩散.基于此,建立热力耦合条件下的WC分解热力学和动力学模型,并计算颗粒尺寸和温度对WC分解含量随时间变化的影响.结果表明:塑性变形碎化形成的WC颗粒尺寸越小及分解温度越高,WC 分解速率越大;800℃时,直径为10nm的WC颗粒完全分解时间约为0.7 μs.【期刊名称】《安徽工业大学学报(自然科学版)》【年(卷),期】2015(032)002【总页数】6页(P112-117)【关键词】刀具扩散磨损;热力耦合;WC分解;粒子变形回溶【作者】陶盈龙;朱国辉;蒲春雷;杨树宝【作者单位】安徽工业大学冶金工程学院,安徽马鞍山243002;安徽工业大学冶金工程学院,安徽马鞍山243002;北京科技大学材料科学与工程学院,北京100083;安徽工业大学机械工程学院,安徽马鞍山243002【正文语种】中文【中图分类】TG115金属切削中,第二变形区高的应力(变)分布及温度分布造成刀具的磨损形式主要有粘结磨损、磨料磨损和扩散磨损[1]。
其中,扩散磨损常指前刀面刀屑连接区,刀具中硬相组成元素向工件切屑扩散,使刀具表层软化而加速刀具破环的过程[2]。
高速切削时,切削温度较高,使刀具磨损中扩散磨损比重增加[3]。
Ti合金、中碳钢的切削实验表明[4-5],硬质合金刀具主要元素W,C,Co在切削中会扩散到切屑中,切削速度越高,扩散磨损量越大。
W和C在刀具中以化合物WC形式存在,元素扩散首先需要WC的分解。
TC11钛合金叶轮等温锻造过程三维有限元模拟

TC11钛合金叶轮等温锻造过程三维有限元模拟
史科;单德彬;吕炎
【期刊名称】《锻压技术》
【年(卷),期】2008(33)2
【摘要】设计了不同的TC11钛合金叶轮精密成形方案及模具装置,采用三维有限元程序DEFORM-3D对叶轮的等温成形过程进行数值模拟,研究了成形方案、模具结构和坯料形状等因素对成形过程中金属流动规律的影响,给出了不同压下量下锻件内部应力、应变分布情况及不同方案下载荷比较。
研究结果表明:采用等温成形技术可整体精密成形出带径向扭曲叶片的叶轮类锻件;采用较细的圆柱形坯料成形可有效地提高金属充填模腔的能力并降低成形所需载荷。
模拟结果与实验相符,可有效指导实际生产工艺的制定。
【总页数】4页(P19-22)
【关键词】TC11钛合金:叶轮;等温锻造;数值模拟
【作者】史科;单德彬;吕炎
【作者单位】哈尔滨工业大学材料科学与工程学院
【正文语种】中文
【中图分类】TG302
【相关文献】
1.TC11钛合金压气机盘等温锻造工艺研究 [J], 魏志坚
2.汽轮机钛合金叶片锻造过程的三维刚粘塑性有限元数值模拟 [J], 王金吕;吴静
3.TC11钛合金叶片精锻过程三维热力耦合有限元模拟 [J], 王中原;齐广霞
4.TC4钛合金锻件锻造过程三维热力耦合有限元模拟 [J], 吕成;张立文;牟正君;裴继斌
5.TC11钛合金多道次镦拔工艺三维有限元模拟 [J], 王忠堂;段小亮;张海燕;宋鸿武;张士宏
因版权原因,仅展示原文概要,查看原文内容请购买。
基于ABAQUS的TC11钛合金车削力仿真和参数优化
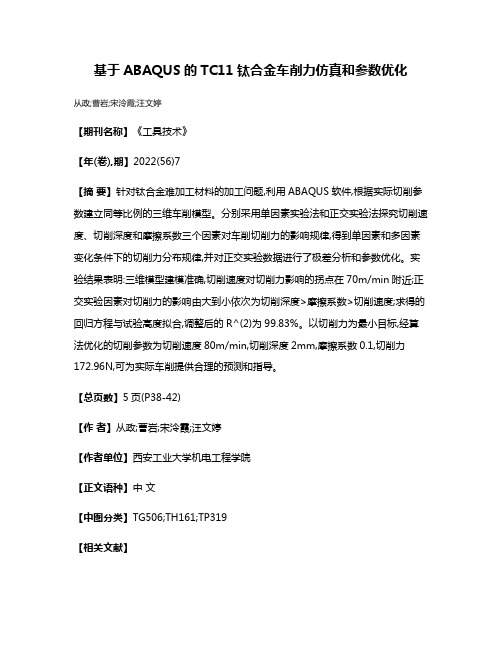
基于ABAQUS的TC11钛合金车削力仿真和参数优化
从政;曹岩;宋泠霞;汪文婷
【期刊名称】《工具技术》
【年(卷),期】2022(56)7
【摘要】针对钛合金难加工材料的加工问题,利用ABAQUS软件,根据实际切削参数建立同等比例的三维车削模型。
分别采用单因素实验法和正交实验法探究切削速度、切削深度和摩擦系数三个因素对车削切削力的影响规律,得到单因素和多因素变化条件下的切削力分布规律,并对正交实验数据进行了极差分析和参数优化。
实验结果表明:三维模型建模准确,切削速度对切削力影响的拐点在70m/min附近;正交实验因素对切削力的影响由大到小依次为切削深度>摩擦系数>切削速度;求得的回归方程与试验高度拟合,调整后的R^(2)为99.83%。
