高难度的汽车物流管理BMW的例子
物流管理案例分析:宝马制造厂创新物流作业

宝马制造厂创新物流作业和通用、福特、戴姆勒·克莱斯勒三大汽车巨子主打公共型汽车分歧,宝马以豪华汽车为主。
宝马出产的汽车中绝大大都都是按赐顾帮衬客个性化要求进行定制的,例如新车型X5 SUV(行为良多功能车)给车主供给了8种车体结构、12种颜色、19个策念头型号和其他60多个个性化要求可供选择。
是以,宝马在全球各地的经销商处只保有很有限的车辆,它把发卖工作的重心放在汽趁魅展厅上,在那儿那里顾客可以进行不美观摩,并综合个性需求进行下单。
1998年,宝马成立了一个新的车身制造车间,扩充了组装线,专门用来装配X5 SUV,厂房面积扩大到2 100 000平方英尺。
2001年宝马又一个新的车身制造车间落成,专门用来制造和装配双排座Z4敞篷跑车。
Spartanburg制造厂是宝马惟一的同时出产这两个车型的工场,出产出的车辆面向全球发卖。
这也是Spartanburg惟一的两个车型。
为了顺应定制出产的需要,宝马对南卡罗莱那州Spartanburg的制造厂进行了扩充,从头设置了厂内结构,对物料搬运系统进行改良,实施新的软件系统,在整个制造流程中实施实时信息掌控,实施接单出产和柔性出产。
对于每一个制造厂来说,达到厂内空间的全数操作是至关主要的。
宝马有自己的零部件仓库,但为了便利装配工作,它在组装厂内也储存有部门经常用备件。
宝马原有的7 500平方英尺的存储区域只能知足一条出产线的装配工作,当它在Spartanburg制造厂添加出产线时,就挤占了原出产线的组装用备件存储区域。
增添出产线往后,组装车间备用件储存量增大,摆在宝马面前的是,要么扩大存储面积,要么找出缔造性解决这个问题的做法。
面临货色措置量大和空间有限的两难境地,宝马最终在车间诚恳行立体仓储体例,安装了五个立体存储单元采用立体存储体例使宝马省去了800平方英尺的车间地面仓储面积。
同时为了便于操作工人提取货色,立体存储单元中存放的货色的高度可自动调节。
案例一宝马项目
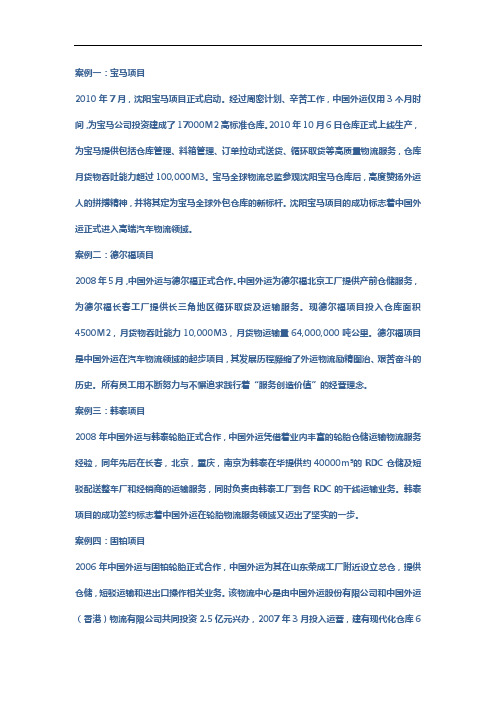
案例一:宝马项目2010年7月,沈阳宝马项目正式启动。
经过周密计划、辛苦工作,中国外运仅用3个月时间,为宝马公司投资建成了17000M2高标准仓库。
2010年10月6日仓库正式上线生产,为宝马提供包括仓库管理、料箱管理、订单拉动式送货、循环取货等高质量物流服务,仓库月货物吞吐能力超过100,000M3。
宝马全球物流总监参观沈阳宝马仓库后,高度赞扬外运人的拼搏精神,并将其定为宝马全球外包仓库的新标杆。
沈阳宝马项目的成功标志着中国外运正式进入高端汽车物流领域。
案例二:德尔福项目2008年5月,中国外运与德尔福正式合作。
中国外运为德尔福北京工厂提供产前仓储服务,为德尔福长春工厂提供长三角地区循环取货及运输服务。
现德尔福项目投入仓库面积4500M2,月货物吞吐能力10,000M3,月货物运输量64,000,000吨公里。
德尔福项目是中国外运在汽车物流领域的起步项目,其发展历程凝缩了外运物流励精图治、艰苦奋斗的历史。
所有员工用不断努力与不懈追求践行着“服务创造价值”的经营理念。
案例三:韩泰项目2008年中国外运与韩泰轮胎正式合作,中国外运凭借着业内丰富的轮胎仓储运输物流服务经验,同年先后在长春,北京,重庆,南京为韩泰在华提供约40000m³的RDC仓储及短驳配送整车厂和经销商的运输服务,同时负责由韩泰工厂到各RDC的干线运输业务。
韩泰项目的成功签约标志着中国外运在轮胎物流服务领域又迈出了坚实的一步。
案例四:固铂项目2006年中国外运与固铂轮胎正式合作,中国外运为其在山东荣成工厂附近设立总仓,提供仓储,短驳运输和进出口操作相关业务。
该物流中心是由中国外运股份有限公司和中国外运(香港)物流有限公司共同投资2.5亿元兴办,2007年3月投入运营,建有现代化仓库6座,总仓储面积71000m³,月出入库4万吨,月进出库条数达到200万条。
固铂项目为中国外运在继米其林轮胎业务之后,成功运作的第二大知名轮胎物流项目,同时扩大了中国外运在轮胎物流服务领域的领军优势。
宝马制造厂的创新物流作业
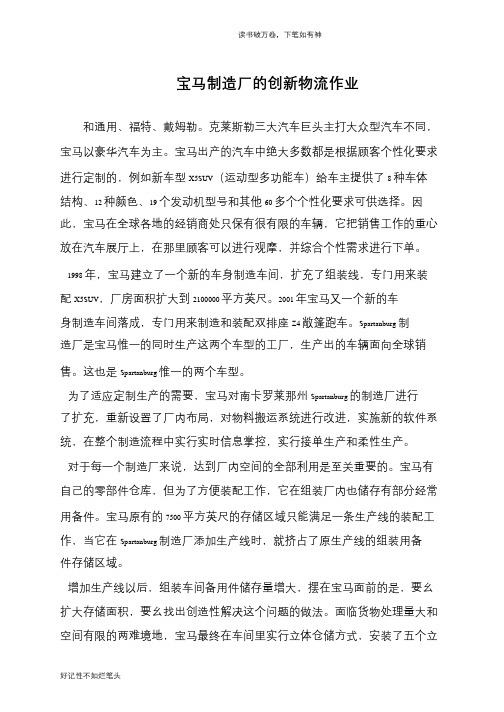
读书破万卷,下笔如有神宝马制造厂的创新物流作业和通用、福特、戴姆勒。
克莱斯勒三大汽车巨头主打大众型汽车不同,宝马以豪华汽车为主。
宝马出产的汽车中绝大多数都是根据顾客个性化要求进行定制的,例如新车型X5SUV(运动型多功能车)给车主提供了8 种车体结构、12 种颜色、19 个发动机型号和其他60 多个个性化要求可供选择。
因此,宝马在全球各地的经销商处只保有很有限的车辆,它把销售工作的重心放在汽车展厅上,在那里顾客可以进行观摩,并综合个性需求进行下单。
1998 年,宝马建立了一个新的车身制造车间,扩充了组装线,专门用来装配X5SUV,厂房面积扩大到2100000 平方英尺。
2001 年宝马又一个新的车身制造车间落成,专门用来制造和装配双排座Z4 敞篷跑车。
Spartanburg 制造厂是宝马惟一的同时生产这两个车型的工厂,生产出的车辆面向全球销售。
这也是Spartanburg 惟一的两个车型。
为了适应定制生产的需要,宝马对南卡罗莱那州Spartanburg 的制造厂进行了扩充,重新设置了厂内布局,对物料搬运系统进行改进,实施新的软件系统,在整个制造流程中实行实时信息掌控,实行接单生产和柔性生产。
对于每一个制造厂来说,达到厂内空间的全部利用是至关重要的。
宝马有自己的零部件仓库,但为了方便装配工作,它在组装厂内也储存有部分经常用备件。
宝马原有的7500 平方英尺的存储区域只能满足一条生产线的装配工作,当它在Spartanburg 制造厂添加生产线时,就挤占了原生产线的组装用备件存储区域。
增加生产线以后,组装车间备用件储存量增大,摆在宝马面前的是,要幺扩大存储面积,要幺找出创造性解决这个问题的做法。
面临货物处理量大和空间有限的两难境地,宝马最终在车间里实行立体仓储方式,安装了五个立好记性不如烂笔头。
{物流管理}BMW的物流管理中心

(物流管理)BMW的物流管理中心配送管理实务02汽车物流案例下载-样例.doc汽车生产和零部件企业物流案例二○○八年五月目录长久:扎根汽车物流4整车企业如何才能实现实时物流管理7大连柴油机厂整合供应链有成效9汽车零部件物流运输系统设计11汽车制造业的第三方物流策略及应用14现代物流--汽车企业降低成本的法宝16BMW的物流管理中心19丰田公司的实时物流管理战略21上海通用:打倒存货“魔鬼” 降低物流成本23TNT物流北美公司RFID技术于汽车零部件配送中的应用25福田物流,于快车道上奔驰27重庆安吉天地红岩物流XX公司的物流优化29本田(HONDA)汽车的供应链改造32上海通用的供应链整合34零部件物流的长安模式36物理管理之高难度的汽车物流38澳大利亚丰田汽车备件物流配送系统40解析汽车供应物流共同化模式43壹汽大众轿车二厂物流配送模式46中国制造业企业的物流发展49ILIPT开启汽车物流的新设想52东风汽车零部件的调达物流模式54震后汽车业调查:震颤的供应链58福特:顶级供应链之旅61北京现代:高效物流系统支撑企业高速发展64长久:扎根汽车物流长久公司创建于1992年,前身为1990年创建的长春市绿园区捷达汽车发送XX公司。