以切削力为最小目标,经算法优化的切削参数为切削速度80m/min,切削深度2mm,摩擦系数0.1,切削力172.96N,可为实际车削提供合理的预测和指导。
【总页数】5页(P38-42)
【作者】从政;曹岩;宋泠霞;汪文婷
【作者单位】西安工业大学机电工程学院
【正文语种】中文
【中图分类】TG506;TH161;TP319
【相关文献】
1.基于ABAQUS的TC11单颗粒砂带磨削过程仿真
2.基于灰色关联理论的空冷辅助车削钛合金端面的工艺参数优化
3.基于灰色理论的TC4钛合金车削工艺参数优化
4.基于响应曲面法的钛合金干式车削工艺参数优化
5.TC11钛合金力热耦合仿真分析及双目标参数优化
因版权原因,仅展示原文概要,查看原文内容请购买。
切削加工热力耦合建模及其试验研究
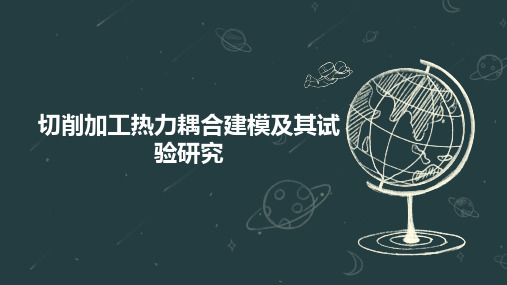
文献综述
自20世纪初以来,切削加工热力耦合建模及其试验研究一直是机械工程领域的 研究热点。早期的研究主要集中在基于经验的公式拟合和简化模型的建立上, 如摩擦学、传热学和弹塑性力学等。随着计算机技术和数值计算方法的快速发 展,研究者们开始采用数值模拟方法对切削加工过程中的热力耦合行为进行模 拟,从而更准确地预测切削温度和刀具磨损等情况。
3、本研究采用实验与数值模拟相结合的方法,对切削加工过程中的热力耦合 行为进行了深入研究。通过考虑材料变形、摩擦生热和热传导等多种因素,建 立了相应的数学模型,从而更准确地预测切削温度和刀具磨损等情况。
参考内容
高速切削加工技术及其加工工艺在现代化工业制造中具有广泛的应用前景。这 种技术以其高效率、高精度和高表面质量的特点,成为机械制造、汽车工业、 航空航天等领域的热点技术。本次演示将详细介绍高速切削加工技术的定义和 特点,高速切削加工工艺及其在各行业的应用前景,最后对高速切削加工技术 的未来发展方向和挑战进行总结。
高速切削加工工艺是指利用高速切削加工技术进行切削加工的工艺流程和技术 参数。高速切削加工工艺包括以下步骤:首先,选用合适的刀具材料,如硬质 合金、陶瓷等,这些材料具有高硬度、高耐磨性和高耐热性等特点。其次,确 定合理的切削参数,如切削速度、进给速度、刀具角度等,这些参数需要根据 工件材料、刀具材料等因素进行调整。最后,选择适合的冷却剂和润滑剂,以 降低切削温度和减小刀具磨损。
高速切削加工技术是一种采用高速度、高进给和高转速的切削加工方法。它具 有以下特点:首先,高速切削加工技术可以实现高效率的加工,有效缩短了加 工周期,提高了生产效率。其次,高速切削加工技术可以实现高精度的加工, 有效提高了工件的精度和表面质量。最后,高速切削加工技术还可以实现低温 切削,降低了切削力和切削热,避免了工件的热变形和烧伤等问题。
TA11钛合金叶片制坯过程三维热力耦合数值模拟
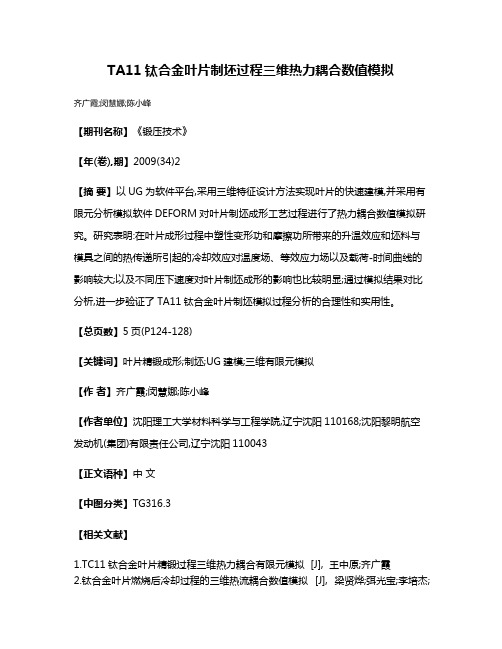
TA11钛合金叶片制坯过程三维热力耦合数值模拟
齐广霞;闵慧娜;陈小峰
【期刊名称】《锻压技术》
【年(卷),期】2009(34)2
【摘要】以UG为软件平台,采用三维特征设计方法实现叶片的快速建模,并采用有限元分析模拟软件DEFORM对叶片制坯成形工艺过程进行了热力耦合数值模拟研究。
研究表明:在叶片成形过程中塑性变形功和摩擦功所带来的升温效应和坯料与模具之间的热传递所引起的冷却效应对温度场、等效应力场以及载荷-时间曲线的影响较大;以及不同压下速度对叶片制坯成形的影响也比较明显;通过模拟结果对比分析,进一步验证了TA11钛合金叶片制坯模拟过程分析的合理性和实用性。
【总页数】5页(P124-128)
【关键词】叶片精锻成形;制坯;UG建模;三维有限元模拟