1997年成立吉林省长久实业XX公司,2003年8月正式成立吉林省长久集团。
目前,设有17个子公司,8个分支机构,总资产6.5亿元。
于中国汽车物流业中,长久可排进前三甲,能提供整车物流规划、仓储、运输、汽车销售、售后服务等服务。
经过多年的发展,长久于汽车物流市场找到了自己的壹片生存和发展天地。
为近身了解长久,1.见好汽车物流市场中国汽车产业蓬勃发展,且已成为全球第三大汽车市场。
据有关统计,2003年中国汽车零部件行业的销售收入达3000亿元,约占整个汽车行业销售总额的1/3,其中汽车及零部件出口总额达47.1亿美元,出口国家和地区超过100个。
2004年,国产汽车产量507.05万辆,销售507.11万辆。
BMW零配件物流管理分析

•BWM零配件之运输
•运输控 制
➢根据生产步骤所需提出订单
•由生产顺序决定需要量,其零件大多在极短时间内 此种提出订单方式对整个送货链的控制及时间要求 用在大量、高价值或是变化大的零件。
➢根据当日需要量提出订单
•对于大多数的组装程序而言,只要确定当天需要 性货运公司在前一天从供货商处取货,把这些货物 多数只停放一晚,隔天就送抵BMW组装工厂。
• 缺点:
•以占用库存资金(年消耗量*单价) 为标准来划分,忽视了汽车零部件的 其他考核因素。
•模糊综合评判 法
•零部件 •库存
BMW零配件物流管理分析
•BWM零配件之仓储
➢ 根据模糊问题的各个评 价因素、评价标准、自 然状态以及各因素的相 对重要程度建立模糊综 合评价的模型。
•零部件 •库存
•
PPT文档演模板
•
PPT文档演模板
BMW零配件物流管理分析
•BWM零配件之仓储
PPT文档演模板
BMW零配件物流管理分析
•BWM零配件之仓储
PPT文档演模板
BMW零配件物流管理分析
•BWM零配件之仓储
PPT文档演模板
BMW零配件物流管理分析
•BWM零配件之仓储
PPT文档演模板
BMW零配件物流管理分析
•BWM零配件之仓储
BMW零配件物流管理分析
•BWM零配件之运输
PPT文档演模板
•供应商 •配送中心
•4S店
BMW零配件物流管理分析
•BWM零配件之运输
•由于供应商对配送
中心 的运输 为大批
量规模运输 ,而配送
•中配心送对中4心S 店选的址运模输 型为小批量 , 且汽车
宝马的三大秘籍案例分析答案

宝马的三大秘籍案例分析答案
案例:
宝马供应链管理的三大秘笈:
1.在定单方面,宝马BMW挖掘“当日需要量”潜力
2.在仓储方面,宝马BMW积极处理低存货带来的运输成本
3.供应链方面,宝马BMW已把合作伙伴纳入成为考量因子
分析:
1.在定单方面
宝马BMW挖掘“当日需要量”潜力在汽车组装零件的送货控制中,最重要的是提出订货需求,也就是把货物的需要量和日期通知物流采购中心。
与丰田公司、戴尔公司等全球知名企业施行JIT制相比,宝马BMW在生产规划过程中,可以针对10个月后所需提出订货需求,供货商也可藉此预估本身对上游供货商所需提出货物的种类及数量。
当然,这得随着生产日期的接近,双方才会更明确地知道需要量。
2.在仓储方面
宝马BMW积极处理低存货带来的运输成本为了降低宝马BMW的仓储设备成本,该公司向来积极减少本身存货数量,如此导致供货商送货频率的提高,造成货运成本提高。
“前置运送”及“主要运送”的费用计算有所不同,前者的费用计算是把转运点到供货商的路程、等待及装载时间都列入计算,与运送次数成正比,但与装载数量的多少无关。
而后者的费用计算是与货物量成正比,不受送货次数影响。
3.供应链方面
宝马BMW已把合作伙伴纳入成为考量因子现代企业的竞争已不
是企业与企业之间的竞争,而是供应链与供应链之间的竞争。
宝马
BMW公司很审慎地选择自己的合作伙伴,它把其供应链上的合作伙伴,纳入成本节约的考量因子,这也是物流链管理的意义所在。
在此基础上,他们建立成本方程式,例如在一次的前置运送中,安排替几个宝马BMW工厂同时取货。
德国宝马(BMW)的物流秘笈-物流案例
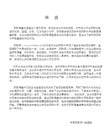
·排名靠前,赢得货主询价来
·相逢恨晚 从此寻代不再愁
八大港口第一时间运价
锦程物流网 - 资讯中心 >> 综合物流 >> 物流案例 >> 正文
首页 新闻 | 实务 | 海运 | 空运 | 陆运 | 综合物流 | 进出口 | 专题 | 工具 | 展会 | 人才 | 数据 |
1、在定单方面,BMW挖掘“当日需要量”潜力
在汽车组装零件的送货控制中,最重要的是提出订货需求,也就是把货物的需要量和日期通知物流采购中心。与丰田公司、戴尔公司等全球知名企业施行JIT制相比,BMW在生产规划过程中,可以针对10个月后所需提出订货需求,供货商也可藉此预估本身对上游供货商所需提出货物的种类及数量。当然,这得随着生产日期的接近,双方才会更明确地知道需要量。
大多数供货商接到BMW不同工厂的订单,可由同一个货运公司把货物集中到统合的转运站,然后由此再配送到各所需工厂,这样有产地安排取货路径,降低前置运送所需成本。同时也考虑各工厂间整合性仓储设备及运送的供应链管理、各个价值创造的部分程序及次系统,使其产生互动影响,出发点不再只限于局部最佳化,而是以整体成本为决定的依归。
汽车行业第三方物流优化设计——以宝马汽车企业物流为例

汽车企业的 第三方物流发展概 况作 以介 绍 , 然后从 效率 、 服务, 优势 、 考核 、 风险五 个方面提 出了对宝马汽 车企业物流发展过 程 中所
存在 的 问题 , 最后针 对各 个问题 分别给 出解 决对策 , 从 而使 汽车行业 第三 方物 流进 一步得 以优化 , 提 升企业效率和效益 。
与信 息 ,以保证仓 储 、 分拣 、 配货 、 运输 等 标准 化管理水平 、 效率有待提高 。 能力减 弱 , 对 企业形成 潜在 的威胁 。而且 作业 环节 间的协 调一致 , 降低整个物 流成 2 宝马汽 车企业 第三 方物流对顾 客的 没 有 其他 第三 方物 流企 业 与 其形 成竞 争 本, 提高整体效 益 。即生产 经营企业 为集 服务水平 有很大提升 的空间。没有充分利 使 企业在 二者关系 中显得 被动 , 第 三方物 中企 业 资源搞好 主业 , 把原 来要 由 自己处 用其 第三 方物 流帮 助 自己开 拓 市场 , 其在 流企业 具有与企业讨价还价 的能力。此 时 理 的 物流 活 动以 合 同方 式委 托 给专 业 物 市场 中的提 高竞争 力 , 进 而影 响了信 息传 如 果是三足 鼎立的形 式 , 各第 三方物 流企 流服 务企 业 , 同时通过 信息 系统 与物 流企 递速度 , 降低了物流服 务效 率和 质量。 业之间的竞争无疑会给企业带来很大的 业 保持密 切联系 , 以达到对 物流全 程管理 3 宝马汽 车企业 对第三 方物流企 业可 优 势 , 还 可 以变被 动 被主 动 , 也 不 会有 一
一
、
汽 车行 业物流背景分 析
( 一) 国 内汽 车 物 流 现 状