【作者】齐广霞;闵慧娜;陈小峰
【作者单位】沈阳理工大学材料科学与工程学院,辽宁沈阳110168;沈阳黎明航空发动机(集团)有限责任公司,辽宁沈阳110043
【正文语种】中文
【中图分类】TG316.3
【相关文献】
1.TC11钛合金叶片精锻过程三维热力耦合有限元模拟 [J], 王中原;齐广霞
2.钛合金叶片燃烧后冷却过程的三维热流耦合数值模拟 [J], 梁贤烨;弭光宝;李培杰;
曹京霞;黄旭
3.叶片制坯过程三维热力耦合数值模拟 [J], 余江山;齐广霞;李淑梅
4.漏斗型结晶器内坯壳凝固过程热力耦合数值模拟 [J], 金昕;任廷志;关杰;李强
5.钛合金挤压三维热力耦合数值模拟技术研究 [J], 何铁宁;李海峰
因版权原因,仅展示原文概要,查看原文内容请购买。
- 1、下载文档前请自行甄别文档内容的完整性,平台不提供额外的编辑、内容补充、找答案等附加服务。
- 2、"仅部分预览"的文档,不可在线预览部分如存在完整性等问题,可反馈申请退款(可完整预览的文档不适用该条件!)。
- 3、如文档侵犯您的权益,请联系客服反馈,我们会尽快为您处理(人工客服工作时间:9:00-18:30)。
。但是由于切削
过程本身是很复杂的 工 艺 过 程, 它不但涉及到弹塑性 力学 、 断裂力学, 还有 热 力 学 和 摩 擦 学 等, 因此利用解 析方法很难对切削机 理 进 行 定 量 的 分 析 和 研 究; 同 时 对金属切削过程中内部应力 、 应变 受实验技术的限制, 和温度的变化也不能获得较准确的实时测量结果 。 计 使得利用 算机的快速更新和有 限 元 技 术 的 快 速 发 展, 有限元技术对金属的切削过程进行仿真成为可能 。 近
= u + Δ t ( t + Δ t) u N ( t - ( Δ t / 2 ) ) 分别为第 N 个质点当前时 和u
N ( t + ( Δt / 2) )
∫P d S
i S
( 2)
N N 间段和前一个时间段的中点速度,u ( t + Δ t) 和 u t 则分别
将力 平 衡 方 程 ( 2 ) 代 入 能 量 守 恒 方 程 ( 1 ) , 可得 热 — 力耦合的能量守恒方程
引言
金属切削工艺主要是通过刀具切除材料表面多余 的材料层来获得理想的工件形状 。 切削广泛用于现代 例如在 汽 车 、 铁 路、 轮船和飞机制造等都 制造工业中, 离不开金属的切削工艺 。 因此, 为了提高切削质量 、 提 减少成本, 较好地理解金属切削过程机理是非 高效率 、 国内外许多学者就金属切削 常必要的 。 正因为如 此, 进行大量的理论 分 析 和 实 验 研 究
∫ρ v
V
i
∫ ∫
S
∫ρ
V
(
珚 Q + bi vi ) dV + ( 1)
( 9)
(
P i vi - Η ) dS
运动方程的计算 采 用 中 心 差 分 时 间 积 分, 当前时 段的速度和位移由下式求的
v i 为 速 度 场,U 为 给 定 内 能,珚 Q 为给定体积热 式中, b i 为给定体积力, P i 为单位面积上的边界力, H为 流, t 表示时间 。 边界上单位面积的热流强度, 积分形式的力平衡方程为
[1 3]
年来, 国内外对金属 切 削 工 艺 的 有 限 元 模 拟 研 究 已 有 较多的研究报道
[4]394404[57]
, 但是这些研究大多局限于