( 二) 第三方物流理论 l 汽车企业物流主 要包括供应物流 、 生 ( 三) 优 势 第三 方物流 ( T h i r d P a r t y L o g i s t i c s , 简 产物 流 、 销售物 流 、 售后物 流等 几个 方面 。 对第 三方物流 企业 单一 的依靠 , 会 使 称T P L ) 是指独立 于供需双 方 , 利 用信息体 宝 马汽车 的第 三方物流 系统性 不够 完善 、 其对 本企 业 的物 流业 务 上介 入程 度 的 过 系有效管理备 物流作业 , 提 供相 关的数据 信 息化程 度低 、库 存控制 可进一 步优 化 、 深 , 能 力过 度加 强 , 使 企业 对 物流 的 管理
- 1、下载文档前请自行甄别文档内容的完整性,平台不提供额外的编辑、内容补充、找答案等附加服务。
- 2、"仅部分预览"的文档,不可在线预览部分如存在完整性等问题,可反馈申请退款(可完整预览的文档不适用该条件!)。
- 3、如文档侵犯您的权益,请联系客服反馈,我们会尽快为您处理(人工客服工作时间:9:00-18:30)。
高难度的汽车物流管理
B M W的例子
The following text is amended on 12 November 2020.
高难度的汽车物流管理—BMW的例子
汽车制造工业对物流供应要求相当高,其中最难的地方在于有效提供生产所需的千万种零件器材。
居世界汽车领导地位的德国BMW公司,针对顾客个别需求生产多样车型,因而让难度已经颇高的汽车制造物流,更增添其复杂性。
其3个在德国境内负责3、5、7系列车型的工厂,每天装配所需的零件高达4万个运输容器,供货商上千家。
面对如此庞大的供应链,非藉助一套锦囊妙计不可。
BMW的订单要求
在汽车组装零件的送货控制中,最重要的是提出订货需求,也就是把货物的需要量和日期通知物流采购中心。
BMW在生产规划过程中,可以针对10个月后所需提出订货需求,供货商也可藉此预估本身对上游供货商所需提出货物的种类及数量。
不过,随着生产日期的接近,双方才会更明确地知道需要量。
针对送货控制而言,一般可分为两种不同形式:一为根据生产步骤所需提出订单,另一种为视当日需要量提出需求。
前者为由生产顺序决定需要量(Just-in-Sequence),其零件大多在极短时间内多次运送,由于此种提出订单方式对整个送货链的控制及时间要求相当严格,因此适用在大量、高价值或是变化大的零件。
对于大多数的组装程序而言,只要确定当天需要量就足够了,区域性货运公司在前一天从供货商处取货,把这些货物储放在转运点,大多数只停放一晚,隔天就送抵BMW 组装工厂。
在送抵BMW工厂的先前取货并停放在转运点的过程称为「前置运送」,而第二阶段送达BMW工厂的步骤称为「主要运送」。
过去几年里,BMW公司已把根据生产顺序所需的订货方式最佳化。
视当日需要量提出订单方式仍有极大发展潜能,所以BMW公司目前积极对此项最佳化进行研究。
高送货频率,高成本
为了降低BMW的仓储设备成本,该公司向来积极减少本身存货数量,如此导致供货商送货频率的提高,例如每周多次送货,或甚至达到必须每天送货,造成货运成本提高。
「前置运送」及「主要运送」的费用计算有所不同,前者的费用计算是把转运点到供货商的路程、等待及装载时间都列入计算,与运送次数成正比,但与装载数量的多寡无关。
而后者的费用计算是与货物量成正比,不受送货次数影响。
最佳化潜能
基本上前置运送与仓储设备成本是互相抵触的,因为为了降低仓储成本而减少仓储设备,会造成运送频率及其成本的提高。
为降低前置运送成本,尽量一次满载,囤积存货,势必造成仓储成本的提高。
因此,两者间取得平衡,降低整体成本,达到最佳化的策略势在必行。
(如图1所示)
图1:设备及前置运送成本与送货频率之关系