在三维切 削 过 程 的 数 值 模 拟 方 面 还 鲜 有 报 二维模型, 道 。 然而, 在实际切削过程中, 工件和刀刃具有三维的 几何形状; 工件和刀具的相对移动也不总是正交的; 因 此切削是在三维状态 下 形 成 的, 要准确描述三维的切 应当建立三 维 的 数 值 模 型 来 模 拟 实 际 的 切 削 削过程, 8]中 虽 然 对 金 属 切 削 过 程 进 过程 。 而郭建英在文献[ 行了三维有 限 元 分 析, 但 也 仅 局 限 于 应 力、 应变的模 拟, 没有模拟切削过程温度场的变化 。 考虑到三维切削 过 程 热 力 耦 合 计 算 的 复 杂 性, 本 文以金属块体为研究 对 象, 采用动态显式积分有限元 程序 ABAQUS , 建立热弹塑性模型, 模拟切屑的形成过 程, 对切削过程进行三维数值仿真 。 对切屑的形成 、 工 分离等模拟技术进行初步研究, 获得 件与刀具的接触 、 工件和切屑中的残余应力 、 应变和温度的分布, 同时分
为该质点在当前时间段结束和当前时间段开始时的位 ¨N 移,u t 代表质点在当前时间段的加速度 。 稳定时间步长 Δ t 由下式确定
∫[ (
V
v i U + dV = ρ 珚 σ ij Q - x i t
)
]
∫H d S
S
( 3)
Δ t ≤ min
(
L min L 2 min , Cd 2α
基本控制方程 在切削过程中, 随着刀具的运动, 工件发生变形主
D、 p 为应变率参数, 本文的 屈服强度和静态屈服强度, , 工 件 的 塑 性 变 形 和 切 屑—刀 具 界 面 的摩擦是产生热量的 主 要 热 源, 生成的热量作为热载 荷, 一半施加给工件, 另一半则施加给刀具 。 由塑性变 形功和摩擦产生的热量分别见式( 6 ) 和式( 7 ) q pl = η σ d ε p q fr = F fr v r
The cutting processes of a metal block were numerically simulated by the dynamic explicit finite element code
the simulation presented the variation of temperature , ABAQUS. Taking thermo-mechanical coupling effect into consideration , stress and strain distribution in the workpiece and chip. The effective plastic strain failure criterion was applied to modeling the chip separation and plastic formation. The phenomenon of the contact and friction between the workpiece and the cutting tool were described. And the effect of the cutting velocity on the chip formation was analyzed. This work will help as a reference to tackle more complex cutting processes. Key words Metal cutting ; 3D ; Thermomechanical coupling ; Numerical simulation Corresponding author : CHEN YuZhe ,E-mail : chyzh @ caep. ac. cn ,Tel : + 86 816 2484417 ,Fax : + 86 816 2281485 The project supported by the Foundation of China Academy of Engineering Physics ( No. 2005Z0302 ) . Manuscript received 20091015 ,in revised form 20100211.
[9]2. 1. 14. 5. 4
∫
( 6) ( 7)
q 为塑 性 功 转 化 的 单 位 体 积 热 流; η 为 塑 性 功 式中, 生成 热 的 比 例 因 子, 按 照 经 验, 对金属一般取 η = 0. 9 ; σ 为应力; ε p 为塑性应变; q fr 为摩擦热流; F fr 为 接触表面摩擦力; v r 表示表面相对滑动速度 。 发生在工件和空气以及刀具和空气中的热交换为 q = αk ( T - Tk ) 的温度 。 在一个时间步 Δ t 中, 温度场的计算采用向前差分 那么第 N 个质点在当前时间段的温度 时间 积 分, θ ( t + Δ t) 等于前一个时间段的温度 θ t 与这个温度的变化 N θ 即 t 之和,
Journal of Mechanical Strength
2011 ,33 ( 6 ) : 845849
金属切削过程热力耦合的三维数值仿真
*
3D NUMERICAL SIMULATION OF METAL CUTTING PROCESSES USING A THERMOMECHANICAL COUPLED APPROACH
846
机
械
强
度
·
2011 年
析切削速度对不同形貌切屑形成的影响 。 分析方法与 结果为金属切削过程的数值模拟以及机理研究提供技 术参考 。
·
pl 珔 ε = D
σ (σ
珚
0
-1
)
p
( 5)
pl 珔 珚 式中, ε 为等效塑性应变率, σ 和 σ 0 分别为动态等效
1
1. 1
切削过程数值模拟的关键技术
pl
主变形区是指从刀具的前端点 要集中于两个变形区, 延伸至未变形工件和 已 变 形 的 切 屑 的 相 邻 处, 在此区 域材料承受大的剪切变形 。 另外由于塑性变形产生的 切 热量也会使得此区 域 的 温 度 升 高 。 在 次 变 形 区 内, 屑沿着工件表层和刀 具 交 界 面 滑 移, 此变形区内切屑 沿着工件与刀具的交 界 面 滑 动, 这里的温度升高是由 于刀具和切削交界面的摩擦生热而造成的 。 因此切削 工艺从整个加工过程看, 虽然属于冷加工范畴, 但就切 屑形成的局部看, 却 具 有 高 温 的 特 点。金 属 在 高 速 切 剧烈的摩擦和 塑 性 变 形 使 得 局 部 区 域 的 温 度 迅 削下, 速上升, 材 料 的 各 种 性 能 参 数 势 必 受 到 温 度 的 影 响。 为了分析这种与高温 、 高应变率耦合的大变形和断裂 本文采用热力耦合的动态显式积分有限元方法, 问题, 基本控制方程
)
( 11 )
P i = n i σ ij , 式中,σ ij 为柯西应力, 其 中 ni 表 示 表 面 S v i 的单 位 法 线 方 向, 表示节点速度在三个方向的偏 x i i = 1, 2, 3; j = 1, 2, 3。 导, 根据虚功原理, 结构位移 u i 需满足下式 δ u i dV = σ ij x i V v i ρb i δu i dV - ρ δu i dV t V V
L min 为 单 元 的 最 小 特 征 尺 寸; C d 为 介 质 中 的 弹 式中, k 为 介 质 的 导 热 率,c 为 介 质 的 导 性波速; α = k / ρ c , 热系数 。 1. 2 切屑形成和分离的模拟 切削加工是一个 被 加 工 材 料 不 断 分 离 的 过 程, 在