大多数供货商接到BMW不同工厂的订单,可由同一个货运公司把货物集中到统合的转运站(Hub),然后由此再配送到各所需工厂,这样有效地安排取货路径,降低前置运送所需成本。
同时也考虑各工厂间整合性仓储设备及运送的供应链管理、各个价值创造的部分程序及次系统,使其产生互动影响,着眼点不再只限于局部最佳化,而是以整体成本为决定的依归。
成本方程式及最佳化运算法
在最佳化的过程里,首先必须定义一个成本方程式,此方程式的变量为:货运距离及重量的运输费率,此参考基准为以到1993年止所实施的GNT及GFT(货物远、近距离运输费率表)。
不过这费率参考表并不适用于BWM公司的前置运送上,因为在前置运
送中,同一货运公司并不只是服务某一固定供货商,因而无法以单纯方式计算运输成本。
图2:物流成本最佳化之潜能
图2显示目前的货运费率及实际前置运送费用,图中显示横向补助的效果(区域
(1)),蓝色虚线部分表示前置运送实际成本,棕色虚线部分为前置运送的费率。
以目前的运送费率最佳化,会产生高送货频率(图2中(2))。
如果依实际前置运送成本计算,则最佳化点将移向送货频率低处(图2中(3))。
如此,可把整体成本在实际前置运送成本下达到最低值(图2中(4)所视为物流成本节省部分)。
BMW 公司尝试把其供应链上的合作伙伴(如运输公司等),纳入成本节约的考量因子,这也是物流链管理的意义所在。
根据上述考虑因素,建立成本方程式,当中亦考虑到不同取货方式,例如在一次的前置运送中,安排替几个BMW 工厂同时取货。
这个成本方程式是建立在最佳化计算法的基础上,考虑因素为对供货商成本最低化之送货频率、其它与实务有关的不同附随条件,例如尽可能让运输工具满载、每周固定时间送货等。
如果同一货运公司替多个BMW 工厂送货,则必须安排送货先后次序,以达成本最佳化。
此外,运送货量最好一星期内平均分配,让运输工具及仓储达到最高使用率,不致影响等待进货时间。
个案专题研究结果
目前
送貨頻率
(通常為高頻率)(2)
最佳化送貨頻率(很多狀況為
低頻率)(3)
際置運送本
置運送
費率成
本
在實際
運送成本下的
體成本送費率下的
體成本
根据此最佳化研究结果,对多数货运公司而言,高载率及每天送货所造成的成本最划算。
相反地,对小量的供货商而言,减少送货频率,可以明显降低整体成本。
图3所
示,对一个只专门服务BMW 的某工厂之供货商而言,在每天送货的情况下,前置运送的成本将占整体成本的大部分,而仓储设备所造成影响则较小。
如果这家供货商每周只送货两次,则会造成仓储设备需求提高,不过,前置运 送的节省部分可以贴补仓储成本提高的部分。
图3:BMW 公司某厂房送货过程的物流成本
图4为BMW 三个组装厂对同一家供货商的4种最佳化之不同选择,其共同处为整体成本差异不大,其中选择1的仓储设备及前置运送成本同时降低,节省成本约23%。
图4:3个BMW 工厂的供货商的4种最佳化替代方案 前景
此个案研究结果显示,采购过程的物流成本可明显地降低,这项最佳化只与规划之计
算法有关,可以很容易地整合到系统里。
此步骤只显示物流链管理的第一步,其它部分也具有最佳化潜能,例如供货商的处理程序及成本,更进一步的是考虑供货商的制造及库存状况。
如此,可以降低整个价值创造链上的库存成本,这也是整个物流供应链里,提高竞争力的最佳利器。
(经资中心 石育贤)
每日物
流成
本
經由最佳化節省整體成本
23%
前置運送成
本倉
儲設備成本
整
體
成
本
1234
目前
每日物
流成
本
經由最佳化節省整體成本
33%
目前5 次運送
/週最佳化:2 次運送
/週
送貨頻率
前置運送成本倉儲設備成
本
整
體
成
本。